汽轮机大轴直轴方案
防止汽轮机大轴弯曲技术范本

防止汽轮机大轴弯曲技术范本汽轮机大轴弯曲是一种常见的问题,可能会导致机器的失效和意外。
因此,防止汽轮机大轴弯曲是非常重要的。
本文将介绍一些防止汽轮机大轴弯曲的技术范本。
1. 合理设计大轴结构合理设计大轴的结构是防止大轴弯曲的基础。
首先,应尽量避免轴上的集中负载,将负载适当分散到整个轴上,以降低轴的应力。
其次,轴的直径和长度要符合工作负荷和转速的要求,以保证轴的刚度和强度。
2. 选择合适的材料选择合适的材料对于防止大轴弯曲非常重要。
高强度和刚性的材料可以有效地防止轴的弯曲变形。
常用的材料有高合金钢、铸钢和高强度铸铁等。
此外,还应对材料进行适当的热处理,提高其硬度和强度。
3. 加装支撑装置在大轴的设计中加装支撑装置可以有效地防止大轴的弯曲。
支撑装置的作用是增加轴的刚度,减小轴的挠度,从而防止轴弯曲。
常见的支撑装置有轴承和滑动轴承等。
在选择支撑装置时,还应根据轴的受力状况和转速要求进行合理的选择。
4. 合理安装和调整轴的位置在安装大轴时,应保证轴的安装位置和轴心线的垂直度和平行度符合要求。
同时,在安装过程中应注意避免轴的过度拉伸和弯曲变形。
在调整大轴的位置时,应根据轴的受力情况和运行条件进行合理的调整。
5. 加强轴的保养和维护定期对大轴进行保养和维护是防止大轴弯曲的重要措施之一。
保养和维护工作主要包括轴的润滑、冷却和清洁等。
适当的润滑可以减小轴的摩擦和磨损,提高轴的工作效率和寿命。
适当的冷却可以降低轴的温度,减小热膨胀和热变形的影响。
总结起来,防止汽轮机大轴弯曲的技术范本主要包括合理设计大轴结构、选择合适的材料、加装支撑装置、合理安装和调整轴的位置,以及加强轴的保养和维护。
通过采取这些措施,可以有效地减小大轴的弯曲变形,提高汽轮机的工作效率和可靠性。
防止汽轮机大轴弯曲技术范本(2篇)
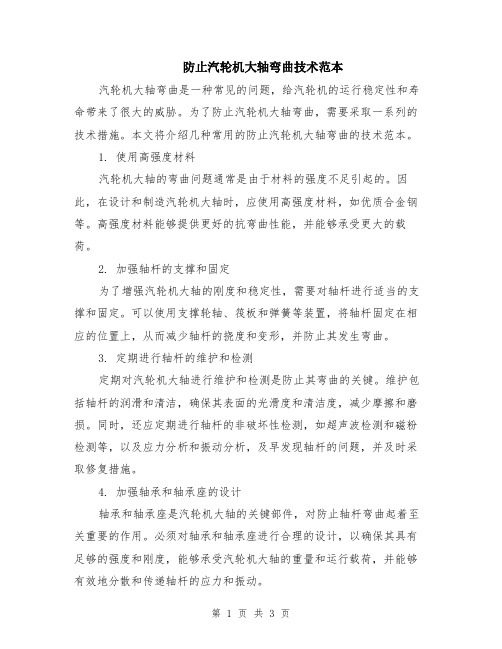
防止汽轮机大轴弯曲技术范本汽轮机大轴弯曲是一种常见的问题,给汽轮机的运行稳定性和寿命带来了很大的威胁。
为了防止汽轮机大轴弯曲,需要采取一系列的技术措施。
本文将介绍几种常用的防止汽轮机大轴弯曲的技术范本。
1. 使用高强度材料汽轮机大轴的弯曲问题通常是由于材料的强度不足引起的。
因此,在设计和制造汽轮机大轴时,应使用高强度材料,如优质合金钢等。
高强度材料能够提供更好的抗弯曲性能,并能够承受更大的载荷。
2. 加强轴杆的支撑和固定为了增强汽轮机大轴的刚度和稳定性,需要对轴杆进行适当的支撑和固定。
可以使用支撑轮轴、筏板和弹簧等装置,将轴杆固定在相应的位置上,从而减少轴杆的挠度和变形,并防止其发生弯曲。
3. 定期进行轴杆的维护和检测定期对汽轮机大轴进行维护和检测是防止其弯曲的关键。
维护包括轴杆的润滑和清洁,确保其表面的光滑度和清洁度,减少摩擦和磨损。
同时,还应定期进行轴杆的非破坏性检测,如超声波检测和磁粉检测等,以及应力分析和振动分析,及早发现轴杆的问题,并及时采取修复措施。
4. 加强轴承和轴承座的设计轴承和轴承座是汽轮机大轴的关键部件,对防止轴杆弯曲起着至关重要的作用。
必须对轴承和轴承座进行合理的设计,以确保其具有足够的强度和刚度,能够承受汽轮机大轴的重量和运行载荷,并能够有效地分散和传递轴杆的应力和振动。
5. 提高汽轮机的运行稳定性汽轮机在运行过程中的不稳定因素也会导致大轴弯曲的发生。
为了防止大轴弯曲,需要提高汽轮机的运行稳定性。
在汽轮机设计和操作中,应充分考虑各种因素的影响,如温度变化、压力变化、负载变化等,采取相应的措施来减少这些因素对汽轮机大轴的影响,从而确保汽轮机的运行稳定性。
综上所述,防止汽轮机大轴弯曲是一个复杂的工程问题,需要从多个方面来进行考虑和解决。
通过使用高强度材料、加强轴杆的支撑和固定、定期进行轴杆的维护和检测、加强轴承和轴承座的设计以及提高汽轮机的运行稳定性等技术手段,可以有效地防止汽轮机大轴的弯曲问题的发生,提高汽轮机的运行效率和寿命。
防止汽轮机大轴弯曲事故技术措施标准版本
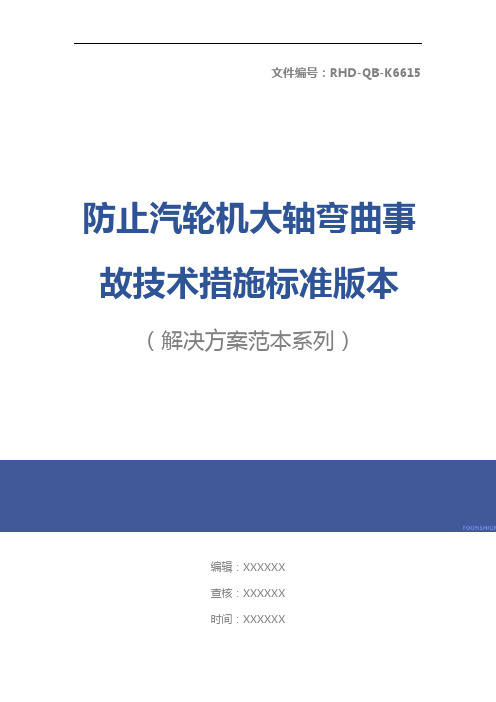
文件编号:RHD-QB-K6615 (解决方案范本系列)编辑:XXXXXX查核:XXXXXX时间:XXXXXX防止汽轮机大轴弯曲事故技术措施标准版本防止汽轮机大轴弯曲事故技术措施标准版本操作指导:该解决方案文件为日常单位或公司为保证的工作、生产能够安全稳定地有效运转而制定的,并由相关人员在办理业务或操作时进行更好的判断与管理。
,其中条款可根据自己现实基础上调整,请仔细浏览后进行编辑与保存。
在机组启、停过程中或正常运行时,由于汽缸变形、振动过大而引起摩擦以及热状态下汽轮机进冷水、冷汽等原因都可能导致汽轮机转子的弯曲。
为防止此类事故发生,特制订以下措施:1、汽缸保温良好,能保证在启、停及正常运行过程中上、下缸不产生过大的温差。
2、首次启动过程中,应适当延长暖机时间,以利于全面检查,并避免潮湿的保温造成汽缸表面受热不均而变形。
3、汽轮机的监测仪表如转速表、大轴晃度表、振动表、汽缸金属温度表、轴向位移表、差胀表等必须齐全、完好、准确、可靠。
4、冲转前,必须符合下列条件,否则禁止启动:4.1大轴晃度值不超过原始值0.02mm,转子偏心小于0.0762mm。
4.2主蒸汽温度应至少高于汽缸最高金属温度50℃,蒸汽过热度不低于50℃4.3转子进行充分的连续盘车,一般不少于4小时。
5、启、停及带负荷过程中,汽轮机各监视仪表都应投入,严格监视汽缸温差、胀差和轴向位移的变化。
有专人监测振动,瓦振达到50μm报警,100μm以上时停机,严禁在临界转速下停留。
6、疏水系统应保证疏水畅通。
机组负荷在20%额定负荷以下,应开启低压调节阀后所有疏水;在10%额定负荷以下时,开启主汽阀后所有汽机本体疏水。
7、热态启动时,严格按规程选择合理的主汽参数,严格遵守操作规程。
轴封供汽温度应与汽缸金属温度匹配,轴封管道经充分疏水后方可投汽,并应先送轴封,后抽真空。
8、机组在启、停和变工况运行时,应按规定曲线和技术指标控制参数变化,特别是应避免汽温大幅度快速变化。
43关于防止20万机组大轴弯曲的技术措施

关于防止20万机组大轴弯曲的技术措施本措施是为防止20万kW汽轮机大轴弯曲事故而制定的,其它容量和型式的汽轮机可结合各机型的特点参照执行。
本措施内容只涉及为防止大轴弯曲事故而须注意的问题和要求,为保证机组安全运行的其它方面要求,仍应按有关法规、规程t规定等执行。
一、认真地做好每台机组的基础技术工作1.每台机组均必须具备以下资料、数据,主要值班人员应熟悉掌握。
(1)转子原始弯曲的最大晃动值(双幅)和最大弯曲点的轴向位置及圆周方向的相位。
(2)大轴弯曲表测点安装位置转子的原始晃动值(双幅)及最高点在圆周方向的相位。
(3)汽轮发电机组轴系临界转速及正常启动运行情况的各轴的振动值(包括1300r/min中速暖机时,临界转速时和定速后的振动数值)。
外(4)正常情况下盘车电流及电流摆动值(应注明记录时的油温、顶轴油压等)。
:(5)正常情况下停机时的惰走曲线(注明真空、顶铀油泵开启时间等)和紧急破坏真空停机时的情走曲线。
(6)停机后正常情况下汽缸各主要金属温度测点的温度的下降曲线(7)通流部分轴向间隙,径向间隙值。
。
以上数据、资料,在机组安装、调试过程应测取并在投运后经常进行核对和修正。
如发生异常情况应及时汇报、分析、处理。
2.应根据制造厂的规定及同型机组的运行经验制定出机组各状态下的典型启动曲线和好机曲线,经实践后纳入运行规程。
3.机组启、停应有专门的记录。
侈机后仍要定时记录汽缸各金属温度、大轴弯曲、盘车电流、汽缸膨胀、胀差等参数直到到机组下船热恋启动或汽缸金属温度低于150℃为止。
4.运行规程中未作具体规定的重要特殊运行操作或试验必须事先制定技术措施,并经领导批准后执行。
5.新机组启动前应制定专门的启动方案与安全、技术措施。
二、设备、系统方面的技术措施1.汽缸保温。
(1)汽缸保温应保证机朗船舶显:上、下缸硷统雨超过35℃,最大不超过50℃。
(2)采用保温性能良好段僳掘粉料f如碳酸侣纤维毡微孔硅酸钙等。
(3)改进保温施工皿笆1如采用粘贴的办法辞),保证保温材料不发生裂纹及与汽缸服空现象。
防止汽轮机大轴弯曲技术
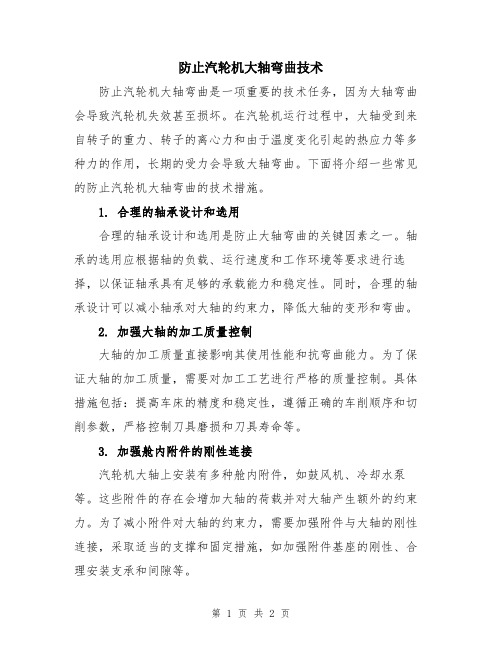
防止汽轮机大轴弯曲技术防止汽轮机大轴弯曲是一项重要的技术任务,因为大轴弯曲会导致汽轮机失效甚至损坏。
在汽轮机运行过程中,大轴受到来自转子的重力、转子的离心力和由于温度变化引起的热应力等多种力的作用,长期的受力会导致大轴弯曲。
下面将介绍一些常见的防止汽轮机大轴弯曲的技术措施。
1. 合理的轴承设计和选用合理的轴承设计和选用是防止大轴弯曲的关键因素之一。
轴承的选用应根据轴的负载、运行速度和工作环境等要求进行选择,以保证轴承具有足够的承载能力和稳定性。
同时,合理的轴承设计可以减小轴承对大轴的约束力,降低大轴的变形和弯曲。
2. 加强大轴的加工质量控制大轴的加工质量直接影响其使用性能和抗弯曲能力。
为了保证大轴的加工质量,需要对加工工艺进行严格的质量控制。
具体措施包括:提高车床的精度和稳定性,遵循正确的车削顺序和切削参数,严格控制刀具磨损和刀具寿命等。
3. 加强舱内附件的刚性连接汽轮机大轴上安装有多种舱内附件,如鼓风机、冷却水泵等。
这些附件的存在会增加大轴的荷载并对大轴产生额外的约束力。
为了减小附件对大轴的约束力,需要加强附件与大轴的刚性连接,采取适当的支撑和固定措施,如加强附件基座的刚性、合理安装支承和间隙等。
4. 针对大轴的温度变化采取整体热处理汽轮机运行中,大轴由于温度的变化会产生热应力,从而导致大轴发生变形和弯曲。
为了减小温度变化对大轴的影响,可以采取整体热处理的方法,通过控制热处理过程和温度来降低大轴的内部应力。
5. 加强对大轴的在线监测和维护对于汽轮机大轴,需要进行定期的在线监测和维护,及时发现和修复存在的问题,避免因轴的变形和弯曲而引发更严重的故障。
在线监测可以采用振动监测、温度监测等手段,及时获得大轴的工作状态和变化情况,为维护提供重要的依据。
综上所述,为了防止汽轮机大轴弯曲,需要从轴承设计、加工质量、舱内附件连接、温度变化和在线监测等多个方面进行综合考虑和措施实施。
通过这些技术措施的应用,可以有效地保护大轴的安全运行,延长汽轮机的使用寿命。
汽轮机高压转子直轴方案

#3汽轮机高压转子直轴方案#3机(#4机)系哈尔滨汽轮机厂生产超高压中间再热纯凝汽式汽轮机(69型),机组额定功率210 MW,由于各种原因造成高压转子弯曲(弯曲部位及弯曲值不详),为确保直轴工作顺利进行, 制定本方案如下:一、设备主要技术规范及其转子结构型号:N210─130/535/535─1型;形式:超高压中间再热纯凝汽式机组(69型);额定功率:210MW;额定转数:3000 rPm;新蒸汽压力:12.75 MPa;新蒸汽温度:535 ℃;再热冷段压力:2.507 MPa;再热冷段温度:313 ℃;背压:6.376 KPa;新蒸汽耗量:627.6 t/h;高压转子临界转数:1869 rpm。
高压转子有一个单列调节级和11个压力级,高压转子的叶片及轴为整锻成一体,轴中心孔为Φ100,转子材料为30CrMo20V合金钢,经调质处理,布氏硬度HB=240,转子总长为4381mm,转子总重为6404Kg。
二、汽轮机高压转子弯曲情况(详情待查)略。
三、直轴方案选择:转子发生永久性弯曲大都因单侧磨擦过热而引起,金属过热部分受热膨胀,因受热周围温度较低部分的限制而产生压应力,该压应力大于该温度下的屈服极限,受热部分金属受压而缩短,则产生永反方向的弯曲,永久变形。
大直径合金刚转子采用其它方法直轴有一定局限性,其共性是转子校直后,都存在残余应力,这些应力决定着校直的轴可承受的弯曲力矩,当轴局部受热时,校直位置上的残余应力可能超过强度极限而引起裂纹,以及校直处稳定性差,运行中还可能产生弯曲裂纹等缺点。
内应力松驰法是比较安全可靠,直轴效果为现阶段最好的一种方法,其原理是利用金属在高温下的松驰特性,即在一定的应变下作用于零件的应力会逐渐降低的现象,而在应力降低的同时,零件的弹性变形转变为塑形变形,人为控制加热温度外加一定力并持续一定时间而完成较直工作。
这样校直后的轴具有良好的稳定性,因此选用松驰法直轴较为稳妥。
QJ-09 防止汽轮机大轴弯曲的综合预案

华能荆门热电有限责任公司运行部防止汽轮机大轴弯曲的综合预案第一章总则汽轮机大轴一旦出现热弯曲,将导致大机设备严重损坏。
为防止汽轮机大轴弯曲事故的发生,特制定以下事故综合预案:第二章内容与要求一、汽轮机轴系简介1、高中压转子是无中心孔合金钢整锻转子,带有主油泵叶轮及超速跳闸装置的轴通过法兰螺栓刚性地与高中压转子在调端连接在一起,主油泵叶轮轴上还带有推力盘。
2、低压转子也是无中心孔合金钢整锻转子。
3、高中压转子和低压转子之间装有刚性的法兰联轴器,低压转子和发电机转子通过联轴器刚性联接。
4、转子系统由安装在前轴承箱内的推力轴承定位,并有6个支撑轴承支撑。
二、防止汽轮机大轴弯曲的措施1、应具备和熟悉掌握的资料。
1.1 转子安装原始弯曲的最大晃动值(双振幅),最大弯曲点的轴向位置及在圆周方向的位置。
1.2 大轴弯曲表测点安装位置,转子的原始晃动值(双振幅),最高点在圆周方向的位置。
1.3 机组正常起动过程中的波特图和实测轴系临界转速。
1.4 正常情况下盘车电流和电流摆动值,以及相应的油温和顶轴油压。
1.5 正常停机过程的惰走曲线,以及相应的真空和顶轴油泵的开启时间。
紧急破坏真空停机过程的惰走曲线。
1.6 停机后,机组正常状态下的汽缸主要金属温度的下降曲线。
1.7 通流部分的轴向间隙和径向间隙。
1.8 应具有机组在各种状态下的典型起动曲线和停机曲线,并应全部纳入运行规程。
1.9 记录机组起停全过程中的主要参数和状态。
停机后定时记录汽缸金属温度、大轴弯曲、盘车电流、汽缸膨胀、胀差等重要参数,直到机组下次热态起动或汽缸金属温度低于150℃为止。
1.10 系统进行改造、运行规程中尚未作具体规定的重要运行操作或试验,必须预先制定安全技术措施,经上级主管部门批准后再执行。
2、汽轮机起动前必须符合以下条件,否则禁止起动。
2.1 大轴晃动、串轴、胀差、低油压和振动等表计显示正确,保护正常投入。
2.2 大轴晃动值不应超过制造厂的规定值,或原始值的±0.02mm。
直轴法——精选推荐

现场应用的直轴方法有下列几种:1、机械加压法;2、捻打法;3、局部加热法;4、局部加热加压法;5、应力松弛法。
机械加压法和捻打法只适用于直径较小、工作温度不高的弯轴校正;局部加热法广泛用于锅炉钢梁、柱的校直,也有小汽机主轴应用先例;后两种方法,特别是应力松弛法则是火电厂现场直轴的主要方法,并在朝阳、鲤鱼江等电厂有成功的经验。
后三法在原理和实施上均有关连,下文逐一简介。
a、局部加热法将轴弯曲处的凸面向上放置,用石棉布把最大的弯曲处包起来。
以最大弯曲点为中心,在石棉布上开出矩形的加热孔,用6、7号火咀对加热孔处的轴面加热,从而把轴校直过来。
加热孔的长度(沿轴的圆周方向)约等于该处轴径的25~30%,孔的宽度(沿轴线方向)根据弯曲度确定,一般为该处轴颈的10~15%。
在用局部加热法直轴时,应注意以下几点:● 加热火咀距离轴面约15~20mm,先从孔中心开始,然后向两侧移动,千万不要停留在一处不动。
● 当温度升至500~550℃时,停止加热,并立即用石棉布把加热孔盖起来,避免急剧冷却,产生裂纹。
● 待轴全部冷却后,拆开保温,检查轴的弯曲度,若未达到要求,可继续按上述方法和要求进行校正。
● 若在该处经再次加热仍无效果,须改变加热位置,即在最大弯曲处附近同时用两个火咀局部校正。
● 轴的局部加热校直需要稍有过校现象,即跟原弯曲方向相反约有0.03~0.04mm的过弯值。
待轴进行退火处理后,这一过弯值将自行消失。
● 汽轮机转子在局部加热校直后,必须进行热处理,以消除残余应力,避免运行中轴在高温下重新弯曲。
但对在常温或低温下工作的轴,如风机,循环水泵,工业泵,深井泵等轴则可以不进行热处理。
b、局部加热加压法:局部加热加压法也叫热力机械直轴法,其对轴的加热部位、温度、加热时间、冷却方式及注意事项与局部加热法完全相同。
有区别的是在加热之前,用加压工具在弯曲处附近施加压力,使轴产生与原弯曲方向相反的预变形(即弹性变形)。
210MW汽轮机大轴弯曲原因分析及直轴方法
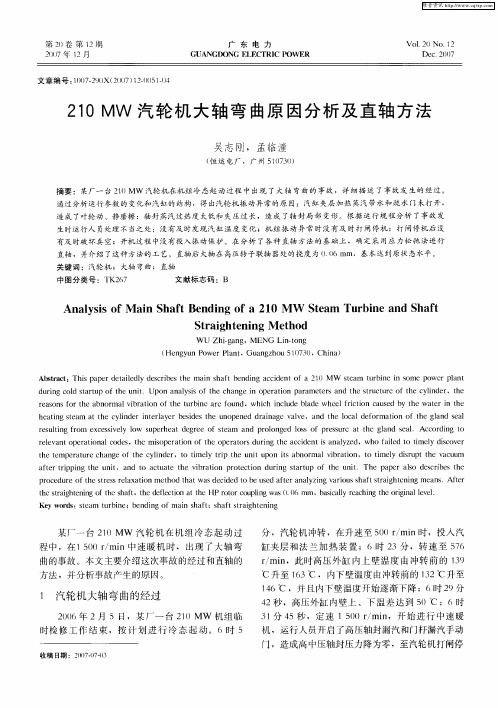
t e t mp r t r h n e o h y i d r o t ey t i h n tu o t a n r a i r t n t i l ir p h a u m h e e a u e c a g f t e c l e ,t i l rp t e u i p n is b o m lv b a i . o t n m o me y d s u t t e v c u
维普资讯
第 2) 第 1 期 (卷 2 20 0 7年 1 2月
广 东 电 力
GUANGD 0.1 _ )N 2 D e 20 c 07
文 章 编 号 :0 72 0 2 0 )20 5 一4 10 —9 X(0 7 1-0 1 ) (
关 键 词 :汽轮 机 ; 大轴 弯 曲 ; 直轴
中图 分 类 号 :TK 6 27
文 献 标 志 码 :B
Ana y i fM a n Sh f n i f a 2 W t a r n n h f l ss o i a tBe d ng o 0 M 1 S e m Tu bi e a d S a t S r i ht n ng M e ho t ag e i t d
有及 时破 坏 真 空 ; 开机 过 程 中没 有 投 入 振 动 保 护 。在 分 析 了 各 种 直轴 方 法 的基 础 上 ,确 定 采 用 应 力 松 弛 法 进 行
防止汽轮机组大轴弯曲的技术措施

防止汽轮机组大轴弯曲的技术措施1、汽轮机冲转前必须检查大轴偏心度<0.076mm,大轴晃动值不超过原始值的0.02 mm。
汽轮机大修后启动时,必须用千分表在每个轴承挡油环上测量主轴的跳动量<0.0254mm。
2、汽缸上下缸温差(指调端高压缸上下部排汽区;中压缸上下两端排汽区)>42℃汽轮机组禁止启动。
主汽阀入口温度至少具有56℃的过热度。
3、机组冷、热态启动应按“启动时主蒸汽参数”、“冷态启动转子加热规程”、“热态启动推荐值”图表曲线进行。
4、在任何情况下,汽轮机第一级蒸汽温度不允许比第一级金属温度低56℃或高111℃。
5、热态启动时,应先送汽封后抽真空,汽封送汽前必须充分疏水,确认管道无水后才可向汽封送汽。
6、汽封供汽必须具有14℃以上的过热度,低压供汽封汽温度控制在121~177℃之间。
7、机组未盘车前禁止向汽封供汽。
8、当高、中压汽封供汽温度小于150℃或汽封供汽温度与调端高压缸端壁温差小于85℃时,检查汽封喷水应关闭。
9、在机组启动过程中,按“汽轮机转速保持推荐值”“冷态转子加热规程” “热态启动推荐值”曲线进行暖机,暖机时间由中压缸进汽温度达到260℃时开始计算。
10、在机组启动过程中,要有专人监视汽轮机组各轴瓦振动,汽轮的轴振动应在0.125mm以下,通过临界转速时,轴承振动超过0.1mm或相对轴振动值超过0.254mm时立即打闸停机。
严禁强行通过临界转速或降速暖机。
11、机组运行过程中轴承振动不超过0.03mm或相对轴振动不超过0.08mm,超过时应设法消除,当相对轴振动大于0.254mm应立即打闸停机;当轴承振动变化±0.015mm或相对轴振动变化±0.05mm时,应查明原因设法消除,当轴承振动突然增加0.05mm,应立即打闸停机。
12、按《集控运行规程》,当发现有汽轮机水冲击现象时,立即打闸停机。
13、所有高、低加、除氧器水位保护应投入运行且定期试验,发现加热器泄漏时,应立即停止加热器运行并将抽汽逆止门关闭。
2024年防止汽轮机大轴弯曲技术(三篇)

2024年防止汽轮机大轴弯曲技术1机组在启动前检查偏心、蒸汽参数、盘车时间等各启动条件必须符合《集控运行技术标准》的规定,否则严禁启动。
机组在600rpm 以下时,用打偏心表的方法来监视偏心。
2锅炉点火到机组并列期间,以及机组解列到高压首级金属温度或中压持环温度降到150℃期间,应详细进行启、停机记录,发现异常情况及时汇报处理。
3启动前必须确认振动跳闸保护好用,否则不得启动。
4严格按《集控运行技术标准》投入轴封汽源,轴封供汽温度在规定范围内,轴封系统应充分暖管,疏水,保证轴封供汽不低于14℃的过热度。
5热态启动前应检查停机记录,并与正常停机记录比较,发现异常情况及时汇报处理。
6启动过程中严格按《集控运行技术标准》开、关各高、中压疏水,经常监视缸体上、下温差,发现异常及时汇报、分析、处理。
7启动过程中严密监视振动情况,如有异常应立即停止升速,查明原因处理,严禁硬闯临界转速或降速暖机。
8启动过程中,中速暖机结束后,必须按运行规程中规定确认高、中压缸膨胀达到要求后方可继续升速。
9机组因振动大而跳闸时,应立即破坏真空,紧急停机,同时进行停机各参数的记录。
10机组因振动大跳闸后再次启动时,必须查明原因,并经全面检查确认机组已符合启动条件,偏心恢复到原始值,再连续盘车不小于4小时后,方可再次启动,严禁盲目再次启动。
11启、停机过程中,当主蒸汽过热度较低时,主汽门、调速汽门大幅度的摆动,有可能使汽轮机产生一定程度的水冲击,此时应严密监视机组的振动、差胀、轴向位移等,超过极限应立即紧急停机。
12机组在启停机变工况运行时,严格按《集控运行技术标准》规定的速率控制汽温、汽压的变化,避免汽温大幅度直线变化。
当对照其它测点后确认主、再热汽温直线下降65℃时,应立即打闸停机。
13低负荷和启、停机过程中不得投入主、再热蒸汽的减温水。
14转子静止后,应立即投入连续盘车,并严密监视盘车电流和转子偏心,当盘车电流较大摆动、盘车有异音时,应及时分析、汇报、处理,如汽缸内有明显的金属磨擦声,应立即停止连续盘车,改为定期盘车180°,如动静磨擦严重,盘车不动时,不得用任何手段进行强制盘车。
汽轮机大轴弯曲

汽轮机大轴弯曲汽轮机大轴弯曲是汽轮发电机机组恶性事故中最为突出的事故,必须引起足够重视。
特别是大容器量汽轮机由于缸内结构复杂,使得汽缸的热膨胀和热变形变得复杂,增大了汽轮机大轴弯曲的可能性。
一、汽轮机大轴弯曲的原因引起汽轮机大轴弯曲的原因是多方面的,但在运行现场,形成大轴弯曲主要有以下几种情况:(1)由于通流部分动静摩擦,转子局部过热(热点温度可达650~1300℃),一方面显著降低了该部位屈服极限,另一方面受热局部的热膨胀受限制周围材料而产生很大压应力。
当应力超过该部位屈服极限时,发生塑性变形。
当转子温度均匀后,该部位呈现凹面永久性弯曲。
(2)在第一临界转速下,大轴热弯曲方向与转子不平衡力方向大致一致,动静碰磨时将产生恶性循环,致使大轴产生永久弯曲;在第一临界转速上,热弯曲方向与转子不平衡力方向趋于相反,有使摩擦脱离的趋向,所以高转速时引起大轴弯曲的危害要比低转速时要小(3)汽缸进冷气、冷水。
停机后在汽缸温度较高时,因某种原因使冷气、冷水进入汽缸时,汽缸和转子将由于上下缸温差产生很大的热变形,甚至中断盘车,加速大轴弯曲,严重时将造成永久弯曲。
(4)转子的原材料存在过大的内应力,在较高的工作温度下经过一段时间的运行以后,内应力逐渐得到释放,从而使转子弯曲变形。
(5)运行人员在机组启动或运行中由于未严格执行规程规定的启动条件、紧急停机规定等,硬撑硬顶也会造成大轴弯曲。
二、防止汽轮机大轴弯曲事故发生的措施为防止大轴弯曲事故发生,通常可采取如下一些措施:(1)认真做好每台机组的基础技术工作1)每台机组必须备有机组安装和大修的资料及大轴原始弯曲度、临界转速、盘车电流及正常摆动值等重要数据,并要求只要值班人员熟悉掌握。
2)运行规程中必须编制各机不同状态下的启动曲线以及停机惰走曲线。
3)机组启停应有专业的记录。
停机后仍要认真监视、定时记录各金属温度、大轴弯曲、盘车电流、汽缸膨胀、胀差、轴向位移等。
(2)设备、系统方面的技术措施1)汽缸应有良好的保温,保证机组停机后上下缸温差不超过35℃,最大不超过50℃.2)机组在安装和大修中,必须考虑热状态变化的条件,合理地调整动静间隙,保证在正常运行中不会发生动静摩擦。
燃气蒸汽联合循环机组单轴与多轴配置的特点及方案比较

燃气蒸汽联合循环机组单轴与多轴配置的特点及方案比较摘要:联合循环机组中的燃气轮机、汽轮机和发电机的不同布局关系而形成的轴系配置型式,与电厂的总体布置和厂房结构、检修方式等有关,而且对机组运行、操作与性能(特别是变负荷)以及投资成本等都有很大关系。
本文将从电气设备、控制系统、安装、运行特性、维修、建设安排、事故影响等方面对不同配置方案进行对比分析。
关键词:燃气轮机;联合循环机组;方案1.引言燃气-蒸汽联合循环机组有单轴机型和多轴机型两大类。
所谓单轴即燃机、汽机、发电机共用一根轴;多轴是指燃机和燃机发电机一根轴,汽机和汽机发电机另一根轴。
早期机组配置中一般大容量燃机用于调峰,多配单轴;容量较小的常用于热电联产,一般按多轴配置。
近几年大型燃机用于热电联产的工程增多,对于此类项目,也有单轴和多轴两种布置。
一般在供热量不是很大的情况下可选用单轴机组,在供热量较大的情况下则选用多轴机组较多。
2.单轴配置的特点单轴布置的配置方式即燃气轮机、发电机和蒸汽轮机串联安装在同一根轴系上,由燃气轮机和汽轮机共同驱动一台发电机。
发电机可以位于燃气轮机和汽轮机之间,也可以位于汽轮机排汽端。
这种方案只能用于单台燃机、单台余热锅炉和单台汽轮机匹配的情况,即所谓1+1+1单轴布置方案。
单轴配置又有两种方式:2.1发电机尾置方式燃气轮机+向下排汽的汽轮机+发电机的连接方式,简称发电机尾置方式。
这种连接方式的优点是:发电机位于机组端部,发电机出线和检修时抽转子比较方便。
缺点是:①汽轮机在中间,汽轮机向下排汽使整套联合循环机组必须布置在较高的运转层上。
②发电机只有当燃气轮机和汽轮机都安装完毕后才能投运,不利于安装周期较短的燃气轮机及早投产发电。
③运行中蒸汽系统出现故障时,燃气轮机仍拖着汽轮机空转,一方面汽轮机不能停机检修,另一方面汽轮机叶片鼓风发热,还必须设置小的辅助锅炉,产生辅助蒸汽通入汽缸进行冷却。
④汽轮机正常启动时,也需要辅助蒸汽汽源提供轴封汽和汽轮机一开始空转时汽缸所需的冷却蒸汽。
防止汽轮机大轴弯曲技术模版(三篇)
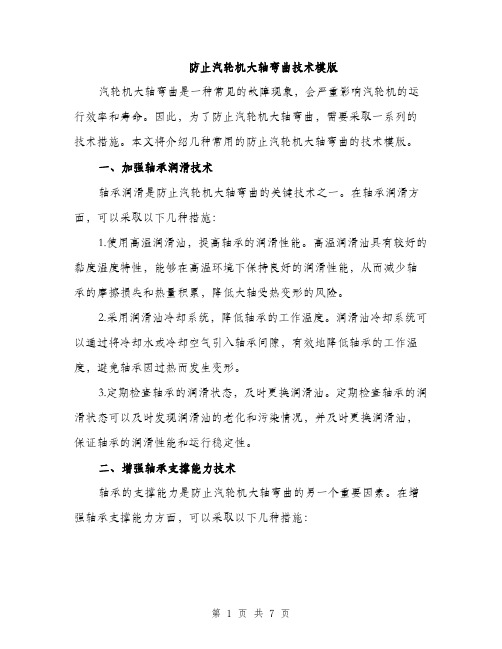
防止汽轮机大轴弯曲技术模版汽轮机大轴弯曲是一种常见的故障现象,会严重影响汽轮机的运行效率和寿命。
因此,为了防止汽轮机大轴弯曲,需要采取一系列的技术措施。
本文将介绍几种常用的防止汽轮机大轴弯曲的技术模版。
一、加强轴承润滑技术轴承润滑是防止汽轮机大轴弯曲的关键技术之一。
在轴承润滑方面,可以采取以下几种措施:1.使用高温润滑油,提高轴承的润滑性能。
高温润滑油具有较好的黏度温度特性,能够在高温环境下保持良好的润滑性能,从而减少轴承的摩擦损失和热量积累,降低大轴受热变形的风险。
2.采用润滑油冷却系统,降低轴承的工作温度。
润滑油冷却系统可以通过将冷却水或冷却空气引入轴承间隙,有效地降低轴承的工作温度,避免轴承因过热而发生变形。
3.定期检查轴承的润滑状态,及时更换润滑油。
定期检查轴承的润滑状态可以及时发现润滑油的老化和污染情况,并及时更换润滑油,保证轴承的润滑性能和运行稳定性。
二、增强轴承支撑能力技术轴承的支撑能力是防止汽轮机大轴弯曲的另一个重要因素。
在增强轴承支撑能力方面,可以采取以下几种措施:1.优化轴承结构,提高轴承刚度。
通过优化轴承结构,采用高刚度材料和精密制造工艺,提高轴承的刚度,使其能够更好地支撑大轴重量和受力,减少大轴的挠曲。
2.增加轴承的数量和布局密度。
通过增加轴承的数量和布局密度,可以使大轴获得更好的支撑和平衡力,减少大轴的弯曲和振动。
3.采用弹性轴承技术。
弹性轴承能够在汽轮机运行时对大轴进行主动的弹性支撑和平衡,减少大轴的受力变形和振动。
三、减少外界载荷技术外界载荷是导致汽轮机大轴弯曲的另一个重要原因。
在减少外界载荷方面,可以采取以下几种措施:1.降低大轴的受力工况。
在汽轮机的设计和运行过程中,要合理设计叶轮和传动装置,减少大轴的受力过程,降低大轴的弯曲风险。
2.加强大轴的支撑和固定力。
通过加强大轴的支撑和固定力,增加大轴的刚度,提高大轴抵抗外界载荷变形的能力。
3.优化汽轮机的结构和布局。
防止汽轮机大轴弯曲安全技术措施标准版本

文件编号:RHD-QB-K2472 (解决方案范本系列)编辑:XXXXXX查核:XXXXXX时间:XXXXXX防止汽轮机大轴弯曲安全技术措施标准版本防止汽轮机大轴弯曲安全技术措施标准版本操作指导:该解决方案文件为日常单位或公司为保证的工作、生产能够安全稳定地有效运转而制定的,并由相关人员在办理业务或操作时进行更好的判断与管理。
,其中条款可根据自己现实基础上调整,请仔细浏览后进行编辑与保存。
为了防止汽轮机大轴弯曲事故的发生,特制定安全技术措施如下:一、汽缸保温1、汽缸保温应保证机组停止后,上下缸温差不超过35度,最大不超过50度2、采用保温性能良好的保温材料3、提高保温工艺质量,保证保温材料不发生裂纹及与汽缸脱落现象二、疏水系统1、疏水系统应保证畅通,每次大修后应对汽缸疏水用压缩空气吹疏水管2、停机后防腐门应全开3、停炉时应开放疏水门,注意汽温三、检修1、检修时应对大轴弯曲进行测量2、轴风间隙应调整合适,不应出现过大或过小的情况3、检修后组装时应盘车无异音四、运行1、转子冲动前,测量大轴晃动不超过原始值的0.02毫米,高压缸上下缸温差不超过35度2、冲动前转子应进行充分连续盘车3、启动升速过程中,应有专人监视振动,在1500转以前,轴瓦振动超过0.04毫米,应立即打闸停机4、机组启动中,因振动大而打闸停机必须经过全面检查,严禁盲目启动5、汽轮机运行中,振动明显增大时应汇报,分析。
突然增大到0.06毫米时,应打闸停机6、停机后既投入盘车7、停机后因故暂时停止盘车时,应监视转子弯曲的变化,如热弯曲较大时,应先盘车180度后再投入连续盘车。
这里写地址或者组织名称Write Your Company Address Or Phone Number Here。
防止汽轮机组大轴弯曲的技术措施
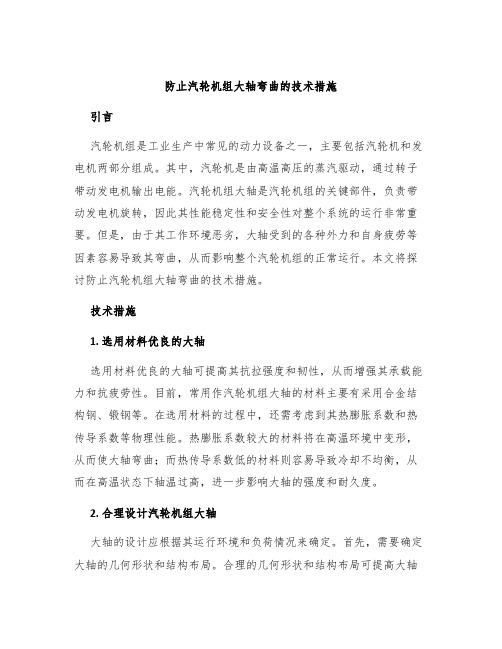
防止汽轮机组大轴弯曲的技术措施引言汽轮机组是工业生产中常见的动力设备之一,主要包括汽轮机和发电机两部分组成。
其中,汽轮机是由高温高压的蒸汽驱动,通过转子带动发电机输出电能。
汽轮机组大轴是汽轮机组的关键部件,负责带动发电机旋转,因此其性能稳定性和安全性对整个系统的运行非常重要。
但是,由于其工作环境恶劣,大轴受到的各种外力和自身疲劳等因素容易导致其弯曲,从而影响整个汽轮机组的正常运行。
本文将探讨防止汽轮机组大轴弯曲的技术措施。
技术措施1. 选用材料优良的大轴选用材料优良的大轴可提高其抗拉强度和韧性,从而增强其承载能力和抗疲劳性。
目前,常用作汽轮机组大轴的材料主要有采用合金结构钢、锻钢等。
在选用材料的过程中,还需考虑到其热膨胀系数和热传导系数等物理性能。
热膨胀系数较大的材料将在高温环境中变形,从而使大轴弯曲;而热传导系数低的材料则容易导致冷却不均衡,从而在高温状态下轴温过高,进一步影响大轴的强度和耐久度。
2. 合理设计汽轮机组大轴大轴的设计应根据其运行环境和负荷情况来确定。
首先,需要确定大轴的几何形状和结构布局。
合理的几何形状和结构布局可提高大轴的受力均匀性和抗疲劳性。
其次,还应对大轴的镟制和加工进行控制,避免过度加工或过度镟制等造成不必要的变形。
此外,除了考虑大轴自身的设计以外,还应根据实际情况选择适当的大轴轴承和轴承座,以提高其受力均匀性和稳定性。
3. 适时的检测和维护适时的检测和维护是防止汽轮机组大轴弯曲的重要保障。
检测和维护可及时发现大轴的损伤和缺陷,避免其扩大化。
在检测和维护过程中,需要注意以下几个方面:•应定期检测大轴的状态变化,例如轴温、轴径、轴承温度等。
•发现大轴存在问题时,应立即停机处理,避免问题进一步扩大。
•检测工具要选择准确、可靠的设备,避免误差。
4. 加强工人培训和安全意识工人在维修和操作汽轮机组时需要深入了解大轴的构成和作用,并遵循操作规程,保证正确操作。
另外,加强安全意识的培养也是防止大轴弯曲的关键。
200mw汽轮机大轴校直时温度场的分析计算

200mw汽轮机大轴校直时温度场的分析计算机械传动技术是现代工业技术发展进程中不可或缺的一个重要的分支,机械传动设备的校直是保证该设备的正常运行的关键一步。
汽轮机大轴是汽轮机传动系统的重要组成部分,是承担转子、叶片及系统的负载的重要件。
汽轮机大轴校直时温度场的变化特点是传动系统的核心内容。
本文以200mW汽轮机大轴为研究对象,结合有限元分析软件ANSYS,通过研究该汽轮机大轴在校直时的温度场变化特点,为根据温度分析对汽轮机大轴进行校直提供依据。
首先,根据汽轮机大轴的实际结构和参数,构建一个三维有限元模型,确定汽轮机大轴的材料性能数据,建立ANSYS中的适当温度定义。
其次,根据汽轮机大轴的轮子叶片及系统的负载情况,进行汽轮机大轴校直时温度场的分析计算,计算出汽轮机大轴的温度场在校直前和校直后的变化情况,探讨其校直时温度场的特点,以及温度场分布在汽轮机大轴上的变化。
在实际分析中,首先通过有限元模型构建200mW汽轮机大轴的结构,给出该汽轮机大轴的材料性能数据,确定汽轮机大轴的质量,然后建立对应的汽轮机大轴校直时的温度场分析模型。
经过温度分析,可得出汽轮机大轴校直时的温度场图,显示汽轮机大轴的温度分布,从而掌握汽轮机大轴校直时温度场的变化特征。
在分析计算结果中,汽轮机大轴校直前结构上温度场分布均匀,温度范围为290K-310K;汽轮机大轴校直后温度场分布不均匀,温度变化较大,除了轴腔等位置温度比较稳定外,其他部位温度波动较大,温度差异达到了50K以上,显示温度场分布有明显的变化,这也是汽轮机大轴校直后温度场的特征。
从上述分析结论得出,汽轮机大轴的温度场变化特征是:校直前温度场分布均匀,温度范围较小,温度波动平缓;校直后温度场分布不均匀,温度变化较大,温度波动较大,温度差异达50K以上,温度分布有明显变化。
根据汽轮机大轴温度场的变化特征,可以为校直操作提供有效的参考依据,有助于更准确地评估汽轮机大轴的校直情况以及机械结构的整体可靠性。
汽轮机大轴直轴方案

汽轮机转子弯曲现场应力松驰法直轴Xxxxxx电厂xx一、概述:某热电厂,装机容量xxxx万千瓦。
其汽轮机为xx汽轮机厂制造,型号C50-8.82/0.98,进汽调节方式:喷咀调节。
高压单缸冲动单抽汽凝汽式。
工作转速3000r/min,临界转速1678r/min,盘车为50r/min,汽轮机转子与发电机转子为刚性联接。
汽轮机分一个调节级,十七个压力级和一个抽汽级共19级组成,转子为整锻加套装轮盘结构,第1到14级叶轮为整锻式叶轮,直接从整锻转子上车出,第15至19级叶轮则为红套装配式叶轮,转子材料为:30Cr2M0V,其中心孔Ф100。
该厂#1汽轮发电机运行中,因电气操作时“转速≥3420r/min”超速继电器保护误动,关闭自动主汽门导致发电机组解列,汽机破坏真空紧急停机,电动盘车。
1小时后系统恢复正常,#1汽轮机准备重新冲转。
检查发现盘车电流24—28A偏大,晃动度7丝,上下缸温差接近50℃,用听筒听机组,未发现异常,继续盘车1小时后,盘车电流降至24A,晃动度5丝,其它无异常。
机组开始热态定参数冲转,定速至并网带负荷2MW,机组振动正常,1小时后负荷升至5MW,汽机水平振动升至5丝,立即降负荷振动不变,负荷至零,#2轴承急剧上升至13.5 丝,#1轴瓦、#3轴瓦振动报警,紧急停机,投入电动盘车,测量晃动度为10丝,盘车至汽缸常温,测量晃动度仍有10丝,转子大轴弯曲。
二、检查及测量:揭盖检查及测量轴弯曲时发现,前轴封、隔板汽封9到14级外圆周有明显摩擦痕迹,其中11级最为严重。
在汽发对轮脱开状态测量弯曲度,绘出曲线如图:由图可见,最大弯曲点在测量点12,直径为620处(第8级与第9级叶轮间),凸出方位在第#7对轮螺栓孔与#8中间处,其值为0 .10 mm.三、直轴方案的选择:由于该轴为整锻合金材料,弯曲度较小,所以决定采用先对轴做稳定性热处理(应力松驰),再做低速动平衡,其方案主要对温度的控制。
防止汽轮机大轴弯曲技术范文

防止汽轮机大轴弯曲技术范文在汽轮机运行过程中,由于各种因素的影响,特别是过载等工况下,很容易导致汽轮机大轴的弯曲。
而大轴的弯曲不仅会降低汽轮机的效率,还可能导致零部件的卡住、磨损等问题,严重影响汽轮机的安全运行。
因此,研究和应用防止汽轮机大轴弯曲的技术是非常重要的。
为了解决汽轮机大轴弯曲的问题,需要从设计、制造、安装和使用等方面综合考虑,并采取相应的措施。
以下是一些建议和技术范例,用于防止汽轮机大轴弯曲。
1. 合理的设计和制造首先,在汽轮机的设计和制造过程中,需要充分考虑大轴的承载能力和抗弯性能。
通过增加大轴的直径、提高材料的强度和硬度、优化大轴的几何形状等手段,可以有效地提高大轴的抗弯能力。
同时,在制造过程中要保证大轴的加工精度和表面质量,以降低大轴的内在应力和表面缺陷,减少弯曲的可能性。
2. 合理的安装和调整汽轮机的安装和调整也是防止大轴弯曲的重要环节。
在安装过程中,应保证大轴和轴承的配合间隙合理,避免轴承的过紧或过松。
同时,在调整过程中要注意大轴的对中情况,避免大轴受到外力的不均匀作用,引起弯曲。
在真实运行前,可以采用静力负荷测试和动态振动测试等手段进行调整和监测,以确保大轴的安装质量。
3. 过载保护和运行监控过载是导致大轴弯曲的主要因素之一。
因此,在汽轮机的运行中,应采取相应的过载保护措施,避免汽轮机在超负荷运行状态下工作。
可以通过设置过载保护装置、控制参数的设定和优化等方式,实现对汽轮机的保护和控制。
同时,还可以通过振动监测、温度监测和油液分析等手段,及时监测和诊断汽轮机的运行情况,发现问题并及时解决,防止大轴弯曲的发生。
4. 定期维护和检修对于汽轮机大轴来说,定期的维护和检修非常重要。
在维护过程中,可以采取润滑、紧固和除尘等措施,保证大轴的润滑和清洁。
同时,在检修过程中,可以通过检查和修复轴承、检查和修复轴瓦、调整和校准设备等手段,保证汽轮机大轴的正常运行。
通过定期的维护和检修,可以及时发现并处理大轴的问题,防止大轴的进一步弯曲和损坏。
- 1、下载文档前请自行甄别文档内容的完整性,平台不提供额外的编辑、内容补充、找答案等附加服务。
- 2、"仅部分预览"的文档,不可在线预览部分如存在完整性等问题,可反馈申请退款(可完整预览的文档不适用该条件!)。
- 3、如文档侵犯您的权益,请联系客服反馈,我们会尽快为您处理(人工客服工作时间:9:00-18:30)。
汽轮机转子弯曲现场应力松驰法直轴
Xxxxxx电厂xx
一、概述:
某热电厂,装机容量xxxx万千瓦。
其汽轮机为xx汽轮机厂制造,型号C50-8.82/0.98,进汽调节方式:喷咀调节。
高压单缸冲动单抽汽凝汽式。
工作转速3000r/min,临界转速1678r/min,盘车为50r/min,汽轮机转子与发电机转子为刚性联接。
汽轮机分一个调节级,十七个压力级和一个抽汽级共19级组成,转子为整锻加套装轮盘结构,第1到14级叶轮为整锻式叶轮,直接从整锻转子上车出,第15至19级叶轮则为红套装配式叶轮,转子材料为:30Cr2M0V,其中心孔Ф100。
该厂#1汽轮发电机运行中,因电气操作时“转速≥3420r/min”超速继电器保护误动,关闭自动主汽门导致发电机组解列,汽机破坏真空紧急停机,电动盘车。
1小时后系统恢复正常,#1汽轮机准备重新冲转。
检查发现盘车电流24—28A偏大,晃动度7丝,上下缸温差接近50℃,用听筒听机组,未发现异常,继续盘车1小时后,盘车电流降至24A,晃动度5丝,其它无异常。
机组开始热态定参数冲转,定速至并网带负荷2MW,机组振动正常,1小时后负荷升至5MW,汽机水平振动升至5丝,立即降负荷振动不变,负荷至零,#2轴承急剧上升至13.5 丝,#1轴瓦、#3轴瓦振动报警,紧急停机,投入电动盘车,测量晃动度为10丝,盘车至汽缸常温,测量晃动度仍有10丝,转子大轴弯曲。
二、检查及测量:
揭盖检查及测量轴弯曲时发现,前轴封、隔板汽封9到14级外圆周有明显
摩擦痕迹,其中11级最为严重。
在汽发对轮脱开状态测量弯曲度,绘出曲线如图:
由图可见,最大弯曲点在测量点12,直径为620处(第8级与第9级叶轮间),凸出方位在第#7对轮螺栓孔与#8中间处,其值为0 .10 mm.
三、直轴方案的选择:
由于该轴为整锻合金材料,弯曲度较小,所以决定采用先对轴做稳定性热处理(应力松驰),再做低速动平衡,其方案主要对温度的控制。
该转子为30Cr2M0V钢,抗松驰性能较好,故加热温度取660℃—680℃,低于回火温度30—50℃,以防引起性能改变。
为了加快直轴过程工作需连续进行。
四、直轴前的准备工作:
根据现场条件及设备,经研究决定:
①支承:将汽机转子放入下半空缸内,#1、#2汽机轴承为支承,轴瓦及轴
承盖回装,通入润滑油,50r/min电动盘车装置通过变频至5r/min,连续
电动盘车。
②加热:选用5、6号焊嘴,焊炬总长1130mm的焊炬六把,焊嘴距离轴面
约20—25mm,温度控制在660℃—680℃。
③测量:用0—1000℃手持式红外测温仪测量轴表面温度,在前轴承箱晃动
度测点监测晃动。
五、直轴:
各轴承检查,通往润滑油,油压检查,投入电动盘车5r/min,电机电流检查,大轴晃动度检查,并做好相关记录,施工场地清理,施工人员职责确定,分工明确,加热工具检查,一切完备后开始加热。
先从第十四级隔板处开始,六只焊炬同时分上下左右对轴加热,严格控制温度,升至680℃停止加热,迅速保温,连续逐级加热,保温至前轴封。
连续工作10小时,加热工作结束,保持电动盘车5r/min。
30小时后转子温度降至常温,测量弯曲度为最大0.03 mm ,认为轴已校直合格。
直轴后轴晃动值不大,决定不作动平衡。
汽机与发电机转子连接后,测得高压轴端晃动度为0.04mm,直轴后,第一次启动前盘车检查,连续盘车1小时无异常,开始冲动转子,汽机在400r/min及1200r/min处各暖机1小时,一切正常后升速到3000r/min。
整个升速过程中振动均在合格的范围内,定速后各轴承振动也在合格范围,带负荷后振动也合格。
以后又多次起动,振动情况不变,实践证明,直轴效果良好。
六、结束语:
这次直轴选用金属材料的松驰特性进行直轴的方法效果良好,使“应力松驰法”在电厂汽轮机本体检修工作中的现场直轴工艺得到很好的证明。
此次检修工作中关键是根据大轴的金属材料选择加热温度及工作中严格控制温度,在
检修过程中,分析此次大轴弯曲事故的原因,主要是,紧急停机后热态启动中后轴封减温水门内漏大,汽封温度低且汽封投入时间过长,导致上下缸温差大,且高温状态转子局部冷却使大轴弹性变形弯曲,又强行起动使大轴发生摩擦,局部过热造成永久性弯曲。
通过这次的检修工作也告诉我们只有严格执行电厂设备运行规程的规定,才能避免事故的发生,才能保证生产的安全。