纺织品常见疵点及其成因
通常布面的疵点及其产生原因
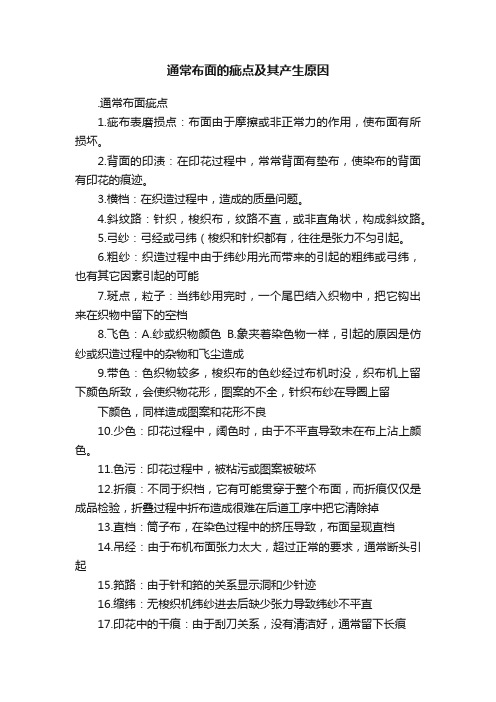
通常布面的疵点及其产生原因.通常布面疵点1.疵布表磨损点:布面由于摩擦或非正常力的作用,使布面有所损坏。
2.背面的印渍:在印花过程中,常常背面有垫布,使染布的背面有印花的痕迹。
3.横档:在织造过程中,造成的质量问题。
4.斜纹路:针织,梭织布,纹路不直,或非直角状,构成斜纹路。
5.弓纱:弓经或弓纬(梭织和针织都有,往往是张力不匀引起。
6.粗纱:织造过程中由于纬纱用光而带来的引起的粗纬或弓纬,也有其它因素引起的可能7.斑点,粒子:当纬纱用完时,一个尾巴结入织物中,把它钩出来在织物中留下的空档8.飞色:A.纱或织物颜色B.象夹着染色物一样,引起的原因是仿纱或织造过程中的杂物和飞尘造成9.带色:色织物较多,梭织布的色纱经过布机时没,织布机上留下颜色所致,会使织物花形,图案的不全,针织布纱在导圈上留下颜色,同样造成图案和花形不良10.少色:印花过程中,阔色时,由于不平直导致未在布上沾上颜色。
11.色污:印花过程中,被粘污或图案被破坏12.折痕:不同于织档,它有可能贯穿于整个布面,而折痕仅仅是成品检验,折叠过程中折布造成很难在后道工序中把它清除掉13.直档:筒子布,在染色过程中的挤压导致,布面呈现直档14.吊经:由于布机布面张力太大,超过正常的要求,通常断头引起15.筘路:由于针和筘的关系显示洞和少针迹16.缩纬:无梭织机纬纱进去后缺少张力导致纬纱不平直17.印花中的干痕:由于刮刀关系,没有清洁好,通常留下长痕18.少纱:织布和针织机断纱时仍在运转19.飞花:长在纺纱过程中杂质等飞入导致,纱线不纯20.全横档(疵):边对边全排可见的疵点允许2-3次/100码,如果超过3处,就视作为降等,如在6码内出现这些疵点,应扣除这6码数量21.综落下:一般织物吊综带断,导致织造图案的破坏22.孔:破损或破洞23.少经:各种织机停经自动装置无或失灵,导致少经时机器仍在转24.缩皱:未温而皱,通常在两头较多,当布展开来的时候,表现出来为皱纹和波浪,有时在验布机上验布时,如果下面的罗拉紧一点,就会漏过这些疵点25.混纱:纤维或纱支,差错织入布中,布看上去有一些厚或薄,如果纤维不同成品后颜色也不同26.针路:由于弯针引起,针的针痕,通常是垂直方向27.针孔:后加工过程中用于定28.印花错位:由于印花滚筒不是同步进行,导致颜色位置不对,而错位29.聚浆:由于印花过程中停机,导致这一位置中的染料太多30.皱边:预缩过程中导致皱边,缩边等31.筘路:由于筘号不符或用错导致整个图案的筘路32.经路不良:针织布由于针不良,尖针,跳针导致垂直方向的经路33.少经:针织布由于断针,导致少针,通常有断经自停装置34.折痕:布折处,经过印花机时,没有印上去35.背印:在印花过程中,由于印花压力而引起下面的布反印到布上36.松边或长边:布边比布身长,导致在拉布时走布起皱和波浪状。
面料及坯布疵点分析大全

面料及坯布疵点分析大全(1)棉粒(Nep)外观:布面呈现类似接头大小之棉纤维团,且系纺入纱中者。
如将之拔下,则纱呈断裂或将至断裂之状态。
低等级原棉纺成之粗纱,常有此种瑕疵。
成因:1)。
原棉中有死棉纤维团,于清花过程中未彻底除去.2)。
梳棉时锡林或针板之针不够尖锐,或两者间之隔距设定不当,未能充份发挥梳理作用。
(2)棉籽皮(Seeds)外观:纯棉或棉纤维混纺之胚布面,有甚小黑色或深色之非纤维纤碎片点.成因:1).轧棉工程在将棉纤维与棉籽分离时,纤维根端带有棉籽皮,或棉籽被碾碎而掺附于原棉中. 2)。
清花过程未能将棉籽皮彻底清除。
(3)粗结(Slub)外观:织物之经纱或纬纱上,偶有一小段长约5至20mm较纱之正常直径为粗,较炒之正常捻数为少之簇状纤维。
成因:1)。
精纺时喂入之粗纱内,纤维内密度不均匀,有较小型密集之梭状纤维束。
2).精纺机之皮辊及皮圈未能均一将喂入之粗纱把持。
(4)飞花(Flyer)外观:与粗结相似,但其较粗,不像粗结般之细长,纤维成团状。
将纱略予退捻,可不致使纱断裂。
成因:细纱间内飘浮于空中之纤维团,或积集在机器喂入附近台面上之纤维团,缠绕于纱上。
(5)节纱(Cockled Yarn)外观:在约纤物幅宽长度之一段纱中,有间隔性之大粗结.纱之粗细变化似竹节状,一般在粗纱织物之纬纱较常见,故亦称竹节纬。
成因:精纺机之牵伸罗拉设定大紧,罗拉盖太松,喂入之粗纱中偶有异长之纤维.(6)纱支不均(Uneven Yarn)外观:由织物长面观察,织入之纱有粗细不均匀之现象。
一般多发生在纬纱。
成因:细纱机纺出之纱,由于牵伸机构故障,或性能不良,致纺出之纱在一段间,时有略粗时有略细者。
(7)云织(Cloudd of Weaaving)外观:纬纱之支数显著不均匀,织造时粗者或细者恰好集中排列在一起,形成片状,布面外观似片片浮云,故称云织。
成因:纬纱有规律性之不匀,于织造时纬纱之排列又恰好粗者或细者汇集在一起.(8)纤维点(Fiber Spot)外观:染色之织物,布面中有极少量之纤维不上色,或上色较浅,而呈现泛白色者。
纺织品疵点及其成因大全
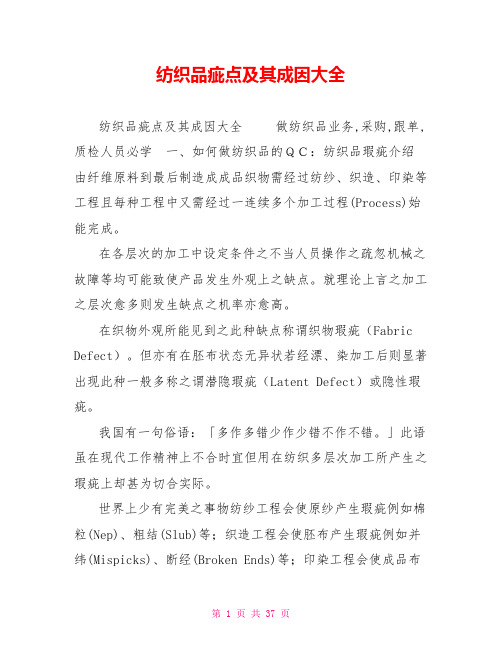
纺织品疵点及其成因大全纺织品疵点及其成因大全做纺织品业务,采购,跟单,质检人员必学一、如何做纺织品的QC:纺织品瑕疵介绍由纤维原料到最后制造成成品织物需经过纺纱、织造、印染等工程且每种工程中又需经过一连续多个加工过程(Process)始能完成。
在各层次的加工中设定条件之不当人员操作之疏忽机械之故障等均可能致使产品发生外观上之缺点。
就理论上言之加工之层次愈多则发生缺点之机率亦愈高。
在织物外观所能见到之此种缺点称谓织物瑕疵(Fabric Defect)。
但亦有在胚布状态无异状若经漂、染加工后则显著出现此种一般多称之谓潜隐瑕疵(Latent Defect)或隐性瑕疵。
我国有一句俗语:「多作多错少作少错不作不错。
」此语虽在现代工作精神上不合时宜但用在纺织多层次加工所产生之瑕疵上却甚为切合实际。
世界上少有完美之事物纺纱工程会使原纱产生瑕疵例如棉粒(Nep)、粗结(Slub)等;织造工程会使胚布产生瑕疵例如并纬(Mispicks)、断经(Broken Ends)等;印染工程会使成品布产生瑕疵例如染料点(Dye Spot)、结尾色差(Tailing or Ending)等。
品质优良之成品织物其瑕疵应为极少。
如某种成品织物之瑕疵甚多无论是用作制衣、被服、或其它日用品及装饰品均会影响其美观而降低其价值。
二、织物瑕疵之外观特征与成因由纤维至成品织物加工之阶段可分为纺纱(Spinning)织造(Weaving)练漂、染色、印花(Scouring & BleachingDyeingPrinting)与整理加工(Finishing)四大阶段。
现以在各阶段中可能发生之瑕疵用工厂一般通用之名称就其外观特征与生成之原因分述于下: 1.属于纤维原料、纱支原因者 2.属于织造原因者 3.属于印染整理原因者 4.生成原因难以归属及专业加工者 1.属于纤维原料、纱支原因者 (1)棉粒(Nep) (2)棉籽皮(Seeds) (3)粗结(Slub) (4)飞花(Flyer) (5)节纱(Cockled Yarn) (6)纱支不均(Uneven Yarn) (7)云织(Cloudd of Weaaving) (8)纤维点(Fiber Spot) (9)批号不同(Different Iots) (10)蒸纱不良(11)白点 (1)棉粒(Nep) 外观:布面呈现类似接头大小之棉纤维团且系纺入纱中者。
织布疵点原因及预防措施

11:落布操作时,由于木辊直径较大,容易与卷布刺辊上的刺毛铁皮相摩擦而产生类似边撑疵坏布。
12:边撑盒盖上螺栓头部碰撞筘帽前夹木或碰撞飞梭装置铁杆。
13:平车或拆坏布后,用手将布边拉入边撑盒的操作不当。
B:消除方法1:边撑、刺辊配套良好,安装正确。
2:使织机有关部件处于正常状态。
3:加强各工种的操作管理。
4:加强温湿度调节工作。
5:几项技术改进。
(1):采用单只刺辊。
(2):采用颗粒橡胶刺辊或乳胶管辊与铁刺辊混用。
(3):采用十片铜刺辊,比木刺辊或铁刺辊伸幅作用大1~1.5CM。
既可消除因伸幅不良造成的断边,也可减少边撑疵点。
(4):检查木刺辊、铁刺辊、铜刺辊是否达到技术要求。
(5):织机卷布刺辊两端包布,防止落布后将布头卷紧时,布边和刺毛辊表面摩擦而产生边撑疵。
(6):织机卷布辊托脚木轴承厚度,可有原来的19.2MM减为9.6MM,防止落布时布辊直径过大与卷布刺毛辊相擦而造成类似的边撑疵布。
(三):烂边第一类大烂边A:形成原因1:纬纱上的棉结杂质,特别是中、细特纱上的大杂质,以及细纱纺制时的飞花、回丝附入而产生的细节,与纬纱退绕气圈相碰,造成意外阻力。
2:纬管腔内积有回丝,因梭子冲击而从纬管头部小眼内脱出,阻塞梭子骑马钢丝或瓷眼通道,致使纬纱引伸受阻,张力增加。
3:织机揩扫时飞花落入梭子瓷眼,使纬纱引伸不畅,增加意外张力。
4:梭管配合不良,两者中心不一,梭芯高低位置不正,梭芯忽高忽低,纬管内孔磨损等,均会使纬纱退绕时的张力严重不匀。
B:消除方法1:提高纬纱质量,根据织造品种不同,提出原纱棉结杂质的具体要求,一般棉杂要小而少。
2:纬管内孔回丝,纺部要设法解决,织造车间应结合纬管定期检修,加以消除。
3:清扫织机时,落梭箱需用盖布遮住,防止飞花落入,阻塞梭子瓷眼。
4:做好梭、管配套工作。
第二类小烂边A:形成原因1:边撑伸幅作用不够,边撑刺辊第握持力不足,边纱控制不牢。
特别在纬纱由满纱逐渐退绕至小纱时更为突出。
纺织品瑕疵原因分析及处理方法

服装材料纺织品瑕疵纤维原料到最后制造成成品织物,需经过纺纱、织造、印染等工程,且每种工程中,又需经过一连续多个加工过程(Process)始能完成。
在各层次的加工中,设定条件之不当,人员操作之疏忽,机械之故障等,均可能致使产品发生外观上之缺点。
就理论上言之,加工之层次愈多,则发生缺点之机率亦愈高。
在织物外观所能见到之此种缺点,称谓织物瑕疵(Fabric Defect)。
但亦有在胚布状态无异状,若经漂、染加工后则显著出现,此种一般多称之谓潜隐瑕疵(Latent Defect)或隐性瑕疵。
我国有一句俗语:「多作多错,少作少错,不作不错。
」,此语虽在现代工作精神上不合时宜,但用在纺织多层次加工所产生之瑕疵上却甚为切合实际。
世界上少有完美之事物,纺纱工程会使原纱产生瑕疵,例如棉粒(Nep)、粗结(Slub)等;织造工程会使胚布产生瑕疵,例如并纬(Mispicks)、断经(Broken Ends)等;印染工程会使成品布产生瑕疵,例如染料点(Dye Spot)、结尾色差(Tailing or Ending)等。
品质优良之成品织物,其瑕疵应为极少。
如某种成品织物之瑕疵甚多,无论是用作制衣、被服、或其它日用品及装饰品,均会影响其美观,而降低其价值。
二、织物瑕疵之外观特征与成因由纤维至成品织物,加工之阶段可分为纺纱(Spinning),织造(Weaving),练漂、染色、印花(Scouring & Bleaching,Dyeing,Printing)与整理加工(Finishing)四大阶段。
现以在各阶段中可能发生之瑕疵,用工厂一般通用之名称,就其外观特征与生成之原因分述于下:1.属于纤维原料、纱支原因者2.属于织造原因者3.属于印染整理原因者4.生成原因难以归属及专业加工者1.属于纤维原料、纱支原因者(1)棉粒(Nep)外观:布面呈现类似接头大小之棉纤维团,且系纺入纱中者。
如将之拔下,则纱呈断裂或将至断裂之状态。
常见织疵造成原因

常见织疵造成原因织疵是指纺织品上出现的缺陷或瑕疵。
这些缺陷或瑕疵可以是织物表面的瑕疵,也可以是织物结构上的缺陷。
对于一个完美的织物,没有任何缺陷是理想的,但由于各种原因,织疵在生产过程中总是会出现。
下面将介绍一些常见的织疵造成原因。
第一,织机故障是一个常见的织疵造成原因。
织机在运作过程中可能会出现各种问题,比如织机的各个部件的磨损,不正常的振动或运动,机器的故障等。
这些故障可能导致织物上出现缺陷,比如断纬、断经、错纱等。
第二,纱线质量问题也是织疵造成原因之一。
纱线在织物生产过程中充当了重要的角色,它们是织物的基础。
如果纱线的质量不好,比如存在断丝、返纺、破编等问题,那么织物上就会出现相应的缺陷。
第三,操作人员的错误也是织疵造成原因之一。
在织物生产过程中,操作人员的技术水平和经验直接影响着织物的质量。
如果操作人员不熟悉织机的操作,或者在织物检查过程中出现疏忽,就容易导致织物上出现各种缺陷,比如错编、错纬、错织、粗织等。
第四,原料的质量问题也是织疵造成原因之一。
织物的质量受到原料质量的直接影响。
如果原料的质量不好,比如存在杂质、纤维断裂、扭曲等问题,那么织物上就会出现相应的缺陷。
第五,生产环境和工艺问题也会导致织疵的产生。
在织物生产过程中,生产环境和工艺的合理性对织物的质量有着重要的影响。
比如,如果生产环境的温度、湿度等参数不合适,或者采用了不恰当的工艺流程,都可能导致织物上出现各种缺陷。
第六,外部因素也可能导致织疵的产生。
比如运输过程中的振动、摩擦,还有织物在使用过程中的洗涤、摩擦等都可能导致织物上出现疵点。
织疵的产生是一个复杂的过程,涉及到织机、纱线、操作人员、原料、生产环境和工艺等多个方面的因素。
为了减少织疵的产生,可以采取一些有效的措施,比如密切关注织机的运行状态,定期维护和保养织机,严格控制纱线的质量,提高操作人员的技术水平和责任心,加强对原料的质量监控,优化生产环境和工艺流程等。
只有在综合考虑和解决以上因素的基础上,才能够减少织疵的产生,提高织物的质量。
纺织病疵分析大全

纺织病疵分析大全纺织病疵分析大全--集三十七年病疵分析之经验纺织病疵分析大全--集三十七年病疵分析之经验改贴进行中........2楼.一、经纱断头原因。
(不包含纱原纱品质及准备工用原因)3.二、细纱断头的原因4.色差的成因与预防5整理产品常见疵病分析一、通常外观疵病6. 二、通常内在疵病7. 三、特殊内在疵病8. 织物疵点专用术语9. 涤纶织物产生风印的症状10. 常见烧毛疵病及克服方法11. 防止真丝绸泛黄有什么较好的方法12. 滚筒印花疵病及其预防措施13. 如何减少腈纶筒子纱染色大小样色差14. 如何减少卷染机染色头尾(梢) 与左中右色差15. 毛织物染色后表面出现深浅斑渍、斑点、渍印问题16. 普通涤纶织物高温高压染色色花的防止17. 羊绒衫掉绒起球的原因分析与解决措施18. 印染布疵点产生的原因及检测方法19. bjckxj MM留位20. xiaoke MM留位!织物病疵分析鉴定报告21. 锦纶HOY长丝,已出现丝筒严重变形22. 计算坯布到成品的经向缩率23. 布面经柳原因分析24. 布面经柳原因分析25. 布面白斑原因分析26. 布面纬档原因分析27. 布面经柳原因分析28. 布面横条原因分析29. 布面经条原因分析30. 布面纬档原因分析31. 成品阳离子格子布布面经向强力过度损伤原因分析32. 大有光染色成品布布面产生经柳的原因33. 一块TTR染色成品布布面产生鸡爪印的原因。
34.一块涤纶染色成品布布面产生经柳的原因35. 四面弹染色成品布布面产生纬档原因分析36. 150D醋酯纤维绞状色丝及筒装本色丝色丝产生色差的原因37. 平板四面弹染色成品布布面产生钩毛的原因38. 成品牛仔裤及部分装饰镀件裤面出现斑点状色点的原因39. 染色成品布布面出现白条的原因40. T恤衫布面出现黑点的原因41.. 针织布布面产生横条的原因42. T/R平纹四面弹印染成品布布面产生纬档的原因43. 全棉布布面出现色差的原因44. 针织布布面产生直条的原因45.. 牛仔色织布布面产生门幅不一的原因46. 裤子袋口破裂产生47. 涤纶针织氨纶布布面产生横条的原因48. 棉氨汗布布面产生横条的原因49. 长丝四面弹染色成品布布面产生经柳的原因50. TTR染色成品布布面纬向产生黑点的原因.51.裤片产生纬档的原因52.植绒印花布(印花布、坯布各一)布面出现脱毛及色差的原因53.四面弹染色成品布布面经向产生色差的原因54.圆机布染色成品布布面产生横路的原因55. 涤纶弹力染色成品布布面产生纬档的原因56.人丝乔其染色成品布布面产生白条的原因57.纬弹染色成品布料布面产生经柳的原因58.针织布布面横路的原因59.54565115留位60.染色成品布布面产生纬档的原因61. 条子涤毛布布面经向产生断丝的原因62. 灯芯绒成品裤裤面产生横条的原因63. 二块染色涤纶弹力布及一块坯布分析布面产生经条的原因64. 二条色织牛仔裤裤面产生条纹病疵的原因65. 针织成品布布面产生横路的原因66. 点子布布面产生纬向色条的原因67. 两块布样门幅不一的原因68. 起绒布布面产生横路的原因69. 染色成品布料布面产生经柳的原因70. 大圆机布成品进行检测,分析布面产生横路的原因71.提花阳离子绉布布面局部不起绉72.涤纶四面弹进行检测,分析布面产生经柳的原因73.布面产生色点病疵的原因及检测棉纱等级74.全棉印花布布面产生破洞的原因75.布面产生色差病疵的原因76.针织汗布布面产生横条病疵的原因77.罗缎染色成品布布面产生经柳病疵的原因78.布面产生经条病疵的原因79布面色点病疵产生的原因.80.布面产生断纬现象的原因81.布面经向起泡病疵产生的原因82.人丝乔其连匹出现色差的原因83.一块四面弹出现经向白条的原因84.一块涤纶经编条绒出现色点的原因85.块100%兔绒机织布布面出现纬档的原因86.一块装饰布布面纬向色档病疵产生的原因87.一块纬弹成品布布面纬档产生的原因88一块纬弹成品布布面经向黑点产生的原因。
织布疵点大全

织造品质织疵成因一、经纱断头原因。
(不包括纱原纱品质及准备工用原因)1.综框过高低,左右不平。
2.开口过大过小,过早过迟。
3.经纱路线过短,(后梁过前),经纱张力太大4.后梁及停经架位置赤字高,上下层经不张力悬殊太大。
5.停经架与综框距离过远过低。
6.空气调节、湿度过高过低。
(尤其麻纱反应最大)7.剑颈、钢筘、综丝、停经片、剑带等毛糙。
8.过撑位置过高,应距最低位置1mm。
9.结头纱尾、飞花杂物搅入经纱。
10. 值车对经纱倒断头、搅头处理不良,断经后接纱结头不良;如纱尾长。
二、断纬原因1.纬纱强力过低、松捻纱、大结头、棉籽屑、飞花回丝夹附。
2.络筒时强力过太、张力太大、成形不良。
3.边撑太前撞筘,距离钢筘到少要有1mm的间隙。
三、双纬1.纬纱断头为主要原因,首先须减少断纬线。
2.值车工不注意在断头后,未将织口内断纬拉清。
3.值车工在断纬后未将开开口顺序较主合适时开车。
4. 纬纱断头后断纬运动未立即作用停车,而中间缺少数根或一根纬纱。
四、 缩纬1.纬纱捻度过大。
3.开口不清。
5.纬纱引出张力太小。
6.经纱张力不足。
7.纬纱筒子有大结头、飞花、杂物附着、粗节纱造成部分开口不清。
五、 小稀路1.筘座及卷取刺毛辊松动或腐蚀。
2.经纱张力过大或过小。
3.经纱上下两层纱张力相差悬殊。
4.停车过久后开车时梭口未较正。
5.停车后开车起动太缓慢影响打纬力。
(主电机皮带松驰无力)六、 纬纱尾织入1.右测经纱距离顺风管太远,废边纱未能很好夹持纱尾。
2.纬纱张力太小,剑头开启时间太晚。
七、 稀路1.起因均为断纬、首先须减少断纬。
2. 断纬卷取退卷绕装置不良。
八、 跳花1、综框松动、不平或过低。
2、 经纱张力上下两层相差悬殊。
3、浆纱过毛、开口粘滞、上浆不良引起绒球或毛羽。
2.纬纱太干或太湿。
4. 开口时间过早或过迟。
4、经纱有飞毛、纱尾及大结头。
5、综丝头尾损断或综丝搅乱。
6、部分经纱松弛或张力过低。
7、开口时间不对。
常见织疵形成的原因

常见织疵形成的原因泡泡布形成原因:1.氨纶丝未经导丝辊,从侧面进入。
2.导丝轮不转或不灵活。
3.无芯纱流入下工序未卡住。
4.氨纶丝位置不当,导致包覆不良。
预防措施:1.定期检查芯丝位置,确保芯丝在须条中间偏左位置。
2.精心挑拣已落下的纱,避免无芯纱流入下工序。
3.加强巡回,丝轮不转及时发现,将纱卡下并维修丝轮。
条干布形成原因:1.牵伸部件运转不良,如皮辊损伤、偏心、跳动,罗拉粘棉结、杂物,罗拉轴承座磨损,无下皮圈纺纱,上下皮圈损伤,罗拉偏心、弯曲、上肖失效等。
2.一头缠花严重,另一头继续纺纱(失压)。
3.导纱动程跑偏。
4.罗拉加压不良(并条、粗纱等)。
5.纱条通道不光洁,造成挂花。
竹节纱(灰竹节)形成原因:1.清梳工序漏底花堆积太多,带入棉层。
2.各工序通道粘、缠、挂、堵带入(三角区、龙头,并粗、细纱牵伸通道)3.绒板、绒套、绒辊花带入(并条、粗纱、精梳、细纱)。
4.高空清洁积花掉入半成品或正在纺纱机内。
5.各工序清洁方法不当。
6.卡疵把关不严,疵点流入下工序。
7.清洁不彻底(例如粗纱斜坡、车面清洁不及时,巡回吹吸风吹入,打擦板时的飞花卷入纱条等)。
8.各工序揩车不良,油飞花粘附纱条,半成品棉条、粗纱掉地,造成污染。
三丝疵布形成原因:1.拣花间未拣净,后工序未卡住。
2.个别员工在工作场所梳头,清洁工具破损掉毛仍在使用。
应对措施:1.加强员工拣色杂责任心教育,后续工序严格执行卡疵把关制度。
2.加强管理,严格要求,杜绝在工作场所梳头现象;同时,车间定期对清洁工具检查,发现掉毛立即停止使用。
粗经、粗纬形成原因:1.粗纱断头、烂纱后未及时停车,飘入邻纱未处理干净。
2.条子粘连,机后换条子破条或机后双条喂入。
3.接头不符合操作法要求(并条、粗纱、细纱等工序)。
4.细纱断头飘入邻纱(主要是混纺纱)5.细纱续粗纱或粗纱纱尾飘入邻纱,细纱机车顶板的粗纱尾巴下垂,被卷入上排粗纱。
纬缩形成原因:1.纬纱质量不良。
2.纬纱捻度过高。
干货纺织品62种瑕疵及成因汇总,如何帮客户解决?
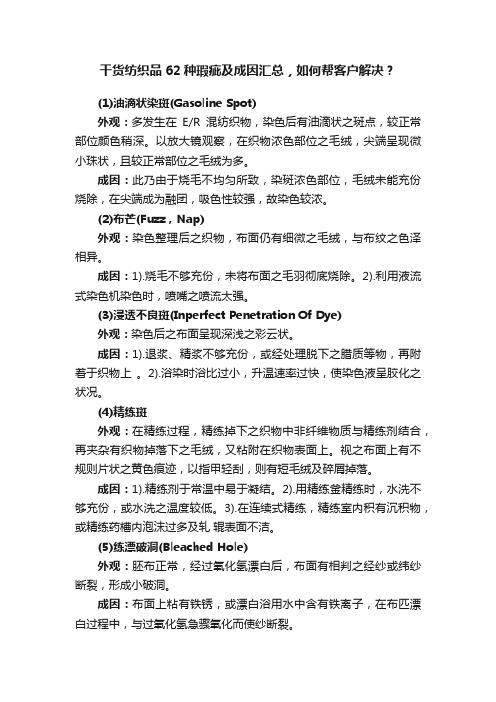
干货纺织品62种瑕疵及成因汇总,如何帮客户解决?(1)油滴状染斑(Gasoline Spot)外观:多发生在E/R混纺织物,染色后有油滴状之斑点,较正常部位颜色稍深。
以放大镜观察,在织物浓色部位之毛绒,尖端呈现微小珠状,且较正常部位之毛绒为多。
成因:此乃由于烧毛不均匀所致,染斑浓色部位,毛绒未能充份烧除,在尖端成为融团,吸色性较强,故染色较浓。
(2)布芒(Fuzz,Nap)外观:染色整理后之织物,布面仍有细微之毛绒,与布纹之色泽相异。
成因:1).烧毛不够充份,未将布面之毛羽彻底烧除。
2).利用液流式染色机染色时,喷嘴之喷流太强。
(3)浸透不良斑(Inperfect Penetration Of Dye)外观:染色后之布面呈现深浅之彩云状。
成因:1).退浆、精浆不够充份,或经处理脱下之腊质等物,再附着于织物上。
2).浴染时浴比过小,升温速率过快,使染色液呈胶化之状况。
(4)精练斑外观:在精练过程,精练掉下之织物中非纤维物质与精练剂结合,再夹杂有织物掉落下之毛绒,又粘附在织物表面上。
视之布面上有不规则片状之黄色痕迹,以指甲轻刮,则有短毛绒及碎屑掉落。
成因:1).精练剂于常温中易于凝结。
2).用精练釜精练时,水洗不够充份,或水洗之温度较低。
3).在连续式精练,精练室内积有沉积物,或精练药槽内泡沫过多及轧辊表面不洁。
(5)练漂破洞(Bleached Hole)外观:胚布正常,经过氧化氢漂白后,布面有相判之经纱或纬纱断裂,形成小破洞。
成因:布面上粘有铁锈,或漂白浴用水中含有铁离子,在布匹漂白过程中,与过氧化氢急骤氧化而使纱断裂。
(6)色花(Skilteriness)外观:布面有不规则片状之颜色深浅。
成因:前处理工程之退浆,精练未能彻底作好。
(7)雾斑(Mist)外观:片状之染斑,有深有浅,轮廓不明显,形状大小不一,发生之位置不集中,亦无一定之规则。
成因:1).待染之织物,被溅到污水或其它药品。
2).练漂后未立即烘干,长时间堆积在布车上,部份织物发生风干之水印。
纺织品瑕疵介绍(四)

纺织品瑕疵介绍(四)(31)异色污染(Colored Spot)外观:织物表面呈现大面积无一定形状之其它颜色污染。
成因:1.织物在湿润状态时,与不同颜色之染色织物接触所发生之污染。
若颜色相差悬殊者更为明显。
2.在加工或搬运过程中,器具未能彻底洗净。
(32)泡沫污染(Scum Spot)外观:织物表面有泡沫残渣贴附,烘干后成大片状或粗条状颜色略白之痕迹。
成因:1.染色液之泡沫较多,附着于布面上。
多由于选用之分散剂与助剂不当。
2.还原液之泡沫较多,尤以使用瓮染料染色后还原时较易发生。
3.在**酚显色液中,若含有无法重氮化之不纯物时,则会形成泡沫浮渣。
(33)凝集污染(Tarring Strining)外观:染色时染料相互间、染料与助剂间发生凝集,而使染料溶解不良。
染色后在布面上发生纹状或短条状颜色较深之污染。
成因:1.染料溶解、分散欠佳,或染料中混有其它化学药品,及染色用水之硬度过高。
2.染料与助剂之组合不相宜,或助剂之添加时机、次序不恰当34)滚筒污染。
外观:布疋在染整过程中,经过圆筒形装置时,因圆筒周面之不洁,例如黏有油质、化学药品、染料及其它污秽物等,污染到布面上。
形状多为小片状,且两处污染间有一定之距离。
成因:1.导布辊黏有油迹。
2.压辊黏有焦油状色淀,或由织物上脱落下之短纤维等污秽物。
3.烘干之圆筒黏有油渍及污秽物。
(35)药品污染(Chemicals Staining)外观:织物表面有点状、片状之变褪色、污染或变质。
成因:由于非应该使用之化学药品渗入织物中而形成。
(36)染色停机痕(Dyeing Stop Mark)外观:沿织物之纬向或横向,有一条2自10公分宽之痕迹,较正常之颜色为深或浅,且其两边有似水印状。
成因:机械在正常运转期中,因停电、卷布或其它机械故障,突然停止运转时,织物被夹持在两轧辊间,发生在压吸染色液或压吸还原液时。
(37)色斑外观:已包装好之成品织物,打开后布面有同色较深之斑点。
面料和坯布疵点分析大全

面料及坯布疵点分析大全(1)棉粒(Nep)外观:布面呈现类似接头大小之棉纤维团,且系纺入纱中者。
如将之拔下,那么纱呈断裂或将至断裂之状态。
低品级原棉纺成之粗纱,常有此种瑕疵。
成因:1).原棉中有死棉纤维团,于清花进程中未完全除去。
2).梳棉时锡林或针板之针不够尖锐,或二者间之隔距设定不妥,未能充份发挥梳理作用。
(2)棉籽皮(Seeds)外观:纯棉或棉纤维混纺之胚布面,有甚小黑色或深色之非纤维纤碎片点。
成因:1).轧棉工程在将棉纤维与棉籽分离时,纤维根端带有棉籽皮,或棉籽被碾碎而掺附于原棉中。
2).清花进程未能将棉籽皮完全清除。
(3)粗结(Slub)外观:织物之经纱或纬纱上,偶有一小段长约5至20mm较纱之正常直径为粗,较炒之正常捻数为少之簇状纤维。
成因:1).精纺时喂入之粗纱内,纤维内密度不均匀,有较小型密集之梭状纤维束。
2).精纺机之皮辊及皮圈未能均一将喂入之粗纱把持。
(4)飞花(Flyer)外观:与粗结相似,但其较粗,不像粗结般之细长,纤维成团状。
将纱略予退捻,可不致使纱断裂。
成因:细纱间内飘浮于空中之纤维团,或积集在机械喂入周围台面上之纤维团,缠绕于纱上。
(5)节纱(Cockled Yarn)外观:在约纤物幅宽长度之一段纱中,有距离性之大粗结。
纱之粗细转变似竹节状,一样在粗纱织物之纬纱较常见,故亦称竹节纬。
成因:精纺机之牵伸罗拉设定大紧,罗拉盖太松,喂入之粗纱中偶有异长之纤维。
(6)纱支不均(Uneven Yarn)外观:由织物长面观看,织入之纱有粗细不均匀之现象。
一样多发生在纬纱。
成因:细纱机纺出之纱,由于牵伸机构故障,或性能不良,致纺出之纱在一段间,时有略粗时有略细者。
(7)云织(Cloudd of Weaaving)外观:纬纱之支数显著不均匀,织造时粗者或细者恰好集中排列在一路,形成片状,布面外观似片片浮云,故称云织。
成因:纬纱有规律性之不匀,于织造时纬纱之排列又恰好粗者或细者聚集在一路。
纺织面料瑕疵总结
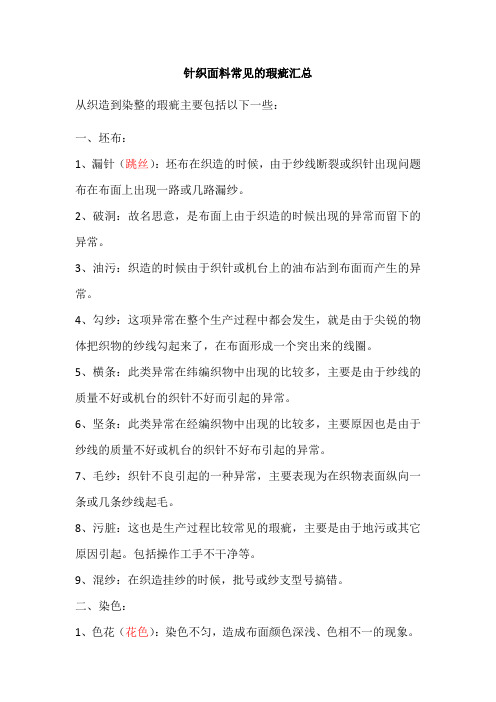
针织面料常见的瑕疵汇总从织造到染整的瑕疵主要包括以下一些:一、坯布:1、漏针(跳丝):坯布在织造的时候,由于纱线断裂或织针出现问题布在布面上出现一路或几路漏纱。
2、破洞:故名思意,是布面上由于织造的时候出现的异常而留下的异常。
3、油污:织造的时候由于织针或机台上的油布沾到布面而产生的异常。
4、勾纱:这项异常在整个生产过程中都会发生,就是由于尖锐的物体把织物的纱线勾起来了,在布面形成一个突出来的线圈。
5、横条:此类异常在纬编织物中出现的比较多,主要是由于纱线的质量不好或机台的织针不好而引起的异常。
6、坚条:此类异常在经编织物中出现的比较多,主要原因也是由于纱线的质量不好或机台的织针不好布引起的异常。
7、毛纱:织针不良引起的一种异常,主要表现为在织物表面纵向一条或几条纱线起毛。
8、污脏:这也是生产过程比较常见的瑕疵,主要是由于地污或其它原因引起。
包括操作工手不干净等。
9、混纱:在织造挂纱的时候,批号或纱支型号搞错。
二、染色:1、色花(花色):染色不匀,造成布面颜色深浅、色相不一的现象。
2、色迹:也叫色点,形成原因很多。
有操作不当、染料、缸等众多因素。
3、色差:生产的大货与原样(客户来办)颜色相差太大,包话色调、明度、饱和度方面存在差异。
4、边中差:由于布边卷起,而产成染色时吃色不匀。
布边的颜色跟中间的颜色不一致。
5、前后色差:布的头和尾颜色不一致。
主要由于预定型前后温度相差太大或染色升温太快而引起。
6、左右色差:左右颜色不一,主要由于织造张力或纱支的问题而引起。
7、阴阳色:布的正反面颜色不一,主要是由于纱支规格不一样出现染色时的竞染。
8、色移:主要出现在一些荧光色和大红色系上,由于染色出缸后布面温度不一或放置时间过长,而造成布面染料转移的一种异常。
9、缸污:因排缸不当或洗缸不彻底而被缸内殘留的染料污染。
10、白斑:因缸内污垢沾在布面经定型后,殘留在布面的一种异常。
11、折皱:染色时浴比太小或降温太快和水洗太快,造成布面不平整,也叫鸡爪痕。
常见主要织疵的原因分析[资料]
![常见主要织疵的原因分析[资料]](https://img.taocdn.com/s3/m/1537f3fd80c758f5f61fb7360b4c2e3f572725ab.png)
常见主要织疵的原因分析常见主要织疵的原因分析.断经原因:原纱质量,浆纱质量,综筘保养,经纱上机张力,工艺参数选择,车间温度控制不当。
2.筘痕布面上出现经向的直线条纹即为筘痕。
主要原因:筘齿内排列不均匀,筘齿变形。
次要因素:经纱绞头,综框变形导致综丝不能自由游动。
3.双纬和百脚纬纱在布边外断头,梭子带着纱尾飞行,出梭口时,被梭口夹住织入布边,又继续引纬,对于平纹织物这会产生缺纬或双纬织疵,对于斜纹织物则称为百脚疵点。
梭子从开关侧投向换梭侧时,如有断纬,须待梭子回到开关侧时,纬纱叉才起关车作用,这是织口内缺一根纬纱,会形成双纬或百脚织疵。
4.脱纬原因:投梭力过大,使梭子回跳过大;纬纱卷绕过松;纬管上纱圈之间摩擦力太小等都会造成纬纱退绕量过多,在织物表面形成纬圈。
5.云织织物表面局部稀密不匀,形似云斑状的疵点称为云织,严重时在织物表面呈现稀疏方眼。
送经机构发生故障,使送经量不匀;卷取机构失灵,使卷取时快时慢,都会产生云织。
6.纬缩纬纱织入织物时呈扭结状,或织物表面出现纬圈,均称为纬缩。
纬纱捻度过大,纬纱给湿不足,开口不清,张力不足,梭子回跳过大,都会产生纬缩。
对于喷气织机,开口不清或在纬纱出口侧引纬力不足是产生纬缩的主要原因。
7.锯齿边布边对着织物的外观,染整过程能否顺利进行有着重要影响。
纬纱退绕不顺利,张力忽大忽小,使得布边内卷,最容易产生锯齿边。
织轴上机不良,边部经纱张力不匀,使布边不平整,同样会产生锯齿边。
8.方眼平纹织物布面呈现网针孔状的现象称为方眼。
后梁过低,开口时间过迟,打纬前后上下层经纱张力相近,在与纬纱交织时,部分经纱不能测向移动,便会产生方眼。
9.跳花跳纱星形跳花三根及三根以上的经纱或纬纱脱离组织,并列的跳过纬纱或经纱而浮于织物表面的称为跳花。
一根和两根经纱或纬纱,跳过三根及以上的纬纱或经纱的称为跳纱。
一根经纱或纬纱,跳过二根至四根纬纱或经纱,且形成星点状疵点的称为星形跳花,简称星跳。
纺织品整理常见外观疵病分析

纺织品整理常见外观疵病分析1.高温变色⒉搭色⒊松板印⒋极光(轧光印、条印)⒌卷边⒍纬斜⒎手感疲软⒏披裂⒐木盘渍10。
圆花不圆⒒甩水印(鸡爪印、眉毛皱) ⒓破边⒔凸铗⒕脱铗⒖油渍⒗边深浅及正反面色差⒘吸水管印⒙手感粗糙⒚头皱⒛皱条21.树脂渍22。
潮白柳23. 污渍24.针洞进“肉”,双缉边⒈高温变色⑴形态:深浅不均的变色,呈金属色样的色块。
⑵产生原因:①烘燥整理时单辊筒烘燥机第一道烘燥蒸汽压力过高,或多辊筒烘燥机第一捧烘筒蒸汽压力过高。
②烘燥整理车速过慢。
⑶防止办法:①蒸汽压力采用先低后高。
②掌握适当的烘躁车速。
⒉搭色⑴形态:辊筒搭色、压辊布搭色。
⑵产生原因:①辊筒未擦干净。
②深、浅色织物烘燥整理时,压辊布不分。
⑶防止办法:①做好烘燥机辊筒的清洁工作;调换色泽时多辊筒烘燥机需用水将前几只烘简上沾着的绒毛冲干净。
②深、浅色织物烘燥整理时,压辊布要分开⒊松板印⑴形态:布面显示出树木生长的年轮花纹。
⑵产生原因:①烘躁时产生的水蒸气未排净。
②导布未烘焊,产生头梢松板印。
③单辊筒或多辊筒烘燥机卷轴皮带过紧,张力过大。
⑶防止办法:①在保证质量的前提下,卷轴皮带不宜过紧。
②加大鼓风量,吹走水蒸气。
③导布慢速烘燥,直至干燥。
⒋极光(轧光印、条印)⑴形态:布面呈现有规律或无规律的点状、条状或块状亮光。
⑵产生原因:①压辊布包得不平整,压辊布已损坏,呢毯起皱,造成有规律的极光。
②压辊布内裹入纱头或其他杂物,与布面摩擦产生极光。
③定形整理时,出风口处幅宽与中位幅宽接近,在织物边部产生极光印。
④烘燥整理时,揿布过重,与织物摩擦产生无规律的经向极光。
⑶防止办法:①呢毯整理时,必须在呢毯运转平服后再开车。
②烘燥整理时,以将织物揿直为标准。
③定形整理时,出口处门幅应大于中位门幅1~1.5cm,这对长丝织物定形更为必要。
④开车前检查压辊布是否平挺,损坏的压辊布应及时更换。
⑤开车前检查压辊布是否有小硬结杂质,如有,应及时清除。
⒌卷边⑴形态:边口不平挺,两层叠起。
面料织疵分析
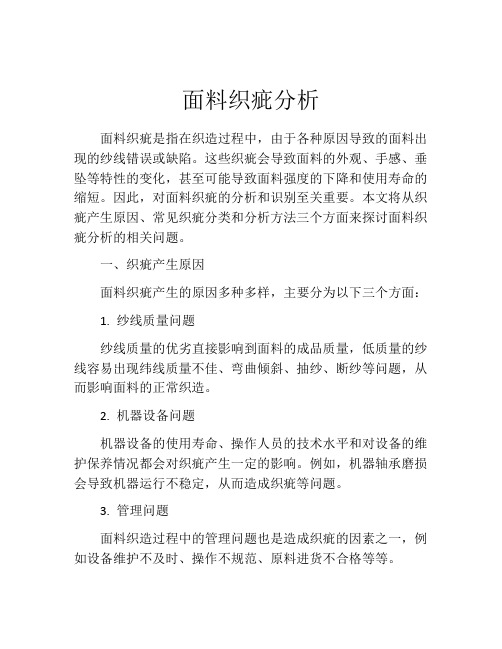
面料织疵分析面料织疵是指在织造过程中,由于各种原因导致的面料出现的纱线错误或缺陷。
这些织疵会导致面料的外观、手感、垂坠等特性的变化,甚至可能导致面料强度的下降和使用寿命的缩短。
因此,对面料织疵的分析和识别至关重要。
本文将从织疵产生原因、常见织疵分类和分析方法三个方面来探讨面料织疵分析的相关问题。
一、织疵产生原因面料织疵产生的原因多种多样,主要分为以下三个方面:1. 纱线质量问题纱线质量的优劣直接影响到面料的成品质量,低质量的纱线容易出现纬线质量不佳、弯曲倾斜、抽纱、断纱等问题,从而影响面料的正常织造。
2. 机器设备问题机器设备的使用寿命、操作人员的技术水平和对设备的维护保养情况都会对织疵产生一定的影响。
例如,机器轴承磨损会导致机器运行不稳定,从而造成织疵等问题。
3. 管理问题面料织造过程中的管理问题也是造成织疵的因素之一,例如设备维护不及时、操作不规范、原料进货不合格等等。
二、常见面料织疵分类1. 结构性疵点结构性疵点指的是面料上出现的结构性变化,例如缺纬、漏纬、抽纱等。
这些疵点会影响面料的垂坠度、外观和手感等特性,甚至会导致面料的运用寿命降低。
2. 色线疵点色线疵点主要包括色差、错花、织花等问题,这些疵点对面料的颜色、图案、质感也有一定的影响。
3. 尺寸性疵点尺寸性疵点指的是面料大小、厚度、密度等方面的织疵。
这些疵点如果严重则会导致面料失去应有的使用功能,例如不适合制作衣物等。
三、面料织疵分析方法1. 观察法通过目视观察,找出布面上的不规则点、掌纹、节每扭曲、疵片等。
不仅要看疵点的大小和形状,还要通过观察它的位置和分布规律等信息确定是何种织疵。
2. 毛细管吸气法毛细管吸气法可用于观察织疵扭曲、断裂及织结的位置等信息。
通过对织疵吸气时毛细管内的水的变化观察,得出织疵的位置与形状。
3. 线追踪法线追踪法是一种通过对织疵产生的图案特征进行描述,然后追踪相应的纬线或经线,以确定其在布面上的位置与形状的方法。
学习常见布料外观疵点图解及成因分析
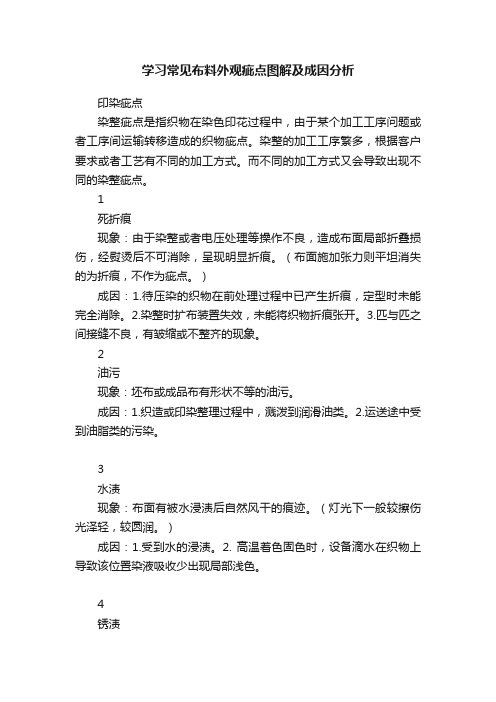
学习常见布料外观疵点图解及成因分析印染疵点染整疵点是指织物在染色印花过程中,由于某个加工工序问题或者工序间运输转移造成的织物疵点。
染整的加工工序繁多,根据客户要求或者工艺有不同的加工方式。
而不同的加工方式又会导致出现不同的染整疵点。
1死折痕现象:由于染整或者电压处理等操作不良,造成布面局部折叠损伤,经熨烫后不可消除,呈现明显折痕。
(布面施加张力则平坦消失的为折痕,不作为疵点。
)成因:1.待压染的织物在前处理过程中已产生折痕,定型时未能完全消除。
2.染整时扩布装置失效,未能将织物折痕张开。
3.匹与匹之间接缝不良,有皱缩或不整齐的现象。
2油污现象:坯布或成品布有形状不等的油污。
成因:1.织造或印染整理过程中,溅泼到润滑油类。
2.运送途中受到油脂类的污染。
3水渍现象:布面有被水浸渍后自然风干的痕迹。
(灯光下一般较擦伤光泽轻,较圆润。
)成因:1.受到水的浸渍。
2. 高温着色固色时,设备滴水在织物上导致该位置染液吸收少出现局部浅色。
4锈渍现象:织物沾锈后留下的痕迹。
成因:1、织物保存时,湿润环境下保存时与金属有接触;2、喷水织机织造后,没及时处理,容易因为织物湿润遭受金属污染。
5霉斑现象:布面出现灰黑色或淡红色发霉斑点。
成因:存放环境湿度高,或者织物湿润状态下存放时间过久。
6练漂破洞现象:经过氧化剂处理后,坯布布面含铁锈或者霉斑相近的经纱或纬纱断裂,形成小破洞。
成因:布面锈渍或者霉斑位置纤维已经遭受侵蚀破坏,氧化反应后破损。
7色花现象:布面有不规则片状的颜色深浅。
成因:前处理退浆精炼不彻底或者缸染中途停机温度变化,导致着色不均匀。
8首尾色差与缸别色差首尾色差:一批含数匹或数十匹的织物,在同样设定的条件下连续染色后,布头与布尾颜色有深浅差别。
缸别色差:大批量织物分数缸或一缸数次染色时,不是同缸同批染色导致深浅差异。
各缸虽同一型式,但其功能会略有差别。
在染色制程中,各次操作条件亦无法尽同。
9预缩皱现象:在预缩工序中,因为预缩机张力过大,导致内部熨烫滚筒卷布时造成的纬向不平整皱痕。
常见织疵形成的原因及预防措施
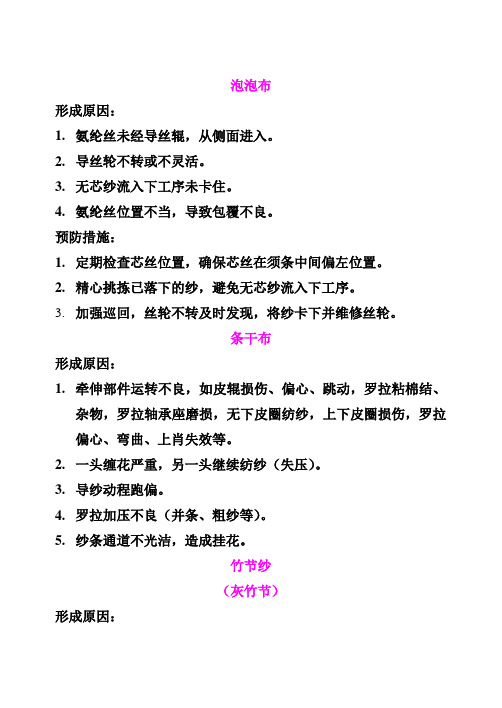
泡泡布形成原因:1.氨纶丝未经导丝辊,从侧面进入。
2.导丝轮不转或不灵活。
3.无芯纱流入下工序未卡住。
4.氨纶丝位置不当,导致包覆不良。
预防措施:1.定期检查芯丝位置,确保芯丝在须条中间偏左位置。
2.精心挑拣已落下的纱,避免无芯纱流入下工序。
3.加强巡回,丝轮不转及时发现,将纱卡下并维修丝轮。
条干布形成原因:1.牵伸部件运转不良,如皮辊损伤、偏心、跳动,罗拉粘棉结、杂物,罗拉轴承座磨损,无下皮圈纺纱,上下皮圈损伤,罗拉偏心、弯曲、上肖失效等。
2.一头缠花严重,另一头继续纺纱(失压)。
3.导纱动程跑偏。
4.罗拉加压不良(并条、粗纱等)。
5.纱条通道不光洁,造成挂花。
竹节纱(灰竹节)形成原因:1.清梳工序漏底花堆积太多,带入棉层。
2.各工序通道粘、缠、挂、堵带入(三角区、龙头,并粗、细纱牵伸通道)3.绒板、绒套、绒辊花带入(并条、粗纱、精梳、细纱)。
4.高空清洁积花掉入半成品或正在纺纱机内。
5.各工序清洁方法不当。
6.卡疵把关不严,疵点流入下工序。
7.清洁不彻底(例如粗纱斜坡、车面清洁不及时,巡回吹吸风吹入,打擦板时的飞花卷入纱条等)。
8.各工序揩车不良,油飞花粘附纱条,半成品棉条、粗纱掉地,造成污染。
三丝疵布形成原因:1.拣花间未拣净,后工序未卡住。
2.个别员工在工作场所梳头,清洁工具破损掉毛仍在使用。
应对措施:1.加强员工拣色杂责任心教育,后续工序严格执行卡疵把关制度。
2.加强管理,严格要求,杜绝在工作场所梳头现象;同时,车间定期对清洁工具检查,发现掉毛立即停止使用。
粗经、粗纬形成原因:1.粗纱断头、烂纱后未及时停车,飘入邻纱未处理干净。
2.条子粘连,机后换条子破条或机后双条喂入。
3.接头不符合操作法要求(并条、粗纱、细纱等工序)。
4.细纱断头飘入邻纱(主要是混纺纱)5.细纱续粗纱或粗纱纱尾飘入邻纱,细纱机车顶板的粗纱尾巴下垂,被卷入上排粗纱。
疵点条子形成原因:粗细条:生条:1、棉卷片段重量差异大或粘卷、破洞、头码过厚、双层卷。
- 1、下载文档前请自行甄别文档内容的完整性,平台不提供额外的编辑、内容补充、找答案等附加服务。
- 2、"仅部分预览"的文档,不可在线预览部分如存在完整性等问题,可反馈申请退款(可完整预览的文档不适用该条件!)。
- 3、如文档侵犯您的权益,请联系客服反馈,我们会尽快为您处理(人工客服工作时间:9:00-18:30)。
一、纺织品瑕疵介绍由纤维原料到最后制造成成品织物,需经过纺纱、织造、印染等工程,且每种工程中,又需经过一连续多个加工过程(Process)始能完成。
在各层次的加工中,设定条件之不当,人员操作之疏忽,机械之故障等,均可能致使产品发生外观上之缺点。
就理论上言之,加工之层次愈多,则发生缺点之机率亦愈高。
在织物外观所能见到之此种缺点,称谓织物瑕疵(Fabric Defect)。
但亦有在胚布状态无异状,若经漂、染加工后则显著出现,此种一般多称之谓潜隐瑕疵(Latent Defect)或隐性瑕疵。
我国有一句俗语:「多作多错,少作少错,不作不错。
」,此语虽在现代工作精神上不合时宜,但用在纺织多层次加工所产生之瑕疵上却甚为切合实际。
世界上少有完美之事物,纺纱工程会使原纱产生瑕疵,例如棉粒(Nep)、粗结(Slub)等;织造工程会使胚布产生瑕疵,例如并纬(Mispicks)、断经(Broken Ends)等;印染工程会使成品布产生瑕疵,例如染料点(Dye Spot)、结尾色差(Tailing or Ending)等。
品质优良之成品织物,其瑕疵应为极少。
如某种成品织物之瑕疵甚多,无论是用作制衣、被服、或其它日用品及装饰品,均会影响其美观,而降低其价值。
二、织物瑕疵之外观特征与成因由纤维至成品织物,加工之阶段可分为纺纱(Spinning),织造(Weaving),练漂、染色、印花(Scouring & Bleaching,Dyeing,Printing)与整理加工(Finishing)四大阶段。
现以在各阶段中可能发生之瑕疵,用工厂一般通用之名称,就其外观特征与生成之原因分述于下:1、属于纤维原料、纱支原因者(1)、棉粒(Nep)外观:布面呈现类似接头大小之棉纤维团,且系纺入纱中者。
如将之拔下,则纱呈断裂或将至断裂之状态。
低等级原棉纺成之粗纱,常有此种瑕疵。
成因:1.原棉中有死棉纤维团,于清花过程中未彻底除去。
2.梳棉时锡林或针板之针不够尖锐,或两者间之隔距设定不当,未能充份发挥梳理作用。
(2)棉籽皮(Seeds)外观:纯棉或棉纤维混纺之胚布面,有甚小黑色或深色之非纤维纤碎片点。
成因:1.轧棉工程在将棉纤维与棉籽分离时,纤维根端带有棉籽皮,或棉籽被碾碎而掺附于原棉中。
2.清花过程未能将棉籽皮彻底清除。
(3)粗结(Slub)外观:织物之经纱或纬纱上,偶有一小段长约5至20mm较纱之正常直径为粗,较炒之正常捻数为少之簇状纤维。
成因:1.精纺时喂入之粗纱内,纤维内密度不均匀,有较小型密集之梭状纤维束。
2.精纺机之皮辊及皮圈未能均一将喂入之粗纱把持。
(4)飞花(Flyer)外观:与粗结相似,但其较粗,不像粗结般之细长,纤维成团状。
将纱略予退捻,可不致使纱断裂。
成因:细纱间内飘浮于空中之纤维团,或积集在机器喂入附近台面上之纤维团,缠绕于纱上。
(5)节纱(Cockled Yarn)外观:在约纤物幅宽长度之一段纱中,有间隔性之大粗结。
成因:精纺机之牵伸罗拉设定大紧,罗拉盖太松,喂入之粗纱中偶有异长之纤维。
(6)纱支不均(Uneven Yarn)外观:由织物长面观察,织入之纱有粗细不均匀之现象。
一般多发生在纬纱。
成因:细纱机纺出之纱,由于牵伸机构故障,或性能不良,致纺出之纱在一段间,时有略粗时有略细者。
(7)云织(Cloudd of Weaaving)外观:纬纱之支数显著不均匀,织造时粗者或细者恰好集中排列在一起,形成片状,布面外观似片片浮云,故称云织。
成因:纬纱有规律性之不匀,于织造时纬纱之排列又恰好粗者或细者汇集在一起。
(8)纤维点(Fiber Spot)外观:染色之织物,布面中有极少量之纤维不上色,或上色较浅,而呈现泛白色者。
成因:1.棉纤维中有死棉纤维。
2.在纺纱过程中,因疏忽或管制欠妥,混入极少量之聚酯纤维,于染色时非使用分散性染料,及非高温施染,则聚酯纤维不上色。
(9)批号不同(Different Iots)外观:化纤丝或化纤加工丝织物,混纺纱织物,支数粗细与密度均符合规定,但经染色后,经纱间或纬纱间有界限分明颜色深浅之不同。
成因:在织造时使用之混纺纱,虽支数与密度符合规定,但纱中纤维之混纺率不同,在经染色后则有颜色深浅之差别。
(10)蒸纱不良:外观:T/C混纺布,经退浆、精练、漂白后,布幅有间隔性宽窄不同之变化。
成因:混纺纱于细纱落管后,需利用高压饱和蒸汽于密闭之容器内热蒸处理,以稳定纱之物性。
如蒸纱温度或时间不足,未能使纱定型,则于练漂时蒸煮后,织物布面横向呈现一段紧,一段松之现象。
(11)白点:外观:染色之织物,布面呈现未上色之纤维团,尤以染中深色者较为显著。
成因:多发生在中、下等级之棉质染色布,纱中死棉纤维所形成之棉粒,于精练,丝光时未能清除。
染色时因该种死棉纤维上色性甚差,故难以染着而呈现白点。
近来20Ne以下之纯棉开端纺纱织成之织物,于染色时经常发生。
2属于织造原因者(1)异纱(Wrong Yarn)外观:在针织物之毛中,横向连续之毛圈,由较规格用纱为粗或细之纱织造而成。
一般多为单根,但偶亦有并列或间隔多根者。
视之稀密、厚薄与正常者不同。
成因:在针织物织造时,操作人员误用非指定支数或丹尼规格之纱编织。
误用较细之纱,则织物显得稀薄。
误用较粗之纱,则织物显得密厚(2)异经(Wrong End)外观:梭织物之经纱有单独一根或并列数根非指定规格之粗细者。
若为较细之纱,则称谓细经(Fine End)。
若为较粗之纱,则称谓粗经(Coarse End) 。
成因:于整经时取用牵经之筒子纱支数错误,使用非指定规格之经纱。
此种瑕疵经常为全疋性者。
(3)异纬(Wrong Pick)外观:梭织物之纬物,有一根或连续多根非指定规格之粗细者。
若为较细之纱,则称谓细纬(Fine Pick)。
若为较粗之纱,则称谓粗纬(Coarse Pick)。
成因:于织造时,纬纱管之纬纱,或无梭织机喂入之筒子纱支数错误,使用非指定规格之纬纱。
操作人员于发现后,多予以停机拆除。
但自动换管之织机,则往往不易发现。
(4)组织错误(Wrong Weaving)外观:即织法错误,布面之织纹与原设计者不同。
例如左斜纹织成右斜纹等。
成因:一般多为穿综错误所造成。
其它如提花织物之纹板错误,多规格经纱织物之经纱排列错误等。
(5)并经(Wrong Draw)外观:相邻之两根经纱并在一起,依织物组织当作一根织入布中者。
视之,该根(实为两根)纱显得特别粗。
此种瑕疵均为全疋性者,如在经轴初织时发现,剔除并列中之一根,则能完全避免。
成因:1.整经牵纱时即疏忽将两根当作一根。
2.浆纱后分纱不清,两根黏在一起,形同一根。
3.穿综时两根穿入同一综丝。
(6)并纬(Mispick)外观:纬纱两根织入同一织口内,偶亦有三根或更多根者。
并纬之长度长短不等,以织物全幅宽者,与在近两布边10公分上下者较多。
成因:1.织物全幅长之并纬,系因停机排除故障后,未查对织口开车。
或探纬针失效,断纬未自停。
2.非全幅长之并纬,经因保险纱之长度不够,边剪设定不当或不够锐利,及断纬后未将纱尾清除。
(7)稀衖(Set Mark,Fine)外观:布面上纬纱排列之密度较规定稀少。
沿织物长度一段织入之纬纱,由正常密度逐渐变稀,再由最稀逐渐恢复至原来密度,形成一条等宽窄之稀疏布面。
成因:1.探纬针失灵,无纬纱时继续空转送经。
2.织造时经纱张力控制不当。
3.停机再开车前经纱张力调整太紧。
(8)密路(Set Mark,Coarse)外观:布面上纬纱排列之密度,较规定密集。
沿织物长度一段织入之纬纱,由正常密度逐渐变密,再由最密逐渐恢复至原来密度,形成一条等宽窄之紧密布面。
成因:1.织造时经纱张力控制不当。
2.停机再开车时经纱张力调整太松。
(9)拆痕(Pick-Out Mark)外观:胚布纬纱拆除不善,再继续织造后,布面上仍留有痕迹者。
成因:在织物织造中,作业人员发现有异纬织入,或织造出严重之密路、稀衖,立即停机将该织入之纬纱剪断拆除。
于拆除时经纱受到纬纱摘下之摩擦,产生大量之毛羽,故重织后,在原拆除之范围,呈现一条宽窄相等之多毛羽布面。
(10)断经(Broken End)外观:织物之经纱断掉一根或多根,致其左右两相邻纱间之距离变大。
在平纹织物,则变成两根断纱并列,如同并经。
在斜纹织物,则布纹有间断之现象。
成因:经纱于织造中断掉,自停装置失灵,未将经纱接妥而继续织造。
(11)断纬(Broken Pick)外观:织物中之纬纱断掉,但断开之两端距离甚近,即断掉之长短较小。
此种瑕疵一般多不显著。
成因:1.纬纱于织造中断裂,但瞬间仍继续织入,仅缺一小段距离。
2.纬纱上有严重之粗结与飞花等,于拆除时导致纬纱断裂。
(12)百脚(缺纬)外观:此种瑕疵仅发生在斜纹织造,在每一完全组织同部位之经纱,同时浮于布面,状似一集蜈蜙之多脚。
成因:斜纹布少织入一根纬纱,则交织点减少,部份经纱连续两次浮于纬纱上。
(13)经缩(End Snarl)外观:织物经纱中之一根,有一小段卷缩缠扭在一起而织入布中。
在强捻纱织造之织物则较易发生。
成因:在整经时其中之一根经纱过份松弛,致而有一段发生卷缩。
(14)纬缩(Filling Snarl)外观:织物纬纱有一小段卷缩缠扭在一起而织入布中。
在强捻纱织造之织物则较易发生。
成因:1.纬纱管中或作纬纱用之筒子纱中,已有小段纱卷缩缠扭之现象。
2.纬纱管成形不当,退纱时不畅顺。
3.纬纱张力太小,织口开口不清等。
(15)筘痕(Reed Mark)外观:在胚布之两根经纱间,有较大之间隔,且能看到织入之纬纱,受钢筘筘齿之作用而锯齿形痕迹。
成因:1.钢筘筘齿变形,未能将经纱控制在定位,或者筘齿发生松动。
2.经纱中有一根或间隔之数根,于织造时所受之张力过大。
(16)边撑痕(Temple Mark)外观:在布边内有约2至5公分宽之针刺或受针刺刮拉之痕迹。
严重者致使该部位之纬纱发生波浪形之弯曲。
成因:边撑器选用之针粗细不宜,及边撑器刺环卡死不能回转,或回转不够畅顺。
(17)轧梭外观:在近布边之位置,连续有甚多根之断经,虽经接妥,但在续织后布面仍有许多纱尾,且接合部位织出之布面,稀密异常。
成因:梭子在梭道中被夹持,因之截断甚多之经纱。
多由梭子结构不良,投梭与开口运动受到阻碍所形成。
现使用之无梭织机,则可避免此种瑕疵之发生。
(18)方眼(Reedness)外观:相判之两根经纱挤在一起,左两根与右两根间之空隙则增大,与纬纱形成棋盘状之小方格子。
成因:1.织造时织口启开之角度过大。
2.上下两层之经纱张力相差过大。
3.钢筘之筘齿排列密度不匀。
(19)纱尾(Yarn Tail)外观:在布面上或布边处,残留有伸出布面之纱尾。
成因:因经纱或纬纱断裂,接妥后未将纱尾剪除。
或织机之边剪失灵,未将换纬后之纱尾剪除。