液体石油管道内腐蚀直接评价方法
油气管道完整性管理全套PPT-7-直接评价方法
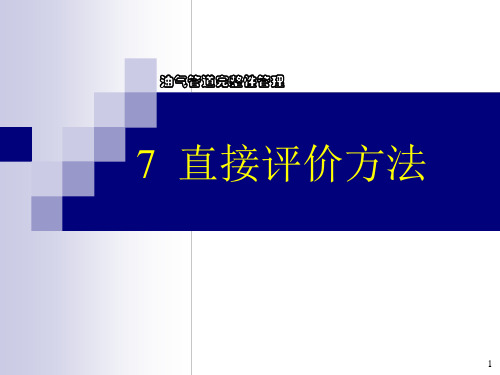
• 可在沿管道方向的任意地方对杂散 电流进行监测。
• 定位杂散电流汇集流入点及流出点。 • 快速评估杂散电流缓解措施的效果。 SCM杂散电流测试仪
26
➢ JG-2A型直流电火花检测仪
• JG-2A型直流电火花检测仪是用于检测金属防腐涂层质 量的专用仪器。
2
7.1 腐蚀防护系统检测方法
• 腐蚀防护系统检测包括外防腐层检测和阴极保护检 测,检测针对管道外防腐层的状态和阴极保护的保 护效果。
• 外防腐层状况主要是指:表现防腐层整体状况的绝 缘电阻率,是否有局部破损点。
• 阴极保护效果主要是看:保护电位是否能处于有效 的保护范围内,是否出现欠保护与过保护的情况。
• RD400-PCM的4Hz频率和C-SCAN的973.5Hz频率得到了NACE RP0502-2002标准的推荐。
• C-SCAN仪器带有测量检测间距的GPS定位 系统,能标志破损点位置。
PCM
注:NACE—美国国际腐蚀工程师协会 C-SCAN
10
2. PEARSON检测法
11
PEARSON检测法优缺点
12
3.ACVG(交流电位梯度)法
13
A字架的破损点定位过程
• 电流方向在破损点两侧发生变化。如果在一个新位置电流指向前, 而在第二个位置电流指向后,就证明操作人员走过了故障点。
14
4. 直流电压梯度测试技术(DCVG)
15
DCVG测量过程
16
DCVG的破损点查找及定位过程
17
破损点处管体腐蚀活性判断
油气管道完整性管理
7 直接评价方法
1
概述
• 直接评价管道完整性评价方法之一。 • 三种直接评价方法:
管道完整性与外腐蚀直接评价与其相应配套技术

Defect Acceptance Curve 缺陷临界曲线
NOT OK x
x
OK
d/t
x
x
x xxx
x
L
Allowable measured defect size for 41.3 bar
1.0
Relative defect depth (d/t)
0.8
Defect size
Allow able defect size
0.6
0.4
2 defects Not OK
0.2
0.0 0
200
400
600
800
1000
1200
Defect length (mm)
DNV RP F101 acceptance curve at inspection time (2002)
(general corrosion, PL02) DNV 评价方法
EMAT 检测器
EMAT 检测器
电磁声传感器在在线检测设备中的应用目 前还处于发展阶段;
电磁声传感器不需要耦合介质,可以稳定 的应用于气体输送管道。
该检测器的特点是专用于气管线、无液体 耦合的要求、高精度检测、定位和尺寸。
超声波液体耦合检测器
超声波液体耦合检测器 (ULTROSCAN CD)
COMPOSITE MATERIAL - FIBER CARBON REPAIR TECHNOLOGY
复合材料补强技术
Exposy with sleeve
-3.0
第一年
-2.5
-2.0
每年 CP
-1.5
电位
-1.0
对比
-0.5
600
石油系统腐蚀率测试标准
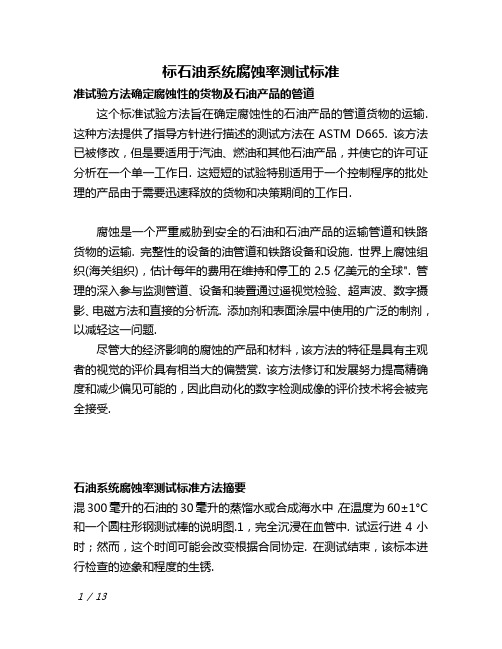
标石油系统腐蚀率测试标准准试验方法确定腐蚀性的货物及石油产品的管道这个标准试验方法旨在确定腐蚀性的石油产品的管道货物的运输. 这种方法提供了指导方针进行描述的测试方法在ASTM D665. 该方法已被修改,但是要适用于汽油、燃油和其他石油产品,并使它的许可证分析在一个单一工作日. 这短短的试验特别适用于一个控制程序的批处理的产品由于需要迅速释放的货物和决策期间的工作日.腐蚀是一个严重威胁到安全的石油和石油产品的运输管道和铁路货物的运输. 完整性的设备的油管道和铁路设备和设施. 世界上腐蚀组织(海关组织),估计每年的费用在维持和停工的2.5亿美元的全球". 管理的深入参与监测管道、设备和装置通过遥视觉检验、超声波、数字摄影、电磁方法和直接的分析流. 添加剂和表面涂层中使用的广泛的制剂,以减轻这一问题.尽管大的经济影响的腐蚀的产品和材料,该方法的特征是具有主观者的视觉的评价具有相当大的偏赞赏. 该方法修订和发展努力提高精确度和减少偏见可能的,因此自动化的数字检测成像的评价技术将会被完全接受.石油系统腐蚀率测试标准方法摘要混300毫升的石油的30毫升的蒸馏水或合成海水中,在温度为60±1°C 和一个圆柱形钢测试棒的说明图.1,完全沉浸在血管中. 试运行进4小时;然而,这个时间可能会改变根据合同协定. 在测试结束,该标本进行检查的迹象和程度的生锈.石油系统腐蚀率测试标准意义和使用其他标准:NACE标准TM0172测试方法,用于确定腐蚀性的货物及石油产品的管道标本是根据尺寸如下图所示,并应该准备从钢根据参照ASTM A108. 棒从以前的测试只能使用,如果他们是免费的,从生锈或其他明显的违规行为. 如果是这种情况的初步研磨步骤可以省略.混300毫升的石油的30毫升的蒸馏水或合成海水中,在温度为60±1°C 和一个圆柱形钢测试棒的说明图.1,完全沉浸在血管中. 试运行进4小时;然而,这个时间可能会改变根据合同协定. 在测试结束,该标本进行检查的迹象和程度的生锈.石油系统腐蚀率测试标准意义和使用这个标准试验方法的目的是要使用通过腐蚀工程师、防腐技术、腐蚀顾问、科学家和其他有关确定的防锈特性的汽油蒸馏物燃料和矿物油的运输通过石油产品的管道.石油系统腐蚀率测试标准试试准备标本是根据尺寸如下图所示,并应该准备从钢根据参照ASTM A108. 棒从以前的测试只能使用,如果他们是免费的,从生锈或其他明显的违规行为. 如果是这种情况的初步研磨步骤可以省略.样本将安装在卡盘的研磨装置,它的速度旋转的1700–1800转. 最后抛光的样本无法触摸的裸露的手是清洁棉绒布和储存在异辛烷直到必要的. 请验证,这样符合维定在下图中和咨询的完整版本NACE TM0172或ASTM D665标准的更多详细棒的制备和使用.图1. 钢棒用于试验腐蚀性的原油和产品程序自动化的数字检测成像的评价测试方法D665是严格遵守所描述的标准最后的修订.该装置的描述,自动评价测试程序、校准、验证和解释的结果将按照.程序注射的样本是自动的,根据该Eralytic的模型和说明. 注射样品的专用密度计发生无论是通过手动装置的一个注射器或者自动地通过一个建立在泵根据KEM操作手册和模型. 自动或手动的注射器注射在所有生产线采取预防措施,对样品的完整性和气泡没有为describied在D4052部12. 按照制造商的说明为确保完整性的测试样本的分析之前,以及转让有代表性的测试样品进入文书进行分析.术语定义:腐蚀、n—化学或电化学反应之间的材料,通常是金属,并且它的环境产生了恶化材料及其属性.生锈,n腐蚀的产品组成主要的水氧化铁.讨论锈是一个长期正常仅适用于铁合金.首字母缩略词:铁的数字检测成像石油系统腐蚀率测试标准测试设备和装置在一般的装置包括一个恒温控制洗浴能够控制温度的试验样品的38±1°C(100±2°F). 修改(挡板放在180°突出10毫米)烧杯容量为400毫升贝采利乌斯类型玻璃杯会议的尺寸如图所示.2如下. 挡板应102毫米长.烧杯盖由聚甲基丙烯酸甲酯应该有三个洞的容纳11.66到12.17搅拌机和一个6尺1至6.6毫米中心容纳的测试棒件. 第三个孔的直径一个类似的搅拌器,应为中心的复盖在正确的角度向其他两个孔.图2. 原理和测试设备,用于NACE TM0172和ASTM D665自动NACE/锈装置的安娜–TM0172交替的测试棒可以放在NACE ANA装置安娜图所示. 3. 这是一个自动化的单位测试设备. 安娜的节省了运营商的时间序列,控制锁在位置、时间和温度. 后编程的时间安娜将自动升起的头,以制止暴和嗡嗡声警报的操作者检索的标本或视觉或自动的评价.图3. 原理自动化测试的设备的安娜–NACE TM0172和ASTM D665石油系统腐蚀率测试标准检测程序测试方法D665是严格遵守所描述的标准最后的修订.两杯和盖应进行彻底的清洗异辛烷或ASTM沉淀油和干烤箱. 彻底清洗再次热水和干在烤箱温度在<65°C300毫升的试样应放在浴温度保持在38±1°C(100±2°F),见图2和3用图的测试设备,复盖烧杯的地方两个搅拌器和温度传感器在指定的距离,并开始搅拌,以允许的样品到达试验温度. 插入的铁棒的搅拌在1000±50转为30分钟. 在这一点上的传感器被删除,以允许增加30毫升的蒸馏水浇或通过注射传感器孔. 搅拌然后继续为3,5小时在所设定的温度. 在试样中除去,用二甲苯和苯随后通过丙酮、干燥和速率根据的规模在表1中提供.石油系统腐蚀率测试标准数字检测成像装置维萨亚酒店铁的数字检测成像装置(),提高了视觉评价通过确定程度的腐蚀性数字和整体地确定确切级别的腐蚀在4步自动化的愿景算法和分类的过程. 使用高分辨率照相机用CCD的数字检测的算法. 该系统提供了高度重复的结果通过旋转样一体360°记录的高分辨率图像和综合的总面积曝光自动进行量化,速和显示器的腐蚀程度上的样品测试.数字检测成像()评价装置—是第一个高科技的测试仪器供电的先进光学、促进和提高了视觉上的评价的方法ASTM D665,D7548和NACE TM0172.数字检测成像是通过一个独特的视觉算法和光盒子,记录,计算并显示精确的腐蚀率在几秒钟. 这一装置显示在图4a; 4b和5进行一个标准化的测量,腐蚀的试样,同时提高了视觉上的收视率的方法和样品处理程序进行当前的实验室测试.的申请专利的程序处理--提供一个标准化的方法保持试样的理想的角度和方向的分析. 的装和紧固机构消除了利用脆弱的和昂贵的玻璃器皿为观察. 一个独特的特征的程序处理的说明图. 6融步进电机和电子产品负责的适当标本旋转. 通过有机的综合成的程序处理,基本上所有的关键活动部件都放在一个易于取代大会的快速和容易的维护. 适当地处理样品是至关重要的一个准确的评价手动和通过使用技术.图. 4数字检测成像装置(a). 截面图(b)图. 5后视图. 6程序处理石油系统腐蚀率测试标准校准和验证一个特殊的校准程序,可以在该领域中使用,定期核查. 光条件下,颜色和算法,保持不变,在整个序列测试,从而确保适当的质控程序的必要用户和经认可的实验室.校准的标准程序开始通过启动和调节的LED灯. 电压电流控制光盒为一致的环境的光环境.快速和容易的校准程序,确保是报告在最佳水平.解释的结果:自动化的程序率测试棒的试样和报告石油作为通过或失败,将暴露的试样在的评价文书下的操作手册的说明. 将自动进行分析的任何测试棒,已经暴露到任何材料的所有测试描述的程序在第9、10和11的标准试验方法D665;第10部分的加速腐蚀铁的方法D7548或部分4的NACE TM-0172方法.不锈钢的试样检查:腐蚀数字的评价是执行下列自动步骤:步骤1:在开头插入样品进入专业服务架图. 6第2步:将随架成仪器步骤3:LED光源是自动启动和监管的步骤4:软件可识别和计算的维数据步骤5:软件转样,在特定程度的增量步骤6:读数表列出和处理通过算法步骤7:最后的结果显示在一个高分辨率的触摸屏幕显示在图. 7.然后将其运行的分析采用同样的方法作为完全自动化的模式,然而,显示的数据将是不同的. 这些差异包括:评价显示框会显示该手册的评价沿用的自动评价最终评价的选择,这样做是通过选择手动或自动复盖的评价还可以用在这一模式.操作者可以选择手动或自动的评价作为最后的评价值.所有预先装载试验方法遵守ASTM D665,NACE TM0172和ASTM D7548的实验条件下为不同的石油产品类别定义的范围的指定标准方法.解释的腐蚀性的试样按照度的生锈的描述第12节,注16的D665的标准试验方法,或分类的加速ASTM D7548铁腐蚀试图描述于表1和第5部分,评价的测试样本的NACE TM0172方法.自动评价:使用复杂的算法对于确定程度的腐蚀的标准测试铁杆. 该系统将转样一体360°记录的高分辨率图片集成到地区的总面积暴露出自动定量和分类. 在罕见的场合,用户不同意的评级,用户可以点击的复盖的评价..."按钮带来了一个熟悉看的图表,这可以使用手工选择一个等级作为确定的. 会再储存这些数据与原来的自动评价.手册的评价:当一个样本是在显而易见的过渡状态中,操作者有权选择做人工核查和视觉检查以前的最后的分类是已达和显示如图所示. 7.重复试验,如果瑕疵由于指纹都观察到的、或由于位置的任何颗粒或水滴可能已触及试验期间的消化的时期.重复试验也是,如果该地区的样本显示有异常情况因以色或粗糙度,可能需要试后处理或研磨.评价%的测试表面腐蚀(%)一个0B++小于0.1(2或3点不超过1毫米(0.04.) 直径)B+小于5B5到25C25至50D50至75E75至100表1. 评价的试验标本.报告自动评价程序:报告的腐蚀性,在根据一个分类列于表1. 国家的持续时间测试和试验温度在以下格式:腐蚀分类测试报告还应包含以下内容:的类型和标识的产品使用该日期的测试一个参考这ASTM-IP标准,表明是否过程A、B或C的使用. 由于法C可以接着用蒸馏水或海水中,一定要包括的种类使用的水,在这种情况下,在测试期间方法进行测试和特殊的实验条件下之后任何偏离规定的程序和测试的结果,包括严重程度的生锈,如果需要的话.图. 7显示的结果和评价在自动模式石油系统腐蚀率测试标准精确度和偏见没有普遍接受的方法用于确定精度或偏见的是目前可提供.内部的重复性研究一个小型的圆罗宾在十二个样本与两个测量的每一显示一个优秀的重复性分析. 表2中显示的收视率分配和重要的参数,如复盖的总面积以及相应的测试尺寸. 值清楚地表明绝对遵守ASTM重复性定义.表2. 实验结果安全预防措施试验应进行,在很大,通风良好的实验室或中提取罩,以避免的浓度易燃的蒸气. 人员进行测试应该意识到的危险处理的挥发性产品,例如汽油. 请参照ASTM D4057标准和安全要求的实验室.。
谈石油化工设备的腐蚀分析和寿命评价
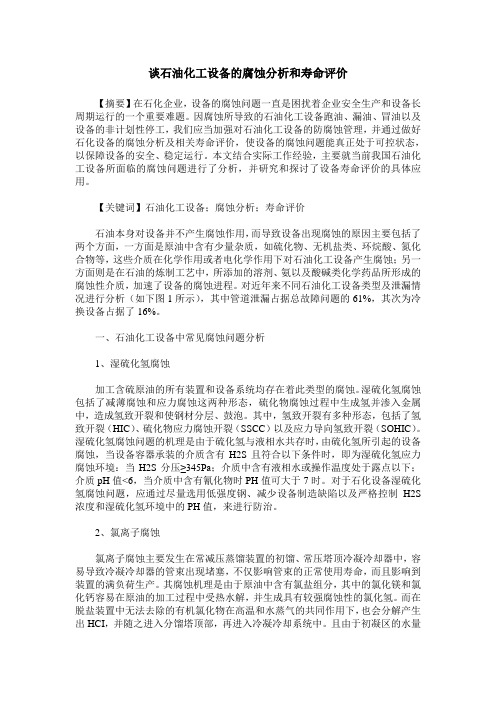
谈石油化工设备的腐蚀分析和寿命评价【摘要】在石化企业,设备的腐蚀问题一直是困扰着企业安全生产和设备长周期运行的一个重要难题。
因腐蚀所导致的石油化工设备跑油、漏油、冒油以及设备的非计划性停工,我们应当加强对石油化工设备的防腐蚀管理,并通过做好石化设备的腐蚀分析及相关寿命评价,使设备的腐蚀问题能真正处于可控状态,以保障设备的安全、稳定运行。
本文结合实际工作经验,主要就当前我国石油化工设备所面临的腐蚀问题进行了分析,并研究和探讨了设备寿命评价的具体应用。
【关键词】石油化工设备;腐蚀分析;寿命评价石油本身对设备并不产生腐蚀作用,而导致设备出现腐蚀的原因主要包括了两个方面,一方面是原油中含有少量杂质,如硫化物、无机盐类、环烷酸、氮化合物等,这些介质在化学作用或者电化学作用下对石油化工设备产生腐蚀;另一方面则是在石油的炼制工艺中,所添加的溶剂、氨以及酸碱类化学药品所形成的腐蚀性介质,加速了设备的腐蚀进程。
对近年来不同石油化工设备类型及泄漏情况进行分析(如下图1所示),其中管道泄漏占据总故障问题的61%,其次为冷换设备占据了16%。
一、石油化工设备中常见腐蚀问题分析1、湿硫化氢腐蚀加工含硫原油的所有装置和设备系统均存在着此类型的腐蚀。
湿硫化氢腐蚀包括了减薄腐蚀和应力腐蚀这两种形态,硫化物腐蚀过程中生成氢并渗入金属中,造成氢致开裂和使钢材分层、鼓泡。
其中,氢致开裂有多种形态,包括了氢致开裂(HIC)、硫化物应力腐蚀开裂(SSCC)以及应力导向氢致开裂(SOHIC)。
湿硫化氢腐蚀问题的机理是由于硫化氢与液相水共存时,由硫化氢所引起的设备腐蚀,当设备容器承装的介质含有H2S且符合以下条件时,即为湿硫化氢应力腐蚀环境:当H2S分压≥345Pa;介质中含有液相水或操作温度处于露点以下;介质pH值<6,当介质中含有氰化物时PH值可大于7时。
对于石化设备湿硫化氢腐蚀问题,应通过尽量选用低强度钢、减少设备制造缺陷以及严格控制H2S 浓度和湿硫化氢环境中的PH值,来进行防治。
ICDA管道内腐蚀直接评价方法探析

ICDA管道内腐蚀直接评价方法探析ICDA(In-Line Inspection and Corrosion Direct Assessment)管道内腐蚀直接评价方法是一种用于评价管道内部腐蚀情况的方法。
本文将对这种方法进行探析。
ICDA评价方法包括三个步骤:第一步是对管道的条件进行外部评估,第二步是对管道进行内部评估,第三步是基于前两个步骤的结果进行风险评估和管理。
其中第二步是评价管道内部的腐蚀情况。
管道内部腐蚀是导致管道泄漏和损坏的主要原因之一。
因此,了解管道内部的腐蚀情况是至关重要的。
ICDA评价方法采用的是一种直接评价方法,这意味着评估人员需要直接检查管道的内部情况,以确认是否存在腐蚀情况。
ICDA评价方法直接评估管道内部的腐蚀情况的方法主要有两种:一种是使用腐蚀探测器,另一种是对管道进行挖掘。
这两种方法都有其优缺点。
使用腐蚀探测器是一种非破坏性检测方法,可以检测到管道内部的腐蚀情况,但是其检测范围有限,只能检测到探头能够到达的区域,而且其检测结果也不是非常准确,可能会出现误判情况。
此外,使用腐蚀探测器需要专业的技术人员进行操作,成本较高。
对管道进行挖掘是一种直接检查管道内部情况的方法,可以检测到管道内部的所有腐蚀情况,评估结果比较准确,但是这种方法需要对管道进行破坏性操作,对管道造成一定的损坏,同时也会对周围环境造成一定的影响。
此外,对管道进行挖掘需要大量的人力和物力成本。
两种方法各有优劣,ICDA评价方法选择哪种方法需要根据实际情况进行权衡。
如果管道比较长,采用挖掘的方法成本较高,而采用腐蚀探测器的方法可以快速检测到可能存在的腐蚀,那么可以选择使用腐蚀探测器的方式进行评估。
如果管道较短,采用挖掘的方法成本较低,而且检测结果比较准确,那么可以选择采用挖掘的方法进行评估。
总之,ICDA评价方法是一种直接评价管道内部腐蚀情况的方法,其核心在于第二步——对管道进行内部评估。
采用哪种方法进行内部评估需要根据实际情况进行权衡。
液体石油管道内腐蚀直接评价方法
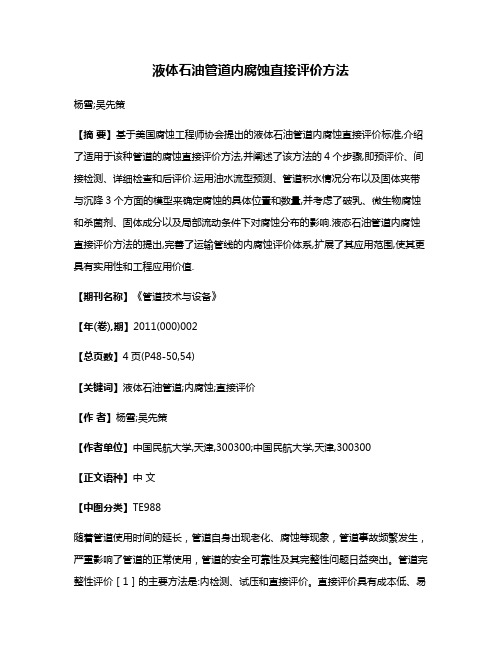
液体石油管道内腐蚀直接评价方法杨雪;吴先策【摘要】基于美国腐蚀工程师协会提出的液体石油管道内腐蚀直接评价标准,介绍了适用于该种管道的腐蚀直接评价方法,并阐述了该方法的4个步骤,即预评价、间接检测、详细检查和后评价.运用油水流型预测、管道积水情况分布以及固体夹带与沉降3个方面的模型来确定腐蚀的具体位置和数量,并考虑了破乳、微生物腐蚀和杀菌剂、固体成分以及局部流动条件下对腐蚀分布的影响.液态石油管道内腐蚀直接评价方法的提出,完善了运输管线的内腐蚀评价体系,扩展了其应用范围,使其更具有实用性和工程应用价值.【期刊名称】《管道技术与设备》【年(卷),期】2011(000)002【总页数】4页(P48-50,54)【关键词】液体石油管道;内腐蚀;直接评价【作者】杨雪;吴先策【作者单位】中国民航大学,天津,300300;中国民航大学,天津,300300【正文语种】中文【中图分类】TE988随着管道使用时间的延长,管道自身出现老化、腐蚀等现象,管道事故频繁发生,严重影响了管道的正常使用,管道的安全可靠性及其完整性问题日益突出。
管道完整性评价[1]的主要方法是:内检测、试压和直接评价。
直接评价具有成本低、易实施等特点,该方法近年得到了广泛的应用。
内腐蚀直接评价[2]是在外腐蚀评价研究的基础上发展起来的,综合利用收集到的资料和检查、检测、计算等的结果来判断内腐蚀是否已严重影响钢质管道的物理完整性,从而确定对腐蚀缺陷实施修补和防护的措施。
内腐蚀直接评价方法包括输气管道内腐蚀直接评价(DG - ICDA)[3-4]、湿气管线内腐蚀直接评价(WG-ICDA)[5]以及液体石油管道内腐蚀直接评价(LP-ICDA)。
液体石油管道中含有H2S、CO2、盐、沙子和蜡等,且管道内多相流的流动受多种因素的影响,因此,多相流内壁材料的损失机理十分复杂,是一种腐蚀和冲蚀联合交互作用的过程[6-7]。
这类环境中,液滴、气泡、颗粒都可能冲击管壁,使表面产生的腐蚀物脱落,同时也可直接作用于表面,产生磨损。
内腐蚀直接评价标准
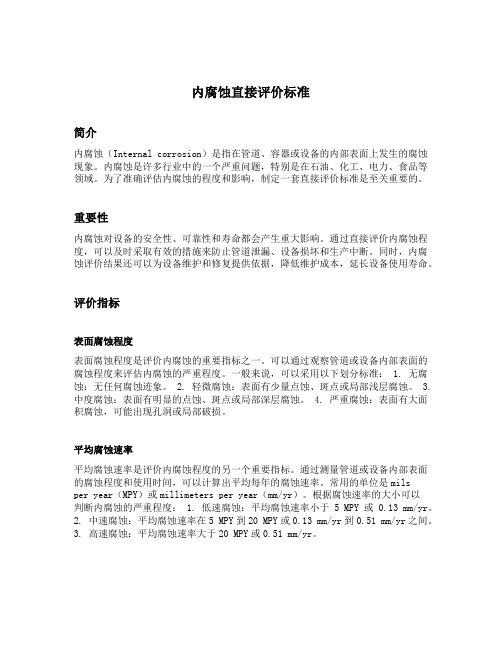
内腐蚀直接评价标准简介内腐蚀(Internal corrosion)是指在管道、容器或设备的内部表面上发生的腐蚀现象。
内腐蚀是许多行业中的一个严重问题,特别是在石油、化工、电力、食品等领域。
为了准确评估内腐蚀的程度和影响,制定一套直接评价标准是至关重要的。
重要性内腐蚀对设备的安全性、可靠性和寿命都会产生重大影响。
通过直接评价内腐蚀程度,可以及时采取有效的措施来防止管道泄漏、设备损坏和生产中断。
同时,内腐蚀评价结果还可以为设备维护和修复提供依据,降低维护成本,延长设备使用寿命。
评价指标表面腐蚀程度表面腐蚀程度是评价内腐蚀的重要指标之一。
可以通过观察管道或设备内部表面的腐蚀程度来评估内腐蚀的严重程度。
一般来说,可以采用以下划分标准: 1. 无腐蚀:无任何腐蚀迹象。
2. 轻微腐蚀:表面有少量点蚀、斑点或局部浅层腐蚀。
3. 中度腐蚀:表面有明显的点蚀、斑点或局部深层腐蚀。
4. 严重腐蚀:表面有大面积腐蚀,可能出现孔洞或局部破损。
平均腐蚀速率平均腐蚀速率是评价内腐蚀程度的另一个重要指标。
通过测量管道或设备内部表面的腐蚀程度和使用时间,可以计算出平均每年的腐蚀速率。
常用的单位是milsper year(MPY)或millimeters per year(mm/yr)。
根据腐蚀速率的大小可以判断内腐蚀的严重程度: 1. 低速腐蚀:平均腐蚀速率小于 5 MPY或0.13 mm/yr。
2. 中速腐蚀:平均腐蚀速率在5 MPY到20 MPY或0.13 mm/yr到0.51 mm/yr之间。
3. 高速腐蚀:平均腐蚀速率大于20 MPY或0.51 mm/yr。
腐蚀类型内腐蚀可以有不同的腐蚀类型,包括普通腐蚀、点蚀腐蚀、应力腐蚀等。
评价内腐蚀的直接标准也应包括对腐蚀类型的鉴别和判断。
不同的腐蚀类型可能需要采取不同的防护措施和修复方法。
评价方法直接观察法直接观察法是最常用的评价内腐蚀的方法之一。
通过人工进入管道或设备,并使用工具和设备观察内部表面的腐蚀情况。
油气集输管道腐蚀检测技术及应用

油气集输管道腐蚀检测技术及应用
油气集输管道是将油气从生产地输送到加工厂或销售地的管道,其重要性不言而喻。
由于长期运输和使用的原因,管道容易出现腐蚀问题,导致安全隐患和经济损失。
对油气
集输管道进行定期的腐蚀检测是必不可少的。
腐蚀检测技术是一种非破坏性测试方法,通过对管道表面和内部的检测,来评估管道
的腐蚀情况。
以下是常用的腐蚀检测技术及其应用:
1. 超声波检测
超声波检测是通过超声波的传播速度和幅度的变化来判断管道壁厚度和腐蚀情况的技术。
它适用于对管道壁厚度进行定量分析和评估,并可以检测到管道的内部腐蚀情况。
2. 磁粉探伤
磁粉探伤是通过施加磁场和喷洒磁性粉末,来检测管道表面和内部的腐蚀缺陷。
它适
用于对管道表面的腐蚀进行定性和定位分析,并可以检测到管道内部的腐蚀情况。
1. 管道维护和管理
腐蚀检测可以帮助运营单位及时了解管道的腐蚀情况,及时采取保护措施,延长管道
的使用寿命,减少运维成本。
2. 安全监控
腐蚀检测可以帮助运营单位及时发现管道的腐蚀缺陷,及时采取修复措施,防止发生
管道泄漏和爆炸等事故,保障人员和设备的安全。
3. 环境保护
腐蚀检测可以帮助运营单位及时发现管道泄漏和污染,并采取相应的措施,保护环境,减少对土壤和水体的污染。
油气集输管道腐蚀检测技术在油气行业中起着至关重要的作用。
通过定期的腐蚀检测,可以及时了解管道的腐蚀情况,并采取措施进行维护和修复,确保管道的安全运行和延长
寿命。
油气管道腐蚀检测

油气管道腐蚀检测油气管道腐蚀的检测摘要:油气管道运输中的泄漏事故,不仅损失油气和污染环境,还有可能带来重大的人身伤亡。
近些年来,管道泄漏事故频繁发生,为保障管道安全运行和将泄漏事故造成的危害减少到最小,需要研究泄漏检测技术以获得更高的泄漏检测灵敏度和更准确的泄漏点定位精度。
本文介绍几种检测方法并针对具体情况进行具体分析。
关键字:腐蚀检测涡流漏磁超声波引言:在油气管道运输中管道损坏导致的泄漏事故不仅浪费了石油和天然气,而且泄露的有毒气体不仅污染环境,而且对人和动物造成重大的伤害,因此直接有效的检测技术是十分必要的,油气管道检测是直接利用仪器对管壁进行测试,国内外主要以超声波、漏磁和祸流等领域的发展为代表。
[1] 1、涡流检测电涡流效应的产生机理是电磁感应. 电涡流是垂直于磁力线平面的封闭的旋涡!状感应电流, 与激励线圈平面平行, 且范围局限于感应磁场所能涉及的区域. 电涡流的透射深度见图1, 电涡流集中在靠近激励线圈的金属表面, 其强度随透射深度的增加而呈指数衰减, 此即所谓的趋肤效应. [1]电涡流检测金属表面裂纹的原理是: 检测线圈所产生的磁场在金属中产生电涡流, 电涡流的强度与相位将影响线圈的负载情况, 进而影响线圈的阻抗. 如果表面存在裂纹, 则会切断或降低电涡流, 即增大电涡流的阻抗, 降低线圈负载. 通过检测线圈两端的电压, 即可检测到材料中的损伤. 电涡流检测裂纹原理见图2.[2]涡流检测是一种无损检测方法,它适用于导电材料。
涡流检测系统适应于核电厂、炼油厂、石化厂、化学工厂、海洋石油行业、油气管道、食品饮料加工厂、酒厂、通风系统检查、市政工程、钢铁治炼厂、航空航天工业、造船厂、警察/军队、发电厂等各方面的需求.[2]涡流检测的优点为:1.对导电材料和表面缺陷的检测灵敏度较高;2.检测结果以电信号输出,可以进行白动化检测;3.涡流检测仪器重量轻,操作轻便、简单;4.采用双频技术可区分上下表面的缺陷:5.不需要祸合介质,非接触检测;6.可以白动对准_!:件探伤;7.应用范围广,可检测非铁磁性材料。
ICDA管道内腐蚀直接评价方法探析
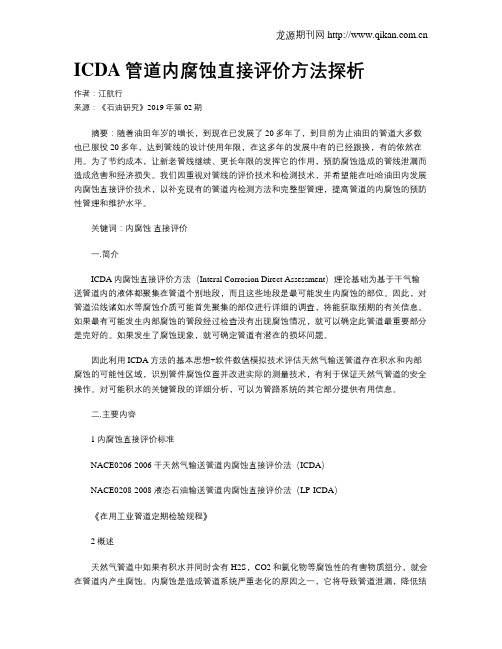
ICDA管道内腐蚀直接评价方法探析作者:江航行来源:《石油研究》2019年第02期摘要:随着油田年岁的增长,到现在已发展了20多年了,到目前为止油田的管道大多数也已服役20多年,达到管线的设计使用年限,在这多年的发展中有的已经跟换,有的依然在用。
为了节约成本,让新老管线继续、更长年限的发挥它的作用,预防腐蚀造成的管线泄漏而造成危害和经济损失。
我们因重视对管线的评价技术和检测技术,并希望能在吐哈油田内发展内腐蚀直接评价技术,以补充现有的管道内检测方法和完整型管理,提高管道的内腐蚀的预防性管理和维护水平。
关键词:内腐蚀直接评价一.简介ICDA内腐蚀直接评价方法(Interal Corrosion Direct Assessment)理论基础为基于干气输送管道内的液体都聚集在管道个别地段,而且这些地段是最可能发生内腐蚀的部位。
因此,对管道沿线诸如水等腐蚀介质可能首先聚集的部位进行详细的调查,将能获取预期的有关信息。
如果最有可能发生内部腐蚀的管段经过检查没有出现腐蚀情况,就可以确定此管道最重要部分是完好的。
如果发生了腐蚀现象,就可确定管道有潜在的损坏问题。
因此利用ICDA方法的基本思想+软件数值模拟技术评估天然气输送管道存在积水和内部腐蚀的可能性区域,识别管件腐蚀位置并改进实际的测量技术,有利于保证天然气管道的安全操作。
对可能积水的关键管段的详细分析,可以为管路系统的其它部分提供有用信息。
二.主要内容1内腐蚀直接评价标准NACE0206-2006 干天然气输送管道内腐蚀直接评价法(ICDA)NACE0208-2008 液态石油输送管道内腐蚀直接评价法(LP-ICDA)《在用工业管道定期检验规程》2概述天然气管道中如果有积水并同时含有H2S,CO2和氯化物等腐蚀性的有害物质组分,就会在管道内产生腐蚀。
内腐蚀是造成管道系统严重老化的原因之一,它将导致管道泄漏,降低结构强度,并严重威胁整个输气系统的安全性、完整性和经济性。
输油管道腐蚀因素分析与评价

输油管道腐蚀因素分析与评价摘要:面对输油管道的腐蚀问题,本文将研究某油田作为研究对象,检测地层水含有的矿化度和离子含量、腐蚀因素。
在“静态挂片”试验中,PH值和含水率与腐蚀速率有直接关系。
通过试验结果得知,酸性环境和高矿化度为管道腐蚀的直接因素。
当含水率越高,则达标腐蚀性越严重。
文章通过浅析输油管道的危害,详细分析输油管道腐蚀因素,对防止输油管道腐蚀具有重要意义。
关键词:输油管道;腐蚀;因素分析管道运输具备运送距离长、数量大、安全性高等优点,故被广泛地应用在石油工业当中。
我国大部分油田处于条件恶劣和人烟稀少的地区,为将原油运输至发达地区实施炼制,必须经过长时间的管道运输。
在运输石油过程中,输油管道腐蚀为影响油田生产的主要问题。
管道腐蚀可直接导致管道与设备破损,对油田的正产开采产生直接影响。
据相关数据统计,因管道腐蚀发生事故的概率超过40%,最高可达到70%。
一、输油管道腐蚀的危害输油管道腐蚀可以分成内腐蚀、外腐蚀。
在铺设管道的过程中,为防止外界因素破坏管道会将管道埋在地下。
土壤中含有微生物、水分等多种成分,这部分因素与管道发生接触,必定导致管道外壁被腐蚀。
管道中运输的产出液含有氯离子和氧化物等腐蚀介质,其对管道内壁产生一定腐蚀性。
在腐蚀作用下,对输油管道的安全使用产生直接影响。
腐蚀可直接应用管道使用年限,我国个别油田的管道在正式投产后2-3年便出现腐蚀问题,部分管道在正式投产之后5-6年便受到腐蚀问题而报废。
因输油管道产生的“间断性生产”,既会导致管道输送效率下降,又会使管道养护与运行难度增加。
当未及时更新腐蚀管道,不仅会发生原油泄漏的问题,还会发生安全事故,严重威胁生产人员的人身安全和健康,为企业带来经济损失。
当原油泄漏,会对四周的水体、空气、土壤造成严重污染,原油当中富含大量的难降解物质和有毒物质,若土壤与水体遭到污染,治理恢复的难度大大增加。
石油中含有的多环芳烃可危害人们的皮肤与呼吸道,从而引起胃癌、肺癌、皮肤癌。
石油钻井管道腐蚀性能试验与预测方法比较
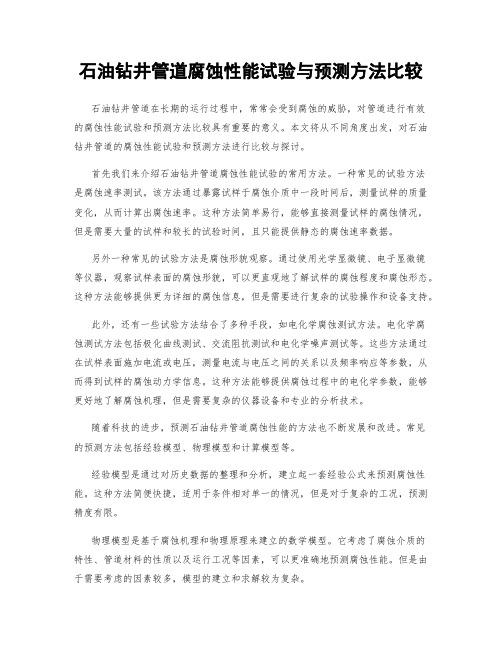
石油钻井管道腐蚀性能试验与预测方法比较石油钻井管道在长期的运行过程中,常常会受到腐蚀的威胁,对管道进行有效的腐蚀性能试验和预测方法比较具有重要的意义。
本文将从不同角度出发,对石油钻井管道的腐蚀性能试验和预测方法进行比较与探讨。
首先我们来介绍石油钻井管道腐蚀性能试验的常用方法。
一种常见的试验方法是腐蚀速率测试。
该方法通过暴露试样于腐蚀介质中一段时间后,测量试样的质量变化,从而计算出腐蚀速率。
这种方法简单易行,能够直接测量试样的腐蚀情况,但是需要大量的试样和较长的试验时间,且只能提供静态的腐蚀速率数据。
另外一种常见的试验方法是腐蚀形貌观察。
通过使用光学显微镜、电子显微镜等仪器,观察试样表面的腐蚀形貌,可以更直观地了解试样的腐蚀程度和腐蚀形态。
这种方法能够提供更为详细的腐蚀信息,但是需要进行复杂的试验操作和设备支持。
此外,还有一些试验方法结合了多种手段,如电化学腐蚀测试方法。
电化学腐蚀测试方法包括极化曲线测试、交流阻抗测试和电化学噪声测试等。
这些方法通过在试样表面施加电流或电压,测量电流与电压之间的关系以及频率响应等参数,从而得到试样的腐蚀动力学信息。
这种方法能够提供腐蚀过程中的电化学参数,能够更好地了解腐蚀机理,但是需要复杂的仪器设备和专业的分析技术。
随着科技的进步,预测石油钻井管道腐蚀性能的方法也不断发展和改进。
常见的预测方法包括经验模型、物理模型和计算模型等。
经验模型是通过对历史数据的整理和分析,建立起一套经验公式来预测腐蚀性能。
这种方法简便快捷,适用于条件相对单一的情况,但是对于复杂的工况,预测精度有限。
物理模型是基于腐蚀机理和物理原理来建立的数学模型。
它考虑了腐蚀介质的特性、管道材料的性质以及运行工况等因素,可以更准确地预测腐蚀性能。
但是由于需要考虑的因素较多,模型的建立和求解较为复杂。
计算模型利用计算机模拟的方法,通过对管道系统进行数值仿真分析,预测腐蚀性能。
这种方法能够考虑到各种复杂的因素和工况变化,提供模拟真实工况下的腐蚀情况。
油气水混输管道内腐蚀及直接评价方法研究
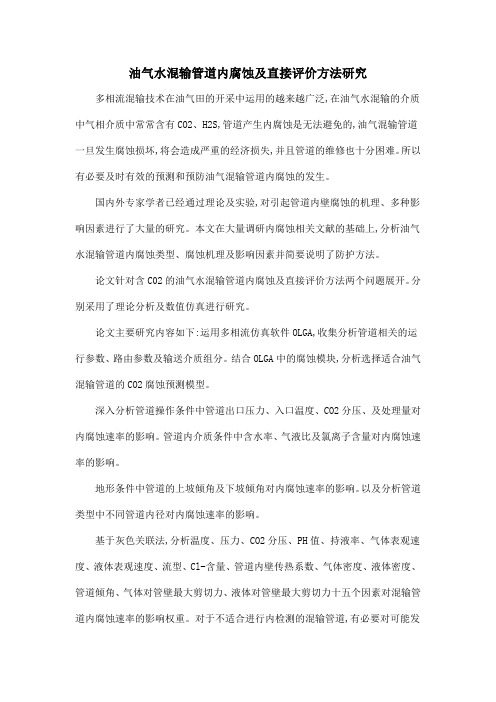
油气水混输管道内腐蚀及直接评价方法研究多相流混输技术在油气田的开采中运用的越来越广泛,在油气水混输的介质中气相介质中常常含有CO2、H2S,管道产生内腐蚀是无法避免的,油气混输管道一旦发生腐蚀损坏,将会造成严重的经济损失,并且管道的维修也十分困难。
所以有必要及时有效的预测和预防油气混输管道内腐蚀的发生。
国内外专家学者已经通过理论及实验,对引起管道内壁腐蚀的机理、多种影响因素进行了大量的研究。
本文在大量调研内腐蚀相关文献的基础上,分析油气水混输管道内腐蚀类型、腐蚀机理及影响因素并简要说明了防护方法。
论文针对含C02的油气水混输管道内腐蚀及直接评价方法两个问题展开。
分别采用了理论分析及数值仿真进行研究。
论文主要研究内容如下:运用多相流仿真软件OLGA,收集分析管道相关的运行参数、路由参数及输送介质组分。
结合OLGA中的腐蚀模块,分析选择适合油气混输管道的CO2腐蚀预测模型。
深入分析管道操作条件中管道出口压力、入口温度、CO2分压、及处理量对内腐蚀速率的影响。
管道内介质条件中含水率、气液比及氯离子含量对内腐蚀速率的影响。
地形条件中管道的上坡倾角及下坡倾角对内腐蚀速率的影响。
以及分析管道类型中不同管道内径对内腐蚀速率的影响。
基于灰色关联法,分析温度、压力、CO2分压、PH值、持液率、气体表观速度、液体表观速度、流型、Cl-含量、管道内壁传热系数、气体密度、液体密度、管道倾角、气体对管壁最大剪切力、液体对管壁最大剪切力十五个因素对混输管道内腐蚀速率的影响权重。
对于不适合进行内检测的混输管道,有必要对可能发生内腐蚀破坏的管道进行直接评价。
本文结合NACE提出的内腐蚀直接评价方法(ICDA),结合实例对油气水混输管道内腐蚀直接评价关键件技术进行研究,确定重点检查的子评价区间,以及子区间中需要详细检测的具体位置。
内腐蚀直接评价方法在输油管道中的应用

43管道运输是石油、天然气最为经济且便捷的输送方式之一,然而,由于原油介质中含有 CO 2,H 2S 和水等腐蚀性介质,引起管线内部产生腐蚀,导致管道泄漏甚至是火灾、爆炸事故,严重威胁人员、财产和能源输送的安全。
统计显示[1],国内部分地区发生的管线事故中,因内腐蚀造成的破坏失效所占比例超过70%,平均事故率2.3次/(1000km·a),高于发达国家的平均水平。
因此,定期进行管道检查以确保管道安全运行,是整个管道设计、制造、安装、使用的首要问题。
当前针对管道内部腐蚀有很多的有效的手段[2]。
智能漏磁检测是国内当前应用最为广泛的内检测方法,但是其对检验条件较为严格,需要工艺条件及管道结构等满足一定的条件。
低频导波技术广泛用于管道内外壁腐蚀检测,但是其须通过机械采用机械或气体施加到探头的背面以保证探头与管道表面接触,同时在工作过程中“机械波”易于被管道内部的介质及管道外壁的防腐层及土壤吸收削弱,单次检测的距离十分有限。
C扫、低频电磁等尽管能针对管道面扫,但是需要开挖,打磨管体,检验效率比低频导波还低。
因此,为满足国家法规及输油管道安全运行要求,亟需研究管道内检测的替代方案。
内腐蚀直接评价法(ICDA)最早由美国腐蚀工程师协会(NACE)提出,是在外腐蚀直接评价法的基础(EDCA)上发展起来的综合评估方法,国内标准《输油管道内腐蚀外检测方法》34350—2017于2017年颁布,本文针对某输油管道,在分析管道本体、介质条件、操作工况的基础上,应用内腐蚀直接评价方法对管道易于发生腐蚀的位置进行预测,并结合低频导波、C扫、低频电磁等技术进行开挖检验,对内腐蚀直接评价方法的准确性和有效性进行验证。
1 某输油管道概况某输油管道规格为Φ377×6.4/mm,材质为L360,2008年5月投入使用,操作压力<6.5MPa,介质为原油。
计划对84#测试桩至96#测试桩进行内腐蚀评价,该管道无内涂层,未进行清管工作,管道运行期间不存在连续水相,沿线可以开挖。
油气水混输管道内腐蚀及直接评价方法研究

油气水混输管道内腐蚀及直接评价方法研究首先,对于油气水混输管道内腐蚀的研究,需要了解腐蚀的机理。
油气水混输管道受到腐蚀的主要原因是介质中的水分和硫化物含量较高,导致了腐蚀介质的酸性增强。
此外,管道材料的选择也会影响腐蚀的发生,因此需要对不同材料在不同环境条件下的腐蚀行为进行研究。
其次,需要对油气水混输管道内腐蚀的直接评价方法进行研究。
常用的方法包括腐蚀速率的测定、腐蚀产物的分析、电化学测试和无损检测等。
腐蚀速率的测定可以通过在实际工业管道上安装腐蚀样品,并定期取出进行测量来获得。
腐蚀产物的分析可以通过取样分析来确定产物的种类和含量,进而判断腐蚀形式和机制。
电化学测试可以通过测量电位和电流来了解管道内腐蚀的程度和变化趋势。
无损检测则是使用超声波、X射线或磁性粉等方法对管道进行检测,以发现腐蚀的存在和程度。
除了直接评价方法,还可以通过环境监测和运行数据分析等方法来间接评价油气水混输管道内腐蚀。
环境监测包括水质监测和气体监测,可以通过采集和分析水样和气体样品来了解管道周围环境的腐蚀性,从而间接评价管道内腐蚀的程度。
运行数据分析则可以通过分析管道的工作参数、温度、压力等数据来判断腐蚀的发生和变化趋势。
最后,需要将以上研究成果应用到实际生产中,制定相应的维护和管理策略,以延长油气水混输管道的使用寿命和确保其安全运行。
这包括定期监测和维护管道的状态,通过防腐保温、注脱脂、防腐涂层等方法来控制腐蚀的发生,以及定期进行管道的修复和更换。
综上所述,油气水混输管道内腐蚀及直接评价方法的研究是一个重要课题,对于确保管道的安全运行具有重要意义。
通过深入研究油气水混输管道的腐蚀机理和开展直接评价方法的研究,可以有效地预测和控制腐蚀的发生,进而延长管道的使用寿命和保证其安全运行。
原油工艺管道内腐蚀检测技术及方法
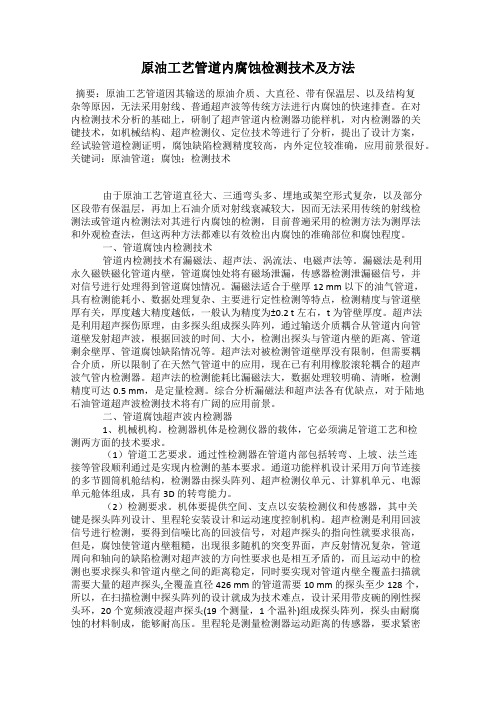
原油工艺管道内腐蚀检测技术及方法摘要:原油工艺管道因其输送的原油介质、大直径、带有保温层、以及结构复杂等原因,无法采用射线、普通超声波等传统方法进行内腐蚀的快速排查。
在对内检测技术分析的基础上,研制了超声管道内检测器功能样机,对内检测器的关键技术,如机械结构、超声检测仪、定位技术等进行了分析,提出了设计方案,经试验管道检测证明,腐蚀缺陷检测精度较高,内外定位较准确,应用前景很好。
关键词:原油管道;腐蚀;检测技术由于原油工艺管道直径大、三通弯头多、埋地或架空形式复杂,以及部分区段带有保温层,再加上石油介质对射线衰减较大,因而无法采用传统的射线检测法或管道内检测法对其进行内腐蚀的检测,目前普遍采用的检测方法为测厚法和外观检查法,但这两种方法都难以有效检出内腐蚀的准确部位和腐蚀程度。
一、管道腐蚀内检测技术管道内检测技术有漏磁法、超声法、涡流法、电磁声法等。
漏磁法是利用永久磁铁磁化管道内壁,管道腐蚀处将有磁场泄漏,传感器检测泄漏磁信号,并对信号进行处理得到管道腐蚀情况。
漏磁法适合于壁厚12 mm 以下的油气管道,具有检测能耗小、数据处理复杂、主要进行定性检测等特点,检测精度与管道壁厚有关,厚度越大精度越低,一般认为精度为±0.2 t左右,t 为管壁厚度。
超声法是利用超声探伤原理,由多探头组成探头阵列,通过输送介质耦合从管道内向管道壁发射超声波,根据回波的时间、大小,检测出探头与管道内壁的距离、管道剩余壁厚、管道腐蚀缺陷情况等。
超声法对被检测管道壁厚没有限制,但需要耦合介质,所以限制了在天然气管道中的应用,现在已有利用橡胶滚轮耦合的超声波气管内检测器。
超声法的检测能耗比漏磁法大,数据处理较明确、清晰,检测精度可达0.5 mm,是定量检测。
综合分析漏磁法和超声法各有优缺点,对于陆地石油管道超声波检测技术将有广阔的应用前景。
二、管道腐蚀超声波内检测器1、机械机构。
检测器机体是检测仪器的载体,它必须满足管道工艺和检测两方面的技术要求。
液体石油管道内腐蚀直接评价方法
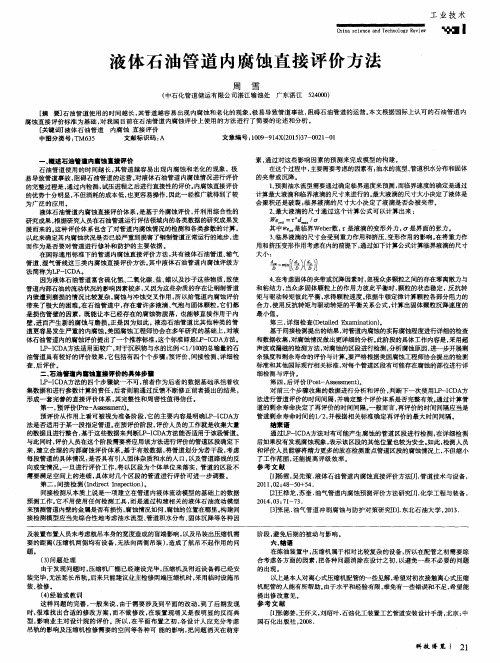
C hi n a s c i en c e a nd T e c h n o l o g y R e v i e w
●I
液 体 石 油 管道 内腐 蚀 直 接评 价 方 法
周 雪
( 中石 化 管道 储 运有 限 公司 湛江 输 油处 广 东湛 江 5 2 4 0 0 0 ) [ 摘 要] 石 油管 道使 用 的时 间越 长 , 其 管道 越容 易 出现 内腐 蚀 和老 化 的现象 , 极易 导 致管道 事 故 , 阻碍石 油管 道 的运 营 。 本 文根据 国 际上认 可 的石 油管 道 内 腐 蚀直 接 评价标 准 为基 础 , 对 我 国 目前 在 石油 管道 内腐 蚀评 价 上使 用 的方法 进行 了简 要 的论述 和 分析 。
而 作为 是否 要 对管 道进 行 修补 和 防护 的主 要依据 。 在 国际通 用标 准 下的 管道 内腐蚀 直接 评价 方法 , 共有 液 体石油 管道 、 输气 管道、 湿 气管 线这 三类 内腐 蚀直 接评 价方 法 。 其 中液体 石油 管道 内腐 蚀评级 方 法 简 称 为L P - I C D A。 因为液体 石 油管道 富 含硫 化氢 、 二 氧化碳 、 盐、 蜡 以及沙 子这 些物 质 , 致使
大小 :
鲁 一㈣ , ( 钏
4 、 在考 虑固体 的夹带 或沉降 因素时 , 忽视 众多颗粒 之 间的存在 零离散力 与 和粘结力 , 当众多固体颗粒上的作用力彼此平衡时, 颗粒的状态稳定 , 反抗转 矩 与驱动 转矩 彼此 平衡 , 求 得颗粒 速 度 依据牛 顿定 律计 算颗 粒各 部分 阻力 的 合力 , 使用反抗转矩与驱动转矩的平衡关系公式, 计算出固体颗粒沉降速度的 最小值 。 第三 , 详 细检 查 ( D e t a i l e d E x a mi n a t i o n ) 。 基于间接检测提出的结果, 对管道内腐蚀的实际腐蚀程度进行详细的检查 和数据收集 , 对腐蚀情况做出更详细的分析。 此阶段的具体工作内容是, 采用超 声波或漏磁的检测方法, 对腐蚀的区段进行检测, 分析腐蚀原因, 进一步开展剩 余强 度和剩 余寿命 的评 价与计算 。 要 严格根 据美 国腐蚀工 程师协 会提 出的检 测 标准 和其他 国际现 行相 关标准 , 对每 个管道 区段有 可能存 在腐蚀 的部 位进行详 细 检测 与评 价 。 第四, 后 评价 ( P o s t —A s s e s s me n t ) 对前 三个 步骤 收集 的数 据进行 分 析和评 价 , 判 断下 一次使 用1 2- 1 C D A 方 法 进行 管道 评价 的时 间间 隔 , 并确定 整个 评价 体系 是否 完整有 效 。 通过 计算 管 道的剩余寿命决定了再评价的时间间隔。 一般而言 , 再评价的时间间隔应当是 管道剩余寿命时间的1 / 2 , 并根据相关标准确定再评价的最大时间间隔。 结束 语 通过 L P - I C D A方法 对有 可能 产生 腐蚀 的管道 区段 进行 检 测 , 在详 细检 测 后 如果没 有发现 腐蚀 现象 , 表示该 区段 的其他 位置也 较为安 全 。 如此 , 检测 人员 和 评价人 员能够 将精力 更多 的放在检 测重 点管道 区段 的腐 蚀情 况上 , 不但 缩小 了工作 范 围 , 还 能提高 评级 效 率 。 参 考 文 献 [ 1 雪, 吴先策. 液体石油管道内腐蚀直接评价方法[ J 】 . 管道技术与设备,
石油管道腐蚀缺陷的评估治理和安全管理
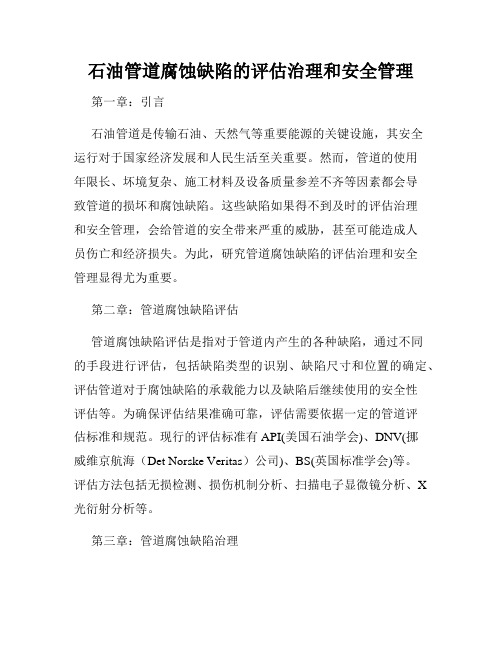
石油管道腐蚀缺陷的评估治理和安全管理第一章:引言石油管道是传输石油、天然气等重要能源的关键设施,其安全运行对于国家经济发展和人民生活至关重要。
然而,管道的使用年限长、坏境复杂、施工材料及设备质量参差不齐等因素都会导致管道的损坏和腐蚀缺陷。
这些缺陷如果得不到及时的评估治理和安全管理,会给管道的安全带来严重的威胁,甚至可能造成人员伤亡和经济损失。
为此,研究管道腐蚀缺陷的评估治理和安全管理显得尤为重要。
第二章:管道腐蚀缺陷评估管道腐蚀缺陷评估是指对于管道内产生的各种缺陷,通过不同的手段进行评估,包括缺陷类型的识别、缺陷尺寸和位置的确定、评估管道对于腐蚀缺陷的承载能力以及缺陷后继续使用的安全性评估等。
为确保评估结果准确可靠,评估需要依据一定的管道评估标准和规范。
现行的评估标准有API(美国石油学会)、DNV(挪威维京航海(Det Norske Veritas)公司)、BS(英国标准学会)等。
评估方法包括无损检测、损伤机制分析、扫描电子显微镜分析、X 光衍射分析等。
第三章:管道腐蚀缺陷治理管道腐蚀缺陷治理是指对于评估出来的缺陷进行处理的过程,其目的是减少缺陷对管道安全性的影响。
目前,管道腐蚀缺陷治理方法主要包括抛光、打磨、喷涂、加压注胶、补焊、加固和更换等。
治理方法需要根据缺陷的类型、位置和尺寸等不同因素选择合适的方法。
同时,治理过程也需要依照规定的标准和要求,对于不安全的缺陷不得继续使用,对于已经处理的缺陷需要进行再评估和监测。
第四章:管道腐蚀缺陷的安全管理作为重要的能源运输设施,石油管道的安全管理是保证管道持续安全运行的前提。
安全管理主要包括对于管道日常维护、巡检、评估、治理以及应急预案等方面的管理。
在管道的日常管理中,需要建立完善的监测体系、定期开展管道评估和检测以及进行合理的维护措施。
同时,应急预案是处理突发事件和事故的重要保障。
在石油管道安全管理体系中,需要明确责任分工,依据管道规模和重要性对管道实施分类管理,加强与有关监管部门的沟通和协作。
管线内腐蚀直接评价方法的现场应用
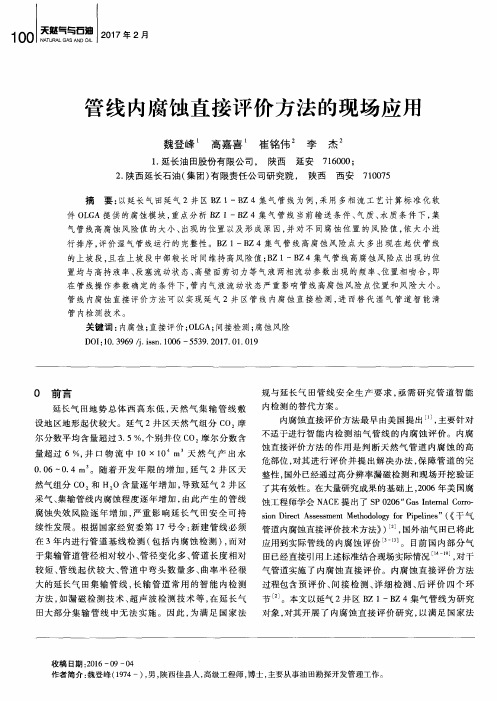
收稿 日期 : 2 0 1 6— 0 9— 0 4 作者简介 : 魏登峰 ( 1 9 7 4一) , 男, 陕西佳县人 , 高 级工程师 , 博士 , 主要从事油 田勘探开发管理工作 。
第3 5卷 第 l 期
CORROSl ON AND CORROSI ON PR0THale Waihona Puke CTl ON 0 前 言
规 与延长气 田管线 安 全 生产 要 求 , 亟需 研 究 管道 智 能
延长气 田地 势 总体 西 高 东低 , 天 然气 集 输 管线 敷 内检测 的替 代方案 。 内腐 蚀直接评价方 法最早 由美 国提 出 , 主要针对 设地 区地形起 伏较大 。延气 2井 区天然气 组分 C O, 摩 尔分数平 均含量超过 3 . 5%, 个别井位 C O 摩尔分数 含
腐蚀与日 厅 护1 01
n
舰干 ¨ 延 K气 川
管 线 安 个 乍 的 要 求 , 促 进 延 长气 丌 1
表1 延气 2井 区 B Z 1一B Z 4集 气 管线 桩 号及 高 程
安 个 可 持 续 性 发展
桩号
B o o 1 B 0 0 2 B 0 0 3 B 0 0 4 B 0 0 6
于集输 管道管径相 对较小 、 管径 变化 多、 管 道长 度相 对 田已经直接引用上述标 准结合 现场实 际情况
大 的延 长气 田集 输管 线 , 长 输管 道 常 用 的智 能 内检 测
, 对干
较短 、 管 线起 伏 较 大 、 管 道 中弯 头数 量 多 、 曲率 半径 很 气管道实施 了 内腐 蚀 直接 评价 。内腐 蚀直 接评 价方 法
过程包含 预评 价 、 间 接 检测 、 详细检测、 后 评 价 四个 环
- 1、下载文档前请自行甄别文档内容的完整性,平台不提供额外的编辑、内容补充、找答案等附加服务。
- 2、"仅部分预览"的文档,不可在线预览部分如存在完整性等问题,可反馈申请退款(可完整预览的文档不适用该条件!)。
- 3、如文档侵犯您的权益,请联系客服反馈,我们会尽快为您处理(人工客服工作时间:9:00-18:30)。
摘 要 : 于美 国腐蚀 工程 师协会 提 出的液 体石 油 管道 内腐 蚀 直接 评 价 标 准 , 绍 了适 用 于该 种 管 基 介
道 的腐蚀 直接 评 价方 法 , 阐述 了该方 法 的 4个 步骤 , 并 即预 评 价 、 间接 检 测 、 细检 查 和后 评 价 。运 用 详
油水 流型预 测 、 管道积 水情 况分 布 以及 固体 夹 带与 沉 降 3个 方 面 的模 型 来 确 定 腐 蚀 的 具体 位 置 和 数 量, 并考虑 了破 乳 、 生 物腐蚀 和 杀菌 剂 、 微 固体成 分 以及局 部流 动条 件 下对 腐蚀 分布 的影 响 。液 态石油 管道 内腐蚀 直接评 价 方法的提 出, 完善 了运输 管线 的 内腐 蚀评 价 体 系, 扩展 了其 应 用 范围 , 其 更具 有 使
2 1 0 1焦
第 2期
管 道 技 术 5 设 各
Pi ei e Te h i u a d Eq i me t p ln c nq e n up n
2 1 01
No 2 .
液体 石 油管 道 内腐 蚀 直 接 评价 方 法
杨 雪, 吴先 策
300 ) 03 0 ( 国 民航 大 学 , 中 天津
T e e mo es i cu e ah d o a b n w trf w atr t e a c mu ain o t r n e tai e o a d t ee t i me t n h s d l n l d y r c r o — ae o p t n,h c u l t wae d ra s t d f w, n n r n n d l e o f u r f l i h a a
实用性 液体 石 油管道 ; 内腐蚀 ; 直接 评价 中图分 类号 :E 8 T 98 文献标 识 码 : A 文章 编号 :0 4— 6 4 2 1 )2— 0 8—0 10 9 1 (0 1 0 0 4 3
I t r a r o in r c s s m e to q i to e m p ln n e n lCo r so Die tAse s n fLi u d Per lu Pi ei e
d p s in o o is Ma y f cos ma f c e c ro in d sr u i n s c s e li n b e k n MI n ic d s s l sc r— e i o s l . n a t r o t f d y a e t h o rso i i t , u h a mu so r a ig, C a d b o i e , oi o t tb o d n o i o a w c n i o s I s o cu e t e e d t a e p o a L p st n a d lc l o o dt n . ti c n ld d i h n h t h r p s l P —I A e f cst e I A t o oo y s s i n o l f i n t o f o CD p re t h CD me h lg y - d tr ft n miso ie ie , r a e si p l ai n s o e a d ma e t r r c ia d a p ia l n t e r lv n n i e r e o a s s in p p l s b o d n t a p i t c p k s i mo e p a t l a p l b e i h ee a t g n e — n r n s c o n c n c e
i g n.
Ke r s l u d p toe m i ei e i tr a or so ; i c s s me t y wo d :i i e l u pp l ;ne n lc ro in dr t e s n q r n e a s
YANG e. U a c Xu W Xin— e
( il Cv iA ̄a o ies yo hn , i j 0 3 0 C ia i f nUnvri fC ia Ta i 3 00 , hn ) t nn
Ab t a t A p o o e to o ie ta s s me t f iu d p t lu p p l ei tr a c ro i n h sb e e eo e . h sr c : r p s d meh d f r d rc s e s n q i er e m ie i ne n l o r so a e n d v l p d T e a ol o n u d r i g b sso ep p s d a p o c sp o i e y NAC F u tp ft i me h d h v e n e p u d d wh c r r — n e l n a i t r o e p r a h i r vd d b y f h o E. o rse s o s h t o a e b e x n e , ih a e p e o s e s n ,n ie td tci , ea l x mi ai n ta s s me t T r e mo es f t i p r a h h v e n c n ie e . a s s me t i d r c ee t n d t i d e a n t n a d p s se s n . h e d l o h s a p o c a e b e o sd r d o e o o