铸钢技术
铸造低合金钢(ZG30Cr06)技术要求

铸造低合金钢(ZG30Cr06)技术要求
1.使用范围
本标准规定了铸造低合金钢(ZG30Cr06)用于液压支架铸件的技术要求。
2.引用标准
下列标准所包含的条文通过本标准引用而成为本标准的条文。
GB11352-89 一般工程用铸造碳钢件
GB222-81 钢铁及合金化学分析方法
GB228-76 金属拉力试验法
GB231 金属布氏硬度试验法
3.技术要求
3.1 技术要求
3.1.1 合金成分
低合金铸钢(ZG30Cr06)的化学成分见表1
ZG30Cr06化学成分表1
注:碳当量CE按下式计算,此公式已为国际焊接学会和美国ASTM学会采用。
CE=(C+Mn/6+Cr/5)%,碳当量CE一般控制在≤0.61%。
3.1.2 机械性能
低合金铸钢(ZG30Cr06)的机械性能见表2,应根据不同的使用要求进行选择。
ZG30Cr06的机械性能表2
注:单铸拉力试棒(标准试棒),拉力试棒随铸件同炉浇注,同炉热处理。
3.1.3 其他性能要求
低合金铸钢(ZG30Cr06)铸件的技术要求,除机械性能外,其它性能按一般铸件国家通用标准执行。
铸钢节点应用技术规程
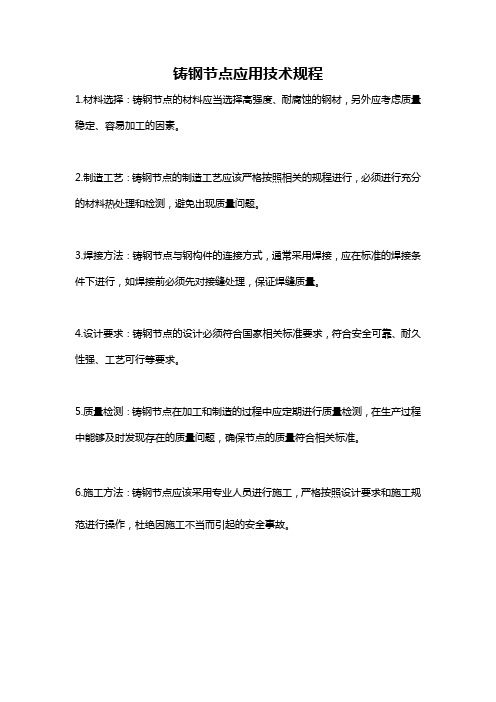
铸钢节点应用技术规程
1.材料选择:铸钢节点的材料应当选择高强度、耐腐蚀的钢材,另外应考虑质量稳定、容易加工的因素。
2.制造工艺:铸钢节点的制造工艺应该严格按照相关的规程进行,必须进行充分的材料热处理和检测,避免出现质量问题。
3.焊接方法:铸钢节点与钢构件的连接方式,通常采用焊接,应在标准的焊接条件下进行,如焊接前必须先对接缝处理,保证焊缝质量。
4.设计要求:铸钢节点的设计必须符合国家相关标准要求,符合安全可靠、耐久性强、工艺可行等要求。
5.质量检测:铸钢节点在加工和制造的过程中应定期进行质量检测,在生产过程中能够及时发现存在的质量问题,确保节点的质量符合相关标准。
6.施工方法:铸钢节点应该采用专业人员进行施工,严格按照设计要求和施工规范进行操作,杜绝因施工不当而引起的安全事故。
铸钢轧辊表面处理技术
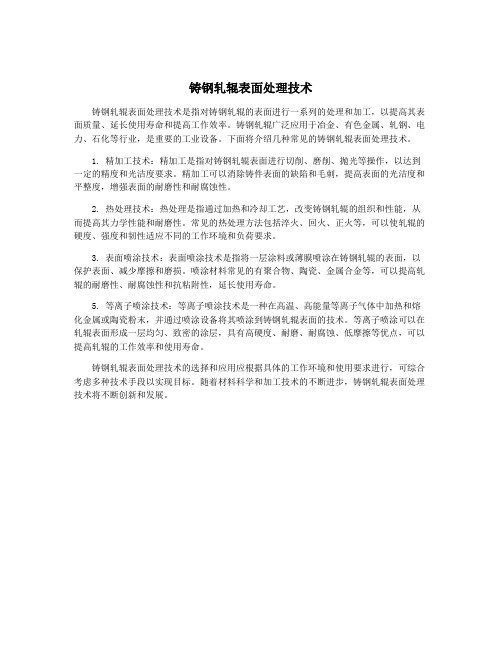
铸钢轧辊表面处理技术
铸钢轧辊表面处理技术是指对铸钢轧辊的表面进行一系列的处理和加工,以提高其表面质量、延长使用寿命和提高工作效率。
铸钢轧辊广泛应用于冶金、有色金属、轧钢、电力、石化等行业,是重要的工业设备。
下面将介绍几种常见的铸钢轧辊表面处理技术。
1. 精加工技术:精加工是指对铸钢轧辊表面进行切削、磨削、抛光等操作,以达到一定的精度和光洁度要求。
精加工可以消除铸件表面的缺陷和毛刺,提高表面的光洁度和平整度,增强表面的耐磨性和耐腐蚀性。
2. 热处理技术:热处理是指通过加热和冷却工艺,改变铸钢轧辊的组织和性能,从而提高其力学性能和耐磨性。
常见的热处理方法包括淬火、回火、正火等,可以使轧辊的硬度、强度和韧性适应不同的工作环境和负荷要求。
3. 表面喷涂技术:表面喷涂技术是指将一层涂料或薄膜喷涂在铸钢轧辊的表面,以保护表面、减少摩擦和磨损。
喷涂材料常见的有聚合物、陶瓷、金属合金等,可以提高轧辊的耐磨性、耐腐蚀性和抗粘附性,延长使用寿命。
5. 等离子喷涂技术:等离子喷涂技术是一种在高温、高能量等离子气体中加热和熔化金属或陶瓷粉末,并通过喷涂设备将其喷涂到铸钢轧辊表面的技术。
等离子喷涂可以在轧辊表面形成一层均匀、致密的涂层,具有高硬度、耐磨、耐腐蚀、低摩擦等优点,可以提高轧辊的工作效率和使用寿命。
铸钢轧辊表面处理技术的选择和应用应根据具体的工作环境和使用要求进行,可综合考虑多种技术手段以实现目标。
随着材料科学和加工技术的不断进步,铸钢轧辊表面处理技术将不断创新和发展。
铸钢轧辊表面处理技术

铸钢轧辊表面处理技术1.硬面焊接技术硬面焊接技术是一种利用电弧焊、气焊、等离子焊等方法,在铸钢轧辊表面涂上一层高硬度、耐磨损的合金层以提高轧辊的表面硬度、抗撞击性能和耐磨损性能。
硬面焊接技术具有安装简单、耐磨损、寿命长等优点,但焊层与基体之间容易形成接口裂纹,从而影响焊层的完整性和耐久性。
2.电镀技术电镀技术是一种将金属离子通过电解作用沉积在铸钢轧辊表面上的表面处理技术。
通过控制电解液、电流密度、温度等参数,可在轧辊表面形成一层具有较高硬度、耐磨损性能的表层。
电镀技术具有成本低、易于操作、操作灵活等优点,但不能处理大尺寸轧辊且存在涂层表面不均匀、厚度难以控制等问题。
3.喷涂技术喷涂技术是一种直接利用气体或液体将粉末、涂料等物质喷涂在铸钢轧辊表面上,形成一种具有多种特殊性能的表面处理技术。
喷涂技术具有物料选择范围广、粘附性好、对轧辊表面无损伤等优点,但不能解决涂层粗糙度较大、耐磨性能差、涂层厚度难控制等问题。
4.热处理技术热处理技术是一种将铸钢轧辊表面加热处理以改变其物理、化学性能的技术。
通过控制加热时间、温度等参数,可以使轧辊表面硬度、强度等性能得到提高。
热处理技术具有适用范围广、处理效果好、不改变轧辊表面形状等优点,但无法解决轧辊表面制造质量低、干燥处理困难等问题。
1.多种表面处理技术的结合通过将多种表面处理技术相结合,可克服单一表面处理技术的弊端,提高轧辊表面的综合性能。
例如,可以将热处理与电镀、硬面焊接等技术相结合,从而提高轧辊表面硬度、抗磨损性能和使用寿命。
随着环保意识的不断提升,未来的铸钢轧辊表面处理技术应该做到绿色高效。
例如,可以开发出新型的无污染和低污染的表面处理技术,以满足环保要求。
3.智能化表面处理技术智能化表面处理技术是未来铸钢轧辊表面处理技术的重要方向之一。
通过将先进的自动化装备、机器人技术等应用到表面处理过程中,可以大幅提高生产效率和处理质量,并且降低了工人的劳动强度和生产成本。
大型铸钢件铸造工艺技术

大型铸钢件铸造工艺技术大型铸件生产周期长、工序复杂,一般要经历众多工序(如图2—1所示),合理设置其铸造过程中各项工艺是决定铸件最终成功铸造的关键要素。
图2—1大型铸钢件铸造工艺流程2.1大型铸钢件造型用砂铸钢件尤其是大型铸钢件大都采用自硬砂地面造型。
大型铸钢件通常具有厚大断面和高的金属静压头、浇注时间较长,加上铸件凝固过程中金属液体与砂型之间的热作用、机械作用、化学反应非常强烈;铸件表面,尤其在砂芯或砂型凹陷及转角处极易产生金属渗透粘砂,易造成铸件尺寸稳定性差和表面缺陷。
因而大型铸钢件对砂型的高温力学性能、型砂材料的抗粘砂能力要求非常高。
目前国内重机行业用于大型铸钢件的造型用砂主要有水玻璃砂(C02吹气硬化和有机醋自硬化)、树脂自硬砂〔峡喃树脂自硬砂、碱酚醛树脂自硬砂)国内一些主要大型铸件生产企业已逐步完成使用自硬砂铸造工艺的技术改造。
大型铸钢件的面砂一般采用铬铁矿砂等特种砂,这些原砂比硅砂的价格高出很多。
因此,对于旧砂再生系统中铬铁矿砂与石英砂的分离技术也是一项合理利用资源及降低成本的关键性技术。
2.2 铬铁矿砂在造型中的应用2.2.1铬铁矿呋喃树脂砂面砂应用实例(见表2—1)222 铬铁矿砂成份及选择铬铁矿砂属于铬尖晶石。
一般以(FeMg 0・(CrAIFe)2Q形式存在,其中杂质主要为CaO MnQ SiO2、TQ2等金属氧化物和碳酸盐化合物。
铬铁矿砂的比重为(4.4〜4.5 )3 3kg/cm,堆积比重为(2.0〜2.7 )kg/cm ,耐火度为2000土25C,熔融触点2040C。
铬铁矿砂的选择主要依据需要配制的型(芯)砂后的工艺参数、铸件质量以及旧砂再生回收率的高低来不断摸索确定。
铬铁矿砂的化学成分及质量分数(%见表2—1。
表2—1 铬铁矿砂的化学成分及质量分数(%2.2.2.1 酸耗值我们在采用呋喃树脂砂工艺时其催(固)化剂为磺酸、苯磺酸之类酸性固化剂硬化,要求原砂呈中性,如存在诸如滑石粉的碱性化合物,固化剂的消耗必然要加大,从而砂型固化慢甚至不能硬化。
铸钢技术

铸钢技术对于强度、塑性和韧性要求更高的机器零件,需要采用铸钢件。
铸钢件的产量仅次于铸铁,约占铸件总产量的15%。
一、按照化学成分铸钢可分为碳素铸钢和合金铸钢两大类。
其中以碳素铸钢应用最广,占铸钢总产量的80%以上。
1、碳素铸钢一般的,低碳钢ZG15的熔点较高、铸造性能差,仅用于制造电机零件或渗碳零件;中碳钢ZG25~ZG45,具有高于各类铸铁的综合性能,即强度高、有优良的塑性和韧性,因此适于制造形状复杂、强度和韧性要求高的零件,如火车车轮、锻锤机架和砧座、轧辊和高压阀门等,是碳素铸钢中应用最多的一类;高碳钢ZG55的熔点低,其铸造性能较中碳钢的好,但其塑性和韧性较差,仅用于制造少数的耐磨件。
2、合金铸钢根据合金元素总量的多少,合金铸钢可分为两低合金钢和高合金钢大类。
1)低合金铸钢,我国主要应用锰系、锰硅系及铬系等。
如ZG40Mn、ZG30MnSi1、ZG30Cr1MnSi1等。
用来制造齿轮、水压机工作缸和水轮机转子等零件,而ZG40Cr1常用来制造高强度齿轮和高强度轴等重要受力零件。
2)高合金铸钢,具有耐磨、耐热或耐腐蚀等特殊性能。
如高锰钢ZGMn13,是一种抗磨钢,主要用于制造在干磨擦工作条件下使用的零件,如挖掘机的抓斗前壁和抓斗齿、拖拉机和坦克的履带等;铬镍不锈钢ZG1Cr18Ni9和铬不锈钢ZG1Cr13和ZGCr28等,对硝酸的耐腐蚀性很高,主要用于制造化工、石油、化纤和食品等设备上的零件。
二、铸钢的铸造工艺特点铸钢的机械性能比铸铁高,但其铸造性能却比铸铁差。
因为铸钢的熔点较高,钢液易氧化、钢水的流动性差、收缩大,其体收缩率为10~14%,线收缩为1.8~2.5%。
为防止铸钢件产生浇不足、冷隔、缩孔和缩松、裂纹及粘砂等缺陷,必须采取比铸铁复杂的工艺措施:1、由于钢液的流动性差,为防止铸钢件产生冷隔和浇不足,铸钢件的壁厚不能小于8mm;浇注系统的结构力求简单、且截面尺寸比铸铁的大;采用干铸型或热铸型;适当提高浇注温度,一般为1520°~1600℃,因为浇注温度高,钢水的过热度大、保持液态的时间长,流动性可得到改善。
zg310—570铸钢技术标准

zg310—570铸钢技术标准
ZG310-570 是中国标准中关于铸钢的技术标准之一。
这个标准定义了一系列与铸造钢材料相关的技术要求、化学成分、机械性能等方面的规范。
一般而言,ZG310-570 标准主要涉及以下内容:
1. 化学成分要求:包括铸钢的主要化学成分要求,如碳含量、硅、锰、磷、硫等元素的限制范围。
2. 机械性能要求:规定了铸钢材料的机械性能指标,例如抗拉强度、屈服强度、延伸率等。
3. 热处理:对于需要热处理的铸钢材料,标准可能包含了相应的热处理方法、温度要求等规定。
4. 检测方法:包括对铸钢材料进行化学成分分析、机械性能测试等的测试方法和标准。
这些标准旨在确保铸钢材料的质量符合特定的标准要求,以保障其在特定工程、结构或设备中的安全和可靠使用。
如需具体的技术细节或标准内容,建议查询中国相关的标准文档或向专业机构或相关领域的专家咨询。
1。
一般工程与结构用铸钢件的技术要求
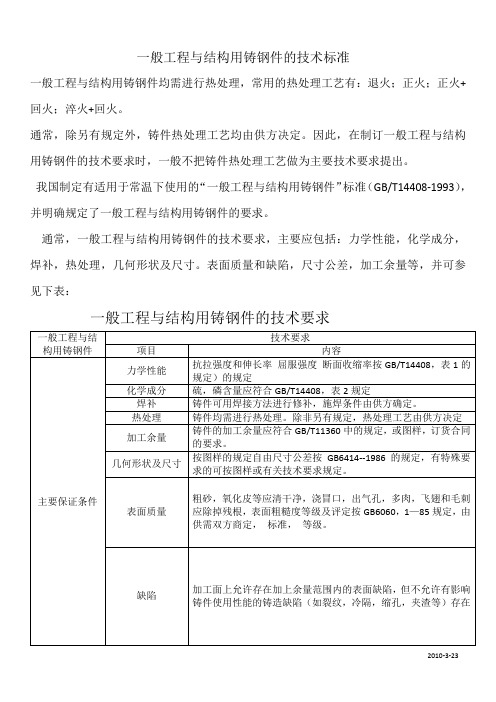
一般工程与结构用铸钢件的技术标准
一般工程与结构用铸钢件均需进行热处理,常用的热处理工艺有:退火;正火;正火+回火;淬火+回火。
通常,除另有规定外,铸件热处理工艺均由供方决定。
因此,在制订一般工程与结构用铸钢件的技术要求时,一般不把铸件热处理工艺做为主要技术要求提出。
我国制定有适用于常温下使用的“一般工程与结构用铸钢件”标准(GB/T14408-1993),并明确规定了一般工程与结构用铸钢件的要求。
通常,一般工程与结构用铸钢件的技术要求,主要应包括:力学性能,化学成分,焊补,热处理,几何形状及尺寸。
表面质量和缺陷,尺寸公差,加工余量等,并可参见下表:
一般工程与结构用铸钢件的技术要求。
铸钢的熔炼技术与规范PPT课件

2. 铸造工艺特点
(1)铸钢件的结构设计要合理 (2)浇注系统的开设 正确引导钢液入型是防止铸件产生裂纹和缩孔的有效办法。开设浇注系 统时要明确铸件的凝固顺序。
3. 铸钢件用造型材料
(1)铸钢件干型用砂 铸钢件造型时,型砂一般分为面砂和背砂。采用砂粒较细的面砂,型砂塑性 好,可得到较光洁的铸件,而背砂使用较粗的砂粒可以提高透气性,还可以降低 成本。 (2)铸钢件湿型用砂 有些小型铸钢件可以采用湿型铸造。 (3)铸钢件用芯砂 要提高铸钢件的表面质量,除了要求芯砂有高的耐火性外,还要增加它的退 让性,不易出砂的型芯可采用油砂。
感谢聆听!
(4)铸钢用涂料 铸钢干型涂料一般采用石英粉;重型铸钢件可采用铬矿粉。
二、铸钢熔炼用原材料
1. 耐火材料
(1)炉衬材料 炼钢炉炉衬的耐火材料有碱性、酸性和中性三种。 (2)黏结剂 炉衬材料的黏结剂有焦油、沥青、卤水、硼酸和水玻璃。
2. 炉料
(1)钢铁材料
(2)铁合金
(3)造渣材料
(4)氧化剂
(5)脱氧剂和增碳材料
(4)氧化期 炼钢过程中进行硅、锰、磷和碳等元素氧化反应的阶段叫氧化期。 (5)还原期 还原期的主要任务是: 造好还原渣,对钢液进行脱氧、脱硫,调整化学成 分,控制好出钢温度。 (7)出钢 出钢时要求钢液流柱要粗,不能散流,将钢液和钢渣全部倾入盛钢桶中, 然后在钢液表面盖上保温材料。
4.评分标准 评分标准见下表。
图8-16 三相电弧炉结构
(1)炉体 炉体是电弧炉的主要部分,它的外壳由钢板焊成,内部用耐火材料砌筑而成。 (2)炉盖 炉盖是用钢板焊成的炉盖圈(空心的,内部通水冷却),在圈内用耐火砖砌筑。 (3)电极升降机构 电弧炉中的电极上升与下降一般是自动控制的,电极升降的自动控制系统由 电气部分和电极升降机构两部分组成。 电极夹持机构一般用弹簧固紧的夹板或螺栓固紧的夹板夹持电极。
铸钢的概念
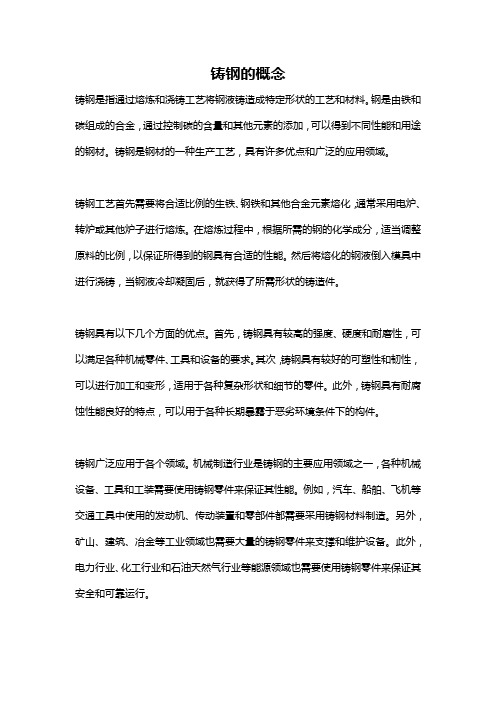
铸钢的概念铸钢是指通过熔炼和浇铸工艺将钢液铸造成特定形状的工艺和材料。
钢是由铁和碳组成的合金,通过控制碳的含量和其他元素的添加,可以得到不同性能和用途的钢材。
铸钢是钢材的一种生产工艺,具有许多优点和广泛的应用领域。
铸钢工艺首先需要将合适比例的生铁、钢铁和其他合金元素熔化,通常采用电炉、转炉或其他炉子进行熔炼。
在熔炼过程中,根据所需的钢的化学成分,适当调整原料的比例,以保证所得到的钢具有合适的性能。
然后将熔化的钢液倒入模具中进行浇铸,当钢液冷却凝固后,就获得了所需形状的铸造件。
铸钢具有以下几个方面的优点。
首先,铸钢具有较高的强度、硬度和耐磨性,可以满足各种机械零件、工具和设备的要求。
其次,铸钢具有较好的可塑性和韧性,可以进行加工和变形,适用于各种复杂形状和细节的零件。
此外,铸钢具有耐腐蚀性能良好的特点,可以用于各种长期暴露于恶劣环境条件下的构件。
铸钢广泛应用于各个领域。
机械制造行业是铸钢的主要应用领域之一,各种机械设备、工具和工装需要使用铸钢零件来保证其性能。
例如,汽车、船舶、飞机等交通工具中使用的发动机、传动装置和零部件都需要采用铸钢材料制造。
另外,矿山、建筑、冶金等工业领域也需要大量的铸钢零件来支撑和维护设备。
此外,电力行业、化工行业和石油天然气行业等能源领域也需要使用铸钢零件来保证其安全和可靠运行。
铸钢工艺和材料的进步也在不断推动着铸造行业的发展。
随着新材料、新工艺的引入,铸钢的性能得到了进一步提升。
例如,利用真空浇注技术、连铸技术和喷射成形技术等先进工艺,可以制造出无气孔、无夹渣和无缺陷的高质量铸钢材料。
此外,通过控制热处理工艺和提高元素纯度,可以获得更高强度、更好耐腐蚀性能的特殊铸钢材料。
尽管铸钢具有许多优点和广泛应用的领域,但也存在一些限制和挑战。
首先,铸钢工艺需要高温熔炼和冷却过程,能源消耗较大,环境污染较严重。
其次,铸钢的生产工艺和设备要求较高,需要专业技术和设备的支持。
此外,由于铸造过程中的不均匀冷却和凝固,铸钢零件可能存在缩孔、气孔和裂纹等缺陷。
铸钢轧辊表面处理技术
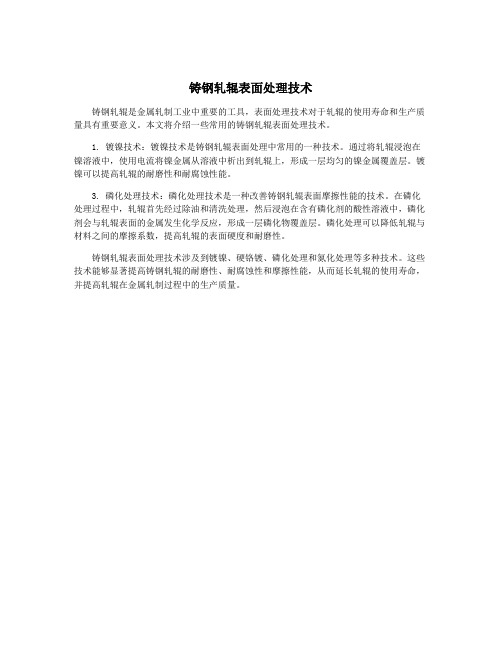
铸钢轧辊表面处理技术
铸钢轧辊是金属轧制工业中重要的工具,表面处理技术对于轧辊的使用寿命和生产质量具有重要意义。
本文将介绍一些常用的铸钢轧辊表面处理技术。
1. 镀镍技术:镀镍技术是铸钢轧辊表面处理中常用的一种技术。
通过将轧辊浸泡在镍溶液中,使用电流将镍金属从溶液中析出到轧辊上,形成一层均匀的镍金属覆盖层。
镀镍可以提高轧辊的耐磨性和耐腐蚀性能。
3. 磷化处理技术:磷化处理技术是一种改善铸钢轧辊表面摩擦性能的技术。
在磷化处理过程中,轧辊首先经过除油和清洗处理,然后浸泡在含有磷化剂的酸性溶液中,磷化剂会与轧辊表面的金属发生化学反应,形成一层磷化物覆盖层。
磷化处理可以降低轧辊与材料之间的摩擦系数,提高轧辊的表面硬度和耐磨性。
铸钢轧辊表面处理技术涉及到镀镍、硬铬镀、磷化处理和氮化处理等多种技术。
这些技术能够显著提高铸钢轧辊的耐磨性、耐腐蚀性和摩擦性能,从而延长轧辊的使用寿命,并提高轧辊在金属轧制过程中的生产质量。
铸钢技术要求
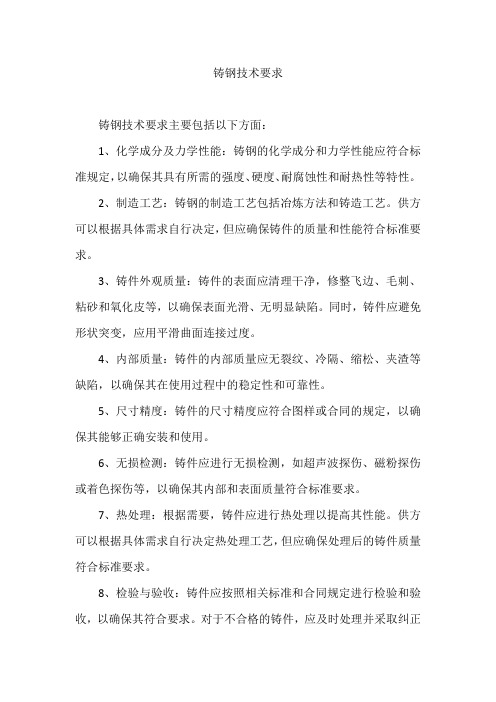
铸钢技术要求
铸钢技术要求主要包括以下方面:
1、化学成分及力学性能:铸钢的化学成分和力学性能应符合标准规定,以确保其具有所需的强度、硬度、耐腐蚀性和耐热性等特性。
2、制造工艺:铸钢的制造工艺包括冶炼方法和铸造工艺。
供方可以根据具体需求自行决定,但应确保铸件的质量和性能符合标准要求。
3、铸件外观质量:铸件的表面应清理干净,修整飞边、毛刺、粘砂和氧化皮等,以确保表面光滑、无明显缺陷。
同时,铸件应避免形状突变,应用平滑曲面连接过度。
4、内部质量:铸件的内部质量应无裂纹、冷隔、缩松、夹渣等缺陷,以确保其在使用过程中的稳定性和可靠性。
5、尺寸精度:铸件的尺寸精度应符合图样或合同的规定,以确保其能够正确安装和使用。
6、无损检测:铸件应进行无损检测,如超声波探伤、磁粉探伤或着色探伤等,以确保其内部和表面质量符合标准要求。
7、热处理:根据需要,铸件应进行热处理以提高其性能。
供方可以根据具体需求自行决定热处理工艺,但应确保处理后的铸件质量符合标准要求。
8、检验与验收:铸件应按照相关标准和合同规定进行检验和验收,以确保其符合要求。
对于不合格的铸件,应及时处理并采取纠正
措施。
总之,铸钢技术要求涉及到多个方面,供方在生产过程中应严格控制每个环节,确保铸件的质量和性能符合标准要求。
铸钢轧辊表面处理技术
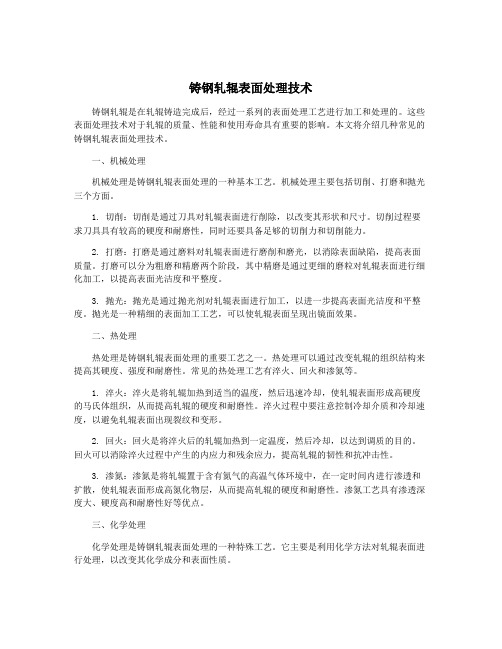
铸钢轧辊表面处理技术铸钢轧辊是在轧辊铸造完成后,经过一系列的表面处理工艺进行加工和处理的。
这些表面处理技术对于轧辊的质量、性能和使用寿命具有重要的影响。
本文将介绍几种常见的铸钢轧辊表面处理技术。
一、机械处理机械处理是铸钢轧辊表面处理的一种基本工艺。
机械处理主要包括切削、打磨和抛光三个方面。
1. 切削:切削是通过刀具对轧辊表面进行削除,以改变其形状和尺寸。
切削过程要求刀具具有较高的硬度和耐磨性,同时还要具备足够的切削力和切削能力。
2. 打磨:打磨是通过磨料对轧辊表面进行磨削和磨光,以消除表面缺陷,提高表面质量。
打磨可以分为粗磨和精磨两个阶段,其中精磨是通过更细的磨粒对轧辊表面进行细化加工,以提高表面光洁度和平整度。
3. 抛光:抛光是通过抛光剂对轧辊表面进行加工,以进一步提高表面光洁度和平整度。
抛光是一种精细的表面加工工艺,可以使轧辊表面呈现出镜面效果。
二、热处理热处理是铸钢轧辊表面处理的重要工艺之一。
热处理可以通过改变轧辊的组织结构来提高其硬度、强度和耐磨性。
常见的热处理工艺有淬火、回火和渗氮等。
1. 淬火:淬火是将轧辊加热到适当的温度,然后迅速冷却,使轧辊表面形成高硬度的马氏体组织,从而提高轧辊的硬度和耐磨性。
淬火过程中要注意控制冷却介质和冷却速度,以避免轧辊表面出现裂纹和变形。
2. 回火:回火是将淬火后的轧辊加热到一定温度,然后冷却,以达到调质的目的。
回火可以消除淬火过程中产生的内应力和残余应力,提高轧辊的韧性和抗冲击性。
3. 渗氮:渗氮是将轧辊置于含有氮气的高温气体环境中,在一定时间内进行渗透和扩散,使轧辊表面形成高氮化物层,从而提高轧辊的硬度和耐磨性。
渗氮工艺具有渗透深度大、硬度高和耐磨性好等优点。
三、化学处理化学处理是铸钢轧辊表面处理的一种特殊工艺。
它主要是利用化学方法对轧辊表面进行处理,以改变其化学成分和表面性质。
1. 酸洗:酸洗是将轧辊置于酸液中进行处理,以去除表面氧化铁皮、锈蚀和杂质等,使轧辊表面呈现出洁净的金属光泽。
铸钢件技术条件
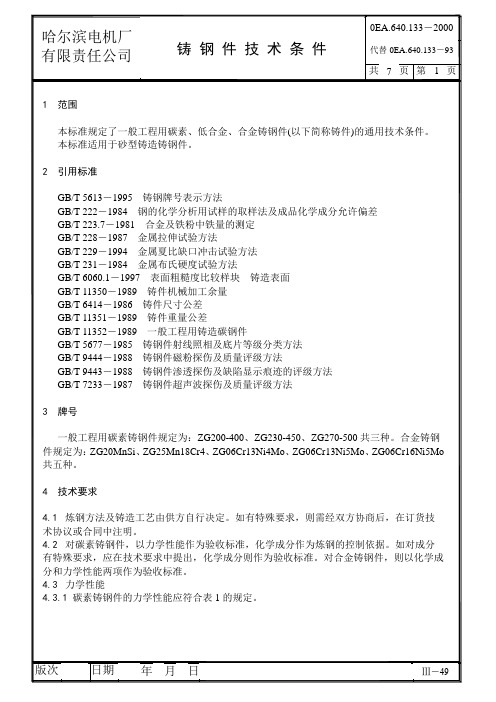
Ni
Cr
Cu
Mo
V
ZG200-400
允许分析偏差
0.20
0.50
0.80
0.04
0.04
0.30
0.35
0.30
0.20
0.05
GZ230-450
允许分析偏差0.30.50.90.04
0.04
0.03
0.35
0.30
0.20
0.05
ZG270-500
允许分析偏差
0.4
0.5
0.9
0.04
0.04
后按6.5.1条、6.5.2条重新试验。
6.5.3.2重新热处理的次数不得超过两次(回火除外),高合金钢可多次。
6.5.4当备用试块不足时,允许从铸件上取样,取样部位由工艺确定。
6.6表面质量
铸件的表面按4.6条要求逐件检验。
4.10尺寸公差、加工余量
4.10.1尺寸公差应符合图纸的要求,如无要求,执行标准0EA.621.044(GB/T 6414)的规定。
4.10.2加工余量执行标准0EA.621.040(GB/T 11350)的规定,或符合图纸、订货合同的要
求。
4.11重量公差执行GB/T 11351的规定。
5试验方法
0.30
0.35
0.30
0.20
0.05
注:
1对上限每减少0.01%的碳,允许增加0.04%的锰。对ZG200-400,锰最高至1.00%;而ZG230-450和
ZG270-500,锰最高至1.20%。
2残余元素总量不超过1.00%,如无特殊要求残余元素可不进行分析。
3化学元素的允许分析偏差是指化学成分分析时允许的偏差。
铸钢熔炼工艺技术
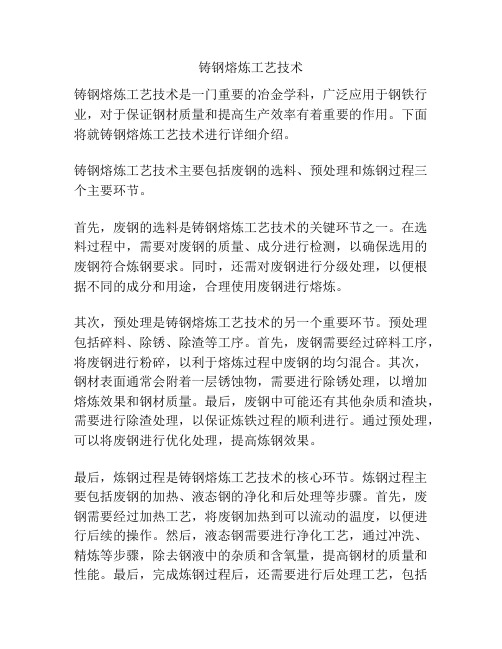
铸钢熔炼工艺技术铸钢熔炼工艺技术是一门重要的冶金学科,广泛应用于钢铁行业,对于保证钢材质量和提高生产效率有着重要的作用。
下面将就铸钢熔炼工艺技术进行详细介绍。
铸钢熔炼工艺技术主要包括废钢的选料、预处理和炼钢过程三个主要环节。
首先,废钢的选料是铸钢熔炼工艺技术的关键环节之一。
在选料过程中,需要对废钢的质量、成分进行检测,以确保选用的废钢符合炼钢要求。
同时,还需对废钢进行分级处理,以便根据不同的成分和用途,合理使用废钢进行熔炼。
其次,预处理是铸钢熔炼工艺技术的另一个重要环节。
预处理包括碎料、除锈、除渣等工序。
首先,废钢需要经过碎料工序,将废钢进行粉碎,以利于熔炼过程中废钢的均匀混合。
其次,钢材表面通常会附着一层锈蚀物,需要进行除锈处理,以增加熔炼效果和钢材质量。
最后,废钢中可能还有其他杂质和渣块,需要进行除渣处理,以保证炼铁过程的顺利进行。
通过预处理,可以将废钢进行优化处理,提高炼钢效果。
最后,炼钢过程是铸钢熔炼工艺技术的核心环节。
炼钢过程主要包括废钢的加热、液态钢的净化和后处理等步骤。
首先,废钢需要经过加热工艺,将废钢加热到可以流动的温度,以便进行后续的操作。
然后,液态钢需要进行净化工艺,通过冲洗、精炼等步骤,除去钢液中的杂质和含氧量,提高钢材的质量和性能。
最后,完成炼钢过程后,还需要进行后处理工艺,包括半成品的冷却、柱状途径的切割、产品的整形等,最终得到符合要求的铸钢产品。
铸钢熔炼工艺技术的发展离不开科技的支持。
随着现代化科技的不断进步,熔炼工艺技术也在不断创新和完善。
例如,采用先进的电炉设备和自动化控制系统,可以提高熔炼效率和生产质量;利用计算机模拟和数值模拟技术,可以对炉温、材料流动、反应过程等进行模拟和分析,优化炼钢工艺参数,提高工艺效益等。
总之,铸钢熔炼工艺技术是一门重要的冶金学科,它对于保证钢材质量和提高生产效率有着重要的作用。
通过废钢的选料、预处理和炼钢过程的合理控制,可以实现废钢的再利用,提高钢铁行业的可持续发展。
铸钢件综合技术条件

铸钢件综合技术条件1 主题内容与适用范围本标准根据GB 11352和GB/T 6967的相关内容,规定了一般工程用铸造碳钢件、一般工程与结构用低合金铸钢件的牌号及铸件技术条件。
以下所涉及的铸钢件均指此两类铸造碳钢件。
本标准适用于砂型或导热性与砂型相当的铸型铸造的碳钢件。
对用其他铸型铸造的铸钢件亦可参照使用。
2 牌号2.1 一般工程用铸造碳钢件按GB 5613的规定分为:ZG200-400;ZG230-450;ZG270-500;ZG310-570;ZG340-640五种铸钢牌号。
2.2 一般工程与结构用低合金铸钢件共包含八种牌号:ZGD270-480;ZGD290-510;ZGD345-570;ZGD410-620;ZGD535-720;ZGD650-830;ZGD730-910;ZGD840-1030。
3 技术要求3.1 生产方法除另有规定外,生产方法和铸造工艺可由供方自行决定。
3.2 化学成分各牌号的化学成分应符合表1的规定:表1 铸钢牌号及化学成分牌号元素最高含量(%)C Si Mn S P残余元素Ni Cr Cu Mo V 总和ZG200-400 0.2 0.5 0.80.04 0.04 0.30 0.35 0.30 0.20 0.05 1.00ZG230-450 0.3 0.5 0.9ZG270-500 0.4 0.5 0.9ZG310-570 0.5 0.6 0.9ZG340-640 0.6 0.6 0.9ZGD270-480 / / / / / / / / / ZGD290-510 / / / / / / / / / ZGD345-570 / / / / / / / / / ZGD410-620 / / / / / / / / / ZGD535-720 / / / / / / / / / ZGD650-830 / / / / / / / / /ZGD730-910 / / /0.35 0.35 / / / / / /ZGD840-1030 / / / / / / / / / 注:1)一般工程用铸造碳钢件对上限减少0.01%的碳,允许增加0.04%的锰;对ZG200-400的锰最高至1.00%,其余四个牌号锰最高至1.20%。
不锈钢铸钢件的技术质量要求

不锈钢铸钢件的技术质量要求
不锈钢铸钢件的技术质量要求包括以下几个方面:
1. 化学成分:不锈钢铸钢件的化学成分应符合相关标准要求,确保材料的成分符合使用要求,以提供良好的耐腐蚀性能。
2. 机械性能:不锈钢铸钢件的机械性能应符合相关标准要求,包括抗拉强度、屈服强度、伸长率等指标,以保证其在使用过程中的强度和韧性。
3. 晶粒度:不锈钢铸钢件的晶粒度应符合相关标准要求,过大的晶粒会降低材料的机械性能和耐腐蚀性能。
4. 压制缺陷:不锈钢铸钢件的压制缺陷应符合相关标准要求,例如气孔、夹杂物和缩松等缺陷,在一定范围内可以接受,但过多或过大的缺陷会影响材料的强度和密封性能。
5. 表面质量:不锈钢铸钢件的表面质量应符合相关标准要求,包括平整度、表面光洁度、裂纹和表面氧化等问题,以确保其在使用时不会出现漏气、漏液等问题。
6. 焊接性能:不锈钢铸钢件的焊接性能应符合相关标准要求,包括焊接接头的强度、韧性和密封性等指标,以保证焊接部位的可靠性。
综上所述,不锈钢铸钢件的技术质量要求涵盖材料的化学成分、机械性能、晶粒度、压制缺陷、表面质量和焊接性能等多个方
面。
以上要求旨在保证不锈钢铸钢件在使用过程中能够提供良好的耐腐蚀性能、机械性能和密封性能。
铸钢生产工艺概述

铸钢生产工艺概述铸钢是一种重要的铸造工艺,用于制造各种不锈钢、合金钢和碳素钢零件。
铸钢生产工艺包括模具设计和制造、原材料准备、熔化和浇注、冷却和固化、精加工等环节。
首先,在铸钢生产过程中,需要设计和制造合适的模具。
模具的设计要满足铸造零件的形状和尺寸要求,并考虑到零件的结构和旋转部件等特殊要求。
然后,通过数控加工设备制造模具,确保其尺寸和形状的准确性。
接下来,准备原材料。
原材料一般是钢锭、铸坯或钢材,其中包含所需合金元素。
根据铸钢零件的要求,选择适当的原材料,并加以预热和预处理,以去除杂质和气体,提高原材料的熔化性能。
然后,熔化和浇注。
将预处理好的原材料放入电弧炉或感应炉中进行熔化。
在熔化过程中,控制炉温和时间,使原料彻底熔化,形成熔融态的钢液。
然后,将熔融的钢液从炉中倒入机床或浇注装置中,进行浇注成型。
在冷却和固化阶段,铸钢零件逐渐冷却,并逐渐由熔融态变为固态。
这个过程的时间和方式取决于零件的尺寸和形状。
大型铸钢件通常需要较长的时间来冷却和固化,以避免内部应力和缺陷。
在此阶段,应该注意零件的冷却速度和温度控制,以避免产生裂纹和变形。
最后是精加工。
经过冷却和固化后,铸钢零件还需要进行加工和整形,以满足最终零件的要求。
精加工包括切割、钻孔、铣削、磨削等工序。
这些工序需要根据零件的形状和尺寸,选择适当的加工工具和设备,进行精确、高效的加工。
综上所述,铸钢生产工艺是一个复杂的过程,需要经过模具设计和制造、原材料准备、熔化和浇注、冷却和固化、精加工等多个环节。
每个环节都需要严格控制,以确保最终产出的铸钢零件质量符合要求。
铸钢工艺的研究和不断改进,为制造业的发展提供了重要的支持。
铸钢工艺技术
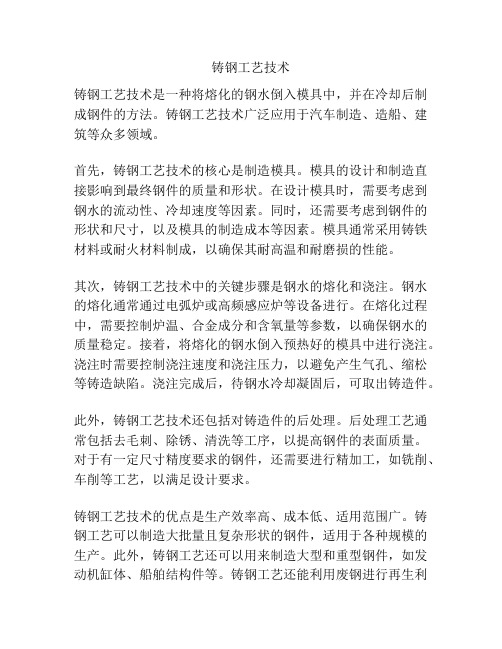
铸钢工艺技术铸钢工艺技术是一种将熔化的钢水倒入模具中,并在冷却后制成钢件的方法。
铸钢工艺技术广泛应用于汽车制造、造船、建筑等众多领域。
首先,铸钢工艺技术的核心是制造模具。
模具的设计和制造直接影响到最终钢件的质量和形状。
在设计模具时,需要考虑到钢水的流动性、冷却速度等因素。
同时,还需要考虑到钢件的形状和尺寸,以及模具的制造成本等因素。
模具通常采用铸铁材料或耐火材料制成,以确保其耐高温和耐磨损的性能。
其次,铸钢工艺技术中的关键步骤是钢水的熔化和浇注。
钢水的熔化通常通过电弧炉或高频感应炉等设备进行。
在熔化过程中,需要控制炉温、合金成分和含氧量等参数,以确保钢水的质量稳定。
接着,将熔化的钢水倒入预热好的模具中进行浇注。
浇注时需要控制浇注速度和浇注压力,以避免产生气孔、缩松等铸造缺陷。
浇注完成后,待钢水冷却凝固后,可取出铸造件。
此外,铸钢工艺技术还包括对铸造件的后处理。
后处理工艺通常包括去毛刺、除锈、清洗等工序,以提高钢件的表面质量。
对于有一定尺寸精度要求的钢件,还需要进行精加工,如铣削、车削等工艺,以满足设计要求。
铸钢工艺技术的优点是生产效率高、成本低、适用范围广。
铸钢工艺可以制造大批量且复杂形状的钢件,适用于各种规模的生产。
此外,铸钢工艺还可以用来制造大型和重型钢件,如发动机缸体、船舶结构件等。
铸钢工艺还能利用废钢进行再生利用,减少资源浪费和环境污染。
然而,铸钢工艺技术也存在一些局限性。
首先,由于钢水的高温和高压,铸钢工艺对设备要求较高。
其次,铸钢工艺中会产生一定数量的废料和废水,需要专门进行处理。
另外,对于一些对材料强度和性能要求较高的钢件,铸钢工艺可能无法满足其要求。
总之,铸钢工艺技术是一种重要的制造工艺,广泛应用于各个领域。
通过不断改进和创新,铸钢工艺技术将在未来发展中更加完善和成熟,为各个行业提供更高质量和更高效率的钢件制造服务。
- 1、下载文档前请自行甄别文档内容的完整性,平台不提供额外的编辑、内容补充、找答案等附加服务。
- 2、"仅部分预览"的文档,不可在线预览部分如存在完整性等问题,可反馈申请退款(可完整预览的文档不适用该条件!)。
- 3、如文档侵犯您的权益,请联系客服反馈,我们会尽快为您处理(人工客服工作时间:9:00-18:30)。
铸钢件的制造技术(一)作者:不明 转贴自:铸造之家 点击数:1016您要打印的文件是:铸钢件的制造技术(一)打印本文四、铸钢的熔炼铸钢的熔炼一般采用平炉,电弧炉和感应炉等。
平炉的特点是容量大、可利用废钢作原料、能准确控制钢的成分并能熔炼优质钢及低合金钢,多用于熔炼质量要求高的、大型铸钢件用的钢液。
三相电弧炉的开炉和停炉操作方便,能保证钢液的成分和质量、对炉料的要求不甚严格、容易升温,故能炼优质钢、高级合金钢和特殊钢等,是生产成型铸钢件的常用设备。
此外,采用工频或中频感应炉,能熔炼各种高级合金钢和碳含量极低的钢。
感应炉的熔炼速度快、合金元素烧损小、能源消耗少、且钢液质量高,即杂质含量少、夹杂少,适于小型铸钢车间采用。
近十多年来,生产清洁钢一直是各国铸钢业界广泛关注的问题,为进行这方面的研究,花费了可观的时间、金钱和人力。
对于铸钢业界,生产清洁钢的含义是:加强脱氧和防止出钢和浇注过程中的二次氧化,从而减少钢中和铸件表面上的氧化物夹杂。
说起来,这是个老问题,搞铸钢的谁都知道,但实际上大多数同仁对此并无切实的认识和了解。
据国外所作的统计分析,铸钢件的直接生产成本中,表面清理费用约占20%,其中,大部分是用于清除和焊修氧化夹杂缺陷的。
美国铸钢研究学会(SFSA)自1985年起进行了大量研究工作,从各类铸钢件(包括碳钢件、低合金钢件和中高合金钢件)中取样500件以上,作研究分析,结果表明:铸钢件表面上的宏观夹杂的来源如下:l83%是由于钢液脱氧不好和二次氧化;l14%来自造型材料;l2%来自炉渣;l1%来自耐火材料。
因此,铸钢件表面上形成宏观氧化物的主要原因是钢的清洁度不够好。
从而,铸造用钢的清洁度,可用每吨铸件表面上需清除的宏观夹杂物的体积来衡量,也可以用每吨铸件修补所用的焊条量来衡量。
当然,钢中微观夹杂物的数量,形态及分布状况也与其清洁度相关,但其影响较小。
在许多铸钢厂现场所作的调查表明:不同炉次之间的铸件,每吨铸件修补所需的焊条量差别很大;同一炉次所浇注的铸件,从最先浇注的到最后浇注的,每吨铸件的焊条用量差别不大。
而且,铸件上宏观夹杂物多的炉次约占20~25%。
这说明:熔炼方面容易失控的变数较多,而浇注过程中的变数较少。
铸钢件中也会含有其他杂质,如硫化物和氮含量等,但是,钢中的氮含量可以通过脱碳沸腾可靠地加以控制,碱性炉炼钢控制含硫量也不成问题,而且钢中硫化物的情况也与脱氧有关。
因此,加强脱氧和防止二次氧化是当前铸钢业界所面对的重大问题之一。
一. 钢的脱氧使钢脱氧方法很多,所用的脱氧剂也不一而足,这里只谈及主要的脱氧作业,即最终脱氧。
1.铝脱氧由于铝的脱氧能力强,对钢中FeO的溶有量影响很大,影响钢中铁-氧-硫三元素的平衡,因而对钢中硫化物的数量、形态及分布状况都有很大的影响。
在炼钢温度下,氧化物和硫化物在钢中都有一定的溶解度,在钢液凝固过程中,因氧化物和硫化物溶解度的变化,会按一定的规律析出非金属夹杂物。
所以,钢中的非金属夹杂物并不都是混杂在钢中的异物。
只用硅-锰脱氧,或加铝量很少,钢中残留铝量极低时,钢中溶解的氧较多。
此时,硫化物的溶解度下降,在钢液凝固初期,就有硫化物或以硫化物为主的硫氧复合化合物析出。
这样形成的硫化夹杂物是较大的、分布不规的近球形夹杂物,即第I类硫化物夹杂。
这类夹杂物对钢的韧性影响很小。
但是,在此种条件下,铸件中的晶粒粗大,而且很难避免气孔、针孔等疵病。
实际上,此种工艺是不可取的。
加铝量较多,钢中残留铝量为0.01-0.03%时,钢中氧的溶有量很低,硫化物在钢中的溶解度增大,不在钢液的凝固初期析出,而在稍后钢液温度进一步下降后,以硫化物与铁的共晶形式析出,分布在晶界上,呈连续网状,即第II类硫化物夹杂。
在此情况下,钢的韧性显著下降。
此种工艺也不可取。
加铝量够多,钢中残留铝量在0.04%以上时,铝会和硫生成Al2S3。
Al2S3又与硫化铁(锰)形成复合硫化物,其在钢中的溶解度很低,在钢的凝固初期析出。
这种情况下,硫化物是尺寸较大、形状不太圆、分布也不规则的夹杂物,即第I II类硫化夹杂物。
这种夹杂物对钢的韧性影响也不大。
钢终脱氧所用的铝量,是考虑其脱氧效果和对硫化物的影响而确定的。
不加铝则钢不能完全脱氧;加铝量太少,则钢既不能有效地脱氧,又不能细化晶粒;加铝量多,但不超过每吨钢0.7kg,则有招致第II类硫化物的危险。
因此,作为最终脱氧剂的铝,用量一般是每吨钢0.8~1.2kg。
从前面谈到的几点,对加铝量下限(每吨钢0.8kg)的确定是不难理解的。
那么,铝既然是很好的脱氧剂,多加些岂不更好?为什么要规定加入量的上限呢?第二次世界大战初期,发现有的铸钢件在调质(淬火加回火)后脆断,断口为石状或冰糖状。
由于其后果是灾难性的,立即成为研究的课题。
起初还以为是氢脆,到1947年才确认此种缺陷的主要原因是氮化铝析出。
AlN可以溶于钢液,在铸钢件凝固的后期,在较低的温度下沿晶界析出呈网状,致使铸件脆断。
由于铝的脱氧效果好,铸钢厂为确保铸件不出气孔,随意多加的事是十分常见的。
同时,电弧炉炼的钢含氮量较高,一般为100ppm左右,如脱碳沸腾作业不佳,还会高于此值。
在钢中残留铝量高、含氮量高的情况下,铸件就易于发生石状断口脆断。
我国的铸钢厂中,这种情况也并不鲜见。
因此,严格控制加铝量的上限,是十分必要的。
在这里顺便还要说一说,发生石状断口脆断并不只限于经调质处理的低合金钢铸件,经正火、回火的马氏体不锈钢铸件也可出现,还有报道说,低碳钢铸件也发生过此种脆断。
此外,虽然AlN析出是造成石状析口脆断的主要原因,但也不是唯一的原因,沿晶界析出的硼化物,碳化物或硫化物也都可以使铸件发生脆断。
脆断总与晶界缺陷有关。
每一家铸钢厂都要在炼钢时加铝,也都会加铝。
但是,如果问加铝的工艺是否妥当?加铝的收得率是否稳定?恐怕会有不少的铸钢厂难以回答。
铝的密度不及钢液的1/2,在炉中加铝,除采用插入方式外,容易裹在钢渣中不易与钢液作用。
如果所用的铝块大小不一,就更难有稳定的效果。
为了严格控制钢中残留铝量,国外有的铸钢厂不用铝而用含Al3 5%左右的铝铁合金。
铝铁合金的密度约为6.15g/m3,比钢渣的密度高,与钢液的密度相近。
虽成本略高,但脱氧效果好而且稳定。
2.复合脱氧剂脱氧到目前为止,铸钢厂所用的复合脱氧剂,都以硅和钙为主要成分。
60多年以前,就有人注意到钙在钢中的脱氧作用。
钙在钢中溶解度很小,但它与氧、硫的亲和力都很强。
在钢的脱氧过程中,钙和铝有互补增益的共同作用,很像硅和锰的共同作用。
氧化钙可以和氧化铝复合成易熔的铝酸钙,甚至在src=UploadFiles/20075895621355.gif炼钢温度下可以是液相,见附图。
740)this.width=740 border=undefi ned>附图CaO-AL2O3相图铸钢件的制造技术(二)作者:不明 转贴自:铸造之家 点击数:890您要打印的文件是:铸钢件的制造技术(二)打印本文合金Ca Si Ba Al Fe 国外常用的硅钙合金28-32 60-65 -- -- -- 硅-钙-钡合金(Calsibar) 14-17 57-62 14-18 -- <5 硅-钙-钡-铝合金(Hypercal)10-13 38-40 9-12 19-21 <7 我国硅-钙-钡-铝合金(YB/T067-1995) ≥12≥9≥6 ≥30 ≥35 ≥40 ≥9 ≥9≥ ≥12 ≥16 ≥12 ≥8--很低。
在此情况下,注意以下几点,并严格工艺控制,就可能有较明显的效果。
首先,要保证钢液脱氧良好,国外铸钢厂出钢前钢渣中的FeO含量要求在0.5%以下。
目前我国多数铸钢厂渣中FeO含量都在1%以上,能达到0.8%的为数不多。
近期内应努力做到渣中FeO不超过0.5%。
这不需要搞技术改造,也无需投资,只要求敬业和认真。
其次是要严格控制碳钢和低合金钢中的硅含量在0.5%~0.6%的水平,以保证钢液有防止二次氧化的脱氧余力。
不少铸钢厂至今还按含硅0.17%~0.37%或0.2%~0.4%的要求生产,这样的标准早已过时,并已废止了。
最终脱氧用的铝,块度应有要求,加入量和加入方法应严格控制。
3.钢包中加钙补充脱氧目前,在钢包中加钙补充脱氧是最有较的克服二次氧化影响的措施之一,但所用的含钙材料和加入方法至关重要。
国外不少铸钢厂试用过在钢包中加CaC2,效果都不好。
也有铸钢厂在出钢时,将硅钙合金投入钢液,由于合金漂浮在表面,收得率很低。
在包中加硅钙合金,则合金浮在钢渣表面。
最有较的方法是喂丝法。
用铁皮包裹的硅钙粉通过钢渣插入钢液中,不到3秒钟硅钙合金就可熔化于钢液中。
钙在钢中的作用,前面已经谈过。
每吨钢的加钙量约为0.3kg。
国外铸钢厂采用喂丝法后,铸件上的宏观夹杂缺陷平均减少4 0%。
4.钢包中用等离子弧精炼在钢包上方装一中间有小孔的石墨电极,出钢后,使电极与钢液间产生电弧,再自电极中心的孔吹入氩气以产生等离子弧,并使之稳定。
同时,自钢包底部的多孔塞吹入氩气搅拌钢液,使之脱氧。
氩气的流率可调。
搅拌速率较高,则有利于均匀温度并脱S;低速搅拌,则使钢液中的夹杂物上浮。
等离子弧的极性也是可变的,负极性用于加热钢液和钢渣;正极性则用于脱氧和脱硫。
因此种装置。
可使钢液中含氧量很低,脱硫效果也好,可得到非常清洁的钢。
与酸性电弧炉配用,可使钢液的品质达到碱性炉钢的水平。
后期,还可用喂丝法加钙,以控制硫化物和夹杂物的形态。
此种方法,小型铸钢厂不宜采用。
5.氩气保护工艺尚待探索钢液被二次氧化,主要是因其暴露于大气中的氧,因而自然会想到用氩气予以保护。
氩的密度高于空气,有可能使其处于钢液和大气之间,形成保护气氛。
由于铸钢厂出钢和浇注的情况复杂,国外不少铸钢厂试用过多种多样的氩气保护方法,如浇注时用氩气保护钢流、在包中用氩气覆盖钢液、直接向钢液表面吹氩等。
但是,迄今为止还未找到经济而有效的屏蔽方法,这方面尚有待进一步探索。