长输天然气管道内腐蚀直接评价
ICDA管道内腐蚀直接评价方法探析

ICDA管道内腐蚀直接评价方法探析在传统的管道内腐蚀评价中,采用了一些常见的方法,比如电化学法、超声波检测法,X射线检测法等。
这些方法虽然具有一定的可行性,但是在实际应用中存在着一些不足之处,例如需要大量的人力物力、高昂的成本、操作复杂等。
需要进一步探索管道内腐蚀直接评价的方法,提高评价的准确性和效率,保障管道的安全运行。
二、ICDA管道内腐蚀直接评价方法ICDA(Internal Corrosion Direct Assessment)管道内腐蚀直接评价方法是一种目前比较先进的评价方法。
该方法主要是通过对管道内壁进行直接的腐蚀评价,以确定管道内部的腐蚀情况,并进一步确定管道的安全状态。
ICDA方法主要包括以下几个步骤:1.数据收集:需要对管道进行全面的数据收集,包括管道的材质、管道使用年限、介质性质等信息,并结合实地调查记录管道的运行情况。
2.风险评估:在数据收集的基础上,对管道的腐蚀风险进行评估,包括腐蚀速率、腐蚀形式、腐蚀位置等因素进行综合分析。
3.直接评价:通过对管道内壁进行直接腐蚀评价,采用现代化的检测设备,结合实际情况对管道内部腐蚀情况进行准确评估。
4.安全评价:利用评估结果进行管道的安全评价,确定管道的安全状态,包括安全使用寿命、修复方案等。
ICDA方法的优点在于可以直接对管道内部进行腐蚀评价,减少了对外部环境的依赖,评价的准确性和可靠性更高。
而且ICDA方法相对传统方法来说,操作简单,成本低,效率高,更适合实际工程中的应用。
三、ICDA方法的不足尽管ICDA方法在管道腐蚀直接评价中具有一定的优势,但是也存在一些不足之处需要进一步改进和完善。
1.检测技术:目前,ICDA方法中所采用的检测技术还不够成熟,对于一些特殊材质和结构的管道难以有效检测,需要进一步研发和改进相关技术。
2.评价准确性:由于管道内腐蚀具有一定的随机性,ICDA方法在评价准确性上还需要不断提高,避免误判。
3.数据分析:ICDA方法中数据量大,需要进行大量的数据分析工作,当前的数据分析方法还不够完善,需要引入更多的先进技术和算法。
珠三角某天然气管段内腐蚀直接评价技术应用

66
TOTAL CORROSION CONTROL VOL.34 No.10 OCT. 2020
经验交流 Experience Exchange
完整性检测常用方法有内检测、直接评价、水压试 积液的位置;在详细检查中采用超声测厚,C扫描、
验[1-3]。
相控阵等无损检测技术测试这些最容易积液位置的
相较于内检测与水压试验,直接评价技术具 内部腐蚀情况;后评价部分是评价ICDA方法的有效 有成本低、工作量小、无清管限制、无需停输等优 性并确定再评价的时间间隔[6]。
本文挑选分输站至C工厂这一典型管段为例,
适用于正常条件下输送干气但可能遭受非经常性短 详细介绍预评估、间接评估、详细检查、后评价各
期液体侵扰而引起损坏的天然气管道,腐蚀性的水 步骤。
经验交流 Experience Exchange
珠三角某天然气管段内
腐蚀直接评价技术应用
侯向峰
(中海广东天然气有限责任公司,广东 珠海 519000)
摘 要:内腐蚀直接评价ICDA作为管道完整性管理评估技术之一,因其成本低、工作量小、
无清管条件限制、无需停输等优点而受到国内外专家学者的重视,特别是对于无法开展内检测的
Direct Assessment Technology (ICDA) has attracted the attention of experts and scholars because of
its low cost, small workload, no pigging conditions, no shutdown and other advantages, especially for
evaluation technology plays an important role in pipeline integrity.
天然气长输管道内材料腐蚀原因分析及防护控制措施

天然气长输管道内材料腐蚀原因分析及防护控制措施摘要:随着社会经济水平的不断上升,促进了长输天然气管道的快速发展,并且人们对环境提出了更高的要求。
对于天然气长输管道被腐蚀这一问题而言,它不仅会对其运输产生重要影响,而且还会威胁到人们的生命财产安全。
那么,为了使该问题能够得到有效的处理和解决,就应做好管道腐蚀的预防和处理工作,对防腐处理的重要性进行充分的认识,并针对相关问题制定完善的解决方案和控制措施。
关键词:天然气长输管;防腐措施;应用引言通常情况下,长输天然气管道是以架空或填埋的方式进行铺设的,所以很容易受环境和气候因素的影响而出现管道腐蚀的问题。
一旦天然气管道遭到腐蚀,就会使大量的气体泄露出来,甚至会出现严重的火灾,不管是在资源方面,还是在人力、物力方面,都造成了极大的损失。
如果天然气管道因腐蚀而发生爆炸,就会造成严重的后果,不仅威胁到人们的财产安全,而且还污染到大气环境。
因此,需要对长输天然气管道的腐蚀问题进行深层次的分析和研究,并有针对性的选择有效的预防措施和处理方案。
在一定程度上,可以延长长输天然气管道的使用寿命,进而为长输天然气管道的安全运行提供了重要的基础保障。
1长输天然气管道防腐的重要性对于长输天然气管道,它可以对天然气能源进行长距离的传输。
在处理管道时,通常会采用地下埋设和架空敷设这两种方法,但该方法会受各种因素的影响而导致管道出现腐蚀的问题。
由于土壤具有一定的腐蚀性,所以很容易使管道的外壁被侵蚀,大大的缩短了管道的使用寿命。
如果天然气管道长时间处于腐蚀状态,就会加大天然气管道出现泄漏事件的概率,会对大气环境造成严重的污染,甚至还会发生一些危害性较高的事故,比如火灾、爆炸等,对人们的生命财产安全造成严重的威胁。
因此,需要采取合理、有效的解决办法来对长输天然气管道进行更好的预防与保护,从而提升天然气能源传输的安全性、稳定性,大幅度的降低了天然气管道出现泄漏问题,保证了人们的生命财产安全。
长输管道的腐蚀风险评价
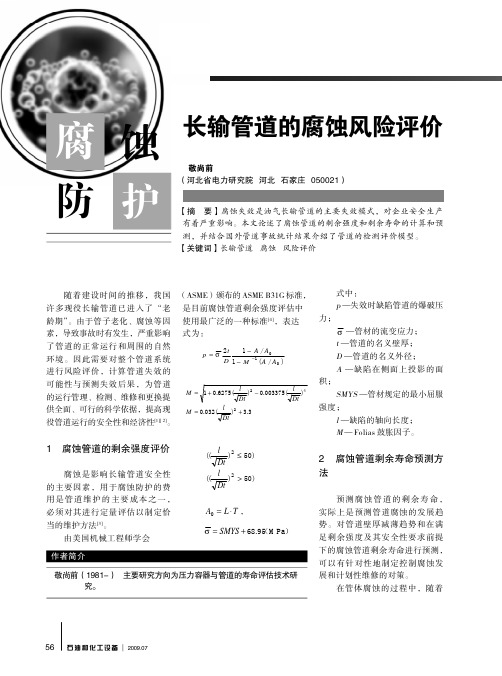
事故抢险时间,取其平均值,也可 以根据评估要求取其最大值。
4 结束语
腐蚀管道的安全至关重要, 我国目前还缺乏完整和有效的保 证体系。管道的风险评价可以供 制定和发展我国管道安全评价体 系参考借鉴;是保证现役管道安全 可靠运行必不可少和亟待深入开 展的一项工作;对于当前热门的管 道完整性研究领域,发展有效的 完整性检测和评价技术极其重要。 因此,应加强风险评价的技术跟 踪,尽快开发适用于现役管道风 险评估的软件系统,提高我国石 化管道运行的可靠性和经济性。
在管体腐蚀的过程中,随着
56 石 油 和 化 工 设 备 2009.07
腐蚀防护
FU SHI FANG HU
时间的增加,对整条管道而言,腐 蚀缺陷点数、腐蚀区域、腐蚀程度 和失效概率呈增加趋势,如不经 维修,出现泄漏或破裂的次数会 逐年增加。但由于不同区段管体 腐蚀条件存在差异,腐蚀的发展 趋势也不尽相同。
hazard pipelines 2000
9.钱成文.牛国赞 基于风险分析的管道检测(RBI)与评价[期刊论文]-油气储运 2000(08)
相似文献(10条)
1.期刊论文 赵新潮.罗艳红.盘丁铨 基于Smart-CET技术石油长输管道内腐蚀实时在线监测系统构建 -科学时代(上半月)2010,""(4)
Smart-CET技术是美国霍尼韦尔公司旗下的InterCorr国际腐蚀公司开发的自动电化学监测专利技术,本文论述了该技术在石油长输管道的现场适用性.其可以对长输管道内腐蚀状态进 行实时检测、动态跟踪、分析和评估,反映内腐蚀变化过程,从而减小腐蚀危害.
2009.07 石 油 和 化 工 设 备 57
工 艺 创新
表 2 不同等级外腐蚀泄漏事故的发生频率[3]
天然气管道内腐蚀直接评价方法原理与范例
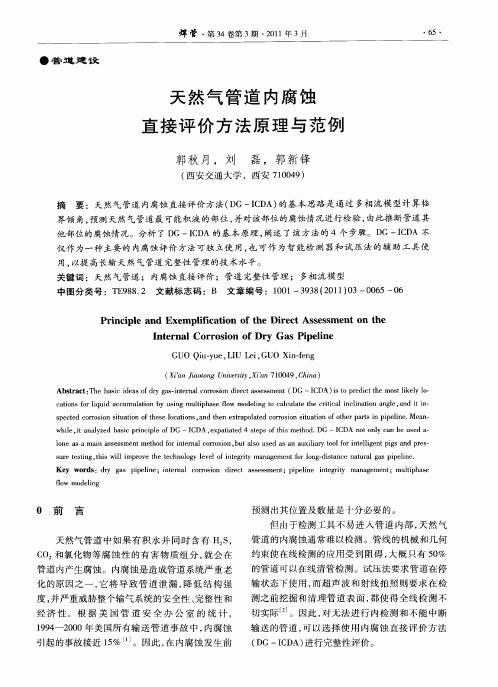
界倾 角 , 预测 天 然 气管道 最 可 能积液 的部位 , 并对该部位 的腐 蚀情况进 行检验 , 由此推 断管道其 他部位 的腐蚀情 况。分析 了 D G—I D 的基本 原 理 , CA 阐述 了该 方 法的 4个 步骤 。D G—ID C A不
仅 作为 一种 主要 的 内腐 蚀评 价 方法 可独立 使 用 , 可作 为智 能检 测 器和 试 压 法的 辅 助 工具 使 也
0 前
言
预 测 出其位 置及 数量 是 十分必 要 的 。
但 由于 检测 工 具不 易进 入 管 道 内部 , 天然 气 天然 气管 道 中如 果 有 积 水 并 同时 含 有 H S ,,
C: O 和氯 化物 等腐 蚀 性 的有 害物 质 组 分 , 就会 在
管 道 的 内腐 蚀通 常难 以检 测 。管线 的机 械 和几何
约束 使在 线 检测 的应 用 受 到 阻碍 , 大概 只 有 5 % 0
管道 内产 生腐蚀 。内腐蚀 是造 成管 道 系统严 重 老 化 的原 因之 一 , 将 导 致 管 道 泄 漏 , 低 结 构 强 它 降 度 , 严重 威胁整 个输 气 系统 的安全 性 、 并 完整性 和 经济 性。根 据 美 国 管 道 安 全 办 公 室 的 统 计 , 19 - 2 0 9 4 0 0年美 国所有 输 送 管道 事故 中 , 内腐 蚀 引起 的事 故接 近 1 % 。因此 , 内腐 蚀发 生 前 5 在
用, 以提 高长输天 然 气管道 完整性 管理 的技 术 水平 。
关键 词 :天 然 气管道 ;内腐蚀 直接 评 价 ;管道 完整性 管理 ; 多相 流模 型 中图分 类号 :T 9 8 2 文 献标 志码 :B 文 章编 号 :10 3 3 ( 0 1 0 5— 6
试析天然气长输管道内腐蚀原因分析及控制
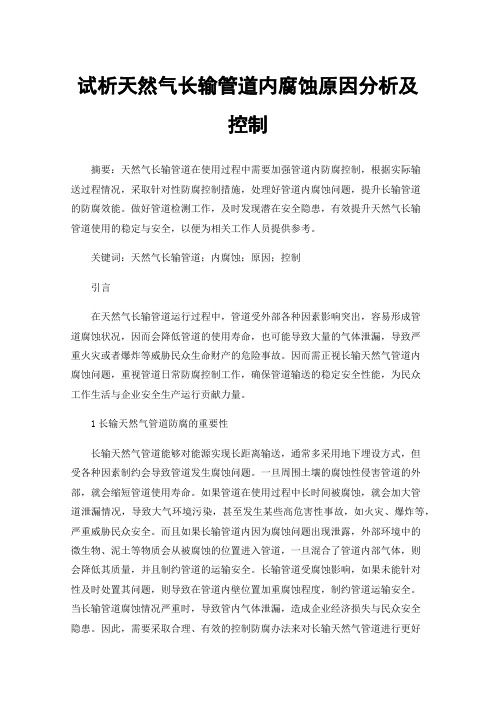
试析天然气长输管道内腐蚀原因分析及控制摘要:天然气长输管道在使用过程中需要加强管道内防腐控制,根据实际输送过程情况,采取针对性防腐控制措施,处理好管道内腐蚀问题,提升长输管道的防腐效能。
做好管道检测工作,及时发现潜在安全隐患,有效提升天然气长输管道使用的稳定与安全,以便为相关工作人员提供参考。
关键词:天然气长输管道;内腐蚀;原因;控制引言在天然气长输管道运行过程中,管道受外部各种因素影响突出,容易形成管道腐蚀状况,因而会降低管道的使用寿命,也可能导致大量的气体泄漏,导致严重火灾或者爆炸等威胁民众生命财产的危险事故。
因而需正视长输天然气管道内腐蚀问题,重视管道日常防腐控制工作,确保管道输送的稳定安全性能,为民众工作生活与企业安全生产运行贡献力量。
1长输天然气管道防腐的重要性长输天然气管道能够对能源实现长距离输送,通常多采用地下埋设方式,但受各种因素制约会导致管道发生腐蚀问题。
一旦周围土壤的腐蚀性侵害管道的外部,就会缩短管道使用寿命。
如果管道在使用过程中长时间被腐蚀,就会加大管道泄漏情况,导致大气环境污染,甚至发生某些高危害性事故,如火灾、爆炸等,严重威胁民众安全。
而且如果长输管道内因为腐蚀问题出现泄露,外部环境中的微生物、泥土等物质会从被腐蚀的位置进入管道,一旦混合了管道内部气体,则会降低其质量,并且制约管道的运输安全。
长输管道受腐蚀影响,如果未能针对性及时处置其问题,则导致在管道内壁位置加重腐蚀程度,制约管道运输安全。
当长输管道腐蚀情况严重时,导致管内气体泄漏,造成企业经济损失与民众安全隐患。
因此,需要采取合理、有效的控制防腐办法来对长输天然气管道进行更好的防护工作,进一步提升天然气能源传输的安全性、稳定性,有效降低天然气管道的泄漏问题,有效保障社会经济民众生活生产水平稳定发展。
2长输天然气管道内腐蚀原因2.1 内部介质因素通常情况下,天然气长输管道一方面是长距离运输,另一方面输送量较大,在整个使用过程中需要保持高温高压环境。
输气管道腐蚀控制措施及评价
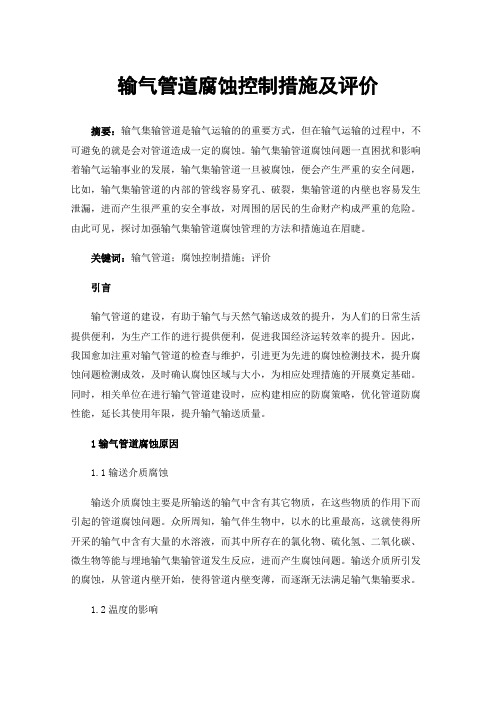
输气管道腐蚀控制措施及评价摘要:输气集输管道是输气运输的的重要方式,但在输气运输的过程中,不可避免的就是会对管道造成一定的腐蚀。
输气集输管道腐蚀问题一直困扰和影响着输气运输事业的发展,输气集输管道一旦被腐蚀,便会产生严重的安全问题,比如,输气集输管道的内部的管线容易穿孔、破裂,集输管道的内壁也容易发生泄漏,进而产生很严重的安全事故,对周围的居民的生命财产构成严重的危险。
由此可见,探讨加强输气集输管道腐蚀管理的方法和措施迫在眉睫。
关键词:输气管道;腐蚀控制措施;评价引言输气管道的建设,有助于输气与天然气输送成效的提升,为人们的日常生活提供便利,为生产工作的进行提供便利,促进我国经济运转效率的提升。
因此,我国愈加注重对输气管道的检查与维护,引进更为先进的腐蚀检测技术,提升腐蚀问题检测成效,及时确认腐蚀区域与大小,为相应处理措施的开展奠定基础。
同时,相关单位在进行输气管道建设时,应构建相应的防腐策略,优化管道防腐性能,延长其使用年限,提升输气输送质量。
1输气管道腐蚀原因1.1输送介质腐蚀输送介质腐蚀主要是所输送的输气中含有其它物质,在这些物质的作用下而引起的管道腐蚀问题。
众所周知,输气伴生物中,以水的比重最高,这就使得所开采的输气中含有大量的水溶液,而其中所存在的氯化物、硫化氢、二氧化碳、微生物等能与埋地输气集输管道发生反应,进而产生腐蚀问题。
输送介质所引发的腐蚀,从管道内壁开始,使得管道内壁变薄,而逐渐无法满足输气集输要求。
1.2温度的影响温度是影响输气管道运行的重要因素。
输气在实际输送过程中,其温度并不是一成不变的,而是处于时刻变化状态中,加之外界温度变化的影响,管道腐蚀的概率随之增加。
同时,输气管道位于地下的部分较多,其初始埋设深度的不同,会使得温度对其的影响有所差异,若管道设计线路不同,温度的影响也随之产生变化,温度的提高,会增加管道腐蚀概率。
同时,土壤结构成分与其含水量等均会对输气管道的外壁产生一定影响,使其产生腐蚀现象,甚至可能导致输气管道出现泄漏问题,安全风险随之增加,为人们安全带来较大威胁。
内腐蚀直接评价标准

内腐蚀直接评价标准
内腐蚀直接评价标准应包括以下方面:
1.内腐蚀程度:根据腐蚀量大小和深度来评估内腐蚀程度,可以采用
切割法、X射线透视、超声波检测等方法进行评价。
2.腐蚀分布范围:评估内腐蚀在管道、容器等设备内的分布范围,包
括局部腐蚀、范围腐蚀、点腐蚀等,以便制定相应的检修计划。
3.腐蚀速率:评估内腐蚀的速率,包括初始速率和稳态速率,以便制
定定期检查和维护计划。
4.腐蚀质量:评估腐蚀产生的物质对设备的影响,如造成管道、容器
等设备的损坏或漏气等,以便确定应采取的修理措施。
5.安全风险等级:根据内腐蚀的程度、分布范围、速率和质量等因素,评估设备的安全风险等级,以便制定相应的管控措施和预防措施。
浅谈燃气管道防腐技术及其腐蚀评价
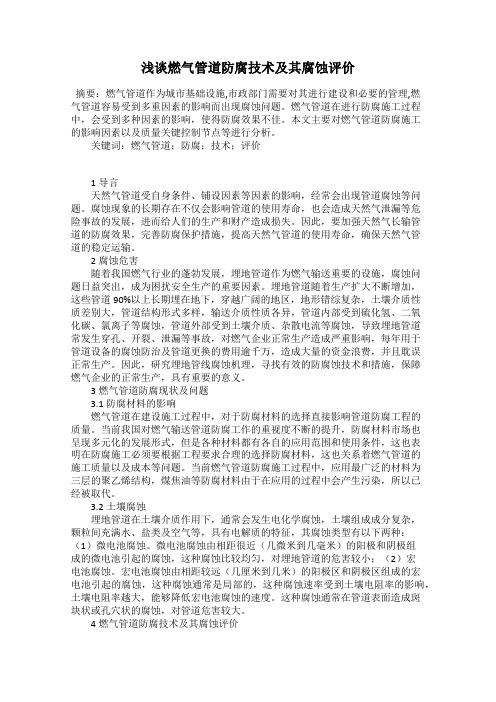
浅谈燃气管道防腐技术及其腐蚀评价摘要:燃气管道作为城市基础设施,市政部门需要对其进行建设和必要的管理,燃气管道容易受到多重因素的影响而出现腐蚀问题。
燃气管道在进行防腐施工过程中,会受到多种因素的影响,使得防腐效果不佳。
本文主要对燃气管道防腐施工的影响因素以及质量关键控制节点等进行分析。
关键词:燃气管道;防腐;技术;评价1导言天然气管道受自身条件、铺设因素等因素的影响,经常会出现管道腐蚀等问题。
腐蚀现象的长期存在不仅会影响管道的使用寿命,也会造成天然气泄漏等危险事故的发展,进而给人们的生产和财产造成损失。
因此,要加强天然气长输管道的防腐效果,完善防腐保护措施,提高天然气管道的使用寿命,确保天然气管道的稳定运输。
2腐蚀危害随着我国燃气行业的蓬勃发展,埋地管道作为燃气输送重要的设施,腐蚀问题日益突出,成为困扰安全生产的重要因素。
埋地管道随着生产扩大不断增加,这些管道90%以上长期埋在地下,穿越广阔的地区,地形错综复杂,土壤介质性质差别大,管道结构形式多样,输送介质性质各异,管道内部受到硫化氢、二氧化碳、氯离子等腐蚀,管道外部受到土壤介质、杂散电流等腐蚀,导致埋地管道常发生穿孔、开裂、泄漏等事故,对燃气企业正常生产造成严重影响,每年用于管道设备的腐蚀防治及管道更换的费用逾千万,造成大量的资金浪费,并且耽误正常生产。
因此,研究埋地管线腐蚀机理,寻找有效的防腐蚀技术和措施,保障燃气企业的正常生产,具有重要的意义。
3燃气管道防腐现状及问题3.1防腐材料的影响燃气管道在建设施工过程中,对于防腐材料的选择直接影响管道防腐工程的质量。
当前我国对燃气输送管道防腐工作的重视度不断的提升,防腐材料市场也呈现多元化的发展形式,但是各种材料都有各自的应用范围和使用条件,这也表明在防腐施工必须要根据工程要求合理的选择防腐材料,这也关系着燃气管道的施工质量以及成本等问题。
当前燃气管道防腐施工过程中,应用最广泛的材料为三层的聚乙烯结构,煤焦油等防腐材料由于在应用的过程中会产生污染,所以已经被取代。
长输天然气管道完整性管理与管道腐蚀检测技术

长输天然气管道完整性管理与管道腐蚀检测技术所谓的管道完整性主要指的是针对目前在用的管道实际运行状况从定量以及定性角度进行全面分析,在具体的管道完整性评价过程中管道腐蚀检测是一个重要的组成部分,是全面获取管道实际运行信息的有效手段,充分利用管道检测手段能够实现对各种管道问题进行有针对性的处理,从而最大程度保障管道实现安全、稳定运行。
标签:长输管道;完整性管理;腐蚀检测引言天然气经过开采之后需要通过集输管道集中输送后在净化厂进行深度处理,长输管道在运输天然气的过程中是将天然气置于密闭的环境下进行输送,这样就形成了一个密闭的输气系统。
长输管道通常情况下分布范围比较广,而且在其建设过程中所面临的地域类型也比较复杂,发生事故后会造成严重的环境污染事故,甚至造成人员伤亡事故,因此,必须要进一步提升长输管道完整性管理的整体水平,才能充分保障长输管道实现安全、稳定运行。
1 管道完整性管理所谓的管道完整性管理主要指的是在管道长期处于安全可靠的可控运行工况下时,相关的管理人员通过采取多种手段对管道事故的发生进行有效预防。
管道完整性在很大程度上与管道设计压力、施工作业、运营维护等各个环节都紧密联系。
针对在役管道完整性进行管理的过程中必须要求相关的管理单位针对管道运行过程中所面临的风险因素进行有效识别,并在此基础上制定出合理的控制措施。
针对一些可能导致管道出现失效等风险的因素進行有效检测,对管道适应性进行合理评估,针对识别过程中出现的不利因素进行进一步改善,实现管道运行风险管理水平的进一步提升,让管道能够始终处在可接受的风险范围内运行。
针对管道的完整性管理是一个循序渐进、持续的监控管理过程,需要通过一定的周期针对管道进行进一步检测、风险评估,并采取风险控制措施,让管道的事故风险得到有效控制,保证管道实现经济、合理、安全运行。
天然气长输管道在实际运行过程中由于会受到腐蚀、老化、疲劳、自然灾害以及机械损伤等各种因素影响从而引起失效,因此必须要针对管道进行持续性的风险分析、检测、完整性评价和合理的运维管理[1]。
长输天然气管道内腐蚀分析与对策
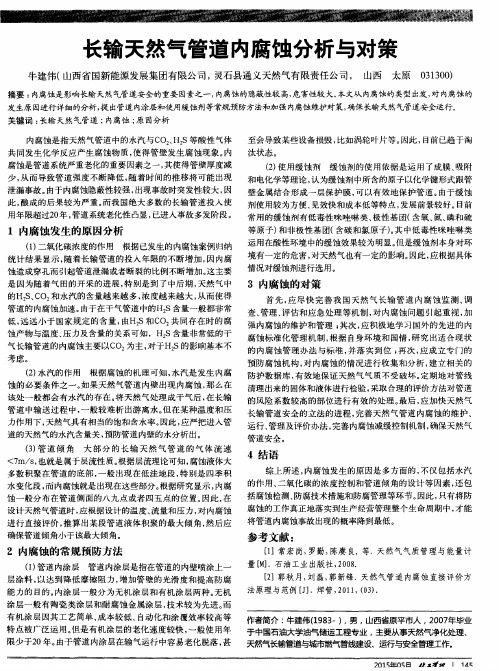
查、 管理 、 评 估和 应急 处理 等机制 , 对内腐 蚀 问题 引起重 视 , 加
强 内腐 蚀的 维护和 管理 ; 其次 , 应 积极地 学 习国外的 先进 的内
腐蚀标 准化 管理 机制 , 根 据 自身环境 和 国情 , 研究 出适 合现状 的 内腐 蚀管理 办 法 与标 准 , 并 落 实到 位 ; 再次, 应成 立专 门 的 预防腐 蚀机 构 , 对 内腐蚀 的情 况进行 收集 和分 析 , 建立 相关 的
和 电化 学等理论 , 认 为缓蚀剂 中所含 的原 子以化 学键形式 跟管
壁金 属结 合形 成一 层保护 膜 , 可以 有效 地保护 管道 。 由于缓 蚀 剂使用 较为方便 、 见效 快和成本 低等特 点 , 发 展前景较 好。 目前 常用 的缓蚀 剂有 低毒性 咪唑 啉类 、 极性 基 团( 含氧、 氮、 磷和 硫
蚀一 般分 布在 管道 侧面的 八九 点或者 四五 点的位 置 。 因此 , 在
设计 天然气管 道时 , 应 根据设计 的温度 、 流量和压 力 , 对 内腐蚀 确保 管道倾角小于 该最大倾 角。
括腐蚀检测 、 防 腐技术措施 和防腐 管理等 环节。 因此 , 只有将防 腐蚀的 工作真正地落 实到生 产经营管 理整个生 命周期 中 , 才 能
情况对缓蚀 剂进行选 用。
3 内腐 蚀的 对策
首先, 应 尽 快 完 善我 国天 然 气 长输 管 道 内 腐 蚀监 测 、 调
管 道的 内腐蚀加速 。 由于 在干 气管道 中的H s含量 一般都非 常
低, 远 远 小于 国家 规 定的含 量 , 由H2 S和C 0: 共 同存 在 时的 腐 蚀 产物与 温度 、 压力及含 量的关 系可知 ,H: s含量 非常低 的干
天然气集输管道内腐蚀直接评价方法研究
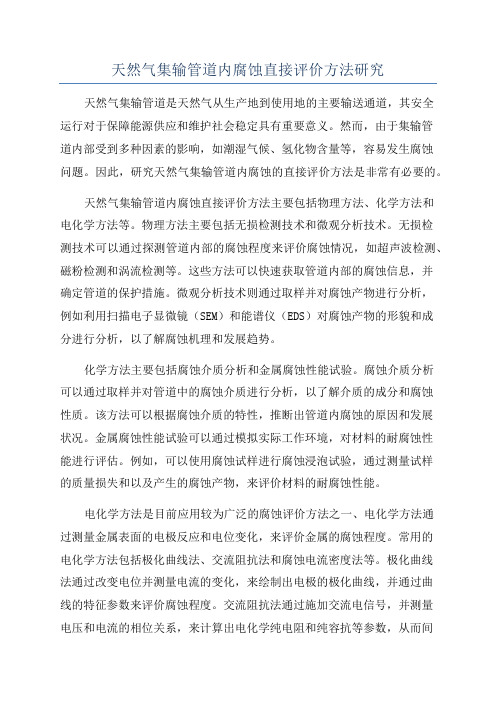
天然气集输管道内腐蚀直接评价方法研究天然气集输管道是天然气从生产地到使用地的主要输送通道,其安全运行对于保障能源供应和维护社会稳定具有重要意义。
然而,由于集输管道内部受到多种因素的影响,如潮湿气候、氢化物含量等,容易发生腐蚀问题。
因此,研究天然气集输管道内腐蚀的直接评价方法是非常有必要的。
天然气集输管道内腐蚀直接评价方法主要包括物理方法、化学方法和电化学方法等。
物理方法主要包括无损检测技术和微观分析技术。
无损检测技术可以通过探测管道内部的腐蚀程度来评价腐蚀情况,如超声波检测、磁粉检测和涡流检测等。
这些方法可以快速获取管道内部的腐蚀信息,并确定管道的保护措施。
微观分析技术则通过取样并对腐蚀产物进行分析,例如利用扫描电子显微镜(SEM)和能谱仪(EDS)对腐蚀产物的形貌和成分进行分析,以了解腐蚀机理和发展趋势。
化学方法主要包括腐蚀介质分析和金属腐蚀性能试验。
腐蚀介质分析可以通过取样并对管道中的腐蚀介质进行分析,以了解介质的成分和腐蚀性质。
该方法可以根据腐蚀介质的特性,推断出管道内腐蚀的原因和发展状况。
金属腐蚀性能试验可以通过模拟实际工作环境,对材料的耐腐蚀性能进行评估。
例如,可以使用腐蚀试样进行腐蚀浸泡试验,通过测量试样的质量损失和以及产生的腐蚀产物,来评价材料的耐腐蚀性能。
电化学方法是目前应用较为广泛的腐蚀评价方法之一、电化学方法通过测量金属表面的电极反应和电位变化,来评价金属的腐蚀程度。
常用的电化学方法包括极化曲线法、交流阻抗法和腐蚀电流密度法等。
极化曲线法通过改变电位并测量电流的变化,来绘制出电极的极化曲线,并通过曲线的特征参数来评价腐蚀程度。
交流阻抗法通过施加交流电信号,并测量电压和电流的相位关系,来计算出电化学纯电阻和纯容抗等参数,从而间接评价腐蚀情况。
腐蚀电流密度法则是通过测量电极的腐蚀电流密度,并结合电位变化,来评价腐蚀的严重程度。
综上所述,天然气集输管道内腐蚀直接评价方法研究是为了实时了解管道腐蚀的情况和趋势。
长输油气管道风险评价及防腐探讨
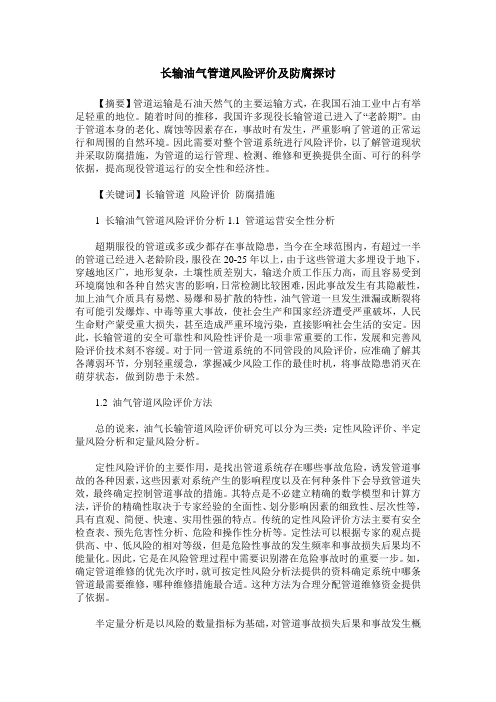
长输油气管道风险评价及防腐探讨【摘要】管道运输是石油天然气的主要运输方式,在我国石油工业中占有举足轻重的地位。
随着时间的推移,我国许多现役长输管道已进入了“老龄期”。
由于管道本身的老化、腐蚀等因素存在,事故时有发生,严重影响了管道的正常运行和周围的自然环境。
因此需要对整个管道系统进行风险评价,以了解管道现状并采取防腐措施,为管道的运行管理、检测、维修和更换提供全面、可行的科学依据,提高现役管道运行的安全性和经济性。
【关键词】长输管道风险评价防腐措施1 长输油气管道风险评价分析1.1 管道运营安全性分析超期服役的管道或多或少都存在事故隐患,当今在全球范围内,有超过一半的管道已经进入老龄阶段,服役在20-25年以上,由于这些管道大多埋设于地下,穿越地区广,地形复杂,土壤性质差别大,输送介质工作压力高,而且容易受到环境腐蚀和各种自然灾害的影响,日常检测比较困难,因此事故发生有其隐蔽性,加上油气介质具有易燃、易爆和易扩散的特性,油气管道一旦发生泄漏或断裂将有可能引发爆炸、中毒等重大事故,使社会生产和国家经济遭受严重破坏,人民生命财产蒙受重大损失,甚至造成严重环境污染,直接影响社会生活的安定。
因此,长输管道的安全可靠性和风险性评价是一项非常重要的工作,发展和完善风险评价技术刻不容缓。
对于同一管道系统的不同管段的风险评价,应准确了解其各薄弱环节,分别轻重缓急,掌握减少风险工作的最佳时机,将事故隐患消灭在萌芽状态,做到防患于未然。
1.2 油气管道风险评价方法总的说来,油气长输管道风险评价研究可以分为三类:定性风险评价、半定量风险分析和定量风险分析。
定性风险评价的主要作用,是找出管道系统存在哪些事故危险,诱发管道事故的各种因素,这些因素对系统产生的影响程度以及在何种条件下会导致管道失效,最终确定控制管道事故的措施。
其特点是不必建立精确的数学模型和计算方法,评价的精确性取决于专家经验的全面性、划分影响因素的细致性、层次性等,具有直观、简便、快速、实用性强的特点。
输气管道内腐蚀直接评价方法
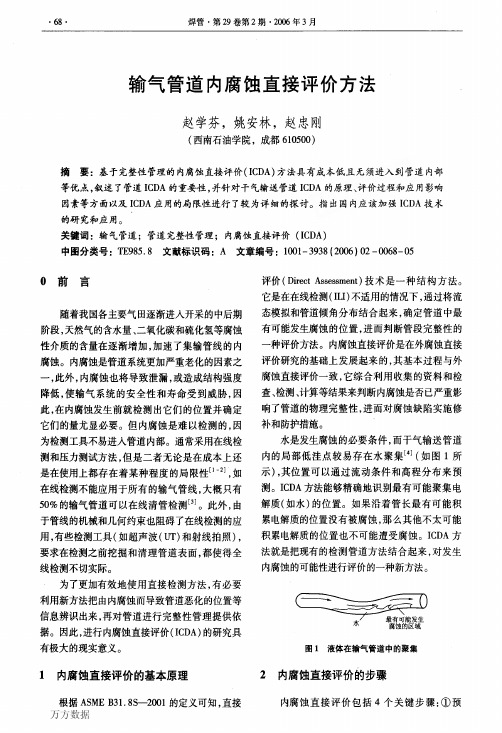
1 内腐蚀直接评价的基本原理
2 内腐蚀直接评价的步骤
根据ASME B31.8s-2001的定义可知,直接 万方数据
内腐蚀直接评价包括4个关键步骤:①预
第29卷第2期
赵学芬等:输气管道内腐蚀直接评价方法
·69·
评价;②间接检测,③直接检验,④后评价。 在预评价阶段,风险工程师必须量化潜在的风险 威胁,并选择对特定风险直接评价的可靠方法;间 接检测阶段,主要是使用各种无需实际接触管道 的方法来了解管道的情况;直接检验阶段是利用 直接与管道接触得到的数据(比如超声波传递厚 度计、ILl等)来评价管道的情况;后评价阶段是 利用检测方法来量化潜在威胁,以评价前些阶段 的可靠性。 2.1预评价
流动方向向前流动的气体与液体之间的剪应力之
间的平衡定义为液体在管道中聚集的临界角,并
建议把改进的弗劳德数(Froude number)用于倾
角为p,内径为d;的管道上,用来估计临界角。
当气体密度由总压力和温度确定后,将模拟
结果用改进的弗劳德数表示:
F:堕丑.哗.sin0,
(1)
Ps
秽g‘
式中P¨Ps一液体和气体密度,kg/m3;
前三个阶段收集的数据,目的是评价直接评价方 法的有效性并确定再评价的时间间隔。输气管道 的ICDA是基于间断扰动这个假设,并且具备这 种假设条件的管道会有较小程度的腐蚀或无腐 蚀。如果在任意位置都发现大面积腐蚀,则假设 不成立,也就是说ICDA是无效的。
文献[7]对两段管道进行了评价验证,对于 万方数据
蓦
一一一~一一一 将缓蚀作为完整性 管理程序的一部分 (直接评价范围之外的内容)
图3给定管道长度的ICDA流程图
腐蚀检测工具,操作人员可增加检测时间间隔,并 最好在最易发生腐蚀的位置进行实时监测。对于 ICDA,最经济有效的方法就是在部分管道上安装 一种在线检测工具,然后根据这个结果评估清管 器无法运行的下游内腐蚀。这是因为ICDA预测 的腐蚀更可能是上游的而不是下游的,上游位置 的完整性检验会考虑到下游位置得到结论。如果 确定出最易发生腐蚀的位置没有发生破坏,就保 证了大部分管道的完整性;反之如果发现腐蚀,也 能辨识出潜在的完整性问题。
长输天然气管道内腐蚀检测及防护
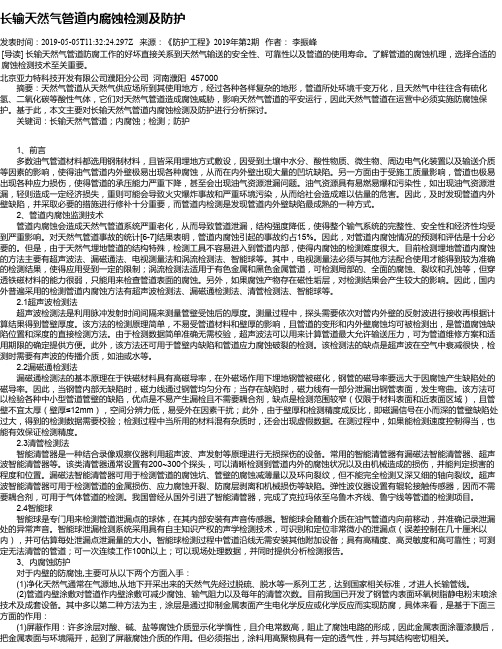
长输天然气管道内腐蚀检测及防护发表时间:2019-05-05T11:32:24.297Z 来源:《防护工程》2019年第2期作者:李振峰[导读] 长输天然气管道防腐工作的好坏直接关系到天然气输送的安全性、可靠性以及管道的使用寿命。
了解管道的腐蚀机理,选择合适的腐蚀检测技术至关重要。
北京亚力特科技开发有限公司濮阳分公司河南濮阳 457000摘要:天然气管道从天然气供应场所到其使用地方,经过各种各样复杂的地形,管道所处环境千变万化,且天然气中往往含有硫化氢、二氧化碳等酸性气体,它们对天然气管道造成腐蚀威胁,影响天然气管道的平安运行,因此天然气管道在运营中必须实施防腐蚀保护。
基于此,本文主要对长输天然气管道内腐蚀检测及防护进行分析探讨。
关键词:长输天然气管道;内腐蚀;检测;防护1、前言多数油气管道材料都选用钢制材料,且皆采用埋地方式敷设,因受到土壤中水分、酸性物质、微生物、周边电气化装置以及输送介质等因素的影响,使得油气管道内外壁极易出现各种腐蚀,从而在内外壁出现大量的凹坑缺陷。
另一方面由于受施工质量影响,管道也极易出现各种应力损伤,使得管道的承压能力严重下降,甚至会出现油气资源泄漏问题。
油气资源具有易燃易爆和污染性,如出现油气资源泄漏,轻则造成一定经济损失,重则可能会导致火灾爆炸事故和严重环境污染,从而给社会造成难以估量的危害。
因此,及时发现管道内外壁缺陷,并采取必要的措施进行修补十分重要,而管道内检测是发现管道内外壁缺陷最成熟的一种方式。
2、管道内腐蚀监测技术管道内腐蚀会造成天然气管道系统严重老化,从而导致管道泄漏,结构强度降低,使得整个输气系统的完整性、安全性和经济性均受到严重影响。
对天然气管道事故的统计[6-7]结果表明,管道内腐蚀引起的事故约占15%。
因此,对管道内腐蚀情况的预测和评估是十分必要的。
但是,由于天然气埋地管道的结构特殊,检测工具不容易进入到管道内部,使得内腐蚀的检测难度很大。
目前检测埋地管道内腐蚀的方法主要有超声波法、漏磁通法、电视测量法和涡流检测法、智能球等。
内腐蚀直接评价的关键指标
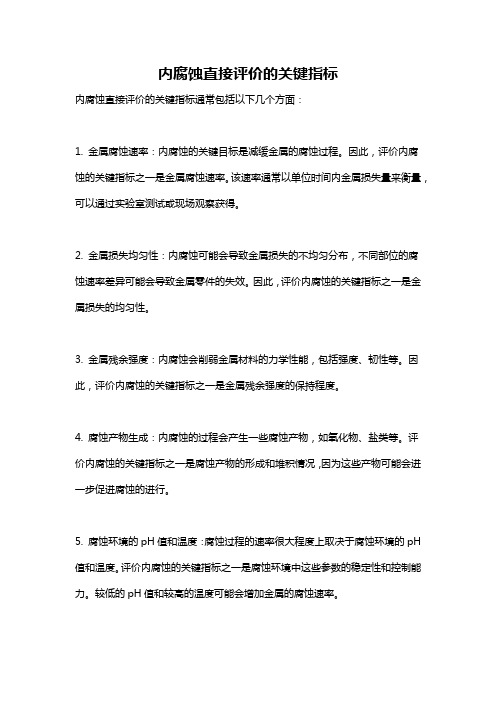
内腐蚀直接评价的关键指标
内腐蚀直接评价的关键指标通常包括以下几个方面:
1. 金属腐蚀速率:内腐蚀的关键目标是减缓金属的腐蚀过程。
因此,评价内腐蚀的关键指标之一是金属腐蚀速率。
该速率通常以单位时间内金属损失量来衡量,可以通过实验室测试或现场观察获得。
2. 金属损失均匀性:内腐蚀可能会导致金属损失的不均匀分布,不同部位的腐蚀速率差异可能会导致金属零件的失效。
因此,评价内腐蚀的关键指标之一是金属损失的均匀性。
3. 金属残余强度:内腐蚀会削弱金属材料的力学性能,包括强度、韧性等。
因此,评价内腐蚀的关键指标之一是金属残余强度的保持程度。
4. 腐蚀产物生成:内腐蚀的过程会产生一些腐蚀产物,如氧化物、盐类等。
评价内腐蚀的关键指标之一是腐蚀产物的形成和堆积情况,因为这些产物可能会进一步促进腐蚀的进行。
5. 腐蚀环境的pH值和温度:腐蚀过程的速率很大程度上取决于腐蚀环境的pH 值和温度。
评价内腐蚀的关键指标之一是腐蚀环境中这些参数的稳定性和控制能力。
较低的pH值和较高的温度可能会增加金属的腐蚀速率。
总之,评价内腐蚀的关键指标包括金属腐蚀速率、金属损失均匀性、金属残余强度、腐蚀产物生成以及腐蚀环境的pH值和温度。
这些指标可以帮助我们了解内腐蚀的程度和影响,并采取相应的防护措施。
天然气管道内腐蚀的原理及直接评价
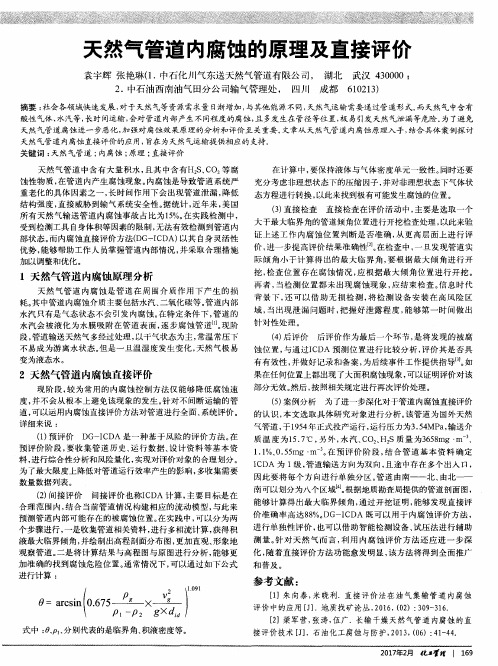
1 . 1 %、 0 . 5 5 mg・ m一。 在 预 评价 阶 段 , 结 合管 道 基 本 资 料 确 定 I C DA 为 I 级, 管道输 送方 向为双 向 , 且 途中存 在多个 出入 口, 因此 要将 每个 方 向进 行单 独分 区 。 管道 由南——北 、 由北 —— 南可以划 分为八 个区域 。 根据地 质勘查局 提供的管 道剖面 图 , 能够 计算 得 出最大 临界 倾角 , 通 过开 挖证 明 , 能够 发现 直接 评 价 准 确率 高达 8 8 %。 DG-I C DA 既可 以 用于 内腐蚀 评价 方 法 , 进 行单 独性 评价 , 也可 以借 助智 能检测 设备 、 试压 法进 行辅 助 测量 。 针对天然气而言, 利 用 内腐 蚀 评 价 方法 还 应 进 一 步 深 化, 随着直 接 评价 方法 功能 愈发 明显 , 该方法 将得 到全 面推 广
耗。 其 中管道 内腐蚀介 质主要包 括水汽 、 二氧 化碳等 。 管 道 内部 水 汽 只有是 气态 状态 不会 引发 内腐蚀 。 在特 定条件 下 , 管 道的 水 汽 会被 液 化为 水 膜吸 附 在管 道表 面 , 逐 步 腐蚀 管 道 。 现阶 段, 管 道输送天 然气 多经过处理 , 以干气状态 为主 , 常温 常压下 不 易成 为游 离水 状态 。 但 是一 旦温 湿度 发生 变化 , 天 然气 极 易
天然 气 管道 中含有 大 量积 水 , 且 其 中含 有H: S、 C O 等 腐 蚀性 物 质 , 在 管道 内产 生腐 蚀现 象 。 内腐 蚀是 导致 管道 系统 严 重老 化 的具 体 因素 之一 , 长 时 间作用 下会 出现 管道 泄漏 , 降低 结构 强度 , 直 接威 胁到 输气 系统 安全性 。 据统 计 , 近年 来 , 美 国 所有 天然 气 输送 管 道 内腐蚀 事 故 占比为 1 5 % 。 在实 践检 测 中, 受到检测 工具 自身体积等 因素 的限制 , 无法有 效检测 到管道 内 部 状 态。 而 内腐蚀直 接评 价 方法( DG= I C DA) 以 其 自身 灵活性 优势 , 能够 帮 助工 作人 员掌握 管道 内部 情况 , 并采 取合理 措施 加 以调整 和优化 。 在 计算 中, 要保 持液 体 与气体 密度 单元一 致性 。 同时还 要 充分考 虑非理想 状态 下的压缩 因子 , 并对 非理想状 态下 气体状 态方程进 行转换 , 以此 来找到极 有可能发 生腐蚀的位 置 。 ( 3 ) 直 接 检查 直 接检 查在评 价 活动 中 , 主要 是选 取一 个 大 于最大 临界 角的管道倾 角位 置进行开 挖检查 处理 , 以此来 验 证 上 述 工作 内腐 蚀 位 置判 断 是 否准 确 , 从 更 高层 面上 进 行评 价, 进 一步 提高 评价 结果 准确性 J 。 在 检查 中 , 一旦 发现管 道 实 际倾 角小 于 计算 得 出的 最大 临 界 角, 要根 据 最大 倾 角进 行 开 挖, 检 查 位 置存 在 腐蚀 情 况 , 应 根 据 最大 倾 角位 置 进行 开 挖 。
天然气管道内腐蚀直接评价方法原理与范例
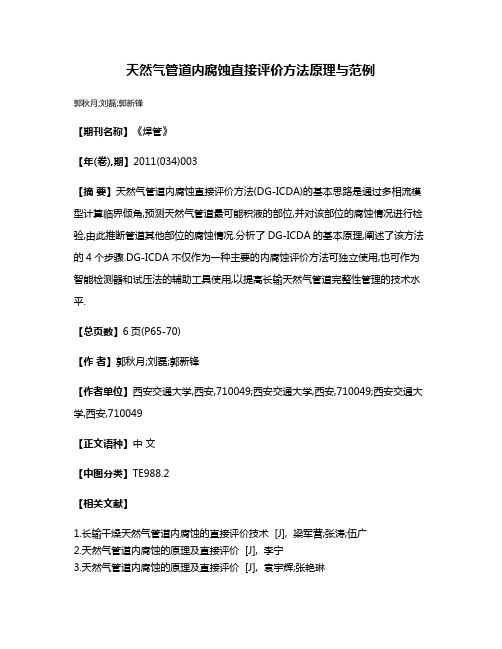
天然气管道内腐蚀直接评价方法原理与范例
郭秋月;刘磊;郭新锋
【期刊名称】《焊管》
【年(卷),期】2011(034)003
【摘要】天然气管道内腐蚀直接评价方法(DG-ICDA)的基本思路是通过多相流模型计算临界倾角,预测天然气管道最可能积液的部位,并对该部位的腐蚀情况进行检验,由此推断管道其他部位的腐蚀情况.分析了DG-ICDA的基本原理,阐述了该方法的4个步骤.DG-ICDA不仅作为一种主要的内腐蚀评价方法可独立使用,也可作为智能检测器和试压法的辅助工具使用,以提高长输天然气管道完整性管理的技术水平.
【总页数】6页(P65-70)
【作者】郭秋月;刘磊;郭新锋
【作者单位】西安交通大学,西安,710049;西安交通大学,西安,710049;西安交通大学,西安,710049
【正文语种】中文
【中图分类】TE988.2
【相关文献】
1.长输干燥天然气管道内腐蚀的直接评价技术 [J], 梁军营;张涛;伍广
2.天然气管道内腐蚀的原理及直接评价 [J], 李宁
3.天然气管道内腐蚀的原理及直接评价 [J], 袁宇辉;张艳琳
4.某海底多相流管线内腐蚀直接评价方法 [J], 汪江斌;闫婷婷;杨萍;王修云
5.国外天然气管道内腐蚀直接评价案例分析 [J], 罗鹏;赵霞;张一玲;关中原;林立明;王娟;张倩
因版权原因,仅展示原文概要,查看原文内容请购买。
天然气长输管道腐蚀缺陷评估与剩余寿命预测

因此,开展适合于天然气长输管道的腐蚀缺陷评估
(4)
和剩余寿命预测方法日益迫切。
本文针对某天然气长输管道腐蚀缺陷内检测数
(5)
据,对管道整体腐蚀状况进行了分析,采用Modified
B31G评价方法和Kastner评价方法,分析管道在不同
(6)
压力和厚度下剩余强度的变化,并预测管道的剩余
寿命,定制了管道修复计划。
method; kastner evaluation method
作者简介:庞洪晨 (1989-) ,男,山东临沂人,工程师,本科,主要从事天然气管道完整性管理 工作。
108
TOTAL CORROSION CONTROL VOL.33 No.12 DEC. 2019
腐蚀研究 Corrosion Research
相关信息,在不同压力和壁厚上,采用Modified B31G和Kastner评价方法计算了管道的剩余强度,
并进行了剩余寿命预测。结果表明:基于Modified B31G 评价方法,在评价维修;基于Kastner 评价方法,在评价压力3.9MPa下,没有金属
M = 0.032 L2 + 3.3, L2 > 50
(3)
Dt
Dt
1.2 Kastner评价方法 Modified B31G评价方法主要是分析缺陷长度
对管道的影响,为了解缺陷宽度对管道安全的影 响,British Gas(英国燃气公司)进行了大量水压 试验,试验结果表明Kastner法是分析此类问题的最 佳模型之一[6]。该方法的主要计算公式(4):
腐蚀研究 Corrosion Research
天然气长输管道腐蚀
缺陷评估与剩余寿命预测
庞洪晨1 杨立君2
长输(油气)管道全面检查项目与要求

D2.1.4后期评价
该步骤包括分析D2.1.1~D2.1.3中收集的数据资料,评价内腐蚀直接检测方法的有效性。
D2.2应力腐蚀开裂直接检测
对有应力开裂严重倾向的管道,一般采用直接对管道进行无损检测的方法或者其他适宜的方法进行检查。除输送有应力腐蚀介质导致的管道内壁应力腐蚀开裂倾向外,同事满足下列所有条件的管道,一般确定为具有管道外壁应力腐蚀开裂倾向:
D2.3.2防腐(保温)层状况不开挖检测
对防腐(保温)层与腐蚀活性区域,采用不开挖方法进行检测,主要检测方法有直流(交流)电位梯度法、直流电位(交流电流)衰减法。检测过程中应当少选择两种相互补充的检测方法。
D2.3.3管道阴极保护有效性检测
对采用外加电流阴极保护或者可断电的牺牲阳极阴极保护的管道,应当采用相应检测技术测试管道的真实阴极保护极化电位;对阴极保护效果较差的管道,应当采用密间隔电位检测技术。
对于输送无水介质或者含水分较少的天然气、原油或者成品油的钢管焊缝,冲击性能测试内容包括0°C下的夏比冲击功。
具体的测试方法按照相应国家标准或者行业标准的规定。
D2.6.4金相分析
应当对管道母材和焊缝的显微组织、夹杂物进行金相分析.
D3耐压(压力)试验
当内检测或直接检测不可实施时,可以采用耐压(压力)试验的方法进行检验。耐压(压力)试验按照相应国家标准或者行业标准的规定。
- 1、下载文档前请自行甄别文档内容的完整性,平台不提供额外的编辑、内容补充、找答案等附加服务。
- 2、"仅部分预览"的文档,不可在线预览部分如存在完整性等问题,可反馈申请退款(可完整预览的文档不适用该条件!)。
- 3、如文档侵犯您的权益,请联系客服反馈,我们会尽快为您处理(人工客服工作时间:9:00-18:30)。
图 2 剪切力与重力三种条件下与液体积聚的关系
2.2 流动计算结果
通过一系列多相流模拟计算确定了压力、 温度、 气体流速和管径对水分积聚临界倾角的 影响。图 3 为压力对临界倾角的关系。压力越高,液体越容易带走,所以临界倾角随压力的 增大而增大。图 4 所示为管径与温度对临界倾角的影响。相同气体流速下,管径越大,临界 倾角越小。温度越低,临界倾角越小,但温度的影响相对较小。
图 1 气-液管道的 5 种流态
分层流是管道中最主要的液体水传送机理,任何液滴都会被气化。相对于水分,在气相
第五届全国腐蚀大会论文集(2009 年 9 月 14-17 日,北京)
中的液滴是不饱和的,在传输过程中会汽化。液滴具有高的表面/体积比,液滴表面的气体 流速非常大。 管道中薄膜流驱动力为流动气体的剪切力和管道倾角产生的重力。 图 2 列出了 3 种条件下的流动状态。气液之间剪切力与重力的平衡关系决定了液体积聚的临界倾角。倾 角大于临界倾角的位置容易积聚水分, 倾角低于临界倾角位置的积液易被带走, 直到在倾角 大于临界倾角的位置处停留下来。 水分优先在第一个倾角大于临界倾角的位置积聚, 连续的 水分进入且没有挥发,使得水分充满第一个临界倾角,然后带到下一个倾角。
图 3 临界倾角与压力之间的关系
第五届全国腐蚀大会论文集(2009 年 9 月 14-17 日,北京)
图 4 温度与管径对临界倾角的影响
Moghissi等[2]还用改进的弗劳德常数F用于计算临界倾角,其公式如下,
F
式中,
l g g * did * * sin( ) g Vg 2
(1)
Internal Corrosion Direct Assessment Methodology for Transmission Pipeline Carrying Normally Dry Natural Gas (DG-ICDA)
Luo Peng, Chen Hongyuan, Zhang Yiling, Lin Lingli (1 PetroChina Pipeline R&D Center, Hebei, Langfang, 06500)
1 概述
尽管天然气在进入长输管道之前都经过了脱水、脱硫等处理,但在实际的运行过程中, 由于事故工况或其它原因(如凝析等),管道不可避免的会进入水汽、CO 2 以及H 2 S等腐蚀性 在 2003~2004 年间, 介质, 从而导致内腐蚀的发生。 美国管道安全办公室(OPS)统计显示[1], 美国长输天然气管道由内腐蚀引起的失效占整个腐蚀失效的 16%,直接财产损失达 198 万 美元。 由于管道输送的密闭性, 以及检测评价手段的不成熟, 管道内腐蚀具有较大的隐蔽性, 有时候内腐蚀导致的问题是灾难性的。 2000 年 8 月 19 日EI Paso公司在新墨西哥卡尔斯巴附 近的一条φ760 运营管线发生内腐蚀失效事故,引发大火并造成 12 人死亡,直接财产损失 达 100 万美元,赔偿损失高达 1550 万美元,事故原因调查表明,正是由于管线底部长期积 液导致内部腐蚀穿孔所引起的。 国内天然气管道由于运行时间不长, 内部腐蚀问题还不太严 重,但也出现了不同程度的内部腐蚀,如 2006 年对中石油某输气管道进行内检测时发现, 在不到 500 km的管段中, 出现了上千个内部金属腐蚀点, 最大内腐蚀速率达到了 0.46 mm/yr。 可以预见的是,随着我国天然气管网运行时间的延长,内部腐蚀问题将会越来越复杂。
步骤 1:计算基准状态下的气体密度:
g
P MV (3.4 0.10325) 16 0.028 g / cm 3 Z R T 0.83 (8.314 289)
步骤 2:计算基准状态下气体的表观速度
OPFlowRate
STPFlowRate T ZPSTP P TSTP
第五届全国腐蚀大会论文集(2009 年 9 月 14-17 日,北京)
到目前为止, 油气管道的内腐蚀几乎都是在既成事实之后才进行检测的, 如漏磁检测技 术、超声波检测技术、涡流检测技术、射线检测技术和导波检测技术等,这意味着公司收入 的大量流失并使管道业主的管道停产检修。 如何在内腐蚀成为问题之前就提出解决办法, 进 行预防性维护就成了管道维护的关键所在。油气管道外腐蚀直接评价技术(ECDA)已日趋 较成熟,所以,同样需要开发管道内腐蚀直接评价技术对管道的内部腐蚀情况进行评价,国 外即采用内腐蚀直接评价方法(ICDA)[2-5]。 《美国联邦法典》CFR 49-192 也规定,对存在内 腐蚀威胁的管道,应进行内腐蚀检测或ICDA评价[6]。ICDA方法适用于那些正常输送干燥天 然气,但可能遭受湿气或液体水(或其它电解质)干扰的输气管道。它通过计算预测沿线最有 可能首先积聚电解质,如水及乙二醇的位置,并进行开挖验证,以提供剩余管道的信息。本 文分析了内腐蚀直接评价输的理论基础及执行步骤, 以期为我国开展内腐蚀直接评价提供参 考。
(413000 289 0.83 0.101325) (3.4 0.101325) 273
10.5 10 3 m 3 / h
Vg
OPFlowRate OPFlowRate 2 Area [ (d id / 4)]
10.5 10 3 (1 / 3600) [0.6918] 2 / 4 6.69m / s
2 理论基础
内腐蚀直接评价技术最早是由美国西南研究院提出来的, 主要是针对于那些不能进行内 检测的天然气管道的内腐蚀评价。这个方法得到了美国完整性管理体系的大力推崇,并于 2006 年美国腐蚀工程师协会形成了标准NACE SP 0206 《干气管道内腐蚀直接评价技术》 [Internal Corrosion Direct Assessment Methodology for Pipelines Carryings Normally Dry Natural Gas (DG-ICDA)] [7]。 这个方法的最初目的是用来确定所选管道是否可能发生内腐蚀, 如果说最有可能发生水分积聚的位置没有发生内腐蚀,则其它位置也不太可能发生内腐蚀, 无需再进一步进行检测。
表 1 临界值计算参数条件 流量 kNm3/h 最大值 平均值 最小值 413 313 0 压力 MPa 5.9 4.8 3.4 温度 ℃ 16 16 16
第五届全国腐蚀大会论文集(2009 年 9 月 14-17 日,北京)
表 2 临界值计算所需其它参数 管径 mm 数 16 重力常数 m/s2 9.81 8.314 0.83 气体常数 压缩因子
Abstract: As a part of pipeline integrity management technologies, internal corrosion direct assessment methodology plays an import role in pipeline management. The theory basis, application conditions and implementing procedure were discussed in detail. The indirect inspection calculation case was also developed. Finally, the development of DG-ICDA in China was foreseen, pointing out that the research and application of ICDA technology should be enhanced. Keyword: internal corrosion, direct assessment, pipeline, integrity management
3.2 间接检测
间接检测的目标是在一定的 DG-ICDA 管段区间内,用流动模拟结果预测最可能发生内 腐蚀的位置。间接检测的理论依据是基于管道内部介质为分层流(气体和液体单独流动) , 通过对可能积水位置的识别,预测出内腐蚀的高风险位置。其主要内容包括以下三个方面: 1) 2) 3) 使用所收集的数据资料进行多相流计算,确定持液的最大临界倾角。 绘制管道高程剖面图和倾角分布图。 对比分析流动模拟计算结果和管道高程剖面和倾角分布图, 判断内腐蚀可能出现的 位置。 NACE SP 0206-2006 内腐蚀直接评价标准中推荐使用的临界角计算式就是该经验公 式,即
(3)
第五届全国腐蚀大会论文集(2009 年 9 月 14-17 日,北京)
arcsin(
(elevation) ) (distance)
(4)
3 内腐蚀直接评价执行步骤
3.1 预评价
天然气管道内腐蚀直接评价仍是一种基于风险(risk-based)的评价方法,所以在预评 价阶段需收集管道的基本运行数据(包括历史和当前数据),进行综合分析和风险量化,确定 DG-ICDA 是否可行,并对评价区域进行分区。其需收集的资料包括设计资料,建设记录, 运行与维护历史,线路图,腐蚀调查报告,气质分析报告以及以前的完整性评价报告和维修 记录等,具体可参见 NACE SP 0206。
2.1 气-液两相流流态分析
对于天然气管道,液体积聚主要取决于气体流速和管道倾角。气-液管道存在 5 种基本 的流态形式,如图 1 所示,光滑分层流、波浪分层流、间歇流(活塞流和栓塞流) 、液体分 散环状流、气泡分散两相流。输气管道中液体相非常的少,而且无序间断分布。当液体速率 增加,才会发生间歇流;气泡分散两相流需要大量连续液体相;液体分散环状流需要大量液 体覆盖管道所有内壁,即使只有很少量被气体带走;所以,输送管道只可能会产生分层流和 分散液滴。
ρ 为密度;g 为重力加速度;V 为气体表观速度;θ 为临界倾角。
图 5 为流动模型计算的弗劳德常数分布图。当倾角小于 0.5 度时,F=0.33±0.07;当倾角 大于 2 度时,F=0.56±0.02。倾角在 0.5 度至 2 度之间,与层流与湍流的转变有关。压缩因子 可以通过下面公式计算,