腐蚀事例
硫化氢金属腐蚀

精选ppt
17
• 四川局威远23井,下入7″(N-80)的技 术套管,对丝扣连接不放心,在连接处 电焊加固,而这口井恰好含H2S,因井口 压力大,很快就将焊口蹩破,井口被抬 起,引起爆炸着火,火焰高达100米,3 分钟后井架倒塌,烧了44天,损失1亿多 元。
精选ppt
18
5、时间:
精选ppt
20
2、加入缓蚀剂
原理:金属表面氧化生成钝化膜或改变 金属腐蚀电位起保护作用。
精选ppt
21
• 3、控制溶液的PH值
提高溶液PH值降低溶液中H+含量,可提 高钢材对硫化氢的耐腐蚀能力,维持PH 值在9~11之间,不仅可有效预防硫化氢 腐蚀,又可同时提高钢材疲劳寿命。
• 4、减少硫化氢溶液有管材的接触时间
精选ppt
2
事例:
2003年,河南油田70119井队在T708 井的试采中发生氢脆断裂。该井设计井 深5600米。完井后试采一周,开始起钻 具,起了有500米左右突然发生氢脆断裂, 钻具断为好几节掉入井内。事后测得井 口硫化氢浓度为1000ppm左右,距离井 口周围方圆50米左右,测得硫化氢浓度 为500——600ppm。最后不得不采取封 井措施,放弃该井,造成两千多万的经 济损失。
管材与硫化氢溶液接触的时间越长,发生电化 学失重腐蚀、氢脆和硫化物应力腐蚀破裂的程 度就越严重。
精选ppt
19
三、硫化氢应力腐蚀开裂和氢损伤的预防
• 1、选用抗硫管材: • 成份合理 • 采用有害元素含量很低的纯净钢材 • 良好的淬透性和均匀细小的回火组织,硬度
波动尽可能小 • 回火稳定性好,回火温度高(大于600度) • 良好的韧性 • 消除残余拉应力
案例▕史上分析最透彻的腐蚀破坏事故

小化04-04原文事例1-20某石油化工厂常减压车间减粘事故线在109号阀后管道穿孔,引起火灾,使常压工段停工。
破口在管线底部距法兰盘50mm处,破口呈三角形,高85mm,宽72mm。
事故线介质为减压蒸馏塔底渣油,温度400℃,含硫量1.2%,流速0.3m/s。
事故线材质为20号钢,原厚度7mm,使用2年被蚀穿,最大腐蚀率达3.5mm/a。
评述与上一事例一样,渣油系统的腐蚀主要为高温硫腐蚀。
该厂渣油硫含量高(1.2%),温度达400℃,H2S和H2S分解生成的活性S反应生成无保护性的FeS,所以对碳钢腐蚀十分严重。
另外,流速和流动状态对高温硫腐蚀也有很大影响。
事故线渣油流速为0.3m/s,平常操作中109阀开度不足二分之一,在阀后一定距离流体界面最小,流速最大(约为0.8m/s),渣油直接冲击管线底部,故对该处管线产生严重磨损腐蚀,造成穿孔。
所以,应选择更耐腐蚀和磨损的材料。
比如管道可选低合金钢Cr5Mo,弯头和阀后管道可选1Cr18Ni8不锈钢。
介质流速也是一个很重要的环境因素。
但流速对材料腐蚀的影响又是很复杂的。
不过在很多情况下流速增大将使材料腐蚀率增加。
因为当流速增大时腐蚀剂的供应会更充足,使浓度极化降低;腐蚀产物会更容易流走,难以对被腐蚀金属表面提供保护。
特别当介质流速很高时,会造成一种破坏性很大的局部腐蚀形态:磨损腐蚀。
这是由于高速流动介质产生的机械冲刷和腐蚀的联合作用所造成的破坏。
流体的冲刷使材料表面保护膜被破坏,露出新鲜金属表面,遭受介质的腐蚀;腐蚀造成表面不平,流动紊乱,形成涡流和涡旋,进一步增大了流体的冲刷。
这种相互促进的联合作用导致设备壁厚严重减薄,最终穿孔。
流动系统中的设备,如管道、管件、阀门、搅拌器、泵、叶轮、汽轮机叶片等,磨损腐蚀是一种常见的腐蚀破坏原因。
前面两个事例都属于高速高温硫化物环境中的磨损腐蚀破坏。
对这种环境中工作的设备,在选材时不仅要考虑到介质的腐蚀性,还要考虑介质流速和流动状态与腐蚀的联合作用。
过程装备腐蚀与防护考点内容

主要试题题型:一、简答题(约30分)二、填空题(约20分)三、选择题(约10分)四、腐蚀事例分析(3- 4小题,共40分)第一章 腐蚀电化学基础1、金属与溶液的界面特性——双电层金属浸入电解质溶液内,其表面的原子与溶液中的极性水分子、电解质离子、氧等相互作用,使界面的金属和溶液侧分别形成带有异性电荷的双电层。
2.电极电位电极电位:电极反应使电极和溶液界面上建立的双电层电位跃。
3.金属电化学腐蚀的热力学条件(1). 金属溶解的氧化反应若进行,则金属的实际电位必更正于金属的平衡电极电位。
E>Ee,M(2)去极化反应若进行,则有金属电极电位必更负于去极剂的氧化还原反应电位。
E<Ek0上述条件需同时满足。
4、极化极化现象:电池工作过程中,由于电流流动而引起电极电位偏离初始值的现象。
极化现象的根本原因:电极反应与电子迁移的速度差。
极化曲线定义:用来表示极化电位与极化电流或极化电流密度之间关系的曲线。
作用:判断电极材料的极化特性。
腐蚀极化图定义:将构成腐蚀电池的阴极和阳极极化曲线绘在同一E -I 坐标上得到的图线,简称极化图。
对给定的腐蚀电池,工作稳定时的腐蚀电流为Icorr ,则初始电动势问题:如增加最有效的阴极的面积,或添加去极剂,搅拌等,将使Ex -S 水平线向正方向移动(为什么?)5、超电压(过电位)腐蚀电池工作时,由于极化作用使阴极电位变负,阳极电位变正。
这个值与各极的初始电位差值的绝对值称为超电压或过电位。
以η表示。
超电压量化的反映了极化的程度,对研究腐蚀速度非常重要。
6.金属的耐蚀性能评定(针对全面腐蚀 为什么?)金属耐蚀性也叫化学稳定性,即金属抵抗介质作用的能力。
对全面腐蚀,通常以腐蚀速度评定。
对受均匀腐蚀的金属,常以年腐蚀深度来评定耐腐蚀的等级7、腐蚀速度的工程表示方法重量法:以金属腐蚀前后金属质量的变化来表示,分失重法和增重法。
常为实验室采用。
失重法适用于腐蚀产物能很好地除去而不损伤主体。
腐蚀案例
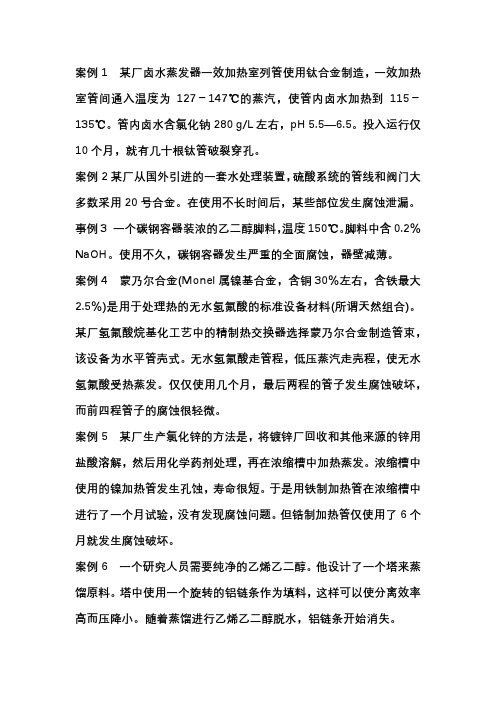
案例1 某厂卤水蒸发器一效加热室列管使用钛合金制造,一效加热室管间通入温度为127-147℃的蒸汽,使管内卤水加热到115-135℃。
管内卤水含氯化钠280 g/L左右,pH 5.5—6.5。
投入运行仅10个月,就有几十根钛管破裂穿孔。
案例2某厂从国外引进的一套水处理装置,硫酸系统的管线和阀门大多数采用20号合金。
在使用不长时间后,某些部位发生腐蚀泄漏。
事例3 一个碳钢容器装浓的乙二醇脚料,温度150℃。
脚料中含0.2%NaOH。
使用不久,碳钢容器发生严重的全面腐蚀,器壁减薄。
案例4 蒙乃尔合金(Monel属镍基合金,含铜30%左右,含铁最大2.5%)是用于处理热的无水氢氟酸的标准设备材料(所谓天然组合)。
某厂氢氟酸烷基化工艺中的精制热交换器选择蒙乃尔合金制造管束,该设备为水平管壳式。
无水氢氟酸走管程,低压蒸汽走壳程,使无水氢氟酸受热蒸发。
仅仅使用几个月,最后两程的管子发生腐蚀破坏,而前四程管子的腐蚀很轻微。
案例5 某厂生产氯化锌的方法是,将镀锌厂回收和其他来源的锌用盐酸溶解,然后用化学药剂处理,再在浓缩槽中加热蒸发。
浓缩槽中使用的镍加热管发生孔蚀,寿命很短。
于是用铁制加热管在浓缩槽中进行了一个月试验,没有发现腐蚀问题。
但锆制加热管仅使用了6个月就发生腐蚀破坏。
案例6 一个研究人员需要纯净的乙烯乙二醇。
他设计了一个塔来蒸馏原料。
塔中使用一个旋转的铝链条作为填料,这样可以使分离效率高而压降小。
随着蒸馏进行乙烯乙二醇脱水,铝链条开始消失。
海洋管道腐蚀 案例

海洋管道腐蚀案例
海洋管道腐蚀的案例之一是新疆的一条X52钢输油管道。
该管道在2003年发生了一次爆管泄露事件,经过调查发现,管道沿线的起伏管段是内腐蚀穿孔泄漏事故的多发地带。
原因是这些管段低洼处有微量游离水或积水聚积,为硫酸盐还原菌(SRB)提供了生长环境,导致管道局部腐蚀失效。
此外,还有一艘船在船底喷砂、喷漆和更换阳极锌块后,船体进水。
经调查发现,海水管道的腐蚀、腐烂和故障可能是导致进水的原因。
同时,舱底水中的硫酸盐还原菌(SRB)数量远高于舱外海水,说明SRB在舰船的舱底水中大量存在,可能对船体造成腐蚀。
因此,在海洋管道和船只维护过程中,需要特别注意防止管道和船体的腐蚀问题,尤其是在管道的起伏管段和船底区域。
同时,对于船只来说,还需要注意舱底水的处理和监控,防止硫酸盐还原菌的大量繁殖对船体造成腐蚀。
腐蚀事例——精选推荐

腐蚀事例第⼆章:电偶腐蚀:实例1:六⼗年代初,美国破冰船壳上的焊缝很快腐蚀,⽐船壳钢板腐蚀还更严重,原因是焊接⾦属对船壳是阳极。
加之船壳的涂层系统被冰擦伤,阴极保护系统的阳极也被冰刮落,失去了保护作⽤。
Eg:焊缝是阳极,船壳是阴极,这就构成了⼩阳极⼤阴极的电偶腐蚀电池。
在“制造”部分已经讲到,由于焊缝⾼温熔化和冷却过程中成分和组织的变化,如果焊条选择不当,很容易造成焊缝耐腐蚀性低于母体,使焊缝发⽣优先腐蚀。
如果焊缝的电位⽐母体低得多,那么焊缝与母材组成电偶腐蚀电池,焊缝的腐蚀将⼤⼤的加速。
所以在选择焊接⾦属时⼀个基本的原则:焊缝相对于母材应是阴极性的。
///对于船舶来说,船壳上都有涂层,⼤多数还使⽤阴极保护。
涂料层如果完整致密,将船体和海⽔隔开,⽽阴极保护⼜将船壳控制在同⼀个保护电位,消除了电位的差异。
所以只要涂层和阴极保护正常。
那么焊缝与母材的电偶腐蚀问题是不会发⽣的。
实例2:某发电⼚凝汽器的管束材质为黄铜,花板未碳钢。
原来使⽤河⽔作凝汽器的冷却⽔,后来因为缺⽔,便掺⼊了⼀些海⽔。
结果许多设备的腐蚀都加剧了,特别是凝汽器的花板,膨接处的腐蚀率达到20-25mm/a。
Eg:黄铜管束与碳钢花板组成了电偶对,碳钢作为阳极⽽黄铜作为阴极。
由于黄铜管束⾯积⽐碳钢⾯积⼤得多,这⼜是⼀个⼩阳极⼤阴极的组合。
因⽽天花板可能遭到电偶腐蚀。
///在使⽤河⽔作冷却⽔时电偶腐蚀问题并不明显,没有引起注意;⽽在河⽔中掺⼊海⽔是电偶腐蚀问题突出了。
这是因为河⽔的电阻率⼤,导电性不好,⽽海⽔的导电性很好。
腐蚀电池的电流回路包括溶液的欧姆电阻,欧姆电阻⼤则电池⼯作阻⼒⼤,腐蚀电流⼩。
海⽔电阻率⼩,腐蚀电池电流回路的欧姆电阻笑,因⽽阳极碳钢花板的电偶腐蚀⼤⼤加剧。
实例2:某啤酒⼚的⼤啤酒罐,⽤碳钢制造,表⾯涂覆防腐涂料,⽤了20年。
为了解决罐底涂料层容易损坏的问题,新造贮罐采⽤了不锈钢板作罐底,筒体仍⽤碳钢。
认为不锈钢完全耐蚀就没有涂覆涂料。
石油化工典型腐蚀案例1407

不足,造成低PH的泄漏;国内蒸馏案例三;QDLH--蒸馏塔顶2205材料空冷投用3个月顶排中部穿孔。
估计与洗塔有关,大量盐酸不能及时中和。
国内蒸馏案例五;由于注水导致换热器露点腐蚀位置提前国内蒸馏案例六;控制壁温在结晶温度温度上电场不稳,原油脱后含水影响蒸馏操作;初馏塔前的换热器碱脆:螺栓、法兰、换热器管口等;原因分析:不合格的法兰,在硫化物环境中腐蚀疲劳与应力开裂;裂纹℉℃C用镍合金B炭钢消除应力处理(阀门内件镍合金)A炭钢不消除应力处理原设计改进设计设计压力:1.7MPa,设计温度:40℃,操作压力:1.2MPa,操作温度:45℃,介质为含硫化氢富气、凝缩油和含硫污水;现场检测厚度有18处分层;判断是湿硫化氢应力腐蚀SSCC与HIC/SOHIC开裂;¾2#瓦斯压缩机气阀阀座与升程限制器连接螺栓断裂,二级入口气阀固定螺栓材质3Cr13,断裂固定螺栓硬度高达HRC58.6。
在应力集中的螺纹尾部产生应力腐蚀断裂,造成气阀座松脱,气阀阀座与连接螺栓从死点区进入到活塞工作区,致使活塞能猛烈撞击大盖是发生事故的第一原因。
建议采用隔离式的安全阀;焦炭塔上段复合板裂纹高镍合金焊缝/热影响区与复合板裂纹天津石化250万吨/年延迟焦化装置4台Φ9400焦炭塔复层焊缝制造发现上千条裂纹;微裂纹出现在焊缝上,怀疑是焊接时线能量太大所致。
采用625焊条,焊接时层间温度应小于100℃,应尽量采用小焊接线能量焊接,热输入量宜控制在0.5~1.0KJ/mm。
国内外有报道由不锈钢导凝管开工过程的氯离子浓缩导致爆炸着火的案例不少。
建议材料升级到高镍合金或取消导凝管。
我国新建加氢装置已取消了。
管焊缝开裂,裂纹由里向外。
2) 湿硫化氢应力腐蚀开裂投产二年九个月后首检发现厚壁不锈钢管线焊缝开裂,金相显示属于晶界开裂,原因是施工为赶进度造成大量的热裂纹,又没有发现。
返修后三年第二次检修,裂纹开裂更加严重,已构成安全问题,需全部更换。
不当焊接引起的奥氏体不锈钢结构应力腐蚀破裂事例

第10卷第2期1998年3月 腐蚀科学与防护技术CORROSI ON SC IENCE AND PROTECT I ON TECHNOLOG Y V o l.10N o.2M ar.1998不当焊接引起的奥氏体不锈钢结构应力腐蚀破裂事例潘希德沈风刚董俊明薛锦(西安交通大学西安710049)摘 要 针对某厂一套316L设备多次沿焊接热影响区(HA Z)发生的断裂事故,进行失效分析,认为该设备的断裂属于SCC,焊接接头的质量差是造成断裂的根本原因,并提出了提高焊接质量,防止SCC的办法.关键词 焊接接头,应力腐蚀破裂,失效分析学科分类号 T G172.82奥氏体不锈钢是一种性能优良、应用广泛的钢种,但其抗应力腐蚀特别是在氯化物中的SCC性能较差,这方面的研究已有很多报导[1,2].而在实际应用中常常发生由于安装,特别是焊接质量差引起的SCC,应该引起足够的重视.某厂一套奥氏体不锈钢设备炉体自1988年投入使用,到1994年曾多次发生沿焊接HA Z的断裂事故,造成了该设备多次停产,损失很大.厂方虽将原1828型材料换成了316L不锈钢,进行补焊修复,仍无法阻止断裂的发生.1994年11月作者与该厂联合,对该设备第四次断裂的断口进行了失效分析,认为该设备的断裂属于SCC,而安装质量特别是焊接质量差是导致断裂的根本原因.1失效分析设备炉体及断口如图1所示,炉体尺寸为 1000mm×14000mm,根据厂方提供的资料,工作环境为富C l-溶液.为确定断裂类型及原因,对断口进行宏观、微观、焊接质量及电化学分析.1.1断口宏观分析该炉体是用不锈钢板卷圆焊接而成的(如图1所示),原板厚10mm,补焊段板厚12mm.断口位于环焊缝的HA Z,炉体周长约3140mm,裂纹长度约1970mm,其余约1170mm长的断口为无腐蚀产物、较平直的、光亮的机械失稳断裂断口.从断口上可看出:裂纹产生于环焊缝的HA Z,而在母材及焊缝上未发现裂纹,说明断裂与安装及焊接过程有关;在纵向焊缝及其HA Z上未发现裂纹,说明该炉体的断裂问题是可以解决的. 收到初稿:1997203223,收到修改稿:19972062281.2断口微观分析图2是断口的金相照片.裂纹均沿晶发展,呈网状、龟裂形式,属于典型的晶间腐蚀并导致应力腐蚀破裂断口.这种晶间腐蚀与焊接所造成的奥氏体不锈钢的敏化有关,在焊接时,HA Z 被加热到很高的温度,有利于碳向晶界上扩散,在那里与C r 结合成铬的碳化物,使得晶界上贫C r ,因而产生晶间腐蚀.所以在焊接奥氏体不锈钢时,要尽量减小热输入量,提高冷却速度.F ig .1Schem e of the fu rnace stack and its m acro fractu re F ig .2F ractograph of the w elded j o in t ×200由于断口在腐蚀介质中浸泡时间过长,断口上的腐蚀产物堆积很厚,故无法用电镜作进一步的断口形貌分析.从金相组织上可以看出,母材为均匀的奥氏体组织,而HA Z 的组织不均匀且有大量的孪晶存在,孪晶中存在大量的位错,这对于应力腐蚀裂纹的产生和扩展都是十分有利的.1.3接头质量分析由上述分析可知,断裂可能与安装及焊接质量有很大的关系,故必须对焊缝质量、焊接工艺、安装质量等等作详细的分析.1.3.1焊缝质量及焊接工艺 焊接采用的是手工电弧焊,国产A 042焊条,其熔敷金属组织相当于E 00223213M o 2216,是一种超低碳不锈钢焊条,有良好的抗裂性及耐蚀性,主要用于焊接同类型的超低碳不锈钢.表1是A 042及316L 的标准成分,从成分对比及防腐焊条的选用准则上看,用A 042焊条焊接316L 是基本上合适的.再者,奥氏体型焊条熔敷金属的塑性、韧性较高,这样匹配的接头的耐蚀性及抗SCC 性能应该是较好的.Table 1Che m ica l co m position of 316L and A 042(wt %)CM n Si S P C r N i M o 316L<0.03<2.00<1.00<0.030<0.04516.0~18.010.0~14.02.00~3.00A 042≤0.040.5~2.5≤0.9≤0.030≤0.03522~2512~242~3焊缝金属的能谱分析结果表明,焊缝中C r 、N i 、M o 的含量分别为22.7w t %、13.3w t %、0.17w t %,其中M o 含量远低于标准要求,将大大降低焊缝的抗SCC 性能.这可能是焊条的质9112期潘希德等:不当焊接引起的奥氏体不锈钢结构应力腐蚀破裂事例量问题.F ig .3D istribu ting cu rve of hardness HV in j o in t F ig .4Jo in t p reparati on 图3是测得的接头硬度分布.可以看出:焊缝金属的硬度分布极不均匀,熔合线附近的硬度最高,说明焊缝的组织不均匀,成分偏析严重.在后面将会讲到,所焊焊缝存在咬边、焊缝增高过大等几何不连续性,从而很容易在熔合区产生裂纹.从焊缝的外观上可以看出很明显的咬边、焊缝宽度及增高过大等缺陷.咬边可能是焊接规范不当,焊接电流过大、焊接速度过慢引起的.焊缝宽度及增高过大说明焊接速度慢、焊条摆动大,这对于奥氏体不锈钢的焊接是非常忌讳的,是造成HA Z 组织粗大,SCC 敏感性增加的重要原因.补焊用板材与原材在厚度上有2mm 的差别,可能是制订焊接工艺规范时,增加焊缝宽度和余高的原因.1.3.2安装质量 在炉内发现有在圆周上沿焊缝均匀分布的小筋板结构.这可能是在设备安装时起点固作用的,而在设备安装完毕后没有作必要的处理,遗留在炉体内.观察发现,多处筋板的连接焊缝上产生了应力腐蚀裂纹,且有几块筋板已沿焊缝HA Z 发生断裂.这种点固焊缝与环焊缝交叉易产生较大的三轴焊接残余应力,而且,与介质接触时,C l -离子很容易在此处聚集、浓缩,使得焊缝和HA Z 处于高浓度的介质中,更易于产生SCC ,裂纹也易于从此处产生和扩展.前面讲到的焊缝的宽度及余高过大,以及咬边等缺陷也可能引起氯离子的聚集,一定要引起足够的重视.对于点固用的焊缝建议取消,或者将其置于不与介质接触的炉体的外表面.2焊接工艺要点为保证焊接结构的抗SCC 性能,建议采用下述焊接工艺.(1)焊接方法 焊接引起的不锈钢母材敏化与焊接方法中热量的输入量关系最为密切.热输入量大,焊接速度慢,又没有辅助冷却的方法,往往很容易引起敏化,而用高焊接速度的弧焊方法,如氩弧焊则比较好,该设备的纵向焊缝不产生SCC 就是一个最好的例证.所以建议采用氩弧焊,焊丝可用与母材相同的材料,如316L 或318焊条.若条件有限也可用手弧焊,选用A 042焊条.(2)焊前准备 对于两块厚度不同不锈钢板的对焊,不可采取摆动焊条,降低焊接速度的方法.可采用机械的方法先消薄厚的一侧钢板,再开坡口,如图4所示,其中l =3(∆2-∆1).在制备坡口时,若用碳弧气刨,则会使坡口表面渗碳,因此焊前应用机械的方法清理坡口,直到露出金属光泽为止. (3)焊接规范 在制订焊接规范时,建议注意以下几点:(a )采用小规范,快速焊,焊缝要021腐蚀科学与防护技术10卷窄,焊条不得作横向摆动.焊接电流按I =(25~40) 确定,其中 为焊条直径.(b )采用直流反极性,以保证电弧稳定燃烧.(c )不要在坡口以外的金属表面上引弧,金属表面的烧伤及飞溅等会降低接头抗SCC 性能[3].(d )采用短弧焊,收弧时要注意填满弧坑.(e )多层焊时,要严格控制层间温度不得超过60℃,即要等到前一层焊缝冷却到不烫手时,才能再焊下一道焊缝.(f )多层焊时,层间要严格清理,避免形成夹渣.(g )采用双面焊时,由于坡口开在炉体的外表面,并考虑到炉体内表面要与介质相接触,所以要先焊炉体的外表面,用砂轮清根后,再焊内表面.(h )对于盖面焊缝的余高最好用砂轮打磨,使母材到焊缝能园滑过渡.(i )焊接过程中进行强迫冷却.在焊接过程中可通过水冷、风吹对焊缝进行强制冷却,这对于降低焊接引起的母材敏化是十分有益的.(j )焊后处理,焊后可采取喷丸韧化处理等措施.许多研究表明,对有应力腐蚀破裂危险的装置的某此危险部位,采取喷丸韧化处理是十分有效的.3结 论1失效分析表明,该设备的断裂是氯离子介质SCC 引起的.2焊接及安装质量差是产生SCC 的根本原因.3通过控制焊接及安装质量防止该设备的再次断裂是完全可能的.参考文献1F rignani A .Co rro s .Sci .1984,24(6):9172黄彦良,曹楚南,林海潮,等.腐蚀科学与防护技术,1993,5(3):1923N eukomm K ,L ucerne .W elding and Cutting ,1992,12:78SCC ON AN AUSTEN IT I C STA INL ESS STEEL W ELD EDSTRUCTURE D UE T O POOR W ELD ING QUAL IT YPAN X ide ,SH EN Fenggang ,DON G Junm ing ,XU E J in(X i ’an J iaotong U n iversity ,X i ’an 710049)ABSTRACT 316L stain less steel is a k ind of m aterial w ith good co rro si on 2resistance ,bu t its p rop erties of an ti 2SCC are con siderab ly affected by assem b ling quality ,esp ecially by w elding quality .T he failu re on the heat affected zone (HA Z )in a 316L stain less steel w eld 2ing structu re is analysed in the p resen t p ap er .T he resu lts show that the failu re is cau sed by SCC ,and the bad w elding quality is the basic reason .T he w ay to i m p rove the w elding quali 2ty and p reven t SCC is p resen ted .KEY WORD S w elding j o in t ,stress co rro si on crack ing ,failu re analysis1212期潘希德等:不当焊接引起的奥氏体不锈钢结构应力腐蚀破裂事例。
具体腐蚀事例
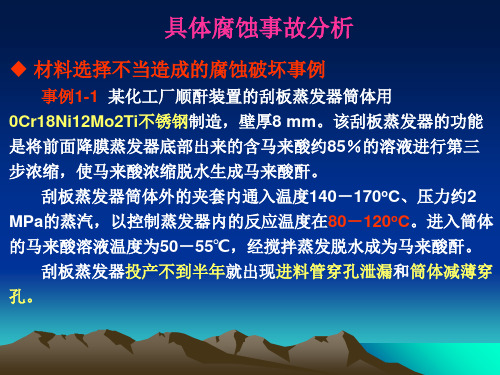
实际考查一下本事例中所使用的泵,原来硫酸是经 过了一个洗涤喷嘴后才进入泵,在经过喷嘴时吸入了空 气。因此泵送的硫酸中含有饱和的空气,这就使哈氏合 金B泵的腐蚀行为和不含空气的“纯硫酸”中该合金的腐 蚀行为有很大差别,而这一点在选材时被忽视了。
对于这种含有空气的硫酸,应选用哈氏合金C。哈氏 合金C含有18%的铬,提高了对氧化性介质的耐蚀性,使 它在含氧化剂的酸中的耐蚀性优干哈氏合金B。
因此钛合金管工作在发生 腐蚀的区域,破坏也就是不 可避免的了。
所以,在选材时温度是一个十分重要的环境因素。在设备 操作运行中也是影响腐蚀的十分重要因素,许多设备腐蚀破坏 事故发生是由于环境温度超出了材料的耐蚀温度范围,必须进 行严格的论证。
对于实际生产设备来说,除了考虑主体温度外,还须注 意以下几点:
腐蚀原因是管路中有一个喷嘴。 评述 腐蚀图中的硫酸是指“纯硫酸”,即硫酸中不含 其他杂质。如果硫酸中含有氧化性物质,如溶解氧、硝酸等, 哈氏合金B的腐蚀率将大大增加。 这是因为哈氏合金B的主要成分是镍(68%)、钼(28%), 另有少量铁(5%)、钒(1%),不含对氧化性介质耐蚀性好的合 金元素铬,所以哈氏合金B只是在非氧化性酸中表现出优良的 耐蚀性,比如在不含溶解氧的纯盐酸中,在整个浓度和温度 范围内哈氏合金B都是耐蚀的。
所以蒙乃尔合金在脱氧条件下,能用于各种浓度的 氢氟酸,当氢氟酸中含氧化性杂质时腐蚀速度增大。
工业无水氢氟酸含0.001%的硫酸。 这种含量的硫酸对蒙乃尔合金本来不会造成腐蚀影 响,问题是在本事例的设备中,由于硫酸沸点高并不蒸 发;氢氟酸的蒸发造成硫酸在最后两程管子里聚集。热 的浓硫酸属强氧化性介质,造成蒙乃尔合金管的腐蚀破 坏。
事例1-11 某造纸厂漂白工段制备二氧化氯漂白液 设备,使用直径为22 mm工业纯钛管,输送钢瓶装氯气, 氯气流过仅半小时,钛管即烧毁.只剩下未烧完的钛法 兰。
钢结构事故案例分析(二)

• 原因分析:对积水后荷载进行计算,如下
• 当屋面最深积水达到35cm,支座节点附近受压腹杆接 近压杆压屈的临界荷载,拉力超过螺栓M27的允许承 载力,
• 当积水深度45cm,腹杆压力超过临界值,支座附近的 腹杆压屈,拉杆的高强螺栓拉断,导致网架倒塌。
• 但是网架拉杆在弹性范围内。 • 可以看出,结论与现场情况是吻合的。
1995年5月25日早晨,广州海印斜拉桥一根钢索突然 断裂,近百米的钢索坠落在桥面,距离当时大桥 建成6年半。每一根钢索都有近两百根直径5mm的 高强钢丝组合而成。钢索的防腐蚀做法是:每一 小根钢丝表面镀锌50μm,钢丝束组成的钢索外套 高密度聚乙烯管,馆内灌注水泥浆。事故调查发 现,钢丝上段水泥浆未充满,从而腐蚀。后来对 全部钢索更换为高密度聚乙烯直接在镀锌钝化钢 丝上挤压而成的钢索。
构本身计算(图集中也有不合理之处) • 例题3-1:四楼接层钢屋架倒塌等
• 3.2 第二类-----网架结构质量事故
• 事故原因: • 1.设计失误—荷载组合不当,力学模型、计算简
图不当、节点不当未考虑吊装荷载
• 2.制作失误—下料尺寸不准、节点焊接不过关
•
焊接连接质量不满足
• 3.拼装失误—安装顺序失误、临时支撑少
• 概况:某通讯楼为网架结构,焊接空心球节点棋盘 形四角锥网架,平面尺寸13.2m*17.99m,网格数5*7, 网格尺寸2.64m*2.57m,网架高1m,支撑时上弦周边 支撑。材料均为Q235,网架上弦¢73*4钢管,下弦 ¢89*4.5,腹杆¢38*3,空心球¢200*6.图纸注明贴角 焊缝厚度7.5mm,焊条规定是T42.
•
吊点不合理、多台起重机不协调工作
• 例题3-5通讯楼网架坍塌
腐蚀事例分析及防护方法

腐蚀实例分析及防护方法(应力腐蚀实例)【1】北方一条公路下蒸气冷凝回流管原用碳钢制造,由于冷凝液的腐蚀发生破坏,便用304型不锈钢(0Cr18Ni9)管更换。
使用不到两年出现泄漏,检查管道外表面发生穿晶型应力腐蚀破裂。
分析:北方冬季在公路上撒盐作为防冻剂,盐渗入土壤使公路两侧的土壤中的氯化钠的含量大大增加,奥氏体不锈钢在这种含有很多氯化物的潮湿土壤中,为奥氏体不锈钢发生应力腐蚀破裂提供特定的氯化物的环境,从而发生应力腐蚀。
防护措施:1、把奥氏体不锈钢管换成碳钢管【2】某化工厂生产氯化钾的车间,一台SS-800型三足式离心机转鼓突然发生断裂,转鼓材质为1Cr18Ni9Ti。
经鉴定为应力腐蚀破裂。
分析:氯化钾溶液经过离心转鼓过滤后,氯化钾浓度升高。
然而离心转鼓的材质为(1Cr18Ni9Ti)奥氏体不锈钢。
而氯离子的含量远远超过发生应力腐蚀的临界氯离子浓度,为奥氏体不锈钢发生应力腐蚀破裂提供特定的氯化物的环境。
所以转鼓会发生应力腐蚀从而发生断裂。
防护措施:1、更换转鼓的材质定期清洗表面的氯化物【3】 CO2压缩机一段、二段和三段中间冷却器为304L(00Cr19Ni10)型不锈钢制造。
投产一年多相继发生泄漏。
经检查,裂纹主要发生在高温端水侧管子与管板结合部位。
所用冷却水含氯化物0.002%~0.004%。
分析:管与管板连接形成的缝隙区。
由于闭塞条件使物质迁移困难,容易形成盐垢,造成氯离子浓度增高。
高温端冷却水强烈汽化,在缝隙区形成水垢使氯化物浓缩。
防护措施:1、改进管与管板的联接结构,消除缝隙。
2、立式换热器的结构改进,提高壳程水位,使管束完全被水浸没。
3、管板采用不锈钢—碳钢复合板,以碳钢为牺牲阳极【4】一高压釜用18-8不锈钢制造,釜外用碳钢夹套通水冷却。
冷却水为优质自来水,含氯化物量很低。
高压釜进行间歇操作,每次使用后,将夹套中的水排放掉。
仅操作了几次,高压釜体外表面上形成大量裂纹。
分析:操作时高压釜外表面被冷却水浸没,停运时夹套中的水被放掉。
腐蚀实例——精选推荐

腐蚀实例事例一家汽车旅馆的热水循环系统使用铜管,开张几个月后管线泄漏。
修理人员把责任归于安装不良,而承包商否认安装责任,拒付修理费。
腐蚀专家切开热水管检查,管子内部严重腐蚀,很多地方壁厚已减小到零。
在弯头和配件内表面呈特征性的波纹形,说明破坏属磨损腐蚀(冲刷腐蚀)。
原来承包商想使热水供应更充足,安装了一个较大的泵。
这样,热水流速超过了铜管允许流速值的3~4倍(正常值为0.9~1.5m/s,当水是热的或腐蚀性较强时还应更低)。
评述这里又是流速过大造成的磨损腐蚀破坏。
这个承包商想把事情办得更好,却事与愿违,不但未取得效果,反而造成管道的腐蚀破坏。
原因就在于不懂腐蚀与防护知识。
事故发生后还不知道是怎么发生的。
事例某厂聚氯乙烯生产中的转化器是列管式换热器,壳体和列管都是碳钢,管子与花板胀接。
乙炔气和氯化氢气经混合脱水后自下而上通过转化器,完成加成反应得到氯乙烯气体。
反应温度120~180℃。
使用1年多后陆续发生泄漏,最长的18个月,最短的不到13个月。
造成腐蚀的主要原因是原料气带水。
其次是壳程热水水质差,pH值低,氯离子含量高。
评述碳钢在干燥的高浓度氯化氢气中有很好的耐蚀性,腐蚀率0.05~0.5mm/y,当氯化氢气含水超过0.02%,腐蚀率迅速增大。
同样,碳钢在含水量极低的氯气(包括液氯)中也是耐蚀的,而氯气含水则使碳钢严重腐蚀。
所以对于处理干燥氯气(液氯)、氯化氢气的碳钢设备,控制含水量是极其重要的。
事例LSB型高温浓硫酸液下泵是一种新型循环酸泵,在硫酸生产厂得到成功应用。
但有两家硫酸厂的泵运行仅2个月,发现合金铸铁件泵体和进、出酸管腐蚀严重,泵体穿孔。
硫酸浓度97~98%,温度75~85℃。
而其他厂有的温度达90℃以上,或酸浓度在90%以下,几年未出现问题。
评述检查分析,这两个厂采用的是热浓酸洗流程(其他厂为水洗或封闭酸洗),使吸收循环酸中杂质含量高。
如Cu2+,AsO43+,Fe3+,SeO42-,都是强氧化剂。
化验室事故例子汇总

化验室事故例子汇总(8至9楼)1.蒸馏甲苯的过程中,忘记加入沸石,发生爆沸而引起其火。
2.将还剩有有机溶剂的容器进行玻璃加工时,引起着火爆炸而受伤。
3.把沾有废汽油的东西投入火中焚烧时,产生意想不到的猛烈火燃而烧伤。
4.用丙酮洗涤烧瓶,然后置于干燥箱中进行干燥时,残留的丙酮气化而引起爆炸。
干燥箱的门被炸坏飞至远处。
5.将经过加热的溶液,于分液漏斗中用二甲苯进行萃取,当打开分液漏斗的旋塞时,喷出二甲苯而引起着火。
6.将润滑油进行减压蒸馏时,用气体火焰直接加热。
蒸完后,立刻打开减压旋塞,于烧瓶中放入空气时发生爆炸。
7.将油浴加热到高温的过程中,当熄灭气体火焰而关闭空气开关时,突然伸出很长的摇曳火焰而使油浴着火(熄灭气体火焰时,要先关闭其主要气源的旋塞).8.对着火的油浴覆盖四氯化碳进行灭火时,结果它在油中沸腾,致使着火的油飞溅反而使火势扩大。
9.在蒸馏硝化反应物的过程中,当蒸至剩下很少残液时,突然发生爆炸(因在蒸馏残物中,有多硝基化合物存在故不能蒸馏的太净)。
10.用旧的乙醚进行苹取操作,然后把由萃取液蒸去乙醚而得到的物质,放在烘箱里加热干燥时发生爆炸,烘箱的门被炸碎。
11.将四氢呋喃进行蒸馏回收时,用剩下贱液的同一烧瓶蒸馏数次,即发生爆炸(因生成乙醚和四氢呋喃的过氧化物之故)。
12.当拔出30%浓度的过氧化氢试剂瓶的塞子时,常会发生爆炸。
13.用过氧化氢制氧气的过程中,当加入二氧化锰时,剧烈地发生反应,致使烧瓶破裂。
14误认为充有氯气的钢瓶空了,但当打开阀门时,喷出大量氯气而中毒。
15.将丙烯与氨的混合气体进行加压反应的过程中,发现阀门有少量漏气。
在修理过程中,泄漏增大,以致不能进行修理并中毒(在加压情况下进行修理很危险)。
16.于自制的容器中填充氨气,用帆布包裹,在搬远过程中,由于容器的焊缝破裂,冲出氨气而冻伤。
并且,呼吸器官也受到损害。
17.直接闻到溶解在反应生成物中未起反应的氨的臭味而摔倒、受伤。
腐蚀品事故案例分系

第八类腐蚀品1、硝酸惹祸的两起事故[案情介绍] 案例一1973年11月3日,欧罗巴帕美国航空公司的一架喷气式货运飞机自纽约机场起飞。
数分钟后,机场的地面指挥系统就接到飞机机长的报告:机上发生异常状况,机舱内着火。
尽管采取了自救措施仍未见效果。
35分钟后,飞机坠毁于波士顿机场,三名机组人员全部死亡。
经有关部门对事故进行深入调查发现:在所装的货物中有一批硝酸。
其包装不符合运输要求,是桶装容器外套木板箱,中间用木屑作衬垫。
货物在装上飞机时,作业人员没有注意箱顶上“该面朝上”的指示标志,而是随意堆放。
由于箱内货物倒置,硝酸自桶中渗漏出来,与木屑相混,自燃而引起火灾。
案例二1989年2月6日下午4时20分,从西安开往济南的207次列车行至三门峡铁门路段时,8号车厢尽头的行李架上突然冒出一股呛人的烟雾,旅客纷纷夺路而逃。
车上秩序顿时大乱。
这时列车员与乘警不顾个人安危,冲上去抓起那只冒烟的手提包,打开车窗扔到窗外,接着又拉下紧急刹车的制动阀。
经现场展开的调查,查实了手提包的主人是河南省灵宝县程村乡的一个叫朱红军的农民。
他携带了一瓶硝酸,逃过车站的检查后自以为没事了,没想到手提包在行李架上倾倒,硝酸自瓶口渗出,险些酿成大祸。
就是这样,奋不顾身扔包的女列车员的手背已被多次灼伤,身上的衣服也被腐蚀后发脆、变色。
这个肇事者当即受到治安拘留的处理。
[事故原因分析] 硝酸,联合国编号为2031,属第八类·腐蚀品,是具有严重危险性的物品。
硝酸透明、无色,通常因溶有二氧化氮而呈红棕色。
有独特的窒息性气体。
硝酸的化学性能相当活泼,具有极强氧化性,几乎可以与一切金属、非金属起反应。
硝酸中溶有的二氧化氮越多,其氧化能力越强,腐蚀性就越大。
硝酸在发生腐蚀反应时一般总会生成有毒气体一氧化氮或二氧化氮,从而对人体生成危害。
硝酸的氧化能力能引起木材和其他纤维素物品燃烧。
一般常见的有机物如松节油、醋酸、丙酮、乙醇等与浓硝酸相混即发生爆炸。
腐蚀事例

二、轻烃储罐的腐蚀与防护1.概况原油稳定装置原料是常减压和重整装置的初馏塔顶C1-C5末凝气。
经过处理后主要产品为轻烃,副产品是高压瓦斯。
其中V300和V400罐是储存处理后的液态烃。
其液态烃送到乙烯做原料,分离出的末凝气靠自身的压力送入高压瓦斯管网。
来源于常减压和重整装置的初馏塔顶末凝气含有HCI、H2S和水。
造成轻烃罐内壁金属表面腐,出现直径有5mm左右大小不一的点蚀坑,原有的金属表面已经腐蚀没有。
腐蚀率达到0.5-1毫米/年。
3年前采用300微米热喷铝防腐涂层已经腐蚀没有,表面产生大量的灰白色铝的锈蚀物。
2.腐蚀原因分析这两座罐使用于1986年7月, 其主要条件见表一。
其主要条件为表一储存的介质中的HCI来源于原油中含有的氯盐和水。
氯盐中的主要成分是NaCl,MgCl2,CaCl2,其中NaCl约占75%,MgCl2约占15%,CaCl2约占10%。
在原油加工时,当加热到120℃以上时,MgCl2和CaCl2即开始水解生成HCI。
其反应为:MgCl2+H2O ―― Mg(OH)2 + 2HCl ↑CaCl2+H2O ―― Ca(OH)2 + 2HCl ↑一般气相部位腐蚀较轻微,液相部位腐蚀严重。
影响该部位腐蚀的主要因素是原油中的盐水解后生成HCI 及H2S而引起的。
这些部位的腐蚀形态为碳钢表面的全面腐蚀、均匀减薄。
从检查的情况看这些部位属于低温HCI-H2S-H2O体系的腐蚀。
虽然在进入这两个罐前进行了脱硫,但是液化石油气中含硫量在0.118%-2.5%,易产生低温HCI-H2S-H2O的腐蚀。
2.1腐蚀反应2.1.1防腐层的腐蚀在轻烃罐内其中V300(V400没有防腐)内壁表面原采用金属热喷涂的方法,做300微米厚铝防腐层,采用E44环氧银粉漆做封闭层。
在大气中铝是耐蚀的的,甚至有SO2及CO2存在时影响也很小,但附着在铝表面的污染物可能形成氧的浓差电池而产生点蚀。
铝在PH4-11的淡水中是很耐蚀的,但PH值小于4时出现酸性侵蚀,PH大于11时出现碱性侵蚀。
- 1、下载文档前请自行甄别文档内容的完整性,平台不提供额外的编辑、内容补充、找答案等附加服务。
- 2、"仅部分预览"的文档,不可在线预览部分如存在完整性等问题,可反馈申请退款(可完整预览的文档不适用该条件!)。
- 3、如文档侵犯您的权益,请联系客服反馈,我们会尽快为您处理(人工客服工作时间:9:00-18:30)。
第二章:电偶腐蚀:实例1:六十年代初,美国破冰船壳上的焊缝很快腐蚀,比船壳钢板腐蚀还更严重,原因是焊接金属对船壳是阳极。
加之船壳的涂层系统被冰擦伤,阴极保护系统的阳极也被冰刮落,失去了保护作用。
Eg:焊缝是阳极,船壳是阴极,这就构成了小阳极大阴极的电偶腐蚀电池。
在“制造”部分已经讲到,由于焊缝高温熔化和冷却过程中成分和组织的变化,如果焊条选择不当,很容易造成焊缝耐腐蚀性低于母体,使焊缝发生优先腐蚀。
如果焊缝的电位比母体低得多,那么焊缝与母材组成电偶腐蚀电池,焊缝的腐蚀将大大的加速。
所以在选择焊接金属时一个基本的原则:焊缝相对于母材应是阴极性的。
///对于船舶来说,船壳上都有涂层,大多数还使用阴极保护。
涂料层如果完整致密,将船体和海水隔开,而阴极保护又将船壳控制在同一个保护电位,消除了电位的差异。
所以只要涂层和阴极保护正常。
那么焊缝与母材的电偶腐蚀问题是不会发生的。
实例2:某发电厂凝汽器的管束材质为黄铜,花板未碳钢。
原来使用河水作凝汽器的冷却水,后来因为缺水,便掺入了一些海水。
结果许多设备的腐蚀都加剧了,特别是凝汽器的花板,膨接处的腐蚀率达到20-25mm/a。
Eg:黄铜管束与碳钢花板组成了电偶对,碳钢作为阳极而黄铜作为阴极。
由于黄铜管束面积比碳钢面积大得多,这又是一个小阳极大阴极的组合。
因而天花板可能遭到电偶腐蚀。
///在使用河水作冷却水时电偶腐蚀问题并不明显,没有引起注意;而在河水中掺入海水是电偶腐蚀问题突出了。
这是因为河水的电阻率大,导电性不好,而海水的导电性很好。
腐蚀电池的电流回路包括溶液的欧姆电阻,欧姆电阻大则电池工作阻力大,腐蚀电流小。
海水电阻率小,腐蚀电池电流回路的欧姆电阻笑,因而阳极碳钢花板的电偶腐蚀大大加剧。
实例2:某啤酒厂的大啤酒罐,用碳钢制造,表面涂覆防腐涂料,用了20年。
为了解决罐底涂料层容易损坏的问题,新造贮罐采用了不锈钢板作罐底,筒体仍用碳钢。
认为不锈钢完全耐蚀就没有涂覆涂料。
几个月后,碳钢罐壁靠近不锈钢的一条窄带内发生大量蚀孔泄漏。
Eg:碳钢罐壁和不锈钢罐底组成了电偶腐蚀电池,碳钢作为阳极,可能发生加速腐蚀破坏。
失误(碳钢罐壁表面涂覆了涂料,而不锈钢罐底表面没有涂覆涂料。
如果当初在不锈钢罐底也涂漆的话,碳钢罐壁是不会发生这么迅速的腐蚀破坏的)。
涂料层由于薄,很难避免空隙。
空隙中裸露出的碳钢变成为小小的阳极区;而罐底不锈钢作为很大的阳极区。
根据阳极对阳极的面积比估计,空隙内碳钢的腐蚀率可达到25mm/a,难怪在几个月之内将碳钢罐壁出了很多小孔。
应力腐蚀:事例1:某轻油制氢装置再生塔底重沸器为U型管换热器。
管程走低变气167℃,壳程走本菲尔溶液117 ℃,其中加有V2O5作为缓蚀剂。
换热管为1Cr18Ni9Ti不锈钢,管板为16Mn钢。
使用两年后,发现管子与管板连接处的缝隙内发生腐蚀。
分析:V2O5是一种钝化剂,能使16Mn钝化,表面生成保护膜。
使用钝化剂的基本要求是:钝化剂的浓度必须超过临界致钝浓度。
Eg:这里考虑奥氏体不锈钢的氯化物溶液中的scc,冷去水中氯化物含量控制很低,但仍然发生了scc破坏。
///设备为热交换器,结构为管壳式。
工艺介质走管程,水走壳程,进行热交换。
因此,不锈钢管子外面接触的的介质都是水而不是氯化物溶液。
水中所含氯化物只是一种杂志,其含量是很低的。
应该不会发生scc的。
问题主要发生在氯化物浓缩富集。
对管壳式热交换器来说,当壳程走水时,氯化物浓缩主要部位是高温端管子与管板连接部位,即管头。
//氯化物浓缩原因是气化,浓缩。
//改进方法:a改进管子和管板的联结结构以消除缝隙,如采用深孔封焊。
在用胀联结时一定要用胀满,以尽量减少缝隙。
也可以用涂料将缝隙封闭。
b对立式热交换器,在结构上作出改进,提高壳程水位,使管束完全被水浸没,不形成汽液界面,可大大减轻管头部位的腐蚀破坏。
C管板采用不锈钢-碳钢复合板,以碳钢为牺牲阳极,对不锈钢管头起阴极保护作用,对降低scc破坏也有效。
实例一:一条碳钢管道输送98%浓硫酸,原来的流速为0.6m/s,输送时间需1小时。
为了缩短输送时间,安装了一台大马力的泵,流速增加到1.52m/s,输送时间只需要15分钟。
但管道在不到一周时间内就破坏了。
Eg:对于接触流体的设备来首,流速是一个重要的环境因素,但流速对金属材料腐蚀速度的影响是复杂。
当金属的耐腐蚀性是依靠表面膜的保护作用时,如果流速超过了某一个临界值的时候,由于表面膜被破坏就会使腐蚀速度迅速增大。
这种局部腐蚀称为磨损腐蚀。
是介质的腐蚀和流体的冲刷的联合作用造成的破坏。
流体冲刷使表面膜破坏,露出新鲜金属表面在介质腐蚀作用下发生溶解,形成蚀坑。
蚀坑形成识液流更急急乱,湍流又将新生的表面膜破坏。
这样子使设备更快穿孔。
///在选择流速时面临两个方面的因素。
一方面,流速较低则管道直径就要较大,(对一定的流量),设备费用增加。
另一方面,流速较高,管道腐蚀速度增大,使用寿命缩短,甚至可能造成更大的事故。
这样需要考虑金属材料的临界流速,进行适当的选择。
同时,在设计管道系统的工作中,应尽量避免流动方向突然变化,流动截面积突然变化,减小对流动的阻碍,以避免形成湍流和涡旋。
事例1…某化工厂生产氯化钾的车间,一台SS-800型三足式离心机转鼓突然发生断裂,转鼓材质为1Cr18Ni9Ti。
经鉴定为应力腐蚀破裂。
Eg:在氯化钾生产中选用1cr18Ni9Ti这种奥氏体不锈钢转鼓是不当的。
氯化钾溶液是通过离心机转鼓过滤的。
氯化钾浓度为28be,氯离子含量远远超过了发生应力腐蚀破裂所需的临界氯离子的浓度,溶液ph值在中性范围内。
加之设备间断运行,溶液与空气的氧气能充分接触。
这就是奥氏体不锈钢发生应力腐蚀破裂提供特定的氯化物的环境。
/// 保护,如停用期间使之完全浸与水中,与空气隔离;定期冲洗去掉表面氯化物等,尽量减轻发生应力破裂的环境条件,以延长使用寿命,不过,发生这种转鼓断裂飞出的恶性事故可能有一定的偶然性,但这种普通的奥氏体不锈钢用于这种高浓度氯化物环境,即使不发生这种恶性事故,其寿命也不长,因为除应力腐蚀还有,孔蚀,缝隙腐蚀等。
实例1:北方一条公路下蒸气冷凝回流管原用碳钢制造,由于冷凝液的腐蚀发生破坏,便用304型不锈钢(00Cr18Ni9)管更换。
使用不到两年出现泄漏,检查管道外表面发生穿晶型应力腐蚀破裂。
Eg:在北方冬季公路上撒盐作防冻剂,盐渗入土壤使公路两侧的土壤中氯化钠的含量大大提高,而选材者却不了解没有对土壤腐蚀做过分析。
就决定更换不锈钢管。
将奥氏体不锈钢用在这种含有很多氯化钠的潮湿土壤中,不锈钢肯定表现不佳,也需还不如碳钢呢。
实例二:高压聚乙烯车间反应器R-4240及产品冷却器E-4219,在运行过程中出现多处夹套水泄漏现象,2004年10月出现多处夹套水泄漏现象后,停车对夹套泄漏点周边1米范围进行了超探检查,发现夹套进口处内侧的夹套壁厚由δ8mm减小到δ3mm左右,夹套其他位置的壁厚减小至δ7.3mm左右(见图A中夹套泄漏点)。
提示:由于入水处死角内的水过热造成了局部汽化,引起汽蚀冲刷减薄第六章:事例一:某公司选用不锈钢管作地下输油管道。
安装后大约一年准备投入使用,油从一端泵入,在另一端却未见油出现。
检查发现管道上因腐蚀形成了许多小孔,油全部漏掉了。
又发现该管道附近有一条碳钢管道实施了阴极保护,认为不锈钢是耐蚀材料,并没有将不锈钢连接到阴极保护系统。
Eg:对埋地管道和其他设施,效果最好的防护技术是涂层加阴极保护。
对于大面积的设备来说,如果表面没有涂层(裸金属),需要的电流还是很大。
另一方面,被保护设备表面的电流分布是不均匀的(电流分布均匀性称为分散力),对于长的管道,一个阳极站保护的管道长度比较短,使阳极站的设计很复杂。
///阳极保护电机从埋地阳极通过土壤流向被保护的管道。
当附近有其他管道时,电流可能从一个部位流出。
电流流出的部位成为阳极区,使该处管道遭到腐蚀。
即使是不锈钢也一样会发生杂散电流腐蚀。
///为了避免阴极保护造成的杂散电流腐蚀,可采如下方法:a最好的方法在设计将附近的管道和设施都纳入阴极保护系统,一道进行保护。
b提高管道相交段的表面绝缘等级,或涂覆新的绝缘层,以避免杂散电流流入。
涂覆长度一般10m左右。
c在多管道地区,最好采用多个阳极站,每个站的保护电流较小,阳极站离被保护管道较近,以缩小保护电流范围。
D在地下设施密集的城市地区,可采用深井埋置阳极(井深15m以上),阳极在井中垂直方向安装。
事例二:海边一座混凝土石油装运码头,混凝土台面支撑在钢管上。
钢管表面涂漆并加阴极保护。
电源负极连在钢筋上。
阳极是镀铂钛悬挂在海水中。
在石油装卸过程中,码头受到周期性机械应力,引起混凝土某些物理破坏。
使用12年后发现,平台的混凝土台面出现严重胀裂,钢筋暴露出来。
Eg:在阴极保护实施中电连接十分重要,被保护设备和电影负极用导线连通,被保护设备和电极负极用导线连通,导线直径要和保护电流相匹配,以减小线路电压降;导线与设备要连接牢固,电接触良好,不存在大的电阻,特别要防止在使用过程中短线,使保护失效。
///施工时将导线接到混凝土钢筋上而不是支撑钢管上,可能是图方便。
因为钢筋与平台支撑钢管是导通的,所以开始不会出现问题。
但随着码头的运行,混凝土平台发生某些物理破坏。
钢筋之间的电连接减弱甚至中断。
某些钢筋脱离了阴极保护系统,电流不能通过电路排出,就会发生杂散电流腐蚀。
腐蚀产物体积一般大于被腐蚀金属,腐蚀产物膨胀产生很大应力。
腐蚀严重时,混凝土覆层被胀裂。
///对混凝土中的钢筋也可以采用阴极保护,为了保证电路通畅,避免某些钢筋因脱离而受到杂散电流腐蚀,钢筋绑扎后还需焊接。