钢轨生产技术
国内外重轨钢生产技术调研

发展。
关键词
1 前 言
‘
从 l世 纪中期 到现在 ,钢轨 钢的发 展经历 了漫长 9
施 。 以生产具有 极少夹 杂 、低氢 和较均匀 化学成 分 的 钢轨 。
的过程 ,它 的前 1 年是一个不引人注 目的渐进的历 2 0 钢轨加 工方 面包括 万能轧 机轧制 、高压 水除 鳞 。 史。 在随后的时间里, 钢轨钢的发展发生了一场革命。 在线轨头淬火和改进 的辊校直以及检测方法等 。目标 自19 年以来 ,美国钢铁协会就先后组织了三次钢轨 是生产具有高耐磨性 、低残余应力和窄公差范同的钢 90 冶金专题 讨论会。即: “ 优质钢轨钢”。 “ 钢轨钢的 轨 。 开 发 、生产 与性 能” 和 “l 2世纪 的钢轨 钢” 。我 国现 22我 国钢轨钢的生产现状 . 国外重 轨钢生 产_ T艺基 本相 似忙 :高炉 铁水一 ・ 为 有铁路营运里程约7 万k 。 . m 随着全国铁路第六次大提 5 速 ,这标 志着 我国铁 路建设 已经有 了长足 的进步 。但 铁水l脱一顶底复合吹炼一L 炉一连铸 ( 一 F 大方坯 ) 一 是同我国的社会与经济发展需求相对照起来 ,铁路的 万能轧机 。目 前国内重轨钢的生产也普遍采用 “ 铁水 运能运力仍属限制性环节,铁路运输的高速重载化刚 预 处理—转炉一 L F炉外精炼一 真 空脱气一 连铸 ”T艺 T 刚起步,我国面临着铁路运输现代化的繁重而巨大的 进 行生产 ,在各 }艺 环节 中采用相 关技 术进行 钢 水杂 任务。我国现有4 家重轨生产厂( 攀钢 、 包钢 、 鞍钢和 质 元素 的控 制技术 ,以达 到净化 钢水 的 目的。 武钢) 产能力相 当 ,从数量 上看虽可基本 满足要求 , 生 目前生产重 轨 的厂家 是攀钢 、鞍钢 、包钢 和武钢 , 但 高速重 载轨 的开 发在 国内 才起 步不久 ,全 长淬火轨 这 四家重 轨生产 企业 南于技 术装 备条 件不 同 ,因此 。 供不应求。为了提高重轨的质量等级 ,以适应市场对 重 轨生产技 术和产 品实物 质量 存在 差异 ,下 面将对 四 高速重载钢轨的要求 , 并向国际标准靠拢,迎接人世 家重 轨生产企 业的重 轨生产 现状分 别加 以评述 。 . 1包 2 “4 ‘ 冲击 ,提高重轨在国际国内两个市场的竞争能力 ,就 2 . 钢 的重 轨钢生 产 }
轨道施工方法、工艺及措施

轨道施工方法、工艺及措施一、轨排组装⑴工艺流程图轨排组装施工工艺流程图见下图:⑵工艺流程说明施工准备:按施工设计资料计算轨节表,备齐轨料并堆码于生产线两侧。
摆放轨枕:用10吨龙门吊将轨枕吊到组装台上。
上钢轨:利用两台10吨龙门吊吊轨。
按轨排表计算值用方尺控制钢轨相错量,将钢轨吊到轨枕承轨槽内。
画线方枕:在钢轨内侧用白油漆画线,对线方正轨枕。
散配件、组装:将配件散放在轨枕头上,用专用工具使扣件将钢轨和轨枕组装成轨排。
成品轨排检查:由质检员详细检查轨排质量是否符合标准,不合格的重新处理,并作好原始记录,在每个轨排上配齐鱼尾板及螺栓带帽,并涂油放在轨排接头上,用油漆在轨排铺设终端标注轨枕分中线,轨排号及生产班组。
吊装轨排:用两台10吨龙门吊将成品轨排按铺设顺序吊运装车或存放于轨排场。
⑶质量控制及检测轨枕检查:检查轨枕,如有不合格一律不用,对个别有缺陷的轨枕进行处理。
吊枕时轨枕生产厂标在单侧一致,如有不对的必须逐根掉头,每次自轨枕堆码场起吊不超过10根轨枕。
钢轨检查:吊轨前检查钢轨型号、长度是否与设计一致,直线段钢轨配对时两钢轨偏差在3mm以内,曲线地段按轨排表计划选配缩短轨。
并将钢轨长度正负误差值写在轨头上。
配件检查:各种零件安装齐全,位置正确。
二、铺轨机铺轨⑴艺流程图铺轨机铺轨施工工艺流程图见下图。
⑵工艺流程说明①施工准备复核铺轨面标高和线路中心线,加密线路中心桩;将中心桩引入路肩上并作明显标记;施工设备就位;在铺架基地按轨节表拼装轨节并装车。
②运输轨节到施工地点,立换装龙门架机车推送铺轨机龙门吊及轨节到施工地点。
列车编组如下:机车→龙门架→轨节→轨节→轨节→轨节。
机车推送轨节在距轨道作业1~2km处适当地点,立换装龙门架。
换装龙门架地点选在直线地段或R>1000m以上缓和曲线上,如果条件困难,可将已铺曲线轨道在立换装龙门架位置上拨直,两端拨圆顺,两换装龙门架中心距用粉笔标出位置后,搭设龙门架基础的木垛。
武钢高速重轨全能轧机工艺装备特色
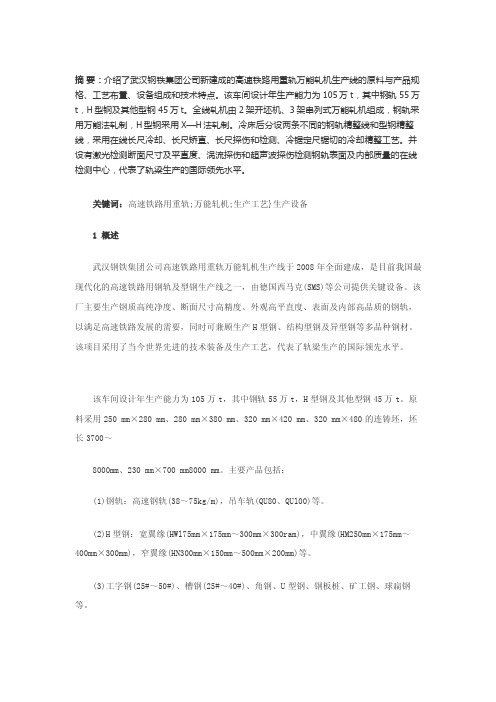
摘要:介绍了武汉钢铁集团公司新建成的高速铁路用重轨万能轧机生产线的原料与产品规格、工艺布置、设备组成和技术特点。
该车间设计年生产能力为105万t,其中钢轨55万t,H型钢及其他型钢45万t。
全线轧机由2架开坯机、3架串列式万能轧机组成,钢轨采用万能法轧制,H型钢采用X—H法轧制。
冷床后分设两条不同的钢轨精整线和型钢精整线,采用在线长尺冷却、长尺矫直、长尺探伤和检测、冷锯定尺锯切的冷却精整工艺。
并设有激光检测断面尺寸及平直度、涡流探伤和超声波探伤检测钢轨表面及内部质量的在线检测中心,代表了轨梁生产的国际领先水平。
关键词:高速铁路用重轨;万能轧机;生产工艺}生产设备1 概述武汉钢铁集团公司高速铁路用重轨万能轧机生产线于2008年全面建成,是目前我国最现代化的高速铁路用钢轨及型钢生产线之一,由德国西马克(SMS)等公司提供关键设备。
该厂主要生产钢质高纯净度、断面尺寸高精度、外观高平直度、表面及内部高品质的钢轨,以满足高速铁路发展的需要,同时可兼顾生产H型钢、结构型钢及异型钢等多品种钢材。
该项目采用了当今世界先进的技术装备及生产工艺,代表了轨梁生产的国际领先水平。
该车间设计年生产能力为105万t,其中钢轨55万t,H型钢及其他型钢45万t。
原料采用250 mm×280 mm、280 mm×380 mm、320 mm×420 mm、320 mm×480的连铸坯,坯长3700~8000mm、230 mm×700 mm8000 mm。
主要产品包括:(1)钢轨:高速钢轨(38~75kg/m),吊车轨(QU80、QUl00)等。
(2)H型钢:宽翼缘(HWl75mm×175mm~300mm×300ram),中翼缘(HM250mm×175mm~400mm×300mm),窄翼缘(HN300mm×150mm~500mm×200mm)等。
异型轨
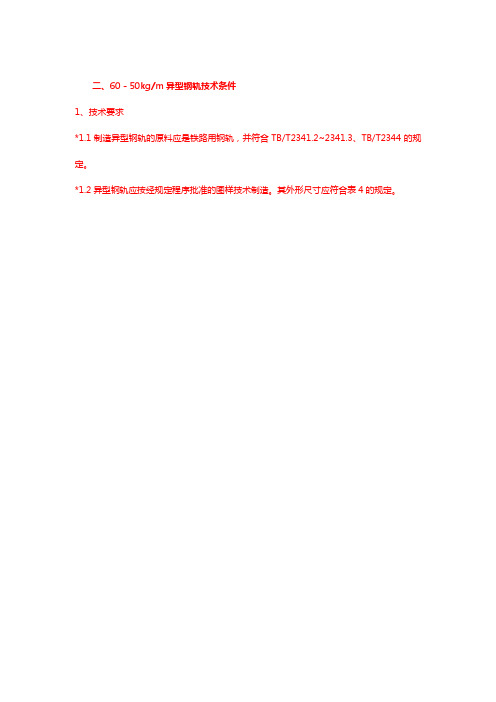
二、60-50kg/m异型钢轨技术条件1、技术要求*1.1制造异型钢轨的原料应是铁路用钢轨,并符合TB/T2341.2~2341.3、TB/T2344的规定。
*1.2异型钢轨应按经规定程序批准的图样技术制造。
其外形尺寸应符合表4的规定。
表4 外形尺寸单位:mm1.3异型钢轨的长度一般分为6.25m和12.5m两种。
也可按需要要求制造。
但应不大于25m。
其长度L<12.5m时,L±3mm;长度≥12.5m时,L±6mm。
*1.4异型钢轨的异型部位外部结构尺寸见下图。
*1.5异型钢轨的成形段的断面尺寸、孔加工尺寸公差应符合TB/T2341.2-TB2341.3的规定。
1.6异型钢轨的锻造成形段及过渡段不得有裂纹、过烧、局部凹坑等锻造缺陷。
1.7异型钢轨的过渡段部位的各相交面应圆顺平滑过渡。
*1.8异型钢轨尖角须纵向打磨圆顺,达到图样要求。
1.9异型钢轨的轨顶面及轨头侧面平直度公差每米范围内小于等于0.5mm。
轨端轨头顶面不允许向下弯曲。
*1.10异型钢轨变形段及热影响区应正火处理,长度为800mm-1000mm,其金相组织为珠光和少量铁素体,不得有过烧组织。
其晶粒度不得低于母体。
1.11 异型钢轨的轨端淬火应符合TB/T2344中的4.4的规定。
1.12异型钢轨的异型部位及热影响区均应进行超声波探伤。
*1.13异型钢轨的落锤试验数据按表2规定进行,试件不得断裂。
*1.15异型钢轨的机械性能应符合TB/T2344中4.3.1的规定。
2、检验规则2.1型式试验在下列情况下进行:2.1.1异型钢轨试生产;2.1.2工艺改变时;2.1.3周期性生产检验不合格、复检结果仍不合格时;2.1.4正常生产满三年时;2.1.5停产一年以上恢复生产时;2.1.6上级质量部门要求检验时。
2.2异型钢轨出厂检验逐一进行,检验项目为轨端踏面硬度、超声波探伤及外观检查。
2.3异型钢轨型式试验内容为全部出厂检验项目,轨端淬火层形状硬度检验、落锤、疲劳、金相、拉伸试验。
钢轨最新的国标标准

钢轨最新的国标标准钢轨是铁路运输中的重要组成部分,其质量直接关系到列车的安全和运行效率。
为了确保铁路运输的安全和可靠性,国家对钢轨的标准制定了一系列严格的规定。
钢轨的最新国标标准是铁道部颁布的《GB/T 2585-2018 钢轨》标准,本文将就该标准的主要内容进行介绍和解读。
首先,该标准对钢轨的材质和化学成分进行了详细的规定。
钢轨的主要材质为优质碳素结构钢,其中含有一定比例的碳、硅、锰等元素。
标准对这些元素的含量范围和允许的偏差进行了规定,以确保钢轨的材质符合强度和韧性的要求。
其次,标准对钢轨的几何尺寸和外观质量进行了严格的要求。
钢轨的几何尺寸包括轨头高度、轨底宽度、轨身高度、轨身宽度等参数,这些参数的偏差直接影响着钢轨的安装和使用。
同时,标准还规定了钢轨表面的缺陷和允许的缺陷尺寸,以确保钢轨表面的光洁度和平整度符合要求。
此外,标准还对钢轨的热处理和机械性能进行了详细的规定。
钢轨在生产过程中需要经过多道热处理工艺,以提高其强度和硬度。
标准规定了钢轨的热处理工艺参数和性能指标,包括抗拉强度、屈服强度、延伸率等参数,以确保钢轨在使用过程中能够承受列车的荷载和动态载荷。
最后,标准还对钢轨的检验和试验方法进行了详细的规定。
钢轨在生产出厂前需要经过严格的检验和试验,以确保其质量符合标准的要求。
标准规定了钢轨的化学成分分析、几何尺寸检验、外观质量检验、热处理质量检验等一系列检验项目和方法,以确保钢轨的质量可控可靠。
总的来说,《GB/T 2585-2018 钢轨》标准对钢轨的材质、几何尺寸、外观质量、热处理和机械性能、检验和试验方法等方面进行了全面的规定,为我国铁路运输的安全和可靠性提供了重要的技术保障。
各相关企业和单位在生产和使用钢轨时,应严格按照该标准的要求进行生产、检验和使用,以确保铁路运输的安全和可靠性。
钢轨生产技术
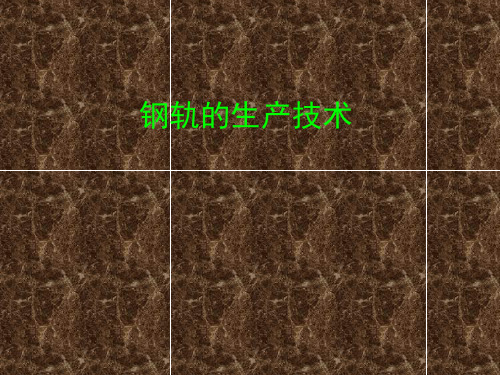
2020年12月10日
第4页 共 页
钢轨的现代生产设备和工艺:
• 转炉冶炼、连铸、万能轧机轧制、 平立复合矫直等,实现钢轨生产的 “精炼”、“精轧”、“精整”、 “质量自动检测”和“长尺化” 。 钢轨的内在和外观质量均得到大幅 度的提高,是生产高速铁路钢轨所 必须的。
2020年12月10日
第30页 共 页
• 日本钢轨生产采用高纯净冶炼、 万能轧机轧制、平立复合矫直、 涡流、超声波探伤等先进设备和 工艺,所生产钢轨无论是外观还 是内部质量均属上乘。
2020年12月10日
第25页 共 页
2 国外钢轨生产技术介绍
2020年12月10日
第26页 共 页
法国钢轨生产
• 法国Sollac工厂采用精炼和连铸 工艺生产钢轨用钢坯,具体工艺 流程为:生铁脱硫预处理——氧 气顶吹转炉冶炼——除渣处理— —LF炉外精炼——真空脱气—— 四流连铸——热锯钢坯。
2020年12月10日
第28页 共 页
日本钢轨生产
• 日本钢轨生产有新日铁(NSC)和钢管 公司(NKK)。新日铁(NSC)八藩厂 生产钢轨已有100余年的历史,累计生产 钢轨2000多万t。日本钢管公司(NKK) 福山钢厂于1973年填海新建,年产钢轨 10万t,其中半数为淬火轨,1993年1月建 成钢轨余热淬火生产线。
2020年12月10日
第23页 共 页
所以长定尺钢轨具有以下优点: • 焊接接头少; • 轨端平直度高; • 轨端没有探伤盲区;
可极大地提高轨道的平顺性,是高速铁 路建设技术的重要标志之一。
2020年12月10日
第24页 共 页
(完整版)胶接绝缘钢轨技术条件TBT2975
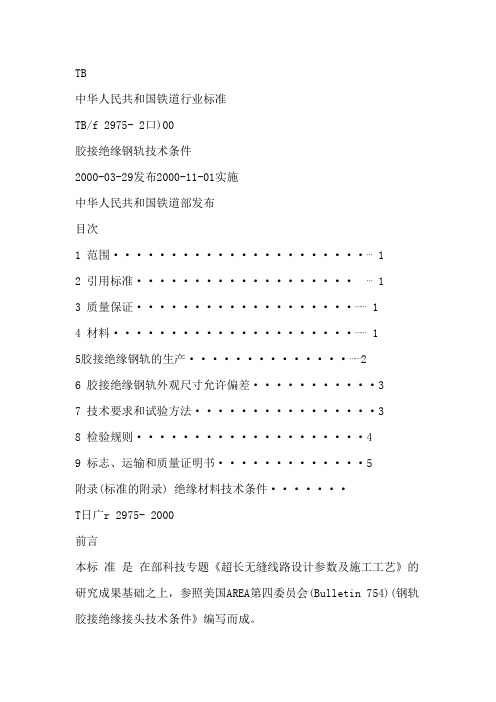
TB中华人民共和国铁道行业标准TB/f 2975- 2口)00胶接绝缘钢轨技术条件2000-03-29发布2000-11-01实施中华人民共和国铁道部发布目次1 范围······················⋯ 12 引用标准···················⋯ 13 质量保证···················⋯⋯ 14 材料·····················⋯⋯ 15胶接绝缘钢轨的生产··············⋯⋯26 胶接绝缘钢轨外观尺寸允许偏差 (3)7 技术要求和试验方法 (3)8 检验规则 (4)9 标志、运输和质量证明书 (5)附录(标准的附录) 绝缘材料技术条件·······T日广r 2975- 2000前言本标准是在部科技专题《超长无缝线路设计参数及施工工艺》的研究成果基础之上,参照美国AREA第四委员会(Bulletin 754)(钢轨胶接绝缘接头技术条件》编写而成。
钢轨生产表面缺陷分析与改进

钢轨生产表面缺陷分析与改进钢轨是铁路交通的重要组成部分,其质量直接影响着铁路运营的安全性和稳定性。
在钢轨生产过程中,可能会产生一些表面缺陷,如裂纹、松散、气泡等问题,影响钢轨的使用寿命和安全性。
对钢轨生产表面缺陷进行分析与改进非常重要。
钢轨的表面缺陷主要有以下几种类型:1.裂纹:钢轨的裂纹可能是由于生产过程中的冷却不均匀、温度变化过大或者材料的缺陷等因素引起的。
裂纹会对钢轨的强度和稳定性产生较大影响,可能导致断裂和事故发生。
2.松散:钢轨的松散主要是指轨头和轨底之间存在的间隙过大,可能是由于焊接不牢固、材料质量不好或者生产过程中的振动等因素引起的。
松散会导致轨道不平整,影响列车的行驶稳定性,并容易造成轨道走偏和事故。
为了解决钢轨生产表面缺陷问题,可以采取以下改进措施:1.加强质量控制:对钢轨生产过程进行严格监控,确保原材料的质量符合要求,避免使用有缺陷的材料。
加强生产工艺的控制,确保各个环节的操作正确无误,避免因操作不当引起的缺陷。
2.改进工艺:钢轨的生产工艺需要不断改进和优化,减少因温度变化、冷却不均匀等因素引起的裂纹问题。
可以采用先进的控制技术,确保钢轨的均匀冷却,避免产生裂纹。
3.加强焊接技术:钢轨的焊接质量直接影响着松散问题的发生。
可以采用先进的焊接技术,确保焊接牢固,避免出现轨头和轨底之间的松散现象。
4.强化质量检测:加强对钢轨进行质量检测,及时发现并修复存在的缺陷问题。
可以采用无损检测和显微镜等先进技术,对钢轨进行全面、细致的检测,确保其质量符合标准要求。
钢轨生产表面缺陷的分析与改进是保障铁路运营安全的重要环节。
通过加强质量控制、改进生产工艺、加强焊接技术和强化质量检测等措施,可以有效提升钢轨的质量,延长使用寿命,并确保铁路运营的安全性和稳定性。
重轨轧制工艺概况

(1)上下对称轧制,不存在闭口槽:
(2)万能轧机左右立辊直径水同,压F量较大的头部立辊直径较小,而压下量较小的底部立辊直径大,以保证咬八时是右立辊能同时接触轧件,防止轧ቤተ መጻሕፍቲ ባይዱ^二右窜动,并保持其变形区长度和左右立辊轧制力近似相等;
(3)轧边机可快速横移。由于万能轧机的水平辊和立辊辊型固定,孔型大小随各道压下量而变,而轧边机只轧制轨头和轨底侧面,不轧腰,因此轧边机上刻有数个尺寸不同的孔型,在往复轧制过程中,轧边机要快速横移。
鞍钢
攀钢
包钢
武钢
步进式加热炉→多级除磷→万能轧机(5机架)→自动热打印→热锯切头尾→钢轨预弯→步进式冷床冷却
步进式加热炉→多级除磷→万能轧机(7机架)→自动热打印→热锯切头尾→钢轨预弯→步进式冷床冷却
步进式加热炉→多级除磷→万能轧机(5机架)→自动热打印→热锯切头尾→钢轨预弯→步进式冷床冷却
步进式加热炉→多级除磷→万能轧机(5机架)→自动热打印→热锯切头尾→钢轨预弯→步进式冷床冷却
图3鞍钢万能轧制生产重轨工艺流程图
1.2
1.2.1加热炉
炉前装料机采用适合四流连铸坯直接热装需要的硬钩式吊车;加热炉为步进式加热炉,其步进机构采用双轮斜轨高刚度框架,配合预应力炉梁安装,冷态试车跑偏量≤2mm,计算机控制烧钢,操作画面直观逼真,操作简单易学。
主要技术参数:
( 1)炉子有效尺寸: 36295mm×8600mm;
图4攀钢万能轧机生产重轨的工艺平面布置图
2.2
2.2.1加热炉
加热炉为2座步进梁式炉,有效长度32m,有效宽度8.9m,加热能力为每座120t/ h(冷坯),最大加热能力为每座156t/ h,钢坯加热温度1150~1200℃,燃料为高、焦炉混合煤气。
高铁及既有线铁路工务钢轨基本知识

-
0.02 0.10 0.15 0.030 0.020 0.025
0.01
- 0.35
-
0.20
三、钢轨钢的组织与性能
3.1 钢轨钢的组织 珠光体、贝氏体、马氏体
3.2 钢轨钢的性能 强度、塑性、硬度、韧性、疲劳、耐磨、焊接
三、钢轨钢的组织与性能
3.1 钢轨钢的组织 珠光体
珠光体钢轨钢的组 织是由铁素体片和 渗碳体片交替构成, 其中铁素体是软韧 的相,而渗碳体是 硬脆相。
U77MnCr热轧钢轨;
1080MPa级,如EN320Cr合金钢轨,日本HH340在线热处
理钢轨;
1180MPa级和1280 MPa级热处理钢轨,
一般,强度等级为1080MPa及以上的钢轨才被称为耐磨轨 或高强轨。
目前,我国铁路常用的钢轨有U75V/U75VG、 U71Mn /U71MnG(U71Mnk)、U77MnCr、U78CrV、U76CrRE及其 热处理钢轨。
美国、法国、德国、中国等国家钢轨断面单重及长度
国别
美国
俄罗斯 日本 法国 德国 中国
钢轨断面单重(kg/m)
钢轨长度(m)
AREA115(57 kg/m)、AREA119(60 kg/m) 、AREA132(65 kg/m)、AREA133(66 kg/m)、AREA136(68 kg/m)、 AREA147(73 kg/m)
39ft(12m) 、78ft(24m)、 82ft(25m)
50、65、75 30、37、40、50、60
54、60 54、60 38、43、50、60、75
12.5、25 25、50 36、75(76) 36、120 12.5、25、75、100
一、钢轨的断面、定尺长度及类型
轨梁厂生产工艺设备简介(重点是设备20130723讲解稿)
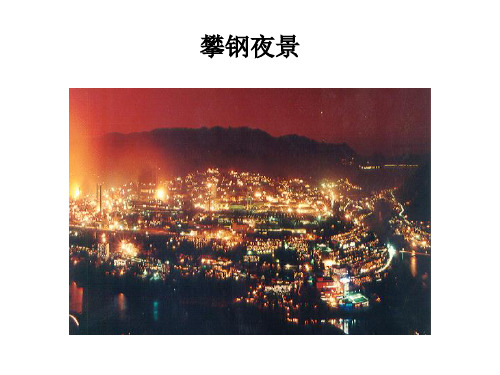
技 攻
与设计单位结 合研究对该生 产线的扩能改 造。
术 关
总结分析:现代 设备管理本质上是 现代化设备与现代 化管理理论与方法 的结合
9、钢轨矫进机HMI的自主研制
以精整钢轨矫进机HMI的研制及程序改进优化
的实施,现运行正常,保证在原控制上位机发生 故障时,马上倒入新系统,进行生产,避免了可 能造成重大停产事故的发生,解出了老外对钢轨 矫进机的技术封锁,有较大的社会效益和推广使 用价值。
组建设备专家组,提升设备状态管理水平
用各作业区的精英人才,组建跨区域的专家组,制定精密 点检、状态监测、裂化倾向分析等设备范围或设备点, 开展预知维修的贮备和推广应用。
6、做好备件“三化”实施管理工作
• 重点做好检测中心导向对中装置和超声波 轨头踏面升降装置 • 国产化研制;万能线E1/U1轧机前工作辊道 长寿化研究 • 实施工作;重轨矫直机水平、立辊主减速 机国产化研制实施等工作, • 为节约备120万元以上,缩短备件订货周期 , • 为生产创造良好的设备条件。
2 3 4
突出专职点检的核心地位 规范点检业务流程,深化促进作业长制 设立倒班作业长,行使“8小时设备室主任”职责
5
深化设备事故故障管理,切实开展技术分析
3、应用现代化管理方法,控制成本,
降低备件消耗
• 应用现代化管理方法
•措施执行严格
•对全厂与备件、材料相关的 各项标分解到各作业区 •对备件、材料的订货、跟踪、 验收及上下机流程操作进行 了严格的规定和考核
2 主要装备 ——万能线
(4)钢轨打印机
钢轨打印机安装在万能精轧机后,具有自动快速更换字符功能,与轧 制速度相匹配。两台打印机一用一备。
主要参数:轧件速度:0.5~5.0m/s,打印轮字符个数:共22个,更换
钢轨生产表面缺陷分析与改进

钢轨生产表面缺陷分析与改进钢轨是铁路运输系统的重要组成部分,它承载着列车的重量,并且需要在长期使用中保持良好的运行状态。
由于制造工艺、材料质量等原因,钢轨表面可能会出现一些缺陷,这些缺陷可能对列车运行产生不良影响,甚至会对行车安全造成一定的隐患。
对钢轨表面缺陷进行分析并采取相应的改进措施具有重要意义。
一、钢轨表面缺陷种类及原因分析1. 表面裂纹表面裂纹是钢轨表面常见的一种缺陷,它可能由于材料内部的应力集中、冷却速度不均匀等原因造成。
在使用过程中,轨道上车辆的重压和挤压也会加剧表面裂纹的扩大和延伸。
这种缺陷一旦形成,很容易导致钢轨的断裂,严重影响行车安全。
2. 锈蚀由于天气、环境等因素的影响,钢轨表面容易发生锈蚀。
锈蚀不仅会降低钢轨的表面硬度,还会使得钢轨表面粗糙,影响列车的正常行驶。
3. 凹坑在使用过程中,钢轨表面可能会出现一些凹坑,这些凹坑可能由碰撞、磨损等因素造成。
凹坑的存在会增加列车的颠簸程度,对车轮和车体的磨损也会加剧。
二、钢轨表面缺陷改进技术1. 制定严格的制造标准钢轨厂家应该根据国家标准和行业规范,制定严格的生产工艺和质量控制标准,确保钢轨的各项性能符合要求。
2. 采用先进的生产工艺现代制造技术可以通过精密的轧制设备和工艺流程,减少钢轨表面缺陷的产生。
通过对轧制温度、冷却速度等参数进行精确控制,可以有效减少钢轨表面的裂纹和变形。
3. 加强质量检测在生产过程中,对钢轨进行全程跟踪检测,及时发现表面缺陷,并做好记录和分析。
这样可以及时调整生产工艺,保证产品质量。
4. 技术改进不断研发新的钢轨材料和生产工艺,提高材料的抗磨损性能和耐腐蚀能力,减少表面缺陷的产生。
三、改进对策与建议1. 完善钢轨生产工艺通过引进现代化生产设备、改进轧制工艺和加强工艺控制等手段,减少钢轨表面裂纹和变形的产生。
2. 加强质量控制建立健全的质量管理体系,加强对钢轨表面缺陷的检测和分析,及时发现和处理问题。
3. 提高材料质量选择优质的钢材原料,加强对材料的原料控制,确保钢轨的材料质量达到国家标准。
高速铁路有关知识

高速铁路钢轨1 高速铁路对钢轨的要求高速铁路轴重轻,速度快,磨耗少;线路条件和列车状态好,曲线半径大,轨道平顺,高速铁路对钢轨的要求:(1)高平直度、高几何尺寸精度(2)高韧性(3)高纯净度(4)高焊接性能(5)高安全性和可靠性2 高速铁路钢轨材质的选择2.1 国外高速铁路采用的钢轨材质国外高速铁路基本采用800~880MPa强度等级的热轧钢轨。
从材料角度来看,钢轨强度等级低,虽然耐磨性要差一些,但韧性、塑性、焊接工艺性、打磨性较好(硬度低易打磨,并不易出现脆性马氏体组织),钢轨的安全储备大、质量可靠性高,这正是高速铁路所要求的最重要的性能指标。
日本是世界上最早建设高速铁路的国家。
日本新干线一直采用强度等级为800MPa、轨面硬度大于235HB的热轧钢轨。
法国在上世纪80年代建设的第一条高速铁路即东南线(巴黎—里昂)时采用700MPa的热轧钢轨(UIC700)。
该线路自1983年开通,至今未大修换轨。
后来修建的高速铁路均采用强度等级为880MPa的UIC900A钢轨。
德国高速铁路客货混线,采用强度等级880MPa的UIC900A 钢轨。
其他欧洲国家以及韩国等修建的高速铁路也均采用强度等级为880MPa的UIC900A钢轨。
日本、欧洲高速铁路用钢轨的强度等级及其性能注*:在新颁布的欧洲标准将UIC900A改为R260,并优化了化学成分。
2.2 我国钢轨的化学成分及性能特点2.2.1 我国钢轨的化学成分我国铁路目前广泛使用的钢轨主要有强度等级为880MPa的U71Mn和强度等级为980MPa的U75V。
我国主要钢轨化学成分/%2.2.2 我国U75V和U71Mn钢轨的性能特点U71Mn轨为我国至今使用时间最长的强度等级为880MPa 钢轨,有较好的韧、塑性,尤其低温性能较好,焊接性能优良。
U75V轨在U71Mn钢轨的基础上,增加了碳、硅含量,添加了微合金元素钒,降低了Mn含量,热轧后强度等级为980MPa,比U71Mn钢轨高一个强度等级。
钢轨打磨技术

韶山4B型干线货运电力机车
韶山4B型干线货运电力机车,代号SS4B,技术参数与 SS4基本相同。
为实现干线货运机车简统化、系列化目标,进一步提 高机车安全性、可靠性、互换性,根据铁道部科技函 [1991]499号和[1992]239号文件,由株机厂和株洲所共同 研制SS4B型8轴重载货运电力机车。
韶山3B型重载货运电力机车
韶山3B型重载货运电力机车,代号SS3B。株洲电力机 车厂2002年在SS系列机车的设计平台上开发的一种12轴重 载货运电力机车。该车由两节完全相同的6轴电力机车通过 内重联环节连接组成,每节车为一完整系统。
机车功率持续2×4350kW,最大速度100km/h,车长 2×20200mm,轴式2(C0-C0),电流制为单相工频交流。
钢轨打磨技术
内容
一、轨面管理与轮轨系统动力学 二、机车车辆及动车组结构基本知识 三、车辆-轨道系统动力学的基本知识 四、轮轨接触几何学的基本知识 五、钢轨合理断面及钢轨打磨 六、讨论
一、轨面管理与轮轨系统动力学
1、轨面的概念与内涵 轨面(为行车提供的运行平台) 轨面的作用(运行的平面、导向、承载、传载) 轨面的工作特点
韶山7C型电力机车
韶山7C型电力机车,代号SS7C。该车是从牵引客车的实际 出发,吸收国内外客车的成熟经验,对机车的牵引性能、动力 学性能、主要电机电器性能等方面进行了专门设计,是韶山7型 电力机车系列化产品之一。
它具有以下特点:牵引性能优良,加速和高速性能匹配合 理;轴重轻、簧下重量小,动力学性能在既有线路上表现良好; 满足客车的用电、用风要求;运用可靠等。技术先进、布置合 理、外形美观、运用可靠、维护方便、操作顺畅。机车功率持 续4800kW,最大速度120km/h,车长20200mm,轴式B0-B0-B0, 电流制为单相工频交流。大同机车厂制造。
2975-2000胶接绝缘钢轨技术条件
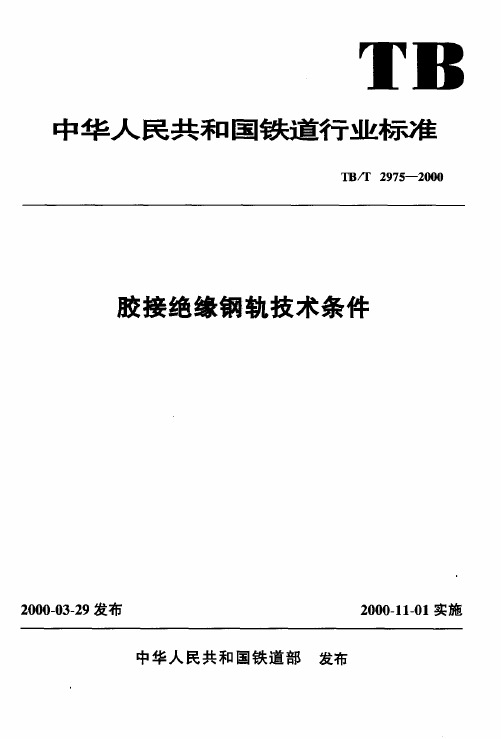
生产厂家应建 立符合 G B / I ' 1 9 0 0 2 -I S O 9 0 0 2 -1 9 9 4 的质量保证体系。
4 材料
用于生产胶 接绝 缘钢轨 的各部件 , 包括钢轨 、 夹板 、 螺栓 、 绝缘 材料等 , 应经检验 合格。 4 . 1 钢轨
4 . 1 . 1 钢轨型式尺寸、 允许偏差、 技术要求应符合 T B / I ' 2 3 4 4 的规定。
2 7 0 0 3 0 0 0 3 3 0 0 0. 5 mm
3
检 验 要 求
不 破坏, 卸载后钢轨与夹板相对位移量不超过
同上 同上
干燥和潮湿 两种状 态均达到规定 , 为合格 。
电阻值大于 1 干燥状态: 0 Md L 潮湿状态: 电阻值大于 1 0 0 0 n o 7 . 1 . 3 疲劳 试验 疲劳试验过程中, 跨中 截面的 最大 位移不超过 1 . 8 0 m m . 7 . 2 试验方法 7 . 2 . 1 整体剪切试验 分别沿胶接绝缘钢轨中间的端板和距夹板端外侧 3 一5 c m处锯切( 端面垂直度偏差不超 过0 . 1 5 n u n ) 成两个试件。在锯切时应不破坏胶接 槽板。 试 验时沿钢轨的轴线纵向 加载, 钢轨与夹板相对位移稳定后, 再增加荷载, 每次增加 1 5 0
直径 士0 . 5 r m m
位置 士 0 . 5 m m
4 . 2 夹板
4 . 2 . 1 夹板采用 B 7 钢或性能优于B 钢的其他优质钢制造。 4 . 2 . 2 夹板经热处理后的力学性能应符合表 1 的规定。
布 氏硬度
月王B
表 1 抗 拉强 度
5胶 接 绝 缘 钢 轨的 生产 ・ ・ ・ ・ ・ ・ ・ ・ ・ ・ ・ ・ ・ ・ ・ ・ ・ ・ ・ ・ ・ ・ ・ ・ ・ ・ ・ ・ ・ ・ ・ ・ ・ ・ ・ ・ ・ ・ ・ ・ ・ ・ ・ ・ ・ ・ ・ ・ ・ ・ ・ ・ ・ ・ ・ ・ ・ ・ ・ ・ ・ ・ ・ ・ ・ ・ ・ ・ ・ ・ ・ ・ … …2
工业用钢轨的轨床固定与连接技术
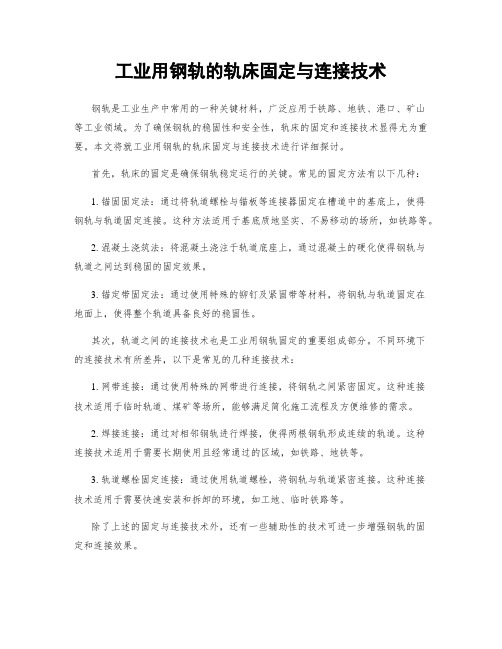
工业用钢轨的轨床固定与连接技术钢轨是工业生产中常用的一种关键材料,广泛应用于铁路、地铁、港口、矿山等工业领域。
为了确保钢轨的稳固性和安全性,轨床的固定和连接技术显得尤为重要。
本文将就工业用钢轨的轨床固定与连接技术进行详细探讨。
首先,轨床的固定是确保钢轨稳定运行的关键。
常见的固定方法有以下几种:1. 锚固固定法:通过将轨道螺栓与锚板等连接器固定在槽道中的基底上,使得钢轨与轨道固定连接。
这种方法适用于基底质地坚实、不易移动的场所,如铁路等。
2. 混凝土浇筑法:将混凝土浇注于轨道底座上,通过混凝土的硬化使得钢轨与轨道之间达到稳固的固定效果。
3. 锚定带固定法:通过使用特殊的铆钉及紧固带等材料,将钢轨与轨道固定在地面上,使得整个轨道具备良好的稳固性。
其次,轨道之间的连接技术也是工业用钢轨固定的重要组成部分。
不同环境下的连接技术有所差异,以下是常见的几种连接技术:1. 网带连接:通过使用特殊的网带进行连接,将钢轨之间紧密固定。
这种连接技术适用于临时轨道、煤矿等场所,能够满足简化施工流程及方便维修的需求。
2. 焊接连接:通过对相邻钢轨进行焊接,使得两根钢轨形成连续的轨道。
这种连接技术适用于需要长期使用且经常通过的区域,如铁路、地铁等。
3. 轨道螺栓固定连接:通过使用轨道螺栓,将钢轨与轨道紧密连接。
这种连接技术适用于需要快速安装和拆卸的环境,如工地、临时铁路等。
除了上述的固定与连接技术外,还有一些辅助性的技术可进一步增强钢轨的固定和连接效果。
1. 涂抹防锈剂:在轨道固定连接之前,在连接部位涂抹一层防锈剂,能够有效防止钢轨生锈以及连接部位的腐蚀现象。
2. 使用垫片:在连接钢轨时,可以适当添加垫片,能够提供额外的支撑和稳固,增强钢轨固定的效果。
3. 定期检查维护:定期检查轨道的固定和连接部位,及时发现并处理存在问题,确保钢轨的稳定性和安全性。
需要注意的是,在进行轨道固定和连接技术时,需要根据具体的工程场景和使用要求进行选择。
中国铁路无缝焊接钢轨规范
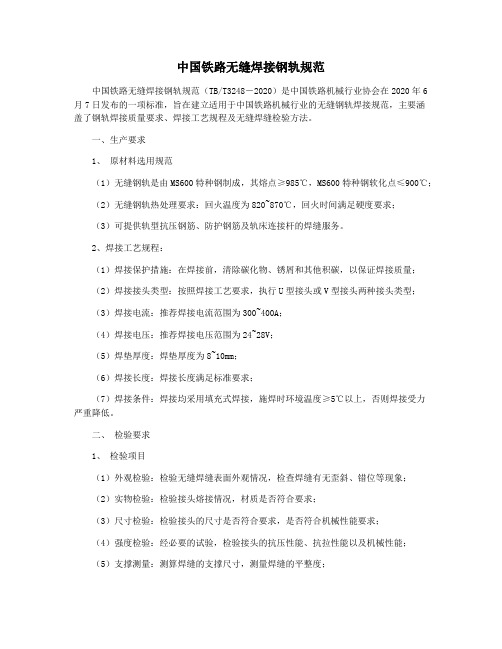
中国铁路无缝焊接钢轨规范中国铁路无缝焊接钢轨规范(TB/T3248-2020)是中国铁路机械行业协会在2020年6月7日发布的一项标准,旨在建立适用于中国铁路机械行业的无缝钢轨焊接规范,主要涵盖了钢轨焊接质量要求、焊接工艺规程及无缝焊缝检验方法。
一、生产要求1、原材料选用规范(1)无缝钢轨是由MS600特种钢制成,其熔点≥985℃,MS600特种钢软化点≤900℃;(2)无缝钢轨热处理要求:回火温度为820~870℃,回火时间满足硬度要求;(3)可提供轨型抗压钢筋、防护钢筋及轨床连接杆的焊缝服务。
2、焊接工艺规程:(1)焊接保护措施:在焊接前,清除碳化物、锈屑和其他积碳,以保证焊接质量;(2)焊接接头类型:按照焊接工艺要求,执行U型接头或V型接头两种接头类型;(3)焊接电流:推荐焊接电流范围为300~400A;(4)焊接电压:推荐焊接电压范围为24~28V;(5)焊垫厚度:焊垫厚度为8~10mm;(6)焊接长度:焊接长度满足标准要求;(7)焊接条件:焊接均采用填充式焊接,施焊时环境温度≥5℃以上,否则焊接受力严重降低。
二、检验要求1、检验项目(1)外观检验:检验无缝焊缝表面外观情况,检查焊缝有无歪斜、错位等现象;(2)实物检验:检验接头熔接情况,材质是否符合要求;(3)尺寸检验:检验接头的尺寸是否符合要求,是否符合机械性能要求;(4)强度检验:经必要的试验,检验接头的抗压性能、抗拉性能以及机械性能;(5)支撑测量:测算焊缝的支撑尺寸,测量焊缝的平整度;(6)抗拉性检验:检验支撑尺寸是否符合标准规定要求;(7)平整度检验:检验支撑地面平整度是否符合标准规定;(8)抗冲击检验:检验焊缝对冲击的耐久性和抗裂性。
三、覆盖范围本标准适用于中国铁路机械行业钢轨的焊接,不适用于无缝钢轨的施工现场实践安装、调整现场、铺装现场以及拆卸现场等技术服务。
高速铁路钢轨的设计与制造工艺研究

高速铁路钢轨的设计与制造工艺研究随着现代交通工具的发展和人们对交通效率的不断追求,高速铁路成为了全球范围内的重要交通建设项目。
而高速铁路钢轨作为高速铁路的基本组成部分之一,其设计与制造工艺的研究对于保障铁路运输的安全、稳定以及舒适性至关重要。
首先,钢轨的设计应考虑到列车运行过程中的力学与热力学特性。
高速列车的高速运行会给钢轨带来较大的载荷和温度变化,因此钢轨的设计需要确保其能够承受列车的重量和动力,同时在高温条件下具备较好的膨胀和收缩性能。
通过优化轨底的形状与钢轨的截面尺寸,可提高钢轨的强度和刚度,从而提高铁路的运行速度和曲线通过能力。
其次,在高速铁路钢轨的制造过程中需考虑到材料的选择与处理。
一般而言,高速铁路钢轨应采用高强度合金钢材料制造,以保证其在高载荷和高温环境下的耐久性和可靠性。
此外,通过适当的热处理工艺,可以提高钢轨的硬度和强度,增强其抗疲劳和抗变形的能力。
目前,常用的制造工艺包括连铸轧制、控轧和TMCP (热机械控制轧制)等,这些工艺能够有效地控制钢材的组织结构,提高钢轨的力学性能和表面质量。
另外,钢轨的表面处理与轨床维护也是关键的研究点。
在高速列车运行过程中,钢轨表面会受到很大的冲击和摩擦力,如果表面质量不达标,将会影响列车的行驶平稳性和乘坐舒适度。
因此,在钢轨制造过程中,要注重表面的研磨和抛光工艺,确保钢轨表面的光洁度和平整度。
此外,对于已经投入使用的高速铁路,及时进行轨面维护也十分重要。
例如,采用超声波、红外线等先进技术对钢轨表面进行检测可以提前发现隐蔽的裂纹和缺陷,并及时进行修复和更换。
最后,高速铁路钢轨的设备与测试技术也不容忽视。
在钢轨制造过程中,需要配备合适的生产设备和工具,以确保钢轨的加工精度和质量。
此外,为了对钢轨进行质量检测和性能评估,需引入先进的物理、化学和力学测试技术。
例如,利用电子显微镜、拉伸试验机和机械性能检测仪等设备,可对钢轨的微观组织、硬度、强度等进行准确的测试和分析。
- 1、下载文档前请自行甄别文档内容的完整性,平台不提供额外的编辑、内容补充、找答案等附加服务。
- 2、"仅部分预览"的文档,不可在线预览部分如存在完整性等问题,可反馈申请退款(可完整预览的文档不适用该条件!)。
- 3、如文档侵犯您的权益,请联系客服反馈,我们会尽快为您处理(人工客服工作时间:9:00-18:30)。
3.4
钢轨矫直
在钢轨标准中各国均做出严格规定,即成品钢轨必 须以平直状态交货,就必须对钢轨进行矫直。 钢轨的矫直过程是一个弹塑性变形的复杂过程。 可分成两个阶段:反向弯曲阶段和弹性恢复阶段。 在反向弯曲阶段,钢轨受到外力和外力矩作用,产 生弹塑性变形; 在弹性恢复阶段,钢轨在存储在自身内的弹性变形 能的作用下,力图恢复到原来的平衡状态。
2.2
钢轨断面特点和发展趋势
在轨腰与轨底过渡区,为实现断面平稳过渡,也采 用复曲线设计,逐步过渡与轨底斜度平滑相连。 UIC60kg/m轨,采用R120—R35—R7; 日本60kg/m轨,采用R500—R19; 中国的60kg/m轨,采用R400—R20。
2.2
钢轨断面特点和发展趋势
2.2
钢轨断面特点和发展趋势
日本的60kg/m钢轨,轨头圆弧R600—R50—R13。 中国的60kg/m和75kg/m轨头圆弧R300—R80—R13 和R500—R80—R15 现代钢轨轨头断面设计的主要特点是采用复曲线, 三个半径。 在轨头侧面则采用上窄下宽的直线型,直线斜度一 般为1:20~1:40。 在轨头下腭处多采用斜度较大的直线,其斜度一般 为1:3~1:4。
3.4
钢轨矫直
用900MPa级UIC60kg/m钢轨和1100MPa级136RE合金 轨进行比较试验,拉伸矫直与辊式矫直相比: 钢轨的裂纹扩展时间要延长40%~60%,且具有低 的疲劳扩展速度。 总的使用寿命,拉伸矫直钢轨增加30%~50%,其 疲劳表面积增加50%以上,使钢轨寿命延长40%。 经过拉伸矫直,UIC耐磨轨屈服强度提高70Mpa, 136RE合金轨屈服强度提高90MPa。
3.3
钢轨孔型设计
孔型系统的特点: 吸收了万能法大压下系数的优点,设置了一个梯形 孔,使轧件变成一个高的矩形,有利于轧件在帽形 孔中能得到较大的压下量,与改善轨头和轨底质量; 在第一个帽形孔底部采用高的切楔和较大的张开角 度及圆弧半径,以利强化轨底; 轨形孔腰部均采用不等厚设计,以增加腿根部压下 量和宽展量,保证腿长的增长,同时适当减小轨形 孔宽展量,以保证轨高尺寸。
3.4
钢轨矫直
法国从1976年开始研究新的钢轨矫直工艺,到1981 年发明了钢轨拉伸法矫直的新工艺。 采用这种工艺,可以保证钢轨具有高的平直度精度 和微小的残余应力。 拉伸矫直是在钢轨两端施加大于被矫钢轨钢屈服强 度的拉力,钢轨在拉力作用下,沿其长度方向伸长, 伸长多少取决于平直度要求。 与辊矫工艺相比,拉伸矫直钢轨残余拉应力仅为辊 式矫直的1/10。
3.5
钢轨热处理工艺
钢轨热处理工艺按其原理分为三大类 : 淬火回火工艺(QT工艺) 、欠速淬火工艺(SQ工艺) 、 控制轧制加在线热处理工艺,也称形变热处理 。 淬火回火工艺按加热方法可分为两种: 感应加热轨头淬火工艺 、整体加热整体淬火工艺 。 欠速淬火工艺按加热方法可分为三种: 感应加热欠速淬火工艺 、煤气加热欠速淬火工艺 、 余热热处理的欠速淬火工艺 。
3.4
钢轨矫直几何条件:
1
钢轨矫直
反
1
弹
1
残
钢轨矫直应力条件: σ s≤σ 矫<σ
b
3.4
钢轨矫直
钢轨矫直有三种工艺:压力矫直工艺、辊式矫直工 艺和拉仲矫直工艺。 压力矫直工艺速度低,仅用于对钢轨进行补充矫直。 钢轨常规矫直主要采用辊式矫直工艺。 在辊式矫直中又分为大变形量矫直与小变形量矫直。 采用大变形量矫直钢轨可以用较少的矫直棍对钢轨 进行矫直,但往往使钢轨的残余应力较大。 用小变形量矫直,则需要较多的娇直辊,但钢轨的 残余应力较小。
1.2
钢轨轨单重看各国普遍认为: 在大轴重、大运量的重载线路上应使用60~75kg/ m钢轨。 在车速小于160km/h的普通客运线路上应使用50~ 60kg/m钢轨 在车速超过160km/h的准高速及高速线路上应采用 60~65kg/m钢轨。
1.2
2.2
钢轨断面特点和发展趋势
在轨头与轨腰过渡区为减少应力集中所造成的裂缝, 增加鱼尾板与钢轨间的摩擦阻力,在轨头与轨腰过 渡区也采用复曲线,在腰部采用大半径设计。 UIC的60kg/m钢轨,其轨头与腰过渡区采用R7— R35—R120。 日本的60kg/m轨,其轨头与腰过渡区采用R19— R19—R500。
2.1
钢轨的品种
矿山铁路用轻轨 中国主要有:9kg/m、12kg/m、15kg/m、22kg/ m、30kg/m五种 日本主要有:6kg/m、9kg/m、10kg/m、12kg/m、 15kg/m、22kg/m六种。 客货运铁路重轨 中国主要有:38kg/m、43kg/m、50kg/m、60kg /m、75kg/m五种。 日本主要有:30kg/m、37kg/m、40kg/m、50kg /m、60kg/m五种。
3.4
钢轨矫直
辊式矫直工艺存在两种弊病: 一是造成钢轨残余应力大。过大的残余应力将会威 胁列车的行车安全,减少钢轨寿命; 二是辊矫工艺无法矫直每支钢轨的两端,为保证端 头的平直度,还必须采用压力矫对端头进行补矫, 即使这样,压力矫也很难使钢轨端头达到高速铁路 对钢轨端头平直度(0.1mm/m)的要求。
3.2
钢轨轧制孔型系统
钢轨孔型系统一般采用: 箱形孔、梯形孔、帽形孔和轨形孔。 两种轧制法在钢轨粗轧阶段均采用箱形孔(或梯形 孔)、帽形孔和轨形进行开坯。 通常采用3~5个帽形孔,帽形孔配置在二辊式可逆 开坯轧机上 。 粗轧轨形孔也多配置在二辊式可逆轧机上,轧件在 粗轧轨形孔中变形,并逐渐接近成品钢轨断面尺寸。
3.1
现代钢轨生产工艺
目前,世界上主要采用两种现代钢轨生产工艺: 长流程工艺、短流程工艺。
3.1
现代钢轨生产工艺
3.1
现代钢轨生产工艺
3.2
钢轨轧制孔型系统
钢轨孔型系统分为两类:一类为孔型轧制法孔型系 统,另一类为万能轧制法孔型系统。 两者不同之处在于对具有初步轨形的轧件的进一步 加工和最终加工方法上。 孔型法是继续在二辊式轧机(或三辊式轧机)上采用 闭口式轨形孔进行中轧和精轧。 万能法是在万能轧机(包括二辊轧边机)上采用万 能孔型进行中轧和精轧。
2.2
钢轨断面特点和发展趋势
改进轨头断面设计也是提高刚度和耐磨性方法之一。 各国在轨头踏面设计上遵循了这样一条原则:轨顶 踏面圆弧尽量符合车轮踏面的尺寸,即采用了轨头 在接近磨耗后的踏面圆弧尺寸。 UIC的60kg/m钢轨,轨头圆弧R300—R80—R13; 美国的56.9kg/m钢轨,轨头圆弧R254—R31.75— R9.52; 前苏联的65kg/m钢轨,轨头圆弧R500—R80—R15;
3.3
钢轨孔型设计
国内60kg/m钢轨孔型设计 我国60kg/m钢轨断面采用铁道部推荐断面,轨高 176mm、头宽73mm、腰厚16.5mm、底宽150mm、截面 面积77.45cm2、单重60.35kg/m。 轧机为950/800轨梁轧机,原料为300mm×350mm初 轧坯,压缩比为13.5。 采用包括两个箱形孔、一个梯形孔、三个帽形孔和 五个轨形孔的孔型系统。
2.2
钢轨断面特点和发展趋势
铁路车速和轴重的不断提高,要求钢轨具有更大的 刚度和更好的耐磨性。 为使钢轨具有足够的刚度,可适当增加钢轨高度, 以保证钢轨有大的水平惯性矩。 同时为使钢轨有足够的稳定性,在设计轨底宽度时 应尽可能选择宽一些。 为使刚度与稳定性匹配最佳,各国通常在设计钢轨 断面时控制其轨高与底宽之比,即H/B。一般H/B 控制在1.15~1.248。
3.3
钢轨孔型设计
国内75kg/m钢轨孔型设计 75kg/m钢轨断面采用前苏联国家标淮断面,即轨 高192mm、轨头宽75mm、底宽150mm、腰厚20mm、断 面面积95cm2。 轧机为950/800轨梁轧机,原料为300mm×330mm初 轧坯,压缩比为13.5。 采用1个梯形孔、3个帽形孔和5个轨形孔孔型系统。 其主要特点是在第一个荒轧帽形孔设计上采用较大 的压下系数,以强化轨头、轨底。
2.1
钢轨的品种
根据用途的不同,现代钢轨可以分为三类: 矿山铁路用轻轨、客货运铁路用重轨、吊车轨 根据钢种的不同,钢轨又可以分为: 碳素轨、合金轨和热处理轨三种。 按钢轨的力学性能,通常钢轨分为三类: 普通轨,它是指抗张强度不小于800MPs的钢轨; 高强轨,它是指抗拉强度不小于900MPa的钢轨; 耐磨轨,它是指抗拉强度不小于1100MPa的钢轨。
1.2
钢轨的发展趋势
普遍采用重型断面钢轨 50年代平均轨重43~50kg/m,60年代平均轨重 49~52kg/m,70年代平均轨重52~65kg/m。 目前各国铁路采用钢轨的最大单重为: 中国60kg/m及75kg/m轨 前苏联65kg/m及75kg/m轨 日本60kg/m轨,法国60kg/m轨,英国57kg/m轨, 美国68kg/m,意大利64kg/m轨,波兰60kg/m轨。
钢轨的发展趋势
研究开发马氏体或贝氏体钢轨钢 在钢轨的材质上随着钢轨工作条件的不断苛刻,对 钢轨性能也逐步提出了更高要求,要求钢轨钢的抗 拉强度从800MPa到900MPa到1100MPa,硬度从300HB 到350HB到388HB。 开发了碳素钢轨钢,且研制了合金钢轨钢和热处理 钢轨钢。 目前正开始研究马氏体或贝氏体钢轨钢,以获得比 珠光体钢更好的断裂韧性、耐磨性和抗疲劳性能。