13.2 连铸机的主要设备
13.2 连铸机的主要设备

第一页,编辑于星期四:十四点 十五分。
13.2.1 连铸机的基本参数 13.2.2 钢包 13.2.3 中间包 13.2.4 结晶器 13.2.5 二次冷却系统
Your company slogan 第二页,编辑于星期四:十四点 十五分。
13.2.6 拉坯矫直装置 13.2.7 引锭装置 13.2.8 辊缝测量装置 13.2.9 铸坯切割装置 13.2.10 出坯系统的各种设备
好的保温性能。一般常用的中间包断面形状 为圆形、椭圆形、三角形、矩形和”T”字形 等。中间包内衬是由保温层、永久层和工作 层组成。保温层紧贴包壳钢板,以减少散热 ,一般可用石棉板、保温砖或轻质挠注料砌 筑。永久层与钢液直接接触,可用高铝砖、 镁质砖砌筑,也可用硅质绝热板、镁质绝热 板或镁橄榄石质绝热板组装砌筑。
Your company slogan 第十六页,编辑于星期四:十四点 十五分。
13.2.4 结晶器
13.2.4.2 结晶器的重要参数 在连铸过程中,结晶器充当着一次冷却的角色,其长度是个非常重要的参数。确定结 晶器长度的主要依据,是铸坯出结晶器下口时的坯壳最小厚度。对于大断面铸坯,要求 坯壳厚度大于15mm,小断面铸坯为8—10mm。根据大量的理论研究和实践经验,结晶 器长度一般在700一900mm比较合适,也有的是1200mm。目前大多数倾向于把结晶器 长度增加到900mm,以适应高拉速的需要。 为了获得良好的一次冷却效果,凝固坯壳与结晶器铜板必须保持良好的接触。由于钢 液在结晶器内冷却凝固生成坯壳的同时伴随着体积收缩.因此结晶器铜板内腔必须设计 成上大下小的形状.即所谓的结晶器锥度。这样可以减少因收缩产生气隙,改善结晶器 的导热。结晶器倒锥度常见有构种表示方法:
连续铸造原理和连铸设备简介(PDF 28页)
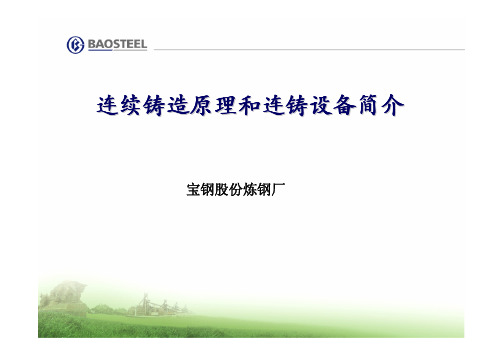
宽度可调结晶器
�小辊密排 �二冷宽向无级调节
扇形段装置
扇形段更换装置
中间包预热
中间包车 自动加渣 引锭杆系统
液压振动
结晶器液面控制 幅切气雾冷却
扇型段轻压下
一连铸概况
一次火焰切割机
一次火焰切割机
去毛刺机
去毛刺机
喷印机
铸坯管理辊道 精整区辊道
推钢机/堆垛机
局部清理机
手清
宽厚板厂
2050热轧
外供
宝钢连铸采用的新技术
2#-8#扇形段:280 min 9#-14#扇形段:220min 15#-17#扇形段:150min 单流驱动电机总功率:209KW
300t转炉
一连铸概况
中间包预热
中间包车 自动加渣 引锭杆系统
液压振动
结晶器液面控制 幅切气雾冷却
扇型段轻压下
LF/RH/KIP/CAS 钢包回转台 中间包
宽度可调结晶器
连续铸造原理和连铸设备简介
宝钢股份炼钢厂
连续铸造原理
一连铸概况
一连铸现装备三台二机二流大型板坯连铸机,2010年实现 年产合格铸坯750万吨。从钢包回转台接受钢水一直到把板坯送 到与轧钢厂的交接点为止的整个连铸过程,已经实现了由计算 机全程控制。
连铸主要工艺
钢包到达 回转台
钢包开浇 流入中间包
炼钢厂连铸设备简介
炼钢厂连铸设备简介
中间包
参数 走行形式
铸机
升降形式
水口形式
SN快换 机构
拖链形式
等离子 设备
长水口 机械手
中间包 形式
中间包 额定 容量
称量 精度
1CC
电机-减 速机
涡轮千斤顶
连铸设备PPT课件

立式连铸机基本特点
• 设备高度大,一般高度为25~35m以上, 且,铸坯断面越大,拉速越快,定尺长度 越长,设备总高度就越高。这样,造成建 设费用大,操作不方便,设备维护及事故 处理很困难。
• 铸坯因钢水静压力大,板坯鼓肚变形缺陷 较为严重。
设备总高度高,限制了立式连铸机的应用。
16
立弯式连铸机基本特点
• 薄板坯连铸机 • 轮式连铸机
12
各种连铸机的特点
13
立式连铸机基本特点
14
立式连铸机基本特点
• 铸机主要设备布置在垂直线上,从钢水浇注到 铸坯切割定尺,整个工序均在垂直位置完成。 铸坯切成定尺以后,由升降装置或者运输机运 到地面。
• 钢水在直立的结晶器内和二次冷却区逐渐结晶 凝固,铸坯在整个过程中不受任何弯曲、矫直 作用,这样适用于对裂纹敏感性高的钢种。同 时,铸坯坯壳均匀生长,钢水中的非金属夹杂 物上浮和分布均匀,对浇注优质钢有利。
• 内外弧冷却强度不一致。所以要合理布 置二冷强度。
设备高度的降低,使得弧形连铸机得到广 泛使用
20
多点矫直弧形连铸机基本特点
21
多点矫直弧形连铸机基本特点
• 原理和设备和单点矫直弧形连铸机一样。 • 拉速增加,使得钢水不能在四分之一圆弧内完
全凝固,因此在矫直时,铸坯中心还有钢液液 芯,形成所谓带液芯矫直。 • 单点矫直会导致带液芯矫直时的一次变形量大, 铸坯中心区产生裂纹缺陷。而将一次变形变成 多次变形,可解决这一问题。
• 有利于大型夹杂物上浮及钢中夹杂物均匀分 布。适合生产对内部夹杂物、偏析严格的钢 种
• 具有和弧形连铸机相同的设备高度低等特点
24
直结晶器弧形连铸机基本特点
• 存在两处多点矫直区:先多点弯曲、再多点矫 直。导致裂纹缺陷容易产生,设备结构复杂、 检修维护难度增大。
连铸基础知识---钢包

连铸设备的基础知识介绍连铸设备: 1钢包-2中间包-3结晶器-4结晶器振动装置-5二次冷却设备-6拉坯矫直设备-7铸坯导向设备-8切割设备-9出坯设备凡是共用一个钢包同时浇铸一流或多流铸坯的一套设备就是一台连铸机。
一台连铸机可以有多个机组(机组是指拥有独立的传动系统和工作系统的连铸设备)。
连铸机流数是指同时浇铸的铸坯数量。
一、钢包1钢包又叫钢水包或大包。
其作用是盛放、运载钢水及部分熔渣, 在浇铸过程中可以通过开启水口的大小来控制钢流量, 还可以用于炉外精炼, 通过炉外精炼可以使钢水的温度调整精度, 成分控制命中率及钢水纯净度进一步提高。
故钢包的作用可以简洁的总结为:盛放、运载、精炼、浇铸钢水, 还具有倾翻, 倒渣落地放置等作用。
二、钢包容量的确定钢包容量与炼钢炉的最大岀钢量相匹配, 另外考虑到岀钢量的波动留有10%的余量和一定的炉渣量(大型钢包炉渣量为金属量的3%~5%而小型钢包的渣量是金属的5%~10%)。
除此之外, 钢包上口还应该留有200mm以上的净空, 为了更好的用于炉外精炼要留出更大的空间。
三、钢包的形状确定(1)钢包是截面为圆形的桶状容器, 其形状与尺寸应该满足以下条件:钢包的直径与高度比。
钢包容量一定时, 为了减少散热损失和有利于夹杂物的上浮应该尽量减小钢包的内表面面积, 故钢包平均内径与高的比值为0.9~1.1。
四、锥度。
为了在浇铸后方便倒出残留的钢液, 钢渣以及取出包底凝固块, 一般的钢包内部都设计成上大下小带有一定锥度, 钢包壁应该有10%~15%的倒锥度。
大型钢包底应该向水口方向倾斜3%~5%。
五、(3)钢包外形。
为了有利于钢液中气体的排出, 夹杂物的上浮, 减少浇铸时钢液的冲击, 钢包外形不能做成细高形, 尽量做成矮胖型。
六、钢包结构1.钢包本体(1)外壳。
支座和氩气配管等, 外壳是钢包的主体构架, 由钢板焊接而成, 外壳有一定数量的排气孔, 可以排除耐火材料中的湿气。
(2)加强箍。
连铸主要设备介绍

RH示意图
(五)VOD真空吹氧脱碳法炉 VOD法(Vacuum Oxygen Decarburization)称为真空吹氧脱碳法, 它是1965年由德国维腾公司开发出的技术。 VOD设备与VD设备的构成基本相同,主要 的区别在于VOD法增加了氧枪及其升降系 统、供氧系统。
真空循环脱气的工作原理:当两个插入管 插入钢液一定深度时,启动真空泵,真空 室被抽成真空,由于内外压力差,钢液上 升一定高度;与此同时上升管输入驱动气 体(氩气),受热膨胀,引起等温膨胀, 钢液与气体混合比重降低,驱动钢液项喷 泉一样涌入真空室,使真空室的平衡破坏, 为保持平衡,一部分钢液从下降管回到钢 包中,就这样在钢水压力差和驱动气体的 作用下不断地从上升管涌入真空室,并经 过下降管回落到钢包内,周而复始的实现 钢液循环,从而通过造渣净化钢液。
(二)双流板坯连铸机的主要平台及设备 主要设备由钢包回转台、中间包(车)、结晶器、结晶 器振动装置、二次冷却和铸坯导向装置、拉坯矫直装置、 切割装置、出坯装置等部分组成
连铸机横向布置示意图 1—操作台,2—转炉;3—铸锭 设备;4—连铸机 5—铸坯运行辊道;6—大包转 台
1、浇注平台及二冷室(功能及结构)
8、钢包长水口操作机构 功能及结构: 长水口操作机构用于钢包长口的安装,操 作过程手动完成。把长水口接到钢包滑动 水口下端后,由液压缸压紧。为避免吸入 空气,长水口将接上Ar气。 长水口操作机构位于长水口操作平台上, 并有一个保护罩以防钢水喷溅。 液压动力来源是铸机主液压系统。
连铸设备介绍
一、浇注跨的布置形式 分为:横向布置、纵向布置及靠近轧钢车间布置等几种形式 1、横向布置:横向布置是指连铸机的中心线与厂房纵向柱列 线相垂直的布置形式,我厂主厂房有 、原料跨、转炉跨、分配 跨(钢水及炉外精炼跨)、浇铸跨、出坯跨、成品跨多个跨间 平行布置。而连铸机的摆布采用的就是这种横向布置方式。
连铸的主要设备的组成
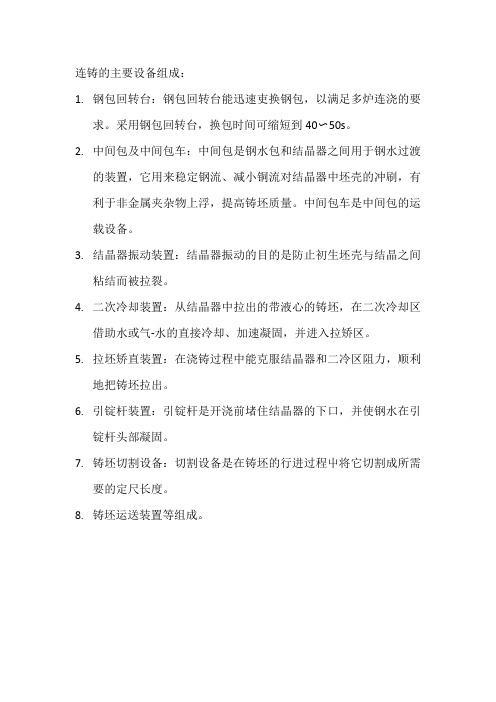
连铸的主要设备组成:
1.钢包回转台:钢包回转台能迅速吏换钢包,以满足多炉连浇的要
求。
采用钢包回转台,换包时间可缩短到40〜50s。
2.中间包及中间包车:中间包是钢水包和结晶器之间用于钢水过渡
的装置,它用来稳定钢流、减小铜流对结晶器中坯壳的冲刷,有利于非金属夹杂物上浮,提高铸坯质量。
中间包车是中间包的运载设备。
3.结晶器振动装置:结晶器振动的目的是防止初生坯壳与结晶之间
粘结而被拉裂。
4.二次冷却装置:从结晶器中拉出的带液心的铸坯,在二次冷却区
借助水或气-水的直接冷却、加速凝固,并进入拉矫区。
5.拉坯矫直装置:在浇铸过程中能克服结晶器和二冷区阻力,顺利
地把铸坯拉出。
6.引锭杆装置:引锭杆是开浇前堵住结晶器的下口,并使钢水在引
锭杆头部凝固。
7.铸坯切割设备:切割设备是在铸坯的行进过程屮将它切割成所需
要的定尺长度。
8.铸坯运送装置等组成。
连续铸造原理和连铸设备简介
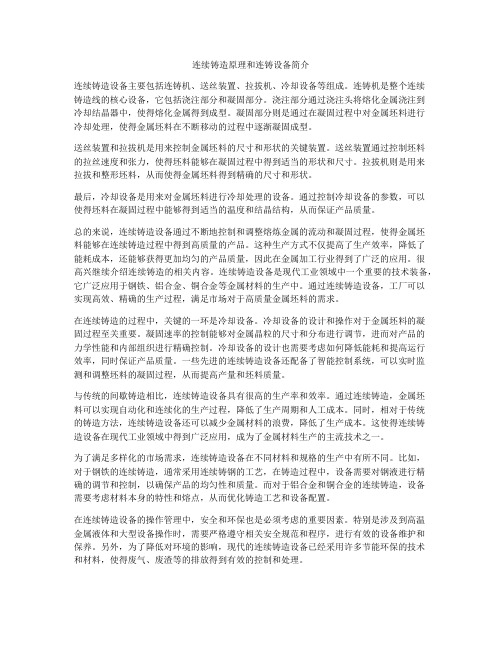
连续铸造原理和连铸设备简介连续铸造设备主要包括连铸机、送丝装置、拉拔机、冷却设备等组成。
连铸机是整个连续铸造线的核心设备,它包括浇注部分和凝固部分。
浇注部分通过浇注头将熔化金属浇注到冷却结晶器中,使得熔化金属得到成型。
凝固部分则是通过在凝固过程中对金属坯料进行冷却处理,使得金属坯料在不断移动的过程中逐渐凝固成型。
送丝装置和拉拔机是用来控制金属坯料的尺寸和形状的关键装置。
送丝装置通过控制坯料的拉丝速度和张力,使得坯料能够在凝固过程中得到适当的形状和尺寸。
拉拔机则是用来拉拔和整形坯料,从而使得金属坯料得到精确的尺寸和形状。
最后,冷却设备是用来对金属坯料进行冷却处理的设备。
通过控制冷却设备的参数,可以使得坯料在凝固过程中能够得到适当的温度和结晶结构,从而保证产品质量。
总的来说,连续铸造设备通过不断地控制和调整熔炼金属的流动和凝固过程,使得金属坯料能够在连续铸造过程中得到高质量的产品。
这种生产方式不仅提高了生产效率,降低了能耗成本,还能够获得更加均匀的产品质量,因此在金属加工行业得到了广泛的应用。
很高兴继续介绍连续铸造的相关内容。
连续铸造设备是现代工业领域中一个重要的技术装备,它广泛应用于钢铁、铝合金、铜合金等金属材料的生产中。
通过连续铸造设备,工厂可以实现高效、精确的生产过程,满足市场对于高质量金属坯料的需求。
在连续铸造的过程中,关键的一环是冷却设备。
冷却设备的设计和操作对于金属坯料的凝固过程至关重要。
凝固速率的控制能够对金属晶粒的尺寸和分布进行调节,进而对产品的力学性能和内部组织进行精确控制。
冷却设备的设计也需要考虑如何降低能耗和提高运行效率,同时保证产品质量。
一些先进的连续铸造设备还配备了智能控制系统,可以实时监测和调整坯料的凝固过程,从而提高产量和坯料质量。
与传统的间歇铸造相比,连续铸造设备具有很高的生产率和效率。
通过连续铸造,金属坯料可以实现自动化和连续化的生产过程,降低了生产周期和人工成本。
连铸设备主要技术参数
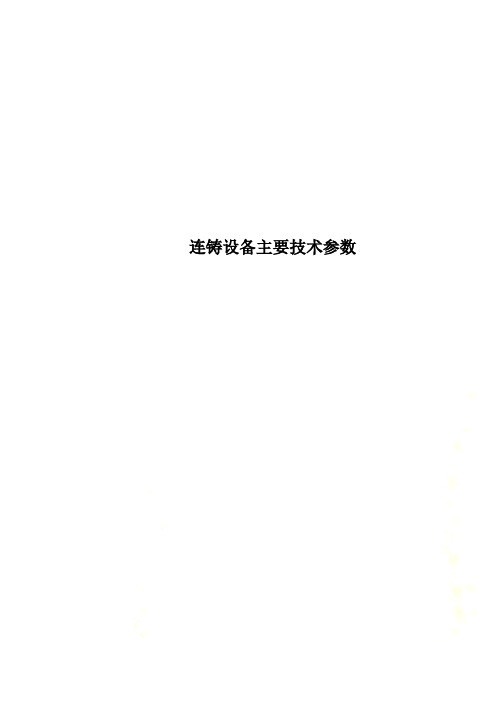
连铸设备主要技术参数2010连铸设备及岗位职能love2010-1-51.设备主要技术参数1.1.设备主要技术参数:连铸机型式弧形小方坯连铸机弧形半径 R=6000mm流数三机三流流间距 1200mm铸坯断面 120×120mm 150×150mm Φ110-Φ160mm铸坯定尺长度 3.7-12米钢水罐支撑方式钢包回转台中间罐车台数 2台中间罐型式、容量电动缸自动控制塞棒开闭式,容量12t结晶器结构形式铜管水套组合式铸坯导向装置上段为活动段下段为固定段拉矫机拉速范围 0.6-6.0m/min铸坯切断方式火焰切割机出坯方式轨道,双层翻转冷床,翻缸机,移缸机和推钢机轨道速度 32m/min移钢能力 3.2t钢结构平台上层平台面标高 +6.700m(轨道面标高+0.60m)上层平台面长宽 23800×13100mm下层平台面标高 +4.05mm连铸机长度(基准线至固定挡板面) 39680mm1.2 主要设备技术性能1.2.1钢包回转台承载能力 2×80t(钢水重40t,钢包重40t)回转半径 3500mm旋转速度正常1r/min,启、制动0.1r/min旋转角度±180°;故障时±360°旋转用电机 YZR160MB-6 AC 8.5KW 930r/min 单轴伸 IM1001 380V H级绝缘 IP54事故旋转速度 0.5rpm事故旋转角度 180°事故旋转油马达斜轴式轴向柱塞马达A2F63W2P1 P=10-13MPa471r/min N=5.2-6.8KW放钢包时冲击系数 2干油润滑系统:1.2.1.1齿轮润滑系统多点干油泵 ZB-2型 N=18KW工作压力 31.5MPa贮油容积 30L给油量 3.2立方厘米/minDC24V喷射嘴 GPZ-135型(JB/ZQ4538-86)空气压力 0.45-0.6MPa喷射直径 135mm喷嘴与润滑表面距离 200mm气动三联件 398.263二位二通电磁阀 DF-10 DC24V润滑介质连铸机专用脂空气工作压力 0.45-0.6MPa1.2.1.2 轴承圈润滑系统电动干油泵 DRB4-M120Z换向阀 24EJF-M(JB/ZQ4584-86)压差开关 YCK-M5 (JB/ZQ4585-86)双线分配器 4SSP2-M1.5(JB/ZQ4583-86)2SSP2-M1.5(JB/ZQ4583-86)润滑介质连铸机专用脂1.2.2中间罐车结构型式框型结构的车架,单侧链轮驱动载重量 15.5t轨距 1700mm轮架 3800mm最大轮压 80KN减速器 BWD2.2-3-29摆线针轮行星减速器车轮直径Φ350mm走行速度 9.52m/min走行方向微调手动操作中间罐横向微调行程±30mm车体运行距离±8000mm供电方式电缆卷筒操作方式固定操作箱1.2.3中间罐烘烤站结构型式烧嘴可垂直旋转升降80°烧嘴型式鼓风助燃的天然气火焰燃烧嘴烘烤温度 -25~1100℃烘烤时间 45~60min烧嘴数量 2个/台天然气压 0.2MPa空气压力 0.4MPa风机型号(2#机配置) GY8-12-1 NO.6 右旋1.2.4 结晶器结构型式弧形铜管水套组合式外弧半径 6000mm断面尺寸 120×120mm 150×150mm Φ110-Φ160mm铜管长度方坯750mm,圆坯 800mm冷却水量 95立方米/小时水压 0.6MPa-0.8Mpa足辊水方坯角喷 120(4×4) 150(8×4);圆坯Φ110-Φ160mm(6×3),Φ160-Φ180(8×3)喷嘴型号 3/8〞PZ2265QZ11.2.5结晶器振动装置结构型式四连杆短臂振动弧形半径 R6000mm振动方式正弦曲线振幅±3~±6mm(实际±5)频率 0~300Hz(可调)1.2.6二冷装置活动段结构型式弧形导架体气缸摆动驱动用气缸 S型尾部悬挂式气缸Φ160×750mm气缸工作压力 0.4-0.6MPa1.2.7.二冷装置固定1段结构型式带导向夹辊托辊固定式水冷弧形导向架夹辊Φ160×180mm夹辊最大辊面间距 200mm1.2.8二冷装置固定Ⅱ段同固定Ⅰ段1.2.9拉矫机1.2.9.1拉矫机2#连铸机铸坯断面mm 120×120mm 150×150mm Φ110-Φ160mm 拉坯速度m/min 0.3-5m/min开口度mm 85-237拉矫辊直径×宽Φ350×250mm 个数 5驱动辊两个上辊驱动减速器型号F1212.1(上海新中专利)总速比430.25液压缸型号UY-TF/MI(JB/ZQ4181-97)规格Φ140/Φ100-320,Φ140/Φ100-520 工作压力0-10MPa1.2.9.2辅助拉矫机2#连铸机铸坯断面mm 120×120mm 150×150mm Φ110-Φ160mm拉坯速度m/min 0.3-5m/min开口度mm 85-237拉矫辊直径×宽Φ350×250mm 个数 5驱动辊上辊单辊驱动减速器型号F1212.1(上海新中专利)总速比430.25液压缸型号UY-TF/MI( JB/ZQ4181-97)规格Φ140/Φ100-320工作压力0-10MPa1.2.10 蒸汽排出装置2#连铸机配风机 Y4-73N010D-4 左风量 44004立方米/min1.2.11 引锭杆承放装置结构型式气缸驱动,四连杆摆动摆动距离(升高×距离) 80×260mm托架个数/流 8每流驱动气缸数 2气缸型号 2#连铸机:SΦ200×250mm空气压力 0.4-0.6MPa1.2.12 引锭杆结构型式箱型对扣式半板簧引锭杆总长 111000mm节距 400mm插入结晶器长度 150mm引锭杆断面 145×143mm(150坯)115×113mm(120坯)Φ105(Φ110坯)Φ115(Φ120坯)Φ125(Φ130坯)Φ135(Φ140坯)Φ145(Φ150坯)Φ155(Φ160坯)1.2.13轨道1.2.13.1主要参数2#机结构型式辊子双轴承支座,分组集中链条传动(辊径×辊身长)输出辊道Φ165×180 冷床区Φ220×200辊道运行速度32m/min冷床区32.17m/min减速机行星摆线针轮减速器BWD18-23-2.2 i=23冷床区辊道:XWD4-29-2.2i=29链条16A-1(GB1243.1-83)1.2.13.2辊道分组(每流)输出辊道分组编号辊道名称每组辊子数辊子编号辊距mm备注Ⅰ切前辊道 4 1~4 820 水冷Ⅱ切后辊道 6 8~12 900Ⅲ输出辊道(一)6 13~18 900Ⅳ输出辊道(二)4 19~22 900Ⅴ输出辊道(三)5 23~27 9002#机冷床区辊道Ⅰ 3 28~30 900 30~31辊距1200 Ⅱ 4 31~34120Ⅲ 3 35~371201.2.14 双层翻转冷床(2#机)铸坯定尺 2600mm-12000mm铸坯截面 20×120mm 150×150mm Φ110-Φ160mm铸坯翻转角度 90°液压缸(2个) Y-HGI-E100×380LEI-HL10T2系统最大压力 14MPa1.2.15横向移钢机横移铸坯重量 3200Kg横移速度 23m/min横移行程 6200mm减速器 ZS82.5-1-Ⅲ型 i=51.22制动器 YWZ300/25型配YT1-25 ZC/4电力液压推动器额定推力 250N额定行程 40mm制动瓦退距 0.7mm制动力矩 320Nm1.2.16 推钢机和冷床冷床尺寸长12005mm 宽 11350mm存放铸坯最大重量 42t推钢机行程 1000mm液压缸(2个) SDG-160/110-e型行程650mm系统最大压力 14MPa1.2.17 中间包倾翻装置(2#机)倾翻速度 1.785rpm倾翻方向逆时针方向倾翻角度±180°行星减速器 NGW123-11 i=56输入1000r/min时允许输入功率7.5kw制动器 YT1-25电动液压推动器1.2.18 拉矫机干油润滑站(2#连铸机)干油润滑泵(江苏启东润滑设备有限公司)型号 HA-Ⅲ1X公称压力 40MPa额定给油量 430ml/min电机功率 1.5kw贮油筒容积 60升电动加油泵(江苏启东润滑设备有限公司)型号 DJB-V70/860公称压力 3.15MPa额定给油量 70L/H电机功率 0.37kw贮油筒容积 200升润滑介质连铸机专用脂1.2.19 二冷活动段,气动阀门站分水滤气器 QSL-25 1MPa空气减压阀 QTY-25 1MPa压力表 Y-60ZT 0-1.6MPa油雾器 QIU-25 1MPa电控电器滑阀 K25D2-15-L1 直流24v消音器 XS-L15-L11.2.20二冷固定段气动阀门站压力 0.2~0.6MPa流量 0.13~0.15立方米/min减压阀 QTY-25 G1〞 1Mpa节流阀 L41H-25电控电气滑阀 k25D2-15-L1 DC24及以下项目1.2.20.1快速调压阀1/2〞 AR4000-04 烟台未来气动组件设备有限公司技术参数:进口压力 0.7~1.0MPa压力调节范围 0.05~0.6MPa输入压力波动 0.2MPa时输入压力波动<0.02MPa压力变换时间 2~5秒1.2.20.2旋塞阀X13W-10 G1/2〞1.2.20.3压力表Y-100ZT 0~1.6MPa1.2.21火焰切割机型号:FGR3 方圆坯火焰切割车上海新中切割钢种:普碳钢、优质钢、低合金钢切割铸坯断面尺寸: 100×100 120×120 180×180 220×220 240×240 Φ100-Φ200mm铸坯最大拉速: 3.5m/min切割速度:300-450mm/min能源介质:乙炔、天然气、液化石油气、丙烷、丙烯、焦炉煤气等。
连铸设备主要技术参数

2010连铸设备及岗位职能love2010-1-51.设备主要技术参数1.1.设备主要技术参数:连铸机型式弧形小方坯连铸机弧形半径 R=6000mm流数三机三流流间距 1200mm铸坯断面 120×120mm 150×150mm Φ110-Φ160mm铸坯定尺长度 3.7-12米钢水罐支撑方式钢包回转台中间罐车台数 2台中间罐型式、容量电动缸自动控制塞棒开闭式,容量12t结晶器结构形式铜管水套组合式铸坯导向装置上段为活动段下段为固定段拉矫机拉速范围 0.6-6.0m/min铸坯切断方式火焰切割机出坯方式轨道,双层翻转冷床,翻缸机,移缸机和推钢机轨道速度 32m/min移钢能力 3.2t钢结构平台上层平台面标高 +6.700m(轨道面标高+0.60m)上层平台面长宽 23800×13100mm下层平台面标高 +4.05mm连铸机长度(基准线至固定挡板面) 39680mm1.2 主要设备技术性能1.2.1钢包回转台承载能力 2×80t(钢水重40t,钢包重40t)回转半径 3500mm旋转速度正常1r/min,启、制动0.1r/min旋转角度±180°;故障时±360°旋转用电机 YZR160MB-6 AC 8.5KW 930r/min 单轴伸 IM1001 380V H级绝缘 IP54事故旋转速度 0.5rpm事故旋转角度 180°事故旋转油马达斜轴式轴向柱塞马达A2F63W2P1 P=10-13MPa471r/min N=5.2-6.8KW放钢包时冲击系数 2干油润滑系统:1.2.1.1齿轮润滑系统多点干油泵 ZB-2型 N=18KW工作压力 31.5MPa贮油容积 30L给油量 3.2立方厘米/minDC24V喷射嘴 GPZ-135型(JB/ZQ4538-86)空气压力 0.45-0.6MPa喷射直径 135mm喷嘴与润滑表面距离 200mm气动三联件 398.263二位二通电磁阀 DF-10 DC24V润滑介质连铸机专用脂空气工作压力 0.45-0.6MPa1.2.1.2 轴承圈润滑系统电动干油泵 DRB4-M120Z换向阀 24EJF-M(JB/ZQ4584-86)压差开关 YCK-M5 (JB/ZQ4585-86)双线分配器 4SSP2-M1.5(JB/ZQ4583-86)2SSP2-M1.5(JB/ZQ4583-86)润滑介质连铸机专用脂1.2.2中间罐车结构型式框型结构的车架,单侧链轮驱动载重量 15.5t轨距 1700mm轮架 3800mm最大轮压 80KN减速器 BWD2.2-3-29摆线针轮行星减速器车轮直径Φ350mm走行速度 9.52m/min走行方向微调手动操作中间罐横向微调行程±30mm车体运行距离±8000mm供电方式电缆卷筒操作方式固定操作箱1.2.3中间罐烘烤站结构型式烧嘴可垂直旋转升降80°烧嘴型式鼓风助燃的天然气火焰燃烧嘴烘烤温度 -25~1100℃烘烤时间 45~60min烧嘴数量 2个/台天然气压 0.2MPa空气压力 0.4MPa风机型号(2#机配置) GY8-12-1 NO.6 右旋1.2.4 结晶器结构型式弧形铜管水套组合式外弧半径 6000mm断面尺寸 120×120mm 150×150mm Φ110-Φ160mm铜管长度方坯750mm,圆坯 800mm冷却水量 95立方米/小时水压 0.6MPa-0.8Mpa足辊水方坯角喷 120(4×4) 150(8×4);圆坯Φ110-Φ160mm(6×3),Φ160-Φ180(8×3)喷嘴型号 3/8〞PZ2265QZ11.2.5结晶器振动装置结构型式四连杆短臂振动弧形半径 R6000mm振动方式正弦曲线振幅±3~±6mm(实际±5)频率 0~300Hz(可调)1.2.6二冷装置活动段结构型式弧形导架体气缸摆动驱动用气缸 S型尾部悬挂式气缸Φ160×750mm气缸工作压力 0.4-0.6MPa1.2.7.二冷装置固定1段结构型式带导向夹辊托辊固定式水冷弧形导向架夹辊Φ160×180mm夹辊最大辊面间距 200mm1.2.8二冷装置固定Ⅱ段同固定Ⅰ段1.2.9拉矫机1.2.9.1拉矫机2#连铸机铸坯断面mm120×120mm 150×150mm Φ110-Φ160mm 拉坯速度m/min0.3-5m/min开口度mm85-237拉矫辊直径×宽Φ350×250mm 个数5驱动辊两个上辊驱动减速器型号F1212.1(上海新中专利)总速比430.25液压缸型号UY-TF/MI(JB/ZQ4181-97)规格Φ140/Φ100-320,Φ140/Φ100-520工作压力0-10MPa1.2.9.2辅助拉矫机2#连铸机铸坯断面mm120×120mm 150×150mm Φ110-Φ160mm拉坯速度m/min0.3-5m/min开口度mm85-237拉矫辊直径×宽Φ350×250mm 个数5驱动辊上辊单辊驱动减速器型号F1212.1(上海新中专利)总速比430.25液压缸型号UY-TF/MI( JB/ZQ4181-97)规格Φ140/Φ100-320工作压力0-10MPa1.2.10 蒸汽排出装置2#连铸机配风机 Y4-73N010D-4 左风量 44004立方米/min1.2.11 引锭杆承放装置结构型式气缸驱动,四连杆摆动摆动距离(升高×距离) 80×260mm托架个数/流 8每流驱动气缸数 2气缸型号 2#连铸机:SΦ200×250mm空气压力 0.4-0.6MPa1.2.12 引锭杆结构型式箱型对扣式半板簧引锭杆总长 111000mm节距 400mm插入结晶器长度 150mm引锭杆断面 145×143mm(150坯)115×113mm(120坯)Φ105(Φ110坯)Φ115(Φ120坯)Φ125(Φ130坯)Φ135(Φ140坯)Φ145(Φ150坯)Φ155(Φ160坯)1.2.13轨道1.2.13.1主要参数2#机结构型式辊子双轴承支座,分组集中链条传动(辊径×辊身长)输出辊道Φ165×180 冷床区Φ220×200辊道运行速度32m/min冷床区32.17m/min减速机行星摆线针轮减速器BWD18-23-2.2 i=23冷床区辊道:XWD4-29-2.2i=29链条16A-1(GB1243.1-83)1.2.13.2辊道分组(每流)输出辊道分组编号辊道名称每组辊子数辊子编号辊距mm备注Ⅰ切前辊道41~4820水冷Ⅱ切后辊道68~12900Ⅲ输出辊道(一)613~18900Ⅳ输出辊道(二)419~22900Ⅴ输出辊道(三)523~279002#机冷床区辊道Ⅰ328~3090030~31辊距1200Ⅱ431~341200Ⅲ335~3712001.2.14 双层翻转冷床(2#机)铸坯定尺 2600mm-12000mm铸坯截面 20×120mm 150×150mm Φ110-Φ160mm铸坯翻转角度 90°液压缸(2个) Y-HGI-E100×380LEI-HL10T2系统最大压力 14MPa1.2.15横向移钢机横移铸坯重量 3200Kg横移速度 23m/min横移行程 6200mm减速器 ZS82.5-1-Ⅲ型 i=51.22制动器 YWZ300/25型配YT1-25 ZC/4电力液压推动器额定推力 250N额定行程 40mm制动瓦退距 0.7mm制动力矩 320Nm1.2.16 推钢机和冷床冷床尺寸长12005mm 宽 11350mm存放铸坯最大重量 42t推钢机行程 1000mm液压缸(2个) SDG-160/110-e型行程650mm系统最大压力 14MPa1.2.17 中间包倾翻装置(2#机)倾翻速度 1.785rpm倾翻方向逆时针方向倾翻角度±180°行星减速器 NGW123-11 i=56输入1000r/min时允许输入功率7.5kw制动器 YT1-25电动液压推动器1.2.18 拉矫机干油润滑站(2#连铸机)干油润滑泵(江苏启东润滑设备有限公司)型号 HA-Ⅲ1X公称压力 40MPa额定给油量 430ml/min电机功率 1.5kw贮油筒容积 60升电动加油泵(江苏启东润滑设备有限公司)型号 DJB-V70/860公称压力 3.15MPa额定给油量 70L/H电机功率 0.37kw贮油筒容积 200升润滑介质连铸机专用脂1.2.19 二冷活动段,气动阀门站分水滤气器 QSL-25 1MPa空气减压阀 QTY-25 1MPa压力表 Y-60ZT 0-1.6MPa油雾器 QIU-25 1MPa电控电器滑阀 K25D2-15-L1 直流24v消音器 XS-L15-L11.2.20二冷固定段气动阀门站压力 0.2~0.6MPa流量 0.13~0.15立方米/min减压阀 QTY-25 G1〞 1Mpa节流阀 L41H-25电控电气滑阀 k25D2-15-L1 DC24及以下项目1.2.20.1快速调压阀1/2〞 AR4000-04 烟台未来气动组件设备有限公司技术参数:进口压力 0.7~1.0MPa压力调节范围 0.05~0.6MPa输入压力波动 0.2MPa时输入压力波动<0.02MPa压力变换时间 2~5秒1.2.20.2旋塞阀X13W-10 G1/2〞1.2.20.3压力表Y-100ZT 0~1.6MPa1.2.21火焰切割机型号:FGR3 方圆坯火焰切割车上海新中切割钢种:普碳钢、优质钢、低合金钢切割铸坯断面尺寸: 100×100 120×120 180×180 220×220 240×240 Φ100-Φ200mm铸坯最大拉速: 3.5m/min切割速度:300-450mm/min能源介质:乙炔、天然气、液化石油气、丙烷、丙烯、焦炉煤气等。
连铸机设备技术规格

项目:VISAKHAPATNAM钢厂《4#连铸机技术附件》附件2:4#连铸机本体设备技术规格书4#连铸机设备技术规格目录一、4#连铸机设施 (1)1工艺设施 (1)1.1工艺结构 (1)1.2蒸汽密封室 (1)1.3蒸汽排出装置和钢包回转台 (2)1.4钢包称重系统(机电一体品) (3)1.5钢包盖 (4)1.6钢包加盖装置 (4)1.7钢包长水口机械手 (4)1.8下渣检测系统(机电一体品) (5)1.9中间罐 (5)1.10中间罐钢水温度测量系统(机电一体品) (6)1.11中间罐盖 (6)1.12中间罐车 (7)1.13中间罐称重系统(机电一体品) (8)1.14中间罐塞棒机构(机电一体品) (8)1.15中间罐预热装置及水口预热装置(机电一体品) (8)1.16渣盘 (9)1.17溢流罐 (10)1.18事故溜槽 (10)1.19加渣机(机电一体品) (10)1.20悬挂操作箱(含操作箱) (11)1.21结晶器装配 (11)1.22结晶器框架 (12)1.23结晶器铜管 (12)1.24结晶器电磁搅拌装置(M-EMS)(机电一体品) (13)1.25铸流末端电磁搅拌器(外置式) (13)1.26结晶器液面检测及控制系统(机电一体品) (13)1.27结晶器液压振动装置 (14)1.28浸入式水口快换机构(带事故闸板)(机电一体品) (15)1.29足辊喷淋系统 (15)1.30铸坯导向段 (15)1.31二冷喷淋架 (18)1.32拉矫机 (18)1.33链式引锭杆杆身 (19)1.34引锭杆过渡链节 (20)1.35引锭杆头 (20)1.36引锭杆存放装置 (20)1.37火焰切割机(含定尺测长装置)(机电一体品) (21)1.38取样切割枪 (22)1.39取样收集箱 (22)1.40手动切割枪 (22)1.41坯头坯尾收集装置 (23)1.42切前辊道(含脱引锭辊) (23)1.43切割区辊道 (25)1.44输送辊道(一) (26)1.45输送辊道(二) (27)1.46去毛刺机(含溜槽、渣箱)(机电一体品) (28)1.47出坯辊道(含翻钢机) (29)1.48横向移钢机 (30)1.49固定挡板 (31)1.50升降挡板 (31)1.51铸坯喷号机(机电一体品) (32)1.52步进冷床及收集台架(含拨钢机) (32)1.53铸坯存储跨输送辊道 (33)1.54铸坯过跨运输车(KL、LM、MQ和QR跨) (34)1.55圆坯旋转台 (35)1.56推钢机(含收集台) (36)1.57圆坯升降装置 (37)1.58高位辊道 (37)1.59圆坯检查和处理设施(机电一体品) (38)1.60连铸机防护罩 (38)1.61液压和润滑设备(含管道) (38)1.62介质管道 (38)1.63结晶器、导向段和拉矫机维修设施 (38)1.64中间罐维修区 (40)1.65设备过跨台车(结晶器、扇形段和中间罐的运输) (42)1.66中间罐吊具 (43)1.67废料箱 (43)1.68中间罐手动拆衬装置 (43)1.69结晶器对弧样板和导向段对弧样板 (43)1.70在线对弧样板(用于结晶器和导向段) (44)1.71用于操作维护的提升装置,工具,吊具,仪表和仪器 (44)1.72人体冷却器 (44)1.73500KG能力的客货电梯 (44)1.74电动葫芦/手动葫芦 (44)1.75基础螺栓和锚固件 (44)1.76稀油,干油,润滑剂和化学药剂等的第一次填充 (44)1.77调试备件 (44)1.78保险备件 (44)1.79耐火材料和消耗件 (44)1.80水冷却器 (44)1.81更换件 (44)1.82保证连铸机正常生产的其它设备。
连铸主要设备介绍PPT51页
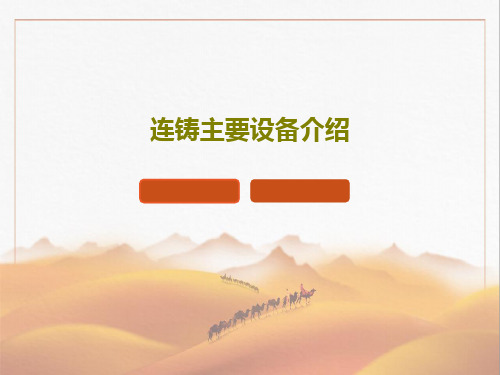
31、园日涉以成趣,门虽设而常关。 32、鼓腹无所思。朝起暮归眠。 33、倾壶绝余沥,窥灶不见烟。
34、春秋满四泽,夏云多奇峰,秋月 扬明辉 ,冬岭 秀孤松 。 35、丈夫志四海,我愿不知老。
ቤተ መጻሕፍቲ ባይዱ
谢谢你的阅读
❖ 知识就是财富 ❖ 丰富你的人生
71、既然我已经踏上这条道路,那么,任何东西都不应妨碍我沿着这条路走下去。——康德 72、家庭成为快乐的种子在外也不致成为障碍物但在旅行之际却是夜间的伴侣。——西塞罗 73、坚持意志伟大的事业需要始终不渝的精神。——伏尔泰 74、路漫漫其修道远,吾将上下而求索。——屈原 75、内外相应,言行相称。——韩非
连铸主要设备介绍页PPT文档
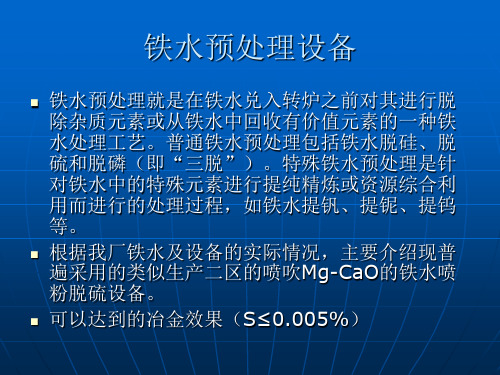
氮气管路
精炼设备简介
一、二次冶金工艺流程: 高炉——铁水预处理——转炉——钢水二次精
炼——连铸 二、主要的精炼方式: 二次精炼就是对转炉钢水根据目的进行炉外(相
长水口操作机构位于长水口操作平台上, 并有一个保护罩以防钢水喷溅。
液压动力来源是铸机主液压系统。
9、结晶器确定铸坯的断面形状,钢液在结晶器内 开始冷却凝固,并形成足够的坯壳。是连铸机上 最关键的部件之一,成为连铸机的心脏。
结晶器的主要部件包括结晶器框架、结晶器插入 件宽边、结晶器插入件窄边、结晶器足辊、窄面 铸坯导向辊及结晶器罩等组成。
2、钢包回转台
连铸机生产过程中,用于承载和转送钢水包,
能以最短的时间将钢水包从接收位置转送至浇注
位置。钢包的加速、减速及定位通过PLC系统和
行程开关来完成。另外,也可采用手动回转模式。
由于回转台设置了两个回转臂,因而可实现多炉
连浇,减少了车间吊车作业。每个臂可独立提升,
两臂同时旋转,并具有钢包加盖功能,实现钢水
为使中间罐浸入式水口在浇注位对准结晶器, 在车上设有行走方式微调(变频调速)和横向 微调机构。中间罐车的升降机构,可把侵入式 水口插入结晶器内。称量装置可称量中间罐内 的钢水重量。
4、带盖中间罐:用于贮存及分配钢水。钢包内的 钢水注入中间罐后,在其中均匀温度及成分,钢 水中的非金属夹杂物充分上浮,然后通过安装在 下面的浸入式水口由塞棒控制送入结晶器内。
对于转炉)处理。为了创造最佳的冶金反应条件, 所采用的基本手段不外乎搅拌、真空、加热、渣 洗、喷吹及喂丝等几种或几种的组合。 根据主要 功能,常见的精炼设备有: 吹氩设备、喂丝设备、LF炉 、DH、RH、LVD、 ASEA-SKF、V0D等
目前连铸机上常用的切割装置主要有火焰切割机

• 1、火焰切割概念 • 利用预热氧气和可燃气(Βιβλιοθήκη 炔、丙烷、天然气、焦炉煤气、氢气等)混
合燃烧的火焰,将切缝处的金属熔化,同时用高压氧气把熔化的金属 吹掉,直至把铸坯切断。 • 优点是:设备轻:加工制造容易;切缝质量好,且不受铸温度和断面 大小的限制;设备的外形尺寸较小,对多流连铸坯机尤为适合。 • 缺点是:切割时间长、切缝宽、材料损失大,切割时产生的烟雾和熔 渣污染环境,需要繁重的清渣工作。金属损失大,约为铸坯重的 1%~1.5%;切割时间慢;在切割时产生氧化铁、废气和热量,需必 要的运渣设备和除尘设施;当切割短定尺时需要增加二次切割;消耗 大量的氧和燃气。
2、火焰切割机组成:
由车架及车体走行装置、同步机 构、切割枪横移装置、切割枪、 边部检测器等组成
二、机械剪切装置 机械剪切设备简称机械剪或剪机,由
下剪切是在运动过程中进行的,所以 连铸机上用的剪机又称为飞剪。采用 机械剪切,设备较大,但其剪切速度 快,剪切时间只需2~4s,定尺精度 高,特别是生产定尺较短的铸坯时, 因其无金属损耗且操作方便,在小方 坯连铸机上应用较为广泛。
四、后序其他装置
• • 翻板机与垛板机、板坯横移车及转盘、打号机。
• 输送辊道的辊面标高,一般与拉矫机的下辊辊面持平,呈 水平布置。
• 铸坯切割区的辊道大多采用浮动式。
二、铸坯的横移及冷却装置
• 铸坯的横移装置主要有推钢机和拉钢机,用于横向移动铸坯。铸坯 的冷却设备土要有冷床和强迫冷却装置,用于铸坯的冷却。
三、铸坯表面清理装置
• 常用的铸坯清理装置有火焰清理机、氧一乙 炔手工割炬、手提砂轮机及风铲等类型。
铸坯输出装置
输出装置的任务是把切成定尺的铸 坯冷却、精整、出坯,以保证连铸机 的连铸生产。一般情况下,输出装置 包括输送辊道、铸坯的横移装置、铸 坯的冷却装置、铸坯表面清理装置、 铸坯的吊具和打号机等。
连铸设备主要技术参数

2010连铸设备及岗位职能love2010-1-51.设备主要技术参数1.1.设备主要技术参数:连铸机型式弧形小方坯连铸机弧形半径 R=6000mm流数三机三流流间距 1200mm铸坯断面 120×120mm 150×150mm Φ110-Φ160mm铸坯定尺长度 3.7-12米钢水罐支撑方式钢包回转台中间罐车台数 2台中间罐型式、容量电动缸自动控制塞棒开闭式,容量12t结晶器结构形式铜管水套组合式铸坯导向装置上段为活动段下段为固定段拉矫机拉速范围 0.6-6.0m/min铸坯切断方式火焰切割机出坯方式轨道,双层翻转冷床,翻缸机,移缸机和推钢机轨道速度 32m/min移钢能力 3.2t钢结构平台上层平台面标高 +6.700m(轨道面标高+0.60m)上层平台面长宽 23800×13100mm下层平台面标高 +4.05mm连铸机长度(基准线至固定挡板面) 39680mm1.2 主要设备技术性能1.2.1钢包回转台承载能力 2×80t(钢水重40t,钢包重40t)回转半径 3500mm旋转速度正常1r/min,启、制动0.1r/min旋转角度±180°;故障时±360°旋转用电机 YZR160MB-6 AC 8.5KW 930r/min 单轴伸 IM1001 380V H级绝缘 IP54事故旋转速度 0.5rpm事故旋转角度 180°事故旋转油马达斜轴式轴向柱塞马达A2F63W2P1 P=10-13MPa471r/min N=5.2-6.8KW放钢包时冲击系数 2干油润滑系统:1.2.1.1齿轮润滑系统多点干油泵 ZB-2型 N=18KW工作压力 31.5MPa贮油容积 30L给油量 3.2立方厘米/minDC24V喷射嘴 GPZ-135型(JB/ZQ4538-86)空气压力 0.45-0.6MPa喷射直径 135mm喷嘴与润滑表面距离 200mm气动三联件 398.263二位二通电磁阀 DF-10 DC24V润滑介质连铸机专用脂空气工作压力 0.45-0.6MPa1.2.1.2 轴承圈润滑系统电动干油泵 DRB4-M120Z换向阀 24EJF-M(JB/ZQ4584-86)压差开关 YCK-M5 (JB/ZQ4585-86)双线分配器 4SSP2-M1.5(JB/ZQ4583-86)2SSP2-M1.5(JB/ZQ4583-86)润滑介质连铸机专用脂1.2.2中间罐车结构型式框型结构的车架,单侧链轮驱动载重量 15.5t轨距 1700mm轮架 3800mm最大轮压 80KN减速器 BWD2.2-3-29摆线针轮行星减速器车轮直径Φ350mm走行速度 9.52m/min走行方向微调手动操作中间罐横向微调行程±30mm车体运行距离±8000mm供电方式电缆卷筒操作方式固定操作箱1.2.3中间罐烘烤站结构型式烧嘴可垂直旋转升降80°烧嘴型式鼓风助燃的天然气火焰燃烧嘴烘烤温度 -25~1100℃烘烤时间 45~60min烧嘴数量 2个/台天然气压 0.2MPa空气压力 0.4MPa风机型号(2#机配置) GY8-12-1 NO.6 右旋1.2.4 结晶器结构型式弧形铜管水套组合式外弧半径 6000mm断面尺寸 120×120mm 150×150mm Φ110-Φ160mm铜管长度方坯750mm,圆坯 800mm冷却水量 95立方米/小时水压 0.6MPa-0.8Mpa足辊水方坯角喷 120(4×4) 150(8×4);圆坯Φ110-Φ160mm(6×3),Φ160-Φ180(8×3)喷嘴型号 3/8〞PZ2265QZ11.2.5结晶器振动装置结构型式四连杆短臂振动弧形半径 R6000mm振动方式正弦曲线振幅±3~±6mm(实际±5)频率 0~300Hz(可调)1.2.6二冷装置活动段结构型式弧形导架体气缸摆动驱动用气缸 S型尾部悬挂式气缸Φ160×750mm气缸工作压力 0.4-0.6MPa1.2.7.二冷装置固定1段结构型式带导向夹辊托辊固定式水冷弧形导向架夹辊Φ160×180mm夹辊最大辊面间距 200mm1.2.8二冷装置固定Ⅱ段同固定Ⅰ段1.2.9拉矫机1.2.9.1拉矫机2#连铸机铸坯断面mm120×120mm 150×150mm Φ110-Φ160mm 拉坯速度m/min0.3-5m/min开口度mm85-237拉矫辊直径×宽Φ350×250mm 个数5驱动辊两个上辊驱动减速器型号F1212.1(上海新中专利)总速比430.25液压缸型号UY-TF/MI(JB/ZQ4181-97)规格Φ140/Φ100-320,Φ140/Φ100-520工作压力0-10MPa1.2.9.2辅助拉矫机2#连铸机铸坯断面mm120×120mm 150×150mm Φ110-Φ160mm拉坯速度m/min0.3-5m/min开口度mm85-237拉矫辊直径×宽Φ350×250mm 个数5驱动辊上辊单辊驱动减速器型号F1212.1(上海新中专利)总速比430.25液压缸型号UY-TF/MI( JB/ZQ4181-97)规格Φ140/Φ100-320工作压力0-10MPa1.2.10 蒸汽排出装置2#连铸机配风机 Y4-73N010D-4 左风量 44004立方米/min1.2.11 引锭杆承放装置结构型式气缸驱动,四连杆摆动摆动距离(升高×距离) 80×260mm托架个数/流 8每流驱动气缸数 2气缸型号 2#连铸机:SΦ200×250mm空气压力 0.4-0.6MPa1.2.12 引锭杆结构型式箱型对扣式半板簧引锭杆总长 111000mm节距 400mm插入结晶器长度 150mm引锭杆断面 145×143mm(150坯)115×113mm(120坯)Φ105(Φ110坯)Φ115(Φ120坯)Φ125(Φ130坯)Φ135(Φ140坯)Φ145(Φ150坯)Φ155(Φ160坯)1.2.13轨道1.2.13.1主要参数2#机结构型式辊子双轴承支座,分组集中链条传动(辊径×辊身长)输出辊道Φ165×180 冷床区Φ220×200辊道运行速度32m/min冷床区32.17m/min减速机行星摆线针轮减速器BWD18-23-2.2 i=23冷床区辊道:XWD4-29-2.2i=29链条16A-1(GB1243.1-83)1.2.13.2辊道分组(每流)输出辊道分组编号辊道名称每组辊子数辊子编号辊距mm备注Ⅰ切前辊道41~4820水冷Ⅱ切后辊道68~12900Ⅲ输出辊道(一)613~18900Ⅳ输出辊道(二)419~22900Ⅴ输出辊道(三)523~279002#机冷床区辊道Ⅰ328~3090030~31辊距1200Ⅱ431~341200Ⅲ335~3712001.2.14 双层翻转冷床(2#机)铸坯定尺 2600mm-12000mm铸坯截面 20×120mm 150×150mm Φ110-Φ160mm铸坯翻转角度 90°液压缸(2个) Y-HGI-E100×380LEI-HL10T2系统最大压力 14MPa1.2.15横向移钢机横移铸坯重量 3200Kg横移速度 23m/min横移行程 6200mm减速器 ZS82.5-1-Ⅲ型 i=51.22制动器 YWZ300/25型配YT1-25 ZC/4电力液压推动器额定推力 250N额定行程 40mm制动瓦退距 0.7mm制动力矩 320Nm1.2.16 推钢机和冷床冷床尺寸长12005mm 宽 11350mm存放铸坯最大重量 42t推钢机行程 1000mm液压缸(2个) SDG-160/110-e型行程650mm系统最大压力 14MPa1.2.17 中间包倾翻装置(2#机)倾翻速度 1.785rpm倾翻方向逆时针方向倾翻角度±180°行星减速器 NGW123-11 i=56输入1000r/min时允许输入功率7.5kw制动器 YT1-25电动液压推动器1.2.18 拉矫机干油润滑站(2#连铸机)干油润滑泵(江苏启东润滑设备有限公司)型号 HA-Ⅲ1X公称压力 40MPa额定给油量 430ml/min电机功率 1.5kw贮油筒容积 60升电动加油泵(江苏启东润滑设备有限公司)型号 DJB-V70/860公称压力 3.15MPa额定给油量 70L/H电机功率 0.37kw贮油筒容积 200升润滑介质连铸机专用脂1.2.19 二冷活动段,气动阀门站分水滤气器 QSL-25 1MPa空气减压阀 QTY-25 1MPa压力表 Y-60ZT 0-1.6MPa油雾器 QIU-25 1MPa电控电器滑阀 K25D2-15-L1 直流24v消音器 XS-L15-L11.2.20二冷固定段气动阀门站压力 0.2~0.6MPa流量 0.13~0.15立方米/min减压阀 QTY-25 G1〞 1Mpa节流阀 L41H-25电控电气滑阀 k25D2-15-L1 DC24及以下项目1.2.20.1快速调压阀1/2〞 AR4000-04 烟台未来气动组件设备有限公司技术参数:进口压力 0.7~1.0MPa压力调节范围 0.05~0.6MPa输入压力波动 0.2MPa时输入压力波动<0.02MPa压力变换时间 2~5秒1.2.20.2旋塞阀X13W-10 G1/2〞1.2.20.3压力表Y-100ZT 0~1.6MPa1.2.21火焰切割机型号:FGR3 方圆坯火焰切割车上海新中切割钢种:普碳钢、优质钢、低合金钢切割铸坯断面尺寸: 100×100 120×120 180×180 220×220 240×240 Φ100-Φ200mm铸坯最大拉速: 3.5m/min切割速度:300-450mm/min能源介质:乙炔、天然气、液化石油气、丙烷、丙烯、焦炉煤气等。
机械专业毕业设计说明书——钢包回转台

摘要钢包回转台设在连铸机浇铸位置上方用于运载钢包过跨和支承钢包进行浇铸的设备,是现代连铸生产中的重要设备之一,为实现连铸创造了连续提供钢液的条件。
钢包回转台有四个工作特点:1 它能迅速准确的将载满钢水的钢包运送至浇钢位置,并在浇钢过程中支承钢包;2 更换钢包迅速、能适应多炉连浇的需要;发生事故或断电时,能迅速将钢包移至安全位置;3 能实现保护浇注,并通过安装钢水称重装置,浇注更顺利;4 占用浇铸平台面积小,有利于浇注操作。
本课设计以SMS公司设计生产的蝶式可升降钢包回转台为参照。
主要对回转装置进行相关设计计算,设计包括计算驱动装置功率和电机选型校核、减速器的选型、开式齿轮校核、回转支承的选型和地脚螺栓的校核等。
关键词:蝶式钢包回转台;回转装置;驱动装置;AbstractLadle turret position in continuous casting machine casting ladle over the top for the delivery and support across the ladle for casting equipment, is important in the production of modern casting one of the devices, in order to achieve the creation of a continuous casting of molten steel to provide the conditions.Ladle turret has four work characteristics:1.It will quickly and accurately ladle full of molten steel pouring position transported to and support the process of pouring steel ladle.2.Replacement Ladle quickly able to adapt to the needs of multi-continuous casting furnace;accident or a power out age can quickly ladle to a safe location.3.To achieve protection of casting,and by installing steel weighingdevice,pouring more smoothly.4.Small are a occupied by casting platform is conducive to pouring operation.5.SMS lesson design butterfly design and production company can lift the ladle turret as a reference.Mainly related design calculations rotary device.Design, including the drive unit power and check motor selection,reducer selection,open gear check,slewing ring selection and The calibration of anchor bolts.Key words:Butterfly Ladle Turret;Rotary device; drives motor reducer;目录摘要 (I)Abstract (II)目录 (III)第一章绪论 (1)1.1 连续铸钢技术的发展概述 (1)1.1.1 连续铸钢与铸模的区别 (1)1.1.2 国外连铸技术的发展概况 (1)1.1.3 我国连铸技术的发展概况及与国外连铸技术对比 (1)1.2 连铸机的主要设备及分类 (2)1.3 连铸机钢包回转台的结构和分类 (8)1.3.1 钢包旋转台的形式 (8)1.3.2 钢包旋转台主要结构特点 (9)1.3.3 钢包回转台的分类 (11)<1>直臂式钢包回转台 (11)<2>蝶式钢包回转台 (11)<3>双臂式钢包回转台 (12)<4>四连杆式钢包回转台 (13)第二章初步确定方案 (15)2.1 已知条件 (15)2.1.1 主要技术参数 (15)2.2 方案的总体布置形式 (15)2.3 回转台具体部件设计方案的确定 (16)2.3.1 钢包旋转驱动方式 (16)2.3.2 锁紧方式 (16)2.3.3 钢包盖的升降装置 (17)2.3.4 长水口机械手动作方式 (17)2.3.5 钢包升降驱动方案 (18)第三章回转功率的计算及电机等的选取 (19)3.1 钢包回转功率的计算 (19)3.1.1 基本数据的计算 (19)3.1.2 载荷情况Ⅰ的回转功率计算 (21)3.1.3 载荷情况Ⅱ的回转功率计算: (22)3.1.4 载荷情况Ⅲ的回转功率计算 (24)3.2 电动机和气动马达的选择 (26)3.2.1 电机功率的选择: (26)3.2.2 马达的选择 (26)3.3 减速器的设计 (26)3.3.1 确定减速器的结构 (26)3.3.2 各级减速传动比的确定 (27)3.3.3 各级减速齿轮基本参数确定 (27)第四章回转台主要构件分析 (33)4.1 回转轴承的有关计算 (33)4.1.1 回转轴承当量轴向负荷的计算 (33)4.1.2 回转轴承当量倾翻力矩的计算 (34)4.2 轴向滚柱的分析 (36)4.3 地脚螺栓的计算 (37)4.4 升降液压缸的选择 (39)4.5 钢包盖升降和回转系统的设计 (40)4.5.1 升降系统采用液压驱动 (40)4.5.2 回转系统采用液压系统 (42)4.6 称量传感器的型式选择与容量计算 (42)4.7 提升液压缸球绞应力计算 (43)第五章销齿传动的设计与计算 (45)5.1 销轮轴转矩3T (45)5.2 选材及许用应力的确定 (45)5.3 销齿直径确定 (47)5.4 校核齿轮弯曲强度 (48)5.5 确定尺寸 (48)第六章设备操作安装与维修 (50)6.1 大包回转台的操作 (50)6.2 一些设备的安装 (50)6.2.1 滚柱旋转轴承的使用方法和保管以及安装 (50)6.2.2 提升缸的安装与拆卸 (50)6.3 钢包回转台设备使用以及维护要点 (51)结束语 (52)参考文献 (53)第一章绪论1.1 连续铸钢技术的发展概述1.1.1连续铸钢与铸模的区别铸钢生产可以分为钢锭模浇注(以下简称铸模)和连续铸钢(以下简称连铸)两大类。
- 1、下载文档前请自行甄别文档内容的完整性,平台不提供额外的编辑、内容补充、找答案等附加服务。
- 2、"仅部分预览"的文档,不可在线预览部分如存在完整性等问题,可反馈申请退款(可完整预览的文档不适用该条件!)。
- 3、如文档侵犯您的权益,请联系客服反馈,我们会尽快为您处理(人工客服工作时间:9:00-18:30)。
Your company slogan
13.2.1
连铸机的基本参数
13.2.1.1 弧形连铸机规格表示方法 弧形连铸机规格表示方法为:aRb-C 其中 a—组成1台铸机的机数,机数为1时可以省略; R—机型为弧形或圆形连铸机; b—连铸机的圆弧半径(m),若椭圆形铸机为多个半径之乘积,也 示 表示可浇铸坯的最大厚度:坯厚= b/(30~36) mm C—表示铸机拉坯辊辊身长度,mm,还表示可容纳铸坯的最大宽度 : 坯宽=C—(150~200) mm 13.2.1.2 铸坯断面尺寸规格 铸坯断面尺寸是确定连铸机的依据。由于成材需要,铸坯断面形状和尺才也不同。目 前已生产的连铸坯形状和尺寸范围如下: 小方坯:70×70~200×200mm2; 大方坯: 200×200~450×450mm2;
Your company slogan
13.2.2
钢包
钢包又称为大包,是用于盛放钢液并进行精练和浇铸的容器。钢包的容量应 与炼钢炉的最大出钢量相匹配。钢包由外壳、内衬和注流控制机构三部分组成。 钢包内衬一般由保温层、永久层和工作层组成。内衬耐火材料的选择对改善钢 的质量、稳定操作、提高生产率有着重要的意义。钢包使用前必须经过充分烘烤
13.2.3
中间包
中间包的结构应具有最小的散热面积,良 好的保温性能。一般常用的中间包断面形状 为圆形、椭圆形、三角形、矩形和”T”字 形等。中间包内衬是由保温层、永久层和工 作层组成。保温层紧贴包壳钢板,以减少散 热,一般可用石棉板、保温砖或轻质挠注料 砌筑。永久层与钢液直接接触,可用高铝砖 、镁质砖砌筑,也可用硅质绝热板、镁质绝 热板或镁橄榄石质绝热板组装砌筑。 中间包没有包盖,目的在于保温和保护 钢包包底不致过分受烤而变形。在包盖上开 有注入孔和塞棒孔。水口直径应根据连铸机 在最大拉速时所需的钢液流量来确定。水口 直径可由下式计算确定:
连铸机的基本参数
(3)最大拉坯速度。限制拉坯速度的因素主要是铸坯出结晶器下口坯壳的安全厚
度。对于小断面铸坯坯壳安全厚度为8-10mm;大断面板坯坯壳厚度应≥15mm。
vmax
Km Lm
2
2
Km
Lm v max
式中
vmax —最大拉坯速度,m/min; Lm—结晶器有效长度(结晶器长度—100mm); Km—结晶器内钢液凝固系数,mm/min0.5; δ—坯壳厚度,mm。
漏钢。目前先进的连铸机同时配有这两套检
测系统。
Your company slogan
13.2.4
13.2.4.2 结晶器的重要参数
结晶器
在连铸过程中,结晶器充当着一次冷却的角色,其长度是个非常重要的参数。确 定结晶器长度的主要依据,是铸坯出结晶器下口时的坯壳最小厚度。对于大断面铸
坯,要求坯壳厚度大于15mm,小断面铸坯为8—10mm。根据大量的理论研究和
实践经验,结晶器长度一般在700一900mm比较合适,也有的是1200mm。目 前大多数倾向于把结晶器长度增加到900mm,以适应高拉速的需要。 为了获得良好的一次冷却效果,凝固坯壳与结晶器铜板必须保持良好的接触。由 于钢液在结晶器内冷却凝固生成坯壳的同时伴随着体积收缩.因此结晶器铜板内腔
必须设计成上大下小的形状.即所谓的结晶器锥度。这样可以减少因收缩产生气隙
,改善结晶器的导热。结晶器倒锥度常见有构种表示方法:
Your company slogan
13.2.4
结晶器
Your company slogan
13
结晶器的材质与寿命
由于站晶器内壁直接与高温钢液接触,要求其内壁材质导热系数要高,膨胀系 数要低,在高温下有足够的强度和耐磨性,塑性要好,易于加工。目前使用铜合 金做结晶器内壁。在铜中加入含量为0.08%-0.12%的银,能提高结晶器内壁的 高温强度和耐磨性。在铜中加入含量为0.5%的铬或加入一定量的磷,可显著提高 结晶器的使用寿命。还可以使用铜-铬-锆-砷合金或铜-锆-镁合金制作结晶器内壁
Your company slogan
13.2.3
中间包
中间包用塞棒与水口相配合来控制注流。一般用厚壁钢管作棒芯,挠注时在芯管 内插入直径稍小的钢管引入压缩空气进行冷却,也可以将塞棒作为中间包吹氩棒。中 间包塞棒是用锆—碳质或铝—碳质耐火材料,经过高压整体成型。 中间包采用滑动水口,安全可靠,有利于实现自动控制。但对结晶器内钢液的流 动也有不利影响,易造成偏流。中间包的滑动水口装置通常做成三层滑板。上下滑板 固定不动,中间用一块活动滑板控制注流。小方坯连铸机中间包采用稳定性好的耐火 材料制成的定径水口。目前除了部分小方坯连铸机外.都采用了浸入式水口加保护渣 的保护浇注。浸入式水口的形状和尺寸直接影响结晶器内钢液流动,从而对铸坯的表 面和内部质量乃至连铸的顺行产生直接影响。 目前采用最多的浸入式水口有单孔直筒形和双侧孔氏式两种。双侧孔浸入式水口 其侧孔有向上倾斜、向下倾斜和水平状三种,如图13—5所示。浇注大型板坯可采 用箱式浸入式水口,如图13—6所示。 定径水口采用锆质ZrO2耐火材料,或者内镶锆质、外套高铝质复合材料制作。 中间包的支承、运输、更换均是在专门的中间包小车上实现的。小车的结构要利 于浇注、捞渣和烧氧等操作,同时应具有横移和升降调节功能。小车行走机构一般是 两侧单独驱动,并有自动停车定位装置。中间包的升降机构有电动或液压驱动两种。 中间包车还设有电子称量系统和保护渣自动下料装置。
13.2
连铸机的主要设备
13.2.1
连铸机的基本参数
13.2.2
钢包
13.2.3
中间包
13.2.4
结晶器
13.2.5
二次冷却系统
Your company slogan
13.2.6
拉坯矫直装置
13.2.7
引锭装置
13.2.8
辊缝测量装置
13.2.9
铸坯切割装置
13.2.10
出坯系统的各种设备
Your company slogan
。钢包通过滑动水口开启、关闭来调节钢液注流的流量。滑动水口由上水口、上
滑板、 下滑板、下水口组成部分。长水口又称保护套管,用于钢包与中间包之 间保护注流,避免了注流的二次氧化、飞溅以及敞外浇铸带来的卷渣问题。目前 长水口的材质有熔融石英质和铝碳质两种。 目前.承托钢包的方式主要有钢包回转台和钢包支架等。 钢包回转台有直臂式和双臂式两种,均设有独立的称量系统。为了适应连铸工 艺的要求,目前钢包回转台趋于多功能化,增加了吹氩、调温、倾翻倒渣、加盖 保温等功能。
Your company slogan
13.2.3
中间包
中间包简称中包。中间包是位于钢包与结晶器之间,起着减压、稳流、去渣、贮 钢、分流等作用。当前对钢产品质量的要求变得更加严格。中间包不仅仅只是生产 中的一个容器,而且在纯净钢的生产中发挥着重要作用。20世纪70年代人们已认 识到改变中间包形状相加大中间包容积可以达到延长钢液的停留时间,提高夹杂物
Your company slogan
13.2.1
13.2.1.5
连铸机的基本参数
液相穴深度和冶金长度
液相穴深度L液是指从结晶器液面开始到铸坯中心液相凝固终了的长度,也称为 液心长度。液相穴深度是确定连铸机二冷区长度的重要参数,对于弧形铸机来说 ,液相穴深度也是确定圆弧半径的主要参数。它直接影响铸机的总长度和总高度 。 液相穴深度与拉速的关系式为
L液
D2 vc 2 4 K凝
液相穴深度与铸坯厚度、拉坯速度和冷却强度有关。铸坯越厚,拉速越快,液 相穴深度就越大,连铸机也越长。在一定程度内,增加冷却强度,有助于缩短液 相穴深度。但对一些钢种来说,冷却强度需要特别控制。 根据最大拉速确定的液相穴深度为冶金长度L冶。冶金长度是连铸机的重要结 构参数,决定着连铸机的生产能力,也决定了铸机半径或高度,对二次冷却区和 矫直区结构以及铸坯的质量都会产生重要影响。
去除率的目的;安装挡渣墙/坝,控制钢液的流动,实现夹杂物有效碰撞、长大和
上浮。80年代发明了多孔导流挡墙和中间包过滤器。在防止钢液被污染的技术开发 中,最近已有实质性的进展。借助先进的中间包设汁和操作如中间包加热,热周转 操作,惰性气氛喷吹,顶熔型中间包渣.活性钙内壁,中间包喂丝,以及中间包夹
杂物行为的数学模拟等,如图13—4所示。在现代连铸的应用和发展过程中,中间
Your company slogan
13.2.3
中间包
Your company slogan
13.2.4
13.2.4.1 结晶器的结构
结晶器
结晶器是连铸机非常重要的部件,称之为连铸设备的“心脏”。钢液在结晶器内 冷却初步凝固成一定坯壳厚度的铸坯外形,并被连续地从结晶器下口拉出,进入二冷 区。结晶器应具有良好的导热性和刚性,不易变形和内表面耐磨等优点,而且结构要 简单,便于制造和维护。 按结晶器的外形可分为直结晶器和弧形结晶器。直结晶器用于立式、立弯式及直 弧形连铸机,而弧形结晶器用在全弧形和椭圆形连铸机上。从结构来看,有管式结晶 器和组合式结晶器。小方坯及矩形多采用管式结晶器,而大型方坯、矩形坯和板坯多 采用组合式结晶器。 管式结晶器结构简单,易于制造、维修.广泛应用于中小断面铸坯的浇铸,最大 浇铸断面为180mm×180mm。 组合式结晶器如图13—7所示,是由4块复合壁板组合而成。每块复合壁板都是由 铜质内壁和钢质外壳组成。在与钢壳接触的铜板面亡铣出许多沟槽形成中间水缝。复 合壁板用双螺栓连接固定,冷却水从下部进入,流经水缝后从上部排出。4块壁板有各 自独立的冷却水系统。在4块复合壁板内壁相结合的角部,垫上厚3—5mm并带来45°倒 角的铜片,以防止铸坯角裂。