图纸技术要求
CAD图纸技术要求
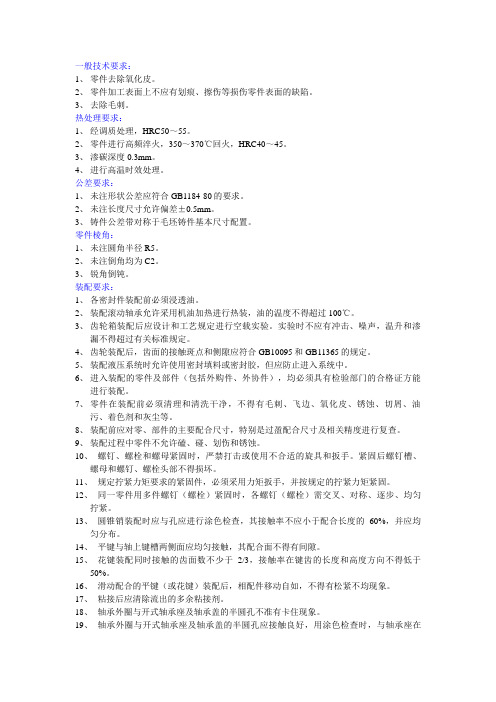
一般技术要求:1、零件去除氧化皮。
2、零件加工表面上不应有划痕、擦伤等损伤零件表面的缺陷。
3、去除毛刺。
热处理要求:1、经调质处理,HRC50~55。
2、零件进行高频淬火,350~370℃回火,HRC40~45。
3、渗碳深度0.3mm。
4、进行高温时效处理。
公差要求:1、未注形状公差应符合GB1184-80的要求。
2、未注长度尺寸允许偏差±0.5mm。
3、铸件公差带对称于毛坯铸件基本尺寸配置。
零件棱角:1、未注圆角半径R5。
2、未注倒角均为C2。
3、锐角倒钝。
装配要求:1、各密封件装配前必须浸透油。
2、装配滚动轴承允许采用机油加热进行热装,油的温度不得超过100℃。
3、齿轮箱装配后应设计和工艺规定进行空载实验。
实验时不应有冲击、噪声,温升和渗漏不得超过有关标准规定。
4、齿轮装配后,齿面的接触斑点和侧隙应符合GB10095和GB11365的规定。
5、装配液压系统时允许使用密封填料或密封胶,但应防止进入系统中。
6、进入装配的零件及部件(包括外购件、外协件),均必须具有检验部门的合格证方能进行装配。
7、零件在装配前必须清理和清洗干净,不得有毛刺、飞边、氧化皮、锈蚀、切屑、油污、着色剂和灰尘等。
8、装配前应对零、部件的主要配合尺寸,特别是过盈配合尺寸及相关精度进行复查。
9、装配过程中零件不允许磕、碰、划伤和锈蚀。
10、螺钉、螺栓和螺母紧固时,严禁打击或使用不合适的旋具和扳手。
紧固后螺钉槽、螺母和螺钉、螺栓头部不得损坏。
11、规定拧紧力矩要求的紧固件,必须采用力矩扳手,并按规定的拧紧力矩紧固。
12、同一零件用多件螺钉(螺栓)紧固时,各螺钉(螺栓)需交叉、对称、逐步、均匀拧紧。
13、圆锥销装配时应与孔应进行涂色检查,其接触率不应小于配合长度的60%,并应均匀分布。
14、平键与轴上键槽两侧面应均匀接触,其配合面不得有间隙。
15、花键装配同时接触的齿面数不少于2/3,接触率在键齿的长度和高度方向不得低于50%。
技术图纸要求

技术图纸要求一.图纸1.图纸图幅应符合国家制图标准允许使用的图幅,其中A4应为竖幅,其他均为横幅;2.图纸应有完整、标准的标题栏,打印时因图纸缩小的标题栏应保证栏内文字清晰;3.每张图纸应有必要的技术要求,根据图纸的性质(装配图、部件图零件图)撰写,内容可包括:技术参数、装配要求(装配工艺、重点、精度)、加工要求(热处理、抛光、喷砂、拉丝、配作、去毛刺、倒角、倒锐、倒棱、焊接、打磨、清渣、清洗、除尘等)、检测、防护、标记、包装、运输等及其他;4.技术要求等文字、字母应清晰、文字简洁、明了,一般选用“四号仿宋字”;技术要求一般置于图纸右下方;5.加工图纸都应有粗糙度要求,有位置、形状要求的应标注形位公差;6.装配图应有基本的外形尺寸及必要的装配尺寸(配合公差等);7.由于技术人员使用的绘图软件未统一,各人所出图纸差异较大,但设计者不能因软件不同而降低图纸质量,在正确、清楚的情况小,应考虑布图美观、合理;8.由于产品以薄板件为主,厚度小,绘图时线条极易重叠,可能会引起误读、造成错误,因此,应尽量用放大、剖面、局部视图等手段,保证图纸质量;9.成台产品图纸标题栏内的设计、审核、批准栏的签名必须完整(姓名、日期),一般图纸必须有设计、审核签名;10.图纸必须加盖“受控”章才可下发,有“受控”章图纸只发一份至生产部(见附表:图纸发放记录表),其他用图(外协、检验等)只能“复制”;11.成套产品必须有《零件明细表》、《外购件明细表》,在图纸下发时一起提供生产部(加盖“受控”章)。
因生产需要,《外购件明细表》可以提前下发或分几次下发,但最后必须整理成正式技术文件存档;12.结构简单、图纸上明细表清楚的产品,单件产品和没有外购件的产品可以不出《零件明细表》、《外购件明细表》。
二.图纸的更正、更换1. 图纸下发后,其他部门或职工发现或指出的错误,应及时更正。
根据图纸错误程度,可采取换图或原图上改正的办法,一般由设计者决定,更换的图纸必须收回,原图上改正必须由设计者在改正处签名;2. 图纸下发后,其他部门或职工提出的异议,应耐心听取、了解并及时处理,重要的可开会进行专门讨论决定;3. 图纸更正、更换应及时与各部门相关人员沟通,同时将更正、更换情况及时输入电子文档,作好记录。
图纸技术要求文本
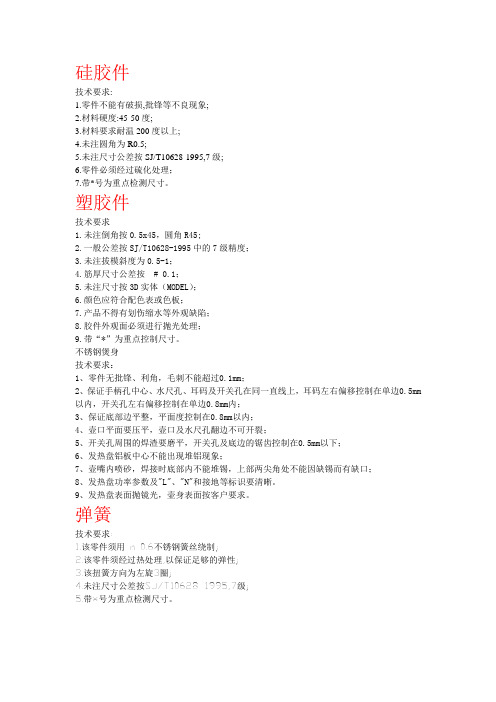
硅胶件技术要求:1.零件不能有破损,批锋等不良现象;2.材料硬度:45-50度;3.材料要求耐温200度以上;4.未注圆角为R0.5;5.未注尺寸公差按SJ/T10628-1995,7级;6.零件必须经过硫化处理;7.带*号为重点检测尺寸。
塑胶件技术要求1.未注倒角按0.5x45,圆角R45;2.一般公差按SJ/T10628-1995中的7级精度;3.未注拔模斜度为0.5-1;4.筋厚尺寸公差按#0.1;5.未注尺寸按3D实体(MODEL);6.颜色应符合配色表或色板;7.产品不得有划伤缩水等外观缺陷;8.胶件外观面必须进行抛光处理;9.带“*”为重点控制尺寸。
不锈钢煲身技术要求:1、零件无批锋、利角,毛刺不能超过0.1mm;2、保证手柄孔中心、水尺孔、耳码及开关孔在同一直线上,耳码左右偏移控制在单边0.5mm 以内,开关孔左右偏移控制在单边0.8mm内;3、保证底部边平整,平面度控制在0.8mm以内;4、壶口平面要压平,壶口及水尺孔翻边不可开裂;5、开关孔周围的焊渣要磨平,开关孔及底边的锯齿控制在0.5mm以下;6、发热盘铝板中心不能出现堆铝现象;7、壶嘴内喷砂,焊接时底部内不能堆锡,上部两尖角处不能因缺锡而有缺口;8、发热盘功率参数及"L"、"N"和接地等标识要清晰。
9、发热盘表面抛镜光,壶身表面按客户要求。
弹簧技术要求:1.该零件须用n0.6不锈钢簧丝绕制;2.该零件须经过热处理,以保证足够的弹性;3.该扭簧方向为左旋3圈;4.未注尺寸公差按SJ/T10628-1995,7级;5.带*号为重点检测尺寸。
图纸技术要求

图纸技术要求(冷轧板喷涂件图纸技术要求)1.基础材料性能应符合:JIS G3141-2005《冷轧碳素薄钢板和钢带》的要求,制件特性应符合JB/T 4378.2-1999《金属冷冲压件通用技术条件》相应图纸技术要求(除外观);2.喷涂件涂层性能应符合GB/T21776-2008《粉末涂料及其涂层的检测标准指南》的要求;3.未注冲裁圆角为R2.0,未注弯曲内圆角为R0.5;4.未注尺寸公差应符合GB/T13914《冲压件尺寸公差》(6)级要求;5.外观颜色应符合公司规定的色板编号及颜色名称的要求,并符合色板要求;图纸技术要求(镀锌板非喷涂件)1.电镀锌板材料性能应符合GB/T15675-2008《连续电镀锌、锌镍合金镀层钢板及钢带》的要求;2.未注冲裁圆角为R2.0,未注弯曲内圆角为R0.5;3.未注尺寸公差应符合GB/T 13914《冲压件尺寸公差》(6)级要求;图纸技术要求(弯曲配管的技术要求)1.配管材料应符合GB 1527-2006《铜及铜合金拉制管》的要求;2.未注直线和角度尺寸公差应分别符合GB/T1804-c和GB/T1804-v;3.未注弯曲半径R= ,弯曲处压扁率<15%;4.成品应用塑料包装袋封装,并能防尘、防潮;5.弯曲配管在加工过程中只允许使用不含氯元素的挥发油、脂润滑油或碱性清洗剂;清洗时不能让其接触到带氯元素的清洗剂(如盐酸等);图纸技术要求(直配管)1.配管材料应符合GB 1527-2006《铜及铜合金拉制管》的要求;2.未注直线尺寸公差应符合GB/T1804-c;3.成品应用塑料包装袋封装,并能防尘、防潮;4.直配管在加工过程中只允许使用不含氯元素的挥发油、脂润滑油或碱性清洗剂;清洗时不能让其接触到带氯元素的清洗剂(如盐酸等);图纸技术要求(高、低压阀组件)1.焊接时,有定位的以定位点为插入深度限制点、无定位的以扩(缩)口限位为插入深度进行焊接;2.各焊口应光滑,无虚焊、漏焊、焊堵等缺陷;3.组件焊好后,不得有明显变形、弯曲,应满足图纸中装配尺寸要求;4.未注直线和角度尺寸公差应分别符合GB/T1804-c和GB/T1804-v;5.焊接时,必须将高、低压阀需保护部分放置在水箱中,并完全浸没在50℃以下水中(直观感觉是手能放进水中不感觉到烫)才能焊接接口,焊接完的阀体必须在水中停留3-5秒钟,保证阀体不烫手;6.成品应干燥后使用塑料包装袋封装,并能防尘、防潮;7.图示箭头方向为单向阀导通方向;(仅适用有单向阀的组件)8.所有管类零件,在加工过程中,不能让其接触到带氯元素的材料(如盐酸等);图纸技术要求(普通管路焊接)1.焊接时,有定位的以定位点为插入深度限制点、无定位的以扩(缩)口限位为插入深度进行焊接;并且充氮保护;2.各焊口应光滑,无虚焊、漏焊、焊堵等缺陷;3.配管焊接完毕后,允许整形,但不得有明显变形、弯曲,应满足图纸中装配尺寸要求;4.未注直线和角度尺寸公差应分别符合GB/T1804-c和GB/T1804-v;5.成品应使用塑料包装袋封装,并能防尘、防潮;6.所有管类零件,在加工过程中,不能让其接触到带氯元素的材料(如盐酸等);图纸技术要求(总装图纸技术要求)1.各零件、部件应安装牢固,焊接时以扩(缩)口或定位点限位为插入深度, 并且要充氮保护;2.各零件、部件的焊口应无泄漏、虚焊、焊堵等现象;3.各零件、部件之间整形后或采取设计要求的防护措施(如管件间增加橡胶垫、防振胶、软质PVC等)后无互相碰撞、摩擦等缺陷;4.系统的冷媒泄漏量不大于2克/年;5.焊接时应确保配管与焊接管口的同轴度,配管焊接完毕后,允许整形,但各零部件不得有明显变形、弯曲;且满足制冷系统总图的方向;6.所有管类零件在装配过程中,不能让其接触到带氯元素的材料(如盐酸等);7.所有管类零件在装配过程前必须检验,与图纸不符的所有管类零件不得上线生产;8.配重块和防振胶必须按照图纸标注的尺寸和角度装配;9.该机组执行的标准GB/T 21363-2008。
图纸技术要求大全
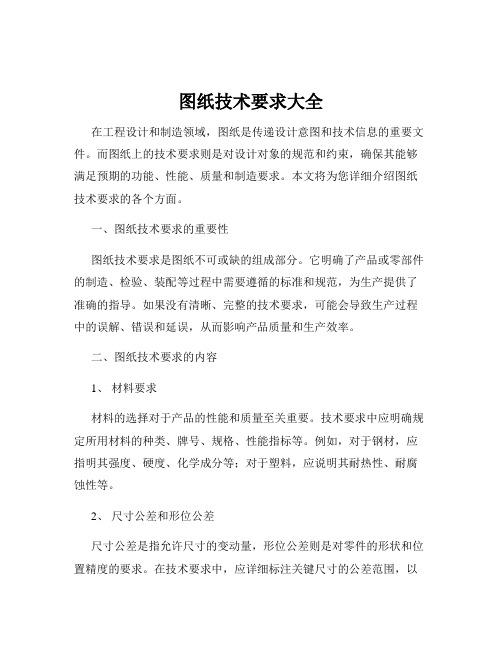
图纸技术要求大全在工程设计和制造领域,图纸是传递设计意图和技术信息的重要文件。
而图纸上的技术要求则是对设计对象的规范和约束,确保其能够满足预期的功能、性能、质量和制造要求。
本文将为您详细介绍图纸技术要求的各个方面。
一、图纸技术要求的重要性图纸技术要求是图纸不可或缺的组成部分。
它明确了产品或零部件的制造、检验、装配等过程中需要遵循的标准和规范,为生产提供了准确的指导。
如果没有清晰、完整的技术要求,可能会导致生产过程中的误解、错误和延误,从而影响产品质量和生产效率。
二、图纸技术要求的内容1、材料要求材料的选择对于产品的性能和质量至关重要。
技术要求中应明确规定所用材料的种类、牌号、规格、性能指标等。
例如,对于钢材,应指明其强度、硬度、化学成分等;对于塑料,应说明其耐热性、耐腐蚀性等。
2、尺寸公差和形位公差尺寸公差是指允许尺寸的变动量,形位公差则是对零件的形状和位置精度的要求。
在技术要求中,应详细标注关键尺寸的公差范围,以及形状(如平面度、圆度)和位置(如平行度、垂直度)的公差要求。
这有助于保证零件之间的配合精度和装配质量。
3、表面质量要求表面质量直接影响产品的外观、耐磨性和耐腐蚀性等。
技术要求中应规定表面粗糙度、表面处理方式(如电镀、喷漆)以及表面缺陷的允许程度。
4、热处理要求对于需要进行热处理的零件,应明确热处理的类型(如淬火、回火、退火)、工艺参数(如温度、时间)以及处理后的性能指标。
5、加工工艺要求这包括加工方法(如车削、铣削、磨削)、加工顺序、切削参数等。
此外,对于一些特殊的加工工艺,如焊接、铸造、锻造等,也应给出相应的技术要求。
6、装配要求如果是装配图,应规定零部件的装配顺序、配合要求、紧固力矩等,以确保装配的正确性和可靠性。
7、检验要求明确检验的方法、量具、检验项目和验收标准。
这有助于保证产品在生产过程中的质量控制。
8、包装和标识要求说明产品的包装方式、防护措施以及标识内容(如产品名称、型号、批次、生产日期等),以便于产品的储存、运输和识别。
加工图纸中的技术要求大全
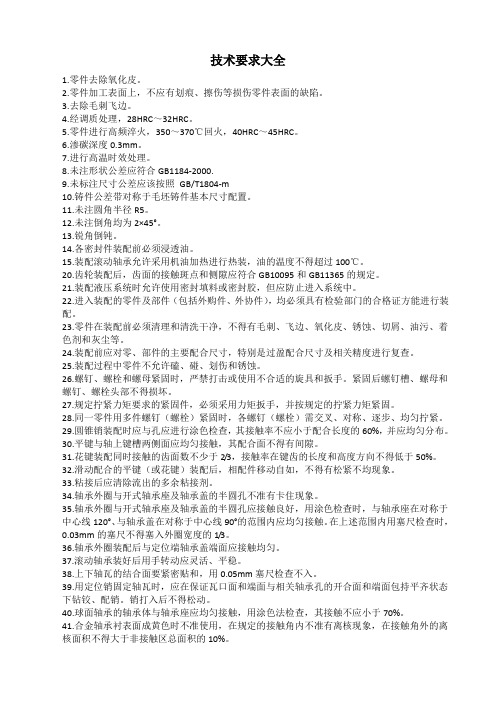
技术要求大全1.零件去除氧化皮。
2.零件加工表面上,不应有划痕、擦伤等损伤零件表面的缺陷。
3.去除毛刺飞边。
4.经调质处理,28HRC~32HRC。
5.零件进行高频淬火,350~370℃回火,40HRC~45HRC。
6.渗碳深度0.3mm。
7.进行高温时效处理。
8.未注形状公差应符合GB1184-2000.9.未标注尺寸公差应该按照GB/T1804-m10.铸件公差带对称于毛坯铸件基本尺寸配置。
11.未注圆角半径R5。
12.未注倒角均为2×45°。
13.锐角倒钝。
14.各密封件装配前必须浸透油。
15.装配滚动轴承允许采用机油加热进行热装,油的温度不得超过100℃。
20.齿轮装配后,齿面的接触斑点和侧隙应符合GB10095和GB11365的规定。
21.装配液压系统时允许使用密封填料或密封胶,但应防止进入系统中。
22.进入装配的零件及部件(包括外购件、外协件),均必须具有检验部门的合格证方能进行装配。
23.零件在装配前必须清理和清洗干净,不得有毛刺、飞边、氧化皮、锈蚀、切屑、油污、着色剂和灰尘等。
24.装配前应对零、部件的主要配合尺寸,特别是过盈配合尺寸及相关精度进行复查。
25.装配过程中零件不允许磕、碰、划伤和锈蚀。
26.螺钉、螺栓和螺母紧固时,严禁打击或使用不合适的旋具和扳手。
紧固后螺钉槽、螺母和螺钉、螺栓头部不得损坏。
27.规定拧紧力矩要求的紧固件,必须采用力矩扳手,并按规定的拧紧力矩紧固。
28.同一零件用多件螺钉(螺栓)紧固时,各螺钉(螺栓)需交叉、对称、逐步、均匀拧紧。
29.圆锥销装配时应与孔应进行涂色检查,其接触率不应小于配合长度的60%,并应均匀分布。
30.平键与轴上键槽两侧面应均匀接触,其配合面不得有间隙。
31.花键装配同时接触的齿面数不少于2/3,接触率在键齿的长度和高度方向不得低于50%。
32.滑动配合的平键(或花键)装配后,相配件移动自如,不得有松紧不均现象。
图纸技术要求大全

图纸技术要求大全在工程和制造领域,图纸是至关重要的沟通工具,它能够清晰地传达设计意图和规范,确保产品或项目的顺利实施。
而图纸上的技术要求则是对设计的进一步补充和说明,为生产、加工、检验等环节提供了明确的指导。
下面我们就来详细了解一下图纸技术要求的方方面面。
一、尺寸与公差要求尺寸是图纸中最基本的元素之一,它准确地描述了零件或结构的大小和形状。
在标注尺寸时,需要遵循一定的标准和规范,确保尺寸的清晰、准确和完整。
同时,为了保证零件在制造过程中的互换性和功能性,还需要规定公差。
公差是允许尺寸的变动量,分为尺寸公差和形位公差。
尺寸公差控制零件的尺寸精度,形位公差则控制零件的形状和位置精度。
例如,对于一个圆柱形零件,不仅要规定其直径的尺寸和公差,还要规定圆柱度、同轴度等形位公差要求。
二、材料要求材料的选择直接影响到产品的性能、质量和成本。
在图纸技术要求中,需要明确指定所使用的材料种类、牌号、规格等信息。
例如,对于机械零件,可以指定使用 45 号钢、铝合金等材料,并注明其热处理要求,如淬火、回火等。
对于建筑结构,可能会指定使用混凝土的强度等级、钢材的型号等。
此外,还需要考虑材料的供应情况和成本,选择合适的替代材料方案。
三、表面处理要求表面处理可以提高零件的耐腐蚀性、耐磨性、美观度等性能。
常见的表面处理方法包括电镀、喷涂、氧化等。
在图纸技术要求中,需要明确表面处理的种类、工艺要求和质量标准。
例如,对于需要防锈的零件,可以要求进行镀锌处理,并规定镀层的厚度和质量要求。
对于外观要求较高的零件,可以进行喷漆处理,并指定漆的颜色、光泽度等要求。
四、加工工艺要求加工工艺是将原材料转化为成品的过程,它直接影响到产品的质量和生产效率。
在图纸技术要求中,需要根据零件的结构和功能,规定合理的加工工艺方法和顺序。
例如,对于一个复杂的零件,可能需要先进行铸造或锻造,然后再进行机械加工。
对于有精度要求的孔和轴,可能需要采用磨削加工工艺。
图纸上的技术要求汇总【模板范本】
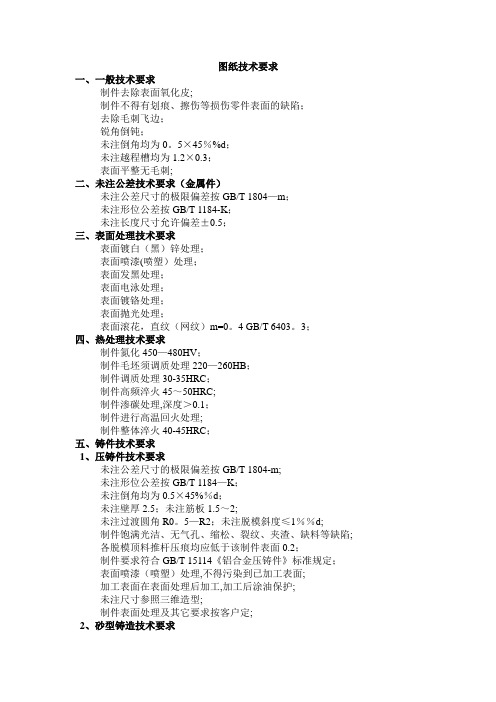
图纸技术要求一、一般技术要求制件去除表面氧化皮;制件不得有划痕、擦伤等损伤零件表面的缺陷;去除毛刺飞边;锐角倒钝;未注倒角均为0。
5×45%%d;未注越程槽均为1.2×0.3;表面平整无毛刺;二、未注公差技术要求(金属件)未注公差尺寸的极限偏差按GB/T 1804—m;未注形位公差按GB/T 1184-K;未注长度尺寸允许偏差±0.5;三、表面处理技术要求表面镀白(黑)锌处理;表面喷漆(喷塑)处理;表面发黑处理;表面电泳处理;表面镀铬处理;表面抛光处理;表面滚花,直纹(网纹)m=0。
4 GB/T 6403。
3;四、热处理技术要求制件氮化450—480HV;制件毛坯须调质处理220—260HB;制件调质处理30-35HRC;制件高频淬火45~50HRC;制件渗碳处理,深度>0.1;制件进行高温回火处理;制件整体淬火40-45HRC;五、铸件技术要求1、压铸件技术要求未注公差尺寸的极限偏差按GB/T 1804-m;未注形位公差按GB/T 1184—K;未注倒角均为0.5×45%%d;未注壁厚2.5;未注筋板1.5~2;未注过渡圆角R0。
5—R2;未注脱模斜度≤1%%d;制件饱满光洁、无气孔、缩松、裂纹、夹渣、缺料等缺陷;各脱模顶料推杆压痕均应低于该制件表面0.2;制件要求符合GB/T 15114《铝合金压铸件》标准规定;表面喷漆(喷塑)处理,不得污染到已加工表面;加工表面在表面处理后加工,加工后涂油保护;未注尺寸参照三维造型;制件表面处理及其它要求按客户定;2、砂型铸造技术要求未注铸造圆角R5-10;铸件应彻底清砂,浇冒口应清除平整;铸件需人工时效;铸件不得有砂眼、气孔、缩松、裂纹等缺陷;粗加工后应再次进行人工时效;不加工表面涂底漆;六、冲压件技术要求制件未注公差尺寸的极限偏差按GB/T 15055—m;制件未注形位公差按GB/T 13916-2级;制件不得有裂纹或缺损;制件表面平整,不得有沟痕、碰伤等损坏表面,降低强度及寿命的缺陷;去除边角毛刺;表面处理:七、塑料件技术要求未注公差尺寸的极限偏差按GB/T 14486—MT6级;制件应饱满光整、色泽均匀;无缩痕、裂纹、银丝等缺陷;浇口、溢边修剪后飞边≤0.3,且不得伤及本体;未注壁厚3;未注筋板1。
图纸通用技术要求
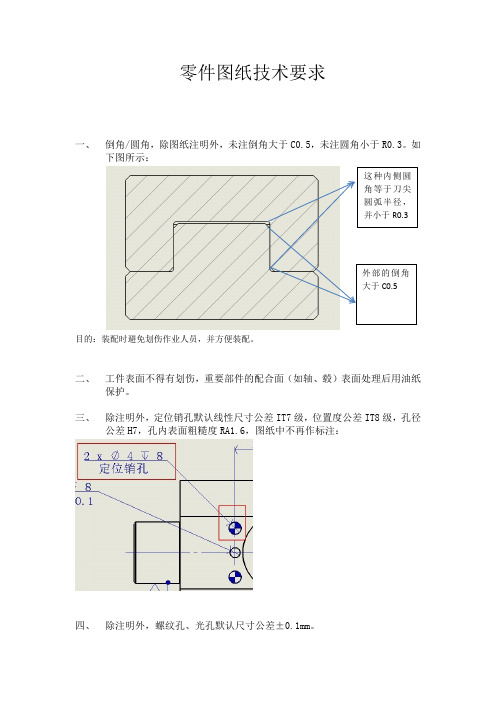
零件图纸技术要求
一、倒角/圆角,除图纸注明外,未注倒角大于C0.5,未注圆角小于R0.3。
如
下图所示:
目的:装配时避免划伤作业人员,并方便装配。
二、工件表面不得有划伤,重要部件的配合面(如轴、毂)表面处理后用油纸
保护。
三、除注明外,定位销孔默认线性尺寸公差IT7级,位置度公差IT8级,孔径
公差H7,孔内表面粗糙度RA1.6,图纸中不再作标注:
四、除注明外,螺纹孔、光孔默认尺寸公差±0.1mm。
这种内侧圆
角等于刀尖
圆弧半径,
并小于R0.3
外部的倒角
大于C0.5
五、使用孔表的图纸(见下图),默认线性尺寸公差IT8级,位置度公差IT9级,孔径公差H8,孔内表面粗糙度RA3.2。
图纸中不再作标注。
六、零件出厂前应自检,合格后再发货。
发货前清除干净碎屑、毛刺等杂物,做到零件表面整洁美观。
七、机加零件涂油防锈,精密面采用油纸、纱网保护防止划伤,钣金零件不得多个叠放防止挤压变形。
钣金件喷涂、镀层前应注意螺纹保护。
塑胶制品防止挤压开裂、变形。
八、螺纹孔、光孔配合面必须倒角去毛刺。
倒角C0.3-C0.5
九、加工图纸必须随零件返回,即供应商送货零件必须附有图纸。
十、未注尺寸公差GB/T1804-2000-M;
未注形位公差GB/T1184-1996-K.。
图纸上的技术要求汇总

图纸技术要求一、一般技术要求制件去除表面氧化皮;制件不得有划痕、擦伤等损伤零件表面的缺陷;去除毛刺飞边;锐角倒钝;未注倒角均为0.5×45%%d;未注越程槽均为1.2×0.3;表面平整无毛刺;二、未注公差技术要求(金属件)未注公差尺寸的极限偏差按GB/T 1804-m;未注形位公差按GB/T 1184-K;未注长度尺寸允许偏差±0.5;三、表面处理技术要求表面镀白(黑)锌处理;表面喷漆(喷塑)处理;表面发黑处理;表面电泳处理;表面镀铬处理;表面抛光处理;表面滚花,直纹(网纹)m=0.4 GB/T 6403.3;四、热处理技术要求制件氮化450-480HV;制件毛坯须调质处理220-260HB;制件调质处理30-35HRC;制件高频淬火45~50HRC;制件渗碳处理,深度>0.1;制件进行高温回火处理;制件整体淬火40-45HRC;五、铸件技术要求1、压铸件技术要求未注公差尺寸的极限偏差按GB/T 1804-m;未注形位公差按GB/T 1184-K;未注倒角均为0.5×45%%d;未注壁厚2.5;未注筋板1.5~2;未注过渡圆角R0.5-R2;未注脱模斜度≤1%%d;制件饱满光洁、无气孔、缩松、裂纹、夹渣、缺料等缺陷;各脱模顶料推杆压痕均应低于该制件表面0.2;制件要求符合GB/T 15114《铝合金压铸件》标准规定;表面喷漆(喷塑)处理,不得污染到已加工表面;加工表面在表面处理后加工,加工后涂油保护;未注尺寸参照三维造型;制件表面处理及其它要求按客户定;2、砂型铸造技术要求未注铸造圆角R5-10;铸件应彻底清砂,浇冒口应清除平整;铸件需人工时效;铸件不得有砂眼、气孔、缩松、裂纹等缺陷;粗加工后应再次进行人工时效;不加工表面涂底漆;六、冲压件技术要求制件未注公差尺寸的极限偏差按GB/T 15055-m;制件未注形位公差按GB/T 13916-2级;制件不得有裂纹或缺损;制件表面平整,不得有沟痕、碰伤等损坏表面,降低强度及寿命的缺陷;去除边角毛刺;表面处理:七、塑料件技术要求未注公差尺寸的极限偏差按GB/T 14486-MT6级;制件应饱满光整、色泽均匀;无缩痕、裂纹、银丝等缺陷;浇口、溢边修剪后飞边≤0.3,且不得伤及本体;未注壁厚3;未注筋板1.5~2;表面打光(喷砂)处理;未注过渡圆角取R0.3~R1,脱模斜度≤0.3%%d;各脱模顶料推杆压痕均应低于该制件表面0.2;与对应装配结合面外形配合错位≤0.5;制件应进行时效处理;制件机械强度须符合GB 3883.1标准规定;制件内腔表面打上材料标记和回收标志;未注尺寸参照三维造型;制件表面处理及其它要求由客户定;八、焊接件技术要求未注公差线性及角度尺寸的极限偏差均按GB/T 19804-B级;未注形位公差按GB/T 19804-F级;焊缝应均匀平整,焊渣清理干净;焊缝应焊透,不得烧穿及产生裂纹等影响机械性能的缺陷;九、各类零、部件技术要求1、齿轮(齿轴)技术要求未注公差尺寸的极限偏差按GB/T 1804-m;未注形位公差按GB/T 1184-K;制件毛坯须调质220~260HB;制件材料的化学成分和力学性能应符合GB/T 3077的规定;齿面接触斑点:按齿高不小于40%,按齿长不小于50%;齿面高频淬火回火至49-52HRC;制件表面不应有锈迹、裂纹、灼伤等影响使用寿命的伤痕及缺陷;最终工序热处理表面不得有氧化皮;2、一般轴芯(无铣齿)技术要求未注公差尺寸的极限偏差按GB/T 1804-m;未注形位公差按GB/T 1184-K;未注倒角均为0.5×45%%d;未注越程槽均为1.2×0.3;制件毛坯须调质220~260HB;尺寸%%c 档车正反两条螺旋槽,螺距10,深0.4;螺纹表面不允许有磕碰、乱扣、毛刺等缺陷;热处理:表面处理:3、包轴毛坯(一次成型)技术要求未注公差尺寸的极限偏差按GB/T 1804-m;未注形位公差按GB/T 1184-K;绝缘层应饱满光洁,无裂纹、气孔、缺料、杂质等缺陷;包轴毛坯:绝缘层%%c 档(注:指冲片配合档)与轴芯间应能承受50Hz,实际正弦波电压2500V历时1min不击穿,其余绝缘层档3750V历时1min不击穿;一次成型:铁芯与轴芯间应能承受50Hz,实际正弦波电压2500V历时1min不击穿,其余绝缘层档3750V历时1min不击穿;4、包轴(加工)技术要求未注公差尺寸的极限偏差按GB/T 1804-m;未注形位公差按GB/T 1184-K;塑层应饱满光洁,无裂纹、气孔、缺料、杂质等缺陷;塑层%%c 档(注:指冲片配合档)与轴芯间应能承受50Hz,实际正弦波电压2500V历时1min不击穿,其余塑层档3750V历时1min不击穿;制件磨加工后应烘干除水处理;5、转子技术要求未注公差尺寸的极限偏差按GB/T 1804-m;未注形位公差按GB/T 1184-K;绕组接线按转子绕线原理图;绕组绝缘漆应均匀充满绕组并充分固化,漆膜应均匀无气泡或裂痕;云母槽开深0.8~1,槽宽0.6,槽内不得残留云母片;绕组冷态绝缘电阻不低于50MΩ;装风叶后校动平衡,其精度应不低于G6.3级;去重不允许有冲片铣穿、残缺现象;铁芯外圆不加工,绝缘漆不得高出铁芯外圆,并不得有明显积瘤;铁芯与轴芯间应能承受50Hz,实际正弦波电压2500V,1min不击穿;绕组与铁芯间应能承受50Hz,实际正弦波电压1250V,1min不击穿;匝间绝缘应能承受1000Hz,峰值为2100V,历时3s不击穿;换向器与轴芯间应能承受50Hz,实际正弦波电压3750V,1min不击穿;应去除铁屑、铜粉、油污等杂质;铁芯外圆应涂透明淡金水防锈处理;6、定子技术要求绕组绕制整齐无松散;引线接头应牢固可靠且充分绝缘;绕组与铁芯间应能承受50Hz,实际正弦波电压1250V历时1min不击穿;匝间绝缘应能承受1000Hz,峰值为2100V,历时3s不击穿;绕组绝缘漆应均匀充满绕组并充分固化,漆膜应均匀无气泡或积瘤;铁芯表面不得有明显绝缘漆;7、定、转子铁芯技术要求未注公差尺寸的极限偏差按GB/T 1804-m;未注形位公差按GB/T 1184-K;冲片叠装应紧密可靠,片间无夹杂,表面及槽内无污物和油渍;冲片按同一冲制方向压装;冲片齿槽口整齐与转轴平行,误差不大于0.5;铁芯两端弹开度不大于0.5;8、定、转子冲片技术要求制件未注公差尺寸的极限偏差按GB/T 15055-m;制件未注形位公差按GB/T 13916-2级;制件应表面平整,完整无缺料;尖角处允许用R0.3过渡;制件毛刺不大于0.05(注:高速冲时不大于0.02);制件应不含油脂,剪切油不能用机油;9、绝缘纸技术要求表面不得有划痕、折痕;裁边不起毛;10、换向器技术要求未注公差尺寸的极限偏差按GB/T 1804-m;未注形位公差按GB/T 1184-K;外观完整,表面光滑,应无裂纹、毛刺、锈蚀、气孔、夹杂等缺陷;绝缘电阻:室温下内孔与换向片之间大于50MΩ;云母片厚度取0.5;换向片对换向器轴线偏斜度不大于云母片厚度的1/3;介电强度:片间承受频率50Hz,泄露电流为0.1mA,实际正弦波电压600V历时1s不击穿;换向片与内孔轴芯间承受频率50Hz,泄露电流为0.25mA,实际正弦波电压3750V历时1min不击穿;试验与检验应符合JB/T 10107《电动工具换向器》标准要求;11、电缆线技术要求电缆线长度尺寸指工具电缆出口至插头的导线部分,不包括插头和插脚;软电缆应符合GB/T 5013《额定电压450V/750V及以下橡皮绝缘电缆》标准要求;聚氯乙烯电缆应符合GB/T 5023《额定电压450V/750V及以下聚氯乙烯绝缘电缆》标准要求;插脚与可触及插头表面的绝缘应能承受50Hz,实际正弦波电压3750V历时1min不击穿;制件还应符合GB 1002《家用和类似用途单相插头插座型式、基本参数和尺寸》和GB 2099《家用和类似用途插头插座》标准要求;12、开关技术要求未注公差尺寸的极限偏差按SJ/T 10628-7级;除本图要求的外形尺寸、功能、图形、文字外,试验和检验均应符合GB/T22692《电动工具开关》标准要求;开关的使用性能应保证5万次无故障正常使用;13、电缆护套技术要求未注公差尺寸的极限偏差按GB/T 3672.1-2级;未注形位公差按GB/T 3672.2-M级;制件不得有缺料、破裂等缺陷。
图纸一般技术要求
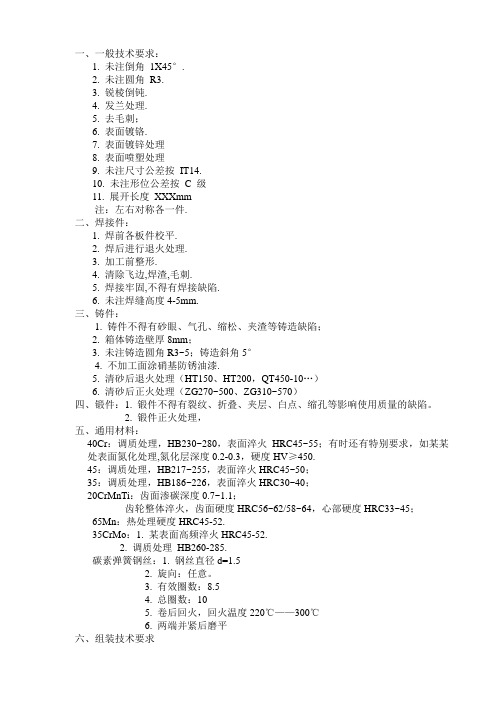
一、一般技术要求:1. 未注倒角1X45°.2. 未注圆角R3.3. 锐棱倒钝.4. 发兰处理.5. 去毛刺;6. 表面镀铬.7. 表面镀锌处理8. 表面喷塑处理9. 未注尺寸公差按IT14.10. 未注形位公差按C 级11. 展开长度XXXmm注:左右对称各一件.二、焊接件:1. 焊前各板件校平.2. 焊后进行退火处理.3. 加工前整形.4. 清除飞边,焊渣,毛刺.5. 焊接牢固,不得有焊接缺陷.6. 未注焊缝高度4-5mm.三、铸件:1. 铸件不得有砂眼、气孔、缩松、夹渣等铸造缺陷;2. 箱体铸造壁厚8mm;3. 未注铸造圆角R3~5;铸造斜角5°4. 不加工面涂硝基防锈油漆.5. 清砂后退火处理(HT150、HT200,QT450-10…)6. 清砂后正火处理(ZG270~500、ZG310~570)四、锻件:1. 锻件不得有裂纹、折叠、夹层、白点、缩孔等影响使用质量的缺陷。
2. 锻件正火处理,五、通用材料:40Cr:调质处理,HB230~280,表面淬火HRC45~55;有时还有特别要求,如某某处表面氮化处理,氮化层深度0.2-0.3,硬度HV≥450.45:调质处理,HB217~255,表面淬火HRC45~50;35:调质处理,HB186~226,表面淬火HRC30~40;20CrMnTi:齿面渗碳深度0.7~1.1;齿轮整体淬火,齿面硬度HRC56~62/58~64,心部硬度HRC33~45;65Mn:热处理硬度HRC45-52.35CrMo:1. 某表面高频淬火HRC45-52.2. 调质处理HB260-285.碳素弹簧钢丝:1. 钢丝直径d=1.52. 旋向:任意。
3. 有效圈数:8.54. 总圈数:105. 卷后回火,回火温度220℃——300℃6. 两端并紧后磨平六、组装技术要求1. 组装前将箱体、各零件清洗干净.2. 组装端盖前应在端盖根部均匀涂抹密封胶;/各密封接合面及纸垫应保持清洁无油,涂密封铰,钻通的螺孔,其螺栓应粘附厌氧胶后拧紧,确保无渗油3. 组装完成后注入升油.4. 组装后应检查图示装配尺寸XX、XX、XX、XX,合格后方可进行总装.5. 轴转动灵活无卡阻,操作手柄准确无误七、焊接箱体技术要求:1. 未注焊缝均为角焊缝K=5-7mm2. 焊缝应密封可靠;3. 组焊后整形并退火处理;4. 焊后焊缝应打磨光滑;5. 全部棱角到角2X45%°;6. 组装前箱内应除锈清渣,并涂耐油防锈漆;7. 螺孔不得钻穿,以免漏油。
图纸技术要求大全
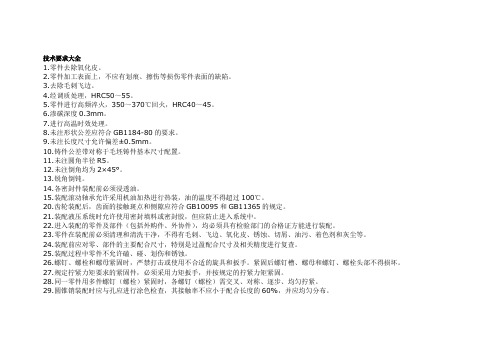
技术要求大全1.零件去除氧化皮。
2.零件加工表面上,不应有划痕、擦伤等损伤零件表面的缺陷。
3.去除毛刺飞边。
4.经调质处理,HRC50~55。
5.零件进行高频淬火,350~370℃回火,HRC40~45。
6.渗碳深度0.3mm。
7.进行高温时效处理。
8.未注形状公差应符合GB1184-80的要求。
9.未注长度尺寸允许偏差±0.5mm。
10.铸件公差带对称于毛坯铸件基本尺寸配置。
11.未注圆角半径R5。
12.未注倒角均为2×45°。
13.锐角倒钝。
14.各密封件装配前必须浸透油。
15.装配滚动轴承允许采用机油加热进行热装,油的温度不得超过100℃。
20.齿轮装配后,齿面的接触斑点和侧隙应符合GB10095和GB11365的规定。
21.装配液压系统时允许使用密封填料或密封胶,但应防止进入系统中。
22.进入装配的零件及部件(包括外购件、外协件),均必须具有检验部门的合格证方能进行装配。
23.零件在装配前必须清理和清洗干净,不得有毛刺、飞边、氧化皮、锈蚀、切屑、油污、着色剂和灰尘等。
24.装配前应对零、部件的主要配合尺寸,特别是过盈配合尺寸及相关精度进行复查。
25.装配过程中零件不允许磕、碰、划伤和锈蚀。
26.螺钉、螺栓和螺母紧固时,严禁打击或使用不合适的旋具和扳手。
紧固后螺钉槽、螺母和螺钉、螺栓头部不得损坏。
27.规定拧紧力矩要求的紧固件,必须采用力矩扳手,并按规定的拧紧力矩紧固。
28.同一零件用多件螺钉(螺栓)紧固时,各螺钉(螺栓)需交叉、对称、逐步、均匀拧紧。
29.圆锥销装配时应与孔应进行涂色检查,其接触率不应小于配合长度的60%,并应均匀分布。
30.平键与轴上键槽两侧面应均匀接触,其配合面不得有间隙。
31.花键装配同时接触的齿面数不少于2/3,接触率在键齿的长度和高度方向不得低于50%。
32.滑动配合的平键(或花键)装配后,相配件移动自如,不得有松紧不均现象。
33.粘接后应清除流出的多余粘接剂。
图纸上的技术要求汇总
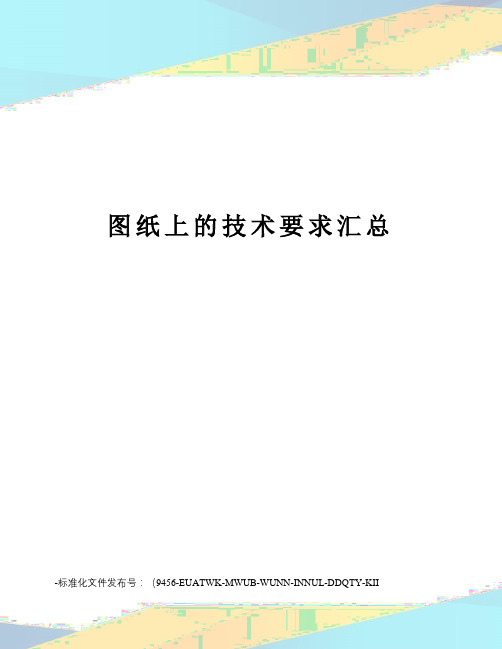
图纸上的技术要求汇总-标准化文件发布号:(9456-EUATWK-MWUB-WUNN-INNUL-DDQTY-KII图纸技术要求一、一般技术要求制件去除表面氧化皮;制件不得有划痕、擦伤等损伤零件表面的缺陷;去除毛刺飞边;锐角倒钝;未注倒角均为0.5×45%%d;未注越程槽均为1.2×0.3;表面平整无毛刺;二、未注公差技术要求(金属件)未注公差尺寸的极限偏差按GB/T 1804-m;未注形位公差按GB/T 1184-K;未注长度尺寸允许偏差±0.5;三、表面处理技术要求表面镀白(黑)锌处理;表面喷漆(喷塑)处理;表面发黑处理;表面电泳处理;表面镀铬处理;表面抛光处理;表面滚花,直纹(网纹)m=0.4 GB/T 6403.3;四、热处理技术要求制件氮化450-480HV;制件毛坯须调质处理220-260HB;制件调质处理30-35HRC;制件高频淬火45~50HRC;制件渗碳处理,深度>0.1;制件进行高温回火处理;制件整体淬火40-45HRC;五、铸件技术要求1、压铸件技术要求未注公差尺寸的极限偏差按GB/T 1804-m;未注形位公差按GB/T 1184-K;未注倒角均为0.5×45%%d;未注壁厚2.5;未注筋板1.5~2;未注过渡圆角R0.5-R2;未注脱模斜度≤1%%d;制件饱满光洁、无气孔、缩松、裂纹、夹渣、缺料等缺陷;各脱模顶料推杆压痕均应低于该制件表面0.2;制件要求符合GB/T 15114《铝合金压铸件》标准规定;表面喷漆(喷塑)处理,不得污染到已加工表面;加工表面在表面处理后加工,加工后涂油保护;未注尺寸参照三维造型;制件表面处理及其它要求按客户定;2、砂型铸造技术要求未注铸造圆角R5-10;铸件应彻底清砂,浇冒口应清除平整;铸件需人工时效;铸件不得有砂眼、气孔、缩松、裂纹等缺陷;粗加工后应再次进行人工时效;不加工表面涂底漆;六、冲压件技术要求制件未注公差尺寸的极限偏差按GB/T 15055-m;制件未注形位公差按GB/T 13916-2级;制件不得有裂纹或缺损;制件表面平整,不得有沟痕、碰伤等损坏表面,降低强度及寿命的缺陷;去除边角毛刺;表面处理:七、塑料件技术要求未注公差尺寸的极限偏差按GB/T 14486-MT6级;制件应饱满光整、色泽均匀;无缩痕、裂纹、银丝等缺陷;浇口、溢边修剪后飞边≤0.3,且不得伤及本体;未注壁厚3;未注筋板1.5~2;表面打光(喷砂)处理;未注过渡圆角取R0.3~R1,脱模斜度≤0.3%%d;各脱模顶料推杆压痕均应低于该制件表面0.2;与对应装配结合面外形配合错位≤0.5;制件应进行时效处理;制件机械强度须符合GB 3883.1标准规定;制件内腔表面打上材料标记和回收标志;未注尺寸参照三维造型;制件表面处理及其它要求由客户定;八、焊接件技术要求未注公差线性及角度尺寸的极限偏差均按GB/T 19804-B级;未注形位公差按GB/T 19804-F级;焊缝应均匀平整,焊渣清理干净;焊缝应焊透,不得烧穿及产生裂纹等影响机械性能的缺陷;九、各类零、部件技术要求1、齿轮(齿轴)技术要求未注公差尺寸的极限偏差按GB/T 1804-m;未注形位公差按GB/T 1184-K;制件毛坯须调质220~260HB;制件材料的化学成分和力学性能应符合GB/T 3077的规定;齿面接触斑点:按齿高不小于40%,按齿长不小于50%;齿面高频淬火回火至49-52HRC;制件表面不应有锈迹、裂纹、灼伤等影响使用寿命的伤痕及缺陷;最终工序热处理表面不得有氧化皮;2、一般轴芯(无铣齿)技术要求未注公差尺寸的极限偏差按GB/T 1804-m;未注形位公差按GB/T 1184-K;未注倒角均为0.5×45%%d;未注越程槽均为1.2×0.3;制件毛坯须调质220~260HB;尺寸%%c 档车正反两条螺旋槽,螺距10,深0.4;螺纹表面不允许有磕碰、乱扣、毛刺等缺陷;热处理:表面处理:3、包轴毛坯(一次成型)技术要求未注公差尺寸的极限偏差按GB/T 1804-m;未注形位公差按GB/T 1184-K;绝缘层应饱满光洁,无裂纹、气孔、缺料、杂质等缺陷;包轴毛坯:绝缘层%%c 档(注:指冲片配合档)与轴芯间应能承受50Hz,实际正弦波电压2500V历时1min不击穿,其余绝缘层档3750V历时1min不击穿;一次成型:铁芯与轴芯间应能承受50Hz,实际正弦波电压2500V历时1min不击穿,其余绝缘层档3750V历时1min不击穿;4、包轴(加工)技术要求未注公差尺寸的极限偏差按GB/T 1804-m;未注形位公差按GB/T 1184-K;塑层应饱满光洁,无裂纹、气孔、缺料、杂质等缺陷;塑层%%c 档(注:指冲片配合档)与轴芯间应能承受50Hz,实际正弦波电压2500V历时1min不击穿,其余塑层档3750V历时1min不击穿;制件磨加工后应烘干除水处理;5、转子技术要求未注公差尺寸的极限偏差按GB/T 1804-m;未注形位公差按GB/T 1184-K;绕组接线按转子绕线原理图;绕组绝缘漆应均匀充满绕组并充分固化,漆膜应均匀无气泡或裂痕;云母槽开深0.8~1,槽宽0.6,槽内不得残留云母片;绕组冷态绝缘电阻不低于50MΩ;装风叶后校动平衡,其精度应不低于G6.3级;去重不允许有冲片铣穿、残缺现象;铁芯外圆不加工,绝缘漆不得高出铁芯外圆,并不得有明显积瘤;铁芯与轴芯间应能承受50Hz,实际正弦波电压2500V,1min不击穿;绕组与铁芯间应能承受50Hz,实际正弦波电压1250V,1min不击穿;匝间绝缘应能承受1000Hz,峰值为2100V,历时3s不击穿;换向器与轴芯间应能承受50Hz,实际正弦波电压3750V,1min不击穿;应去除铁屑、铜粉、油污等杂质;铁芯外圆应涂透明淡金水防锈处理;6、定子技术要求绕组绕制整齐无松散;引线接头应牢固可靠且充分绝缘;绕组与铁芯间应能承受50Hz,实际正弦波电压1250V历时1min不击穿;匝间绝缘应能承受1000Hz,峰值为2100V,历时3s不击穿;绕组绝缘漆应均匀充满绕组并充分固化,漆膜应均匀无气泡或积瘤;铁芯表面不得有明显绝缘漆;7、定、转子铁芯技术要求未注公差尺寸的极限偏差按GB/T 1804-m;未注形位公差按GB/T 1184-K;冲片叠装应紧密可靠,片间无夹杂,表面及槽内无污物和油渍;冲片按同一冲制方向压装;冲片齿槽口整齐与转轴平行,误差不大于0.5;铁芯两端弹开度不大于0.5;8、定、转子冲片技术要求制件未注公差尺寸的极限偏差按GB/T 15055-m;制件未注形位公差按GB/T 13916-2级;制件应表面平整,完整无缺料;尖角处允许用R0.3过渡;制件毛刺不大于0.05(注:高速冲时不大于0.02);制件应不含油脂,剪切油不能用机油;9、绝缘纸技术要求表面不得有划痕、折痕;裁边不起毛;10、换向器技术要求未注公差尺寸的极限偏差按GB/T 1804-m;未注形位公差按GB/T 1184-K;外观完整,表面光滑,应无裂纹、毛刺、锈蚀、气孔、夹杂等缺陷;绝缘电阻:室温下内孔与换向片之间大于50MΩ;云母片厚度取0.5;换向片对换向器轴线偏斜度不大于云母片厚度的1/3;介电强度:片间承受频率50Hz,泄露电流为0.1mA,实际正弦波电压600V历时1s不击穿;换向片与内孔轴芯间承受频率50Hz,泄露电流为0.25mA,实际正弦波电压3750V历时1min不击穿;试验与检验应符合JB/T 10107《电动工具换向器》标准要求;11、电缆线技术要求电缆线长度尺寸指工具电缆出口至插头的导线部分,不包括插头和插脚;软电缆应符合GB/T 5013《额定电压450V/750V及以下橡皮绝缘电缆》标准要求;聚氯乙烯电缆应符合GB/T 5023《额定电压450V/750V及以下聚氯乙烯绝缘电缆》标准要求;插脚与可触及插头表面的绝缘应能承受50Hz,实际正弦波电压3750V历时1min不击穿;制件还应符合GB 1002《家用和类似用途单相插头插座型式、基本参数和尺寸》和GB 2099《家用和类似用途插头插座》标准要求;12、开关技术要求未注公差尺寸的极限偏差按SJ/T 10628-7级;除本图要求的外形尺寸、功能、图形、文字外,试验和检验均应符合GB/T 22692《电动工具开关》标准要求;开关的使用性能应保证5万次无故障正常使用;13、电缆护套技术要求未注公差尺寸的极限偏差按GB/T 3672.1-2级;未注形位公差按GB/T 3672.2-M级;制件不得有缺料、破裂等缺陷。
机械图纸技术要求大全
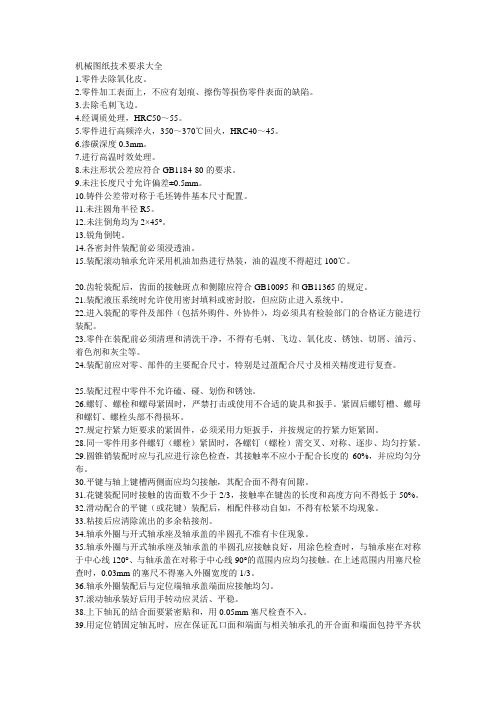
机械图纸技术要求大全1.零件去除氧化皮。
2.零件加工表面上,不应有划痕、擦伤等损伤零件表面的缺陷。
3.去除毛刺飞边。
4.经调质处理,HRC50~55。
5.零件进行高频淬火,350~370℃回火,HRC40~45。
6.渗碳深度0.3mm。
7.进行高温时效处理。
8.未注形状公差应符合GB1184-80的要求。
9.未注长度尺寸允许偏差±0.5mm。
10.铸件公差带对称于毛坯铸件基本尺寸配置。
11.未注圆角半径R5。
12.未注倒角均为2×45°。
13.锐角倒钝。
14.各密封件装配前必须浸透油。
15.装配滚动轴承允许采用机油加热进行热装,油的温度不得超过100℃。
20.齿轮装配后,齿面的接触斑点和侧隙应符合GB10095和GB11365的规定。
21.装配液压系统时允许使用密封填料或密封胶,但应防止进入系统中。
22.进入装配的零件及部件(包括外购件、外协件),均必须具有检验部门的合格证方能进行装配。
23.零件在装配前必须清理和清洗干净,不得有毛刺、飞边、氧化皮、锈蚀、切屑、油污、着色剂和灰尘等。
24.装配前应对零、部件的主要配合尺寸,特别是过盈配合尺寸及相关精度进行复查。
25.装配过程中零件不允许磕、碰、划伤和锈蚀。
26.螺钉、螺栓和螺母紧固时,严禁打击或使用不合适的旋具和扳手。
紧固后螺钉槽、螺母和螺钉、螺栓头部不得损坏。
27.规定拧紧力矩要求的紧固件,必须采用力矩扳手,并按规定的拧紧力矩紧固。
28.同一零件用多件螺钉(螺栓)紧固时,各螺钉(螺栓)需交叉、对称、逐步、均匀拧紧。
29.圆锥销装配时应与孔应进行涂色检查,其接触率不应小于配合长度的60%,并应均匀分布。
30.平键与轴上键槽两侧面应均匀接触,其配合面不得有间隙。
31.花键装配同时接触的齿面数不少于2/3,接触率在键齿的长度和高度方向不得低于50%。
32.滑动配合的平键(或花键)装配后,相配件移动自如,不得有松紧不均现象。
机械图纸技术要求大全(整理版)【范本模板】

一般技术要求1. 零件去除氧化皮.2. 零件加工表面上,不应有划痕、擦伤等损伤零件表面的缺陷。
3. 去除毛刺飞边。
热处理要求4。
经调质处理,HRC50~55。
5.零件进行高频淬火,350~370℃回火,HRC40~45.6.渗碳深度0.3mm。
7。
进行高温时效处理。
公差要求8.未注形状公差应符合GB1184-80的要求。
9。
未注长度尺寸允许偏差±0.5mm。
10。
铸件公差带对称于毛坯铸件基本尺寸配置.零件棱角11.未注圆角半径R5。
12。
未注倒角均为2×45°。
13。
锐角/尖角/锐边倒钝。
装配要求14.各密封件装配前必须浸透油。
15。
装配滚动轴承允许采用机油加热进行热装,油的温度不得超过100℃。
20.齿轮装配后,齿面的接触斑点和侧隙应符合GB10095和GB11365的规定.21。
装配液压系统时允许使用密封填料或密封胶,但应防止进入系统中。
22.进入装配的零件及部件(包括外购件、外协件),均必须具有检验部门的合格证方能进行装配.23.零件在装配前必须清理和清洗干净,不得有毛刺、飞边、氧化皮、锈蚀、切屑、油污、着色剂和灰尘等。
24。
装配前应对零、部件的主要配合尺寸,特别是过盈配合尺寸及相关精度进行复查。
25.装配过程中零件不允许磕、碰、划伤和锈蚀。
26.螺钉、螺栓和螺母紧固时,严禁打击或使用不合适的旋具和扳手。
紧固后螺钉槽、螺母和螺钉、螺栓头部不得损坏.27.规定拧紧力矩要求的紧固件,必须采用力矩扳手,并按规定的拧紧力矩紧固。
28。
同一零件用多件螺钉(螺栓)紧固时,各螺钉(螺栓)需交叉、对称、逐步、均匀拧紧。
29。
圆锥销装配时应与孔应进行涂色检查,其接触率不应小于配合长度的60%,并应均匀分布.30。
平键与轴上键槽两侧面应均匀接触,其配合面不得有间隙。
31。
花键装配同时接触的齿面数不少于2/3,接触率在键齿的长度和高度方向不得低于50%。
32.滑动配合的平键(或花键)装配后,相配件移动自如,不得有松紧不均现象。
机械制图工程图技术要求全

机械图纸-技术要求汇总一般技术要求1. 零件去除氧化皮。
2. 零件加工表面上,不应有划痕、擦伤等损伤零件表面的缺陷。
3. 去除毛刺飞边。
热处理要求1. 经调质处理,HRC50~55。
2. 零件进行高频淬火,350~370℃回火,HRC40~45。
3. 渗碳深度0.3mm。
4. 进行高温时效处理。
公差要求1. 未注形状公差应符合GB1184-80的要求。
2. 未注长度尺寸允许偏差±0.5mm。
3. 铸件公差带对称于毛坯铸件基本尺寸配置。
零件棱角1. 未注圆角半径R5。
2. 未注倒角均为2×45°。
3. 锐角/尖角/锐边倒钝。
装配要求1. 各密封件装配前必须浸透油。
2. 装配滚动轴承允许采用机油加热进行热装,油的温度不得超过100℃。
3. 齿轮装配后,齿面的接触斑点和侧隙应符合GB10095和GB11365的规定。
4. 装配液压系统时允许使用密封填料或密封胶,但应防止进入系统中。
5. 进入装配的零件及部件(包括外购件、外协件),均必须具有检验部门的合格证方能进行装配。
6. 零件在装配前必须清理和清洗干净,不得有毛刺、飞边、氧化皮、锈蚀、切屑、油污、着色剂和灰尘等。
7. 装配前应对零、部件的主要配合尺寸,特别是过盈配合尺寸及相关精度进行复查。
8. 装配过程中零件不允许磕、碰、划伤和锈蚀。
9. 螺钉、螺栓和螺母紧固时,严禁打击或使用不合适的旋具和扳手。
紧固后螺钉槽、螺母和螺钉、螺栓头部不得损坏。
10. 规定拧紧力矩要求的紧固件,必须采用力矩扳手,并按规定的拧紧力矩紧固。
11. 同一零件用多件螺钉(螺栓)紧固时,各螺钉(螺栓)需交叉、对称、逐步、均匀拧紧。
12. 圆锥销装配时应与孔应进行涂色检查,其接触率不应小于配合长度的60%,并应均匀分布。
一般的图纸技术要求填写
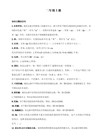
铸钢件表面堆焊接时,焊道间的重叠量不得小于焊道宽度的1/3。
10.锻件要求:
每个钢锭的水口、冒口应有足够的切除量,一以保证锻件无缩孔和严重的偏折。
锻件应在有足够能力的锻压机上锻造成形,以保证锻件内部充分锻透。
锻件不允许有肉眼可见的裂纹、折叠和其他影响使用的外观缺陷。局部缺陷可以清除,但清理深度不得超过加工余量的75%,锻件非加工表面上的缺陷应清理干净并圆滑过渡。
滑动配合的平键(或花键)装配后,相配件移动自如,不得有松紧不均现象。
粘接后应清除流出的多余粘接剂。
轴承外圈与开式轴承座及轴承盖的半圆孔不准有卡住现象。
轴承外圈与开式轴承座及轴承盖的半圆孔应接触良好,用涂色检查时,与轴承座在对称于中心线120°、与轴承盖在对称于中心线90°的范围内应均匀接触。在上述范围内用塞尺检查时,0.03mm的塞尺不得塞入外圈宽度的1/3。
渗碳深度0.3mm。
进行高温时效处理。
3.公差要求:
未注形状公差应符合GB1184-80的要求。
未注长度尺寸允许偏差±0.5mm。
铸件公差带对称于毛坯铸件基本尺寸配置。
4.零件棱角:
未注圆角半径R5。
未注倒角均为2×45°。
锐角倒钝。
5.装配要求:
各密封件装配前必须浸透油。
装配滚动轴承允许采用机油加热进行热装,油的温度不得超过100℃。
规定拧紧力矩要求的紧固件,必须采用力矩扳手,并按规定的拧紧力矩紧固。
同一零件用多件螺钉(螺栓)紧固时,各螺钉(螺栓)需交叉、对称配合长度的60%,并应均匀分布。
平键与轴上键槽两侧面应均匀接触,其配合面不得有间隙。
- 1、下载文档前请自行甄别文档内容的完整性,平台不提供额外的编辑、内容补充、找答案等附加服务。
- 2、"仅部分预览"的文档,不可在线预览部分如存在完整性等问题,可反馈申请退款(可完整预览的文档不适用该条件!)。
- 3、如文档侵犯您的权益,请联系客服反馈,我们会尽快为您处理(人工客服工作时间:9:00-18:30)。
Owner :Sweeney, Carol (t6762cs)
-------------------------------------------------------------------------------------
ENGINEERING STANDARDS APPLIED
-------------------------------------------------------------------------------------
MATERIAL CONTENT REPORTING, MARKING, AND RECYCLABIL
ITY
供应商要求车辆和服务部分:材料内容报道,标记和再循环能力
8 CS-9022 COLOR AND GLOSS REQUIREMENTS FOR INTERIOR TRIM COMPO
general notes:
2.part must be free of flash, burrs and sharp edges that adversely effect product quality, function, fit or safe handling
划痕和3月汽车内部涂料和外部阻力塑料使用五指测试仪
14 LP-463KC-09-01 ODOR
气味
15 LP-463LB-12-01 RESISTANCE TO HUMIDITY HOT AND COLD CYCLING OF TRIM
MATERIALS TEST
耐湿度调整材料的冷热循环测试 (修剪材料对 耐湿冷热循环测试的抵抗)
int Standard)
几何尺寸和公差实践(联合标准)
12 FMVSS302 FMVSS302 - AVAILABLE IN THE AUTOMOTIVE LEGISLATION O
NLINE (ALO) WEBSITE
联邦机动车安全标准302——可用在汽车立法在线(ALO)网站
FMVSS 302 Flammability of materials used in the occupant compartments of motor vehicles
TITLE BLOCK INFORMATION
-------------------------------------------------------------------------------------
Item Number :FC00AAN04467
Item Revision :003
内饰材料的可燃性测试
20 PF-10254 SEAT COMPLETE ASSEMBLY PERFORMANCE STANDARD
座椅总成性能标准
21 PF-11203 MATERIAL DURABILITY REQUIREMENTS FOR INTERIOR PLASTI
C TRIM COMPONENTS
6.No sink mark,flow lines or other visual imperfections to be on visible surfaces.
6。没有缩痕、流痕或其他视觉可见的表面缺陷。
7.Tolerance on material thickness is to be +-5% of thickness defined in math model
和定义
31 PS-7300<D> PRODUCT QUALITY - USE OF DIAMONDS <D>
产品质量——使用钻石< D >
32 PS-9065 REGRIND - REUSE OF MOLDING MATERIALS
26 PS-10052 INFORMATION SECURITY
信息安全
27 PS-1285 PLASTIC PART - SURFACE FINISHES
塑料产品-表面加工
28 PS-4480 A IDENTIFICATION OF PARTS
产品识别
29 PS-4559<A> DISTRIBUTION OF MASTER SPECIMENS FOR DESIGNATED APPE
克莱斯勒(CHRYSLER GROUP LLC)商标识别在产品上.
5 CS-8891 MAXIMUM ALLOWABLE CONDITION FOR PARTING LINE FLASH A
ND DIE MISMATCH FOR PLASTIC INJECTION MOLD边缘,严重影响产品质量,功能,健康或安全的处理
3. all dimensions applicable after graining
所有的尺寸成型后适用.
4. parting line and die draw defined in math dada can not be altered without chrysler written permission.
-------------------------------------------------------------------------------------
PART INFORMATION PAGE
-------------------------------------------------------------------------------------
4。分型线和模具图明确在数据里就不能改变在没有克莱斯勒书面许可下。
5.gate location must be approved by chrysler engineering and placed on nonvisible surfaces.
5。进胶点的位置必须经批准克莱斯勒工程批准和放在看不到表面。
SPECIAL CHARACTERISTICS
-------------------------------------------------------------------------------------
R PARTS (SUPERSEDED BY MS-JP-9-4)
检验测试特点要求特殊质量控制监测——可燃性室内部分(由M
S-JP-9-4取代)
7 CS-9003 SUPPLIER REQUIREMENTS FOR VEHICLE AND SERVICE PARTS:
要求验证,验证和持续的一致性测试
24 PF-HOMOLOGATION PRODUCT HOMOLOGATION
产品同系化反应
25 PF-SAFETY<S> PRODUCT SAFETY - USE OF SAFETY SHIELDS <S>
产品安全,使用安全保护<年代>
7。在材料厚度公差是+ -5%的数学模型中定义的厚度
reference chrysler standard cep12679 for s and h definition and requirements
参考标准克莱斯勒cep12679 s和h的定义和要求
Tue, 25 Mar 2014
对内饰塑料部件材料耐久性要求
22 PF-12063 FRONT SEAT STRUCTURE PERFORMANCE STANDARD
前座结构性能标准
23 PF-8500 REQUIREMENTS FOR VERIFICATION, VALIDATION AND CONTIN
UING CONFORMANCE TESTING
NENTS
内饰部件颜色和光泽要求
9 CS-9800 GENERAL INFORMATION
一般信息
10 CS-9801 QUALITY REQUIREMENTS
质量要求
11 FC-12421 GEOMETRIC DIMENSIONING AND TOLERANCING PRACTICES (Jo
粉料再生——成型材料的重用
33 PS-9227 CAD/CAM DATA EXCHANGE POLICY
CAD / CAM数据交换政策
-------------------------------------------------------------------------------------
AUTOMOTIVE GRADES.
塑料-热塑性聚丙烯(PP)——所有汽车的等级。
18 MS-JP-1-3 COLOR DURABILITY OF INTERIOR MATERIALS
室内材料的颜色耐久性
19 MS-JP-9-4<S> FLAMMABILITY TESTING OF INTERIOR MATERIALS
16 LP-463PB-57-03 AUTOMOTIVE FLUIDS STAINING OF PLASTICS - DETERMINATI
ON OF
汽车塑料液体染色——测定
17 MS-DB-500 PLASTICS - THERMOPLASTIC - POLYPROPYLENE (PP) - ALL
5 cs - 8891分型线毛边和对塑料注塑模具产品模具错位最大允许条件
6 CS-9001 INSPECTION TEST CHARACTERISTICS REQUIRING SPECIAL QU
ALITY CONTROL SURVEILLANCE - FLAMMABILITY OF INTERIO