基于plc控制的电热锅炉
基于PLC的锅炉电加热控制系统设计

基于PLC的锅炉电加热控制系统设计摘要本文针对锅炉电加热控制系统的实际需求,基于PLC,设计了一种可靠的电加热控制系统。
该系统通过PLC的控制,实现了对电加热器的开启、关闭、电流的调节等功能。
同时,系统还通过人机界面进行了参数设置和异常报警等功能。
实验结果表明,该系统具有高可靠性、稳定性,能够满足锅炉电加热的实际需求。
关键词:PLC、锅炉、电加热、控制系统一、引言锅炉是工业生产中常用的一种设备,其主要作用是将水加热为蒸汽,并通过蒸汽驱动液体或气体来完成工业生产流程。
而锅炉的加热方式一般有煤、油、气、电等多种方式,其中电加热由于其无污染、易控制等优点,被广泛应用于各种工业生产环节中。
然而,锅炉电加热控制系统的设计存在一些问题,如控制精度低、容易出现故障等。
这些问题给锅炉电加热操作带来了很大的不便,因此,需要设计一种基于PLC的锅炉电加热控制系统,以提高其可靠性和稳定性。
二、设计思路和方法1.设计思路基于以上问题,本文设计了一种基于PLC的锅炉电加热控制系统。
该系统采用西门子S7-200 PLC作为主控制器,通过PLC与电加热装置进行连接,实现对电加热装置的开关控制和电流调节。
同时,本文还设计了人机界面,以便进行参数设置和异常报警等功能。
通过该系统,可以实现对电加热的精确控制,从而提高锅炉的加热效率和生产稳定性。
2.设计方法(1)硬件部分设计系统硬件包含主要的PLC、电加热器、人机界面等几个部分。
PLC:采用西门子S7-200 PLC作为主控制器,通过该控制器,实现对电加热设备的精确控制。
电加热器:采用模块化的电加热器,可以根据实际需求进行扩展和修改。
人机界面:设计了触摸屏人机界面,以便进行电加热控制和参数设置等功能。
(2)软件部分设计软件部分主要包含PLC程序和人机界面程序两部分。
PLC程序:由于锅炉电加热主要是控制电加热的开关和电流调节,因此,PLC程序中主要包含电加热开关控制、电流调节等基本功能。
基于PLC控制的锅炉供热控制系统设计毕业设计说明书 精品推荐

基于PLC控制的锅炉供热控制系统设计1 引言1.1 技术综述自70年代以来,由于工业过程控制的需要,特别是在电子技术的迅猛发展,以及自动控制理论和设计方法发展的推动下,国外温度控制系统发展迅速,并在智能化自适应参数自整定等方面取得成果。
在这方面以日本、美国、德国、瑞典等国技术领先,并且都生产出了一批商品化的性能优异的温度控制器及仪器仪表,在各行业广泛应用。
目前,国外温度控制系统及仪表正朝着高精度智能化、小型化等方面快速发展。
温度控制系统在国内各行各业的应用虽然已经十分广泛,但从国内生产的温度控制器来讲,总体发展水平仍然不高,同国外的日本、美国、德国等先进国家相比,仍然有着较大的差距。
目前,我国在这方面总体技术水平处于20世纪80年代中后期水平。
成熟产品主要以“点位”控制及常规的PID控制器为主,它只能适应一般温度系统控制,难于控制滞后复杂时变温度系统控制,而且适应于较高控制场合的智能化、自适应控制仪表国内技术还不十分成熟,形成商品化并广泛应用的控制仪表较少。
现在,我国在温度等控制仪表业与国外还有着一定的差距。
温度控制系统大致可分别用3种方式实现,一种是用仪器仪表来控制温度,这种方法控制的精度不高。
另一种是基于单片机进行PID控制,然而单片机控制的DDC 系统软硬件设计较为复杂, 特别是涉及到逻辑控制方面更不是其长处, 而PLC 在这方面却是公认的最佳选择。
随着PLC功能的扩充在许多PLC控制器中都扩充了PID 控制功能。
因此本设计选用西门子S7-300PLC来控制加热炉的温度。
1.2 系统工作原理加热炉温度控制系统基本构成如图1-1所示,它由PLC主控系统、固态继电器、加热炉、温度传感器等4个部分组成。
PLC主控系统图1-1 加热炉温度控制系统基本组成加热炉温度控制实现过程是:首先温度传感器将加热炉的温度转化为电压信号,PLC主控系统内部的A/D将送进来的电压信号转化为西门子S7-300PLC可识别的数字量,然后PLC将系统给定的温度值与反馈回来的温度值进行比较并经过PID运算处理后,给固态继电器输入端一个控制信号控制固态继电器的输出端导通与否从而使加热炉开始加热或停止加热。
基于PLC和触摸屏的电热锅炉控制系统改造

为 了限 制循 环 泵 的起 动 电 流 , 化 起 动 过 程 , 原 有 循 环 泵 优 将 的 自耦 变 压 器起 动装 置 更 换 为 软 启 动 装 置 ,可 以利 用 软 启 动 装 置 的软 停 车 功 能 降低 停 泵 时 的 水锤 效 应 。
4 工 作 原 理
用单 片机 为 控 制核 心 的专 用 控制 系统 。
5 系统 设 计 5 1 系 统 硬件 设 计 ( ) 辑控 制 部 分 1逻
供 暖 系 统 主 要 由 2台 电锅 炉 、 中每 台 电热 锅 炉 包 含 有 1 其 O 组 8 W 加 热 器 。2台 75W 补 水 泵 、 k .k 2台 3 k 循 环 水 泵 以 及 0W 若 干管 道 、 门等 构 成 , 别 由 1台单 片 机控 制 系 统 控 制 , 水 阀 分 补 泵 和循 环 水 泵均 采 用 传 统 继 电器 控 制 。 工 作原 理 是 : 台锅 炉 其 两 并 列 运 行 , 片 机 控 制 系统 对 电热 锅 炉 内水 温进 行 监 测 , 据 温 单 根 度 情 况 对 电 加热 器 进 行 投 退 控 制 ,控 制 锅 炉 内水 温 度 在 设 定 范 围 内 , 同时 1台循 环 水 泵 运 行 将 锅 炉 内热 水 向办 公 区和 生 活 区
tols t m r yse wors, t i de cr t o ch un t n o l sgn k de al ed s i i p on fea f ci alm due de i ap oa . o pr ch
Ke wo d : L t c s ee ee ti i s,o to1r so mat y r s P C, ou h cr n,lc r bol c n r .an fr c er t i on
基于plc的锅炉控制系统的设计方案
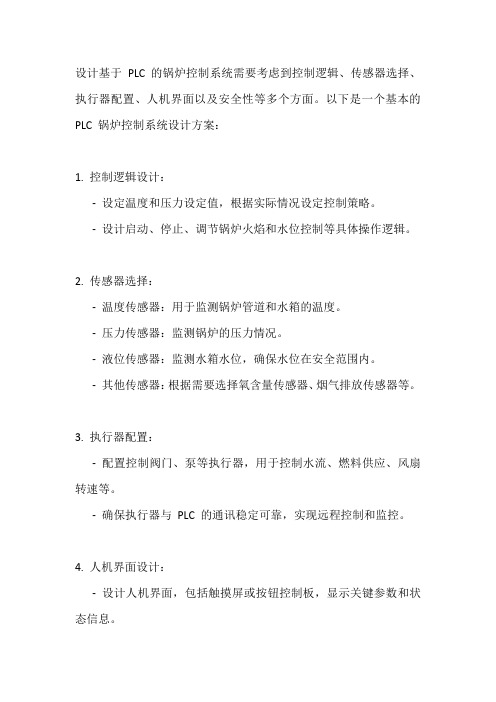
设计基于PLC 的锅炉控制系统需要考虑到控制逻辑、传感器选择、执行器配置、人机界面以及安全性等多个方面。
以下是一个基本的PLC 锅炉控制系统设计方案:1. 控制逻辑设计:-设定温度和压力设定值,根据实际情况设定控制策略。
-设计启动、停止、调节锅炉火焰和水位控制等具体操作逻辑。
2. 传感器选择:-温度传感器:用于监测锅炉管道和水箱的温度。
-压力传感器:监测锅炉的压力情况。
-液位传感器:监测水箱水位,确保水位在安全范围内。
-其他传感器:根据需要选择氧含量传感器、烟气排放传感器等。
3. 执行器配置:-配置控制阀门、泵等执行器,用于控制水流、燃料供应、风扇转速等。
-确保执行器与PLC 的通讯稳定可靠,实现远程控制和监控。
4. 人机界面设计:-设计人机界面,包括触摸屏或按钮控制板,显示关键参数和状态信息。
-提供操作界面,方便操作员设定参数、监控运行状态和进行故障诊断。
5. 安全性设计:-设计安全保护系统,包括过压保护、过温保护、水位保护等,确保锅炉运行安全。
-设置报警系统,当参数超出设定范围时及时警示操作员。
6. 通讯接口:-考虑与其他系统的通讯接口,如SCADA 系统、远程监控系统等,实现数据传输和远程控制。
7. 程序设计:-使用PLC 编程软件编写程序,包括控制逻辑、报警逻辑、自诊断等功能。
-测试程序逻辑,确保系统稳定可靠,符合设计要求。
以上是基于PLC 的锅炉控制系统设计方案的基本步骤,具体设计还需根据实际情况和需求进行调整和优化。
在设计过程中,还需遵循相关标准和规范,确保系统安全可靠、运行稳定。
基于PLC的电热锅炉控制系统的设计
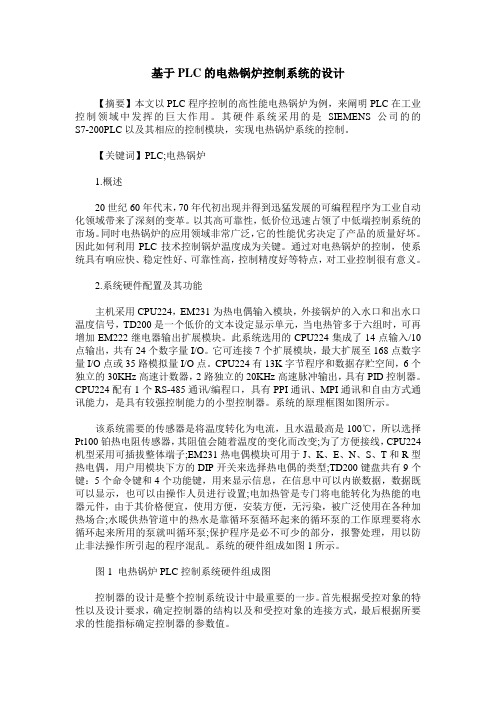
基于PLC的电热锅炉控制系统的设计【摘要】本文以PLC程序控制的高性能电热锅炉为例,来阐明PLC在工业控制领域中发挥的巨大作用。
其硬件系统采用的是SIEMENS公司的的S7-200PLC以及其相应的控制模块,实现电热锅炉系统的控制。
【关键词】PLC;电热锅炉1.概述20世纪60年代末,70年代初出现并得到迅猛发展的可编程程序为工业自动化领域带来了深刻的变革。
以其高可靠性,低价位迅速占领了中低端控制系统的市场。
同时电热锅炉的应用领域非常广泛,它的性能优劣决定了产品的质量好坏。
因此如何利用PLC技术控制锅炉温度成为关键。
通过对电热锅炉的控制,使系统具有响应快、稳定性好、可靠性高,控制精度好等特点,对工业控制很有意义。
2.系统硬件配置及其功能主机采用CPU224,EM231为热电偶输入模块,外接锅炉的入水口和出水口温度信号,TD200是一个低价的文本设定显示单元,当电热管多于六组时,可再增加EM222继电器输出扩展模块。
此系统选用的CPU224集成了14点输入/10点输出,共有24个数字量I/O。
它可连接7个扩展模块,最大扩展至168点数字量I/O点或35路模拟量I/O点。
CPU224有13K字节程序和数据存贮空间,6个独立的30KHz高速计数器,2路独立的20KHz高速脉冲输出,具有PID控制器。
CPU224配有1个RS-485通讯/编程口,具有PPI通讯、MPI通讯和自由方式通讯能力,是具有较强控制能力的小型控制器。
系统的原理框图如图所示。
该系统需要的传感器是将温度转化为电流,且水温最高是100℃,所以选择Pt100铂热电阻传感器,其阻值会随着温度的变化而改变;为了方便接线,CPU224机型采用可插拔整体端子;EM231热电偶模块可用于J、K、E、N、S、T和R型热电偶,用户用模块下方的DIP开关来选择热电偶的类型;TD200键盘共有9个键:5个命令键和4个功能键,用来显示信息,在信息中可以内嵌数据,数据既可以显示,也可以由操作人员进行设置;电加热管是专门将电能转化为热能的电器元件,由于其价格便宜,使用方便,安装方便,无污染,被广泛使用在各种加热场合;水暖供热管道中的热水是靠循环泵循环起来的循环泵的工作原理要将水循环起来所用的泵就叫循环泵;保护程序是必不可少的部分,报警处理,用以防止非法操作所引起的程序混乱。
基于PLC的锅炉供热控制系统的设计

基于PLC的锅炉供热控制系统的设计一、本文概述随着科技的不断发展,可编程逻辑控制器(PLC)在工业自动化领域的应用日益广泛。
作为一种高效、可靠的工业控制设备,PLC以其强大的编程能力和灵活的扩展性,成为现代工业控制系统的重要组成部分。
本文旨在探讨基于PLC的锅炉供热控制系统的设计,通过对锅炉供热系统的分析,结合PLC控制技术,实现对供热系统的智能化、自动化控制,提高供热效率,降低能耗,为工业生产和居民生活提供稳定、可靠的热源。
文章首先介绍了锅炉供热系统的基本构成和工作原理,分析了传统供热系统存在的问题和不足。
然后,详细阐述了PLC控制系统的基本原理和核心功能,包括输入/输出模块、中央处理单元、编程软件等。
在此基础上,文章提出了基于PLC的锅炉供热控制系统的总体设计方案,包括系统硬件选型、软件编程、系统调试等方面。
通过本文的研究,期望能够实现对锅炉供热控制系统的优化设计,提高供热系统的控制精度和稳定性,降低运行成本,促进节能减排,为工业生产和居民生活提供更加安全、高效的供热服务。
也为相关领域的研究人员和技术人员提供有价值的参考和借鉴。
二、锅炉供热系统基础知识锅炉供热系统是一种广泛应用的热能供应系统,其主要任务是将水或其他介质加热到一定的温度,然后通过管道系统输送到各个用户端,满足各种热需求,如工业生产、居民供暖等。
该系统主要由锅炉本体、燃烧器、热交换器、控制系统和辅助设备等几部分构成。
锅炉本体是供热系统的核心设备,负责将水或其他介质加热到预定温度。
其根据燃料类型可分为燃煤锅炉、燃油锅炉、燃气锅炉、电锅炉等。
锅炉的性能参数主要包括蒸发量、蒸汽压力、蒸汽温度等。
燃烧器是锅炉的重要组成部分,负责燃料的燃烧过程。
燃烧器的性能直接影响到锅炉的热效率和污染物排放。
燃烧器需要稳定、高效、低污染,同时要适应不同的燃料类型和负荷变化。
热交换器是锅炉供热系统中的关键设备,负责将锅炉产生的热能传递给水或其他介质。
热交换器的设计应保证高效、稳定、安全,同时要考虑到热能的充分利用和防止结垢、腐蚀等问题。
毕业设计-基于PLC控制的电热锅炉

电热锅炉是把电能转化为热能,把水加热至有压力的热水或蒸汽(饱和蒸汽)的一种电力设备。
电热锅炉无需炉膛、烟道和烟囱,同样无需储存燃料的空间,很大程度上减少了常规燃煤锅炉使用产生的污染。
电热锅炉具有低污染,低噪声,体积小,安装使用便利,自动化程度高,安全可靠,热效率高达98%以上等特点,电热属于一种绿色环保产品。
一些国家在20世纪70年代后期到80年代初期就已经开始研究设计电热锅炉。
中国在80年代中期,开始设计电热锅炉产品,到了90年代中期,许多公司将电热锅炉用来采暖、中央空调和热水供应。
1 绪论1.1电热锅炉的介绍在当今社会,电加热锅炉的使用领域已经越来越广泛了。
它的经济性,安全性和较高的自动化程度越来越受到人们的认同。
可是电加热锅炉的性能优劣充分的反映了电热锅炉的质量好坏。
电加热锅炉已逐渐进入人民的生活,成为洗浴,供热等场所的首选设备。
目前电热锅炉的控制系统多采用以微处理器为核心的PLC控制技术,既提高产品的自动化程度又增加了锅炉的控制精度。
现在使用的大部分电加热锅炉控制系统的设计还不完善,因此需要设计一种全新的、自动化程度较高的电加热锅炉控制系统来代替和完善以前的控制系统。
现在工业生产所使用的控制器大多数是用继电器、接触器为主的控制装置。
使用继电器电路组成的控制系统出现的误操作较多,其可靠性不好。
而该设计所使用的是以PLC来取代原有的控制系统。
控制系统的要求:补水泵和循环泵交替使用,互为备用;缺相报警,水泵停止运行;循环泵主/备用泵能手动选择。
1.2 电热锅炉的分类电热锅炉就是以电为能量来加热的锅炉,即使用清洁的电能转化为热能,从而把常温水加热为高温度热水或具有压力蒸汽的热能电气设备。
电热锅炉分为两大类:LDR(WDR)电热蒸汽锅炉和CLDZ(CWDZ)电热热水锅炉及KS-D电开水锅炉。
其中电开水锅炉又分为KS-D电开水锅炉和XKS-D电蓄热开水锅炉。
电开水锅炉配置微电脑控制器、陶瓷电热管,采用电磁阀作为补水装置配合水位电极、感温探头全自动工作,连续大量供应饮用开水,广泛适用于政府机关、企业、工厂、医院、学校、宾馆、酒店等企事业单位使用。
基于PLC的锅炉温度控制系统
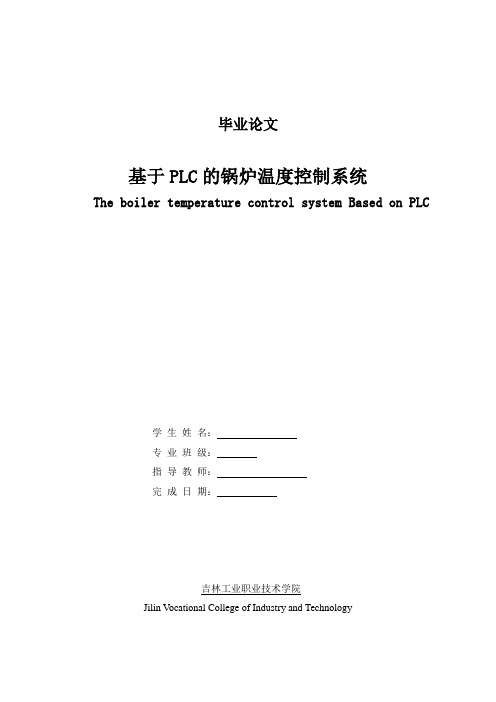
毕业论文基于PLC的锅炉温度控制系统The boiler temperature control system Based on PLC学生姓名:专业班级:指导教师:完成日期:吉林工业职业技术学院Jilin V ocational College of Industry and Technology摘要从上世纪80年代至90年代中期,PLC得到了快速的发展,在这时期,PLC在处理模拟量能力、数字运算能力、人机接口能力和网络能力得到大幅度提高,PLC逐渐进入过程控制领域,在某些应用上取代了在过程控制领域处于统治地位的DCS系统。
PLC具有通用性强、使用方便、适应面广、可靠性高、抗干扰能力强、编程简单等特点。
PLC在工业自动化控制特别是顺序控制中的地位,在可预见的将来,是无法取代的。
本文介绍了以锅炉为被控对象,以锅炉出口水温为主被控参数,以炉膛内水温为副被控参数,以加热炉电阻丝电压为控制参数,以PLC为控制器,构成锅炉温度串级控制系统;采用PID算法,运用PLC梯形图编程语言进行编程,实现锅炉温度的自动控制。
电热锅炉的应用领域相当广泛,在相当多的领域里,电热锅炉的性能优劣决定了产品的质量好坏。
目前电热锅炉的控制系统大都采用以微处理器为核心的计算机控制技术,既提高设备的自动化程度又提高设备的控制精度。
本文分别就电热锅炉的控制系统工作原理,温度变送器的选型、PLC配置、组态软件程序设计等几方面进行阐述。
通过改造电热锅炉的控制系统具有响应快、稳定性好、可靠性高,控制精度好等特点,对工业控制有现实意义。
关键词:电热锅炉的控制系统温度控制串级控制 PLC PIDThe boiler temperature control system Based on PLCAbstractFrom the last century to 90 in the mid 80's, PLC has been rapid development in this period, PLC capability in dealing with analog and digital computing power, man-machine interface capabilities and network capabilities are greatly improved, PLC gradually entering the field of process control, replaced in some applications in the field of process control dominant DCS.PLC has the versatility, ease of use, wide adaptation, high reliability and strong anti-interference, simple to program and so on.PLC control, especially in the industrial automation sequence control the position, in the foreseeable future, is no substitute.This paper introduces the boiler as the charged object to the boiler water temperature of the main accused of the export parameters to furnace temperature as deputy accused of parameters to control the heating resistance wire voltage parameters to PLC, controller, constitutes a series of boiler temperaturelevel control system; using PID algorithm, the use of PLC ladder programming language, programming, boiler temperature control.Electric boilers a wide range of applications, in a considerable number of field, the electric boiler performance advantages and disadvantages of the decision The quality of the product.Electric boiler control systems currently used mostly for computer control microprocessor core technology, both to improve the automation equipment have improved the control precision equipment.This paper on the heating boiler control system works, selection of temperature transmitter, PLC configurations, the configuration software design aspects were described.Through the transformation of electric boiler control system has fast response, good stability, high reliability, control accuracy and good features, practical significance for industrial control.Key words: heating boiler control system temperature control cascade control PLC PI目录摘要 (I)ABSTRACT (II)1.1课题背景及研究目的和意义 (6)1.2国内外研究现状 (6)1.3项目研究内容 (7)第二章 PLC和组态软件基础.............................................................................................................................. - 8 -2.1可编程控制器基础 (8)2.1.1可编程控制器的产生和应用 .................................................................................................................... - 8 -2.1.2可编程控制器的组成和工作原理 ............................................................................................................ - 9 -2.1.3可编程控制器的分类及特点 ................................................................................................................... - 11 -2.2组态软件的基础 (12)2.2.1组态的定义.............................................................................................................................................. - 12 -2.2.2组态王软件的特点 .................................................................................................................................. - 13 -2.2.3组态王软件仿真的基本方法 .................................................................................................................. - 13 -第三章 PLC控制系统的硬件设计........................................................................................................................ - 14 -3.1PLC控制系统设计的基本原则和步骤 (14)3.1.1 PLC控制系统设计的基本原则 .............................................................................................................. - 14 -3.1.2 PLC控制系统设计的一般步骤 ............................................................................................................ - 14 -3.1.3 PLC程序设计的一般步骤 .................................................................................................................... - 15 -3.2PLC的选型和硬件配置 (16)3.2.1 PLC型号的选择...................................................................................................................................... - 16 -3.2.2 S7-200 CPU的选择 .............................................................................................................................. - 16 -3.2.4 热电式传感器 ..................................................................................................................................... - 17 -3.2.5 可控硅加热装置简介 ........................................................................................................................... - 18 -3.3系统整体设计方案和电气连接图 (18)3.4.1 控制系统数学模型的建立 ..................................................................................................................... - 18 -3.4.2 PID控制及参数整定 ............................................................................................................................ - 19 -第四章 PLC控制系统的软件设计 ........................................................................................................................ - 22 -4.1PLC程序设计的方法 (22)4.2编程软件STEP7--M ICRO/WIN概述 (23)4.2.1 STEP7--Micro/WIN 简单介绍 ............................................................................................................. - 23 -4.2.2 计算机与PLC的通信 ........................................................................................................................... - 24 -4.3程序设计 (24)4.3.1 程序设计思路......................................................................................................................................... - 24 -4.3.2 PID指令向导.......................................................................................................................................... - 25 -4.3.3 控制程序及分析 ..................................................................................................................................... - 33 -第五章组态画面的设计 ....................................................................................................................................... - 38 -5.1组态变量的建立及设备连接 (38)5.1.1 新建项目................................................................................................................................................. - 38 -5.2创建组态画面 (44)5.2.1 新建主画面............................................................................................................................................. - 44 -5.2.2 新建PID参数设定窗口 ......................................................................................................................... - 44 -5.2.3 新建数据报表......................................................................................................................................... - 45 -5.2.4 新建实时曲线......................................................................................................................................... - 46 -5.2.5 新建历史曲线......................................................................................................................................... - 47 -5.2.6 新建报警窗口......................................................................................................................................... - 47 -第六章系统测试 ................................................................................................................................................... - 50 -6.1启动组态王 (50)6.2实时曲线观察 (51)6.3分析历史趋势曲线 (51)6.4查看数据报表 (54)6.5系统稳定性测试 (55)结束语 ........................................................................................................................................................................... - 6 -参考文献 ..................................................................................................................................................................... - 58 -致谢 ......................................................................................................................................................................... - 59 -第一章绪论1.1课题背景及研究目的和意义电热锅炉的应用领域相当广泛,电热锅炉的性能优劣决定了产品的质量好坏。
基于PLC的热水锅炉自动化控制系统(全文)

基于PLC的热水锅炉自动化操纵系统引言】目前,我国很多在运行的锅炉都存在自动化水平不高、效率低和环境污染严峻的问题,因此实现锅炉的自动操纵具有重要的意义。
PLC自动化系统采纳模块化设计,程序也采纳模块化设计,且每个模块都可以单独的优化,以便于整个系统的升级、操纵治理和日后的维护,保证了系统的可开发性,和有良好的可扩充性,发挥系统的最大性价比。
正文】热水锅炉的工作原理是通过煤的燃烧,将锅炉中的水加热,并将加热到一定程度的热水通过增加迫使其流出,为外界供暖。
操纵系统需要根据工艺需求实时的调整燃烧系统。
按工艺要求,自控程序分锅炉负荷操纵(燃烧自动操纵)、循环泵自动操纵和补水定压操纵等几部分。
其中水系统(循环泵、补水泵)操纵相对比较简单,负荷操纵较为复杂,以下是XX对热水锅炉及机组总结出的负荷操纵的操纵方案。
1.锅炉负荷操纵锅炉负荷操纵的目的是:根据供暖需求的热量,通过一系列中间操纵环节操纵锅炉的供回水温度和流量,使住户处的室内温度达到并维持在合适的温度值,且锅炉运行在节能状态。
当供暖面积一定时,出水流量基本就不变了,所以因为室外温度的变化,所需的热量主要就通过改变供回水温差来实现。
理论上,锅炉负荷操纵应该操纵总XX供回水温差,因为温差可以直接反映出供热质量,温差太大或太小都说明供热质量不很理想。
但实际上,负荷操纵是根据总XX供水温度操纵的,因为总XX回水温度测量存在滞后性,一般就直接采纳供水温度操纵,这也可以更直接反映出锅炉的燃烧情况,使燃烧过程维持在一个动态平衡上,以达到节能的效果。
所以,负荷操纵就是总XX供水温度操纵。
如下图1所示,前提是供暖面积一定,出水流量是一定的,室外温度的变化直接影响用户需要的热量,直接受控对象是出水温度,主要的操纵方式有三种:手动操纵、恒温操纵和温度曲线操纵。
图1 负荷操纵框图1、手动操纵手动操纵是由司炉工根据经验手动给定各执行机构的操纵参数,根据供、回水温度的实际值来衡量当前供暖情况。
基于PLC控制的电锅炉控制系统

基于PLC控制的电锅炉控制系统电锅炉控制系统是现代工业制造中常见的一种设备,它通过PLC(可编程逻辑控制器)来实现对电锅炉的精确控制。
PLC控制技术具有灵活、方便、可靠等优点,能够实现复杂的逻辑控制和自动化控制功能。
本文将从PLC控制系统的原理、功能及特点入手,结合电锅炉的工作原理,详细介绍基于PLC控制的电锅炉控制系统的设计与实现。
1. PLC控制系统原理PLC控制系统是一种专门设计用于工业自动化控制的设备,其核心是一个可编程的CPU,通过不同的输入/输出模块和通信模块,与外部传感器、执行器等设备连接,实现对生产过程的控制。
PLC控制系统通过预先编写好的程序,根据不同的输入信号执行相应的逻辑控制,以达到自动化控制的目的。
2. 电锅炉工作原理电锅炉是一种利用电能进行加热的设备,通常由加热元件、控制系统、水泵等部件组成。
在工作过程中,电能被加热元件转换为热能,将水加热至设定的温度,为生产或生活提供热水或蒸汽。
电锅炉的控制系统通常包括温度传感器、压力传感器、水位传感器等,用于监测和控制锅炉的工作状态。
3. 基于PLC控制的电锅炉控制系统设计基于PLC控制的电锅炉控制系统主要由PLC控制器、传感器、执行器、人机界面等部件组成。
在设计过程中,首先需要根据电锅炉的工作原理和需求确定系统的功能要求和控制策略,然后编写PLC程序实现相应的逻辑控制。
通过合理的硬件布局和接线连接,将各部件连接到PLC控制器上,实现信号的采集和输出。
4. 控制系统功能与特点基于PLC控制的电锅炉控制系统具有如下功能与特点:1)灵活性:PLC控制系统可根据需要进行程序修改,实现不同的控制策略;2)可靠性:PLC控制器具有较高的稳定性和可靠性,可以长时间稳定运行;3)精确性:通过PLC控制系统可以实现对电锅炉的精确控制,提高生产效率和产品质量;4)扩展性:PLC控制系统可根据需要扩展输入/输出模块和功能模块,实现系统的功能扩展。
5. 控制系统优化与应用为了进一步优化电锅炉控制系统的性能,可以采用PID控制算法、模糊控制算法等先进的控制技术,提高系统的响应速度和稳定性。
基于信捷PLC电热锅炉温控系统的设计
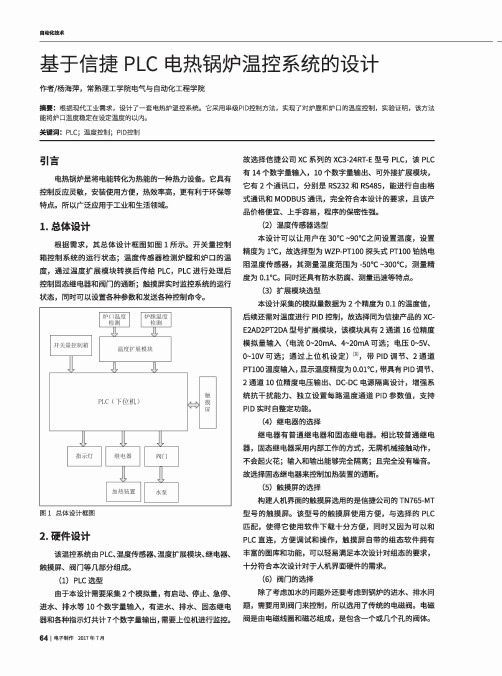
炉口温度 检测
炉膛温度
检测j
后续还需对温度进行PID控 制 ,故选择同为信捷产品的XCE2AD2 PT2 DA型号扩展模块,该 模 块 具 有 2 通 道 1 6 位精度
温度扩展模块
模 拟 量 输 入 (电 流 0~20mA、4 ~ 2 0 mA可 选 ;电 压 0~5V、 0~10V 可 选 ;通 过 上 位 机 设 定 )[1],带 PID调 节 、2 通道
引言
电 热 锅 炉 是 将电能转化为热能的一种热力设备。 它具有 控 制 反 应 灵 敏 ,安 装 使 用 方 便 ,热 效 率 高 ,更有利 于 环 保 等 特点。所以广泛应用于工业和生活领域。
故 选 择 信 捷 公 司 X C 系 列 的 XC3-源自4RT-E 型 号 PLC,该 PLC
有 1 4 个数字量输入,1 0 个数字量输出、可外接扩展模块,
度 ,通 过 温 度 扩 展 模 块 转 换 后 传 给 PLC,PLC进行处理后
控 制 固 态 继 电 器 和 阀 门 的 通 断 ;触 摸 屏 实 吋 监 控 系 统 的 运 行 状 态 ,同时可以设置各种参数和发送各种控制命令。
( 2 ) 温度传感器选型
本 设 计 可 以 让 用 户 在 3 0 °C ~90°C之 间 设 置 温 度 ,设置 精 度 为 1°C ,故 选 择 型 为 WZP-PT1 0 0 探 头 式 PT1 0 0 铂热电 阻温 度 传 感 器 ,其 测 量 温 度 范 围 为 -50°C ~300°C ,测量精 度 为 0.1°C。同时还具有防水防腐、测量迅速等特点。
(2) PID参数整定
由于对炉膛的温度控制要求不高,对炉口的温度控制要
PLC电热锅炉供热控制系统设计

PLC电热锅炉供热控制系统设计一、引言随着社会的不断发展,人们对于供热系统的要求也越来越高。
为了提高供热系统的自动化程度和安全性,PLC(可编程逻辑控制器)技术得到了广泛应用。
本文将针对PLC电热锅炉供热控制系统的设计进行详细讨论,以确保系统运行稳定、安全。
二、PLC电热锅炉供热控制系统设计方案1. 系统架构设计PLC电热锅炉供热控制系统主要由PLC控制器、传感器、执行器等组成。
其中,PLC控制器作为系统的大脑,负责对各个执行器的控制和监测工作。
传感器用于采集环境温度、水箱水位等信息,反馈给PLC控制器,从而实现对系统的自动控制。
2. 系统功能设计(1)温度控制功能:通过传感器实时监测环境温度,当环境温度低于设定值时,PLC控制器将启动电热锅炉,加热水箱中的水,直到温度达到设定值为止。
(2)水位控制功能:传感器监测水箱水位,当水位低于设定值时,PLC将启动给水泵进行给水,保证水箱水位在合适范围内。
(3)故障诊断功能:系统内置故障诊断模块,通过监测系统各部件的运行状态,及时发现故障并进行报警提示,保证系统安全稳定运行。
3. 系统性能设计(1)稳定性:系统采用双PLC热备份设计,确保系统在一台PLC故障时可以自动切换到备用PLC,保证系统的连续运行。
(2)可靠性:系统采用高品质的传感器和执行器,具有较高的抗干扰能力和稳定性,从而确保系统的可靠性。
4. 系统通信设计系统采用以太网通信方式,PLC控制器通过以太网与上位机连接,实现对系统的远程监控和控制。
上位机可以实时监测系统运行状态、温度水位等信息,方便操作人员进行远程管理。
三、系统实施与调试1. 硬件安装:安装PLC控制器、传感器、执行器等硬件设备,确保设备安装位置合理,连接正确。
2. 软件编程:编写PLC控制程序,包括温度控制、水位控制、故障诊断等功能模块。
3. 系统调试:进行系统联调和调试,检验系统各部件是否正常工作,确保系统实现预期功能。
四、系统运行维护1. 定期检查:定期检查系统各部件的运行状态,及时更换老化部件,保持系统的正常运行。
基于PLC的锅炉加热温度控制系统设计

基于PLC的锅炉加热温度控制系统设计锅炉加热温度控制系统设计是一个非常重要的工程项目,特别是在工业生产中。
PLC(可编程逻辑控制器)是一种高级自动化控制设备,可以实现对锅炉加热温度的精确控制。
本文将介绍一个基于PLC的锅炉加热温度控制系统的设计。
【系统概述】该系统的基本目标是稳定地控制锅炉的加热温度,保证锅炉在正常工作范围内运行,并尽可能地提高热效率。
具体来说,系统需要实现以下功能:1.实时监测锅炉温度。
2.控制锅炉加热功率。
3.响应温度变化,并自动调整加热功率。
4.报警和故障保护功能。
【系统设计】1.硬件设计:硬件部分包括传感器、执行机构和PLC。
传感器用于实时监测锅炉温度,常用的温度传感器有热电偶和敏感电阻。
执行机构用于控制加热功率,可采用电磁阀或电加热器。
PLC负责处理数据和控制信号,可以选择常用的西门子、施耐德等PLC。
2.软件设计:软件部分主要包括PLC编程和人机界面设计。
PLC编程可以使用基于LD(梯形图)或SFC(时序功能图)的编程语言,根据具体控制要求,设计合适的控制算法和逻辑。
人机界面设计可以使用HMI(人机界面)或SCADA(监控与数据采集系统),实时显示锅炉温度、加热功率和系统状态,并提供控制和设定温度的功能。
3.控制策略设计:控制策略需要根据具体情况进行设计,一般分为开环控制和闭环控制两种。
开环控制是根据经验或数学模型预先设定温度和加热功率曲线,直接输出控制信号。
闭环控制则根据实时监测的温度反馈信息,通过控制算法动态调整加热功率,使实际温度尽可能接近设定温度。
4.报警和故障保护设计:系统需要具备报警和故障保护功能,当温度超出设定范围或系统出现故障时,及时发出警报并采取相应的措施,以保护锅炉和工艺安全。
【实施与测试】在实施前,需要进行系统调试,确保PLC编程和硬件连接正常。
在实际运行中,需要对系统进行定期检测和维护,以保证系统的稳定性和可靠性。
总结起来,基于PLC的锅炉加热温度控制系统的设计是一个复杂的工程,需要综合考虑硬件和软件的因素。
基于PLC的锅炉控制系统的设计
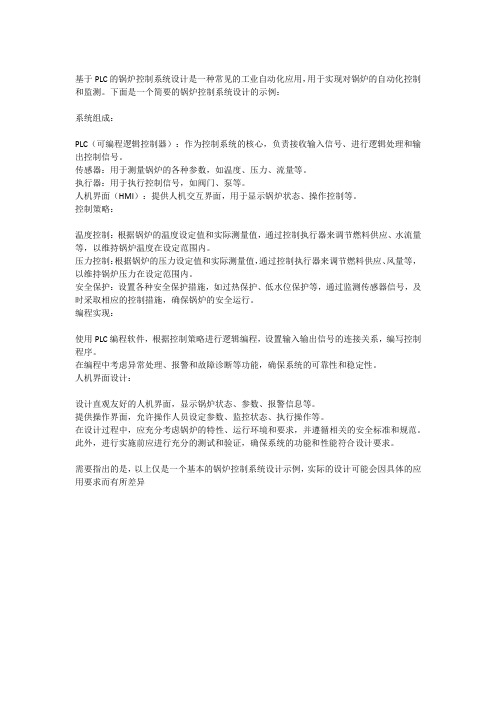
基于PLC的锅炉控制系统设计是一种常见的工业自动化应用,用于实现对锅炉的自动化控制和监测。
下面是一个简要的锅炉控制系统设计的示例:
系统组成:
PLC(可编程逻辑控制器):作为控制系统的核心,负责接收输入信号、进行逻辑处理和输出控制信号。
传感器:用于测量锅炉的各种参数,如温度、压力、流量等。
执行器:用于执行控制信号,如阀门、泵等。
人机界面(HMI):提供人机交互界面,用于显示锅炉状态、操作控制等。
控制策略:
温度控制:根据锅炉的温度设定值和实际测量值,通过控制执行器来调节燃料供应、水流量等,以维持锅炉温度在设定范围内。
压力控制:根据锅炉的压力设定值和实际测量值,通过控制执行器来调节燃料供应、风量等,以维持锅炉压力在设定范围内。
安全保护:设置各种安全保护措施,如过热保护、低水位保护等,通过监测传感器信号,及时采取相应的控制措施,确保锅炉的安全运行。
编程实现:
使用PLC编程软件,根据控制策略进行逻辑编程,设置输入输出信号的连接关系,编写控制程序。
在编程中考虑异常处理、报警和故障诊断等功能,确保系统的可靠性和稳定性。
人机界面设计:
设计直观友好的人机界面,显示锅炉状态、参数、报警信息等。
提供操作界面,允许操作人员设定参数、监控状态、执行操作等。
在设计过程中,应充分考虑锅炉的特性、运行环境和要求,并遵循相关的安全标准和规范。
此外,进行实施前应进行充分的测试和验证,确保系统的功能和性能符合设计要求。
需要指出的是,以上仅是一个基本的锅炉控制系统设计示例,实际的设计可能会因具体的应用要求而有所差异。
基于PLC的锅炉控制系统的设计

基于PLC的锅炉控制系统的设计本文介绍基于PLC的锅炉控制系统的设计的背景和目的。
锅炉控制系统是基于PLC(可编程逻辑控制器)的设计,采用了分布式控制策略。
整体架构包括以下几个组成部分:1.控制器控制器是锅炉控制系统的核心部分,由PLC实现。
PLC具备高速计算能力和强大的输入输出功能,可以对各个设备进行监控和控制。
它接收来自传感器的输入信号,并根据预设的逻辑和算法进行实时处理,向执行器发送输出信号以控制设备运行。
2.传感器传感器负责将锅炉系统的各个参数转化为电信号,并传输给PLC进行处理。
常见的传感器包括温度传感器、压力传感器、流量传感器等。
3.执行器执行器根据PLC的控制信号来执行相应的操作,如调节燃料供给、控制排放阀等。
它们与PLC之间通过信号线或总线进行连接。
4.人机界面人机界面提供给操作员与锅炉控制系统进行交互的界面。
它可以是触摸屏、计算机软件等形式,用于监视系统运行状态、设定参数以及显示报警信息等。
5.通信模块通信模块用于实现锅炉控制系统与外部设备的数据传输和通信。
它可以连接到局域网或远程服务器,实现与其他系统或监控中心的数据交互。
6.电源供应为了保证锅炉控制系统的稳定运行,需要提供可靠的电源供应。
这可以通过备用电源或UPS(不间断电源)来实现。
综上所述,基于PLC的锅炉控制系统采用分布式控制策略,通过控制器、传感器、执行器、人机界面、通信模块和电源供应等组成部分协同工作,实现对锅炉设备的监控和控制。
本文介绍基于PLC的锅炉控制系统所采用的控制策略和算法。
控制策略是指通过采取不同的控制方法和算法,在锅炉运行中实现温度、压力、流量等参数的稳定控制。
基于PLC的锅炉控制系统采用了以下主要的控制策略:PID控制:PID(比例、积分、微分)控制是一种常用的控制方法。
它通过根据控制对象的偏差来调节控制器的输出,使得偏差逐渐趋向于零,从而实现控制目标。
在锅炉控制系统中,PID控制常用于调节温度、压力和流量等参数。
基于PLC的电热锅炉温度控制系统设计

b c me v i b ef ro e a o d f h p r t g p r mee sa c r i g t o t l f c .T e eo e i e o sa a l l p r trt mo i t e o e ai a a t r c o dn c n r e t h rf r t a o o y n o o e
热锅炉控制系统 的工作原理、L P C配置 、 软件程序设
计 等几 方面进行 阐述 , 计 的电 热锅 炉 控制 系 统 具 设 有 响应快 、 稳定性 好 、 靠性高 、 可 控制 精度好 等特点 ,
对工 业控 制有现 实意义 。
编程器 的作用 是供 用户进行 程序 的输入 、 编辑 、 调试 和监 视 。编 程 器 一 般 分 为 简 易 型 和 智 能 型 两
类, 简易型 只能联机 编程 , 且往 往需要将 梯形 图转化
1 可编程控制器 ( L ) P C
目前 ,L P C的主要 生产 厂家 有德 国西 门子 公 司 、
为机器语 言 助 记 符 后 才 能 送 人 ; 能 型 编程 器 ( 智 又 称 图形 编程 器 )不 但 可 以连 机编 程 , , 而且 还 可 以脱 机编 程 , 操作 方便且 功 能强大 。
摘
要 :利 用可编 程控制 器 ( L )技 术对 锅 炉工作过 程进行 自动 控制 ,其优 点在 于 :首先提 高 PC
了燃 料的燃 烧效 率 ;其 次提 高 了锅 炉控 制 过程 的 自动化 处理 程 度 ; 另外 , 良好 的人 机监 控 界 面
使操作人员在监控计算机上能根据控制效果及 时地修 改运行参数 ,从 而提 高了生产过程 的实时
构成 。
P C电源 为 P C各 模 块 的集 成 电路 提 供 工 作 L L
基于PLC的锅炉温度控制系统

基于PLC的锅炉温度控制系统摘要从上世纪80年代至90年代中期,PLC得到了快速的发展,在这时期,PLC在处理模拟量能力、数字运算能力、人机接口能力和网络能力得到大幅度提高,PLC 逐渐进入过程控制领域,在某些应用上取代了在过程控制领域处于统治地位的DCS系统。
PLC具有通用性强、使用方便、适应面广、可靠性高、抗干扰能力强、编程简单等特点。
PLC在工业自动化控制特别是顺序控制中的地位,在可预见的将来,是无法取代的。
本文介绍了以锅炉为被控对象,以锅炉出口水温为主被控参数,以炉膛内水温为副被控参数,以加热炉电阻丝电压为控制参数,以PLC为控制器,构成锅炉温度帘级控制系统;采用PID算法,运用PLC梯形图编程语言进行编程,实现锅炉温度的自动控制。
电热锅炉的应用领域相当广泛,在相当多的领域里,电热锅炉的性能优劣决定了产品的质量好坏。
口前电热锅炉的控制系统大都采用以微处理器为核心的讣算机控制技术,既提高设备的自动化程度乂提高设备的控制精度。
本文分别就电热锅炉的控制系统工作原理,温度变送器的选型、PLC配置、组态软件程序设讣等儿方面进行阐述。
通过改造电热锅炉的控制系统具有响应快、稳定性好、可靠性高,控制精度好等特点,对工业控制有现实意义。
关键词:电热锅炉的控制系统温度控制审级控制PLC PID摘要 (1)1绪论 (1)课题背景及研究目的和意义 (1)1.2国内外研究现状 (3)1.3项目研究内容 (4)2PLC和组态软件基础 (5)2.1可编程控制器基础 (5)2.1.1可编程控制器的产生和应用 (5)2.1.2可编程控制器的组成和工作原理....... 错误!未定义书签。
2.1.3可编程控制器的分类及特点 (7)2.2组态软件的基础 (8)2.2.1组态的定义 (8)2.2. 2组态王软件的特点 (8)2.2. 3组态王软件仿真的基本方法 (8)3PLC控制系统的硬件设计 (9)3.1 PLC控制系统设计的基本原则和步骤 (9)3.1.1PLC控制系统设计的基本原则 (9)3.1.2PLC控制系统设计的一般步骤 (9)3.1.3PLC程序设计的一般步骤 (10)3.2PLC的选型和硬件配置 (11)3.2.1PLC型号的选择 (11)3.2.2S7-200CPU 的选择 (12)3.2.3EM235模拟量输入/输出模块 (12)3.2.4热电式传感器 (12)3.2.5可控硅加热装置简介 (12)3.3系统整体设计方案和电气连接图 (13)3.4 PLC控制器的设计 (14)3.4. 1控制系统数学模型的建立 (14)3.4.2PID控制及参数整定 (14)4PLC控制系统的软件设计 (16)4.1PLC程序设计的方法 (16)4.2编程软件 STEP7—Micro/WIN 概述 (17)4.2. 1 STEP7—Micro/WIN 简单介绍 (17)4.2.2计算机与PLC的通信 (18)4.3 程序设计 (18)4.3. 1程序设计思路 (18)4.3. 2 PID指令向导 (19)4.3. 3控制程序及分析 (25)5组态画面的设计 (29)5.1组态变量的建立及设备连接 (29)5.1. 1新建项目 (29)5.2创建组态画面 (33)5.2. 1新建主画面 (33)5.2.2新建PID参数设定窗口 (34)5.2. 3新建数据报表 (34)5.2. 4新建实时曲线 (35)5.2.5新建历史曲线 (35)5.2.6新建报警窗口 (36)6系统测试 (37)6.1启动组态王 (37)6.2实时曲线观察 (38)6.3分析历史趋势曲线 (38)6.4查看数据报表 (40)6.5系统稳定性测试 (42)结束语 (43)参考文献 (44)致谢 (45)华北电力大学成人教冇毕业设计(论文)1绪论1.1课题背景及研究目的和意义电热锅炉的应用领域相当广泛,电热锅炉的性能优劣决定了产品的质量好坏。
基于PLC控制的电锅炉控制系统
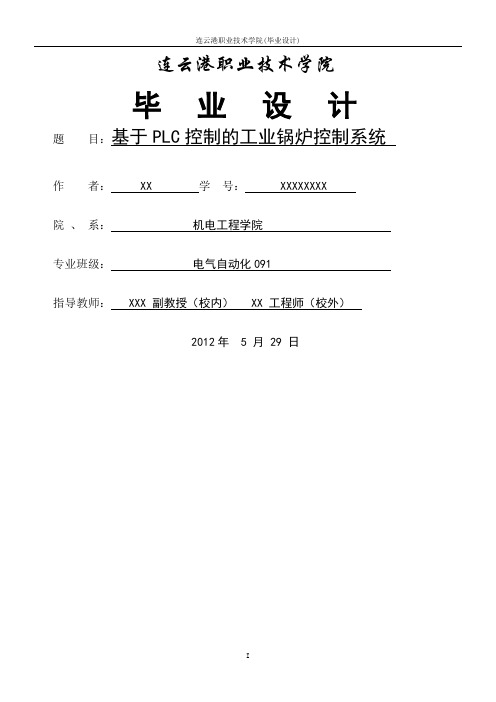
连云港职业技术学院毕业设计题目:基于PLC控制的工业锅炉控制系统作者:XX 学号:XXXXXXXX 院、系:机电工程学院专业班级:电气自动化091指导教师: XXX 副教授(校内) XX 工程师(校外)2012年 5 月 29 日基于PLC控制的工业锅炉控制系统摘要锅炉是特种压力容器设备,它是化工、发电、供热、炼油和制糖等工业及民用部门必不可少的重要的动力设备。
随着计算机控制技术的飞速发展和广泛应用,锅炉的控制系统和方式越来越引起人们的重视,而且对控制系统的要求越来越高,工业锅炉实现自动控制可以将锅炉的水位、温度、压力等参数控制在规定的范围内,并能自动适应负荷的变化,从而使锅炉安全可靠经济的运行。
本论文通过对工业锅炉电气系统主回路进行分析,计算出电动机、断路器、交流接触器、继电器、变送器、电缆线等主要电器的参数后,再选择了相应电器的型号及具体数据。
然后相应设计出工业锅炉的压力控制系统、水位控制系统。
在综合考虑系统的精度、效率以及经济性等的因素之后,最终确定以PLC为控制核心。
本毕业设计过程包括工业锅炉电气控制系统程序,用计算机绘制电气主电路图和PLC外围接线图等。
关键词:工业锅炉;水位控制;压力控制; PLCBased on the PLC control in industrial boiler control systemAbstractBoiler is a special pressure vessel equipment, it is chemical, power generation, heating, oil and sugar and other industrial and civil departments indispensable important power equipment. Along with the computer control technology of the rapid development and extensive application of the boiler control system, and the way people pay more and more attention, but also to the control system of the increasingly high demand, industrial electric heating boiler automatic control of boiler water level, can be temperature, pressure and other parameters control in the specified range, and can automatically adapt load change, so that the boiler safe and economic operation.The present paper through to the industrial boiler electrical system main circuit analysis, calculate the motor, AC contactor, breaker, relay, transmitter, cable and other electrical parameters, and then select the corresponding electric models and specific data. Then the corresponding design of industrial boiler pressure control system, water level control system. Considering the system precision, efficiency and economy and other factors, finally determined with PLC as the control core.This graduation design process including electric boiler electric control system for computer aided drawing program, the main electrical circuit diagram and PLC external wiring diagram.Key Words: industrial boiler; water level control; pressure control; PLC目录摘要 (I)ABSTRACT (II)第一章文献综述 (1)1.1课题研究目的 (1)1.2工业锅炉的概述 (2)1.2.1锅炉的基本构造 (2)1.2.2锅炉的基本组成 (2)1.2.3 锅炉的工作原理 (3)1.3锅炉自动控制的发展 (3)1.4本文的研究方向 (4)第二章技术方案的选择 (4)2.1方案论证 (4)2.1.1方案1 (4)2.1.2方案2 (4)2.1.3方案3 (5)2.2方案选择 (5)2.3程序的设计思路 (5)第三章 PLC基础知识 (5)3.1PLC的概述 (5)3.2PLC的组成 (6)3.3PLC的工作过程 (6)3.4FX2N-4AD模拟转换器 (6)第四章设计工业锅炉电气控制系统 (9)4.1锅炉的电气控制系统的介绍 (9)4.1.1锅炉自动控制的任务 (9)4.1.2程序控制 (9)4.1.3锅炉保护装置 (10)4.2锅炉主要电气设备的计算及选择 (10)4.2.1 电动机的选择 (10)4.2.2 热继电器的选择 (10)4.2.3接触器的选择 (11)4.2.4 断路器的选择 (11)4.2.5 电缆线的选择 (12)4.3水位控制系统及压力控制系统的设计 (12)4.3.1工业锅炉水位控制系统 (12)4.3.2工业锅炉压力控制系统 (14)4.4电源欠压、过压及电机的过流保护的设计 (16)4.4.1电压变送器 (16)4.4.2电流变送器及电流互感器 (17)4.4.3欠压、过压、过流保护的实现 (18)第五章结论 (20)谢辞 (21)参考文献 (21)附录1 (22)附录2 (22)附录3 (22)第一章文献综述随着计算机和控制理论的发展,锅炉控制技术[6]在国外发展越来越快。
- 1、下载文档前请自行甄别文档内容的完整性,平台不提供额外的编辑、内容补充、找答案等附加服务。
- 2、"仅部分预览"的文档,不可在线预览部分如存在完整性等问题,可反馈申请退款(可完整预览的文档不适用该条件!)。
- 3、如文档侵犯您的权益,请联系客服反馈,我们会尽快为您处理(人工客服工作时间:9:00-18:30)。
电热锅炉是把电能转化为热能,把水加热至有压力的热水或蒸汽(饱和蒸汽)的一种电力设备。
电热锅炉无需炉膛、烟道和烟囱,同样无需储存燃料的空间,很大程度上减少了常规燃煤锅炉使用产生的污染。
电热锅炉具有低污染,低噪声,体积小,安装使用便利,自动化程度高,安全可靠,热效率高达98%以上等特点,电热属于一种绿色环保产品。
一些国家在20世纪70年代后期到80年代初期就已经开始研究设计电热锅炉。
中国在80年代中期,开始设计电热锅炉产品,到了90年代中期,许多公司将电热锅炉用来采暖、中央空调和热水供应。
1 绪论1.1电热锅炉的介绍在当今社会,电加热锅炉的使用领域已经越来越广泛了。
它的经济性,安全性和较高的自动化程度越来越受到人们的认同。
可是电加热锅炉的性能优劣充分的反映了电热锅炉的质量好坏。
电加热锅炉已逐渐进入人民的生活,成为洗浴,供热等场所的首选设备。
目前电热锅炉的控制系统多采用以微处理器为核心的PLC控制技术,既提高产品的自动化程度又增加了锅炉的控制精度。
现在使用的大部分电加热锅炉控制系统的设计还不完善,因此需要设计一种全新的、自动化程度较高的电加热锅炉控制系统来代替和完善以前的控制系统。
现在工业生产所使用的控制器大多数是用继电器、接触器为主的控制装置。
使用继电器电路组成的控制系统出现的误操作较多,其可靠性不好。
而该设计所使用的是以PLC来取代原有的控制系统。
控制系统的要求:补水泵和循环泵交替使用,互为备用;缺相报警,水泵停止运行;循环泵主/备用泵能手动选择。
1.2 电热锅炉的分类电热锅炉就是以电为能量来加热的锅炉,即使用清洁的电能转化为热能,从而把常温水加热为高温度热水或具有压力蒸汽的热能电气设备。
电热锅炉分为两大类:LDR(WDR)电热蒸汽锅炉和CLDZ(CWDZ)电热热水锅炉及KS-D电开水锅炉。
其中电开水锅炉又分为KS-D电开水锅炉和XKS-D电蓄热开水锅炉。
电开水锅炉配置微电脑控制器、陶瓷电热管,采用电磁阀作为补水装置配合水位电极、感温探头全自动工作,连续大量供应饮用开水,广泛适用于政府机关、企业、工厂、医院、学校、宾馆、酒店等企事业单位使用。
电蓄热开水锅炉配置微电脑控制器、陶瓷电热管,采用电磁阀作为补水装置配合水位电极、感温探头利用夜间(低谷电)时间全自动工作,可以在白天(用电高峰期)大量供应饮用开水,广泛适用于政府机关、企业、工厂、医院、学校、宾馆、酒店等企事业单位使用。
电热蒸汽锅炉将水加热产生蒸汽的电锅炉,又名电热蒸汽发生器。
按结构分为立式和卧式两种锅炉。
按产生的蒸汽压力分为低压、中压、高压三种规格锅炉。
0.4MPa 及以下工作压力的电热锅炉称为低压电锅炉,主要用于生活供热。
0.7~1 MPa 的电热燕汽锅炉称为中压电锅炉,可供生活、生产用汽。
1.6 MPa以上的电热蒸汽锅炉称为高压电锅炉,现多用于试验室。
由于承压指标不同,在使用选型方面要注惫区分。
中国生产的定型电热蒸汽锅炉的最大出力为Zt/h,最高工作压力为1.6 MPa. 电热热水锅炉将水加热提供热水的电锅炉。
电热热水锅炉在结构上也分立式和卧式两种。
随着锅炉功率的增加,电热热水锅炉有双头和单头之分。
加热电功率在360 kw及以下的卧式电热热水锅炉,大多做成单头,加热电功率大于360 kw的电热热水锅炉,一般做成双头电锅炉。
热水温度小于95℃的电热热水锅炉,常用于供应开水或洗浴的场所。
1.3电热锅炉的主要部件电热锅炉的主要部件有:加热管、控制器、水泵等。
2 可编程控制器(PLC)简介2.1 PLC的基本概念可编程控制器实质是一种专用于工业控制的计算机,其硬件结构基本上与微型计算机相同,如图2.1所示:图2.1 可编程控制器控制系统示意图(1)中央处理单元(CPU)中央处理单元(CPU)是可编程控制器的控制中枢。
它按照可编程控制器系统程序具备的功能收取并储存从编程器输入的程序和数据;检验电源、存储器、I/O 以及警戒定时器的状态,还可以诊断用户程序中出现的的语法错误。
当可编程控制器工作时,最开始它以扫描的方式接收使用场所各输入设备的状态和数据,并各自存入I/O映象区,接着从用户程序储存器里逐条读取用户的程序,对命令进行解释后再按照指令规定的算数运算或执行逻辑结果输入数据寄存器内或I/O 映象区。
直到所有的用户程序执行结束之后,循环运行,直到运行停止。
(2)存储器可编程控制器常用的存储器类型RAM这是一种读/写存储器(随机存储器),速度快,用锂电池供电。
EPROM(Erasable Programmable Read Only Memory)可擦除只读储存器。
具有断电保持功能EEPROM(Electrical Erasable Programmable Read Only Memory)这是一种电可擦除的只读存储器。
(3)输入/输出模块输入/输出模块是可编程控制器与工业生产设备及过程的连接接口。
传感输出的开关量或模拟量、限位开关、按钮开关以及行程开关等输入信号,送人可编程控制器都需经过输入模块。
PLC中央处理器只能处理标准电平的信息,但是输入到模块的信号种类繁多。
因此将这些信号转化为PLC能够处理和接受的数字信号也是输入模块的一个重要功能。
输出模块往往是用来接收CPU处理过的数字信号,把信号转换成现场执行部件所能接受的控制信号,以驱动如电磁阀、电机等执行机构。
PLC有多种输入/输出模块,包括数字量输入/输出模块和模拟量输出/输入模块。
这些模块又包括电流和电压、交流和直流的不同分类,不同分类参数等级也不同,主要有模拟量输出/输入模块和数字量输出/输入模块,部件上往往都设置有用来输入接线的端子排,这些模块上都带有电平转换、信号锁存、滤波电路来滤除信号的噪声和便于可编程控制器处理内部信号。
数字量输入模块比模拟量输入模块多了光电祸合电路,可以让可编程控制器隔离外部电路,以提高可编程控制器的抗干扰能力。
数字量输出有可控硅输出、继电器输出和晶体管输出3种方式。
实现数字量与模拟量之间的转换即D/A或A/D转换由模拟量输入/输出模块来执行。
(4)扩展模块当一个可编程控制器中心单元的I/0点数不够时,就要对系统进行扩展。
随着PLC在工控中的广泛应用和快速发展,各PLC制造厂家已开发出一系列的智能接口模块,使PLC的功能更加强大和完善。
(5)电源PLC中的电源一般有3类: +5V、±15V:锂电池及其充电电源。
考虑到系统光电隔离器的使用以及可靠性,不同类型的电源其地线也不同。
目前PLC的发展非常迅速,型号众多,各种特殊功能模板不断涌现。
2.3 PLC控制系统设计的基本原则和步骤2.3.1 PLC控制系统设计的基本原则1.充分发挥PLC功能,最大限度地满足被控对象的控制要求。
2.在满足控制要求的前提下,力求使控制系统简单、经济、使用及维修方便。
3.保证控制系统安全可靠。
4.应考虑生产的发展和工艺的改进,在选择PLC的型号、I/O点数和存储器容量等内容时,应留有适当的余量,以利于系统的调整和扩充。
2.3.2 PLC控制系统的控制原理最初研究制造的可编程控制器主要用来替代传统的由接触器继电器构成的控制装置,但这两者的运行方式是截然不同的。
继电器控制装置采用硬逻辑并行运行的方式,即假设该继电器的线圈通断电,那该继电器每一个触点(包括其常闭触点或常开触点)在控制线路上都会同时动作。
可编程控制器的中央处理器扫描用户程序则采用顺序逻辑的运行方式。
但为了消除2者之间不同的运行方式而造成的差异,并且继电器控制装置触点的动作时间通常在100ms以上,而可编程控制器扫描用户程序的时间一般均小于100ms,因此,可编程控制器采以与一般计算机不同的方式运行——扫描技术。
在对I/O口响应速度要求不高的场合,可编程控制器与继电器控制装置的处理结果就没有什么区别了。
当可编程控制器开始工作后,其工作过程一般分为三个阶段,即输入采样、用户程序执行和输出刷新三个阶段。
完成上述三个阶段称作一个扫描周期。
在整个运行期间,可编程控制器的中央处理器以一定的扫描速度重复执行上述三个阶段。
如图2.2所示:图2.2 可编程控制器扫描周期图一般来说,可编程控制器的扫描周期包括自诊断、通讯等,如下图所示,即一个扫描周期等于自诊断、通讯、输入采样、用户程序执行、输出刷新等所有时间的总和。
如图2.3所示上电RUN自诊断通讯输入采样用户程序执行输出刷新故障图2.3 可编程控制器扫描周期示意图2.3.3 PLC程序设计的一般步骤1.绘制系统的功能图。
2.设计梯形图程序。
3.根据梯形图编写指令表程序。
4.对程序进行模拟调试及修改,直到满足控制要求为止。
调试过程中,可采用分段调试的方法,并利用编程器的监控功能。
PLC控制系统的设计步骤可参考图 2.4 :图2.4 PLC控制系统的设计步骤3控制系统方案设计3.1系统技术要求对系统技术要求如下:(1)对温度控制范围:入水温度65°C;出水温度85°C。
(2)对锅炉控制的基本要求: ①加热管自动加减投入数量;②自动检测循环水量并补充循环水;③可根据室外气温的变化自动调节出(回)水温度;④自动检测调节炉体内水温和气压;⑤自动报警报警,电加热管停止加热;⑥循环泵主/备用泵可选择;⑦补水泵交替运行,互为备用;⑧所有水泵均具有过载、短路、缺相保护功能;⑨缺相报警,水泵停止运行;3.2电热锅炉的设计方案及工作原理基于PLC控制电热锅炉系统是由电热锅炉、可编程控制器、传感器和水泵机组组成一个完整的锅炉供热系统,该系统的原理框图如图3.1所示。
图3.1原理框图锅炉首次使用时,通过补水泵往锅炉内注水,自来水管接有软水装置,将自来水软化成锅炉内使用热量传递的软水。
当锅炉内液位符合使用标准时,由液位传感器发出信号到PLC控制器,开始进行加热。
此时温度传感器I(入水口水温)和温度传感器O(出水口水温)偏差较大(出水口水温要求85°C),故同时使用四根加热管进行迅速加热。
当炉内温度达到供暖要求后自动关闭两根加热管,以做到低能耗运行。
当春秋季供暖需求低时,出水温度与入水口温度偏差量小,基本值为65°C(I)和85°C(O),为避免电能浪费,只需使用一根加热管进行加热。
而冬天出水温度与入水温度偏差量大,基本值为85°C(O)和50°C(I),正常工作为两根加热管,入水口温度低于50°C时使用第三根加热管进行加热,以确保供暖效果最佳。
其原理图如图3.2所示:图3.2原理图3.3热传感器的工作原理及作用本系统中采用三个传感器,分别是温度传感器I,温度传感器O和液位传感器。
温度传感器I为入水口温度传感器,装在锅炉进水口,用以观测进水口温度,与温度传感器O所观测温度相对比,反映供热系统的状况,及时调整锅炉功率,保证供暖循环系统正常有效的工作。