顺铣与逆铣
顺铣和逆铣的区别及如何选择

在圆周铣削加工中,铣刀旋转切入工件方向和切削进给方向相反。
顺铣与逆铣的区别
当切削刃刚进行切削时,在逆铣中,切削厚度为最小值,在顺铣中则是达到其最大值。
一般而言,在逆铣中刀具寿命比在顺铣中短,这是因为在逆铣中产生的热量比在顺铣中明显地高。
在逆铣中当切屑厚度从零增加到最大时,切削刃受到的摩擦比在顺铣中强因而会产生更多的热量。
逆铣中径向力也明显高,这对主轴轴承有不利影响。
在顺铣中,切削刃主要受到的是压缩应力,这与逆铣中产生的拉力相比,对硬质合金刀片或整体硬质合金刀具的影响有利得多。
因此,应尽可能多使用顺铣。
使用逆铣的情况
1.当使用整体硬质合金立铣刀进行侧铣时,特别是在淬硬材料中,逆铣是首选。
这更容易获得更小公差的壁直线度和更好的90度角。
不同轴向走刀之间如果有不重合的话,接刀痕也非常小。
这主要是因为切削力的方向。
如果在切削中使用非常锋利的切削刃,切削力便趋向将刀“拉”向材料。
2.可以使用逆铣的另一个例子是,使用老式手动铣床进行铣削,老式铣床的丝杠有较大的间隙。
逆铣产生消除间隙的切削力,使铣削动作更平稳。
铣工的顺铣与逆铣ppt课件

三、切削特点
• 1、顺铣特点:顺铣时,铣刀刀刃的切削厚度由最 大到零,不存在滑行现象,刀具磨损较小,工件冷 硬程度较轻。垂直分力Fv向下,对工件有一个压紧 作用,有利于工件的装夹。但是水平分力Fh方向与 工件进给方向相同,不利于消除工件台丝杆和螺母 间的间隙,切削时振动大。但其表面光洁度较好, 适合精加工。
G03X-20Y30R20
G40X-62Y52
G00Z50
X0Y0
M30
13
G02I-15J0
G40G01X62Y0
G00Z50
X0Y0
M30
10
典型零件的数控铣削加工工艺分析
粗加工H9的第二级凸台
%0021
G54
M04S500
G00X-62Y52
Z5
G01Z-9F100
G41G01X-40Y30D01F200
G01X30
G02X40Y20R10
G01Y-20
G02X30Y-30R10
加
至
工
15%
7
四、顺铣和逆铣的选择原则
(1)机床精度好、刚性好、精加工,较适应 顺铣。反之较适应逆铣。
(2)零件内拐角处精加工强烈建议要用顺铣。 (3)粗加工:逆铣较好。精加工:顺铣较好
8
典型零件的数控铣削加工工艺分析
外形轮廓加工
这个图像在我们不平端面的 情况下我们可以分成两段程 序加工: 1,加工ɸ30高度H4的凸台 2,加工H9的第二级凸台
§1.5 铣削重要常识 ——顺铣与逆铣
1
在加工中,铣刀的旋转方向一般是不变 的,但进给方向是变化的。就出现了铣 削加工中常见的两种现象:顺铣与逆铣。
2
二、顺铣和逆铣的定义
顺铣和逆铣的定义

顺铣和逆铣的定义
顺铣和逆铣是金属加工中的两种铣削方式,用于对工件进行表面加工和形状修整。
顺铣(Conventional milling)是指工件相对于刀具的转动方向
与切削速度方向相同的铣削方式。
在顺铣中,刀具从工件的边缘或者表面进入,并沿着工件逆时针方向旋转。
这样铣削过程中,切屑产生的方向与刀具移动方向相反。
顺铣适用于大多数铣削操作,可以获得较好的表面质量和切削稳定性。
逆铣(Climb milling)是指工件相对于刀具的转动方向与切削
速度方向相反的铣削方式。
在逆铣中,刀具从工件的边缘或者表面进入,并沿着工件顺时针方向旋转。
这样铣削过程中,切屑产生的方向与刀具移动方向相同。
逆铣具有较小的切削力,有助于提高加工效率和表面质量,但在具体的铣削操作中要注意刀具的选择和工艺参数的合理确定,以克服切削阻力引起的振动和过载等问题。
选择顺铣还是逆铣需要根据具体的加工要求和工件材料来确定,一般而言,顺铣适用于大多数情况下的铣削操作,而逆铣适用于加工难度较大、材料硬度较高的工件,或者要求极高表面质量的情况。
顺铣与逆铣
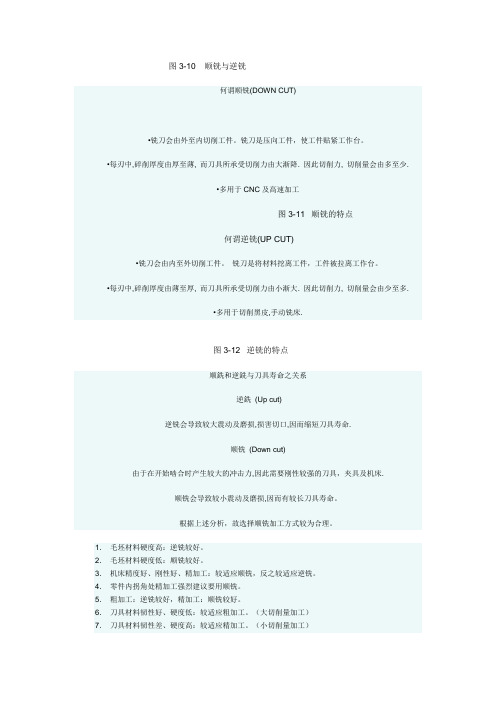
图3-10 顺铣与逆铣何谓顺铣(DOWN CUT)•铣刀会由外至内切削工件。
铣刀是压向工件,使工件贴紧工作台。
•每刃中,碎削厚度由厚至薄, 而刀具所承受切削力由大渐降. 因此切削力, 切削量会由多至少.•多用于CNC及高速加工图3-11 顺铣的特点何谓逆铣(UP CUT)•铣刀会由内至外切削工件。
铣刀是将材料挖离工件,工件被拉离工作台。
•每刃中,碎削厚度由薄至厚, 而刀具所承受切削力由小渐大. 因此切削力, 切削量会由少至多.•多用于切削黑皮,手动铣床.图3-12 逆铣的特点顺銑和逆銑与刀具寿命之关系逆銑(Up cut)逆铣会导致较大震动及磨损,损害切口,因而缩短刀具寿命.顺铣(Down cut)由于在开始啮合时产生较大的冲击力,因此需要刚性较强的刀具,夹具及机床.顺铣会导致较小震动及磨损,因而有较长刀具寿命。
根据上述分析,故选择顺铣加工方式较为合理。
1.毛坯材料硬度高:逆铣较好。
2.毛坯材料硬度低:顺铣较好。
3.机床精度好、刚性好、精加工:较适应顺铣,反之较适应逆铣。
4.零件内拐角处精加工强烈建议要用顺铣。
5.粗加工:逆铣较好,精加工:顺铣较好。
6.刀具材料韧性好、硬度低:较适应粗加工。
(大切削量加工)7.刀具材料韧性差、硬度高:较适应精加工。
(小切削量加工)1、A顺铣:铣刀对工件作用力F c在垂直方向分力F N始终向下,对工件起压紧作用,切削平稳,适于不易夹紧或细长薄板形工件。
逆铣:垂直分力F N向上,工件需较大的夹紧力。
B顺铣:铣刀刀刃切入工件初,切屑厚度最大,逐渐减小到0。
后刀面与已加工表面挤压、摩擦小,刀刃磨损慢,表面质量好。
逆铣:切屑厚度从0到最大,因刀刃不能刃磨绝对锋利,故开始时不能立即切入工件,存在对工件挤压与摩擦。
工件出现加工硬化,降低表面质量。
此外,刀齿磨损快耐用度降低。
C 顺铣:水平分力F f与工作台进给方向相同,当工作台进给丝杠与螺母间隙较大,工作台易出现轴向窜动。
导致刀齿折断,刀轴弯曲,工件与夹具产生位移甚至机床损坏。
顺铣和逆铣的特点
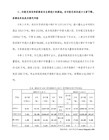
顺铣时刀齿的切削厚度是从最大到零,但刀齿切入工件时的冲击力较大,尤其工件待加工表面是毛坯或者有硬皮时。
(2)切削力ห้องสมุดไป่ตู้向的影响
顺铣时作用于工件上的垂直切削分力FfN始终压下工件 ,这对工件的夹紧有利。
逆铣时FfN 向上,有将工件抬起的趋势,易引起振动,影响工件的夹紧。铣薄壁和刚度差工件时影响更大。
1)逆铣 铣刀旋转方向与工件进给方向相反。铣削时每齿切削厚度从零逐渐到最大而后切出。
(2)顺铣 铣刀旋转方向与工件进给方向相同。铣削时每齿切削厚度从最大逐渐减小到零。特点:
(1)切削厚度的变化
逆铣时,每个刀齿的切削厚度由零增至最大。但切削刃并非绝对锋利,铣刀刃口处总有圆弧存在,刀齿不能立刻切入工件,而是在已加工表面上挤压滑行,使该表面的硬化现象严重,影响了表面质量,也使刀齿的磨损加剧。
铣床工作台的移动是由丝杠螺母传动的,丝杠螺母间有螺纹间隙。顺铣时工件受到纵向分力Ff与进给运动方向相同,而一般主运动的速度大于进给速度υf,因此纵向分成Ff有使接触的螺纹传动面分离的趋势,当铣刀切到材料上的硬点或因切削厚度变化等原因,引起纵向分力F f 增大,超过工作台进给摩擦阻力时,原是螺纹副推动的运动形式变成了由铣刀带动工作台窜动的运动形式,引起进给量突然增加。这种窜动现象不但会引起“扎刀”,损坏加工表面;严重时还会使刀齿折断,或使工件夹具移位,甚至损坏机床。
顺铣与逆铣的区别
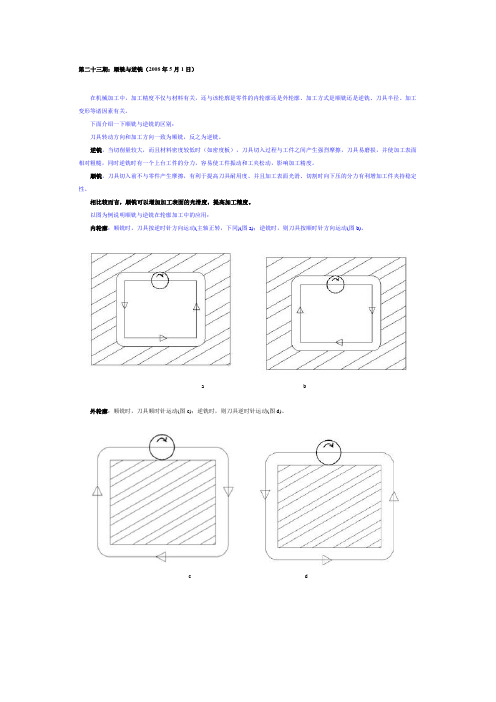
第二十三期:顺铣与逆铣(2008年5月1日)
在机械加工中,加工精度不仅与材料有关,还与该轮廓是零件的内轮廓还是外轮廓、加工方式是顺铣还是逆铣、刀具半径、加工变形等诸因素有关。
下面介绍一下顺铣与逆铣的区别:
刀具转动方向和加工方向一致为顺铣,反之为逆铣。
逆铣,当切削量较大,而且材料密度较低时(如密度板),刀具切入过程与工件之间产生强烈摩擦,刀具易磨损,并使加工表面相对粗糙,同时逆铣时有一个上台工件的分力,容易使工件振动和工夹松动,影响加工精度。
顺铣,刀具切入前不与零件产生摩擦,有利于提高刀具耐用度、并且加工表面光滑、切割时向下压的分力有利增加工件夹持稳定性。
相比较而言,顺铣可以增加加工表面的光滑度,提高加工精度。
以图为例说明顺铣与逆铣在轮廓加工中的应用:
内轮廓:顺铣时,刀具按逆时针方向运动(主轴正转,下同)(图a);逆铣时,则刀具按顺时针方向运动(图b)。
a b
外轮廓:顺铣时,刀具顺时针运动(图c);逆铣时,则刀具逆时针运动(图d)。
c d。
顺铣或者逆铣

1. 刚性好(尤 其是粗加工 刀具)、精度 高、抗振及 热变形小;
2. 互换性 好,便于快 速换刀;
3. 寿命高, 切削性能稳 定、可靠;
4. 刀具的尺 寸便于调 整,以减少 换刀调整时 间;
5. 刀具应能 可靠地断屑 或卷屑,以 利于切屑的 排除;
在进行自由 曲面(模具) 加工时,由 于球头刀具 的端部切削 速度为零, 因此,为保 证加工精 度,切削行 距一般采用 顶端密距, 故球头常用 于曲面的精 加工。而平 头刀具在表 面加工质量 和切削效率 方面都优于 球头刀,因 此,只要在 保证不过切 的前提下, 无论是曲面 的粗加工还 是精加工, 都应优先选 择平头刀。 另外,刀具 的耐用度和 精度与刀具 价格关系极 大,必须引 起注意的 是,在大多 数情况下, 选择好的刀 具虽然增加 了刀具成
1. 切削深度 ap。在机床 、工件和刀 具刚度允许 的情况下, ap就等于加 工余量,这 是提高生产 率的一个有 效措施。为 了保证零件 的加工精度 和表面粗糙 度,一般应 留一定的余 量进行精加 工。数控机 床的精加工 余量可略小 于普通机床 。
2. 切削宽度 L。一般L与 刀具直径d成 正比,与切 削深度成反 比。经济型 数控机床的 加工过程 中,一般L的 取值范围 为:L=(0.6 ~0.9)d。
在经济型数 控机床的加 工过程中, 由于刀具的 刃磨、测量 和更换多为 人工手动进 行,占用辅 助时间较 长,因此, 必须合理安 排刀具的排 列顺序。一 般应遵循以 下原则:① 尽量减少刀 具数量;② 一把刀具装 夹后,应完 成其所能进 行的所有加 工步骤;③ 粗精加工的 刀具应分开 使用,即使 是相同尺寸 规格的刀 具;④先铣 后钻 ;⑤先 进行曲面精 加工,后进 行二维轮廓 精加工;⑥ 在可能的情 况下,应尽 可能利用数 控机床的自 动换刀功
浅析顺铣与逆铣
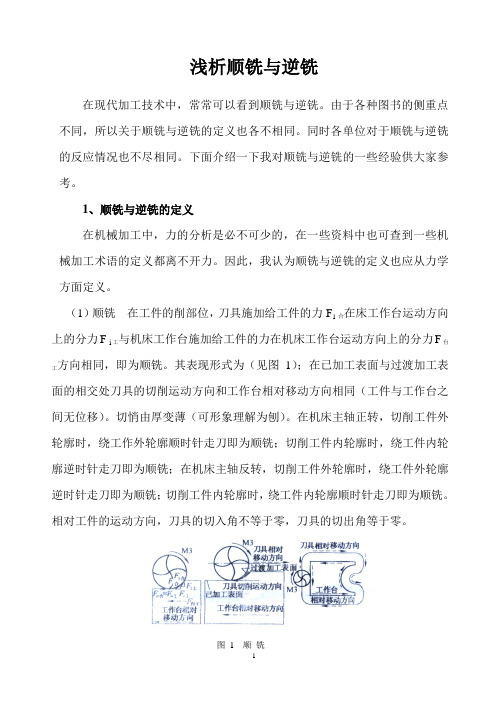
浅析顺铣与逆铣在现代加工技术中,常常可以看到顺铣与逆铣。
由于各种图书的侧重点不同,所以关于顺铣与逆铣的定义也各不相同。
同时各单位对于顺铣与逆铣的反应情况也不尽相同。
下面介绍一下我对顺铣与逆铣的一些经验供大家参考。
1、顺铣与逆铣的定义在机械加工中,力的分析是必不可少的,在一些资料中也可查到一些机械加工术语的定义都离不开力。
因此,我认为顺铣与逆铣的定义也应从力学方面定义。
(1)顺铣在工件的削部位,刀具施加给工件的力F1合在床工作台运动方向上的分力F i工与机床工作台施加给工件的力在机床工作台运动方向上的分力F台1);在已加工表面与过渡加工表工方向相同,即为顺铣。
其表现形式为(见图面的相交处刀具的切削运动方向和工作台相对移动方向相同(工件与工作台之间无位移)。
切悄由厚变薄(可形象理解为刨)。
在机床主轴正转,切削工件外轮廓时,绕工作外轮廓顺时针走刀即为顺铣;切削工件内轮廓时,绕工件内轮廓逆时针走刀即为顺铣;在机床主轴反转,切削工件外轮廓时,绕工件外轮廓逆时针走刀即为顺铣;切削工件内轮廓时,绕工件内轮廓顺时针走刀即为顺铣。
相对工件的运动方向,刀具的切入角不等于零,刀具的切出角等于零。
图 1 顺铣(2)逆铣在工件的切削部位,刀具施加给工件的力F1合在机床工作合运动方向上的分力F i工与机床工作台施加给工件的力在机床工作台运动方向上分力F台工方向相反,即为逆铣。
其表现形式为(见图2):在已加工表面与过渡加工面的相交处刀具的切削运动方向和工作台的移动方向相反(工件与工作台之间无位移),切屑由薄变厚(可形象理解为挖)。
在机床主轴正转,切削工件外轮廓时,绕工件外轮廓逆时针走刀即为逆铣;切削工件内轮廓时,绕工件内轮廓顺时针走刀即为逆铣;在机床主轴反转3时,切削工件外轮廓时,绕工件外轮廓顺时针走刀即为逆铣;切削工件内轮廓时,绕工件内轮廓逆时针走刀即逆顺铣。
相对工件的运动方向,刀具的切入角等于零,刀具的切出角不等于零。
图 2 逆铣2、顺铣与逆铣对切削的影响在不考虑机床主轴刚性的情况下,机床间隙与切削加工时刀具所产生的弹性弯曲变形最终都将会反应在工件上。
顺铣和逆铣

1)工件运动方向与刀具旋转方向相同时为顺铣2)工件运动方向与刀具旋转方向相反时为逆铣沿着刀具的进给方向看,如果工件位于铣刀进给方向的右侧,那么进给方向称为顺时针。
反之,当工件位于铣刀进给方向的左侧时,进给方向定义为逆时针。
如果铣刀旋转方向与工件进给方向相同,称为顺铣;铣刀旋转方向与工件进给方向相反,称为逆铣。
逆铣时,切削由薄变厚,刀齿从已加工表面切入,对铣刀的使用有利。
逆铣时,当铣刀刀齿接触工件后不能马上切入金属层,而是在工件表面滑动一小段距离,在滑动过程中,由于强烈的磨擦,就会产生大量的热量,同时在待加工表面易形成硬化层,降低了刀具的耐用度,影响工件表面光洁度,给切削带来不利。
另外,逆铣时,由于刀齿由下往上(或由内往外)切削。
顺铣时,刀齿开始和工件接触时切削厚度最大,且从表面硬质层开始切入,刀齿受很大的冲击负荷,铣刀变钝较快,但刀齿切入过程中没有滑移现象。
顺铣的功率消耗要比逆铣时小,在同等切削条件下,顺铣功率消耗要低5%~15%,同时顺铣也更加有利于排屑。
一般应尽量采用顺铣法加工,以提高被加工零件表面的光洁度(降低粗糙度),保证尺寸精度。
但是在切削面上有硬质层、积渣、工件表面凹凸不平较显著时,如加工锻造毛坯,应采用逆铣法。
顺铣和逆铣的特点1.逆铣时,每个刀的切削厚度都是有小到大逐渐变化的。
当刀齿刚与工件接触时,切削厚度为零,只有当刀齿在前一刀齿留下的切削表面上滑过一段距离,切削厚度达到一定数值后,刀齿才真正开始切削。
顺铣使得切削厚度是由大到小逐渐变化的,刀齿在切削表面上的滑动距离也很小。
而且顺铣时,刀齿在工件上走过的路程也比逆铣短。
因此,在相同的切削条件下,采用逆铣时,刀具易磨损。
2.逆铣时,由于铣刀作用在工件上的水平切削力方向与工件进给运动方向相反,所以工作台丝杆与螺母能始终保持螺纹的一个侧面紧密贴合。
而顺铣时则不然,由于水平铣削力的方向与工件进给运动方向一致,当刀齿对工件的作用力较大时,由于工作台丝杆与螺母间间隙的存在,工作台会产生窜动,这样不仅破坏了切削过程的平稳性,影响工件的加工质量,而且严重时会损坏刀具。
顺铣和逆铣

顺铣和逆铣Document serial number【LGGKGB-LGG98YT-LGGT8CB-LGUT-LGG08】顺铣和逆铣1、顺铣和逆铣2、答:在切削部位刀齿的旋转方向和零件的进给方向相同时为顺铣。
在切削部位刀齿的旋转方向和零件的进给方向相反时为逆铣。
3、2、机械加工结构工艺性4、答:指零件所具有的结构是否便于制造、装配和拆卸。
5、3、定位与夹紧6、答:加工时,首先要把零件安装在工作台或夹具里,使它和刀具之间有正确的相对位置,这就是定位。
零件定位后,在加工过程中要保持正确的位置不变,才能得到所要求的尺寸精度,因此必须把零件夹住,这就是夹紧7、4、标注角度与工作角度8、答:刀具的标注角度是刀具制造和刃磨的依据,主要有:前角、后角、主偏角、副偏角和刃倾角。
切削加工过程中,由于刀具安装位置的变化和进给运动的影响,使得参考平面坐标系的位置发生变化,从而导致了刀具实际角度与标注角度的不同。
刀具在工作中的实际切削角度称为工作角度。
9、10、11、5、积屑瘤12、第Ⅱ变形区内,在一定范围的切削速度下切削塑性材料且形成带状刀屑时,常有一些来自切削底层的金属黏接层积在前刀面上,形成硬度很高的楔块,称为积屑瘤。
13、、简述前角、后角的改变对切削加工的影响。
14、答:在主剖面内测量的前刀面与基面之间的夹角为前角。
适当增加前角,则主切削刃锋利,切屑变形小,切削轻快,减小切削力和切削热。
但前角过大,切削刃变弱,散热条件和受力状态变差,将使刀具磨损加快,耐用度降低,甚至崩刀或损坏。
在主剖面内测量的主后刀面与基切削平面之间的夹角为后角。
后角用以减少刀具主后刀面与零件过度表面间的摩擦和主后刀面的磨损,配合前角调整切削刃的锋利程度与强度;直接影响加工表面质量和刀具耐用度。
后角大,摩擦力小,切削刃锋利。
但后角过大,将使切削刃变弱,散热条件变差,加速刀具磨损15、、简述金属切削过程中切削热的来源,为减小切削热、降低切削温度,通常可采取哪些撒施?16、答:金属切削过程中的切削热的来源有以下三方面:(1)加工表面和已加工表面所发生的弹性变形或塑性变形产生的热量;(2)切屑与刀前面之间的摩擦而产生的热量;(3)工件与刀具后面之间的摩擦所产生的热量。
数控加工工艺分析——顺铣、逆铣
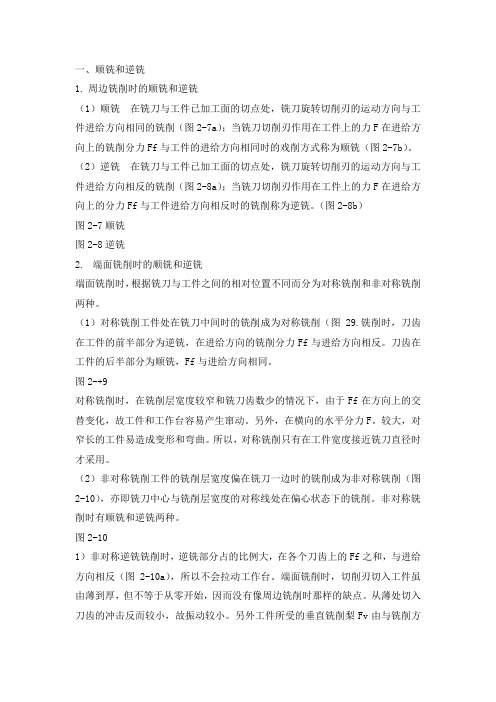
一、顺铣和逆铣1.周边铣削时的顺铣和逆铣(1)顺铣在铣刀与工件已加工面的切点处,铣刀旋转切削刃的运动方向与工件进给方向相同的铣削(图2-7a);当铣刀切削刃作用在工件上的力F在进给方向上的铣削分力Ff与工件的进给方向相同时的戏削方式称为顺铣(图2-7b)。
(2)逆铣在铣刀与工件已加工面的切点处,铣刀旋转切削刃的运动方向与工件进给方向相反的铣削(图2-8a);当铣刀切削刃作用在工件上的力F在进给方向上的分力Ff与工件进给方向相反时的铣削称为逆铣。
(图2-8b)图2-7顺铣图2-8逆铣2.端面铣削时的顺铣和逆铣端面铣削时,根据铣刀与工件之间的相对位置不同而分为对称铣削和非对称铣削两种。
(1)对称铣削工件处在铣刀中间时的铣削成为对称铣削(图29.铣削时,刀齿在工件的前半部分为逆铣,在进给方向的铣削分力Ff与进给方向相反。
刀齿在工件的后半部分为顺铣,Ff与进给方向相同。
图2-+9对称铣削时,在铣削层宽度较窄和铣刀齿数少的情况下,由于Ff在方向上的交替变化,故工件和工作台容易产生窜动。
另外,在横向的水平分力F。
较大,对窄长的工件易造成变形和弯曲。
所以,对称铣削只有在工件宽度接近铣刀直径时才采用。
(2)非对称铣削工件的铣削层宽度偏在铣刀一边时的铣削成为非对称铣削(图2-10),亦即铣刀中心与铣削层宽度的对称线处在偏心状态下的铣削。
非对称铣削时有顺铣和逆铣两种。
图2-101)非对称逆铣铣削时,逆铣部分占的比例大,在各个刀齿上的Ff之和,与进给方向相反(图2-10a),所以不会拉动工作台。
端面铣削时,切削刃切入工件虽由薄到厚,但不等于从零开始,因而没有像周边铣削时那样的缺点。
从薄处切入刀齿的冲击反而较小,故振动较小。
另外工件所受的垂直铣削梨Fv由与铣削方式无关。
因此在端面铣削时,应采用非对称逆铣。
2)非对称逆铣时,顺铣部分占的比例较大,在各个刀齿上的Ff之和,与进给方向相同(图2-10b),故易拉动工作台。
另外,垂直铣削力Fv又不因顺铣而一定向下。
《铣工的顺铣与逆铣》课件
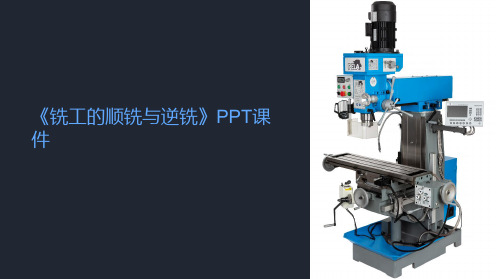
广泛应用于扁平面铣削、开槽、平面等加工。
2 逆铣
常用于钢材的高效粗铣、粗加工表面铣削等工艺。
刀具选择和参数调整
1
调整切削参数
2
合理设置进给速度、进给量、切削深度
等参数。
3
选择合适的刀具
考虑刀具类型、刀杆材料、刀具齿数等 因素。
定期检查刀具状态
确保刀具的磨损程度和刀面质量。
小结和要点
• 顺铣和逆铣是铣工常用的两种铣削方式。 • 它们在刀具路径、优缺点和应用领域等方面有一些区别。 • 选择合适的刀具和调整切削参数是确保加工质量的关键。
逆铣的刀具路径
逆铣中,铣刀从工件的一端开始,顺时针绕着工件移动,完成铣削加工。刀具路径在工件表面形成交错的切削 轨迹,提高表面质量。
顺铣和逆铣的优缺点
顺铣
优点:切削稳定,加工效率高。 缺点:切削力大,对刀具耐用性要求高。
逆铣
优点:表面质量好,切削《铣工的顺铣与逆铣》PPT课 件
铣工顺铣与逆铣的定义
顺铣是指铣刀逆时针旋转、工件相对铣刀静止或移动的铣削方式。逆铣则是 指铣刀顺时针旋转、工件相对铣刀静止或移动的铣削方式。
顺铣的刀具路径
顺铣中,铣刀从工件的一端开始,逆时针绕着工件移动,完成铣削加工。刀 具路径可形成连续的切削轨迹,提高加工效率。
铣工的顺铣与逆铣课件

逆铣的定义
逆铣:在铣削过程中,铣刀的旋转方向与工件的进给方向相反的铣削方式称为逆 铣。
逆铣时,工件受到的切削力方向与工作台进给方向相同,因此工件与工作台之间 的摩擦力较大,容易产生振动,影响加工质量和效率。
顺铣与逆铣的适用场合
顺铣适用于加工表面质量要求较 高、切削余量较小、切削力较大 的铣削加工,如平面、斜面和台
高效与高质并重
在铣工实践中,根据加工需求将顺铣与逆铣结合使用, 既能提高加工效率,又能保证加工质量。
材料与工艺匹配
应用二:不同材料适用不同铣削方式
针对不同材料选择合适的铣削方式,如顺铣或逆铣,能 够充分发挥各自的优势,提高加工效果。
05
顺铣与逆铣的发展 趋势
顺铣技术的发展趋势
高效加工
随着制造业对加工效率的 要求不断提高,顺铣技术 也在不断改进,以提高加 工效率。
智能化
随着智能制造技术的不断 发展,顺铣技术也在逐渐 实现智能化,以适应自动 化生产的需求。
环保化
随着环保意识的不断提高 ,顺铣技术也在不断向环 保化发展,以减少对环境 的污染。
逆铣技术的发展趋势
高效加工
01
逆铣技术同样也在不断改进,以提高加工效率。
稳定性提高
02
逆铣技术在加工过程中具有较好的稳定性,未来将进一步提高
顺铣的切削深度逐渐增加,有利于提 高材料去除速度,从而提高加工效率 。
表面质量较高
由于切削力的减小,顺铣可以减小切 削过程中产生的振动,从而提高工件 的表面质量。
逆铣的特点
01
02
03
切削力较大
逆铣在切削过程中,刀具 的切入是突然进行的,切 削力较大,容易导致刀具 磨损和铣床振动。
表面粗糙度较高
简述在数控铣削过程中顺铣与逆铣的定义与特点

简述在数控铣削过程中顺铣与逆铣的定义与特点数控铣削是一种利用数控技术控制铣床进行加工的方法。
在数控铣削过程中,顺铣与逆铣是常用的两种铣削方式,它们有着不同的定义和特点。
1.顺铣顺铣是指工件相对运动方向与铣刀旋转方向相同的铣削方式。
具体的过程是,在铣床主轴顺时针旋转的情况下,工件在X轴上向正方向移动,或在Y轴上向负方向移动,并通过数控机床控制工具路径进行削除材料的过程。
顺铣的特点如下:(1)切削力方向与运动方向一致:在顺铣过程中,由于工件与铣刀的相对运动方向一致,切削力的方向与工件的运动方向也一致,这样能够减小切削力对工件的影响,提高加工质量和效率。
(2)削减铣削轻薄肋:顺铣适用于削减铣削轻薄肋,因为切削力与运动方向一致,工件容易固定,减小振动,从而减少了轻薄肋的形成。
(3)表面质量好:由于切削力的方向与运动方向一致,切削过程相对稳定,能够得到较好的加工表面质量。
(4)适用于高速铣削:顺铣适用于高速铣削,因为切屑在刀具刀面上不停地产生,而且容易排除,不会对刀具和工件产生较大的磨损和热变形。
2.逆铣逆铣是指工件相对运动方向与铣刀旋转方向相反的铣削方式。
具体的过程是,在铣床主轴顺时针旋转的情况下,工件在X轴上向负方向移动,或在Y轴上向正方向移动,并通过数控机床控制工具路径进行削除材料的过程。
逆铣的特点如下:(1)切削力方向与运动方向相反:在逆铣过程中,切削力的方向与工件运动的方向相反,这样会增加切削力对工件的影响,对工件的固定要求较高。
(2)容易形成轻薄肋:逆铣不适用于削减铣削轻薄肋,因为切削力与运动方向相反,容易导致工件振动,增加形成轻薄肋的可能性。
(3)表面质量较差:由于切削力的方向与运动方向相反,切削过程相对不稳定,容易产生振动和滑移,导致加工表面质量较差。
(4)推荐用于加工薄壁结构:逆铣适用于加工薄壁结构,因为切削力相对较小,不容易变形和破坏工件。
综合而言,顺铣和逆铣在数控铣削过程中具有各自的特点和优劣之处。
顺铣和逆铣的特点
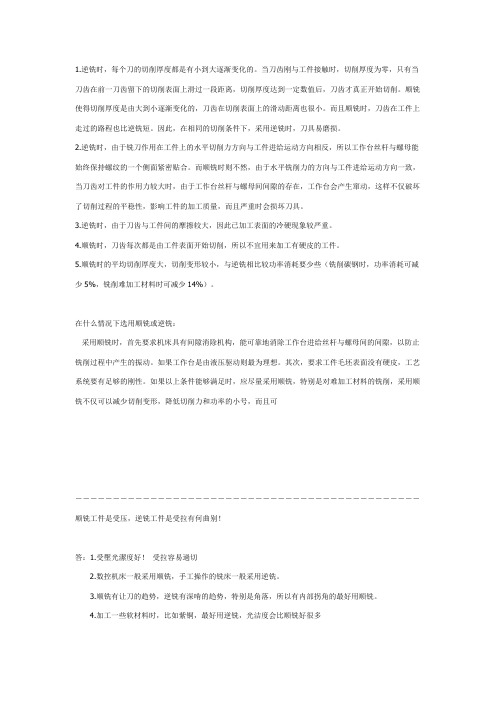
1.逆铣时,每个刀的切削厚度都是有小到大逐渐变化的。
当刀齿刚与工件接触时,切削厚度为零,只有当刀齿在前一刀齿留下的切削表面上滑过一段距离,切削厚度达到一定数值后,刀齿才真正开始切削。
顺铣使得切削厚度是由大到小逐渐变化的,刀齿在切削表面上的滑动距离也很小。
而且顺铣时,刀齿在工件上走过的路程也比逆铣短。
因此,在相同的切削条件下,采用逆铣时,刀具易磨损。
2.逆铣时,由于铣刀作用在工件上的水平切削力方向与工件进给运动方向相反,所以工作台丝杆与螺母能始终保持螺纹的一个侧面紧密贴合。
而顺铣时则不然,由于水平铣削力的方向与工件进给运动方向一致,当刀齿对工件的作用力较大时,由于工作台丝杆与螺母间间隙的存在,工作台会产生窜动,这样不仅破坏了切削过程的平稳性,影响工件的加工质量,而且严重时会损坏刀具。
3.逆铣时,由于刀齿与工件间的摩擦较大,因此已加工表面的冷硬现象较严重。
4.顺铣时,刀齿每次都是由工件表面开始切削,所以不宜用来加工有硬皮的工件。
5.顺铣时的平均切削厚度大,切削变形较小,与逆铣相比较功率消耗要少些(铣削碳钢时,功率消耗可减少5%,铣削难加工材料时可减少14%)。
在什么情况下选用顺铣或逆铣:采用顺铣时,首先要求机床具有间隙消除机构,能可靠地消除工作台进给丝杆与螺母间的间隙,以防止铣削过程中产生的振动。
如果工作台是由液压驱动则最为理想。
其次,要求工件毛坯表面没有硬皮,工艺系统要有足够的刚性。
如果以上条件能够满足时,应尽量采用顺铣,特别是对难加工材料的铣削,采用顺铣不仅可以减少切削变形,降低切削力和功率的小号,而且可――――――――――――――――――――――――――――――――――――――――――――――顺铣工件是受压,逆铣工件是受拉有何曲别!答:1.受壓光潔度好!受拉容易過切2.数控机床一般采用顺铣,手工操作的铣床一般采用逆铣。
3.顺铣有让刀的趋势,逆铣有深啃的趋势,特别是角落,所以有内部拐角的最好用顺铣。
铣床加工的顺洗和逆洗

顺洗和逆洗铣削方法分为两种:端铣和周铣;周铣又分为顺铣和逆铣,周铣时,铣刀接触工件时的旋转方向和工件的进给方向相同的铣削方式叫顺铣;反之,周铣时,铣刀接触工件时的旋转方向和工件的进给方向相反的铣削方式叫逆铣.顺铣,作用垂直分力向下,逆洗垂直分力向上,易翻转工件,发生事故;顺铣刀具寿命长于逆洗一倍;但机床要有防"爬走"装置,因为方向一致,切力大于驱动力和切力小于驱动力有....;材料硬,逆铣,切入时应降速,易打刀;材料软,顺铣;逆铣表面光洁度要好,顺铣要差一点,;机床精度好、刚性好、精加工:较适应顺铣,反之较适应逆铣零件内拐角处精加工强烈建议要用顺铣。
粗加工:逆铣较好,精加工:顺铣较好顺铣和逆铣的特点:1.顺铣时,每个刀的切削厚度都是有小到大逐渐变化的。
当刀齿刚与工件接触时,切削厚度为零,只有当刀齿在前一刀齿留下的切削表面上滑过一段距离,切削厚度达到一定数值后,刀齿才真正开始切削。
逆铣使得切削厚度是由大到小逐渐变化的,刀齿在切削表面上的滑动距离也很小。
而且顺铣时,刀齿在工件上走过的路程也比逆铣短。
因此,在相同的切削条件下,采用逆铣时,刀具易磨损。
2.逆铣时,由于铣刀作用在工件上的水平切削力方向与工件进给运动方向相反,所以工作台丝杆与螺母能始终保持螺纹的一个侧面紧密贴合。
而顺铣时则不然,由于水平铣削力的方向与工件进给运动方向一致,当刀齿对工件的作用力较大时,由于工作台丝杆与螺母间间隙的存在,工作台会产生窜动,这样不仅破坏了切削过程的平稳性,影响工件的加工质量,而且严重时会损坏刀具。
3.逆铣时,由于刀齿与工件间的摩擦较大,因此已加工表面的冷硬现象较严重。
4.顺铣时,刀齿每次都是由工件表面开始切削,所以不宜用来加工有硬皮的工件。
5.顺铣时的平均切削厚度大,切削变形较小,与逆铣相比较功率消耗要少些(铣削碳钢时,功率消耗可减少5%,铣削难加工材料时可减少14%)。
通俗解释顺铣:所切下来的废料从工件边缘铣出。
顺铣和逆铣的优缺点及应用

顺铣和逆铣的优缺点及应用顺铣和逆铣是CNC铣床加工过程中经常使用的两种基本方法。
顺铣和逆铣有不同的优缺点和适用范围,本篇文章将对这两种方法进行介绍和分析。
一. 顺铣顺铣是在工件表面上沿一个固定的方向进行加工,通常是从左到右或者从下到上。
顺铣是CNC铣床加工中常用的一种方法,它有以下的优缺点:1. 优点(1)采用顺铣方式进行加工会使切削力沿着铣刀旋转方向工作,这样切削力就会被稳定地释放,从而使切削更加容易、更加平滑。
(2)在顺铣过程中,切削时的进给方向与铣刀先前切过的区域相同,这就保证了加工中横向切割不会留有太多痕迹。
(3)顺铣过程中,工件加工的速度可以更高,因为不会出现铣刀移动速度过快导致工件受损的情况。
2. 缺点(1)由于挤压加工的不均匀,顺铣过程中有时会导致切削区域出现较多的撕裂和毛刺。
(2)由于顺铣方式的切削不如其他方式的切削平滑,因此可能导致工件表面的表面粗糙度较高。
(3)在顺铣中,由于切削是在工件上进行的,所以需要更多的工具和设备来保证不破坏工件的形状和结构。
二. 逆铣逆铣是在工件表面上沿相反的方向进行切割。
逆铣在一些特定的加工场合中有着很好的适用性,它的优缺点如下:1. 优点(1)逆铣可以使铣刀与工件表面的夹角更小,这样可以使铣削更加平滑,痕迹更少。
(2)逆铣可以更好地控制切削力,在加工坚固材料时非常适合。
(3)逆铣在加工粉末金属材料时具有更好的适用性,因为这样的材料在顺向切削时容易产生折叠,形成毛刺,而逆切削能有效地解决这个问题。
2. 缺点(1)逆铣容易导致工件表面的疲劳,因为切削面在工件表面沿相反的方向切削,由于工件表面负载不均匀,容易导致表面疲劳裂纹。
(2)逆铣的加工速度较慢,容易造成铣削过度或痕迹较多的问题。
(3)逆铣难度较大,需要对加工的工件进行非常严格的控制,否则可能会发生误差或工件损坏。
三. 适用范围顺铣和逆铣在不同的加工工艺中都有其适用范围,一些例子如下:1. 顺铣适用于加工更加脆性的材料,因为这样的材料在铣削时可以更好地保持其结构。
顺铣和逆铣的特点

1,对切削力的影响
逆铣时作用于工件上的垂直分力始终向上,有将工件抬起的趋势,易引起震动,影响工件的夹紧,这种情况在铣薄壁和刚度差工件时表现尤为突出,顺铣时作用于工件上的垂直切削分力始终压于工件,这对工件的夹紧有利。
2 对刀具弹性变形的影响
采用立铣刀顺铣时,工件对刀具的反作用力指向刀具方向,刀具的弹性变形使刀具产生“让刀”(即欠切)现象。
采用逆铣时,工件对刀具的反作用力指向轮廓内部,刀具的弹性变形使刀具产生“啃刀”(即过切)现象。
当刀具直径越小,刀杆伸越长时,让刀和啃刀现象越明显。
针对这种现象,粗加工采用顺铣时,可留少量精加工余量。
粗加工逆铣时,须多留精加工余量,以防过切,产生报废。
3 对刀具磨损的影响
顺铣的垂直切削分力将工件压向工作台,刀齿与已加工面滑行,摩擦现象小,对减小刀齿磨损,减少工件加工硬化现象和减小表面粗糙度均有利。
另外,顺铣时刀齿的切削厚度是从最大到零,使刀齿切入工件时的冲击力较大,尤其工件待加工表面是毛坯或者有硬皮时,会使刀具产生较大的振动。
但顺铣时刀齿在工件上走过的路程也比逆铣短,平均切削厚度大。
因此,在相同的切削条件下,采用逆铣时,刀具易磨损,消耗的切削功率要多些。
逆铣时每个刀齿的厚度有零增至最大。
但切削刃并非绝对锋利,铣刀刃口处总有圆弧存在,刀齿不能立刻切入工件,而是在已加工表面上挤压滑行,使该表面的硬化现象严重,影响了表面质量,也使刀齿的磨损加剧。
什么时候采用顺铣,什么时候采用逆铣呢?
零件粗加工时,通常采用逆铣,因为逆铣时,刀具从已加工表面切入,不会蹦刃,且机床的传动间隙不会引起振动和爬行。
精加工时,为防止过切现象,通常采用顺铣。
顺铣和逆铣的判断方法与选用技巧
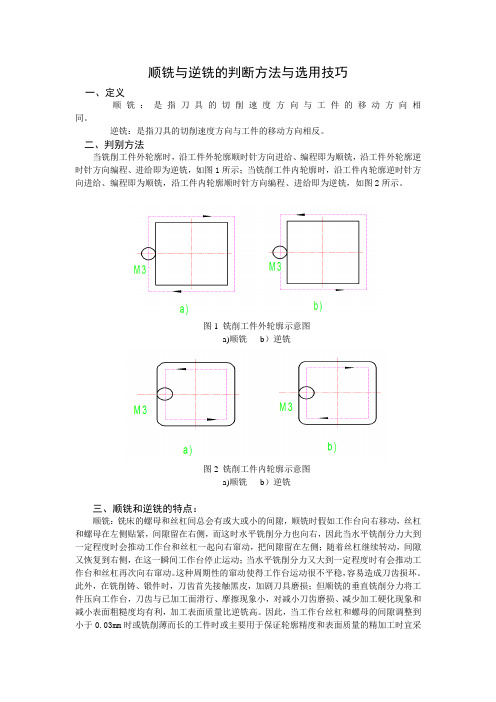
顺铣与逆铣的判断方法与选用技巧一、定义顺铣:是指刀具的切削速度方向与工件的移动方向相同。
逆铣:是指刀具的切削速度方向与工件的移动方向相反。
二、判别方法当铣削工件外轮廓时,沿工件外轮廓顺时针方向进给、编程即为顺铣,沿工件外轮廓逆时针方向编程、进给即为逆铣,如图1所示;当铣削工件内轮廓时,沿工件内轮廓逆时针方向进给、编程即为顺铣,沿工件内轮廓顺时针方向编程、进给即为逆铣,如图2所示。
图1 铣削工件外轮廓示意图a)顺铣b)逆铣图2 铣削工件内轮廓示意图a)顺铣b)逆铣三、顺铣和逆铣的特点:顺铣:铣床的螺母和丝杠间总会有或大或小的间隙,顺铣时假如工作台向右移动,丝杠和螺母在左侧贴紧,间隙留在右侧,而这时水平铣削分力也向右,因此当水平铣削分力大到一定程度时会推动工作台和丝杠一起向右窜动,把间隙留在左侧;随着丝杠继续转动,间隙又恢复到右侧,在这一瞬间工作台停止运动;当水平铣削分力又大到一定程度时有会推动工作台和丝杠再次向右窜动。
这种周期性的窜动使得工作台运动很不平稳,容易造成刀齿损坏。
此外,在铣削铸、锻件时,刀齿首先接触黑皮,加剧刀具磨损;但顺铣的垂直铣削分力将工件压向工作台,刀齿与已加工面滑行、摩擦现象小,对减小刀齿磨损、减少加工硬化现象和减小表面粗糙度均有利,加工表面质量比逆铣高。
因此,当工作台丝杠和螺母的间隙调整到小于0.03mm时或铣削薄而长的工件时或主要用于保证轮廓精度和表面质量的精加工时宜采用顺铣。
逆铣:逆铣时铣削垂直分力将工件上抬,刀齿与已加工面滑行使摩擦加大。
但铣削水平分力有助于丝杠和螺母贴紧,使工作台运动比较平稳,铣削铸、锻件引起的刀齿磨损也较小,同时采用逆铣可以使加工效率大大提高,但由于逆铣切削力大,易导致切削变形增加,刀具磨损也快。
因此一般以去除工件余量、保证加工效率为主的粗铣削多采用逆铣。
四、选择技巧1、尽可能多使用顺铣。
因为数控铣床的结构特点,丝杠和螺母的间隙很小,若采用滚珠丝杠副,基本可消除间隙,因而不存在间隙引起工作台窜动问题。
顺铣与逆铣的概念

顺铣与逆铣的概念顺铣与逆铣是数控铣床加工中的两种常见的铣削方式。
它们基本上是相反的过程,具有不同的工作方式和特点。
首先,顺铣是指在铣床上工作台上进行铣削操作时,刀具沿工件上的一个轮廓线从一侧到另一侧按照一定方向进行削除工件材料的过程。
顺铣的特点是刀具从工件的外侧不断切入,直到达到所需尺寸,然后刀具从工件的另一侧退出。
顺铣的工作方式是刀具顺时针旋转和工件反向移动,这种方式适用于大多数的铣削操作。
顺铣主要用于加工工件的外周轮廓、平面和槽。
与之相反,逆铣是指刀具在铣床上工作台上倒转沿轮廓线从工件的一侧到另一侧逆向削除工件材料的过程。
逆铣的特点是刀具从工件的内部开始削除,然后沿轮廓线逆向移动,以达到所需的尺寸。
逆铣的工作方式是刀具逆时针旋转,而工件向前移动。
逆铣主要用于加工较深的槽、腔和曲面。
顺铣和逆铣在铣削加工中具有各自的优缺点。
首先,顺铣的切削载荷较小,因为工件材料在切削中的逐渐消失,这有利于延长刀具寿命。
另外,顺铣的切削力向下压工件,增加了工件的稳定性,使得加工过程更加稳定可靠。
然而,顺铣对于工件材料较硬的情况下可能会产生较高的表面粗糙度。
相反,逆铣的切削载荷较大,因为切削过程中刀具一直对工件进行切削,这可能缩短刀具的使用寿命。
此外,逆铣的切削力向上拉工件,降低了工件的稳定性,可能引起振动和不稳定性。
然而,由于逆铣从工件的内部开始,可以更好地控制切削过程,加工较深的槽和腔时优势明显。
综上所述,顺铣和逆铣是数控铣床加工中常见的两种铣削方式。
它们具有不同的工作方式和特点,适用于不同类型的铣削操作。
顺铣通过从外到内的切削方式和稳定的切削负荷适用于大多数切削操作。
而逆铣适用于加工较深的槽、腔和曲面,在切削负荷较大的情况下需要更好的切削控制。
在实际加工中,需要根据具体工件的要求和材料的特性选择适当的铣削方式。
- 1、下载文档前请自行甄别文档内容的完整性,平台不提供额外的编辑、内容补充、找答案等附加服务。
- 2、"仅部分预览"的文档,不可在线预览部分如存在完整性等问题,可反馈申请退款(可完整预览的文档不适用该条件!)。
- 3、如文档侵犯您的权益,请联系客服反馈,我们会尽快为您处理(人工客服工作时间:9:00-18:30)。
2)工件运动方向与刀具旋转方向相反时为逆铣
从理论上来说顺铣比逆铣好,切削力由多到少刀具损耗不大,不易拉动工件,易排削……但普通铣床上丝杆间歇太大,故在此设备上只能做逆铣加工,摇动x或y轴之前要背掉另一轴的间歇,防止拉刀……
8.铣外形时用顺时针铣,铣内腔时用逆时针铣,这是顺铣的法则。
在什么情况下选用顺铣或逆铣:
螺母间的间隙,以防止铣削过程中产生的振动。如果工作台是由液压驱动则最为理想。其次,要求工件毛坯表面没有硬皮,工艺系统要有足够的刚性。如果以上条件能够满足时,应尽量采用顺铣,特别是对难加工材料的铣削,采用顺铣不仅可以减少切削变形,降低切削力和功率的小号.
实际生产中多用逆铣,因为顺铣情况下铣刀的切削力会使工件向前窜动,窜动是由于工作台的进给丝杠螺纹间有间隙,且间隙在运动的前方,顺铣时受前向突然增大的切削力,使工作台和工件向前跳动.
但是实际上,顺铣比逆铣能减少刀具磨损,提高表面光洁度. 如果能消除丝杠间隙的话, 还是顺铣较好. 只是目前没有有效消除间隙的方法.所以实际生产还是用逆铣.
采用顺铣时,首先要求机床具有间隙消除机构,能可*地消除工作台进给丝杆与
顺铣:切削力F的水平分力,Fx的方向与进给方向的f相同。
逆铣:切削力F的水平分力,Fx的方向与进给方向的f相反。
顺铣和逆铣的特点
1.逆铣时,每个刀的切削厚度都是有小到大逐渐变化的。当刀齿刚与工件接触时,切削厚度为零,只有当刀齿在前一刀齿留下的切削表面上滑过一段距离,切削厚度达到一定数值后,刀齿才真正开始切削。顺铣使得切削厚度是由大到小逐渐变化的,刀齿在切削表面上的滑动距离也很小。而且顺铣时,刀齿在工件上走过的路程也比逆铣短。因此,在相同的切削条件下,采用逆铣时,刀具易磨损。
角落加工无论逆铣还是顺铣都容易过切,我一般是先用小刀清角,此时余量给大点,再用合适的刀具加工,而且最好角落处刀路FEED慢一点,并且刀路带一点R
6.我的方法是不管是外銑或內銑﹐用G42作刀補的那一種方法即可
7. 还背得出原来在技校时学的,简单明了:
1)工件运动方向与刀具旋转方向相同时为顺铣
3.逆铣时,由于刀齿与工件间的摩擦较大,因此已加工表面的冷硬现象较严重。
4.顺铣时,刀齿每次都是由工件表面开始切削,所以不宜用来加工有硬皮的工件。
5.顺铣时的平均切削厚度大,切削变形较小,与逆铣相比较功率消耗要少些(铣削碳钢时,功率消耗可减少5%,铣削难加工材料时可减少14%)。
顺铣工件是受压,逆铣工件是受拉有何区别!
1.受压光洁度好! 受拉容易过切
2.数控机床一般采用顺铣,手工操作的铣床一般采用逆铣。
3.顺铣有让刀的趋势,逆铣有深啃的趋势,特别是角落,所以有内部拐角的最好用顺铣。
4.加工一些软材料时,比如紫铜,最好用逆铣,光洁度会比顺铣好很多
5.尽量用顺铣,逆铣很容易过切,尤其是开粗时.
沿着刀具的进给方向看,如果工件位于铣刀进给方向的右侧,那么进给方向称为顺时针。反之,当工件位于铣刀进给方向的左侧时,进给方向定义为逆时针。如果铣刀旋转方向与工件进给方向相同,称为顺铣,如下图左图所示;铣刀旋转方向与工件进给方向相反,称为逆铣,如下图右图所示。逆铣时,切削由薄变厚,刀齿从已加工表面切入,对铣刀的使用有利。逆铣时,当铣刀刀齿接触工件后不能马上切入金属层,而是在工件表面滑动一小段距离,在滑动过程中,由于强烈的磨擦,就会产生大量的热量,同时在待加工表面易形成硬化层,降低了刀具的耐用度,影响工件表面光洁度,给切削带来不利。另外,逆铣时,由于刀齿由下往上(或由内往外)切削。顺铣时,刀齿开始和工件接触时切削厚度最大,且从表面硬质层开始切入,刀齿受很大的冲击负荷,铣刀变钝较快,但刀齿切入过程中没有滑移现象。顺铣的功率消耗要比逆铣时小,在同等切削条件下,顺铣功率消耗要低5%~15%,同时顺铣也更加有利于排屑。一般应尽量采用顺铣法加工,以提高被加工零件表面的光洁度(降低粗糙度),保证尺寸精度。但是在切削面上有硬质层、积渣、工件表面凹凸不平较显著时,如加工锻造毛坯,应采用逆铣法。
2.逆铣时,由于铣刀作用在工件上的水平切削力方向与工件进给运动方向相反,所以工作台丝杆与螺母能始终保持螺纹的一个侧面紧密贴合。而顺铣时则不然,由于水平铣削力的方向与工件进给运动方向一致,当刀齿对工件的作用力较大时,由于工作台丝杆与螺母间间隙的存在,工作台会产生窜动,这样不仅破坏了切削过程的平稳性,影响工件的加工质量,而且严重时会损坏刀具。