合成氨工艺指标[修改版]
合成氨与尿素生产工艺指标
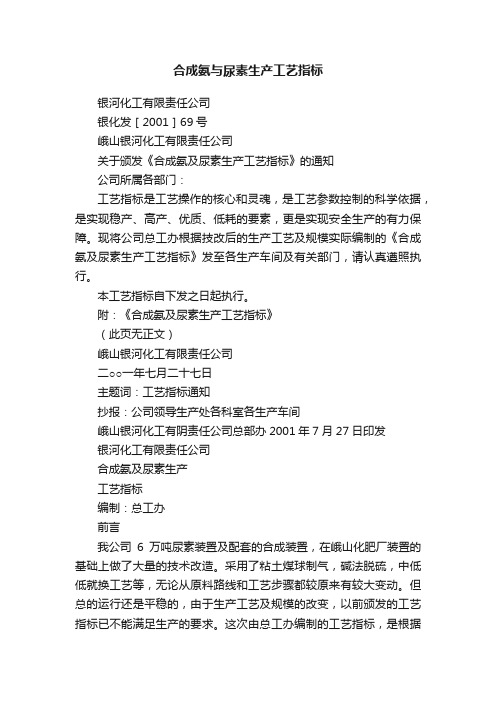
合成氨与尿素生产工艺指标银河化工有限责任公司银化发[2001]69号峨山银河化工有限责任公司关于颁发《合成氨及尿素生产工艺指标》的通知公司所属各部门:工艺指标是工艺操作的核心和灵魂,是工艺参数控制的科学依据,是实现稳产、高产、优质、低耗的要素,更是实现安全生产的有力保障。
现将公司总工办根据技改后的生产工艺及规模实际编制的《合成氨及尿素生产工艺指标》发至各生产车间及有关部门,请认真遵照执行。
本工艺指标自下发之日起执行。
附:《合成氨及尿素生产工艺指标》(此页无正文)峨山银河化工有限责任公司二○○一年七月二十七日主题词:工艺指标通知抄报:公司领导生产处各科室各生产车间峨山银河化工有阴责任公司总部办2001年7月27日印发银河化工有限责任公司合成氨及尿素生产工艺指标编制:总工办前言我公司6万吨尿素装置及配套的合成装置,在峨山化肥厂装置的基础上做了大量的技术改造。
采用了粘土煤球制气,碱法脱硫,中低低就换工艺等,无论从原料路线和工艺步骤都较原来有较大变动。
但总的运行还是平稳的,由于生产工艺及规模的改变,以前颁发的工艺指标已不能满足生产的要求。
这次由总工办编制的工艺指标,是根据我公司实际情况,参照原化工部颁发的工艺指标及兄弟厂的经验编制的。
现发到各生产车间及与生产有关的管理部门,要求认真贯彻执行,在运行中个性,以至完善。
工艺指标是工艺操作的核心和灵魂,是工艺参数控制的科学依据,是实现稳产高产优质低耗的要素,是实现安全生产的有力保障。
希望生产一线的操作工人和生产管理者严格执行工艺指标,与生产有关的管理人员要熟悉和掌握工艺指标,要做到生产操作与调度指挥以工艺指标为规的协调和统一,要充分认识工艺指标的严肃性、科学性和灵活性。
要制定切实可行的考核办法,进行工艺指标的分类和分级管理考核,把哪此与安全生产、高产、优质、低耗、延长设备运行周期的重要指标列为厂控制指标。
工艺指标合格率由生产管理部门作为重要指标来考核,以期达到安全、高产、优质、低耗的目的。
合成氨生产各岗位工艺操作指标
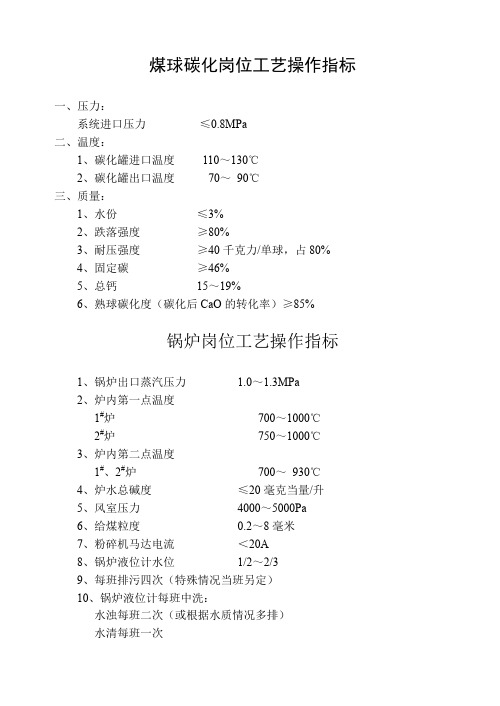
煤球碳化岗位工艺操作指标一、压力:系统进口压力≤0.8MPa二、温度:1、碳化罐进口温度110~130℃2、碳化罐出口温度70~90℃三、质量:1、水份≤3%2、跌落强度≥80%3、耐压强度≥40千克力/单球,占80%4、固定碳≥46%5、总钙15~19%6、熟球碳化度(碳化后CaO的转化率)≥85%锅炉岗位工艺操作指标1、锅炉出口蒸汽压力 1.0~1.3MPa2、炉内第一点温度1#炉700~1000℃2#炉750~1000℃3、炉内第二点温度1#、2#炉700~930℃4、炉水总碱度≤20毫克当量/升5、风室压力4000~5000Pa6、给煤粒度0.2~8毫米7、粉碎机马达电流<20A8、锅炉液位计水位1/2~2/39、每班排污四次(特殊情况当班另定)10、锅炉液位计每班中洗:水浊每班二次(或根据水质情况多排)水清每班一次11、排烟温度150~200℃12、鼓风机电流70~85A13、引风机电流50~80A14、喂煤机电流0.2~3.0A15、每小时巡回检查一次16、除尘器每班排灰:1#炉每两小时一次2#炉每小时一次造气微机岗位工艺操作指标一、压力:1、减压前蒸汽压力>0.9MPa2、减压后蒸汽压力0.08~0.12MPa3、入炉蒸汽压力0.05~0.07MPa4、鼓风机风压1800~2400mm水柱5、微机油压 4.0~6.0MPa6、汽泡压力<0.2MPa二、循环时间(150秒):1、二次上吹5~10秒2、吹净6~7秒3、吹风24~32秒4、上吹30~43秒5、下吹50~60秒三、温度:1、炉上温度350~400℃2、炉下温度180~250℃3、水夹套温度<135℃4、洗气塔≤50℃四、风机风量:吹风时风机电流≤340A五、蒸汽入炉流量:上吹 1.8~2.5吨/时下吹 1.6~2.5吨/时六、炉内炭层高度(空程)Φ2260 2.2~2.5mΦ2400 2.3~2.6m七、出渣次数块煤3次/班炉煤球5次/班炉八、气体成份:半水煤气中CO2≤13%O2≤0.5%CO ≥25%(H2+CO)>68%循环气中H250~60%H2/N2 2.0~2.8九、液位:汽泡液位1/3~1/2脱硫再生岗位工艺操作指标1、脱硫后半水煤气H2S含量<0.2g/m32、再生氨水中脱硫剂催化剂含量0.1~0.3g/L3、再生氨水浓度10~20tt4、再生效率≥65%5、再生泵出口压力≥0.36MPa6、电动机电流及温升按铭牌规定7、液位控制:脱硫塔1/3~1/28、再生氨水槽(按现标尺刻度)23~24注:再生氨水槽液位一定按规定值来控制液位过低将会引起硫泡沫排重新沉淀,过高则排出带走过多的脱硫氨水。
合成氨生产工艺合成岗位2
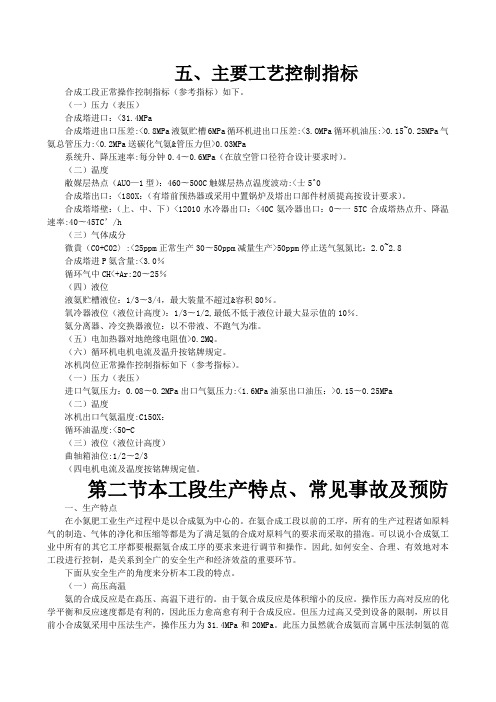
五、主要工艺控制指标合成工段正常操作控制指标(参考指标)如下。
(一)压力(表压)合成塔进口:<31.4MPa合成塔进出口压差:<0.8MPa液氨贮槽6MPa循环机进出口压差:<3.OMPa循环机油压:>0.15~0.25MPa气氨总管压力:<0.2MPa送碳化气氨&管压力但>0.03MPa系统升、降压速率:每分钟0.4〜0.6MPa(在放空管口径符合设计要求时)。
(二)温度敝媒层热点(AUO—1型):460〜500C触媒层热点温度波动:<士5^0合成塔出口:<180X:(有塔前预热器或采用中置锅炉及塔出口部件材质提高按设计要求)。
合成塔塔壁:(上、中、下)<12010水冷器出口:<40C氨冷器出口:0〜一5TC合成塔热点升、降温速率:40〜45TC’/h(三)气体成分微貴(C0+C02〉:<25ppm正常生产30〜50ppm减量生产>50ppm停止送气氢氮比:2.0~2.8合成塔进P氨含量:<3.0%循环气中CH<+Ar:20〜25%(四)液位液氨贮槽液位:1/3〜3/4,最大装量不超过&容积80%。
氧冷器液位(液位计高度):1/3〜1/2,最低不低于液位计最大显示值的10%.氨分离器、冷交换器液位:以不带液、不跑气为准。
(五)电加热器对地绝缘电阻值>0.2MQ。
(六)循环机电机电流及温升按铭牌规定。
冰机岗位正常操作控制指标如下(参考指标)。
(一)压力(表压)进口气氨压力:0.08〜0.2MPa出口气氨压力:<1.6MPa油泵出口油压:>0.15〜0.25MPa(二)温度冰机出口气氨温度:C150X:循环油温度:<50-C(三)液位(液位计高度)曲轴箱油位:1/2〜2/3(四电机电流及温度按铭牌规定值。
第二节本工段生产特点、常见事故及预防一、生产特点在小氮肥工业生产过程中是以合成氨为中心的。
(工艺技术)合成氨工艺简介

合成氨工艺控制方案总结一合成氨工艺简介中小型氮肥厂是以煤为主要原料,采用固定层间歇气化法制造合成氨原料气。
从原料气的制备、净化到氨的合成,经过造气、脱硫、变换、碳化、压缩、精炼、合成等工段。
工艺流程简图如下所示:该装置主要的控制回路有:(1)洗涤塔液位;(2)洗涤气流量;(3)合成塔触媒温度;(4)中置锅炉液位;(5)中置锅炉压力;(6)冷凝塔液位;(7)分离器液位;(8)蒸发器液位。
其中触媒温度控制可采用全系数法自适应控制,其他回路采用PID控制。
二主要控制方案(一)造气工段控制工艺简介:固定床间歇气化法生产水煤气过程是以无烟煤为原料,周期循环操作,在每一循环时间里具体分为五个阶段;(1)吹风阶段约37s;(2)上吹阶段约39s;(3)下吹阶段约56s;(4)二上吹阶段约12s;(5)吹净阶段约6s.l、吹风阶段此阶段是为了提高炉温为制气作准备的。
这一阶段时间的长短决定炉温的高低,时间过长,炉温过高;时间过短,炉温偏低并且都影响发气量,炉温主要由这一阶段控制。
般工艺要求此阶段的操作时间约为整个循环周期的18%左右。
2、上吹加氮制气阶段在此阶段是将水蒸汽和空气同时加入。
空气的加入增加了气体中的氮气含量,是调节H2/N2的主要手段。
但是为了保证造气炉的安全该段时间最多不超过整个循环周期的26%。
3、上吹制气阶段该阶段与上吹加氯制气总时间为整个循环的32%,随着上吹制气的进行下部炉温逐渐下降,为了保证炉况和提高发气量,在此阶段蒸汽的流量最好能得以控制。
4、下吹制气阶段为了充分地利用炉顶部高温、提高发气量,下吹制气也是很重要的一个阶段。
这段时间约占整个循环的40%左右。
5、二次上吹阶段为了确保生产安全,造气炉再度进行吹风升温之前,须把下吹制气时留在炉底及下部管道中的半水煤气吹净以防不测,故进行第二次上映。
这段时间约占7%左右。
6、吹净阶段这段时间主要是回收上行煤气管线及设备内的半水煤气。
约占整个循环的3%。
合成氨工艺指标

4.工艺控制指标(1)脱硫工序铁锰脱硫出口: S≤5ppm 氧化锌出口硫含量:≤0.1ppm加氢量: 2~5% 进口温度TIC-111: 380±5℃氧化锌出口温度:≤360℃进脱硫系统压力:≤4.1 MPa(2)转化工序水碳比: 3.2~3.5 一段炉出口甲烷:≤12.84%一段炉进口压力:≤3.82 MPa 燃料气压力PI-811:≤0.35 MPa对流段出口烟压:-2000 Pa 排烟温度:≤170℃炉膛负压:-100 Pa 混合气盘管出口温度:≤610℃工艺空气盘管温度:≤615℃过热蒸汽盘管NO.3:≤360℃原料天然气盘管NO.4:≤400℃原料天然气盘管NO.7:≤295℃燃料天然气预热盘管:≤200℃一段炉出口温度:≤801℃一段炉阻力:≤0.35 MPa 二段炉阻力:≤92 KPa二段炉出口温度:≤997℃二段炉水夹套温度:≤100℃二段炉出口甲烷:≤0.5% 中压汽包蒸汽压力:≤4.2 MPa脱氧槽液位:80%以上脱氧槽压力:≤20KPa中压汽包液位:1/3~2/3 锅炉给水PH值: 8.8~9.3 锅炉给水O2含量:≤0.007ppm 二段炉出口甲烷≤ 0.5%(3)变换工序高变进口温度: TIC-157 370±5℃高变出口温度:≤436℃高变出口CO:≤3 % 高变汽包液位: 1/3~2/3 高变汽包蒸汽压力:≤2.5 MPa 低变进口温度TIC-220 :200±5℃低变出口温度:≤228℃低变出口CO:≤0.3 %(4)脱碳工序(碳酸钾溶液)吸收嗒入气温度: 81℃±5℃吸收塔出气温度: 70℃±5℃吸收塔进贫液温度:70℃±5℃吸收塔进半贫液温度: 112℃±5℃再生气温度:<40℃再生塔出口贫液温度: 120℃±5℃吸收塔压差:<45KPa 再生塔压差:<20KPa再生塔出再生气压力:<75KPa 低变废锅蒸汽压力: 0.40~0.50MPa 吸收塔出二氧化碳含量:≤0.1% 再生气纯度:≥98.5 %汽提塔出口水中电导率:≤10μs/cm吸收塔液位: 1/2~2/3 闪蒸槽液位: 1/2~2/3低水分液位: 1/3~2/3 低变废锅液位: 1/3~2/3净水分液位: 1/3~2/3 铁离子含量:<100ppm汽提塔液位: 1/2~2/3 再生塔上部液位:≥30 %再生塔中部液位: 1/3~2/3 再生塔下部液位: 1/2~2/3贫液流量:≤ 96 t / h 半贫液流量:≤ 778 t / h总碱度: 25~30% 贫液再生度: 1.15~1.25半贫液再生度: 1.35~1.45 DEA : 2~3%V5+/V4+:≥0.5 总矾: 0.7~1.0%(以KVO3)(5)甲烷化工序甲烷化进口温度: 310℃±5℃甲烷化床层温度:≤350℃甲水分出口温度:<40℃甲烷化出口CO+CO2:≤10ppm甲水分液位:≤10 %。
合成氨工艺指标

4.工艺控制指标(1)脱硫工序铁锰脱硫出口: S≤5ppm 氧化锌出口硫含量:≤0.1ppm加氢量: 2~5% 进口温度TIC-111: 380±5℃氧化锌出口温度:≤360℃进脱硫系统压力:≤4.1 MPa(2)转化工序水碳比: 3.2~3.5 一段炉出口甲烷:≤12.84%一段炉进口压力:≤3.82 MPa 燃料气压力PI-811:≤0.35 MPa对流段出口烟压:-2000 Pa 排烟温度:≤170℃炉膛负压:-100 Pa 混合气盘管出口温度:≤610℃工艺空气盘管温度:≤615℃过热蒸汽盘管NO.3:≤360℃原料天然气盘管NO.4:≤400℃原料天然气盘管NO.7:≤295℃燃料天然气预热盘管:≤200℃一段炉出口温度:≤801℃一段炉阻力:≤0.35 MPa 二段炉阻力:≤92 KPa二段炉出口温度:≤997℃二段炉水夹套温度:≤100℃二段炉出口甲烷:≤0.5% 中压汽包蒸汽压力:≤4.2 MPa脱氧槽液位:80%以上脱氧槽压力:≤20KPa中压汽包液位:1/3~2/3 锅炉给水PH值: 8.8~9.3 含量:≤0.007ppm 二段炉出口甲烷≤ 0.5%锅炉给水O2(3)变换工序高变进口温度: TIC-157 370±5℃高变出口温度:≤436℃高变出口CO:≤3 % 高变汽包液位: 1/3~2/3 高变汽包蒸汽压力:≤2.5 MPa 低变进口温度TIC-220 :200±5℃低变出口温度:≤228℃低变出口CO:≤0.3 %(4)脱碳工序(碳酸钾溶液)吸收嗒入气温度: 81℃±5℃吸收塔出气温度: 70℃±5℃吸收塔进贫液温度:70℃±5℃吸收塔进半贫液温度: 112℃±5℃再生气温度:<40℃再生塔出口贫液温度: 120℃±5℃吸收塔压差:<45KPa 再生塔压差:<20KPa再生塔出再生气压力:<75KPa 低变废锅蒸汽压力: 0.40~0.50MPa 吸收塔出二氧化碳含量:≤0.1% 再生气纯度:≥98.5 %汽提塔出口水中电导率:≤10μs/cm吸收塔液位: 1/2~2/3 闪蒸槽液位: 1/2~2/3低水分液位: 1/3~2/3 低变废锅液位: 1/3~2/3净水分液位: 1/3~2/3 铁离子含量:<100ppm汽提塔液位: 1/2~2/3 再生塔上部液位:≥30 %再生塔中部液位: 1/3~2/3 再生塔下部液位: 1/2~2/3贫液流量:≤ 96 t / h 半贫液流量:≤ 778 t / h总碱度: 25~30% 贫液再生度: 1.15~1.25半贫液再生度: 1.35~1.45 DEA : 2~3%)V5+/V4+:≥0.5 总矾: 0.7~1.0%(以KVO3(5)甲烷化工序甲烷化进口温度: 310℃±5℃甲烷化床层温度:≤350℃甲水分出口温度:<40℃甲烷化出口CO+CO:≤10ppm2甲水分液位:≤10 %。
焦炉气制合成氨尿素(18-30规模)全厂工艺指标
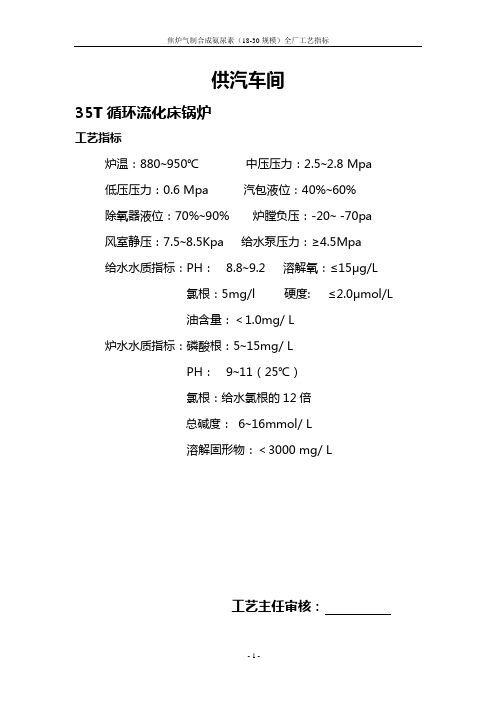
供汽车间35T循环流化床锅炉工艺指标炉温:880~950℃中压压力:2.5~2.8 Mpa低压压力:0.6 Mpa 汽包液位:40%~60%除氧器液位:70%~90% 炉膛负压:-20~ -70pa风室静压:7.5~8.5Kpa 给水泵压力:≥4.5Mpa给水水质指标:PH:8.8~9.2 溶解氧:≤15μg/L氯根:5mg/l 硬度: ≤2.0μmol/L油含量:<1.0mg/ L炉水水质指标:磷酸根:5~15mg/ LPH:9~11(25℃)氯根:给水氯根的12倍总碱度:6~16mmol/ L溶解固形物:<3000 mg/ L工艺主任审核:车间主任审核:供水车间合成循环水工艺指标:电机电流:≤28.5A液位:1/2~2/3.风机电流:≤168A供水总管压力:0.25~0.4Mpa尿素循环水工艺指标:1.风机电流: ≤246A2.电机电流: ≤31.1A3.水位:1/2~2/3.4.供水压力:0.25~0.4Mpa.脱盐水工艺指标:1.机械过滤器压力:0.3~0.5Mpa2.精密过滤器压力:0.25~0.3Mpa3.高压泵前压力:>0.1Mpa4.膜前压力:<1.3Mpa5.段间压力:<0.9Mpa6.浓水压力: <0.7 Mpa7.硬度= 0 mmol/L8.电导率:≤20μs/cm9.PH: 7~9一次水泵房工艺指标:一次水泵电机电流:<150A.消防泵电机电流:<260A.稳压泵电机电流:<22A.一次水总管压力:0.3~0.5Mpa.消防泵总管压力:0.8~1.2Mpa.工艺主任审核:车间主任审核:合成车间冰机岗位工艺指标1、压力进口:0.05~0.25MPa出口:≤1.6MPa油压:高于排气压力0.25~0.3MPa氨贮槽:1.6MPa循环水:≥0.25Mpa2、温度出口温度:≤105℃冷凝温度≤45℃油温温度:≤65℃电机温度:≤65℃循环水温度:≤25℃3、液位油液位:1/2~2/3氨槽高限:≤槽容积80%氨槽低限:≥槽容积13%4、电流KA31.5----1型机≤110A氨库岗位工艺指标1、去尿素液氨压力 2.3MPa2、液氨球罐压力<2.4MPa3、液氨球罐温度-5~30℃4、液氨球罐液位10~80%(夏天最高控制70%)等压岗位工艺指标等压吸收塔压力控制在2.3~2.5MPa柱塞泵压力大于塔内压力0.2~0.5MPa冷却水压力≥0.25MPa等压塔液位保持在1/2~1/3软水槽液位1/2~1/3等压塔出口氨水滴度保持在150~200tt合成压力(MPa)补充气≤31.4系统压差≤2.5合成塔压差≤0.8气氨总管压力≤0.3放氨压力2.5~2.9合成废锅压力<2.52、温度(℃)触媒层温度:初期465±5,后期490±5塔壁温度≤140塔二出口温度300~350水冷前气体温度80水冷后气体温度40NH3冷温度0~-103、成分精炼气(CO+CO2)≤20ppm入塔氨含量2.5~2.8% 出塔氨含量11~15%新鲜气中惰性气体含量≤2.0%循环气惰性气体含量15.0~21.0%循环气H2/N2 2.2~2.84、液位冷交氨分1/2~2/3废锅40-70%5、电炉电流≤2KA透平机:进气压力≤29.2MPa出气压力≤31.4MPa压差≤2.2MPa进气温度≤30℃打气量620m3/h电机转速2970r/min电机功率680KW电机电压380V电机运行电流≤1062A电机非负荷端轴承温度≤75℃电机负荷轴承温度≤75℃透平机进口轴承温度≤75℃透平机出口轴承温度≤75℃电机定子温度≤100℃电机绝缘电阻值≥0.5MΩ氨冷器保护器进口温度≤35℃氨冷器保护气出口温度5~15℃压缩岗位工艺指标(1)气体压力一段进口压力≈1.5Mpa 一段出口压力≈3.4Mpa 二段进口压力≈3.3 Mpa 二段出口压力≈7.2Mpa 三段进口压力≈7.2 Mpa 三段出口压力≈14.11 Mpa 四段进口压力≈12 Mpa 四段出口压力≈31.4 Mpa (2)气体温度一段进口温度<40℃一段出口温度<130℃二段进口温度<40℃二段出口温度<130℃三段进口温度<40℃三段出口温度<130℃四段进口温度<40℃四段出口温度<130℃(3)循环冷却水工作压力0.4 Mpa(4)润滑油型号:L-DAB150, 工作温度<50℃(5)曲轴箱油位:1/2-2/3 注油器油位:1/2~2/3 (6)循环油压<0.2 Mpa时,压缩机联锁停车。
合成氨国标

合成氨国标
一、概述
合成氨是一种重要的化工原料,广泛应用于农业、工业和日常生活中。
为了规范合成氨的生产和使用,国家制定了一系列的标准,即合成氨国标。
合成氨国标是保障产品质量、安全和环保的重要依据,对于促进合成氨行业的健康发展具有重要意义。
二、合成氨国标的主要内容
1.原料和生产工艺要求
合成氨国标对原料和生产工艺提出了明确的要求。
对于原料,标准规定了所需原料的种类、质量和纯度。
对于生产工艺,标准要求采用高效、低耗、环保的工艺路线,确保生产过程的安全、稳定和连续。
2.产品质量和规格
合成氨国标对产品的质量和规格进行了详细的规定。
标准规定了合成氨的纯度、水分、硫化物、砷化物等各项指标,以确保产品质量符合要求。
同时,标准还规定了产品的包装、标识和贮存等方面的要求,以确保产品的安全和环保。
3.安全和环保要求
合成氨国标高度重视安全和环保问题。
标准规定了生产过程中的安全操作规程、危险源控制和应急处置等方面的要求,以确保生产过程的安全可控。
同时,标准还规定了废气、废水、固废等处理和排放的要求,以确保企业的环保合规。
4.检测和检验方法
为了确保合成氨的质量和安全,合成氨国标还规定了相应的检测和检验方法。
标准规定了各项指标的检测原理、仪器设备和操作方法,以确保检测结果的准确性和可靠性。
同时,标准还规定了产品的检验规则,包括抽样方法、检验项目和判定依据等。
三、总结
合成氨国标是保障合成氨产品质量、安全和环保的重要依据。
通过严格执行合成氨国标,可以促进合成氨行业的健康发展,提高企业的竞争力,为我国经济的可持续发展做出贡献。
合成氨产品质量指标

合成氨产品质量指标一、合成氨产品概述合成氨(Anhydrous Ammonia,简称NH3)是一种无色、有毒、有刺激性气味的气体。
它是工业上最重要的氨源,广泛应用于肥料、化工、石油精炼等领域。
在农业领域,合成氨作为氮肥的重要原料,对提高农作物产量具有重要作用。
二、合成氨产品质量指标的重要性合成氨产品质量指标是衡量产品性能和应用效果的关键参数。
合理的质量指标能确保合成氨在各个领域的安全、有效应用,反之则可能引发设备腐蚀、环境污染等问题。
因此,了解和掌握合成氨产品质量指标至关重要。
三、合成氨产品质量指标的具体内容1.氨含量:合成氨产品中氨含量是衡量产品质量的核心指标。
一般情况下,合成氨的氨含量要求在99.5%以上。
高氨含量有利于提高肥料利用率,降低环境污染风险。
2.杂质含量:合成氨中的杂质含量对其应用领域有重要影响。
常见的杂质有水分、氢气、氧气、二氧化碳等。
过高杂质含量可能导致设备腐蚀、催化剂失活等问题。
因此,合成氨中的杂质含量应控制在规定范围内。
3.水分含量:合成氨中水分含量对其稳定性和安全性具有重要影响。
一般情况下,水分含量应控制在0.2%以下。
过高水分含量可能导致合成氨液化、泄漏等安全隐患。
4.颜色和气味:合成氨的颜色和气味也是质量指标之一。
正常情况下,合成氨应为无色,无刺激性气味。
若颜色和气味异常,可能表明产品存在质量问题。
四、质量指标对合成氨应用的影响质量指标直接影响着合成氨在各个领域的应用效果。
高氨含量、低杂质含量的合成氨产品具有更好的安全性和稳定性,能确保设备运行顺畅,降低环境污染风险。
而优质的颜色和气味能让用户更容易接受。
五、提高合成氨产品质量的策略1.严格控制生产工艺,确保产品氨含量达到要求。
2.加强原料和设备的检查与维护,降低杂质含量。
3.优化干燥工艺,控制水分含量在合适范围内。
4.加强产品质量检测,确保产品符合标准。
六、结论合成氨产品质量指标是衡量产品性能和应用效果的关键因素。
合成氨及尿素生产工艺指标
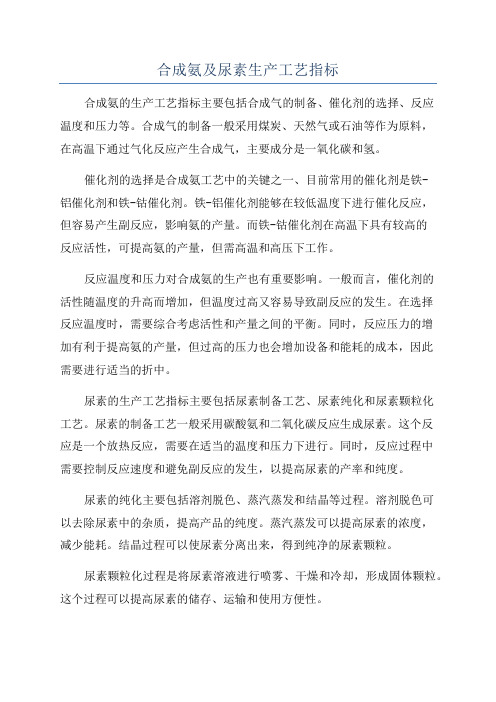
合成氨及尿素生产工艺指标合成氨的生产工艺指标主要包括合成气的制备、催化剂的选择、反应温度和压力等。
合成气的制备一般采用煤炭、天然气或石油等作为原料,在高温下通过气化反应产生合成气,主要成分是一氧化碳和氢。
催化剂的选择是合成氨工艺中的关键之一、目前常用的催化剂是铁-铝催化剂和铁-钴催化剂。
铁-铝催化剂能够在较低温度下进行催化反应,但容易产生副反应,影响氨的产量。
而铁-钴催化剂在高温下具有较高的反应活性,可提高氨的产量,但需高温和高压下工作。
反应温度和压力对合成氨的生产也有重要影响。
一般而言,催化剂的活性随温度的升高而增加,但温度过高又容易导致副反应的发生。
在选择反应温度时,需要综合考虑活性和产量之间的平衡。
同时,反应压力的增加有利于提高氨的产量,但过高的压力也会增加设备和能耗的成本,因此需要进行适当的折中。
尿素的生产工艺指标主要包括尿素制备工艺、尿素纯化和尿素颗粒化工艺。
尿素的制备工艺一般采用碳酸氨和二氧化碳反应生成尿素。
这个反应是一个放热反应,需要在适当的温度和压力下进行。
同时,反应过程中需要控制反应速度和避免副反应的发生,以提高尿素的产率和纯度。
尿素的纯化主要包括溶剂脱色、蒸汽蒸发和结晶等过程。
溶剂脱色可以去除尿素中的杂质,提高产品的纯度。
蒸汽蒸发可以提高尿素的浓度,减少能耗。
结晶过程可以使尿素分离出来,得到纯净的尿素颗粒。
尿素颗粒化过程是将尿素溶液进行喷雾、干燥和冷却,形成固体颗粒。
这个过程可以提高尿素的储存、运输和使用方便性。
总结起来,合成氨及尿素的生产工艺指标包括合成气制备、催化剂选择、反应温度和压力等对合成氨的生产影响,以及尿素制备、纯化和颗粒化工艺对尿素的生产影响。
这些指标的选择需要综合考虑经济性、能耗和产品质量等因素,以实现高效、可持续的生产。
合成氨工艺流程与工艺指标

合成氨工艺流程与工艺指标第一节工艺流程1 工艺流程简述:1.11#合成工艺流程由压缩机七段(六段)出口总管送来的铜洗精炼气经导入阀送入氨冷器出口管,与循环气混合后,进入冷凝塔底部分离套筒内,分离气体中的液氨与油水后进入上部换热器管间,与管内来自水冷排的热气体换热后去循环机加压,气体自循环机出来后进入油分,分离掉油水后气体分四路进入合成塔(一路主线、一路冷副、二路冷激),主线气体由合成塔顶部一次入口进入合成塔内外筒间的环隙,换热后从一次出口出塔,进入气气换热器管间,和管内气体换热后从合成塔二次入口进入塔内下部换热器,与催化剂层来的反应气体换热提温后经中心管进入催化剂层反应,反应后的气体自塔二次出口进入废热锅炉管内。
与废锅内的软水换热,使软水汽化,副产的饱和蒸汽,供变换使用,从废锅出来的混合气体进入软水加热器进行换热,换热后的热软水供铜洗再生使用,出水加热器的气体再进入气气换热器管内,和合成塔一出气体换热。
换热后自换热器底部出,进入水冷却器冷却降温,出冷却器的气体再进入冷凝塔上部换热器管内进一步冷却后进入氨分,分离掉部分液氨,其后气体再进入氨冷器进一步冷却降温,出氨冷器后的循环气和补入的新鲜气混合后一同进入冷凝塔分离液氨,并洗除油水后送循环机加压进行下一个循环,不断产生液氨。
本流程中塔后放空设在氨分离器后,放空气体送提氢岗位回收氢。
氨分和冷交换器分离出来的液氨,放入液氨贮槽。
液氨贮槽的液氨分别再输送到尿素车间生产氨及有关岗位,或送氨冷器做冷冻剂使用,各个氨冷器蒸发后的气氨送至冷冻岗位重新液化成液氨后循环使用。
1.22#合成工艺流程由压缩六段.七段送来合格的精练气经导入阀与氨冷器出口的循环气混合后进入超虑的上部,液氨被分离下来,分离后气体从顶部出来进入冷凝塔底部氨分离套筒内,分离气体中的液氨,油水后进入上部换热气器的管间,与管内冷排来的热气体换热后从上部出来进入循环机,气体经循环机加压后进入油分离器,分离掉油水后的气体分两路进入合成塔(一路线.一路冷副)主线从上部进入沿内外筒环隙顺流而下进入螺旋板换热器板间,从下部螺旋板换热器板间出来进入上部列管换热器的管间,换热后的气体与冷副管来的气体混合进入分器盒,气体被分配到三套管的内管,从外冷管进入集器盒,提温后的气体经中心进入触媒反应,反应后的气体经上部列管内出来进入废锅的管内,气体从废锅出来从二进进入下部螺旋板换热器的板内,经降温后的气体从二出出来进入水冷排下部,气体在冷排被水降温后由上部出来进入冷交上部,气体经换热后从塔顶部出来进入氨分的上部,气体中的氨进一部分离后从顶部出来进入氨冷器的上部,气体在氨冷器降温,气体从底部出来与导入来的气体混合进行下一步的循环.放空气去提氢岗位.2 工艺流程图合成塔油分废 锅去蒸汽管冷 排循环水氨冷氨分冷交气氨去冰机去提氢去提氢导入放空液氨去尿素减压去等压回收塔冰机来去铜洗去冰机放氨液氨贮槽缓冲罐超滤冷副主阀主线近路第二节工艺指标催化剂热点温度:445-500℃(根据催化剂活性情况调整,A±5℃) 成品氨的纯度:≥99.6%循环气中入口甲烷:10-14%循环气中入口氨含量:≤3.5%1#合成塔压差:≤1.0MPa2#合成塔压差:≤2.0MPa废锅炉水碱度:≤10mgN/L废锅炉水氯根:≤30 mgN/L循环机出口压力:≤32.0MPa系统压力:≤31.0MPa系统压差:≤2.5MPa循环机油压:0.3-0.6 MPa循环机填料加氨:0.3-0.4MPa 1#合成废锅压力:≤1.4MPa2#合成废锅压力:≤1.3MPa 中间槽压力:≤2.1 MPa系统升压速率≤0.5MP/分氨冷器气氨压力:≤0.3MPa合成塔塔壁上部温度:≤100℃合成塔塔壁中下部温度:≤150℃水冷温度:≤50℃氨冷温度:-5-5℃废热锅炉液位:1/2~2/3中间槽液位:10-30吨冷交液位:0-50循环机曲轴箱液位:1/2-2/3电炉绝缘电阻值:≥0.2兆欧催化剂同平面温差:≤30℃运行中电机绝缘: >0.5兆欧注油量:20-30滴/分保护气温度:5-20℃保护气流量:500-800m3/h轴承温度:<75℃定子温度:<120℃透平机电流:<1150A透平机功率:<680KWh循环气入口温度:<40℃循环氢:>60%轴承运行时间:2880小时功率记录仪指示无突跳.轴承定子运行温度记录平稳透平机进出口压差:≤3.0Mpa。
合成氨工艺控制方案精选全文完整版

典型工艺
(1)节能AMV法;
(2)德士古水煤浆加压气化法;
(3)凯洛格法;
(4)甲醇与合成氨联合生产的联醇法;
(5)纯碱与合成氨联合生产的联碱法;
(6)采用变换催化剂、氧化锌脱硫剂和甲烷催化剂的“三催化”气体净化法等。
(2)高温、高压气体物料从设备管线泄漏时会迅速膨胀与空气混合形成爆炸性混合物,遇到明火或因高流速物料与裂(喷)口处摩擦产生静电火花引起着火和空间爆炸;
(3)气体压缩机等转动设备在高温下运行会使润滑油挥发裂解,在附近管道内造成积炭,可导致积炭燃烧或爆炸;
(4)高温、高压可加速设备金属材料发生蠕变、改变金相组织,还会加剧氢气、氮气对钢材的氢蚀及渗氮,加剧设备的疲劳腐蚀,使其机械强度减弱,引发物理爆炸;
重点监控工艺参数
合成塔、压缩机、氨储存系统的运行基本控制参数,包括温度、压力、液位、物料流量及比例等。
安全控制的基本要求
合成氨装置温度、压力报警和联锁;物料比例控制和联锁;压缩机的温度、入口分离器液位、压力报警联锁;紧急冷却系统;紧急切断系统;安全泄放系统;可燃、有毒气体检测报警装置。
宜采用的控制方式
可编辑修改精选全文完整版
5、合成氨工艺
反应类型
吸
热反应
重点监控单元
合成塔、压缩机、氨储存系统
工艺简介
氮和氢两种组分按一定比例(1:3)组成的气体(合成气),在高温、高压下(一般为400—450℃,15—30MPa)经催化反应生成氨的工艺过程。
工艺危险特点
(1)高温、高压使可燃气体爆炸极限扩宽,气体物料一旦过氧(亦称透氧),极易在设备和管道内发生爆炸;
将合成氨装置内温度、压力与物料流量、冷却系统形成联锁关系;将压缩机温度、压力、入口分离器液位与供电系统形成联锁关系;紧急停车系统。
合成氨工艺卡片模板

合成氨车间
合成塔压差
MPa
≤0.34
车间级
合成氨车间
气氨总管压力( 1#氨冷)
MPa
0.35~0.52
车间级
合成氨车间
气氨总管压力( 2#氨冷)
MPa
0.16~0.26
车间级
合成氨车间
闪蒸槽压力
MPa
3.0~3.5
车间级
合成氨车间
合成触媒热点温度
℃
465±5
公司级
合成氨厂
塔壁温度
℃
≤120
车间级
车间级
合成氨车间
排气压力
MPa
≤1.6MPa
车间级
合成氨车间
油压高于排气压力
MPa
0.15-0.3MPa
车间级
合成氨车间
冰机氨槽液位
%
13~80
车间级
合成氨车间
氨槽压力
MPa
≤1.6MPa
车间级
合成氨车间
冰机排气温度
℃
≤100℃
车间级
合成氨车间
冰机油温
℃
45℃~65℃
车间级
合成氨车间
冰机电机温度
℃
≤65℃
车间级
合成氨车间
四、 工艺设备运行指标
1.氮气压缩机
项 目
单 位
指 标
分级
控 制 部 门
低压氮气纯度
%
≥99.99%
厂级
甲醇厂
低压氮气压力
kPa
5~20
厂级
甲醇厂和合成氨厂
循环润滑系统供油压力
MPa
0.4±0.2
车间级
合成氨车间
循环油润滑系统供油温度
合成氨产品质量指标

合成氨产品质量指标
一、纯度
合成氨产品的纯度应符合国家标准,其中氢气含量应小于0.1%,氮气含量应小于0.2%,二氧化碳含量应小于0.1%,氧气含量应小于0.05%。
二、含水量
合成氨产品中含水量应小于0.3%,以防止在储存和运输过程中结冰。
三、氨的损失
氨的损失是衡量合成氨产品质量的一个重要指标。
氨的损失量应小于0.3%。
四、游离氨
游离氨是指合成氨产品中未与氮原子形成化合物的氨。
游离氨含量应小于
0.1%。
五、催化剂含量
合成氨产品中催化剂含量应符合生产工艺要求,以保证产品的质量和产量。
一般要求催化剂含量在规定范围内,并保证催化剂的活性。
六、无机杂质
无机杂质是指合成氨产品中除氨和氮以外的其他物质,如硫化物、氰化物、氧化物等。
无机杂质含量应符合国家标准,以保证产品的质量和用途。
七、有机物含量
有机物是指合成氨产品中含碳元素的物质,如甲烷、乙烷等。
有机物含量应符合国家标准,以保证产品的质量和用途。
八、颗粒大小
颗粒大小是指合成氨产品中固体颗粒的大小和形状。
颗粒大小应符合生产工艺要求,以保证产品的质量和产量。
一般要求颗粒大小在规定范围内,以保证产品的稳定性和流动性。
氨合成的工艺流程和指标
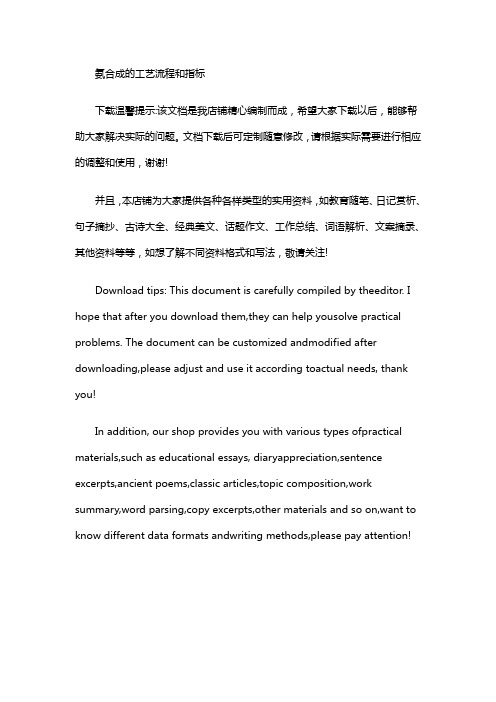
氨合成的工艺流程和指标下载温馨提示:该文档是我店铺精心编制而成,希望大家下载以后,能够帮助大家解决实际的问题。
文档下载后可定制随意修改,请根据实际需要进行相应的调整和使用,谢谢!并且,本店铺为大家提供各种各样类型的实用资料,如教育随笔、日记赏析、句子摘抄、古诗大全、经典美文、话题作文、工作总结、词语解析、文案摘录、其他资料等等,如想了解不同资料格式和写法,敬请关注!Download tips: This document is carefully compiled by theeditor. I hope that after you download them,they can help yousolve practical problems. The document can be customized andmodified after downloading,please adjust and use it according toactual needs, thank you!In addition, our shop provides you with various types ofpractical materials,such as educational essays, diaryappreciation,sentence excerpts,ancient poems,classic articles,topic composition,work summary,word parsing,copy excerpts,other materials and so on,want to know different data formats andwriting methods,please pay attention!氨合成是通过哈柏-博施过程(Haber-Bosch process)来实现的,这是一种工业生产氨气的方法,主要步骤包括氮气和氢气的反应,在高温、高压和催化剂的作用下生成氨气。
合成氨产品质量指标
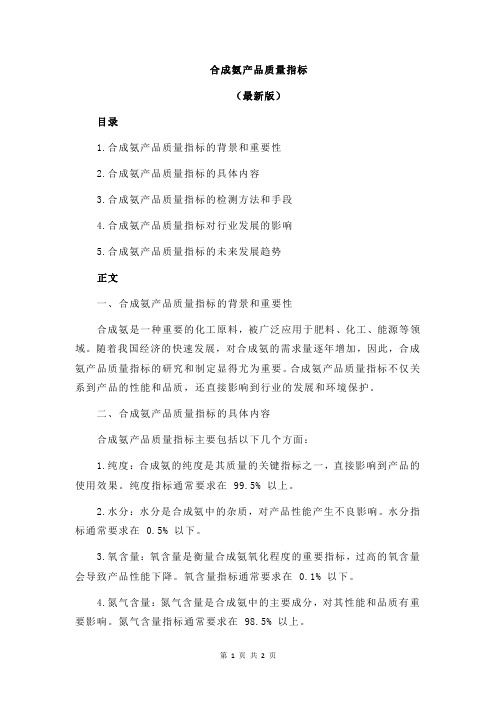
合成氨产品质量指标(最新版)目录1.合成氨产品质量指标的背景和重要性2.合成氨产品质量指标的具体内容3.合成氨产品质量指标的检测方法和手段4.合成氨产品质量指标对行业发展的影响5.合成氨产品质量指标的未来发展趋势正文一、合成氨产品质量指标的背景和重要性合成氨是一种重要的化工原料,被广泛应用于肥料、化工、能源等领域。
随着我国经济的快速发展,对合成氨的需求量逐年增加,因此,合成氨产品质量指标的研究和制定显得尤为重要。
合成氨产品质量指标不仅关系到产品的性能和品质,还直接影响到行业的发展和环境保护。
二、合成氨产品质量指标的具体内容合成氨产品质量指标主要包括以下几个方面:1.纯度:合成氨的纯度是其质量的关键指标之一,直接影响到产品的使用效果。
纯度指标通常要求在 99.5% 以上。
2.水分:水分是合成氨中的杂质,对产品性能产生不良影响。
水分指标通常要求在 0.5% 以下。
3.氧含量:氧含量是衡量合成氨氧化程度的重要指标,过高的氧含量会导致产品性能下降。
氧含量指标通常要求在 0.1% 以下。
4.氮气含量:氮气含量是合成氨中的主要成分,对其性能和品质有重要影响。
氮气含量指标通常要求在 98.5% 以上。
5.酸度:酸度是衡量合成氨酸性程度的指标,过高的酸度会影响产品的稳定性和使用效果。
酸度指标通常要求在 0.1% 以下。
三、合成氨产品质量指标的检测方法和手段合成氨产品质量指标的检测方法和手段主要包括以下几个方面:1.气相色谱法:气相色谱法是一种常用的合成氨分析方法,可以准确测定产品的纯度、水分、氧含量等指标。
2.红外光谱法:红外光谱法可以快速、准确地测定合成氨中的氮气含量。
3.滴定法:滴定法可以用于测定合成氨的酸度。
4.质量法:质量法是一种常用的合成氨产品质量检测方法,可以准确测定产品的纯度和水分等指标。
四、合成氨产品质量指标对行业发展的影响合成氨产品质量指标的制定和实施,对行业的发展具有重要影响。
首先,质量指标的制定可以引导企业提高产品质量,提升竞争力;其次,质量指标的实施可以加强对市场的监管,维护消费者权益;最后,质量指标的完善可以推动行业的技术进步和转型升级。
氨合成工艺指标.docm

氨合成工艺指标1、压力(Mpa表压)循环段出口压力: ≤16.4 操作压力: ≤14系统压差: ≤1 操作压力: ≤0.6塔压差: ≤0.6 操作压力: ≤0.35废锅Ⅰ(E2501)蒸汽压力: ≤3 操作压力: ≤2.5废锅Ⅱ(E2502)蒸汽压力: ≤1.3 操作压力:≤0.7低压氮气总管压力:≤0.7 操作压力:≤0.4开工加热炉(F2501)燃料气进口总管压力: ≤1操作压力:≤0.7 开工加热炉(F2501)进出口气体压差: ≤氨换热器(E2509)壳程液氨压力:≤2.2 操作压力: ≤1.7 中压氨分(V2502)壳程压力:≤4.0 操作压力: ≤3.2 2.温度(℃)合成塔(R2501)触媒层温度:≤560 操作温度≤506合成塔(R2501)出口气体温度:≤420 操作温度:≤385.2 合成塔(R2501)进口气体温度:≤300 操作温度:≤155 废锅Ⅰ(E2501)管程气体出口温度:≤270 操作温度≤236 废锅Ⅱ(E2502)管程气体出口温度:≤210 操作温度:≤180 热交(E2503)壳程气体进口温度:≤100 操作温度:≤61.7 热交(E2503)壳程气体出口温度:≤200 操作温度:≤155 合成塔(R2501)塔壁温度:≤300 操作温度:≤150氨冷(E2508)管程气体出口温度:≤80 操作温度:≤-10 高压氨分(V2501)出口气体温度:≤80 操作温度:≤-10 中压氨分(V2502)壳程温度:≤80 操作温度:≤-7.4 氨换热器(E2509)壳程液氨进口温度:≤80 操作温度≤40 废锅Ⅰ(E2501)补水温度:≤150 操作温度:≤104 废锅Ⅱ(E2502)补水温度:≤120 操作温度:≤104 蒸发水冷器(E2504)补水温度:≤60 操作温度:≤30深度水冷(E2506)上水温度:≤50 操作温度:≤7深度水冷(E2506)回水温度:≤50 操作温度:≤12 3.气体成分热交(E2503)壳程进口氢气含量: 73%热交(E2503)壳程进口氨气含量: 2.5%热交(E2503)壳程进口氮气含量:24%热交(E2503)管程进口氢气含量: 61%热交(E2503)管程进口氨气含量:18%热交(E2503)管程进口氮气含量:20%等压回收工艺指标等压吸收塔压力控制在 2.3~2.5MPa柱塞泵压力大于塔内压力 0.2~0.5 MPa等压塔液位保持在 1/2~2/3稀氨水槽液位,软水槽液位 1/2~2/3等压吸收塔出口氨水滴度保持在 150~220tt冷却水压力≥0.25 MPa氨库工艺指标1、压力 2.2~2.5Mpa2、液位氨槽底限≥130 m3(设计容积的13%)氨槽高限≤800m3 (设计容积的80%)冷冻部分工艺指标1、压力进口:0.065MPa 排气压力≤1.726MPa油压高于排气压力:小氨槽压力:≤1.6MPa循环水:≥0.2MPa2、温度进口温度:-38℃排气温度:≤103℃油温:45℃~65℃电机温度≤65℃循环水温≤25℃3、液位氨槽底限:≥13% VLNG工艺指标1.压力工作压力内罐≤15Kpa 外罐0.5 Kpa设计压力内罐20/-0.5 Kpa 外罐 1.0/-0.5 Kpa气密性试验压力内罐20 Kpa 外罐1.0 Kpa有效容积内罐1500 m3几何容积内罐1618 m3 外罐1025(夹层)m3贮存介质内罐LNG 外罐珠光砂+N2直径(mm)内罐Φ12400 mm 外罐Φ14800 mm 储罐总高(mm)内罐15285 外罐17700主体材质内罐06Cr19Ni10(S30408) 外罐Q345R 材料厚度(mm)内罐12/8/6 外罐6/8设计液位(mm)内罐12421设计风速(m/s)外罐30设计温度(o C)内罐-196~+50 外罐-19~+40蒸发率0.12% /d(LNG)环境温度20度内槽射线探伤比例内罐100%RTⅡ级外罐100%PT腐蚀裕量内罐0 外罐1焊缝系数按API620-APP.Q设备总重(t)约300设备满重(t)约1005 LNG密度按0.47T/m3计设计寿命≥20年。
- 1、下载文档前请自行甄别文档内容的完整性,平台不提供额外的编辑、内容补充、找答案等附加服务。
- 2、"仅部分预览"的文档,不可在线预览部分如存在完整性等问题,可反馈申请退款(可完整预览的文档不适用该条件!)。
- 3、如文档侵犯您的权益,请联系客服反馈,我们会尽快为您处理(人工客服工作时间:9:00-18:30)。
第一篇:合成氨工艺指标4.工艺控制指标(1)脱硫工序铁锰脱硫出口:S≤5ppm 氧化锌出口硫含量:≤0.1ppm 加氢量:2~5% 进口温度TIC-111:380±5℃氧化锌出口温度:≤360℃进脱硫系统压力:≤4.1 MPa (2)转化工序水碳比:3.2~3.5 一段炉进口压力:≤3.82 MPa 对流段出口烟压:-2000 Pa 炉膛负压:-100 Pa 工艺空气盘管温度:≤615℃原料天然气盘管NO.4:≤400℃燃料天然气预热盘管:≤200℃一段炉阻力:≤0.35 MPa 二段炉出口温度:≤997℃二段炉出口甲烷:≤0.5% 脱氧槽液位:80%以上中压汽包液位:1/3~2/3 锅炉给水O2含量:≤0.007ppm (3)变换工序高变进口温度:TIC-157 370±5℃高变出口CO:≤3 % 高变汽包蒸汽压力:≤2.5 MPa 低变出口温度:≤228℃(4)脱碳工序(碳酸钾溶液)吸收嗒入气温度:81℃±5℃吸收塔进贫液温度:70℃±5℃再生气温度:<40℃吸收塔压差:<45KPa 一段炉出口甲烷:≤12.84% 燃料气压力PI-811:≤0.35 MPa 排烟温度:≤170℃混合气盘管出口温度:≤610℃过热蒸汽盘管NO.3:≤360℃原料天然气盘管NO.7:≤295℃一段炉出口温度:≤801℃二段炉阻力:≤92 KPa 二段炉水夹套温度:≤100℃中压汽包蒸汽压力:≤4.2 MPa 脱氧槽压力:≤20KPa锅炉给水PH值:8.8~9.3 二段炉出口甲烷≤0.5% 高变出口温度:≤436℃高变汽包液位:1/3~2/3 低变进口温度TIC-220 :200±5℃低变出口CO:≤0.3 % 吸收塔出气温度:70℃±5℃吸收塔进半贫液温度:112℃±5℃再生塔出口贫液温度:120℃±5℃再生塔压差:<20KPa再生塔出再生气压力:<75KPa 低变废锅蒸汽压力:0.40~0.50MPa 吸收塔出二氧化碳含量:≤0.1% 再生气纯度:≥98.5 % 汽提塔出口水中电导率:≤10μs/cm 吸收塔液位:1/2~2/3 闪蒸槽液位:1/2~2/3 低水分液位:1/3~2/3 低变废锅液位:1/3~2/3 净水分液位:1/3~2/3 铁离子含量:<100ppm 汽提塔液位:1/2~2/3 再生塔中部液位:1/3~2/3 贫液流量:≤96 t / h 总碱度:25~30% 半贫液再生度:1.35~1.45 DEA V5+/V4+:≥0.5 甲烷化工序甲烷化进口温度:310℃±5℃甲水分出口温度:<40℃甲水分液位:≤10 %再生塔上部液位:≥30 % 再生塔下部液位:1/2~2/3 半贫液流量:≤778 t / h 贫液再生度:1.15~1.25 :2~3% 总矾:0.7~1.0%(以KVO3) 甲烷化床层温度:≤350℃甲烷化出口CO+CO2:≤10ppm (5)第二篇:合成氨工艺合成氨工艺陈昶君化九三20090118921.合成氨生产工艺流程图(1)煤为源头工艺路线:以无烟煤为原料生成合成氨常见过程是:造气->半水煤气脱硫->压缩机1,2工段->变换->变换气脱硫->压缩机3段->脱硫->压缩机4,5工段->铜洗->压缩机6段->氨合成->产品NH3造气过程为以煤为原料,用间歇式固定层常压气化法,反应方程为煤+氧气→二氧化碳二氧化碳+煤→一氧化碳煤+水蒸气→一氧化碳+氢气(2)天然气为源头采用天然气、焦化千气力原料的合成氨生产工艺流程包括:脱硫、转化、变换、脱碳、甲烷化、氨的合成、吸收制冷及输入氨库和氨吸收八个工序(一)脱琉原料气进入后,首先进入三段脱硫塔.第一、二段分别采用5—6%Na0H和10。
12%Na0H碱洗,第三段采用水洗。
在脱硫塔内。
气体中大部分无机硫和部分有机硫被碱液吸收,湿法脱硫后的焦化干气由压缩机道往一段转化炉对流段,加热至340—3500C后,进人干法脱硫槽。
干法脱硫剂通常采用氧化锰、氧化锌或钴—铜催化剂。
经干法脱硫后。
焦化干气中的总硫量要求低于3ppm.这里需要进行痕量硫的测定。
(二)转化经脱硫合格的焦化干气返回对流五段与来自废热锅炉的蒸汽混合,加热至500.610%后,进入一段转化炉(简称一段炉),控制共水碳比为3.5.4.0。
在催化刘作用下原料气转化为氢气、一氧化碳和二氧化碳。
反应所需的大量热能由转化炉两倜均匀分布的无焰燃烧喷嘴供给,反应温度控制在760—7的℃;出口气中残余甲烷含量要求小于10%。
一段沪出口气与空气压缩机送来的空气相混合,进人二段转化炉(简称二段炉)内燃烧,温度达到900一950。
C,在催化捌作用下,甲烷转化成一氧化碳和二氧化碳;二段炉出口气中残余甲烷应小于0.3%。
同时获取合成气所需的氮气,并控制氢、氮比在2.8—3.1之问。
在整个转化过程要进行原料气的总碳分析和一、二段炉出口气残余甲烷的分析。
(三)变换从二段炉出来的气体,进入消化废热锅炉。
利用热能获得蒸汽,同时使气体温度降至350—380℃,再进入中温变换炉(简称中变炉)。
在中变催化剂作用下,一氧化碳与水蒸气反应生成氢和二氧化碳。
一氧化碳含量要求降低到3.5%左右,个变炉出口气体温度达到400。
C左右。
经过小变炉回收热量产生蒸汽,同时使1气体温度降到180—200℃,然后进入低温变换炉(简称低变炉)。
在低变偿化剂作用下,一氧化碳进一步发生变换反应,使一氧化碳减到0.3%以下,出口气温度达到200—220℃。
此时气体尚含有大量湿热和潜热。
这部分热量经锅炉给永加热器和制冷再沸2R恢热,使温度降至40℃左右,送往脱碳系统。
在变换过程中主要控制一氧化碳的含量。
检查变换效率。
(四)脱碳由变换工序来的低变气进脱碳系统的吸收塔,经本非尔溶液或环丁洲一乙醇胺溶液吸收二氧化碳。
出塔气中二氧化碳含量要求小于0.1%。
为了防止气体中央带脱碳液,让共进入洗涤塔,用软水洗去液沫后再进入甲烷化换热器。
脱碳塔出来的富他经换热器后.减压送至二氧化碳再生培,用蒸汽加热再沸器,在温度128℃下脱去二氧化碳。
为了提高脱碳效率和净化反,主要进行脱碳液酌组分分析和服碳塔出u净化气中二氧化碳的分析。
由再生塔顶出来的二氧化族,经空冷器和永冷器,气体温度降至柏℃。
再经二氧化碳分离器除去冷凝水,送到尿素车间作原料。
再生后的脱碳掖(贫液),先进溶液空冷器。
冷却至65℃左右,由溶液循环泵加压。
再经溶液水冷器冷却至40℃后。
送人二氧化碳吸收塔循环使用。
(五)甲烷化由吸收塔出来的净化气,先经甲烷化换热器换热,气体温度升高到320℃左右,再进入学烷化加热器,使气体温度提到350℃;然后进入甲烷化炉,在催化刘的作用下一氧化碳、二氧化碳与氢气反应。
生成甲烷。
甲烷化后出口气中一氧化碳和二氧化碳的总置应小于10ppm。
这里需要采用连续自动痕员分析仪,进行测量和控翻。
(六)氨的合成经压缩后的氢气与循环气混合后进人氨冷凝器上部与氨蒸发器出来的冷气换热。
部分氨被冷凝。
气体进入氨蒸发器后,被外层的液氨冷却至-2℃左右,返回到冷凝塔的下部。
经液氨分离器冷交换后的气体中含氨誊最终降刭3%以下。
再进人合成塔,经主换热器换热后。
再经催化剂筐内冷却管换热。
使温度升至400一450℃后,从中心管进入催化剂后。
氨的合成在高温、高压、催化剂作用下进行,反应式如下:3H一-Nf·2NHfrQ。
反应后的气体含氨量在18.5%左右,温度为480—530℃,由塔底进入的冷气进行换热。
使气体温度降至375℃左右,再进人中置锅炉回收反应热量。
气体温度下降到235‘c左右返回合成塔下部,气体经主换热器内冷却至110—130℃。
气体出合成塔后,进人u型管水冷器,冷却至35℃左右,部分氨冷凝成液体,经氨分离器分离出液氨后,气体重新返回系统循环。
在此需要分析循环气,保证甲烷含量不大于15%,合成塔入口氨含量不大于3%。
由冷疑塔氮分离器出来的液氨减压后,送往液氨缓冲槽液氨经计量表计量后送住氨库.气榴部分送往氨吸收。
2.合成氨反应器(1)催化剂热力学计算表明,低温、高压对合成氨反应是有利的,但无催化剂时.反应的活化能很高,反应几乎不发生。
当采用铁触媒作催化剂时,由于改变了反应历程,降低了反应的活化能,使反应以显著的速率进行。
铁触媒是由融熔的铁的氧化物制成的,它含有钾、钙和铝的氧化物作为稳定剂与促进剂,而且是以氧化态装到合成塔中去的,在进行氨的生产以前,铁触媒2必须加以活化,把氧化铁还原成基本上是纯的元素铁。
铁触媒还原期间,合成气是循环通过合成塔的,当反应已经开始进行时,非常重要的是循环气要尽可能地加以冷却(但设备中不能结冰的危险),把气体中的水份加以冷凝开除去以后再重新进入合成塔,否则,水汽浓度高的气体将进入已经还原了的触媒床,水蒸汽会使已经还原过的触媒和活性降低或中毒,一旦合成氨的反应开始进行,生成的氨就会使冰点下降,这就可以在更低的温度下把气流中的水分除去。
另外,温度压力都会影响催化剂活性,一些氧化物如CO等还可能引起催化剂中毒。
(2)工艺条件:高压法:操作压力70~100MPa,温度为550~650度;中压法:操作压力20~60MPa,温度为450~550度;高压法:操作压力10MPa左右,温度为400~450度。
目前中压法技术成熟,经济性较好,被广泛采用。
(3)反应器结构合成氨反应器是合成氨生产的关键设备,作用是氢氮混和气在塔内催化剂层中合成为氨。
由于反应是在高温高压下进行,因此要求反应器不仅要有较高的机械强度,而且应有高温下抗蠕变和松弛的能力。
同时在高温、高压下,氢、氮对碳钢有明显的腐蚀作用,使反应器的工作条件更为复杂。
为了适应氨合成反应条件,合理解决存在的矛盾,反应器由内件和外筒两部分组成,内件置于外筒之内。
进入反应器的气体(温度较低)先经过内件与外筒之间的环隙,内件外面设有保温层,以减少向外筒散热。
因而,外筒主要承受高压(操作压力与大气压之差),但不承受高温,可用普通低合金钢或优质碳钢制成。
内件在500℃左右高温下操作,但只承受环系气流与内件气流的压差,一般只有1~2MPa,即内件只承受高温不承受高压,从而降低对内件材料和强度的要求。
内件一般用合金钢制作,塔径较小的内件也可用纯铁制作。
内件由催化剂筐、热交换器、电加热器三个主要部分组成,大型氨合成反应器的内件一般不设电加热器,而由塔外加热炉供热。
3.参考文献:孟岩《合成氨的生产方法以及工艺流程研究》3第三篇:合成氨工艺简介合成氨工艺控制方案总结一合成氨工艺简介中小型氮肥厂是以煤为主要原料,采用固定层间歇气化法制造合成氨原料气。
从原料气的制备、净化到氨的合成,经过造气、脱硫、变换、碳化、压缩、精炼、合成等工段。