《设备点检初》PPT课件
合集下载
设备点检基础知识ppt课件

12
13
14
15
16
17
18
19
20
根据前面六定制定点检记录表
设备日常点检记录
A班
设备编号: 2422889
序号
点检内容
1
清洁夹紧装置白色靠轮
2 开机检胶桶喉部润滑液面正常,无干胶 3 查 门锁保护开关在插入位置
4
涂胶机器人例行涂胶三至五分钟
5
机器人机械手臂转动灵活
6
控制箱上按钮和指示灯良好
涂 胶
正常
5 单 手动涂胶枪完好无损,出胶正常
6
元 举升机构功能正常,传感器完好
7
检查人机界面及手持单元外观无损坏,操作系统运行正 常
8
检查电柜空调及灯光正常工作
9
检查清胶机构工作正常,无异响
10
电控柜按钮指示灯报警灯完好无损,功能正常
11
检查加热温度在设定值内,胶型正常
12
检查电气柜空调正常工作
13 输 检查人机界面外观无损坏,操作系统运行正常 胶
班组长签名
序号
设备编号
缺陷描述
2
1
3
点检标记 : 工段长:
良好: √
带非功能性缺陷工作: #
备注:工段长和车间设备员负责设备点检的检查和监督并在每月的最后一个工作日进行签名。
4
5
故障不可用:
╳
故障修复: 车间设备员:
33
部门:
2012 年 6 月
工段(工位):1工段
A班
设备名称:
项目
内容
1 清洁控制柜、箱外表的灰尘和油污
日常点检情况记录 1 2 3 4 5 6 7 8 9 10 11 12 13 14 15 16 17 18 19 20 21 22 23 24 25 26 27 28 29 30 31
13
14
15
16
17
18
19
20
根据前面六定制定点检记录表
设备日常点检记录
A班
设备编号: 2422889
序号
点检内容
1
清洁夹紧装置白色靠轮
2 开机检胶桶喉部润滑液面正常,无干胶 3 查 门锁保护开关在插入位置
4
涂胶机器人例行涂胶三至五分钟
5
机器人机械手臂转动灵活
6
控制箱上按钮和指示灯良好
涂 胶
正常
5 单 手动涂胶枪完好无损,出胶正常
6
元 举升机构功能正常,传感器完好
7
检查人机界面及手持单元外观无损坏,操作系统运行正 常
8
检查电柜空调及灯光正常工作
9
检查清胶机构工作正常,无异响
10
电控柜按钮指示灯报警灯完好无损,功能正常
11
检查加热温度在设定值内,胶型正常
12
检查电气柜空调正常工作
13 输 检查人机界面外观无损坏,操作系统运行正常 胶
班组长签名
序号
设备编号
缺陷描述
2
1
3
点检标记 : 工段长:
良好: √
带非功能性缺陷工作: #
备注:工段长和车间设备员负责设备点检的检查和监督并在每月的最后一个工作日进行签名。
4
5
故障不可用:
╳
故障修复: 车间设备员:
33
部门:
2012 年 6 月
工段(工位):1工段
A班
设备名称:
项目
内容
1 清洁控制柜、箱外表的灰尘和油污
日常点检情况记录 1 2 3 4 5 6 7 8 9 10 11 12 13 14 15 16 17 18 19 20 21 22 23 24 25 26 27 28 29 30 31
【培训课件】设备点检培训幻灯片

【培训课件】设备点检培训 幻灯片
2023-10-30
目录
• 设备点检的重要性 • 设备点检的分类与操作 • 设备点检的技术与工具 • 设备点检的实践案例 • 设备点检的未来趋势与发展
01
设备点检的重要性
设备点检的定义
设备点检是指对设备进行预防性检查,定期对设备的关键部位、功能和性能进行 检查,以预防设备故障和停机。
机遇
通过智能化、自动化等技术应用,可以提高点检的效率和准 确性,降低人力成本;同时,通过预防性点检和精细化维护 ,可以提高设备的运行效率和寿命,为企业创造更多价值。
感谢您的观看
THANKS
04
设备点检的实践案例
案例一:某制造企业的设备点检实践
总结词
全面、精细、规范
详细描述
该制造企业在进行设备点检时,采用了全面的检查策略,不仅关注设备的运行状态,还对设备的维护和保养情 况进行了检查。同时,企业还制定了精细的点检标准,明确了各项检查内容和标准,使得点检工作更加规范和 可操作。
案例二:某化工企业的设备点检实践
维修操作规范
确保在维修过程中遵守维 修流程和操作规程,如使 用合适的工具、按照规定 的步骤进行维修等。
验收操作规范
在完成维修后,对设备进 行验收,确保设备恢复正 常运行状态,并记录验收 结果。
03
设备点检的技术与工具
设备点检的技术
直接观察法
通过直接观察设备运行状态, 检查设备是否有异常声音、震
动、磨损等情况。
设备点检的益处
提高设备的可靠性
通过定期检查可以及时发现潜在问 题,避免设备在生产过程中出现故 障,提高设备的可靠性和稳定性。
减少维修成本
设备点检可以预防设备重大故障, 避免生产中断和安全事故,减少维 修成本和采购成本。
2023-10-30
目录
• 设备点检的重要性 • 设备点检的分类与操作 • 设备点检的技术与工具 • 设备点检的实践案例 • 设备点检的未来趋势与发展
01
设备点检的重要性
设备点检的定义
设备点检是指对设备进行预防性检查,定期对设备的关键部位、功能和性能进行 检查,以预防设备故障和停机。
机遇
通过智能化、自动化等技术应用,可以提高点检的效率和准 确性,降低人力成本;同时,通过预防性点检和精细化维护 ,可以提高设备的运行效率和寿命,为企业创造更多价值。
感谢您的观看
THANKS
04
设备点检的实践案例
案例一:某制造企业的设备点检实践
总结词
全面、精细、规范
详细描述
该制造企业在进行设备点检时,采用了全面的检查策略,不仅关注设备的运行状态,还对设备的维护和保养情 况进行了检查。同时,企业还制定了精细的点检标准,明确了各项检查内容和标准,使得点检工作更加规范和 可操作。
案例二:某化工企业的设备点检实践
维修操作规范
确保在维修过程中遵守维 修流程和操作规程,如使 用合适的工具、按照规定 的步骤进行维修等。
验收操作规范
在完成维修后,对设备进 行验收,确保设备恢复正 常运行状态,并记录验收 结果。
03
设备点检的技术与工具
设备点检的技术
直接观察法
通过直接观察设备运行状态, 检查设备是否有异常声音、震
动、磨损等情况。
设备点检的益处
提高设备的可靠性
通过定期检查可以及时发现潜在问 题,避免设备在生产过程中出现故 障,提高设备的可靠性和稳定性。
减少维修成本
设备点检可以预防设备重大故障, 避免生产中断和安全事故,减少维 修成本和采购成本。
设备点检培训(PPT)

3 排污阀连接 目
受 磷 槽 目
无渗漏,无变形
责任人点检完成后签名
故障说明
1.点检每4小时一次,每点检一次进行一次记录,正常用“√”:发现异常或故障并已报修用“×”:小故障已有操作工即时排除用“○”:故障情况写入故障说明栏中。
2.操作工在润滑工作中做好五定:既1定人,2定机,3定时,4定量,5定油品进行润滑工作。
设备点检的“五定”
• • • • • 1定点——设定点检部位、项目和内容 2定法——设定点检方法 3定标——制定点检标准 4定期——设定点检周期 5定人——确定点检项目由谁实施
如何确定设备点检工作
各子公司主管设备的领导与设备员根据本部门各工序的 实际情况,按岗位划分责任区,按岗位工作内容制定设 备点检路线、设备点检标准、设备点检表(包括日常点 检表和专业点检表)。包括: 1、规定点检路线及点检设备。 2、规定设备点检事项,包括:设备卫生、润滑、冷却、 声响及要求监视和监测的特殊部位和运行参数等(如振 动、温度、压力等)。 3、确定点检频次和点检时刻,制定设备点检记录表。 4、规定设备点检记录的要求。 5、其它事项。 6、各子公司可根据实际情况制定各工序各岗位设备点检 的实施细则。
设备点检培训
设备点检培训内容
设备点检的定义
• 为了提高、维持生产设备的原有性能,通 过人的五感(视、听、嗅、味、触)或者 借助简单的工具、仪器,按照预先设定的 周期和方法,对设备上的规定部位(点) 进行有无异常的预防性周密检查的过程, 以使设备的隐患和缺陷能够得到早期发现、 早期预防、早期处理,这样的设备检查称 为点检。
专业点检频次 日常点检频次
电 机
电机接线盒 泵 填 料 电机轴承
每 每 每 每 每 每 每 每 每
设备点检ppt课件
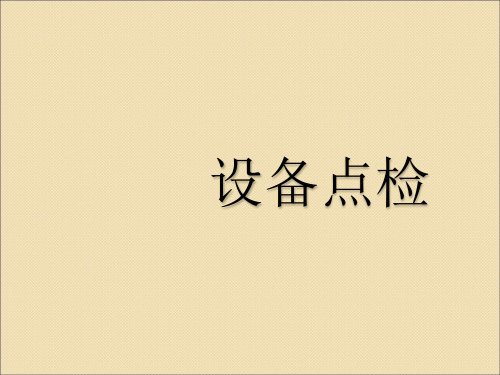
15
七、专职点检人员的点检 业务及职责
收集设备状态情报进行倾向管理、定量分析、 掌握机件劣化程度
参加事故分析处理,提出修复、预防及改善 设备性能的意见
提供维修记录,进行有关故障、检修、费用 等方面的实绩分析,提出改善设备的对策和 建议
参与精密点检
16
八、点检管理的四个环节
制定点检标准和点检计划(P) 按计划和标准实施点检和修理工程(D) 检查实施结果,进行实绩分析(C) 在实绩检查分析的基础上制定措施,自主改
视觉——视感的作用是首位的。通过观察,看准问题点,使脑神
经系统进入思考,把已有的知识和经验与看到的现象作比较,再 进行活动,并把问题记录下来,采取行动进行必要的处置。
听觉 ——听觉的作用不亚于视觉,人对声波的刺激是相当敏感的。
听到声响后,通过与已有的知识和经验进行比较,以找出异常点
触觉——触感与视感、听觉是密切联系的。有时触感是第一作用,
进(A) ——即PDCA循环
17
八、点检管理的四个环节
点检实施的PDCA管理循环
P --计划点检计划、维 修计划、维修费用预
算、周期管理表等
不断提高
D --执行点检、倾向 检查、施工配合、 协调、故障管理等
A –反馈调整业务、 修改计划、标准 等
C --检核记录、整理、 分析、实绩报告、对策 建议、评价等
13
六、点检员的基本素质
全面熟悉所管辖设备的结构、性能、设备 的操作维护规程 、检修规程;
有一定的设备管理理论、技术素质和实践 经验,能进行一般的制图;
有较强的故障判断能力,能使用简易的诊 断仪器;
有一定的协调能力与其他专业进行横向联 络。
14
七、专职点检人员的点检 业务及职责
收集设备状态情报进行倾向管理、定量分析、 掌握机件劣化程度
参加事故分析处理,提出修复、预防及改善 设备性能的意见
提供维修记录,进行有关故障、检修、费用 等方面的实绩分析,提出改善设备的对策和 建议
参与精密点检
16
八、点检管理的四个环节
制定点检标准和点检计划(P) 按计划和标准实施点检和修理工程(D) 检查实施结果,进行实绩分析(C) 在实绩检查分析的基础上制定措施,自主改
视觉——视感的作用是首位的。通过观察,看准问题点,使脑神
经系统进入思考,把已有的知识和经验与看到的现象作比较,再 进行活动,并把问题记录下来,采取行动进行必要的处置。
听觉 ——听觉的作用不亚于视觉,人对声波的刺激是相当敏感的。
听到声响后,通过与已有的知识和经验进行比较,以找出异常点
触觉——触感与视感、听觉是密切联系的。有时触感是第一作用,
进(A) ——即PDCA循环
17
八、点检管理的四个环节
点检实施的PDCA管理循环
P --计划点检计划、维 修计划、维修费用预
算、周期管理表等
不断提高
D --执行点检、倾向 检查、施工配合、 协调、故障管理等
A –反馈调整业务、 修改计划、标准 等
C --检核记录、整理、 分析、实绩报告、对策 建议、评价等
13
六、点检员的基本素质
全面熟悉所管辖设备的结构、性能、设备 的操作维护规程 、检修规程;
有一定的设备管理理论、技术素质和实践 经验,能进行一般的制图;
有较强的故障判断能力,能使用简易的诊 断仪器;
有一定的协调能力与其他专业进行横向联 络。
14
设备点检实务基础管理ppt课件
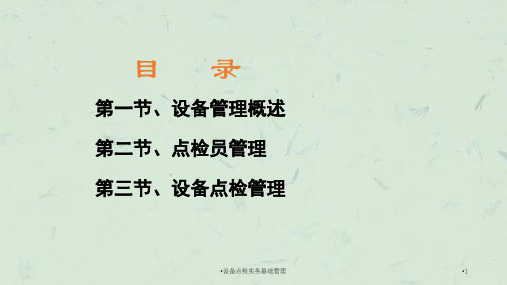
•设备点检实务基础管理
•30
第二节 点检员管理
二、点检员的资格管理
1、点检员的资格证分为两类:
专业点检资格证
取证人员范围: 厂部专职点检员、协力专职点检员
运行点检资格证
取证人员范围: 厂部生产操作人员、协力运保人员、其他从
事辅助点检工作的人员
•设备点检实务基础管理
•31
第二节 点检员管理
二、点检员的资格管理
目录
第一节、设备管理概述 第二节、点检员管理 第三节、设备点检管理
•设备点检实务基础管理
•1
第一节 设备管理概述
一、 设备管理基本理念 二、 设备系统组织架构 三、 设备管理业务流程
•设备点检实务基础管理
•2
复杂化
现代化设备特点
大型化
设备管理概述
设备是固定资产的主要组
成部分,是工业生产中可 供长期使用并在使用中基 本保持原有实物形态的物 质资料的总称。
•设备点检实务基础管理
•29
第二节 点检员管理
一、点检员的分层管理
2、专项点检员的素质要求
• 一年及以上本专业的点检或检修实践经验。 •熟悉点检日常业务管理知识,能熟练判断和排除所管
辖区域一般的设备故障(事故),基本熟悉和掌握所
管辖区域设备结构及控制原理,熟悉和掌握所管辖区域 的工艺流程、工艺参数,并了解相关专业简单的设备原 理。 •受教育年限12年及以上。
•设备点检实务基础管理
•10
设备管理概述
设备一生管理
试车 验收
采购
招标\选型 决策
安装 制造
初期 管理
前期 管理
设计
调研
规划
更新
生产 运行
设备点检ppt课件
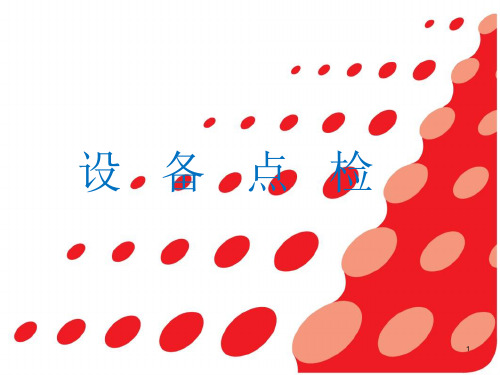
13
测振仪使用方法二、
前端为探头部分,即测 点接触部分,分为长探 头和短探头,图为长探 头;
14
前端为探头部分, 即测点接触部分, 图为短探头;
15
测振仪使用 方法三、
上面有两个可拨动的选择 开关,靠近探头部分为高 频、低频选择开关(只在 测量加速度时有用);另 一个是测量方式开关;
16
测 量 方 法:
11
红外线测温器
是一种在线监测(不停电)式高科技检 测技术,它集光电成像技术、计算机技 术、图像处理技术于一身,通过接收物 体发出的红外线(红外辐射),将其热 像显示在荧光屏上,从而准确判断物体 表面的温度分布情况,具有准确、实时、 快速等优点。
12
测振仪使用方法一 、
正面黑色测量按钮为电源 开关,长按则示数变动, 松开则保留示数一分钟, 然后自动断电。
点检的五定内容:[1] 定点、定期、定标、定法、定人。
6
点检主要检查设备特性:
压力 温度
流量
泄漏 润滑 异声
振动
磨损
松紧
7
点检分类
·日常点检.点检员所进行的常规点巡检. ·重点点检.重要设备每周进行的重点项 目的检查和调整,或发现异常时进行的 重点检查. ·简易诊断.点检员用简易仪器进行设备 运行状态量的测量,以及时重要设备进 行的定期检测和趋势分析. ·精密点检.由专业人员进行的设备检测 和故障诊断,设备点检制的基本框架
定期
设定检查的周期
定法
定点检检查方法 是采用五感
定人
确定点检项目谁 实施
4
简介
设备管理是企业生产经营活动中的重要组成部分,现代化的企业生产经营需 要与其相适应的现代化设备管理体系。如何建立高效的有保障设备管理体系 、解决好设备的使用与维修问题一直是设备管理工作者不断探索的课题。设 备点检制自20世纪80年代从工业先进国家引入中国,得到广泛的应用,为探 索适应中国工业企业设备管理发展提供了一种有效的方法,特别对流程工业 企业更具有其重要性和先进性。但把这种先进方法应用到生产实践中,却经 历了认识——初步应用——再认识——成熟应用的过程。有的走了一些弯路 ,有的甚至半途而废。然而国内不少大型的、先进的企业最终都成功地应用 了设备点检制,建立了以设备点检制为主体的设备管理体系。
测振仪使用方法二、
前端为探头部分,即测 点接触部分,分为长探 头和短探头,图为长探 头;
14
前端为探头部分, 即测点接触部分, 图为短探头;
15
测振仪使用 方法三、
上面有两个可拨动的选择 开关,靠近探头部分为高 频、低频选择开关(只在 测量加速度时有用);另 一个是测量方式开关;
16
测 量 方 法:
11
红外线测温器
是一种在线监测(不停电)式高科技检 测技术,它集光电成像技术、计算机技 术、图像处理技术于一身,通过接收物 体发出的红外线(红外辐射),将其热 像显示在荧光屏上,从而准确判断物体 表面的温度分布情况,具有准确、实时、 快速等优点。
12
测振仪使用方法一 、
正面黑色测量按钮为电源 开关,长按则示数变动, 松开则保留示数一分钟, 然后自动断电。
点检的五定内容:[1] 定点、定期、定标、定法、定人。
6
点检主要检查设备特性:
压力 温度
流量
泄漏 润滑 异声
振动
磨损
松紧
7
点检分类
·日常点检.点检员所进行的常规点巡检. ·重点点检.重要设备每周进行的重点项 目的检查和调整,或发现异常时进行的 重点检查. ·简易诊断.点检员用简易仪器进行设备 运行状态量的测量,以及时重要设备进 行的定期检测和趋势分析. ·精密点检.由专业人员进行的设备检测 和故障诊断,设备点检制的基本框架
定期
设定检查的周期
定法
定点检检查方法 是采用五感
定人
确定点检项目谁 实施
4
简介
设备管理是企业生产经营活动中的重要组成部分,现代化的企业生产经营需 要与其相适应的现代化设备管理体系。如何建立高效的有保障设备管理体系 、解决好设备的使用与维修问题一直是设备管理工作者不断探索的课题。设 备点检制自20世纪80年代从工业先进国家引入中国,得到广泛的应用,为探 索适应中国工业企业设备管理发展提供了一种有效的方法,特别对流程工业 企业更具有其重要性和先进性。但把这种先进方法应用到生产实践中,却经 历了认识——初步应用——再认识——成熟应用的过程。有的走了一些弯路 ,有的甚至半途而废。然而国内不少大型的、先进的企业最终都成功地应用 了设备点检制,建立了以设备点检制为主体的设备管理体系。
车间看板设备点检课件
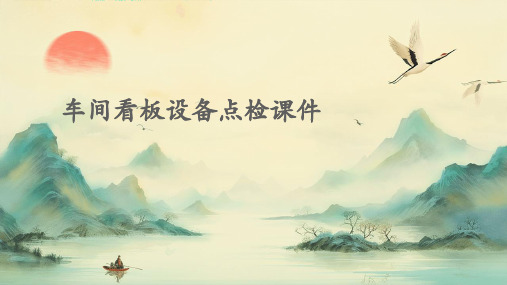
04
清洗法
对设备外壳、传感器等部 件进行清洗,去除灰尘、 油污等污染物,以解决因 污染导致的故障。
05
设备维护与保养
日常维护保养内容
后,应对设备 进行清洁,清除设备表面的 污垢和灰尘,确保设备干净
整洁。
根据设备使用要求,定期对 设备的滑动部位、轴承等部 位进行润滑保养,确保设备
防产生意外伤害。
B
C
D
保持现场整洁
维护保养过程中,应保持现场整洁,及时 清算废弃物和油污,确保工作环境安全。
遵守操作规程
维护保养人员应熟悉设备操作规程,按照 规程进行操作,避免操作失误导致事故。
THANKS
感谢观看
04
设备故障诊断与排除
常见故障及原因
电气故障
通常由电路短路、过载或元件老化引起,可 能导致设备无法启动或正常运行。
传感器故障
原因可能是传感器污染、破坏或失调,会导 致不准确的数据读取和设备误动作。
机械故障
可能由磨损、松动或断裂的零部件引起,会 影响设备的精度和性能。
软件故障
可能由程序错误、病毒感染或不当操作造成 ,会导致设备死机或功能特殊。
促进生产管理改进
车间看板设备能够直观地展示生产过程中的问题和特殊情况,有助 于发现和改进生产管理中的瓶颈和不足。
设备的组成和结构
显示屏幕
数据采集模块
车间看板设备通常采用大屏幕显示器,以 便于远距离观看和多人同时查看。
设备通过数据采集模块与生产现场的各类 传感器、控制器等连接,实时获取生产数 据。
数据处理与分析模块
车间看板设备点检课件
• 车间看板设备概述 • 设备点检基础 • 设备点检操作流程 • 设备故障诊断与排除 • 设备维护与保养
如何做好设备的日常点检ppt课件

每半年更换油品
.
17
目视化管理适用四
❖ 油位计(油位观察视窗)使用 范围表示
❖ 确保正常给油量。在油位计的 上下限各划一条红线,如压缩 空气的油雾器的油杯等。
油量保持在红线 之内
.
18
故障的基本概念
所谓故障,是指设备丧失规定的功能。故障 的种类有:
1)功能停止型故障:设备突发性停止的故障 。 2)功能降低型故障:虽可以动作,但加工能
3)改善设计。通过不拘泥于原设计的改善维修,主动维修方式,使劣化彻 底根除,反馈到设计部门,改善设计,提高新设备的可靠性,达到维修 预防的目的。
4)彻底的预防维修。设备可分六大系统:气动系统、润滑系统、液压系统 、驱动传递系统、运动系统、电气控制系统。
对这六大系统进行定期的检查,看是否有异常,并研究其自然劣化的周
尘土 松动 断裂
划痕 存水 振动 疲劳 最终故障
电化学反应 微裂纹
锈蚀 裂纹
.
21
减少故障损失的对象
减少故障损失要从初始的清洁开始,逐步深入到点检、润滑保养和维 修各个环节,其对策如下:
保持 状态
遵守操作 规程
修复 自然劣化
纠正 缺陷设计
防止 人为劣化
发现防止 劣化
创新 维修方法
防止 操作失误
防止 维修失误
健康医疗所发展起来的那些医疗检测手段,如心电图、血 压计、X光、CT等,也应发展到设备诊断领域中。
现代设备振动监测仪器、油分析设备即是这种从医疗向设 备诊断的扩展。
.
28
设备点检制的具体内容和特点
所谓的点检制,是按照一定的标准、一定周期、对设备规定的部 位进行检查,以便早期发现设备故障隐患,及时加以修理调整,使设 备保持其规定功能的设备管理方法。 值得指出的是,设备点检制不仅仅是一种检查方式,而且是一种制度 和管理方法。 设备点检制的特点是:
.
17
目视化管理适用四
❖ 油位计(油位观察视窗)使用 范围表示
❖ 确保正常给油量。在油位计的 上下限各划一条红线,如压缩 空气的油雾器的油杯等。
油量保持在红线 之内
.
18
故障的基本概念
所谓故障,是指设备丧失规定的功能。故障 的种类有:
1)功能停止型故障:设备突发性停止的故障 。 2)功能降低型故障:虽可以动作,但加工能
3)改善设计。通过不拘泥于原设计的改善维修,主动维修方式,使劣化彻 底根除,反馈到设计部门,改善设计,提高新设备的可靠性,达到维修 预防的目的。
4)彻底的预防维修。设备可分六大系统:气动系统、润滑系统、液压系统 、驱动传递系统、运动系统、电气控制系统。
对这六大系统进行定期的检查,看是否有异常,并研究其自然劣化的周
尘土 松动 断裂
划痕 存水 振动 疲劳 最终故障
电化学反应 微裂纹
锈蚀 裂纹
.
21
减少故障损失的对象
减少故障损失要从初始的清洁开始,逐步深入到点检、润滑保养和维 修各个环节,其对策如下:
保持 状态
遵守操作 规程
修复 自然劣化
纠正 缺陷设计
防止 人为劣化
发现防止 劣化
创新 维修方法
防止 操作失误
防止 维修失误
健康医疗所发展起来的那些医疗检测手段,如心电图、血 压计、X光、CT等,也应发展到设备诊断领域中。
现代设备振动监测仪器、油分析设备即是这种从医疗向设 备诊断的扩展。
.
28
设备点检制的具体内容和特点
所谓的点检制,是按照一定的标准、一定周期、对设备规定的部 位进行检查,以便早期发现设备故障隐患,及时加以修理调整,使设 备保持其规定功能的设备管理方法。 值得指出的是,设备点检制不仅仅是一种检查方式,而且是一种制度 和管理方法。 设备点检制的特点是:
设备日常点检作业案例PPT课件
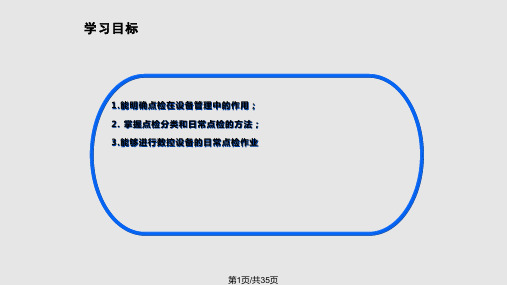
第29页/共35页
四、设备日常点检作业
• 案例:观看数控设备日常点检作业录相
第30页/共35页
学习小结
• 1. 设备点检管理理念; • 2. 设备点检作用、分类、内容; • 3. 设备点检的方法和手段; • 4. 设备点检作业方法和步骤
第31页/共35页
课外作业
• 完成教材配套《学习手册》中 • 学习情境1 • 任务1.3. 设备日常保养作业 • 练习题
一、设备点检的概念
(一)点检管理的由来与发展
预防医学
日常 预防
防止老化
日常维护 清扫、补油 拧紧、点检
健康 诊断
测老化度
检查 诊断
早期 治疗
修复老化
预防修理 定期更换
预防维修
延长寿命
第5页/共35页
一、设备点检的概念
(一)点检管理的由来与发展
借助人类预防医学的观点,人们对自己的孩子进行精心呵护、 养育,每天检查、测定其体温;喂水、喂奶,照顾饮食;清理排泄 等,以预防各种疾病。
第25页/共35页
数控铣床日常点检作业标准指导书
第26页/共35页
数控铣床日常点检表
第27页/共35页
四、设备日常点检作业
3.设备日常点检的原则
• (1).完整性
• 要按照点检项目逐项检查、逐项确认,不 能有遗漏。
• (2)做好标记
• 对确认无问题的,要标明规定符号;未经 检查的,不得作标记。对有问题的,要注明相 应标记并作好记录,并向上级报告。
第11页/共35页
一、设备点检的概念
(二)设备点检的作用
第12页/共35页
第13页/共35页
一、设备点检的概念
(二)设备点检的作用
四、设备日常点检作业
• 案例:观看数控设备日常点检作业录相
第30页/共35页
学习小结
• 1. 设备点检管理理念; • 2. 设备点检作用、分类、内容; • 3. 设备点检的方法和手段; • 4. 设备点检作业方法和步骤
第31页/共35页
课外作业
• 完成教材配套《学习手册》中 • 学习情境1 • 任务1.3. 设备日常保养作业 • 练习题
一、设备点检的概念
(一)点检管理的由来与发展
预防医学
日常 预防
防止老化
日常维护 清扫、补油 拧紧、点检
健康 诊断
测老化度
检查 诊断
早期 治疗
修复老化
预防修理 定期更换
预防维修
延长寿命
第5页/共35页
一、设备点检的概念
(一)点检管理的由来与发展
借助人类预防医学的观点,人们对自己的孩子进行精心呵护、 养育,每天检查、测定其体温;喂水、喂奶,照顾饮食;清理排泄 等,以预防各种疾病。
第25页/共35页
数控铣床日常点检作业标准指导书
第26页/共35页
数控铣床日常点检表
第27页/共35页
四、设备日常点检作业
3.设备日常点检的原则
• (1).完整性
• 要按照点检项目逐项检查、逐项确认,不 能有遗漏。
• (2)做好标记
• 对确认无问题的,要标明规定符号;未经 检查的,不得作标记。对有问题的,要注明相 应标记并作好记录,并向上级报告。
第11页/共35页
一、设备点检的概念
(二)设备点检的作用
第12页/共35页
第13页/共35页
一、设备点检的概念
(二)设备点检的作用
机械设备的点检PPT课件

28
常用的对中调整方法
直尺塞尺法
2011-10-14
导入最符合中国企业的 TnPM —— 全面规范化生产维护管理模式
常用的对中调整方法
百分表测量法
D 表头180°方向上离的,距离,略小于联轴器直径 L1 表头到前地脚的轴向距离 L2 表头到后地脚的轴向距离
导入最符合中国企业的 TnPM —— 全面规范化生产维护管理模式
导入最符合中国企业的 TnPM —— 全面规范化生产维护管理模式
减速机是原动机和工作机之间的独立的闭 式传动装置,用来降低转速、增大转矩,满足 工作需要。
减速机常见分类
分类方法
减速机类型
传动类型
齿轮减速机、蜗杆减速机、行星减速机以 及组合的减速机
传动级数
单级和多级减速机
齿轮形状 布置形式
圆柱齿轮、圆锥齿轮和圆锥一圆柱齿轮减 速机
导入最符合中国企业的 TnPM —— 全面规范化生产维护管理模式
破损
沟道面的破裂、 冲击负荷过大 缺损 (图6)
适当的负荷条件
过盈量过大
表面剥落或烧伤 的进展
安装部的圆角大
适当的配合 轴和套的修整
把圆角修整成比
适当的负荷条件
运转中游隙过大 配合和轴承游隙 复查
P1
振动分析潜在故障点
P2
油液分析潜在故障点
P3
噪声分析潜在故障点
成本最低
P4 手摸发热潜在故障点
F
功能故障点
P1’ P2’ P3’P4’ F’
导入最符合中国企业的 TnPM —— 全面规范化生产维护管理模式
27
维修策略的理解
• 1 要维护,先检测 • 2 要预防,先监测
导入最符合中国企业的 TnPM —— 全面规范化生产维护管理模式
《设备点检培训》课件

检查设备的各项功能是否正常。
定期维护
根据设备的使用频率和工作环境制定相应的保养计 划。
设备点检的注意事项
• 安全第一 • 严格按照操作手册进行点检 • 做好记录和报告
设备点检的常见问题
点检过程中出现安全事 故
设备点检前应了解相关危险, 进行相应的防护措施。
点检记录不完整或不规 范
做好记录可以提高点检的效 率,并为后期的设备维护提 供有力的支撑。
电子设备点检记录不规范导致维 修成本增加
由于点检记录不规范,导致对设备状态 的判断不准确,在维修时出现了额外的 维修成本。
设备点检的实践演练
实践操作流程演练
根据实际设备情况,模拟点检操作流程,并进 行实践操作。
点检记录填写实践演练
根据点检记录的填写要求,模拟点检记录的填 写,并互相检查和改进。
总结
设备点检培训
设备点检是设备维护的关键环节。本课程将介绍设备点检的方法,注意事项, 以及常见问题的解决方案。
为什么需要设备点检?
• 提高设备使用寿命 • 降低维修成本 • 提高设备工作效率
设备点检的方法
外观检查
检查设备外部有无变形、损坏、磨损等。
现场测试
观察和测试设备在正常状态下的运转情况。
功能性检查
点检步骤不清晰或操作 失误
按照操作手册进行点检,或 在点检前进行训练,可以提 高点检的准确性和效率。
设备点检的案例分析
1
电梯点检不及时导致安全事故发生2电梯在过载状态下出现故障,后经检查
发现原因是点检不及时,致使问题演变
成安全事故。
3
机床点检不规范导致机床故障
机床在长时间使用后出现故障,后经检 查发现原因是点检不规范导致未能及时 发现设备存在的问题。
定期维护
根据设备的使用频率和工作环境制定相应的保养计 划。
设备点检的注意事项
• 安全第一 • 严格按照操作手册进行点检 • 做好记录和报告
设备点检的常见问题
点检过程中出现安全事 故
设备点检前应了解相关危险, 进行相应的防护措施。
点检记录不完整或不规 范
做好记录可以提高点检的效 率,并为后期的设备维护提 供有力的支撑。
电子设备点检记录不规范导致维 修成本增加
由于点检记录不规范,导致对设备状态 的判断不准确,在维修时出现了额外的 维修成本。
设备点检的实践演练
实践操作流程演练
根据实际设备情况,模拟点检操作流程,并进 行实践操作。
点检记录填写实践演练
根据点检记录的填写要求,模拟点检记录的填 写,并互相检查和改进。
总结
设备点检培训
设备点检是设备维护的关键环节。本课程将介绍设备点检的方法,注意事项, 以及常见问题的解决方案。
为什么需要设备点检?
• 提高设备使用寿命 • 降低维修成本 • 提高设备工作效率
设备点检的方法
外观检查
检查设备外部有无变形、损坏、磨损等。
现场测试
观察和测试设备在正常状态下的运转情况。
功能性检查
点检步骤不清晰或操作 失误
按照操作手册进行点检,或 在点检前进行训练,可以提 高点检的准确性和效率。
设备点检的案例分析
1
电梯点检不及时导致安全事故发生2电梯在过载状态下出现故障,后经检查
发现原因是点检不及时,致使问题演变
成安全事故。
3
机床点检不规范导致机床故障
机床在长时间使用后出现故障,后经检 查发现原因是点检不规范导致未能及时 发现设备存在的问题。
- 1、下载文档前请自行甄别文档内容的完整性,平台不提供额外的编辑、内容补充、找答案等附加服务。
- 2、"仅部分预览"的文档,不可在线预览部分如存在完整性等问题,可反馈申请退款(可完整预览的文档不适用该条件!)。
- 3、如文档侵犯您的权益,请联系客服反馈,我们会尽快为您处理(人工客服工作时间:9:00-18:30)。
• 1.操作人员的日常点检 • 通过日常点检,一旦发现异常,除及时通知专业点检人员外,还能自己动
手排除异常,进行小修理,这是预防事故发生的第一层防护线. • 2.专业点检员的专业点检 • 主要依靠五官或借助某些工具、简易仪器实施点检,对重点设备实行倾
向检查管理,发现和消除隐患,分析和排除故障,组织故障修复,这是第二 层防护线. • 3.专业技术人员的精密点检及精度测试检查 • 在日常点检、定期专业点检的基础上,定期对设备进行严格的精密检 查、测定、调整和分析,这是第三层防护线. • 4.设备技术诊断 • 设备技术诊断是一种在运转时或非解体状态下,对设备进行点检定量测 试,帮助专业点检员作出决策,防止事故的发生,这是第四层防护线. • 5. 设备维修 • 通过上述四层防护线,可以摸清设备劣化的规律,减缓劣化进度和延长 机件的寿命.但还有可能发生突发性故障,这时就要维修.维修技术的高 低又直接影响设备的劣化速度,因此需要一支维修技术高,责任心强的 维修队伍.可以说设备维修也是点检制的一个重要环节,这是设备的第 五层防护线.
善 • 第六阶段:90年代TPM走向世界
设备管理的形成与发展
设备管理从产生至今,经历了三个不同的发展时期:
在工业革命初期,加工规模小,设备简陋,设备的维修一般由操作 工负责,并无专门的设备管理。
上世纪初,随着工业化的不断普及,机械作业逐步替代手工作业, 它克服了手工作业的质量不稳定、无法大批量生产、成本高等缺点。尤 其是上世纪30年代以后,美国的制造加工业对机械装备的依赖性越来越 突出,伴随而来的设备故障率也与日俱增,严重影响着产品品质和生产 效率的进一步提升。
• 不准乱开、乱拆、乱割、乱焊; • 不准随意改动调整值、严禁取消安全装置; • 不准在无润滑状态下运行; • 不准考试不合格人员上岗操作及独立从事维护工
自主保全
TPM管 理体系
专业保全
日常点检 预防保养 定期点检 设备诊断 改良保全 事后保全
计划保养 预知保养
11
设备点检的定义
• 为了维持生产设备的原有性能,通过人的五感(视、听、嗅、味、触)或简单 的工具、仪器,按照预先设定的周期和方法,对设备上的规定部位(点)进行 有无异常的预防性周密检查的过程,以使设备的隐患和缺陷能够得到早期的发 现,早期预防,早期处理,这样的设备检查称为点检
6
预防保全-PM的开展包括三个方面活动: 1. 设备的日常维护(清洁、检查和润滑)。 2. 对设备进行定期检查,及时掌握设备的劣化状况。 3. 对设备的劣化采取复原活动。
从推行PM开始,设备管理开始由事后维修向定期预 防维修转变,强调采用适当的方法和组织措施, 尽早发 现设备隐患,通过预防和修理相结合,保证设备的正常 运行。
设备点检培训
全员生产维修TPM
什么是TPM?
• TPM 是英文Total Productive Maintenance的 缩写,中文译为“全面生产维护”,也可译为 “全员生产维修”或“全员生产保全”。它是以 提高设备综合效率为目标,以全系统的预防维护 为过程、全体人员参加为基础的设备保养和维修 体制。
– 设备进行预防性管理:通过点检人员对设备进行点检 来准确掌握设备技术状况,实行有效的计划维修,维 持和改善设备工作性能,预防事故发生,延长机件寿 命,减少停机时间,提高设备的有效作业率,保证正 常生产,降低维修费用。
设备的劣化
• 设备劣化的主要表现形式 • (1)机械磨损;(2)裂纹;(3)塑性断裂和脆性断裂;
设备点检定修制
• 点检定修制是一套加以制度化的、比较完善的科学管理方式。它要求按 规定的检查周期和方法对设备进行预防性检查,取得准确的设备状态情 报,制订有效的维修对策。并在适当的时间里进行恰当的维修,以有限 的人力完成设备所需要的全部检修工作量,把维修工作做在设备发生故 障之前,使设备始终处于最佳状态。其实质就是以预防维修为基础、以 点检为核心的全员维修制度。其主要内容有;
1. 记录日常检查结果和发生故障的详细情况。 2. 对故障发生源进行有效的改善。
为了保证设备不出故障、不制造不良品,又出现了“保全预防” (Maintenance Prevention ,MP / 1960 )。从设备的设计阶段就开始对设备 故障进行控制,其最终目的是实现无故障和简便的日常维护。 MP是依据对设 备的运行和维护情况的完整记录,帮助设计人员对设备的结构进行改进。
对策,为第四层防护 • 每半年或一年一次的精密检测是第五层防护线
• 建议对公司全员分批进行设备保全与点检意识培 训,通过全员系统培训规划公司设备“三位一体” 系统模型。
• 为确保设备运转正常,日常点检、定期点检、精密点检(含精度测试) 、 设备技术诊断和设备维修结合在一起,构成了设备完整的防护体系.具 体可分为以下五个层次:
——90年代: 全世界的制造企业都开始推行TPM。
9
TPM:工厂全面改善
1、建立不断生产追求生产效率的体制为目标 2、通过公司领导到第一线员工全员参与的改善活动 3、构建能预防管理及生产工序中所有的损耗 4、最终达到损耗最小化和利益最大化
设备管理的目的:减少设备事故的发生,保持、提 高设备的性能、精度、降低维修费用,提高企业 的生产能力和经济效益。
最终,美国通用公司将BM、PM、CM、MP四种活动结合起来称之为“生 产保全” ( PM ,Productive Maintenance ),从此出现了设备管理的科学方 法,这就是TPM的雏形。
8
TPM的产生及其演进过程
20世纪60年代,日本引进PM活动并改造成以生产部门为主的 TPM改善活动。(即Total Productive Maintenance,全员效率保全, 通过全员参加的设备保全管理来提高生产效率,使生产效益最大化)
——71年,日本设立了全日本PM奖,丰田公司的下属企业日本电 装公司首先得奖。
——80年代: TPM作为一套有效的企业管理体系,得到了广泛认 同,世界上许多公司引进了TPM系统。
与此同时,TPM本身也在不断发展完善, 拓展为全公司(包括非 生产部门)、全员参与的管理行为。从最初的设备维护管理,发展到 安全、健康、环保、质量、产品开发、供应链、人事培训和办公室管 理等各个领域,形成了一套综合性的企业管理体系。
• 受介质腐蚀、沾附部位。
• 电气设备劣化的主要原因 • 电的作用; • 高温及温度变化的作用; • 机械力的作用; • 潮湿的作用; • 化学的作用; • 宇宙放射线作用。
• 电气(仪表、计算机)设备的劣化部位 • 绝缘部位; • 与介质接触、腐蚀部位; • 受灰尘污染部位; • 受温度影响部位; • 受潮气侵入部位。
• 参考资料:L
润湿周期
责任者
2天
运行人员
油具 油杯
2 3 4 备注
C
39ML
4天
运行人员
油枪
B
11ML
1天
运行人员
油杯
D
27ML
7天
技术人员
油杯
A 代表机油 B 代表黄油 C代表液压油 D 代表太古油
使用设备的“六不准”规定
• 不准拼设备,严禁超压、超速、超载、超温等超 负荷运行;
业形象
3
TPM的起源及其作用
• 第一阶段:1950年美国,事后保全 • 第二阶段:1955年前后,规律性,周期性的出现
问题---定期维护 • 第三阶段:1960年 不发生故障的设备从设计、安
装开始 • 第四阶段:1960年,美国GE公司提出生产性保全:
PM • 第五阶段:70年代初,日本丰田提出TPM=全面改
使设备停止工作。
• 预防劣化的对策 • 预防劣化对策:预防劣化、测定劣化、修复劣化 • 预防劣化:(1)日常点检维护:给油脂、更换、调整、紧固、清扫;(2)
改善维修:维持性能。
• 测定劣化:点检检查-良否点检、倾向检查。 • 修复劣化:(1)修理:预防预知维修、事后维修;(2)更新:更新、改造。
• 机械设备的劣化部位 • 机械设备的劣化一般发生在以下六个部位: • 机件滑动工作部位; • 机械传动工作部位; • 机件旋转工作部位; • 受力支撑及连接部位; • 与原料、灰尘接触、粒附部位;
随着设备构造的日益复杂,先进设备的维护越来越困难,其本身的 品质以及组合精度严重影响着产品的质量,加上操作者不熟悉设备的性 能和机能、误操作、延误管理等,几方面因素导致设备维护成本不断增 加。
5
为了解决这些问题,美国制造业提出了“事后保全 (Breakdown Maintenance ,BM)”,即当装备出现故障后马上采 取应急措施进行事后处置。
修复缺陷、调整精度、操作更换、恢复公差、消除泄 露、设计记录、制订对策
三位一体: • 岗位操作工人的日常点检 • 专业点检员的定期点检 • 专业技术人员的精密点检
五层防护线
• 岗位操作工人的日常点检作为第一层防护线 • 把专业点检和定期点检作为第二层防护线 • 专业技术人员的精密点检作为第三层防护线 • 进一步利用技术诊断和倾向管理探明因果,做出
设备使用的“三好”、“四会”
• 要求岗位操作工、岗位维修工做到的“三好”、“四会”是 • “三好”是用好设备,管好设备,修好设备。 • “四会”是会使用,会维护、会点检,会紧急处理故障。
设备点检工作的“五定”内容
• 定点——设定检查的部位、项目和内容; • 定法——定点检检查方法,是采用五感,还是工具、仪器; • 定标——制订维修标准; • 定期——设定检查的周期; • 定人——确定点检项目由谁实施。
TPM的效益
P:减少故障停机(1/10—1/290)、提高生产率(2倍)、提高计划达 成率、缩短生产周期
Q:降低不良品率(1/10)、提高产品质量(缺陷率为1/10) C:减少人工费、节省维修成本和制造成本(50%) S:改善工作环境和自然环境、减少事故机率、提高安全性(实现零灾
害) M:增强市场意识、提升员工士气(提案数量上升5—10倍) 、树立企
手排除异常,进行小修理,这是预防事故发生的第一层防护线. • 2.专业点检员的专业点检 • 主要依靠五官或借助某些工具、简易仪器实施点检,对重点设备实行倾
向检查管理,发现和消除隐患,分析和排除故障,组织故障修复,这是第二 层防护线. • 3.专业技术人员的精密点检及精度测试检查 • 在日常点检、定期专业点检的基础上,定期对设备进行严格的精密检 查、测定、调整和分析,这是第三层防护线. • 4.设备技术诊断 • 设备技术诊断是一种在运转时或非解体状态下,对设备进行点检定量测 试,帮助专业点检员作出决策,防止事故的发生,这是第四层防护线. • 5. 设备维修 • 通过上述四层防护线,可以摸清设备劣化的规律,减缓劣化进度和延长 机件的寿命.但还有可能发生突发性故障,这时就要维修.维修技术的高 低又直接影响设备的劣化速度,因此需要一支维修技术高,责任心强的 维修队伍.可以说设备维修也是点检制的一个重要环节,这是设备的第 五层防护线.
善 • 第六阶段:90年代TPM走向世界
设备管理的形成与发展
设备管理从产生至今,经历了三个不同的发展时期:
在工业革命初期,加工规模小,设备简陋,设备的维修一般由操作 工负责,并无专门的设备管理。
上世纪初,随着工业化的不断普及,机械作业逐步替代手工作业, 它克服了手工作业的质量不稳定、无法大批量生产、成本高等缺点。尤 其是上世纪30年代以后,美国的制造加工业对机械装备的依赖性越来越 突出,伴随而来的设备故障率也与日俱增,严重影响着产品品质和生产 效率的进一步提升。
• 不准乱开、乱拆、乱割、乱焊; • 不准随意改动调整值、严禁取消安全装置; • 不准在无润滑状态下运行; • 不准考试不合格人员上岗操作及独立从事维护工
自主保全
TPM管 理体系
专业保全
日常点检 预防保养 定期点检 设备诊断 改良保全 事后保全
计划保养 预知保养
11
设备点检的定义
• 为了维持生产设备的原有性能,通过人的五感(视、听、嗅、味、触)或简单 的工具、仪器,按照预先设定的周期和方法,对设备上的规定部位(点)进行 有无异常的预防性周密检查的过程,以使设备的隐患和缺陷能够得到早期的发 现,早期预防,早期处理,这样的设备检查称为点检
6
预防保全-PM的开展包括三个方面活动: 1. 设备的日常维护(清洁、检查和润滑)。 2. 对设备进行定期检查,及时掌握设备的劣化状况。 3. 对设备的劣化采取复原活动。
从推行PM开始,设备管理开始由事后维修向定期预 防维修转变,强调采用适当的方法和组织措施, 尽早发 现设备隐患,通过预防和修理相结合,保证设备的正常 运行。
设备点检培训
全员生产维修TPM
什么是TPM?
• TPM 是英文Total Productive Maintenance的 缩写,中文译为“全面生产维护”,也可译为 “全员生产维修”或“全员生产保全”。它是以 提高设备综合效率为目标,以全系统的预防维护 为过程、全体人员参加为基础的设备保养和维修 体制。
– 设备进行预防性管理:通过点检人员对设备进行点检 来准确掌握设备技术状况,实行有效的计划维修,维 持和改善设备工作性能,预防事故发生,延长机件寿 命,减少停机时间,提高设备的有效作业率,保证正 常生产,降低维修费用。
设备的劣化
• 设备劣化的主要表现形式 • (1)机械磨损;(2)裂纹;(3)塑性断裂和脆性断裂;
设备点检定修制
• 点检定修制是一套加以制度化的、比较完善的科学管理方式。它要求按 规定的检查周期和方法对设备进行预防性检查,取得准确的设备状态情 报,制订有效的维修对策。并在适当的时间里进行恰当的维修,以有限 的人力完成设备所需要的全部检修工作量,把维修工作做在设备发生故 障之前,使设备始终处于最佳状态。其实质就是以预防维修为基础、以 点检为核心的全员维修制度。其主要内容有;
1. 记录日常检查结果和发生故障的详细情况。 2. 对故障发生源进行有效的改善。
为了保证设备不出故障、不制造不良品,又出现了“保全预防” (Maintenance Prevention ,MP / 1960 )。从设备的设计阶段就开始对设备 故障进行控制,其最终目的是实现无故障和简便的日常维护。 MP是依据对设 备的运行和维护情况的完整记录,帮助设计人员对设备的结构进行改进。
对策,为第四层防护 • 每半年或一年一次的精密检测是第五层防护线
• 建议对公司全员分批进行设备保全与点检意识培 训,通过全员系统培训规划公司设备“三位一体” 系统模型。
• 为确保设备运转正常,日常点检、定期点检、精密点检(含精度测试) 、 设备技术诊断和设备维修结合在一起,构成了设备完整的防护体系.具 体可分为以下五个层次:
——90年代: 全世界的制造企业都开始推行TPM。
9
TPM:工厂全面改善
1、建立不断生产追求生产效率的体制为目标 2、通过公司领导到第一线员工全员参与的改善活动 3、构建能预防管理及生产工序中所有的损耗 4、最终达到损耗最小化和利益最大化
设备管理的目的:减少设备事故的发生,保持、提 高设备的性能、精度、降低维修费用,提高企业 的生产能力和经济效益。
最终,美国通用公司将BM、PM、CM、MP四种活动结合起来称之为“生 产保全” ( PM ,Productive Maintenance ),从此出现了设备管理的科学方 法,这就是TPM的雏形。
8
TPM的产生及其演进过程
20世纪60年代,日本引进PM活动并改造成以生产部门为主的 TPM改善活动。(即Total Productive Maintenance,全员效率保全, 通过全员参加的设备保全管理来提高生产效率,使生产效益最大化)
——71年,日本设立了全日本PM奖,丰田公司的下属企业日本电 装公司首先得奖。
——80年代: TPM作为一套有效的企业管理体系,得到了广泛认 同,世界上许多公司引进了TPM系统。
与此同时,TPM本身也在不断发展完善, 拓展为全公司(包括非 生产部门)、全员参与的管理行为。从最初的设备维护管理,发展到 安全、健康、环保、质量、产品开发、供应链、人事培训和办公室管 理等各个领域,形成了一套综合性的企业管理体系。
• 受介质腐蚀、沾附部位。
• 电气设备劣化的主要原因 • 电的作用; • 高温及温度变化的作用; • 机械力的作用; • 潮湿的作用; • 化学的作用; • 宇宙放射线作用。
• 电气(仪表、计算机)设备的劣化部位 • 绝缘部位; • 与介质接触、腐蚀部位; • 受灰尘污染部位; • 受温度影响部位; • 受潮气侵入部位。
• 参考资料:L
润湿周期
责任者
2天
运行人员
油具 油杯
2 3 4 备注
C
39ML
4天
运行人员
油枪
B
11ML
1天
运行人员
油杯
D
27ML
7天
技术人员
油杯
A 代表机油 B 代表黄油 C代表液压油 D 代表太古油
使用设备的“六不准”规定
• 不准拼设备,严禁超压、超速、超载、超温等超 负荷运行;
业形象
3
TPM的起源及其作用
• 第一阶段:1950年美国,事后保全 • 第二阶段:1955年前后,规律性,周期性的出现
问题---定期维护 • 第三阶段:1960年 不发生故障的设备从设计、安
装开始 • 第四阶段:1960年,美国GE公司提出生产性保全:
PM • 第五阶段:70年代初,日本丰田提出TPM=全面改
使设备停止工作。
• 预防劣化的对策 • 预防劣化对策:预防劣化、测定劣化、修复劣化 • 预防劣化:(1)日常点检维护:给油脂、更换、调整、紧固、清扫;(2)
改善维修:维持性能。
• 测定劣化:点检检查-良否点检、倾向检查。 • 修复劣化:(1)修理:预防预知维修、事后维修;(2)更新:更新、改造。
• 机械设备的劣化部位 • 机械设备的劣化一般发生在以下六个部位: • 机件滑动工作部位; • 机械传动工作部位; • 机件旋转工作部位; • 受力支撑及连接部位; • 与原料、灰尘接触、粒附部位;
随着设备构造的日益复杂,先进设备的维护越来越困难,其本身的 品质以及组合精度严重影响着产品的质量,加上操作者不熟悉设备的性 能和机能、误操作、延误管理等,几方面因素导致设备维护成本不断增 加。
5
为了解决这些问题,美国制造业提出了“事后保全 (Breakdown Maintenance ,BM)”,即当装备出现故障后马上采 取应急措施进行事后处置。
修复缺陷、调整精度、操作更换、恢复公差、消除泄 露、设计记录、制订对策
三位一体: • 岗位操作工人的日常点检 • 专业点检员的定期点检 • 专业技术人员的精密点检
五层防护线
• 岗位操作工人的日常点检作为第一层防护线 • 把专业点检和定期点检作为第二层防护线 • 专业技术人员的精密点检作为第三层防护线 • 进一步利用技术诊断和倾向管理探明因果,做出
设备使用的“三好”、“四会”
• 要求岗位操作工、岗位维修工做到的“三好”、“四会”是 • “三好”是用好设备,管好设备,修好设备。 • “四会”是会使用,会维护、会点检,会紧急处理故障。
设备点检工作的“五定”内容
• 定点——设定检查的部位、项目和内容; • 定法——定点检检查方法,是采用五感,还是工具、仪器; • 定标——制订维修标准; • 定期——设定检查的周期; • 定人——确定点检项目由谁实施。
TPM的效益
P:减少故障停机(1/10—1/290)、提高生产率(2倍)、提高计划达 成率、缩短生产周期
Q:降低不良品率(1/10)、提高产品质量(缺陷率为1/10) C:减少人工费、节省维修成本和制造成本(50%) S:改善工作环境和自然环境、减少事故机率、提高安全性(实现零灾
害) M:增强市场意识、提升员工士气(提案数量上升5—10倍) 、树立企