模具冷却系统设计
注塑模冷却系统设计原则及结构形式
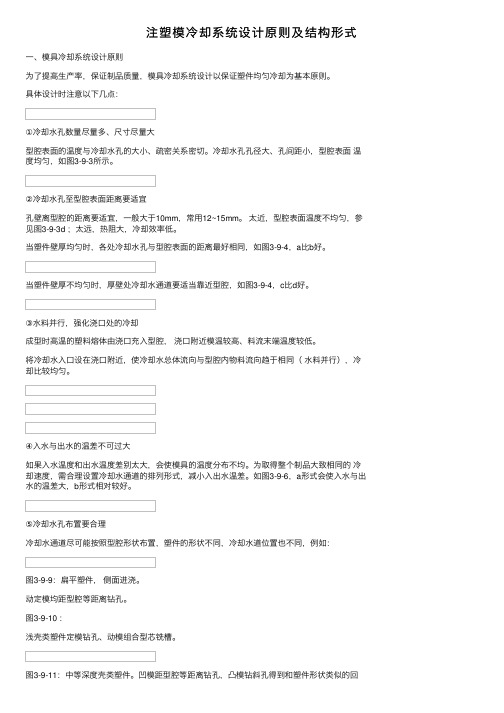
注塑模冷却系统设计原则及结构形式⼀、模具冷却系统设计原则为了提⾼⽣产率,保证制品质量,模具冷却系统设计以保证塑件均匀冷却为基本原则。
具体设计时注意以下⼏点:①冷却⽔孔数量尽量多、尺⼨尽量⼤型腔表⾯的温度与冷却⽔孔的⼤⼩、疏密关系密切。
冷却⽔孔孔径⼤、孔间距⼩,型腔表⾯温度均匀,如图3-9-3所⽰。
②冷却⽔孔⾄型腔表⾯距离要适宜孔壁离型腔的距离要适宜,⼀般⼤于10mm,常⽤12~15mm。
太近,型腔表⾯温度不均匀,参见图3-9-3d ;太远,热阻⼤,冷却效率低。
当塑件壁厚均匀时,各处冷却⽔孔与型腔表⾯的距离最好相同,如图3-9-4,a⽐b好。
当塑件壁厚不均匀时,厚壁处冷却⽔通道要适当靠近型腔,如图3-9-4,c⽐d好。
③⽔料并⾏,强化浇⼝处的冷却成型时⾼温的塑料熔体由浇⼝充⼊型腔,浇⼝附近模温较⾼、料流末端温度较低。
将冷却⽔⼊⼝设在浇⼝附近,使冷却⽔总体流向与型腔内物料流向趋于相同(⽔料并⾏),冷却⽐较均匀。
④⼊⽔与出⽔的温差不可过⼤如果⼊⽔温度和出⽔温度差别太⼤,会使模具的温度分布不均。
为取得整个制品⼤致相同的冷却速度,需合理设置冷却⽔通道的排列形式,减⼩⼊出⽔温差。
如图3-9-6,a形式会使⼊⽔与出⽔的温差⼤,b形式相对较好。
⑤冷却⽔孔布置要合理冷却⽔通道尽可能按照型腔形状布置,塑件的形状不同,冷却⽔道位置也不同,例如:图3-9-9:扁平塑件,侧⾯进浇。
动定模均距型腔等距离钻孔。
图3-9-10 :浅壳类塑件定模钻孔、动模组合型芯铣槽。
图3-9-11:中等深度壳类塑件。
凹模距型腔等距离钻孔,凸模钻斜孔得到和塑件形状类似的回路。
图3.9 1:深腔制品。
凸凹模均采⽤组合式,车螺旋槽冷却,从中⼼进⽔,在端⾯(浇⼝处)冷却后沿环绕成型零件的螺旋形⽔道顺序流出模具。
⑥冷却⽔道要便于加⼯装配冷却⽔道结构设计必须注意其加⼯⼯艺性,要易于加⼯制造,尽量采⽤钻孔等简单加⼯⼯艺。
对于镶装组合式冷却⽔道还要注意⽔路密封,防⽌冷却⽔漏⼊型腔造成型腔锈蚀。
第9章 压铸模加热和冷却系统设计

温金属液预热。 4)预热后的压铸模应进行必要的清理和润滑。 5)冷却液应该在压铸模预热之前此时通入,否
则将因激冷而引起压铸模产生裂纹甚至破裂。
9.2 模具的冷却 一、压铸模的冷却方法 压铸模的冷却方法主要有风冷和水冷两种形式. (一)风冷
通入成型镶缺或型芯内从而实现冷却,因此水冷模 具结构较风冷复杂。水冷速度比风冷速度快得多, 它能有效地提高生产效率。一般可以通过测定进水 口和出水口的温度以及模具型腔表面温度,据此控 制水流量,从而调节冷却效率。大中型铸件或厚壁 铸件以及大批量连续操作时为了保证散热员较大的 要求,通常采用水冷。
二、冷却通道的设计计算
2.熔融金属传给模具的热流量 熔融金属传给模具的热流量Q可 按下式计算
Q=qNm 式中 q——凝固热量(J/k g);
N——压铸机生产率(次/h); m——每次压铸的合金重量(kg/次)。 不同合金的凝固热量q 值,见表。
3.模具自然传走的热流量 模具自然传走的热量Q1是通 过周围辐射和传导而散发的。 其计算式可表示为
三、冷却系统的布置 (一)冷却通道的设计要点 设计冷却通道时应注意下述几点: ‘
1)冷却水道要求布置在型腔内温度最高、热量比较 集中的区域,流路要通畅,无堵塞现象。
2)模具镶拼结构上有冷却水通过时要求采取密封措 施,防止泄漏。
3)水管接头尽可能设置在模具下面或操作者的对面 一侧,其外径尺寸应统一,以便接装输水胶管。
活动型芯或者推杆发生干涉。加热孔径与电热元 件的壳体外径的配合间隙不应太大,以免降
低传热率。在动模和定模的套板上可以布置供安 装热电偶的测温孔,以便控制模温,其配合 尺寸应按照所选用的热电偶的规格而定。
模具冷却系统设计

家用电器模具冷却系统设计案例
散热器设计
家用电器模具的散热器 设计需考虑散热面积、 散热翅片间距和散热翅 片形状等因素,以提高 散热效率。
循环水道
家用电器模具的冷却系 统通常采用循环水道, 以确保冷却液能够持续 不断地流过模具表面, 带走热量。
控制系统
家用电器模具的控制系 统需具备温度控制、时 间控制和压力控制等功 能,以确保模具温度的 稳定和冷却液的循环。
05
模具冷却系统应用案例
汽车模具冷却系统设计案例
冷却水道设计
汽车模具冷却系统中的水道设计需根据模具的形状和大小进行定制, 以确保冷却液能够均匀地流过模具表面,提高冷却效果。
高效换热器
为了快速将热量从模具中带走,汽车模具冷却系统通常采用高效换 热器,如板式换热器或翅片式换热器。
控制系统
汽车模具冷却系统的控制系统需具备温度控制、流量控制和压力控制 等功能,以确保模具温度的稳定和冷却液的循环。
高生产效率。
降低能耗
选择高效的泵和风扇,以及合 适的冷却液,以降低系统能耗
。
03
模具冷却系统设计流程
确定设计目标
01
02
03
降低模具温度
通过冷却系统降低模具温 度,保证模具在连续工作 过程中温度稳定。
提高产品质量
通过控制模具温度,减少 产品成型过程中的收缩和 翘曲,提高产品尺铝等,以提高冷却效果。
加工性能
选择易于加工和制造的材料,如钢材、铝材等,以降低生产成本 和加工难度。
冷却水道加工工艺
铸造法
适用于大型模具的冷却水道加工,可以制作复杂形状的水道。
机械加工法
适用于小型模具的冷却水道加工,可以通过钻孔、铣削等机械加工 方式制作水道。
塑料模具冷却系统设计

塑料模具冷却系统设计1运水位置1.1.对收缩大的产品如PP﹑PE﹑PVC等﹐尽量沿制品收缩大的方向排布运水。
1.2.在保证模具材料强度的前提下,运水尽可能靠近型腔或型芯表面,并且围绕所成型的制品均匀布置.其尺寸要求如图:1.3.当模具采用镶拼结构,且镶件尺寸足够大时,应单独冷却,如齿轮镶件等圆形镶件,一般设置环形水路;大的行位也要单独冷却。
D=d+(1~2) (d为水道直径)1.4.模具各部分一定要均匀冷却,因结构不能设计运水的地方﹐采用铍铜方式冷却。
1.5.当两条水路空间交叉或在同一平面位置时﹐水路长度小于150,其最小间距为3mm, 水路长路大于150,其最小间距为5mm,如图:1.6. 运水应避开顶针﹑司筒﹑镶针﹑斜顶﹑直顶﹑螺丝等零件﹐其周边最小间距为3mm,当模具设置先复位机构时﹐其出入水位置不得与之发生开涉。
1.7. 当一套模具中,运水组数超过2组时,应在各出入水位置做“OUT”和“IN”的标记。
“OUT”表示出水,“IN”表示入水.同时应加上序号,表示连接的顺序。
2. 水路大小尽量选用大的水路,其最小直径为ø1/4”,迫不得已时可采用ø3/16”的水路,但最大也不能超过ø1/2”,常用水路为ø1/4”、ø5/16”、ø3/8”。
水路中各水道的直径应尽量相同,避免流速不均。
模具中,单独一组水路转接不可太多,以免影响冷却效果。
3. 水路与模胚位置关系3.1.优先考虑在模胚的宽度方向接入﹑导出运水,否则须在模胚长度方向加四支角柱。
3.2.运水原则上从模胚导入﹐不直接入内模;当运水必须直接入内模或者冷却行位时﹐应在模胚上喉咀避空槽其宽度为20~40。
3.3.直身模﹐避免水管从码模坑通过﹐应保证运水攻牙边距码模坑边5mm.。
如图所示:3.4.当前后模运水从同一方向接入﹐导出时﹐其间距应大于35mm.。
3.5.当面板厚度较小﹐又需通过运水时﹐应保证运水中心与面板顶15mm的距离。
注塑模大赛模具冷却系统优化设计及分析

注塑模大赛模具冷却系统优化设计及分析引言在注塑模具制造行业中,模具冷却系统的设计和优化对于模具的使用寿命和产品质量有着非常重要的影响。
冷却系统的设计不仅影响着产品的成型质量,还直接影响着生产效率和能耗。
对模具冷却系统进行优化设计和分析显得尤为重要。
本文将针对注塑模大赛中的模具冷却系统进行优化设计及分析,从而提高模具的使用寿命和产品的质量。
一、冷却系统的现状分析目前在注塑模具制造中,常见的冷却系统包括水冷却和油冷却两种方式。
其中水冷却是较为常见的一种方式,它通过循环水冷却来降低模具的温度,从而提高产品的成型质量和生产效率。
目前存在着一些问题需要解决:1. 冷却水温度不稳定:冷却水温度的稳定性对于模具的使用寿命和产品质量具有非常重要的影响。
目前一些冷却系统存在水温波动较大的问题,需要进一步优化。
2. 冷却水流速不均匀:在模具结构复杂的情况下,冷却水的流速分布不均匀,导致部分部位的温度较高,影响了产品的成型质量。
3. 冷却系统能耗较高:传统的冷却系统中,水泵的能耗较高,提高了生产成本,需要降低能耗,并提高能源利用效率。
以上问题的存在,导致了模具的使用寿命短、生产效率低和能耗高的情况,需要进行优化设计和分析。
二、冷却系统的优化设计1. 优化冷却水供应系统:为了解决冷却水温度不稳定的问题,需要对冷却水供应系统进行优化设计。
可以考虑设置温控阀门及温度传感器,实现对冷却水温度的精确控制。
可以考虑增加水箱的容量,提高冷却水的储备量,从而提高冷却水的稳定性。
2. 优化冷却水流通路径:针对冷却水流速不均匀的问题,可以对模具内部的冷却水通道进行优化设计。
通过调整通道的结构和布局,实现冷却水的均匀流通,提高冷却效果。
可以考虑利用CAD/CAE技术进行模拟分析,优化冷却水通道的设计,从而提高冷却效果。
3. 优化冷却系统的能耗:为了降低冷却系统的能耗,可以考虑使用高效节能的水泵,并通过优化管道布局和阀门设置,降低系统的压力损失。
模具冷却系统设计

模具冷却系统设计嘿,朋友们!咱今天来聊聊模具冷却系统设计这档子事儿。
你说这模具冷却系统啊,就好比是咱夏天里的那台大空调,没它可真不行!你想想看,模具在工作的时候那可是热气腾腾啊,就像人跑了几公里一样,浑身发烫。
这时候要是没有冷却系统来给它降降温,那可不得出问题呀!这冷却系统就像是模具的贴心小棉袄,时刻照顾着它。
咱设计这冷却系统可得讲究点。
首先呢,你得清楚模具的结构和工作原理吧,就像你得知道自己家的电器怎么用一样。
然后根据这些来选择合适的冷却方式。
是用水冷呢,还是风冷呢?这可得好好琢磨琢磨。
就说水冷吧,那水就像是一股清泉,哗啦啦地给模具冲个凉。
但你得注意水的温度和流量啊,不能太冷也不能太热,不然模具可就不高兴了。
风冷呢,就像是一阵微风,轻轻地吹走模具的热气。
可这风也得吹得恰到好处,不能乱吹一气。
还有啊,冷却管道的布置也很重要呢!你不能随便乱摆,得像排兵布阵一样,让冷却效果达到最佳。
不然这边凉了,那边还热着呢,那可不行!这就好比你给房间装空调,总不能只吹一个角落吧。
另外,冷却系统的维护也不能马虎。
你得定期检查检查,看看有没有漏水啊,管道有没有堵塞啊。
这就跟咱人要定期体检一样,有问题早发现早解决。
要是等出了大问题再去管,那可就麻烦了。
咱再说说这冷却系统设计不好会咋样。
那模具就可能变形啦,产品质量也没法保证啦,这不是给自己找麻烦嘛!你说咱辛辛苦苦做个模具,不就是为了做出好产品嘛,要是因为冷却系统没弄好搞砸了,那多冤啊!所以啊,大家可别小瞧了这模具冷却系统设计。
这可是个技术活,得用心去做。
咱得把模具当成宝贝一样照顾好,让它能好好工作,为我们生产出漂亮的产品。
你说是不是这个理儿?反正我觉得这模具冷却系统设计真的太重要啦,大家可得重视起来呀!。
模具设计规范
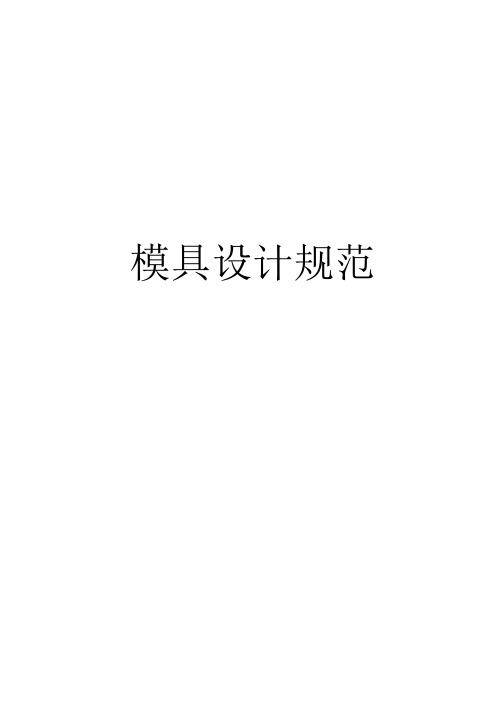
3
5 5
3.5
5 6
φ 3、φ 2.5、φ 2
φ 4、φ 5、φ 6、φ 7 φ 8 、 φ 9 、 φ 10 、 φ 12 、 φ 16 、 φ 20
d
d1+0.5
h
2.方式二:对于非DMG客户的模具顶杆止转及定位采用以下方式:
2.2
为了减少顶杆的加工量,并防止顶杆安装方向错误,特修订我公司顶杆 的杯头止转形式。改为杯头单面止转。设计尺寸见图2。 对于外单模具,若客户另有要求,按客户标准执行。无要求,则按新标 准执行。
模具设计规范
前言
• 为了满足设计及制造的要求, 指导设计工作,现将设计及制 造中应注意的问题加以整理。 待设计标准系统化后再行纳入。
•
海尔模具标准化办公室
一、冷却系统设计
1.1、模板冷却设计要求
* 三板模:要求水口板加冷却水路。 * 热流道模具:要求热流道板加冷却水 路。每个热嘴必须单独冷却。 * 对于模具长度超过1000MM的情况下, 底针板,底板必须加单独的冷却回路, 以保证针板与后模板温度一致。
*三板模倒锥形拉料杆:
三板模倒锥形拉料杆的作用主要是通过倒 扣力拉断点浇口.其设计参照:《标准件库》
*分流道拉料杆:
图5 分流道拉料杆设计
设计要点: (1)对于较长的分流道系统,应设计分流道拉 料杆.其主要作用是顶出分流道. (2) 分流道拉料杆的头部设有冷料井 , 深度 3MM 左右 , 目的为了分流道料把顶出过 程中起到导向作用,使料把顶出平衡.
以上两种形式在没有海尔模具的标准,对于没有特殊设计标准的模具均采用上述方式加工。
3.2、搭接流道设计
对于锥形流道加工在模具的两个零件上的情况,应考虑脱模, 将流道设计成如图3.1形式。一般C>0.2MM.
模具冷却系统设计意义

模具冷却系统设计意义在现代化工业生产中,模具冷却系统发挥着至关重要的作用。
本文将详细探讨模具冷却系统的设计意义,以及它在提高生产效率、保证产品质量方面所起到的重要职能。
一、什么是模具冷却系统?模具冷却系统是注塑模具、压铸模具等热加工模具中不可或缺的组成部分。
其主要功能是在模具内部循环冷却介质,通过吸收模具热量,达到控制模具温度、保证产品质量和提高生产效率的目的。
二、模具冷却系统设计意义1.提高生产效率在热加工过程中,模具温度过高会导致生产周期延长,降低生产效率。
通过设计合理的模具冷却系统,可以有效控制模具温度,使得生产周期缩短,提高生产效率。
2.保证产品质量模具温度对产品质量具有重要影响。
合理的模具冷却系统可以确保模具温度均匀分布,减少产品变形、应力集中等缺陷,从而提高产品质量。
3.延长模具寿命过高的模具温度会导致模具材料性能下降,加速模具磨损,降低模具寿命。
通过设计合理的模具冷却系统,可以有效降低模具温度,延长模具的使用寿命。
4.减少能源消耗在热加工过程中,合理的模具冷却系统可以降低能源消耗。
因为冷却系统可以快速将模具热量带走,减少了对加热设备的依赖,从而降低了能源消耗。
5.提高产品竞争力设计合理的模具冷却系统,可以使得产品质量更高、生产周期更短,从而提高产品竞争力。
三、模具冷却系统设计要点1.合理选择冷却介质:根据生产需求和模具材料,选择合适的冷却介质,如水、油、空气等。
2.确定冷却通道布局:根据模具结构和产品要求,合理布局冷却通道,确保模具温度均匀分布。
3.优化冷却系统参数:根据实际生产情况,调整冷却系统参数,如流量、压力等,以实现最佳冷却效果。
4.考虑模具材料热导率:不同模具材料的热导率不同,设计时要充分考虑这一点,以提高冷却效果。
5.重视冷却系统的维护:定期检查、清洗和更换冷却系统部件,确保冷却效果稳定。
总结:模具冷却系统设计在热加工行业中具有重要意义。
通过合理设计,可以降低模具温度、提高生产效率、保证产品质量、延长模具寿命,从而提高产品竞争力。
注塑模冷却系统设计

注塑模冷却系统设计一、冷却系统原理冷却系统的设计原则包括以下几点:1.均匀冷却:冷却通道应布置得均匀,确保注塑模腔内的温度分布均匀,避免产生缺陷。
2.高效冷却:冷却通道应尽可能靠近模具表面,并减小冷却通道的截面积,以增加冷却介质对模具的冷却效果,提高生产效率。
3.多角度冷却:在模具中设置多个冷却通道,使冷却介质能够从不同的角度覆盖模具表面,提高冷却效果。
4.控制温度:通过合理设置冷却通道的长度、截面积和数量等参数,控制注塑模的冷却速度,确保产品达到理想的尺寸和性能。
二、冷却系统设计流程1.模具结构分析:根据产品的形状和尺寸,对模具进行结构分析,确定冷却通道的位置和数量。
2.冷却通道设计:根据模具结构,设计冷却通道的形状、截面积和长度等参数。
一般来说,冷却通道应尽量靠近模具表面,避免过于接近模腔导致冷却效果不佳。
3.冷却通道布置:根据模具结构和产品的需求,合理布置冷却通道的位置和数量。
通常情况下,冷却通道应均匀分布在模具的各个部位,并且覆盖整个模具表面。
4.冷却介质选型:选择合适的冷却介质,通常是冷水。
冷却介质的选择应考虑到模具材料的热导率、流动性以及生产环境等因素。
5.防止冷却死角:在冷却系统设计中,应尽量避免冷却死角的产生。
冷却死角是指冷却介质在注塑模内积聚,无法很好地冷却模具的局部区域。
为了避免冷却死角,可以设置细小的冷却通道或者采用多角度冷却。
三、冷却系统优化方面为了进一步提高冷却系统的效果,可以从以下几个方面进行优化:1.模腔温度分析:利用模具流动分析软件,对模腔的温度分布进行分析,找出温度较高或较低的区域,并针对性地调整冷却通道的布置。
2.冷却介质控制:通过对冷却介质的输送速度、温度和压力等参数进行控制,进一步提高冷却效果。
3.冷却材料选择:选择具有较好导热性能的冷却材料,如铜合金等,以提高冷却效果。
4.模具表面处理:在模具表面进行特殊处理,如磨削、喷砂等,增加表面的热传导性,提高冷却效果。
模具设计中的冷却系统设计与优化分析

模具设计中的冷却系统设计与优化分析在模具设计中,冷却系统的设计和优化是非常重要的一部分。
冷却系统的设计直接影响着模具的使用寿命、生产效率和产品质量。
本文将从冷却系统的设计原则、优化方法和实际案例分析三个方面来探讨模具设计中的冷却系统设计与优化分析。
一、冷却系统的设计原则冷却系统的设计原则主要包括以下几个方面:1. 冷却系统的位置和布局:冷却系统应该尽可能地靠近模具的加热部位,以提高冷却效果。
同时,冷却系统的布局应该合理,避免冷却死角,确保冷却水能够充分覆盖模具表面。
2. 冷却水的流速和温度:冷却水的流速应该适中,过大会浪费资源,过小则无法有效降温。
冷却水的温度也需要控制在合适的范围内,过高会导致冷却效果不佳,过低则可能引起冷凝水等问题。
3. 冷却系统的材料选择:冷却系统的材料应该具有良好的导热性和耐腐蚀性。
常见的冷却系统材料有铜、铝、不锈钢等。
在选择材料时,需要考虑模具的工作环境和使用寿命。
4. 冷却系统的管道设计:冷却系统的管道设计应该尽量简洁明了,避免过多的弯曲和分支,以减少流阻和压力损失。
同时,管道的直径和厚度也需要合理选择,以保证冷却水的流量和压力。
二、冷却系统的优化方法在模具设计中,冷却系统的优化方法主要包括以下几个方面:1. 流场模拟分析:通过流场模拟分析,可以预测冷却水的流动情况和温度分布,帮助设计师找出冷却死角和热点位置,并进行合理的优化设计。
2. 冷却系统的分区设计:根据模具的不同部位和工艺要求,将冷却系统划分为不同的区域,以便针对性地进行优化设计。
例如,在需要加热的部位增加冷却水的流量和温度,以提高冷却效果。
3. 冷却系统的循环方式:冷却系统的循环方式有单循环和双循环两种。
单循环适用于冷却要求相对较低的模具,而双循环适用于冷却要求较高的模具。
在选择循环方式时,需要考虑冷却效果和成本之间的平衡。
三、实际案例分析为了更好地理解模具设计中的冷却系统设计与优化分析,下面将以一个注塑模具为例进行实际案例分析。
模具加热及冷却系统设计
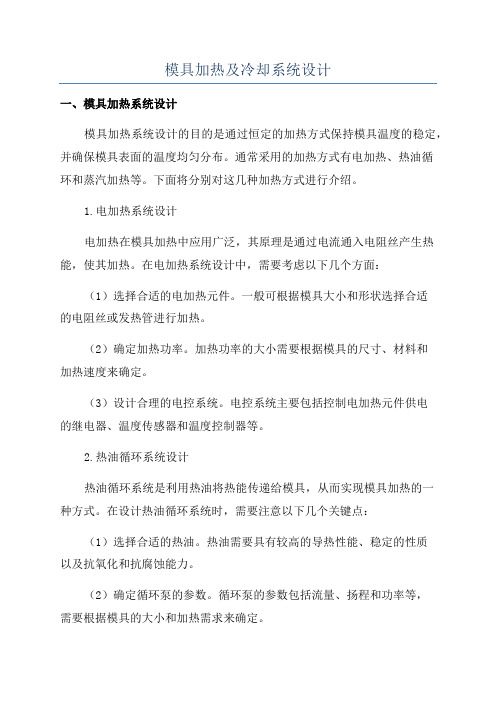
模具加热及冷却系统设计一、模具加热系统设计模具加热系统设计的目的是通过恒定的加热方式保持模具温度的稳定,并确保模具表面的温度均匀分布。
通常采用的加热方式有电加热、热油循环和蒸汽加热等。
下面将分别对这几种加热方式进行介绍。
1.电加热系统设计电加热在模具加热中应用广泛,其原理是通过电流通入电阻丝产生热能,使其加热。
在电加热系统设计中,需要考虑以下几个方面:(1)选择合适的电加热元件。
一般可根据模具大小和形状选择合适的电阻丝或发热管进行加热。
(2)确定加热功率。
加热功率的大小需要根据模具的尺寸、材料和加热速度来确定。
(3)设计合理的电控系统。
电控系统主要包括控制电加热元件供电的继电器、温度传感器和温度控制器等。
2.热油循环系统设计热油循环系统是利用热油将热能传递给模具,从而实现模具加热的一种方式。
在设计热油循环系统时,需要注意以下几个关键点:(1)选择合适的热油。
热油需要具有较高的导热性能、稳定的性质以及抗氧化和抗腐蚀能力。
(2)确定循环泵的参数。
循环泵的参数包括流量、扬程和功率等,需要根据模具的大小和加热需求来确定。
(3)设计供热系统。
供热系统包括加热炉、加热管、加热器和控制系统等。
3.蒸汽加热系统设计蒸汽加热系统是将蒸汽传导至模具表面进行加热的一种方式。
在进行蒸汽加热系统设计时,需要注意以下几个方面:(1)选择合适的蒸汽压力。
蒸汽压力需要根据模具的形状和尺寸来确定,以确保蒸汽能够充分覆盖模具表面。
(2)设计合理的蒸汽供应系统。
蒸汽供应系统包括蒸汽管道、调压阀、过滤器和控制系统等。
(3)确保安全性。
蒸汽加热系统应采取必要的安全措施,如安装安全防护装置、检测和处理漏气等。
模具冷却系统设计的目的是通过冷却水或冷却剂将模具温度降低到所需的范围内,以便于产品成型和模具的连续使用。
冷却系统设计的关键点包括冷却方式、冷却水路设计和冷却剂的选择等。
1.冷却方式常见的模具冷却方式有直接冷却和间接冷却两种。
(1)直接冷却是将冷却水通过冷却水道直接注入模具腔体中进行冷却。
塑胶模具冷却系统设计
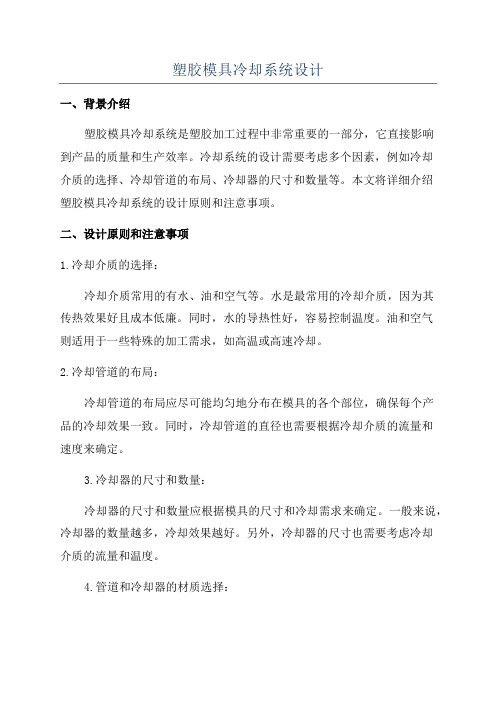
塑胶模具冷却系统设计一、背景介绍塑胶模具冷却系统是塑胶加工过程中非常重要的一部分,它直接影响到产品的质量和生产效率。
冷却系统的设计需要考虑多个因素,例如冷却介质的选择、冷却管道的布局、冷却器的尺寸和数量等。
本文将详细介绍塑胶模具冷却系统的设计原则和注意事项。
二、设计原则和注意事项1.冷却介质的选择:冷却介质常用的有水、油和空气等。
水是最常用的冷却介质,因为其传热效果好且成本低廉。
同时,水的导热性好,容易控制温度。
油和空气则适用于一些特殊的加工需求,如高温或高速冷却。
2.冷却管道的布局:冷却管道的布局应尽可能均匀地分布在模具的各个部位,确保每个产品的冷却效果一致。
同时,冷却管道的直径也需要根据冷却介质的流量和速度来确定。
3.冷却器的尺寸和数量:冷却器的尺寸和数量应根据模具的尺寸和冷却需求来确定。
一般来说,冷却器的数量越多,冷却效果越好。
另外,冷却器的尺寸也需要考虑冷却介质的流量和温度。
4.管道和冷却器的材质选择:管道和冷却器的材质应具有良好的导热性和抗腐蚀性。
常用的材质有铜、铝和不锈钢等。
同时,材质的选择也需要考虑成本和耐用性等方面。
5.控制冷却温度:冷却温度的控制对产品的成型质量有直接影响。
应根据具体产品的要求来确定冷却温度。
一般来说,温度过低会导致产品收缩过大,而温度过高则会导致产品变形。
6.检测和维护:冷却系统应配备温度传感器和压力传感器等装置,对冷却效果进行实时监测。
同时,冷却系统还需要进行定期的清洗和维护,确保其正常运行和延长使用寿命。
三、冷却系统设计实例以注塑模具为例,冷却系统的设计可以按照以下步骤进行:1.确定冷却介质的选择:一般使用水作为冷却介质,因为其成本低廉且传热效果好。
2.根据模具的尺寸和形状设计冷却管道的布局:确保冷却管道能够均匀地覆盖整个模具,并避免冷却死角。
3.根据冷却需求选择冷却器的尺寸和数量:根据模具的尺寸和冷却需求,选择合适的冷却器尺寸和数量。
4.选择合适的管道和冷却器材质:选择具有良好导热性和抗腐蚀性的材质,如不锈钢。
注塑模具冷却水路设计

注塑模具冷却水路设计一、冷却系统的设计原则1.均匀性原则:冷却水应能均匀地覆盖整个模具表面,保证模具各部位的冷却效果一致,避免出现局部过热或过冷的现象。
2.高效性原则:冷却水应尽可能快速地吸收模具上的热量,提高冷却速度,并迅速排出,以提高生产效率。
3.经济性原则:冷却系统的设计应尽量减少冷却水的流量和能耗,降低生产成本。
4.安全性原则:冷却系统的设计应考虑防止冷却水泄漏、烫伤操作人员等安全问题。
二、冷却水路的布置方式1.双水路布置:常用的冷却水路设计方式是双水路布置,即将进水和出水管道分开设置。
进水管道和出水管道应相对布置,使冷却水能够充分覆盖模具的表面,使冷却效果更好。
2.直线布置:冷却水路一般采用直线布置,以迅速传递模具表面的热量,提高冷却效果。
直线布置的冷却水路应尽量减少弯头和弯管,以降低水流阻力。
3.弯头布置:当模具的形状不规则或空间有限时,可以采用弯头布置的冷却水路,使冷却水能够覆盖到模具的各个部位。
但是,弯头布置会增加水流阻力,影响冷却效果,所以应尽量减少弯头的数量。
4.分级布置:对于大型模具或需要长时间注塑的产品,可以采用分级布置的冷却水路,将冷却水路分为多段,以提高冷却效果。
三、冷却水路的设计步骤1.根据产品的形状和结构,确定冷却水路的布置方式,包括进水管道和出水管道的位置和数量。
2.根据模具的尺寸和材料,计算冷却水路的长度和直径,并确定冷却水的流量和压力。
3.选择合适的冷却水路元件,如水管、弯头、分流装置等,并计算和确定它们的尺寸和数量。
4.验算冷却水路的设计是否符合要求,包括冷却水的流速、流量、冷却时间等。
5.根据模具的具体情况,设计冷却水路的进水和出水管道的接口,确保冷却水能够顺利流入和排出。
6.绘制冷却水路的详细图纸,包括冷却水路的布置、元件的尺寸和位置等。
四、注意事项1.冷却水路的布置应尽量远离模具的加热部位,避免冷却水的温度受到影响。
2.冷却水路的材料应选择耐腐蚀的材料,如不锈钢、铜等,以防止冷却水对模具的腐蚀。
模具冷却系统设计

模具冷却系统设计模具冷却系统是模具加工过程中非常重要的一部分,它能够有效控制模具的温度,保证产品质量和生产效率。
在模具冷却系统的设计中,需要考虑多个方面的因素,包括冷却介质、冷却方式、冷却剂的选择以及冷却系统的布局等。
首先,选择合适的冷却介质是模具冷却系统设计的第一步。
目前常用的冷却介质有水、油和空气等。
水是最常用的冷却介质,因为它的导热性非常好。
在选择冷却介质时,需要考虑模具的材质和加工需求,并根据不同工况选取不同的冷却介质。
其次,冷却方式的选择也是模具冷却系统设计的一个重要环节。
常见的冷却方式有直接冷却和间接冷却。
直接冷却是指冷却介质直接接触到模具表面进行冷却,效果较好。
间接冷却则是通过冷却系统将冷却介质传导到模具表面进行冷却。
冷却方式的选择要根据具体情况进行,确保能够达到预期的冷却效果。
冷却剂的选择也非常重要,它决定了模具冷却系统的性能和寿命。
常见的冷却剂有水溶液、油和空气等。
水溶液是目前最常用的冷却剂,因为它的导热性能好,且成本较低。
油是另一种常见的冷却剂,通常用于高温和高压的工作环境。
空气冷却剂则适用于特殊的工况,如空气冷却系统。
最后,冷却系统的布局也是模具冷却系统设计的一个重要考量因素。
良好的布局能够确保冷却介质能够均匀地分布到整个模具表面,从而提高冷却效果。
通常情况下,冷却系统会设计成多个通道,通过管道连接到模具的各个部位,以实现效果的均匀冷却。
除了上述几个方面的考虑因素外,还应该考虑冷却系统的控制和监测。
冷却系统通常会配有温度控制器和传感器用来监测和调节冷却介质的温度。
这样能够确保冷却系统始终处于最佳工作状态。
总之,模具冷却系统设计需要综合考虑多个因素,包括冷却介质的选择、冷却方式的选择、冷却剂的选择、冷却系统的布局以及控制和监测等。
只有根据具体的工况和需求进行合理的设计,才能确保模具冷却系统的效果和性能最佳。
模具冷却系统设计

提高生产效率
通过快速冷却模具,缩短成型 周期,提高生产效率。
02
模具冷却系统设计基础
冷却液的选择
冷却液类型
根据模具材料、工艺要求和冷却 效果,选择合适的冷却液,如水 、油、丙二醇等。
冷却液性能
考虑冷却液的沸点、冰点、比热 容、粘度等物理性质,以确保良 好的冷却效果和流动性。
分析模具热量来源
了解模具在工作过程中产生的热量来源,如塑料熔体注入、模具与材料摩擦等, 以便合理分配冷却液流量和压力。
设计冷却液流道
确定冷却液流道数量和位置
根据模具结构和热量分布情况,合理确定冷却液流道数量和位置,以确保冷却液均匀分布到模具各部 分。
设计冷却液流道尺寸和形状
根据冷却液流量和压力要求,设计合理的流道尺寸和形状,以提高冷却效果和减少冷却时间。
模具冷却系统设计
汇报人:文小库 2023-12-25
目录
• 模具冷却系统简介 • 模具冷却系统设计基础 • 模具冷却系统设计流程 • 模具冷却系统优化设计 • 模具冷却系统设计实例
01
模具冷却系统简介
冷却系统的重要性
01
02
03
控制模具温度
保持模具温度在适宜范围 内,确保塑料在模具内流 动和成型过程的稳定性。
冷却系统的热交换效率分析
热交换面积
通过增加或减少热交换面积,优化热交换效率。
热交换器效率
分析热交换器的设计参数,如传热系数、流体阻力等,以提高热交换效率。
03
模具冷却系统设计流程
确定模具温度需求
确定模具各部分需要达到的冷却温度范围
根据产品要求、模具结构和工艺参数,确定模具各部分需要达到的冷却温度范围 ,以确保产品成型质量和模具寿命。
锌合金模具冷却系统设计
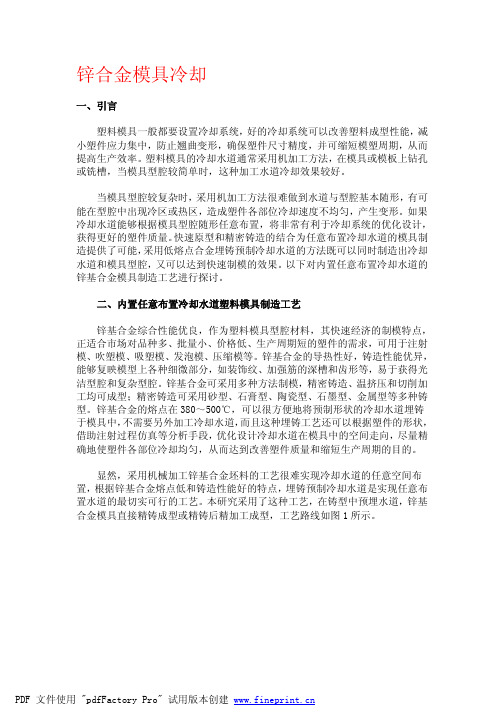
锌合金模具冷却一、引言塑料模具一般都要设置冷却系统,好的冷却系统可以改善塑料成型性能,减小塑件应力集中,防止翘曲变形,确保塑件尺寸精度,并可缩短模塑周期,从而提高生产效率。
塑料模具的冷却水道通常采用机加工方法,在模具或模板上钻孔或铣槽,当模具型腔较简单时,这种加工水道冷却效果较好。
当模具型腔较复杂时,采用机加工方法很难做到水道与型腔基本随形,有可能在型腔中出现冷区或热区,造成塑件各部位冷却速度不均匀,产生变形。
如果冷却水道能够根据模具型腔随形任意布置,将非常有利于冷却系统的优化设计,获得更好的塑件质量。
快速原型和精密铸造的结合为任意布置冷却水道的模具制造提供了可能,采用低熔点合金埋铸预制冷却水道的方法既可以同时制造出冷却水道和模具型腔,又可以达到快速制模的效果。
以下对内置任意布置冷却水道的锌基合金模具制造工艺进行探讨。
二、内置任意布置冷却水道塑料模具制造工艺锌基合金综合性能优良,作为塑料模具型腔材料,其快速经济的制模特点,正适合市场对品种多、批量小、价格低、生产周期短的塑件的需求,可用于注射模、吹塑模、吸塑模、发泡模、压缩模等。
锌基合金的导热性好,铸造性能优异,能够复映模型上各种细微部分,如装饰纹、加强筋的深槽和齿形等,易于获得光洁型腔和复杂型腔。
锌基合金可采用多种方法制模,精密铸造、温挤压和切削加工均可成型;精密铸造可采用砂型、石膏型、陶瓷型、石墨型、金属型等多种铸型。
锌基合金的熔点在380~500℃,可以很方便地将预制形状的冷却水道埋铸于模具中,不需要另外加工冷却水道,而且这种埋铸工艺还可以根据塑件的形状,借助注射过程仿真等分析手段,优化设计冷却水道在模具中的空间走向,尽量精确地使塑件各部位冷却均匀,从而达到改善塑件质量和缩短生产周期的目的。
显然,采用机械加工锌基合金坯料的工艺很难实现冷却水道的任意空间布置,根据锌基合金熔点低和铸造性能好的特点,埋铸预制冷却水道是实现任意布置水道的最切实可行的工艺。
模具冷却系统设计课件

温度控制系统设计
设计精确的温度控制系统,实现模具 温度的精确控制,提高锻件质量。
CHAPTER
模具冷却系统设计优化与改 进建议
提高冷却效率的优化措施
优化冷却管道设计
增加冷却液流量 采用多级冷却系统
降低能耗的改进建议
采用更高效的冷却液
01
优化冷却时间
02
模具冷却系统设计课 件
目 录
• 模具冷却系统概述 • 模具冷却系统设计基础 • 模具冷却系统设计实例 • 模具冷却系统设计优化与改进建议 • 模具冷却系统设计常见问题及解决方案 • 模具冷却系统设计发展趋势与展望
contents
CHAPTER
模具冷却系统概述
模具的定义与重要性
在生产过程中,模具需要承受高温、 高压、摩擦等恶劣条件,因此其质量 和稳定性对于生产效率和产品质量至 关重要。
冷却系统在模具中的作用与重要性
冷却系统在模具中起到控制温度的作用,使模具在生产过程中保持稳定 的温度状态。
冷却系统可以有效地降低模具的温度,防止模具过热或变形,从而提高 模具的使用寿命和产品的质量。
如果模具温度控制不当,可能会导致产品变形、开裂、起泡等问题,同 时也会缩短模具的使用寿命,增加生产成本。因此,冷却系统在模具中 具有重要的作用。
模具冷却系统设计发展趋势 与展望
高效节能技术的发展趋势
智能化控制技术的发展趋势
绿色制造技术的发展趋势
WATCHING
冷却时间过长问题及解决方案
冷却时间过长问题
解决方案
冷却液泄漏问题及解决方案
冷却液泄漏问题
冷却液泄漏不仅会污染环境,还会导致模具过早失效。
解决方案