某公司生产车间工艺管道安装、焊接施工方案(图)
工艺管道焊接施工方案
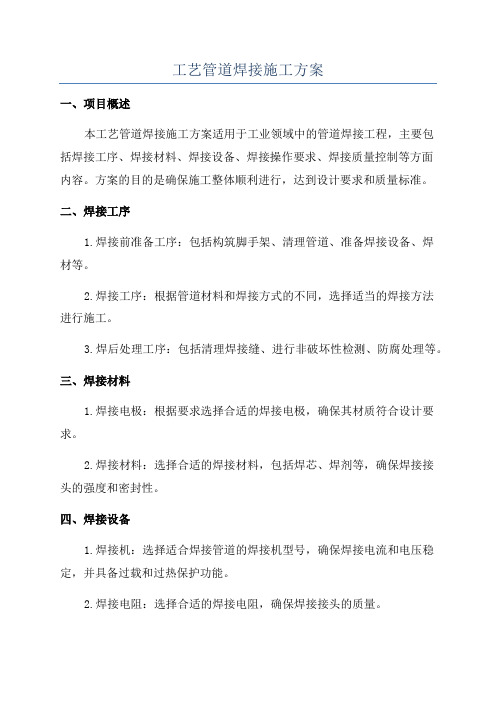
工艺管道焊接施工方案一、项目概述本工艺管道焊接施工方案适用于工业领域中的管道焊接工程,主要包括焊接工序、焊接材料、焊接设备、焊接操作要求、焊接质量控制等方面内容。
方案的目的是确保施工整体顺利进行,达到设计要求和质量标准。
二、焊接工序1.焊接前准备工序:包括构筑脚手架、清理管道、准备焊接设备、焊材等。
2.焊接工序:根据管道材料和焊接方式的不同,选择适当的焊接方法进行施工。
3.焊后处理工序:包括清理焊接缝、进行非破坏性检测、防腐处理等。
三、焊接材料1.焊接电极:根据要求选择合适的焊接电极,确保其材质符合设计要求。
2.焊接材料:选择合适的焊接材料,包括焊芯、焊剂等,确保焊接接头的强度和密封性。
四、焊接设备1.焊接机:选择适合焊接管道的焊接机型号,确保焊接电流和电压稳定,并具备过载和过热保护功能。
2.焊接电阻:选择合适的焊接电阻,确保焊接接头的质量。
五、焊接操作要求1.焊接工人:具备合格的焊接技术,经过培训并取得相应的焊接证书。
2.焊接操作规程:严格按照施工设计的焊接工艺规程进行操作,包括预热温度、焊接电流和电压、焊接速度等参数的控制。
3.安全措施:穿戴必要的防护装备,确保焊接工人的人身安全。
4.环境保护:严格控制焊接过程中产生的废气、废水和废渣,按环保要求进行处理。
六、焊接质量控制1.检查焊接材料和焊接设备的合格证明,确保其质量可靠。
2.在焊接前进行焊缝预处理,包括清洁焊缝、除去氧化层等。
3.焊接过程中进行必要的焊口尺寸和形状的检查,确保其符合设计要求。
4.完成焊接后进行非破坏性检测,包括超声波、X射线等,确保焊接接头的质量。
5.对焊接接头进行防腐处理,包括涂覆保护涂料等,保证其抗腐蚀能力。
七、项目管理与安全措施1.施工前编制详细的施工计划,明确施工进度和工期。
2.对施工现场进行周边环境的评估,确保施工安全。
3.制定施工安全措施,包括安全教育、施工现场的安全围栏、警示标识等。
4.定期检查和维护焊接设备,确保其正常运行。
6.1、工艺管道安装施工方案
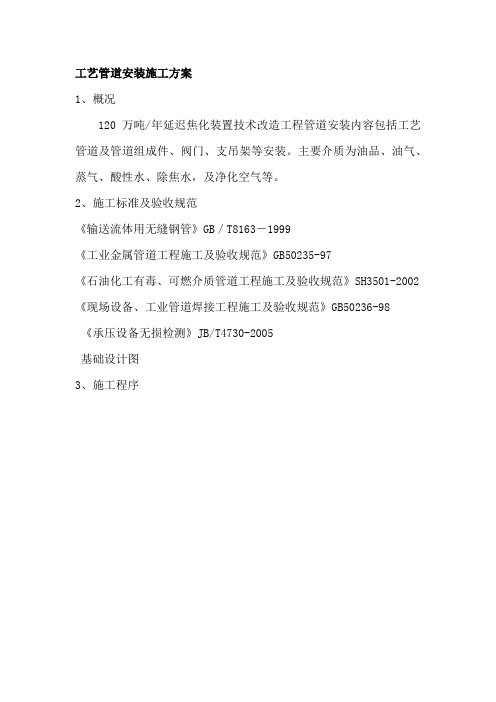
工艺管道安装施工方案1、概况120万吨/年延迟焦化装置技术改造工程管道安装内容包括工艺管道及管道组成件、阀门、支吊架等安装。
主要介质为油品、油气、蒸气、酸性水、除焦水,及净化空气等。
2、施工标准及验收规范《输送流体用无缝钢管》GB/T8163-1999《工业金属管道工程施工及验收规范》GB50235-97《石油化工有毒、可燃介质管道工程施工及验收规范》SH3501-2002 《现场设备、工业管道焊接工程施工及验收规范》GB50236-98《承压设备无损检测》JB/T4730-2005基础设计图3、施工程序施工准备施工方案编制、审批原材料领出、运输复验、标识 焊接工艺评定压力管道安装报审 管道防腐无损检测不合格 质量检查合格确认管道试压吹扫及内部清理防腐补口检测竣工及交工资料整理 管道预制、组对 管道号标识管道焊接焊工号标识 无损检测不合格 管道运输管道安装、就位固定口焊接焊工号标识 技术交底防腐检测不合格检查合格确认不合格 防腐补口不合格4、施工准备a、图纸会审施工前由管道安装、焊接、防腐、土建等有关专业技术人员会同设计、业主代表及监理进行图纸会审,会审时做好图纸会审记录,把图纸会审中提出的问题解决在开工之前。
b、焊接工艺评定首次焊接的管道材料、焊接结构和首次使用的焊接材料必须按《钢制压力容器焊接工艺评定》(JB4708)进行焊接工艺评定。
焊接工艺评定合格后方可在此基础上编制焊接工艺、焊接方案。
亦可使用已有合格的焊接工艺评定编制焊接工艺、焊接方案、焊接工艺指导书。
焊接工艺评定经监理及业主批准、认可。
c、压力管道安装报审压力管道安装报审前,首先由有关人员对施工图纸进行合法性审查。
管道安装前,项目经理部按要求向当地压力管道安全监察部门和压力管道检验单位递交压力管道安装申请报告及监检申请。
批准后,向公司质量部门报批包括经批准的监检申请报告(复印件)、各专业有资格要求人员的资格情况、施工现场施工设备及施工文件准备情况,经批准后才可施工,并存档备查。
工艺管道施工技术方案(完整版)

工艺管道施工技术方案(完整版)一、项目背景及目标这个项目是我们公司承接的一项大型化工企业工艺管道安装工程,涉及到的管道种类繁多,有不锈钢管道、碳钢管道、合金管道等。
我们的目标是确保管道安装质量达到国家相关标准,满足生产需求,同时保证施工安全、环保。
二、施工准备1.技术准备:我们要对施工图纸进行深入研究,了解管道的走向、规格、材质等信息。
同时,对施工工艺、施工方法、施工流程进行梳理,确保施工过程中的每一个环节都有章可循。
2.人员准备:选拔具有丰富经验的施工队伍,进行技术培训,确保每个施工人员都熟悉工艺管道的安装要求。
3.物资准备:提前采购符合国家标准的管道、阀门、法兰等材料,保证施工过程中的材料供应。
三、施工流程及要点1.管道预制:根据施工图纸,将管道进行分段预制,确保管道安装的准确性。
预制过程中,要注意管道的清洁、除锈、焊接等环节。
3.管道试压:管道安装完毕后,进行试压,检查管道的严密性。
试压合格后,进行管道冲洗,确保管道内部清洁。
4.阀门安装:根据施工图纸,将阀门安装到指定位置,确保阀门的开闭灵活、严密。
5.管道保温:对需要保温的管道进行保温处理,确保管道在运行过程中保持稳定温度。
6.管道防腐:对管道进行防腐处理,延长管道的使用寿命。
四、施工质量控制1.严格执行国家标准,确保管道安装质量。
2.施工过程中,对关键环节进行严格把控,如管道焊接、试压等。
3.对施工人员进行质量意识培训,提高施工质量。
4.定期进行质量检查,发现问题及时整改。
五、施工安全及环保1.严格执行国家安全生产法规,确保施工安全。
2.对施工现场进行合理布局,减少安全隐患。
3.对施工人员进行安全培训,提高安全意识。
4.施工过程中,注意环保,减少对环境的影响。
六、施工进度安排1.制定详细的施工进度计划,确保施工进度顺利进行。
2.对施工进度进行实时监控,确保施工进度与计划相符。
3.遇到施工难题,及时进行调整,确保施工进度不受影响。
七、施工验收1.施工完成后,进行验收,确保施工质量达到国家相关标准。
工艺管道安装施工方案

工艺管道安装施工方案 The document was finally revised on 2021工艺管道安装施工方案1.工艺管道施工的一般性要求和应遵循的原则工艺管道安装应对照工艺设备及管道布置图执行,并同时对照各流程图、系统图配合使用。
如发现设计图纸有错误或不合理时,应征得设计单位同意后方可修改。
安装施工前施工人员应熟悉图纸及有关规定、规范,并由工程技术人员对图纸进行必要的技术交底。
管道系统中所有的管子、管件、阀门及仪表必须具有制造厂的合格证;并应按《规范》进行检验。
2、工艺管道安装主要程序管道施工程序详见《工艺管道安装程序图》。
工艺管道安装程序图熟悉图纸资料设计交底现场测原材料除锈油漆支吊托架支吊托架的管子附件与除锈防腐管材下料管子套管子组管子安管子坡管子组管子焊管子吊管道系系统防腐3、管子支吊架的安装安装前的准备工作:管道支吊架用的弹簧应进行外观、外形尺寸检查;并应有出厂合格证。
根据设计图纸先确定出固定支架及补偿器的位置,再按管道标高确定支架的标高及位置。
无坡度的管道,在同一水平直线上把支架位置画在墙或柱于上。
有坡度的管道,应根据两点的距离和坡度大小,算出两点间高差,在两点间拉一直线,按照支架的间距,在墙上或柱子上画出每个支架的位置。
安装要求:3.2.1支架、横梁应牢固地固定在墙、柱子或其他结构物上;横梁长度方向应水平,顶面应与管子中心线平行。
3.2.2支吊架与管子接触部分要良好、紧密,一般不得有间隙,管道与托架焊接时,不得有咬肉、烧穿等现象。
3.2.3 从干管接出的较大管径支管为立管敷设时,立管的荷重应设置专用托架承担,不得由干管与支管的焊接口承担。
3.2.4活动支架不应妨碍管道由于热膨胀所引起的移动。
管道在支架横梁或支座上滑动时,支架或支座不应出现水平偏斜、倒塌或使管道卡住。
保温层不得妨碍热位移。
3.2.5补偿器的两侧应按要求安装导向支架,使管道在支架上伸缩时不至偏移中心线。
3.2.6不得在钢屋架上任意焊接支、吊架,确实需要焊接时,应征得设计单位同意;不得在设备上任意焊接支架,如设计同意焊接时,应在设备上焊接加强板,再焊接支架。
工艺管道安装施工方案
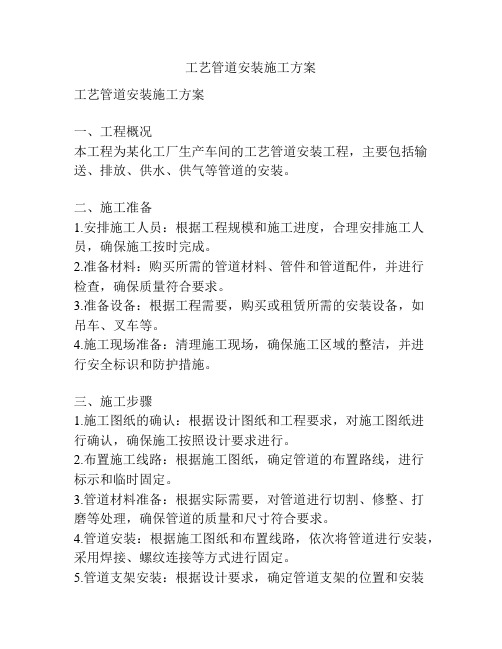
工艺管道安装施工方案工艺管道安装施工方案一、工程概况本工程为某化工厂生产车间的工艺管道安装工程,主要包括输送、排放、供水、供气等管道的安装。
二、施工准备1.安排施工人员:根据工程规模和施工进度,合理安排施工人员,确保施工按时完成。
2.准备材料:购买所需的管道材料、管件和管道配件,并进行检查,确保质量符合要求。
3.准备设备:根据工程需要,购买或租赁所需的安装设备,如吊车、叉车等。
4.施工现场准备:清理施工现场,确保施工区域的整洁,并进行安全标识和防护措施。
三、施工步骤1.施工图纸的确认:根据设计图纸和工程要求,对施工图纸进行确认,确保施工按照设计要求进行。
2.布置施工线路:根据施工图纸,确定管道的布置路线,进行标示和临时固定。
3.管道材料准备:根据实际需要,对管道进行切割、修整、打磨等处理,确保管道的质量和尺寸符合要求。
4.管道安装:根据施工图纸和布置线路,依次将管道进行安装,采用焊接、螺纹连接等方式进行固定。
5.管道支架安装:根据设计要求,确定管道支架的位置和安装方式,并进行固定。
6.管道的测试与检查:安装完毕后,对管道进行压力测试和泄漏检查,确保管道的安全性和可靠性。
7.防腐保温处理:根据工艺要求,对管道进行防腐保温处理,确保管道的使用寿命和工艺要求。
8.验收及试运行:完成管道安装后,进行验收及试运行,确保设备的正常运行。
四、安全措施1.施工现场要划定区域,设置安全警示标志,确保施工人员的安全。
2.施工人员要带好个人防护用品,如安全帽、安全鞋等,严禁操作时戴帽子、拖鞋等不符合安全要求的行为。
3.施工人员要严格按照操作规程进行施工,禁止翻越管道、跨越设备等危险行为。
4.施工过程中要定期检查设备、工具和材料的使用情况,确保其安全可靠。
5.对施工人员进行安全培训,教育其安全知识与操作规程,提高施工安全意识。
以上是本次工艺管道安装施工方案的主要内容,通过合理的组织和安排,确保施工质量和进度,同时加强安全措施,最大程度地减少施工事故的发生。
工艺管道安装工程方案
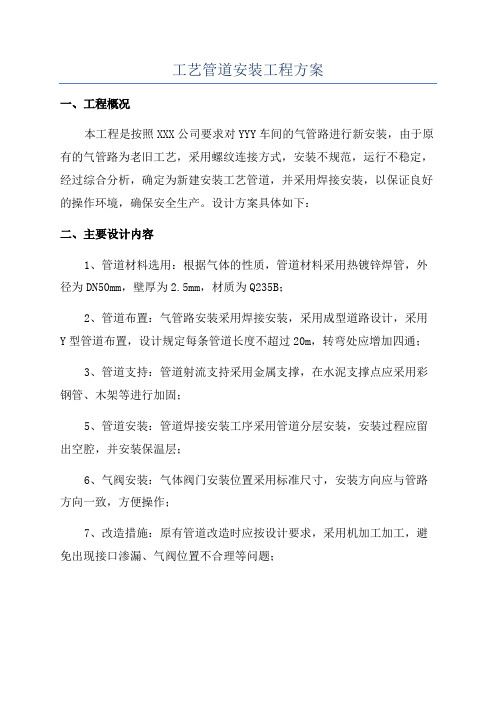
工艺管道安装工程方案
一、工程概况
本工程是按照XXX公司要求对YYY车间的气管路进行新安装,由于原有的气管路为老旧工艺,采用螺纹连接方式,安装不规范,运行不稳定,经过综合分析,确定为新建安装工艺管道,并采用焊接安装,以保证良好的操作环境,确保安全生产。
设计方案具体如下:
二、主要设计内容
1、管道材料选用:根据气体的性质,管道材料采用热镀锌焊管,外径为DN50mm,壁厚为2.5mm,材质为Q235B;
2、管道布置:气管路安装采用焊接安装,采用成型道路设计,采用Y型管道布置,设计规定每条管道长度不超过20m,转弯处应增加四通;
3、管道支持:管道射流支持采用金属支撑,在水泥支撑点应采用彩钢管、木架等进行加固;
5、管道安装:管道焊接安装工序采用管道分层安装,安装过程应留出空腔,并安装保温层;
6、气阀安装:气体阀门安装位置采用标准尺寸,安装方向应与管路方向一致,方便操作;
7、改造措施:原有管道改造时应按设计要求,采用机加工加工,避免出现接口渗漏、气阀位置不合理等问题;。
现场工艺管道焊接施工方案
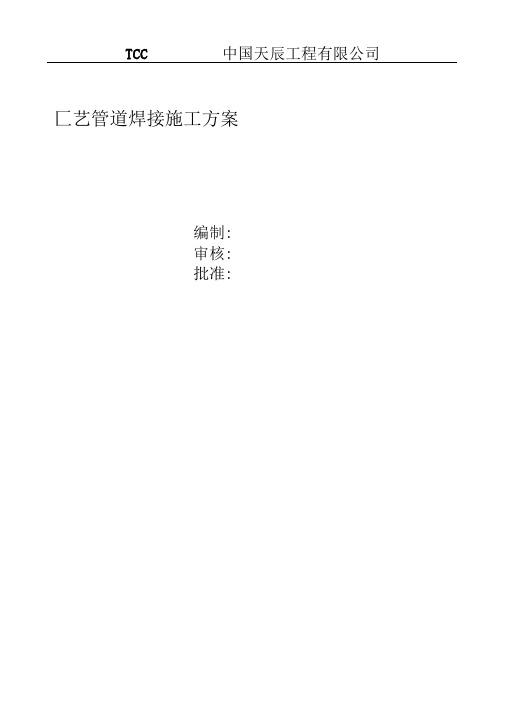
匚艺管道焊接施工方案编制:审核:批准:1.编制说明2.工程概况3.施工组织4.施工机具5.施工方法和工艺措施6.焊接检验107.焊缝返工118.焊接质量控制点11 9.危险源分析•1210,施工HSE措施14〕艺管道焊接方案,编制说明和依据1,编制说明本方案为神华包头煤制烯烃项目,全厂外管廊工艺管道安装,焊接方案。
本方案重点叙述了金属管道安装,焊接,施工方法、质量检验、质量保证措施,对管道的吹扫试压仅作了一般原则性的规定。
具体详细方案要根据现场实际情况作出切实、合理、可行的试压,吹扫,冲洗方案。
本方案根据设计文件,业主、EPCM等有关领导人的意见要求编制,不是很完善,如有的地方可作必要的修改和补充。
编制依据2, 1招标文件及施工图纸,设计说明2施工验收规范1.1 编制目的本方案适用于全厂外管廊工艺管道安装焊接。
为了神华煤制烯烃项目全厂外管廊,能够顺利进行,安全,质量,进度,满足业主的要求,各项技术指标达到和满足设计,国家标准的要求。
2,编制依据施工图纸;设计文件神华包头煤制烯烃项目管理规定和国家相应施工验收标准。
本工程,管道材质主要有:碳钢、不锈钢、耐热合金钢和低温钢等。
参照国家以及相关行业标准规范GB50235-2010,工业金属管道施工及验收规范GB50236-2011,现场设备,工艺管道焊接工程施工及验收规范GB50184-2010,工业金属管道工程质量检验评定标准GB50185-93,工业设备及管道绝热工程质量检验评定标准SH350J2002,石油化工剧毒,可燃介质管道工程施工及验收规范GB/T3323-2005,金属熔化焊焊接接头射线照相GB985-88,气焊,手工电弧焊及气体保护焊焊缝坡口基本形式与尺寸,GB98395 ,不锈钢焊条 GB511795 ,碳钢焊条 GB511895 ,低合金钢焊条GB/T8110-95 ,气保焊,碳钢,低合金钢焊丝 GB/T14957-94,熔化焊用焊丝 GB/T14958-94,气保焊用焊丝GB/T4241-2006,焊接用不锈钢盘条,《焊丝》 GB/T19419-2003,焊接管理,任务与职责 GB8923-88,涂装前钢材表面锈蚀等级和除锈等级 GB/T19866-2005,焊接工艺规程及评论的一般原则 YB/T5092-2005,焊接用不锈钢焊丝 SH3520-91,石化铬钼耐热钢焊接工艺规程 SH3525-2004,石油化工低温钢焊接工艺规程 SH3526-99,石油化工异种钢焊接规程二,工程概况2.1工程概述全厂外管廊分三个标段:JB4708-2000, 钢制压力容器焊接工艺评定 JB4709-2007, 钢制压力容器焊接工艺规程 JB4730-2005, 金属熔化焊焊接接头射线照相 JB/T3223-96, 焊接材料质量管理规程A 、B 、C1,A 标段:2、3、& 9、10、12、13、14、17、24、25、个管廊,工艺管道约: 33637.9米,其中:碳钢无缝管:22931.9米,碳钢有缝管:4887.3米,合金钢管:2157.9米,不锈钢管: 4200.8 米,焊接:132961达因数。
管道焊接专项施工方案
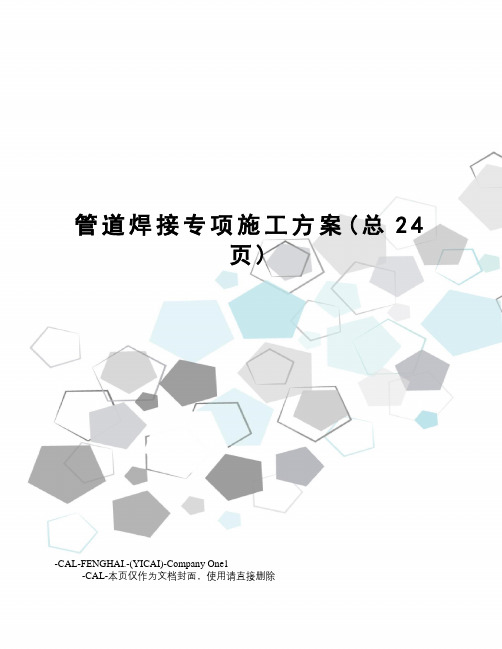
管道焊接专项施工方案(总24页)-CAL-FENGHAI.-(YICAI)-Company One1-CAL-本页仅作为文档封面,使用请直接删除管道焊接专项施工方案1工程管理目标1.1焊接材料使用准确率达100%;1.2焊接、检验及热外理施工规范、标准及技术措施的贯彻率100%;1.3分项工程管道焊口焊接接头表面质量合格率100%,优良品率≥98%;1.4管道焊口射线探伤一次质量合格率96%(按片数计),合格率100%;1.5建筑、安装工程焊接接头焊口(缝)合格率达100%;1.6无损探伤、金属检验及热处理施工准确率达100%;1.7焊接、检验及热处理施工人员持证上岗率100%;2焊接施工适用焊接规范3焊接工程量介绍管径最大的2000㎜,管道长度50.3km,管件数量约为700个,达因数约为88000。
管道材质主要包括15CrMoG、16MnDG、0Cr19Ni9、20#、L245、20#镀锌、20G、Q235B、09MnNiDR。
另外,管道附件有各种类型和材质的阀门、管件等。
管道介质主要为:空气、氮气、氧气、氢气、合成气、各类甲醇、C4类气体、各类火炬气、丙烯、丁烯-1、乙烯、蒸汽、冷凝液、酸性水、硫酸、热水、瓦斯气、乙烯-1、异烷、32%烧碱、丙烷、净化水、脱盐水等。
4主要焊接施工设备机具和人员计划4.1主要焊接施工设备机具4.2主要焊接施工人员计划5主要焊接管理人员职责与专业分工5.1总工程师●组织审核和批准焊接专业施工方案、焊接工艺评定及焊接管理制度等;●组织协调所需焊接人员、焊接设备、焊接机具等资源,确保焊接工作正常开展;●主持新材料、新工艺评定;●支持焊接专业工程师开展焊接技术管理。
5.2焊接工程师●整理上报焊接工艺评定和组织焊工考试有关事宜;●焊接、检验及热处理施工作业指导书以及技术方案措施的编制及实施;●焊接监督范围内的原材料、成品、半成品的进厂检验和验收签证;●焊接、检验及热处理施工人员资质培训、资格审查与日常管理;●焊接、检验及热处理施工过程的质量检查和验收;●主持焊接、检验及热处理施工各类记录、报告及技术文件资料的日常检查、归档和竣工移交工作。
化工工艺设备安装及管道安装施工方案
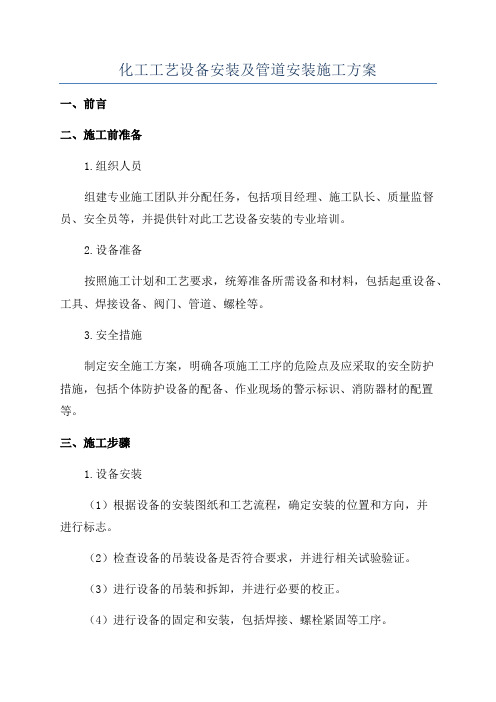
化工工艺设备安装及管道安装施工方案一、前言二、施工前准备1.组织人员组建专业施工团队并分配任务,包括项目经理、施工队长、质量监督员、安全员等,并提供针对此工艺设备安装的专业培训。
2.设备准备按照施工计划和工艺要求,统筹准备所需设备和材料,包括起重设备、工具、焊接设备、阀门、管道、螺栓等。
3.安全措施制定安全施工方案,明确各项施工工序的危险点及应采取的安全防护措施,包括个体防护设备的配备、作业现场的警示标识、消防器材的配置等。
三、施工步骤1.设备安装(1)根据设备的安装图纸和工艺流程,确定安装的位置和方向,并进行标志。
(2)检查设备的吊装设备是否符合要求,并进行相关试验验证。
(3)进行设备的吊装和拆卸,并进行必要的校正。
(4)进行设备的固定和安装,包括焊接、螺栓紧固等工序。
2.管道安装(1)根据管道系统设计图纸,确定管道系统的布置和排布。
(2)对设备间和设备与管道之间的联接进行焊接、螺纹连接等操作,并进行相关试验验证。
(3)安装阀门、法兰等附件,并进行必要的调试和校验。
(4)对管道进行固定和支撑,保证管道系统的牢固和稳定。
3.管道系统测试和清理(1)进行管道系统的试压测试,检查管道系统的密封性能。
(2)对管道系统进行清洗,除去管道内的杂质和残留物。
(3)进行管道系统的通水、通气试验,检查管道系统是否正常运行。
四、质量控制1.设备和材料的检验对所购买的设备和材料进行必要的检验和验收,包括材料的质量、型号和数量等。
2.施工现场质量控制制定施工质量验收标准,严格按照标准进行施工质量的检查和验收,确保所安装的设备和管道符合要求。
3.施工记录和报告对施工过程中的重要数据和信息进行记录和报告,包括焊接记录、试验数据、设备规格、管道图纸等,以备后期的过程追溯和质量评估。
五、安全控制1.安全培训组织施工人员进行必要的安全培训,提高施工人员的安全意识和技能。
2.安全监督设立专门的安全检查组,定期进行现场安全检查和隐患排查,及时发现和处理安全问题。
工艺管道安装施工方案
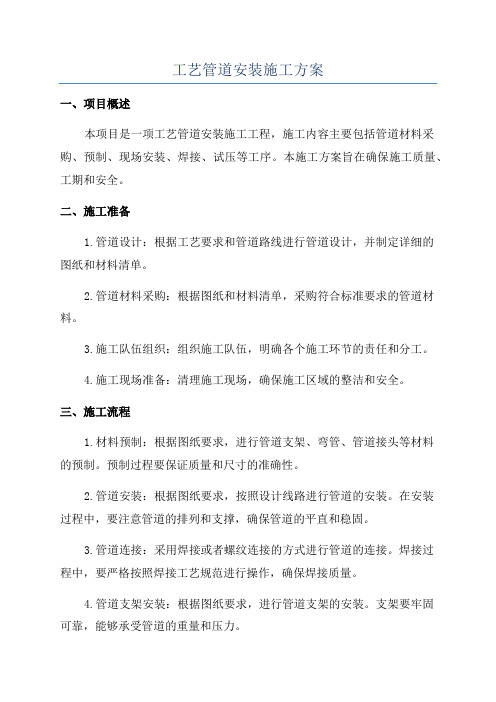
工艺管道安装施工方案一、项目概述本项目是一项工艺管道安装施工工程,施工内容主要包括管道材料采购、预制、现场安装、焊接、试压等工序。
本施工方案旨在确保施工质量、工期和安全。
二、施工准备1.管道设计:根据工艺要求和管道路线进行管道设计,并制定详细的图纸和材料清单。
2.管道材料采购:根据图纸和材料清单,采购符合标准要求的管道材料。
3.施工队伍组织:组织施工队伍,明确各个施工环节的责任和分工。
4.施工现场准备:清理施工现场,确保施工区域的整洁和安全。
三、施工流程1.材料预制:根据图纸要求,进行管道支架、弯管、管道接头等材料的预制。
预制过程要保证质量和尺寸的准确性。
2.管道安装:根据图纸要求,按照设计线路进行管道的安装。
在安装过程中,要注意管道的排列和支撑,确保管道的平直和稳固。
3.管道连接:采用焊接或者螺纹连接的方式进行管道的连接。
焊接过程中,要严格按照焊接工艺规范进行操作,确保焊接质量。
4.管道支架安装:根据图纸要求,进行管道支架的安装。
支架要牢固可靠,能够承受管道的重量和压力。
5.管道试压:安装完成后,对管道进行试压,确保管道的密封性和耐压能力。
6.管道验收:在试压合格后,对管道进行验收,确保管道的安装符合设计和规范要求。
7.清理整理:清理施工现场,整理材料和工具,确保施工现场的整洁和安全。
四、安全措施1.严格按照安全操作规程进行施工,确保施工人员的人身安全。
2.施工现场设置安全警示标识,防护措施要到位。
3.对施工人员进行安全培训,提高他们的安全意识和应急处理能力。
4.使用符合标准的防护装备,确保施工过程中的安全。
五、质量控制1.管道材料的采购要严格按照标准要求,确保材料的质量。
2.施工过程中要进行质量检测,如焊缝的X射线检测、管道的尺寸检测等,确保施工质量。
3.施工过程中要严格按照焊接工艺规范操作,确保焊接质量。
4.施工完成后,进行管道的试压,确保管道的密封性和耐压能力。
六、施工进度控制1.制定详细的施工计划和进度安排,明确各个施工环节的工期。
工艺管道焊接施工方案范本

工艺管道焊接施工方案范本1. 引言本文档旨在提供一份工艺管道焊接施工方案的范本,以帮助施工团队编写详细的施工方案。
施工方案是为了确保工艺管道焊接施工的顺利进行,对组织施工活动、确保工程质量、提高工作效率起到重要的指导作用。
2. 目标工艺管道焊接施工方案的目标如下:•确保施工工艺管道的质量符合相关标准和规范要求;•组织施工队伍合理布置,确保施工进度按计划进行;•确保施工过程安全,预防事故的发生;•保持与业主、监理单位的良好沟通,及时解决施工中的问题。
3. 施工准备工作在开始施工前,需要进行以下准备工作:3.1 材料准备根据设计图纸和材料清单,准备所需的焊接材料,包括焊丝、焊条、输送管道等。
确保材料的品质符合相关标准和规范的要求。
3.2 人员组织组织施工队伍,包括焊接工、助焊工、安全员等,确保每个岗位上有合格的人员执行施工任务。
3.3 设备检查检查焊接设备的完好性和安全性,确保设备能正常运行,并做好设备的维护和保养工作。
制定并宣传安全操作规程,培训施工人员的安全意识,确保施工过程中安全操作。
4. 施工流程4.1 确定焊接参数根据设计要求和焊接材料的特性,确定焊接参数,包括焊接电流、焊接电压、焊接速度等。
4.2 表面处理针对待焊接的管道材料,进行必要的表面处理,包括除锈、打磨等,确保焊接接头的质量。
4.3 焊接工艺选择根据工程要求和焊接材料的特性,选择合适的焊接工艺,包括手工电弧焊、气体保护焊等。
按照焊接工艺进行焊接施工,确保焊接接头的质量和强度满足设计要求。
在施工过程中,应注意焊接工艺的控制和焊接质量的检查。
4.5 清理整理在焊接施工完成后,进行清理整理工作,包括焊接接头的除渣、清理现场等,确保施工现场整洁。
5. 质量控制5.1 焊接质量检查进行焊接质量的检查工作,包括外观检查和尺寸检测等,确保焊接接头的质量符合相关标准和规范要求。
5.2 非破坏性检测根据焊接接头的重要性和工艺要求,进行必要的非破坏性检测工作,如超声波检测、射线检测等,确保焊接接头的质量。
工艺管道施工方案
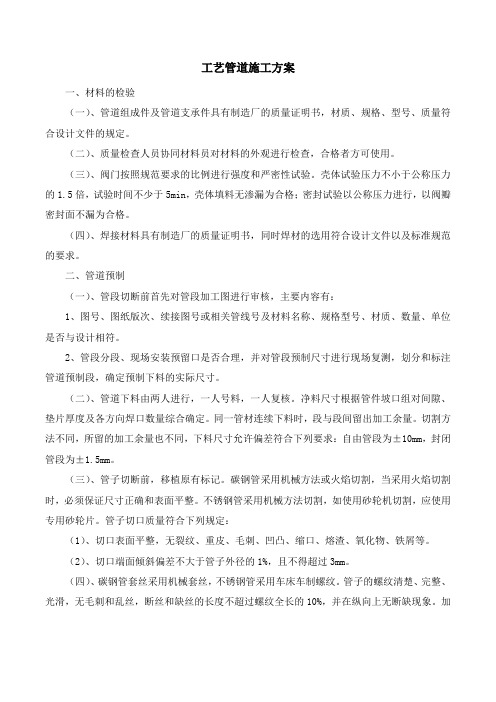
工艺管道施工方案一、材料的检验(一)、管道组成件及管道支承件具有制造厂的质量证明书,材质、规格、型号、质量符合设计文件的规定。
(二)、质量检查人员协同材料员对材料的外观进行检查,合格者方可使用。
(三)、阀门按照规范要求的比例进行强度和严密性试验。
壳体试验压力不小于公称压力的1.5倍,试验时间不少于5min,壳体填料无渗漏为合格;密封试验以公称压力进行,以阀瓣密封面不漏为合格。
(四)、焊接材料具有制造厂的质量证明书,同时焊材的选用符合设计文件以及标准规范的要求。
二、管道预制(一)、管段切断前首先对管段加工图进行审核,主要内容有:1、图号、图纸版次、续接图号或相关管线号及材料名称、规格型号、材质、数量、单位是否与设计相符。
2、管段分段、现场安装预留口是否合理,并对管段预制尺寸进行现场复测,划分和标注管道预制段,确定预制下料的实际尺寸。
(二)、管道下料由两人进行,一人号料,一人复核。
净料尺寸根据管件坡口组对间隙、垫片厚度及各方向焊口数量综合确定。
同一管材连续下料时,段与段间留出加工余量。
切割方法不同,所留的加工余量也不同,下料尺寸允许偏差符合下列要求:自由管段为±10mm,封闭管段为±1.5mm。
(三)、管子切断前,移植原有标记。
碳钢管采用机械方法或火焰切割,当采用火焰切割时,必须保证尺寸正确和表面平整。
不锈钢管采用机械方法切割,如使用砂轮机切割,应使用专用砂轮片。
管子切口质量符合下列规定:(1)、切口表面平整,无裂纹、重皮、毛刺、凹凸、缩口、熔渣、氧化物、铁屑等。
(2)、切口端面倾斜偏差不大于管子外径的1%,且不得超过3mm。
(四)、碳钢管套丝采用机械套丝,不锈钢管采用车床车制螺纹。
管子的螺纹清楚、完整、光滑,无毛刺和乱丝,断丝和缺丝的长度不超过螺纹全长的10%,并在纵向上无断缺现象。
加工螺纹长度以拧紧后露出2~3扣为合格。
管口螺纹加工后妥善保护,可拧上一个管箍或用胶带纸包扎。
(五)、坡口的加工采用机械方法,碳钢管也可采用氧乙炔焰热加工方法,在采用热加工方法加工坡口后,要除去坡口表面的氧化皮、熔渣及影响接头质量的表面层,并将凹凸不平处打磨平整。
管道焊接专项施工方案

XXXX工程管道焊接专项施工方案编制人:审核人:审批人:编制单位:XXXXX有限公司编制日期:XXXXX年目录一、工程概况 (3)二、编制说明 (6)三、施工准备 (6)四、焊接工艺技术 (10)五、质量控制检查 (11)六、安全保证措施及文明施工 (14)一、工程概况XXXXXX项目设备与管道安装工程,包括新工艺生产车间、成品罐区(QA罐+高位酸罐)、酸碱原料/新糖化罐区、水道车间、空压站区域设备、管网、设备及管网相关传感器与执行器、保温等安装工程。
XXXXX有限公司老车间设备与管道改造工程,包括老生产车间、原成品罐区、原糖化罐区、原调浆罐区、以及蒸汽外网。
新建及改造工程内容包括:工艺设备安装、不锈钢管网、碳钢管网、风管管网、碳钢衬胶管网、UPVC/FRP管网、软管、不锈钢阀门、碳钢阀门、碳钢衬胶阀门及非金属阀门、不锈钢管件、碳钢、碳钢衬胶及非金属管件、其他管件(螺栓,软连接、垫片等)、仪表及配件、非标结构、保温材料、防腐材料。
本次需进行焊缝探伤检测的是中压蒸汽(LMS)(10%)、低压蒸汽(LLS)管线(5%)、中压凝结水(SCM)(5%)、低压凝结水(SCL)(5%)、以及不锈钢工艺管道(5%)。
本工程采用X射线机或Se75进行透照,以保证正常的检测质量。
工程工艺管线射线检测工作量大致如下:二、编制说明1、为了保证焊接这一特殊工序的全过程能得到有效的控制和顺利的实施,确保管道焊接的质量和施工进度,特编制该管道焊接方案,用以指导现场的焊接工作。
2、编制依据及引用标准(1)《钢结构设计规范》GB50017-2003(2)《钢结构工程施工质量验收规范》GB50205-2001(3)《现场设备、工业管道焊接工程施工规范》GB50236-2011 (4)《现场设备工业管道焊接工程施工质量验收规范》GB50683-2011 (5)《工业金属管道工程施工质量验收规范》GB50184-2011(6)《埋地钢质管道环氧煤沥青防腐层技术标准》SY/T0447-2014 (7)《碳钢焊条》GB/T5117-20123、焊接工程量及主要技术要求三、施工准备1、焊前准备焊件的切割和坡口加工应符合下列规定:碳钢及碳锰钢坡口加工可采用机械方法和火焰切割方法;焊件组对前及焊接前,应将坡口及内外侧表面不小于20mm范围内的杂质、污物、毛刺和镀锌层等清理干净,并不得有裂纹、夹层等缺陷。
管道安装焊接工程施工方案
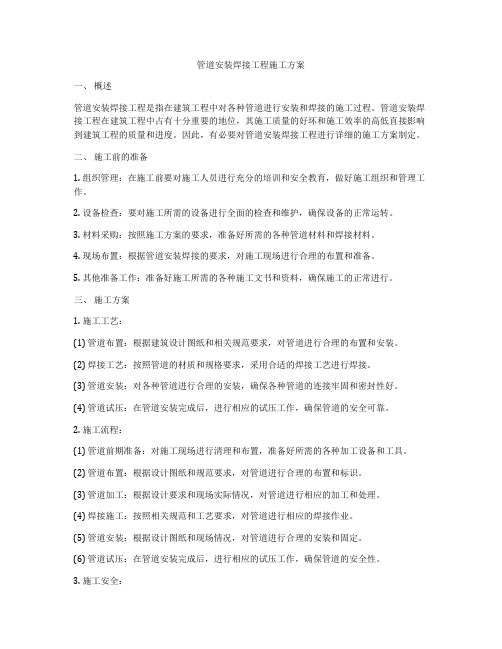
管道安装焊接工程施工方案一、概述管道安装焊接工程是指在建筑工程中对各种管道进行安装和焊接的施工过程。
管道安装焊接工程在建筑工程中占有十分重要的地位,其施工质量的好坏和施工效率的高低直接影响到建筑工程的质量和进度。
因此,有必要对管道安装焊接工程进行详细的施工方案制定。
二、施工前的准备1. 组织管理:在施工前要对施工人员进行充分的培训和安全教育,做好施工组织和管理工作。
2. 设备检查:要对施工所需的设备进行全面的检查和维护,确保设备的正常运转。
3. 材料采购:按照施工方案的要求,准备好所需的各种管道材料和焊接材料。
4. 现场布置:根据管道安装焊接的要求,对施工现场进行合理的布置和准备。
5. 其他准备工作:准备好施工所需的各种施工文书和资料,确保施工的正常进行。
三、施工方案1. 施工工艺:(1) 管道布置:根据建筑设计图纸和相关规范要求,对管道进行合理的布置和安装。
(2) 焊接工艺:按照管道的材质和规格要求,采用合适的焊接工艺进行焊接。
(3) 管道安装:对各种管道进行合理的安装,确保各种管道的连接牢固和密封性好。
(4) 管道试压:在管道安装完成后,进行相应的试压工作,确保管道的安全可靠。
2. 施工流程:(1) 管道前期准备:对施工现场进行清理和布置,准备好所需的各种加工设备和工具。
(2) 管道布置:根据设计图纸和规范要求,对管道进行合理的布置和标识。
(3) 管道加工:根据设计要求和现场实际情况,对管道进行相应的加工和处理。
(4) 焊接施工:按照相关规范和工艺要求,对管道进行相应的焊接作业。
(5) 管道安装:根据设计图纸和现场情况,对管道进行合理的安装和固定。
(6) 管道试压:在管道安装完成后,进行相应的试压工作,确保管道的安全性。
3. 施工安全:(1) 现场管理:建立健全的施工现场管理制度,确保施工现场的秩序和安全。
(2) 安全教育:对施工人员进行全面的安全教育和培训,提高其安全意识和操作技能。
(3) 安全设施:配备必要的安全设施,确保施工现场的安全和环?;嵋淞砵么某ぁ保?。
工艺管道安装施工方案
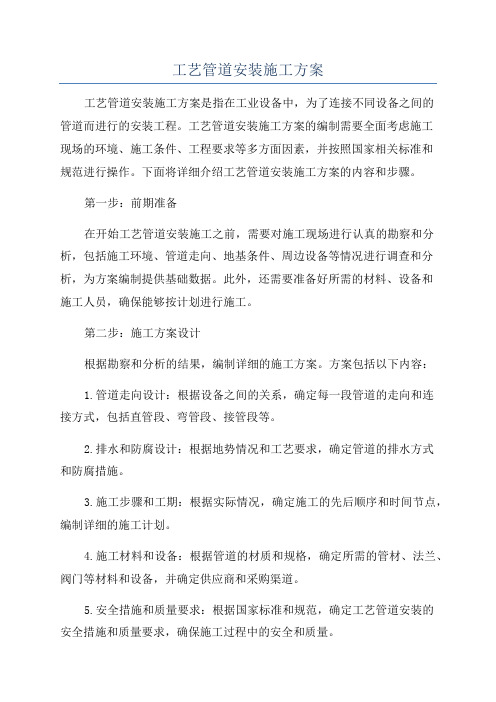
工艺管道安装施工方案工艺管道安装施工方案是指在工业设备中,为了连接不同设备之间的管道而进行的安装工程。
工艺管道安装施工方案的编制需要全面考虑施工现场的环境、施工条件、工程要求等多方面因素,并按照国家相关标准和规范进行操作。
下面将详细介绍工艺管道安装施工方案的内容和步骤。
第一步:前期准备在开始工艺管道安装施工之前,需要对施工现场进行认真的勘察和分析,包括施工环境、管道走向、地基条件、周边设备等情况进行调查和分析,为方案编制提供基础数据。
此外,还需要准备好所需的材料、设备和施工人员,确保能够按计划进行施工。
第二步:施工方案设计根据勘察和分析的结果,编制详细的施工方案。
方案包括以下内容:1.管道走向设计:根据设备之间的关系,确定每一段管道的走向和连接方式,包括直管段、弯管段、接管段等。
2.排水和防腐设计:根据地势情况和工艺要求,确定管道的排水方式和防腐措施。
3.施工步骤和工期:根据实际情况,确定施工的先后顺序和时间节点,编制详细的施工计划。
4.施工材料和设备:根据管道的材质和规格,确定所需的管材、法兰、阀门等材料和设备,并确定供应商和采购渠道。
5.安全措施和质量要求:根据国家标准和规范,确定工艺管道安装的安全措施和质量要求,确保施工过程中的安全和质量。
第三步:施工现场准备在施工开始之前,需要对施工现场进行准备工作,包括以下内容:1.土方开挖和地基处理:根据管道走向的要求,进行土方开挖和地基处理,确保管道的铺设和支撑稳固。
2.施工场地平整和通风:确保施工现场平整,便于操作,并提供良好的通风条件。
第四步:管道安装根据施工方案进行管道的铺设和安装,包括以下步骤:1.管道定位和布局:按照设计要求,将管道进行定位,并按照布局图将各个管段进行连接,并使用法兰进行固定。
2.管道焊接和密封:根据管道材质和规格,进行管道的焊接和密封处理,确保管道的完整性和耐用性。
3.管道支撑和固定:根据管道规格和重量,在施工现场进行管道的支撑和固定,确保管道的稳定性和安全性。
车间工艺管道安装施工方案
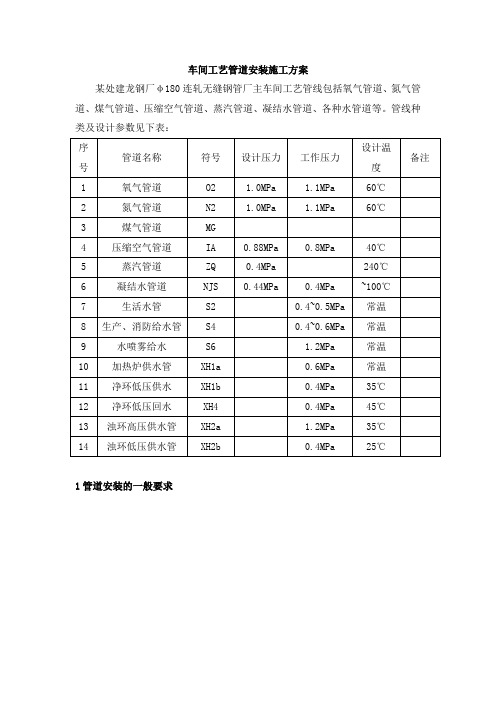
车间工艺管道安装施工方案某处建龙钢厂φ180连轧无缝钢管厂主车间工艺管线包括氧气管道、氮气管道、煤气管道、压缩空气管道、蒸汽管道、凝结水管道、各种水管道等。
管线种类及设计参数见下表:1管道安装的一般要求a) 管道施工程序b) 管道材料验收1)管子、管件到位后,按有关国家和行业标准对其外观进行检查验收。
2)管子、管件安装焊接前要进行酸洗除锈及有脱脂要求的管子还必须进行酸洗、脱脂。
管子、管件酸洗、脱脂要有相应的验收资料或出厂检验合格资料。
酸洗、脱脂后的管子及管件运到现场前其两端一定要封扎严实。
3)阀门到货后对有强度及密封性试验要求的阀门要进行强度及密封性试验。
c) 预制的内容1)管材到货及验收后,应根据图纸和走向空间,能地面组对、煨弯的,应尽量在地面进行,减少空中作业。
2)管道支架应提前预制好。
3)埋地管道施工前应进行管道的防腐工作,根据设计要求确定防腐材料,防腐后的管道根据设计及业主要求进行电火花检测及粘贴强度和防腐厚度的检验。
4)针对不锈钢材质的特性,不锈钢管的现场切割应采用手锯、管刀、等离子切割机等,不得使用氧-乙炔焰切割。
在管径及壁厚较小,采用管刀切割时,管口毛刺要用锉刀进行加工。
d) 管道安装要求管道安装总体精度要求如下,如与设计不符应按设计要求执行。
管道安装的允许偏差表e) 主车间架空管道的安装架空管道可利用车间内天车和临时吊具(吊杆和配重组成)将管道送到安装部位,或者利用挂在上部厂房上的定滑轮用卷扬机吊装到位,对于重量较轻较小的管道,可利用人力拽滑轮组的方法吊装就位。
f) 管道焊接1)管道的焊接要求①焊工一定要持证上岗,对压力管道施焊的焊工还必须要有焊接压力容器的上岗证书。
②管子及管件在对接之前一定要打坡口,坡口加工宜采用机械方法进行,如用气焊切割,必须将坡口部分打磨平整后方可进行焊接。
管道焊接的坡口型式和要求③焊条、焊丝的选用应符合设计文件的要求,焊条要在规定的温度和时间烘干后才可使用,且要有专人负责管理。
- 1、下载文档前请自行甄别文档内容的完整性,平台不提供额外的编辑、内容补充、找答案等附加服务。
- 2、"仅部分预览"的文档,不可在线预览部分如存在完整性等问题,可反馈申请退款(可完整预览的文档不适用该条件!)。
- 3、如文档侵犯您的权益,请联系客服反馈,我们会尽快为您处理(人工客服工作时间:9:00-18:30)。
D:法兰外径 d:孔径
b、安装允许偏差
管道安装允许偏差
项目
架空
坐标及 标高
室外 室内
地沟 埋地 架空 地沟
水平管
Dg≤100(mm)
弯曲
Dg≥100(mm)
立管垂直度
成排
以同一平面上
管段
间距
交叉
管外壁或保温层间距
表 4-3 允许偏差 mm
15
15
25
10
15
1/1000 1.5/1000
最大 20
2/1000
7
而产生的异物应清除干净。
4.3.4 支、吊架预制作
4.3.4.1 支、吊架形式按设计图纸要求选用标准图集。
4.3.4.2 支、吊架的形式、材质、加工尺寸及焊接等应符合设计要求。
4.3.4.3 制作合格的支、吊架,应进行防锈处理,编号标记,妥善保管。
4.4 管道安装就位
4.4.1 管道安装的一般规定
b、角焊缝坡口形状
坡口形式
角焊缝坡口形式
尺寸 a:2.4-4mm b:1-2mm
图 4-1B
b
a
ab
t
a:1.5-3mm b:6.4mm 或 t 中较小者
a:2.4-4mm
6
补强板
坡口形式
尺寸 a:2.4— 4mm b:-1— 1mm c:0.8— 2.4mm d:3— 6mm θ′:30±5 度 θ:45±5 度 a:1.5— 3mm b:3mm 或 0.5t 中较小的 c:0.8— 2.4mm θ:45±5 度
试压前 共检
返修
试压
工程交接
联动试车
综合检查
气密试验
水冲洗
系统吹扫
图 3-1 管道安装流程图
3
4.1.3 施工方案经审批,技术交底和必要的技术培训已完成。 4.1.4 管道施工图纸已按施工需要进行了预处理,探伤比例已确定。 4.1.5 施工执行的标准、规范和验评标准已经确定。 4.1.6 施工各种材质管道的焊接工艺评定合格,焊工具有上岗操作证。 4.1.7 工程材料的检验、试验工作完成,并已作好相应材质的标记。 4.1.8 施工记录和质量评定记录表格齐全。 4.1.9 现场三通一平已满足施工要求,工、机具,手段用料能满足需要。 4.2 材料检验 4.2.1 管子、管件、阀门、紧固件必须有制造厂的合格证明书,其指标应符合本 装置设计及其指定的规范和标准的要求。无质量证明文件及合格证的产品不得使 用。 4.2.2 管子、管件、阀门在领料及使用前首先应核对其规格、型号、材质是否符 合设计要求,然后进行外观检查,要满足以下要求:
Cx min=1.25T , 但 不 小 于 3.2mm
c、对不等厚材料,当厚度差超过 1.5mm 时,应按下图进行加工:
4 1:4 1:4
图 4-2 坡口加工图 d、管道组对错边量不应超过母材壁厚的 10%,且不大于 2.0mm。 4.3.3 管道预制的一般规定 4.3.3.1 预制组件应有足够的刚性,不得产生永久变形。预制完后应及时编号、 封口,妥善保管。 4.3.3.2 管道预制应在 X、Y、Z 三个方向上的适当部位预留调整段或调整口, 调整口的直管段宜加长 50-100mm,调整段宜现场实测。 4.3.3.3 管道上的开孔应在预制时完成。当在已安装管道上开孔时,管内因切割
5
4.3.2.5 坡口及组对
a、管道的坡口加工形式及组对间隙见图 4-1A 和图 4-1B。
对接坡口形式及组对间隙
图 4-1A
(t)壁厚 坡口形状
尺寸
≤8mm
θ b
a′:1.5~2.5mm b:1~1.5mm θ:32.5±2.5 度
>8mm
θ b
a′:2~3mm b:1~1.5mm θ:31.25±2.5 度
钢板尺
图 管道对口平直度
4.4.1.9 管道焊缝位置应符合下列要求: a、直管段两环缝距离不应小于 100mm。 b、焊缝距变管起弯点不得小于 100mm,且不小于管径。 c、环焊缝距支、吊架的净距不小于 50mm,需热处理的焊缝距支、吊架不
得小于焊缝宽度的 5 倍,且不小于 100mm。 d、在环缝上不得开孔,如必须开孔时,焊缝应经无损探伤检查合格。 e、加固圈距环缝不小于 50mm。
某公司车间 工艺管道焊接、安装施工方案
编 制: 审 核: 审 批:
目录
1 编制说明 2 编制依据 3 施工程序 4 管道安装的一般技术要求 5 焊接及焊接检验 6 管道系统压力试验 7 管道系统吹洗 8 安全技术措施 9 施工组织措施 10 工、机具及手段材料计划 11 检验、测量器具配备表
1
1 编制说明 1.1 我单位所承担的裕克施乐 3D 打印车间管道分为:不锈钢空压焊接管道、氧 气铜管道、工艺冷却水不锈钢卡接式管道。 2 编制依据 2.1 《工业金属管道工程施工及验收规范》GB50235-97 2.2 《现场设备、工业管道焊接工程施工及验收规范》GB50236-97 2.3 《工业安装工程质量检验评定统一标准》GB51252-94 2.4 《工业管道工程质量检验评定标准》GB50184-94 3 施工程序 3.1 管道安装的施工程序见图 3-1 3.2 现场管道安装应遵循下列原则: 3.2.1 先地下后地上,先“工艺”后“辅助”,先大后小,并与其它专业工程施 工协调配合,合理交叉,做到安全文明施工,科学管理。 3.2.2 管廊夹套管线与伴热管线同时施工。 3.2.3 管道系统试压应在焊缝检验合格后进行。 3.2.4 管道系统试压完毕后,进行吹扫工作。 4 管道安装的技术要求 4.1 管道安装前具备下列条件: 4.1.1 与管道有关的土建工程经检查合格,满足安装要求。 4.1.2 设计及其它相应技术文件齐全,施工图纸已会审完成。
4.4.2 与传动设备的配管 4.4.2.1 对传动设备,尤其是复杂的传动设备的配管要求。
9
a、设备的进、出口管道,特别是进口管道必须严格清扫,做到彻底无杂物、 焊渣、锈皮等。
b、管道的安装不允许对设备产生任何附加应力,不得用强力拉、推、扭的 方法来补偿安装偏差。
c、管道与设备应做到自由对中。在自由状态下,管道法兰面安装偏差应符 合第 4.4.1.2 条 b 的要求。
a、无裂纹、缩孔、夹渣、折叠、重皮等缺陷。 b、无超过壁厚负偏差的锈蚀或凹陷。 c、验收合格后,不锈钢与碳素钢应分开存放,不得与碳素钢接触。 4.2.3 紧固件检验 4.2.3.1 对所有到货的螺栓紧固件仔细进行检查,螺栓与螺母的螺纹应完整,无 伤痕,毛刺等缺陷,无松动,卡死等现象。 4.2.3.2 检查紧固件的规格、材质的标记,印记应齐全,正确,并符合设计及产 品质量证明书的规定。 4.2.4 法兰检验 4.2.4.1 合金钢法兰应对每批进货(同制造厂、同规格、同型号、同时到货)进 行材质复查,并应做标记。 4.2.4.2 法兰验收应分清型式,其密封面应平整光洁,不得有毛刺及径向沟槽, 凸凹、榫槽面法兰应能自然嵌合。 4.2.5 非金属垫片应质地柔韧,无老化分层现象,表面不应有折损,皱纹等缺陷, 金属垫片的加工尺寸,光洁度和硬度应符合要求,表面不得有裂纹、毛刺、凹槽、 径向划痕及锤斑等缺陷。
2
施工技术准备
工艺 评定
规范及验 评标准
图纸 会审
管架、管托预制 管架安装
方案编写 技术交底
管道预制
下料及 坡口加工
组对
现场 三通 一平
劳动力、工 机具等资 料配置
标记 移植
标记 编号
材料 检验
阀门 检验
材料验收
焊接
管内清扫 封闭(不 锈钢管道 焊缝的酸 洗、冲洗
返修
无损检验
现场 安装
组对
焊接
无损 检验
最大 15
±5
±5
±10
4.4.1.3 管道连接时,不得采用强力对口,加热管子,加偏垫或多层垫等方法来
8
消除接口端面的空隙、偏差、错口或不同心等偏差。 4.4.1.4 流量孔板上、下游直管段的长度应严格按图施工,且在此范围内的焊缝 内表面应与管道内表面平齐。 4.4.1.5 管道与设备连接前应将管内清理干净,并将管道与设备接口用带有特殊 标记的临时盲板隔离。 4.4.1.6 不锈钢管道安装时,不得用铁质工具敲击管道,不得用火焰直接加热调 整,与管道支架之间应用氯离子含量小于 40ppm 的材料隔离。 4.4.1.7 需反复拆装的部位,如设备进、出口、调节阀、孔板法兰、安全阀及所 有水压试验吹扫中需拆除的管段法兰,应选用临时垫片,最后复位时再加装正式 垫片,但加装临时垫片,应在图纸上做记录,临时垫片厚度应与正式垫片厚度一 致。 4.4.1.8 管道对口时应检查平直度(如图 4-4),在距接口中心 200mm 处测量, 当 DN<100mm 时,允许偏差为 1 mm;当 DN≥100mm 时,允许偏差为 2mm, 但全长允许偏差均为 10mm。
d、管道的固定焊口要远离设备。 e、管道经试压吹扫合格后,管道与设备再次连接时的偏差值应符合 b 及 d 条的规定。若有超差则应通过调整支架等办法,使差值缩小直至合格。 4.4.2.2 配管方法和步骤: a、配管应从设备一侧开始安装,其水平度和铅垂度偏差应符合要求。 b、管道法兰和设备法兰组对前,必须把密封面清理干净。注意螺栓孔的中 心对中,使连接螺栓能在螺栓孔内自由出入。 c、管道组装过程中,所有管道支吊架应按设计位置就位。吊架不得倾斜, 弹簧支架的定荷卡板不得取下。在管道封闭焊前,可以使用临时支、吊架或其它 手段使管子就位。从设备口延伸的管段亦可暂用螺栓与机体相连,并在弯头处设 置临时支撑,避免因管道的重量引起设备轴线的偏移(位移)。待合拢口点焊固 定后,即应将所有的临时支架以及设备口法兰的螺栓拆除。使管道在设计支架系 统的支承下及设备法兰口处于自己状态下进行焊接。焊接过程中,经常检查法兰 的相对平行度和对中度,其偏差应符合第 4.4.1.2 条 b 款的规定。否则,应采取 对称焊接变形法将偏差超过部分矫正过来。 4.4.2.3 管道的调整 管道因组对、焊接、焊口热处理、水压(气压)试验、吹扫等工作而产生的法 兰口相对水平度和对中度误差,在设备试车前必须采取措施进行最后调整。调整 方法如下: a、当偏差较小的情况下,一般通过调整支架达到法兰对中。 b、当偏差较大时,割口重焊。 c、不锈钢管不得采用任何加热矫正的方法,但可选择适宜位置的焊缝,应用 焊接变形原理来调整中心,先将焊道层局部打磨,打磨的长度与深度应视 矫正量而定,但深度不超过焊肉厚度的 1/2 为宜。然后重新对打磨部位施焊,