57000DWT散货船船体建造原则工艺
57000吨散货船上层建筑整体吊装方案设计

De s i g n o f S u p e r s t r u c t u r e Un i t Li f t i n g f o r 5 7 0 0 0 DW T Bu l k Ca r r i e r
QI U J i a o mi n , HUANG T i a n we n
( 1 )保证整体 吊装过程 中上建结构不被破 坏 ; ( 2 )最大 限度地保证 上建 的舾 装及结 构完整性 , 以及 结构及舾装件 不被损伤 ;
( 2)吊排 布 置 在前 后 围壁 。根 据桥 楼 甲板 与前
( 3 )尽可 能的减少材 料浪费 ,减少重 复施工 ,保 后 围壁 的结构形 式 ,有效利 用 围壁 伸 出甲板 的特点 , 吊排可布 置在前 后 围壁板上 ,采用 焊接形 式与 围壁板 证 方便施工 。
( 3)吊排布 置 在 左右 侧 壁 。根 据 桥楼 甲板 与左
作者简 介 :邱 角敏 ( 1 9 8 1 - )男 , 助理工程 师。主要从 事船舶设 计工作。
黄添文 ( 1 9 8 5 - )男 , 助理工程师。主要从事船舶设 计工作。
收稿 日期 :2 0 1 2 — 0 4 — 2 6
1 引 言
本文 根据 公 司限 于龙 门 吊的起重 能力 不 能满 足约
结构局形式 ,选取 吊排 的位置 。
同 时 ,位 置 的选取 还需 要考 虑到 材料成 本 、施 工
4 0 0 吨上层 建筑总段 吊装 ,需租用 浮 吊完成上层建 筑总 成本 和方便施工等 因素 。 5 7 0 0 0 吨散货船 的上建整体 的 吊装方案选取 ,主要 段 吊装 的情况 ,设 计在建 的5 7 0 0 0 吨散货船 上层建 筑总
.
五万七散货船施工要领
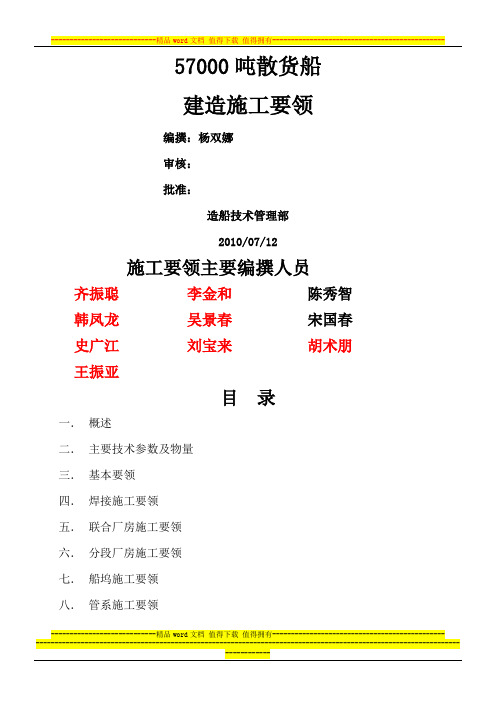
57000吨散货船建造施工要领编撰:杨双娜审核:批准:造船技术管理部2010/07/12施工要领主要编撰人员齐振聪李金和陈秀智韩凤龙吴景春宋国春史广江刘宝来胡术朋王振亚目录一.概述二.主要技术参数及物量三.基本要领四.焊接施工要领五.联合厂房施工要领六.分段厂房施工要领七.船坞施工要领八.管系施工要领----------------------------精品word文档值得下载值得拥有----------------------------------------------九.电装施工要领十.甲舾施工要领十一.涂装施工要领1.概述:本船是为香港宏达国际船务公司建造的57000吨用于无限航区贸易航运散货船,运煤矿、铁矿、谷物、铁卷及干货。
不装载甲板货及危险品等。
船型:本船为单机单桨、单壳型散货船,柴油机驱动,载重57000吨散货船。
1.1船东和工程编号船东:香港宏达国际船务公司工程编号:NB001—1、NB001—2/31.2规范和入级NB001—1、NB001—2/3 本船包括其机械装置和设备应按 LR规范设计和建造。
入级:LR级挂旗:香港旗1.3建造质量检验标准:按CSQS、GB、CB和新港船舶重工有限责任公司有关标准。
1.4建造日成计划表:工程编号NB001-1 NB001-2 NB001-3开工: 2010/08/30 2010/11/01 2010/11/30漂浮状态: 2010/03/10 2011/04/30 2011/04/30出坞: 2011/04/30 2011/06/15 2011/06/15试航: 2011/07/10 2011/08/15 2011/08/25交船: 2011/07/30 2011/08/30 2011/09/152.主要技术参数和物量2.1 船型参数:总长 189.98m垂涎间长 185.0m型宽 32.26m----------------------------精品word文档值得下载值得拥有----------------------------------------------型深 18.10m设计吃水 11.20m结构吃水 12.85m航速 14.30kn(11.20m吃水)主机: MAN-B&W 6S50MC-C8型数量: 1台CMCR: 输出功率: 9960KW, 转数:127rpm发电机: 600KW×3台载重量:(结构吃水12.85m时,平浮状态下,海水密度1.025t/m3,载重吨约为)57000t2.2船体结构参数:2.2.1甲板间高上甲板~A甲板3.10mA甲板~B甲板 2.80mB甲板~C甲板 2.80mC甲板~驾驶甲板 2.80m驾驶甲板~罗经甲板 2.85m2.2.2甲板梁拱主甲板梁拱(折角直线梁拱) 0.7m驾驶甲板 0.10m罗经甲板 0.10m其它甲板梁拱 0机舱平台 0首部升高 02.2.3肋距和双层底主船体肋距艉~FR12 600m/mFR12~FR217 820m/mFR217~艏 600m/m货舱双层底高度 1780m/m机舱双层底高度 1980m/m克令吊 4台2.3主要物量:分段总数: 84个坞内钩数: 30钩(不包括舱口围、克令吊及围屋)----------------------------精品word文档值得下载值得拥有----------------------------------------------空船重量:~ 10900吨钢板:~ 9340吨( 船体8492 t 舱盖~ 800 t 铁舾~210t)全船管子重量:~ 270吨电缆总长度:~130 km除锈涂装面积:~ 162000 m22.4本船特点:主甲板为露天连续干舷甲板,设置艏楼,带球鼻首。
57000T船体大合拢原则工艺
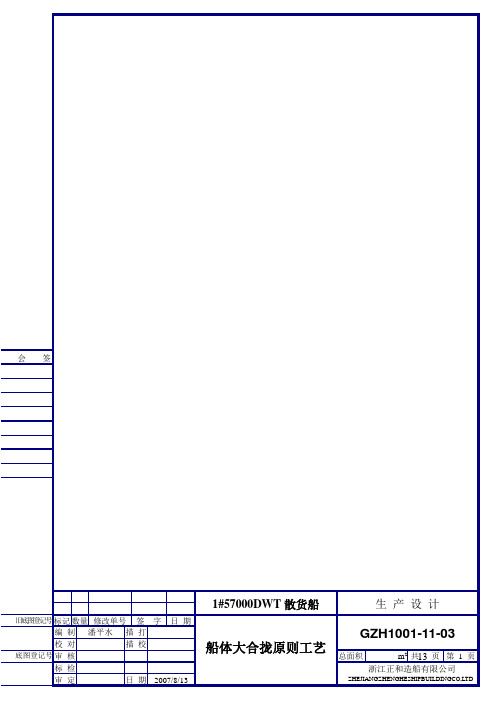
审 定 日 期 2007/8/13 标 检审 核校 对 描 校编 制 潘平水 描 打1#57000DWT 散货船 生 产 设 计 船体大合拢原则工艺 GZH1001-11-03 浙江正和造船有限公司ZHEJIANGZHENGHESHIPBUILDINGCO,LTD 标记 数量 修改单号 签 字 日 期总面积 m 2 共 页 13 第 页 1 会 签旧底图登记号 底图登记号57000DWT散货船大合拢原则工艺1.基本尺寸:1.1.基本尺寸:总长:189.99m 垂线间长:185.00m 型宽:32.26m 型深:18.00m 设计吃水:11.30m 结构吃水:12.80m 1.2.甲板层高度上甲板—A甲板 2.70m A甲板—B甲板 2.70m B甲板—C甲板 2.70m C甲板—桥楼甲板 2.70m 桥楼甲板—罗径甲板 2.60m 1.3 .甲板梁拱主甲板550mm 艏楼甲板: 150mm 艉楼甲板: 150mm 罗经甲板: 150mm 其它甲板无梁拱1.4.基本点高度所在位置和距基线高度:距BL艉楼甲板端点: 17470mm 艉上甲板端点: 14250mm 艉封下端点: 9000mm 艉轴管中心线: 3100mm 艏上甲板端点: 15347mm 艏楼甲板端点: 17734mm 艏舷墙:(艏端点)18834mm 1.5.全船肋距艉——FR13#650mm FR13#——FR201#770mm FR201#——艏650mm 1.6.龙骨高度(距基线BL)本数据为理论尺寸(仅供参考)艉:FR6# (2500mm)FR8# (200mm)FR9#-FR206# (0 mm)艏:FR211#(550mm)FR215#(750mm)2.概况2.1.本船为钢质、货舱机舱为双层底.货舱双层底及顶、底边舱为纵骨架式结构;机舱部位、艏、艉部位及上层建筑为横骨架式结构.全船划分为208个分段,参见《船体分段划分图》(DX31-01-2)3.分段上船台大合拢前技术要求:3.1.分段装焊基本完工.船台合拢分段指一般分段或总组后的分段(以下同义).3.2.分段预舾装装焊完毕.3.3.分段内结构焊接经检验符合要求,分段大接头两端构件应预留300mm缓焊区,待分段大合拢完毕后再焊接,以便于构件对接时调节工作的进行.3.4.分段局部变形或缺陷经校正或修补完毕.3.5.分段完工后测量其外形尺寸及形位公差均应符合CSQS《中国造船质量标准》(CB/T4000-2005)的要求.3.6.分段按涂装工艺要求涂装.(涂装工艺由施工单位编制,本厂涂装课确认.)3.7.经船东和船级社验船师认可.3.8.每个分段应报完工测量并以表格形式记录备查,同时应将该测量数据反馈给有关技术、制造、质检部门,以供分段合拢时参考.3.9.分段上船台前,应认真检查吊马的设置及电焊等是否符合吊马工艺要求.3.10.分段上的定位肋位线、分段中心线等检验线要勘划就绪.3.11.分段上船台的临时支撑应合理设置并预制完毕.4.船台准备4.1.船台中心线的确定;用激光经纬仪在船台中心预埋件上勘划船台中心线并打上洋冲印,用色漆标示,红漆打底,白漆划线;中心线偏差在±1mm之内.4.2.船台肋位检验线,在船台中心线预埋件上逐档或间隔5档划出肋骨位置线,并用色漆标上肋位号码.4.3.制作标准高度标杆,应在船台两侧预制固定的标杆,在标杆上按型线放样提供的数据划出基线、水线、甲板边线等全部理论高度线,作为船台布墩、分段吊装定位、船体合拢基线和测量变形等的高度基准.4.4.作为测量基准的船中心线、肋位检验线、高度标杆应做成不可移动的永久性的固定标志.4.5.分段上船台前应进行船台划线,划线前应对船台进行彻底清理,然后按照船台布置图进行划线.4.6.施工单位应对船台划线进行检查,并申报质检、船检认可.4.7.船台布墩按《船台布墩图》(GZH1001-11-06)执行,确保合拢过程中船体有足够的刚性.5.船台大合拢工艺5.1.本船大合拢在#1船台上进行,以CB03P/S、CB04P/S、CT21PCS为总组分段(CB04P/S)为基准定位分段,向前、后,左、右延伸分段顺序吊装,呈“塔式”建造法。
【开题报告】57000DWT散货船船台大合拢工艺设计

开题报告船舶与海洋工程57000DWT散货船船台大合拢工艺设计一、综述本课题国内外研究动态,说明选题的依据和意义:现代造船工艺是在综合采用先进制造技术和现代科学管理的条件下研究船舶建造过程及方法的一门应用科学。
造船工艺的主要任务是建立最佳的船舶生产工艺系统,包括船舶建造方案、制造方法和工艺流程、工艺装备、施工精度标准及检测方法,以及最大限度应用现代科学技术成果和扩大新技术应用。
现在,工艺学的概念本质已从狭义扩展到广义,从技术手段、原材料、信息、生产资源、计划控制系统到自然环境保护等,均在生产过程中有所体现。
造船工艺已经成为缩短船舶建造周期、提高建造质量和降低建造成本,甚至是实现生产与社会、自然和谐发展的关键因素。
我国现代造船工艺源于上世纪50年代的前苏联造艇技术的引进,60年代开始了自主工艺科研,70年代取得了一批有影响的成果。
1978年3月,全国科学大会召开,是年12月十一届三中全会的召开,有力地促进了造船工艺技术的发展。
改革开放30年,我国造船工艺为我国造船工业的巨大发展起到了强劲助力的作用。
这30年可以分为80年代、90年代、新世纪以来三个发展阶段。
80年代造船工艺发展的典型特征是焊接工艺水平显著提高,基本解决了我国造船高效焊接问题;同时,成组技术和生产设计开始在我国造船界推行。
90年代造船工艺的发展着力点放到了造船模式的转换上,特别是引进造船成组技术和推行生产设计,通过造船工艺技术、设计与生产体制全面学习日本,以中间产品组织生产为基本特征的现代造船模式得以初步确立。
新世纪以来,尤其是近几年来,船舶市场持续兴旺的大好契机,我国造船工艺技术围绕着推进建立现代造船模式、流程再造、建造方式、工法和工艺装备等的创新获得了快速发展。
中国造船的产能也得到了快速扩充,据不完全统计,在建的或者在5年内要形成产能的30万吨级干船坞不下30个,加上已有的,估计在40个左右,加上阿芙拉型和苏伊士型船坞和船台,以及所配置的起重能力都是十分巨大的,一个船坞一般配置两台龙门吊,抬重能力在1200吨,有些企业单台起重能力将突破1500吨,我国造船产能在造船设施上已基本具备了世界第一的条件(这也是其他造船国家称雄世界的必由之路)。
散货船分段涂装生产设计及原则工艺

资料范本本资料为word版本,可以直接编辑和打印,感谢您的下载散货船分段涂装生产设计及原则工艺地点:__________________时间:__________________说明:本资料适用于约定双方经过谈判,协商而共同承认,共同遵守的责任与义务,仅供参考,文档可直接下载或修改,不需要的部分可直接删除,使用时请详细阅读内容高等教育自学考试毕业设计(论文)题目57000DWT散货船分段涂装生产设计及原则工艺专业班级游艇设计与制造姓名赵飞指导教师姓名、职称李庆宁教授所属助学单位武汉船舶职业技术学院2014年5月16 日57000DWT散货船分段涂装生产设计及原则工艺学院:武汉理工大学专业:船舶与海洋工程姓名:赵飞指导教师:李庆宁目录一、开题报告………………………..………………3-5二、涂装生产设计(分段涂装)1.分段示意图 (6)2.涂装明细表………………………..………………6-73.油漆明细表 (7)4.施工说明………………………..………………8-9三、涂装原则工艺………………………..………………10-20四、设计总结五、参考文献武汉理工大学本科生毕业设计(论文)开题报告大学生本科毕业设计是对我大学本科期间专业综合知识水平的一次全面检验。
毕业设计水平的好坏直接反映了我整个大学期间对专业知识掌握情况好坏。
大学毕业设计是我毕业前的最后一次大型课程设计,是对我专业知识的掌握和运用能力的全面检验,它涉及到的知识量大,繁琐复杂,而且要求严格,不同于平时的小打小闹。
这也是我毕业前的最后一次实践,我要好好珍惜这个机会,得以好好的锻炼自己,提升自己的能力。
我这次设计的内容是《57000吨散货船船涂装生产设计及原则工艺》。
涂装生产设计的由来船舶的涂装工作,主要指船体及各种钢铁构件的除锈和涂料涂敷作业。
对于建造一艘新船来说,涂装工作贯穿于整个建造过程,并与船舶的装焊、管系、机电设备、舾装件的安装有密切关系。
57000DWT散货船舵叶制作工艺的改进探讨

( 1 )细化 工艺 流程及 工艺要 求 ,在 高度方 向上将
① 焊接后变形造成 四角水平翘起约 1 5 ~ 2 0 H u n ,后 以距基4 8 5 0 m m为中心向上 下两端加放 的1 0 m l T l 的反变
作者简介 :李德派 ( 1 9 8 5 一),男 ,助理工程师。主要从事船舶建造工艺工作。
( 2)舵 叶 的 直线 度 、尾 边 圆钢 的直 线 度 、舵 叶
① 施 工过程 中施工工 艺未严格执行 ,如坡 口间隙
上下 封板 的垂 直度及 上下端 面 中心对 称度在公 差范 围 偏大 、未采用 正确的焊接顺序 和焊接参数 ; ② 铸钢件定 位时未加 放反变形 ,以致 焊接后 上翘 内 ,舵 叶的四角水平度满足镗床划线要求 ;
Di s c us s a me l i o r a t i o n a b o ut t he 5 7 0 0 0 DW T bul k c a r r i e r r udde r bl a de ma nu f a c t ur e t e c hn i c s
( 3 )舵杆承座 、舵销承座轴孔 的 中心偏差程度 在 水平超差 ;
公差范 围内 ,能满足镗孑 L 要求 。
③ 高度方 向上加放 的反变形 不够 ,焊接后水平偏
差大。
2 存在 问题及原 因分析
前几艘 同型船 的舵 叶制 作 时 ,一般 仅对 高度方 向 3 改进措 施 加 放反变形 ( 即以距 基4 8 5 0 r n l T l 为 中心 向上下两 端放 l O m m的反变形 )。现以N 2 2 6 船为例进行分析 。 ( 1 ) 存 在的主要问题 结 合前几 艘船 的舵 叶测量数 据 ,对施工 工艺 作 出
浅析57000 DWT散货船船体生产设计
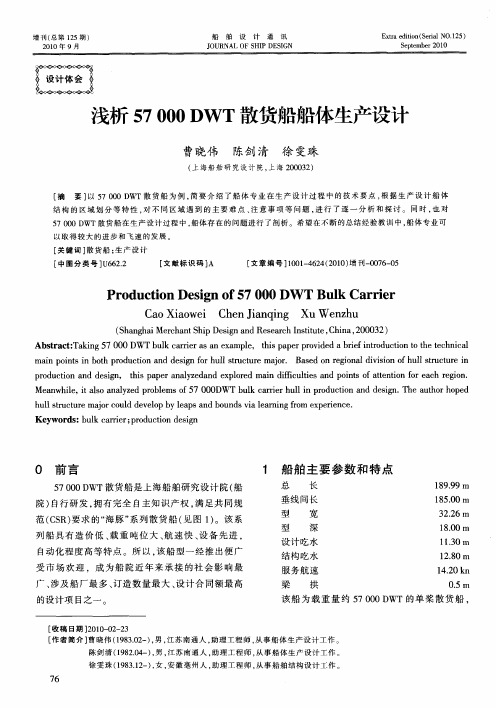
1 .0m 80
范 ( S 要 求 的“ 豚 ” 列散 货 船 ( 图 1 。该 系 C R) 海 系 见 )
列 船具 有 造 价 低 、 重 吨 位 大 、 速 快 、 备 先 进 . 载 航 设
宽
深
设计 吃水
结 构吃水
1. 1 0m 3
1. 28 0m
的设 计 项 目之一 。
该 船 为 载 重 量 约 5 0 WT的单 桨 散货 船 , 70 0D
[ 收稿 日期 ]0 0 0 — 3 2 1— 2 2 [ 作者 简 介 ] 晓伟 (9 30 一 , , 苏 南 通 人 , 理 工 程 师 , 事 船 体 生 产设 计 工 作 。 曹 18. )男 江 2 助 从 陈剑 清 (9 2 4 )男 , 苏 南通 人 , 理 工 程师 , 事 船 体生 产 设 计 工 作 。 18 . 一 , 江 0 助 从 徐 雯 珠 (9 31一 , , 徽 亳 州人 , 理 工 程 师 , 事 船 舶结 构设 计 工 作 。 18 . )女 安 2 助 从
p o u t n a d d sg , t i a e n l z d n x lr d ma n d f c l e n on so t n i n fr e c e i n r d ci n e i n o h sp p ra ay e a d e p o e i i u t sa d p it fa t t a h r g o . i i e o o Me n i , t lo a a y e r b e f5 0 DW T b l a i rh l i r d ci n a d d sg . h u h rh p d a wh l i a s n l z d p o l mso 7 O 0 e uk c r e ul n po u t n ein T ea to o e o
57000T散货船双层底结构设计 船体

毕业论文(设计)57000T散货船双层底结构设计摘要船底位于船体的最下部,是保证船体总纵强度和局部强度的重要构件。
作用在船底上的力主要有:(1)总纵弯曲引起的压伸应力和压缩应力。
(2)局部横向载荷:船底板架承受底部水压力,液舱内液体的压力,货物和机器设备的重力及船舶进坞时龙骨墩的反支力。
(3)偶然载荷:船舶搁浅或航行于浅水时,船底可能与河床摩擦。
而双层底除了船底板外,还有一层内底板,当船底在触礁和搁浅等意外情况下遭到破损时,双层底能保证船舶的安全。
双层底结构有利于提高船舶抗沉性,确保航行安全。
本文阐述的主要内容是57000T散货船双层底结构从设计到现场施工的具体施工工艺。
关键词:船舶双层底目录实习单位简介 (4)第一章船舶的主要参数 (7)第二章双层底结构的设计原则 (8)1 船底骨架形式的选择原则 (8)2 双底骨架设计 (9)(1)中桁材和旁桁材 (9)(2)箱形中底桁 (10)(3)纵骨 (10)(4)实肋板 (11)(5)水密肋板 (12)(6)开孔 (12)第三章双层底胎架的制作 (13)1画胎架格线 (13)2 在平台上竖立模板 (13)3模板画线 (14)4切割模板 (14)5 安装纵向角钢和边缘角钢 (14)第四章双层底的装焊 (15)1 双层底分段正造法 (15)2 外底板的拼接 (15)3 内底板的拼接 (16)4 在底板上画纵横构架线 (16)5 纵横构件的安装 (16)6 内底纵骨的装焊 (16)7 焊接 (16)8 内底板的装焊 (17)9 分段完工画线 (17)10 分段翻身 (17)11 检验 (18)12 涂装 (18)致谢 (18)参考文献 (20)实习单位简介南通明德重工有限公司成立于2004年10月,位于江苏省南通市通州区五接镇,是一家迅速崛起的以船舶与海洋工程修造为主业的民营企业,目前总投资额近2亿美元。
公司地处长江南通段北侧的泓北沙下游,江岸线长1600米,占地近2000亩。
散货船驳船船体建造原则工艺

散货船驳船船体建造原则工艺1 目的为了确保各项目建造质量,指导各项目的船体建造和施工,特制定本通用工艺。
2 适用范围本原则工艺规定了本船船体建造的工艺要求及过程,适用于公司内所有船舶产品的建造过程。
3 引用文件相关造船质量标准。
4 材料用于船体建造的钢材是要经过船级社认可的标准品质的普通钢和高强度钢,所有钢料包括铸钢件和锻钢件都要在质量上符合船级社的要求。
普通钢和高强度钢用于主船体的建造,高强度钢和普通钢又可清楚地识别。
没有经过船级社认定的钢材要符合船舶行业标准和建造方的标准。
所有船体构件的尺寸都要基于结构吃水进行计算,并得到船级社的认可。
船级社没有明确要求的构件,其尺寸要符合建造方的标准。
5 船体建造(通用工艺)5.1 钢材表面预处理本船满足PSPC规定,预处理及涂装要求必须符合本船涂装原则工艺;本船所有板材及型材均应进行钢材表面预处理,钢材经预处理后,材料的牌号、钢号及炉批号等应及时跟踪标注。
5.2 放样下料5.2.1 放样间地板应保持平整,其局部不平度,以3米平直尺在任何方向检查,不得超过5mm。
线条宽度不大于0.1mm~0.12mm,线条应光顺连续,粗细均匀,不应有间断和不清楚的地方;5.2.2 船体型线放样时,对型线图中型值的修改,一般不要超过型线图面比例;5.2.3 样板形状准确,边缘与零件展开面的曲线轮廓相符合,其结构牢固,防止变形,制作好的样板应根据其用途不同划上必要的线条与标记,如角尺线、检验线、外板或甲板接缝线、船体中心线、水平检验线、胎架中心线、所属产品名称及图号、零件名称、安装位置、材料规格、号料数量以及加工符号和余量数值等;5.2.4 样条和样杆截面均匀,边缘平直,变形小,各种标记清楚正确;5.2.5 船体理论线见《理论线图》及各分段结构图;5.2.6 下料前,应清除钢材表面的铁锈、油污、检查表面有无缺陷,边缘有无裂缝、分层,如发现钢板表面有大量麻点、氧化铁压入物等表面缺陷时,应及时与检验部门联系,并按《中国造船质量标准》(2005 版)有关规定进行处理,应做好拓印存档工作;5.2.7 零件号料应用记号笔,不得使用油漆及硬质号料工具;5.2.8 严禁不必要的随意切割,切割后产生的缺陷应自行修补完整,不计工时。
57000吨散装货船船体建造工艺设计

船舶工程系毕业设计57000吨级N226散装货船船体建造工艺设计姓名:学号:2010年06月11日前言造船生产设计是从施工立场出发,通过设计形式,考虑高质量、高效率、短周期、并确保安全、合理组织造船生产的一种设计,它主要统筹和指导协调本船从设计开始至交船期间船舶建造各环节的相关工作。
民船的船舶设计过程通常分为初步设计、详细设计和生产设计。
初步设计和详细设计的大部分工作都是由科研院所来完成的,而生产设计一般都是由新船的建造单位来完成。
由于各单位的建造场地、加工设备以及起重能力的不同,即使是同一船舶,不同的建造单位,它的生产设计也是有所不同的。
本说明书是以广东中远船务有限公司为新船的建造单位,来阐述船舶生产设计的整个过程。
首先,对新建船舶(即TOXOTIS (特凯迪斯)N226 57000吨级散货船)以及公司的具体情况进行综合分析,确定新船的船台建造方案、船体的分段划分及分段装配原则工艺。
本说明书在编写过程中,得到了广东中远船务有限公司设计所及造船分厂的帮助和支持,在此深表谢意。
限于本人的知识水平,本说明书中的缺点和错误在所难免,恳请各位老师批评指正。
摘要本文主要针对TOXOTIS (特凯迪斯) N226 57000T级散装货船船体生产设计进行论述,从前期船厂生产能力和本船结构形式入手,分别对船舶的分段划分、船体分段的下料、装配顺序、焊接工艺、船体分段的总装过程进行了分析和叙述,提出了有效并适合船厂生产能力的装配、焊接工艺方案,为以后同类船舶的制造提供了有意义的参考。
关键词散装货轮;分段;制作工艺Bulk carrier;Block;Fabrication technics目录一.广东中远船务工程有限公司生产条件简介 (3)二.概述 (4)三.分段制造要领 (16)1.货舱区底部分段 (16)2.货舱区主甲横壁分段 (24)3.货舱区舷侧分段 (28)四.分段总组 (40)五.船坞合拢 (42)六.典型分段施工设计说明 (44)七.参考文献 (48)八.设计图纸 (49)一. 广东中远船务工程有限公司生产条件简介广东中远船务工程有限公司广州分公司是中远船务集团所属的大型专业化修船企业,是中国华南地区一流、国内十强修船企业,于1971年成立,并于2000年10月实行转制重组,2001年6月正式成为中远船务工程集团有限公司五大修船基地之一。
57000DWT散货船船体生产设计—货舱舷侧及顶边舱524534分段
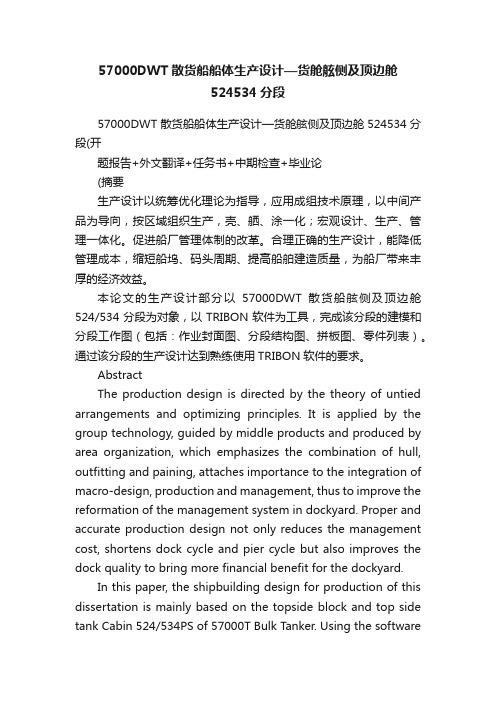
57000DWT散货船船体生产设计—货舱舷侧及顶边舱524534分段57000DWT散货船船体生产设计—货舱舷侧及顶边舱524534分段(开题报告+外文翻译+任务书+中期检查+毕业论(摘要生产设计以统筹优化理论为指导,应用成组技术原理,以中间产品为导向,按区域组织生产,壳、舾、涂一化;宏观设计、生产、管理一体化。
促进船厂管理体制的改革。
合理正确的生产设计,能降低管理成本,缩短船坞、码头周期、提高船舶建造质量,为船厂带来丰厚的经济效益。
本论文的生产设计部分以57000DWT散货船舷侧及顶边舱524/534分段为对象,以TRIBON软件为工具,完成该分段的建模和分段工作图(包括:作业封面图、分段结构图、拼板图、零件列表)。
通过该分段的生产设计达到熟练使用TRIBON软件的要求。
AbstractThe production design is directed by the theory of untied arrangements and optimizing principles. It is applied by the group technology, guided by middle products and produced by area organization, which emphasizes the combination of hull, outfitting and paining, attaches importance to the integration of macro-design, production and management, thus to improve the reformation of the management system in dockyard. Proper and accurate production design not only reduces the management cost, shortens dock cycle and pier cycle but also improves the dock quality to bring more financial benefit for the dockyard.In this paper, the shipbuilding design for production of this dissertation is mainly based on the topside block and top side tank Cabin 524/534PS of 57000T Bulk Tanker. Using the softwareTRIBON to complish the modeling and the working drawing of this block (including the covers of working drawing, the part list, the drawings of the structure, the drawings of the spell).We can be up on TRIBON and the techno-language of ship drawings through the design for production of the block.Keywords: Bulk Tanker, design for production, Tribon目录第一章绪论 11.1 综述 11.1.1散货船研究背景 11.1.2散货船的研究现状及发展 11.1.3 散货船特点及类型 11.1.4 国内外散货船的发展及趋势 3第二章造船生产设计 52.1 现代造船模式 52.1.1 现代造船模式的基本理念 52.1.2 现代造船模式的技术特征 52.1.3 现代造船模式与传统造船模式的比较 52.2造船生产设计的由来及其发展 62.2.1生产设计的由来 62.2.2生产设计是船厂推行现代造船模式的基础 72.2.3造船生产设计的发展 82.2.4生产设计的主要作用 102.3 TRIBON 软件介绍 112.3.1 TRIBON简介 112.3.2 Tribon软件主要模块 112.3.3 平面建模模块 122.3.4 装配计划模块(Assembly Planning) 122.3.5 TRIBON软件的二次开发深化了造船生产设计13 第三章57000DWT 散货船船体生产设计 143.1 57000DWT散货船的基本概述 143.2 57000DWT散货船的结构特点 143.3分段施工要领 153.4 524/534分段的划线及操作步骤 173.5 524/534分段生产设计 17第四章分段涂装施工要领 234.1涂装在船舶建造中的作用 234.2船舶涂料的特性 234.3涂装时的注意事项 234.4涂装方法 244.5漆膜厚度要求 244.6施工环境要求 24第五章524/534分段脚手架及吊环吊马的选择 265.1 脚手架图 265.2 分段翻身要领和吊环、吊马图 265.2.1 吊环的设置原则 265.2.2 对吊环制作与安装的工艺要求 275.3 524/534舷侧分段的变形处理和预防 285.4 524/534舷侧分段翻身和吊运要求 29结语 30致谢 31参考文献 32附录1:英文翻译原文附录2:524/534舷侧及顶边舱分段相关图纸(结构图,装配图,拼板图等)附录3:524/534舷侧及顶边舱分段零件明细表。
57000施工要领(散货船)

57000吨散货船建造施工要领编撰:杨双娜审核:批准:造船技术管理部2010/07/12施工要领主要编撰人员齐振聪李金和陈秀智韩凤龙吴景春宋国春史广江刘宝来胡术朋王振亚目录一.概述二.主要技术参数及物量三.基本要领四.焊接施工要领五.联合厂房施工要领六.分段厂房施工要领七.船坞施工要领八.管系施工要领九.电装施工要领十.甲舾施工要领十一.涂装施工要领1.概述:本船是为香港宏达国际船务公司建造的57000吨用于无限航区贸易航运散货船,运煤矿、铁矿、谷物、铁卷及干货。
不装载甲板货及危险品等。
船型:本船为单机单桨、单壳型散货船,柴油机驱动,载重57000吨散货船。
1.1船东和工程编号船东:香港宏达国际船务公司工程编号:NB001—1、NB001—2/31.2规范和入级NB001—1、NB001—2/3 本船包括其机械装置和设备应按 LR规范设计和建造。
入级:LR级挂旗:香港旗1.3建造质量检验标准:按CSQS、GB、CB和新港船舶重工有限责任公司有关标准。
1.4建造日成计划表:工程编号NB001-1 NB001-2 NB001-3开工: 2010/09/01 2010/11/01 2010/11/30漂浮状态: 2010/03/10 2011/04/30 2011/04/30出坞: 2011/04/30 2011/06/15 2011/06/15交船: 2011/07/30 2011/08/30 2011/09/152.主要技术参数和物量2.1 船型参数:总长 189.98m垂涎间长 185.0m型宽 32.26m型深 18.10m设计吃水 11.20m结构吃水 12.85m航速 14.30kn(11.20m吃水)主机: MAN-B&W 6S50MC-C8型数量: 1台CMCR: 输出功率: 9960KW, 转数:127rpm发电机: 600KW×3台载重量:(结构吃水12.85m时,平浮状态下,海水密度1.025t/m3,载重吨约为)57000t2.2船体结构参数:2.2.1甲板间高上甲板~A甲板3.10mA甲板~B甲板 2.80mB甲板~C甲板 2.80mC甲板~驾驶甲板 2.80m驾驶甲板~罗经甲板 2.85m2.2.2甲板梁拱主甲板梁拱(折角直线梁拱) 0.7m驾驶甲板 0.10m罗经甲板 0.10m其它甲板梁拱 0机舱平台 0首部升高 02.2.3肋距和双层底主船体肋距艉~FR12 600m/mFR12~FR217 820m/mFR217~艏 600m/m货舱双层底高度 1780m/m机舱双层底高度 1980m/m克令吊 4台2.3主要物量:分段总数: 84个坞内钩数: 30钩(不包括舱口围、克令吊及围屋)空船重量:~ 10900吨钢板:~ 9340吨( 船体8492 t 舱盖~ 800 t 铁舾~210t)全船管子重量:~ 270吨电缆总长度:~130 km除锈涂装面积:~ 162000 m22.4本船特点:主甲板为露天连续干舷甲板,设置艏楼,带球鼻首。
57000DWT大灵便型散货船详细设计概述[30136]
![57000DWT大灵便型散货船详细设计概述[30136]](https://img.taocdn.com/s3/m/045e4c50312b3169a451a49d.png)
8
船更高的货舱利用率。按照目前的国际公约和规则, 该型散货船为 B-60 型干舷, 应满足 1966 年载重线 公约第 27 条的破损稳性要求。 由于该船载重量和 货舱舱容很大,特别是第一货舱容积相对偏大,在方 案设计阶段我们就发现要满足破舱稳性要求具有一 定的难度,而且新 SOLAS-XII 的要求对货舱进水后 的稳性和强度控制提出更高的要求。 经过反复调整 分舱长度、压载系统的布置以及空气管位置,计算满 足稳性和强度要求的最佳搭配,反复计算平衡,最终 确定了目前的货舱布置方案。 该方案不仅有效地控 制了船舶总纵弯矩,实现了对结构重量的控制,同时 使货舱区域布置合理,达到货物装卸方便安全的要 求。
本船满足所有当时颁布的新规范,包括结构共 同规范、燃油舱保护规则、检验通道规则、新破舱稳 性规则等。
1 船舶主要性能和特点
1.1 船舶概况 本船为单机、定距桨、单舵、球鼻首、方尾,设有
单层连续甲板,机舱位于尾部;设有 5 个货舱,配备 5 对液压折叠式舱盖及 4 台甲板克令吊,设有首楼;
[收 稿 日 期 ]2008-11-3 [作 者 简 介 ]李 昆 仑 (1974.10-),男 ,高 级 工 程 师 ,从 事 船 舶 轮 机 设 计 及 项 目 管 理 工 作 。
张 卓(1979.11-),男,工程师,从事船舶总体设计工作。 郭 林 丽 (1977.6-),女 ,工 程 师 ,从 事 船 舶 轮 机 设 计 工 作 。 周 建 桦 (1982.11-),男 ,助 工 ,从 事 船 舶 电 气 设 计 工 作 。
6
李昆仑 张 卓 郭林丽 周建桦:57 000 DWT 大灵便型散货船详细设计概述Leabharlann 14.6 kn续航力
57000船建造方针
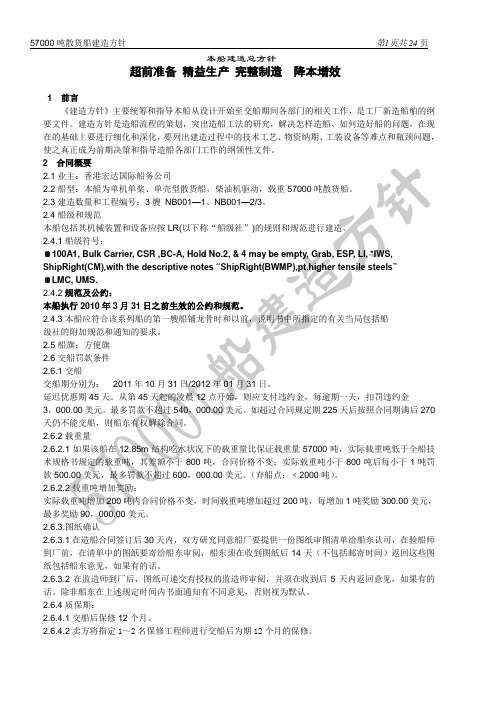
本船建造总方针超前准备精益生产完整制造降本增效1 前言《建造方针》主要统筹和指导本船从设计开始至交船期间各部门的相关工作,是工厂新造船舶的纲要文件。
建造方针是造船流程的策划,突出造船工法的研究,解决怎样造船、如何造好船的问题,在现在的基础上要进行细化和深化,要列出建造过程中的技术工艺、物资纳期、工装设备等难点和瓶颈问题,使之真正成为前期决策和指导造船各部门工作的纲领性文件。
2 合同概要2.1业主:香港宏达国际船务公司2.2船型:本船为单机单桨、单壳型散货船,柴油机驱动,载重57000吨散货船。
2.3建造数量和工程编号:3艘NB001—1、NB001—2/3。
2.4船级和规范本船包括其机械装置和设备应按LR(以下称“船级社”)的规则和规范进行建造。
2.4.1船级符号:✠100A1, Bulk Carrier, CSR ,BC-A, Hold No.2, & 4 may be empty, Grab, ESP, LI, *IWS, ShipRight(CM),with the descriptive notes “ShipRight(BWMP),pt.higher tensile steels”✠LMC, UMS.2.4.2规范及公约:本船执行2010年3月31日之前生效的公约和规范。
2.4.3本船应符合该系列船的第一艘船铺龙骨时和以前,说明书中所指定的有关当局包括船级社的附加规范和通知的要求。
2.5船旗:方便旗2.6交船罚款条件2.6.1交船交船期分别为:2011年10月31日/2012年01月31日。
延迟优惠期45天。
从第45天起的凌晨12点开始,则应支付违约金,每逾期一天,扣罚违约金3,000.00美元。
最多罚款不超过540,000.00美元。
如超过合同规定期225天后按照合同期满后270天仍不能交船,则船东有权解除合同。
2.6.2载重量2.6.2.1如果该船在12.85m结构吃水状况下的载重量比保证载重量57000吨,实际载重吨低于全船技术规格书规定的载重吨,其差额小于800吨,合同价格不变;实际载重吨小于800吨后每小于1吨罚款500.00美元,最多罚款不超过600,000.00美元。
57000DWT散货船船体生产设计
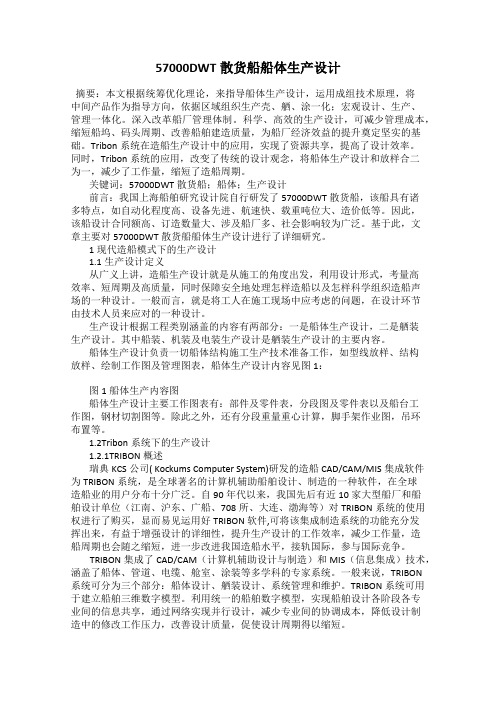
57000DWT散货船船体生产设计摘要:本文根据统筹优化理论,来指导船体生产设计,运用成组技术原理,将中间产品作为指导方向,依据区域组织生产壳、舾、涂一化;宏观设计、生产、管理一体化。
深入改革船厂管理体制。
科学、高效的生产设计,可减少管理成本,缩短船坞、码头周期、改善船舶建造质量,为船厂经济效益的提升奠定坚实的基础。
Tribon系统在造船生产设计中的应用,实现了资源共享,提高了设计效率。
同时,Tribon系统的应用,改变了传统的设计观念,将船体生产设计和放样合二为一,减少了工作量,缩短了造船周期。
关键词:57000DWT散货船;船体;生产设计前言:我国上海船舶研究设计院自行研发了57000DWT散货船,该船具有诸多特点,如自动化程度高、设备先进、航速快、载重吨位大、造价低等。
因此,该船设计合同额高、订造数量大、涉及船厂多、社会影响较为广泛。
基于此,文章主要对57000DWT散货船船体生产设计进行了详细研究。
1现代造船模式下的生产设计1.1生产设计定义从广义上讲,造船生产设计就是从施工的角度出发,利用设计形式,考量高效率、短周期及高质量,同时保障安全地处理怎样造船以及怎样科学组织造船声场的一种设计。
一般而言,就是将工人在施工现场中应考虑的问题,在设计环节由技术人员来应对的一种设计。
生产设计根据工程类别涵盖的内容有两部分:一是船体生产设计,二是舾装生产设计。
其中船装、机装及电装生产设计是舾装生产设计的主要内容。
船体生产设计负责一切船体结构施工生产技术准备工作,如型线放样、结构放样、绘制工作图及管理图表,船体生产设计内容见图1:图1船体生产内容图船体生产设计主要工作图表有:部件及零件表,分段图及零件表以及船台工作图,钢材切割图等。
除此之外,还有分段重量重心计算,脚手架作业图,吊环布置等。
1.2Tribon系统下的生产设计1.2.1TRIBON概述瑞典KCS公司( Kockums Computer System)研发的造船CAD/CAM/MIS集成软件为TRIBON系统,是全球著名的计算机辅助船舶设计、制造的一种软件,在全球造船业的用户分布十分广泛。
57000DWT大灵便型散货船详细设计概述[30136]
![57000DWT大灵便型散货船详细设计概述[30136]](https://img.taocdn.com/s3/m/045e4c50312b3169a451a49d.png)
6
李昆仑 张 卓 郭林丽 周建桦:57 000 DWT 大灵便型散货船详细设计概述
大灵便型散货船在整个散货船系列中有其自身 独特的优势:其尺度适合进出大多数港口;配备货物 吊,可自行完成装卸;对港口条件要求低,特别适合 印度等东南亚国家;适合运输包括煤、谷物、大米、水 泥等各种散货,同时其设计中对于钢卷板的运输进 行了特殊的考虑。
57 000 DWT 散货船是 2006 年上海船舶研究设 计 院 ( 以 下 简 称 “SDARI”) 根 据 船 舶 、 航 运 市 场 的 发
燃油储存舱、 柴油储存舱以及容积大于 30 m3 的油
舱全部采用双壳保护形式,设置洗舱污水存放舱和
淡水洗舱水舱; 主、 辅柴油机排气中的氮氧化物
(NOx)排放量满足 MARPOL73/78 附则 VI 的有关要
求。
1.2 主尺度及性能指标
总长
189.99 m
垂线间长
185.00 m
型宽
32.20 n mile
航区
无限
船员
26 人
1.3 船级规范、规则及公约
首制船入 BV 船级社,入级符号为:
BV HULL, MACH,Bulk carrier BC-A,GRAB (20),CSR,Holds 2,4 may be empty,ESP,unrestricted navigation,
通过对球首和尾部螺旋桨区域进行多次精心改 进,较好地解决了超大方型系数的尾部来流不畅影 响螺旋桨效率和风浪中失速的问题。 由于该船型批 量很大而且采用超大方形系数线型,因此对船舶的 操纵性、耐波性、螺旋桨空泡及激振力测试等进行了 全面的试验和分析比较,结果非常理想。 目前已交 付的 3 艘船舶, 在航行试验中的服务航速均达到 14.6 kn,傅氏数达到 1.76,表现出良好的快速性能, 且船舶振动及操纵性也完全符合合同要求,船东对 此非常满意。
- 1、下载文档前请自行甄别文档内容的完整性,平台不提供额外的编辑、内容补充、找答案等附加服务。
- 2、"仅部分预览"的文档,不可在线预览部分如存在完整性等问题,可反馈申请退款(可完整预览的文档不适用该条件!)。
- 3、如文档侵犯您的权益,请联系客服反馈,我们会尽快为您处理(人工客服工作时间:9:00-18:30)。
船体建造原则工艺一,概况该散货船为单桨、单舵、双底、单壳、全钢质焊接结构的自航式散货船,入“CCS”级挂五星红旗。
船体主尺度如下:船长L189.99m 型宽B 32.26m 型深D 18.00m OA设计吃水T 11.30m二,目的使参与57000DWT散货船建造的有关工程技术人员、生产管理人员、施工人员在生产施工过程中按照2006版CCS船级社规范/2006版CSR规范、法规和有关作业指导手的要求;更好地掌握施工要领、工艺流程要求;减少出错和返工;保证施工质量满足散货船建造的要求和生产进度按计划顺利进行。
最终达到该船建造能够按质按量按期完成。
三,施工图纸1,分段划分图全船分段划分总共为137个,主甲板以下117个,(机舱8个、艉部5个、货舱96个、艏部8个),主甲板以上20个(上建8个、舱口围5个、储藏室4个、舷墙1个、艏楼2个)。
2,预制分段结构图考虑到该艘船的交船周期比较紧凑加上本地区7月降雨量相对较大,分段在外场制造必然会受到天气因素的制约,和本厂正在扩建中船台数量相对较少等因素,故考虑将部分分段在车间内预制,部分分段在外场预制。
预制分段结构图中必须明确规定:材料名称规格、材质、数量、重量、构件面积、备注等明细表;还必须明确规定:使用的焊材、规格、焊接要求、使用范围、装焊次序、吊装(及反身)的吊环、检验要求、检测要求、精度控制和数控切割的构件在材料表和零件草图中标注清楚避免重复下料及所购钢材规格与下料图上板材规格之间的转换等。
四,施工要领1,材料、预处理本船主船体和上层建筑部分结构所用的钢材为CCSA、CCSB船用钢,主甲板大开口处采用CCSAH32、CCSAH36等高强度钢。
所用板材和型材均应符合或不低于中国船级社的要求;本船所用的焊接材料应符合中国船级社的有关要求,并经船级社认可;钢材订货到厂后,组织有关质检人员会同业主/船东代表、现场验船师和油漆商代表对材料的材质进行抽查核对;对外观、抛丸除锈的质量及喷保养漆的质量进行抽检验收;喷保养漆后应将钢材的材质牌号、规格、炉批号转移标明。
2,号料、下料、切割板材经预处理后才能进下料车间,经核对材质牌号、规格(钢材上的材质标记用色漆标出)无误后方可进行划线号料。
号料人员必须清楚零件图纸及图上的工艺信息;切割工不得一人看管二台或二台以上的半自动切割机,数控切割机由固定的专人负责操作。
具体要求如下:2.1,号料线粗大小≤1mm;2.2,零件边缘的直线度大小≤1mm,切割后≤2mm;2.3,零件对角线的允许偏差为0~+1.0mm;切割后允许偏差为0~+3.0mm;2.4,零件的宽度/长度允许偏差为0~ +1.0mm;切割后允许偏差为0~+2.0mm;2.5,零件曲线样板上任意点偏离允许偏差为:0~+1.0mm;切割后允许偏差为0~+2.0mm;2.6,零件剪切尺寸允许偏差为:± 2mm;剪切后打磨披锋;2.7,号料的零件上应标记:船名、零件标记、加工标记/余量线/检验线(须打印洋冲),拼接方向,零件装配方向,坡口形式、方向及尺寸;(参考有关的作业指导和工艺手册);2.8,(半)自动切割的预留切口量为3mm (板厚≤20mm), 预留切口量为4mm (板厚>20mm);切割后的零件自由边必须光顺,不得有氧化渣,弧坑(安装一侧必须补磨);2.9,(半)自动切割的切割面及尺寸偏差按有关工艺要求执行;2.10, 数控切割构件的标识符号按手工/半自动切割的要求(参考零件编号说明书);2.11,下料/切割前后需进行组内的检查、质量保障部要对下料零件拼板进行跟踪检查(可随机抽样检验),但对第一个零件,板材必须全面认真的检验,发现切割尺寸于图纸不符立即停止下料并通知技术人员,以免造成原材料的浪费。
2.12,下料切割后零件的材质、规格、炉批号必须做好记录;3,装配要求3.1,按生产计划安排的施工工位准备场地的清洁、划地样线;3.2,装配工使用的量具必须是经检验的合格品,并与检验员使用的量具进行核对误差值;3.3,按照胎架图的工艺材料和工艺信息进行胎架的预制、划出检验线(须打洋冲);3.4,有梁拱和曲面线型的胎架须用木样板划余量线及划检验线(须打洋冲);3.5,周边的胎架材料应适当加强、加密布置或大号规格的工艺材料;3.6,整个胎架焊接报验合格后才能进行余量切割、端口打磨光顺(以检验线为基准检查);3.7,铺基准面板与胎架固定:通过小板(50x80mm)来连接固定,与检验线之间的误差值≤+1mm;必须在其他地方(如墙壁/柱或另竖标杆等)有与胎架检验线一样的标高线;3.8,划构件安装的理论线的线粗≤1mm,余量按工艺要求预留;3.9,构件装配安装前必须先对过焊孔、流水孔、透气孔、止流孔、构件靠壁有间隙的边端进行打磨光顺,对剪切构件不得有披锋;3.10,主要结构的平行焊缝应保持一定距离,对接焊缝之间的平行距离不得小于100mm,对接焊缝与角接焊缝之间的平行距离不得小于50mm,具体详见施工结构图中的施工信息;3.11,不同板厚钢板对接处,其厚度差若大于或等于4mm时,厚板的削斜(均匀过渡)宽度不小于厚度差的4倍;3.12,型材的装配应用角尺装准,并在两侧加码板/扁铁点焊固定(不能与型材面平齐);3.13,如遇间段焊接的角焊接,装配的固定焊点必须在间段焊的焊接范围内;3.14,如遇有坡口的角/对接焊缝,装配的固定焊点尽可能在背面无坡口的一侧;3.15,如遇两边有坡口的角/对接焊缝,装配的固定焊点必须在小坡口的一侧或易回火清根一侧;3.16,如遇焊前难对焊缝进行打磨清洁的坡口,必须先打磨清洁好;3.17,装配的构件尺寸小于图纸,先采用前后左右分担误差,无法满足的则须先进行长焊、衬垫焊;3.18,有线型经冷/热加工的零件在装配时发现变形/加工误差太大,不得靠强加外力进行装配,必须有火工配合或返回重新进行冷/热加工;3.19,装配报验前必须做好必要的加强措施,防焊接变形、吊装变形;3.20,装配报验前必须在基准面板上/下用洋冲打出中心线,须与地样中心线重合;3.21,装配报验前必须实行自检互检,保证结构装配的完整性;3.22,装配报验前应将吊环/耳装配完(吊耳焊接采用低氢焊条);3.23,焊后离胎架,分段的中心线与地样中心线重合时进行检测焊接变形,确定调正方案;3.24,密切配合焊后的主尺寸检测记录,根据精度控制图看分段焊接完了后的误差控制情况如超过精度控制要求的要上报技术人员分析原因采去更先进的工艺;3.25,按施工工艺要求将不留合拢余量的余量切割和边缘打磨处理好;3.26,船台合拢的标高在未完成主尺度报验前必须保护完好不得改变、移动;3.27,分段合拢报验时,地样中心线必须投影到甲板面上、内底板、平台面板、船底板内侧并上打洋冲,洋冲位不准打在板的余量处,为防设备安装后舱内无法查找中心线则需在其他位置增加几个点,同样在各层平台、甲板面上应将地样中心线引到并打洋冲印;3.28,主体、上建等焊接件等焊接完成及主要的大型设备进舱后,配合进行船舶主尺度的测量:总长、两柱间长、型宽、型深、船体中心线与地样中心线、艏艉上翘值;等;3.29,主尺度报验后,进行六面水尺、载重线、干舷、船名、港籍名等的装焊报验;3.30,轻、重水线处按一定距离焊一段焊点:约高2mm宽3mm长30-40mm,平直部位:约隔2米、弯曲面部位:1米到1.5米,焊点底在水线标高处;4,构件预制4.1,构件拼装焊接在平台上进行构件的拼装,拼板时点焊固定的焊接材料选用E4303(对BVA、BVB选用Ф3.2mm或Ф4mm的酸性焊条,对铸锻件选用Ф3.2mm或Ф4mm的碱性焊条)。
纵/横向板对接焊缝选用Ф3.2mm焊条进行焊封底,对接焊缝采用埋弧自动焊,两端引弧板尺寸100x100mm,与焊接件同厚度,船傍/船底/甲板板板背面需清根确保全熔透焊。
对不同板厚的对接按理论线进行装配。
如下位置的构件需进行拼装用埋弧自动焊:船壳平直板、平台面板、舱壁板和甲板板等。
构件预制具体的工艺流程流程如下:构件材质及规格检查平台(胎架)上装配及固定焊封底埋弧自动焊QC抽检反面回火清根清洁 QC检查焊接修补焊路 QC 抽检焊后对焊接变形调正构件安装、固定及加强材焊前QC检查(对过焊孔、流水孔、透气孔、难打磨到自由边端必须安装前处理好)焊接焊后部分加强材拆除、补磨焊疤/弧坑、打磨焊珠、清洁离胎架拆固定焊/码板调正外观/主要尺寸QC检测(办交接登记手续)到下一道工序(分段预制)。
4.2,分段预制零件、冷热加工件和构件预拼装经检验合格后,运送到分段预制工位。
未能及时安装的构件必须临时堆放好避免因无序堆放或其他外力产生的零/构件变形。
在装配过程中点焊固定的焊接材料采用E4303焊条(对铸锻件等不同材质之间的点焊/焊接必须采用Ф3.2mm或Ф4mm 的碱性焊条)。
装配施工工艺流程如下:(严禁在外板对接时的装配码板焊在船壳外的一侧)清场地划地样线及检验立胎架、激光打水平(检验线)割正胎架、处理切割口检查铺基准面板及固定面板上划装配理论线及检验装配零/构件及固定装配加强材焊前QC检查(对过焊孔、流水孔、透气孔、难打磨到自由边端必须安装前处理好)焊接焊后部分加强材拆除、补磨焊疤/弧坑、打磨焊珠、清洁离胎架拆固定焊/码板调正外观/主要尺寸QC检测到下一道工序(分段内舾装二次除锈涂装合拢)5,焊接要求(详见焊接施工原则工艺)5.1,焊工作业人员必须持证上岗,施工操业必须符合证书规定作业内容/范围;5.2,使用焊材必须是经现场验船师认可在该船可以使用的焊材,并满足有关规定要求:不得有焊条/丝生锈、潮湿、油污、药皮开裂/脱落;使用焊条须经按规定要求处理;5.3,碱性焊条在使用过程中严格按有关规定进行通电保温、盖紧保温桶盖;5.4, 严禁碱性焊条在雨天使用;5.5,钢材/天气太潮湿须在施工开始时对焊接口进行加热除潮湿;焊进行焊接作业;5.6,在密闭舱室内严禁使用CO25.7,在进行CO焊时严禁采用风机正对施焊部位;25.8,在进行CO衬垫焊时,坡口及边缘的除锈打磨质量必须符合规范要求或工艺要求;25.9,在进行CO2衬垫焊时,陶瓷衬垫的粘贴必须稳固(坡口背面点焊装配码板可用铁丝来加稳固陶瓷衬垫,严禁贪图方便用焊条来加固陶瓷衬垫);5.10,对与板厚≤7mm的角/对接的焊接口必须采用CO2焊或采用Ф3.2/2.5mm的焊条;5.11,对与舷侧船壳板角/对接的焊接,能采用CO2焊的尽可能使用(半自动、手工);5.12,对主船体的外壳板对接尽可能使用埋弧自动焊(盖面焊);5.13,重要设备的吊环/耳,重量大分段的吊环/耳的焊接必须采用碱性焊条进行焊接,焊后必须进行磁探检查焊缝质量;5.14,严格执行焊接工艺流程、施焊次序、按焊接规格表要求控制焊脚尺寸,控制焊接变形达到最小量;5.15,焊后必须及时清洁焊缝、打磨焊珠、修补弧坑;5.16,对重要部位的焊接缝上原装配工点焊固定的焊点必须清除干净;5.17,对合拢缝手工焊接时,必须进行施焊前报验工作;5.18,密切配合施工报验和主体的无损探伤报验,认真完成检测出的缺陷修补工作。