零件的加工精度包括哪些【详细】
零件的加工精度包括哪些【详细版】
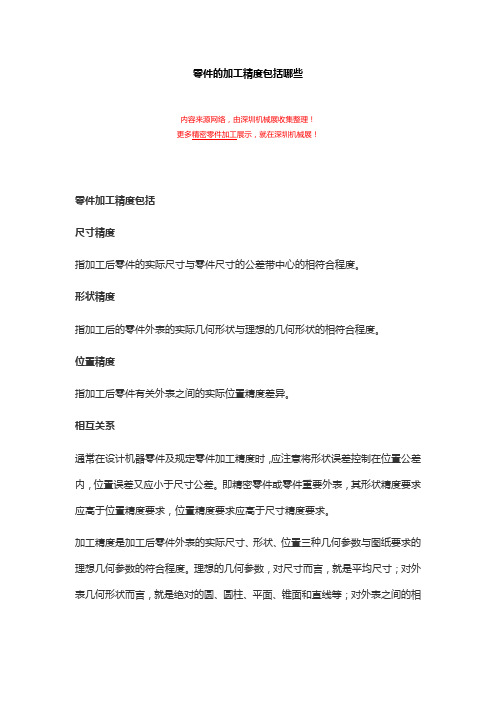
零件的加工精度包括哪些内容来源网络,由深圳机械展收集整理!更多精密零件加工展示,就在深圳机械展!零件加工精度包括尺寸精度指加工后零件的实际尺寸与零件尺寸的公差带中心的相符合程度。
形状精度指加工后的零件外表的实际几何形状与理想的几何形状的相符合程度。
位置精度指加工后零件有关外表之间的实际位置精度差异。
相互关系通常在设计机器零件及规定零件加工精度时,应注意将形状误差控制在位置公差内,位置误差又应小于尺寸公差。
即精密零件或零件重要外表,其形状精度要求应高于位置精度要求,位置精度要求应高于尺寸精度要求。
加工精度是加工后零件外表的实际尺寸、形状、位置三种几何参数与图纸要求的理想几何参数的符合程度。
理想的几何参数,对尺寸而言,就是平均尺寸;对外表几何形状而言,就是绝对的圆、圆柱、平面、锥面和直线等;对外表之间的相互位置而言,就是绝对的平行、垂直、同轴、对称等。
零件实际几何参数与理想几何参数的偏离数值称为加工误差。
加工精度主要用于生产产品程度,加工精度与加工误差都是评价加工外表几何参数的术语。
加工精度用公差等级衡量,等级值越小,其精度越高;加工误差用数值表示,数值越大,其误差越大。
加工精度高,就是加工误差小,反之亦然。
公差等级从IT01,IT0,IT1,IT2,IT3至IT18一共有20个,其中IT01表示的话该零件加工精度高的,IT18表示的话该零件加工精度是低的。
任何加工方法所得到的实际参数都不会绝对准确,从零件的功能看,只要加工误差在零件图要求的公差范围内,就认为保证了加工精度。
机器的质量取决于零件的加工质量和机器的装配质量,零件加工质量包含零件加工精度和外表质量两大部分。
机械加工精度是指零件加工后的实际几何参数〔尺寸、形状和位置〕与理想几何参数相符合的程度。
它们之间的差异称为加工误差。
加工误差的大小反映了加工精度的高低。
误差越大加工精度越低,误差越小加工精度越高。
加工精度根据不同的加工精度内容以及精度要求,采用不同的测量方法。
国家开放大学数控加工工艺第3次作业试题

国家开放大学《数控加工工艺》第3次作业试题题目1:零件的机械加工精度主要包括()。
: 机床精度、几何形状精度、相对位置精度; 尺寸精度、几何形状精度、相对位置精度; 尺寸精度、定位精度、相对位置精度; 尺寸精度、几何形状精度、装夹精度题目2:制订加工方案的一般原则为先粗后精、先近后远、先内后外,程序段最少,()及特殊情况特殊处理。
: 将手工编程改成自动编程; 走刀路线最短; 将空间曲线转化为平面曲线; 将复杂轮廓简化成简单轮廓题目3:换刀点是指在编制数控程序时,相对于机床固定参考点而设置的一个自动换刀的位置,它一般不能设置在()。
: 浮动原点上; 加工零件上; 机床固定参考点上; 程序原点上题目4:加工精度高、()、自动化程度高,劳动强度低、生产效率高等是数控机床加工的特点。
: 加工轮廓简单、生产批量又特别大的零件; 装夹困难或必须依靠人工找正、定位才能保证其加工精度的单件零件; 对加工对象的适应性强; 适于加工余量特别大、质及余量都不均匀的坯件题目5:在数控加工中,()相对于工件运动的轨迹称为进给路线,进给路线不仅包括了加工内容,也反映出加工顺序,是编程的依据之一。
: 刀具原点; 刀具刀尖点; 刀具刀位点; 刀具题目6:下列叙述中(),不属于确定加工路线时应遵循的原则。
: 应使加工路线最短,这样既可以减少程序短,又可以减少空刀时间; 使数值计算简单,以减少编程工作量; 对于既有铣面又有镗孔的零件,可先铣面后镗孔; 加工路线应保证被加工零件的精度和表面粗糙度题目7:尺寸链按功能分为设计尺寸链和()。
: 封闭尺寸链; 工艺尺寸链; 零件尺寸链; 装配尺寸链题目8:下列关于尺寸链叙述正确的是()。
: 由相互联系的尺寸按顺序排列的链环; 一个尺寸链可以有一个以上封闭环; 在极值算法中,封闭环公差大于任一组成环公差; 分析尺寸链时,与尺寸链中的组成环数目多少无关题目9:零件的相互位置精度主要限制()。
: 限制加工表面的宏观几何形状误差; 加工表面与其基准间尺寸误差不超过一定的范围; 限制加工表面与其基准间的相互位置误差; 限制加工表面的宏观几何形状误差题目10:在下列内容中,不属于工艺基准的是()。
各种机械加工方法的加工精度

各种机械加工方法的加工精度
机械加工方法是指利用机床和切削工具对金属、合金、塑料等材料进行切削、锻造、焊接、抛光等操作,以达到工件设计尺寸、形状和表面粗糙度要求的一系列工艺过程。
不同的机械加工方法有着不同的加工精度,下面将对常见的几种机械加工方法的加工精度进行详细介绍。
1.车、铣、刨、磨加工:
车、铣、刨、磨加工是最常见的机械加工方法之一,其加工精度通常可达到0.01mm级别。
其中,精度最高的是磨加工,其加工精度可达到0.001mm级别。
而车、铣、刨加工的加工精度相对较低,通常在0.01mm 至0.015mm之间。
2.钻削加工:
钻削加工是通过钻头旋转和轴向进给运动,以及工件的切削超前量来进行的。
其加工精度一般可达到0.02mm级别。
3.线切割加工:
线切割是利用金属丝或者金刚线经过电火花腐蚀加工,从而将工件切割成所需形状的加工方法。
其加工精度可达到0.005mm级别。
4.电火花加工:
电火花加工是利用放电现象进行切削的一种加工方法,其加工精度可达到0.001mm级别。
5.冲压加工:
冲压加工是通过冲床对金属板材进行冲裁、弯曲、深冲等形变加工的方法。
其加工精度一般在0.05mm至0.1mm之间。
6.锻造加工:
锻造加工是通过加热和机械力的作用,改变金属原始形状并获得所需形状的一种加工方法。
其加工精度通常为0.2mm至0.5mm之间。
7.激光加工:
激光加工是利用激光束对工件进行切割、焊接等加工的方法。
其加工精度通常可以达到0.01mm级别。
机械加工精度(机械专业课)
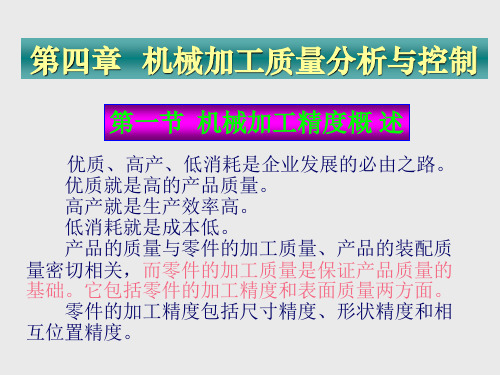
刀具回转类
加工时误差敏感
镗床
方向和切削力方
向随主轴回转而
不断变化
下面以在镗床上镗孔、车床上车外圆为例来 说明主轴回转误差对加工精度的影响。
①主轴的纯径向跳动对车削和镗削加工精度的影响
镗削加工:镗刀回转,工件不转
假设由于主轴的纯径向跳动而使轴线在y坐标方向作简谐
运动(图4-4),其频率与主轴转速相同,简谐幅值为A;
则:
Y = Acosφ ( φ=ωt)
且主轴中心偏移最大(等于A)时,镗刀尖正好通过水
平位置1处。
当镗刀转过一个φ角时(位置1’),刀尖轨迹的水平 分量和垂直分量分别计算得:
y=Acosφ+Rcosφ=(A+R)cosφ Z=Rsinφ 将上两式平方相加得: y2/(A+R)2+Z2/R2=1
表明此时镗出的孔为椭圆形。
Z1 δ1 δ1n=i1nδ1
Z2 δ2 δ2n=i2nδ2
………………
Zn δn δnn=innδn 在任一时刻,各齿轮的转角误差反映到丝杠的总误差为:
n
Σ 1n 2n nn ji jn j 1
(3)减少传动链误差的措施
1)尽量缩短传动链。 2)提高传动件的制造和安装精度,尤其是末端 零件的精度。 3)尽可能采用降速运动,且传动比最小的一级 传动件应在最后。 4)消除传动链中齿轮副的间隙。 5)采用误差校正机构
一、加工精度与加工误差
1.加工精度
加工精度是指零件加工后的实际几何参数(尺寸、
形状及各表面相互位置等参数)与理想几何参数的符合程 度。符合程度越高,加工精度就越高。反之,越低。
理想几何参数
➢表面——绝对平面、圆柱面等; ➢位置——绝对平行、垂直、同
机械加工精度
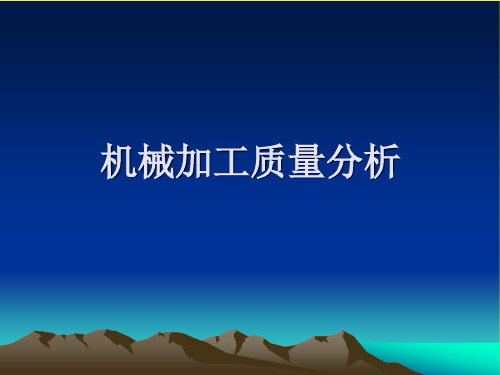
机械加工精度
1. 获得尺寸精度的方法
(1) (2) (3) (4) 试切法 调整法 定尺寸法 自动控制法
机械加工精度
2. 获得形状精度的方法 (1)轨迹法 (2)成形法 (3)展成法 3. 获得位置精度的方法 (1)根据工件加工过的表面进行找正的 方法; (2)工件的位置精度由夹具来保证。
机械加工精度
机械加工表面质量
四、 影响表面层物理机械性能的因素 1.影响表面层冷作硬化的因素
(1)切削用量 ①切削速度: 随着切削速度的增大,被加工金属塑性变形减小,同时由于 切削温度上升使回复作用加强,因此冷硬程度下降。 ②进给量: 进给量增大使切削厚度增大,切削力增大,工件表面层金属的 塑性变化增大,故冷硬程度增加。 (2)刀具 ①刀具刃口圆弧半径 增大,表面层金属的塑性变形加剧,冷硬程度增大。 ②刀具后刀面磨损宽度VB 增大,刀具后刀面与工作表面摩擦加剧,塑性变 形增大,导致表面层冷硬程度增大。 ③前角增大,可减小加工表面的变形,故冷硬程度减小。刀具后角、主偏角、 副偏角及刀尖圆角半径等对表面层冷硬程度影响不大。 (3)工件材料 工件材料的塑性越大,加工表面层的冷硬程度越严重,碳钢中含碳量越高, 强度越高,其冷硬程度越小。
机械加工精度
4)刀具热变形及对加工精度的影响 (1)刀具连续工作时 (2)刀具间歇工作 ξ(μm)
ξmax
连续切削升温曲线
间断切削升温曲线 冷却曲线
图中 ξ—— 热伸长量; ξmax —— 达到热平衡热伸长量; τ—— 切削时间; τc —— 时间常数(热伸长量为热平 衡热伸长量约63%的时间,常取3~4分钟 )。
机械加工表面质量
二、 表面质量对零件使用性能的影响 1.表面质量对零件耐磨性的影响
机械加工精度概述 管理资料

机械加工精度概述管理资料1、加工精度是指零件加工后的实际几何参数(尺寸、形状和位置)与理想几何参数的符合程度,1)零件的尺寸精度:加工后零件的实际尺寸与零件理想尺寸相符的程度。
2)零件的形状精度:加工后零件的实际形状与零件理想形状相符的程度。
3)零件的位置精度:加工后零件的实际位置与零件理想位置相符的程度。
2、获得加工精度的方法:1)试切法:即试切--测量--再试切--直至测量结果到达图纸给定要求的方法。
2)定尺寸刀具法:用刀具的相应尺寸来保证加工外表的尺寸。
3)调整法:按零件规定的尺寸预先调整好刀具与工件的相对位置来保证加工外表尺寸的方法。
4)自动控制法:使用一定的装置(自动测量或数字控制),在工件到达要求尺寸时,自动停止加工。
3、加工误差:实际加工不可能做得与理想零件完全一致,总会有大小不同的偏差,零件加工后的实际几何参数对理想几何参数的偏离程度,称为加工误差。
加工误差的大小表示了加工精度的上下,4、误差的敏感方向:加工误差对加工精度影响最大的方向,为误差的敏感方向。
例如:车削外圆柱面,加工误差敏感方向为外圆的直径方向。
因素分析法:通过分析、计算或实验、测试等方法,研究某一确定因素对加工精度。
一般不考虑其它因素的同时作用,主要是分析各项误差单独的变化规律。
统计分析法:运用数理统计方法对生产中一批工件的实测结果进行数据处理,用以控制工艺过程的正常进行。
主要是研究各项误差综合的变化规律,只适合于大批、大量的生产条件。
由机床、夹具、刀具和工件组成的机械加工工艺系统(简称工艺系统)会有各种各样的误差产生,这些误差在各种不同的具体工作条件下都会以各种不同的方式(或扩大、或缩小)反映为工件的加工误差。
工艺系统中但凡能直接引起加工误差的因素都称为原始误差。
工艺系统的原始误差主要有:1、加工前的误差(原理误差、调整误差、工艺系统的几何误差、定位误差)2、加工过程中的误差(工艺系统的受力变形引起的加工误差、工艺系统的受热变形引起的加工误差)3、加工后的误差(工件内应力重新分布引起的变形以及、测量误差)等。
零件加工精度获得方法

影响加工精度的因素
影响加工精度的主要因素:
1. 原理误差 2. 工艺系统的制造精度和磨损 3. 工艺系统的受力变形 4. 工艺系统的受热变形 5. 工艺系统调整误差 6. 工件安装夹紧误差 7. 度量误差
1. 原理误差
由于采用了近似的加工运动或者近似的刀具廓轮而 产生的。
➢ 如车削模数螺纹,由于模数螺纹的导程t=πm,而π是一 个无限小数,用交换齿轮来得到导程值时,就引入了原 理误差
系统 误差
常值系统误差
如由于铰刀直径较大,加工的孔 直径也较大
变值系统误差
如刀具磨损以及热伸长所造成的 工件尺寸误差。
三. 机械加工误差的分类
随机误差
➢ 加工过程中规律性不强,表现为噪声误差性质,符合统 计规律
➢ 如由于工件材质不均、毛坯尺寸形状差异而引起的误差
三. 机械加工误差的分类
按是否与切削状态有关来分:静态误差和切削状态 误差
当工件经n次走刀后,其径向截面形状精度可用总的误差复映系数来表
示:总n 0 Nhomakorabea1 0
2 1
n n1
1 2 n
如果每次走刀所用刀具和切削用量等都相同,忽略K系统的变化,则各次
走刀的εi相等,则:
n
总
i n为走刀次数
走刀次数(或工步次数)越多,总的误差复映系数越小,零 件形状精度越高
系统刚度越好,加工精度越高 切削深度值的大小并不影响误差复映系数值,因为误差复映
➢ 精度越高,误差越小; ➢ 精度越低,误差越大。
加工精度的内容
零件的几何参数包括几何形状、尺寸和相互位置三个方面 加工精度包括:
➢ 尺寸精度:限制加工表面与其基准间尺寸误差不超过一定的范围; ➢ 几何形状精度:限制加工表面宏观几何形状误差,如圆度、圆柱
1.1.4加工精度和加工表面质量

加工精度和加工表面质量
一
1、零件的加工质糙度
物理机械参数:强度、硬度、磁性 其它参数:防腐性、平衡性、密封性
可以概括为两方面的含义: 1)宏观几何参数(加工精度) 2)微观几何参数与物理机械性能参数(加工表面质量)
2、加工精度概念的产生: 由于加工时不可能得到准确的参数值,并且从使用要 求方面讲也不需要绝对准确,于是就产生的加工精度的概念。
重载 轻载
思考:
新车为什么要磨合?
2、对疲劳强度的影响:
交变载荷下,零件表面不平的缺陷,最容易产生应力集中, 并可发展为疲劳裂纹,从而导致零件的疲劳破坏。
1)表面粗糙度的影响:表面粗糙度值大,将降低疲劳强度。
2)表面残余应力的影响:表面的残余压应力将抵消部分交变载荷引起的 拉应力,提高了零件的疲劳强度。
冷作硬化的程度与下列因素有关:
1)产生塑性变形的力:力越大,塑性变形越大,硬化程度越 大。 2)变形速度:速度越大,塑性变形越不充分,硬化程度越小。 3)被加工材料:材料硬度越小、塑性越大,硬化程度越大。 4)刀具:刃口圆角和后面磨损增大时,硬化程度增大。 5)切削用量:切削速度越大,硬化程度越小;进给量较大或 较小,会使硬化程度增大。
3、加工精度与加工误差是相关联的,加工精度在数 值上通过加工误差反映出来。
加工精度的概念
1、加工精度:实际加工的点、线、面与理想的几何参 数相符合的程度。 理想的几何参数: 1)尺寸:尺寸的公差带中心 2)形状:绝对准确的圆柱面、平面、锥面等。 3)位置:绝对平行、垂直、同轴 加工精度包括:尺寸精度、形状精度、相互位置精度
3)表面冷作硬化的影响:适当的冷硬能减小交变载荷引起的交变幅值, 阻止疲劳裂纹扩展,提高疲劳强度。
精密加工——精选推荐

精密加⼯1、加⼯精度:是指零件在加⼯以后的⼏何参数(尺⼨、形状、位置)与图纸规定的理想零件的⼏何参数相符合的程度。
符合程度越⾼,加⼯精度则越⾼。
2、表⾯质量:指已加⼯表⾯粗糙度、残余应⼒及加⼯硬化。
3、普通加⼯:加⼯精度在1µm 以上(粗加⼯IT13~IT9、半精加⼯IT8~IT7、精加⼯IT6~IT5),粗糙度Ra0.1-0.8µm。
4、精密加⼯:加⼯精度在1~0.1µm ,粗糙度Ra0.1µm 以下(⼀般Ra0.01~0.1µm )的加⼯⽅法。
5、超精密加⼯:加⼯精度在0.1~0.01µm ,粗糙度⼩于Ra0.01µm (Ra0.01~Ra0.001µm)的加⼯⽅法。
6、特种加⼯:a.电物理加⼯如:电⽕花加⼯(EDM),电⼦束加⼯(EBM),离⼦束加⼯(IBM)等。
b.电化学加⼯如:电解加⼯(ECM)和涂镀加⼯(EPM)。
c.物理加⼯如:超声波加⼯(USM)、激光束加⼯(LBM)。
d.化学加⼯光刻加⼯包括刻蚀加⼯和光化学加⼯e.复合加⼯常规⽅法与特种加⼯⽅法结合形成的加⼯,如电解磨削、机械化学研磨。
7、精密和超精密加⼯设备应具有以下⼀些要求:⾼精度、⾼刚度、⾼稳定性、⾼⾃动化。
8、⼯作环境条件恒温:20℃±(1~0.02)℃恒湿:35﹪~45﹪空⽓净化、防振等。
9、超精密加⼯要求测量精度⽐加⼯精度⾼⼀个数量级10、⾦刚⽯晶格中有三种重要晶⾯,(100),(110),(111)。
11、⾦刚⽯⼑具的特点:a、硬度极⾼:HV8000~10000,切削刃锋利b、耐热性差:不宜超过800℃;c、强度低:⾃脆性⼤,对振动敏感,只能微量切削;d、与铁有强的化学亲和⼒:不宜加⼯⿊⾊⾦属,适宜有⾊⾦属、⾮⾦属e、超精密切削使⽤天然单晶⾦刚⽯⼑具:切削刃可磨得极锋利,硬度极⾼(是硬度最⾼的物质),耐磨性好,热传导系数⾼,摩擦系数低。
零件的加工质量包括加工精度和表面质量

零件的加工质量包括加工精度和表面质量。
其中加工精度有尺寸精度、形状精度和位置精度,表面质量的指标有表面粗糙度、表面加工硬化的程度、残余应力的性质和大小。
表面质量的主要指标是表面粗糙度。
1.极限与配合现代化机械制造工业中大多数产品成批生产或大量生产,要求生产出来的零件不经任何修配和挑选就能装到机器上去,并能达到规定的配合(紧松要求) 和满足所需要的技术要求。
在同一规格的一批零件中,任取一个。
不需任何就能装到机器上去。
并达到规定的技术性能要求,我们称这种零件具有互换性。
互换性在机械制造中具有重要的作用. 例如,自行车和手表的零件损坏后,修理人员很快就可以用同样规格的琴件换上,恢复自行车和手表的功能。
在实际生产过程中,加工出来的零件不可避免地会产生误差,这种误差称为加工误差。
实践证明,只要加工误差控制在一定范围内,零件就能够具有互换性. 按零件的加工误差及其控制范环制订出的技术标准,称为极限与配合标准。
它是实现互换性的基础。
为了满足各种不同精度的要求,国家标准 GB/T.1000.3 -18《极限与配合基础第3 部分:标准公差和基本偏差数值表》规定标准公差分为20 个公差等级(公差等级是指确定尺寸精确程度的等级) ,它们是 IT01、IT0、IT1,rl-,...,IT18. IT 表示标准公差,数字表示公差等级.其中IT01为最高,IT18为最低。
公差等级高,公差值小,精确程度高;公差级低,则公差值大,精确度低。
2.加工精度实际零件的形状、尺寸和理想零件的形状、尺寸相符合的程度。
精度的高低用公差来表示。
(1)尺寸精度及其检验1)尺寸精度尺寸精度是指实际零件的尺寸和理想零件的尺寸相符合的程度,即尺寸准确的程度,尺寸精度是由尺寸公差(简称公差)控制的。
同一基本尺寸的零件,公差值的大小就决定了零件的精确程度,公差值小的,精度高,公差值大的,精度低。
车、铣、刨、磨、钻、镗等加工精度详解
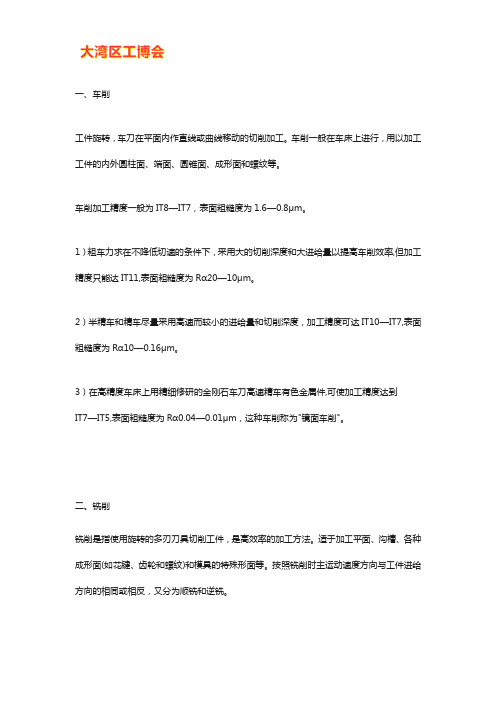
一、车削工件旋转,车刀在平面内作直线或曲线移动的切削加工。
车削一般在车床上进行,用以加工工件的内外圆柱面、端面、圆锥面、成形面和螺纹等。
车削加工精度一般为IT8—IT7,表面粗糙度为1.6—0.8μm。
1)粗车力求在不降低切速的条件下,采用大的切削深度和大进给量以提高车削效率,但加工精度只能达IT11,表面粗糙度为Rα20—10μm。
2)半精车和精车尽量采用高速而较小的进给量和切削深度,加工精度可达IT10—IT7,表面粗糙度为Rα10—0.16μm。
3)在高精度车床上用精细修研的金刚石车刀高速精车有色金属件,可使加工精度达到IT7—IT5,表面粗糙度为Rα0.04—0.01μm,这种车削称为"镜面车削"。
二、铣削铣削是指使用旋转的多刃刀具切削工件,是高效率的加工方法。
适于加工平面、沟槽、各种成形面(如花键、齿轮和螺纹)和模具的特殊形面等。
按照铣削时主运动速度方向与工件进给方向的相同或相反,又分为顺铣和逆铣。
铣削的加工精度一般可达IT8—IT7,表面粗糙度为6.3—1.6μm。
1)粗铣时的加工精度IT11—IT13,表面粗糙度5—20μm。
2)半精铣时的加工精度IT8—IT11,表面粗糙度2.5—10μm。
3)精铣时的加工精度IT16—IT8,表面粗糙度0.63—5μm。
三、刨削刨削加工是用刨刀对工件作水平相对直线往复运动的切削加工方法,主要用于零件的外形加工。
刨削加工精度一般可达IT9—IT7,表面粗糙度为Ra6.3—1.6μm。
1)粗刨加工精度可达IT12—IT11,表面粗糙度为25—12.5μm。
2)半精刨加工精度可达IT10—IT9,表面粗糙度为6.2—3.2μm。
3)精刨加工精度可达IT8—IT7,表面粗糙度为3.2—1.6μm。
四、磨削磨削是指用磨料,磨具切除工件上多余材料的加工方法,属于精加工在机械制造行业中应用比较广泛。
磨削通常用于半精加工和精加工,精度可达IT8—IT5甚至更高,表面粗糙度一般磨削为1.25—0.16μm。
加工精度
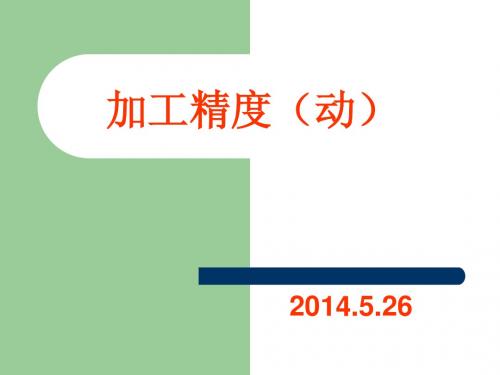
2、工艺系统受热变形引起的误差: 1) 工件受热变形: 工件受热温度升高后,热伸长 量△L为: △ L=αL△t 式中:α为工件材料的热 膨胀系数; L为工件长度; △ t为工件的温升。 例如:死顶尖装夹工件时,热变形将造成工件弯 曲。在磨床上为消除热变形的影响,而采用弹簧 顶尖。 2) 机床受热变形: 当机床受热不均时,造成机床 部件产生变形。 例如:机床主轴前、后端受热不 均,将造成主轴抬高,并倾斜。 3) 刀具受热变形: 刀具受热以后,引起刀具热伸 长,刀尖位置发生变化,因而影响加工精度。
(二)工艺系统受热变形引起的误差 工艺系统热变形对加工精度的影响比较大,特别 是在精密加工和大件加工中,由热变形所引起的 加工误差有时可占工件总误差的40%~70%。机 床、刀具和工件受到各种热源的作用,温度会逐 渐升高,同时它们也通过各种传热方式向周围的 物质和空间散发热量。当单位时间传入的热量与 其散出的热量相等时,工艺系统就达到了热平衡 状态。 1、工艺系统的热源——内部热源和外部热源 内部 热源:如系统内部的摩擦热(由轴承副、齿轮副 等产生)、切削热等; 外部热源:如外部环境温 度、阳光辐射等。
(2)表层的残余应力
残余应力产生的原因: 1)热态塑性变形,2)金相组织的变化,3)冷态塑性变形 1)影响切削表层残余应力的因素 切削用量影响:进给量↑ ,会使表层金属塑性变形增加,残余应力的数 值及扩展深度相应增大。切削速度 ↑,冷塑性变形↓,热塑性变形↑,金相 组织发生变化的可能性增加. 刀具角度的影响:前角.切削刃钝圆半径、刀具磨损状态. 工件材料的影响:塑性大的材料,切削加工后表面层一般产生残余拉应力 ;脆性材料,表面层产生残余压应力。 磨削用量的影响 : 磨削深度对表面层残余应力的性质、数值有很大影响。 砂轮速度 ↑,表面金属产生拉伸残余应力的倾向增大。 加大工件的回转速度和进给速度 ,表面金属中产生拉伸残余应力的趋势逐 渐减小,而产生压缩残余应力的趋势逐渐增大。 工件材料的影响:工件材料的强度越高、导热性越差、塑性越低,在磨削 时表面金属产生拉伸残余应力的倾向就越大。
加工精度等级

加工精度国家标准规定:常用的精度等级分为20级,分别用IT01、IT0、IT1、IT2……IT18表示。
数字越大,精度越低。
其中IT5- IT12常用。
高精度:IT5、IT6通常由模削加工获得。
中等精度:IT7-IT10通常由精车、铣、刨获得。
低精度:IT11-IT13通常由粗车、铣、刨、钻等加工方法获得。
零件精度等级及其相应的加工方法精度等级尺寸精度范围 Ra值范围(un)相应的加工方法低精度IT13~IT11 25~12.5 粗车、粗镗、粗铣、粗刨、钻孔等中等精度IT10~IT96.3~3.2半精车、半精镗、办精铣、半精刨、扩孔等IT8~IT71.6~0.8 精车、精镗、精铣、精刨、粗磨、粗铰等高精度 IT7~IT6 0.8~0.2 精磨、精铰等特别精密精度IT5~IT2Ra<0.2 研磨、超精加工、抛光、珩磨等表面粗糙度:零件微观表面高低不平的程度。
产生的原因:1)切屑时刀具与工件相对运动产生的摩擦; 2)机床、刀具和工件在加工时的振动;3)切屑时从零件表面撕裂的切屑产生的痕迹; 4)加工时零件表面发生塑性变形;表面粗糙度对零件质量的影响:零件的表面粗糙度对机器零件的性能和使用寿命影响较大,主要有以下几个方面:1)零件表面粗糙,将使接触面积减少,单位面积压力加大,接触变形加大,摩擦阻力增大,磨损加快;2)表面粗糙度影响配合性质。
对于间隙配合,表面粗糙易磨损,造成间隙迅速加大;对于过盈配合,在装配时,可使微小凸峰挤平,有效过盈量减少,使配合件强度降低; 3)零件表面粗糙,低谷处容易聚积腐蚀性物质,且不易消除,造成表面腐蚀; 4)当零件受载荷时,凹谷处易产生应力集中,以致产生裂纹而造成零件断裂。
常见加工方法的Ra表面特征加工方法 Ra(um) 表面特征粗车粗镗粗铣粗刨钻孔 50 可见明显刀痕 25 可见刀痕 12.5 微见刀痕精铣精刨半精车 6.3 可见加工痕迹 3.2 微见加工痕迹精车1.6 看不清加工痕迹粗磨 0.8 可辨加工痕迹方向精磨 0.4 微辨加工痕迹方向精密加工0.1-0.012只能按表面光着辨识。
加工精度概念

加工精度概念
加工精度指的是加工工艺的精准度和精度。
在制造业中,工件的加工精度直接影响着产品的性能和质量。
加工精度包括尺寸精度、形状精度、位置精度和表面粗糙度等方面。
尺寸精度指的是工件的长度、宽度、高度等尺寸的精确度;形状精度指的是工件的平整度、圆度、平行度等形状的精确度;位置精度指的是工件内部各部分之间的位置关系的精确度;表面粗糙度指的是工件表面的光洁度、粗糙度等表面性质的精确度。
加工精度与加工工艺、机床性能、加工材料等因素密切相关。
提高加工精度是制造业不断追求的目标之一。
- 1 -。
- 1、下载文档前请自行甄别文档内容的完整性,平台不提供额外的编辑、内容补充、找答案等附加服务。
- 2、"仅部分预览"的文档,不可在线预览部分如存在完整性等问题,可反馈申请退款(可完整预览的文档不适用该条件!)。
- 3、如文档侵犯您的权益,请联系客服反馈,我们会尽快为您处理(人工客服工作时间:9:00-18:30)。
零件的加工精度包括哪些【详细版】————————————————————————————————作者:————————————————————————————————日期:零件的加工精度包括哪些内容来源网络,由深圳机械展收集整理!更多精密零件加工展示,就在深圳机械展!零件加工精度包括尺寸精度指加工后零件的实际尺寸与零件尺寸的公差带中心的相符合程度。
形状精度指加工后的零件表面的实际几何形状与理想的几何形状的相符合程度。
位置精度指加工后零件有关表面之间的实际位置精度差别。
相互关系通常在设计机器零件及规定零件加工精度时,应注意将形状误差控制在位置公差内,位置误差又应小于尺寸公差。
即精密零件或零件重要表面,其形状精度要求应高于位置精度要求,位置精度要求应高于尺寸精度要求。
加工精度是加工后零件表面的实际尺寸、形状、位置三种几何参数与图纸要求的理想几何参数的符合程度。
理想的几何参数,对尺寸而言,就是平均尺寸;对表面几何形状而言,就是绝对的圆、圆柱、平面、锥面和直线等;对表面之间的相互位置而言,就是绝对的平行、垂直、同轴、对称等。
零件实际几何参数与理想几何参数的偏离数值称为加工误差。
加工精度主要用于生产产品程度,加工精度与加工误差都是评价加工表面几何参数的术语。
加工精度用公差等级衡量,等级值越小,其精度越高;加工误差用数值表示,数值越大,其误差越大。
加工精度高,就是加工误差小,反之亦然。
公差等级从IT01,IT0,IT1,IT2,IT3至IT18一共有20个,其中IT01表示的话该零件加工精度高的,IT18表示的话该零件加工精度是低的。
任何加工方法所得到的实际参数都不会绝对准确,从零件的功能看,只要加工误差在零件图要求的公差范围内,就认为保证了加工精度。
机器的质量取决于零件的加工质量和机器的装配质量,零件加工质量包含零件加工精度和表面质量两大部分。
机械加工精度是指零件加工后的实际几何参数(尺寸、形状和位置)与理想几何参数相符合的程度。
它们之间的差异称为加工误差。
加工误差的大小反映了加工精度的高低。
误差越大加工精度越低,误差越小加工精度越高。
加工精度根据不同的加工精度内容以及精度要求,采用不同的测量方法。
一般来说有以下几类方法:1、按是否直接测量被测参数,可分为直接测量和间接测量。
直接测量:直接测量被测参数来获得被测尺寸。
例如用卡尺、比较仪测量。
间接测量:测量与被测尺寸有关的几何参数,经过计算获得被测尺寸。
显然,直接测量比较直观,间接测量比较繁琐。
一般当被测尺寸或用直接测量达不到精度要求时,就不得不采用间接测量2、按量具量仪的读数值是否直接表示被测尺寸的数值,可分为绝对测量和相对测量。
绝对测量:读数值直接表示被测尺寸的大小、如用游标卡尺测量。
相对测量:读数值只表示被测尺寸相对于标准量的偏差。
如用比较仪测量轴的直径,需先用量块调整好仪器的零位,然后进行测量,测得值是被侧轴的直径相对于量块尺寸的差值,这就是相对测量。
一般说来相对测量的精度比较高些,但测量比较麻烦。
3、按被测表面与量具量仪的测量头是否接触,分为接触测量和非接触测量。
接触测量:测量头与被接触表面接触,并有机械作用的测量力存在。
如用千分尺测量零件。
非接触测量:测量头不与被测零件表面相接触,非接触测量可避免测量力对测量结果的影响。
如利用投影法、光波干涉法测量等。
4、按一次测量参数的多少,分为单项测量和综合测量。
单项测量;对被测零件的每个参数分别单独测量。
综合测量:测量反映零件有关参数的综合指标。
如用工具显微镜测量螺纹时,可分别测量出螺纹实际中径、牙型半角误差和螺距累积误差等。
综合测量一般效率比较高,对保证零件的互换性更为可靠,常用于完工零件的检验。
单项测量能分别确定每一参数的误差,一般用于工艺分析、工序检验及被指定参数的测量。
5、按测量在加工过程中所起的作用,分为主动测量和被动测量。
主动测量:工件在加工过程中进行测量,其结果直接用来控制零件的加工过程,从而及时防治废品的产生。
被动测量:工件加工后进行的测量。
此种测量只能判别加工件是否合格,仅限于发现并剔除废品。
6、按被测零件在测量过程中所处的状态,分为静态测量和动态测量。
静态测量;测量相对静止。
如千分尺测量直径。
动态测量;测量时被测表面与测量头模拟工作状态中作相对运动。
动态测量方法能反映出零件接近使用状态下的情况,是测量技术的发展方向。
调整方法编辑减少传动链传动误差1)传动件数少,传动链短,传动精度高;2)采用降速传动(i<1),是保证传动精度的重要原则,且越接近末端的传动副,其传动比应越小;3)末端件精度应高于其他传动件。
[1]减小刀具磨损在刀具尺寸磨损达到急剧磨损阶段前就必须重新磨刀。
减小工艺系统的受力变形1、提高系统的刚度,特别是提高工艺系统中薄弱环节的刚度;2、减小载荷及其变化3、尽量减少连接面的数目;4、防止有局部低刚度环节出现;5、应合理选择基础件、支撑件的结构和截面形状。
对工艺系统进行调整1、试切法调整通过试切—测量尺寸—调整刀具的吃刀量—走刀切削—再试切,如此反复直至达到所需尺寸。
此法生产效率低,主要用于单件小批生产。
2、调整法通过预先调整好机床、夹具、工件和刀具的相对位置获得所需尺寸。
此法生产率高,主要用于大批大量生产。
减小机床误差1)提高主轴部件的制造精度①选用高精度的滚动轴承;②采用高精度的多油锲动压轴承;③采用高精度的静压轴承2)对滚动轴承适当预紧①可消除间隙;②增加轴承刚度;③均化滚动体误差。
减小工艺系统热变形.①减少热源的发热和隔离热源1)采用较小的切削用量;2)零件精度要求高时,将粗精加工工序分开;3)尽可能将热源从机床分离出去,减少机床热变形;4)对主轴轴承、丝杆螺母副、高速运动的导轨副等不能分离的热源,从结构、润滑等方面改善其摩擦特性,减少发热或用隔热材料;5)采用强制式风冷、水冷等散热措施。
②均衡温度场③采用合理的机床部件结构及装配基准1)采用热对称结构——在变速箱中,将轴、轴承、传动齿轮等对称布置,可使箱壁温升均匀,箱体变形减小;2)合理选择机床零部件的装配基准。
④加速达到传热平衡⑤控制环境温度[2]影响原因编辑机床误差机床误差是指机床的制造误差、安装误差和磨损。
主要包括机床导轨导向误差、机床主轴回转误差、机床传动链的传动误差。
•机床导轨导向误差1、导轨导向精度——导轨副运动件实际运动方向与理想运动方向的符合程度。
主要包括:① 导轨在水平面内直线度Δy和垂直面内的直线度Δz(弯曲);②前后两导轨的平行度(扭曲);③ 导轨对主轴回转轴线在水平面内和垂直面内的平行度误差或垂直度误差。
2.、导轨导向精度对切削加工的影响主要考虑导轨误差引起刀具与工件在误差敏感方向的相对位移。
车削加工时误差敏感方向为水平方向,垂直方向引起的导向误差产生的加工误差可以忽略;镗削加工时误差敏感方向随刀具回转而变化;刨削加工时误差敏感方向为垂直方向,床身导轨在垂直平面内的直线度引起加工表面直线度和平面度误差。
•机床主轴回转误差机床主轴回转误差是指实际回转轴线对于理想回转轴线的漂移。
主要包括主轴端面圆跳动、主轴径向圆跳动、主轴几何轴线倾角摆动。
1、主轴端面圆跳动对加工精度的影响:①加工圆柱面时无影响;②车、镗端面时将产生端面与圆柱面轴线垂直度误差或端面平面度误差;③加工螺纹时,将产生螺距周期误差。
2、主轴径向圆跳动对加工精度的影响:①若径向回转误差表现为其实际轴线在y轴坐标方向上作简谐直线运动,镗床镗出的孔为椭圆形孔,圆度误差为径向圆跳动幅值;而车床车出的孔没什么影响;②若主轴几何轴线作偏心运动,无论车、镗都能得到一个半径为刀尖到平均轴线距离的圆。
3.、主轴几何轴线倾角摆动对加工精度的影响:①几何轴线相对于平均轴线在空间成一定锥角的圆锥轨迹,从各截面看相当于几何轴心绕平均轴心作偏心运动,而从轴向看各处偏心值不同;②几何轴线在某一平面内作摆动,从各截面看相当于实际轴线在一平面内作简谐直线运动,而从轴向看各处跳动幅值不同;③实际上主轴几何轴线的倾角摆动为上述两种的叠加。
[3]•机床传动链的传动误差机床传动链的传动误差是指传动链中首末两端传动元件之间的相对运动误差。
加工原理误差加工原理误差是指采用了近似的刀刃轮廓或近似的传动关系进行加工而产生的误差。
加工原理误差多出现于螺纹、齿轮、复杂曲面加工中。
例如,加工渐开线齿轮用的齿轮滚刀,为使滚刀制造方便,采用了阿基米德基本蜗杆或法向直廓基本蜗杆代替渐开线基本蜗杆,使齿轮渐开线齿形产生了误差。
又如车削模数蜗杆时,由于蜗杆的螺距等于蜗轮的周节(即mπ),其中m是模数,而π是一个无理数,但是车床的配换齿轮的齿数是有限的,选择配换齿轮时只能将π化为近似的分数值(π =3.1415)计算,这就将引起刀具对于工件成形运动(螺旋运动)的不准确,造成螺距误差。
在加工中,一般采用近似加工,在理论误差可以满足加工精度要求的前提下(《=10%-15%尺寸公差),来提高生产率和经济性。
[1]调整误差机床的调整误差是指由于调整不准确而产生的误差。
工件内部的残余应力残余应力的产生:1)毛胚制造和热处理过程中产生的残余应力;2)冷校直带来的残余应力;3)切削加工带来的残余应力。
加工现场环境影响加工现场往往有许多细小金属屑,这些金属屑如果存在与零件定位面或定位孔位置就会影响零件加工精度,对于高精度加工,一些细小到目视不到的金属屑都会影响到精度。
这个影响因素会被识别出来但并无十分到位的方法来杜绝,往往对操作员的作业手法依赖很高。
夹具的制造误差和磨损夹具的误差主要指:1)定位元件、刀具导向元件、分度机构、夹具体等的制造误差;2)夹具装配后,以上各种元件工作面间的相对尺寸误差;3)夹具在使用过程中工作表面的磨损。
刀具的制造误差和磨损刀具误差对加工精度的影响根据刀具的种类不同而异。
1)定尺寸刀具(如钻头、铰刀、键槽铣刀及圆拉刀等)的尺寸精度直接影响工件的尺寸精度。
2)成型刀具(如成型车刀、成型铣刀、成型砂轮等)的形状精度将直接影响工件的形状精度。
3)展成刀具(如齿轮滚刀、花键滚刀、插齿刀具等)的刀刃形状误差会影响加工表面的形状精度。
4)一般刀具(如车刀、镗刀、铣刀),其制造精度对加工精度无直接影响,但刀具易磨损。
[3]工艺系统受力变形工艺系统在切削力、夹紧力、重力和惯性力等作用下会产生变形,从而破坏了已调整好的工艺系统各组成部分的相互位置关系,导致加工误差的产生,并影响加工过程的稳定性。
主要考虑机床变形、工件变形以及工艺系统的总变形。
切削力对加工精度的影响只考虑机床变形,对加工轴类零件来讲,机床受力变形使加工工件呈两端粗、中间细的鞍形,即产生圆柱度误差。
只考虑工件变形,对加工轴类零件来讲,工件受力变形使加工后工件呈两端细、中间粗的鼓形。
而对加工孔类零件来讲,单独考虑机床或工件的变形,加工后工件的形状与加工的轴类零件相反。