熔模精密铸造过程疑难问题解答
熔模铸造表面和内部缺陷总结经验

熔模铸造表面和内部缺陷总结经验A.浇不到(欠铸):液体金属未充满型腔造成铸件缺肉B 冷隔: 铸件上有未完全融合的缝隙,其交接边缘圆滑原因分析:1.浇注温度和型壳退度低,流动性差2..金属液含气最大,氧化严重以致流动性下降3.铸件壁厚薄4.浇注系统大小和设置位置不合理,直浇道高度不够5.型壳焙烧不充分或型壳透气性差,在铸型中形成气袋6.浇注速度过慢或浇注时金属液断流7.浇注量不足防止办法:1.适当提高浇注温度和型壳温度2.采用正确的熔炼工艺,减少金属液的含气量和非金属杂质3.对于薄壁件应注意浇注系统设计,减少流动阻力和流程,增加直浇道高度4 .焙烧要充分,提高型壳透气性5.适当提高浇注速度,并避免浇注过程断流6 .保证必须的浇注量C 结疤(夹砂):铸件表面上有大小不等,形状不规则的疤片状突起物由于型壳内层局部分层剥离,浇注时金属液充填已剥离的型壳部位,致使铸件表面局部突起1.撒砂时浮砂太多或砂拉中粉尘、细砂多,在砂粒之间产生分层2.涂料粘度大,局部堆积,硬化不透,在涂料之间产生分层3.气温高或涂料与撤砂间隔时间长,撤砂时涂料表面已结成硬皮,涂料与砂粒之间产生分层4.第二层或加固层涂料粘度大、流动性差,涂料不能很好渗入前层细砂间隙,在后层涂料与前层砂粒之间产生分层5.型壳前层残留硬化剂过多,后层涂料不能很好渗入前层间隙。
在后层涂料和前层砂粒之间产生分层6.硬化温度大大高出工作室温度,硬化后骤冷收缩造成型壳局部开裂剥离7.易熔模与面层涂料的润湿性差,在型壳层和易熔模之间形成空隙8.型壳焙烧、浇注时膨胀收缩变化大造成内层开裂剥离9.涂料粘度小,料层过薄或撒砂不足,造成型壳硬化过度,开裂剥离10.面层和加固层耐火材料差异太大,膨胀收缩不一致,便面层分层剥离防止办法:1.撒砂砂粒不可过细且要尽里均匀,粉尘要少,湿度不宜过高,撒砂时要抖去浮砂2.严格控制涂料粘度,涂料要涂均匀,力求减少局部堆积,并应合理选择硬化工艺参数3.缩短涂料与撒砂的间隔时闻4.适当减小第二层或加固层涂料的粘度,采用低粘度的过渡层涂料5.干燥时间要控制适当。
[熔模铸造蜡模表面欠注等缺陷的应对分析]表面缺陷有哪些
![[熔模铸造蜡模表面欠注等缺陷的应对分析]表面缺陷有哪些](https://img.taocdn.com/s3/m/fc58f72e657d27284b73f242336c1eb91a373388.png)
[熔模铸造蜡模表面欠注等缺陷的应对分析]表面缺陷有哪些熔模铸造蜡模表面欠注等缺陷的应对分析1提出问题熔模铸造的蜡基模料种类繁多、配比多样;但是由于石蜡—硬脂酸蜡料具有取材容易、价格便宜,以及流动性好、配制简单、回用性好、两者的互溶性好等一系列优点而得到广泛的应用。
当蜡模存在欠注、冷隔和鼓泡等表面缺陷时,不仅浪费了人工和生产时间,有时会影响到生产进度。
因此,应及时有效地解决蜡模上述的缺陷。
2缺陷概述2.1缺陷种类一般情况下,蜡模表面的缺陷主要有:欠注、冷隔和鼓泡三种。
2.2外部特征欠注:蜡模局部欠注处,呈现圆弧状的表面。
冷隔:在蜡模上,蜡料的交汇处出现圆滑的沟槽。
鼓泡:蜡模的表面上有局部、空心、大小不等的圆弧凸起。
3欠注3.1产生原因3.1.1注蜡时,压型或蜡料的温度太低,蜡料的流动性差,充填能力低。
压型温度和蜡料温度是制模工艺的主要参数之一。
压制蜡模时,由于压型的温度低或蜡料的温度低,降低了蜡料的流动性和充填能力,使蜡料不易快速充填压型的型腔,造成蜡模欠注。
3.1.2注蜡压力小,注射速度太低,或注蜡中断。
注射压力是制模工艺的主要参数之一。
压制蜡模时,由于注射的压力小,注射的速度低,或注蜡中断,降低了蜡料的流动性和充填能力,造成蜡模欠注。
3.1.3注蜡孔的位置不合理,或注蜡孔的截面太小。
注蜡孔位置的设置和注蜡孔截面尺寸是压型设计的重要参数,注蜡孔位置设置不当,使蜡料在压型中的流程过长,不利于蜡料充填压型;注蜡孔的截面太小,注入的蜡料量不够,难以充填满压型的型腔;造成蜡模欠注。
3.1.4压型的排气不良。
压型的排气不良,阻碍了蜡料充填压型,导致蜡模欠注。
3.2防止措施3.2.1注蜡时,适当的提高压型或蜡料的温度。
注蜡温度一般选用45℃~48℃;压型的温度一般选用20℃~25℃,以提高蜡料的流动性和充填能力。
3.2.2适当的提高注蜡压力与速度。
当选用气动压蜡机注射蜡料时,对于硬脂酸蜡料,由于其粘度低、流动性好,而常用注射压力为0.2MPa~0.6MPa(根据蜡模的大小、形状等因素而选择)。
熔模铸造产品缩孔问题的理解与分析

熔模铸造产品缩孔问题的理解与分析王在现代工业领域中,熔模铸造技术以其无与伦比的精度和复杂程度,广泛应用于各类精密零件的制造。
然而,随着生产技术的持续进步,我们面临着一系列挑战。
其中,熔模铸造产品的缩孔及缩松问题显得尤为突出。
这是一个充满复杂性的问题,需要我们深入理解其产生的机理,并找出有效的解决方案。
首先,我们要理解什么是熔模铸造产品的缩孔。
在熔模铸造过程中,由于金属液体在冷却过程中体积收缩,会在铸件内部形成空洞,这就是我们所说的缩孔。
这些缩孔不仅会影响铸件的外观质量,更重要的是,它们会降低铸件的机械性能,甚至可能导致铸件的破裂。
那么,为什么会出现缩孔呢?原因主要有两个方面。
一方面,是由于金属液体在冷却过程中的体积收缩,这是物理规律,无法避免。
另一方面,是由于铸造工艺的问题。
例如,如果铸造速度过快,金属液体在壳模中的冷却时间不足,钢水无法补缩就会导致缩孔的产生。
那么,如何解决这个问题呢?我认为,主要可以从以下几个方面入手:首先,优化铸造工艺。
从产品结构分析,确认产品热节,设置合理的浇口大小以及组树方式,热节-浇口-流道-三者的比例;通过调整铸造速度以及浇注温度,延长金属液体在壳模中的冷却时间,可以有效减少缩孔的产生。
控制液态金属的流动速度和冷却时间,以确保铸件内部结构的稳定性和外观的完整性。
其次,改变以往陈旧观念,尽可能的降低壳模厚度,在产品制壳时应当分析产品在制壳过程中,会不会产生积浆积砂情况,这些问题在制壳过程中要去避免,积浆积砂会导致产品散热不好,出现缩孔及缩松现象,同时壳模厚度减薄利于产品散热,同时也能避免其他铸造问题;此外,通过调整铸造速度以及浇注温度,延长金属液体在壳模中的冷却时间,可以有效减少缩孔的产生。
控制液态金属的流动速度和冷却时间,以确保铸件内部结构的稳定性和外观的完整性。
最后,采用定向凝固技术。
通过改变铸件的凝固方向(如贴保温岩棉、浇注前壳模蘸水、浇注后局部浇水降温等方式),可以使金属液体在凝固过程中产生的缩孔集中在铸件的某一部位,从而减少缩孔对铸件性能的影响。
脱蜡铸造法问题回答

脱蜡铸造法脱蜡铸造法是一种常见的铸造工艺,也被称为“失蜡法”或“熔模法”。
它是通过制作模具,将涂有蜡的模型浸入陶瓷涂料中,然后在高温下将蜡熔掉并排出,最后将金属或合金熔化倒入模具中,待凝固后取出模具得到所需的铸件。
这种铸造方法适用于制造复杂形状的零件和精密零件。
它可以生产出精度高、表面光滑、尺寸准确、内部结构紧密的铸件。
因此,在航空航天、汽车、机械和电子等领域广泛应用。
下面我们详细介绍一下脱蜡铸造法的制作过程:1. 制作模型首先需要根据产品图纸或样品制作出一个精确的模型。
这个模型可以是用3D打印机打印出来的,也可以是手工雕刻或机器加工得到的。
在制作过程中需要注意保证模型表面光滑、尺寸准确,并留有足够厚度以承受后续工艺中可能产生的压力。
2. 涂蜡将模型浸入液态蜡中,待其表面附着一层均匀的蜡涂层后取出。
这一步需要反复进行多次,以使蜡涂层厚度达到所需的要求。
在每次涂蜡前需要等待上一层蜡干燥。
3. 制作模具将涂有蜡的模型放入特制的陶瓷涂料中,等待其干燥并形成一个坚硬的外壳。
然后将整个模具放入高温烤箱中进行烘烤,使内部的蜡全部熔化并排出。
这样就形成了一个空心的模具。
4. 浇铸将金属或合金加热至液态状态,然后倒入已经制作好的空心模具中。
待铸件冷却凝固后,取出模具并清理表面杂质即可得到所需产品。
总之,脱蜡铸造法是一种高精度、高质量、高效率的铸造方法。
它可以制造出各种复杂形状和精密零件,并且可以用于大批量生产。
但是由于其制作过程较为复杂和耗时,成本也相对较高。
因此,在选择铸造方法时需要根据具体情况进行综合考虑。
熔模铸件之常见熔模铸造缺陷的防止
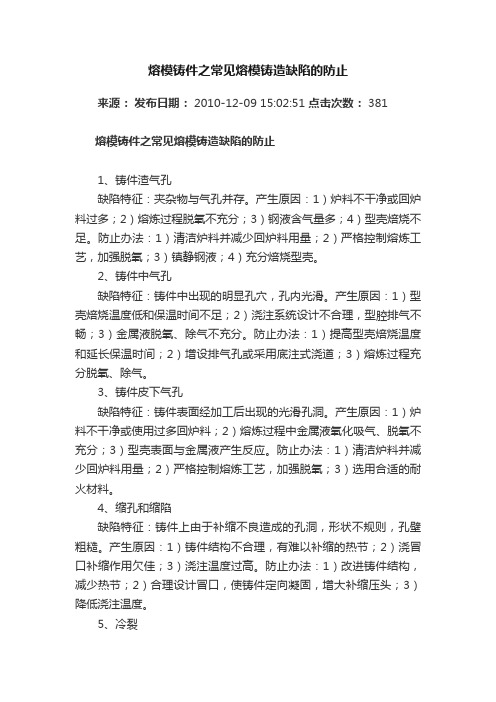
熔模铸件之常见熔模铸造缺陷的防止来源:发布日期: 2010-12-09 15:02:51 点击次数: 381熔模铸件之常见熔模铸造缺陷的防止1、铸件渣气孔缺陷特征:夹杂物与气孔并存。
产生原因:1)炉料不干净或回炉料过多;2)熔炼过程脱氧不充分;3)钢液含气量多;4)型壳焙烧不足。
防止办法:1)清洁炉料并减少回炉料用量;2)严格控制熔炼工艺,加强脱氧;3)镇静钢液;4)充分焙烧型壳。
2、铸件中气孔缺陷特征:铸件中出现的明显孔穴,孔内光滑。
产生原因:1)型壳焙烧温度低和保温时间不足;2)浇注系统设计不合理,型腔排气不畅;3)金属液脱氧、除气不充分。
防止办法:1)提高型壳焙烧温度和延长保温时间;2)增设排气孔或采用底注式浇道;3)熔炼过程充分脱氧、除气。
3、铸件皮下气孔缺陷特征:铸件表面经加工后出现的光滑孔洞。
产生原因:1)炉料不干净或使用过多回炉料;2)熔炼过程中金属液氧化吸气、脱氧不充分;3)型壳表面与金属液产生反应。
防止办法:1)清洁炉料并减少回炉料用量;2)严格控制熔炼工艺,加强脱氧;3)选用合适的耐火材料。
4、缩孔和缩陷缺陷特征:铸件上由于补缩不良造成的孔洞,形状不规则,孔壁粗糙。
产生原因:1)铸件结构不合理,有难以补缩的热节;2)浇冒口补缩作用欠佳;3)浇注温度过高。
防止办法:1)改进铸件结构,减少热节;2)合理设计冒口,使铸件定向凝固,增大补缩压头;3)降低浇注温度。
5、冷裂缺陷特征:裂纹大多穿过晶粒,表面光亮。
产生原因:1)铸件结构不合理;2)浇注系统设计不合理;3)铸件在搬运和清砂过程中受撞击;4)铸件在矫正时操作不当或未退火。
防止办法:1)改进铸件结构和浇注系统设计,减小收缩应力;2)避免撞击和抛甩铸件;3)矫正前进行退火,并改进矫正操作;4)减少型壳层数,并改善退让性;5)降低铸件的冷却速度,例如型壳可改用填砂浇注。
6、热裂缺陷特征:裂纹沿晶界生长,表面有氧化颜色。
产生原因:1)铸型温度低,冷却速度过快;2)型壳退让性差,阻碍收缩;3)铸件结构不合理,壁厚相差悬殊,过渡突变,应力过大;4)浇注补缩系统设计不合理,造成铸件局部过热或收缩受阻。
特种铸造关键技术问题对策2005-熔模铸造关键技术问题对策
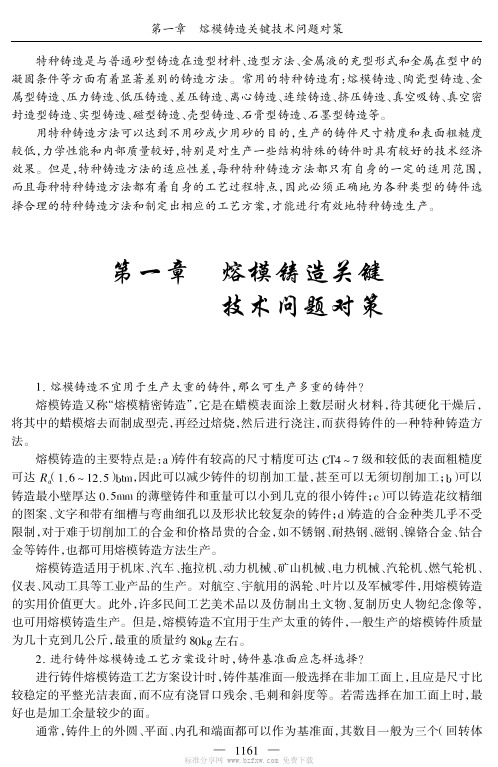
第一章
熔模铸造关键 技术问题对策
那么可生产多重的铸件? !" 熔模铸造不宜用于生产太重的铸件, 熔模铸造又称 “熔模精密铸造” , 它是在蜡模表面涂上数层耐火材料, 待其硬化干燥后, 将其中的蜡模熔去而制成型壳, 再经过焙烧, 然后进行浇注, 而获得铸件的一种特种铸造方 法。 熔模铸造的主要特点是: 铸件有较高的尺寸精度可达 $%& ’ ( 级和较低的表面粗糙度 #) 可达 !( 因此可以减少铸件的切削加工量, 甚至可以无须切削加工; 可以 ,-., ,) # !") ’ !*"+) 铸造最小壁厚达 /"+.. 的薄壁铸件和重量可以小到几克的很小铸件; 可以铸造花纹精细 0) 的图案、 文字和带有细槽与弯曲细孔以及形状比较复杂的铸件; 铸造的合金种类几乎不受 1) 限制, 对于难于切削加工的合金和价格昂贵的合金, 如不锈钢、 耐热钢、 磁钢、 镍铬合金、 钴合 金等铸件, 也都可用熔模铸造方法生产。 熔模铸造适用于机床、 汽车、 拖拉机、 动力机械、 矿山机械、 电力机械、 汽轮机、 燃气轮机、 仪表、 风动工具等工业产品的生产。对航空、 宇航用的涡轮、 叶片以及军械零件, 用熔模铸造 的实用价值更大。此外, 许多民间工艺美术品以及仿制出土文物、 复制历史人物纪念像等, 也可用熔模铸造生产。但是, 熔模铸造不宜用于生产太重的铸件, 一般生产的熔模铸件质量 为几十克到几公斤, 最重的质量约 2/34 左右。 铸件基准面应怎样选择? *" 进行铸件熔模铸造工艺方案设计时, 进行铸件熔模铸造工艺方案设计时, 铸件基准面一般选择在非加工面上, 且应是尺寸比 较稳定的平整光洁表面, 而不应有浇冒口残余、 毛刺和斜度等。若需选择在加工面上时, 最 好也是加工余量较少的面。 通常, 铸件上的外圆、 平面、 内孔和端面都可以作为基准面, 其数目一般为三个 (回转体
【干货】精密铸造工艺常见问题知识汇总~
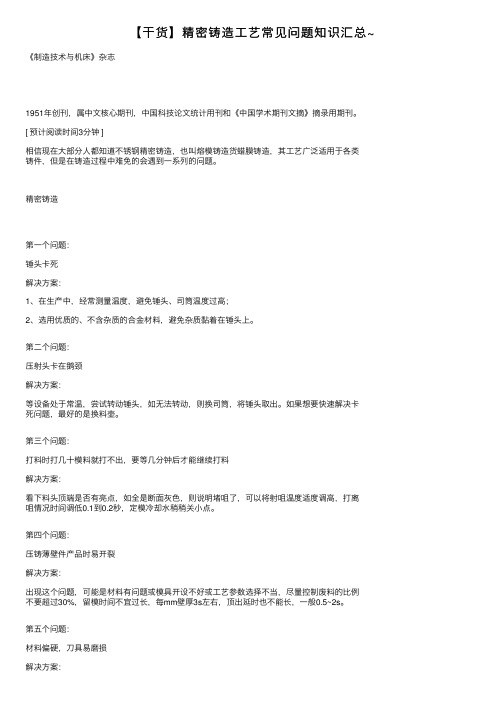
【⼲货】精密铸造⼯艺常见问题知识汇总~《制造技术与机床》杂志1951年创刊,属中⽂核⼼期刊,中国科技论⽂统计⽤刊和《中国学术期刊⽂摘》摘录⽤期刊。
[ 预计阅读时间3分钟 ]相信现在⼤部分⼈都知道不锈钢精密铸造,也叫熔模铸造货蜡膜铸造,其⼯艺⼴泛适⽤于各类铸件,但是在铸造过程中难免的会遇到⼀系列的问题。
精密铸造第⼀个问题:锤头卡死解决⽅案:1、在⽣产中,经常测量温度,避免锤头、司筒温度过⾼;2、选⽤优质的、不含杂质的合⾦材料,避免杂质黏着在锤头上。
第⼆个问题:压射头卡在鹅颈解决⽅案:等设备处于常温,尝试转动锤头,如⽆法转动,则换司筒,将锤头取出。
如果想要快速解决卡死问题,最好的是换料壶。
第三个问题:打料时打⼏⼗模料就打不出,要等⼏分钟后才能继续打料解决⽅案:看下料头顶端是否有亮点,如全是断⾯灰⾊,则说明堵咀了,可以将射咀温度适度调⾼,打离咀情况时间调低0.1到0.2秒,定模冷却⽔稍稍关⼩点。
第四个问题:压铸薄壁件产品时易开裂解决⽅案:出现这个问题,可能是材料有问题或模具开设不好或⼯艺参数选择不当,尽量控制废料的⽐例不要超过30%,留模时间不宜过长,每mm壁厚3s左右,顶出延时也不能长,⼀般0.5~2s。
第五个问题:材料偏硬,⼑具易磨损解决⽅案:⽤原始材料配⽐,不⽤再⽣材料,采⽤专门为硬质合⾦⽽⽣产的宝⽯⼑⽚。
第六个问题:铝压铸件在磨光时有⿊斑解决⽅案:减少喷涂剂的浓度,改⽤别的喷涂剂;或加长喷涂后的吹风时间。
第七个问题:压铸过程中⾦属外溅解决⽅案:重新安装模具;加⼤锁模⼒,调整压铸机,使动、定模安装板相互保持平⾏;在动模上增加⽀板,增加套板的刚度。
第⼋个问题:压铸件阳极氧化后有花纹产⽣解决⽅案:喷涂、压射油散步不均、⾼速切换位置不当或氧化槽铜离⼦含量过⾼会造成花纹问题,因此可以让喷涂、压射油散布均匀,不聚齐在局部,或设置好⾼速切换位置,减少⽋铸现象。
第九个问题:压铸模具粘料解决⽅案:1、检查模温是否正常,适度降低合⾦液浇注温度和模具温度;2、检查脱模剂配⽐是否异常,尝试更换脱模剂;3、调试喷涂位置表⾯进⾏抛光,对已氮化过的模具,慎重抛光,防⽌破坏掉表⾯的氮化层,形成越抛越粘的情况;4、改进浇注系统设计结构,避免合⾦液持续冲刷型腔壁或型芯;5、修改模具冷却系统;6、调整压铸⼯艺参数,适当降低压射速度,缩短⼆速⾏程。
材料成型工艺学 思考题 第一章 熔模铸造

第一章熔模铸造1.熔模铸造的特点是什么?简述熔模铸造的工艺过程。
优点:(1)精度高-尺寸精度、表面光滑度(2)形状无限制。
适合于铸造某些结构、形状复杂的铸件。
(因无需拔模,无分型面)(3)合金不受限制(一般适用于贵金属)缺点(1)铸件性能不好因为铸态且为热浇(保证轮廓清晰)晶粒粗大,机械性能不好,(2)工艺复杂成本高。
(相对铸造高,而综合成本不高,相当于10倍的砂型铸造成本)(3)铸件尺寸受限制太大解决不了蜡蠕变和收缩变形问题(4)批量受限制-大批量。
大批量生产成本降低。
2.熔模铸造中的“模”用什么材料制成?通常使用的模料分为哪几类?各有何基本特点?蜡基模料: 石蜡50% + 硬脂酸50%特点:强度高、刚性好、熔点适中,但流动性、润湿性差,膨胀系数大。
松香基模料:松香60% + 川蜡30% + 地蜡5% + 聚乙烯5%松香75% + 川蜡15% — + 地蜡5% + 聚乙烯5%中高熔点模料。
主要用来生产要求高的熔模铸件,3.模料配制需要遵循哪些原则?蜡基模料配制有几种方式?根据各组分的互溶性来确定加料顺序严格控制温度上限和高温停留时间及合适的熔化装置。
蜡基配置方式:蒸汽加热、热水槽加热a 旋转浆叶搅拌法b活塞搅拌法4.回收的蜡基模料性能会发生哪些变化?造成回收模料性能变坏的原因是什么?性能会变坏:脆性增大,灰尘增多,流动性下降,收缩率增大,颜色由白变褐,这些主要与模料中硬脂酸变质有关,原因:(1)蜡基模料中硬脂酸变质(发生皂化反应)(2)砂和涂料的污染(3)熔失熔模时过热,石蜡烧坏、氧化变质5.哪几种处理方法可以使旧的蜡基模料的性能得到一定程度的恢复?(1)盐酸(硫酸)处理法(2)活性白土处理法(3)电解法6.熔模铸造的型壳是如何制造的(由哪三个基本步骤组成)?熔模铸造制造一般铸件时型壳需要涂挂几层?涂覆涂料→撒砂→干燥硬化重复5-7次7.熔模铸造制造型壳时可以采用哪几种粘结剂,各种粘结剂有何特点?它们的硬化机理是什么,工业上分别采用什么方法硬化?1 硅酸乙酯水解液特点:强度高,高温稳定性好,价格贵硅酸乙酯是优质黏结剂,所以型壳性能好:①涂挂性好(醇基)②涂料粉液比高(黏度小)涂层致密,铸件光洁③型壳室温,高温强度高,抗变形能力强,尺寸稳定④烘干(氨催化)生产周期短原理:第一阶段:硅酸乙酯→硅酸乙酯水解液第二阶段:干燥硬化方法:一次水解法:水解时温度不得超过40-50度综合水解法:所得涂料分散度高,均匀性好。
熔模铸造十大经常被问到的问题
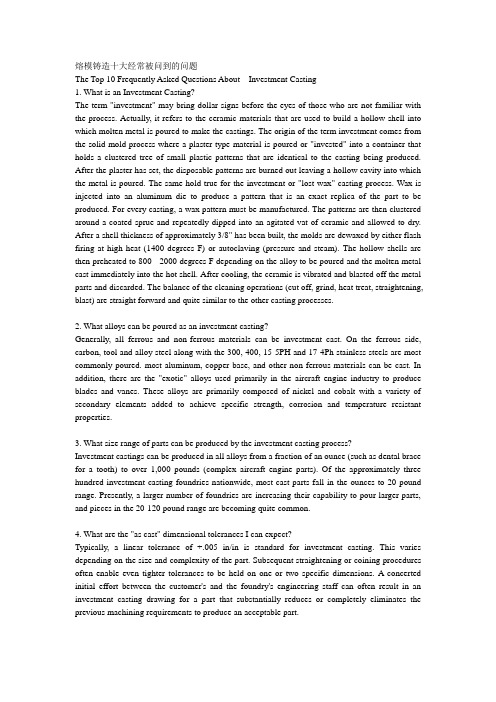
熔模铸造十大经常被问到的问题The Top 10 Frequently Asked Questions About Investment Casting1. What is an Investment Casting?The term "investment" may bring dollar signs before the eyes of those who are not familiar with the process. Actually, it refers to the ceramic materials that are used to build a hollow shell into which molten metal is poured to make the castings. The origin of the term investment comes from the solid mold process where a plaster type material is poured or "invested" into a container that holds a clustered tree of small plastic patterns that are identical to the casting being produced. After the plaster has set, the disposable patterns are burned out leaving a hollow cavity into which the metal is poured. The same hold true for the investment or "lost wax" casting process. Wax is injected into an aluminum die to produce a pattern that is an exact replica of the part to be produced. For every casting, a wax pattern must be manufactured. The patterns are then clustered around a coated sprue and repeatedly dipped into an agitated vat of ceramic and allowed to dry. After a shell thickness of approximately 3/8" has been built, the molds are dewaxed by either flash firing at high heat (1400 degrees F) or autoclaving (pressure and steam). The hollow shells are then preheated to 800 - 2000 degrees F depending on the alloy to be poured and the molten metal cast immediately into the hot shell. After cooling, the ceramic is vibrated and blasted off the metal parts and discarded. The balance of the cleaning operations (cut off, grind, heat treat, straightening, blast) are straight forward and quite similar to the other casting processes.2. What alloys can be poured as an investment casting?Generally, all ferrous and non-ferrous materials can be investment cast. On the ferrous side, carbon, tool and alloy steel along with the 300, 400, 15-5PH and 17-4Ph stainless steels are most commonly poured. most aluminum, copper base, and other non-ferrous materials can be cast. In addition, there are the "exotic" alloys used primarily in the aircraft engine industry to produce blades and vanes. These alloys are primarily composed of nickel and cobalt with a variety of secondary elements added to achieve specific strength, corrosion and temperature resistant properties.3. What size range of parts can be produced by the investment casting process?Investment castings can be produced in all alloys from a fraction of an ounce (such as dental brace for a tooth) to over 1,000 pounds (complex aircraft engine parts). Of the approximately three hundred investment casting foundries nationwide, most cast parts fall in the ounces to 20 pound range. Presently, a larger number of foundries are increasing their capability to pour larger parts, and pieces in the 20-120 pound range are becoming quite common.4. What are the "as cast" dimensional tolerances I can expect?Typically, a linear tolerance of +.005 in/in is standard for investment casting. This varies depending on the size and complexity of the part. Subsequent straightening or coining procedures often enable even tighter tolerances to be held on one or two specific dimensions. A concerted initial effort between the customer's and the foundry's engineering staff can often result in an investment casting drawing for a part that substantially reduces or completely eliminates the previous machining requirements to produce an acceptable part.5. What type of surface finish can I expect from an investment casting?Because the ceramic shell is built around smooth patterns produced by injecting wax into a polished aluminum die, the resultant casting finish is excellent. A 125 micro finish is standard and even finer finishes (63 or 32) are not uncommon on aircraft engine castings. Each foundry has its own standards for surface blemishes (positives, negatives). These are discussed and agreed upon with the customer based on the function and cosmetic requirements of the part prior to release of the tooling order.6. Aren't investment castings expensive? And if so, how can they save me money?While investment castings are generally more expensive than forged parts or those produced by other casting methods, they make up for higher cost through the reduction of machining achieved through the near net shape tight tolerances that can be held as cast. Many parts that require milling, turning, drilling, and grinding to finish can be investment cast with only .020-.030 finish stock. Again, it is imperative for the engineering staff of the foundry and customer to get together and discuss what can or cannot be cast to determine final finishing requirements and the potential cost savings.7. How many pieces do I need to make buying an investment casting practical?Not as many as you think! Tooling amortization is a key factor in determining whether or not an investment casting is practical. The machine tool industry will often specify an investment casting on 25 pieces of a new part. This is bought once and after that only one or two pieces at a time for replacements. Conversely, quantities exceeding 100,000 parts per month are produced by some foundries largely for automotive use. The bulk of investment castings produced fall in the 100 - 10,000 piece annual range.8. What type of tooling or pattern equipment is necessary?Typically, a split cavity aluminum die is manufactured that is the "female" mold from which the "male" wax patterns are produced. Depending on the complexity of the casting, carious combinations of aluminum, ceramic or soluble cores may be employed to yield the desired configuration. Most tooling for investment castings falls in the $1,000 - $10,000 category.9. What about the integrity of an investment casting?Will I have problems with porosity and shrinkage that are usually non-existent in bar stock or forgings? Investment castings are used for many critical applications that require the parts to be x-rayed and meet definite soundness criteria. The integrity of an investment casting can be far superior to parts produced by other methods.10. What are the lead times I can expect when ordering an investment casting?Nothing varies more than lead times depending on part complexity and foundry capacity. Generally 6-12 weeks is typical for tooling and sample casting and 6-12 weeks for production.。
熔模铸造常见的缺陷及防止措施

(2)用水玻璃做黏结剂时,型壳残余盐类与金属液产生反应形成麻坑;
(3)金属液脱氧不良或出钢时渣料未扒干净
(1)用硅酸乙酯做黏结剂时,适当增加水的加入量和增大涂料工作室的相对湿度,尽量减少残余不完全水解物;
(1)铸件冷却过程中收缩受阻,产生热应力和相变应力超过在弹性状态下铸件材料的强度而断裂;
(2)在清壳、切割浇冒口或矫正过程中,有残余应力的铸件受到外力作用而断裂
(1)在易产生冷裂部位增设加强肋,提高型壳的可退让性,减少收缩受阻和铸造应力;
(2)在后处理的工序中应避免铸件受剧烈撞击
气孔:铸件上有明显的或暗的内表面光滑孔眼
(1)型壳透气性差,浇注时型腔内气体来不及排出;
(2)型壳焙烧不充分,未充分排除模料残余物及制壳材料中的发气物质;
(3)金属液气体含量过高,脱氧不良;
(4)浇注系统设置不合理,浇注时卷入气体
(1)改善型壳透气性,必要时可增设排气孔;
(2)充分焙烧型壳;
(3)改善脱氧方法;
(4)改进浇注系统
麻点:在铸件表面局部有密集圆点状凹坑
熔模铸造常见的缺陷及防止措施
名称及特征
产生原因
防止措施
欠铸和冷隔:欠铸常在铸件的薄壁或远离内浇道处局部缺肉,其边缘呈圆弧状;冷隔是两股金属液未完全融合,有明显接缝
(1)金属液浇注温度和铸型温度低;
(2)浇注速度慢或浇道设置不合理,金属流程太长;
(3)铸件壁厚太薄,金属液铸型温度;
(1)改进铸件结构,减少热节;
(2)合理设置冒口,或外加能用加工方法去除的补缩肋,增加压力头,使铸件能在一定压力头作用下得到顺序凝固;
熔模精密铸造实践报告总结(2篇)

第1篇一、引言熔模精密铸造是一种先进的铸造技术,具有精度高、表面光洁、机械性能好等优点,广泛应用于航空航天、汽车、医疗器械等领域。
本报告主要对熔模精密铸造的实践过程进行总结,分析存在的问题及改进措施,以期为今后类似项目的实施提供参考。
二、熔模精密铸造实践过程1. 原材料准备熔模精密铸造的原材料主要包括蜡、石英砂、粘土、水、耐火材料等。
在实践过程中,首先要对原材料进行筛选和加工,确保其质量符合要求。
2. 熔模制作熔模制作是熔模精密铸造的关键环节。
具体步骤如下:(1)蜡模制作:根据产品图纸,采用手工或机器加工方法制作蜡模,要求蜡模表面光滑、尺寸准确。
(2)蜡模组合:将多个蜡模组合成一个整体,以便后续进行熔模铸造。
(3)熔模组装:将蜡模组合体放入砂箱中,进行熔模组装,确保砂箱内的蜡模组合体与砂箱内壁之间形成良好的密封。
3. 熔模铸造熔模铸造主要包括以下步骤:(1)预热:将砂箱内的熔模预热至一定温度,以降低蜡模熔化时的收缩应力。
(2)熔化蜡模:将预热后的熔模放入熔化炉中,熔化蜡模。
(3)浇注:将熔化的金属液浇注到砂箱内的蜡模中,使金属液填充蜡模空腔。
(4)冷却凝固:待金属液凝固后,取出砂箱,去除砂模,得到铸件。
4. 铸件后处理铸件后处理主要包括以下步骤:(1)打磨:对铸件表面进行打磨,去除浇注系统和浇注冒口等。
(2)热处理:根据铸件材料性能要求,进行相应的热处理。
(3)检验:对铸件进行尺寸、形状、表面质量、机械性能等方面的检验。
三、存在问题及改进措施1. 问题一:蜡模精度不足原因分析:蜡模制作过程中,手工加工误差较大,导致蜡模精度不足。
改进措施:采用高精度加工设备,如数控机床等,提高蜡模加工精度。
2. 问题二:熔模铸造过程中出现缩孔、裂纹等缺陷原因分析:熔模铸造过程中,金属液冷却速度过快,导致缩孔、裂纹等缺陷。
改进措施:优化熔模设计,采用合理的浇注系统,降低冷却速度,提高铸件质量。
3. 问题三:铸件表面质量差原因分析:铸件表面质量受多种因素影响,如熔模表面质量、浇注温度、冷却速度等。
铸造时常见的问题及解决办法

铸造时常见的问题及解决办法砂洞一般分为气化砂洞和收缩砂洞;气化砂洞呈圆球形,很微细到铅笔头一样大都有。
收缩砂洞呈角形,大小不一内呈结晶状表面,多在铸件的厚身部份发现。
气化砂洞 :1) 调高失腊时间。
有需要加长在最高温度逗留的时间以便去除炭化物。
2) 检查焗炉通风喉,若用火烧焗炉时,检查火焰强度。
3) 检查旧金表面有否积存石羔粉。
4) 若用火枪熔金,检查是否混入太多氧气。
5) 核查倒模温度是否太高或测温器显示不正确温度。
6) 覆用时用太多旧金。
7) 核对石羔温度有否过高。
收缩砂洞 :1) 检查放置水口位是否正确。
水口必须放在铸件最厚的位置。
2) 检查水口厚度是否配合铸件的体形及重量。
切记水口要呈喇叭形进入铸件,不能有太急转弯位。
3) 核对石羔温度是否太高4) 有些铸件在设计上要多放水口令金属易于进入。
有裂痕1) 核对淬水时间;过快会造成裂缝。
2) 核对倒模温度;含硅脱氧剂的合金需较高温度。
3) 核对石羔温度;在薄件发现的裂缝可能使用太低石羔温度。
4) 不要用盐酸去清除石羔粉,因会使低成色铸件爆裂。
5) 不正确或不足够地放置水口,这类裂痕多发现在水口与铸件交接位置。
6) 在厚身与薄身的交接位置会发现薄身位置有裂缝,这因为不同程度凝固速度使然。
这时候要多加水口在厚身部份。
7) 用过量旧金会产生裂痕。
8) 用10K或14K补口去铸造18K会令铸件破裂或脆弱。
不完全填满1) 倒模温度过低。
2) 石羔温度过低。
3) 抽真空铸造力度不够,要检查有关设备。
4) 离心机所使用转速力度不够。
5) 不正确放置水口位置。
6) 不完成失腊,令石羔内空气膨涨。
令铸件变形表面粗糙1) 倒模温度过高。
2) 石羔温度过高。
3) 手板粗糙。
4) 腊模粗糙,检查胶模是否残留太多脱模剂。
5) 检查石羔浆是否混合太多水。
6) 核对失腊或蒸腊前石羔等待时间会否不足够。
7) 蒸腊时间可能过长。
8) 石羔盅加热太快 (将石羔盅放入高温的焗炉内)有鳍状物1) 石羔粉与水比例不正确。
铸造可能遇到的问题和解决方案

铸造可能遇到的问题和解决方案标题,铸造中常见问题及解决方案。
在铸造过程中,常常会遇到一些问题,这些问题可能会影响产品的质量和生产效率。
以下是一些铸造中常见的问题以及可能的解决方案。
1. 气孔和气泡。
气孔和气泡是铸造中常见的质量问题,可能会导致产品强度不足或者外观质量不佳。
这可能是由于熔融金属中的气体未能完全排除所致。
解决方案,采取适当的浇注系统设计,确保熔融金属能够充分充填模具,同时使用合适的除气剂和浇口设计来减少气孔和气泡的产生。
2. 热裂纹。
热裂纹是由于金属在冷却过程中产生的应力超过了其承受能力
而引起的。
这可能会导致产品在使用过程中出现裂纹。
解决方案,通过合理的冷却控制和合适的金属合金选择,可以减少热裂纹的发生。
此外,预热模具和采用合适的退火工艺也可以有效减少热裂纹的产生。
3. 金属收缩。
金属在冷却过程中会收缩,如果不加以控制,可能会导致产品尺寸不准确甚至变形。
解决方案,通过合理的浇注系统设计和冷却控制,可以减少金属收缩对产品质量的影响。
此外,采用合适的模具设计和金属合金选择也可以减少金属收缩带来的问题。
总之,铸造过程中可能会遇到各种质量问题,但通过合理的工艺控制和技术手段,这些问题是可以得到解决的。
只有不断改进工艺和技术,才能确保铸造产品的质量和稳定性。
熔模精密铸造过程疑难问题解答

熔模精密铸造过程疑难问题解答熔模精密铸造过程疑难问题解答前言三百六十行,行行出人才。
各行各业都有自己的特长。
各从业人员必须熟练地掌握本行业、本岗位的职业技能,具备一定的包括职业技能在内的职业素质,才能胜任工作,把工作做好,为本行业做出应有的贡献,实现自己的人生价值。
熔模铸造业是技术密集型的行业。
本行业对其职工职业素质的要求比较高。
在科学技术迅速发展的今天,更是这样。
精铸业的职工队伍中,大部分是技术员工。
他们是企业的主力军,是振兴和发展本企业的技术力量。
技术人员素质如何,直接关系到本企业的生存和发展。
在市场经济条件下,企业之间的竞争,是质量之竞争;价格之竞争;也是技术之竞争;归根结底是人才的竞争。
优秀的技术员工是企业各类人才中重要的组成部分。
企业必须有这样一支高素质的技术工人队伍,有这样一批技术过硬、技艺精湛的能工巧匠,才能保证产品质量,提高生产效率,降低物料消耗,使企业获得经济效益;才能支持企业不断生产出高难度的产品,去发掘市场、占领市场;才能在激烈的市场竞争中立于不败之地!由于本人水平有限,加之时间仓促,难免存在不足和错误,诚恳希望专家,工程师和同仁批评指正。
吴光来第一章熔模铸件工艺设计与模具设计§1、熔模铸件工艺设计1.1、熔模铸件的尺寸精度受到哪些因素的影响?答:铸件尺寸精度受铸件结构、材质、制模、制壳、焙烧、浇注等多种因素的影响。
1)、铸件结构的影响:(1)、铸件壁厚,收缩率大;铸件壁薄,收缩率小;(2)、自由收缩率大,阻碍收缩率小。
2)、材质的影响:(1)、材料中含碳量越高,线收缩率越小,含碳量越低,线收缩率越大;(2)常见材质的铸造收缩率如下:铸造收缩率K=(LM-LJ)/LJ×100%LM—型腔尺寸;LJ—铸件尺寸K受以下因素的影响:蜡模K1、铸件结构K2、合金种类K3、浇注温度K4。
合金种类收缩率自由收缩受阻收缩铸铁件 0.8% 0.7%碳钢及低合金钢 1.6-2.0% 1.3-1.7%不锈钢 2.0-2.3% 1.7-2.0%3)、制模对铸件线收缩率的影响:(1)蜡(模)料的线收缩率约为0.9-1.1%;(2)蜡模径向(受阻)收缩率仅为长度方向(自由)收缩率的30-40%,射蜡温度对自由收缩率的影响远远大于对受阻收缩率的影响。
熔模铸造的铸件缺陷分析与防止
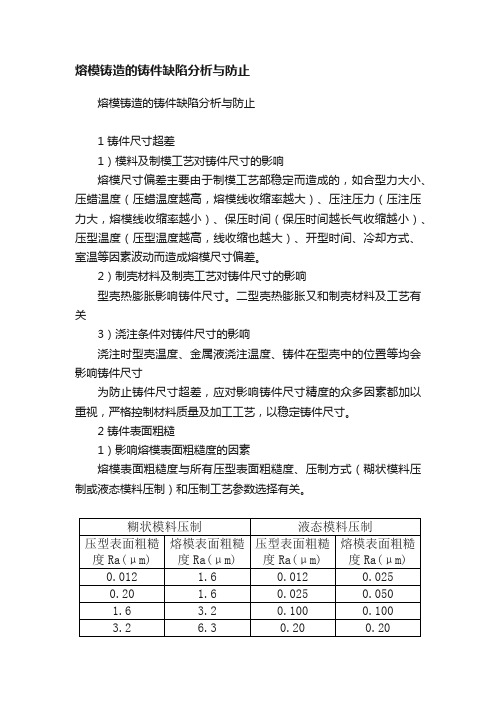
熔模铸造的铸件缺陷分析与防止熔模铸造的铸件缺陷分析与防止1 铸件尺寸超差1)模料及制模工艺对铸件尺寸的影响熔模尺寸偏差主要由于制模工艺部稳定而造成的,如合型力大小、压蜡温度(压蜡温度越高,熔模线收缩率越大)、压注压力(压注压力大,熔模线收缩率越小)、保压时间(保压时间越长气收缩越小)、压型温度(压型温度越高,线收缩也越大)、开型时间、冷却方式、室温等因素波动而造成熔模尺寸偏差。
2)制壳材料及制壳工艺对铸件尺寸的影响型壳热膨胀影响铸件尺寸。
二型壳热膨胀又和制壳材料及工艺有关3)浇注条件对铸件尺寸的影响浇注时型壳温度、金属液浇注温度、铸件在型壳中的位置等均会影响铸件尺寸为防止铸件尺寸超差,应对影响铸件尺寸精度的众多因素都加以重视,严格控制材料质量及加工工艺,以稳定铸件尺寸。
2 铸件表面粗糙1)影响熔模表面粗糙度的因素熔模表面粗糙度与所有压型表面粗糙度、压制方式(糊状模料压制或液态模料压制)和压制工艺参数选择有关。
(1)压型表面粗糙度的影响(2)压制方法的影响(3)压制工艺参数的影响2)影响型壳表面粗糙度的因素(1)涂料不能很好地与熔模润湿(2)面层涂料粉液比嵌、型壳表面不致密在熔模表面粗糙度合格的条件下,型壳表面粗糙度将成为影响铸件粗糙度的重要一环要型壳表面粗糙度嵌,首先应保证面层涂料能很好的润湿熔模,复印熔模;其次,面层要致密,涂层粉液比要足够高(采用双峰级配粉)配粉是按照一定要求配置的粒度分布合理的粉。
该种粉粒度有粗、有细,分布分散,平均粒经适中,能使涂料在高粉液比条件下仍具有适宜的粘度和良好的流动性。
3)影响金属液精确复型的因素(1)型壳温度对金属液复型的因素(2)浇注温度对金属液复型的因素金属液复印型壳工作表面细节的能力,即充型能力;在此简称为“复型“能力。
为使金属液能精确复型,就必须有足够高的型壳温度和金属液温度,并保证金属液有足够的压力头。
提高型壳温度对改善金属液流动能力、复型能力均有良好效果,故型壳温度是予以重视的因素。
熔模铸件缺陷分析及对策

影响型壳表面粗糙度的因素主要有面层涂料对熔模的
湿润性,即复印熔模的性能;其次是涂料的粉液比要足 够高,使制得的面层致密;第三是面层的干燥条件。
铸件表面粗糙
⑴ 涂料的湿润性 为使涂料能很好的湿润熔模,应注意以下几个方面: ① 对熔模表面应清洗干净,去除油等物质。 ② 对水基粘结剂水玻璃、硅溶胶的涂料加入适量的润 湿剂(表面活性剂)。
③ 面层涂料的回性
面层涂料配制好后,不能马上使用,要经过12小时
左右的回性使粘结剂与耐火粉料充分湿润后再用。
铸件表面粗糙
⑵ 面层涂料粉液比对型壳致密性的影响
① 硅溶胶和硅酸乙酯水解液粘结剂本身粘度小,故
配制的面层涂料粉液比较高。
② 水玻璃粘结剂因自身粘度高,故水玻璃涂料粉液 比很低,但也可以通过降低水玻璃密度:1.26~ 1.28g/cm3,模数M3.0~3.2及采用级配石英粉来 提高粉液比。
铸件表面粗糙
⑶ 要得到高质量的熔模表面质量,应注意以下几 个方面: ① 讲究压型制作质量。
② 根据熔模结构,大小,形状的不同,合理选择压
制工艺参数。
③ 注蜡道尺寸应根据熔模大小合理设计。
铸件表面粗糙
2、影响型壳表面粗糙度的因素 在熔模表面粗糙度合格的条件下型壳表面粗糙度将 成为影响铸件表面粗糙度的另一个重要因素。
铸 件 质 量:
工程质量 (广义的)
铸件质量标准:
国标 (GB)
国际标准 (ISO)
行业标准
企业内控标准
前言
广义的铸件(质量)缺陷指铸件质量特性没有达到等 级标准,铸造厂质量管理差, 产品质量得不到有效 保证。(工程质量 问题)
狭义的铸件(质量)缺陷是铸件可检测出的:如尺寸和 重量超差、材质不符合验 收技术条件……。(产品 质量问题)
熔模铸造常见缺陷及防止方法
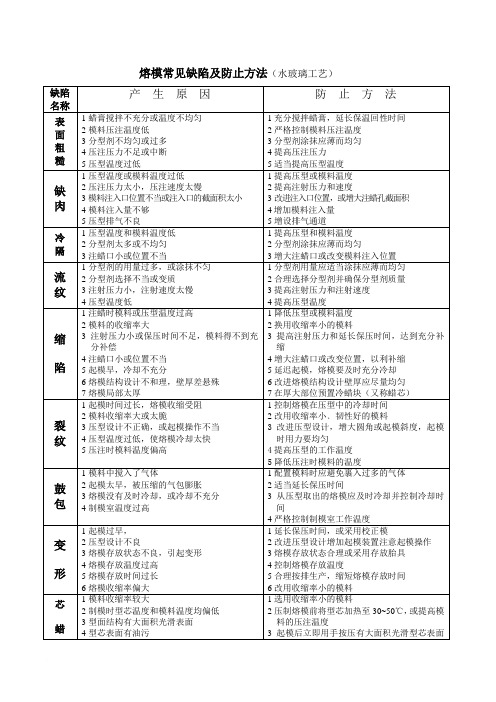
2水玻璃密度不宜过大
3涂料粘度不要过高
4氯化铝硬化剂的PH值要适当,硬化时间要充足
5脱蜡水应保持酸性
熔模铸件常见缺陷及防止方法
名称
缺陷特征
产生原因
防止方法
气孔
铸件中出现明显孔穴,孔内光滑
1型壳焙烧温度低和保温时间不足
2浇注系统设计不和理,型腔排气不畅
3金属液脱氧出气不充分
2在铸型的周围人为的造成还原性气氛
3合理选用耐火材料和粘结剂
4充分焙烧型壳
5严格制壳工艺,保证硬化,风干充分
夹杂物
铸件上存在与基体成分不同的物质,包括涂料层,砂粒,硅酸盐,皂化物
1型壳面层涂料干燥,硬化不良
2涂料层结合不牢,在制壳和焙烧过程中面层涂料剥落
3型壳强度低,承受不了钢液的冲击而损坏
4型壳脱蜡后放置时间短,水分多或焙烧时升温快而损坏
1提高型壳焙烧温度和延长保温时间
2增设排气孔或采用底注式浇道
3熔炼过程充分脱氧
皮下气孔
铸件经加工后出现的光滑孔洞
1炉料不干净或使用过多的回炉料
2熔炼过程中金属液氧化吸气,脱氧不充分
3型壳表面与金属液发生反应
1清洁炉料并减少回炉料用量
2严格控制熔炼工艺,加强脱氧
3选用合适的耐火材料
渣气孔
夹杂物与气孔并存
1蜡模表面缩陷
2型壳分层,型壳面层向内鼓胀
1用表面无缩陷的蜡模
2严格制壳工艺,避免涂料堆积,保证硬化,风干充分
3仔细清理浮砂,降低过渡层涂料粘度
铸瘤
铸件表面凸起的金属小瘤
1涂料中的气泡未被排除
2涂料时蜡模拐角或沟槽处有气泡夹在涂料中
熔模铸件表面麻点缺陷成因分析及对策

熔模铸件表面麻点缺陷成因分析及对策熔模精密铸造(又称熔模铸造)是一种近净形成形工艺,其铸件精密、复杂,接近于零件最后的形状,可不加工直接使用或经很少加工后使用[ 1 ] 。
但由于其工序较长,涉及的原材料很多,经常有许多原因致使铸件的表面出现问题,影响铸件的外观质量,表面麻点就是常见的一种。
1、缺陷表现我厂生产实践中,有时发现成批铸件表面出现麻点(如图1) ,呈规则的半球形小坑,凹坑直径约0. 3 mm~0. 8 mm,深约0. 3 mm~0. 5 mm,未清理前图1表面麻点缺陷凹坑内有黑色熔渣物质。
(一般气孔内壁光滑,且外形不规则) ,麻点呈密集状分布,大件及大平面铸件尤为严重。
该缺陷虽不影响铸件使用性能,但无法修整,严重影响了铸件的表面质量,导致铸件成批报废,不能按时完成订单,延误交期。
2、缺陷的成因及分析经光谱分析,缺陷处金属中硅含量增加,而含锰量极少。
熔渣的金相分析表明,熔渣含有硅酸铁、硅酸锰及硅酸钴等化合物。
X射线衍射证明黑色麻点是由磁铁矿Fe3O4 和铁铬尖晶石FeO·Cr2O3 组成。
对缺陷处金属成分和熔渣成分进行分析后认为:麻点是金属液中氧化物与型壳材料中氧化物发生化学反应形成的。
生产实践中发现导致该缺陷的原因主要有以下几个方面。
2. 1 面层型壳材料高合金钢铸件大都采用锆砂作为型壳面层耐火材料,锆砂又称硅酸锆或锆英石,分子式为ZrO2 · SiO2(或ZrSiO4 ) ,理论组成( 质量分数)为ZrO2 67.23 %,SiO2 32. 77 %。
锆砂的导热性好,蓄热能力大,耐火度高,热震稳定性好,常用作熔模精铸件的面层耐火材料。
纯ZrSiO4的耐火度在2 000 ℃以上,随着杂质含量增加,耐火度相应下降。
锆砂当含有氧化物杂质时,其分解温度会下降,例如含有Ca、Mg氧化物时,分解温度会降至1 300 ℃左右,当含有K、Na氧化物时,其开始分解温度会降至900 ℃左右。
熔模铸造现场问题分析

熔模铸造现场问题分析1、搅拌机改为升降式,温度55度左右,蜡液与腊屑一比一。
2.注蜡机压力为0.2-0.35MPa,保压10-20秒,注蜡机温度48-52度3.蜡模区室温控制在23-26度,搅拌区如蜡模区增加隔离门4.蜡模上的内浇口改为与工件一体,浇口棒用铝模成型以增加蜡棒的光洁度。
5.装蜡棒与蜡模的塑料筐应分开使用,保持料框清洁无残蜡粘附,水池内的浮蜡应及时捞出,保持好工作区域地面整洁。
6.检验后的蜡模要吹净蜡屑,焊接后的蜡组要检查有无焊缝,有多余的蜡滴要刮除干净并水洗干净。
7、制壳区要增加风扇增强通风,避免不同的工作区域模组的风干硬化程度不一。
8、制壳撒砂前应把砂框内的砂粒筛除,使用的砂子太潮应重新复晒后使用。
9、硬化池应定期清理池底杂物,浓度不够时及时补加氯化铵或氯化铝,氯化铝的比重控制在1.17-1.19之间。
10、每层涂料要均匀,不堆积,转角及孔洞盲孔等不宜涂到处要。
用毛笔或小毛刷刷入,夏天时要特别注意涂层不要淋的过干,导致砂子不容易沾上,撒砂要均匀不漏撒。
11、第一层涂料撒砂后硬化15分钟左右,捞上来如有条件的话要用清水水洗,风干30-40分钟(在通风状态下),手感不干不湿时就可以进行第二层涂料,第二层硬化十五分钟,第三层硬化20分钟,第四五六层硬化时间30-40分钟,风干时间不少于30分钟,气温低时适当延长,风干硬化时不碰坏涂层。
12、对易鼓胀变形的产品,在制壳三四层后扎铁丝或加细钢筋固定13、制壳后的模组从硬化池捞出后放置16-24小时方可脱蜡,脱蜡前要把浇口杯上的多余涂料或砂子清除干净。
14、脱蜡溶液中加入1%的盐酸,使蜡料的皂化物明显减少,脱蜡温度控制在90-95度,拖拉框底部应放置麻袋,避免溶液沸腾使底部砂子进入模组,脱蜡后在倒出模壳内的液体时要多晃动,使内部多余的蜡水倒尽,然后在用干净的热水倒入模壳内冲洗,蜡脱尽后的模壳要浇口朝下摆放,并用标识牌标注脱蜡日期,蜡棒要放入热水中洗干净备用15、模壳脱蜡后脱蜡池5天清洗一次,放置8小时以上方可焙烧,储存期一般不超过5天,时间过长会使盐析出模壳产生白色绒毛影响铸件质量,模壳强度也会降低,10天以上严禁使用16、模壳焙烧要根据脱蜡时间先做先用,焙烧温度在850-900度,高温保温30-45分钟,使皂化粉盐类等全部汽化时有白烟从模壳中散出,有模壳外观呈白色或粉红色,浇口杯冒黑烟或喷火苗时说明未焙烧干净,,模壳最多焙烧两次,两次以上严禁使用17、焙烧后的模壳要摆放在挖好的砂坑内,围好砂,围砂石防止砂子进入浇口杯等待浇铸18、钢液成分合格后应加入炉料重量的0.2%的铝线进行脱氧,其中一半加入炉中,一半均匀分散加入各包中,作为补充脱氧,浇铸时的模壳温度不低于600度,浇铸温度应视产品的大小、壁厚而定,一般壁薄的产品温度。
- 1、下载文档前请自行甄别文档内容的完整性,平台不提供额外的编辑、内容补充、找答案等附加服务。
- 2、"仅部分预览"的文档,不可在线预览部分如存在完整性等问题,可反馈申请退款(可完整预览的文档不适用该条件!)。
- 3、如文档侵犯您的权益,请联系客服反馈,我们会尽快为您处理(人工客服工作时间:9:00-18:30)。
熔模精密铸造过程疑难问题解答前言三百六十行,行行出人才。
各行各业都有自己的特长。
各从业人员必须熟练地掌握本行业、本岗位的职业技能,具备一定的包括职业技能在内的职业素质,才能胜任工作,把工作做好,为本行业做出应有的贡献,实现自己的人生价值。
熔模铸造业是技术密集型的行业。
本行业对其职工职业素质的要求比较高。
在科学技术迅速发展的今天,更是这样。
精铸业的职工队伍中,大部分是技术员工。
他们是企业的主力军,是振兴和发展本企业的技术力量。
技术人员素质如何,直接关系到本企业的生存和发展。
在市场经济条件下,企业之间的竞争,是质量之竞争;价格之竞争;也是技术之竞争;归根结底是人才的竞争。
优秀的技术员工是企业各类人才中重要的组成部分。
企业必须有这样一支高素质的技术工人队伍,有这样一批技术过硬、技艺精湛的能工巧匠,才能保证产品质量,提高生产效率,降低物料消耗,使企业获得经济效益;才能支持企业不断生产出高难度的产品,去发掘市场、占领市场;才能在激烈的市场竞争中立于不败之地!由于本人水平有限,加之时间仓促,难免存在不足和错误,诚恳希望专家,工程师和同仁批评指正。
吴光来第一章熔模铸件工艺设计与模具设计§1、熔模铸件工艺设计1.1、熔模铸件的尺寸精度受到哪些因素的影响?答:铸件尺寸精度受铸件结构、材质、制模、制壳、焙烧、浇注等多种因素的影响。
1)、铸件结构的影响:(1)、铸件壁厚,收缩率大;铸件壁薄,收缩率小;(2)、自由收缩率大,阻碍收缩率小。
2)、材质的影响:(1)、材料中含碳量越高,线收缩率越小,含碳量越低,线收缩率越大;(2)常见材质的铸造收缩率如下:铸造收缩率K=(LM-LJ)/LJ×100%LM—型腔尺寸;LJ—铸件尺寸K受以下因素的影响:蜡模K1、铸件结构K2、合金种类K3、浇注温度K4。
合金种类收缩率自由收缩受阻收缩铸铁件 0.8% 0.7%碳钢及低合金钢 1.6-2.0% 1.3-1.7%不锈钢 2.0-2.3% 1.7-2.0%3)、制模对铸件线收缩率的影响:(1)蜡(模)料的线收缩率约为0.9-1.1%;(2)蜡模径向(受阻)收缩率仅为长度方向(自由)收缩率的30-40%,射蜡温度对自由收缩率的影响远远大于对受阻收缩率的影响。
(最佳射蜡温度为57-59℃,温度越高收缩越大。
)(3)射蜡温度、射蜡压力、保压时间对熔模尺寸的影响以射蜡温度最明显,其次为射蜡压力,保压时间在保证熔模成型后对熔模最终尺寸的影响很小。
(4)熔模存放时,将进一步产生收缩,其收缩值约为总收缩量的10%,但当存放12小时后,熔模尺寸基本稳定。
4)、制壳材料的影响:采用锆英砂、锆英粉、上店砂、上店粉因其膨胀系数小,仅为4.6×10-1/℃,因此,可以或略不计。
5)型壳的焙烧:由于型壳的膨胀系数小,当型壳温度为1150℃时,仅为0.05%,因此,也可以或略不计。
6)浇铸温度的影响:浇注温度越高,收缩率越大;浇注温度低,收缩率小,因此浇注温度应适当。
1.2、铸造工艺设计的内容是什么?其设计程序是怎么样的?答:铸造工艺设计的内容为:绘制铸造工艺图、铸件图、型腔装配图和编制填写铸造工艺卡等。
其设计程序为:①对产品(零件)图进行铸造工艺性分析;②选择铸造方法;③选择分型面;④选择工艺参数;⑤设计浇注系统;⑥绘制精铸图;⑦设计工装图。
1.3、简述内浇口设计原则?答:(1)应有利于模具生产,注蜡时便于起模、组模时便于焊接;(2)制壳时便于浸涂和干燥;脱蜡时便于将蜡液流净(因为凡是脱蜡不净的部位,都存在着铸造缺陷,只不过有的缺陷明显――宏观缺陷,有的缺陷不明显――微观缺陷;因此,在设计内浇口或蜡模组装时应充分考虑,以便将残留蜡控制在最少程度);(3)焙烧时便于进出摆放;浇注时便于合金液充型;浇铸后能形成顺序凝固的原则;(4)后道工序应便于切割与打磨等,应有利于提高铸件的外观质量;(5)在保证铸件质量的前提下,应尽量小。
(6)尽可能将内浇口设置在加工面。
1.4、什么是铸造收缩率?其影响因素有哪些?怎样计算?答:铸造收缩率是指:铸件在凝固冷却过程中,因产生线收缩而造成铸件实际尺寸与模样尺寸之间的缩小率。
铸造收缩率的大小主要取决于:合金成分、铸件结构、大小、模料的收缩、制壳耐火材料、合金液的浇铸温度等。
铸造收缩率ε=(L-L1)/L1×100% 式中L为模样尺寸;L1为铸件尺寸。
1.5、铸件的工艺出品率过高或过低说明什么问题?铸钢件出品率的大小,决定于哪些因素?答:铸件的工艺出品率过高,说明浇注系统补缩铸件的金属液可能不够,应适当增加浇注系统尺寸。
如过低,则说明浇注系统尺寸太大,金属液未被充分利用,应适当减少,选择合理的浇注系统。
铸钢件出品率的大小,决定于铸件的结构、大小、复杂程度等等。
1.6、设计工艺筋的作用是什么?答:1)防止铸件变形;2)防止铸件产生裂纹;3)减少大平面面积,防止型壳变形;4)作为补缩通道(补缩肋保证了铸件内部热节部位的补缩,防止产生缩孔);5)改善薄壁件充型、排气条件,防止产生浇不到、冷隔。
§2、熔模铸件模具设计2.1、熔模铸件模具设计有哪些要求?答:2.1.1 模具表面光洁度高;其生产的蜡模应外形美观,没有明显的披缝、变形和凹陷等;2.1.2 模具尺寸精度、形位公差符合要求;2.1.3 型腔内浇口位置及大小合适,流道设计合理,能够满足铸造工艺要求,能够保证蜡模完整充型。
2.1.4 模具操作方便、灵活,起模劳动强度低,起模效率高;2.1.5 小件一型多件,以提高生产率;2.1.6 模具使用寿命长,易于修改及维护。
要达到以上要求,设计者必须精通熔模铸造的相关工艺过程,熟悉模具加工的相关手段。
只有这样,才能设计出尺寸符合要求、操作方便、灵活与制作费用合理的精铸模具。
2.2、模具的设计要考虑哪些因素?答:模具设计首先是一个铸件产品的工艺设计过程。
需要将铸件的毛坯尺寸按适当的缩水比例转化成模具型腔尺寸。
这是一个经验性很强的工作,因为影响铸件收缩的因素很多。
除蜡模及铸件凝固收缩外,铸件在冷却过程中型壳阻碍还会导致收缩受阻及变形。
分型方式、内浇口位置及组模方式也直接影响到铸件的尺寸精度与形位公差。
设计者必须了解熔模铸造的相关工艺过程,在设计模具之前综合考虑,并在设计中确保有可修改模具的可能性。
2.3、模具的常用顶出机构(取模方法)有哪些?答:模具设计中,顶出结构设计是非常关键的。
仅仅是做到蜡模成型,模具设计会很简单。
但我们必须仔细考虑怎样易于将蜡模从模具中不变形地取出,以及怎样合理设计模具顶出机构和抽芯结构,从而提高模具起模效率。
蜡模从模具中取出的方式有以下几种:2.3.1直接用手取出;2.3.2用压缩空气吹出;2.3.3用顶出机构将蜡模顶出。
前两种取出方法易使蜡模在取出时变形,而顶模机构可防止蜡模变形。
所以,对于精度要求较高的机械零件和易变形的零件只能采用顶出机构将蜡模顶出。
2.4、模具总装技术要求有哪些?答:2.4.1分型面配合间隙不大于0.05mm。
2.4.2各组合块及上下型错位不大于0.05mm。
2.4.3顶杆不高出型腔表面,可低于型腔表面0.05mm以内;复位杆不高出分型面,可低于分型面0.05mm以内。
2.4.4型腔表面应无凹凸不平及毛刺等缺陷,型腔边缘应保持锐边;非型腔边缘倒钝。
2.4.5总装后经压蜡试模,取模时无阻卡现象,蜡模飞边厚度不大于0.05mm。
2.4.6模具外表面应刻上模具编号、铸件图号、和其它标记。
2.4.7相同零件或模具大小差不多的模具,注蜡口高度应相等h±0.2mm。
以便同时压蜡。
2.4.8注蜡口大小为:小件Φ6,大件Φ8;注蜡口位置尽可能放在内浇口处。
§3模具制造(详见模具制造工艺守则)第二章蜡模制作1、蜡模尺寸检验标准。
1.1蜡模尺寸检验规定有检验员进行首检。
检验员根据铸件的要求尺寸,去判断蜡模的尺寸是否符合要求;蜡模尺寸的收缩与铸件凝固的收缩不一定完全相同。
例:带槽铸件的蜡模,在未起模之前属于受阻收缩,但起模后的冷却收缩又属于自由收缩;当制壳浇铸后,合金液冷却(即铸件收缩)又属于半阻碍或阻碍收缩。
因此,蜡模尺寸的检验非常重要;如果蜡模的尺寸都不符合要求,那么制壳与浇铸,岂不是枉费心机。
1.2影响蜡模尺寸的因素主要有以下几个方面:1.2.1压蜡温度对熔模尺寸的影响:在54℃-58℃之间影响不大,当大于59℃时,每增加2℃,线收缩率约增加0.1%。
1.2.2压注压力对蜡模尺寸的影响不大;而这种影响在压力较小时较明显。
1.2.3压蜡(充型)时间对蜡模尺寸的影响:时间越短、收缩越大,时间越长、收缩越小,但超过一定的时间,收缩又无明显区别。
1.2.4保压时间对蜡模尺寸的影响:保压时间越短、收缩越大,时间越长、收缩越小,蜡模越厚、影响越大。
1.2.5压型(模具)温度对蜡模尺寸的影响:模具温度越高,蜡模收缩率越大。
1.2.6注蜡工艺蜡缸保温时间射蜡温度/℃保压时间/s 存放时间/h 铸件重量>24h(在54±2℃的条件下) 小件:55±2 6-8 >4-12 <100g中件:57±2 8-10 >12-16 100-200大件:59±2 10-12 >12-24 >200g蜡模尺寸公差蜡模基本尺寸(mm)一般公差(mm)特别公差(mm)≤10 ±0.10 ±0.075>10-25 ±0.15 ±0.10>25-50 ±0.25 ±0.20>50-100 ±0.35 ±0.30>100-150 ±0.40 ±0.35>150-200 ±0.45 ±0.40>200-250 ±0.50 ±0.45>250 ±0.50% ±0.30%备注:当铸件没有特别的要求时,就按照一般公差要求进行抽检;当铸件有特殊尺寸要求,但又无法采用加工来保障时,就必须严格控制每道工序的每个环节,以确保铸件的质量。
2、蜡模组装原则(蜡模在组装时应考虑哪些问题?)答:(1)、检查浇口棒,将浇口棒模上的气泡、裂纹等缺陷修补平整。
(2)、按工艺规定选用合适的浇口棒模,并确定组焊方式、数量和距离(应根据铸件的大小、复杂程度等,合理选择的浇注系统。
)(3)、检查焊接处不应有缝隙;蜡模上不允许有蜡滴、蜡屑。
(4)、在保证铸件质量的前提下,尽可能多组装,以提高工艺出品率。
(5)、组装好的模组,应方便后道工序的生产。
(即便于制壳操作、便于脱蜡、焙烧时便于摆放与进出、壳模浇铸时便于充型、后处理工序应便于震壳、切割)3、蜡模生产工艺(详见蜡模生产工艺守则)第三章型壳制作1、制壳干燥间干湿度控制、型壳干燥时间的确定原理。