神雾气基竖炉直接还原炼铁技术研究新进展
直接还原炼铁技术的最新进展doc

直接还原炼铁技术的最新进展作者: 胡俊鸽,吴美庆,毛艳丽, 钢铁研究摘要撰写人 TsingHua出版日期: 2006年4月30日直接还原铁能够作为电炉、高炉和转炉的炉料。
DRI代替优质废钢更适合于生产对氮和有害元素有严格要求的钢种,如用于石油套管、钢丝绳、电缆线等的钢种。
最近几年,由于钢铁市场升温,废钢资源呈现世界性紧缺。
2003年,我国钢铁企业生产回收的废钢铁和非生产回收废钢铁合计为1502万t;而全年炼钢消耗废钢与辅助炼钢消耗废钢之和为4 750万t。
显然,国内的废钢缺口专门大。
以后几年,随着国际市场废钢资源的欠缺,世界对废钢的需求量将不断增加。
现今,在废钢资源全世界性紧缺、国际市场价钱几回上扬的情形下,关于我国来说,寻觅废钢替代品已迫在眉捷。
直接还原铁和热压块铁是最好的废钢替代品。
1直接还原炼铁技术进展状况2003年世界直接还原铁总量为4900万t。
比2002年增加了10%,不同工艺所生产直接还原铁所占份额如下:Midrex 为%,HyLⅢ为%,HyL Ⅰ为%,Finmet为%,其他气基为%,煤基为%。
直接还原工艺依照还原剂不同可分为气基和煤基。
气基直接还原工艺中,竖炉Midrex、Arex(Midrex改良型)和HyL Ⅲ工艺、反映罐法Hy LⅠ、流化床法Fior和Finmet工艺,都已取得了工业应用,流化床法Fior、Cir cored和碳化铁法在工业上应用不久就停产了。
煤基直接还原法中,取得工业应用的有回转窑法和转底炉法(Inmet-co、Fastmet、Sidcomet、DRylron),新开发的多层转底炉Primus工艺已于2003年2月投产。
气基直接还原工艺气基还原工艺可分为利用球团矿或块矿的工艺和利用铁矿粉的工艺。
各类气基直接还原铁工艺进展状况如表1所示。
表1各类气基直接还原铁工艺进展状况工艺装备工艺特点所用原料目前状况研究进展F ior(委内瑞拉)4个流化床反映器生产能耗高于竖炉Midrex和HyLⅢ铁矿粉Side tur厂于1976年投产,1985年开始,年产量达到35万t~41万t。
《气基直接还原竖炉炉型研究》范文

《气基直接还原竖炉炉型研究》篇一一、引言气基直接还原(DRI)作为钢铁行业中的关键工艺之一,一直受到行业内外专家学者的关注。
而作为实施气基直接还原的主要设备之一,竖炉的设计和优化对提高DRI生产效率、降低能耗、保证产品质量等具有重要意义。
本文将就气基直接还原竖炉的炉型进行研究,探讨其结构特点、操作性能以及优化方向。
二、气基直接还原竖炉概述气基直接还原技术是一种将铁矿石在高温下与还原性气体(如天然气、煤制气等)反应,将铁矿石还原成铁粉(DRI)的技术。
竖炉作为实施这一工艺的主要设备,其结构包括炉体、供气系统、排烟系统等。
通过竖炉内矿石与还原性气体的化学反应,达到将铁矿石转变为金属铁的目的。
三、竖炉结构及工作原理(一)炉体结构竖炉主要由进料系统、主体部分、排料系统等组成。
主体部分呈竖直筒形,其内壁需进行耐高温处理,以承受高温和化学反应的侵蚀。
(二)工作原理在竖炉内,铁矿石与高温还原性气体接触并发生化学反应。
在一定的温度和压力条件下,矿石中的氧化铁逐渐被还原成金属铁。
该过程需要在控制良好的气氛、温度和反应时间下进行,以保障产品的质量和生产效率。
四、气基直接还原竖炉炉型研究(一)不同炉型的特点根据进料方式、反应室设计、排料方式等因素,气基直接还原竖炉的炉型有多种类型。
不同类型竖炉在生产效率、能耗、产品质量等方面存在差异。
例如,对于进料方式,可采用连续进料或分批进料;反应室设计上,需要考虑气流分布、热能利用等因素。
(二)关键因素分析在炉型设计中,需考虑的主要因素包括矿石性质、还原性气体种类及来源、生产规模、环境因素等。
不同因素对竖炉的结构设计、操作性能和产品质量均有影响。
例如,矿石的粒度、化学成分将影响反应的速率和产品的质量;而还原性气体的种类和纯度则影响反应的效率和产品的性能。
(三)优化方向与案例分析针对当前存在的问题和需求,对竖炉进行优化和改进。
首先,提高竖炉的热能利用效率,通过优化气流分布、增加热回收装置等方式降低能耗;其次,改善矿石的还原效果,通过改进进料方式、调整反应温度等方式提高产品质量;最后,加强环保措施,减少排放,实现绿色生产。
《2024年气基直接还原竖炉炉型研究》范文
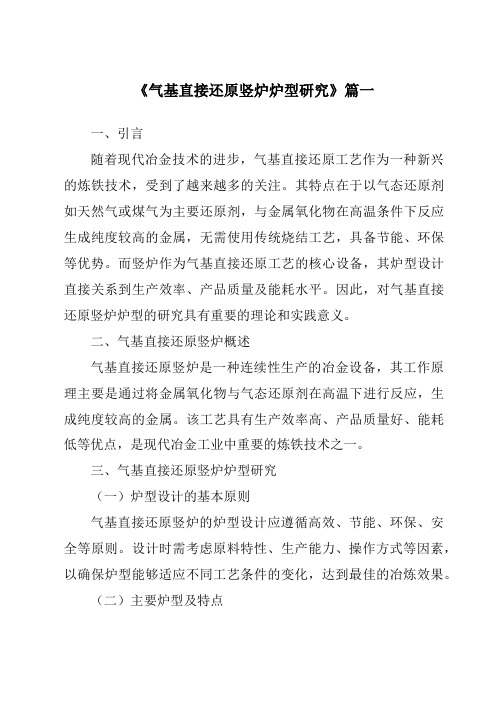
《气基直接还原竖炉炉型研究》篇一一、引言随着现代冶金技术的进步,气基直接还原工艺作为一种新兴的炼铁技术,受到了越来越多的关注。
其特点在于以气态还原剂如天然气或煤气为主要还原剂,与金属氧化物在高温条件下反应生成纯度较高的金属,无需使用传统烧结工艺,具备节能、环保等优势。
而竖炉作为气基直接还原工艺的核心设备,其炉型设计直接关系到生产效率、产品质量及能耗水平。
因此,对气基直接还原竖炉炉型的研究具有重要的理论和实践意义。
二、气基直接还原竖炉概述气基直接还原竖炉是一种连续性生产的冶金设备,其工作原理主要是通过将金属氧化物与气态还原剂在高温下进行反应,生成纯度较高的金属。
该工艺具有生产效率高、产品质量好、能耗低等优点,是现代冶金工业中重要的炼铁技术之一。
三、气基直接还原竖炉炉型研究(一)炉型设计的基本原则气基直接还原竖炉的炉型设计应遵循高效、节能、环保、安全等原则。
设计时需考虑原料特性、生产能力、操作方式等因素,以确保炉型能够适应不同工艺条件的变化,达到最佳的冶炼效果。
(二)主要炉型及特点目前,国内外气基直接还原竖炉的炉型主要分为固定床炉型、半连续式炉型和连续式炉型。
其中,固定床炉型结构简单,操作方便,但生产效率较低;半连续式炉型则通过优化炉体结构,提高了生产效率;连续式炉型则实现了连续性生产,具有更高的生产效率和产品质量。
各类型炉型均具有其独特的优点和适用范围,可根据实际生产需求进行选择。
(三)新型炉型研究针对传统炉型的不足,近年来学者们提出了一些新型的炉型设计。
如通过优化炉体结构、调整进料方式、改进排烟系统等措施,提高竖炉的热效率和还原效率。
同时,还研究了采用新型材料作为竖炉的保温材料和内衬材料,以提高竖炉的耐高温性能和耐腐蚀性能。
这些新型炉型的研究和应用,为气基直接还原竖炉的进一步发展提供了新的思路和方法。
四、研究方法与实验结果(一)研究方法本研究采用理论分析、数值模拟和实验研究相结合的方法。
首先通过查阅文献资料和实地考察,了解国内外气基直接还原竖炉的最新发展动态和趋势;然后运用数值模拟软件对不同炉型进行模拟分析,得出各炉型的优缺点及适用范围;最后通过实验研究验证模拟结果的准确性,并进一步优化炉型设计。
《气基直接还原竖炉流场研究及优化》范文

《气基直接还原竖炉流场研究及优化》篇一一、引言随着钢铁工业的快速发展,气基直接还原技术作为一种重要的炼铁技术,因其高效率、低能耗、环保等优点受到了广泛关注。
而竖炉作为气基直接还原技术中的核心设备,其流场性能直接影响着整个工艺的效率和产品质量。
因此,对气基直接还原竖炉流场的研究及优化具有重要意义。
本文将针对气基直接还原竖炉流场进行研究,分析其特点及存在的问题,并提出相应的优化措施。
二、气基直接还原竖炉流场概述气基直接还原竖炉流场主要由气体和固体颗粒组成。
在炼铁过程中,还原气体(如天然气、煤气等)与氧化铁矿石在高温条件下发生还原反应,生成铁水和其他物质。
同时,固体颗粒(如焦炭、石灰石等)在流场中起到传递热量和参与反应的作用。
气基直接还原竖炉流场的复杂性主要表现在气体和固体颗粒的相互作用以及反应过程中产生的各种物理化学变化。
三、气基直接还原竖炉流场研究1. 流场特性分析通过对气基直接还原竖炉流场的实际观察和数值模拟,可以发现在竖炉内部存在明显的气流分布不均现象。
由于气流在炉内的流动受到多种因素的影响,如炉内结构、气体性质、操作条件等,导致气流速度和方向在炉内发生较大变化。
此外,固体颗粒在流场中的运动也对流场特性产生影响。
2. 存在问题及原因分析在气基直接还原竖炉流场中存在的主要问题包括气流分布不均、温度波动大、能耗高等。
这些问题主要源于以下几个方面:一是炉内结构不合理,导致气流无法均匀分布;二是气体性质和组成影响气流的流动;三是操作条件不当,如风量、风压等参数设置不合理。
四、气基直接还原竖炉流场优化措施1. 优化炉内结构针对气流分布不均的问题,可以通过优化炉内结构来实现。
例如,改进风口设计,使气体更加均匀地进入炉内;优化炉体高度和直径比例,以改善气流在炉内的流动状况;在炉内增设导流板等装置,以引导气流流向。
2. 调整气体性质和组成通过调整气体性质和组成,可以改善气流的流动性能。
例如,调整还原气体的组成比例,使其更加适应反应的需要;对气体进行预处理,如除尘、脱硫等,以降低气体对炉内流场的影响。
《气基直接还原竖炉流场研究及优化》范文

《气基直接还原竖炉流场研究及优化》篇一一、引言气基直接还原法作为一种新兴的冶金工艺,已成为当今工业生产中的热门领域。
在此背景下,对于竖炉内流场的研究变得至关重要。
本论文将重点研究气基直接还原竖炉的流场特性,并通过优化手段提高其工作效率和产品质量。
二、竖炉流场研究背景及意义气基直接还原竖炉是冶金工业中重要的设备之一,其工作原理主要是通过高温和还原气氛将铁矿石进行还原反应,从而得到铁产品。
流场特性对竖炉的还原效率、产品质量以及能耗等方面具有重要影响。
因此,对竖炉流场的研究具有重要的理论意义和实际应用价值。
三、竖炉流场特性研究3.1 实验方法与设备本部分采用数值模拟和实验相结合的方法,对气基直接还原竖炉的流场特性进行研究。
通过搭建物理模型,结合数值模拟软件进行仿真分析。
3.2 流场特性分析通过仿真分析和实验数据,我们可以发现竖炉内部流场存在多种流动现象,如气体的快速流动、回流以及漩涡等。
这些现象都会对还原过程产生一定影响,如造成物料的不均匀还原、能耗增加等问题。
四、流场优化策略4.1 优化目标与原则针对竖炉流场存在的问题,我们提出以下优化目标:提高还原效率、降低能耗、保证产品质量。
在优化过程中,应遵循科学、合理、可操作的原则,确保优化措施的有效性。
4.2 具体优化措施(1)改进原料配比:根据竖炉的实际情况,调整原料的配比,使物料在炉内分布更加均匀,提高还原效率。
(2)优化风速控制:通过调整风速和风量,使气体在炉内分布更加均匀,减少涡流和回流现象,降低能耗。
(3)强化热工制度:通过调整炉温、加热速度等参数,使炉内温度分布更加均匀,提高还原反应的速率和效率。
(4)引入智能控制系统:通过引入智能控制系统,实时监测炉内温度、压力等参数,自动调整风速、风量等操作参数,实现自动化控制,提高工作效率和产品质量。
五、优化效果评估与展望5.1 优化效果评估经过一系列的优化措施后,我们对竖炉的流场特性进行了再次分析和评估。
《气基直接还原竖炉炉型研究》范文

《气基直接还原竖炉炉型研究》篇一一、引言随着钢铁工业的不断发展,对高效率、低能耗、环保型炼铁技术的需求日益增强。
气基直接还原法作为一种新型炼铁技术,以其高效率、低能耗和环保等优点,逐渐成为国内外研究的热点。
气基直接还原竖炉作为该技术的重要设备,其炉型的研究和优化对提高生产效率和产品质量具有重要意义。
本文将针对气基直接还原竖炉的炉型进行研究,为工业应用提供理论支持。
二、气基直接还原竖炉的工作原理及特点气基直接还原竖炉是一种以气体为还原剂,将铁矿石直接还原成海绵铁的设备。
其工作原理主要是通过高温和还原气氛,使铁矿石中的铁氧化物与气体中的氢气或一氧化碳等还原剂发生化学反应,生成海绵铁。
气基直接还原竖炉具有以下特点:1. 高温操作:炉内温度可达到1300-1500℃,有利于铁氧化物的还原反应。
2. 气体还原:以气体为还原剂,反应速度快,还原效率高。
3. 环保:无烟尘排放,减少了对环境的污染。
4. 灵活性:可以处理多种类型的铁矿石,适应性强。
三、气基直接还原竖炉的炉型研究炉型是气基直接还原竖炉的重要参数之一,合理的炉型设计对提高生产效率和产品质量具有重要意义。
目前,国内外对气基直接还原竖炉的炉型进行了大量研究,主要涉及以下几个方面:1. 炉体结构:包括炉身、炉腰、炉腹和炉底等部分的形状和尺寸。
合理的结构可以提高炉内温度分布的均匀性,降低能耗。
2. 风口布置:风口是气体进入炉内的通道,其布置方式对炉内气氛的均匀性和还原效率有很大影响。
研究不同风口布置方式对炉内气氛和还原效率的影响,为优化风口布置提供依据。
3. 排烟系统:排烟系统对炉内气氛的稳定性和能耗有很大影响。
研究不同排烟方式对炉内气氛和能耗的影响,为优化排烟系统提供依据。
4. 炉料分布:炉料在炉内的分布对反应速度和产品质量有很大影响。
研究不同炉料分布方式对反应速度和产品质量的影响,为优化炉料分布提供依据。
四、实验研究及结果分析为了研究气基直接还原竖炉的炉型,我们进行了大量的实验研究。
神雾的最新的转底炉直接还原技术国际领先

神雾的最新的转底炉直接还原技术国际领先神雾集团的核心节能与大气雾霾治理技术创新专利成果“蓄热式转底炉直接还原技术及成套工程化装备”,可处理各种低品位难选矿、复合共伴生矿、低品位红土镍矿、钢铁厂粉尘、有色行业冶金渣等劣质含铁资源。
该技术在高效提取复杂原矿中铁资源的同时,还能够实现对Ni、Ti、V、K、Na、Pb、Zn等元素的协同提取和高值化利用。
该项技术摒弃传统高炉烧结、焦化等高能耗、高污染工序的弊端,对原料的适应性广,只采用普通煤炭资源,就能节能、环保、高效、经济的实现劣质含铁矿物的高效清洁冶炼。
从目前我国铁矿资源来看,普遍存在含铁品位低、含铁矿物粒度细、矿物组成复杂的特点,劣质含铁资源占国内铁矿石储量的97%以上。
此外,现有钢铁厂大量的含铁粉尘、有色行业每年产生的上亿吨冶金废渣的综合开发利用也已迫在眉睫。
为满足高炉炼铁对优质铁矿石资源的刚性需求,国内钢铁企业长期从国外进口优质铁矿石,在进口铁矿石价格谈判上十分被动,这使得积极开发国内现存的大量低品位劣质含铁资源意义重大。
神雾蓄热式转底炉直接还原技术处理劣质含铁资源和冶金固废的技术指标先进:低品位难选矿金属化球团磨矿磁选铁粉品位大于90%,铁回收率大于85%;劣质含铁资源熔分铁回收率大于95%;红土镍矿金属化球团熔分可获得高镍铁,镍回收率大于95%。
神雾技术的工艺能耗较低,以沙钢含锌粉尘的转底炉处理工艺为例,单位产品的投资额相比国外转底炉降低约60%以上,单位产品能耗为209.3kgce,比回转窑工艺节能25%,比普通转底炉工艺节能16%,二氧化碳排放下降15%以上,作业率超过90%。
沙钢30万吨转底炉项目年新增产值3.52亿元、利润1.14亿元,投资回收期1.84年(不含建设期),项目具有较好的经济效益。
据不完全统计,我国每年约产生1800万吨含锌粉尘,如全部采用神雾转底炉直接还原冶炼技术进行处理,可生产直接还原铁球团1100万吨,解决6000多人就业,每年新增产值180亿左右,未来随着含锌粉尘量的不断提高,转底炉处理含锌粉尘将具有更加广阔的市场前景。
《气基直接还原竖炉炉型研究》

《气基直接还原竖炉炉型研究》篇一一、引言随着钢铁工业的不断发展,钢铁制造技术也日新月异。
其中,气基直接还原技术以其高效率、低能耗和环保特性成为了全球范围内广泛关注的研究领域。
气基直接还原竖炉作为该技术的重要组成部分,其炉型设计对生产效率和产品质量具有重要影响。
本文旨在研究气基直接还原竖炉的炉型,通过对现有炉型的分析,为改进炉型设计和提高生产效率提供理论依据。
二、气基直接还原技术概述气基直接还原技术是一种将铁矿石通过还原剂(如天然气、煤制气等)在高温下进行还原反应,得到铁基产品的工艺。
该技术具有高效率、低能耗、低污染等优点,被广泛应用于现代钢铁制造中。
三、气基直接还原竖炉的炉型研究(一)现有炉型分析目前,气基直接还原竖炉的炉型多种多样,主要包括圆形、椭圆形、矩形等。
这些炉型各有优缺点,如圆形炉型热效率高,但热应力大;矩形炉型热应力小,但热效率相对较低。
针对不同地区和不同需求,需要选用合适的炉型。
(二)新炉型研究针对现有炉型的不足,本文提出一种新型的气基直接还原竖炉炉型。
该炉型结合了圆形和矩形炉型的优点,采用特殊的结构设计,以降低热应力和提高热效率。
同时,该炉型还考虑了原料的进料方式、反应区的分布、热能的利用等因素,以实现更高的生产效率和更好的产品质量。
(三)实验验证与结果分析为了验证新型炉型的可行性和效果,本文进行了一系列的实验研究。
实验结果表明,新型炉型在热效率、生产效率和产品质量等方面均表现出较好的性能。
与现有炉型相比,新型炉型具有更高的生产效率和更好的产品质量,且在能耗和环保方面也有明显优势。
四、结论与展望本文通过对气基直接还原竖炉的炉型进行研究,提出了一种新型的炉型设计。
实验结果表明,新型炉型在热效率、生产效率和产品质量等方面均表现出较好的性能。
因此,本文认为新型炉型具有较大的应用潜力,可为钢铁企业提供更好的生产效率和产品质量。
未来,随着钢铁工业的不断发展,气基直接还原技术将得到更广泛的应用。
《气基直接还原竖炉炉型研究》
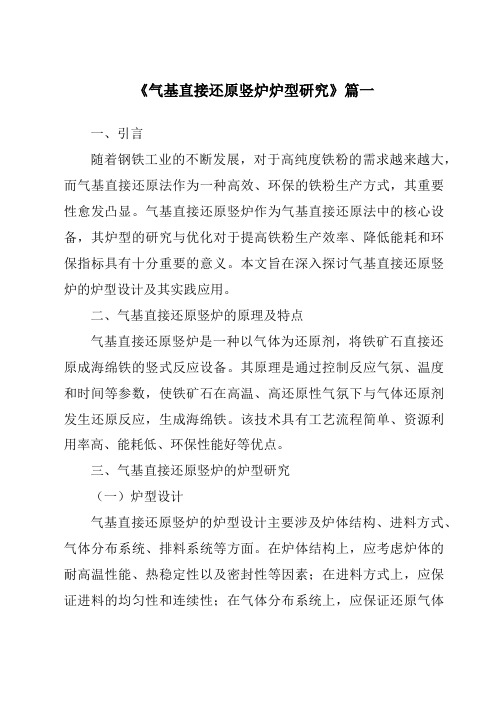
《气基直接还原竖炉炉型研究》篇一一、引言随着钢铁工业的不断发展,对于高纯度铁粉的需求越来越大,而气基直接还原法作为一种高效、环保的铁粉生产方式,其重要性愈发凸显。
气基直接还原竖炉作为气基直接还原法中的核心设备,其炉型的研究与优化对于提高铁粉生产效率、降低能耗和环保指标具有十分重要的意义。
本文旨在深入探讨气基直接还原竖炉的炉型设计及其实践应用。
二、气基直接还原竖炉的原理及特点气基直接还原竖炉是一种以气体为还原剂,将铁矿石直接还原成海绵铁的竖式反应设备。
其原理是通过控制反应气氛、温度和时间等参数,使铁矿石在高温、高还原性气氛下与气体还原剂发生还原反应,生成海绵铁。
该技术具有工艺流程简单、资源利用率高、能耗低、环保性能好等优点。
三、气基直接还原竖炉的炉型研究(一)炉型设计气基直接还原竖炉的炉型设计主要涉及炉体结构、进料方式、气体分布系统、排料系统等方面。
在炉体结构上,应考虑炉体的耐高温性能、热稳定性以及密封性等因素;在进料方式上,应保证进料的均匀性和连续性;在气体分布系统上,应保证还原气体的均匀分布和充分反应;在排料系统上,应保证排料的顺畅性和连续性。
(二)常见炉型分析目前,常见的气基直接还原竖炉炉型包括圆筒形炉、椭圆形炉和矩形炉等。
圆筒形炉具有结构简单、热效率高等优点,但存在热应力大、易变形等问题;椭圆形炉具有较好的热稳定性和耐高温性能,但制造成本较高;矩形炉则具有结构紧凑、空间利用率高等优点,但需考虑炉内气流分布的均匀性。
(三)新型炉型研究针对现有炉型的不足,研究人员提出了一些新型的气基直接还原竖炉炉型。
例如,一种新型的复合式竖炉,该炉型结合了圆筒形炉和矩形炉的优点,既具有较高的热效率,又具有较好的热稳定性和空间利用率。
此外,还有一些研究者通过优化进料方式和气体分布系统等手段,对现有炉型进行改进,以提高其生产效率和降低能耗。
四、实践应用及效果分析通过对不同炉型的实际应用和效果分析,可以发现新型炉型在提高生产效率、降低能耗和环保性能等方面具有显著优势。
《气基直接还原竖炉炉型研究》

《气基直接还原竖炉炉型研究》篇一一、引言随着全球钢铁工业的持续发展,气基直接还原技术已成为钢铁生产领域的重要技术之一。
气基直接还原竖炉(Direct Reduction Shaft Furnace)是这种技术中的核心设备之一,其炉型设计直接关系到生产效率、能源消耗和产品质量。
因此,对气基直接还原竖炉炉型的研究显得尤为重要。
本文将重点研究气基直接还原竖炉的炉型设计及其在钢铁生产中的应用。
二、气基直接还原竖炉的概述气基直接还原技术是一种利用气体还原剂(如天然气、煤制气等)将铁矿石或铁基废弃物在较低温度下进行直接还原的方法。
相较于传统高炉,该技术具有生产效率高、能源消耗低、环境污染小等优点。
气基直接还原竖炉是这种技术的重要设备,其原理是利用气体的热量和化学性质对铁矿石进行加热和还原。
三、气基直接还原竖炉的炉型设计(一)炉型结构气基直接还原竖炉的炉型结构主要包括进料系统、反应区、排料系统等部分。
其中,反应区是整个竖炉的核心部分,其设计直接影响着还原反应的效率和效果。
(二)关键参数1. 炉体高度与直径:炉体的高度和直径决定了竖炉的容量和反应空间,影响生产效率和产品质量。
2. 反应区设计:反应区的温度、气氛和流场分布是决定竖炉性能的关键因素。
应保证在较低的能耗下实现较高的反应速率和较好的产品品质。
3. 燃烧器布局:燃烧器布局影响炉内的热量分布和气流运动,进而影响竖炉的反应效率和能源消耗。
四、不同炉型的比较分析(一)传统竖炉与现代高效竖炉的比较传统竖炉结构简单,投资成本低,但生产效率较低,能源消耗大。
而现代高效竖炉采用先进的控制系统和热工技术,具有较高的生产效率和较低的能耗。
(二)不同类型的气基直接还原竖炉的比较不同类型的气基直接还原竖炉在结构、性能、适用范围等方面存在差异。
应根据具体的生产需求和资源条件选择合适的竖炉类型。
五、实际应用及优化建议(一)实际应用在实际生产中,应根据原料性质、产品要求、能源成本等因素选择合适的炉型和操作参数。
气基竖炉直接还原
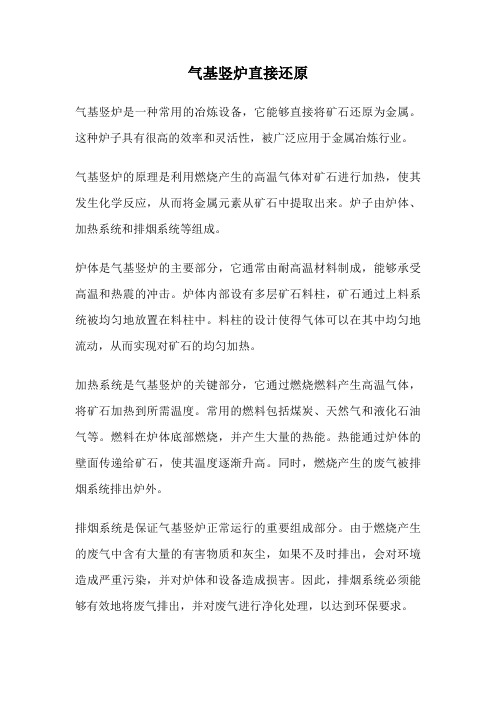
气基竖炉直接还原气基竖炉是一种常用的冶炼设备,它能够直接将矿石还原为金属。
这种炉子具有很高的效率和灵活性,被广泛应用于金属冶炼行业。
气基竖炉的原理是利用燃烧产生的高温气体对矿石进行加热,使其发生化学反应,从而将金属元素从矿石中提取出来。
炉子由炉体、加热系统和排烟系统等组成。
炉体是气基竖炉的主要部分,它通常由耐高温材料制成,能够承受高温和热震的冲击。
炉体内部设有多层矿石料柱,矿石通过上料系统被均匀地放置在料柱中。
料柱的设计使得气体可以在其中均匀地流动,从而实现对矿石的均匀加热。
加热系统是气基竖炉的关键部分,它通过燃烧燃料产生高温气体,将矿石加热到所需温度。
常用的燃料包括煤炭、天然气和液化石油气等。
燃料在炉体底部燃烧,并产生大量的热能。
热能通过炉体的壁面传递给矿石,使其温度逐渐升高。
同时,燃烧产生的废气被排烟系统排出炉外。
排烟系统是保证气基竖炉正常运行的重要组成部分。
由于燃烧产生的废气中含有大量的有害物质和灰尘,如果不及时排出,会对环境造成严重污染,并对炉体和设备造成损害。
因此,排烟系统必须能够有效地将废气排出,并对废气进行净化处理,以达到环保要求。
气基竖炉的优点主要体现在以下几个方面。
首先,它能够直接将矿石还原为金属,不需要经过其他复杂的冶炼过程。
其次,气基竖炉的加热效率高,能够快速将矿石加热到所需温度。
此外,由于燃烧产生的废气可以对矿石进行预热,从而进一步提高炉子的热效率。
最后,气基竖炉具有灵活性,可以根据不同的矿石和冶炼工艺进行调整和优化。
然而,气基竖炉也存在一些问题和挑战。
首先,燃料的选择和燃烧的控制对炉子的运行效果有着重要影响。
如果燃料质量不好或燃烧过程不稳定,会导致炉子温度不均匀,甚至无法正常运行。
其次,废气的处理和排放也是一个难题。
废气中含有大量的有害物质,需要经过复杂的净化处理才能排放到大气中。
另外,气基竖炉的建设和运营成本较高,需要投入大量的资金和人力物力。
气基竖炉是一种能够直接将矿石还原为金属的冶炼设备。
《2024年气基直接还原竖炉炉型研究》范文

《气基直接还原竖炉炉型研究》篇一一、引言随着全球钢铁工业的持续发展,对高效、环保、低能耗的炼铁技术需求日益增长。
气基直接还原技术作为一种新型炼铁技术,以其高效率、低能耗、低污染等优点,逐渐成为钢铁行业的研究热点。
气基直接还原竖炉作为该技术的重要组成部分,其炉型的设计与优化对炼铁过程和产品质量具有重要影响。
本文旨在研究气基直接还原竖炉的炉型,探讨其设计原则、优化方法以及实际应用效果。
二、气基直接还原竖炉的原理及特点气基直接还原技术是指以气体还原剂(如天然气、合成气等)与铁矿石在高温下进行还原反应,生产海绵铁的过程。
气基直接还原竖炉作为该技术的核心设备,其工作原理是将铁矿石与气体还原剂在竖炉内进行高温还原反应,通过控制反应条件,使铁矿石中的铁元素得以还原,并生成海绵铁。
气基直接还原竖炉具有以下特点:1. 高温反应:反应温度高,有利于提高铁的还原率。
2. 气体还原剂:使用气体还原剂,具有较高的还原能力。
3. 连续生产:采用连续生产方式,提高生产效率。
4. 环保节能:减少污染物排放,降低能耗。
三、气基直接还原竖炉型研究1. 炉型设计原则炉型设计是气基直接还原竖炉的核心环节,设计时应遵循以下原则:(1)合理性:根据生产需求和原料特性,合理设计炉体结构。
(2)高效性:优化反应过程,提高铁的还原率和生产效率。
(3)环保性:降低污染物排放,符合环保要求。
(4)可操作性:考虑设备维护、操作便捷等因素。
2. 炉型优化方法针对气基直接还原竖炉的炉型优化,可采取以下方法:(1)改进炉体结构:通过优化炉体结构,提高炉内温度分布均匀性,降低能耗。
(2)调整反应条件:通过控制反应温度、气体流量等参数,优化反应过程,提高铁的还原率。
(3)采用新型材料:使用耐高温、耐腐蚀的新型材料,提高设备使用寿命。
(4)智能化控制:引入自动化、智能化控制系统,实现生产过程的自动控制和优化。
3. 实际应用效果通过对气基直接还原竖炉的炉型进行设计和优化,实际应用效果显著。
《2024年气基直接还原竖炉炉型研究》范文
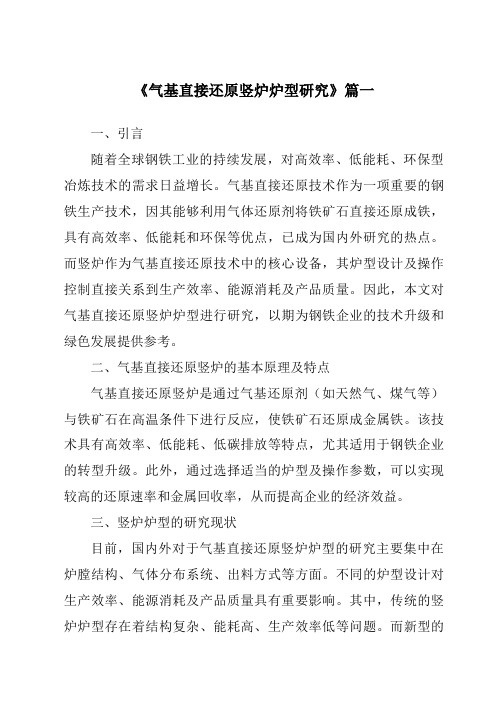
《气基直接还原竖炉炉型研究》篇一一、引言随着全球钢铁工业的持续发展,对高效率、低能耗、环保型冶炼技术的需求日益增长。
气基直接还原技术作为一项重要的钢铁生产技术,因其能够利用气体还原剂将铁矿石直接还原成铁,具有高效率、低能耗和环保等优点,已成为国内外研究的热点。
而竖炉作为气基直接还原技术中的核心设备,其炉型设计及操作控制直接关系到生产效率、能源消耗及产品质量。
因此,本文对气基直接还原竖炉炉型进行研究,以期为钢铁企业的技术升级和绿色发展提供参考。
二、气基直接还原竖炉的基本原理及特点气基直接还原竖炉是通过气基还原剂(如天然气、煤气等)与铁矿石在高温条件下进行反应,使铁矿石还原成金属铁。
该技术具有高效率、低能耗、低碳排放等特点,尤其适用于钢铁企业的转型升级。
此外,通过选择适当的炉型及操作参数,可以实现较高的还原速率和金属回收率,从而提高企业的经济效益。
三、竖炉炉型的研究现状目前,国内外对于气基直接还原竖炉炉型的研究主要集中在炉膛结构、气体分布系统、出料方式等方面。
不同的炉型设计对生产效率、能源消耗及产品质量具有重要影响。
其中,传统的竖炉炉型存在着结构复杂、能耗高、生产效率低等问题。
而新型的竖炉炉型则致力于解决这些问题,如采用多段式设计、优化气体分布系统等手段提高竖炉的生产效率和降低能耗。
四、新型竖炉炉型的研究及设计思路针对传统竖炉的不足,本文提出一种新型的气基直接还原竖炉炉型。
该新型炉型具有以下特点:1. 简化结构:通过优化炉膛结构,减少不必要的部件,使竖炉结构更加简单、紧凑。
2. 高效气体分布:设计合理的气体分布系统,确保还原剂在炉内均匀分布,提高还原速率和金属回收率。
3. 多段式设计:根据反应过程的需要,将竖炉分为多个反应段,每段采用不同的温度和气氛控制,以提高生产效率和降低能耗。
4. 智能化控制:采用先进的自动化控制系统,实时监测炉内温度、压力等参数,实现自动化控制,提高生产效率和产品质量。
五、实验与结果分析为了验证新型竖炉炉型的实际效果,我们进行了实验室模拟实验和工业试验。
《气基直接还原竖炉炉型研究》范文
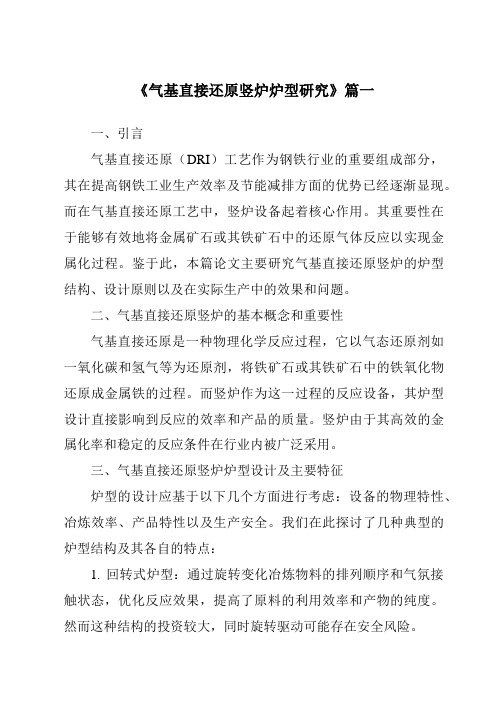
《气基直接还原竖炉炉型研究》篇一一、引言气基直接还原(DRI)工艺作为钢铁行业的重要组成部分,其在提高钢铁工业生产效率及节能减排方面的优势已经逐渐显现。
而在气基直接还原工艺中,竖炉设备起着核心作用。
其重要性在于能够有效地将金属矿石或其铁矿石中的还原气体反应以实现金属化过程。
鉴于此,本篇论文主要研究气基直接还原竖炉的炉型结构、设计原则以及在实际生产中的效果和问题。
二、气基直接还原竖炉的基本概念和重要性气基直接还原是一种物理化学反应过程,它以气态还原剂如一氧化碳和氢气等为还原剂,将铁矿石或其铁矿石中的铁氧化物还原成金属铁的过程。
而竖炉作为这一过程的反应设备,其炉型设计直接影响到反应的效率和产品的质量。
竖炉由于其高效的金属化率和稳定的反应条件在行业内被广泛采用。
三、气基直接还原竖炉炉型设计及主要特征炉型的设计应基于以下几个方面进行考虑:设备的物理特性、冶炼效率、产品特性以及生产安全。
我们在此探讨了几种典型的炉型结构及其各自的特点:1. 回转式炉型:通过旋转变化冶炼物料的排列顺序和气氛接触状态,优化反应效果,提高了原料的利用效率和产物的纯度。
然而这种结构的投资较大,同时旋转驱动可能存在安全风险。
2. 圆筒形炉型:结构简单,易于操作和维护,适合大规模生产。
但其在反应过程中,对物料的搅拌效果相对较弱,因此影响还原反应的效率。
3. 椭圆形或锥形炉型:此类设计可改善气体和矿石之间的混合状态,增加混合强度,从而提高冶炼效率。
但其设计复杂,对操作要求较高。
四、实际生产中的效果和问题在生产实践中,我们发现不同的炉型设计对生产效率和产品质量都有显著影响。
虽然回转式炉型具有较高的冶炼效率和产物纯度,但其高投资和可能的操作风险使得其在某些场合并不适用。
而圆筒形炉型虽然操作简单,但在某些特定的冶炼条件下,其效率可能无法满足生产需求。
对于椭圆形或锥形炉型,虽然其冶炼效率较高,但需要更精细的操作和维护。
此外,我们也发现了一些普遍存在的问题:一是由于气基直接还原过程中的高反应温度和复杂气氛环境,设备的耐热和耐腐蚀性是亟待解决的问题;二是设备内部的气流控制和物料的混合效率问题也影响到了产品的质量;三是操作成本的问题也需要通过提高设备效率等途径来逐步解决。
《2024年气基直接还原竖炉炉型研究》范文

《气基直接还原竖炉炉型研究》篇一一、引言随着全球钢铁工业的持续发展,气基直接还原技术已成为钢铁生产领域的重要技术之一。
气基直接还原竖炉作为该技术的重要组成部分,其炉型设计、操作控制及工艺优化等方面均对提高钢铁生产效率和产品质量具有重要意义。
本文将围绕气基直接还原竖炉的炉型展开研究,以期为钢铁工业的技术进步和效率提升提供有益的参考。
二、气基直接还原竖炉的基本概述气基直接还原竖炉是利用气体还原剂与铁矿石在高温下直接反应,生产出铁水的一种工艺设备。
其核心工艺是将含铁原料(如铁矿、球团矿等)与气态还原剂(如天然气、煤气等)在炉内进行连续的高温反应,以实现铁的直接还原。
竖炉的炉型设计直接关系到反应的效率、产品质量以及能耗等关键指标。
三、气基直接还原竖炉的炉型研究(一)炉型结构气基直接还原竖炉的炉型结构主要包括进料系统、反应区、排料系统等部分。
其中,进料系统负责将含铁原料均匀地送入炉内;反应区是进行铁的还原反应的主要场所;排料系统则负责将反应后的产品从炉内排出。
在炉型设计上,应考虑原料的物理化学性质、反应机理、热量传递等因素,以确保反应的顺利进行。
(二)关键参数与影响因素炉型设计中的关键参数包括炉身高度、炉径大小、风口位置及数量等。
这些参数直接影响着反应区的温度分布、气流流动及停留时间等关键因素。
此外,原料的粒度、含铁量、气体的流量和组成等也会对炉型设计产生影响。
在研究过程中,应综合考虑这些因素,以实现最佳的炉型设计。
(三)新型炉型的设计与优化针对传统竖炉的不足,新型的气基直接还原竖炉设计应考虑更高的反应效率、更低的能耗以及更好的环境保护性能。
通过改进进料方式、优化风口布置、采用新型的保温材料等方式,可以有效提高炉内的热量利用率和反应效率。
此外,还应注重炉型设计的灵活性和可扩展性,以满足不同生产需求的变化。
四、案例分析以某钢铁企业的气基直接还原竖炉为例,通过对该企业现有炉型的运行数据进行深入分析,发现存在进料不均、温度分布不合理等问题。
《2024年气基直接还原竖炉炉型研究》范文

《气基直接还原竖炉炉型研究》篇一一、引言随着现代冶金技术的快速发展,气基直接还原工艺作为新型冶金工艺备受关注。
其中,竖炉作为该工艺的核心设备,其炉型的设计和优化对提高生产效率、降低成本、保证产品质量具有重要意义。
本文将就气基直接还原竖炉炉型展开深入研究,为优化竖炉设计和操作提供理论依据。
二、气基直接还原竖炉工艺概述气基直接还原工艺是指利用还原性气体(如CO、H2)在高温条件下直接将铁矿石还原成铁水的过程。
竖炉作为该工艺的主要设备,具有设备结构简单、投资成本低、操作灵活等优点。
然而,在实际生产过程中,竖炉的炉型设计仍存在诸多问题,如热效率低、能耗高、环境污染等。
因此,对竖炉炉型进行深入研究具有重要的现实意义。
三、气基直接还原竖炉炉型研究现状目前,国内外学者对气基直接还原竖炉炉型进行了大量研究。
从研究现状来看,主要关注以下几个方面:1. 炉体结构:包括炉体高度、直径、料层厚度等参数的优化设计。
2. 气体分布系统:研究气体分布的均匀性、气流速度等对还原过程的影响。
3. 排料系统:研究排料方式、排料速度等对竖炉生产效率的影响。
4. 热量传递与热效率:研究竖炉内的热量传递过程,提高热效率,降低能耗。
四、气基直接还原竖炉炉型设计原则在进行气基直接还原竖炉炉型设计时,应遵循以下原则:1. 考虑原料性质:根据原料的物理化学性质,选择合适的炉型结构。
2. 保证气体分布均匀:确保还原性气体在炉内分布均匀,提高还原效率。
3. 提高热效率:优化热量传递过程,降低能耗。
4. 考虑操作灵活性:设计应具有足够的操作灵活性,便于生产过程中的调整和维修。
五、新型气基直接还原竖炉炉型研究针对现有竖炉存在的问题,本文提出了一种新型的气基直接还原竖炉炉型。
该炉型在以下方面进行了优化:1. 改进了炉体结构:通过增加预热段、优化反应段和设置冷却段,使竖炉更加适应连续生产的需求。
2. 优化了气体分布系统:采用多级分布器,确保气体在炉内的均匀分布。
《气基直接还原竖炉炉型研究》

《气基直接还原竖炉炉型研究》篇一一、引言气基直接还原(DRI)工艺在钢铁生产领域具有重要意义。
通过这种技术,人们能够将含铁矿石高效地还原成金属铁。
在这一过程中,竖炉作为关键设备,其炉型设计直接关系到生产效率、能源消耗以及产品质量。
因此,对气基直接还原竖炉炉型的研究显得尤为重要。
本文旨在探讨气基直接还原竖炉的炉型研究,为优化工艺和设备设计提供参考。
二、气基直接还原竖炉概述气基直接还原竖炉是一种用于将含铁矿石还原成金属铁的设备。
其工作原理主要是通过使用气态还原剂(如天然气、煤气等)与含铁矿石在高温下进行反应,实现矿石的还原过程。
由于这一过程中产生的产品(金属化球团矿)具有优良的冶金性能,使得其在钢铁生产中有着广泛的应用。
三、气基直接还原竖炉炉型研究(一)炉型结构气基直接还原竖炉的炉型结构主要包括进料系统、反应区、排料系统等部分。
其中,进料系统负责将含铁矿石均匀地送入反应区;反应区是矿石还原的主要场所,其设计应考虑到温度控制、气体分布和矿石的还原反应;排料系统则负责将反应后的产品从炉内排出。
(二)炉型研究重点1. 温度控制:在气基直接还原过程中,温度是影响反应速率和产品质量的关键因素。
因此,研究如何合理控制炉内温度,使其在最佳范围内波动,是炉型研究的重要一环。
2. 气体分布:气基直接还原过程中,气体的分布对反应的均匀性和效率有着重要影响。
因此,研究如何优化气体分布系统,使气体在炉内均匀分布,是提高生产效率和产品质量的关键。
3. 炉体结构:炉体结构的设计应考虑到设备的耐用性、热效率以及维护成本等因素。
合理的炉体结构能够提高设备的运行效率,降低生产成本。
(三)新型炉型研究针对传统气基直接还原竖炉的不足,研究者们提出了一些新型炉型。
这些新型炉型在进料系统、反应区设计、排料系统等方面进行了优化,旨在提高生产效率、降低能耗和改善产品质量。
四、研究成果与应用通过对气基直接还原竖炉的炉型研究,我们可以得出以下结论:合理的温度控制和气体分布系统能够提高生产效率和产品质量;新型炉型在实际应用中表现出较好的性能,具有较高的推广价值。
《2024年气基直接还原竖炉炉型研究》范文

《气基直接还原竖炉炉型研究》篇一一、引言随着全球钢铁工业的持续发展,对高效、环保、低能耗的炼铁技术需求日益增长。
气基直接还原法作为一种新兴的炼铁技术,其核心设备——竖炉,对生产效率和产品质量起着至关重要的作用。
因此,对气基直接还原竖炉炉型的研究显得尤为重要。
本文旨在深入探讨气基直接还原竖炉的炉型设计及其优化策略,为实际生产提供理论支持。
二、气基直接还原竖炉的基本原理及工艺流程气基直接还原法是一种利用气体还原剂(如天然气、合成气等)将铁矿石直接还原成海绵铁的炼铁方法。
其基本原理是利用高温气体与铁矿石进行化学反应,实现铁的还原过程。
整个工艺流程主要包括矿石预处理、气基还原、渣铁分离和铁产品精炼等环节。
其中,竖炉作为关键设备,主要承担气基还原的作业。
三、气基直接还原竖炉炉型的现状与问题分析当前,国内外气基直接还原竖炉的炉型设计各异,主要存在以下问题:一是炉体结构复杂,导致操作难度大、能耗高;二是炉内温度分布不均,影响还原反应的进行;三是炉型设计缺乏针对性,难以满足不同原料和工艺的需求。
因此,对炉型进行优化研究具有重要的现实意义。
四、气基直接还原竖炉炉型优化策略针对上述问题,本文提出以下炉型优化策略:1. 简化炉体结构:通过优化炉体结构设计,降低设备的复杂性和操作难度,从而降低能耗。
同时,简化结构有助于提高设备的可靠性,降低故障率。
2. 优化温度分布:通过改进气流分布系统,实现炉内温度均匀分布。
这不仅可以提高还原反应的效率,还有助于减少能耗和环境污染。
3. 针对性设计:根据不同原料和工艺需求,设计不同规格和结构的竖炉。
例如,针对高品位矿石和低品位矿石,可以分别设计不同的进料口和反应区结构。
4. 引入先进技术:如智能控制技术、热工技术等,实现对竖炉的精确控制和高效运行。
智能控制系统可以实时监测炉内状况,自动调整参数,以适应不同工况;热工技术则可以提高热能的利用效率,进一步降低能耗。
五、研究方法与实验结果本文采用理论分析和实验研究相结合的方法,对气基直接还原竖炉的炉型进行深入研究。
《气基直接还原竖炉流场研究及优化》范文

《气基直接还原竖炉流场研究及优化》篇一一、引言随着钢铁工业的快速发展,气基直接还原技术作为一种重要的炼铁技术,其应用越来越广泛。
气基直接还原竖炉作为该技术的重要组成部分,其流场特性的研究对于提高生产效率、降低能耗和改善环境质量具有重要意义。
本文旨在研究气基直接还原竖炉的流场特性,并提出相应的优化措施。
二、气基直接还原竖炉概述气基直接还原竖炉是一种利用气体还原剂将铁矿石还原成铁水或铁粉的设备。
其工作原理主要是通过在高温下,利用还原性气体与铁矿石发生还原反应,从而实现铁的提取。
气基直接还原竖炉的流场特性对反应过程、能耗及产品质量具有重要影响。
三、流场研究方法及模型为了研究气基直接还原竖炉的流场特性,本文采用数值模拟和实验研究相结合的方法。
首先,建立气基直接还原竖炉的三维模型,并运用计算流体动力学(CFD)技术对流场进行数值模拟。
其次,通过实验测量验证数值模拟结果的准确性。
最后,根据流场特性分析结果,提出相应的优化措施。
四、流场特性分析通过对气基直接还原竖炉的流场特性进行分析,发现存在以下问题:一是气体分布不均匀,导致局部区域反应不充分;二是流速过快或过慢,影响还原反应的进行;三是炉内温度分布不均,导致产品质量不稳定。
针对这些问题,本文提出了以下优化措施:1. 优化气体分布:通过调整气体喷嘴的位置和角度,使气体在炉内分布更加均匀,从而提高反应效率和产品质量。
2. 控制流速:根据反应需求,合理控制气体流速,避免流速过快或过慢,以保证还原反应的顺利进行。
3. 调整炉内温度:通过控制加热装置和气体成分,使炉内温度分布更加均匀,从而提高产品质量稳定性。
五、实验验证及结果分析为了验证上述优化措施的有效性,本文进行了实验研究。
通过调整气体喷嘴、流速和温度等参数,观察炉内流场特性的变化。
实验结果表明,经过优化后,气基直接还原竖炉的流场分布更加均匀,反应效率得到提高,能耗降低,产品质量更加稳定。
六、结论及展望本文通过对气基直接还原竖炉的流场特性进行研究及优化,提出了相应的优化措施。