燃烧室设计
高温氢气燃烧的燃烧室设计与性能分析

高温氢气燃烧的燃烧室设计与性能分析概述:在现代工业中,氢气作为一种清洁的能源被广泛应用。
而高温氢气燃烧的燃烧室设计与性能分析是确保燃烧过程的效率、稳定性和安全性的重要步骤。
本文将详细介绍高温氢气燃烧的燃烧室设计方法以及性能分析的关键参数。
一、燃烧室设计1. 燃烧室类型高温氢气燃烧室的设计可分为绝热型和冷却型两种。
绝热型燃烧室通过表面绝热层的保护,实现热量的不外传,提高燃烧温度和效率。
冷却型燃烧室则利用冷却剂对燃烧室进行冷却,防止高温引起燃烧室的热损失。
2. 燃烧室形状高温氢气燃烧室的形状对燃烧过程的效率和性能有着重要影响。
燃烧室通常采用圆形、方形、二维、三维等多种形状。
不同形状的燃烧室对于燃气的流动、混合和燃烧过程有着不同的影响。
3. 燃烧室尺寸燃烧室的尺寸直接影响着燃烧过程的稳定性和能量转化效率。
过小的燃烧室会导致燃气的流动受限、燃烧不完全等问题;而过大的燃烧室则会增加燃气的稀释和燃烧时间,降低燃烧效率。
二、性能分析1. 燃烧效率燃烧效率是衡量燃烧室性能的重要指标。
燃烧效率高意味着燃气能够被充分燃烧,产生更多的热能。
提高燃烧效率可以采用优化燃气喷射和气体混合设计、增大燃气流速、提高氧气浓度等手段。
2. 热传导和热损失燃烧室的热传导和热损失是燃烧过程中需要考虑的重要问题。
优化燃烧室的材料选择、结构设计以及绝热层的应用可以减少热传导和热损失,提高燃烧室的热效率。
3. 振动和噪音高温氢气燃烧室在运行过程中会产生振动和噪音,降低燃烧室的稳定性和工作效率。
通过采用减振和降噪技术,如增加缓冲装置、采用材料隔音等方法,可以有效地减少振动和噪音的产生。
4. 进气和排气燃气的进气和废气的排出对于燃烧室性能的影响也非常重要。
合理的进气系统设计和排气系统排放控制可以保持燃气的稳定供应和对环境的友好。
结论:高温氢气燃烧的燃烧室设计与性能分析是确保燃烧过程效率、稳定性和安全性的关键。
通过合理的燃烧室设计,考虑燃气的流动、混合、燃烧效果以及热传导、振动、噪音等问题,可以优化燃烧室的性能,提高能源利用效率,保护环境。
燃烧与燃烧室设计原理

燃烧与燃烧室设计原理燃烧,指的是物质与氧气发生化学反应时,释放出能量,并产生热、光等现象的过程。
而燃烧室,则是控制燃烧过程的装置。
本文将从燃烧和燃烧室的基本原理入手,介绍燃烧室设计的一些重要原则。
一、燃烧的基本原理燃烧的基本原理是“燃料氧化”,即燃料与氧气发生化学反应,生成二氧化碳、水蒸气和能量。
燃料可以是固体、液体或气体,其中最常见的燃料是石油、天然气和煤炭。
而氧气则来自于空气,空气中氧气的含量约为21%。
在燃烧过程中,燃料需要达到燃点温度才能起火。
一旦起火,就会产生火焰,并伴随着火焰释放出的热量和光线。
火焰的颜色和温度与燃烧所用的燃料种类和燃烧条件有关。
二、燃烧室的基本要素燃烧室是进行燃烧反应的场所,其设计需要考虑以下几个基本要素:1. 空间容积:燃烧室的大小直接影响燃烧的强度和持续时间。
一般来说,燃烧室的容积应根据具体需求确定,容积过小可能导致不完全燃烧,容积过大则会降低燃烧效率。
2. 空气供应:燃烧需要氧气的参与,因此燃烧室的设计中要考虑充足的空气供应。
通常通过进风口或进气口将空气引入燃烧室,确保燃料能够充分与氧气反应。
3. 确保燃料的混合均匀:在燃烧过程中,燃料需要充分与氧气混合才能进行燃烧反应。
因此,燃烧室的设计需要考虑燃料的喷射方式、喷射角度等因素,确保燃料与氧气能够均匀混合。
4. 热量损失控制:燃烧室的设计中需要尽量减少热量损失,提高燃烧效率。
常见的方式包括使用耐高温材料、合理安排燃料喷射口和气流流动等。
三、燃烧室设计的原则在进行燃烧室设计时,需要遵循以下原则:1. 安全性原则:燃烧室的设计应确保燃烧过程稳定且可靠,避免出现意外事故。
必要时,可以采取增加防火材料、排气系统和防爆装置等安全措施。
2. 高效性原则:燃烧室的设计应尽量提高燃烧效率,充分利用燃料的能量。
这可以通过优化空气供应、提高燃料混合均匀度、减少热量损失等方式实现。
3. 可持续性原则:燃烧室的设计应考虑环保因素,减少污染物的排放。
汽车发动机燃烧室设计计算(汽车工程)
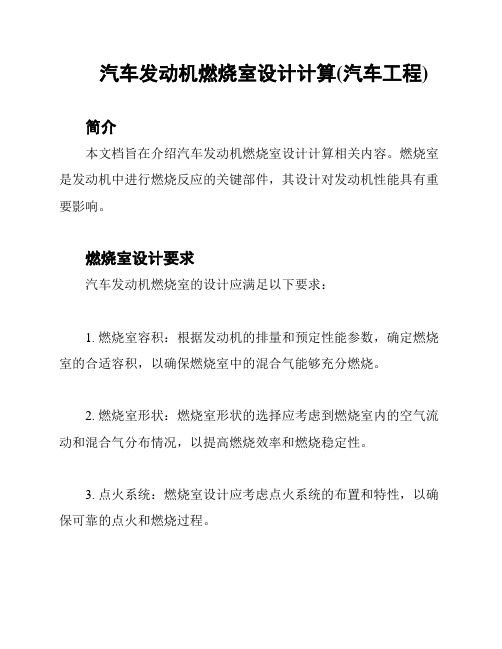
汽车发动机燃烧室设计计算(汽车工程)
简介
本文档旨在介绍汽车发动机燃烧室设计计算相关内容。
燃烧室是发动机中进行燃烧反应的关键部件,其设计对发动机性能具有重要影响。
燃烧室设计要求
汽车发动机燃烧室的设计应满足以下要求:
1. 燃烧室容积:根据发动机的排量和预定性能参数,确定燃烧室的合适容积,以确保燃烧室中的混合气能够充分燃烧。
2. 燃烧室形状:燃烧室形状的选择应考虑到燃烧室内的空气流动和混合气分布情况,以提高燃烧效率和燃烧稳定性。
3. 点火系统:燃烧室设计应考虑点火系统的布置和特性,以确保可靠的点火和燃烧过程。
4. 发动机排放:燃烧室设计也应考虑减少发动机的排放问题,提高燃烧效率,降低有害气体和颗粒物的排放。
燃烧室设计计算方法
在进行汽车发动机燃烧室设计计算时,可以采用以下方法:
1. 模拟计算:利用计算机辅助工程软件,建立燃烧室的数值模型,进行流场和燃烧过程的数值模拟计算,以分析燃烧室内的气体流动和燃烧特性。
2. 实验测量:通过实际测试,测量燃烧室内的温度、压力等参数,以验证设计计算结果的准确性,并进行进一步的优化。
3. 经验公式:根据已有的燃烧室设计经验,并结合相关理论,利用经验公式进行初步的燃烧室设计计算。
4. 工程案例分析:分析已有的类似发动机的燃烧室设计案例,借鉴其设计思路和经验,对新的设计进行参考和改进。
结论
汽车发动机燃烧室设计计算是提高发动机性能和降低排放的重要环节。
通过合理的燃烧室设计,可以提高燃烧效率、优化燃烧稳定性,同时减少有害气体和颗粒物的排放。
在设计计算过程中,应综合运用模拟计算、实验测量、经验公式和工程案例分析等方法,以得到更准确的设计结果。
燃烧室设计

• 4 对燃烧室而言,重要的零部件如旋流器,冷却 和掺混机构,喷嘴等对燃烧室意义颇大,在设计 中应该重视; • 5燃烧室试验是燃烧室设计不可或缺的一部分内容, 燃烧室的设计定型主要是依靠试验手段获得的。 必须通过大量的试验,对初步设计内容做不断的 修改,才可能得到性能良好的燃烧室; • 6 现代燃气轮机的不断发展离不开先进的燃烧技 术,但是目前燃烧理论还很不成熟,对燃烧室设 计而言是个很大的障碍。
d1 D
f
0 . 4 ~ 0 . 425 ;
旋流器内径和外径之比为0.7;
旋流器叶片火焰管入口直径
旋流器叶片数n=8;
ds D
f
0 . 36 ~ 0 . 4
2
180 旋流器叶片喉部宽度 b d 1 sin n D 2 d 2 As 旋流器通流面积 4
ห้องสมุดไป่ตู้
360 cos n
研 究 背 景
现代燃气轮机 技术相对独立 的一个领域
燃烧室是燃气轮 机三大部件之一
燃烧室两种功能
• 由压气机流出的一 部分气体和燃料混 合进行燃烧,为整 个燃气轮机供应能 量;
另一部分压缩空气 与燃烧后的高温燃气 进行掺混,使其温度 降低至涡轮叶片能够 承受的燃气温度
• 燃烧室设计要求: • 1 工作可靠性要求:点火 效率 寿命 强度 温 度场 • 2 经济性能要求:燃烧完全 流阻小 • 3 维护保养方面要求:便于维修 拆装
•
8 燃烧室低污染排放内容的研究
NOx的产生机理 针对性的防污措施 a.改进燃烧管理,如采用高空燃比燃烧,选用含氮量少的 燃料,空气预热适中,烟气循环,喷水等 b.采用新的燃烧技术和装置,如浓淡燃烧,二级或者多级 燃烧,分割火焰燃烧,预混预蒸发燃烧,变几何燃烧装 置,催化燃烧室等。
发动机燃烧室设计与燃烧过程优化技术

发动机燃烧室设计与燃烧过程优化技术发动机燃烧室是内燃机的核心组成部分,对整个发动机的性能和效率起着至关重要的作用。
燃烧室的设计和燃烧过程的优化技术是提升发动机性能、降低燃料消耗和排放的关键所在。
燃烧室设计的目标是实现高效燃烧,达到最佳的能量转化效率。
在燃烧室设计的过程中,考虑到燃烧稳定性、燃烧速率、温度分布、压力脉动和排放等因素,需要综合考虑多个因素。
下面将具体介绍一些燃烧室设计与燃烧过程优化技术。
首先,燃烧室的几何形状对燃烧效率有着重要影响。
传统的燃烧室设计通常采用缸形几何结构,但近年来发展出了更为复杂的燃烧室形状,如顶置燃烧室、壁式燃烧室和腔式燃烧室等。
这些新型燃烧室可以提供更好的空燃比控制、更好的燃烧稳定性和更低的排放水平。
其次,燃烧室的进气系统设计也至关重要。
优化的进气系统设计可以提供更好的空燃比分布,改善燃烧过程的均匀性和稳定性。
例如,采用多点喷射技术可以实现更好的混合气分布,提高燃烧效率。
同时,通过良好的进气系统设计可以降低进气阻力,提高发动机的进气效率。
第三,燃烧室喷射系统的设计也对燃烧室的燃烧效果有着直接影响。
喷射系统的目标是实现燃料和空气的良好混合,以提供更均匀的燃料分布。
传统的喷射系统通常采用单点喷射,但是近年来多点喷射和直接喷射技术的应用越来越广泛。
这些技术可以提供更好的喷雾分布,提高燃烧效率和稳定性。
此外,通过燃烧室壁面的散热设计,可以有效地减少传热损失,提高燃烧室的热效率。
采用散热涂层和冷却通道技术可以降低燃烧室内壁面的温度,减少热损失。
合理的散热设计可以提高发动机的功率输出,并延长发动机的使用寿命。
燃烧过程的优化技术包括燃烧过程仿真和控制系统的优化。
通过燃烧过程仿真,可以模拟并优化燃烧室的燃烧过程,包括燃气的流动、混合和燃烧。
通过仿真可以评估不同设计参数对燃烧效率的影响,优化燃烧室的设计。
在控制系统的优化方面,利用先进的控制算法和传感器技术,可以实现更精准的燃烧控制。
航空发动机燃烧室设计

航空发动机燃烧室设计在航空发动机中,燃烧室是将燃料和氧气进行燃烧的地方。
其主要的任务是将燃料和氧气进行有效的混合,然后在可控的条件下进行燃烧。
燃烧室的设计需要考虑以下几个要素:燃料喷射、空气混合、点火和燃烧控制。
首先,燃料的喷射是燃烧室设计中的一个重要环节。
通过喷射燃料来实现燃烧过程。
喷射的方式可以有多种选择,例如,喷射器的数量和位置,喷嘴的形状和尺寸等。
喷射方式的选择应该能够确保燃料与空气混合良好,使得燃料能够完全燃烧,提供足够的热量。
其次,空气的混合是燃烧室设计的另一个关键因素。
燃料和空气的均匀混合能够保证燃烧过程的高效进行。
燃烧室设计应该确保燃料能够完全与空气混合,防止燃料局部燃烧,导致不均匀的燃烧过程和火焰失稳。
接下来是点火过程的控制。
点火是燃烧过程中的关键一步,它会引发燃料和空气的燃烧反应。
在燃烧室设计中,应该确保点火系统的可靠性和精确性,以保证点火的准确性和时间控制。
同时,燃烧室的设计应该减少点火引起的振动和冲击,以提高发动机的可靠性和寿命。
最后,燃烧控制也是燃烧室设计中的一个重要环节。
燃烧的控制是指燃烧室中的压力、温度、速度等参数的控制。
燃烧室的设计应该考虑如何实现燃烧的稳定和高效。
通过精确控制燃烧室的几何形状、燃料喷射和点火过程,可以实现燃烧过程的优化。
航空发动机燃烧室设计的过程可以归纳为以下几个步骤。
首先,根据发动机性能和要求确定燃烧室的设计参数,例如燃料喷射方式、喷嘴尺寸等。
然后,基于这些参数进行初步的几何设计,包括燃烧室的形状和尺寸。
接下来,通过数值模拟和实验验证燃烧室设计的性能和效果。
最后,根据模拟和实验的结果进行优化设计,并进一步验证和评估。
综上所述,航空发动机燃烧室设计是一个综合考虑燃料喷射、空气混合、点火和燃烧控制等因素的复杂工程问题。
通过合理设计燃烧室,可以提高发动机的性能和效率,从而满足航空工程的要求。
将来,随着材料和工艺技术的不断发展,燃烧室设计将会更加高效、可靠和环保。
燃烧室设计对发动机性能的影响分析

燃烧室设计对发动机性能的影响分析燃烧室作为内燃机的重要组成部分,其设计的优劣直接影响着发动机的性能。
本文将对燃烧室设计对发动机性能的影响进行分析,探讨不同燃烧室设计参数对发动机性能的影响,以期为燃烧室设计提供一定的参考。
燃烧室设计参数对发动机性能的影响燃烧室设计参数包括燃烧室形状、大小、油气混合方式等。
这些参数的不同组合将直接影响发动机的功率、燃油消耗率、排放等性能指标。
燃烧室形状燃烧室的形状对发动机性能有很大的影响。
常见的燃烧室形状有球形、方形、圆柱形等。
研究表明,球形燃烧室可以提供更好的油气混合,提高燃烧效率,从而提高发动机的功率和燃油经济性。
燃烧室大小燃烧室的大小也是影响发动机性能的重要因素。
燃烧室过大,会导致燃烧延迟,降低发动机的功率和燃油经济性;燃烧室过小,则会导致燃烧不完全,增加排放。
因此,合理选择燃烧室大小对于提高发动机性能至关重要。
油气混合方式油气混合方式影响着燃烧的速率和效率。
常见的油气混合方式有预混合燃烧和边喷射燃烧。
预混合燃烧可以提供更好的燃烧速率,提高发动机的功率和燃油经济性;边喷射燃烧则可以提供更好的排放性能。
因此,选择合适的油气混合方式也是提高发动机性能的关键。
燃烧室设计对发动机性能有着重要的影响。
合理的燃烧室形状、大小和油气混合方式的选择,可以提高发动机的功率和燃油经济性,降低排放。
因此,在进行燃烧室设计时,需要充分考虑这些因素,以实现发动机性能的最优化。
这是整篇的内容,下一部分将继续深入分析燃烧室设计参数对发动机性能的影响。
燃烧室设计对发动机性能的详细影响分析燃烧室形状的影响不同的燃烧室形状对发动机性能的影响是显著的。
球形燃烧室由于其独特的几何形状,能够提供更好的油气混合,从而提高燃烧效率。
球形燃烧室的设计有助于减少燃烧延迟,增加燃烧速率,进而提高发动机的功率输出。
此外,球形燃烧室还能有效降低NOx排放,对于满足严格的排放标准具有重要意义。
另一方面,方形和圆柱形燃烧室在某些应用中可能更为合适。
航空发动机燃烧室设计

航空发动机燃烧室设计航空发动机燃烧室设计:1. 燃烧室的基本结构利用燃烧室的合理结构满足内部气流的特性,并且能够实现一个良好的燃烧过程,是一项有技术难度的工作。
燃烧室基本结构由燃烧室壁、发动机尾焰片和入口部件组成,前者主要用于分旋流和折大压力系数,后者主要为了增加热导率和削减气流噪声,最后用于吸入空气和助燃气体。
2. 燃烧室的内壁燃烧室内壁是用以帮助燃烧过程及其它流线形态中的重要组成部分。
除了保持空气的理想状态,内壁还可以降低发动机噪声,减少热群聚,增加发动机性能和燃料消耗效率。
同时,内壁的抗老化和防腐性能也是重要考虑因素,其中一项重要材料是陶瓷纤维制品,其具有良好的抗老化性能和抗压强度,使用寿命长达20年以上。
3. 燃烧室的入口部件为了提高发动机的气体流动,必须设计入口部件,下游是一组混流涡旋,上游是一组分离涡旋。
尾涡旋可以增加燃料分布的一致性,混流涡旋可以增强液滴的发散性,因而有利于提升燃烧效率和加强发动机推力。
同时,为了提高流动特性,入口部件需要把内部流动结构分成多个区域,从而实现减少空气阻力损失和梯度放大的双重功能。
4. 燃烧室的尾焰片尾焰片是一个重要的部件,它将燃烧室内的气体耦合到尾部,以便用少量的热能把空气扩展成大量的推力,从而提高发动机性能。
尾焰片具有一定的翅版构成,可以改变流体的流动特性,消除尾风湍流,增加发动机效率。
5. 燃烧室的流线燃烧室的流线设计是决定一个发动机性能的关键因素。
它必须考虑流量、速度、温度、压力等因素,从而确定出最佳的流线状态,提供最佳的燃烧条件。
一些技术手段可以用来改善燃烧室的流量性能,如多级弯角、折叶面、挡板、凹道等,它们可以把气体推向尾部,从而获得更大的推力。
6. 其他设计要点设计中还应考虑燃烧室内的温度,在最大推力时,温度为1700℃,而在进行爆发性发动机式的运转时,可以达到3000℃左右,因此必须采取措施防止和减少温度热副作用,以保护后部结构元件。
另外,还应当考虑燃烧室残留碳和噪声,碳消析和噪声级别都要在相关规定范围内。
汽车发动机的燃烧室设计优化策略
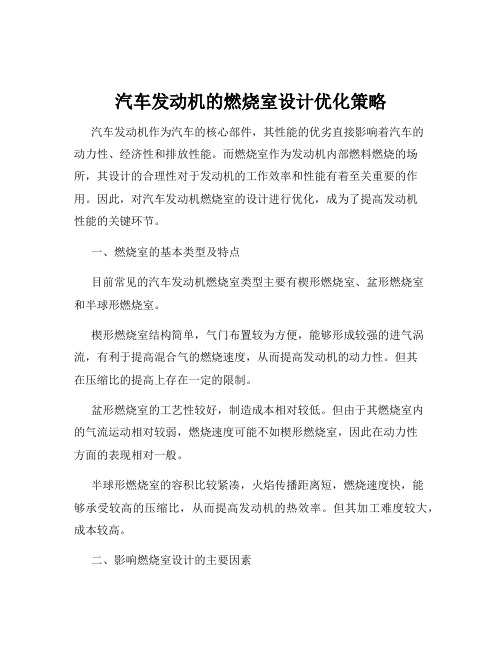
汽车发动机的燃烧室设计优化策略汽车发动机作为汽车的核心部件,其性能的优劣直接影响着汽车的动力性、经济性和排放性能。
而燃烧室作为发动机内部燃料燃烧的场所,其设计的合理性对于发动机的工作效率和性能有着至关重要的作用。
因此,对汽车发动机燃烧室的设计进行优化,成为了提高发动机性能的关键环节。
一、燃烧室的基本类型及特点目前常见的汽车发动机燃烧室类型主要有楔形燃烧室、盆形燃烧室和半球形燃烧室。
楔形燃烧室结构简单,气门布置较为方便,能够形成较强的进气涡流,有利于提高混合气的燃烧速度,从而提高发动机的动力性。
但其在压缩比的提高上存在一定的限制。
盆形燃烧室的工艺性较好,制造成本相对较低。
但由于其燃烧室内的气流运动相对较弱,燃烧速度可能不如楔形燃烧室,因此在动力性方面的表现相对一般。
半球形燃烧室的容积比较紧凑,火焰传播距离短,燃烧速度快,能够承受较高的压缩比,从而提高发动机的热效率。
但其加工难度较大,成本较高。
二、影响燃烧室设计的主要因素1、压缩比压缩比是指气缸总容积与燃烧室容积之比。
压缩比的大小直接影响着混合气的压缩程度和燃烧温度。
较高的压缩比可以提高燃烧效率和热效率,但也容易导致爆震等问题。
因此,在设计燃烧室时,需要综合考虑燃料的性质、发动机的工作条件等因素,选择合适的压缩比。
2、进气涡流进气涡流可以促进混合气的混合和燃烧。
通过合理设计进气道的形状和气门的布置,可以在燃烧室内形成较强的进气涡流,提高燃烧速度和燃烧稳定性。
3、火花塞位置火花塞的位置直接影响着点火的可靠性和火焰传播的速度。
一般来说,火花塞应布置在燃烧室内混合气浓度较高、气流速度适中的位置,以确保快速、可靠地点火和燃烧。
4、燃烧室形状燃烧室的形状应有利于形成均匀的混合气、组织合理的气流运动和火焰传播。
例如,燃烧室的容积分布应尽量均匀,避免出现局部混合气过浓或过稀的情况。
三、燃烧室设计优化的策略1、优化燃烧室形状通过采用先进的计算机模拟技术,如CFD(计算流体动力学)分析,可以对不同形状的燃烧室进行模拟计算,评估其燃烧过程和性能,从而选择最优的燃烧室形状。
汽车发动机燃烧室设计计算
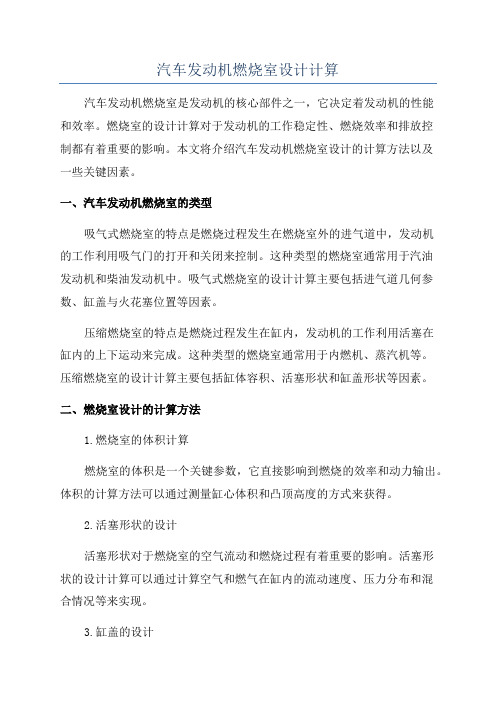
汽车发动机燃烧室设计计算汽车发动机燃烧室是发动机的核心部件之一,它决定着发动机的性能和效率。
燃烧室的设计计算对于发动机的工作稳定性、燃烧效率和排放控制都有着重要的影响。
本文将介绍汽车发动机燃烧室设计的计算方法以及一些关键因素。
一、汽车发动机燃烧室的类型吸气式燃烧室的特点是燃烧过程发生在燃烧室外的进气道中,发动机的工作利用吸气门的打开和关闭来控制。
这种类型的燃烧室通常用于汽油发动机和柴油发动机中。
吸气式燃烧室的设计计算主要包括进气道几何参数、缸盖与火花塞位置等因素。
压缩燃烧室的特点是燃烧过程发生在缸内,发动机的工作利用活塞在缸内的上下运动来完成。
这种类型的燃烧室通常用于内燃机、蒸汽机等。
压缩燃烧室的设计计算主要包括缸体容积、活塞形状和缸盖形状等因素。
二、燃烧室设计的计算方法1.燃烧室的体积计算燃烧室的体积是一个关键参数,它直接影响到燃烧的效率和动力输出。
体积的计算方法可以通过测量缸心体积和凸顶高度的方式来获得。
2.活塞形状的设计活塞形状对于燃烧室的空气流动和燃烧过程有着重要的影响。
活塞形状的设计计算可以通过计算空气和燃气在缸内的流动速度、压力分布和混合情况等来实现。
3.缸盖的设计缸盖的设计主要包括进气道和排气道的形状和尺寸。
进气道的设计计算可以通过流体力学模拟方法来实现,排气道则需要考虑到排气阻力和排气温度的影响。
4.碳烟排放控制的计算碳烟是柴油发动机排放中的一个重要污染物,燃烧室的设计可以通过优化喷油系统、增加空气预混和比例和改变缸压的方式来减少碳烟的排放。
三、燃烧室设计的关键因素1.进气道和排气道的形状和尺寸进气道和排气道的形状和尺寸会直接影响到燃烧室的空气流动和燃烧效率。
进气道需要满足流通性好、油品雾化均匀的要求,排气道则需要满足排气阻力小、排气温度低的要求。
2.缸盖的设计缸盖的设计需要注意到进气道和排气道的布局、火花塞位置和活塞形状等因素。
缸盖的设计需要保证燃烧室的充分混合、燃烧效率高和排气顺畅。
高压燃烧室设计及优化

高压燃烧室设计及优化第一章绪论高压燃烧室是将燃料和空气混合后进行高温高压燃烧的装置,是内燃机、燃气涡轮及工业锅炉等热能设备的重要组成部分。
高压燃烧室的设计和优化对于提高设备的热效率、降低排放和延长使用寿命等方面都具有重要意义。
本文主要介绍高压燃烧室的设计和优化方法。
第二章高压燃烧室的设计高压燃烧室的设计必须考虑燃烧效率、排放、热稳定性等因素。
燃烧室的形状、尺寸、布局、喷嘴位置、进气口、出气口等都会影响燃烧效率和排放。
为了提高燃烧效率和降低排放,设计燃烧室时需要考虑以下几个方面:1. 燃烧室的形状和尺寸燃烧室的形状和尺寸对燃烧效率和稳定性有很大影响。
一般来说,较浅的燃烧室可以提高燃烧效率,但是容易出现燃烧不稳定现象;而较深的燃烧室可以提高稳定性,但不能很好地利用燃料。
因此,需要在形状和尺寸之间寻找最佳平衡点。
2. 喷射器的位置喷嘴的位置对燃烧室的燃烧效率和排放有很大影响。
正确选择喷嘴的位置可以提高燃烧效率和降低排放。
一般来说,应该将喷嘴放在燃烧室中心,这可以提高燃烧效率和稳定性。
3. 进气口和出气口的位置进气口和出气口的位置也对燃烧效率和稳定性有很大影响。
正确选择进气口和出气口的位置可以促进气流的均匀分布,提高燃烧效率和稳定性。
综上所述,高压燃烧室的设计必须考虑多个因素,需要在多个方面进行权衡和妥协,以达到最佳平衡点。
第三章高压燃烧室的优化高压燃烧室的优化是指通过模拟、实验和优化算法等方法,对燃烧室的设计进行优化,以达到更高的燃烧效率和更低的排放。
1. 数字模拟优化数字模拟优化是通过计算流体力学(CFD)等软件模拟燃烧室内的流动、传热和化学反应等过程,分析燃烧室内的温度、压力、反应物浓度和污染物浓度等参数的变化规律,以寻找最佳的设计方案。
2. 实验优化实验优化是通过实验研究,寻找最佳的设计方案。
实验可以采用静态试验和动态试验两种方法。
静态试验主要是在实验室中进行的,通过对不同参数的燃料在不同气体压力下的燃烧进行测试,来确定不同参数下的燃烧室性能。
航空发动机的燃烧室设计与优化

航空发动机的燃烧室设计与优化航空发动机是现代航空技术的核心之一,它直接关系到航空的安全性、经济性以及环境保护。
而燃烧室作为发动机的关键部件之一,其性能直接影响发动机的功率、效率以及排放等方面。
因此,航空发动机的燃烧室设计和优化是现代航空技术的研究热点之一,也是提高发动机性能和降低环境污染的重要手段。
一、燃烧室的基本原理燃烧室是航空发动机的核心部件之一,它是将空气和燃料混合后进行燃烧并产生高温高压气体的地方。
它的主要作用是将汽油等燃油燃烧后产生的高温高压气体推入涡轮机,使其转动从而产生动力。
燃烧室的基本原理是将空气和燃料混合并进行燃烧,产生高温高压气体来驱动涡轮机。
在这个过程中,燃烧室内的温度高达1500℃以上,同时还要经受高压力和高速流动的空气和燃料。
因此,燃烧室的设计和优化至关重要,不仅要保证燃料充分燃烧,还要保证燃烧室的强度和密封性。
二、燃烧室设计的关键因素燃烧室的设计是航空发动机的核心之一。
在燃烧室的设计过程中,涉及到许多关键因素,包括燃料喷射和混合、燃料燃烧和热传递以及燃烧室的强度和密封性等方面。
1.燃料喷射和混合燃料的喷射和混合是燃烧室设计的重要因素之一。
对于燃油等液体燃料,其喷射和混合质量直接影响到燃料的燃烧效率和排放水平。
因此,在燃料喷射和混合方面的研究和优化对于提高发动机的效率和降低污染的有重要的作用。
2.燃料燃烧和热传递燃料的燃烧和热传递是燃烧室设计的另一个重要因素。
在燃料燃烧的过程中,需要保证燃烧的充分性和一致性,同时还要控制燃烧时产生的高温高压气体对燃烧室内部的冷却系统的影响,从而保证发动机的安全性和稳定性。
3.燃烧室的强度和密封性燃烧室的强度和密封性对于发动机的效率和安全性也有重要的影响。
在高温高压气体的环境下,燃烧室需要充分考虑强度和耐久性的问题,同时还需要具有良好的密封性,以避免气体泄漏对发动机产生的危害。
三、燃烧室设计的优化燃烧室设计的优化是航空发动机研究的重要方向之一。
天然气燃烧的燃烧室设计与优化

天然气燃烧的燃烧室设计与优化天然气是一种清洁、高效的能源,广泛应用于家庭和工业领域。
而天然气的燃烧过程中,燃烧室的设计和优化是至关重要的,它直接影响着燃烧效率和排放物的产生。
本文将探讨天然气燃烧的燃烧室设计与优化方法。
一、燃烧室的基本原理燃烧室是将燃料与氧气混合并点燃的空间,通过燃料的燃烧产生热能。
在天然气燃烧室中,需要考虑燃料的混合、点火和燃烧过程的控制。
1. 燃料混合天然气是以甲烷为主要成分的混合气体,燃料混合的均匀程度直接影响着燃烧过程的效率。
因此,在设计燃烧室时,需要考虑如何实现燃料与氧气的充分混合。
2. 点火点火是燃料在燃烧室中开始燃烧的过程。
合适的点火机制可以提高燃料的燃烧效率。
常见的点火方式有电击点火、火花点火和预混合点火等。
3. 燃烧过程控制燃烧过程的控制包括燃烧室内温度的控制、燃料的供给控制、空气的供给控制等。
合理的燃烧过程控制可以提高燃烧的效率和稳定性。
二、燃烧室设计的关键因素1. 空气比和燃料比空气比和燃料比是燃烧室设计中的重要参数。
空气比指的是燃料和氧气之间的比例关系,燃料比指的是燃料和空气之间的比例关系。
合适的空气比和燃料比可以提高燃烧效率和减少氮氧化物的排放。
2. 燃料喷射方式燃料的喷射方式也是燃烧室设计中需要考虑的因素。
常见的喷射方式有分散喷射和预混合喷射。
不同的喷射方式对燃烧过程有不同的影响,需要选择合适的方式来优化燃烧效果。
3. 燃烧室结构燃烧室的结构也会影响燃烧效果。
合适的燃烧室结构可以提供充分的空间和时间供燃料和氧气混合燃烧,提高燃烧效率和稳定性。
三、燃烧室优化方法1. 数值模拟通过数值模拟可以模拟燃烧室内的流动、传热和化学反应等过程,优化燃烧室设计。
数值模拟可以提供详细的参数信息,帮助分析和优化燃烧室的性能。
2. 实验测试实验测试是优化燃烧室设计的重要手段。
通过实验测试可以获得燃烧室内的实际工作状态和性能数据,根据这些数据进行优化。
3. 综合优化燃烧室的设计和优化需要综合考虑空气比、燃料比、喷射方式和燃烧室结构等因素。
火箭发动机燃烧室优化设计

火箭发动机燃烧室优化设计
火箭发动机燃烧室是火箭发动机的核心部件,直接影响火箭的性能和效率。
因此,对燃烧室进行优化设计是非常重要的。
首先,燃烧室的设计需要考虑燃烧效率。
为了提高燃烧效率,可以采用多级燃
烧室设计,即在燃烧室中设置多个燃烧区域,以充分燃烧燃料。
此外,还可以采用预混合燃烧技术,即在燃烧室中预混合燃料和氧化剂,以提高燃料燃烧效率。
其次,燃烧室的设计还需要考虑热冲击和热膨胀问题。
为了减轻燃烧室受到的
热冲击,可以采用陶瓷涂层等材料来增加燃烧室的耐热性。
同时,还可以通过设计合理的冷却系统来减轻燃烧室受到的热膨胀影响,从而延长燃烧室的使用寿命。
另外,燃烧室的设计还要考虑燃气流动问题。
为了提高燃气的流动性能,可以
采用优化的燃气进出口设计,以减少流阻并提高燃烧效率。
此外,还可以通过设计合理的喷嘴结构来控制燃气的流动方向,从而提高火箭的推力和稳定性。
总的来说,火箭发动机燃烧室的优化设计是一个复杂而重要的工程问题,需要
综合考虑各种因素,包括燃烧效率、热冲击和热膨胀问题以及燃气流动性能等因素。
只有通过科学合理的设计和优化,才能提高火箭发动机的性能和效率,实现火箭的顺利发射和飞行。
完全燃烧炉结构设计

完全燃烧炉结构设计一、燃烧室设计燃烧室是燃烧炉的核心部分,其设计应满足高效燃烧、低污染排放和长寿命的要求。
燃烧室应采用耐高温、耐腐蚀的材料,设计应充分考虑热能转换效率和燃料适应性。
同时,燃烧室应具备足够的容量,以适应不同燃料和负荷下的燃烧需求。
二、燃料供应系统燃料供应系统负责将燃料输送到燃烧室,其设计应确保燃料的稳定供应和精确计量。
燃料供应系统应包括燃料储存、输送和计量设备,以及必要的过滤和调节装置。
此外,燃料供应系统还应具备安全切断和过载保护功能,以防止燃料泄漏和设备故障。
三、空气供给系统空气供给系统负责向燃烧室提供足够的氧气,以确保燃料完全燃烧。
空气供给系统应包括鼓风机、调节阀和空气管道等设备,同时还应配备空气过滤装置,以减少空气中的尘埃和有害气体对燃烧过程的影响。
合理的空气供给系统设计能够有效降低氮氧化物等有害气体的排放。
四、热量回收系统热量回收系统负责将燃烧产生的热量进行有效回收和利用。
常见的热量回收方式包括余热锅炉、热交换器和热力管网等。
热量回收系统应根据燃烧炉的工艺要求和热量需求进行设计,以提高热能利用率和降低能耗。
五、排烟系统排烟系统负责将燃烧产生的烟气排出,其设计应确保烟气能够顺畅排出,同时减少对环境的污染。
排烟系统应包括烟囱、除尘器和脱硫脱硝设备等。
此外,排烟系统还应配备烟气流量控制装置和排放监测设备,以确保烟气排放符合环保标准。
六、安全控制系统安全控制系统负责对燃烧炉的运行状态进行实时监测和控制,以确保设备和人员的安全。
安全控制系统应包括温度传感器、压力传感器、火焰监测器等设备,以及安全阀、紧急切断阀等控制装置。
安全控制系统还应具备故障诊断和报警功能,以便及时发现和处理潜在的安全隐患。
七、监测与控制系统监测与控制系统负责对燃烧炉的各项参数进行实时监测和调控,以确保燃烧过程的稳定性和经济性。
监测与控制系统应包括各种传感器、控制仪表和自动化控制设备等。
通过监测与控制系统,可以实现对燃烧过程的精确控制,提高燃烧效率,降低能耗和污染物排放。
汽油机燃烧室的设计原则

汽油机燃烧室的设计原则1.燃烧效率:燃烧室的设计应确保燃烧过程充分、稳定和完全。
燃烧室应该能够提供足够的空气和燃料混合,并且使其在适当的时间和位置点火。
合适的燃烧过程可以保证发动机提供的动力更强大,同时减少能量损失和废气排放。
2.热传递和热损失:燃烧室的设计应尽量减少热能的损失和传递。
通过合理地选择材料和减小热辐射、对流和传导等热能流失方式,可以提高燃烧室热效率,使燃料的能量更好地转化为机械动力,从而提高发动机的整体能效。
3.燃烧稳定性:燃烧室的设计需要保证燃烧的稳定性,因为不稳定的燃烧容易引起发动机噪音、震动、磨损和过度自燃等问题。
通过合理的气缸形状、喷油器的位置和喷雾特性等设计,可以提供稳定的燃烧条件,使发动机运行更加平稳和可靠。
4.污染物排放:燃烧室的设计需要降低废气排放,特别是氮化物(NOx)、碳氢化合物(HC)和颗粒物的排放。
通过优化燃烧室的结构和形状,改善燃烧过程,可以减少废气中有害物质的生成和排放,从而降低对环境的污染。
5.运行特性:燃烧室的设计需要满足不同工况下的需求,包括低负荷和高负荷工况。
燃烧室应该能够在不同负荷下提供合适的燃烧速率、效率和排放性能,并且保持较宽的工作范围。
6.成本和制造工艺:燃烧室的设计还需要考虑成本和制造工艺的因素。
燃烧室的结构应该简单、易于制造,并且能够适应大批量生产的要求。
综上所述,燃烧室的设计要遵循燃烧效率、热能传递、燃烧稳定性、排放控制、运行特性和成本等原则。
通过合理地选择燃烧室的结构、形状、喷油器位置和喷雾特性等设计参数,可以实现更高效、环保和可靠的汽油机燃烧室。
发动机燃烧室的设计与优化

发动机燃烧室的设计与优化发动机燃烧室作为内燃机的核心部件之一,对整体性能和燃烧效率具有重要影响。
本文将从燃烧室的设计原理、结构和优化措施等方面进行探讨。
一、燃烧室的设计原理燃烧室的设计原理包括燃烧模式选择、空燃比控制和燃烧室气流形态等。
根据发动机的工作循环和要求,可以选择不同的燃烧模式,如充分燃烧、混合燃烧或均质燃烧等。
同时,在设计过程中,还需要关注空燃比的控制,以实现最佳的燃烧效率和排放性能。
此外,燃烧室的气流形态也需要合理设置,以达到充分混合、紊流和均质化的效果。
二、燃烧室的结构设计燃烧室的结构设计需要考虑燃烧室的形状、尺寸、进气和排气系统等因素。
首先,燃烧室的形状决定了气流的流动规律和燃烧效果,一般可选择球形、圆柱形或梯形等结构。
其次,燃烧室的尺寸应根据具体应用需求和发动机参数来确定,以实现最佳的燃烧效率和功率输出。
此外,燃烧室的进气和排气系统需要合理设计,以确保充分的进气和排气量,避免压力损失和二次燃烧等不良影响。
三、燃烧室的优化措施为了进一步提高燃烧效率和减少排放,需要采取一系列优化措施。
一方面,可以通过优化燃烧室的喷油系统,实现燃油的均匀喷射和细碎雾化,以增加与空气的充分混合。
另一方面,通过调整燃烧室的缸盖结构和气缸壁面形态,改善燃烧室的流场特性,减小湍流损失和热能损失。
此外,还可以采用陶瓷涂层等新材料和技术,提高燃烧室的热效应和耐火性能。
四、燃烧室的仿真与优化为了更好地研究燃烧室的性能和进行优化设计,可以借助计算流体力学(CFD)等仿真工具进行模拟和分析。
通过建立准确的三维模型和合理的边界条件,可以对燃烧室的气流和燃烧过程进行细致的数值模拟。
同时,还可以进行参数敏感性分析和优化算法,以寻求最佳的燃烧室设计方案。
五、燃烧室的发展趋势随着科技的不断进步和对环保性能要求的提高,燃烧室的设计和优化也面临着新的挑战和机遇。
未来的燃烧室设计将更加注重燃烧效率和排放性能的综合优化,采用更先进的材料和工艺,以适应不同燃料和运行条件的需求。
燃气轮机的燃烧室设计与性能分析

燃气轮机的燃烧室设计与性能分析燃气轮机是一种广泛应用于能源领域的热能转换设备,其核心部件之一就是燃烧室。
燃气轮机通过利用燃料燃烧产生高温高压的气体,驱动涡轮转动,从而完成能量转换。
燃烧室的设计和性能对燃气轮机的运行稳定性、燃烧效率和排放水平等方面起着至关重要的作用。
燃烧室的设计首先要考虑的是能够实现高效的燃烧过程,以提高燃气轮机的热效率。
在传统的燃气轮机燃烧室中,通常采用顶置式燃烧室,即燃烧室位于压气机与涡轮之间,压气机吸入的空气经过燃烧室后驱动涡轮运转。
而在现代燃气轮机的燃烧室设计中,越来越多地采用预混合式燃烧室,即在燃烧过程中预先将燃料和空气充分混合后再进行燃烧。
这种设计可以有效地提高燃烧效率和减少氮氧化物的排放。
燃烧室的性能分析主要包括燃烧效率、燃烧稳定性和排放水平等方面的参数评估。
燃烧效率是衡量燃烧室性能的重要指标之一。
燃气轮机的燃烧室在燃料燃烧过程中要尽可能地释放更多的热能,同时尽量减少未完全燃烧的产物。
通过优化燃烧室的结构和燃烧过程参数,如燃料供给量、空气配比等,可以提高燃烧效率。
燃烧稳定性是燃气轮机燃烧室设计中另一个重要考虑因素。
燃烧室的稳定性决定了燃烧过程的可控性和可靠性。
燃气轮机燃烧室的设计应该能够在不同负荷和工况下保持稳定的燃烧,不会出现过度火焰或火焰熄灭的情况。
为了提高燃烧稳定性,燃烧室通常采用一定的流场设计和稳定器等技术手段。
同时,对燃烧室进行流动仿真分析和实验验证也是提高稳定性的重要途径。
排放水平是燃气轮机燃烧室设计中不可忽视的问题。
燃烧室的燃烧过程中会产生大量的污染物和废气,如氮氧化物、二氧化硫和颗粒物等。
为了减少环境污染,燃气轮机燃烧室设计需要考虑降低这些污染物的排放量。
常用的方法包括提高燃烧效率、采用低氮燃烧技术、使用排放控制装置等。
通过综合考虑燃烧室结构、燃料供给系统和废气处理设备等因素,可以有效地降低燃烧室的排放水平。
总之,燃气轮机的燃烧室设计和性能分析是燃气轮机工程中的重要环节。
内燃机用断流器的燃烧室设计与优化
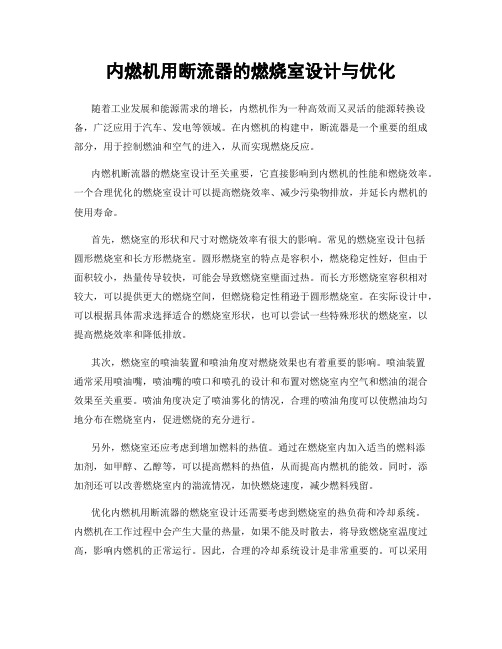
内燃机用断流器的燃烧室设计与优化随着工业发展和能源需求的增长,内燃机作为一种高效而又灵活的能源转换设备,广泛应用于汽车、发电等领域。
在内燃机的构建中,断流器是一个重要的组成部分,用于控制燃油和空气的进入,从而实现燃烧反应。
内燃机断流器的燃烧室设计至关重要,它直接影响到内燃机的性能和燃烧效率。
一个合理优化的燃烧室设计可以提高燃烧效率、减少污染物排放,并延长内燃机的使用寿命。
首先,燃烧室的形状和尺寸对燃烧效率有很大的影响。
常见的燃烧室设计包括圆形燃烧室和长方形燃烧室。
圆形燃烧室的特点是容积小,燃烧稳定性好,但由于面积较小,热量传导较快,可能会导致燃烧室壁面过热。
而长方形燃烧室容积相对较大,可以提供更大的燃烧空间,但燃烧稳定性稍逊于圆形燃烧室。
在实际设计中,可以根据具体需求选择适合的燃烧室形状,也可以尝试一些特殊形状的燃烧室,以提高燃烧效率和降低排放。
其次,燃烧室的喷油装置和喷油角度对燃烧效果也有着重要的影响。
喷油装置通常采用喷油嘴,喷油嘴的喷口和喷孔的设计和布置对燃烧室内空气和燃油的混合效果至关重要。
喷油角度决定了喷油雾化的情况,合理的喷油角度可以使燃油均匀地分布在燃烧室内,促进燃烧的充分进行。
另外,燃烧室还应考虑到增加燃料的热值。
通过在燃烧室内加入适当的燃料添加剂,如甲醇、乙醇等,可以提高燃料的热值,从而提高内燃机的能效。
同时,添加剂还可以改善燃烧室内的湍流情况,加快燃烧速度,减少燃料残留。
优化内燃机用断流器的燃烧室设计还需要考虑到燃烧室的热负荷和冷却系统。
内燃机在工作过程中会产生大量的热量,如果不能及时散去,将导致燃烧室温度过高,影响内燃机的正常运行。
因此,合理的冷却系统设计是非常重要的。
可以采用循环冷却或喷雾冷却的方式,有效地控制燃烧室温度。
另外,还可以在设计中增加一些热隔离材料,减少燃烧室与其他部件之间的热交换,保持较低的温度。
总之,对于内燃机用断流器的燃烧室设计与优化来说,合理的形状和尺寸,喷油装置和角度的选取,以及适当的燃料添加剂和冷却系统的设计,都是关键的因素。
关于燃烧室的设计
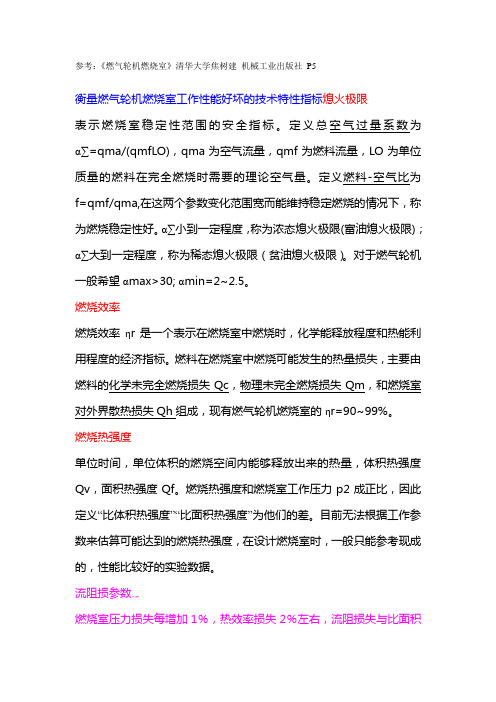
参考:《燃气轮机燃烧室》清华大学焦树建机械工业出版社P5% N: z2 B# D' ^2 R6 n$ w衡量燃气轮机燃烧室工作性能好坏的技术特性指标熄火极限 2 _: P4 A8 Z: W3 |% [表示燃烧室稳定性范围的安全指标。
定义总空气过量系数为α∑=qma/(qmfLO),qma为空气流量,qmf为燃料流量,LO为单位质量的燃料在完全燃烧时需要的理论空气量。
定义燃料-空气比为f=qmf/qma,在这两个参数变化范围宽而能维持稳定燃烧的情况下,称为燃烧稳定性好。
α∑小到一定程度,称为浓态熄火极限(富油熄火极限);α∑大到一定程度,称为稀态熄火极限(贫油熄火极限)。
对于燃气轮机一般希望αmax>30; αmin=2~2.5。
$ E4 f5 L- P; d1 |: l- n% z燃烧效率燃烧效率ηr是一个表示在燃烧室中燃烧时,化学能释放程度和热能利用程度的经济指标。
燃料在燃烧室中燃烧可能发生的热量损失,主要由燃料的化学未完全燃烧损失Qc,物理未完全燃烧损失Qm,和燃烧室对外界散热损失Qh组成,现有燃气轮机燃烧室的ηr=90~99%。
! K, @" I( W! P$ w: G$ @7 k6 Z7 ~燃烧热强度7 E! e% [+ u1 ?1 M6 v+ l) }7 p5 J单位时间,单位体积的燃烧空间内能够释放出来的热量,体积热强度Qv,面积热强度Qf。
燃烧热强度和燃烧室工作压力p2成正比,因此定义“比体积热强度”“比面积热强度”为他们的差。
目前无法根据工作参数来估算可能达到的燃烧热强度,在设计燃烧室时,一般只能参考现成的,性能比较好的实验数据。
流阻损参数: w3 V( v5 n% l# H: T燃烧室压力损失每增加1%,热效率损失2%左右,流阻损失与比面积强度的平方成正比,为了设计燃烧热强度很高的燃烧室,就必须付出提高流阻损失系数的代价。
流阻损失系数Φ定义为(入口静压-出口静压)/入口动压。
- 1、下载文档前请自行甄别文档内容的完整性,平台不提供额外的编辑、内容补充、找答案等附加服务。
- 2、"仅部分预览"的文档,不可在线预览部分如存在完整性等问题,可反馈申请退款(可完整预览的文档不适用该条件!)。
- 3、如文档侵犯您的权益,请联系客服反馈,我们会尽快为您处理(人工客服工作时间:9:00-18:30)。
A
A
A-A向视图
多孔式气膜冷却结构
类型 主燃孔 补燃孔 掺混孔
孔直径 36mm 48mm 18mm
开孔数目 8 双排 8 单排 8 双排
气膜冷却小 孔
5mm
管身均匀分 布
• 3 旋流器设计 逆流 径流式旋流器
d1 D
A αs
b
ds
A
A-A向视图
叶片安装角 sw 90
.
;
旋流器内径
•
8 燃烧室低污染排放内容的研究
NOx的产生机理 针对性的防污措施 a.改进燃烧管理,如采用高空燃比燃烧,选用含氮量少的 燃料,空气预热适中,烟气循环,喷水等 b.采用新的燃烧技术和装置,如浓淡燃烧,二级或者多级 燃烧,分割火焰燃烧,预混预蒸发燃烧,变几何燃烧装 置,催化燃烧室等。
• 9 燃烧室试验研究 试验的必要性:理论不成熟 调整手段 试验的方法:试验 测定参数不断改进 试验需要测定的参数:
b
b
Q Af
变工况性能 点火特性
出口温度场 排气污染成分
火焰管壁面温度
第四部分 燃烧室结构图展示
旋流器
火焰管头部
射流孔布置结构
火焰管壁面气膜冷却结构
火焰管管身结构
火焰管装配图 (无旋流器)
火焰管装配图(带有旋流器)
第五部分 结论
• 1 燃烧室设计的根本原则是如何组织流场, 使空气和燃料能够在有限的空间内有效的 燃烧; • 2 设计过程中的难点和重点是空气的流量的 分配,但是目前还没有成熟的理论用于分 配空气量,主要还是应用经验公式和统计 数据; • 3 筒形燃烧室结构虽然简单,但是要获得性 能良好的燃烧室仍不是易事;
燃烧室总体尺寸计算结果
• 气体流量分配
设计部分
空气流量分配原则
• 一次空气:头部+数约为2~2.2。其 中由旋流器的空气过量系数为0.25~0.35, 主燃孔约为0.75,其余皆通过补燃孔进入 “主燃区”
• 冷却空气量 初步设计的冷却空气量占总空气量的 30~40%,无法精确地计算出冷却空气量, 一般通过经验公式初步确定:
Lt2 Lt1
• 2 火焰管管身设计 火焰管除去头部,火 焰管圆柱段长度是 0.733m。管身上会加 工出各种进气孔且均 为平流孔。火焰管管 身采用双层壁多孔式 气膜冷却结构,在火 焰管管身均匀分布直 径5mm小孔。
L2
L1
L5
主 燃 孔 一
主 燃 孔 二
补 燃 孔
掺 混 孔 一
掺 混 孔 二
L3 L4
The end! 谢谢各位老师,学 生的不足请老师指正
第二部分
论文的主体结构
绪论部分 :研究背景及意义 ;燃烧室设 计的要求和思路;燃烧室设计理论基础
三 大 部 分
设计部分:热力计算;燃烧室总体尺寸 设计;燃烧室气动设计;各主要零部件 设计。 方案后续设计:燃烧室强度计算和校核; 燃烧室选材;喷嘴选型;低排放措施;燃 烧室试验;结构图的绘制。
小型燃机应用 日渐广泛
旋流器叶片长度 h A s nb
• 4 火焰导管设计
按照等速度梯度计算后得到收 敛段截面变化规律为
Lt
Am
Af At Lx 扩张段 收敛段
Ax
Am Lt L x Lt
• 5 点火装置 采用半导体高能点火喷嘴,点火位置确定
L ig 0 . 68 L max 20 mm
第三部分 设计成果综述
已知设计参数
• 结构尺寸设计部分
• 燃烧室总体布置方案:
单个筒形燃烧室,垂直 布置方案,火焰管内外 气流流动形式为逆流 (原因) • 热力计算结果: 总空气过量系数 α=3.92 天然气质量流 量Gf=0.2799kg/s
•
燃烧室尺寸设计结果:
1. 总体 燃烧室外壳直径Dw=0.42m 总长度Lc=1.08m 2 . 火焰管尺寸 火焰管圆柱段横截面积Af=0.06521m2 火焰管管身直径Df=0.2821m(设计参照) 火焰管长度Lf=3.1Df 火焰管头部设计为半球形,长度为0.5Df
d1 D
f
0 . 4 ~ 0 . 425 ;
旋流器内径和外径之比为0.7;
旋流器叶片火焰管入口直径
旋流器叶片数n=8;
ds D
f
0 . 36 ~ 0 . 4
2
180 旋流器叶片喉部宽度 b d 1 sin n D 2 d 2 As 旋流器通流面积 4
360 cos n
符号
Gs
轴向距离 (m) 流量(kg/s) 0 0.0403 0.0806 0.1209 0.1975 0.2821 0.4232 0.5642 0.0160 (注) 管身均匀 分布
1.062 0.638 0.638
第一排头部冷却孔 第二排头部冷却孔 第三排头部冷却孔 第一排主燃孔 第二排主燃孔 补燃孔 第一排掺混孔 第二排掺混孔
各位老师好!
• 任务书中预期完成任务: • 1 小型燃气轮机燃烧室热力和结构设计 • 2 绘制燃烧室结构图
汇报内容
• • • • • 1 任务书完成情况 2 论文主体结构 3 设计成果汇报 4 燃烧室结构图绘制 5 结论
第一部分 任务书完成情况
• • • 完成燃烧室的热力计算 燃烧室的结构和气动设计 燃烧室结构图的绘制
L ig
L ——点火器的轴向安装位置(离旋流器的出口距离)
ig
L max ——回流区最大直径截面离旋流器出口的距离 ,且
L max 0 . 45 D
f
计算结果 L ig 105 . 91 mm
2
• 6 燃料喷嘴选型 天然气燃料的使用 双燃料喷嘴 采用单路离心喷嘴和一个多孔式烧气喷嘴 并联组成一个双燃料喷嘴
do
β
h θ
e
l’
Lt3
三道气膜冷却结构位置确定: Lt1=0.040m Lt2=0.080m Lt3=0.120m
每段斑孔氏气膜冷却机构中环 形结构开口位置,经计算每段 圆环均宽度并考虑加工工艺均 可以取3mm 头部空气过量系数αt=0.45, 空气质量流量 G1=1.914kg/s,11.5%
• 4 对燃烧室而言,重要的零部件如旋流器,冷却 和掺混机构,喷嘴等对燃烧室意义颇大,在设计 中应该重视; • 5燃烧室试验是燃烧室设计不可或缺的一部分内容, 燃烧室的设计定型主要是依靠试验手段获得的。 必须通过大量的试验,对初步设计内容做不断的 修改,才可能得到性能良好的燃烧室; • 6 现代燃气轮机的不断发展离不开先进的燃烧技 术,但是目前燃烧理论还很不成熟,对燃烧室设 计而言是个很大的障碍。
研 究 背 景
现代燃气轮机 技术相对独立 的一个领域
燃烧室是燃气轮 机三大部件之一
燃烧室两种功能
• 由压气机流出的一 部分气体和燃料混 合进行燃烧,为整 个燃气轮机供应能 量;
另一部分压缩空气 与燃烧后的高温燃气 进行掺混,使其温度 降低至涡轮叶片能够 承受的燃气温度
• 燃烧室设计要求: • 1 工作可靠性要求:点火 效率 寿命 强度 温 度场 • 2 经济性能要求:燃烧完全 流阻小 • 3 维护保养方面要求:便于维修 拆装
G 11
G 12
G 13
0.638
1.593 1.593
G
p1
G p2
Gb
4.247
1.084
G d1
Gd2
Gg
1.084
3.330
火焰管气膜冷却空气量
注:第二排掺混孔的轴向参考距离是火焰管出口截面
主要零部件的设计
• 1 火焰管头部设计
半球形,采用三道斑孔氏气膜冷却结构,每道 孔开76个6mm的小孔,β 为60度,气膜长度是 45mm。
• 7 强度校核及选材 燃烧室不是燃气轮机中主要的承力构件,主要承受的是 由于内外压差造成的应力和热应力,尤其是火焰管材料的 选择很重要。燃烧室外壳选用10#钢就满足强度要求,火 焰管选用GH3128 燃烧室外壳按照一端封闭的圆柱体结构进行强度校核,火 焰管按照圆柱体和球形结合体进行强度校核。 经校核所选材料均满足强度要求。
G c 5 . 14 0 . 868 A fs 10
6
kg s
其中头部气膜冷却空气量占总冷却空气量的1/3 左右,其余的用作管身冷却
掺混空气量
• 出去一次空气和气膜冷却空气量,剩余的 就是用于掺混的空气,掺混空气由两排掺 混孔进入火焰管。(空气流量分配结果)
进气孔 旋流器