钢的强韧化处理机制
钢的强韧化处理机制

钢的强韧化处理机制王立洲(辽宁工程技术大学材料科学与工程学院阜新123000)本文根据钢的淬火组织特点,归纳了提高钢强韧性的途径,介绍了一些强韧化处理工艺。
随着工业的发展,各种机械对钢铁材料的机械性能要求逐渐增高。
材料及热处理工艺的研究得到迅速的发展。
其中,利用现有材料,通过调整一般的热处理方法,在同时改善钢的强度和韧性指标方面的工作取得了显著的进步。
它对充分发挥材料的性能潜力有着重要的意义。
这些工艺方法通称为强韧化处理,是热处理发展的一个值得注意的方向。
强韧化处理的发展是建立在我们对钢中各种组织的特点,形成条件,机械性能,以及在外力作用下的破断过程的认识不断深入的基础之上的。
透射电子显微镜技术的应用,使我们对各种组织超显微精细结构的认识跨进了一大步,开始有可能比较深入地研究组织和机械性能的关系。
另一方面,从材料断裂过程的研究中知道,在各种应力作用下,材料的破断是通过微裂纹的形成及扩展的方式进行的。
钢铁材料的各种组织形态在各种应力状态下,抵抗微裂纹的形成和扩展的能力是不同的,因此表现出不同的性能指标。
但是无论哪一种组织,只要它形成微裂纹的倾向比较小,或者微裂纹一旦形成后,在这类组织中扩张时消耗的功愈大,它就会有较高的强韧性。
这样,我们就有可能采用适当的热处理工艺方法和调整工艺参数,能动地控制钢的组织,充分利用对钢强韧化有利的因素,排除不利的因素,更充分地发挥材料的强度和韧性的潜力。
目前发展的强韧化处理工艺有多种多样,归结起来,它们大多通过一种或几种途径达到强韧化效果的。
(1)充分利用位错型马氏体和下贝氏体组织形态,尽量减少或避免片状孪品马氏体的出现。
(2)细化钢的奥氏体晶粒和细化过剩碳化物。
(3)获得马氏体与具有良好塑性的第二相的复合组织。
(4)形变热处理。
下面将简要介绍这些强化处理的机理。
一位错型马氏体的扩大应用很久以来就知道,在保证淬、回火零件强度指标的前提下,选用含碳量较低的钢,能够使零件热处理后获得较高的韧性。
Cr12MoV钢制模具的强韧化处理

摘要:Cr12MoV钢制模具经高温调质、等温淬火等主要工序后,得到下贝氏体、回火马氏体和少量残余奥氏体的复合组织,可获得良好强度和韧性的匹配,其强韧性明显高于常规的热处理方法。
应用于我公司使用的两种模具,其耐用度明显提高。
前言:Cr12MoV钢经热处理后具有高的硬度、强度、耐磨性和良好的淬透性能而被广泛应用于冷作模具。
我们自制的滚丝模具(见图1)和异形冲子(见图2)两种模具使用材料均为Cr12MoV钢。
用常规热处理方法处理后,滚丝模具在使用过程中齿部崩齿而报废,每副模具平均加工零件约1560件。
异形冲子在加工零件500件时,尖角部位出现脆性掉块现象,虽经几次修磨后平均加工零件仅为3000件左右。
这无疑严重影响了每月几十万件零件的生产数量和进度。
因此,解决和提高两种模具耐用度是摆在我们面前的一项研究课题。
1 模具的服役条件和失效分析1.1服役条件滚丝模具是在滚丝机床上加工冷态35钢零件的外螺纹,零件螺纹精度达6级,加工零件外螺纹时由于挤压变形量较大,要求该模具具有较高的抗变形能力、耐磨性和韧性。
异形冲子是在100T冲床上挤压退火态的硬铝零件成型,零件塑性变形量较大,并且零件成型后不再进行后序的机械加工,要求模具工作部位尺寸一致性好,应具有较高的耐压强度、耐磨性和韧性。
1.2失效形式及分析我们对已报废的两种模具逐一进行硬度检测,均为60~62HRC,符合图纸要求,抽样切块经金相检查组织为回火马氏体+少量残留奥氏体+碳化物,碳化物偏析级别为3.5~4.5级不等。
两种模具除少量滚丝模具由于产生磨削裂纹时在使用时又沿原裂纹扩展而报废外,其余模具失效形式的共同特点均为脆性崩齿或掉块,未发现因强度和硬度不足产生的工作部位挤压变形或磨损。
将两种模具硬度降至58~60HRC时,脆性崩齿或掉块现象没有改善,由此可看出:模具工作部位脆性大、韧性不足是造成模具耐用度低的主要原因,保证模具良好强度和韧性的匹配是提高模具耐用度的主要措施。
金属材料强韧化机理及超高强钢开发

一、概述金属材料一直以来都是工程领域中广泛应用的材料之一,其强韧性一直是研究的热点之一。
随着科学技术的不断发展,人们对金属材料强韧化机理及超高强钢的研究也越发深入。
本文将从金属材料强韧化的概念和机理入手,探讨目前超高强钢的开发及应用情况,并对未来的发展方向进行展望。
二、金属材料强韧化的概念及机理1. 强韧化的概念强韧化是指在不同的外力作用下,材料能够保持其在应力下的强度和韧性。
强韧化材料具有抗拉伸、抗弯曲和抗扭转等性能较强的特点。
强韧化的目的是提高材料的使用安全系数,延长材料的使用寿命。
2. 强韧化的机理强韧化的机理包括晶界强化、位错强化和析出强化等。
晶界强化是指通过控制晶界的特性来增强材料的强韧性;位错强化是通过引入位错来增强材料的韧性;析出强化是指通过固溶体中析出出特定的固溶体来增强材料的性能。
三、超高强钢的开发及应用1. 超高强钢的研究历程超高强钢的研究始于二十世纪六十年代,经过多年的发展,目前已经取得了一系列重要的突破。
超高强钢具有高强度、高韧性和良好的冷成型性能,广泛应用于汽车、桥梁和建筑等领域。
2. 超高强钢的应用情况目前,超高强钢在汽车轻量化领域的应用较为广泛,能够显著提高汽车的安全性能和燃油利用率。
超高强钢还被应用于船舶制造、航空航天和军工等领域,取得了良好的效果。
四、未来发展方向展望1. 现代材料加工技术的发展随着现代材料加工技术的不断进步,越来越多的新型金属材料被开发出来。
未来,随着3D打印、激光焊接等新技术的应用,超高强钢的研究和生产将更加多样化和精细化。
2. 新材料的研究与应用未来,人们将更加注重绿色环保型材料的研究与开发,以满足社会可持续发展的需求。
对于高温、高压等复杂工况下的材料需求也将逐渐增加,超高强钢在这些领域的研究与应用将会成为重点。
3. 国际合作与交流未来,随着国际合作与交流的深入,超高强钢的研究与应用将会更加国际化。
通过与国际先进技术的合作,可以更好地借鉴和吸收先进的技术和经验,推动超高强钢的发展。
40Cr钢亚温淬火强韧化机理的试验研究
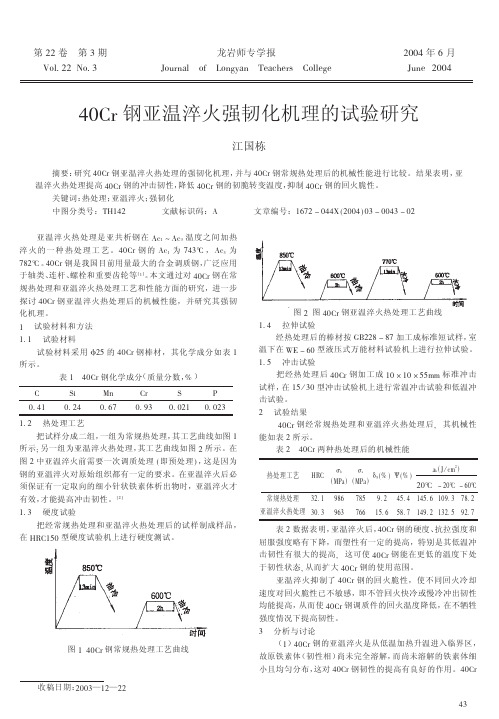
然保持较高的强度和硬度(强度和硬度只是略有下降)。
( )钢的回火脆性是由于钢中 等有害杂质元素在奥氏
体晶界偏聚的结果。 是缩小奥氏体区元素,又有稳定铁素体
的作用,因此 应优先存在于铁素体中。故当亚温淬火组织
中存在着一定数量细小分散的铁素体时, 等有害杂质元素
主要集中在铁素体晶粒内,必然减少杂质在奥氏体晶界上的
把经常规热处理和亚温淬火热处理后的试样制成样品,
在
型硬度试验机上进行硬度测试。
图
钢常规热处理工艺曲线
收稿日期: — —
图 图 钢亚温淬火热处理工艺曲线
拉伸试验
经热处理后的棒材按
加工成标准短试样,室
温下在
型液压式万能材料试验机上进行拉伸试验。
冲击试验
把经热处理后
钢加工成
标准冲击
试样,在
型冲击试验机上进行常温冲击试验和低温冲
综合上面的分析,在
型行星齿轮传动中,太阳轮和
行星轮均采用
钢,其齿面渗碳淬火,小轮为
,大轮为
,心部硬度>
,内轮采
用 ,调质处理
。
制造。
!
钢淬透性低,经渗碳、淬火与低温回火后,心部
强度较低,强度与韧性配合较差。这种钢只可作受力不太大,
不需要高强度的耐磨零件,若性能要求较高时,这种钢在渗
碳后经常采用 次淬火方法。
钢亚温处理后的金相组织为少量游离铁素体 回火索化体
弥散分布的细小残余奥氏体。由于残余奥氏体的存在使裂
纹的扩展变得困难(因受塑性变形或产生部分马氏体转变使
应力 松驰 ), 使钢 的脆 性 降低 ,韧 脆 转变 温度 下 降了 接近
。
( )亚温淬火加热温度较低,在两相区加热时晶粒长大
1.2 第1章_钢合金化概论-钢的强化和韧化
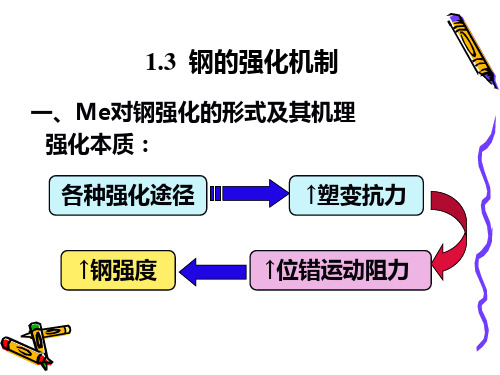
2、影响塑性的因素
溶质 原子
↓ 韧性,间隙溶质原子 > 置换溶质原子。
晶粒 度
第二 相 杂质
细晶既↑σS,又 ↑ 韧性 → 最佳组织因素。
K↓韧性。K 小、匀、圆、适量 → 工艺努力方向。
杂质往往是形变断裂的孔洞形成核心, → 提高钢的冶金质量是必须的。
3、改善钢韧性的途径
1.改善延性断裂的途径 2.改善解理断裂抗力的途 径 3.改善沿晶断裂抗力的途径
锰对钢γ区的影响
铬对钢γ区的影响
3、对γ-Fe区的影响
A形成元素Ni、Mn等使γ-Fe区扩大→钢在室 温下也为A体 — A钢; F形成元素Cr、Si等使γ-Fe区缩小→钢在高 温下仍为F体 — 铁素体钢。
二、 合金钢的加热A化
α+ Fe3C (或 K) →
γ
α→γ: 需要Fe重组和 C扩散
Fe3C或K:需要溶解于γ
s 0 Ks d
著名的Hall-petch公式 式中,d为晶粒直径,Ks为系数
1/ 2
机理
晶粒越细 → 晶界、亚晶界越多→ 有效 阻止位错运动,产生位错塞积强化。
效果
↑钢的强度,又↑塑性和韧度 这是最理想的强化途径.
3、第二相强化
表达式
P K P
1
机理
微粒第二相钉扎位错运动→强化效果 主要有切割机制和绕过机制。在钢中主 要是绕过机制。 两种情况:回火时弥散沉淀析出强化, 淬火时残留第二相强化。 有效提高强度,但稍降低塑韧性。
效果
提高强度,降低塑韧性
固溶强化的规律
( 1)溶质元素在溶剂中的饱和溶解度愈小,其固溶 强化效果愈好。
置换元素对α-Fe屈服强度的影响
固溶强化的规律
钢的强韧化机理及在热轧板带钢生产中的应用

钢的强韧化机理及其在热轧板带钢生产中的应用郭雅楠2013.7.05目录目录 (I)1.钢的强韧化机理 (1)1.1 钢的强化机制 (1)1.1.1固溶强化 (2)1.1.2形变强化 (2)1.1.3 沉淀强化与弥散强化 (2)1.1.4 细晶强化 (2)1.1.5 亚晶强化 (3)1.1.6 相变强化 (3)1.2 材料的韧性 (3)1.2.1韧性的定义及表示 (3)1.2.2钢的韧化方法 (4)2.控制轧制和控制冷却技术 (6)2.1控制轧制 (6)2.1.1控轧轧制定义 (6)2.1.2控制轧制工艺 (6)2.1.3控制轧制特点 (6)2.2控制冷却 (7)3.钢的强韧化在热轧板带钢生产中的应用 (7)3.1热轧带钢用途分类 (7)3.2热轧带钢工艺流程 (8)3.3再结晶控制轧制 (10)3.4单相强制对流换热形式的冷却技术 (11)3.5加速冷却 (11)3.6生产实例—水电站用高强压力钢管用钢 (12)3.7生产实例—含铌微合金化热轧多相钢的控轧控冷工艺 (13)3.8小结 (13)4.结论 (14)参考文献 (14)1.钢的强韧化机理材料通常通过各种指标来确定它的加工性能和使用性能,对于钢材来说,力学性能是其最基本、最重要的,其中强度性能居首位。
同样,我们不能忽视韧性性能,这方面的指标和强度性能指标息息相关,研究某材料的力学性能的时候通常将二者一同考虑。
结构钢材的最新发展方向就是要求材料的强度、韧性等方面有较好的结合,控轧控冷工艺满足这一要求。
下面给出几个定义。
1.强度强度是工程结构用钢的最基本的要求。
强度是指材料对塑性变形和断裂的抗力,用给定条件下所能承受的应力来表示。
2.强度指标屈服强度σs和抗拉强度σb是强度的主要指标。
还包括抗压强度、抗剪强度、疲劳强度、蠕变强度。
3.强化通过合金化、塑性变形和热处理等手段提高金属强度的方法称为金属的强化。
4.韧性韧性是材料塑性变形和断裂全过程中吸收能量的能力。
强韧化热处理工艺
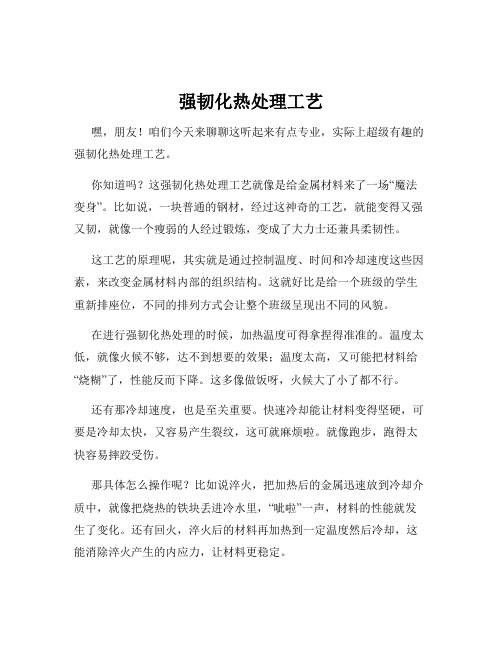
强韧化热处理工艺嘿,朋友!咱们今天来聊聊这听起来有点专业,实际上超级有趣的强韧化热处理工艺。
你知道吗?这强韧化热处理工艺就像是给金属材料来了一场“魔法变身”。
比如说,一块普通的钢材,经过这神奇的工艺,就能变得又强又韧,就像一个瘦弱的人经过锻炼,变成了大力士还兼具柔韧性。
这工艺的原理呢,其实就是通过控制温度、时间和冷却速度这些因素,来改变金属材料内部的组织结构。
这就好比是给一个班级的学生重新排座位,不同的排列方式会让整个班级呈现出不同的风貌。
在进行强韧化热处理的时候,加热温度可得拿捏得准准的。
温度太低,就像火候不够,达不到想要的效果;温度太高,又可能把材料给“烧糊”了,性能反而下降。
这多像做饭呀,火候大了小了都不行。
还有那冷却速度,也是至关重要。
快速冷却能让材料变得坚硬,可要是冷却太快,又容易产生裂纹,这可就麻烦啦。
就像跑步,跑得太快容易摔跤受伤。
那具体怎么操作呢?比如说淬火,把加热后的金属迅速放到冷却介质中,就像把烧热的铁块丢进冷水里,“呲啦”一声,材料的性能就发生了变化。
还有回火,淬火后的材料再加热到一定温度然后冷却,这能消除淬火产生的内应力,让材料更稳定。
这强韧化热处理工艺在工业生产中的应用那可广泛了。
汽车的零部件,要是没有经过这样的处理,怎么能承受住复杂的路况和高强度的使用?飞机的发动机零件,不经过这工艺,怎么能在高温高压的环境下稳定工作?而且呀,这工艺还在不断发展和改进。
科研人员们就像一群勤劳的小蜜蜂,不断探索新的方法和技术,让这工艺越来越厉害。
所以说,强韧化热处理工艺可不是什么遥不可及的高深学问,它就在我们的生活中,为我们制造出更优质、更可靠的产品。
你说,这是不是很神奇?总之,强韧化热处理工艺是个了不起的技术,它让金属材料焕发新生,为我们的现代生活提供了坚实的支撑。
含铌微合金钢强韧化机理

摘要 :对含 N b 微合金钢 14M n N b q 钢板进行了模拟控轧控冷试验 。
利用光学显微镜 、透射电子显微镜 、力学 性能试验等手段 ,对试验结果进行了分析和研究 。
证明该钢具有较好的强韧化综合性能 ,能满足大型桥梁用 钢的技术要求 ,并指出了细晶强化是 14M n N b q 钢的主要强韧化机制 。
关键词 :14M n N b q 钢 ;铌 ;细晶强化 ;沉淀强化中图分类号 :TF 841 . 6 ; TG 142141 文献标识码 :A 文章编号 :025426051( 2003) 0520015203Strengthen ing an d T oughen ing Mec han ism of Nb Microall o yed SteelXU E Chun 2f a ng 1 ,WAN G Xin 2hua 1 , X IN Y i 2de 2(11Depart ment of Mechanical Engineering ,A r m o r ed Fo r ce Engineering Instit u te ,Beijing 100072 ,China ;21Depart ment of Materials Science and Engineering ,Cho n gqing U n iversit y ,Cho n gqing 400044 ,China ) Abstract :A simulated co n t r olled rolling and cooling fo r steel 14M n N b q was carried o u t in t h is paper . The role of t he microall oyed element N b and it s carbo n it ride N b ( CN ) in t he p rocess of defo r mat i o n and t heir effect s o n mi 2 cro st ruct ures and mechanical p roperties of 14M nN bq steel was analyzed by means of op t ical micro scope , T E M and mechanical p ropert y tester . The result s show t hat t he 14M nN bq steel po ssesses high st rengt h and to u ghness and can meet t he technical require ment s of heavy bridge steel . Also it is pointed o ut t hat t he fine 2grain st rengt hening is t h e p r ima ry mechanism of st r engt h ening and to u ghening of 14M n N b q steel .K ey w ords :14M n N b q steel ; n i o b ium ;f ine 2grain st r engt h ening ;p r ecipitati o n st r engt h ening14M n N b q 钢是一种新型微合金化桥梁钢 ,是为满足国内制造大跨度桥梁用钢的需要而研制的 。
第1章钢合金化概论钢的强化和韧化课件

Si能溶于ε ,不溶于Fe3C ,Si要从ε 中出去
↓ε-FeXC的形核、长大
↓ε→ Fe3C 效果: 含2% Si能使M分解温度从260℃提高到350℃以上
(2)对残余A转变的影响
(3)回火时K的形成
各元素明显开始扩散的温度为:
Me
Si
Mn
Cr
(2) Me对A晶粒长大倾向的影响
➢合金元素形成的碳化物在高温下越稳定,
越不易溶入A中,能阻碍晶界长大,显著细 化晶粒。 按照对晶粒长大作用的影响,合 金元素可分为:
①Ti 、V 、Zr 、Nb等强烈阻止A晶粒长大,
Al在钢中易形成高熔点AlN 也能强烈阻止晶粒长大;
、Al2O3细质点,
AlN含量对A晶粒度的影响
第二 相
K ↓韧性。 K 小、匀、圆、适量 → 工艺努力方向。
杂质
杂质往往是形变断裂的孔洞形成核心, → 提高钢的冶金质量是必须的。
3、改善钢韧性的途径
1.改善延性断裂的途径 2.改善解理断裂抗力的途 3.改径善沿晶断裂抗力的途径
4、提高钢韧度的合金化途径
1)细化晶粒、组织—— 如Ti 、V 、Mo; 2) ↑回火稳定性 —— 如强K形成元素 ; 3)改善基体韧度 —— Ni ; 4) 细化K —— 适量Cr 、V ,使K小而匀 ; 5) ↓回脆 —— W 、Mo ; 6)在保证强度水平下,适当↓含C量.
效果
有效提高强度,但稍降低塑韧性。
钢强度表达式
位错被质点障碍物所挡住
4、位错强化
表达式
机理
位错密度ρt →tt位错交割、缠结, → 有效地阻止了位错运动 → t钢强度。
效果
金属材料的强韧化机制与应用

金属材料的强韧化机制与应用对结构材料来说,最重要的性能指标是强度和韧性。
强度是指材料抵抗变形和断裂的能力,强度可分为抗拉强度、抗压强度、抗弯强度、抗剪强度等,各种强度间常有一定的联系,使用中一般较多以抗拉强度作为最基本的强度指标;韧性指材料变形和断裂过程中吸收能量的能力。
以下介绍金属材料的主要强韧化机制。
一、金属材料的强化金属材料强化的类型主要有固溶强化、细晶强化(晶界强化)、第二相粒子强化和相变强化。
(一)固溶强化固溶强化是利用金属材料内部点缺陷(间隙原子和置换原子)对位错运动的阻力使得金属基体(溶剂金属)获得强化的一种方法。
它分为两类:间隙式固溶强化和置换式固溶强化。
1. 间隙式固溶强化:原子直径很小的元素如C、N、O、B 等,作为溶质元素溶入溶剂金属时,形成间隙式固溶体。
C、N等间隙原子在基体中与“位错”产生弹性交互作用,当进入刃型位错附近并沿位错线呈统计分布,形成“柯氏气团”。
当在螺型位错应力场作用下,C、N原子在位错线附近有规则排列就形成“S nock”气团。
这些在位错附近形成的“气团”对位错的移动起阻碍和钉扎作用,对金属基体产生强化效应。
2. 置换式固溶强化:置换式溶质原子在基体晶格中造成的畸变大都是球面对称的,固溶效能比间隙式原子小(约小两个数量级),这种强化效应称为软硬化。
形成置换式固溶体时,溶质原子在溶剂晶格中的溶解度同溶质与溶剂的原子尺寸、电化学性质等因素密切相关,当原子尺寸愈接近,周期表中位置愈相近,其电化学性质也愈接近,则溶解度也愈大。
由于溶质原子置换了溶剂晶格结点上的原子,当原子直径存在差别就会破坏溶剂晶格结点上原子引力平衡,而使其偏离原平衡位置,从而造成晶格畸变,随原子直径差别增加,造成的畸变程度愈大,由此造成的强化效果更大。
(二)细晶强化晶界分为大角度晶界(位向差大于10o)和小角度晶界(亚晶界,位向差1~2o)。
晶界两边相邻晶粒的位向和亚晶块的原子排列位向存在位向差,处于原子排列不规则的畸变状态。
4。钢的强韧化机理

2.气团效应 溶质原子聚集在位错线附近, 溶质原子聚集在位错线附近,形成气 团,对位错起钉扎作用。 对位错起钉扎作用。 刃型位错 螺型位错 Cottrell气团 气团 Snock气团 气团 2 3
置换固溶体中的晶格畸变
1
1
3.电交互作用 位错附近存在畸变区, 位错附近存在畸变区,电子云分布不均匀 受张区: 受张区:电子云密度高 受压区: 受压区:电子云密度低 形成了局部的电偶极 溶质与基体的价电子相差越大, 溶质与基体的价电子相差越大,固溶强化作 用越大
三.晶界强化和塑性、韧性的关系 晶界强化和塑性、 晶界阻碍位错运动——σy↑ 晶界阻碍位错运动 细晶粒使变形均匀——塑性 细晶粒使变形均匀 塑性↑ 塑性 晶界阻碍裂纹扩展——韧性 韧性↑ 晶界阻碍裂纹扩展 韧性 裂纹扩展的临界应力 σc = 2µSp·d-1/2/Ky σc ∝ d-1/2 d——晶粒直径 晶粒直径 d↓, σc ↑,塑性、韧性↑ , ,塑性、韧性
应力集中与位错塞积数目成正比 塞积群大→应力集中大 塞积群大 应力集中大 粗晶粒, 大 塞积距离长,应力集中↑, 粗晶粒,d大,塞积距离长,应力集中 ,所 需外力↓,就可达到 需外力 ,就可达到τc 细晶粒,d小,塞积距离短,应力集中 ,所 细晶粒, 小 塞积距离短,应力集中↓, 需外力↑,才可达到 需外力 ,才可达到τc ,使邻晶粒开动
机理) 1.绕过机理(Orowan机理) 绕过机理( 机理 第二相质点与基体非共格, 第二相质点与基体非共格,质点较硬 第二相质点间距) △σp=K·G·b/λ (λ :第二相质点间距 质点增多, ,强化↑ 质点增多, λ ↓,强化
2.切过机理 质点较细小, 质点较细小,与基体保持共格关系
~ △σp=K·f1/3~1/2·d’1/2
q235钢的强韧化热处理工艺

q235钢的强韧化热处理工艺一. 概述:钢材是一种常用的工业材料,广泛应用于船舶、铁路、房屋、桥梁、机械等领域。
而 q235 钢是一种常用的结构钢材,广泛应用于建筑、桥梁、机械等领域。
正是因为 q235 钢在工业生产中起到重要的作用,所以对于其性能的研究也愈发得到关注。
二. q235 钢的强韧化热处理工艺:1. 强韧化热处理的定义:钢材作为一种重要的结构材料,强韧性是其最基本的性能之一。
在日常使用过程中,若钢材缺乏强韧性,容易出现断裂、变形等问题。
因此,为了保证钢材具有较好的强韧性,常常需要进行强韧化处理。
强韧化处理是指通过改变钢材的化学成分和热处理工艺,提高钢材的强度、塑性和韧性的处理方法。
2. q235 钢的性能:q235 钢是一种中碳钢,具有一定的强度和塑性。
但其韧性较差,易出现断裂现象。
3. q235 钢强韧化热处理工艺:(1) 碳氮共渗:通过碳氮共渗来提高钢材的表面硬度,改善其磨损性能和疲劳寿命,并适当提高其韧性。
碳氮共渗的过程分为三个阶段:氮化、碳化和回火。
氮化阶段:在钢材表面进行气体氮化,形成硬度较高的氮化物层。
碳化阶段:在氮化物层上进行碳化处理,形成类似固体溶解物的结构。
回火阶段:通过回火来改变钢材的强度和韧性。
此种方法能够提高钢材的强度、硬度和韧性,其强韧化效果较好。
(2) 淬火和回火:将 q235 钢材加热至淬硬状态,随后迅速冷却来提高钢材的硬度和强度,然后进行回火处理,改变其韧性。
淬火处理会增加钢材的强度和硬度,但同时也会降低其韧性。
通过回火处理来平衡硬度和韧性。
(3) 微合金化:通过加入微量的钒、铌、钛等元素,提高钢材的韧性和强度。
微合金化的方法可以在不降低钢材的强度和硬度的情况下,提高钢材的韧性。
同时也可以改善钢材的加工性。
4. 结论:q235 钢在工业应用中具有重要的作用,其韧性是其最基本性能之一。
通过强韧化热处理工艺来提高其强度、硬度和韧性,对于提高钢材的整体性能起到重要作用。
金属材料的强韧化机理与实践
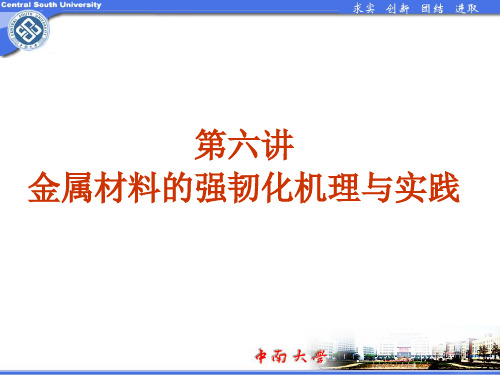
• 钨钼的低温再结晶脆性: 在高温下使用的钨钼回到室温附近时表
现严重的脆性,加工过程及使用过程中产生 各种形式的脆性破裂。
产生原因: 本征脆性 间隙杂质在晶界上偏聚
• 钨钼的强韧化途径:
钨合金 抗震钨 稀土钨
纯净化 合金化
钼合金 掺杂钼 稀土钼
三、铝合金的强韧化
• 细晶强化 • 热处理强化 • 第二相粒子强化
细晶强化
• 变质处理
目的: 减少枝晶距及元素偏析,细化晶粒 变质剂: B、Ti、Zr, RE(La,Ce,Pr,Nd,Sc,Er)
微量Sc和Zr添加到Al-Mg-Mn合金中,因显著细化合金的铸态晶拉, 热轧 态合金的拉伸强度和屈服强度分别提高了75~90 MPa和90~94 MPa,而延 伸率仍保持在11%~12%
固溶强化
固溶强化:C原子在面心立方晶格中造成的 畸变呈球面对称,所以C在A中的间隙强化作用属于 弱硬化。置换原子在A中的强化作用比C原子更小。
固溶强化是钢铁材料主要强化手段之一,其 基本内容可归纳为两点:
①间隙式固溶强化对F基体(包括M)的强化效能最大,但对 韧性、塑性的削弱也很显著;
②置换式固溶强化对F强化作用虽然比较小,却不削弱基 体的塑性和韧性。
如果奥氏体晶粒细化在十级以上,则金属 的强韧性将大大提高,为达此目的,现代发展的热 处理新技术方法有以下三种。
①利用极高加热速度的能量密度进行快速加热的热处理
由于极高的加热能量密度,使加热速度大大提 高,在10-2~1s的时间内,钢件便可加热到奥氏体(A)状 态,此时A的起始晶粒度很小,继之以自冷淬火(冷速达 104℃/s以上),可得极细的马氏体(M)组织,与一般高频 淬 火 比 较 硬 度 可 高 出 Hv50 , 而 变 形 只 有 高 频 淬 火 的 1/4~1/5,寿命可提高1.2~4倍。
材料强韧化处理第一部分
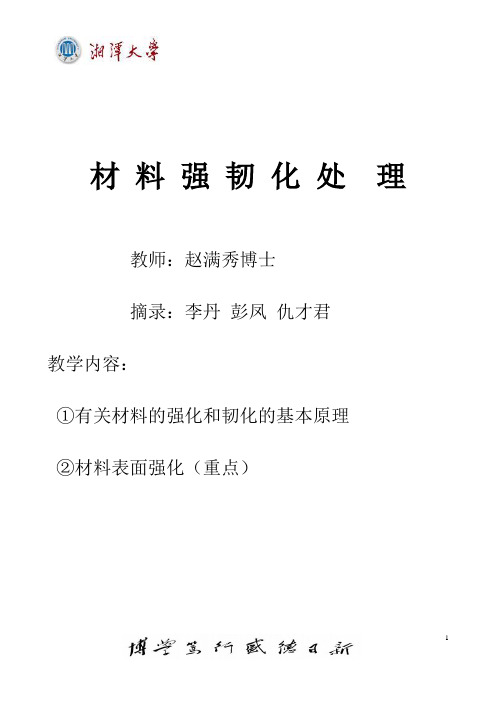
材料强韧化处理教师:赵满秀博士摘录:李丹彭凤仇才君教学内容:①有关材料的强化和韧化的基本原理②材料表面强化(重点)目录第一部分材料的强化和韧化的基本原理第一章材料的强韧化基本原理一、金属材料强韧化的意义①通过强化处理可以优化材料的力学性能指标,充分挖掘材料的潜力。
②工作表面通过表面强化处理,增加耐磨性、耐蚀性、疲劳强度,提高工件使用寿命。
综上所述,材料的强韧化处理就是在保证材料的强化的同时,尽量提高材料的韧性。
二、实现钢铁材料强韧性的两个阶段1、液态阶段(炼钢者研究的重点)方法:细化晶粒、纯洁钢材、合金化(1)、细化晶粒方法:①快速冷却(增大过冷度);②加变质剂:减少表面能,提高形核率;抑制晶粒长大;③震动搅动:机械形核;④合金化(用Al、Nb、Ti脱氧):氧化物熔点高,成为非均匀形核的核心,增加形核率。
Al脱氧的原因:Al与氧的结合力强,生成高熔点的氧化物,成为非均匀形核的核心,提高形核率,细化晶粒。
钢铁冶炼的最后阶段:①脱氧:加Al、Mg、Si与O结合,细化晶粒;②合金化。
(2)纯洁钢材:如模具、刀具(含C 量高、耐磨、高纯净) 方法:去除有害元素S 、P 、O 、H ;去除氧化物、氯化物、硅酸盐;去除有害气体。
2、固态阶段对于固体材料为提高材料的强韧化,常采用常规热处理或者形变两大方法,也可以通过表面强化提高表面强度。
(1)、常规热处理方法:正火、退火、回火、淬火(时效强化、固溶强化、细晶强化、第二相粒子强化)(2)冷变形强化机理:塑性变形使位错密度增加,位错运动受阻。
(3)热加工强化的原因:能焊合某些缺陷、破碎粗大组织、形成纤维组织。
常规热处理与形变工艺如下所示:⎪⎪⎪⎪⎪⎪⎪⎩⎪⎪⎪⎪⎪⎪⎪⎨⎧⎪⎪⎪⎪⎩⎪⎪⎪⎪⎨⎧⎪⎩⎪⎨⎧⎪⎩⎪⎨⎧⎪⎪⎩⎪⎪⎨⎧热挤压热轧热锻热加工挤压滚压喷丸冷变形形变淬火回火退火正火常规热处理诱发M 相变,产生孪晶,提高硬度三、强化的两个途径1、晶体的理论强度和实际强度①理论强度:按完整晶体刚性滑移模型计算出的强度 ②实际强度:实验测得的单晶体临界分切应力 2、材料强度和位错密度的关系须晶:接近完整晶体的须状晶体 强化的两个基本途径:①尽可能减少晶体中的位错密度,使其接近完整晶体或者制成无缺陷的完整晶体,是金属的实际强度接近理论强度。
钢的强韧性
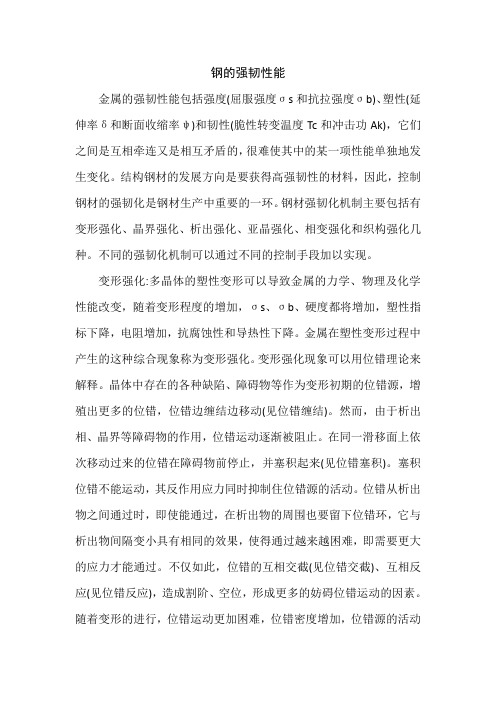
钢的强韧性能
金属的强韧性能包括强度(屈服强度σs和抗拉强度σb)、塑性(延伸率δ和断面收缩率ψ)和韧性(脆性转变温度Tc和冲击功Ak),它们之间是互相牵连又是相互矛盾的,很难使其中的某一项性能单独地发生变化。
结构钢材的发展方向是要获得高强韧性的材料,因此,控制钢材的强韧化是钢材生产中重要的一环。
钢材强韧化机制主要包括有变形强化、晶界强化、析出强化、亚晶强化、相变强化和织构强化几种。
不同的强韧化机制可以通过不同的控制手段加以实现。
变形强化:多晶体的塑性变形可以导致金属的力学、物理及化学性能改变,随着变形程度的增加,σs、σb、硬度都将增加,塑性指标下降,电阻增加,抗腐蚀性和导热性下降。
金属在塑性变形过程中产生的这种综合现象称为变形强化。
变形强化现象可以用位错理论来解释。
晶体中存在的各种缺陷、障碍物等作为变形初期的位错源,增殖出更多的位错,位错边缠结边移动(见位错缠结)。
然而,由于析出相、晶界等障碍物的作用,位错运动逐渐被阻止。
在同一滑移面上依次移动过来的位错在障碍物前停止,并塞积起来(见位错塞积)。
塞积位错不能运动,其反作用应力同时抑制住位错源的活动。
位错从析出物之间通过时,即使能通过,在析出物的周围也要留下位错环,它与析出物间隔变小具有相同的效果,使得通过越来越困难,即需要更大的应力才能通过。
不仅如此,位错的互相交截(见位错交截)、互相反应(见位错反应),造成割阶、空位,形成更多的妨碍位错运动的因素。
随着变形的进行,位错运动更加困难,位错密度增加,位错源的活动
也受到抑制,需要更大的应力才能继续变形,这就形成了变形强化。
金属的强韧化
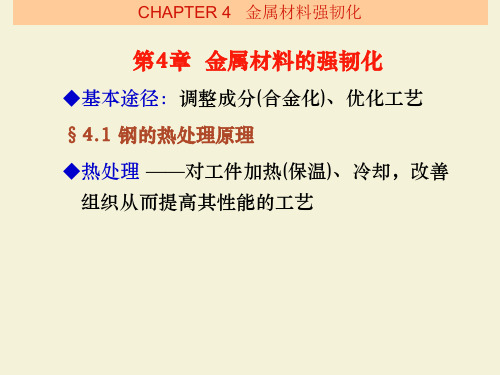
CHAPTER 4 金属材料强韧化
CHAPTER 4 金属材料强韧化
三、淬火与回火 (一)淬火
将钢件加热至Ac3(亚共析钢)或Ac1 (过共析钢) 以上30~50℃,保温后激冷,获得高硬度的M 1.淬火加热温度的确定 亚共析钢:完全A化,无软相F,冷却后得M (或少量AR) 共析钢和过共析钢:加热后组织为:A+Fe3C 淬火后为:M+Fe3C+AR
二、钢在冷却时的转变 方式:等温冷却转变(TTT)
连续冷却转变(CCT)
CHAPTER 4 金属材料强韧化
CHAPTER 4 金属材料强韧化
(一) 共析钢过冷A转变 1.过冷A等温转变曲线(TTT图或C曲线) ⑴ C曲线含义:过冷A等温转变开始时间 和转变终了时间以及转变产物的关系图
CHAPTER 4 金属材料强韧化
温快速转变,大量原子有规律的小距离位移来实现晶格转换 b.变温形成 在Ms下保温,M量不增加; c.体积长大 bcc晶格的c轴被拉长,成为正方。c/a称为正方度,
c/a越大畸变越严重;体积膨胀导致组织应力 d.转变不完全 有残余A--Ar。wc↑,Me↑, → Ar ↑
CHAPTER 4 金属材料强韧化
4.去应力退火:工件加热至500~650℃,保温后 缓冷
◆消除铸件、锻件、焊接件的残余应力,稳定工 件形状和尺寸
CHAPTER 4 金属材料强韧化
二、正火 将工件加热至Ac3或Accm以上30~50℃,保温 后空气中(风中或喷雾)冷却
◆细化晶粒,适当提高中、低碳钢的强度和硬 度便于切削加工
◆冷速快,使过共析钢来不及结成Fe3C网状, 便于球化退火
三、淬火钢的回火转变 ◆回火:将淬火钢件加热至A1线下某温度,保温后冷却。 1. 回火时的组织转变 (1)淬火M转变为回火M(100~200℃) M回—过饱和α-固溶体上分布着细小薄片状ε-碳化物 (2)残余A分解(200~300℃) 过饱和α-固溶体上分布着细粒θ-碳化物 (3)碳化物类型转变(250~400℃)
第1章:钢的强韧化基本理论

钢位 材 塑 轧 的错 料 性 钢 力理 热 变 工 学论 处 形 艺 性 理金学 能 属 学
生产实践
辽宁科技大学 材料与冶金学院 井玉安 微 控 编制 强 强 奥 变 控
韧 性 能 定 义 和 指 标 韧 化 机 制 氏 体 形 变 2 与 再 结 晶 制 轧 制 的 概 念 及 4 思 想 3 形 条 件 下 的 相 变 合 金 元 素 的 作 用 制 冷 却 的 概 念 及 思 6 想 中 厚 板 上 的 应 用 热 连 轧 带 钢 上 的 应 用 薄 板 坯 连 铸 连 轧 上 的 应 用 型 钢 生 产 中 的 应 用 棒 线 材 生 产 上 的 应 用 无 缝 钢 管 生 产 上 的 应 用
B上
σ 材料与冶金学院 σ
b
D B
弹性阶段OA 屈服阶段AB 强化阶段BC 颈缩阶段CD
辽宁科技大学 2.抗拉强度σb
钢材所能承受的最大应力
结构设计中钢材强度取值的依据
A B下
σb
s
屈强比= σ s σ b 屈强比↑,利用率
井玉安
σs σ p
编制
α
O L1 L0
↑,安全可靠程度↓
3.伸长率δδ = L1 − L0 ×100% L0
τ m = G 2π 辽宁科技大学 材料与冶金学院 但从试验数据可以看出:由试验测到的剪切强度与按此关糸求出的理论剪切强
度相差4个数量级。金属的理论抗拉强度大致为其弹性模量的1/10,而其实际抗拉 强度同样也低于理论值的3到4个数量级。
井玉安
编制
School of Materials and Metallurgy
井玉安
University of Science and Technology Liaoning
强化韧化机理
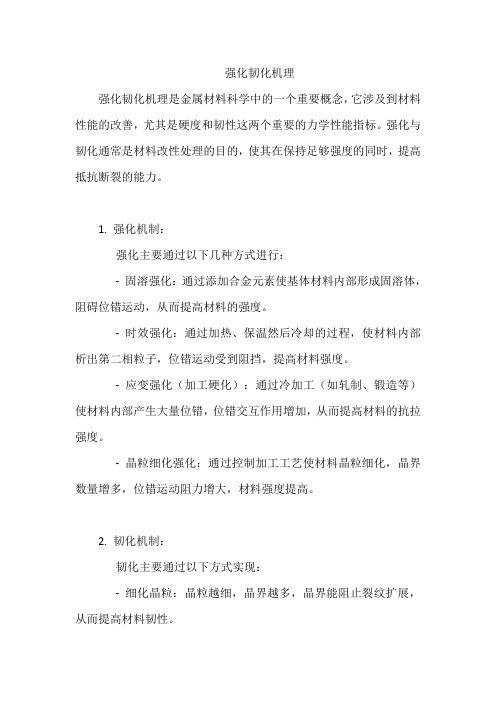
强化韧化机理
强化韧化机理是金属材料科学中的一个重要概念,它涉及到材料性能的改善,尤其是硬度和韧性这两个重要的力学性能指标。
强化与韧化通常是材料改性处理的目的,使其在保持足够强度的同时,提高抵抗断裂的能力。
1. 强化机制:
强化主要通过以下几种方式进行:
- 固溶强化:通过添加合金元素使基体材料内部形成固溶体,阻碍位错运动,从而提高材料的强度。
- 时效强化:通过加热、保温然后冷却的过程,使材料内部析出第二相粒子,位错运动受到阻挡,提高材料强度。
- 应变强化(加工硬化):通过冷加工(如轧制、锻造等)使材料内部产生大量位错,位错交互作用增加,从而提高材料的抗拉强度。
- 晶粒细化强化:通过控制加工工艺使材料晶粒细化,晶界数量增多,位错运动阻力增大,材料强度提高。
2. 韧化机制:
韧化主要通过以下方式实现:
- 细化晶粒:晶粒越细,晶界越多,晶界能阻止裂纹扩展,从而提高材料韧性。
- 第二相颗粒强化:在材料基体中引入弥散分布的第二相颗粒,如陶瓷颗粒、金属间化合物等,可以阻滞裂纹的扩展,起到钉扎位错的作用,提高材料韧性。
- 亚微观结构调控:通过调整材料内部的层片状、孪晶、位错胞等亚微观结构,使材料在遭受冲击或负载时分散并吸收能量,从而提高韧性。
- 混合韧化:结合多种韧化机制,如相变韧化(马氏体钢的相变)、沉淀强化与韧化并存(航空铝合金的时效处理)等,实现强度和韧性的同步提升。
- 1、下载文档前请自行甄别文档内容的完整性,平台不提供额外的编辑、内容补充、找答案等附加服务。
- 2、"仅部分预览"的文档,不可在线预览部分如存在完整性等问题,可反馈申请退款(可完整预览的文档不适用该条件!)。
- 3、如文档侵犯您的权益,请联系客服反馈,我们会尽快为您处理(人工客服工作时间:9:00-18:30)。
钢的强韧化处理机制王立洲(辽宁工程技术大学材料科学与工程学院阜新123000)本文根据钢的淬火组织特点,归纳了提高钢强韧性的途径,介绍了一些强韧化处理工艺。
随着工业的发展,各种机械对钢铁材料的机械性能要求逐渐增高。
材料及热处理工艺的研究得到迅速的发展。
其中,利用现有材料,通过调整一般的热处理方法,在同时改善钢的强度和韧性指标方面的工作取得了显著的进步。
它对充分发挥材料的性能潜力有着重要的意义。
这些工艺方法通称为强韧化处理,是热处理发展的一个值得注意的方向。
强韧化处理的发展是建立在我们对钢中各种组织的特点,形成条件,机械性能,以及在外力作用下的破断过程的认识不断深入的基础之上的。
透射电子显微镜技术的应用,使我们对各种组织超显微精细结构的认识跨进了一大步,开始有可能比较深入地研究组织和机械性能的关系。
另一方面,从材料断裂过程的研究中知道,在各种应力作用下,材料的破断是通过微裂纹的形成及扩展的方式进行的。
钢铁材料的各种组织形态在各种应力状态下,抵抗微裂纹的形成和扩展的能力是不同的,因此表现出不同的性能指标。
但是无论哪一种组织,只要它形成微裂纹的倾向比较小,或者微裂纹一旦形成后,在这类组织中扩张时消耗的功愈大,它就会有较高的强韧性。
这样,我们就有可能采用适当的热处理工艺方法和调整工艺参数,能动地控制钢的组织,充分利用对钢强韧化有利的因素,排除不利的因素,更充分地发挥材料的强度和韧性的潜力。
目前发展的强韧化处理工艺有多种多样,归结起来,它们大多通过一种或几种途径达到强韧化效果的。
(1)充分利用位错型马氏体和下贝氏体组织形态,尽量减少或避免片状孪品马氏体的出现。
(2)细化钢的奥氏体晶粒和细化过剩碳化物。
(3)获得马氏体与具有良好塑性的第二相的复合组织。
(4)形变热处理。
下面将简要介绍这些强化处理的机理。
一位错型马氏体的扩大应用很久以来就知道,在保证淬、回火零件强度指标的前提下,选用含碳量较低的钢,能够使零件热处理后获得较高的韧性。
改变热处理工艺参数,可以在中碳及高碳钢中获得以板条马氏体为主的淬火组织,显著改善中碳钢及高碳钢的强韧性。
这种控制淬火组织形态的方法,已成为中、高碳钢强韧化的一条重要途径。
1、中碳钢的高温淬火一般含碳量为0.35%一0.55%之间的中碳钢经正常温度淬火,获得片状和板条马氏体的混合组织。
这两种淬火马氏体对钢强韧性的贡献是不同的。
钢的含碳量愈高,正常淬火组织中片状马氏体的比例愈高,钢的强度虽然有所增加,但断裂韧度不断减小。
断裂韧度的这种变化是韧性较高的板条马氏体相对量减少的结果。
但是,提高中碳钢淬火温度和延长淬火保温时间,则有利于在淬火后得到较多数量的板条马氏体,提高钢的断裂韧度。
例如,将40CrNIMo 钢的淬火温度从570℃提高到1200℃,淬火后得到了板条马氏体和极少量残留奥氏体。
在淬火不回火状态下,钢的断裂韧度提高70%,在淬火和低温200℃回火状态下,可提高20%。
我们将5CrMnMo热锻模具钢的淬火加热温度从830~850提高到900℃,淬火后将获得近乎单一的板条马氏体组织,图1给出了在500一520℃的高温回火状态下,淬火温度对强度、塑性和断裂韧度的影响。
从图中可以看出,在能够得到比较完全板条马氏体的900℃淬火和高温回火状态下,这种钢的强度、塑性和断裂韧度都达到最大值。
同普通加热淬火相比,断裂韧度增高10%,达360公斤/毫米23,如果适当增加回火时间,可使断裂韧度达418公斤/毫米23,比普通温度淬火者提高30%左右。
这就是使5CrMnMO 钢的断裂韧度优于经正常工艺处理的同样强度40CrNIMo 钢的断裂韧度。
2高碳钢的低温短时间加热淬火高碳钢一般都在淬火低温回火的高硬度状态下使用。
用普通的加热淬火工艺处理的高碳 钢,得到片状马氏体组织,往往表现出很高的脆性。
如果适当控制高碳钢淬火加热时奥氏体 中的含碳量,也可以在淬火后得到以板条马氏体为主的淬火组织,减少片状马氏体可能造成 的脆性,使钢在保持高硬度的同时,还具备良好的韧性。
采用低温短时间加热或快速加热的工艺,都可以收到满意的效果。
当加热温度一定时,加热时间对淬火钢硬度的影响规律见图2在某一较短的淬火保温时间下可以得到最高的硬度[1]。
这个硬度一般高于普通加热淬火的水平。
淬火组织为板条马氏体加细小碳化物,残留奥氏体数量极少[2]。
图2碳量过低强韧化效果不明显。
它说明,这种工艺方法的强化作用主要来自马氏体形态的变化。
此外,原始组织对高碳钢低温短时间加热淬火的强化效果有重要的影响。
原始组织愈细小,按此工艺淬火后的强度和韧性也愈高[3]。
图5比较了调质和球化退火组织对快速加热钢强度和韧性的影响。
可以看到,调质作为这种处理工艺的予先热处班,高碳钢的强度,特别是韧性的增加幅度非常突出。
二等温淬火等温淬火可以显著改善高碳钢的强韧性,即在同样的强度水平,等温淬火钢的塑性、韧性比普通淬火状态有大幅度的增高[16],图6比较了等温淬火和普通淬火CrWMn 钢的强度、塑性和韧性同硬度的关系。
从图6中可以看出,在硬度相同时,等温淬火钢的塑性和韧性比普通淬火高出0.5一1倍。
而在塑性或韧性相同时,等温淬火状态的硬度要高4~6HRC 以上。
在硬度相同时,等温淬火高碳钢还有较高的耐磨性[4]。
根据对马氏体和贝氏体形态和机械性能的研究可知,等温淬火高碳钢较高的强韧性特点,是因为高碳贝氏体的性能优于高碳片状马氏体,并在等温淬火时取代了片状马氏体,避免了它对钢韧性可能的损害。
片状马氏体对淬火钢韧性的损害主要来源于如下三个方面[4],(1)片状马氏体转变时的相互撞击作用,在马氏体片相交的部位或马氏体片内常伴随有显微裂纹的存在。
(2)片状马氏体内含有密集的孪晶亚结构,在外力作用下,当运动的位错同孪晶交截时,往往在孪晶界面形成显微裂纹。
这些潜在的显微裂纹,增大了淬火钢的脆性破坏倾向。
(3)高碳马氏体中固溶的碳量远远高于下贝氏体中的含碳量。
间隙原子的固溶量愈大,固溶强化效应愈高,对钢的韧性造成的损害也愈严重。
三奥氏体晶粒的超细化和碳化物的超细化细化钢的晶粒可以有效地提高钢的强度。
钢的屈服强度s σ同平均品粒直径d 之间有如下的关系:21-0s kd +=σσ称Hall 一Patch 关系,其中。
0σ和K 为常数。
细化钢的品粒还有提高室温韧性和降低脆性转变温度的良好作用。
晶粒愈细小,在外力的作用下,塑性变形的扩展受到晶界的阻碍作用愈大,有利于提高钢的强度。
另一方面,断裂的裂纹穿越晶界扩张消耗的功愈多,钢的韧性也愈好。
由于细化品粒可以同时改善钢的强度和韧性,因此,如何在钢热处理后保持细晶粒的问题,一直是热处理工作者的重要研究课题。
近年来发展了许多获得十级以上超细晶粒的方法——晶粒的超细化处理。
它已经成为一种重要的强韧化手段应用在生产中。
此外,考虑到材料破断时,裂纹往往发源于尺寸较大的第二相,如碳化物上。
所以,细化高碳钢未溶碳化物的问题也受到愈来愈多的注意,发展了碳化物超细化处理的新方法。
1快速循环加热Grange首先提出,利用同图9类似的快速循环加热淬火工艺,可以得到13一14级的超细化晶粒[5]。
循环加热淬火的基本方法是将工件以较快的速度从室温(或低于A1的预热温度)加热到高于A3的温度,经短时间停留即行淬火冷却,如此循环数次。
它同普通热处理的主要差别在于,①加热速度比较快②在得到奥氏体化的前题下,加热温度尽可能的低③加热时间以工件心部达到予定温度为限,不得过长。
加热方式可用感应加热技术,也可采用铅浴加热的方法。
对于后一种情况,铅浴温度往往控制得高于工件实际加热温度。
然而无论采用什么加热方式,循环加热时工件实际达到的最高温度应低于普通热处理时工件的加热温度。
金泽等将12MnMo钢用100KW高频以10℃/秒进行4次快速循环加热,得到平均品粒直径3微米的超细晶粒(相当于13级),提高了这种钢的屈服强度,并使它的脆性转变温度显著下降[6],见图10。
2.交替循环加热利用前述快速循环加热淬火的方法,只能使一般合金结构钢的奥氏体晶粒细化到3一5微米(相当于14~13级晶粒度)[7]。
采用冷变形和适当的热处理相结合的方法,可以将奥氏体晶粒细化到2.3微米(相当14~15级)[8],甚至0.3~1.1微米(相当19~16级)的超细晶粒[9]。
3.碳化物的超细化处理细化过共析钢的过剩碳化物,对钢的韧性和接触疲劳强度有很好的作用。
文[10]指出,在较高的外加应力作用下,高碳钢中直径大于1微米的碳化物是它破断时形成显微裂纹的主要场所。
实践证明,细化高碳钢中的碳化物是提高高碳钢强韧性的一个重要途径。
四复合组织的利用在淬火钢中,与马氏体组织共存一定数量的第二相,如铁素体,残留奥氏体或下贝氏体等,往往能在不降低强度的情况下,显著提高钢的韧性,减低脆性破坏倾向,现在看来,通过热处理获得复合组织的途径,可以很好地发挥钢的性能潜力,是钢强韧化的一个值得注意的研究方向[16]。
这里,将介绍三个方面的问题:获得马氏体和铁素体共存的二相区淬火,残留奥氏体的 应用,以及低碳钢中马氏体和下贝氏体复合组织的性能。
1.)(γα+二相区加热淬火虽然亚共析钢在淬火时沿晶界形成先共析铁素体会损害钢的强韧性,但是亚共析钢在 )(γα+二相区进行不完全加热淬火,得到一定数量铁素体和马氏体的混合组织。
它对提高材料的韧性,减小回脆倾向有明显的效果。
这种热处理方法在普通低合金钢和大型汽轮机转子用钢等方面的应用都有满意的成效。
2.低碳钢中的马氏体和下贝氏体的复合组织低碳低合金钢过去多在热轧状态下使用。
为了提高这类钢的强度和韧性,近年来发展了经淬火回火处理得到回火马氏体的调质型高强度钢。
它的强度可达80一100公斤/毫米2以 上。
还保持较高的韧性。
3.残留奥氏体的应用Webster 在研究超高强度钢AFC77的强韧化问题时发现,适当提高加热温度和减低 回火温度,在钢中保留30%~35%的残留奥氏体的情况下,可以显著增加这种钢的断裂韧度[14]在研究了Fe 一Cr 一C 超高强钢的超显微结构时观察到,在淬火得到的板条马氏体之间 存在着残留奥氏体薄膜。
而且残留奥氏体的存在同这种钢具有较高的断裂韧度有直接的关系[11] 五形变热处理形变热处理是将钢的形变强化同相变强化结合起来的一种综合热处理方法[15]。
在过去二十多年里,形变热处理作为改善钢机械性能的一种新型手段受到广泛的重视,并在生产上得到一定应用。
形变热处理发展之初,人们把主要兴趣放在提高钢的强度方面。
通过形变热处理,钢的实际强度已可达350公斤/毫米2以上。
形变热处理还能在一定程度上提高钢的韧性,近年来,它已经发展成为改善高强度钢韧性的重要强韧化手段应用在生产上。
1形变热处理对钢性能的影晌根据机械形变的温度和在热处理操作中所处的位置,形变热处理有多种类型。