塑料模具外文文献
塑料模具发展中英文对照外文翻译文献

中英文对照外文翻译文献(文档含英文原文和中文翻译)外文:The development of plastic mouldChina's industrial plastic moulds from the start to now, after more than half a century, there has been great development, mold levels have been greatly enhanced. Mould has been at large can produce 48-inchbig-screen color TV Molded Case injection mold, 6.5 kg capacity washing machine full of plastic molds, as well as the overall car bumpers and dashboards, and other plastic mould precision plastic molds, the camera is capable of producing plastic mould , multi-cavity mold small modulus gear and molding mold. --Such as Tianjin and Yantai daysElectrical Co., Ltd Polaris IK Co. manufactured multi-cavity mold VCD and DVD gear, the gear production of such size precision plastic parts, coaxial, beating requirements have reached a similar foreign the level of product, but also the application of the latest gear design software to correct contraction as a result of the molding profile error to the standard involute requirements. Production can only 0.08 mm thickness of atwo-cavity mold and the air Cup difficulty of plastic doors and windows out of high modulus, and so on. Model cavity injection molding manufacturing accuracy of 0.02 to 0.05 mm, surface roughness Ra0.2 μ m, mold quality, and significantly increase life expectancy,non-hardening steel mould life up to 10~ 30 million, hardening steel form up to 50 ~ 10 million times, shorten the delivery time than before, but still higher than abroad,and the gap between a specific data table.Process, the multi-material plastic molding die, efficient multicolor injection mould, inserts exchange structure and core pulling Stripping the innovative design has also made great progress. Gas-assisted injection molding, the use of more mature technologies, such as Qingdao Hisense Co., Ltd., Tianjin factorycommunications and broadcasting companies, such as moldmanufacturers succeeded in 29 ~ 34-inch TV thick-walled shell, as well as some parts on the use of gas-assisted mould technology Some manufacturers also use the C-MOLD gas-assisted software and achieved better results. Prescott, such as Shanghai, such as the newcompany will provide users with gas-assisted molding equipment and technology. Began promoting hot runner mold, and some plants use rate of more than 20 percent, the general heat-thermal hot runner, or device, a small number of units with the world's advanced level of rigorous hot runner-needle device, a small number of units with World advanced level of rigorous needle-hot runner mould. However, the use of hot runner overall rate of less than 10%, with overseas compared to 50 ~ 80%, the gap larger. In the manufacturing technology, CAD / CAM / CAE technology on the level of application of a new level to the enterprise for the production of household appliances representatives have introduced a considerable number of CAD / CAM systems, such as the United States EDS UG Ⅱ, the United States Parametric Technology Pro / Engineer, the United States CV CADS5 company, the British company DOCT5 Deltacam, HZS's CRADE Japan, the company's Cimatron Israel, the United States AC-C-Tech Mold Company and Australia's MPA Mold flow Mold analysis software, and so on. These systems and the introduction of the software, although a lot of money spent, but in our country die industry, and achieving a CAD / CAM integration, and to support CAE technology to forming processes such as molding and cooling, such as computer simulation, and achieved certain The technical and economic benefits, promote and facilitate China's CAD / CAM technology. In recent years, China's own development of the plasticmould CAD / CAM system has achieved significant development, the main guarantor Software Engineering Institute, is the development of CAXA, Huazhong University of Science HSC5.0 development of the system and injection mold CAE software, and so on, these Die of domestic software with the specific circumstances in the application of computer and lower prices, and other characteristics, in order to further universal CAD / CAM technology has created good conditions.In recent years, China has been more extensive use of some new plastic mold steel, such as: P20, 3Cr2Mo, PMS, SM Ⅰ, SM Ⅱ, and the quality of life of mold has a direct significant impact on the overall use of the still less . Plastic Moulds standard model planes, such as standard putter and spring has given more applications, and there have been some of the commercialization of domestic hot runner system components. However, at present China Die level of standardization and commercialization in the general level of below 30 percent and foreign advanced industrial countries has reached 70 percent compared to 80 percent, still a large gap. Table 1, at home and abroad plastic mould technology comparison table? Domestic projects abroad cavity injection model mm0.02 accuracy of 0.005 ~ 0.01 ~ 0.05mm cavity surface roughness Ra0.01 ~ 0.05 μ mRa0.20 μ m non-hardened steel die life 10 to 60 million 10 ~ 30 million hardened steel die life 160 ~ 300 million of 50 ~ 100 million hot runner mould overall utilization rate of more than 80per cent less than 10 per cent level of standardization of 70 ~ 80% less than 30% of medium-sized plastic mould production cycle about a month 2 ~ 4 months in the mold industry in the amount of 30 to 40% 25 to 30% According to the parties concerned forecast, the market's overall vigorous mold is a smooth upward, in the next Die market, the development of plastic mould faster than the other Die, die in the proportion of industry will gradually improve. With the continuous development of the plastics industry, put on the plastic mold growing demands is a normal, and so sophisticated, large-scale, complex, long-life plastic mould development will be higher than the overall pace of development. At the same time, imports in recent years because of the mold, precision, large, complex, long-life die in the majority, therefore, reduce imports, increase Guochanhualu: perspective, in the mold of such high-end market share will gradually increase. The rapid development of theconstruction industry so that the various Profile Extrusion Die, PVC plastic pipe fittings Die Die market become a new economic growth point, the rapid development of highways, car tires also put a higher demand, radial tire Die, Die particularly active pace of development will also be higher than the overall average level of the plastic and wood, plastic and metal to make plastic molds in the automotive, motorcycle industry in the demand for huge household appliances industry in the "10th Five-Year Plan" period have greater development, especially refrigerators,air-conditionersand microwave ovens, and other parts of the great demand for plastic moulds, and electronics and communications products, in addition to audio-video products, such as color televisions, laptop computers and set-top boxes will be given a wider network development, which are Plastic Mold market is the growth point. Second, China's industrial and technological plastic mould the future direction of the major developments will include:1, raising large, sophisticated, complex, long-life mold design and manufacturing standards and proportion. This is due to the molding plastic mould products increasingly large, complex and high-precision requirements, as well as requirements for high productivity and the development of a multi-mode due.2, in the design and manufacture of plastic mould fully promote the use of CAD / CAM / CAE technology. CAD / CAM technology has developed into a relatively mature technology common in recent years CAD / CAM technology hardware and software prices has been reduced to SMEs generally acceptable level of popularity for further create good conditions; based on network CAD / CAM / CAE system integration structure the initial signs of emerging, and it will solve the traditional mixed CAD / CAM system can not meet the actual production process requirements of the division of collaboration; CAD / CAM software will gradually improve intelligence plastic parts and the 3-D mold design andprototyping process 3-D analysis will be in our plastic mould industries play an increasingly important role.3, promote the use of hot runner technology, gas-assisted injection molding technology and high-pressure injection molding technology. Using hot runner mould technology can improve the productivity and quality of parts and plastic parts can be substantial savings of raw materials and energy conservation, extensive application of this technology is a big plastic mould changes. Hot Runner components formulate national standards, and actively produce cheap high-quality components, the development of hot runner mold is the key. Gas-assisted injection molding product quality can be guaranteed under the premise of substantially lower cost. Currently in the automotive and appliance industries gradually promote the use of the Chiang Kai-shek. Gas-assisted injection molding of the ordinary than the traditional injection of more parameters need to identify and control, and its more commonly used in large, complex products, mold design and control more difficult, therefore, the development of gas-assisted molding flow analysis software It seems very important. On the other hand in order to ensure precision plastic parts to continue to study the development of technology and high-pressure injection molding and injection-compression molding mould and die technology is also very important.4, the development of new plastics molding technology and rapid economic mold. To adapt to more variety, less volume of production.5, and improve standardization of plastic mould standard parts usage. China's mold and die level of standard parts standardization still low, the gap between the large and foreign, to a certain extent constraining the development of industries in our country die, die to improve quality and reduce manufacturing costs Die, Die standard parts to vigorously promote the application. To this end, first of all, to formulate a unified national standards, and in strict accordance with the standards of production, secondly it is necessary to gradually scale production, to improve the commercialization of the standard of quality, and reduce costs; again it is necessary to further increase the standard specifications of varieties.6, Die application quality materials and advanced surface treatment technology for improving the quality of life and mold it is necessary.7, research and application of high-speed die measurement technology and reverse engineering. CMM-use 3D scanner or reverse engineering is the realization of plastic moulds CAD / CAM one of the key technologies.Research and Application of diversity, adjustment, cheap detection equipment is to achieve the necessary precondition for reverse engineering.译文:塑料模具的发展我国塑料模工业从起步到现在,历经半个多世纪,有了很大发展,模具水平有了较大提高。
塑料注塑模具中英文对照外文翻译文献
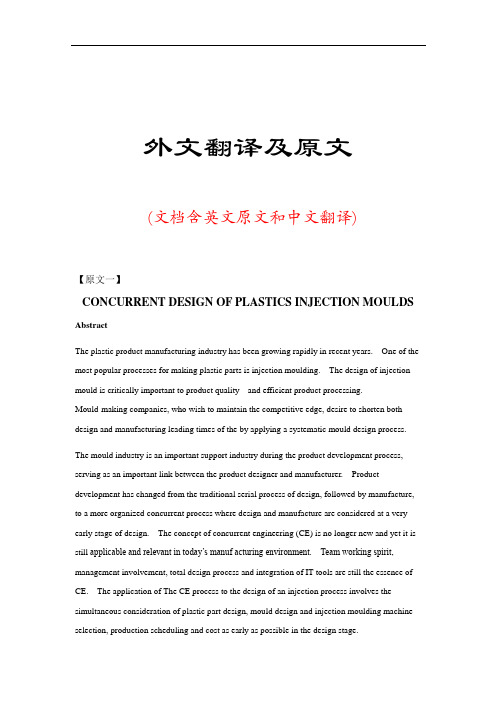
外文翻译及原文(文档含英文原文和中文翻译)【原文一】CONCURRENT DESIGN OF PLASTICS INJECTION MOULDS AbstractThe plastic product manufacturing industry has been growing rapidly in recent years. One of the most popular processes for making plastic parts is injection moulding. The design of injection mould is critically important to product quality and efficient product processing.Mould-making companies, who wish to maintain the competitive edge, desire to shorten both design and manufacturing leading times of the by applying a systematic mould design process. The mould industry is an important support industry during the product development process, serving as an important link between the product designer and manufacturer. Product development has changed from the traditional serial process of design, followed by manufacture, to a more organized concurrent process where design and manufacture are considered at a very early stage of design. The concept of concurrent engineering (CE) is no longer new and yet it is still applicable and relevant in today’s manuf acturing environment. Team working spirit, management involvement, total design process and integration of IT tools are still the essence of CE. The application of The CE process to the design of an injection process involves the simultaneous consideration of plastic part design, mould design and injection moulding machine selection, production scheduling and cost as early as possible in the design stage.This paper presents the basic structure of an injection mould design. The basis of this system arises from an analysis of the injection mould design process for mould design companies. This injection mould design system covers both the mould design process and mould knowledge management. Finally the principle of concurrent engineering process is outlined and then its principle is applied to the design of a plastic injection mould.Keywords :Plastic injection mould design, Concurrent engineering, Computer aided engineering, Moulding conditions, Plastic injection moulding, Flow simulation1.IntroductionInjection moulds are always expensive to make, unfortunately without a mould it can not be possible ho have a moulded product. Every mould maker has his/her own approach to design a mould and there are many different ways of designing and building a mould. Surely one of the most critical parameters to be considered in the design stage of the mould is the number of cavities, methods of injection, types of runners, methods of gating, methods of ejection, capacity and features of the injection moulding machines. Mould cost, mould quality and cost of mould product are inseparableIn today’s completive environment, computer aided mould filling simulation packages can accurately predict the fill patterns of any part. This allows for quick simulations of gate placements and helps finding the optimal location. Engineers can perform moulding trials on the computer before the part design is completed. Process engineers can systematically predict a design and process window, and can obtain information about the cumulative effect of the process variables that influence part performance, cost, and appearance.2.Injection MouldingInjection moulding is one of the most effective ways to bring out the best in plastics. It is universally used to make complex, finished parts, often in a single step, economically, precisely and with little waste. Mass production of plastic parts mostly utilizes moulds. The manufacturing process and involving moulds must be designed after passing through the appearance evaluation and the structure optimization of the product design. Designers face a hugenumber of options when they create injection-moulded components. Concurrent engineering requires an engineer to consider the manufacturing process of the designed product in the development phase. A good design of the product is unable to go to the market if its manufacturing process is impossible or too expensive. Integration of process simulation, rapid prototyping and manufacturing can reduce the risk associated with moving from CAD to CAM and further enhance the validity of the product development.3. Importance of Computer Aided Injection Mould DesignThe injection moulding design task can be highly complex. Computer Aided Engineering (CAE) analysis tools provide enormous advantages of enabling design engineers to consider virtually and part, mould and injection parameters without the real use of any manufacturing and time. The possibility of trying alternative designs or concepts on the computer screen gives the engineers the opportunity to eliminate potential problems before beginning the real production. Moreover, in virtual environment, designers can quickly and easily asses the sensitivity of specific moulding parameters on the quality and manufacturability of the final product. All theseCAE tools enable all these analysis to be completed in a meter of days or even hours, rather than weeks or months needed for the real experimental trial and error cycles. As CAE is used in the early design of part, mould and moulding parameters, the cost savings are substantial not only because of best functioning part and time savings but also the shortens the time needed to launch the product to the market.The need to meet set tolerances of plastic part ties in to all aspects of the moulding process, including part size and shape, resin chemical structure, the fillers used, mould cavity layout, gating, mould cooling and the release mechanisms used. Given this complexity, designers often use computer design tools, such as finite element analysis (FEA) and mould filling analysis (MFA), to reduce development time and cost. FEA determines strain, stress and deflection in a part by dividing the structure into small elements where these parameters can be well defined. MFA evaluates gate position and size to optimize resin flow. It also defines placement of weld lines, areas of excessive stress, and how wall and rib thickness affect flow. Other finite element design tools include mould cooling analysis for temperature distribution, and cycle time and shrinkage analysis for dimensional control and prediction of frozen stress and warpage.The CAE analysis of compression moulded parts is shown in Figure 1. The analysis cycle starts with the creation of a CAD model and a finite element mesh of the mould cavity. After the injection conditions are specified, mould filling, fiber orientation, curing and thermal history, shrinkage and warpage can be simulated. The material properties calculated by the simulation can be used to model the structural behaviour of the part. If required, part design, gate location and processing conditions can be modified in the computer until an acceptable part is obtained. After the analysis is finished an optimized part can be produced with reduced weldline (known also knitline), optimized strength, controlled temperatures and curing, minimized shrinkage and warpage.Machining of the moulds was formerly done manually, with a toolmaker checking each cut. This process became more automated with the growth and widespread use of computer numerically controlled or CNC machining centres. Setup time has also been significantly reduced through the use of special software capable of generating cutter paths directly from a CAD data file. Spindle speeds as high as 100,000 rpm provide further advances in high speed machining. Cutting materials have demonstrated phenomenal performance without the use of any cutting/coolant fluid whatsoever. As a result, the process of machining complex cores and cavities has been accelerated. It is good news that the time it takes to generate a mould is constantly being reduced. The bad news, on the other hand, is that even with all these advances, designing and manufacturing of the mould can still take a long time and can be extremely expensive.Figure 1 CAE analysis of injection moulded partsMany company executives now realize how vital it is to deploy new products to market rapidly. New products are the key to corporate prosperity. They drive corporate revenues, market shares, bottom lines and share prices. A company able to launch good quality products with reasonable prices ahead of their competition not only realizes 100% of the market before rival products arrive but also tends to maintain a dominant position for a few years even after competitive products have finally been announced (Smith, 1991). For most products, these two advantages are dramatic. Rapid product development is now a key aspect of competitive success. Figure 2 shows that only 3–7% of the product mix from the average industrial or electronics company is less than 5 years old. For companies in the top quartile, the number increases to 15–25%. For world-class firms, it is 60–80% (Thompson, 1996). The best companies continuously develop new products. AtHewlett-Packard, over 80% of the profits result from products less than 2 years old! (Neel, 1997)Figure 2. Importance of new product (Jacobs, 2000)With the advances in computer technology and artificial intelligence, efforts have been directed to reduce the cost and lead time in the design and manufacture of an injection mould. Injection mould design has been the main area of interest since it is a complex process involving several sub-designs related to various components of the mould, each requiring expert knowledge and experience. Lee et. al. (1997) proposed a systematic methodology and knowledge base for injection mould design in a concurrent engineering environment.4.Concurrent Engineering in Mould DesignConcurrent Engineering (CE) is a systematic approach to integrated product development process. It represents team values of co-operation, trust and sharing in such a manner that decision making is by consensus, involving all per spectives in parallel, from the very beginning of the productlife-cycle (Evans, 1998). Essentially, CE provides a collaborative, co-operative, collective and simultaneous engineering working environment. A concurrent engineering approach is based on five key elements:1. process2. multidisciplinary team3. integrated design model4. facility5. software infrastructureFigure 3 Methodologies in plastic injection mould design, a) Serial engineering b) Concurrent engineeringIn the plastics and mould industry, CE is very important due to the high cost tooling and long lead times. Typically, CE is utilized by manufacturing prototype tooling early in the design phase to analyze and adjust the design. Production tooling is manufactured as the final step. The manufacturing process and involving moulds must be designed after passing through the appearance evaluation and the structure optimization of the product design. CE requires an engineer to consider the manufacturing process of the designed product in the development phase.A good design of the product is unable to go to the market if its manufacturing process is impossible. Integration of process simulation and rapid prototyping and manufacturing can reduce the risk associated with moving from CAD to CAM and further enhance the validity of the product development.For years, designers have been restricted in what they can produce as they generally have todesign for manufacture (DFM) – that is, adjust their design intent to enable the component (or assembly) to be manufactured using a particular process or processes. In addition, if a mould is used to produce an item, there are therefore automatically inherent restrictions to the design imposed at the very beginning. Taking injection moulding as an example, in order to process a component successfully, at a minimum, the following design elements need to be taken into account:1. . geometry;. draft angles,. Non re-entrants shapes,. near constant wall thickness,. complexity,. split line location, and. surface finish,2. material choice;3. rationalisation of components (reducing assemblies);4. cost.In injection moulding, the manufacture of the mould to produce the injection-moulded components is usually the longest part of the product development process. When utilising rapid modelling, the CAD takes the longer time and therefore becomes the bottleneck.The process design and injection moulding of plastics involves rather complicated and time consuming activities including part design, mould design, injection moulding machine selection, production scheduling, tooling and cost estimation. Traditionally all these activities are done by part designers and mould making personnel in a sequential manner after completing injection moulded plastic part design. Obviously these sequential stages could lead to long product development time. However with the implementation of concurrent engineering process in the all parameters effecting product design, mould design, machine selection, production scheduling,tooling and processing cost are considered as early as possible in the design of the plastic part. When used effectively, CAE methods provide enormous cost and time savings for the part design and manufacturing. These tools allow engineers to virtually test how the part will be processed and how it performs during its normal operating life. The material supplier, designer, moulder and manufacturer should apply these tools concurrently early in the design stage of the plastic parts in order to exploit the cost benefit of CAE. CAE makes it possible to replace traditional, sequential decision-making procedures with a concurrent design process, in which all parties can interact and share information, Figure 3. For plastic injection moulding, CAE and related design data provide an integrated environment that facilitates concurrent engineering for the design and manufacture of the part and mould, as well as material selection and simulation of optimal process control parameters.Qualitative expense comparison associated with the part design changes is shown in Figure 4 , showing the fact that when design changes are done at an early stages on the computer screen, the cost associated with is an order of 10.000 times lower than that if the part is in production. These modifications in plastic parts could arise fr om mould modifications, such as gate location, thickness changes, production delays, quality costs, machine setup times, or design change in plastic parts.Figure 4 Cost of design changes during part product development cycle (Rios et.al, 2001)At the early design stage, part designers and moulders have to finalise part design based on their experiences with similar parts. However as the parts become more complex, it gets rather difficult to predict processing and part performance without the use of CAE tools. Thus for even relatively complex parts, the use of CAE tools to prevent the late and expensive design changesand problems that can arise during and after injection. For the successful implementation of concurrent engineering, there must be buy-in from everyone involved.5.Case StudyFigure 5 shows the initial CAD design of plastics part used for the sprinkler irrigation hydrant leg. One of the essential features of the part is that the part has to remain flat after injection; any warping during the injection causes operating problems.Another important feature the plastic part has to have is a high bending stiffness. A number of feeders in different orientation were added to the part as shown in Figure 5b. These feeders should be designed in a way that it has to contribute the weight of the part as minimum aspossible.Before the design of the mould, the flow analysis of the plastic part was carried out with Moldflow software to enable the selection of the best gate location Figure 6a. The figure indicates that the best point for the gate location is the middle feeder at the centre of the part. As the distortion and warpage of the part after injection was vital from the functionality point of view and it has to be kept at a minimum level, the same software was also utilised to yiled the warpage analysis. Figure 5 b shows the results implying the fact that the warpage well after injection remains within the predefined dimensional tolerances.6. ConclusionsIn the plastic injection moulding, the CAD model of the plastic part obtained from commercial 3D programs could be used for the part performance and injection process analyses. With the aid ofCEA technology and the use of concurrent engineering methodology, not only the injection mould can be designed and manufactured in a very short of period of time with a minimised cost but also all potential problems which may arise from part design, mould design and processing parameters could be eliminated at the very beginning of the mould design. These two tools help part designers and mould makers to develop a good product with a better delivery and faster tooling with less time and money.References1. Smith P, Reinertsen D, The time-to-market race, In: Developing Products in Half the Time. New York, Van Nostrand Reinhold, pp. 3–13, 19912.Thompson J, The total product development organization. Proceedings of the SecondAsia–Pacific Rapid Product Development Conference, Brisbane, 19963.Neel R, Don’t stop after the prototype, Seventh International Conference on Rapid Prototyping, San Francisco, 19974.Jacobs PF, “Chapter 3: Rapid Product Development” in Rapid Tooling: Technologies and Industrial Applications , Ed. Peter D. Hilton; Paul F. Jacobs, Marcel Decker, 20005.Lee R-S, Chen, Y-M, and Lee, C-Z, “Development of a concurrent mould design system: a knowledge based approach”, Computer Integrated Manufacturing Systems, 10(4), 287-307, 19976.Evans B., “Simultaneous Engineering”, Mechanical Engi neering , V ol.110, No.2, pp.38-39, 19987.Rios A, Gramann, PJ and Davis B, “Computer Aided Engineering in Compression Molding”, Composites Fabricators Association Annual Conference , Tampa Bay, 2001【译文一】塑料注塑模具并行设计塑料制品制造业近年迅速成长。
机械设计毕业设计外文文献翻译中英文对照塑料模具CAD集成技术

机械设计毕业设计外文文献翻译中英文对照:塑料模具CAD集成技术毕业设计外文文献翻译毕业设计题目摇控器面板注塑模设计翻译题目The molding tool CAD gathers the technique专业机械设计制造及其自动化姓名班级机械A0731学号指导教师机械与材料工程学院二O一O年十一月[K.P. Rao and K. Sivaram: J. Mater. Proc. Technol., 1993, vol. 37, pp.295-318.]毕业论文(设计)外文翻译课题名称:塑料模具CAD集成技术内容提要:通过分析计算机辅助注射模设计和制造的各个环节中共享的技术和信息,本文揭示了注射模CAD的集成技术的根本内涵,并提出了它的研究热点和趋势。
引言模具CAD集成技术是一项重要的模具先进制造技术, 是一项用高技术改造模具传统技术的重要关键技术。
从六五计划开始,我国有许多模具企业采用CAD 技术, 特别是近年, CAD技术的应用越来越普遍和深入, 大大缩短了模具设计周期,提高了制模质量和复杂模具的制造能力。
然而, 由于许多企业对模具CAD集成技术认识不足, 投资带有盲目性, 不能很好地发挥作用,造成了很大的浪费。
本文就塑料模具CAD集成技术及其应用发表一些观点, 供大家参考。
1、塑料模具CAD集成技术塑料模具的制造, 包括塑料产品的造型设计、模具的结构设计及分析、模具的数控加工铣削、电加工、线切割等、抛光和配试模以及快速成形制造等。
各个环节所涉及的CAD单元技术有:造型和结构设计CAD、产品外形的快速反求RE、结构分析与优化设计CAE、辅助制造CAM、加工过程虚拟仿真SIMULATION、产品及模具的快速成形RP、辅助工艺过程CAPP和产品数据管理技术PDM等。
塑料模具CAD集成技术,? 就是把塑料模具制造过程所涉及的各项单元技术集成起来, 统一数据库和文件传输格式, 实现信息集成和数据资源共享, 从而大大缩短模具的设计制造周期, 提高制模质量。
塑料注射成型外文文献翻译、中英文翻译、外文翻译
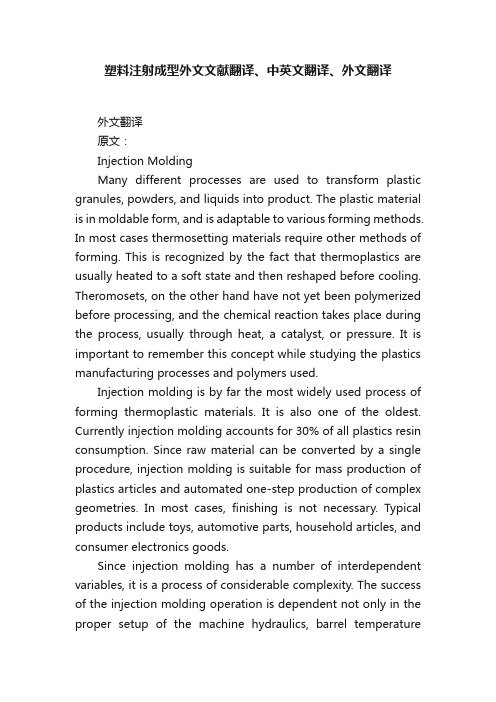
塑料注射成型外文文献翻译、中英文翻译、外文翻译外文翻译原文:Injection MoldingMany different processes are used to transform plastic granules, powders, and liquids into product. The plastic material is in moldable form, and is adaptable to various forming methods. In most cases thermosetting materials require other methods of forming. This is recognized by the fact that thermoplastics are usually heated to a soft state and then reshaped before cooling. Theromosets, on the other hand have not yet been polymerized before processing, and the chemical reaction takes place during the process, usually through heat, a catalyst, or pressure. It is important to remember this concept while studying the plastics manufacturing processes and polymers used.Injection molding is by far the most widely used process of forming thermoplastic materials. It is also one of the oldest. Currently injection molding accounts for 30% of all plastics resin consumption. Since raw material can be converted by a single procedure, injection molding is suitable for mass production of plastics articles and automated one-step production of complex geometries. In most cases, finishing is not necessary. Typical products include toys, automotive parts, household articles, and consumer electronics goods.Since injection molding has a number of interdependent variables, it is a process of considerable complexity. The success of the injection molding operation is dependent not only in the proper setup of the machine hydraulics, barrel temperaturevariations, and changes in material viscosity. Increasing shot-to-shot repeatability of machine variables helps produce parts with tighter tolerance, lowers the level of rejects, and increases product quality (i.e., appearance and serviceability).The principal objective of any molding operation is the manufacture of products: to a specific quality level, in the shortest time, and using repeatable and fully automaticcycle. Molders strive to reduce or eliminate rejected parts in molding production. For injection molding of high precision optical parts, or parts with a high added value such as appliance cases, the payoff of reduced rejects is high.A typical injection molding cycle or sequence consists of five phases;1. Injection or mold filling2. Packing or compression3. Holding4. Cooling5. Part ejectionPlastic granules are fed into the hopper and through an in the injection cylinder where they are carried forward by the rotating screw. The rotation of the screw forces the granules under high pressure against the heated walls of the cylinder causing them to melt. As the pressure building up, the rotating screw is forced backward until enough plastic has accumulated to make the shot. The injection ram (or screw) forces molten plastic from the barrel, through the nozzle, sprue and runner system, and finally into the mold cavities. During injection, the mold cavity is filled volumetrically. When the plastic contacts the cold mold surfaces, it solidifies (freezes) rapidly to produce theskin layer. Since the core remains in the molten state, plastic follows through the core to complete mold filling. Typically, the cavity is filled to 95%~98% during injection. Then the molding process is switched over to the packing phase.Even as the cavity is filled, the molten plastic begins to cool. Since the cooling plastic contracts or shrinks, it gives rise to defects such as sink marks, voids, and dimensional instabilities. To compensate for shrinkage, addition plastic is forced into the cavity. Once the cavity is packed, pressure applied to the melt prevents molten plastic inside the cavity from back flowing out through the gate. The pressure must be applied until the gate solidifies. The process can be divided into two steps (packing and holding) or may be encompassed in one step(holding or second stage). During packing, melt forced into the cavity by the packing pressure compensates for shrinkage. With holding, the pressure merely prevents back flow of the polymer malt.After the holding stage is completed, the cooling phase starts. During, the part is held in the mold for specified period. The duration of the cooling phase depends primarily on the material properties and the part thickness. Typically, the part temperature must cool below the material’s ejection temperature. While cooling the part, the machine plasticates melt for the next cycle.The polymer is subjected to shearing action as well as the condition of the energy from the heater bands. Once the short is made, plastication ceases. This should occur immediately before the end of the cooling phase. Then the mold opens and the part is ejected.When polymers are fabricated into useful articles they are referred to as plastics, rubbers, and fibers. Some polymers, forexample, cotton and wool, occur naturally, but the great majority of commercial products are synthetic in origin. A list of the names of the better known materials would include Bakelite, Dacron, Nylon, Celanese, Orlon, and Styron.Previous to 1930 the use of synthetic polymers was not widespread. However, they should not be classified as new materials for many of them were known in the latter half of the nineteenth century. The failure to develop them during this period was due, in part, to a lack of understanding of their properties, in particular, the problem of the structure of polymers was the subject of much fruitless controversy.Two events of the twentieth century catapulted polymers into a position of worldwide importance. The first of these was the successful commercial production of the plastic now known as Bakelite. Its industrial usefulness was demonstrated in1912 and in the next succeeding years. T oday Bakelite is high on the list of important synthetic products. Before 1912 materials made from cellulose were available, but their manufacture never provided the incentive for new work in the polymer field such as occurred after the advent of Bakelite. The second event was concerned with fundamental studies of the nature polymers by Staudinger in Europe and by Carohers, who worked with the Du Pont company in Delaware. A greater part of the studies were made during the 1920’s. Staudinger’s work was primarily fundamental. Carother’s achievements led t o the development of our present huge plastics industry by causing an awakening of interest in polymer chemistry, an interest which is still strongly apparent today.The Nature of ThermodynamicsThermodynamics is one of the most important areas ofengineering science used to explain how most things work, why some things do not the way that they were intended, and why others things just cannot possibly work at all. It is a key part of the science engineers use to design automotive engines, heat pumps, rocket motors, power stations, gas turbines, air conditioners, super-conducting transmission lines, solar heating systems, etc.Thermodynamics centers about the notions of energy, the idea that energy is conserved is the first low of thermodynamics. It is starting point for the science of thermodynamics is entropy; entropy provides a means for determining if a process is possible.This idea is the basis for the second low of thermodynamics. It also provides the basis for an engineering analysis in which one calculates the maximum amount of useful that can be obtained from a given energy source, or the minimum amount of power input required to do a certain task.A clear understanding of the ideas of entropy is essential for one who needs to use thermodynamics in engineering analysis. Scientists are interested in using thermodynamics to predict and relate the properties of matter; engineers are interested in using this data, together with the basic ideas of energy conservation and entropy production, to analyze the behavior of complex technological systems.There is an example of the sort of system of interest to engineers, a large central power stations. In this particular plant the energy source is petroleum in one of several forms, or sometimes natural gas, and the plant is to convert as much of this energy as possible to electric energy and to send this energy down the transmission line.Simply expressed, the plant does this by boiling water andusing the steam to turn a turbine which turns an electric generator.The simplest such power plants are able to convert only about 25 percent of the fuel energy to electric energy. But this particular plant converts approximately 40 percent;it has been ingeniously designed through careful application of the basic principles of thermodynamics to the hundreds of components in the system.The design engineers who made these calculations used data on the properties of steam developed by physical chemists who in turn used experimental measurements in concert with thermodynamics theory to develop the property data.Plants presently being studied could convert as much as 55 percent of the fuel energy to electric energy, if they indeed perform as predicted by thermodynamics analysis.The rule that the spontaneous flow of heat is always from hotter to cooler objects is a new physical idea. There is noting in the energy conservation principle or in any other law of nature that specifies for us the direction of heat flow. If energy were to flow spontaneously from a block of ice to a surrounding volume of water, this could occur in complete accord with energy conservation. But such a process never happens. This idea is the substance of the second law of thermodynamics.Clear, a refrigerator, which is a physical system used in kitchen refrigerators, freezers, and air-conditioning units must obey not only the first law (energy conservation) but the second law as well.To see why the second law is not violated by a refrigerator, we must be careful in our statement of law. The second law of thermodynamics says, in effect, that heat never flowsspontaneously from a cooler to a hotter object.Or, alternatively, heat can flow from a cooler to a hotter object only as a result of work done by an external agency. We now see the distinction between an everyday spontaneous process, such as the flow of heat from the inside to the outside of a refrigerator.In the water-ice system, the exchange of energy takes place spontaneously and the flow of heat always proceeds from the water to the ice. The water gives up energy and becomes cooler while the ice receives energy and melts.In a refrigerator, on the other hand, the exchange of energy is not spontaneous. Work provided by an external agency is necessary to reverse the natural flow of heat and cool the interior at the expense of further heating the warmer surroundings.译文:塑料注射成型许多不同的加工过程习惯于把塑料颗粒、粉末和液体转化成最终产品。
塑料模具毕业设计中英文对照资料外文翻译文献

中英文对照资料外文翻译文献一个描述电铸镍壳在注塑模具的应用的技术研究摘要:在过去几年中快速成型技术及快速模具已被广泛开发利用. 在本文中,使用电芯作为核心程序对塑料注射模具分析. 通过差分系统快速成型制造外壳模型. 主要目的是分析电铸镍壳力学特征、研究相关金相组织,硬度,内部压力等不同方面,由这些特征参数以生产电铸设备的外壳. 最后一个核心是检验注塑模具.关键词:电镀;电铸;微观结构;镍1. 引言现代工业遇到很大的挑战,其中最重要的是怎么样提供更好的产品给消费者,更多种类和更新换代问题. 因此,现代工业必定产生更多的竞争性. 毫无疑问,结合时间变量和质量变量并不容易,因为他们经常彼此互为条件; 先进的生产系统将允许该组合以更加有效可行的方式进行,例如,如果是观测注塑系统的转变、我们得出的结论是,事实上一个新产品在市场上具有较好的质量它需要越来越少的时间快速模具制造技术是在这一领域, 中可以改善设计和制造注入部分的技术进步. 快速模具制造技术基本上是一个中小型系列的收集程序,在很短的时间内在可接受的精度水平基础上让我们获得模具的塑料部件。
其应用不仅在更加广阔而且生产也不断增多。
本文包括了很广泛的研究路线,在这些研究路线中我们可以尝试去学习,定义,分析,测试,提出在工业水平方面的可行性,从核心的注塑模具制造获取电铸镍壳,同时作为一个初始模型的原型在一个FDM设备上的快速成型。
不得不说的是,先进的电铸技术应用在无数的行业,但这一研究工作调查到什么程度,并根据这些参数,使用这种技术生产快速模具在技术上是可行的. 都产生一个准确的,系统化使用的方法以及建议的工作方法.2 制造过程的注塑模具薄镍外壳的核心是电铸,获得一个充满epoxic金属树脂的一体化的核心板块模具(图1)允许直接制造注射型多用标本,因为它们确定了新英格兰大学英文国际表卓华组织3167标准。
这样做的目的是确定力学性能的材料收集代表行业。
该阶段取得的核心[4],根据这一方法研究了这项工作,有如下:a,用CAD系统设计的理想对象b模型制造的快速成型设备(频分多路系统). 所用材料将是一个ABS塑料c一个制造的电铸镍壳,已事先涂有导电涂料(必须有导电).d无外壳模型e核心的生产是背面外壳环氧树脂的抗高温与具有制冷的铜管管道.有两个腔的注塑模具、其中一个是电核心和其他直接加工的移动版. 因此,在同一工艺条件下,同时注入两个标准技术制造,获得相同的工作。
外文文献翻译《注塑模具的设计与热分析》 (1)

中文译文:注塑模具的设计与热分析摘要:本文介绍了用于生产热变形测试样品的注塑模具的设计,这种模具能为自身实现热分析,从而得到模具的热残余应力的影响。
文章对技术,理论,方法以及在注塑模型设计中需要的考虑的因素也进行了介绍。
模具设计是通过商用计算机辅助设计软件Unigraphics系统的13.0版本实现的。
这种用于分析因样品不均匀冷却产生的热残余应力的模具,已经通过使用13.5版的被称作LUSAS分析员的商业有限元分析软件得到了开发,而且存在问题也已经解决。
该软件通过绘制相应的时间反应曲线为模具提供了温度分布等高线图以及注塑周期中的温度的变化。
结果表明,与其他区域相比,收缩可能更容易发生在冷却渠道附近的区域。
热变形就是这种在模具的不同区域的不均衡降温效果引起的。
关键词:注塑模具;设计;热分析1.引言塑料业是世界上发展最快的工业之一,被列入产值达数十亿美元的产业。
几乎每一个在日常生活中使用的产品都涉及塑料的使用,这些产品大部分可通过注塑成型方法生产。
注塑成型工艺因其制造过程是以较低的成本生产各种形态和复杂几何形状的产品而众所周知。
注塑成型工艺是一个循环工艺,整个过程分为四个重要的阶段,即:充模,保压,冷却和喷射。
在注塑成型过程是从漏斗中把树脂和适当的添加剂注入到注塑成型机的加热/注射系统开始的。
这就是“充模阶段”,在这个过程中,模腔填充了达到注射温度的热聚合物熔体。
在模腔填充后的“保压”阶段,更多的是聚合物熔体在更高的压力下被装进腔体,以补偿因聚合物固化引起的预计萎缩。
接下来便是冷却阶段,在此过程中模具会冷却,直到有足够的刚性部分被弹出。
最后一个阶段是“弹射阶段”,这个阶段模具被打开,成型部分被弹出,过后,模具会再次被关闭开始下一个循环。
因为主要是靠经验,包括了实际工具的反复修改,所以设计和制造所需性能的注塑成型聚合物部件的过程很昂贵的。
在模具设计任务中,由于包含了喷射和气压因素,通常来说,在核心区为模具设计特别附加的几何结构是相当复杂。
注塑模具之模具设计与制造外文文献翻译、中英文翻译
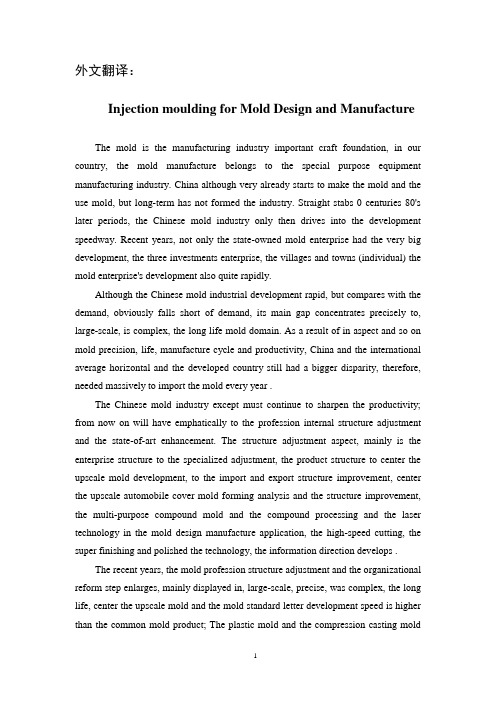
外文翻译:Injection moulding for Mold Design and ManufactureThe mold is the manufacturing industry important craft foundation, in our country, the mold manufacture belongs to the special purpose equipment manufacturing industry. China although very already starts to make the mold and the use mold, but long-term has not formed the industry. Straight stabs 0 centuries 80's later periods, the Chinese mold industry only then drives into the development speedway. Recent years, not only the state-owned mold enterprise had the very big development, the three investments enterprise, the villages and towns (individual) the mold enterprise's development also quite rapidly.Although the Chinese mold industrial development rapid, but compares with the demand, obviously falls short of demand, its main gap concentrates precisely to, large-scale, is complex, the long life mold domain. As a result of in aspect and so on mold precision, life, manufacture cycle and productivity, China and the international average horizontal and the developed country still had a bigger disparity, therefore, needed massively to import the mold every year .The Chinese mold industry except must continue to sharpen the productivity; from now on will have emphatically to the profession internal structure adjustment and the state-of-art enhancement. The structure adjustment aspect, mainly is the enterprise structure to the specialized adjustment, the product structure to center the upscale mold development, to the import and export structure improvement, center the upscale automobile cover mold forming analysis and the structure improvement, the multi-purpose compound mold and the compound processing and the laser technology in the mold design manufacture application, the high-speed cutting, the super finishing and polished the technology, the information direction develops .The recent years, the mold profession structure adjustment and the organizational reform step enlarges, mainly displayed in, large-scale, precise, was complex, the long life, center the upscale mold and the mold standard letter development speed is higher than the common mold product; The plastic mold and the compression casting moldproportion increases; Specialized mold factory quantity and its productivity increase; "The three investments" and the private enterprise develops rapidly; The joint stock system transformation step speeds up and so on. Distributes from the area looked, take Zhujiang Delta and Yangtze River delta as central southeast coastal area development quickly to mid-west area, south development quickly to north. At present develops quickest, the mold produces the most centralized province is Guangdong and Zhejiang, places such as Jiangsu, Shanghai, Anhui and Shandong also has a bigger development in recent years.Although our country mold total quantity had at present achieved the suitable scale, the mold level also has the very big enhancement, after but design manufacture horizontal overall rise and fall industry developed country and so on Yu De, America, date, France, Italy many. The current existence question and the disparity mainly display in following several aspects:(1) The total quantity falls short of demandDomestic mold assembling one rate only, about 70%. Low-grade mold, center upscale mold assembling oneself rate only has 50% about.(2) The enterprise organizational structure, the product structure, the technical structure and the import and export structure does not gatherIn our country mold production factory to be most is from the labor mold workshop which produces assembles oneself (branch factory), from produces assembles oneself the proportion to reach as high as about 60%, but the overseas mold ultra 70% is the commodity mold. The specialized mold factory mostly is "large and complete", "small and entire" organization form, but overseas mostly is "small but", "is specially small and fine". Domestic large-scale, precise, complex, the long life mold accounts for the total quantity proportion to be insufficient 30%, but overseas in 50% above 2004 years, ratio of the mold import and export is 3.7:1, the import and export balances the after net import volume to amount to 1.32 billion US dollars, is world mold net import quantity biggest country .(3) The mold product level greatly is lower than the international standardThe production cycle actually is higher than the international water broadproduct level low mainly to display in the mold precision, cavity aspect and so on surface roughness, life and structure.(4) Develops the ability badly, economic efficiency unsatisfactory our country mold enterprise technical personnel proportion lowThe level is lower, also does not take the product development, and frequently is in the passive position in the market. Our country each mold staff average year creation output value approximately, ten thousand US dollars, overseas mold industry developed country mostly 15 to10, 000 US dollars, some reach as high as 25 to10, 000 US dollars, relative is our country quite part of molds enterprises also continues to use the workshop type management with it, truly realizes the enterprise which the modernized enterprise manages fewTo create the above disparity the reason to be very many, the mold long-term has not obtained the value besides the history in as the product which should have, as well as the most state-owned enterprises mechanism cannot adapt the market economy, but also has the following several reasons: .The mold material performance, the quality and the variety question often can affect the mold quality, the life and the cost, the domestically produced molding tool steel and overseas imports the steel products to compare has a bigger disparity. Plastic,plate, equipment energy balance, also direct influence mold level enhancement.RSP ToolingRapid Solidification Process (RSP) Tooling, is a spray forming technology tailored for producing molds and dies [2-4]. The approach combines rapid solidification processing and netshape materials processing in a single step. The general concept involves converting a mold design described by a CAD file to a tooling master using a suitable rapid prototyping (RP) technology such as stereolithography. A pattern transfer is made to a castable ceramic, typically alumina or fused silica. This is followed by spray forming a thick deposit of tool steel (or other alloy) on the pattern to capture the desired shape, surface texture and detail. The resultant metal block is cooled to room temperature and separated from the pattern. Typically, the deposit’s exterior walls are machined square, allowing it to be used as an insert in a holding block such as a MUD frame [5]. The overall turnaround time for tooling is about three days, stating with a master. Molds and dies produced in this way have been used for prototype and production runs in plastic injection molding and die casting.An important benefit of RSP Tooling is that it allows molds and dies to be made early in the design cycle for a component. True prototype parts can be manufactured to assess form, fit, and function using the same process planned for production. If the part is qualified, the tooling can be run in production as conventional tooling would. Use of a digital database and RP technology allows design modifications to be easily made.Experimental ProcedureAn alumina-base ceramic (Cotronics 780 [6]) was slurry cast using a silicone rubber master die, or freeze cast using a stereolithography master. After setting up, ceramic patterns were demolded, fired in a kiln, and cooled to room temperature. H13 tool steel was induction melted under a nitrogen atmosphere, superheated about100︒C, and pressure-fed into a bench-scale converging/diverging spray nozzle, designed and constructed in-house. An inert gas atmosphere within the spray apparatus minimized in-flight oxidation of the atomized droplets as they deposited onto the tool pattern at a rate of about 200 kg/h. Gas-to-metal mass flow ratio was approximately 0.5.For tensile property and hardness evaluation, the spray-formed material was sectioned using a wire EDM and surface ground to remove a 0.05 mm thickheat-affected zone. Samples were heat treated in a furnace that was purged with nitrogen. Each sample was coated with BN and placed in a sealed metal foil packet as a precautionary measure to prevent decarburization.Artificially aged samples were soaked for 1 hour at temperatures ranging from 400 to 700︒C, and air cooled. Conventionally heat treated H13 was austenitized at 1010︒C for 30 min., air quenched, and double tempered (2 hr plus 2 hr) at 538︒C.Microhardness was measured at room temperature using a Shimadzu Type M Vickers Hardness Tester by averaging ten microindentation readings. Microstructure of the etched (3% nital) tool steel was evaluated optically using an Olympus Model PME-3 metallograph and an Amray Model 1830 scanning electron microscope. Phase composition was analyzed via energy-dispersive spectroscopy (EDS). The size distribution of overspray powder was analyzed using a Microtrac Full Range Particle Analyzer after powder samples were sieved at 200 μm to remove coarse flakes. Sample density was evaluated by water displacement using Archimedes’ principle and a Mettler balance (Model AE100).A quasi 1-D computer code developed at INEEL was used to evaluate multiphase flow behavior inside the nozzle and free jet regions. The code's basic numerical technique solves the steadystate gas flow field through an adaptive grid, conservative variables approach and treats the droplet phase in a Lagrangian manner with full aerodynamic and energetic coupling between the droplets and transport gas. The liquid metal injection system is coupled to the throat gas dynamics, and effects of heat transfer and wall friction are included. The code also includes a nonequilibriumsolidification model that permits droplet undercooling and recalescence. The code was used to map out the temperature and velocity profile of the gas and atomized droplets within the nozzle and free jet regions.Results and DiscussionSpray forming is a robust rapid tooling technology that allows tool steel molds and dies to be produced in a straightforward manner. Each was spray formed using a ceramic pattern generated from a RP master.Particle and Gas BehaviorParticle mass frequency and cumulative mass distribution plots for H13 tool steel sprays are given in Figure 1. The mass median diameter was determined to be 56 μm by interpolation of size corresponding to 50% cumulative mass. The area mean diameter and volume mean diameter were calculated to be 53 μm and 139 μm, respectively. Geometric standard deviation, d=(d84/d16)½ , is 1.8, where d84 and d16 are particle diameters corresponding to 84% and 16% cumulative mass in Figure 1.Figure1. Cumulative mass and mass frequency plots of particles in H13 tool stepsprays.Figure2 gives computational results for the multiphase velocity flow field (Figure 2a), and H13 tool steel solid fraction (Figure2b), inside the nozzle and free jetregions. Gas velocity increases until reaching the location of the shock front, at which point it precipitously decreases, eventually decaying exponentially outside the nozzle. Small droplets are easily perturbed by the velocity field, accelerating inside the nozzle and decelerating outside. After reaching their terminal velocity, larger droplets (〜150 μm) are less perturbed by the flow field due to their greater momentum.It is well known that high particle cooling rates in the spray jet (103-106 K/s) and bulk deposit (1-100 K/min) are present during spray forming [7]. Most of the particles in the spray have undergone recalescence, resulting in a solid fraction of about 0.75. Calculated solid fraction profiles of small (〜30 μm) and large (〜150 μm) droplets with distance from the nozzle inlet, are shown in Figure 2b.Spray-Formed DepositsThis high heat extraction rate reduces erosion effects at the surface of the tool pattern. This allows relatively soft, castable ceramic pattern materials to be used that would not be satisfactory candidates for conventional metal casting processes. With suitable processing conditions, fine surface detail can be successfully transferred from the pattern to spray-formed mold. Surface roughness at the molding surface is pattern dependent. Slurry-cast commercial ceramics yield a surface roughness of about 1 μm Ra, suitable for many molding applications. Deposition of tool steel onto glass plates has yielded a specular surface finish of about 0.076 μm Ra. At the current state of development, dimensional repeatability of spray-formed molds, starting with a common master, is about ±0.2%.Figure 2. Calculated particle and gas behavior in nozzle and free jet regions.(a) Velocity profile.(b) Solid fraction.ChemistryThe chemistry of H13 tool steel is designed to allow the material to withstand the temperature, pressure, abrasion, and thermal cycling associated with demanding applications such as die casting. It is the most popular die casting alloy worldwide and second most popular tool steel for plastic injection molding. The steel has low carbon content (0.4 wt.%) to promote toughness, medium chromium content (5 wt.%) to provide good resistance to high temperature softening, 1 wt% Si to improve high temperature oxidation resistance, and small molybdenum and vanadium additions (about 1%) that form stable carbides to increase resistance to erosive wear[8]. Composition analysis was performed on H13 tool steel before and after spray forming.Results, summarized in Table 1, indicate no significant variation in alloy additions.MicrostructureThe size, shape, type, and distribution of carbides found in H13 tool steel is dictated by the processing method and heat treatment. Normally the commercial steel is machined in the mill annealed condition and heat treated(austenitized/quenched/tempered) prior to use. It is typically austenitized at about 1010︒C, quenched in air or oil, and carefully tempered two or three times at 540 to 650︒C to obtain the required combination of hardness, thermal fatigue resistance, and toughness.Commercial, forged, ferritic tool steels cannot be precipitation hardened becauseafter electroslag remelting at the steel mill, ingots are cast that cool slowly and formcoarse carbides. In contrast, rapid solidification of H13 tool steel causes alloying additions to remain largely in solution and to be more uniformly distributed in the matrix [9-11]. Properties can be tailored by artificial aging or conventional heat treatment.A benefit of artificial aging is that it bypasses the specific volume changes that occur during conventional heat treatment that can lead to tool distortion. These specific volume changes occur as the matrix phase transforms from ferrite to austenite to tempered martensite and must be accounted for in the original mold design. However, they cannot always be reliably predicted. Thin sections in the insert, which may be desirable from a design and production standpoint, are oftentimes not included as the material has a tendency to slump during austenitization or distort during quenching. Tool distortion is not observed during artificial aging ofspray-formed tool steels because there is no phase transformation.注塑模具之模具设计与制造模具是制造业的重要工艺基础,在我国,模具制造属于专用设备制造业。
模具 塑料注射成型 外文翻译 外文文献 英文文献
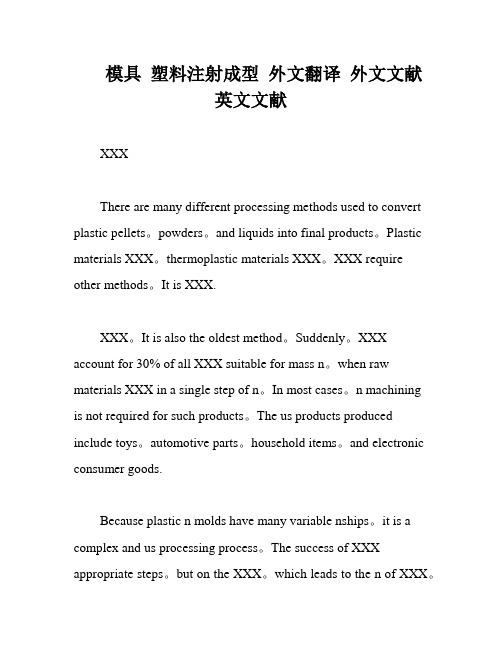
模具塑料注射成型外文翻译外文文献英文文献XXXThere are many different processing methods used to convert plastic pellets。
powders。
and liquids into final products。
Plastic materials XXX。
thermoplastic materials XXX。
XXX require other methods。
It is XXX.XXX。
It is also the oldest method。
Suddenly。
XXX account for 30% of all XXX suitable for mass n。
when raw materials XXX in a single step of n。
In most cases。
n machiningis not required for such products。
The us products produced include toys。
automotive parts。
household items。
and electronic consumer goods.Because plastic n molds have many variable nships。
it is a complex and us processing process。
The success of XXX appropriate steps。
but on the XXX。
which leads to the n of XXX。
barrel temperature changes。
XXX ns can help ce tolerances。
ce defect rates。
and increase product quality.XXX operator is to produce products that e first-rate products in the shortest time。
模具外文翻译外文文献英文文献注塑模

模具外文翻译外文文献英文文献注塑模The Injection Molding1、The injection moldingInjection molding is principally used for the production of the thermoplastic parts,although some progress has been made in developing a method for injection molding some thermosetting materials.The problem of injection a method plastic into a mold cavity from a reservoir of melted material has been extremely difficult to solve for thermosetting plastic which cure and harden under such conditions within a few minutes.The principle of injection molding is quite similar to that of die-casting.The process consists of feeding a plastic compound in powered or granular form from a hopper through metering and melting stages and then injecting it into a mold.After a brief cooling period,the mold is opened and the solidified part ejected.Injection-molding machine operation.The advantage of injection molding are:(ⅰ)a high molding speed adapter for mass production is possible;(ⅱ)there is a wide choice of thermoplastic materials providing a variety of useful properties;(ⅲ)it is possible to mold threads,undercuts,side holes,and large thin section.2、The injection-molding machineSeveral methods are used to force or inject the melted plastic into the mold.The most commonly used system in the larger machines is the in-line reciprocating screw,as shown in Figure 2-1.The screw acts as a combination injection and plasticizing unit.As the plastic is fed to the rotating screw,it passes through three zones as shown:feed,compression,and metering.After the feed zone,the screw-flight depth is gradually reduced,force theplastic to compress.The work is converted to heat by conduction from the barrel surface.As the chamber in front of the screw becomes filled,it forces the screw back,tripping a limit switch that activates a hydraulic cylinder that forces the screw forward and injects the fluid plastic into the closed mold.An antiflowback valve presents plastic under pressure from escaping back into the screw flight.The clamping force that a machine is capable of exerting is part of the size designation and is measured in tons.A rule-of-thumb can be used to determine the tonnage required for a particular job.It is based on two tons of clamp force per square inch of projected area.If the flow pattern is difficult and the parts are thin,this may have to go to three or four tons.Many reciprocating-screw machines are capable of handing thermosetting plastic materials.Previously these materials were handled by compression or transfer molding.Thermosetting materials cure or polymerize in the mold and are ejected hot in the range of 375°C~410°C.T hermosetting parts must be allowed to cool in the mold in order or remove them without distortion. Thus thermosetting cycles can be faster.Of course the mold must be heated rather than chilled,as with thermoplastics.3、Basic Underfeed MouldA simple mould of this type is shown in Figure3-1,and the description of the design and the opening sequence follows.The mould consists of three basic parts,namely:the moving half,the floating cavity plate and the feed plate respectively.The moving half consists of The moving mould plate assembly,support block,backing plate,ejector assembly and the pin ejection system.Thus the moving half in this design is identical with the moving half of basic moulds.The floating cavity plate,which may be of the integer or insert-bolster design,is located on substantial guide pillars(not shown)fitted in the feed plate.These guide pillars must be of sufficient length to support the floating cavity plate over its full movement and still project to perform the function of alignment between the cavity and core when the mould is being closed.Guide bushes are fitted into the moving mould plate and the floating cavity plate respectively.The maximum movement of the floating cavity plate is controlled by stop or similar device.The moving mould plate is suitably bored to provide a clearance for the stop bolt assembly.The stop bolts must be long enough to provide sufficient space between the feed plate and the floating cavity plate for easy removal of the feed system.The minimum space provide for should be 65mm just sufficient for an operator to remove the feed system by hand if necessary.The desire operating sequence is for the first daylight to occur between the floating cavity plate.This ensures the sprue is pulled from the sprue bush immediately the mouldis opened.T o achieve this sequence,springs may be incorporated between the feed plate and the floating cavity plate.The springs should be strong enough to give an initial impetus to the floating cavity plate to ensure it moves away with the moving half.It is normal practice to mount the springs on the guide pillars(Figure3-2)and accommodate them in suitable pocket in the cavity plate.The major part of the feed system(runner and sprue)is accommodated in the feed plate to facilitate automatic operation,the runner should be of a trapezoidal form so that once it is pulled from the feed plate is can easily beextracted.Note that if a round runner is used,half the runner is formed in the floating cavity plate,where it would remain,and be prevented from falling or being wiped clear when the mould is opened.Now that we have considered the mould assembly in the some detail,we look at the cycle of operation for this type of mould.The impressions are filled via the feed system(Figure3-1(a))and after a suitable dwell period,the machine platens commence to open.A force is immediately exerted by the compression springs,which cause the floating cavity plate to move away with the moving half as previously discussed.The sprue is pulled from the sprue bush by the sprue puller.After the floating cavity plate has moved a predetermined distance,it is arrested by the stop bolts.The moving half continues to move back and the moldings,having shrunk on to the cores,are withdrawn from the cavities.The pin gate breaks at its junction with the runner(Figure3-1(b)).The sprue puller,being attached to the moving half,is pulled through the floating cavity plate and thereby release the feed system which is then free to fall between the floating cavity plate and the feed plate.The moving half continues to move back until the ejector system is operated and the moldings are ejected (Figure3-1(c)).When the mould is closed,the respective plates are returned to their molding position and the cycle is repeated.4、Feed SystemIt is necessary to provide a flow-way in the injection mould to connect the nozzle(of the injection machine)to each impression.This flow-way is termed the feed system.Normally thefeed system comprises a sprue,runner and gate.These terms applyequally to the flow-way itself,and to the molded material which is remove from the flow-way itself in the process of extracted the molding.A typical feed system for a four-impression,two plate-type mould is shown in Figure4-1.It is seen that the material passes through the sprue,main runner,branch runner and gate before entering the impression.As the temperature of molten plastic is lowered which going through the sprue and runner,the viscosity will rise;however,the viscosity is lowered by shear heat generated when going through the gate to fill the cavity.It is desirable to keep the distance that the material has to travel down to a minimum to reduce pressure and heat losses.It is for this reason that careful consideration must be given to the impression layout gate’s design.4.1.SprueA sprue is a channel through which to transfer molten plastic injected from the nozzle of the injector into the mold.It is a part of sprue bush,which is a separate part from the mold.4.2.RunnerA runner is a channel that guides molten plastic into the cavity of a mold.4.3.GateA gate is an entrance through which molten plastic enters the cavity.The gate has the following function:restricts the flow and the direction of molten plastic;simplifies cutting of a runner and moldings to simplify finishing of parts;quickly cools and solidifies to avoid backflow after molten plastic has filled up in the cavity.4.4.Cold slug wellThe purpose of the cold slug well,shown opposite the sprue,is theoretically to receive the material that has chilled at the front of nozzle during the cooling and ejection phase.Perhaps of greater importance is the fact that it provides position means whereby the sprue bush for ejection purposes.The sprue,the runner and the gate will be discarded after a part is complete.However,the runner and the gate are important items that affect the quality or the cost of parts.5、EjectionA molding is formed in mould by injecting a plastic melt,under pressure,into animpression via a feed system.It must therefore be removed manually.Furthermore,all thermoplastic materials contract as they solidify,which means that the molding will shrink on to the core which forms it.This shrinkage makes the molding difficult to remove. Facilities are provided on the injection machine for automatic actuation of an ejector system,and this is situated behind the moving platen.Because of this,the mould’s ejector system will be most effectively operated if placed in the moving half of the mould,i.e. the half attached to the moving platen.We have stated previously that we need to eject the molding from the core and it therefore follows that the core,too,will most satisfactorily be located in the moving half.The ejector system in a mould will be discussed under three headings,namely:(ⅰ)the ejector grid;(ⅱ)the ejector plate assembly; and(ⅲ)the method of ejection.5.1、Ejector gridThe ejector grid(Figure5-1)is that part of the mould which supports the mould plate and provides a space into which theejector plate assembly can be fitted and operated.The grid normally consists of a back plate on to which is mounted a number of conveniently shaped “support blocks”.The ejector plate assembly is that part of the mould to which the ejector element is attached.The assembly is contained in a pocket,formed by the ejector grid,directly behind the mould plate.The assembly(Figure5-2)consists of an ejector plate,a retaining plate and an ejector rod.One end of this latter member is threaded and it is screwed into the ejector plate.In this particular design the ejector rod function not only as an actuating member but also as a method of guiding the assembly.Note that the parallel portion of the ejector rod passes through an ejector rod bush fitted in the back plate of the mould.5.2、Ejection techniquesWhen a molding cools,it contracts by an amount depending on the material being processed.For a molding which has no internal form,for example,a solid rectangular block,the molding will shrink away from the cavity walls,thereby permitting a simple ejection technique to be adopted.However,when the molding has internal form,the molding,as it cools,will shrink onto the core and some positive type of ejection is necessary.The designer has several ejection techniques from which to choose,but in general,the choice will be restricted depending upon the shape of the molding.The basic ejection techniques are as follows:(ⅰ)pin ejection(ⅱ)sleeve ejection(ⅲ)stripper plate ejection and(Ⅳ)air ejection.Figure 2-1aFigure 2-1bFigure 3-1Figure 3-2Figure 4-1aFigure 4-1bFigure 5-1Figure 5-2注塑模1、注塑模尽管成型某些热固性材料的方法取得了一定的进步,但注塑模主要(还是)用来生产热塑性塑件。
塑料模具设计外文翻译资料

塑料模具CAD集成技术外文文献翻译、中英文翻译、外文翻译

附录1 英文原文The molding tool CAD gathers the technique Contents brief summary: Pass to analyze the calculator the assistance inject the mold design with make in the each link commonly shared of technique with information, this text announces to public to inject the mold CAD gathers technical and basic content, and the research heat that put forward it orders with trend.0, prefaceThe molding tool CAD gathers the technique is an important molding tool forerunner manufacturing technique, is the item reforms with the high technique traditional technical and important key in molding tool technique. From 6 5 plan beginning,Our country contain many molding tools business enterprise adoption CAD technique, especially recent years, the technical application in CAD is more and more widespread with thorough, shortened consumedly molding tool design period, Increases to make the mold quantity with the manufacturing ability that complicated molding tool.However, gather to the molding tool CAD because of many business enterprises technique cognition shortage, investment take the blindness, can't produce result nicely,Result in very big and wasted.This text gathers for the plastics molding tool CAD technique and its applications announce some standpoint, provide everybody consults.1, the plastics molding tool CAD gathers techniqueThe manufacturing of the plastics molding tool comtains the construction design of the shape design, molding tool and the number of the analysis, molding tools that include the plastics products control to process( I I , electricity process, the line incises etc.), throw the light with go together with to try the mold and take shape manufacturing etc. quickly.The each link a CAD for involving unit technique has:The shape design( CAD) with the construction, fast anti of the product shapebeg( RE), construction analysis with excellent turn the design( CAE), lend support to the manufacturing( CAM) and process the process conjecture imitate true( SIMULATION), product and molding tools take shape( RP) quickly, assistance craft process( CAPP) with product data management technique( PDM) etc..The plastics molding tool CAD gathers technique,Is to gather plastics molding tool manufacturing process a various units for involving technique get up, unify the database to deliver the format with the document, realize the information gather share with the data resources, from but shorten the design manufacturing period of the molding tool consumedly,Increases to make the mold quantity.2, the CAD design of the plastics product begs with fast anti of the shapeThe plastics molding tool that proceed the square one designs the manufacturing is the design of the EU a product.The traditional product design method is a design to product of three is conceive outline to use two I plane chart papers expresses to come out, marking clearly the craft and starting construction the method on the diagram paper, This kind of met hod comes to a decision the simple of a design sketch and can''ts control to make the quantity directly.The modern design method is a design establish the product directly on the computer of three the model of I ,According to the product three I models proceed the molding tool construction the design and excellent turn the design,Design according to the molding tool construction again three I models proceed to process to weave the distance and establishment crafts plan.This kind of method makes product model design, molding tool construction design, process to weave distance and technological designs regard a data as the foundation, realizing the data share, Can not only increases to design the efficiency quickly, but also can guarantee the quantity, decline low cost.The source of the computer EU a product model has three kinds of:Making use of the CAD system software proceeds the product model the design and make use of the real object measures fast anti in proceeding beg to set up the mold andmake use of the standard format document of the other the system of CAD.Source method that aim at these three kinds of products model,Have studied every kind of technique now to the design efficiency that increases product model with quantity.The underneath further analyzes every kind of technical content with the characteristics.Making use of the CAD system software proceeds the product model design,Its technique includes primarily two is are several why the sketch draws, two the parameter of is turn the design of the sketch, three i entity shape design, three icharacteristic shape design, three the parameter of is turn the entity shape the design, three i curved face shape design, free shape in space design, the external appearance of the product exaggerates, product of dynamic advertise to design the etc..These softwareses contain many typical representatives.Two the software of is have: ME10, CADKEY, AUTOCAD, DHCAD, Genis, etc. of Sigraph; three the software of is have:UGII, PRO/ E, IDEAS, CATIA, etc. of EUCLID; free shape in product and advertise the software of the design have:Alias, etc. of CDRS.Two is are several why the sketch draws is to make use of the flat surface CAD software draw the spare parts sketch, then replace the handicraft painting with the calculator; but two the parameter of is turn,Then the calculator realizes the sketch changes the deal designs, making modification more convenient; threeishape designs is a true shape that the product that the arithmetic figure turn design, it expressed completely product,Can be further to designs for the molding tool, analysis with processes the mathematics model of the necessity of offering; the free shape in space design is the art of the product shape to design, making product been not only is a function product, but also art article.It is every kind of need that the external appearance of the product exaggerate that product of the result designs, making product more beautiful, the color can attract people more; the dynamic advertisement design of the product is a result that design to make topromote the advertisement directly the product,Proceed the market expansion.Making use of the real object measures fast anti of proceeding beg to set up mold is current investigative a little bit hot of a,It is an important technique that product imitate the type foundation go forward a line of the product modification designs.Its basic principle is to passes three coordinateses measure the machine, laser measure machine or electronicses copy the few ÒÇ to proceed to scan the diagraph to the real object,The data of large quantity that arithmetic figure turn that gets to measures the acquisition orders anti that send into the high class CAD software beg mold piece or appropriative anti beg the software inside, anti beg the software can read directly a data cluster,Combining can proceed the editor, filter, tidy up, beg the ¾« to a data cluster, row preface, part modification and reorganization, then automatic born curved face, It is end to acquire together the real object precision is consistent of or computer EU a product model that pass through reforms.This way can increases biggest new product design velocity.Current mature curved face anti beg to set up the mold software has: Surfacer,Cimatronrenge, etc. of Strim100.Make use of the standard format document of the other the system of CAD to set up the mold, this way than convenience.Because the world of the market turns with the technical development in the network of INTERNET,The CAD technique exchanges of the molding tool business enterprise with cooperate to have many pass the CAD document method proceed.Because the CAD system category is more, therefore documentary format must follow the international standard,Such as the DXF, IGES, STEP, VDA, etc. of STL.Pass to read standard format document to establish directly or establish the product model after modifying, since can quickly, deepen the customer and the exchanges of the molding tool factory house,Also can shorten the product the design the period.3, the CAD design of the molding tool and analysisThe CAD design of the molding tool, analysis,Include to divide the type, certain type C» according to the product model molding tool of proceeding the design with the type D¾ , molding tool structural and detailed design, the plastics ³a fills process analysis etc. a few aspects.Make use of the advanced characteristic shape software,such as PRO/ E, etc. of UGII, the very easily certain dividing the type,Born top and bottom mold C»with mold D¾ , then the proceeding flows a way, sprinkle a people and cool off the pipe line of arrange etc..Made sure these designses data hereafter, then make use of the molding tool analysis software,Proceed such as the MOLDFLOW, CFLOW the plastics take shape the process analysis.According to the software of MOLDFOLW with it of the material, craft database of plentifulness, pass the importation take shape the craft parameter,Can the development imitate the true analysis plastics to inject in note EU mold C»the process flows the circumstance( the plastics with sprinkle a people more inject remits to flow the analysis of ÎAE ), analyze the temperature pressure variety circumstance and analyze to note EU a ²D remaining should dint etc.,According to analyze the circumstance to the rationality that check the molding tool construction, flow quantity problem etc. of the rationality, product of the appearance.For example whether the esse sprinkles to note the system not reasonable, appear to flow way with sprinkle a position size not appropriate,Can''t equilibrium alive with type C»; whether to exsit product construction absurdity or molding tool constructions or not is not reasonable, appearing the product A dissatisfied( namely short shoot the phenomenon); whether to cool off asymmetry or not, the influence produces the efficiency with product quantity;Whether the esse notes the craft of EU wrong, appear the song of CI of the product transform etc..The molding tool passes the CAD the design with analyze, can dissolve mistake at design the stage, increase to try once the mold the success the rate.At plastics molding tool design with analyze to apply many new computer.aideds technique this stage, if the parameter turns technique, characteristic shape technique, database technique etc..There is many standards piece in the plastics molding tool, Turn such as the standard mold a parameter for outing organization, sprinkling noting system, cooling system...etc. can adopting basing on database managing the characteristic shape design method proceed the design or establish the standard a a, like this since can realize the data share,Can satisfy the customer again to the at any time modifying of the design, make the design analysis of the molding tool fast, accurate, efficiently.The parameter turns the characteristic shape can not only describe the product completely then several why sketch information,And can acquire accuracy, material and assemble etc. informations of the product, its a product for establishing model is a kind of apting to handle and can reflect design intention with process the model of the characteristic.Therefore,The parameter turns the characteristic shape technique is an one of the most important technique in process in manufacturing in molding tools.4, the technical application in CAM of the molding tool, process to imitate true and ml;I processing, line incising to process, electricity spark processing to wait.The technique of CAM rises in the type C» , type D¾ of the complicated molding tool and the I I of the electrodes process particularly more important function.Its main technique characteristics includes:(1) the O , ¾« processes the knife have the track excellent to turn the programming with the instruction of NC creation,(2) the knife has the category, characteristic to establish with the material ,(3) slicing the Ï÷process the craft parameter to really settle,(4)The commonness slices the Ï÷ to slice with the high speed the characteristic that I process controls,(5) over slice the check with process the superficial accuracy control,(6) processing the computer entity of the process imitate the realistic I ,(7) The computercontrol number controls the technique of DNC and clusters of the machine bed control the technical and applied etc..Need the CAD specially in technical application in CAM three I product model data.More profession computer plait distance software,such as MASTERCAM, UNIMOD, etc. of CIMATRON, when the plait distance of many curved faces processes have the higher request to the curved face model of the product,Intend with the high accuracy of the curved face to match such as the directional consistency, curved face in U, V of the close together curved face, inclined rate in curved face continuous variety etc..In high class CAD/ the integral whole of CAM turn system,( such as UGII, PRO/ E)Because making use of the parameter turns the characteristic shape design with same database technique, making the type C of the product model data, molding tool have the track data to have got the inside contact with the type D¾ model data, knife, The modification knife of the product model has the track to also modify automatically.The molding tool processes the entity imitates the true technique more and more mature, also is more and more valued by people.It is mimicry machine bed that processing the entity imitate process the process on the computer, can keep the result that view reflect process,Can takes the gauge of directly quantity that after processing spare parts, can check the mistake that process.At check quantity that after processing spare parts, can at the computer is last to process behind of the entity model proceeds the aleatoric EE slices, Measure its size directly with the accuracy.Therefore, it can dissolve mistake at process the stage of craft plait distance design, reduce to repair after processing with return the work, increases consumedly the manufacturing efficiency of the molding tool with quantity.5, plastics product and its molding tools take shape the manufacturing quicklyPlastics product and its molding tools use the computer CAD techniquewdesign after completing, can pass the fleetness take shape the technique make.This is themanufacturing technique of a kind of all new concept,It abandoned the traditional machine processes the method.Its take shape principle is three I CAD entity models are long.lost set up a series of a layer data of the thickness, make use of the laser take shape machine or others take shape the equipments read these datas,Increase the method technique with the material, pile up the each layer to take shape one by one in order.This technique calls the fleetness to take shape the technique automatically.( Rapid Prototype)It is also a CAD to gather the technical importance constitutes the part.The first pedestal takes shape the equipments quickly to bear in the United States a company in 1987, because of its characteristics is to has nothing to do with the complicated degree of the product of the manufacturing, bringing the manufacturing industry the enormous vibration.Henceforth decade,Take shape quickly the technique be flown to develop soon, the category of the equipments also piles up one after another,Turn from the material I the method can is divided into the laser with not the laser burns the knot method( SLS), solid surface layer shape method( SGC), layer a manufacturing method( LOM) and melt to sink to accumulate the method( FDM), district constituency glues the knot method( DSPC), laser spirit to sink to accumulate method( SALD) etc. mutually.Every kind of method characteristics is:The method of SLA is applied at the earliest stage of took shape the technique quickly, the early market occupied the bigger cent sum, but is narrow because of the material scope, the cost is higher, taking shape the piece was heat.proof and bore the burthen with applied color the ability low,The recent years was gradually replaced by the other method.The method of FDM because of taking shape the speed quick, the cost is low, get the good application in plastics product profession, because the size of the spare parts is small, accuracy bad, Also suffer certainly of restrict.The method of LOM because of adoption paper or is outline edge that thin slice plastics, the cost is low, and the laser projects light upon eachlayer only, as a result take shape the speed quick,But the product surface quantity is bad.The method of SLS proceeds to burn the knot with the laser, adoptive material than wide, if the plastics,A¯ anticipates, porcelain and ceramics, metals etc. all can take shape, taking shape the piece is heat.proof and bear the burthen with apply color the ability stronger,Have the extensive and applied foreground.The other method also gets the application in some special kinds process.According to above take shape the method characteristics, take shape the technical function quickly to consist in primarily:The manufacturing useds for the design with the on trial product model, make to used for the small the molding tool that batch quantity produce to process with the special spare parts in small batch quantity.Take shape the product model of the technique manufacturing quickly in the aspects of material the ratio tradition processes the product model of the method manufacturing has the difference,But in shape and sizes almost complete similar, and there is certain machine strength, can make the function experiment, handles through surface at the same time, looking similar to true product,Can advertise the propaganda material.Take shape the molding tool of the technique manufacturing quickly,Is a soft material to take shape the mold( the mold of A¯ , wreath oxygen resin mold, ¹è rubber mold, low EU orders the metal alloy casts mold etc.) primarily to synthesize the hard type in material C mold with porcelain and ceramics or metals »ùs now.Hard mold in manufacturing the hour can take shape with the fleetness the spare parts makes the female die,Create first the soft mold between wreath oxygen resin mold or other material, sprinkle to note porcelain and ceramics or gypsum molds in soft mold, then sprinkle the steel of Öý steel mold; or sprinkle the admixture that note in soft mold chemistry contain steel powder glue knot,Proceed to burn to become the steel mold.Take shape the steel mold of the techniquemanufacturing quickly to process after needing further did to throw light etc., make into the small batch quantity produce of note the mold of EU .Because the molding tool sprinkles to note or burn the knot with the steel powder but,Material and common molding tool steel contain certain margin, therefore, the life span is shorter, cans make to manufacture on a trial basis product or small batch quantities produce.Moreover, taking shape the technique quickly can also manufacture the special spare parts,If make with the metallurgy powder legal system the metals electrode, nicety cast the legal system makes the copper electrode, ND mold legal system makes graphite electrode etc..Take shape the technique creation molding tool quickly to model the equipments with the product, all is STL to read CAD system creation or CLI etc. document format datas,Different document format data to the product accuracy of the creation contain bigger margin, therefore, study the system of CAD to take shape quickly the document format of the equipments output to have the very important meaning.6, the molding tool CAD gathers technical development trendA calculator for saying, molding tool CAD gathering technique is applying in molding tool making each link assistance technique on the ×U with each link information that realizes the technique gathers.Obviously,The information gathers unify with data the management is a key.The information of the product is to pierces through in the design, analyze, process, examine, assemble a stage,Fluency, solution data format that realizes each link information standardizes and the data maintenance is a point with future CAD that share to gather technique development.The system of PDM emergence is to resolve this problem brought the first light of day.It is molding tool business enterprise application CAD that the system of PDM puts into practice gather technical and important lesson.Design in molding tool manufacturing aspect,The intelligence that imply the research, high speed that abundantexpert''s knowledge turn molding tool CAD/ the system of CAM slices theI÷ processes and its plait distance etc. is a trend that future study the development.2 中文翻译塑料模具CAD集成技术内容提要:通过分析计算机辅助注射模设计和制造的各个环节中共享的技术和信息,本文揭示了注射模CAD的集成技术的根本内涵,并提出了它的研究热点和趋势。
注塑模具 外文文献

International Journal of Automotive Technology , Vol. 13, No. 2, pp. 273−277 (2012)DOI 10.1007/s12239−012−0024−5Copyright ©2012KSAE/063−11pISSN 1229−9138/eISSN 1976-3832273DESIGN OPTIMIZA TION OF AN INJECTION MOLD FOR MINIMIZING TEMPERA TURE DEVIA TIONJ.-H. CHOI 1), S.-H. CHOI 1), D. PARK 2), C.-H. PARK 2), B.-O. RHEE 1)* and D.-H. CHOI 2)1)Graduate School of Mechanical Engineering, Ajou University, Gyeonggi 443-740, Korea 2)Graduate School of Mechanical Engineering, Hanynag University, Seoul 133-791, Korea(Received 24 January 2011; Revised 15 June 2011; Accepted 17 June 2011)ABSTRACT −The quality of an injection molded part is largely affected by the mold cooling. Consequently, this makes it necessary to optimize the mold cooling circuit when designing the part but prior to designing the mold. V arious approaches of optimizing the mold cooling circuit have been proposed previously. In this work, optimization of the mold cooling circuit was automated by a commercial process integration and design optimization tool called Process Integration, Automation and Optimization (PIAnO), which is often used for large automotive parts such as bumpers and instrument panels. The cooling channels and baffle tubes were located on the offset profile equidistant from the part surface. The locations of the cooling channels and the baffle tubes were automatically generated and input into the mold cooling computer-aided engineering program, Autodesk Moldflow Insight 2010. The objective function was the deviation of the mold surface temperature from a given design temperature. Design variables in the optimization were the depths, distances and diameters of the cooling channels and the baffle tubes. For a more practical analysis, the pressure drop and temperature drop were considered the limited values. Optimization was performed using the progressive quadratic response surface method. The optimization resulted in a more uniform temperature distribution when compared to the initial design, and utilizing the proposed optimization method, a satisfactory solution could be made at a lower cost.KEY WORDS :Injection molding, Cooling channel, Cooling analysis, PQRSM, Design optimization1. INTRODUCTIONThe cooling stage is the longest stage during the cycle time of the injection molding process. Therefore, the most effective method to reduce the cycle time is to reduce the cooling time. The cooling time is fundamentally determined by the part thickness and mold temperature, which creates a cooling time limitation. If the mold temperature and part thickness are uniform over a whole part, the cooling time is not a concern; however, non-uniform part thickness and mold temperature distribution lengthen the overall cooling time. A longer cooling time means poor temperature uniformity, which can cause the part to warp. This is especially true for large products, such as automotive bumpers and instrument panels. It is for these types of parts that temperature uniformity becomes the most important factor in mold design.We developed an automated optimization of the cooling circuit for an early part design in order to check the design validity. Usually the early part design is checked by the filing/packing and warpage analyses without a cooling analysis. This is because the assumption is that the mold temperature is uniform, which is not actually true.Providing a rapidly optimized cooling circuit for the designed part would help part designers correct their design (Koresawa and Suzuki, 1999).The optimization was designed to minimize the part temperature deviation using design variables such as the diameters and distances of the cooling channels and baffle tubes and the depths of the part from the mold surface of the cooling channels and baffle tubes. A commercial computer-aided engineering (CAE) tool, Autodesk Moldflow Insight,was used for the cooling analysis. We successfully obtained an optimized cooling circuit in a time much shorter than can be achieved in a manual design. In order to develop the automated optimization of the cooling circuit for the practical mold design, practical design parameters such as the pressure drop limit and the coolant temperature rise were considered in the optimization.The performance of the optimization technique can be affected by numerical noise in the responses. To find an optimum solution effectively when numerical noise exists,we performed an optimization by applying a regression-based sequential approximate optimizer known as the Progressive Quadratic Response Surface Method (PQRSM)(Hong e t al ., 2000), which was part of a commercial process integration and design optimization (PIDO) tool known as the Process Integration, Automation and Optimization (PIAnO) (FRAMAX, 2009).*Corresponding author . e-mail: rhex@ajou.ac.kr274J.-H. CHOI et al.2. MODEL AND CHANNEL CONFIGURATION2.1. Model ConfigurationThe model used for the optimization and CAE analysis was an automotive front bumper (FB). The size of the part was 1,800×600 mm, the element type was triangular and the number of elements in the model was approximately 26,000, with an average aspect ratio of 1.5. The model is shown in Figure 1.2.2. Cooling Channel ConfigurationThe cooling circuit for the automotive bumper mold is typically designed to have a horizontal plane of line cooling channels and to install baffle tubes from the line cooling channels. However, in this design, unnecessarily long baffle tubes attached at a line cooling channel may cause a high pressure drop in the cooling channel. The line cooling channels may not contribute to mold cooling due to their large distance from the part surface. In order to improve the design, the line cooling channels were located along the offset profile of the part surface as shown in Figure 2. The end points of the baffle tubes were also located on the offset profile along a line cooling channel.Either the line cooling channels or baffle tubes were located on the offset profiles with equal arc distances between them.3. FORMULATION3.1. Design ConstraintsThe limitation of the pressure drop and the temperature rise between the inlet and outlet of cooling channel should also be considered in the design of the mold cooling circuit. A high pressure drop usually occurs in a needlessly longcooling circuit. In a long cooling circuit, the flow rate of coolant is low, which results in a high mold temperature and a high temperature rise at the outlet. The design defect could eventually be found in the cooling analysis; however,the optimization is already time consuming, so it is better to instead apply the limits as constraints in the optimization. In this work we assumed that 4 line cooling channels were connected in series as a cluster, as shown in Figure 3.Clusters are connected in parallel by a manifold. Usually,the maximum pressure drop in a cluster is limited to 200kPa, and the maximum temperature rise at the outlet is 5o C (Menges e t al ., 2001). In the cooling analysis, each line cooling channel is regarded as a separate independent circuit for convenience. Because there were 4 line cooling channels in a circuit, the limits on the pressure drop and the temperature rise in each line cooling channel were 50 kPa and 1.25o C, respectively. We also have an additional constraint due to the fact that the diameter of the baffle tube must be greater than or equal to the diameter of the cooling channel because the baffle tube has lower heat removal efficiency than the cooling channel. These three design constraints can be expressed as Equations (1), (2) and (3) ,(1),(2),(3)where G 1 is the constraint on pressure drop, G 2 is the constraint on temperature rise, and G 3 represents the subtraction of the diameter of the baffle tube from the diameter of the cooling channel.3.2. Design V ariablesIn this work, the diameters, distances and depths of the line cooling channels and baffle tubes were chosen as design variables for optimization. The total number of design variables was 6 as shown in Table 1. Typically, the diameters of the cooling channels and baffle tubes are determined by the mold designer according to their rule of0 Pa G 150000 pa ≤≤0 C oG 2 1.2 C o≤≤G 30 mm≤Figure 1. Finite element model of the product used for theoptimization.Figure 2. Configuration of cooling channels located alongthe offset profiles.Figure 3. Clusters consisting of 4 cooling channels with baffle tubes.DESIGN OPTIMIZATION OF AN INJECTION MOLD FOR MINIMIZING TEMPERATURE DEVIATION 275thumb (Rhee et al ., 2010). However, it has been examined in great detail among the mold designers. Table 1 shows the design variables with their ranges and initial values.The minimum values for the cooling channel distance,baffle distance and baffle depth were determined by the constraints of the machining requirement. The maximum values of cooling channel distance and baffle distance were determined by the empirical maximum obtained from the mold designers. The baffle distance was a discrete variable due to a restriction in the automated use of the CAE software. In this work, the baffle distances for optimization were 60, 90 and 120 mm.3.3. Objective FunctionA principal purpose of the mold cooling circuit optimization is to achieve uniform temperature distribution over the part. The uniform temperature distribution means that the temperature deviation caused by the cooling channels is minimized, as shown in Figure 4. The objective function in the optimization was the standard deviation of part temperature as shown in Equation (4). The part temperature was an arithmetic average of the upper and the lower surfaces of the mold halves. The mold surface temperature was calculated from the finite element of the part. min ,(4)whereσ is the standard deviation of the part temperature, E i is the temperature of i -th element, E w is the average temperature of the entire triangular elements, and N is the number of elements.4. OPTIMIZATION4.1. Parametric StudyIn order to examine the effects of the design variables on the objective function, pressure drop and temperature rise,parametric studies were carried out. A parametric study was performed by changing a variable in a certain range while keeping all other variables fixed. Figures 5-7 showthe results of parametric studies for the objective function,pressure drop temperature rise, respectively. In each figure,the x-axis indicates the levels of design variables. Every design variable was divided into 11 levels from its lower bound to its upper bound. -5 and 5 mean the lower and upper bounds, respectively.When examining the temperature deviation, the diameter of the cooling channels shows little influence to the objective function (see Figure 5.). This result was predictable because the cooling channel affects the parttemperature to a lesser degree than the baffle tubes in theautomotive bumper mold. The automotive bumper mold has a deep core so that the mold cooling depends upon the baffle tubes rather than the cooling channels. Another reason of the lack of influence can be that the flow state in the cooling channel remains turbulent in the range of the parametric study. The cooling channel usually has a smaller diameter than the baffle tube. When the flow in the baffle tube is kept in the turbulent state, the flow in the cooling channel will be in the turbulent state.The diameters of the baffle tubes show a tangible influence when it increases above a certain value.Increasing of the diameter changes the flow in the tube to a laminar flow state. This is the cause for the lower heat transfer coefficient when compared to the turbulent flow state. This is why the temperature deviation becomes larger when the baffle tube diameter increases.σE i E w –()2N --------------------i 1=N∑=Figure 4. Scheme of the temperature field by the cooling channels.Table 1. Lower and the upper bounds for design variables and the initial values for the optimization (unit: mm).DescriptionLower Initial Upper X 1Channel diameter 103040X 2Baffle diameter 103040X 3Channel distance 6090120X 4Baffle distance 6060120X 5Channel depth 306090X 6Baffle depth306090Figure 5. Parametric study result of temperature deviation (objective function).276J.-H. CHOI et al.Among all parameters, the baffle depth shows the largest influence on the objective function, as shown in Figure 5.As the baffle depth increases, the objective function increases. This means that the deeper location of the baffle tubes causes the temperature deviation to increase. Also, it confirms that the cooling of the automotive bumper mold depends upon the baffle tubes.The diameters of the cooling channels and the baffle tubes have the highest influence on the pressure drop in the cooling circuit, while the other variables show little influence (see Figure 6.). As the diameters increase, the pressure drop decreases after a certain value. This is also a predictable result as a larger diameter decreases the pressure drop.The influences of the temperature rise at the outlet are shown in Figure 7. The most influential parameters are the baffle diameter and the channel distance. The influence of the baffle diameter shows the highest values in the range from -1 to 3. In the case of the smaller baffle diameter, the reduced surface area for the heat transfer may cause a smaller temperature rise, while the larger baffle diameter may cause the lower heat transfer coefficient due to the lower flow rate.The increased channel distance means that each cooling channel takes up a larger area of the part surface with a larger amount of heat removal. This may give a physical explanation to why the increase of the temperature rise increases with channel distance. The fluctuations shown inFigure 7 are supposed to be numerical noise.4.2. Optimization ResultsThe largest increase in the temperature rise (Figure 7) is approximately 0.15o C. This value is much less than the constraint. The influence of the variables on the temperature rise is not tangible.The baffle distance was considered the discrete variable in this work; hence, it was difficult to apply a general optimization method. Because there were three values,optimizations were carried out 3 times with the 5 design parameters. The baffle distance was fixed in each optimization.Figures 8 and 9 show the temperature deviations as the channel diameter, x 1 and the channel distance, x 3 change by 0.1% using the perturbation method around their initial design values. From these results we recognized that the variations in the temperature deviations as x 1 and x 3 varied included numerical noise.Therefore, we chose PQRSM as the optimization method that could effectively optimize the response withnumerical noise. The PQRSM equipped in a commercialFigure 6. Parametric study result of the pressure drop.Figure 7. Parametric study result of the temperature rise.Figure 8. V ariation of the temperature deviation w.r.t. x 1observed by using 0.1% perturbation method.Figure 9. V ariation of the temperature deviation w.r.t. x 3observed by using 0.1% perturbation method.DESIGN OPTIMIZATION OF AN INJECTION MOLD FOR MINIMIZING TEMPERATURE DEVIATION277PIDO tool, PIAnO, approximates the objective function and constraints with quadratic functions in the trust region, and it sequentially moves and reduces the trust region until it finds the optimum solution.The results of the optimization using the PQRSM are shown in Table 2. Baseline represents the standard condition before applying the optimization. After the optimizations were carried out for the 3 cases of the baffle distance (x4), the lowest temperature deviation was obtained in the case of a baffle distance of 60 mm. Therefore we conclude that a baffle distance of 60 mm is our optimized result.At this optimized result, the temperature deviation was reduced by 19.2% compared to that of the baseline design while satisfying all other design requirements. Among the design variables, the channel diameter, x1, the baffle diameter, x2 and the channel distance, x3 remained close to their initial values while the channel depth, x5 moved toward the upper bound and the baffle depth, x6 toward the lower bound. Thus, we expect a better result if the bounds of the baffle distance, x4, channel depth, x5 and baffle depth, x6 can be relaxed.5. CONCLUSIONIn this study, we carried out the optimization of the cooling circuit for an automotive front bumper. The design objective was to minimize the temperature deviation while satisfying all constraints. There were three design constraints that included the pressure drop, temperature rise and aspect ratio, in addition to side constraints on six design variables.Among the six design variables, the baffle distance was the discrete design variable. Thus, we carried out optimizations for the three cases of baffle distances being 60, 90 and 120 mm. The lowest temperature deviation was obtained in the case of a baffle distance of 60 mm. In this case, the temperature deviation was reduced by 19.2% compared to the baseline design while satisfying all design requirements. It is believed that the design optimization approach of employing CAE and PIDO tools adopted in this study can be applied for the design of many industrial manufacturing processes.REFERENCESFRAMAX Inc (2009). PIAnO Tutorial.FRAMAX Inc(2009). PIAnO User’s Manual.Hong, K. ., Choi, D. H. and Kim, M. S. (2000). Progressive quadratic approximation method for effective constructing the second-order response surface models in the large scaled system design. The Kore an Socie ty of Me chanical Engine e rs(A)24, 12/12, 3040−3052.Koresawa, H. and Suzuki, H. (1999). Autonomous arrangement of cooling channels layout in injection molding. Proc. 1999 Annual Technological Conf. Society of Plastics Engineers, 1073−1077.Menges, G., Michaeli, W. and Mohren, P. (2001). How to MakeInjection Molds. 3rd Edn. Hanser Gardner Publications, Inc.. Ohio. 298−302.Rhee, B. O., Park, C. S., Chang H. K., Jung, H. W. and Lee, Y. J. (2010). Automatic generation of optimum cooling circuit for large injection molded parts. Int. J. Precision Eng. and Manufacturing, 11, 439−444.Table 2. Optimization results summary.Lower Baseline X4=60 X4=90 X4=120 Upperx1 10.00 30.00 29.67 28.39 30.00 40.00 x2 10.00 30.00 30.36 28.39 30.00 40.00 x3 60.00 90.00 89.37 90.29 88.13 120.00 x4 60.00 60.00 60.00 90.00 120.00 120.00 x5 30.00 60.00 87.63 88.81 90.00 90.00 x6 30.00 60.00 30.00 30.00 30.00 90.00 OBJ 6.62 5.35 5.60 5.46G1 016790 16904 16610 8758 50000G2 00.36 0.43 0.33 0.38 1.20G3 0.00 -0.69 0.00 0.00 0.00。
塑料模具毕业外文文献翻译、塑料制品的CADCAE集成的注塑模具设计系统外文翻译、中英文翻译
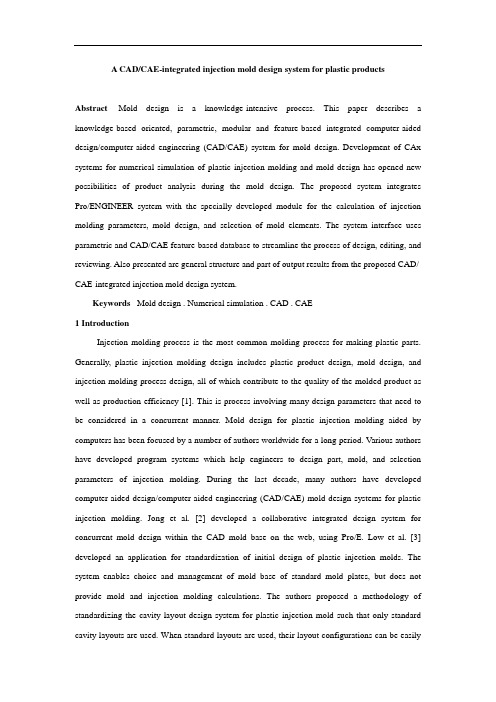
A CAD/CAE-integrated injection mold design system for plastic productsAbstract Mold design is a knowledge-intensive process. This paper describes a knowledge-based oriented, parametric, modular and feature-based integrated computer-aided design/computer-aided engineering (CAD/CAE) system for mold design. Development of CAx systems for numerical simulation of plastic injection molding and mold design has opened new possibilities of product analysis during the mold design. The proposed system integrates Pro/ENGINEER system with the specially developed module for the calculation of injection molding parameters, mold design, and selection of mold elements. The system interface uses parametric and CAD/CAE feature-based database to streamline the process of design, editing, and reviewing. Also presented are general structure and part of output results from the proposed CAD/ CAE-integrated injection mold design system.Keywords Mold design . Numerical simulation . CAD . CAE1 IntroductionInjection molding process is the most common molding process for making plastic parts. Generally, plastic injection molding design includes plastic product design, mold design, and injection molding process design, all of which contribute to the quality of the molded product as well as production efficiency [1]. This is process involving many design parameters that need to be considered in a concurrent manner. Mold design for plastic injection molding aided by computers has been focused by a number of authors worldwide for a long period. Various authors have developed program systems which help engineers to design part, mold, and selection parameters of injection molding. During the last decade, many authors have developed computer-aided design/computer-aided engineering (CAD/CAE) mold design systems for plastic injection molding. Jong et al. [2] developed a collaborative integrated design system for concurrent mold design within the CAD mold base on the web, using Pro/E. Low et al. [3] developed an application for standardization of initial design of plastic injection molds. The system enables choice and management of mold base of standard mold plates, but does not provide mold and injection molding calculations. The authors proposed a methodology of standardizing the cavity layout design system for plastic injection mold such that only standard cavity layouts are used. When standard layouts are used, their layout configurations can be easilystored in a database. Lin at al. [4, 5] describe a structural design system for 3D drawing mold based on functional features using a minimum set of initial information. In addition, it is also applicable to assign the functional features flexibly before accomplishing the design of a solid model for the main parts of a drawing mold. This design system includes modules for selection and calculation of mold components. It uses Pro/E modules Pro/Program and Pro/Toolkit, and consists of modules for mold selection, modification and design. Deng et al. [6, 7] analyzed development of the CAD/CAE integration. The authors also analyzed systems and problems of integration between CAD and CAE systems for numerical simulation of injection molding and mold design. Authors propose a feature ontology consisting of a number of CAD/CAE features. This feature represents not only the geometric information of plastic part, but also the design intent is oriented towards analysis. Part features contain the overall product information of a plastic part, wall features, development features (such as chamfer, ribs, boss, hole, etc.), treatment features which contain analysis-related design information and sub wall developed features. Wall and development features are so called “component features〞. God ec et al. [8, 9] developed a CAE system for mold design and injection molding parameters calculations. The system is based on morphology matrix and decision diagrams. The system is used for thermal, rheological and mechanical calculation, and material base management,Fig. 1 General structure of integrated injection mold design system for plastic productsbut no integration with commercial CAx software is provided. Huang et al. [10] developed a mold-base design system for injection molding. The database they used was parametric and feature-based oriented. The system used Pro/E for modeling database components. Kong et al. [11]developed a parametric 3D plastic injection mold design system integrated with solid works. Other knowledge-based systems, such as IMOLD, ESMOLD, IKMOULD, and IKBMOULD, have been developed for injection mold design. IMOLD divides mold design into four major steps; parting surface design, impression design, runner system design, and mold-base design. The software uses a knowledge-based CAD system to provide an interactive environment, assist designers in the rapid completion of mold design, and promote the standardization of the mold design process. IKB-MOULD application consists of databases and knowledge bases for mold manufacturing. Lou et al. [12] developed an integrated knowledge-based system for mold base design. The system has module for impression calculation, dimension calculation, calculation of the number of mold plates and selection of injection machine. The system uses Pro/ Mold Base library. This paper describes KBS and key technologies, such as product modeling, the frame-rule method, CBS, and the neural networks. A multilayer neural network has been trained by back propagation BP. This neural network adopts length, width, height and the number of parts in the mold as input and nine parameters (length, width, and height of up and down set-in, mold bases side thickness, bottom thickness of the core, and cavity plates) as output. Mok et al. [13, 14] developed an intelligent collaborative KBS for injection molds. Mok at el. [15] has developed an effective reuse and retrieval system that can register modeled standard parts using a simple graphical user interface even though designers may not know the rules of registration for a database. The mold design system was developed using an Open API and commercial CAD/computer aided manufacturing (CAM)/CAE solution. The system was applied to standardize mold bases and mold parts in Hyundai Heavy Industry. This system adopted the method of design editing, which implements the master model using features. The developed system provides methods whereby designers can register the master model, which is defined as a function of 3D CAD, as standard parts and effectively reuse standard parts even though they do not recognize the rules of the database.Todic et al. [16] developed a software solution for automated process planning for manufacturing of plastic injection molds. This CAD/CAPP/CAM system does not provide CAE calculation of parameters of injection molding and mold design. Maican et al. [17] used CAE for mechanical, thermal, and rheological calculations. They analyzed physical, mechanical, and thermal properties of plastic materials. They defined the critical parameters of loaded part. Nardinet al. [18] tried to develop the system which would suit all the needs of the injection molding for selection of the part–mold–technology system. The simulation results consist of geometrical and manufacturing data. On the basis of the simulation results, part designers can optimize part geometry, while mold designers can optimize the running and the cooling system of the mold. The authors developed a program which helps the programmers of the injection molding machine to transfer simulation data directly to the machine. Zhou et al. [1] developed a virtual injection molding system based on numerical simulation. Ma et al. [19] developed standard component library for plastic injection mold design using an object-oriented approach. This is an objector iented, library model for defining mechanical components parametrically. They developed an object-oriented mold component library model for incorporating different geometric topologies and non-geometric information. Over the years, many researchers have attempted to automate a wholeFig. 2 Structure of module for numerical simulation of injection molding processFig. 3 Forms to define the mold geometrymold design process using various knowledge-based engineering (KBE) approaches, such as rule-based reasoning (RBR), and case base (CBR) and parametric design template (PDT). Chan at al. [20] developed a 3D CAD knowledge-based assisted injection mold design system (IKB mold). In their research, design rules and expert knowledge of mold design were obtained from experienced mold designers and handbooks through various traditional knowledge acquisition processes. The traditional KBE approaches, such as RBR, CBR, and simple PDT have been successfully applied to mold cavity and runner layout design automation of the one product mold. Ye et al. [21] proposed a feature-based and object-oriented hierarchical representation and simplified symbolic geometry approach for automation mold assembly modeling. The previously mentioned analysis of various systems shows that authors used different ways to solve the problems of mold design by reducing it to mold configureator (selector). They used CAD/CAE integration for creating precision rules for mold-base selection. Many authors used CAE system for numerical simulation of injection molding to define parameters of injection molding. Several also developed original CAE modules for mold and injection molding process calculation. However, common to all previously mentioned systems is the lack of module for calculation of mold and injection molding parameters which would allow integration with the results of numerical simulation. This leads to conclusion that there is a need to create a software system which integrates parameters of injection molding with the result obtained by numericalFig. 4 Forms to determine the distance between the cooling channels and mold cavityFig. 5 Mold-base selector formssimulation of injection molding, mold calculation, and selection. All this would be integrated into CAD/CAE-integrated injection mold design system for plastic products.2 Structure of integrated CAD/CAE systemAs is well known, various computational approaches for supporting mold design systems of various authors use design automation techniques such as KBE (RBR, CBR, PDT) or design optimisation techniques such as traditional (NLP,LP, BB, GBA, IR, HR) or meta heuristic search such as (TS, SA, GA) and other special techniques such as (SPA, AR, ED).The developed interactive software system makes possible to perform: 3D modeling of the parts, analysis of part design and simulation model design, numerical simulation of injection molding, and mold design with required calculations.The system consists of four basic modules:& Module for CAD modeling of the part& Module for numerical simulation of injection molding processFig. 6 Form for mechanical mold calculation& Module for calculation of parameters of injection molding and mold design calculation and selection& Module for mold modeling (core and cavity design and design all residual mold components) The general structure of integrated injection mold design system for plastic products is shown in Fig. 1.2.1 Module for CAD modeling of the part (module I)The module for CAD modeling of the part is the first module within the integrated CAD/CAE system. This module is used for generating CAD model of the plastic product and appropriate simulation model. The result of this module is solid model of plastic part with all necessary geometrical and precision specifications. Precision specifications are: project name, number, feature ID, feature name, position of base point, code number of simulation annealing, trade material name, material grade, part tolerance, machine specification (name, clamping force, maximal pressure, dimensions of work piece), and number of cavity. If geometrical and precision specification is specified (given) with product model, the same are used as input to the nextmodule, while this module is used only to generate the simulation model.2.2 Module for numerical simulation of injection molding process (module II)Module II is used for numerical simulation of injection molding process. User implements an iterative simulation process for determining the mold ability parameters of injection molding and simulation model specification. The structure of this module is shown in Fig. 2.After a product model is imported and a polymer is selected from the plastic material database, user selects the best location for gating subsystem. The database contains rheological, thermal, and mechanical properties of plastic materials. User defines parameters of injection molding and picks the location for the gating subsystem. Further analyses are carried out: the plastic flow, fill time, injection pressure, pressure drop, flow front temperature, presence of weld line, presence of air traps, cooling quality, etc.The module offers four different types of mold flow analysis. Each analysis is aimed at solving specific problems:& Part analysis—This analysis is used to test a known gate location, material, and part geometry to verify that a part will have acceptable processing conditions.& Gate analysis—This analysis tests multiple gate locations and compares the analysis outputs to determine the optimal gate location.& Sink mark analysis—This analysis detects sink mark locations and depths to resolve cosmetic problems before the mold is built eliminating quality disputes that could arise between the molder and the customer.The most important parameters are the following: [22]& Part thickness& Flow length& Radius and drafts,& Thickness transitions& Part material& Location of gates& Number of gates& Mold temperature& Melt temperature& Injection pressure& Maximal injection molding machine pressureIn addition to the previously mentioned parameters of injection molding, the module shows following simulation results: welding line position, distribution of air traps, the distribution of injection molding pressure, shear stressFig. 7 Segment of the mechanical calculation algorithmdistribution, temperature distribution on the surface of the simulation model, the quality of filling of a simulation model, the quality of a simulation model from the standpoint of cooling, and time of injection molding [22, 23]. A part of output results from this module are the input data for thenext module. These output results are: material grade and material supplier, modulus of elasticity in the flow direction, modulus of elasticity transverse direction, injection pressure, ejection temperature, mold temperature, melting temperature, highest melting temperature thermoplastic, thermoplastic density in liquid and solid state, and maximum pressure of injection molding machine. During implementation of iterative SA procedure, user defines the moldability simulation model and the parameters of injection molding. All results are represented by different colors in the regions of the simulation model.2.3 Module for calculation of parameters of injection molding and mold design calculation and selection (module III)This module is used for analytical calculations, mold sizing, and its selection. Two of the more forms for determining the dimensions of core and cavity mold plates are shown in Fig. 3.Based on the dimensions of the simulation model and clamping force (Fig. 3) user selects the mold material and system calculates the width and length of core and cavity plates. Wall thickness between the mold cavity to the cooling channel can be calculated with the following three criteria: criterion allowable shear stress, allowable bending stress criterion, and the criterion of allowable angle isotherms are shown in Fig. 4 [22, 24]. The system adopts the maximum value of comparing the values of wall thickness calculated by previously mentioned criteria.Fig. 8 Forms for standard mold plates selectionFig. 9 Forms for mold plate model generationBased on the geometry of the simulation model, user select shape and mold type. Forms for the selection mold shape, type, and subsystems are shown in Fig. 5. Once these steps are completed, user implements the thermal, rheological, and mechanical calculation of mold specifications. An example of one of the several forms for mechanical mold calculation is shown in Fig. 6.Segment of the algorithm of mechanical calculations is shown in Fig. 7.f max maximal flexure of cavity platef dop allowed displacement of cavity plateε elastic deformationαmin minimal value of shrinkage factorE k modulus of elasticity of cavity plateG shear modulusS k wall thickness distance measuring between cavity and waterlined KT cooling channel diameterAfter the thermal, rheological, and mechanical calculations, user selects mold plates from the mold base. Form for the selection of standard mold plates is shown in Fig. 8. The system calculates the value of thickness of risers, fixed, and movable mold plates (Fig. 8). Based on the calculated dimensions, the system automatically adopts the first major standard value for the thickness of risers, movable, and fixed mold plate. Calculation of the thickness and the adoption of standard values are presented in the form as shown in Fig. 8.The interactive system recommends the required mold plates. The module loads dimensions from the database and generates a solid model of the plate. After the plate selection, the plate is automatically dimensioned, material plate isFig. 10 Structure of module IVassigned, and 3D model and 2D technical drawing are generated on demand. Dimensions of mold component (e.g., fixed plate) are shown in the form for mold plate mode generation, as shown inThe system loads the plate size required from the mold base. In this way, load up any other necessary standard mold plates that make up the mold subassembly. Subassembly mold model made up of instance plates are shown in Fig. 10Then get loaded other components of subsystems as shown in Fig. 5. Subsystem for selection other components include bolts and washers. The way of components selection are based on a production rules by authors and by company “D-M-E〞[25, 26].2.4 Module for mold modeling (core and cavity design and design all residual mold components; module IV)This module is used for CAD modeling of the mold (core and cavity design). This module uses additional software tools for automation creating core and cavity from simulation (reference) model including shrinkage factor of plastics material and automation splitting mold volumes of the fixed and movable plates. The structure of this module is shown in Fig. 11.Additional capability of this module consists of software tools for:& Applying a shrinkage that corresponds to design plastic part, geometry, and molding conditions, which are computed in module for numerical simulation& Make conceptual CAD model for nonstandard plates and mold components& Design impression, inserts, sand cores, sliders and other components that define a shape of molded part& Populate a mold assembly with standard components such as new developed mold base which consists of DME mold base and mold base of enterprises which use this system, and CAD modeling ejector pins, screws, and other components creating corresponding clearance holes& Create runners and waterlines, which dimensions was calculated in module for calculating of parameters of injection molding and mold design calculation and selection& Check interference of components during mold opening, and check the draft surfacesAfter applied dimensions and selection mold components, user loads 3D model of the fixed (core) and movable (cavity) plate. Geometry mold specifications, calculated in the previous module, are automatically integrated into this module, allowing it to generate the final mold assembly. Output from this module receives the complete mold model of the assembly as shown in Fig. 15. Thismodule allowsFig. 11 Subassembly model of moldFig. 12 CAD model of the test Productmodeling of nonstandard and standard mold components that are not contained in the mold base.3 Case studyThe complete theoretical framework of the CAD/CAE-integrated injection mold design system for plastic products was presented in the previous sections. In order to complete this review, the system was entirely tested on a real case study. The system was tested on few examples of similar plastic parts. Based on the general structure of the model of integrated CAD/CAE design system shown in Fig. 1, the authors tested the system on some concrete examples. One of the examples used for verification of the test model of the plastic part is shown in Fig. 12.The module for the numerical simulation of injection molding process defines the optimal location for setting gating subsystem. Dark blue regions indicate the optimal position for setting gating subsystem as shown in Fig. 13.Based on dimensions, shape, material of the case study product (Fig. 11), optimal gating subsystem location (Fig. 13), and injection molding parameters (Table 1), the simulation model shown in Fig. 14 was generated.One of the rules for defining simulation model gate for numerical simulation:IF (tunnel, plastic material, mass) THEN prediction dimension (upper tunnel, length, diameter1, diameter2, radius, angle, etc.)Part of the output results from module II, which are used in module III are shown in Table 1.Fig. 13 Optimal gating subsystem location in the partTable 1 Part of the output results from the module for the numerical simulation of injection molding processMaterial grade and material supplier Acrylonitrile butadiene styrene 780(ABS 780),Kumho Chemicals Inc.Max injection pressure 100 MPaMold temperature 60°C ili 40Melt Temperature 230°CInjection Time 0,39 s 0,2 sInjection Pressure 27,93 MPaRecommended ejection temperature 79°CModulus of elasticity, flow direction for ABS 780 2,600 MPaModulus of elasticity, transverse direction for ABS 780 2,600 MPaPoision ratio in all directions for ABS 780 0.38Shear modulus for ABS 780 942 MPaDensity in liquid state 0.94032 g/cm3Density in solid state 1.047 g/cm3In module III, the system calculates clamping force F=27.9 kN (Fig. 3), cooling channel diameter d KT=6 mm, cooling channel length lKT090 mm (Fig. 4). Given the shape and dimensions of the simulation model, square shape of mold with normal performance was selected as shown in Fig. 5. Selected mold assembly standard series: 1,616, length and width of mold housing 156×156 mm as shown in Fig. 8. In the segment of calculation shown in Fig. 8, mold design system panel recommends the following mold plates:& Top clamping plate N03-1616-20& Bottom clamping plate N04-1616-20& Fixed mold plate (core plate) N10A-1616-36& Movable plate (cavity plate) N10B-1616-36& Support plate N20-1616-26& Risers N30-1616-46& Ejector retainer plate N40-1616-10& Ejector plate N50-1616-12After finishing the fixed and movable mold plates from the standpoint of CAD modeling core and cavity plates, cooling channel, followed by manual selection of other mold standard components such as sprue bush, locating ring, guide pins, guide bush, leading bushing guide, spacer plates, screws (M4×10, M10×100, M10×30, M6×16, M10×30, etc.) and modeling nonstandard mold components (if any) ejector pins, ejector holes, inserts etc. A complete model of the mold assembly with tested simulation model is shown in Fig. 15.Fig. 14 Simulation model of plastic partFig. 15 Model of the mold assembly with tested simulation model4 ConclusionThe objective of this research was to develop a CAD/CAE integrated system for mold design which is based on Pro/ ENGINEER system and uses specially designed and developed modules for mold design. This paper presents a software solution for multiple cavity mold of identical molding parts, the so-called one product mold. The system is dedicated to design of normal types of molds for products whose length and width are substantially greater than product height, i.e., the system is customized for special requirements of mold manufacturers. The proposed system allows full control over CAD/CAE feature parameters which enables convenient and rapid mold modification. The described CAD/CAE modules are feature-based, parametric, based on solid models, and object oriented. The module for numerical simulation of injection molding allows the determination selection of injection molding parameters. The module for calculation of parameters of injection molding process and mold design calculation and selection improves design Fig. 15 Model of the mold assembly with tested simulation model faster, reduces mold design errors, and provides geometric and precision information necessary for complete mold design. The knowledge base of the system can be accessed by mold designers through interactive modules so that their own intelligence and experience can also be incorporated into the total mold design. Manufacture of the part confirms that the developed CAD/CAE system provides correct results and proves to be a confident software tool.Future research will be directed towards three main goals. The first is to develop a system for automation of family mold design. Another line of research is the integration with CAPP system for plastic injection molds manufacturing developed at the Faculty of Technical Sciences. Finally, following current trends in this area, a collaborative system using web technologies and blackboard architecture shall be designed and implemented.塑料制品的CAD / CAE集成的注塑模具设计系统摘要:模具设计是一个知识密集的过程。
注射注塑模具外文翻译外文文献翻译、中英文翻译、外文翻译
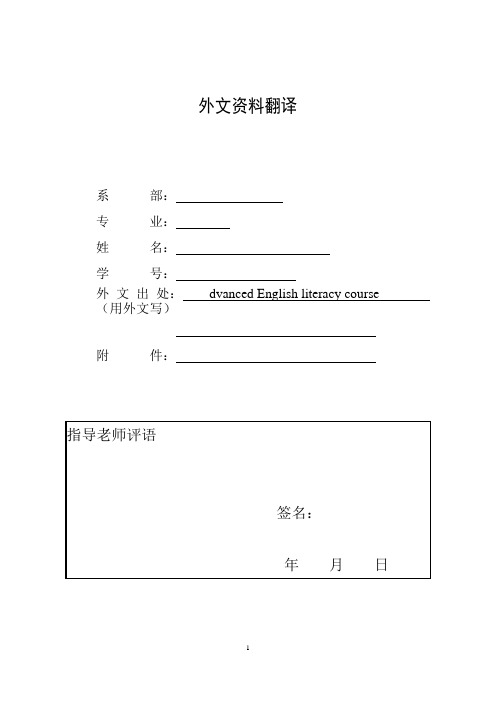
外文资料翻译系部:专业:姓名:学号:外文出处:dvanced English literacy course(用外文写)附件:指导老师评语签名:年月日第一篇译文(中文)2.3注射模2.3.1注射模塑注塑主要用于热塑性制件的生产,它也是最古老的塑料成型方式之一。
目前,注塑占所有塑料树脂消费的30%。
典型的注塑产品主要有杯子器具、容器、机架、工具手柄、旋钮(球形捏手)、电器和通讯部件(如电话接收器),玩具和铅管制造装置。
聚合物熔体因其较高的分子质量而具有很高的粘性;它们不能像金属一样在重力流的作用下直接被倒入模具中,而是需要在高压的作用下强行注入模具中。
因此当一个金属铸件的机械性能主要由模壁热传递的速率决定,这决定了最终铸件的晶粒度和纤维取向,也决定了注塑时熔体注入时的高压产生强大的剪切力是物料中分子取向的主要决定力量。
由此所知,成品的机械性能主要受注射条件和在模具中的冷却条件影响。
注塑已经被应用于热塑性塑料和热固性塑料、泡沫部分,而且也已经被改良用于生产反应注塑过程,在此过程中,一个热固树脂系统的两个组成部分在模具中同时被注射填充,然后迅速聚合。
然而大多数注塑被用热塑性塑料上,接下来的讨论就集中在这样的模具上。
典型的注塑周期或流程包括五个阶段(见图2-1):(1)注射或模具填充;(2)填充或压紧;(3)定型;(4)冷却;(5)零件顶出。
图2-1 注塑流程塑料芯块(或粉末)被装入进料斗,穿过一条在注射料筒中通过旋转螺杆的作用下塑料芯块(或粉末)被向前推进的通道。
螺杆的旋转迫使这些芯块在高压下对抗使它们受热融化的料筒加热壁。
加热温度在265至500华氏度之间。
随着压力增强,旋转螺杆被推向后压直到积累了足够的塑料能够发射。
注射活塞迫使熔融塑料从料筒,通过喷嘴、浇口和流道系统,最后进入模具型腔。
在注塑过程中,模具型腔被完全充满。
当塑料接触冰冷的模具表面,便迅速固化形成表层。
由于型芯还处于熔融状态,塑料流经型芯来完成模具的填充。
模具设计外文参考文献(精选120个最新)
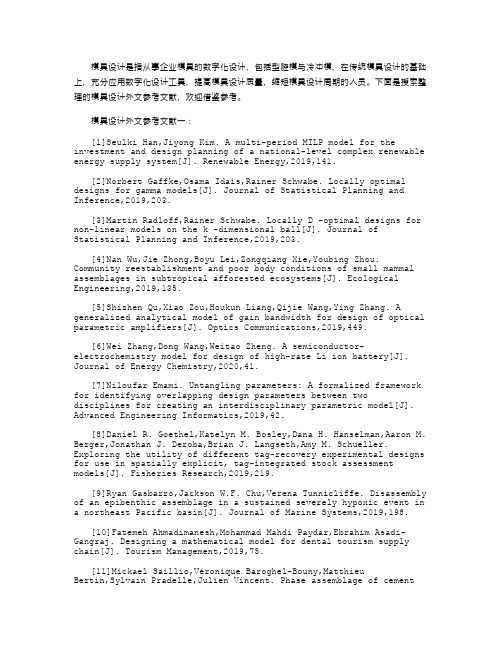
模具设计是指从事企业模具的数字化设计,包括型腔模与冷冲模,在传统模具设计的基础上,充分应用数字化设计工具,提高模具设计质量,缩短模具设计周期的人员。
下面是搜索整理的模具设计外文参考文献,欢迎借鉴参考。
模具设计外文参考文献一: [1]Seulki Han,Jiyong Kim. A multi-period MILP model for the investment and design planning of a national-level complex renewable energy supply system[J]. Renewable Energy,2019,141. [2]Norbert Gaffke,Osama Idais,Rainer Schwabe. Locally optimal designs for gamma models[J]. Journal of Statistical Planning and Inference,2019,203. [3]Martin Radloff,Rainer Schwabe. Locally D -optimal designs for non-linear models on the k -dimensional ball[J]. Journal ofStatistical Planning and Inference,2019,203. [4]Nan Wu,Jie Zhong,Boyu Lei,Zongqiang Xie,Youbing Zhou. Community reestablishment and poor body conditions of small mammal assemblages in subtropical afforested ecosystems[J]. Ecological Engineering,2019,135. [5]Shizhen Qu,Xiao Zou,Houkun Liang,Qijie Wang,Ying Zhang. A generalized analytical model of gain bandwidth for design of optical parametric amplifiers[J]. Optics Communications,2019,449. [6]Wei Zhang,Dong Wang,Weitao Zheng. A semiconductor-electrochemistry model for design of high-rate Li ion battery[J]. Journal of Energy Chemistry,2020,41. [7]Niloufar Emami. Untangling parameters: A formalized framework for identifying overlapping design parameters between twodisciplines for creating an interdisciplinary parametric model[J]. Advanced Engineering Informatics,2019,42. [8]Daniel R. Goethel,Katelyn M. Bosley,Dana H. Hanselman,Aaron M. Berger,Jonathan J. Deroba,Brian J. Langseth,Amy M. Schueller. Exploring the utility of different tag-recovery experimental designs for use in spatially explicit, tag-integrated stock assessment models[J]. Fisheries Research,2019,219. [9]Ryan Gasbarro,Jackson W.F. Chu,Verena Tunnicliffe. Disassembly of an epibenthic assemblage in a sustained severely hypoxic event ina northeast Pacific basin[J]. Journal of Marine Systems,2019,198. [10]Fatemeh Ahmadimanesh,Mohammad Mahdi Paydar,Ebrahim Asadi-Gangraj. Designing a mathematical model for dental tourism supply chain[J]. Tourism Management,2019,75. [11]Mickael Saillio,Véronique Baroghel-Bouny,MatthieuBertin,Sylvain Pradelle,Julien Vincent. Phase assemblage of cementpastes with SCM at different ages[J]. Construction and Building Materials,2019,224. [12]Martina Barto?ová,Jana Schenková,Vendula Polá?ková,Jind?i?ka Bojková,Vanda ?orfová,Michal Horsák. Macroinvertebrate assemblagesof the post-mining calcareous stream habitats: Are they similar to those inhabiting the natural calcareous springs?[J]. Ecological Engineering,2019,136. [13]Fei Zhong,Juan Wu,Yanran Dai,Dongfang Xiang,ZifaDeng,Shuiping Cheng. Responses of water quality and phytoplankton assemblages to remediation projects in two hypereutrophictributaries of Chaohu Lake[J]. Journal of Environmental Management,2019,248. [14]Meng Zhang,Zhihua Liu,Jia Deng,Mengjian Yang,QilongDai,Tianzeng Zhang. Optimum design of compressive residual stress field caused by ultrasonic surface rolling with a mathematicalmodel[J]. Applied Mathematical Modelling,2019,76. [15]Zaheer Masood,Raza Samar,Muhammad Asif Zahoor Raja. Design ofa mathematical model for the Stuxnet virus in a network of critical control infrastructure[J]. Computers & Security,2019,87. [16]J.A. Johnson,C.T. Perry,S.G. Smithers,K.M. Morgan,S.A. Woodroffe. Reef shallowing is a critical control on benthic foraminiferal assemblage composition on nearshore turbid coralreefs[J]. Palaeogeography, Palaeoclimatology,Palaeoecology,2019,533. [17]Subramanian Balaji,Eanoch Golden Julie,Yesudhas Harold Robinson,Raghvendra Kumar,Pham Huy Thong,Le Hoang Son. Design of a security-aware routing scheme in Mobile Ad-hoc Network using repeated game model[J]. Computer Standards & Interfaces,2019,66. [18]Hualing Hu,Meng Li,Guoxi Wang,Marios Drosos,Zhen Li,Zhengyi Hu,Beidou Xi. Water-soluble mercury induced by organic amendments affected microbial community assemblage in mercury-polluted paddy soil[J]. Chemosphere,2019,236. [19]Valentin Pascu,Hugues Garnier,Lennart Ljung,Alexandre Janot. Benchmark problems for continuous-time model identification: Design aspects, results and perspectives[J]. Automatica,2019,107. [20]Dong-Dong Chen,Y.C. Lin,Fan Wu. A design framework for optimizing forming processing parameters based on matrix cellular automaton and neural network-based model predictive controlmethods[J]. Applied Mathematical Modelling,2019,76. [21]Luiza Carvalho Franco,Júlia Castro Mendes,Laís Cristina Barbosa Costa,Rúbia Ricceli Pira,Ricardo André Fiorotti Peixoto. Design and thermal evaluation of a social housing model conceived with bioclimatic principles and recycled aggregates[J]. Sustainable Cities and Society,2019,51. [22]?lise Lacoste,Andréa M. Weise,Marie-France Lavoie,Philippe Archambault,Christopher W. McKindsey. Changes in infaunal assemblage structure influence nutrient fluxes in sediment enriched by mussel biodeposition[J]. Science of the Total Environment,2019,692. [23]Shixiong Yang,Bing Song,Siyuan Ye,Qinghai Xu,Lei He,Guangming Zhao,Jie Li,Edward A. Laws. Regional-scale distributions of pollen and spore assemblages in alluvium around the Bohai Sea: An essential step toward understanding marine palynological sources in China[J]. Marine Geology,2019,415. [24]Sheldon A. Blaauw,James W. Maina,Emile Horak. Towards a mix design model for the prediction of permeability of hot-mixasphalt[J]. Construction and Building Materials,2019,221. [25]Martin Classen,Wolfgang Kurz,Markus Sch?fer,Josef Hegger. A mechanical design model for steel and concrete composite memberswith web openings[J]. Engineering Structures,2019,197. [26]Susana Pinedo,Enric Ballesteros. The role of competitor, stress-tolerant and opportunist species in the development of indexes based on rocky shore assemblages for the assessment of ecological status[J]. Ecological Indicators,2019,107. [27]Kate?ina Francová,Kate?ina ?umberová,Andrea Ku?erová,Martina ?tvrtlíková,Michal ?orf,Jakub Borovec,Bo?ek Drozd,Georg A.Janauer,Jaroslav Vrba. Macrophyte assemblages in fishponds under different fish farming management[J]. Aquatic Botany,2019,159. [28]Michael D. Cook,Eddy H. Trinklein,Gordon G. Parker,Matthew J. Heath,Wayne W. Weaver,Rush D. Robinett,David G. Wilson. Reducedorder model verification of a DC microgrid for controller design and determination of storage requirements[J]. International Journal of Electrical Power and Energy Systems,2020,114. [29]Eduardo López. Annelid assemblages on artificial and natural hard substrata differ decades after building: A case study on a one-century old seawall[J]. Estuarine, Coastal and ShelfScience,2019,227. [30]Pablo Fierro,Claudio Valdovinos,Ivan Arismendi,GustavoDíaz,Alfonso Jara-Flores,Evelyn Habit,Luis Vargas-Chacoff. Examining the influence of human stressors on benthic algae, macroinvertebrate, and fish assemblages in Mediterranean streams of Chile[J]. Science of the Total Environment,2019,686. 模具设计外文参考文献二: [31]R.V. Rodrigues,J.S. Patil,Sathish K,A.C. Anil. Dinoflagellate planktonic-motile-stage and benthic-cyst assemblages from a monsoon-influenced tropical harbour: Elucidating the role of environmental conditions[J]. Estuarine, Coastal and Shelf Science,2019,226. [32]Chengqing Liu,Xinyi Luo,Dengjia Fang,ChuanqingShi,Saydirakhmonov Sarvar,Bida Zhao. Study on flexural stiffness of diagrid non-stiffened node based on four-spring assemblage model[J]. Engineering Structures,2019,198. [33]Li Huang,Shenhua Qian,Ting Li,C.Y. Jim,Cheng Jin,Liang Zhao,Dunmei Lin,Kankan Shang,Yongchuan Yang. Masonry walls as sieve of urban plant assemblages and refugia of native species in Chongqing, China[J]. Landscape and Urban Planning,2019,191. [34]C.I. Montalvo,R.L. Tomassini,R. Sostillo,E. Cerde?o,D.H. Verzi,G. Visconti,A. Folguera,G.I. Schmidt. A Chasicoan (late Miocene) vertebrate assemblage from Cerro Azul Formation, central Argentina. Geomorphological and biochronological considerations[J]. Journal of South American Earth Sciences,2019,95. [35]Hong Yue,Yanyan Zhang,Yanling He,Gehong Wei,Duntao Shu. Keystone taxa regulate microbial assemblage patterns and functional traits of different microbial aggregates in simultaneous anammox and denitrification (SAD) systems[J]. Bioresource Technology,2019,290. [36]Chanachok Chokwitthaya,Yimin Zhu,Robert Dibiano,Supratik Mukhopadhyay. Combining context-aware design-specific data and building performance models to improve building performance predictions during design[J]. Automation in Construction,2019,107. [37]Rosalía Aguilar-Medrano,John R. Durand,Víctor H. Cruz-Escalona,Peter B. Moyle. Fish functional groups in the San Francisco Estuary: Understanding new fish assemblages in a highly altered estuarine ecosystem[J]. Estuarine, Coastal and ShelfScience,2019,227. [38]A.O. Debrot,A. Hylkema,W. Vogelaar,W.F. Prud'homme van Reine,M.S. Engel,J.A. van Hateren,E.H. Meesters. Patterns of distribution and drivers of change in shallow seagrass and algal assemblages of a non-estuarine Southern Caribbean mangrovelagoon[J]. Aquatic Botany,2019,159. [39]Jip de Vries,Michiel H.S. Kraak,Ralf C.M. Verdonschot,PietF.M. Verdonschot. Quantifying cumulative stress acting on macroinvertebrate assemblages in lowland streams[J]. Science of the Total Environment,2019,694. [40]Fatemeh Shabani,Ali Nasrolahi,Martin Thiel. Assemblage of encrusting organisms on floating anthropogenic debris along the northern coast of the Persian Gulf[J]. EnvironmentalPollution,2019,254. [41]Peter R. Wilshusen. Environmental governance in motion: Practices of assemblage and the political performativity of economistic conservation[J]. World Development,2019,124. [42]Philipp J. Donaubauer,Leonhard Schmalhorst,Olaf Hinrichsen.2D flow fields in fixed-bed reactor design: a robust methodology for continuum models[J]. Chemical Engineering Science,2019,208. [43]J.A.G. Cooper,A.N. Green,H. Vital,F.P. Lima-Filho. Geomorphology and clast assemblages of intertidal beachrock: Implications for submerged shoreline preservation[J]. Geomorphology,2019,343. [44]Cristina Val-Peón,Isabel Expósito,María Soto,Francesc Burjachs. A taphonomic approach to the pollen assemblage from layer M of the Abric Romaní archaeological site (NE Iberian Peninsula)[J]. Review of Palaeobotany and Palynology,2019,270. [45]Ilse María Hernández-Romero,Luis Fabián Fuentes-Cortés,Rajib Mukherjee,Mahmoud M. El-Halwagi,Medardo Serna-González,FabricioNápoles-Rivera. Multi-scenario model for optimal design of seawater air-conditioning systems under demand uncertainty[J]. Journal of Cleaner Production,2019,238. [46]Sreejith Krishnan,Arun C. Emmanuel,Shashank Bishnoi. Hydration and phase assemblage of ternary cements with calcined clay and limestone[J]. Construction and Building Materials,2019,222. [47]Hongjun Li,Zhewei Zhou,Xinchen Qu,Yeping Xie,Xun Huang. Evaluation of DBA-L pressure vessel design method by 2D and 3D solid models[J]. Thin-Walled Structures,2019,144. [48]Shu Zheng,Daogang Lu,Qiong Cao,Yunlong Ding,Chao Liu. Contact model analysis on cladding designs against thermal shock for the lower head of central measuring shroud in a fast reactor[J]. Nuclear Engineering and Design,2019,352. [49]Sangjae Jeong,Jeryang Park,Yeong Min Kim,Man Ho Park,Jae Young Kim. Innovation of flux chamber network design for surface methane emission from landfills using spatial interpolationmodels[J]. Science of the Total Environment,2019,688. [50]James Heaton,Ajith Kumar Parlikad,Jennifer Schooling. Design and development of BIM models to support operations andmaintenance[J]. Computers in Industry,2019,111. [51]France Polette,Alexis Licht,Aude Cincotta,David J.Batten,Pauline Depuydt,Didier Néraudeau,Géraldine Garcia,Xavier Valentin. Palynological assemblage from the lower Cenomanian plant-bearing Lagerst?tte of Jaunay-Clan-Ormeau-Saint-Denis (Vienne, western France): Stratigraphic and paleoenvironmentalimplications[J]. Review of Palaeobotany and Palynology,2019,271. [52]Cristina Sousa Rocha,Paula Antunes,Paulo Partidário. Design for sustainability models: A multiperspective review[J]. Journal of Cleaner Production,2019,234. [53]Rosa J. Chilundo,Genito A. Maúre,Ur?nio S. Mahanjane. Dynamic mathematical model design of photovoltaic water pumping systems for horticultural crops irrigation: A guide to electrical energypotential assessment for increase access to electrical energy[J]. Journal of Cleaner Production,2019,238. [54]Edwin E. Dumalagan,Patrick C. Cabaitan,Tom C.L. Bridge,Kevin Thomas Go,Timothy Joseph R. Quimpo,Ronald Dionnie D.Olavides,Jeffrey C. Munar,Cesar L. Villanoy,Fernando P. Siringan. Spatial variability in benthic assemblage composition in shallow and upper mesophotic coral ecosystems in the Philippines[J]. Marine Environmental Research,2019,150. [55]Thibaut Wissocq,Sami Ghazouani,Solène Le Bourdiec. A methodology for designing thermodynamic energy conversion systems in industrial mass/heat integration problems based on MILP models[J]. Energy,2019,185. [56]Morteza Montazeri-Gh,Ali Rasti,Ali Jafari,Milad Ehteshami. Design and implementation of MPC for turbofan engine controlsystem[J]. Aerospace Science and Technology,2019,92. [57]Efstathia Gkioni,Roser Rius,Susanna Dodd,Carrol Gamble. A systematic review describes models for recruitment prediction at the design stage of a clinical trial[J]. Journal of Clinical Epidemiology,2019,115. [58]Jeehyun Kim,Hyunho Wi,Mi Joung,Sonjong Wang,Julien Hillairet. High field side LHCD launcher study for KSTAR[J]. Fusion Engineering and Design,2019,146. [59]Rui Zhu,Bin Duan,Chenghui Zhang,Sizhao Gong. Accuratelithium-ion battery modeling with inverse repeat binary sequence for electric vehicle applications[J]. Applied Energy,2019,251. [60]Artak E. Kostanyan,Zhanetta N. Galieva. Modeling of closed-loop recycling dual-mode counter-current chromatography based onnon-ideal recycling model[J]. Journal of Chromatography A,2019,1603. 模具设计外文参考文献三: [61]Xiaosong Su,Ling Zhang,Zhongbing Liu,Yongqiang Luo,Jinbu Lian,Yongwei Luo. A computational model of an improved cooling radiant ceiling panel system for optimization and design[J].Building and Environment,2019,163. [62]Lu-Kai Song,Guang-Chen Bai,Cheng-Wei Fei. Multi-failure probabilistic design for turbine bladed disks using neural network regression with distributed collaborative strategy[J]. Aerospace Science and Technology,2019,92. [63]D. Giagopoulos,A. Arailopoulos,I. Chatziparasidis,N.S. Sapidis. Optimum design of large-scale systems considering materialnonlinearities and uncertainties[J]. Computers andStructures,2019,223. [64]Pavel Pereslavtsev,Francisco A. Hernández,Guangming Zhou,Lei Lu,Christian Wegmann,Ulrich Fischer. Nuclear analyses of solid breeder blanket options for DEMO: Status, challenges and outlook[J]. Fusion Engineering and Design,2019,146. [65]Jorge A. Sefair,Mónica Espinosa,Eduardo Behrentz,Andrés L. Medaglia. Optimization model for urban air quality policy design: A case study in Latin America[J]. Computers, Environment and Urban Systems,2019,78. [66]Abdelbaset S. El-Sorogy,Talal Alharbi,Sattam Almadani,Mansour Al-Hashim. Molluscan assemblage as pollution indicators in Al-Khobar coastal plain, Arabian Gulf, Saudi Arabia[J]. Journal of African Earth Sciences,2019,158. [67]Magalí Pérez Flores,Guillermo Martínez Pastur,Juan Manuel Cellini,María Vanessa Lencinas. Recovery of understory assemblage along 50 years after shelterwood cut harvesting in Nothofaguspumilio Southern Patagonian forests[J]. Forest Ecology and Management,2019,450. [68]B. Taverna,A. Casonato,F. Bezzo,F. Galvanin. A framework for the optimal design of a minimum set of clinical trials to characterize von Willebrand disease[J]. Computer Methods and Programs in Biomedicine,2019,179. [69]Guangbo Hao,Xiuyun He,Shorya Awtar. Design and analytical model of a compact flexure mechanism for translational motion[J]. Mechanism and Machine Theory,2019,142. [70]Matías Reolid,Philip Copestake,Ben Johnson. Foraminiferal assemblages, extinctions and appearances associated with the Early Toarcian Oceanic Anoxic Event in the Llanbedr (Mochras Farm) Borehole, Cardigan Bay Basin, United Kingdom[J]. Palaeogeography, Palaeoclimatology, Palaeoecology,2019,532. [71]Nezam Bozorgzadeh,Richard J. Bathurst. Bayesian model checking, comparison and selection with emphasis on outlierdetection for geotechnical reliability-based design[J]. Computers and Geotechnics,2019,116. [72]Jun Li,Zhun (Jerry) Yu,Fariborz Haghighat,Guoqiang Zhang. Development and improvement of occupant behavior models towards realistic building performance simulation: A review[J]. Sustainable Cities and Society,2019,50. [73]F. Johansson,L.M. Bini,P. Coiffard,R. Svanb?ck,J. Wester,J. Heino. Environmental variables drive differences in the betadiversity of dragonfly assemblages among urban stormwater ponds[J]. Ecological Indicators,2019,106. [74]Lida Xing,Martin G. Lockley,Hendrik Klein,Liang Qiu,Chunyong Chou,Donghao Wang,W. Scott Persons. A Lower Cretaceous dinosaurtrack assemblage from the Taoqihe Formation in Central Heilongjiang, China[J]. Palaeogeography, Palaeoclimatology,Palaeoecology,2019,532. [75]Peipei Chen,Yi Wu,Lele Zou. Distributive PV trading market in China: A design of multi-agent-based model and its forecastanalysis[J]. Energy,2019,185. [76]Qi An,Sébastien Le Beux,Ian O'Connor,Jacques-Olivier Klein. A comprehensive compact model for the design of all-spin-logic based circuits[J]. Microelectronics Journal,2019,92. [77]Florian Zwicke,Stefanie Elgeti. Inverse design based on nonlinear thermoelastic material models applied to injectionmolding[J]. Finite Elements in Analysis & Design,2019,165. [78]Jean-Paul Martin,Qingguo Li. Design, model, and performance evaluation of a biomechanical energy harvesting backpack[J]. Mechanical Systems and Signal Processing,2019,134. [79]Andrés Solórzano,Alfonso Encinas,René Bobe,Reyes Maximiliano,Gabriel Carrasco. The Early to late Middle Miocene mammalian assemblages from the Cura-Mallín Formation, at Lonquimay, southern Central Andes, Chile (~38°S): Biogeographical and paleoenvironmental implications[J]. Journal of South American Earth Sciences,2019,96. [80]Mengyao Yang,Kangle Lu,Darold P. Batzer,Haitao Wu. Freshwater release into estuarine wetlands changes the structure of benthic invertebrate assemblages: A case study from the Yellow RiverDelta[J]. Science of the Total Environment,2019,687. [81]Brenda Konar,Timothy James Mitchell,Katrin Iken,Heather Coletti,Thomas Dean,Daniel Esler,Mandy Lindeberg,BenjaminPister,Benjamin Weitzman. Wasting disease and static environmental variables drive sea star assemblages in the Northern Gulf ofAlaska[J]. Journal of Experimental Marine Biology andEcology,2019,520. [82]Markéta Chroustová,Radovan Pipík. Late Turonian ostracod assemblages record a shift from mesotrophic to oligtrophic hemipelagic deposits in the Bohemian Cretaceous Basin (Czech Republic)[J]. Cretaceous Research,2019,104. [83]Xiaodong Wang,Shu Li,Megan Price,Yi Lei,Bo Wu,Kan Liu,Zhaobin Song. Longitudinal and seasonal patterns of fish assemblagestructure in the Zhougong River, Sichuan Province, southwestChina[J]. Ecological Indicators,2019,107. [84]F. Pezzimenti,H. Bencherif,A. Yousfi,L. Dehimi. Current-voltage analytical model and multiobjective optimization of designof a short channel gate-all-around-junctionless MOSFET[J]. Solid State Electronics,2019,161. [85]Xin Chen,Haofei Zhou,Yumeng Li. Effective design space exploration of gradient nanostructured materials using active learning based surrogate models[J]. Materials & Design,2019,183. [86]Hong-Zhou Deng,Chao Li,Xue-Qi Song,Fang Li,Peng-Cheng Fu. Tensile resistance and design model of an external double-layered flange connection[J]. Journal of Constructional SteelResearch,2019,161. [87]Ali Shahmohammadi,Kimberley B. McAuley. Sequential model-based A- and V-optimal design of experiments for building fundamental models of pharmaceutical production processes[J]. Computers and Chemical Engineering,2019,129. [88]Estefania Calparsoro,Uxue Sanchez-Garmendia,Gorka Arana,Maite Maguregui,Javier G. I?a?ez. An archaeometric approach to themajolica pottery from alcazar of Nájera archaeological site[J]. Heritage Science,2019,7(1). [89]Arnob Kumar Mondal,Sankar Bose. Evolution of fluid from the ultrahigh temperature lower crust to shallower levels: Constraints from silicate–oxide–sulphide–sulphate assemblages of maficgranulites of the Eastern Ghats Belt, India[J]. Journal of Earth System Science,2019,128(7). [90]Justin Larner,?ke Walldius. The Platform Review Alliance Board: designing an organizational model to bring together producers and consumers in the review and commissioning of platformsoftware[J]. Journal of Organization Design,2019,8(1). 模具设计外文参考文献四: [91]Hyojeong Lee,HeeJae Jin. Conceptual design framework as a model for wheelchair users’ sportswear comfort[J]. Fashion and Textiles,2019,6(1). [92]Renato Bolson Dala-Corte,Adriano Sanches Melo,Fernando Gertum Becker,Fabrício Barreto Teresa. Testing the native invasion hypothesis to explain anthropogenic influence on stream fish assemblages[J]. Aquatic Sciences,2019,81(4). [93]Panayiotis Bobotas,Maria Kateri. Optimal Designs for Step-Stress Models Under Interval Censoring[J]. Journal of Statistical Theory and Practice,2019,13(4). [94]Francisco Marcellán,Mohd Shadab,Saima Jabee. Some New Identities Involving Sheffer–Appell Polynomial Sequences via Matrix Approach[J]. Mediterranean Journal of Mathematics,2019,16(5). [95]Abiola O. Oladapo,Diane Ito,Christopher Hibbard,Stephanie E. Bean,Robert N. Krupnick,Bruce M. Ewenstein. Patient Experience with Congenital (Hereditary) Thrombotic Thrombocytopenic Purpura: A Conceptual Framework of Symptoms and Impacts[J]. The Patient - Patient-Centered Outcomes Research,2019,12(5). [96]Hilary Weingarden,Suraj S. Mothi,Ilana Ladis,Susanne Hoeppner,Hannah E. Reese,Kiara Timpano,Jedidiah Siev,Jessica Rasmussen,Jennifer Ragan,Darin D. Dougherty,Sabine Wilhelm. d -Cycloserine-Augmented Behavior Therapy for Body Dysmorphic Disorder: A Preliminary Efficacy Trial[J]. Cognitive Therapy andResearch,2019,43(5). [97]Sarah G. Mitchell,Bojana Pencheva,Christopher C. Porter. Germline Genetics and Childhood Cancer: Emerging Cancer Predisposition Syndromes and Psychosocial Impacts[J]. Current Oncology Reports,2019,21(10). [98]Nitin Salunkhe,Namdeo Jadhav,Harinath More,Prafulla Choudhari. Sericin Inhibits Devitrification of Amorphous Drugs[J]. AAPS PharmSciTech,2019,20(7). [99]Zbigniew Grobelny,Sylwia Golba,Justyna Jurek-Suliga. Ring-opening polymerization of β-butyrolactone in the presence of alkali metal salts: investigation of initiation course and determination of polymers structure by MALDI-TOF mass spectrometry[J]. Polymer Bulletin,2019,76(10). [100]Yue Yang,Haitao Dai,Feng Yang,Yating Zhang,Dan Luo,Xiaoli Zhang,Kai Wang,Xiao Wei Sun,Jianquan Yao. All-Perovskite Photodetector with Fast Response[J]. Nanoscale ResearchLetters,2019,14(1). [101]Ding Wang,Jiexin Yin,Xin Chen,Changgui Jia,Fushan Wei. On the use of calibration emitters for TDOA source localization in the presence of synchronization clock bias and sensor locationerrors[J]. EURASIP Journal on Advances in SignalProcessing,2019,2019(1). [102]Tembo Nakamoto,Abhijit Chakraborty,Yuichi Ikeda. Identification of key companies for international profit shifting in the Global Ownership Network[J]. Applied Network Science,2019,4(1). [103]K. Prathapan,K. P. Anjali,R. K. Biju. Existence of 15-21 N, 17-23 O, and 19-25 F Neutron Halo Nuclei via Cluster Decay Processin the Superheavy Region[J]. Brazilian Journal ofPhysics,2019,49(5). [104]Lun Song,Jing Wu,Jing Du,Nan Li,Kun Wang,Peng Wang. Comparison of Two Methods to Assess the Size Structure of Phytoplankton Community Assemblages, in Liaodong Bay, China[J]. Journal of Ocean University of China,2019,18(5). [105]Mezzoudj Saliha,Behloul Ali,Seghir Rachid. Towards large-scale face-based race classification on spark framework[J]. Multimedia Tools and Applications,2019,78(18). [106]Yue Hong,Zhang Yanyan,He Yanling,Wei Gehong,Shu Duntao. Keystone taxa regulate microbial assemblage patterns and functional traits of different microbial aggregates in simultaneous anammox and denitrification (SAD) systems.[J]. Bioresource technology,2019,290. [107]Yang Mengyao,Lu Kangle,Batzer Darold P,Wu Haitao. Freshwater release into estuarine wetlands changes the structure of benthic invertebrate assemblages: A case study from the Yellow RiverDelta.[J]. The Science of the total environment,2019,687. [108]Fierro Pablo,Valdovinos Claudio,Arismendi Ivan,Díaz Gustavo,Jara-Flores Alfonso,Habit Evelyn,Vargas-Chacoff Luis. Examining the influence of human stressors on benthic algae, macroinvertebrate, and fish assemblages in Mediterranean streams of Chile.[J]. The Science of the total environment,2019,686. [109]Jeong Sangjae,Park Jeryang,Kim Yeong Min,Park Man Ho,Kim Jae Young. Innovation of flux chamber network design for surface methane emission from landfills using spatial interpolation models.[J]. The Science of the total environment,2019,688. [110]Alhorn K,Schorning K,Dette H. Optimal designs forfrequentist model averaging.[J]. Biometrika,2019,106(3). [111]Walker Donald M,Leys Jacob E,Grisnik Matthew,Grajal-Puche Alejandro,Murray Christopher M,Allender Matthew C. Variability in snake skin microbial assemblages across spatial scales and disease states.[J]. The ISME journal,2019,13(9). [112]Wang Xia,Wen Dongmei,Wang Weijia,Suo Minghuan,Hu Ting. Application of biological variation and six sigma models to evaluate analytical quality of six HbA<sub>1c</sub> analyzers and design quality control strategy.[J]. Artificial cells, nanomedicine, and biotechnology,2019,47(1). [113]Zhong Fei,Wu Juan,Dai Yanran,Xiang Dongfang,Deng Zifa,Cheng Shuiping. Responses of water quality and phytoplankton assemblagesto remediation projects in two hypereutrophic tributaries of Chaohu Lake.[J]. Journal of environmental management,2019,248. [114]Nina Polchaninova,Galina Savchenko,Vladimir Ronkin,Aleksandr Drogvalenko,Alexandr Putchkov. Summer fire in steppe habitats: long-term effects on vegetation and autumnal assemblages of cursorial arthropods[J]. Hacquetia,2019,18(2). [115]Yang Yu,Mengfen Shen,C. Hsein Juang. Assessing Initial Stiffness Models for Laterally Loaded Piles in Undrained Clay: Robust Design Perspective[J]. Journal of Geotechnical and Geoenvironmental Engineering,2019,145(10). [116]Fernando E. Garcia,Jonathan D. Bray. Discrete-Element Analysis of Influence of Granular Soil Density on Earthquake Surface Fault Rupture Interaction with Rigid Foundations[J]. Journal of Geotechnical and Geoenvironmental Engineering,2019,145(11). [117]Wei Li,Spyros Konstantopoulos. Power Computations for Polynomial Change Models in Block-Randomized Designs[J]. The Journal of Experimental Education,2019,87(4). [118]Jo?o Barata,Paulo Rupino da Cunha. The Viable Smart Product Model: Designing Products that Undergo DisruptiveTransformations[J]. Cybernetics and Systems,2019,50(7). [119]Price-Robertson,Duff. Family assemblages[J]. Social & Cultural Geography,2019,20(8). [120]Hamaidia Walid,Zebbiche Toufik,Sellam Mohamed,Allali Abderrazak. Performance improvement of supersonic nozzles design using a high-temperature model[J]. Proceedings of the Institution of Mechanical Engineers,2019,233(13). 以上就是关于模具设计外文参考文献的分享,希望对你有所帮助。
注塑模具中英文对照外文翻译文献
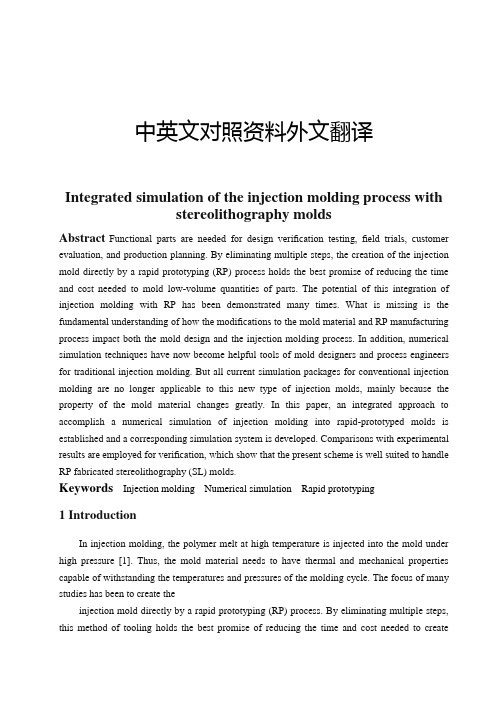
中英文对照资料外文翻译Integrated simulation of the injection molding process withstereolithography moldsAbstract Functional parts are needed for design verification testing, field trials, customer evaluation, and production planning. By eliminating multiple steps, the creation of the injection mold directly by a rapid prototyping (RP) process holds the best promise of reducing the time and cost needed to mold low-volume quantities of parts. The potential of this integration of injection molding with RP has been demonstrated many times. What is missing is the fundamental understanding of how the modifications to the mold material and RP manufacturing process impact both the mold design and the injection molding process. In addition, numerical simulation techniques have now become helpful tools of mold designers and process engineers for traditional injection molding. But all current simulation packages for conventional injection molding are no longer applicable to this new type of injection molds, mainly because the property of the mold material changes greatly. In this paper, an integrated approach to accomplish a numerical simulation of injection molding into rapid-prototyped molds is established and a corresponding simulation system is developed. Comparisons with experimental results are employed for verification, which show that the present scheme is well suited to handle RP fabricated stereolithography (SL) molds.Keywords Injection molding Numerical simulation Rapid prototyping1 IntroductionIn injection molding, the polymer melt at high temperature is injected into the mold under high pressure [1]. Thus, the mold material needs to have thermal and mechanical properties capable of withstanding the temperatures and pressures of the molding cycle. The focus of many studies has been to create theinjection mold directly by a rapid prototyping (RP) process. By eliminating multiple steps, this method of tooling holds the best promise of reducing the time and cost needed to createlow-volume quantities of parts in a production material. The potential of integrating injection molding with RP technologies has been demonstrated many times. The properties of RP molds are very different from those of traditional metal molds. The key differences are the properties of thermal conductivity and elastic modulus (rigidity). For example, the polymers used in RP-fabricated stereolithography (SL) molds have a thermal conductivity that is less than one thousandth that of an aluminum tool. In using RP technologies to create molds, the entire mold design and injection-molding process parameters need to be modified and optimized from traditional methodologies due to the completely different tool material. However, there is still not a fundamental understanding of how the modifications to the mold tooling method and material impact both the mold design and the injection molding process parameters. One cannot obtain reasonable results by simply changing a few material properties in current models. Also, using traditional approaches when making actual parts may be generating sub-optimal results. So there is a dire need to study the interaction between the rapid tooling (RT) process and material and injection molding, so as to establish the mold design criteria and techniques for an RT-oriented injection molding process.In addition, computer simulation is an effective approach for predicting the quality of molded parts. Commercially available simulation packages of the traditional injection molding process have now become routine tools of the mold designer and process engineer [2]. Unfortunately, current simulation programs for conventional injection molding are no longer applicable to RP molds, because of the dramatically dissimilar tool material. For instance, in using the existing simulation software with aluminum and SL molds and comparing with experimental results, though the simulation values of part distortion are reasonable for the aluminum mold, results are unacceptable, with the error exceeding 50%. The distortion during injection molding is due to shrinkage and warpage of the plastic part, as well as the mold. For ordinarily molds, the main factor is the shrinkage and warpage of the plastic part, which is modeled accurately in current simulations. But for RP molds, the distortion of the mold has potentially more influence, which have been neglected in current models. For instance, [3] used a simple three-step simulation process to consider the mold distortion, which had too much deviation.In this paper, based on the above analysis, a new simulation system for RP molds is developed. The proposed system focuses on predicting part distortion, which is dominating defect in RP-molded parts. The developed simulation can be applied as an evaluation tool for RP mold design and process opti mization. Our simulation system is verified by an experimental example.Although many materials are available for use in RP technologies, we concentrate on usingstereolithography (SL), the original RP technology, to create polymer molds. The SL process uses photopolymer and laser energy to build a part layer by layer. Using SL takes advantage of both the commercial dominance of SL in the RP industry and the subsequent expertise base that has been developed for creating accurate, high-quality parts. Until recently, SL was primarily used to create physical models for visual inspection and form-fit studies with very limited func-tional applications. However, the newer generation stereolithographic photopolymers have improved dimensional, mechanical and thermal properties making it possible to use them for actual functional molds.2 Integrated simulation of the molding process2.1 MethodologyIn order to simulate the use of an SL mold in the injection molding process, an iterative method is proposed. Different software modules have been developed and used to accomplish this task. The main assumption is that temperature and load boundary conditions cause significant distortions in the SL mold. The simulation steps are as follows:1The part geo metry is modeled as a solid model, which is translated to a file readable by the flow analysis package.2Simulate the mold-filling process of the melt into a pho topolymer mold, which will output the resulting temperature and pressure profiles.3Structural analysis is then performed on the photopolymer mold model using the thermal and load boundary conditions obtained from the previous step, which calculates the distortion that the mold undergo during the injection process.4If the distortion of the mold converges, move to the next step. Otherwise, the distorted mold cavity is then modeled (changes in the dimensions of the cavity after distortion), and returns to the second step to simulate the melt injection into the distorted mold.5The shrinkage and warpage simulation of the injection molded part is then applied, which calculates the final distor tions of the molded part.In above simulation flow, there are three basic simulation mod ules.2. 2 Filling simulation of the melt2.2.1 Mathematical modelingIn order to simulate the use of an SL mold in the injection molding process, an iterativemethod is proposed. Different software modules have been developed and used to accomplish this task. The main assumption is that temperature and load boundary conditions cause significant distortions in the SL mold. The simulation steps are as follows:1. The part geometry is modeled as a solid model, which is translated to a file readable by the flow analysis package.2. Simulate the mold-filling process of the melt into a photopolymer mold, which will output the resulting temperature and pressure profiles.3. Structural analysis is then performed on the photopolymer mold model using the thermal and load boundary conditions obtained from the previous step, which calculates the distortion that the mold undergo during the injection process.4. If the distortion of the mold converges, move to the next step. Otherwise, the distorted mold cavity is then modeled (changes in the dimensions of the cavity after distortion), and returns to the second step to simulate the melt injection into the distorted mold.5. The shrinkage and warpage simulation of the injection molded part is then applied, which calculates the final distortions of the molded part.In above simulation flow, there are three basic simulation modules.2.2 Filling simulation of the melt2.2.1 Mathematical modelingComputer simulation techniques have had success in predicting filling behavior in extremely complicated geometries. However, most of the current numerical implementation is based on a hybrid finite-element/finite-difference solution with the middleplane model. The application process of simulation packages based on this model is illustrated in Fig. 2-1. However, unlike the surface/solid model in mold-design CAD systems, the so-called middle-plane (as shown in Fig. 2-1b) is an imaginary arbitrary planar geometry at the middle of the cavity in the gap-wise direction, which should bring about great inconvenience in applications. For example, surface models are commonly used in current RP systems (generally STL file format), so secondary modeling is unavoidable when using simulation packages because the models in the RP and simulation systems are different. Considering these defects, the surface model of the cavity is introduced as datum planes in the simulation, instead of the middle-plane.According to the previous investigations [4–6], fillinggoverning equations for the flow and temperature field can be written as:where x, y are the planar coordinates in the middle-plane, and z is the gap-wise coordinate; u, v,w are the velocity components in the x, y, z directions; u, v are the average whole-gap thicknesses; and η, ρ,CP (T), K(T) represent viscosity, density, specific heat and thermal conductivity of polymer melt, respectively.Fig.2-1 a–d. Schematic procedure of the simulation with middle-plane model. a The 3-D surface model b The middle-plane model c The meshed middle-plane model d The display of the simulation result In addition, boundary conditions in the gap-wise direction can be defined as:where TW is the constant wall temperature (shown in Fig. 2a).Combining Eqs. 1–4 with Eqs. 5–6, it follows that the distributions of the u, v, T, P at z coordinates should be symmetrical, with the mirror axis being z = 0, and consequently the u, v averaged in half-gap thickness is equal to that averaged in wholegap thickness. Based on this characteristic, we can divide the whole cavity into two equal parts in the gap-wise direction, as described by Part I and Part II in Fig. 2b. At the same time, triangular finite elements are generated in the surface(s) of the cavity (at z = 0 in Fig. 2b), instead of the middle-plane (at z = 0 in Fig. 2a). Accordingly, finite-difference increments in the gapwise direction are employed only in the inside of the surface(s) (wall to middle/center-line), which, in Fig. 2b, means from z = 0 to z = b. This is single-sided instead of two-sided with respect to the middle-plane (i.e. from the middle-line to two walls). In addition, the coordinate system is changed from Fig. 2a to Fig. 2b to alter the finite-element/finite-difference scheme, as shown in Fig. 2b. With the above adjustment, governing equations are still Eqs. 1–4. However, the original boundary conditions inthe gapwise direction are rewritten as:Meanwhile, additional boundary conditions must be employed at z = b in order to keep the flows at the juncture of the two parts at the same section coordinate [7]:where subscripts I, II represent the parameters of Part I and Part II, respectively, and Cm-I and Cm-II indicate the moving free melt-fronts of the surfaces of the divided two parts in the filling stage.It should be noted that, unlike conditions Eqs. 7 and 8, ensuring conditions Eqs. 9 and 10 are upheld in numerical implementations becomes more difficult due to the following reasons:1. The surfaces at the same section have been meshed respectively, which leads to a distinctive pattern of finite elements at the same section. Thus, an interpolation operation should be employed for u, v, T, P during the comparison between the two parts at the juncture.2. Because the two parts have respective flow fields with respect to the nodes at point A and point C (as shown in Fig. 2b) at the same section, it is possible to have either both filled or one filled (and one empty). These two cases should be handled separately, averaging the operation for the former, whereas assigning operation for the latter.3. It follows that a small difference between the melt-fronts is permissible. That allowance can be implemented by time allowance control or preferable location allowance control of the melt-front nodes.4. The boundaries of the flow field expand by each melt-front advancement, so it is necessary to check the condition Eq. 10 after each change in the melt-front.5. In view of above-mentioned analysis, the physical parameters at the nodes of the same section should be compared and adjusted, so the information describing finite elements of the same section should be prepared before simulation, that is, the matching operation among the elements should be preformed.Fig. 2a,b. Illustrative of boundary conditions in the gap-wise direction a of the middle-plane model b of thesurface model2.2.2 Numerical implementationPressure field. In modeling viscosity η, which is a function of shear rate, temperature and pressure of melt, the shear-thinning behavior can be well represented by a cross-type model such as:where n corresponds to the power-law index, and τ∗ characterizes the shear stress level of the transition region between the Newtonian and power-law asymptotic limits. In terms of an Arrhenius-type temperature sensitivity and exponential pressure dependence, η0(T, P) can be represented with reasonable accuracy as follows:Equations 11 and 12 constitute a five-constant (n, τ∗, B, Tb, β) representation for viscosity. The shear rate for viscosity calculation is obtained by:Based on the above, we can infer the following filling pressure equation from the governing Eqs. 1–4:where S is calculated by S = b0/(b−z)2η d z. Applying the Galerkin method, the pressure finite-element equation is deduced as:where l_ traverses all elements, including node N, and where I and j represent the local node number in element l_ corresponding to the node number N and N_ in the whole, respectively. The D(l_) ij is calculated as follows:where A(l_) represents triangular finite elements, and L(l_) i is the pressure trial function in finite elements.Temperature field. To determine the temperature profile across the gap, each triangular finite element at the surface is further divided into NZ layers for the finite-difference grid.The left item of the energy equation (Eq. 4) can be expressed as:where TN, j,t represents the temperature of the j layer of node N at time t.The heat conduction item is calculated by:where l traverses all elements, including node N, and i and j represent the local node number in element l corresponding to the node number N and N_ in the whole, respectively.The heat convection item is calculated by:For viscous heat, it follows that:Substituting Eqs. 17–20 into the energy equation (Eq. 4), the temperature equation becomes:2.3 Structural analysis of the moldThe purpose of structural analysis is to predict the deformation occurring in the photopolymer mold due to the thermal and mechanical loads of the filling process. This model is based on a three-dimensional thermoelastic boundary element method (BEM). The BEM is ideally suited for this application because only the deformation of the mold surfaces is of interest. Moreover, the BEM has an advantage over other techniques in that computing effort is not wasted on calculating deformation within the mold.The stresses resulting from the process loads are well within the elastic range of the mold material. Therefore, the mold deformation model is based on a thermoelastic formulation. The thermal and mechanical properties of the mold are assumed to be isotropic and temperature independent.Although the process is cyclic, time-averaged values of temperature and heat flux are used for calculating the mold deformation. Typically, transient temperature variations within a mold have been restricted to regions local to the cavity surface and the nozzle tip [8]. The transients decay sharply with distance from the cavity surface and generally little variation is observed beyond distances as small as 2.5 mm. This suggests that the contribution from the transients to the deformation at the mold block interface is small, and therefore it is reasonable to neglect the transient effects. The steady state temperature field satisfies Laplace’s equation 2T = 0 and the time-averaged boundary conditions. The boundary conditions on the mold surfaces are described in detail by Tang et al. [9]. As for the mechanical boundary conditions, the cavity surface is subjected to the melt pressure, the surfaces of the mold connected to the worktable are fixed in space, and other external surfaces are assumed to be stress free.The derivation of the thermoelastic boundary integral formulation is well known [10]. It is given by:where uk, pk and T are the displacement, traction and temperature,α, ν represent the thermal expansion coefficient and Poisson’s ratio of the material, and r = |y−x|. clk(x) is the surfacecoefficient which depends on the local geometry at x, the orientation of the coordinate frame and Poisson’s ratio for the domain [11]. The fundamental displacement ˜ulk at a point y in the xk direction, in a three-dimensional infinite isotropic elastic domain, results from a unit load concentrated at a point x acting in the xl direction and is of the form:where δlk is the Kronecker delta function and μ is the shear modulus of the mold material.The fundamental traction ˜plk , measured at the point y on a surface with unit normal n, is:Discretizing the surface of the mold into a total of N elements transforms Eq. 22 to:where Γn refers to the n th surface element on the domain.Substituting the appropriate linear shape functions into Eq. 25, the linear boundary element formulation for the mold deformation model is obtained. The equation is applied at each node on the discretized mold surface, thus giving a system of 3N linear equations, where N is the total number of nodes. Each node has eight associated quantities: three components of displacement, three components of traction, a temperature and a heat flux. The steady state thermal model supplies temperature and flux values as known quantities for each node, and of the remaining six quantities, three must be specified. Moreover, the displacement values specified at a certain number of nodes must eliminate the possibility of a rigid-body motion or rigid-body rotation to ensure a non-singular system of equations. The resulting system of equations is assembled into a integrated matrix, which is solved with an iterative solver.2.4 Shrinkage and warpage simulation of the molded partInternal stresses in injection-molded components are the principal cause of shrinkage and warpage. These residual stresses are mainly frozen-in thermal stresses due to inhomogeneous cooling, when surface layers stiffen sooner than the core region, as in free quenching. Based onthe assumption of the linear thermo-elastic and linear thermo-viscoelastic compressible behavior of the polymeric materials, shrinkage and warpage are obtained implicitly using displacement formulations, and the governing equations can be solved numerically using a finite element method.With the basic assumptions of injection molding [12], the components of stress and strain are given by:The deviatoric components of stress and strain, respectively, are given byUsing a similar approach developed by Lee and Rogers [13] for predicting the residual stresses in the tempering of glass, an integral form of the viscoelastic constitutive relationships is used, and the in-plane stresses can be related to the strains by the following equation:Where G1 is the relaxation shear modulus of the material. The dilatational stresses can be related to the strain as follows:Where K is the relaxation bulk modulus of the material, and the definition of α and Θ is:If α(t) = α0, applying Eq. 27 to Eq. 29 results in:Similarly, applying Eq. 31 to Eq. 28 and eliminating strain εxx(z, t) results in:Employing a Laplace transform to Eq. 32, the auxiliary modulus R(ξ) is given by:Using the above constitutive equation (Eq. 33) and simplified forms of the stresses and strains in the mold, the formulation of the residual stress of the injection molded part during the cooling stage is obtain by:Equation 34 can be solved through the application of trapezoidal quadrature. Due to the rapid initial change in the material time, a quasi-numerical procedure is employed for evaluating the integral item. The auxiliary modulus is evaluated numerically by the trapezoidal rule.For warpage analysis, nodal displacements and curvatures for shell elements are expressed as:where [k] is the element stiffness matrix, [Be] is the derivative operator matrix, {d} is the displacements, and {re} is the element load vector which can be evaluated by:The use of a full three-dimensional FEM analysis can achieve accurate warpage results, however, it is cumbersome when the shape of the part is very complicated. In this paper, a twodimensional FEM method, based on shell theory, was used because most injection-molded parts have a sheet-like geometry in which the thickness is much smaller than the other dimensions of the part. Therefore, the part can be regarded as an assembly of flat elements to predict warpage. Each three-node shell element is a combination of a constant strain triangular element (CST) and a discrete Kirchhoff triangular element (DKT), as shown in Fig. 3. Thus, the warpage can be separated into plane-stretching deformation of the CST and plate-bending deformation of the DKT, and correspondingly, the element stiffness matrix to describe warpage can also be divided into the stretching-stiffness matrix and bending-stiffness matrix.Fig. 3a–c. Deformation decomposition of shell element in the local coordinate system. a In-plane stretchingelement b Plate-bending element c Shell element3 Experimental validationTo assess the usefulness of the proposed model and developed program, verification is important. The distortions obtained from the simulation model are compared to the ones from SL injection molding experiments whose data is presented in the literature [8]. A common injection molded part with the dimensions of 36×36×6 mm is considered in the experiment, as shown in Fig. 4. The thickness dimensions of the thin walls and rib are both 1.5 mm; and polypropylene was used as the injection material. The injection machine was a production level ARGURY Hydronica 320-210-750 with the following process parameters: a melt temperature of 250 ◦C; an ambient temperature of 30 ◦C; an injection pressure of 13.79 MPa; an injection time of 3 s; and a cooling time of 48 s. The SL material used, Dupont SOMOSTM 6110 resin, has the ability to resist temperatures of up to 300 ◦C temperatures. As mentioned above, thermal conductivity of the mold is a major factor that differentiates between an SL and a traditional mold. Poor heat transfer in the mold would produce a non-uniform temperature distribution, thus causing warpage that distorts the completed parts. For an SL mold, a longer cycle time would be expected. The method of using a thin shell SL mold backed with a higher thermal conductivity metal (aluminum) was selected to increase thermal conductivity of the SL mold.Fig. 4. Experimental cavity modelFig. 5. A comparison of the distortion variation in the X direction for different thermal conductivity; where “Experimental”, “present”, “three-step”, and “conventional” mean the results of the experimental, the presented simulation, the three-step simulation process and the conventional injection molding simulation, respectively.Fig. 6. Comparison of the distortion variation in the Y direction for different thermal conductivitiesFig. 7. Comparison of the distortion variation in the Z direction for different thermal conductivitiesFig. 8. Comparison of the twist variation for different thermal conductivities For this part, distortion includes the displacements in three directions and the twist (the difference in angle between two initially parallel edges). The validation results are shown in Fig.5 to Fig. 8. These figures also include the distortion values predicted by conventional injection molding simulation and the three-step model reported in [3].4 ConclusionsIn this paper, an integrated model to accomplish the numerical simulation of injection molding into rapid-prototyped molds is established and a corresponding simulation system is developed. For verification, an experiment is also carried out with an RPfabricated SL mold.It is seen that a conventional simulation using current injection molding software breaks down for a photopolymer mold. It is assumed that this is due to the distortion in the mold caused by the temperature and load conditions of injection. The three-step approach also has much deviation. The developed model gives results closer to experimental.Improvement in thermal conductivity of the photopolymer significantly increases part quality. Since the effect of temperature seems to be more dominant than that of pressure (load), an improvement in the thermal conductivity of the photopolymer can improve the part quality significantly.Rapid Prototyping (RP) is a technology makes it possible to manufacture prototypes quickly and inexpensively, regardless of their complexity. Rap id Tooling (RT) is the next step in RP’s steady progress and much work is being done to obtain more accurate tools to define the parameters of the process. Existing simulation tools can not provide the researcher with a useful means of studying relative changes. An integrated model, such as the one presented in this paper, is necessary to obtain accurate predictions of the actual quality of final parts. In the future, we expect to see this work expanded to develop simulations program for injection into RP molds manufactured by other RT processes.References1. Wang KK (1980) System approach to injection molding process. Polym-Plast Technol Eng 14(1):75–93.2. Shelesh-Nezhad K, Siores E (1997) Intelligent system for plastic injection molding process design. J Mater Process Technol 63(1–3):458–462.3. Aluru R, Keefe M, Advani S (2001) Simulation of injection molding into rapid-prototyped molds. Rapid Prototyping J 7(1):42–51.4. Shen SF (1984) Simulation of polymeric flows in the injection molding process. Int J Numer Methods Fluids 4(2):171–184.5. Agassant JF, Alles H, Philipon S, Vincent M (1988) Experimental and theoretical study of the injection molding of thermoplastic materials. Polym Eng Sci 28(7):460–468.6. Chiang HH, Hieber CA, Wang KK (1991) A unified simulation of the filling and post-filling stages in injection molding. Part I: formulation. Polym Eng Sci 31(2):116–124.7. Zhou H, Li D (2001) A numerical simulation of the filling stage in injection molding based on a surface model. Adv Polym Technol 20(2):125–131.8. Himasekhar K, Lottey J, Wang KK (1992) CAE of mold cooling in injection molding using a three-dimensional numerical simulation. J EngInd Trans ASME 114(2):213–221.9. Tang LQ, Pochiraju K, Chassapis C, Manoochehri S (1998) Computeraided optimization approach for the design of injection mold cooling systems. J Mech Des, Trans ASME 120(2):165–174.10. Rizzo FJ, Shippy DJ (1977) An advanced boundary integral equation method for three-dimensional thermoelasticity. Int J Numer Methods Eng 11:1753–1768.11. Hartmann F (1980) Computing the C-matrix in non-smooth boundary points. In: New developments in boundary element methods, CML Publications, Southampton, pp 367–379.12. Chen X, Lama YC, Li DQ (2000) Analysis of thermal residual stress in plastic injection molding. J Mater Process Technol 101(1):275–280.13. Lee EH, Rogers TG (1960) Solution of viscoelastic stress analysis problems using measured creep or relaxation function. J Appl Mech 30(1):127–134.14. Li Y (1997) Studies in direct tooling using stereolithography. Dissertation, University of Delaware, Newark, DE..。
塑料模具外文文献
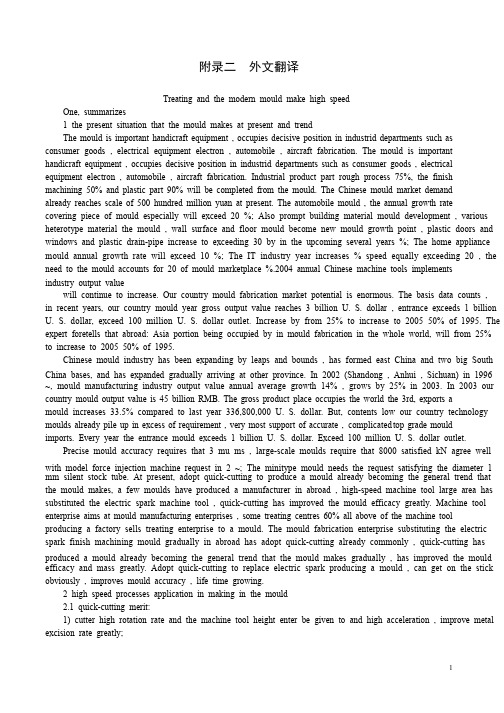
附录二附录二 外文翻译外文翻译Treating and the modern mould make high speed One, summarizes 1 the present situation that the mould makes at present and trend The The mould mould mould is is is important important important handicraft handicraft handicraft equipment equipment equipment , , , occupies occupies occupies decisive decisive decisive position position position in in in industrid industrid industrid departments departments departments such such such as as consumer consumer goods goods goods , , , electrical electrical electrical equipment equipment equipment electron electron electron , , , automobile automobile automobile , , , aircraft aircraft aircraft fabrication. fabrication. fabrication. The The The mould mould mould is is is important important handicraft handicraft equipment equipment equipment , , , occupies occupies occupies decisive decisive decisive position position position in in in industrid industrid industrid departments departments departments such such such as as as consumer consumer consumer goods goods goods , , , electrical electrical equipment equipment electron electron electron , , , automobile automobile automobile , , , aircraft aircraft aircraft fabrication. fabrication. fabrication. Industrial Industrial Industrial product product product part part part rough rough rough process process process 75%, 75%, 75%, the the the finish finish machining machining 50% 50% 50% and and and plastic plastic plastic part part part 90% 90% 90% will will will be be be completed completed completed from from from the the the mould. mould. mould. The The The Chinese Chinese Chinese mould mould mould market market market demand demand already already reaches reaches reaches scale scale scale of of of 500 500 500 hundred hundred hundred million million million yuan yuan yuan at at at present. present. present. The The The automobile automobile automobile mould mould mould , , , the the the annual annual annual growth growth growth rate rate covering piece of mould especially will exceed 20 %; Also prompt building material mould development , various heterotype material the mould , wall surface and floor mould become new mould growth point , plastic doors and windows and plastic drain-pipe increase to exceeding 30 by in the upcoming several years %; The home appliance mould annual growth rate will exceed 10 %; The IT industry year increases % speed equally exceeding 20 , the need need to to to the the the mould mould mould accounts accounts accounts for for for 20 20 20 of of of mould mould mould marketplace marketplace marketplace %.2004 %.2004 %.2004 annual annual annual Chinese Chinese Chinese machine machine machine tools tools tools implements implements industry output value will continue to increase. Our country mould fabrication market potential is enormous. The basis data counts , in recent years, our country mould year gross output value reaches 3 billion U. S. dollar , entrance exceeds 1 billion U. S. dollar, exceed 100 million U. S. dollar outlet. Increase by from 25% to increase to 2005 50% of 1995. The expert foretells that abroad: Asia portion being occupied by in mould fabrication in the whole world, will from 25% to increase to 2005 50% of 1995. Chinese mould industry has been expanding by leaps and bounds , has formed east China and two big South China bases, and has expanded gradually arriving at other province. In 2002 (Shandong , Anhui , Sichuan) in 1996 ~, mould manufacturing industry output value annual average growth 14% , grows by 25% in 2003. In 2003 our country country mould mould mould output output output value value value is is is 45 45 45 billion billion billion RMB. RMB. RMB. The The The gross gross gross product product product place place place occupies occupies occupies the the the world world world the the the 3rd, 3rd, 3rd, exports exports exports a a mould increases 33.5% compared to last year 336,800,000 U. S. dollar. But, contents low our country technology moulds moulds already already already pile pile pile up up up in in in excess excess excess of of of requirement requirement requirement , , , very very very most most most support support support of of of accurate accurate accurate , complicated , complicated top top grade grade grade mould mould imports. Every year the entrance mould exceeds 1 billion U. S. dollar. Exceed 100 million U. S. dollar outlet. Precise mould accuracy requires that 3 mu ms , large-scale moulds require that 8000 satisfied kN agree well with model force injection machine request in 2 ~; The minitype mould needs the request satisfying the diameter 1 mm silent stock tube. At present, adopt quick-cutting to produce a mould already becoming the general trend that the mould makes, a few moulds have produced a manufacturer in abroad , high-speed machine tool large area has substituted the electric spark machine tool , quick-cutting has improved the mould efficacy greatly. Machine tool enterprise enterprise aims aims aims at at at mould mould mould manufacturing manufacturing manufacturing enterprises enterprises enterprises , , , some some some treating treating treating centres centres centres 60% 60% 60% all all all above above above of of of the the the machine machine machine tool tool producing a factory sells treating enterprise to a mould. The mould fabrication enterprise substituting the electric spark finish machining mould gradually in abroad has adopt quick-cutting already commonly , quick-cutting has produced a mould already becoming the general trend that the mould makes gradually , has improved the mould efficacy and mass greatly. Adopt quick-cutting to replace electric spark producing a mould , can get on the stick obviously , improves mould accuracy , life time growing. 2 high speed processes application in making in the mould 2.1 quick-cutting merit: 1) cutter high rotation rate and the machine tool height enter be given to and high acceleration , improve metal excision rate greatly; 2) quick-cutting diminutions cut a force; 3) quick-cutting heat major part generate heat from the cuttings entrainment , workpiece being short; 4) quick-cutting cut down vibration , improve treating mass; 2.2 high speed treating apply to the beneficial result that the mould processes 1) fleetness rough process and half finish machining, improve treating efficiency; 2) high speed high-accuracy finish machining replace only entire the height processing , indicating mass , form accuracy rise , 50%, cuts down repair a mill by hand than EDM processes a potentiation; 3) cuts the surface processing final molding stiffly , improve surface mass , form accuracy, the treating (not only being that surface harshness is low, and the surface radiance is high) , being used for complicated surface has more advantage; 4) the surface loss that EDM treating produces , improve mould life-span 20%; 5) 5) processes processes processes an an an electrode electrode electrode rapidly rapidly rapidly combining combining combining with with with the the the CAD/CAM CAD/CAM CAD/CAM technology technology technology , , , especially, especially, the the form form form is is complicated , thin-wall is similar to an electrode. 3 adopt quick-cutting to process a mould needing the problem solving In in the homeland, since the aspect cause such as fund , technology , the quick-cutting applying produce a mould be in the initial stage stage. Return the machine tool , cutter , handicraft back to existence as well as some problem of aspect needs to proceed orderly other solve. The shortcoming is that finished cost is high, correct cutter sigmatism have comparatively high demand, can not have used big cutters , need to have the complicated computer programming technology to be used for support , equipment running cost height. Two, the high speed processing a mould's processes a machine tool Mould finish machining and hard cutting treating require that the numerical control high-speed machine tool , form form board board board , , , model model model put put put up up up the the the precision precision precision processing processing processing need need need , , , high-effect high-effect high-effect numerical numerical numerical control control control machine machine machine tool tool tool etc.The etc.The mould aiming at produces a lot of machine tool enterprise , some treating centres 60% all above of the machine tool producing a factory sells enterprise to a mould. The The fixed assets fixed assets having having 5 5 billion billion yuan yuan yuan without without without exception exception exception in in in the the the upcoming upcoming upcoming several several several years years years throws throws throws into into into mould mould industry , 80% is the machine tool buying a mould process equipment , just saying every year having 4 billion yuan of RMB to buy Jinqie among them. At At present present present average average average our our our country country country numerical numerical numerical control control control machine machine machine tool tool tool utilization utilization utilization ratio ratio ratio approximately approximately approximately 20%, 20%, 20%, the the high-speed machine tool utilization ratio 3 ~ 5%. Also, mould enterprise has the unit suitable to buy a high-speed machine tool , complies with 6000 ~ 40000 rmp's to have. 1 high-speed machine tool technology parameter demands Process Process centre centre centre chief chief chief axis axis axis high-power high-power high-power , , , high high high rotation rotation rotation rate rate rate , , , satisfied satisfied satisfied rude rude rude finish finish finish machining; machining; machining; The The The finish finish machining mould wants to need to reach 15000 ~ 20000 rmp like the cutter , the machine tool with minor diameter. Generally, the chief axis rotation rate machine tool under 10000 rpm can carry out rough process and half finish machining , cannot reach the finish machining accuracy; Have no way to reach 400 the above m/min cutting speed. 2 five scrolls of machine tools application increases a trend 1) treating route is nimble , the surface form is complicated; 2) treating range is big , the various type mould suitable processes; 3) cuts life-span of condition easy to cut down cutter wear , to raise a cutter,; 3 the softwares buying CAD/CAM and high-speed machine tools assort On the grounds of the machine tool , major part counting , having several billions U. S. dollar to be used to enter port every year, the electromachining machine tool and the high-speed machine tool need to import. Three, quick-cutting mould cutter technology Quick-cutting processes the cutter needing allocating proper quick-cutting. Progressing processing cutter material's in high speed has urged development of high speed treating. The cutter , knife edge headquarter and high tenacity base gathering crystal strengthening the ceramics cutter being able to be used giving consideration to high hardness experience and observe carbide alloy coating becoming possibility. Gather the crystal cube nitriding boron (PCBN) (PCBN) bit, bit, bit, whose whose whose hardness hardness hardness may may may amount amount amount to to to 3500 3500 3500 ~ ~ ~ 4500 4500 4500 HV HV HV. . . Gather Gather Gather crystal crystal crystal miamond miamond miamond (PCD) (PCD) (PCD) it's it's it's hardness hardness hardness but but amount to 6000 ~ 10000 HV . Germany SCS , Japan Mitsubishi (magical steel) and Sumitomo , Switzerland Switzerland Shanteweike Shanteweike Shanteweike , , , USA USA USA Kenna Kenna Kenna are are are in in in recent recent recent years years years swiftly swiftly swiftly large large large wait wait wait for for for the the the famous famous famous abroad abroad abroad cutter cutter company company to to to successively successively successively have have have debuted debuted debuted the the the respective respective respective quick-cutting quick-cutting quick-cutting cutter, cutter, cutter, not not not only only only cutter cutter cutter having having average structural steel of quick-cutting, the ceramics cutter still still having having direct direct quick-cutting quick-cutting of of energy energy quenching hard steel is waiting for an effect to surpass the hard cutter, especially the coating cutter appears all of a sudden sudden , , , bringing bringing bringing into into into play play play in in in quenching quenching quenching half half half finish finish finish machining machining machining and and and finish finish finish machining machining machining of of of hard hard hard steel. steel. steel. New New New cutter cutter material and cutter technology appearing already make the bottleneck problem that high speed has processed no longer be able to appear on the cutter. But, expensive entrance cutter price also blocks quick-cutting mould key factor. Above to come to saying the cutter and the cutter holder acceleration reach 3 gs the sort, the cutter circular runout needs to be smaller than 0.015 mm, but the knife length is unable greater than 4 times cutters diameter. The reality according to SANDVIK company has counted , the carbide alloy has stood on in the entirety using carbon nitriding nitriding titanium titanium titanium (TICN) (TICN) (TICN) coating coating coating when when when milling milling milling cutters cutters cutters (58 (58 (58 HRC) HRC) HRC) carry carry carry out out out high high high speed speed speed bright bright bright metal metal metal chopping chopping chopping , , rough process cutter linear speed has been 100 m/min about , whose linear speed has exceeded but 280 m/min when finish machining and microstoning. Such demands to cutter material (include the hardness , tenacity , red hardness keep the form (include row of crumbs function , surface accuracy , dynamic balance sex etc. (cutting the function) , the cutter under high temperature state)) as well as cutter life-span all has very highly. Experience according to in the homeland mould high speed finish machining, linear speed has exceeded 400 ~ 800 800 m/min m/min m/min when when when adopt adopt adopt the the the young young young diameter diameter diameter ball ball ball head head head milling milling milling cutter cutter cutter to to to carry carry carry out out out mould mould mould finish finish finish machining. machining. machining. The The machine tool choosing sufficient high-speed's cuts mould finish machining stiffly. Delcam adopt 0.8 mm diameter cutter to process the narrow slot , rotation rate 40000 rpm , 0.1 mm depth, feed speed 30 m/min. 1 chooses the cutter parameter , the cutter waits if shouldering an anterior angle. The cutter requires that the ability processing request shock resistance tenacity more highly , requiring that heat resistance pounds than average is strong; 2 adopts various method improving cutter life-span , reduces cutter cost. 3 adopt the high speed hilt , HSK hilt , heat pressing applying the most being at present to pretend to grip a 3 adopt the high speed hilt , HSK hilt , heat pressing applying the most being at present to pretend to grip a cutter. Pay attention to a cutter pretend to grip overall in the day afer tomorrow dynamic balance; 4current cutter enterprise has already done many jobs in the field of the technology resolving the quick-cutting cutter cutter , , , serving serving serving facing facing facing the the the cutter cutter cutter processing processing processing may may may help help help to to to solve solve solve much much much problem problem problem , , , the the the cutter cutter cutter has has has produced produced produced a a manufacturer manufacturer becoming becoming becoming the the the main main main body body body , , , the the the reference reference reference cutter cutter cutter has has has produced produced produced the the the technology technology technology parameter parameter parameter that that that the the manufacturer provides. Four, improve quick-cutting mould efficiency technology 1 cutter diameter and the length choice 2 HSM and the EDM choice 3 does cutting and the lubricating cooling 4 feeds choice: Move forward generally giving amounts <milling cutter diameters 10% , move forward giving a a width width width <milling <milling <milling cutter cutter cutter diameter diameter diameter 40%. 40%. 40%. According According According to to to material, material, material, condition condition condition chooses chooses chooses the the the parameter parameter parameter processing processing handicraft rationally High speed bright metal cuts the mass processing part material abroad fairly good, material quality level is identical , the treating function comparison is stable; But, the cutter that the company produces abroad is also that the the standard standard standard makes makes makes an an an experiment experiment experiment with with with their their their material; material; material; The The The treating treating treating being being being recommended recommended recommended by by by is is is suitable suitable suitable to to to their their standard standard comparatively comparatively comparatively like like like the the the parameter parameter parameter , , , material material material quality quality quality has has has the the the certain certain certain difference difference difference with with with domestic domestic domestic part part part , , , this this difference difference shows shows shows comparatively comparatively comparatively obviously obviously obviously , , , some some some parameters parameters parameters can can can apply apply directly, directly, but but but some some effect dispatches right away comparatively during the period of high speed bright metal chops if using their cutter. But select and use part material quality in the homeland like enterprise having the certain standard, what be put into use part material, can use the part material quality that high speed processes especially , the general meeting is limited in some part material range inner, that this applies the high speed processing technology to us has also provided advantageous condition , has been able to apply to less treating material within range. Being needing to emphasize that here, must choose the treating technological parameter optimizing out a set of capital suitable enterprise on these material , is brought into company standard and. The technology selecting and using the domestic cutter , seldom having the bright metal recommending high speed to chop parametric , is necessary making an experiment, get the comparatively satisfied parameter , produce a manufacturer had better to select and use the fixed cutter , cut down the number of times testing that , the standard forming forming a a a processing processing processing technology, technology, technology, such such such can can can improve improve improve effective effective effective utilization utilization utilization ratio ratio ratio of of of equipment equipment equipment , , , lowers lowers lowers production production costs , can get the fairly good economic effect. Five, quick-cutting route processing a cutter and programming 1) flat surface feeds the route choice 2) 2) outlines process the route choice 3) Keep cutting loading stable 4) keeps relatively stable moving forward giving amounts and feed speed 5) keeps the garden corner in flat surface cutting 6) chooses the finish machining margin rationally Programming demand of HSC finish machining to CAM: 1) the bright metal avoiding a corner to the full cuts motion; 2) tries one's best to avoid external feed of workpiece and enter next depth return knife motion , direct from the outline. Or adopt a helical line or being sure enter slanting to moving forward; 3) constant each edge feed , improve the quality, prolongs cutter life-span; 4) outline treating are kept waiting in level surface. Quick-cutting CAM software: Several years ago will have started quick-cutting processing programming technology research, the Delcam company company , , , has has has developed developed developed the the the quick-cutting quick-cutting quick-cutting automation automation automation programming programming programming software software software module; module; module; Lately, Lately, Lately, the the the MasterCAM MasterCAM company has also developed the quick-cutting automation programming software module; You also are in in the homeland north navigation developing the quick-cutting automation programming software module; Six, high-speed machine tool numerical control system characteristic 1) high speed data is processed 2) corner forecasts are handled 3) NURBS are not justified appearance strip runin curve treating Seven, safe quick-cutting mould problem 1) Monitoring wearing a cutter away and destroying; 2) Intensity that the bit links; 3) Strict with the machine tool and the cutter examination is very important and before the average machine tool processing diversity , safety protects and starts up. Eight, there exists problem in our country at present in adopt high speed to process the mould technology 1 machine tool: 1) domestic high-speed machine tool overall function still has the gap , the function component function to be able to not satisfy a request. Power and rotation rate including the electricity chief axis, entrance machine tool price is high; 2)Under the machine tool high speed, the dynamic behaviour studies the function being not enough to affect a complete machine as a result,; 3)The five scroll of machine tool is not enough mature , entrance machine tool price is very high; 4) supporting technology and equipment are fairly incomplete 2 cutters: 1) domestic cutter is not able to adapt to the quick-cutting application , high speed cuts only entire treating is to affect quick-cutting processing a key especially stiffly. Entrance cutter price is high. The cutter technology factor of mould. 2) supporting technologies are not enough to include hilt , online dynamic balance in complete set etc.. 3 high speed moulds process the technology and the experiment 1) Be short of the accumulation applying experience since high speed processes the mould history comparatively shortly,; 2)The comparison studying comparison stops throwing into lack, sets up a project to quick-cutting handicraft is difficult; 3) Be short of the quick-cutting data base or the handbook , is still blank space at present; 4) moulds produce the manufacturer cognition lack to quick-cutting , the analysis contrast being short of long range beneficial result; 4 Be short of the quick-cutting automation programming software; 5 Be short of a five scroll of gear quick-cutting automation programming CAM software. Concluding remark The mould marketplace has the intense need, but technology to be unable to keep abreast with to high speed treating. Starting is late , the basis is relatively poor , overall engineering level not being taller than , develops slowlyRequire that one by one, aspect coordinated growth , the product mimic inkstone throwing into combining with enlarging, each comprehensive utilization aspect strengths drive quick-cutting application in making in the mould.. Our hope , effort passing every aspect, before the market demand push go down , pass technological progress, look like automobile , machine tool , home appliance , before long, not only our country being going to become a mould producing Great Power, and be going to become a mould producing the powerful country. References1, Jin Diecheng , Song Fangzhi. The modern mould makes the technology , Beijing: Mechanical industry press, 2001. 2, Xu Hefeng, The digitization mould makes the technology , Beijing: Chemical industry press, 2001. 3,Zhao Bo ,High speed processes the forward position technology that the mould processes. Mould technology , 2000 , (2) 4,Zhang Haiou,The fleetness mould makes the technology current situation and their developing trend. Mould technology , 2000 , (6) 5,Guo Dongming,Wang Xiaoming,Be geared to the needs of the particular kind processing technology that the fleetness creates. Chinese mechanical engineering , 2000 , (11) 高速加工和现代模具制造一、概述一、概述1.目前模具制造的发展现状和趋势.目前模具制造的发展现状和趋势模具作为重要的工艺装备,在消费品、电器电子、汽车、飞机制造等工业部门中,占有举足轻重的地位。
注塑模具英文文献
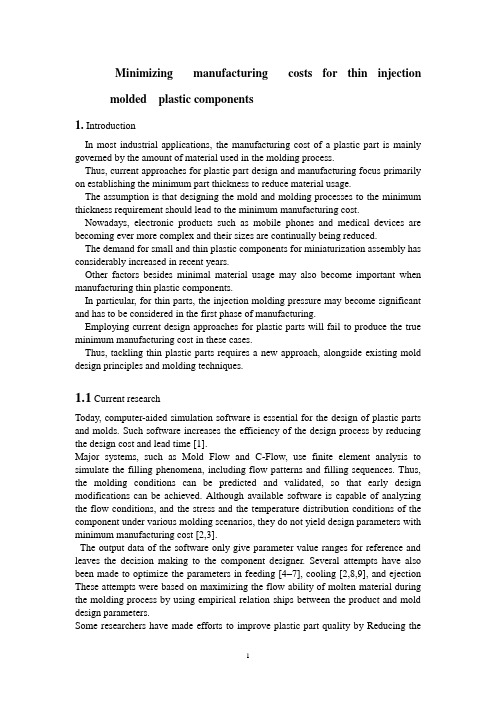
Employing current design approaches for plastic parts will fail to produce the true minimum manufacturing cost in these cases.
Minimizing manufacturing costs for thin injection
molded plastic components
1. Introduction
In most industrial applications, the manufacturing cost of a plastic part is mainly governed by the amount of material used in the molding procend the part deformation after molding [12], analyzing the effects of wall thickness and the flow length of the part [13], and analyzing the internal structure of the plastic part design and filling materials flows of the mold design [14]. Reifschneider [15] has compared three types of mold filling simulation programs, including Part Adviser, Fusion, and Insight, with actual experimental testing. All these approaches have established methods that can save a lot of time and cost. However, they just tackled the design parameters of the plastic part and mold individually during the design stage. In addition, they did not provide the design parameters with minimum manufacturing cost. Studies applying various artificial intelligence methods and techniques have been found that mainly focus on optimization analysis of injection molding parameters [16,17]. For in-stance He et al. [3] introduced a fuzzy- neuro approach for automatic resetting of molding process parameters. By contrast , Helps et al. [18,19] adopted artificial neural networks to predict the setting of molding conditions and plastic part quality control in molding. Clearly, the development of comprehensive molding process models and computer-aided manufacturing provides a basis for realizing molding parameter optimization [3 , 16,17]. Mok et al. [20] propose a hybrid neural network and genetic algorithm approach incorporating Case-Based Reasoning (CBR) to derive initial settings for molding parameters for parts with similar design features quickly and with acceptable accuracy. Mok’s approach was based on past product processing data, and was limited to designs that are similar to previous product data. However, no real R&D effort has been found that considers minimizing manufacturing costs for thin plastic components. Generally, the current practical approach for minimizing the manufacturing cost of plastic components is to minimize the thickness and the dimensions of the part at the product design stage, and then to calculate the costs of the mold design and molding process for the part accordingly, as shown in Fig. 1. The current approach may not be able to obtain the real minimum manufacturing cost when handling thin plastic components. 1.2Manufacturing requirements for a typical thin plastic component As a test example, the typical manufacturing requirements for a thin square plastic part with a center hole, as shown in Fig. 2, are given in Table 1.
- 1、下载文档前请自行甄别文档内容的完整性,平台不提供额外的编辑、内容补充、找答案等附加服务。
- 2、"仅部分预览"的文档,不可在线预览部分如存在完整性等问题,可反馈申请退款(可完整预览的文档不适用该条件!)。
- 3、如文档侵犯您的权益,请联系客服反馈,我们会尽快为您处理(人工客服工作时间:9:00-18:30)。
Treating and the modern mould make high speedOne, summarizes1 the present situation that the mould makes at present and trendThe mould is important handicraft equipment , occupies decisive position in industrid departments such as consumer goods , electrical equipment electron , automobile , aircraft fabrication. The mould is important handicraft equipment , occupies decisive position in industrid departments such as consumer goods , electrical equipment electron , automobile , aircraft fabrication. Industrial product part rough process 75%, the finish machining 50% and plastic part 90% will be completed from the mould. The Chinese mould market demand already reaches scale of 500 hundred million yuan at present. The automobile mould , the annual growth rate covering piece of mould especially will exceed 20 %; Also prompt building material mould development , various heterotype material the mould , wall surface and floor mould become new mould growth point , plastic doors and windows and plastic drain-pipe increase to exceeding 30 by in the upcoming several years %; The home appliance mould annual growth rate will exceed 10 %; The IT industry year increases % speed equally exceeding 20 , the need to the mould accounts for 20 of mould marketplace %.2004 annual Chinese machine tools implements industry output valuewill continue to increase. Our country mould fabrication market potential is enormous. The basis data counts , in recent years, our country mould year gross output value reaches 3 billion U. S. dollar , entrance exceeds 1 billion U. S. dollar, exceed 100 million U. S. dollar outlet. Increase by from 25% to increase to 2005 50% of 1995. The expert foretells that abroad: Asia portion being occupied by in mould fabrication in the whole world, will from 25% to increase to 2005 50% of 1995.Chinese mould industry has been expanding by leaps and bounds , has formed east China and two big South China bases, and has expanded gradually arriving at other province. In 2002 (Shandong , Anhui , Sichuan) in 1996 ~, mould manufacturing industry output value annual average growth 14% , grows by 25% in 2003. In 2003 our country mould output value is 45 billion RMB. The gross product place occupies the world the 3rd, exports a mould increases 33.5% compared to last year 336,800,000 U. S. dollar. But, contents low our country technology moulds already pile up in excess of requirement , very most support of accurate , complicated top grade mould imports. Every year the entrance mould exceeds 1 billion U. S. dollar. Exceed 100 million U. S. dollar outlet.Precise mould accuracy requires that 3 mu ms , large-scale moulds require that 8000 satisfied kN agree well with model force injection machine request in 2 ~; The minitype mould needs the request satisfying the diameter 1 mm silent stock tube. At present, adopt quick-cutting to produce a mould already becoming the general trend that the mould makes, a few moulds have produced a manufacturer in abroad , high-speed machine tool large area has substituted the electric spark machine tool , quick-cutting has improved the mould efficacy greatly. Machine tool enterprise aims at mould manufacturing enterprises , some treating centres 60% all above of the machine tool producing a factory sells treating enterprise to a mould. The mould fabrication enterprise substituting the electric spark finish machining mould gradually in abroad has adopt quick-cutting already commonly , quick-cutting has produced a mould already becoming the general trend that the mould makes gradually , has improved the mould efficacy and mass greatly. Adopt quick-cutting to replace electric spark producing a mould , can get on the stick obviously , improves mould accuracy , life time growing.2 high speed processes application in making in the mould2.1 quick-cutting merit:1) cutter high rotation rate and the machine tool height enter be given to and high acceleration , improve metal excision rate greatly;2) quick-cutting diminutions cut a force;3) quick-cutting heat major part generate heat from the cuttings entrainment , workpiece being short;4) quick-cutting cut down vibration , improve treating mass;2.2 high speed treating apply to the beneficial result that the mould processes1) fleetness rough process and half finish machining, improve treating efficiency;2) high speed high-accuracy finish machining replace only entire the height processing , indicating mass , form accuracy rise , 50%, cuts down repair a mill by hand than EDM processes a potentiation;3) cuts the surface processing final molding stiffly , improve surface mass , form accuracy, the treating (not only being that surface harshness is low, and the surface radiance is high) , being used for complicated surface has more advantage;4) the surface loss that EDM treating produces , improve mould life-span 20%;5) processes an electrode rapidly combining with the CAD/CAM technology , especially, the form is complicated , thin-wall is similar to an electrode.3 adopt quick-cutting to process a mould needing the problem solvingIn in the homeland, since the aspect cause such as fund , technology , the quick-cutting applying produce a mould be in the initial stage stage. Return the machine tool , cutter , handicraft back to existence as well as some problem of aspect needs to proceed orderly other solve.The shortcoming is that finished cost is high, correct cutter sigmatism have comparatively high demand, can not have used big cutters , need to have the complicated computer programming technology to be used for support , equipment running cost height.Two, the high speed processing a mould's processes a machine toolMould finish machining and hard cutting treating require that the numerical control high-speed machine tool , form board , model put up the precision processing need , high-effect numerical control machine tool etc.The mould aiming at produces a lot of machine tool enterprise , some treating centres 60% all above of the machine tool producing a factory sells enterprise to a mould.The fixed assets having 5 billion yuan without exception in the upcoming several years throws into mould industry , 80% is the machine tool buying a mould process equipment , just saying every year having 4 billion yuan of RMB to buy Jinqie among them.At present average our country numerical control machine tool utilization ratio approximately 20%, the high-speed machine tool utilization ratio 3 ~ 5%. Also, mould enterprise has the unit suitable to buy a high-speed machine tool , complies with 6000 ~ 40000 rmp's to have.1 high-speed machine tool technology parameter demandsProcess centre chief axis high-power , high rotation rate , satisfied rude finish machining; The finish machining mould wants to need to reach 15000 ~ 20000 rmp like the cutter , the machine tool with minor diameter. Generally, the chief axis rotation rate machine tool under 10000 rpm can carry out rough process and half finish machining , cannot reach the finish machining accuracy;Have no way to reach 400 the above m/min cutting speed.2 five scrolls of machine tools application increases a trend1) treating route is nimble , the surface form is complicated;2) treating range is big , the various type mould suitable processes;3) cuts life-span of condition easy to cut down cutter wear , to raise a cutter,;3 the softwares buying CAD/CAM and high-speed machine tools assortOn the grounds of the machine tool , major part counting , having several billions U. S. dollar to be used to enter port every year, the electromachining machine tool and the high-speed machine tool need to import.Three, quick-cutting mould cutter technologyQuick-cutting processes the cutter needing allocating proper quick-cutting. Progressing processing cutter material's in high speed has urged development of high speed treating. The cutter , knife edge headquarter and hightenacity base gathering crystal strengthening the ceramics cutter being able to be used giving consideration to high hardness experience and observe carbide alloy coating becoming possibility. Gather the crystal cube nitriding boron (PCBN) bit, whose hardness may amount to 3500 ~ 4500 HV. Gather crystal miamond (PCD) it's hardness but amount to 6000 ~ 10000 HV. Germany SCS , Japan Mitsubishi (magical steel) and Sumitomo , Switzerland Shanteweike , USA Kenna are in recent years swiftly large wait for the famous abroad cutter company to successively have debuted the respective quick-cutting cutter, not only cutter having average structural steel of quick-cutting, the ceramics cutter still having direct quick-cutting of energy quenching hard steel is waiting for an effect to surpass the hard cutter, especially the coating cutter appears all of a sudden , bringing into play in quenching half finish machining and finish machining of hard steel. New cutter material and cutter technology appearing already make the bottleneck problem that high speed has processed no longer be able to appear on the cutter.But, expensive entrance cutter price also blocks quick-cutting mould key factor.Above to come to saying the cutter and the cutter holder acceleration reach 3 gs the sort, the cutter circular runout needs to be smaller than 0.015 mm, but the knife length is unable greater than 4 times cutters diameter. The reality according to SANDVIK company has counted , the carbide alloy has stood on in the entirety using carbon nitriding titanium (TICN) coating when milling cutters (58 HRC) carry out high speed bright metal chopping , rough process cutter linear speed has been 100 m/min about , whose linear speed has exceeded but 280 m/min when finish machining and microstoning. Such demands to cutter material (include the hardness , tenacity , red hardness keep the form (include row of crumbs function , surface accuracy , dynamic balance sex etc. (cutting the function) , the cutter under high temperature state)) as well as cutter life-span all has very highly.Experience according to in the homeland mould high speed finish machining, linear speed has exceeded 400 ~ 800 m/min when adopt the young diameter ball head milling cutter to carry out mould finish machining. The machine tool choosing sufficient high-speed's cuts mould finish machining stiffly.Delcam adopt 0.8 mm diameter cutter to process the narrow slot , rotation rate 40000 rpm , 0.1 mm depth, feed speed 30 m/min.1 chooses the cutter parameter , the cutter waits if shouldering an anterior angle. The cutter requires that the ability processing request shock resistance tenacity more highly , requiring that heat resistance pounds than average is strong;2 adopts various method improving cutter life-span , reduces cutter cost.3 adopt the high speed hilt , HSK hilt , heat pressing applying the most being at present to pretend to grip a cutter. Pay attention to a cutter pretend to grip overall in the day afer tomorrow dynamic balance;4current cutter enterprise has already done many jobs in the field of the technology resolving the quick-cutting cutter , serving facing the cutter processing may help to solve much problem , the cutter has produced a manufacturer becoming the main body , the reference cutter has produced the technology parameter that the manufacturer provides.Four, improve quick-cutting mould efficiency technology1 cutter diameter and the length choice2 HSM and the EDM choice3 does cutting and the lubricating cooling4 feeds choice: Move forward generally giving amounts <milling cutter diameters 10% , move forward givinga width <milling cutter diameter 40%. According to material, condition chooses the parameter processing handicraft rationallyHigh speed bright metal cuts the mass processing part material abroad fairly good, material quality level is identical , the treating function comparison is stable; But, the cutter that the company produces abroad is also that the standard makes an experiment with their material; The treating being recommended by is suitable to theirstandard comparatively like the parameter , material quality has the certain difference with domestic part , this difference shows comparatively obviously , some parameters can apply directly, but some effect dispatches right away comparatively during the period of high speed bright metal chops if using their cutter. But select and use part material quality in the homeland like enterprise having the certain standard, what be put into use part material, can use the part material quality that high speed processes especially , the general meeting is limited in some part material range inner, that this applies the high speed processing technology to us has also provided advantageous condition , has been able to apply to less treating material within range. Being needing to emphasize that here, must choose the treating technological parameter optimizing out a set of capital suitable enterprise on these material , is brought into company standard and.The technology selecting and using the domestic cutter , seldom having the bright metal recommending high speed to chop parametric , is necessary making an experiment, get the comparatively satisfied parameter , produce a manufacturer had better to select and use the fixed cutter , cut down the number of times testing that , the standard forming a processing technology, such can improve effective utilization ratio of equipment , lowers production costs , can get the fairly good economic effect.Five, quick-cutting route processing a cutter and programming1) flat surface feeds the route choice2) 2) outlines process the route choice3) Keep cutting loading stable4) keeps relatively stable moving forward giving amounts and feed speed5) keeps the garden corner in flat surface cutting6) chooses the finish machining margin rationallyProgramming demand of HSC finish machining to CAM:1) the bright metal avoiding a corner to the full cuts motion;2) tries one's best to avoid external feed of workpiece and enter next depth return knife motion , direct from the outline. Or adopt a helical line or being sure enter slanting to moving forward;3) constant each edge feed , improve the quality, prolongs cutter life-span;4) outline treating are kept waiting in level surface.Quick-cutting CAM software:Several years ago will have started quick-cutting processing programming technology research, the Delcam company , has developed the quick-cutting automation programming software module; Lately, the MasterCAM company has also developed the quick-cutting automation programming software module; You also are in in the homeland north navigation developing the quick-cutting automation programming software module;Six, high-speed machine tool numerical control system characteristic1) high speed data is processed2) corner forecasts are handled3) NURBS are not justified appearance strip runin curve treatingSeven, safe quick-cutting mould problem1)Monitoring wearing a cutter away and destroying;2)Intensity that the bit links;3)Strict with the machine tool and the cutter examination is very important and before the average machine tool processing diversity , safety protects and starts up.Eight, there exists problem in our country at present in adopt high speed to process the mould technology1 machine tool:1) domestic high-speed machine tool overall function still has the gap , the function component function to be able to not satisfy a request. Power and rotation rate including the electricity chief axis, entrance machine tool priceis high;2)Under the machine tool high speed, the dynamic behaviour studies the function being not enough to affect a complete machine as a result,;3)The five scroll of machine tool is not enough mature , entrance machine tool price is very high;4) supporting technology and equipment are fairly incomplete2 cutters:1) domestic cutter is not able to adapt to the quick-cutting application , high speed cuts only entire treating especially stiffly. Entrance cutter price is high. The cutter technology is to affect quick-cutting processing a key factor of mould.2) supporting technologies are not enough to include hilt , online dynamic balance in complete set etc..3 high speed moulds process the technology and the experiment1) Be short of the accumulation applying experience since high speed processes the mould history comparatively shortly,;2)The comparison studying comparison stops throwing into lack, sets up a project to quick-cutting handicraft is difficult;3) Be short of the quick-cutting data base or the handbook , is still blank space at present;4) moulds produce the manufacturer cognition lack to quick-cutting , the analysis contrast being short of long range beneficial result;4 Be short of the quick-cutting automation programming software;5 Be short of a five scroll of gear quick-cutting automation programming CAM software.Concluding remarkThe mould marketplace has the intense need, but technology to be unable to keep abreastwith to high speed treating. Starting is late , the basis is relatively poor , overall engineeringlevel not being taller than , develops slowlyRequire that one by one, aspect coordinatedgrowth , the product mimic inkstone throwing into combining with enlarging, eachcomprehensive utilization aspect strengths drive quick-cutting application in making in themould.. Our hope , effort passing every aspect, before the market demand push go down ,pass technological progress, look like automobile , machine tool , home appliance , beforelong, not only our country being going to become a mould producing Great Power, and begoing to become a mould producing the powerful country.References1, Jin Diecheng , Song Fangzhi. The modern mould makes the technology , Beijing:Mechanical industry press, 2001.2, Xu Hefeng, The digitization mould makes the technology , Beijing: Chemical industrypress, 2001.3,Zhao Bo ,High speed processes the forward position technology that the mould processes.Mould technology , 2000 , (2)4,Zhang Haiou,The fleetness mould makes the technology current situation and theirdeveloping trend. Mould technology , 2000 , (6)5,Guo Dongming,Wang Xiaoming,Be geared to the needs of the particular kind processingtechnology that the fleetness creates. Chinese mechanical engineering , 2000 , (11)高速加工和现代模具制造一、概述1.目前模具制造的发展现状和趋势模具作为重要的工艺装备,在消费品、电器电子、汽车、飞机制造等工业部门中,占有举足轻重的地位。