火箭发动机燃烧室壳体成形工艺设计
航天发动机燃烧室结构优化设计
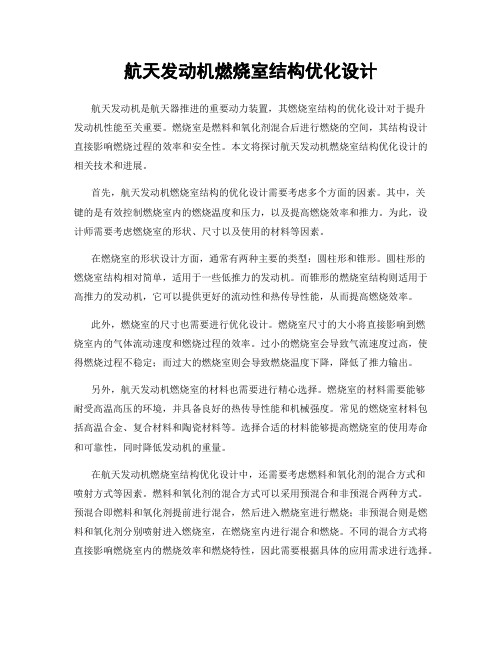
航天发动机燃烧室结构优化设计航天发动机是航天器推进的重要动力装置,其燃烧室结构的优化设计对于提升发动机性能至关重要。
燃烧室是燃料和氧化剂混合后进行燃烧的空间,其结构设计直接影响燃烧过程的效率和安全性。
本文将探讨航天发动机燃烧室结构优化设计的相关技术和进展。
首先,航天发动机燃烧室结构的优化设计需要考虑多个方面的因素。
其中,关键的是有效控制燃烧室内的燃烧温度和压力,以及提高燃烧效率和推力。
为此,设计师需要考虑燃烧室的形状、尺寸以及使用的材料等因素。
在燃烧室的形状设计方面,通常有两种主要的类型:圆柱形和锥形。
圆柱形的燃烧室结构相对简单,适用于一些低推力的发动机。
而锥形的燃烧室结构则适用于高推力的发动机,它可以提供更好的流动性和热传导性能,从而提高燃烧效率。
此外,燃烧室的尺寸也需要进行优化设计。
燃烧室尺寸的大小将直接影响到燃烧室内的气体流动速度和燃烧过程的效率。
过小的燃烧室会导致气流速度过高,使得燃烧过程不稳定;而过大的燃烧室则会导致燃烧温度下降,降低了推力输出。
另外,航天发动机燃烧室的材料也需要进行精心选择。
燃烧室的材料需要能够耐受高温高压的环境,并具备良好的热传导性能和机械强度。
常见的燃烧室材料包括高温合金、复合材料和陶瓷材料等。
选择合适的材料能够提高燃烧室的使用寿命和可靠性,同时降低发动机的重量。
在航天发动机燃烧室结构优化设计中,还需要考虑燃料和氧化剂的混合方式和喷射方式等因素。
燃料和氧化剂的混合方式可以采用预混合和非预混合两种方式。
预混合即燃料和氧化剂提前进行混合,然后进入燃烧室进行燃烧;非预混合则是燃料和氧化剂分别喷射进入燃烧室,在燃烧室内进行混合和燃烧。
不同的混合方式将直接影响燃烧室内的燃烧效率和燃烧特性,因此需要根据具体的应用需求进行选择。
此外,燃料和氧化剂的喷射方式也是优化设计的重要方面。
常见的喷射方式有注入式、气体化和蒸气化等方式。
注入式即将燃料和氧化剂通过喷嘴喷射,气体化则是将液态燃料和氧化剂通过高温和高压进行气化形成气体,蒸气化则是将液态燃料和氧化剂通过加热形成气体。
双流型火箭发动机燃烧室优化设计

双流型火箭发动机燃烧室优化设计随着航天技术的不断进步,火箭发动机作为航天器的核心组件,也在不断推进着自身的发展和优化。
其中,燃烧室作为火箭发动机中最重要的部件之一,直接关系到火箭的性能、效率和安全性。
本文将重点探讨双流型火箭发动机燃烧室的优化设计。
一、双流型火箭发动机燃烧室的基本原理一般情况下,双流型火箭发动机是由两个燃气喷嘴和一个燃烧室构成的。
其中,一个燃气喷嘴负责喷射高热值的燃气,另一个燃气喷嘴则喷射大量的惰性气体,如氮气、氩气等。
这样做的目的主要是降低燃烧室内的燃烧温度,避免过高的燃烧温度对燃烧室和燃烧室内部材料的烧蚀和热应力造成的损坏。
双流型火箭发动机的燃烧室通常由上、下两部分构成。
上部分为高温高压区域,下部分为低温低压区域。
这种结构可以有效地降低燃烧室的温度,并且可以增加燃气流量,提高火箭发动机的推力。
二、双流型火箭发动机燃烧室的优化设计1. 燃烧室内部结构设计燃烧室内部结构的设计是影响火箭发动机性能的重要因素之一。
在设计燃烧室内部结构时,需要考虑到燃气的传输和混合情况。
一般来说,燃气混合得越均匀,燃烧过程就越充分,同时火箭发动机的性能也就越好。
因此,燃烧室内部结构的设计需要保证燃气混合均匀,并且减少燃气的剪切和湍流现象,从而提高燃料的燃烧效率。
2. 喷嘴口径设计喷嘴口径的大小也会对火箭发动机的性能产生影响。
一般来说,较小的喷嘴口径可以增加气流速度,从而提高推力比;但同时也会增加气流速度对燃烧室内部材料的烧蚀和热应力的损害。
因此,在设计喷嘴口径时,需要进行综合考虑,并根据实际需要确定最佳口径大小。
3. 燃气比控制燃气比是指燃料和氧化剂的摩尔比。
在双流型火箭发动机中,需要对燃气比进行控制,以保证燃气在燃烧室内充分混合并燃烧。
同时,也需要注意燃气比的控制必须在安全范围内进行,以避免过高的燃气比导致的燃烧室爆炸等危险情况的发生。
4. 燃烧室材料选择燃烧室内部材料的选择也影响着火箭发动机的性能。
固体火箭发动机燃烧室壳体纤维缠绕模具设计
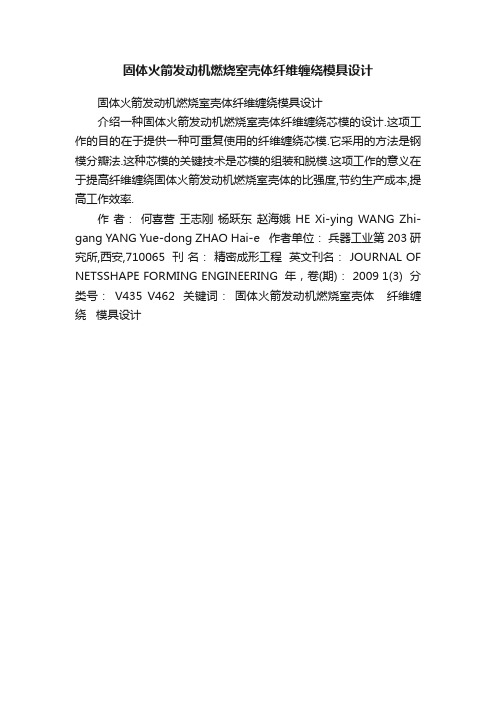
固体火箭发动机燃烧室壳体纤维缠绕模具设计
固体火箭发动机燃烧室壳体纤维缠绕模具设计
介绍一种固体火箭发动机燃烧室壳体纤维缠绕芯模的设计.这项工作的目的在于提供一种可重复使用的纤维缠绕芯模.它采用的方法是钢模分瓣法.这种芯模的关键技术是芯模的组装和脱模.这项工作的意义在于提高纤维缠绕固体火箭发动机燃烧室壳体的比强度,节约生产成本,提高工作效率.
作者:何喜营王志刚杨跃东赵海娥HE Xi-ying WANG Zhi-gang YANG Yue-dong ZHAO Hai-e 作者单位:兵器工业第203研究所,西安,710065 刊名:精密成形工程英文刊名: JOURNAL OF NETSSHAPE FORMING ENGINEERING 年,卷(期): 2009 1(3) 分类号:V435 V462 关键词:固体火箭发动机燃烧室壳体纤维缠绕模具设计。
火箭发动机壳体封头形状最优设计的总极值方法

火箭发动机壳体封头形状最优设计的总极值方法火箭发动机是现代航空航天领域中关键的设备之一,其性能的稳定和可靠性的提高直接关系到任务的成功与否,而火箭发动机的壳体结构则是其重要组成部分之一。
壳体封头作为箱体的重要部件,其设计优化直接影响发动机整体结构的紧凑性和受力性能。
本文将基于总极值方法,简要介绍火箭发动机壳体封头形状最优设计的方法。
总极值方法是一种寻求最优解的优化方法,它的基本思想是在确定的条件下,通过极值问题的求解,找到一个最佳的解决方案。
在火箭发动机中,封头的设计优化就是一个极值问题,主要考虑如下关键因素:拓扑结构、受力状况、约束条件和性能目标。
其中,拓扑结构指封头的外观形状,受力状况是指封头在运行时所承受的载荷,约束条件是指设计过程中需要满足的各种限制条件,如尺寸限制、质量限制等,性能目标则是指设计过程中需要优化的各项性能指标。
封头的形状通常采用数学形式的描述,经常使用的有球冠形、抛物面形、双曲面形、椭球形和圆形等形状。
而封头的优化设计过程就是要寻找一种最优的形状,使得封头在系统的受力、约束和性能目标的条件下,具有稳定、可靠和高效的性能表现。
总极值方法在火箭发动机封头最优设计中的具体应用主要包括以下步骤。
第一步,制定设计目标和优化指标。
根据火箭发动机的运行特点和要求,制定封头的设计目标和相应的优化指标。
这些目标和指标包括:重量、强度、刚度、耐热性能等等。
其中,重量是优化设计的主要目标,因为它直接影响整个系统的质量和功率密度。
第二步,确定运动学和静力学模型。
运动学模型是指封头在运动状态下各项运动参数的计算和分析,根据运动学模型可以确定封头在各种工况下的受力状态和有关的约束条件。
静力学模型则是指封头在静止状态下的加速度、力和力矩等状态,根据静力学模型可以确定封头的强度和刚度等特性。
第三步,执行数值计算和优化分析。
根据确定的运动学和静力学模型,进行数值计算和优化分析。
利用数值计算的方法,对不同的设计方案进行模拟和仿真,获取封头在各种运行状态下的参数和性能指标,并针对优化指标进行分析和比较。
固体火箭发动机T250钢壳体热校形工艺技术研究
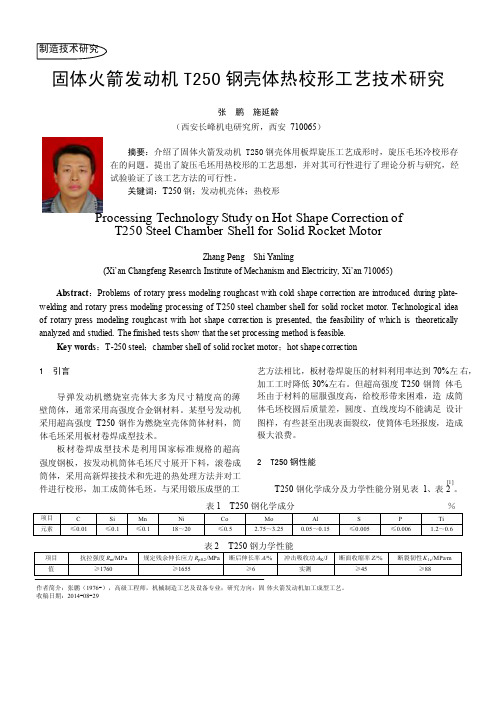
固体火箭发动机 T250 钢壳体热校形工艺技术研究张 鹏 施延龄(西安长峰机电研究所,西安 710065)摘要:介绍了固体火箭发动机 T250 钢壳体用板焊旋压工艺成形时,旋压毛坯冷校形存 在的问题。
提出了旋压毛坯用热校形的工艺思想,并对其可行性进行了理论分析与研究,经 试验验证了该工艺方法的可行性。
关键词:T250钢;发动机壳体;热校形Processing Technology Study on Hot Shape Correction of T250 Steel Chamber Shell for Solid Rocket MotorZhang Peng Shi Yanling(Xi’an Changfeng Research Institute of Mechanism and Electricity, Xi’an 710065)Abstract :Problems of rotary press modeling roughcast with cold shape correction are introduced during plate-welding and rotary press modeling processing of T250 steel chamber shell for solid rocket motor. Technological idea of rotary press modeling roughcast with hot shape correction is presented, the feasibility of which is theoretically analyzed and studied. The finished tests show that the set processing method is f easible.Key words :T-250 steel ;chamber shell of solid rocket motor ;hot shape correction1 引言导弹发动机燃烧室壳体大多为尺寸精度高的薄 壁筒体,通常采用高强度合金钢材料。
固体火箭发动机壳体

固体⽕箭发动机壳体固体⽕箭发动机壳体成型⼯艺固体⽕箭发动机是当今各种导弹武器的主要动⼒装置,在航空航天领域也有相当⼴泛的应⽤。
它的特点是结构简单,因⽽具有机动,可靠,易于维护等⼀系列优点,⾮常适合现代化战争和航天事业的需要。
但是固体⽕箭发动机部件在⼯作中要承受⾼温,⾼压和化学⽓氛下的各种复杂载荷作⽤,因此其材料通常具有极优异的性能,往往代表着当代材料科学的最先进⽔平。
固体⽕箭发动机壳体既是推进剂贮箱⼜是燃烧室,同时还是⽕箭或导弹的弹体,因此,在进⾏发动机壳体材料设计时,要考虑以下⼏个基本原则:(1)固体⽕箭发动机壳体就其⼯作⽅式来讲,是⼀个内压容器,所以壳体承受内压的能⼒是衡量其技术⽔平的⾸要指标;(2)发动机壳体是导弹整体结构的⼀部分,所以⼜要求壳体具有适当结构刚度;(3)作为航天产品,不仅要求结构强度⾼,⽽且要求材料密度⼩;(4)发动机点⽕⼯作时,壳体受到来⾃内部燃⽓的加热,⽽壳体结构材料,尤其是壳体结构复合材料的强度对温度敏感性较强,所以,在设计壳体结构材料时,不能仅限于其常温⼒学性能,⽽应充分考虑其在发动机⼯作过程中,可能遇到的温度范围内的全⾯性能。
结构图⼀、选材1.1、增强纤维:碳纤维固体⽕箭发动机壳体要求复合材料具有⾼的⽐强度,⽐模量和断裂应变。
各种纤维相⽐,碳纤维具有密度⼩,拉伸模量和⽐模量⼤;耐磨耐疲劳等机械性能优秀;耐腐蚀性能好;热膨胀系数⼩,导热率⾼,⾼温下尺⼨稳定性好,不燃,分解温度⾼;具有润滑性;层间剪切强度及纤维强度转化率都⽐较⾼,不易产⽣静电聚集,使⽤温度⾼,不会产⽣热失强,并有吸收雷达波的隐⾝功能等优点。
飞机结构材料要求轻质⾼强,耐疲劳、耐腐蚀性能好,尺⼨稳定,所以碳纤维是最理想的材料。
拉伸模量为262~320GPa,拉伸强度在5GPa左右,断裂延伸率约为1.7%的⾼强中模碳纤维是理想的壳体增强材料。
碳纤维复合材料壳体PV/W值是Keclar49/环氧的1.3~1.4倍,可使壳体质量再度减轻30%,使发动机质量⽐⾼达0.93以上。
燃烧室回转件旋压成形工艺

燃烧室回转件旋压成形工艺燃烧室回转件旋压成形工艺燃烧室作为内燃机的重要组成部分,其质量和功能对整个发动机的性能有着至关重要的影响。
其中,燃烧室回转件是连接高压和低压组成的重要部分,并且对于整个发动机的转速、效率和燃烧效果都有着极为重要的作用。
因此,燃烧室回转件的制造工艺也非常重要。
燃烧室回转件旋压成形工艺就是一种用于制造轴对称轻质壳体的工艺方法。
这种工艺方法具有无切削加工、形成完整、尺寸精度高、表面质量好等优点,被广泛应用于航空航天、船舶、汽车、轮机等高精度领域。
1. 工艺流程燃烧室回转件旋压成形工艺流程主要分为三个步骤:1.1 选材和设计根据燃烧室回转件的具体要求,选择合适的材料并进行设计。
材料要求轻质、强韧、耐高温,如钛合金、铝合金等。
设计要考虑到尺寸、形状和其它要求,并进行三维造型、CAD模拟等。
1.2 热力学处理材料需要先经过热力学处理,消除应力和改善材料性能。
通常包括加热、保温、冷却等处理。
1.3 旋压成形将热力学处理好的材料固定在旋压机上,并根据设计进行旋压成形。
旋压成形是指利用旋转的金属板材依靠轧制变形来实现弯曲、翻边、凸凹成形等,从而形成高精度的轴对称壳体件。
2. 工艺特点2.1 无切削加工燃烧室回转件旋压成形工艺是一种无切削加工的工艺方法,可以避免其他加工方法带来的热变形或机械变形等问题,从而获得更高的成形精度。
2.2 形成完整旋压成形是对整个金属材料进行变形、加工,可以形成较大的轴对称轻质壳体,从而降低零件数量,提高制造效益。
2.3 尺寸精度高燃烧室回转件旋压成形工艺可以实现高精度形状、尺寸,从而可以满足高性能、高要求的燃烧室回转件。
2.4 表面质量好旋压成形能够实现表面光洁度高、无氧化皮、无划痕等特点,可以提高零件表面的耐腐蚀性和美观度。
3. 应用前景随着发动机领域的不断发展,燃烧室回转件旋压成形工艺也得到了广泛的应用,其制造工艺和技术正在不断提高和完善。
未来,在国家大力投入和支持下,燃烧室回转件旋压成形工艺将在高端航空航天、轮机、汽车等领域贡献更大的价值,成为制造业的重要支柱。
火箭发动机燃烧室壳体成形工艺设计

录1 绪论 (1)1.1 课题研究的意义和目的 (1)1.1.1 技术上 (2)1.1.2 经济上 (2)1.2 国内的现状和发展趋势 (3)1.2.1 国内冲压模具发展现状 (3)1.2.2 冲压模具制造技术发展趋势 (4)2 工艺方案设计 (7)2.1 零件工艺性分析 (7)2.2 工艺计算 (7)2.2.1 计算毛坯直径D (7)2.2.2 拉深工艺系数的确定和拉深次数的确定 (8)2.2.3 选取各次半成品底部的圆角半径和各次拉深的高度 (8)2.3 确定工艺方案 (9)3 模具设计 (12)3.1 冲裁模设计 (12)3.1.1 冲裁模具结构形式 (12)3.1.2 模具设计计算 (12)3.2 首次拉深模设计 (16)3.2.1 拉深模工作部分尺寸确定 (16)3.2.2 计算压边力、拉深力 (17)3.2.3 模具的总体设计 (18)3.3 二次拉深模设计 (19)3.3.1拉深模工作部分尺寸确定 (19)3.3.2 计算压边力、拉深力 (19)3.3.3 模具的总体设计 (20)4 冲压工艺规程设计 (22)4.1 冲压工艺规程制定步骤 (22)4.2 该零件冲压工艺的难点 (22)4.3 冲压工艺规程方案的确定 (23)5 模具主要零件的工艺设计 (24)5.1 机械制造工艺设计的一般性原则: (24)5.1.1 零件的工艺分析:结构分析与技术要求分析 (24)5.1.2 毛坯选择 (24)5.1.3 基准选择 (24)5.1.4 拟定工艺路线 (24)5.1.5 机床和工艺装备的确定 (25)5.1.6 工序及加工余量的确定 (25)5.1.7 工序尺寸和公差的确定 (25)5.1.8 切削参数的计算确定 (25)5.1.9 工艺文件的编制 (25)5.2 首次拉深模凹模加工工艺设计 (26)5.2.1 零件分析 (26)5.2.2 选择毛坯 (27)5.2.3 工艺规程设计 (28)5.2.4 工艺卡片的填写 (32)6 结论 (33)参考文献 (34)致谢 (35)1 绪论1.1 课题研究的意义和目的火箭发动机,是指由飞行器自带推进剂(燃料和氧化剂)不依赖外界空气的喷气发动机[1]。
- 1、下载文档前请自行甄别文档内容的完整性,平台不提供额外的编辑、内容补充、找答案等附加服务。
- 2、"仅部分预览"的文档,不可在线预览部分如存在完整性等问题,可反馈申请退款(可完整预览的文档不适用该条件!)。
- 3、如文档侵犯您的权益,请联系客服反馈,我们会尽快为您处理(人工客服工作时间:9:00-18:30)。
录1 绪论 (1)1.1 课题研究的意义和目的 (1)1.1.1 技术上 (2)1.1.2 经济上 (2)1.2 国内的现状和发展趋势 (3)1.2.1 国内冲压模具发展现状 (3)1.2.2 冲压模具制造技术发展趋势 (4)2 工艺方案设计 (7)2.1 零件工艺性分析 (7)2.2 工艺计算 (7)2.2.1 计算毛坯直径D (7)2.2.2 拉深工艺系数的确定和拉深次数的确定 (8)2.2.3 选取各次半成品底部的圆角半径和各次拉深的高度 (8)2.3 确定工艺方案 (9)3 模具设计 (12)3.1 冲裁模设计 (12)3.1.1 冲裁模具结构形式 (12)3.1.2 模具设计计算 (12)3.2 首次拉深模设计 (16)3.2.1 拉深模工作部分尺寸确定 (16)3.2.2 计算压边力、拉深力 (17)3.2.3 模具的总体设计 (18)3.3 二次拉深模设计 (19)3.3.1拉深模工作部分尺寸确定 (19)3.3.2 计算压边力、拉深力 (19)3.3.3 模具的总体设计 (20)4 冲压工艺规程设计 (22)4.1 冲压工艺规程制定步骤 (22)4.2 该零件冲压工艺的难点 (22)4.3 冲压工艺规程方案的确定 (23)5 模具主要零件的工艺设计 (24)5.1 机械制造工艺设计的一般性原则: (24)5.1.1 零件的工艺分析:结构分析与技术要求分析 (24)5.1.2 毛坯选择 (24)5.1.3 基准选择 (24)5.1.4 拟定工艺路线 (24)5.1.5 机床和工艺装备的确定 (25)5.1.6 工序及加工余量的确定 (25)5.1.7 工序尺寸和公差的确定 (25)5.1.8 切削参数的计算确定 (25)5.1.9 工艺文件的编制 (25)5.2 首次拉深模凹模加工工艺设计 (26)5.2.1 零件分析 (26)5.2.2 选择毛坯 (27)5.2.3 工艺规程设计 (28)5.2.4 工艺卡片的填写 (32)6 结论 (33)参考文献 (34)致谢 (35)1 绪论1.1 课题研究的意义和目的火箭发动机,是指由飞行器自带推进剂(燃料和氧化剂)不依赖外界空气的喷气发动机[1]。
火箭发动机主要由燃烧室、燃气发生剂、点火装置及燃气喷嘴组成。
其中火箭发动机燃烧室是用来贮存固体推进剂装药并在其中燃烧的部件。
由筒体壳体、两端封头壳体及绝热层组成。
燃烧室是火箭发动机的重要组成部件,同时也是弹体结构的组成部分,装药在其内燃烧,将化学能转换成热能。
燃烧室承受着高温高压燃气的作用,还承受飞行时复杂的外力及环境载荷[2][3]。
图1.1 固体火箭发动机图1.2 液体火箭发动机由于火箭发动机燃烧室工作时产生高温、高压和强振动,一些推进剂具有极低温和强腐蚀性能,因此燃烧室要求有极高的耐热、耐极低温、抗疲劳、抗腐蚀的性能和良好的机械性能(如强度、刚度等)。
而冲压件刚性好、强度高、重量轻、表面质量好。
冲压加工过程中,材料表面不易遭受破坏,且通过塑性变形还可以使制件的机械性能有所提高[4]。
故用冲压模具来制造该零件。
模具是当今工业生产中使用极为广泛的主要工艺装备,是最重要的工业生产手段和工艺发展方向,一个国家工业水平的高低在很大程度上取决于模具工业的发展水平,模具工业的发展水平是一个国家工业水平的重要的标志之一。
模具工业称作“黄金工业”[5]。
冲压模具作为模具种类之一有以下的优点[6]:1.1.1 技术上(1)在材料消耗不大的前提下,制造出的零件重量轻、刚度好、精度高。
由于在冲压过程中材料的表面不受破坏,使得制件的表面质量较好,外观光滑美观。
并且经过塑性变形后,金属内部组织得到改善,机械强度有所提高。
(2)在压力机的简单冲击作用下,一次工序即可完成由其他加工方法所不能或难以制造完成的较复杂形状零件加工。
(3)制件的精度较高,且能保证零件尺寸的均一性和互换性。
不需要进一步的机械加工即可满足一般的装配和实验要求。
1.1.2 经济上(1)原材料是冶金厂大量生产的价廉的轧制板或带料。
(2)采用适当的工艺后,可大量节约金属材料,可以实现少切屑和无切屑的加工方法。
材料利用率可达75%—85%,因而制件的成本相应地比较低。
(3)节省能源。
冲压时不需要加热,也不象切削加工那样将金属切成碎屑而需要消耗很大的能量。
(4)生产率高。
每分钟一台冲压设备可生产零件从几件到几十件。
目前的高速冲床生产率则每分钟高达数百件甚至上千件。
(5)操作简单,便于组织生产。
在大批量的生产中,易于实现机械化和自动化,进一步提高劳动生产率。
(6)对操作人员的技术要求不高。
当生产需要时,用短期培训的方法既可解决操作人员不足的问题。
由于冲压模具有以上的优点和发展前景和火箭发动机燃烧室壳体严格的质量要求,因此,利用冲压模具来制造火箭发动机热燃烧室壳体工艺设计具有重要意义。
所以本课题的目的就是要制定合理的设计制造工艺(包括模具设计)。
1.2 国内的现状和发展趋势1.2.1 国内冲压模具发展现状改革开放以来,随着国民经济的高速发展,市场对模具的需求量不断增长。
近年来,模具工业一直以15%左右的增长速度快速发展,模具工业企业的所有制成分也发生了巨大变化,除了国有专业模具厂外,集体、合资、独资和私营也得到了快速发展。
浙江宁波和黄岩地区的“模具之乡”;广东一些大集团公司和迅速崛起的乡镇企业,科龙、美的、康佳等集团纷纷建立了自己的模具制造中心;中外合资和外商独资的模具企业现已有几千家。
随着与国际接轨的脚步不断加快,市场竞争的日益加剧,人们已经越来越认识到产品质量、成本和新产品的开发能力的重要性。
而模具制造是整个链条中最基础的要素之一,模具制造技术现已成为衡量一个国家发展水来的标志。
近年许多模具企业加大了用于技术进步的投资力度,将技术进步视为企业发展的重要动力。
一些国内模具企业已普及了二维CAD,并陆续开始使用UG、Pro/Engineer、I-DEAS、Euclid-IS等国际通用软件,个别厂家还引进了Moldflow、C-Flow、DYNAFORM、Optris 和MAGMASOFT等CAE软件,并成功应用于冲压模的设计中。
以汽车覆盖件模具为代表的大型冲压模具的制造技术已取得很大进步,东风汽车公司模具厂、一汽模具中心等模具厂家已能生产部分轿车覆盖件模具。
此外,许多研究机构和大专院校开展模具技术的研究和开发。
经过多年的努力,在模具CAD/CAE/CAM技术方面取得了显著进步;在提高模具质量和缩短模具设计制造周期等方面做出了贡献。
例如,吉林大学汽车覆盖件成型技术所独立研制的汽车覆盖件冲压成型分析KMAS软件,华中理工大学模具技术国家重点实验室开发的注塑模、汽车覆盖件模具和级进模CAD/CAE/CAM软件,上海交通大学模具CAD国家工程研究中心开发的冷冲模和精冲研究中心开发的冷冲模和精冲模CAD软件等在国内模具行业拥有不少的用户。
虽然中国模具工业在过去十多年中取得了令人瞩目的发展,但许多方面与工业发达国家相比仍有较大的差距。
例如,精密加工设备在模具加工设备中的比重比较低;CAD/CAE/CAM技术的普及率不高;许多先进的模具技术应用不够广泛等等,致使相当一部分大型、精密、复杂和长寿命模具依赖进口。
我国的模具技术有了很大发展,模具的精密度、复杂程度和寿命都有很大提高。
如,主要的汽车模具企业已能生产大型、精密的轿车覆盖件模具;体现高水平制造技术的多工位级进模的覆盖面增加;塑料模热流道技术日渐成熟,气体辅助注射技术开始采用;压铸工艺得到发展。
此外,CAD/CAM/CAE技术得到广泛应用,高速加工、复合加工等先进的加工技术也得到进一步推广;快速原型进展很快;模具的标准化程度也有一定提高。
但是,由于我国的模具行业起步较晚,与国外相比,仍存在不小的差距,主要体现在:(1)产需矛盾:随着工业发展水平的不断提高,工业产品更新速度的加快,对模具的需求越来越大。
无论是数量还是质量都无法满足国内市场的需要,只达到70%左右。
造成矛盾突出的原因是模具企业的专业化、标准化程度低,生产周期长。
另外,设计和制造工艺水平还不能完全适应发展的需要。
(2)企业结构不合理:我国很多模具生产能力集中在各主机厂的模具分厂或车间内,模具的商品化程度低,而国外70%以上都是专业模具厂,且走的是“小而精”的道路,因此生产效率和经济效益俱佳。
(3)产品水平:衡量模具的产品水平,主要有模具加工的制造精度和表面粗糙度,加工模具的复杂程度,以及模具的制造周期和使用寿命。
而这几项指标与国外相比的差距都十分明显。
(4)模具工业的整体装备水平也存在相对落后,利用率低的现象。
高素质的模具技术人才缺乏,产品的综合开发能力还急需加强。
1.2.2 冲压模具制造技术发展趋势模具技术的发展应该为适应模具产品“交货期短”、“精度高”、“质量好”、“价格低”的要求服务。
达到这一要求急需发展如下几项[7]:(1)全面推广CAD/CAM/CAE技术模具CAD/CAM/CAE技术是模具设计制造的发展方向。
随着微机软件的发展和进步,普及CAD/CAM/CAE技术的条件已基本成熟,各企业将加大CAD/CAM 技术培训和技术服务的力度;进一步扩大CAE技术的应用范围。
计算机和网络的发展正使CAD/CAM/CAE技术跨地区、跨企业、跨院所地在整个行业中推广成为可能,实现技术资源的重新整合,使虚拟制造成为可能。
(2)高速铣削加工国外近年来发展的高速铣削加工,大幅度提高了加工效率,并可获得极高的表面光洁度。
另外,还可加工高硬度模块,还具有温升低、热变形小等优点。
高速铣削加工技术的发展,对汽车、家电行业中大型型腔模具制造注入了新的活力。
目前它已向更高的敏捷化、智能化、集成化方向发展。
(3)模具扫描及数字化系统高速扫描机和模具扫描系统提供了从模型或实物扫描到加工出期望的模型所需的诸多功能,大大缩短了模具的在研制制造周期。
有些快速扫描系统,可快速安装在已有的数控铣床及加工中心上,实现快速数据采集、自动生成各种不同数控系统的加工程序、不同格式的CAD数据,用于模具制造业的“逆向工程”。
模具扫描系统已在汽车、摩托车、家电等行业得到成功应用,相信在“十五”期间将发挥更大的作用。
(4)电火花铣削加工电火花铣削加工技术也称为电火花创成加工技术,这是一种替代传统的用成型电极加工型腔的新技术,它是有高速旋转的简单的管状电极作三维或二维轮廓加工(像数控铣一样),因此不再需要制造复杂的成型电极,这显然是电火花成形加工领域的重大发展。
国外已有使用这种技术的机床在模具加工中应用。
预计这一技术将得到发展。
(5)提高模具标准化程度我国模具标准化程度正在不断提高,估计目前我国模具标准件使用覆盖率已达到30%左右。
国外发达国家一般为80%左右。