粉末冶金的主要成形方法
第三章粉末冶金
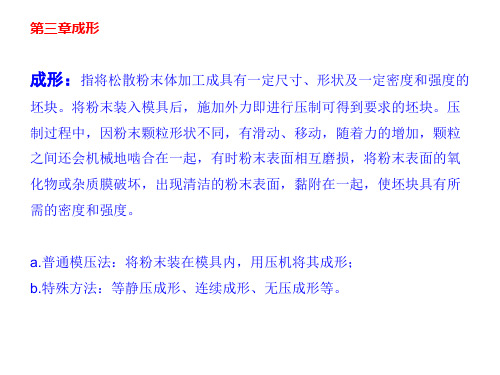
第三章成形 d.弹性后效
加载(或卸载)后经过一段时间应变才增加(或减小)到一定数值的 现象。压制过程中,当卸掉压制力并把坯块从模具内取出后,由于弹性 内应力的作用,坯块发生弹性膨胀,这种现象称为弹性后效。
a.粉末颗粒发生位移,填充孔隙,施加压力,密度增加很快; b.密度达到一定值后,粉末体出现一定压缩阻力,由于位移大大减少, 而变形尚未开始,压力增加,但密度增加很少; c.当压力超过粉末颗粒的临界应力时,粉末颗粒开始变形,使坯块密度 继续增大。
图3-10坯块密度的变化规律
第三章成形
(5)压制压力与坯块相对密度的关系 相对密度指物质的密度与参考物质的密度在各自规定的条件下之比,
第三章成形
退火温度: T退 (0.5 ~ 0.6)T熔
退火气氛: a.还原性气氛(氢、离解氨、转化天然气或煤气) b.惰性气氛 c.真空退火
第三章成形
(2)混合 a.混合:将两种或两种以上不同成分的粉末混合 b. 将相同成分而粒度不同的粉末混合(合批) 混合方法:机械法(干混、湿混)和化学法 机械法:干混用于生产铁基制品;湿混用于生产硬质合金。混料设备有
a.普通模压法:将粉末装在模具内,用压机将其成形; b.特殊方法:等静压成形、连续成形、无压成形等。
第三章成形
1.成形前原料准备 (1)退火
将金属缓慢加热到一定温度,保持足够时间,然后以适宜速度冷却(通 常是缓慢冷却,有时是控制冷却)的一种金属热处理工艺。
金属粉末退火的目的: a.氧化物还原,降低碳和其它杂质的含量,提高粉末的纯度; b.消除粉末的加工硬化,稳定粉末的晶体结构; c.防止超细粉末自燃,将其表面钝化。 加工产品退火的目的: a.降低硬度,改善切削加工性; b.消除残余应力,稳定尺寸,减少变形与裂纹倾向; c.细化晶粒,调整组织,消除组织缺陷。
粉末冶金成型

2.高速压制
瑞典开发出粉末冶金用高速压制法。这可能是 粉末冶金工业的又一次重大技术突破。高速压制采 用液压冲击机,它与传统压制有许多相似之处,但关 键是压制速度比传统快500~1000倍,其压头速度高 达2~30m/s,因而适用于大批量生产。液压驱动的 重锤(5~1200kg)可产生强烈冲击波,0.02s内将压 制能量通过压模传给粉末进行致密化。重锤的质量 与冲击时的速度决定压制能量与致密化程度。
(2)生坯强度高
常规工艺的生坯强度约为10~20MPa,温压压坯的强度则为 25~30MPa,提高了1.25-2倍。生坯强度的提高可以大大降 低产品在转移过程中出现的掉边、掉角等缺陷,有利于制备 形状复杂的零件;同时,还有望对生坯直接进行机加工,免 去烧结后的机加工工序,降低了生产成本。这一点在温压烧结连杆制备中表现得尤为明显。
温压成型技术发展趋势: 预合金化粉末的制造技术; • 新型聚合物润滑剂的设计; • 石墨粉末有效添加技术; • 无偏析粉末的制造技术; • 温压系统制备技术。
温压成型技术应用:
温压技术主要适合生产铁基合金零件。同时人们正在 尝试用这种技术制备铜基合金等多种材料零件。由于温压 零件的密度得到了较好的提高,从而大大提高了铁基等粉 末冶金制品的可靠性,因此温压技术在汽车制造 机械制 造、武器制造等领域存在着广阔的应用前景。
6.注射成形技术
Injection molding technology
金属粉末注射成形技术是随着高分子材料的应用 而发展起来的一种新型固结金属粉、金属陶瓷粉和陶 瓷粉的特殊成形方法。它是使用大量热塑性粘结剂与 粉料一起注入成形模中,施于低而均匀的等静压力, 使之固结成形,然后脱粘结剂烧结。
5.注射成形技术
美国开发出一种能在室温下生产全致密零 件而无需后续烧结的粉末冶金工艺。此工艺称 之为“冷成形粉末冶金”。 它采用特殊配制的活化溶液与革新的进料 靴技术,在压力下精确地将粉末注入模中。加 压输送的进料靴使粉末填充更加均匀,而活性 溶液则防止形成氧化物,从而大大促进了冷焊 效应。
粉末冶金成形及非金属成形
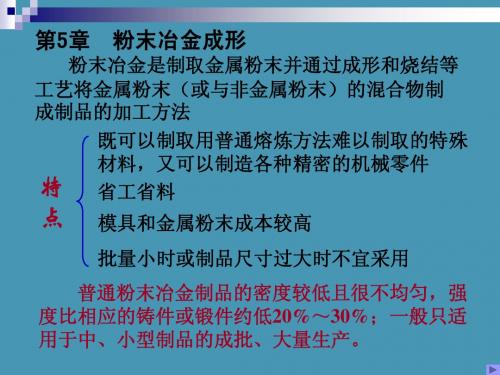
4.等静压制 对粉末(或压坯)表面或对装粉末(或压坯)的软 膜表面施以各向大致相等的压力的压制方法 (1) 冷等静压制: 在室温下的等静压
制,压力传递媒介通常为液体 冷等静压制压坯密度较高,较均匀,力 学性能较好,形状可较复杂,尺寸可较大
(2) 热等静压制: 高温下的等静压制
同时进行压制和烧结,压制压力和烧 结温度均低于冷等静压制,能耗较低,生 产效率较高;制品密度高且均匀,晶粒细 小,力学性能较高,形状和尺寸不受限制; 但投资大。 用于粉末高速钢,难熔金属,高温合 金和金属陶瓷等制品的生产
2)按受热时的性能分类: 按受热时的性能不同分类 ①热塑性塑料:在整个特征温度范围内,能反复加热 (ABS、PA等) 软化和反复冷却硬化,且在软化状态 通过流动能反复模塑为制品 力学性能较好,加工成形方便,耐热性较差
② 热固性塑料:固化时,能变成基本不溶、不熔的 (PF等) 产物。有较高的耐热性,受压时亦 不易变形,但力学性能较差。 (2) 工程塑料的性能特点和应用:工程塑料密度小,比 强度(强度/密度)高,耐磨性、减振性较好, 易于成形;强度、硬度较低,导热性、耐热性 较差,且易老化。 工程塑料可用于替代金属制造工程构件和机械零件
图6-7 密闭式塑炼机工作原理
图6-8 切碎机结构
2、塑料成形方法: (1) 挤出成形: 用于生产具有 一定断面形状的连 续材料,如管材、 板材和中空制品等 还常用于物料 的塑炼和着色等。 生产效率高、工艺适应性强、设备结构简单, 但制品断面形状较简单且精度较低。 适用于几乎各类热塑性塑料和部分热固性塑料。
烧结减摩材料
5.1 粉末冶金基础 5.1.1 粉末的化学成分及性能 粉末通常指尺寸小于1mm的离散颗粒的集合体, 颗粒尺寸一般以微米(μ m)或纳米(nm)计量 1、粉末的化学成分 常用的金属粉末有铁、铜、铝等及其合金的粉 末,杂质和气体的含量一般不超过1%~2%
粉末冶金特种成形技术
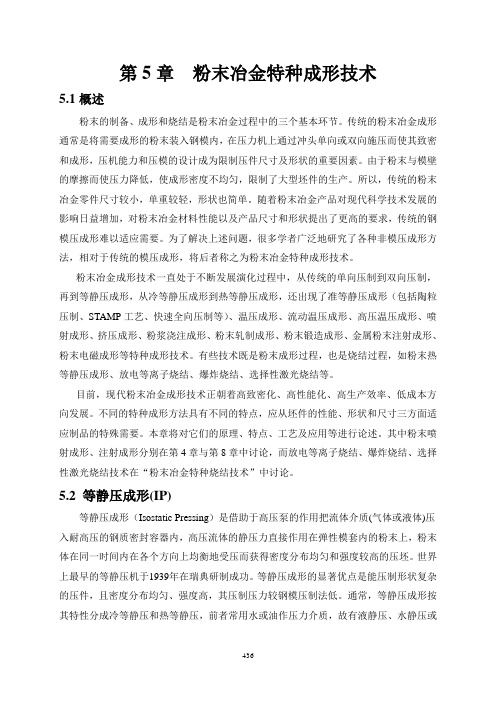
第5章粉末冶金特种成形技术5.1概述粉末的制备、成形和烧结是粉末冶金过程中的三个基本环节。
传统的粉末冶金成形通常是将需要成形的粉末装入钢模内,在压力机上通过冲头单向或双向施压而使其致密和成形,压机能力和压模的设计成为限制压件尺寸及形状的重要因素。
由于粉末与模壁的摩擦而使压力降低,使成形密度不均匀,限制了大型坯件的生产。
所以,传统的粉末冶金零件尺寸较小,单重较轻,形状也简单。
随着粉末冶金产品对现代科学技术发展的影响日益增加,对粉末冶金材料性能以及产品尺寸和形状提出了更高的要求,传统的钢模压成形难以适应需要。
为了解决上述问题,很多学者广泛地研究了各种非模压成形方法,相对于传统的模压成形,将后者称之为粉末冶金特种成形技术。
粉末冶金成形技术一直处于不断发展演化过程中,从传统的单向压制到双向压制,再到等静压成形,从冷等静压成形到热等静压成形,还出现了准等静压成形(包括陶粒压制、STAMP工艺、快速全向压制等)、温压成形、流动温压成形、高压温压成形、喷射成形、挤压成形、粉浆浇注成形、粉末轧制成形、粉末锻造成形、金属粉末注射成形、粉末电磁成形等特种成形技术。
有些技术既是粉末成形过程,也是烧结过程,如粉末热等静压成形、放电等离子烧结、爆炸烧结、选择性激光烧结等。
目前,现代粉末冶金成形技术正朝着高致密化、高性能化、高生产效率、低成本方向发展。
不同的特种成形方法具有不同的特点,应从坯件的性能、形状和尺寸三方面适应制品的特殊需要。
本章将对它们的原理、特点、工艺及应用等进行论述。
其中粉末喷射成形、注射成形分别在第4章与第8章中讨论,而放电等离子烧结、爆炸烧结、选择性激光烧结技术在“粉末冶金特种烧结技术”中讨论。
5.2 等静压成形(IP)等静压成形(Isostatic Pressing)是借助于高压泵的作用把流体介质(气体或液体)压入耐高压的钢质密封容器内,高压流体的静压力直接作用在弹性模套内的粉末上,粉末体在同一时间内在各个方向上均衡地受压而获得密度分布均匀和强度较高的压坯。
高密度粉末冶金成形方法研究及优化

高密度粉末冶金成形方法研究及优化一、引言高密度粉末冶金成形技术是一种通过在粉末表面施加压力和温度实现金属材料成形的加工工艺。
该技术具有高效率、低成本、高精度、可逆性和可重复性等优点。
因此,在改进传统的金属成形过程以及开发新型金属材料时,高密度粉末冶金成形技术已成为一种备受关注的重要研究领域。
二、高密度粉末冶金成形方法的分类高密度粉末冶金成形技术根据成形前后粉末状况的变化,可分为以下几种方法:1. 等静压成形 (HIP)等静压成形是一种将高密度金属粉末放入成型模具中,先以低压力进行预压,随后在高温和高压力的条件下加以成形的加工方法。
等静压成形方法可以制造出具有高密度和高性能的复杂形状金属零件,如滚轮轴承、配气机构、燃气轮机叶片等等。
2. 烧结成型烧结成型是一种通过在制备过程中在粉末中添加一些粘结剂,使得粉末在高温条件下粘结在一起,然后进行成形的方法。
这种方法可以制造出高精度、高可靠性和抗热性能强的机械结构件和高强度、低密度的材料。
3. 挤压成形挤压成形是一种通过将金属粉末放入旋转式模具中,在模具两端施加压力来实现成形的加工方法。
这种方法较其他成形方式更为简单,适用于制作一些规则结构的中间件、链接件和管道接头。
4. 等离子粉末成形等离子粉末成形是一种将金属粉末喷射到等离子体火焰中进行高温加热,通过表面张力形成液态金属,并恰当地加压形成零件的一种成形工艺。
等离子粉末成形方法操作简单、可加工出具有高密度、高强度和高耐磨性的金属零件。
三、高密度粉末冶金成形方法的优化为了进一步提高高密度粉末冶金成形技术的加工效率、成形质量和材料性能,需要进行相应的优化。
优化方案一:材料的合理选择选择合适的材料是决定高密度粉末冶金成形成功与否的关键因素之一。
高密度粉末冶金成形的理想材料是那些粒度大小适中、形状均匀、流动性能好而且作为粉末冶金材料的化学成分方面相同或相似的金属粉末。
因此,选择质量优良、粘度适中的金属粉末是高密度粉末冶金成形过程中一个非常重要的环节。
粉末冶金工艺
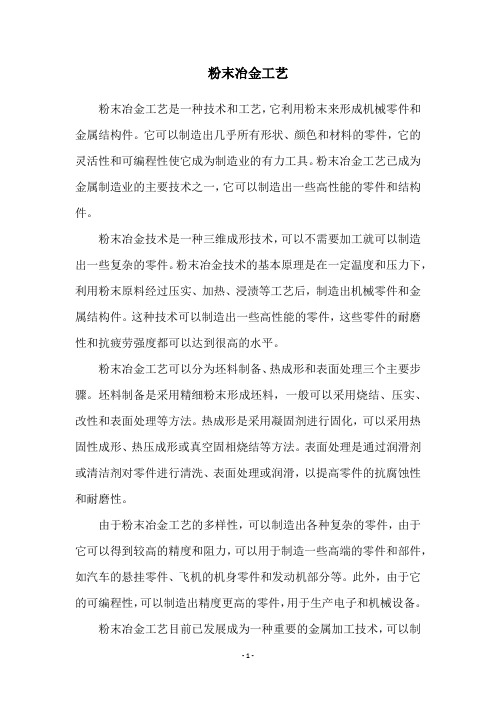
粉末冶金工艺粉末冶金工艺是一种技术和工艺,它利用粉末来形成机械零件和金属结构件。
它可以制造出几乎所有形状、颜色和材料的零件,它的灵活性和可编程性使它成为制造业的有力工具。
粉末冶金工艺已成为金属制造业的主要技术之一,它可以制造出一些高性能的零件和结构件。
粉末冶金技术是一种三维成形技术,可以不需要加工就可以制造出一些复杂的零件。
粉末冶金技术的基本原理是在一定温度和压力下,利用粉末原料经过压实、加热、浸渍等工艺后,制造出机械零件和金属结构件。
这种技术可以制造出一些高性能的零件,这些零件的耐磨性和抗疲劳强度都可以达到很高的水平。
粉末冶金工艺可以分为坯料制备、热成形和表面处理三个主要步骤。
坯料制备是采用精细粉末形成坯料,一般可以采用烧结、压实、改性和表面处理等方法。
热成形是采用凝固剂进行固化,可以采用热固性成形、热压成形或真空固相烧结等方法。
表面处理是通过润滑剂或清洁剂对零件进行清洗、表面处理或润滑,以提高零件的抗腐蚀性和耐磨性。
由于粉末冶金工艺的多样性,可以制造出各种复杂的零件,由于它可以得到较高的精度和阻力,可以用于制造一些高端的零件和部件,如汽车的悬挂零件、飞机的机身零件和发动机部分等。
此外,由于它的可编程性,可以制造出精度更高的零件,用于生产电子和机械设备。
粉末冶金工艺目前已发展成为一种重要的金属加工技术,可以制造出一些高性能的零件和结构件,可以应用到汽车、航空航天、电子电气等众多行业中。
因此,粉末冶金技术受到了越来越多的关注,将在未来发挥更大的作用。
综上所述,粉末冶金工艺是一种重要的金属加工技术,它可以制造出精度更高的零件,用于制造一些高端的零件和部件,是未来金属加工技术的重要方向。
粉末冶金技术的发展有着重要的意义,有助于推动制造业的发展和提高产品的质量,因此,未来粉末冶金技术还将发挥着更大的作用。
粉末冶金成形

通过烧结过程中的物质迁移和相变,使烧结体内部孔隙减小或消失, 提高其密度和性能。
致密化程度
与烧结温度、时间、气氛等因素有关,需根据产品要求进行控制。
03 粉末冶金成形的关键技术
粉末注射成形技术
定义
粉末注射成形是一种将金属粉末与有机粘结 剂混合,通过注射机注入模具中成形,然后 脱脂和烧结的工艺。
能源领域
粉末冶金技术在风力发电、核能等领 域中用于制造高性能的零部件。
粉末冶金成形的优缺点
材料利用率高,减少材料 浪费;
可生产出形状复杂、精度 高的制品;
优点
01
03 02
粉末冶金成形的优缺点
01
可通过控制成分和工艺参数制备高性能材料;
02
适用于大规模生产。
缺点
03
粉末冶金成形的优缺点
生产过程中易产生粉尘污染; 制品内部可能存在孔隙和缺陷; 部分材料制备成本较高。
等静压成形技术
定义
等静压成形技术是一种利用液体介质传递压力,使金属粉末在各 个方向上均匀受压而成形的工艺。
优点
可生产高精度、高密度、高性能的产品,适用于大规模生产。
应用领域
广泛应用于陶瓷、粉末冶金等领域。
04 粉末冶金成形的材料性能
材料力学性能
硬度
抗拉强度
粉末冶金制品的硬度通常较高,可达到 HRC60以上,这主要得益于其致密的结构 和合金元素的固溶强化作用。
粉末冶金制品具有较高的抗拉强度,通常 在1000MPa以上,这与其致密的结构和晶 粒细化有关。
疲劳性能
韧性
由于其良好的力学性能,粉末冶金制品在 循环载荷下表现出良好的疲劳性能。
粉末冶金制品的韧性与其成分、显微组织 和热处理状态有关,通过合理的工艺控制 可以提高其韧性。
粉末冶金成形技术

粉末冶金成形技术总则✶粉末成形技术就是将预混合好的粉末填入设计好的模腔中,通过压机施加一定的压力使之形成所设计的形状的产品,然后由压机将产品脱出模腔的过程。
✶与之相关的有以下几个方面1.粉末制造及粉末混合2.模具3.成形压机4.模架5.模具的组立粉末方面与模具方面 这里不作具体介绍成形压机✶成形压机中模面分两种形式:1.中模面浮动2.中模面固定✶成形压机中模面浮动形式分两种类型:1.脱模位置固定,成形位置可以调整2.成形位置固定,脱模位置可以调整一般,压力吨位较小的采用中模面固定类型,压力吨位较大的采用中模面浮动。
成形过程中压机运转的几个阶段✶1.充填阶段:从脱模结束后开始至中模面上升到最高点结束,压机运行的角度从270度开始至360度左右结束;✶2.加压阶段:是粉末在模腔中受压成形阶段。
一般有上模加压和中模面下降(即下压)加压,有时还有最终加压,即在下压结束后上冲再次加压,压机的运行角度从120度左右开始至180度结束;✶3.脱模阶段:此过程是产品由模腔被顶出的过程。
压机的运行角度由180度开始至270度结束中模面浮动的两种类型的区别:1.脱模位置固定,成形位置可以调整的形式以脱模下死点作为成形压机的基准点,基准点位置的角度270度。
充填的变化只能改变脱模的行程量和加压的行程量,对最终的脱模位置点不可改变,下压的变化不改变充填量;2.脱模位置浮动,成形位置固定的形式以压制过程结束时作为成形压机的基准点,基准点的位置在180度。
充填的变化不光改变脱模行程量和加压行程量,还将改变脱模位置点,下压的变化会改变充填量。
模架✶模架是模具的执行者,在成形过程中模具通过模架的动作从而产生各个冲子之间的相对运动,挤压模腔中的粉末,使之成形成所设定的形状。
✶从模架结构方面来分:有上一下一直至上二下三机构,主要有上模板、中模板、第一浮动板、第二浮动板、固定板和芯棒板组成。
上模板与机台的上加压部连接,芯棒板与机台的主轴连接,芯棒板通过四根导柱与中模板连成一个整体。
粉末冶金的工艺流程-粉末成形

简介 粉末冶金生产中的基本工序之一,目的是将松散的粉末制成具有预定几何形
状、尺寸、密度和强度的半成品或成品。模压(钢模)成形是粉末冶金生产中采 用最广的成形方法。18世纪下半叶和19世纪上半叶,西班牙、俄国和英国为制造 铂制品,都曾采用了相似的粉末冶金工艺。当时俄国索博列夫斯基 (П.Г.Соболевсκий)使用 的是 钢模 和螺 旋压 机。 英 国的 沃拉 斯顿 (W.H.Wol laston )使 用 压 力 更 大 的 拉 杆 式 压 机 和 纯 度 更 高 的 铂 粉 ,制 得 了 几 乎 没 有 残余孔隙的致密铂材。后来,模压成形方法逐渐完善,并用来制造各种形状的铜 基 含 油 轴 承 等 产 品 。 20世 纪 30年 代 以 来 , 在 粉 末 冶 金 零 件 的 工 业 化 生 产 过 程 中 , 压 机 设 备 、模 具 设 计 等 方 面 不 断 改 进 , 模 压 成 形 方 法 得 到 了 更 大 的 发 展 ,机 械 化 和 自动化已达到较高的程度。为了扩大制品的尺寸和形状范围,特别是为了提高制 品密度和改善密度的均匀性相继出现和发展了多种成形方法。早期出现的有粉末 轧制、冷等静压制、挤压、热压等;50年代以来又出现了热等静压制、热挤压、 热锻等热成形方法。这些方法推动了全致密、高性能粉末金属材料的生产。 主要功能
料 为 金 属( 低 碳 钢 、不 锈 钢 、钛 ),还 可 用 玻 璃 和 陶 瓷 。由 于 温 度 和 等 静 压 力 的 同 时作用,可使许多种难以成形的材料达到或接近理论密度,并且晶粒细小,结构 均匀,各向同性和具有优异的性能。热等静压法最适宜于生产硬质合金、粉末高 温合金、粉末高速钢和金属铍等材料和制品;也可对熔铸制品进行二次处理,消 除气孔和微裂纹;还可用来制造不同材质紧密粘接的多层或复合材料与制品。 粉末锻造
粉末冶金螺旋齿轮成形工艺
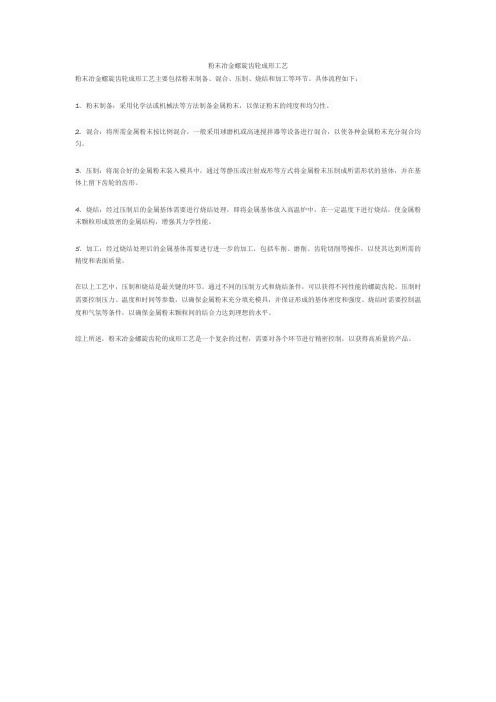
粉末冶金螺旋齿轮成形工艺
粉末冶金螺旋齿轮成形工艺主要包括粉末制备、混合、压制、烧结和加工等环节。
具体流程如下:
1. 粉末制备:采用化学法或机械法等方法制备金属粉末,以保证粉末的纯度和均匀性。
2. 混合:将所需金属粉末按比例混合,一般采用球磨机或高速搅拌器等设备进行混合,以使各种金属粉末充分混合均匀。
3. 压制:将混合好的金属粉末装入模具中,通过等静压或注射成形等方式将金属粉末压制成所需形状的基体,并在基体上留下齿轮的齿形。
4. 烧结:经过压制后的金属基体需要进行烧结处理,即将金属基体放入高温炉中,在一定温度下进行烧结,使金属粉末颗粒形成致密的金属结构,增强其力学性能。
5. 加工:经过烧结处理后的金属基体需要进行进一步的加工,包括车削、磨削、齿轮切削等操作,以使其达到所需的精度和表面质量。
在以上工艺中,压制和烧结是最关键的环节。
通过不同的压制方式和烧结条件,可以获得不同性能的螺旋齿轮。
压制时需要控制压力、温度和时间等参数,以确保金属粉末充分填充模具,并保证形成的基体密度和强度。
烧结时需要控制温度和气氛等条件,以确保金属粉末颗粒间的结合力达到理想的水平。
综上所述,粉末冶金螺旋齿轮的成形工艺是一个复杂的过程,需要对各个环节进行精密控制,以获得高质量的产品。
粉末材料的主要成型方法

粉末材料的主要成型方法
粉末材料的主要成型方法包括:
1. 烧结成型:将粉末材料加压成形后,在高温下进行烧结,使粉末颗粒粘结和合并,形成坚固的固体。
2. 注射成型:将粉末和粘结剂混合后注射到模具中,然后通过加热或固化使粉末颗粒固化成形。
3. 挤出成型:将粉末和粘结剂混合后挤出成型,通过加热或固化使粉末颗粒固化成形。
4. 粉末冶金成型:通过压制、烧结或热压等方式,将粉末材料制成金属产品或零件。
5. 粘结剂成型:将粉末材料与粘结剂混合后进行成型,其中粘结剂的作用是使粉末颗粒粘结在一起。
6. 激光烧结成型:利用激光束将粉末颗粒局部加热,使其熔化和熔接成形。
7. 真空烧结成型:在真空环境中进行烧结成型,可以减少氧化反应和杂质的产生,提高成品质量。
8. 喷雾成型:将粉末材料喷雾成细小颗粒,在加热或加压条件下使其固化成形。
粉末冶金与陶瓷成形概述

粉末冶金与陶瓷成形概述粉末冶金与陶瓷成形是一种非常重要的制备材料的工艺,应用广泛。
同样,这也是一种非常复杂严谨的技术,需要掌握一定的分步骤操作方法。
首先,粉末冶金主要是指将金属粉末和非金属粉末在一定条件下高温热压成形,制成一定形状和性能的金属材料。
基本工艺包括原料处理、制粉、成型、烧结、后处理等步骤。
制粉重点在于粒度控制和纯度控制,成型工艺包括模具设计、模具制作、装粉、压制等。
烧结工艺是冶金过程中的重要步骤,包括热处理、热膨胀、收缩等过程。
后处理工艺包括检验、包装、质量控制、存储等。
其次,陶瓷成形是指利用粉末成型、干燥、烧结、后处理等工艺制备高性能的陶瓷制品。
陶瓷成型的基本步骤包括原料处理、制粉、成型、干燥、烧结、后处理等。
其中,制粉工艺和烧结工艺是决定陶瓷制品性能的最重要的因素。
陶瓷粉末的制备需要精细加工,以得到具有合适粒径分布的陶瓷粉末。
在成型工艺中,常用的成型方法有干压成型、注塑成型、挤出成型等。
在烧结工艺中,烧结温度、保温时间和工艺气氛是影响烧结品质的重要因素。
最后,粉末冶金和陶瓷成形虽然存在一定的区别,但是它们的基本工艺步骤是非常相似的。
两者都强调粉末制备、成型和烧结工艺的重要性,都需要关注粉末的纯度、粒度分布和成型后的烧结密度等质量因素。
同时,由于工艺复杂,它们的制品在应用领域上都需要特殊的研究和创新。
例如,粉末冶金可以用于制备高强度合金材料、摩擦材料和金属陶瓷复合材料等,陶瓷成形可以用于制备高压瓷、机械零件等。
综上所述,粉末冶金与陶瓷成形是目前制备材料所必须掌握的重要工艺,其基本工艺流程必须熟练掌握,切实提高技能水平,以满足社会对高性能材料应用和需求的要求。
粉末冶金工艺
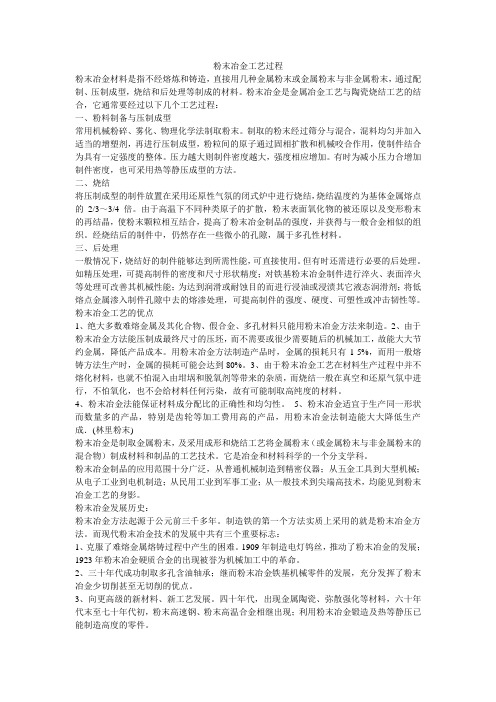
粉末冶金工艺过程粉末冶金材料是指不经熔炼和铸造,直接用几种金属粉末或金属粉末与非金属粉末,通过配制、压制成型,烧结和后处理等制成的材料。
粉末冶金是金属冶金工艺与陶瓷烧结工艺的结合,它通常要经过以下几个工艺过程:一、粉料制备与压制成型常用机械粉碎、雾化、物理化学法制取粉末。
制取的粉末经过筛分与混合,混料均匀并加入适当的增塑剂,再进行压制成型,粉粒间的原子通过固相扩散和机械咬合作用,使制件结合为具有一定强度的整体。
压力越大则制件密度越大,强度相应增加。
有时为减小压力合增加制件密度,也可采用热等静压成型的方法。
二、烧结将压制成型的制件放置在采用还原性气氛的闭式炉中进行烧结,烧结温度约为基体金属熔点的2/3~3/4倍。
由于高温下不同种类原子的扩散,粉末表面氧化物的被还原以及变形粉末的再结晶,使粉末颗粒相互结合,提高了粉末冶金制品的强度,并获得与一般合金相似的组织。
经烧结后的制件中,仍然存在一些微小的孔隙,属于多孔性材料。
三、后处理一般情况下,烧结好的制件能够达到所需性能,可直接使用。
但有时还需进行必要的后处理。
如精压处理,可提高制件的密度和尺寸形状精度;对铁基粉末冶金制件进行淬火、表面淬火等处理可改善其机械性能;为达到润滑或耐蚀目的而进行浸油或浸渍其它液态润滑剂;将低熔点金属渗入制件孔隙中去的熔渗处理,可提高制件的强度、硬度、可塑性或冲击韧性等。
粉末冶金工艺的优点1、绝大多数难熔金属及其化合物、假合金、多孔材料只能用粉末冶金方法来制造。
2、由于粉末冶金方法能压制成最终尺寸的压坯,而不需要或很少需要随后的机械加工,故能大大节约金属,降低产品成本。
用粉末冶金方法制造产品时,金属的损耗只有1-5%,而用一般熔铸方法生产时,金属的损耗可能会达到80%。
3、由于粉末冶金工艺在材料生产过程中并不熔化材料,也就不怕混入由坩埚和脱氧剂等带来的杂质,而烧结一般在真空和还原气氛中进行,不怕氧化,也不会给材料任何污染,故有可能制取高纯度的材料。
粉末冶金:轧制成形与挤压成形

➢ 双金属或多层金属带材 ➢ 包覆型双金属线、板、带材
轧制特殊性能材料:
➢ 弥散强化型合金带材 ➢ 电工电子材料、磁性材料和超导材料 ➢ 耐磨、摩擦材料 ➢ 硬质合金、超硬工具材料
粉末挤压成型
➢什么是粉末挤压成型 ➢粉末挤压成型应用与特点 ➢坯料受力分析 ➢热挤压成型
什么是粉末挤压成型
什么是粉末挤压成型
原理:
什么是粉末挤压成型
粉末挤压成型的应用
➢ 管、棒、条及其他异型产品(齿轮、腰鼓形、 麻花形等)
➢ 金属、合金、复合材料、金属间化合物、陶 瓷
➢ 广泛应用于电子、机械、航空、汽车等领域
粉末挤压成型的应用
➢ 打印机打印针 ➢切烟滚刀 ➢WC-Co微型麻花钻 ➢碳化物棒材 ➢……
粉末轧制成形
➢轧制成形原理
➢轧制成形工艺
➢轧制成形的应用
轧制成形原理
三个不同状态的区 咬入角 咬入厚度
咬入角α
T cos Q R sin
T R tan Q R cos
tan
摩擦系数与侧压系数之和大于咬入角的正切
主要变形系数
质量守恒方程: HB1V1 hb2V2
带坯宽展很小时
热轧制成形
轧制成形的应用
粉末轧制成型的优点 ➢ 能生产常规轧制法难以生产或无法生产
的带材、板材 ➢ 能生产成分精确的带材、板材 ➢ 工艺简单、成本低、节能 ➢ 成材率高 ➢ 设备投资少
轧制成形的应用
轧制金属、合金的致密板、带材
轧制成形的应用
轧制成形的应用
轧制金属、合金的多孔板、带材
轧制成形的应用
H V2 2 h V1 1
H ; V2 ;Z 2
h
V1
粉末冶金成型的工艺过程

粉末冶金成型的工艺过程粉末冶金成型是一种利用粉末金属和其他复合材料制作各种形状和大小的零件的工艺,是一种广泛应用于航空航天、船舶、汽车、石油、机械制造和精密仪器等领域的一种重要工艺。
粉末冶金成型的工艺过程主要包括粉末成形、热处理和表面处理三个步骤。
首先,粉末成形。
将粉末金属或复合材料放入型腔内,然后用轧制机将其压实,形成特定的零件形状。
一般分两种方法:一种是热压成型,将粉末金属或复合材料装入型腔,然后将其加热,并用压力将其压实,使其形成所需的零件形状;另一种是压力成形,将粉末金属或复合材料装入型腔,然后用压力将其压实,使其形成所需的零件形状。
其次,热处理。
热处理对粉末冶金成型产品具有重要意义,其目的是改善材料的力学性能、改变材料的组织结构、调节材料的组织参数、提高材料的硬度和韧性等。
热处理可分为正火处理和回火处理两种,根据所需要的效果,可选用不同的工艺方式,如火焰热处理、氩弧焊热处理、电火花热处理等。
最后,表面处理。
表面处理的目的是使粉末冶金成型后的零件具有良好的外观和耐磨性,并且提高其耐腐蚀性。
表面处理的方法多种多样,如电镀、阳极氧化、氧化处理、涂装、抛光等。
由于粉末冶金成型产品的表面粗糙度较高,一般需要进行抛光处理,以改善表面光洁度和表面粗糙度。
粉末冶金成型的过程比较复杂,需要经过粉末成形、热处理和表面处理这三个步骤,才能得到满足要求的零件。
粉末冶金成型工艺具有加工复杂形状零件的优势,具有节约材料、提高加工精度、改善性能和缩短交货期等优点,已成为航空航天、船舶、汽车、石油、机械制造和精密仪器等领域的重要工艺。
Secondly, heat treatment. Heat treatment is of great significance to powder metallurgy forming products, which aims to improve the mechanical properties of materials, change the structure of materials, adjust the organization parameters of materials, increase the hardness and toughness of materials, etc. Heat treatment can be divided into two types: normalizing and annealing, different process can be selected according to the required effect, such as flame heat treatment, argon arc welding heat treatment, electric spark heat treatment, etc.。
粉末冶金原理
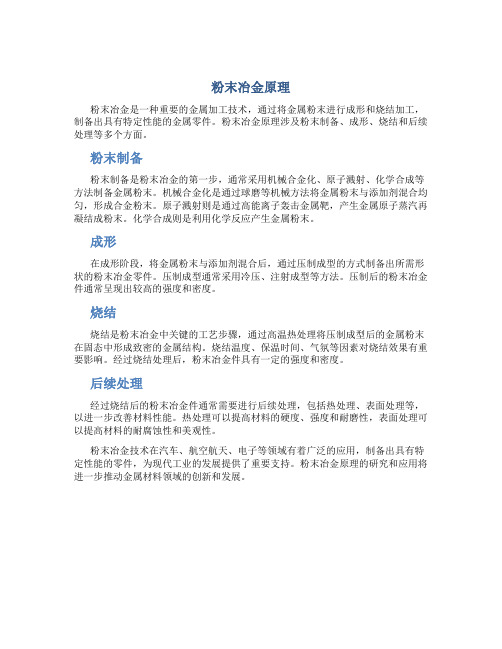
粉末冶金原理
粉末冶金是一种重要的金属加工技术,通过将金属粉末进行成形和烧结加工,制备出具有特定性能的金属零件。
粉末冶金原理涉及粉末制备、成形、烧结和后续处理等多个方面。
粉末制备
粉末制备是粉末冶金的第一步,通常采用机械合金化、原子溅射、化学合成等方法制备金属粉末。
机械合金化是通过球磨等机械方法将金属粉末与添加剂混合均匀,形成合金粉末。
原子溅射则是通过高能离子轰击金属靶,产生金属原子蒸汽再凝结成粉末。
化学合成则是利用化学反应产生金属粉末。
成形
在成形阶段,将金属粉末与添加剂混合后,通过压制成型的方式制备出所需形状的粉末冶金零件。
压制成型通常采用冷压、注射成型等方法。
压制后的粉末冶金件通常呈现出较高的强度和密度。
烧结
烧结是粉末冶金中关键的工艺步骤,通过高温热处理将压制成型后的金属粉末在固态中形成致密的金属结构。
烧结温度、保温时间、气氛等因素对烧结效果有重要影响。
经过烧结处理后,粉末冶金件具有一定的强度和密度。
后续处理
经过烧结后的粉末冶金件通常需要进行后续处理,包括热处理、表面处理等,以进一步改善材料性能。
热处理可以提高材料的硬度、强度和耐磨性,表面处理可以提高材料的耐腐蚀性和美观性。
粉末冶金技术在汽车、航空航天、电子等领域有着广泛的应用,制备出具有特定性能的零件,为现代工业的发展提供了重要支持。
粉末冶金原理的研究和应用将进一步推动金属材料领域的创新和发展。
粉末冶金 (1)
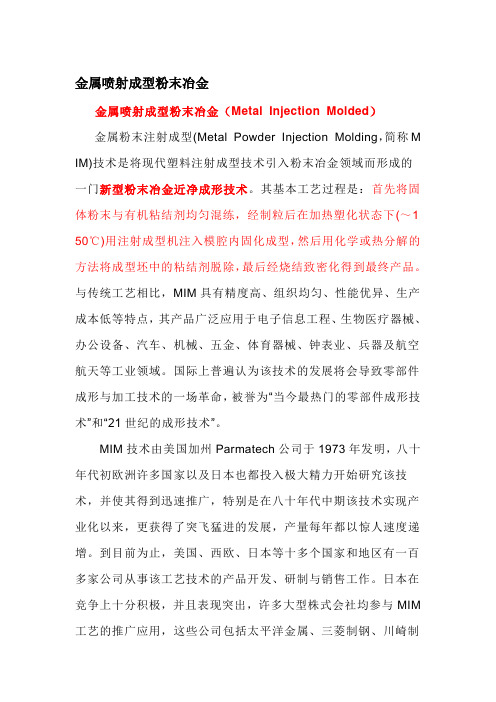
金属喷射成型粉末冶金金属喷射成型粉末冶金(Metal Injection Molded)金属粉末注射成型(Metal Powder Injection Molding,简称M IM)技术是将现代塑料注射成型技术引入粉末冶金领域而形成的一门新型粉末冶金近净成形技术。
其基本工艺过程是:首先将固体粉末与有机粘结剂均匀混练,经制粒后在加热塑化状态下(~1 50℃)用注射成型机注入模腔内固化成型,然后用化学或热分解的方法将成型坯中的粘结剂脱除,最后经烧结致密化得到最终产品。
与传统工艺相比,MIM具有精度高、组织均匀、性能优异、生产成本低等特点,其产品广泛应用于电子信息工程、生物医疗器械、办公设备、汽车、机械、五金、体育器械、钟表业、兵器及航空航天等工业领域。
国际上普遍认为该技术的发展将会导致零部件成形与加工技术的一场革命,被誉为“当今最热门的零部件成形技术”和“21世纪的成形技术”。
MIM技术由美国加州Parmatech公司于1973年发明,八十年代初欧洲许多国家以及日本也都投入极大精力开始研究该技术,并使其得到迅速推广,特别是在八十年代中期该技术实现产业化以来,更获得了突飞猛进的发展,产量每年都以惊人速度递增。
到目前为止,美国、西欧、日本等十多个国家和地区有一百多家公司从事该工艺技术的产品开发、研制与销售工作。
日本在竞争上十分积极,并且表现突出,许多大型株式会社均参与MIM 工艺的推广应用,这些公司包括太平洋金属、三菱制钢、川崎制铁、神户制钢、住友矿山、精工-爱普生、大同特殊钢等。
目前日本有四十多家专业从事MIM产业的公司,其MIM产品的销售总值早已超过欧洲并直追美国。
MIM技术已成为新型制造业中最为活跃的前沿技术领域,是世界冶金行业的开拓性技术,代表着粉末冶金技术发展的主方向。
金属粉末注射成型技术是塑料成型工艺学、高分子化学、粉末冶金工艺学和金属材料学等多学科渗透与交叉的产物,利用模具可注射成型坯件并通过烧结快速制造高密度、高精度、三维复杂形状的结构零件,能够快速、准确地将设计思想物化为具有一定结构、功能特性的制品,并可直接批量生产出零件,是制造技术行业一次新的变革。
粉末压制及烧结方法
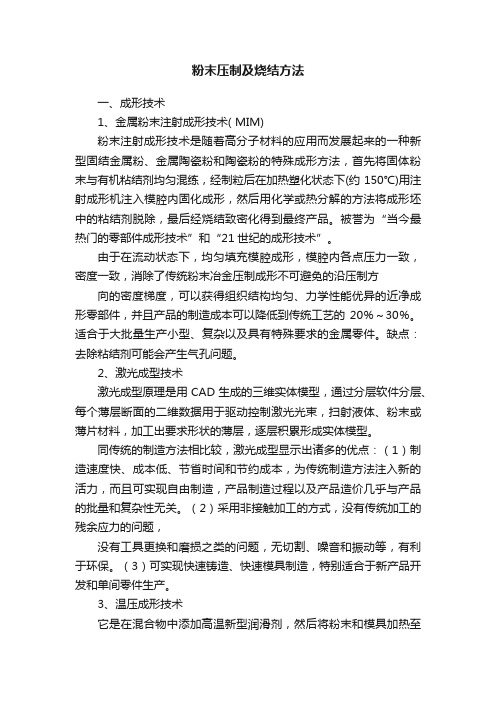
粉末压制及烧结方法一、成形技术1、金属粉末注射成形技术( MIM)粉末注射成形技术是随着高分子材料的应用而发展起来的一种新型固结金属粉、金属陶瓷粉和陶瓷粉的特殊成形方法,首先将固体粉末与有机粘结剂均匀混练,经制粒后在加热塑化状态下(约150℃)用注射成形机注入模腔内固化成形,然后用化学或热分解的方法将成形坯中的粘结剂脱除,最后经烧结致密化得到最终产品。
被誉为“当今最热门的零部件成形技术”和“21世纪的成形技术”。
由于在流动状态下,均匀填充模腔成形,模腔内各点压力一致,密度一致,消除了传统粉末冶金压制成形不可避免的沿压制方向的密度梯度,可以获得组织结构均匀、力学性能优异的近净成形零部件,并且产品的制造成本可以降低到传统工艺的20%~30%。
适合于大批量生产小型、复杂以及具有特殊要求的金属零件。
缺点:去除粘结剂可能会产生气孔问题。
2、激光成型技术激光成型原理是用CAD生成的三维实体模型,通过分层软件分层、每个薄层断面的二维数据用于驱动控制激光光束,扫射液体、粉末或薄片材料,加工出要求形状的薄层,逐层积累形成实体模型。
同传统的制造方法相比较,激光成型显示出诸多的优点:(1)制造速度快、成本低、节省时间和节约成本,为传统制造方法注入新的活力,而且可实现自由制造,产品制造过程以及产品造价几乎与产品的批量和复杂性无关。
(2)采用非接触加工的方式,没有传统加工的残余应力的问题,没有工具更换和磨损之类的问题,无切割、噪音和振动等,有利于环保。
(3)可实现快速铸造、快速模具制造,特别适合于新产品开发和单间零件生产。
3、温压成形技术它是在混合物中添加高温新型润滑剂,然后将粉末和模具加热至150℃左右进行刚性模压制,最后采用传统的烧结工艺进行烧结的技术,是普通模压技术的发展与延伸。
该技术主要有以下几个方面的特点:能以较低的成本制造出高性能的铁基等粉末冶金零部件;提高零部件生坯密度;产品具有高强度;便于制造形状复杂以及要求精密的零部件;密度均匀等该技术目前主要用于生产铁基合金零件,同时人们正在研究用这种技术制备铜基合金、钛合金等其它材料零件。
粉末冶金注射成型工艺
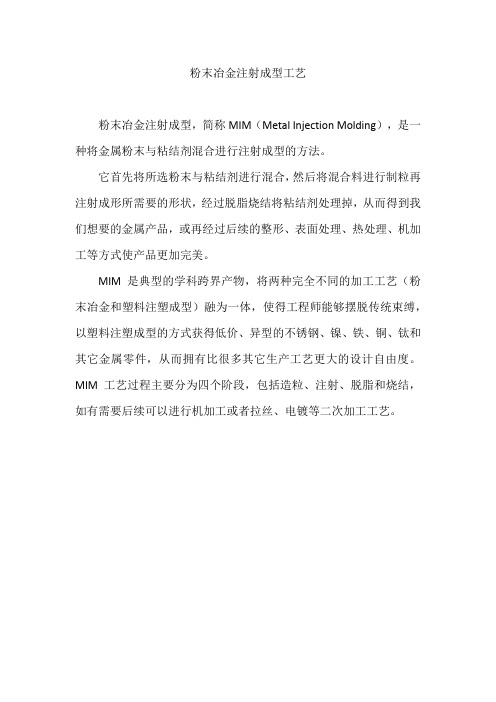
粉末冶金注射成型工艺
粉末冶金注射成型,简称MIM(Metal Injection Molding),是一种将金属粉末与粘结剂混合进行注射成型的方法。
它首先将所选粉末与粘结剂进行混合,然后将混合料进行制粒再注射成形所需要的形状,经过脱脂烧结将粘结剂处理掉,从而得到我们想要的金属产品,或再经过后续的整形、表面处理、热处理、机加工等方式使产品更加完美。
MIM是典型的学科跨界产物,将两种完全不同的加工工艺(粉末冶金和塑料注塑成型)融为一体,使得工程师能够摆脱传统束缚,以塑料注塑成型的方式获得低价、异型的不锈钢、镍、铁、铜、钛和其它金属零件,从而拥有比很多其它生产工艺更大的设计自由度。
MIM工艺过程主要分为四个阶段,包括造粒、注射、脱脂和烧结,如有需要后续可以进行机加工或者拉丝、电镀等二次加工工艺。
粉末冶金成形

• 则得:
ln P l ( 1) C
• 在压力达最大值Pmax即压制终点时相对体积 β=1,所以(β-1)=0,则 • C=lnPmax 所以有: ln P l ( 1) ln P
max
•
•
lnPmax lnP lnP
• • •
β=1 β β
• 巴尔申方程示意图
代人上式得: 两边取对数,则上式变为:
ln P ln S 截 m ln
当压制到最大压力时,ρ 等于1, 所以得:
ln Pmax ln S 截 , 则S 截 Pmax
则可得:
ln P ln Pmax
P m ln , 或 m Pmax
m
或
P Pmax
铁-硫0.3%-石墨2.2%-硬脂酸 锌
青铜6-6-3-石墨0.75%-硬脂酸 锌
530 860
380 460 490 530
1.137 0.12-0.14
1. 085 0.088-0.100 1. 08 2. 0.09
1.09 0.08
•05 0.05-0.06 1.05 0.06
纯铁
纯铜
390
235 490
v sh h v k s k hk hk
dp dm
g / v v k hk 1 g / vk v h
1 , 1
由
代入上式则得:
dh d hk
dP dh k " k " d S hK P S
由虎克定律
代入上式得:
几种粉末与模壁之间的摩擦系数
粉末成分 铁-铜2.5-3%-石墨0.8-0.85%硬脂酸锌0.8% 铁-硫0.3%-石墨1.2%-硬脂酸 锌 860 单位压制压力 MPa 380 530 860 静摩擦系数 μ 静 1.140 2.175 0.17-0.19 0.15 动摩擦系数 μ 动 1.084 •105 0.110 0.10
- 1、下载文档前请自行甄别文档内容的完整性,平台不提供额外的编辑、内容补充、找答案等附加服务。
- 2、"仅部分预览"的文档,不可在线预览部分如存在完整性等问题,可反馈申请退款(可完整预览的文档不适用该条件!)。
- 3、如文档侵犯您的权益,请联系客服反馈,我们会尽快为您处理(人工客服工作时间:9:00-18:30)。
温压成形
温压成形可以显著提高压坯密度的机理一般归于在加热状态下, 粉末的屈服强度降低(如下图)和润滑剂作用增强。在材料达到 同等密度的前提下,温压成形工艺的生产成本比粉末锻造低75 %,比“复压/复烧”低25%,比渗铜低15%;在零件达到同 等力学性能和加工精度的前提下,温压成形工艺的生产提高10~30 倍。
粉末冶金的主要成形方法
粉末成形是将松散的粉末体加工成具有一定尺寸、形状、 密度和强度的压坯的工艺过程,它可分为普通模压成形和 非模压成形两大类。普通模压成形是将金属粉末或混合粉 末装在压模内,通过压力机加压成形,这种传统的成形方 法在粉末冶金生产中占主导地位;非模压成形主要有等静 压成形、连续轧制成形、喷射成形、注射成形等。
温压成形
温压成形的基本工艺过程是将专用金属或合金粉末与聚合 物润滑剂混合后,采用特制的粉末加热系统、粉末输送系 统和模具加热系统,升温到75~150℃,压制成压坯,再 经预烧、烧结、整形等工序,可获得密度高至7.2~ 7.5g/cm3的铁基粉末冶金件。
温压成形的工艺流程
温压装置及其温度分布系统示意图
热压加热方式
1-碳管;2-粉末压坯;3-阴模;4-冲头
轧制成形
轧制成形是将金属粉末通过一个特制的漏斗喂入 转动的轧辊缝中,可轧出具有一定厚度的、长度 连续的、且强度适宜的板带坯料。这些坯料经预 烧结、烧结,又经轧制加工和热处理等工序,可 制成有一定孔隙率的或致密的粉末冶金板带材。 与模压成形相比,粉末轧制法的优点是制品的长 度可不受限制、轧制制品密度较为均匀。但是, 由轧制法生产的带材厚度受轧辊直径的限制,一 般不超过10mm,宽度也受到轧辊宽度的限制。轧制 成形只能制取形状较简单的板带及直径与厚度比 值很大的衬套。
温压对纯铁粉屈服强度的影响
温压成形
温压成形因其成本低、密度高、模具寿命长、效率高、工艺简 单、易精密成形和可完全连续化、自动化等一系列优点而受到 关注,被认为是20世纪90年代粉末冶金零件致密化技术的一项 重大突破,被誉为“开创粉末冶金零件应用新纪元的一项新型 制造技术”。该技术已广泛应用于制造汽车零件和磁性材料制 品,如蜗轮轮毂、复杂形状齿轮、发动机连杆等。
模压成形
温压成形
热压成形
轧制成形
模压成形
模压成形是指粉料在常温下、在封闭的钢模中、按规定的压力 下(一般为150~600MPa)、在普通机械式压力机或自动液压机 上将粉料制成压坯的方法。当对压模中的粉末施加压力后,粉 末颗粒间将发生相对移动,粉末颗粒将填充孔隙,使粉末体的 体积减小,粉末颗粒迅速达到最紧密的堆积。
模压成形
模压成形工装设备简单、成本低,但由于压力分布不均匀, 会使压坯各个部分的密度分布不均匀而影响制品零件的性 能,适用于简单零件、小尺寸零件的成形。但普通模压成 形仍然是粉末冶金行业中最常见的一种工艺方法,通常经 历称粉、装粉、压制、保压、脱模等工序。
模压成形的基本步骤
A-装粉;b-压制;c-脱模
粉末轧制成形
热压成形
热压成形又称为加热烧结,是把粉末装在模腔内,在加压 的同时,使粉末加热到正常烧结温度或更低一些,经过较 短的烧结时间,获得致密而均匀的制品。热压可将压制和 烧结两个工序一并完成,可在较低压力下迅速获得冷压烧 结所达不到的密度,适用于制造全致密难熔金属及其化合 物等材料。热压成形的最大优点是可以大大降低成形压力 和缩短烧结时间,制得密度较高和晶粒较细的材料或制品。 热压模可选用高速钢及其他耐热合金,但使用温度应在 800℃以下。当温度更高(1500~2000℃)时,应采用石墨 材料制作模具,但承压能力要降低到70MPa以下。热压成 形加热的方式分为电阻间接加热式、电阻直接加热式、感 应加热式三种。为了减少空气中氧的危害,真空热压机已 得到广泛应用。