合成氨工艺原理
布朗工艺合成氨
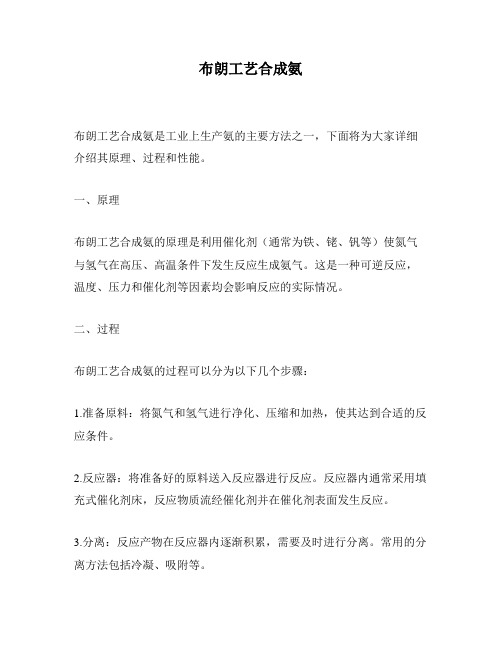
布朗工艺合成氨
布朗工艺合成氨是工业上生产氨的主要方法之一,下面将为大家详细介绍其原理、过程和性能。
一、原理
布朗工艺合成氨的原理是利用催化剂(通常为铁、铑、钒等)使氮气与氢气在高压、高温条件下发生反应生成氨气。
这是一种可逆反应,温度、压力和催化剂等因素均会影响反应的实际情况。
二、过程
布朗工艺合成氨的过程可以分为以下几个步骤:
1.准备原料:将氮气和氢气进行净化、压缩和加热,使其达到合适的反应条件。
2.反应器:将准备好的原料送入反应器进行反应。
反应器内通常采用填充式催化剂床,反应物质流经催化剂并在催化剂表面发生反应。
3.分离:反应产物在反应器内逐渐积累,需要及时进行分离。
常用的分离方法包括冷凝、吸附等。
4.再生:分离出的副产物可进一步回收利用,催化剂因为反应后表面的玻璃化碳堆积而失去活性,需要进行再生。
三、性能
布朗工艺合成氨具有以下优点:
1.反应速度快:由于催化剂的存在,反应速度大大加快。
2.运行成本低:布朗工艺合成氨的原材料易于获得,且反应过程中不需要大量的能源支持。
3.产品纯度高:反应后产生的氨气往往非常纯,只需一些简单的操作就可以达到工业使用标准。
以上就是关于布朗工艺合成氨的原理、过程和性能的详细介绍。
合成氨工艺及反应原理简介

合成氨工艺及反应原理简介合成氨工艺采用烃类蒸汽转化法。
天然气经加压至4.05MPa,经预热升温在脱硫工序脱硫后,与水蒸汽混合,进入一段转化炉进行转化制H2,随后进入二段转化炉,在此引入空气,转化气在炉内燃烧放出热量,供进一步转化,同时获得N2。
工艺气经余热回收后,进入变换系统,将CO变为CO2,随后经脱碳、甲烷化反应除去CO和CO2,分离出的CO2送往尿素工艺。
工艺气进入分子筛系统除去少量水份,为合成氨提供纯净的氢氮混合气。
氢氮混合气经压缩至14MPa,送入合成塔进行合成氨的循环反应,少量惰性气体经过普里森系统分离进行回收利用。
产品氨送往尿素工艺和氨罐保存。
合成氨工艺的5个过程:1、天然气脱硫:R-SH+H2=RH+H2S H2S+ZnO=H2O(汽)+ZnS2、转化CH4+H20(汽)=CO+3H2 CH4+2H2O(汽)=CO2+4H2 (H2+ 1/2 O2=H2O)3、变换:CO+H2O(汽)=CO2+H24、脱碳:1)K2CO3+CO2+H2O⇔2KHCO32KHCO3⇔K2CO3+CO2+H2O2)甲烷化:CO+3H2=CH4+H2O CO2+4H2=CH4+2H2O5、N2+3H2=2NH31 脱硫系统工艺流程及原理1.1流程天然气进入界区后分为两路:一路作原料气,另一路作燃料气。
原料天然气进入原料气压缩机吸入罐116-F,除去携带的液体,经过原料气压缩机102-J被压缩到4.05MPa(G),经过原料气预热盘管预热到399℃,接着原料气与来自合成气压缩机103-J一段的富氢气混合。
经过Co-Mo加氢器101-D把有机硫转换成H2S,将3 ml/m3的有机硫转化为无机硫,原料气中总硫为30~90ml/m3左右,经氧化锌脱硫槽脱硫至总硫小于0.5mg/m3。
随后进入氧化锌脱硫槽,天然气中的硫化物被ZnO所吸附,制得合格原料气。
ZnO脱硫槽共二个,可以串联或并联操作,一般串联操作。
阀门及管线的配置可以使任何一个脱硫槽停止使用而另一个继续运转。
合成氨生产工艺
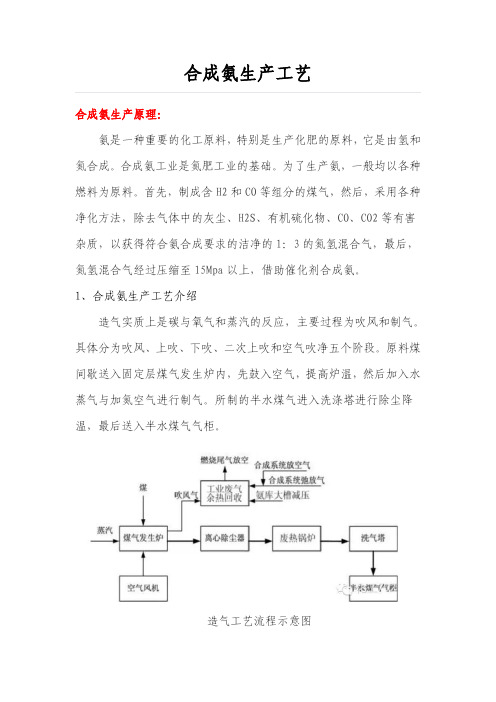
合成氨生产工艺合成氨生产原理:氨是一种重要的化工原料,特别是生产化肥的原料,它是由氢和氮合成。
合成氨工业是氮肥工业的基础。
为了生产氨,一般均以各种燃料为原料。
首先,制成含H2和CO等组分的煤气,然后,采用各种净化方法,除去气体中的灰尘、H2S、有机硫化物、CO、CO2等有害杂质,以获得符合氨合成要求的洁净的1:3的氮氢混合气,最后,氮氢混合气经过压缩至15Mpa以上,借助催化剂合成氨。
1、合成氨生产工艺介绍造气实质上是碳与氧气和蒸汽的反应,主要过程为吹风和制气。
具体分为吹风、上吹、下吹、二次上吹和空气吹净五个阶段。
原料煤间歇送入固定层煤气发生炉内,先鼓入空气,提高炉温,然后加入水蒸气与加氮空气进行制气。
所制的半水煤气进入洗涤塔进行除尘降温,最后送入半水煤气气柜。
造气工艺流程示意图2、脱硫工段煤中的硫在造气过程中大多以H2S的形式进入气相,它不仅会腐蚀工艺管道和设备,而且会使变换催化剂和合成催化剂中毒,因此脱硫工段的主要目的就是利用DDS脱硫剂脱出气体中的硫。
气柜中的半水煤气经过静电除焦、罗茨风机增压冷却降温后进入半水煤气脱硫塔,脱除硫化氢后经过二次除焦、清洗降温送往压缩机一段入口。
脱硫液再生后循环使用。
脱硫工艺流程图3、变换工段变换工段的主要任务是将半水煤气中的CO在催化剂的作用下与水蒸气发生放热反应,生成CO2和H2。
河南中科化工有限责任公司采用的是中变串低变工艺流程。
经过两段压缩后的半水煤气进入饱和塔升温增湿,并补充蒸汽后,经水分离器、预腐蚀器、热交换器升温后进入中变炉回收热量并降温后,进入低变炉,反应后的工艺气体经回收热量和冷却降温后作为变换气送往压缩机三段入口。
变换工艺流程图4、变换气脱硫与脱碳经变换后,气体中的有机硫转化为H2S,需要进行二次脱硫,使气体中的硫含量在25mg/m3。
脱碳的主要任务是将变换气中的CO2脱除,对气体进行净化,河南中科化工有限责任公司采用变压吸附脱碳工艺。
来自变换工段压力约为1.3MPa左右的变换气,进入水分离器,分离出来的水排到地沟。
合成氨工艺原理

合成氨工艺原理合成氨是一种重要的化工原料,广泛应用于肥料、化肥、炸药、染料、医药和塑料等工业领域。
合成氨工艺是通过氮气和氢气在催化剂的作用下发生反应,生成氨气的过程。
下面将介绍合成氨工艺的原理及相关知识。
首先,合成氨工艺的原理是利用哈伯-玻希过程进行氮气和氢气的催化反应。
在工业上,通常采用铁-钼催化剂,通过高温高压条件下进行反应。
氮气和氢气在催化剂的作用下,发生氮氢键的断裂和氢氮键的形成,生成氨气。
这个过程是一个放热反应,需要一定的温度和压力条件才能进行。
其次,合成氨工艺的原理还涉及到氮气和氢气的摩尔比。
在理想的情况下,氮气和氢气的摩尔比应该是1:3,这是为了保证所有的氮气都能够和氢气完全反应,生成氨气。
但在实际生产中,为了提高反应的效率和产量,通常会使用过量的氢气,以保证氮气得到充分利用。
另外,合成氨工艺的原理还涉及到催化剂的选择和运行条件的控制。
催化剂的选择对于反应的速率和选择性有着重要的影响。
铁-钼催化剂是目前应用最广泛的催化剂,它能够在较低的温度和压力下实现高效的氨气合成。
同时,工艺中的温度、压力、气体流速等参数的控制也是十分重要的,它们直接影响着反应的进行和产物的选择性。
最后,合成氨工艺的原理还涉及到反应平衡的问题。
氮气和氢气的反应是一个可逆反应,在一定条件下会达到动态平衡。
为了提高氨气的产量,通常会采取一些措施,如通过改变温度、压力或者利用吸收剂来移除产物,以促进反应向产物的方向进行。
综上所述,合成氨工艺的原理涉及到催化剂的选择、反应条件的控制、反应平衡的问题等多个方面。
通过合理的设计和操作,可以实现高效的合成氨反应,为相关工业领域提供重要的化工原料。
希望本文的介绍能够帮助大家更好地理解合成氨工艺的原理及相关知识。
工业合成氨知识点总结

工业合成氨知识点总结一、引言合成氨是一种重要的化工原料,广泛用于化肥、塑料、药品和其他化工产品的生产中。
而工业合成氨主要是通过哈伯-玻斯曼过程进行生产。
在这个过程中,氮气和氢气以高压、高温和催化剂的作用下,发生反应,生成氨气。
因此,工业合成氨的生产涉及了高压、高温、催化剂和气体分离等方面的工艺技术。
二、合成氨的反应原理工业合成氨的反应过程是氮气和氢气在催化剂的作用下,发生氧化还原反应,生成氨气。
这是一个放热反应,反应方程式为:N₂ + 3H₂ → 2NH₃ + 92.6kJ/mol从反应方程式可以看出,该反应需要大量的氢气,而氮气对反应也起到了催化作用。
在实际生产过程中,合成氨的反应条件一般为300-500°C的温度和100-250atm的压力,同时需要使用铁、钨或镍等金属为催化剂。
三、工业合成氨的生产工艺工业合成氨的生产工艺主要包括氢气制备、氮气制备、合成氨反应和氨气的提取等步骤。
1. 氢气制备氢气是工业合成氨的主要原料之一,通常是通过天然气重整法或电解水法进行制备。
a. 天然气重整法天然气经催化剂重整反应制得合成气,合成气中含有一定比例的氢气。
然后通过甲醇水煤气变换反应得到富含氢气的气体。
b. 电解水法将水分解为氧气和氢气的方法,使用电解槽进行电解水反应,得到纯度高的氢气。
2. 氮气制备氮气是工业合成氨的另一主要原料,一般是从空气中分离得到。
a. 常用的氮气制备方法包括分子筛吸附法、柱塔分离法等。
b. 分子筛吸附法:将空气经过分子筛吸附塔,通过吸附分离得到富含氮气的气体。
c. 柱塔分离法:通过茧状分离塔或塔内吸附塔将空气中的氮气和氧气分离出来。
3. 合成氨反应使用氢气和氮气作为原料,在高压、高温和催化剂(通常是Fe3O4、K₂O、CaO、Al₂O₃或者Ni)的作用下进行反应,得到氨气。
合成氨反应通常分为两个主要阶段:合成氨反应和氨气的提取。
在合成氨反应过程中,氮气和氢气以1:3的比例进入反应器,在压力为100-250bar、温度为300-500°C下进行化学反应。
合成氨工艺原理
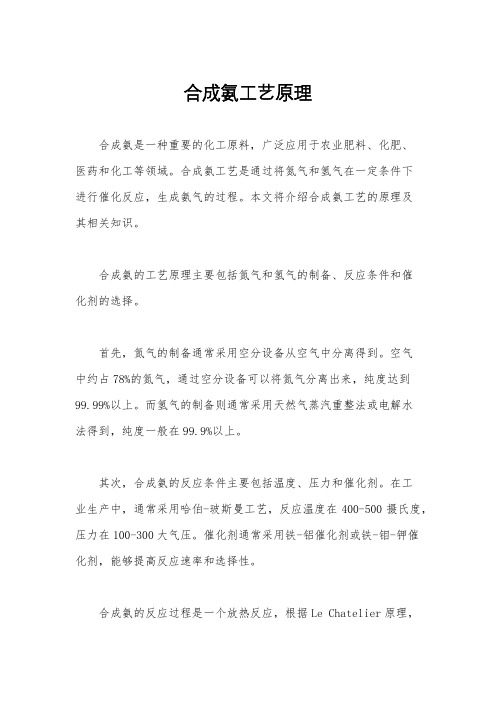
合成氨工艺原理合成氨是一种重要的化工原料,广泛应用于农业肥料、化肥、医药和化工等领域。
合成氨工艺是通过将氮气和氢气在一定条件下进行催化反应,生成氨气的过程。
本文将介绍合成氨工艺的原理及其相关知识。
合成氨的工艺原理主要包括氮气和氢气的制备、反应条件和催化剂的选择。
首先,氮气的制备通常采用空分设备从空气中分离得到。
空气中约占78%的氮气,通过空分设备可以将氮气分离出来,纯度达到99.99%以上。
而氢气的制备则通常采用天然气蒸汽重整法或电解水法得到,纯度一般在99.9%以上。
其次,合成氨的反应条件主要包括温度、压力和催化剂。
在工业生产中,通常采用哈伯-玻斯曼工艺,反应温度在400-500摄氏度,压力在100-300大气压。
催化剂通常采用铁-铝催化剂或铁-钼-钾催化剂,能够提高反应速率和选择性。
合成氨的反应过程是一个放热反应,根据Le Chatelier原理,在高温高压条件下,反应达到平衡时,氨气的生成量会增加。
同时,催化剂的选择也会影响反应速率和选择性,合适的催化剂能够提高反应效率和减少副反应产物的生成。
合成氨工艺的原理虽然简单,但在实际应用中仍然面临着一些挑战。
例如,如何提高反应速率和选择性,如何减少能耗和资源消耗,如何处理反应产物中的杂质等问题都是需要解决的。
因此,合成氨工艺的研究仍然具有重要意义。
总之,合成氨工艺是一项重要的化工工艺,其原理涉及氮气和氢气的制备、反应条件和催化剂的选择。
在实际应用中,需要综合考虑反应速率、选择性、能耗和资源消耗等因素,不断优化工艺条件,提高生产效率,减少环境污染,推动合成氨工艺的发展。
合成氨工艺培训
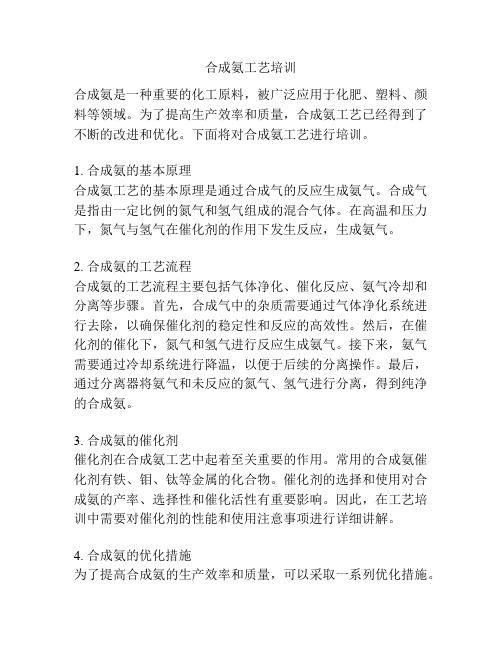
合成氨工艺培训合成氨是一种重要的化工原料,被广泛应用于化肥、塑料、颜料等领域。
为了提高生产效率和质量,合成氨工艺已经得到了不断的改进和优化。
下面将对合成氨工艺进行培训。
1. 合成氨的基本原理合成氨工艺的基本原理是通过合成气的反应生成氨气。
合成气是指由一定比例的氮气和氢气组成的混合气体。
在高温和压力下,氮气与氢气在催化剂的作用下发生反应,生成氨气。
2. 合成氨的工艺流程合成氨的工艺流程主要包括气体净化、催化反应、氨气冷却和分离等步骤。
首先,合成气中的杂质需要通过气体净化系统进行去除,以确保催化剂的稳定性和反应的高效性。
然后,在催化剂的催化下,氮气和氢气进行反应生成氨气。
接下来,氨气需要通过冷却系统进行降温,以便于后续的分离操作。
最后,通过分离器将氨气和未反应的氮气、氢气进行分离,得到纯净的合成氨。
3. 合成氨的催化剂催化剂在合成氨工艺中起着至关重要的作用。
常用的合成氨催化剂有铁、钼、钛等金属的化合物。
催化剂的选择和使用对合成氨的产率、选择性和催化活性有重要影响。
因此,在工艺培训中需要对催化剂的性能和使用注意事项进行详细讲解。
4. 合成氨的优化措施为了提高合成氨的生产效率和质量,可以采取一系列优化措施。
例如,在气体净化环节,可以优化催化剂的配置和操作条件,提高杂质的去除效率;在催化反应中,可以调整反应温度和压力,以提高氨气产率;在氨气冷却和分离过程中,可以优化冷却系统和分离器的设计,提高氨气的纯度和回收率。
通过以上培训内容,学员可以全面了解合成氨工艺的基本原理、工艺流程、催化剂选择和优化措施等方面的知识。
这将为生产实践提供理论指导,帮助提高合成氨生产的效率和质量。
5. 合成氨工艺的安全性和环保性在合成氨工艺中,安全性和环保性是非常重要的考虑因素。
合成氨工艺涉及高温和高压的反应条件,需要严格控制工艺参数和操作过程,以确保生产安全。
培训中可以介绍合成氨工艺的安全操作规范、应急措施以及对环境的影响评估。
6. 合成氨工艺的自动化控制为了提高生产的稳定性和控制精度,自动化控制在合成氨工艺中得到了广泛应用。
工业合成氨的基本原理化学

工业合成氨的基本原理化学工业合成氨是指通过工业方法将氮气和氢气反应得到氨气的过程。
这个过程通常采用的是哈伯-博士过程,也被称为氨合成反应,是在高温高压条件下进行的。
以下将详细介绍工业合成氨的基本原理化学。
工业合成氨的基本原理化学是指通过以下两步反应实现氮气和氢气的转化。
第一步反应是氮气的活化,也称为氮气的固氮。
氮气是一种非常稳定的分子,需要足够的能量才能使其发生反应。
在工业合成氨过程中,一般会使用催化剂来提供活化氮气所需的能量。
常用的催化剂是铁或铁合金,如铁铝合金。
这种催化剂在高温高压下具有较高的活性,能够有效地将氮气分子活化。
活化氮气分子中的电子转移到催化剂上,使氮气分子发生断裂。
第二步反应是氮气和氢气的结合生成氨气。
在活化的氮气与氢气接触催化剂的表面时,它们发生氢化反应。
由于催化剂表面上的氢原子数量较多,氢气在催化剂表面上吸附并被活化。
吸附的氢气分子与活化的氮气分子发生反应,生成氨气。
这个反应是一个可逆反应,同时也是一个放热反应。
在工业合成氨过程中,为了获得较高的氨产率,一般会采用多级反应器和循环气体的方法。
在工业合成氨过程中,除了以上两个基本反应外,还存在一些辅助反应。
例如,氮气和氢气的直接反应是一个较为缓慢的过程,需要高温和高压才能使其反应速率达到一定的程度。
为了提高反应速率,一般会加入一些促进剂,如氨催化剂。
这些促进剂可以提高反应的速率和选择性。
此外,工业合成氨还涉及一系列的工艺。
例如,氮气和氢气的混合需要一定的比例和流动速率,以确保反应的稳定性和高效性。
同时,需要精确控制反应的温度和压力,以提供合适的条件促进反应的进行。
此外,反应产生的氨气还需要经过一系列的分离和纯化步骤,以得到纯度较高的氨气。
总结起来,工业合成氨的基本原理化学是通过催化剂活化氮气,然后与氢气进行反应生成氨气。
这个过程需要高温高压条件,并且还涉及一系列的工艺来保证反应的稳定性和高效性。
通过工业合成氨,可以大量生产氨气,满足农业肥料和化工原料等的需求。
合成氨工作原理与工艺流程
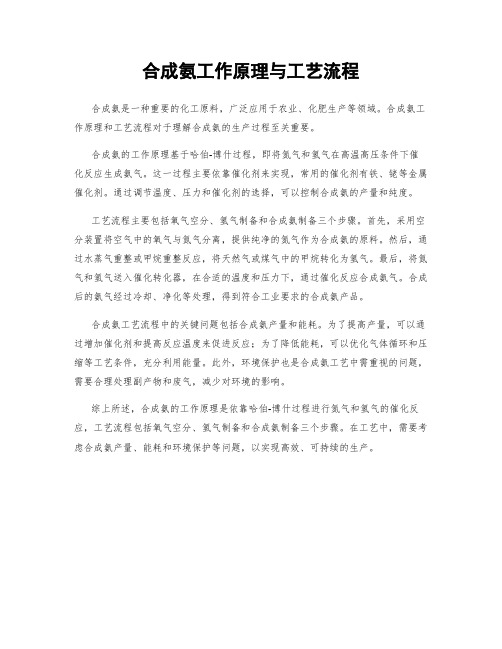
合成氨工作原理与工艺流程
合成氨是一种重要的化工原料,广泛应用于农业、化肥生产等领域。
合成氨工作原理和工艺流程对于理解合成氨的生产过程至关重要。
合成氨的工作原理基于哈伯-博什过程,即将氮气和氢气在高温高压条件下催化反应生成氨气。
这一过程主要依靠催化剂来实现,常用的催化剂有铁、铑等金属催化剂。
通过调节温度、压力和催化剂的选择,可以控制合成氨的产量和纯度。
工艺流程主要包括氧气空分、氢气制备和合成氨制备三个步骤。
首先,采用空分装置将空气中的氧气与氮气分离,提供纯净的氮气作为合成氨的原料。
然后,通过水蒸气重整或甲烷重整反应,将天然气或煤气中的甲烷转化为氢气。
最后,将氮气和氢气送入催化转化器,在合适的温度和压力下,通过催化反应合成氨气。
合成后的氨气经过冷却、净化等处理,得到符合工业要求的合成氨产品。
合成氨工艺流程中的关键问题包括合成氨产量和能耗。
为了提高产量,可以通过增加催化剂和提高反应温度来促进反应;为了降低能耗,可以优化气体循环和压缩等工艺条件,充分利用能量。
此外,环境保护也是合成氨工艺中需重视的问题,需要合理处理副产物和废气,减少对环境的影响。
综上所述,合成氨的工作原理是依靠哈伯-博什过程进行氮气和氢气的催化反应,工艺流程包括氧气空分、氢气制备和合成氨制备三个步骤。
在工艺中,需要考虑合成氨产量、能耗和环境保护等问题,以实现高效、可持续的生产。
KBR的煤制合成氨新工艺

KBR的煤制合成氨新工艺简介煤制合成氨是一种重要的工业化学反应过程,它通过利用煤作为原料,制造合成氨,用于生产化肥和其他化学品。
近年来,KBR公司开发了一种新的煤制合成氨工艺,该工艺具有更高的效率和更低的环境影响,成为行业内的关注焦点。
工艺原理KBR的煤制合成氨新工艺主要基于以下原理:1.煤气化:煤作为主要原料,在高温和高压条件下进行气化反应,生成一氧化碳和氢气。
这一步骤是整个工艺的关键步骤,对产率和产品质量影响显著。
2.合成氨产生:利用一氧化碳和氢气通过低温高压催化反应生成合成氨。
这一步骤需要高效的催化剂和适宜的反应条件,以获得高产率和高纯度的合成氨。
工艺优势KBR的煤制合成氨新工艺相比传统工艺具有以下优势:1.高效能源利用:新工艺能够最大程度地利用煤的能量,减少能源的浪费,提高能源利用效率。
2.低碳排放:通过优化催化剂和反应条件,新工艺能够显著减少二氧化碳等温室气体的排放,减少对全球气候的影响。
3.产品质量稳定:新工艺通过优化反应条件和催化剂选择,能够获得稳定的合成氨产品,提高化肥制造过程的可控性和产品质量。
4.生产成本降低:新工艺简化了反应步骤和操作流程,减少了设备投资和运营成本,提高了生产效益。
工艺应用KBR的煤制合成氨新工艺已经成功应用于多个工业化肥生产厂家,取得了良好的效果和经济效益。
该工艺广泛应用于制造化肥和其他化学品的生产过程中。
结论KBR的煤制合成氨新工艺是一种高效能源利用、低碳排放的工艺,可使化肥生产过程更加可持续和环保。
该工艺的应用加速了煤制合成氨领域的创新发展,推动了煤化工产业的进步。
相信随着技术的不断创新和工艺的优化,煤制合成氨工艺将在未来得到更广泛的应用和推广。
参考文献1.Yan, S., Li, W., Li, D., & Zhao, Z. (2017). A review on ammoniasynthesis catalysts for industry application. Chemical Engineering Journal, 310, 53-59.2.Joensen, F., Yates, I. C., & Rostrup-Nielsen, J. R. (2011). Industrial ammonia synthesis catalysts. In Handbook of heterogeneous catalysis (pp. 1919-1977). Wiley-VCH Verlag GmbH & Co. KGaA.3.Wu, Y. C., Ji, S. J., & Hu, S. H. (2011). The latest development for commercial KBR ammonia converter on energy-saving and emission reduction. China Nitrogen Fertilizer, 38(5), 24-27.。
合成氨的反应原理

合成氨的反应原理合成氨是一种重要的化学工业反应,其原理是将氢气和氮气在一定的条件下进行结合反应,生成氨气。
合成氨的反应原理是依据哈柏法的原理。
哈柏法是由德国化学家哈柏于1905年提出的,该法以铁为催化剂,将氮气和氢气在高温高压下进行反应,生成氨气。
在反应中,氢气和氮气的物质性质发生了变化。
氢气是无色无味的气体,在常温下为不活泼的分子气体,由两个氢原子组成。
氮气是一种无色无味的气体,也是不活泼的分子气体,由两个氮原子组成。
合成氨的反应物为氮气和氢气,反应物中氢气和氮气的化学键发生了断裂和形成的过程。
在背景条件下,铁催化剂有助于降低反应的活化能,促进氮气与氢气发生相互作用。
反应物中的氮气与氢气经过一系列的反应过程,最终会转化为氨气。
合成氨的反应需要在高温高压的条件下进行。
通常情况下,反应温度为400-500,压力约为150-200atm。
高温高压的条件对于将氢气和氮气转化为氨气非常重要,可以提高反应速率和产率。
此外,配合性的铁催化剂也是合成氨反应的关键。
反应中,氢气和氮气发生反应生成氨气的过程可以用以下化学方程式表示:N2 + 3H2 > 2NH3在这个方程式中,氮气与氢气的反应生成了氨气。
根据化学方程式可以看出,氮气和氢气的消耗是按照比例的。
每一摩尔的氮气需要消耗3摩尔的氢气才能生成2摩尔的氨气。
合成氨的反应发生在一个封闭的反应器中。
反应器内部有很强的耐压性,以承受高温高压条件下的反应过程。
反应器内的铁催化剂可以促进反应的进行,提高反应速率和产率。
同时,反应器内要保持一定的温度和压力条件,以便使反应物充分反应,生成氨气。
合成氨是一种重要的化学反应,广泛应用于化学工业的领域。
氨气是一种重要的化学原料,用于制造肥料、塑料等化学产品。
合成氨的反应原理和条件对于合成氨的产量和质量有着重要的影响,因此需要掌握合成氨的反应原理和工艺条件。
合成氨工艺原理

合成氨工艺原理合成氨是一种重要的化工产品,广泛应用于化肥、医药、塑料等领域。
合成氨工艺是通过氮气和氢气在催化剂的作用下进行反应,生成氨气的过程。
本文将从催化剂选择、反应条件、反应原理等方面介绍合成氨工艺的原理。
首先,催化剂的选择对合成氨工艺至关重要。
常用的催化剂包括铁、铑、钼等金属,它们能够促进氮气和氢气的反应,提高反应速率和产物选择性。
其中,铁是最常用的催化剂,它能够在较低的温度和压力下催化氮气和氢气的反应,降低能耗,提高生产效率。
其次,合成氨反应的条件对反应效果有着重要影响。
合成氨的反应是一个放热反应,通常在较高的温度(400-500°C)和压力(100-300atm)下进行。
高温能够提高反应速率,而高压则有利于提高氨气的产率。
此外,还需要适量的催化剂和适当的反应时间来保证反应的充分进行。
合成氨的反应原理主要是氮气和氢气在催化剂的作用下发生氮氢键的断裂和形成,生成氨气。
氮气分子中的三根共价键在催化剂的作用下被分解成氮原子,并与氢气中的氢原子结合形成氨气。
这一过程是一个放热反应,放出大量的热能,因此需要采取相应的措施来控制反应温度,防止过热。
合成氨工艺的原理虽然看似简单,但其中涉及的化学反应、热力学和动力学等知识都需要深入研究和理解。
只有充分了解合成氨工艺的原理,才能够更好地指导工业生产实践,提高合成氨生产的效率和质量。
总之,合成氨工艺的原理涉及到催化剂选择、反应条件和反应原理等多个方面。
只有在这些方面做到科学合理的安排和控制,才能够保证合成氨工艺的顺利进行,从而获得高效率和高产量的合成氨产品。
希望本文的介绍能够对合成氨工艺的理解有所帮助,同时也希望相关领域的研究者能够在此基础上做出更深入的研究和探索。
化工合成氨工艺原理及流程分析

化工合成氨工艺原理及流程分析合成氨是一种重要的化工原料,广泛用于制造化肥、塑料、炸药等工业产品。
化工合成氨的工艺原理及流程分析包括以下几个方面:氨合成反应原理、催化剂选择、反应器类型、反应条件等。
氨合成反应原理:合成氨的反应原理是通过氮气与氢气在适宜的温度、压力和催化剂条件下发生氨合成反应。
反应的化学方程式为:N2 + 3H2 → 2NH3、该反应是一个放热反应,反应热释放为-92 kJ/mol。
催化剂选择:在氨合成中,催化剂起到提高反应速率的作用。
常用的催化剂有铁、铑及铂铑合金等。
其中,铁是最常用的催化剂,它在常压、常温下较容易活化氮分子直接反应生成NH3反应器类型:氨合成反应器主要分为固定床反应器和流化床反应器两种。
固定床反应器是将氨合成催化剂装填在固定的反应器床层中,氮气和氢气在催化剂上发生反应。
流化床反应器则是将催化剂悬浮在气流中,气体通过床层时与催化剂接触反应。
反应条件:氨合成反应需要控制的反应条件包括合适的温度、压力和气体物质的配比。
一般来说,较高温度有利于增加反应速率,但过高会使催化剂失活。
常用的反应温度在300-550摄氏度之间。
反应压力的选择要保证合理的反应速率,一般在100-300atm之间。
氮气和氢气的配比一般为1:3,即1 mol氮气需要3 mol氢气参与反应。
1.氮气和氢气的净化:通过气体净化系统处理供应的氮气和氢气,去除其中的杂质,保证进入反应器的气体纯度。
2.反应器:将纯化后的氮气和氢气以合适的压力和比例输入反应器。
反应器内设置催化剂床层,使氮气和氢气在催化剂上发生反应生成氨。
3.冷却器:反应结束后,将反应后的气体通过冷却器冷却,使氨气在较低温度下凝结成液态。
4.分离器:将液态的氨与未反应的氢气和氮气通过分离器分离,以得到干净的合成氨。
5.回收和再利用:未反应的氢气和氮气可经再循环回收,以减少原料的消耗和降低生产成本。
总结:化工合成氨工艺原理及流程分析包括了氨合成反应原理、催化剂选择、反应器类型、反应条件等。
合成氨工艺原理

合成氨工艺原理
合成氨是一种重要的化工原料,广泛用于制备化肥、塑料、纤维素等产品。
合成氨的工艺原理主要包括两个步骤:氮气催化还原和氢气催化氧化。
氮气催化还原是指将氮气转化为氨气的化学反应。
该反应在催化剂的存在下进行,常用的催化剂有铁、钨等金属或金属合金。
氮气和氢气首先通过压缩机进行压缩,然后以适当的比例进入反应器中。
在反应器内,氮气分子被催化剂吸附并激活,形成活性吸附态。
氢气分子也被吸附到催化剂表面,并与氮气分子进行反应,生成氨气。
反应完成后,氨气被分离出来,纯度达到要求后可以作为成品使用。
氢气催化氧化是指将氢气转化为水的反应过程。
这一步骤是为了去除反应残留的氢气,同时防止反应产物中的氢气杂质。
在氮气催化还原后,残留的氢气与氧气一起进入氢气催化氧化反应器。
催化剂通常是铁氧化物或铝氧化物等,它们可以催化氢气和氧气反应生成水。
反应完成后,反应器中的氢气和水蒸气一同进入冷凝器,通过冷却和分离,分离出纯净的水。
以上就是合成氨的工艺原理,通过氮气催化还原和氢气催化氧化,在合适的条件下,可以高效地制备出纯度高的氨气。
这个工艺过程在化工工业中被广泛应用,为各行各业提供了重要的原料。
合成氨工艺流程原理
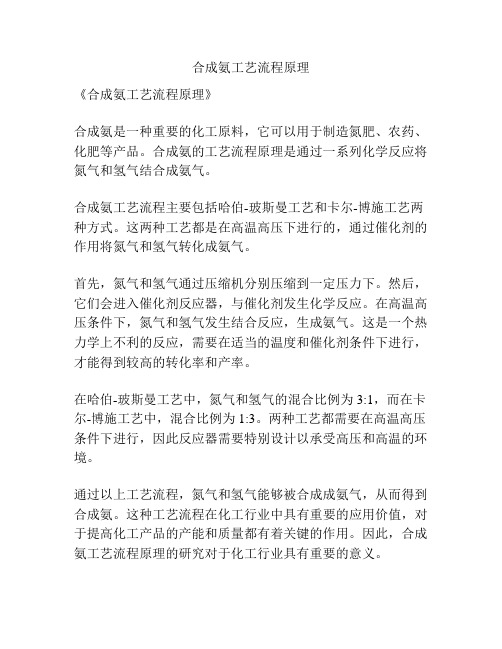
合成氨工艺流程原理
《合成氨工艺流程原理》
合成氨是一种重要的化工原料,它可以用于制造氮肥、农药、化肥等产品。
合成氨的工艺流程原理是通过一系列化学反应将氮气和氢气结合成氨气。
合成氨工艺流程主要包括哈伯-玻斯曼工艺和卡尔-博施工艺两种方式。
这两种工艺都是在高温高压下进行的,通过催化剂的作用将氮气和氢气转化成氨气。
首先,氮气和氢气通过压缩机分别压缩到一定压力下。
然后,它们会进入催化剂反应器,与催化剂发生化学反应。
在高温高压条件下,氮气和氢气发生结合反应,生成氨气。
这是一个热力学上不利的反应,需要在适当的温度和催化剂条件下进行,才能得到较高的转化率和产率。
在哈伯-玻斯曼工艺中,氮气和氢气的混合比例为3:1,而在卡尔-博施工艺中,混合比例为1:3。
两种工艺都需要在高温高压条件下进行,因此反应器需要特别设计以承受高压和高温的环境。
通过以上工艺流程,氮气和氢气能够被合成成氨气,从而得到合成氨。
这种工艺流程在化工行业中具有重要的应用价值,对于提高化工产品的产能和质量都有着关键的作用。
因此,合成氨工艺流程原理的研究对于化工行业具有重要的意义。
合成氨生产工艺介绍[整理]
![合成氨生产工艺介绍[整理]](https://img.taocdn.com/s3/m/d91ca5ee5122aaea998fcc22bcd126fff7055d8f.png)
合成氨生产工艺介绍[整理]合成氨是现代农业、化学工业、燃料等领域的重要原料。
工业合成氨的生产工艺主要是通过哈-博士过程进行的,简称H-B法。
这种方法是将空气中的氮气与氢气在催化剂的存在下进行化学反应,生成氨气。
1. 哈-博士过程的原理H-B法是将氮气和氢气分别通过加热、压缩和清洗等方式处理后,再将两气混合到催化剂层上进行反应。
催化剂通常选用铁、铑、钼等金属催化剂,也可以采用物理和化学合成的单一和复合催化剂。
在反应过程中,氢气在催化剂层上与氮气发生反应,生成氨气,同时放出大量的热量。
生成氨气后,氢气和氮气的剩余量将被回收再利用。
2. 生产工艺流程H-B法合成氨气的生产工艺流程主要包括氢气制备、氮气制备、氢氮混合、压缩、催化反应、分离纯化和氨气回收等环节。
(1)氢气制备:通过蒸汽重整、水气变换和煤制氢等方法将天然气、石油、煤等原料转化为氢气。
(2)氮气制备:常用的方法有空气分离法和氧化铵法。
空气分离法将空气经过压缩、冷却、除尘、空气分离等步骤制备氮气。
氧化铵法则是将高浓度的氨水与纯碳粉混合后在加热反应生成氮气。
(3)氢氮混合:通过控制氢气和氮气的比例制备合适的混合气体。
(4)压缩:利用压缩机将氢氮混合气体压缩至高压。
(5)催化反应:将高压氢氮混合气体经过加热后,进入催化反应器内,在催化剂作用下氮气和氢气发生化学反应生成氨气。
(6)分离纯化:将合成气中的氨气、氢和氮等组分进行分离和纯化,得到高纯度的氨气。
(7)氨气回收:将产生的氨气收集回收,同时将未反应的氢气和氮气回收再利用。
3. 工艺的优缺点H-B法的主要优点是工艺稳定,生产量大,产品纯度高,而且氨气的制备设备易于实现自动化控制,操作简单。
它是目前世界上最为成熟的合成氨气工艺。
但是,H-B法也存在一些缺点。
首先,该工艺所用的原材料,也就是天然气、石油、煤等等,属于有限资源,且成本较高。
其次,反应过程中可能产生一定的有毒和有害物质,对环境和人体健康造成影响。
合成氨工艺原理

合成氨工艺原理合成氨不论采用什么原料和生产方法,大体上包括三个工艺过程:(1)原料气的制造;( 2)原料气的净化(包括脱硫、变换脱除 CO,碳化、脱碳脱除 CO2,精炼脱除微量的 CO、 CO2、 H2S、 O2等);(3)氨的合成和为了满足气体净化及合成各工序工艺条件提供能量补偿的压缩工序。
生产出氨以后再根据需要加工成碳铵、尿素、硝铵等。
其详细原理如下(以煤为原料):一、造气工段合成氨生产所用的半水煤气,要求气体中(CO+H2)与 N2的比例为 3:1 左右。
因此生产上采用间歇地送入空气和蒸汽进行气化,将所得的水煤气配入部分吹风气制成半水煤气。
即以石灰碳化煤球、无烟块煤为原料,在高温下交替与空气和过热蒸汽进行气化反应( C+O2点燃 CO2+Q 、2C+O点燃 2CO+Q、2CO+O2点燃 2CO+Q2H2O(气) +C△CO+2H-Q 制得半水煤气,半水煤气经过除尘,余热回收,水洗降温制得合格的半水煤气,供后工段使用。
二、脱硫工段从造气工段的半水煤气中,除氢气和氮气外,还含有 27%左右 CO、9%左右的 CO2以及少量的硫化物,这些硫化物对合成氨生产是有害的。
它会腐蚀设备、管道,会引起催化剂中毒,会损坏铜液成份。
因此,必须除去少量硫化物,其原理:3用稀氨水(10—15tt )与硫化氢反应(NH3+H2S=NH4HS)将 H2 S 脱除至 0.07g/m (标)以下,使半水煤气净化,以满足合成氨生产工艺要求。
三、变换工段将脱 S 后的半水煤气(含 CO25%—28%)由压缩工段加压后经增温、加热,在一定的温度和压力下,在变换炉内借助催化剂的催化作用,使半水煤气中 CO与 H2O (气)进行化学反应,转变为 CO2和 H2(CO+H2O(气)催化剂高温 CO2+H2+Q),制得合格的变换气,以满足后工段的工艺要求。
其次,系统中设有饱和热水塔、甲交、一水加、二水加、冷却塔等换热设备,以便合理利用反应热和充分回收余热,降低能耗,同时降低变换气温度。
- 1、下载文档前请自行甄别文档内容的完整性,平台不提供额外的编辑、内容补充、找答案等附加服务。
- 2、"仅部分预览"的文档,不可在线预览部分如存在完整性等问题,可反馈申请退款(可完整预览的文档不适用该条件!)。
- 3、如文档侵犯您的权益,请联系客服反馈,我们会尽快为您处理(人工客服工作时间:9:00-18:30)。
合成氨工艺原理
合成氨不论采用什么原料和生产方法,大体上包括三个工艺过程:(1)原料气的制造;(2)原料气的净化(包括脱硫、变换脱除CO,碳化、脱碳脱除CO
2
,
精炼脱除微量的CO、CO
2、H
2
S、O
2
等);(3)氨的合成和为了满足气体净化及合
成各工序工艺条件提供能量补偿的压缩工序.生产出氨以后再根据需要加工成碳铵、尿素、硝铵等。
其详细原理如下(以煤为原料):
一、造气工段
合成氨生产所用的半水煤气,要求气体中(CO+H
2)与N
2
的比例为3:1左右。
因此生产上采用间歇地送入空气和蒸汽进行气化,将所得的水煤气配入部分吹风气制成半水煤气.即以石灰碳化煤球、无烟块煤为原料,在高温下交替与空气和
过热蒸汽进行气化反应(C+O点燃CO
2+Q 、2C+O点燃2CO+Q 、2CO+ O点燃2CO
2
+
Q
2H
2O(气)+C△CO+2H
2
-Q制得半水煤气,半水煤气经过除尘,余热回收,水洗降
温制得合格的半水煤气,供后工段使用。
二、脱硫工段
从造气工段的半水煤气中,除氢气和氮气外,还含有27%左右CO、9%左右的CO
2
以及少量的硫化物,这些硫化物对合成氨生产是有害的。
它会腐蚀设备、管道,会引起催化剂中毒,会损坏铜液成份.因此,必须除去少量硫化物,其原理:用稀
氨水(10—15tt)与硫化氢反应(NH
3+H
2
S=NH
4
HS)将H
2
S脱除至0.07g/m3(标)以下,
使半水煤气净化,以满足合成氨生产工艺要求.
三、变换工段
将脱S后的半水煤气(含CO25%-28%)由压缩工段加压后经增温、加热,在一定的温度和压力下,在变换炉内借助催化剂的催化作用,使半水煤气中CO与
H 2O(气)进行化学反应,转变为CO
2
和H
2
(CO+H
2
O(气)催化剂高温CO
2
+H
2
+Q),
制得合格的变换气,以满足后工段的工艺要求.其次,系统中设有饱和热水塔、甲交、一水加、二水加、冷却塔等换热设备,以便合理利用反应热和充分回收余热,降低能耗,同时降低变换气温度。
四、碳化与脱碳工段
1、碳化
将变换气中26%左右的CO
2用浓氨水与其反应(CO
2
+ H
2
O+ NH
3
=NH
4
HCO
3
)生成
碳酸
氢铵副产品,同时制得合格的原料气。
2、脱碳工段
用MEDA脱碳溶液将变换气中26%左右的CO
2
除去,制成合格的原料气,供后工段使用.
五、压缩机工段
合成氨原料气的制备、净化及氨的合成都要在一定的压力下进行.为适应变换、碳化、脱碳、精炼、合成等工段的工艺要求,要把气体加压,并按需要的不同压力分别输送到以上各工段,这些工作必须通过压缩机来完成。
因此,压缩工段就是运送气体和提高气体压力,以满足合成氨生产的原料气制备、净化和氨合成工段的需要。
六、精炼工段
用醋酸铜氨液来吸收经碳化、脱硫后的原料气中少量CO
2、CO、H
2
S等,制
得合格的精炼气,供合成工段使用.
七、合成工段
合成工段在合成氨生产中是最后一道工序,它是在高温、高压和有催化剂存在的条件下,将由精炼工段来的经过一系列处理的合格氢氮混合气体在合成塔内
进行化合反应,合成为氨。
(3H
2+N催化剂高温高压2 NH
3
),气态氨经冷凝分
离得液氨,液氨在氨冷器中气化后,送经碳化、精炼用。
多余的液氨作为商品氨。
未合成氨的氢、氮混合气继续在合成系统中循环。
合成放空气和氨罐弛放气回收利用.
八、冰机岗位
将气氨压缩、冷凝使之液化,然后将液氨送往氨贮槽或直接送入氨冷器蒸发制冷以满足合成氨生产中冷量的需要。