材料成型计算机模拟1
圆柱体压缩过程模拟
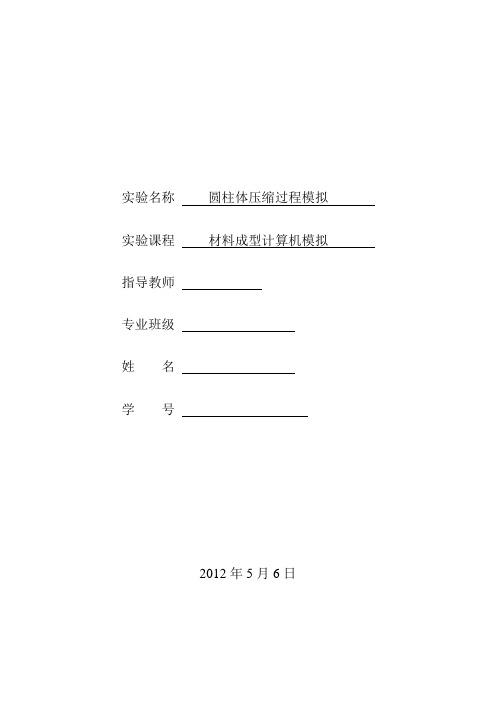
实验名称圆柱体压缩过程模拟实验课程材料成型计算机模拟指导教师专业班级姓名学号2012年5月6日实验一 圆柱体压缩过程模拟1 实验目的与内容1.1 实验目的进一步熟悉AUTOCAD 或PRO/E 实体三维造型方法与技艺,掌握DEFORM 软件的前处理、后处理的操作方法与技能,学会运用DEFORM 软件分析压缩变形的变形力学问题。
1.2 实验内容运用DEFORM 模拟如图1所示的圆柱坯压缩过程。
(一)压缩条件与参数锤头与砧板:尺寸200×200×20mm ,材质DIN-D5-1U,COLD ,温度室温。
工件:材质DIN_CuZn40Pb2,尺寸如表1所示,温度室温。
(二)实验要求砧板工件锤头图1 圆柱体压缩过程模拟(1)运用AUTOCAD或PRO/e绘制各模具部件及棒料的三维造型,以stl格式输出;(2)设计模拟控制参数;(3)DEFORM前处理与运算;(4)DEFORM后处理,观察圆柱体压缩变形过程,载荷曲线图,通过轴对称剖分观察圆柱体内部应力、应变及损伤值分布状态;(5)比较方案1与2、3与4、1与3和2与4的模拟结果,找出圆柱体变形后的形状差别,说明原因;(6)提交分析报告(纸质和电子版)、模拟数据文件、日志文件。
2 模拟控制参数的设计与选择在整个模拟过程中,设定总步长为100,每10步保存一次,当变形体的网格尺寸为最小边界长度的三分之一时停止,即为1.27cm;3 实验过程3.1工模具及工件的三维造型根据给定的几何尺寸,运用AUTOCAD或PRO/E分别绘制坯料、锤头和砧板的几何实体,文件名称分别为workpiece,topdie,bottomdie,输出STL格式。
3.2 压缩过程模拟3.2.1 前处理建立新问题:程序→DEFORM6.1→File→New Problem→Next→在Problem Name栏中填写“Forging”→ Finish→进入前处理界面。
7材料成型过程的计算机模拟——MOLDFLOW
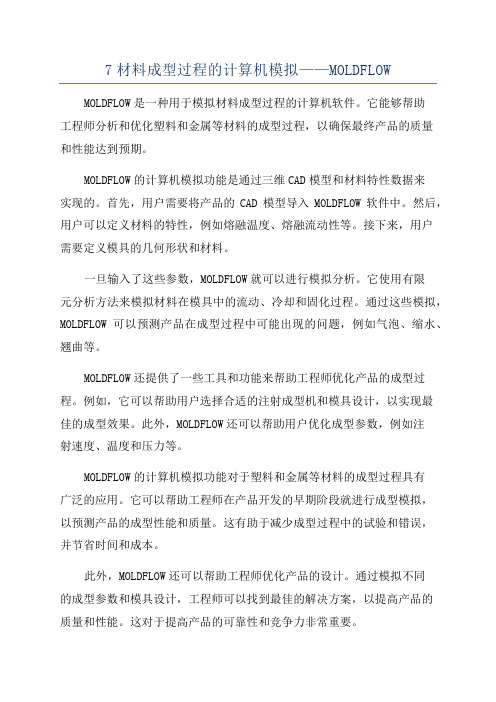
7材料成型过程的计算机模拟——MOLDFLOW MOLDFLOW是一种用于模拟材料成型过程的计算机软件。
它能够帮助工程师分析和优化塑料和金属等材料的成型过程,以确保最终产品的质量和性能达到预期。
MOLDFLOW的计算机模拟功能是通过三维CAD模型和材料特性数据来实现的。
首先,用户需要将产品的CAD模型导入MOLDFLOW软件中。
然后,用户可以定义材料的特性,例如熔融温度、熔融流动性等。
接下来,用户需要定义模具的几何形状和材料。
一旦输入了这些参数,MOLDFLOW就可以进行模拟分析。
它使用有限元分析方法来模拟材料在模具中的流动、冷却和固化过程。
通过这些模拟,MOLDFLOW可以预测产品在成型过程中可能出现的问题,例如气泡、缩水、翘曲等。
MOLDFLOW还提供了一些工具和功能来帮助工程师优化产品的成型过程。
例如,它可以帮助用户选择合适的注射成型机和模具设计,以实现最佳的成型效果。
此外,MOLDFLOW还可以帮助用户优化成型参数,例如注射速度、温度和压力等。
MOLDFLOW的计算机模拟功能对于塑料和金属等材料的成型过程具有广泛的应用。
它可以帮助工程师在产品开发的早期阶段就进行成型模拟,以预测产品的成型性能和质量。
这有助于减少成型过程中的试验和错误,并节省时间和成本。
此外,MOLDFLOW还可以帮助工程师优化产品的设计。
通过模拟不同的成型参数和模具设计,工程师可以找到最佳的解决方案,以提高产品的质量和性能。
这对于提高产品的可靠性和竞争力非常重要。
总之,MOLDFLOW是一种强大的工具,可以帮助工程师模拟和优化材料成型过程。
它能够预测产品在成型过程中可能出现的问题,并提供解决方案。
通过使用MOLDFLOW,工程师可以提高产品的质量和性能,减少成本和时间,从而在市场上取得竞争优势。
材料成型计算机模拟本科教学的若干问题与对策
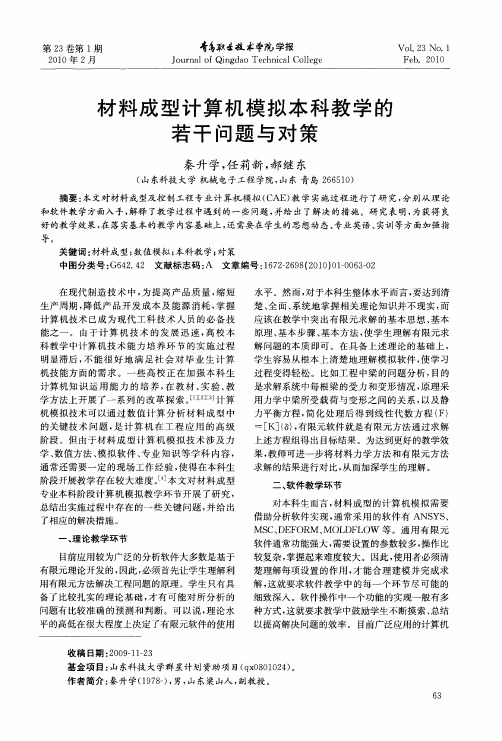
、
理 论教 学环 节
目前应 用 较为广 泛 的分析 软件 大多数 是基 于
有 限元理论 开 发 的 , 因此 , 必须 首先 让学 生理解 利 用有 限元方 法解 决工 程 问题 的原 理 。学生 只有 具
备 了比较扎 实 的理 论 基 础 , 有 可 能对 所 分 析 的 才 问题 有 比较 准 确 的预 测 和判 断 。
收稿 日期 :0 91— 3 2 0 —12
种方式 , 这就要求教学 中鼓励学生不断摸索 、 总结 以提 高解 决 问题 的效率 。 目前广 泛应 用 的计算机
基金 项 目 : 东科技 大 学群 星计 划资助 项 目(x 8 12 ) 山 q 000 4 。 作者 简介 : 秦升 学 (98) 男, 东梁山人 , 17一 , 山 副教授 。
机 模 拟技 术 可 以通 过 数 值 计 算 分 析 材 料 成 型 中
水平 。然而 , 于 本科生 整 体水平 而 言 , 对 要达 到清 楚、 面、 全 系统 地 掌 握相 关 理论 知识 并 不现 实 , 而 应该 在教 学 中突 出有 限元 求 解 的基 本思 想 、 本 基 原理 、 本 步 骤 、 本方 法 , 学 生 理解 有 限元 求 基 基 使
计 算 机 技术 已成 为 现 代 工 科 技 术 人 员 的必 备 技 能之 一 。 由 于计 算 机 技 术 的 发 展 迅 速 , 校 本 高 科 教 学 中计 算 机技 术 能 力 培 养 环 节 的 实 施 过 程 明显 滞后 , 能 很 好 地 满 足 社 会 对 毕 业 生 计 算 不 机 技 能 方 面 的需 求 。一 些 高 校 正 在 加 强 本 科 生 计 算 机 知 识 运 用 能 力 的培 养 , 教 材 、 验 、 在 实 教 学 方 法上 开 展 了一 系 列 的改 革 探 索 。】。3计 算 _ E l ]] Ⅱ
材料力学行为及计算机模拟
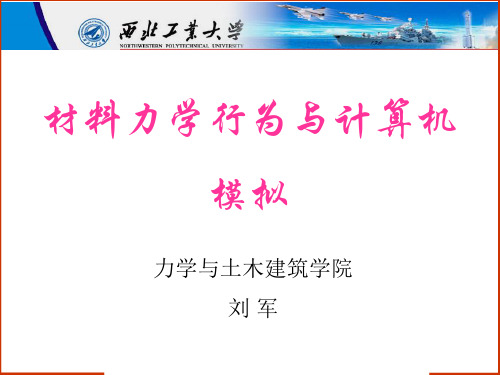
软件分析的一般流程
有 限 元 法
软 件 分 析 流 程 模型建立 前 划分网格 材料、边界 处 理
——
求解计算
求解器 后处理
数据处理
有限元法——常用软件介绍
CAE(前处理+求解器+后处理)
线弹性分析------Msc.Nastran、Anasys
非线性分析------ Msc.Marc、Abaqus
材料力学性能测试技术
对材料力学性能的测试是建立在试验的基础上的, 而材料的各种的力学性能指标的也出要试验来确定。 常用的力学测试技术:
静载拉伸 弹性模量、扭转、压缩、摩擦磨损
…
第2章 计算机模拟
——力学
1. 2.
代表性模拟结果展示 模拟方法介绍
一般力学(运动学、动力学、振动与冲击) ② 振动特性
外界载荷引起桥梁的共振
一般力学(运动学、动力学、振动与冲击)
③ 冲击
冲击的防护
流体力学(静力学、动力学)
气动外形设计:
外形设计过程
固体力学 ① 材料力学行为-----指导材料设计与加工 本课程关注 重点
薄壁工字梁偏心受扭
固体力学(材料、结构) ② 结构力学行为----指导结构设计(功能、经济性)
需要从行为的过程去深入理解性能;重视环境对性能的影
响。
行为
行为是从一个状态到另一个状态。 种材料也会有不同性能。
外界条件 在不同的外界条件(应力、温度、化学介质、磁场等)下,同一 参量化
性能必须参量化,即材料的性能需要定量地加以表述。
材料性能的分类
物理性能:热、光、电、声、磁、辐照性能 … 强度——s 简单性能 力学性能 弹塑性——E, G, d , f
注塑模cae技术1注塑模cae的内容
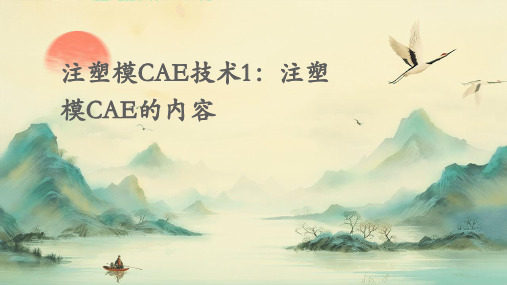
总结词
确保医疗用品结构完整性和安全性
详细描述
医疗用品的成型过程要求非常高,需要保证产品结构的 完整性和安全性。通过注塑模CAE技术进行成型过程模 拟,可以预测产品在成型过程中的可能问题,如收缩、 翘曲、裂纹等,并及时进行调整,确保最终产品的质量 和安全性。
THANKS
感谢观看
模型简化
为了提高计算效率,对模型进 行简化,如忽略倒角、小孔等 细节。
网格划分
将模型划分为有限元网格,以 便进行模拟计算。
边界条件设定
根据实际情况,设定模具与注 射机的连接方式、注射压力、
注射温度等边界条件。
模拟计算
01
02
03
充填模拟
模拟塑料在模具中的流动 行为,预测可能出现的填 充不足、熔接痕等问题。
06
注塑模CAE技术应用案例
案例一:手机壳流动与翘曲分析
总结词
通过流动模拟预测填充行为,翘曲模拟预测产品变形程 度
详细描述
在生产手机壳的注塑过程中,利用CAE技术进行流动模 拟可以预测塑料在模具中的填充行为,优化注射时间和 压力,确保均匀填充。同时,翘曲模拟可以预测产品在 冷却过程中的变形程度,为后续的模具优化和工艺调整 提供依据。
案例二:汽车保险杠冷却分析
总结词
优化冷却管道设计,缩短冷却时间,提高生产效率
详细描述
在汽车保险杠的注塑过程中,通过CAE技术进行冷却 分析可以优化模具中的冷却管道设计。通过模拟冷却 过程中的温度场分布和冷却时间,可以找到最佳的管 道布局和冷却液温度,从而缩短冷却时间,提高生产 效率。
案例三:医疗用品成型过程模拟
塑料制品质量预测
通过模拟塑料在注塑过程中的流动 和冷却过程,注塑模CAE可以预测 塑料制品的质量和可靠性,如尺寸 精度、翘曲变形等。
7材料成型过程的计算机模拟——MOLDFLOW
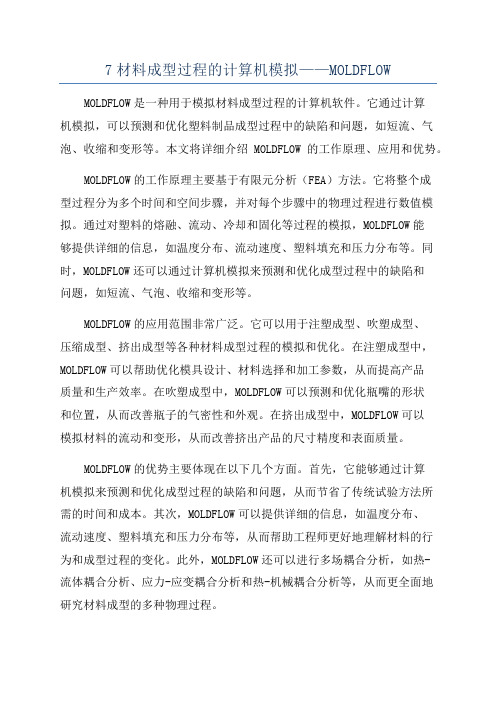
7材料成型过程的计算机模拟——MOLDFLOW MOLDFLOW是一种用于模拟材料成型过程的计算机软件。
它通过计算机模拟,可以预测和优化塑料制品成型过程中的缺陷和问题,如短流、气泡、收缩和变形等。
本文将详细介绍MOLDFLOW的工作原理、应用和优势。
MOLDFLOW的工作原理主要基于有限元分析(FEA)方法。
它将整个成型过程分为多个时间和空间步骤,并对每个步骤中的物理过程进行数值模拟。
通过对塑料的熔融、流动、冷却和固化等过程的模拟,MOLDFLOW能够提供详细的信息,如温度分布、流动速度、塑料填充和压力分布等。
同时,MOLDFLOW还可以通过计算机模拟来预测和优化成型过程中的缺陷和问题,如短流、气泡、收缩和变形等。
MOLDFLOW的应用范围非常广泛。
它可以用于注塑成型、吹塑成型、压缩成型、挤出成型等各种材料成型过程的模拟和优化。
在注塑成型中,MOLDFLOW可以帮助优化模具设计、材料选择和加工参数,从而提高产品质量和生产效率。
在吹塑成型中,MOLDFLOW可以预测和优化瓶嘴的形状和位置,从而改善瓶子的气密性和外观。
在挤出成型中,MOLDFLOW可以模拟材料的流动和变形,从而改善挤出产品的尺寸精度和表面质量。
MOLDFLOW的优势主要体现在以下几个方面。
首先,它能够通过计算机模拟来预测和优化成型过程的缺陷和问题,从而节省了传统试验方法所需的时间和成本。
其次,MOLDFLOW可以提供详细的信息,如温度分布、流动速度、塑料填充和压力分布等,从而帮助工程师更好地理解材料的行为和成型过程的变化。
此外,MOLDFLOW还可以进行多场耦合分析,如热-流体耦合分析、应力-应变耦合分析和热-机械耦合分析等,从而更全面地研究材料成型的多种物理过程。
总之,MOLDFLOW是一种用于模拟材料成型过程的计算机软件。
它通过计算机模拟,可以预测和优化塑料制品成型过程中的缺陷和问题,如短流、气泡、收缩和变形等。
MOLDFLOW的工作原理基于有限元分析方法,它能够模拟塑料的熔融、流动、冷却和固化等过程,并提供详细的信息。
《材料成型技术基础》中计算机辅助成型工艺的研究及进展

《 料 成 型 技 术基 础 》 材 中 计 算 机 辅 助 成 型 工 艺 的研 究及 进 展
济南大学 王 守仁 王 慧 崔 焕 勇
摘要 : 论述了材料成型计算机模拟技术在材料成型领域特别是金属液态成形工艺、 金属塑性成型工艺、 连接成型工
艺三 大 领 域 的 应 用 和 目前 的发 展 趋 势 与 方 向 . 学科 前 沿 角度 对 相 关课 程 教 育 教 学起 到 一 定 引导 作 用 。 从
一
件 产 生 应 力 的 可 能 降低 到 最 低 限 度 , 而 保 证 铸 件 的质 量 。 从 但 铸 金属液 态成 型技术是材料通 过改变物理状态 , 实现“ 固态 由 于 铸 件 的结 构 、 型 材 料 对 铸 件 凝 固过 程 的 影 响 是 非 常 复 这种模拟计算 本身也很 复杂 , 以, 所 应力 的模 拟仍 有很 液态一固态” 的转 变 , 次 性 成 型 来 完 成 产 品生 产 的 工 艺 过 杂 的, 一
迅猛发展 , 成为该领 域最为活跃的研究热点及技术前 沿 。
一
近2 O多年来 , 材料成型技术 的计算机 工艺模 拟技术得 到 应 力 的 形 成 不 仅 影 响 铸 件 最 终 的质 量 和 使 用 效 果 ( 纹 变 形 裂 等 ) 而且 影 响 工艺 设 计 的 质量 ( 缩量 的 准确 给 定等 ) , 收 。如果
、
金 属液 态 成 型 计 算 机 模 拟 技 术
能 模 拟 出铸 件 在 给 定 工 艺 下 的 应 力 分 布 . 可 修 改 工 艺 把铸 就
程。 其成型工艺过程复杂 , 生产周期长 , 响因素多 , 影 质量难 以 长 的 路 要 走 。 控 制 。而 计 算机 的迅 速 发展 使得 解 决 这 些 长 期 阻 碍 铸 造 生 产 4 铸 件 微 观 组 织数 值 模 拟 .
提高《材料成型计算机模拟》课程的实践教学质量研究

法, 使学生理解有限元求解问题的本质即可。
决 问题, 积累经验 , 这样就可事半功倍。 材料成型本科
在具备上述理论的基础上 ,学生容易从 根本上 生 以往 所 学 的理 论 知识 较 多 ,在 过 去学 习 的时候 往 清楚地理解模拟软件 , 使学习过程变得轻松 。比如工 往 比较盲 目, 并且不知道所学知识今后 的用途 , 而学 程中梁的问题分析 ,目的是求解系统中每根梁的受 习计算机 模拟软件 可建立起 理论 与实践 沟通 的桥 力和变形情况 ,原理采用力学中梁所受载荷与变形 梁 , 使学生能够感 到所学的知识 的应用价值 , 并可激 之 间 的关 系 , 以及 静 力 平衡 方 程 , 简 化 处理 后 得 到线 发出对专业的热爱。 比如对 D E F O R M软件, 教师在完 性代数方程{ F [ K] { 6} , 有限元软件就是有限元 成 一个 镦 粗 实例 的教 学基 础 上 ,还 应该 布置 一 些作 方法 通过 求解 上述 方程组 得 出 目标结 果 。 为达 到更 好 业和练 习, 如开展冲裁实例的模拟 , 这样既加深 了学 的教学效果 , 教师可进一步将材料力学方法和有 限元 生对软件 的理解和使用 ,同时还进一步加强 了学生
《 材料成型计算机模拟》 是随着计算机技术 的飞 4 0 h , 迄今 已连续 1 0 届开设此课程 。
速发展和现代塑性有限元理论的逐步成熟而诞生 的 材料成形过程是极其复杂的高温 、 动态和瞬时过 门新开课程 , 2 0 0 2 年起正式作为我校材料成型及 程 , 难以直接观察。 为了获得优质构件 , 必须控制制备
我 们 反 复 认 真研 讨 ,后 经 学 校 教 学 评 价 中 心专
1 掌握理论
目前 应 用 较 为 广泛 的分析 软件 大 多 数 是基 于有 家组充分论证 , 我们 向学校主管部 门提出了修改教学 限元 理 论 开 发 的 , 因此 , 必须 首 先 让 学生 理 解 利用 有 计划的申请 , 决定依托多年来形成的教师队伍条件和 限元 方 法 解 决 工程 问 题 的原 理 。学 生 只有 具 备 了 比 学校计算机仿真实验室装备条件 , 为材料成型及控制 较扎 实 的理 论基 础 ,才有 可 能 对 所分 析 的 问题 有 比 工程专业本科生开设《 材料成型计算机模拟》 课程 。 此 较准确的预测和判断。可以说 , 理论水平 的高低材料成型及控制工 过程使材料的成分、 工艺 、 组织与性能处于最佳状态,
南昌大学2014-2015-1学期个性课课表

纪昌品 林刚,阮禄章,欧阳珊,夏斌,王尚洪 辛天蓉 姜水生,姜水生 陈钢 许小明 许小明 胡东平 陈友华 陈友华 习青华 谢建宏 吴禄慎 廖小建,廖小建 彭杰 欧阳志强 欧阳志强 赵刚 赵刚 赵刚 韩艺 张明锋 陆明 陈奇伟 陆明 吴晓红 郭朝晖
讲师 副教授,教授,教授,教授,副教授 讲师 教授,教授 副教授 副教授 副教授 讲师 副教授 副教授 讲师 副教授 教授 教授,教授 副教授 讲师 讲师 讲师 讲师 讲师 副教授 副教授 讲(Ⅱ) 机械制造技术应用 机械制造装备设计 建筑材料(Ⅱ) 建筑法规 交通工程学 节目主持人通论 金融学 金融学 金融学 金融学 金融学 金融学 金融学 金融学 经济学 经济学原理 经济学原理 客户关系管理 空调用制冷技术 控制工程专题 跨文化管理 领导科学 流体输配管网 伦理学 媒介经营管理
经济管理学院 信息工程学院 法学院 法学院 机电工程学院 经济管理学院 经济管理学院 经济管理学院 经济管理学院 经济管理学院 经济管理学院 经济管理学院 资源环境与化工学院 法学院 资源环境与化工学院 资源环境与化工学院 经济管理学院 经济管理学院 经济管理学院 经济管理学院 经济管理学院 建筑工程学院 信息工程学院 法学院 体育与教育学院 外国语学院 生命科学与食品工程学院
2 2 2 2 2 2 2 2 3 3 2 2 1.5 3 2 3 3 2 2 2 3 3 32 32 32 3 3 2014-12-28
40 32 32 36 32 32 32 32 48 48 40 32 24 48 32 48 48 32 32 32 48 48 32 32 32 48 48
24 32 32 32 32 32 32 32 48 48 24 32 24 48 32 48 48 32 32 32 48 48 32 32 32 48 48
反应注射成型过程的计算机模拟
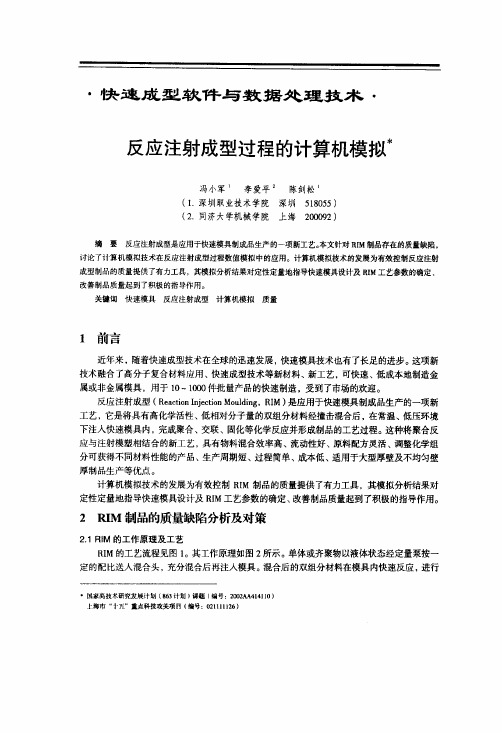
反应注射成型过程的计算机模拟’
・99・4.2关于结果的讨论
(1)充模时间的模拟结果给出了观察RIM充填过程的最佳方式。
可据此判断浇注口位置是否合理,以及可能发生充填不足的地方,为合理设计模具提供了依据。
模拟结果显示材料充填情况良好,说明模具结构是合理的。
(2)对剪切应力分布的模拟有助于分析制品应力集中的位置,判断最大应力是否超过材料许用值。
据此可分析模具及制品结构设计的合理性。
模拟结果未发现有超过材料许用应力的现象。
(3)分析RIM过程中的压力分布状况,可了解锁模及飞边的情况,以及材料充填情况。
图示分析结果表明
圈6几个t要的计算机分析模拟结果
反应注射成型过程的计算机模拟
作者:冯小军, 李爱平, 陈剑松
作者单位:冯小军,陈剑松(深圳职业技术学院(深圳)), 李爱平(同济大学机械学院(上海))本文链接:/Conference_5104306.aspx。
DEFORM实验报告

铜陵学院课程实验报告实验名称圆柱体压缩过程模拟实验课程材料成型计算机模拟指导教师张金标. 专业班级10 材控(2)姓名孟来福学号 1 0 1 0 1 2 1 0 5 82013年05月14日实验一 圆柱体压缩过程模拟1 实验目的与内容1.1 实验目的进一步熟悉AUTOCAD 或PRO/E 实体三维造型方法与技艺,掌握DEFORM 软件的前处理、后处理的操作方法与热能,学会运用DEFORM 软件分析压缩变形的变形力学问题。
1.2 实验内容运用DEFORM 模拟如图1所示的圆柱坯压缩过程。
(一)压缩条件与参数锤头与砧板:尺寸200×200×20mm ,材质DIN-D5-1U,COLD ,温度室温。
工件:材质DIN_CuZn40Pb2,尺寸如表1所示,温度室温。
(二)实验要求砧板工件锤头图1 圆柱体压缩过程模拟(1)运用AUTOCAD或PRO/e绘制各模具部件及棒料的三维造型,以stl格式输出;(2)设计模拟控制参数;(3)DEFORM前处理与运算(参考指导书);(4)DEFORM后处理,观察圆柱体压缩变形过程,载荷曲线图,通过轴对称剖分观察圆柱体内部应力、应变及损伤值分布状态;(5)比较方案1与2、3与4、1与3和2与4的模拟结果,找出圆柱体变形后的形状差别,说明原因;(6)提交分析报告(纸质和电子版)、模拟数据文件、日志文件。
2 实验过程2.1工模具及工件的三维造型根据给定的几何尺寸,运用AUTOCAD或PRO/E分别绘制坯料、锤头和砧板的几何实体,文件名称分别为workpiece,topdie,bottomdie,输出STL格式。
2.2 压缩过程模拟2.2.1 前处理建立新问题:程序→DEFORM5.03→File→New Problem→Next→在Problem Name栏中填写“Forging”→ Finish→进入前前处理界面;单位制度选择:点击Simulation Conrol按钮→Main按钮→在Units栏中选中SI (国际标准单位制度)。
材料成型计算机控制课件

定值存在偏差时,及时调整控制信号,以保证材料成型的稳定性和一致
性。
03
优化与决策
通过对材料成型过程的实时监控和数据分析,可以不断优化生产工艺和
流程,提高生产效率和产品质量。同时,根据市场需求和产品特点,可
以制定相应的生产计划和决策方案。
03
材料成型计算机控制技术
加热控制技术
01
02
03
加热温度控制
材料成型计算机控制课件
目录
• 材料成型计算机控制概述 • 材料成型计算机控制系统 • 材料成型计算机控制技术 • 材料成型计算机控制的实践应用 • 材料成型计算机控制的挑战与未来发展 • 材料成型计算机控制课件总结与展望
01
材料成型计算机控制概述
材料成型的基本概念
材料成型是通过物理或化学手段,将原材料转化为具有特定形状和性能的制件的过 程。
计算机控制系统可以实现生产 过程的自动化和智能化,提高 生产效率和产品质量。
材料成型计算机控制的发展趋势
材料成型计算机控制技术不断发 展,向着更加智能、高效、节能
的方向发展。
人工智能、机器学习等技术在材 料成型计算机控制中得到应用, 实现了工艺参数的智能优化和控
制。
物联网、云计算等技术在材料成 型计算机控制中得到应用,实现 了远程监控和生产数的实时分
根据材料成型的需求,精 确控制加热温度,以保障 成型质量。
加热时间控制
根据成型工艺需求,精确 控制加热时间,以保障材 料充分加热。
加热功率控制
根据成型工艺需求,精确 控制加热功率,以保障材 料加热均匀。
液位控制技术
液位检测
通过液位传感器实时检测 液位高度,确保液位稳定 。
液位调节
材料成型计算机模拟分析(各种仿真软件介绍)课件

• 4) 塑性理论中关于塑性应力应变关系与硬化 模型有多种理论,材料属性有的与时间无关, 有的则是随时间变化的粘塑性问题;于是,采 用不同的理论本构关系不同,所得到的有限元 计算公式也不一样。
• 5) 对于一些大变形弹塑性问题,一般包含材 料和几何两个方面的非线性,进行有限元计算 时必需同时单元的形状和位置的变化,即需采 用有限变形理论。而对于一些弹性变形很小可 以忽略的情况,则必需考虑塑性变形体积不变 条件,采用刚塑性理论。
27
• 结构静力分析用来求解外载荷引起的位移、应 力和力。静力分析很适合于求解惯性和阻尼对 结构的影响并不显著的问题。ANSYS 程序中的 静力分析不仅可以进行线性分析,而且也可以 进行非线性分析,如塑性、蠕变、膨胀、大变 形、大应变及接触分析。结构非线性导致结构 或部件的响应随外载荷不成比例变
• 化。ANSYS 程序可求解静态和瞬态非线性问题, 包括材料非线性、几何非线性和单元非线性三 种。
34
弹塑性有限元
• 在塑性变形过程中,如果弹性变形不能忽略并 对成形过程有较大的影响时,则为弹塑性变形 问题,如典型的板料成形。在弹塑性变形中, 变形体内质点的位移和转动较小,应变与位移 基本成线性关系时,可认为是小变形弹塑性问 题;而当质点的位移或转动较大,应变与位移 为非线性关系时,则属于大变形弹塑性问题; 相应地有小变形弹塑性有限元或大变形(有限 变形)弹塑性有限元。
24
25
有限元软件ANSYS
• ANSYS 软件是由世界上最大的有限元分析软件公司之 一的美国ANSYS 开发,是集结构、流体、电场、
• 磁场、声场分析于一体的大型通用有限元分析软件。
• ANSYS 的前处理模块提供了一个强大的实体建模及网 格划分工具,用户可以方便地构造有限元模型。
材料成形过程模拟仿真

MSC.Mvision
MSC.Mvision 是一个全面商品化的材料数据信息系统,包括 大量应用于航空航天和汽车行业的 材料数据,可以为用户提供 最丰富、最广泛的材料数据信息,如材料的构成图象(含金相), 材料的成分含量,材料的各种特性数据,材料数据的测试环境 信息,生产厂家及材料出厂牌号数据等,并可将材料特性作为 设计变量用于设计、分析阶段的整个过程。Mvision的材料构 造器和评估器可帮助用户建立和评估自己的材料数据信息系统。
将具有无限个自由度的连续体看成只具有有限个自由 度的单元集合体。 单元之间只在指定节点处相互铰接,并在节点处引入 等效相互作用以代替单元之间的实际相互作用。 对每个单元选择一个函数来近似描述其物理量,并依 据一定的原理建立各物理量之间的关系。 最后将各个单元建立起来的关系式加以集成,就可得 到一个与有限个离散点相关的总体方程,由此求得各 个离散点上的未知量,得到整个问题的解。
Laboratory of Materials Numerical Simulation 2008/10
塑性成型过程数值模拟的必要性
现代制造业的高速发展,对塑性成形工艺分析和模具设 计方面提出了更高的要求 。 若工艺分析不完善、模具设计不合理或材料选择不当, 则会在成型过程中产生缺陷,造成大量的次品和废品, 增加了模具的设计制造时间和费用。 传统工艺分析和模具设计,主要依靠工程类比和设计经 验,反复试验修改,调整工艺参数以消除成形过程中的 失稳起皱、充填不满、局部破裂等产品缺陷,生产成本 高,效率低。 随着计算机技术及材料加工过程数值分析技术的快速 发展,可以在计算机上模拟材料成型的整个过程,分析 各工艺参数对成型的影响,优化设计。
Laboratory of Materials Numerical Simulation 2008/10
deform挤压模拟课程设计

.课题: 材料成型计算机模拟系别: 机械工程学院专业班级: 11级材控1班指导教师: 张金标组别: 第五组2014年6月第一章课程设计内容及任务分配 ............................................................................................................................. - 1 - 1.1 概述................................................................................................................................................................................. - 1 - 1.2 设计目的 ....................................................................................................................................................................... - 1 - 1.3 设计内容 ....................................................................................................................................................................... - 1 - 1.4 设计要求 ....................................................................................................................................................................... - 2 - 1.5 挤压方案任务分配..................................................................................................................................................... - 2 - 第二章工艺参数.............................................................................................................................................................. - 3 - 2.1 工艺参数的设计.......................................................................................................................................................... - 3 - 2.1.1 摩擦系数的确定....................................................................................................................................................... - 3 - 2.1.2 挤压速度的确定....................................................................................................................................................... - 3 - 2.1.3 工模具预热温度的确定......................................................................................................................................... - 3 - 第三章模具尺寸的确定................................................................................................................................................ - 4 - 3.1 挤压工模具示意图..................................................................................................................................................... - 4 - 3.2 模具尺寸的确定.......................................................................................................................................................... - 4 - 3.2.1挤压模结构尺寸的确定.......................................................................................................................................... - 4 - 3.2.2 挤压筒结构尺寸的确定......................................................................................................................................... - 6 - 3.2.3 挤压垫的结构及尺寸确定.................................................................................................................................... - 7 - 第四章实验模拟及数据提取分析........................................................................................................................... - 8 - 4.1挤压工模具及工件的三维造型............................................................................................................................... - 8 - 4.2 挤压模拟 ....................................................................................................................................................................... - 8 - 4.3 后处理............................................................................................................................................................................ - 9 - 4.4分析数据......................................................................................................................................................................... - 9 - 4.5 坯料温度对挤压力的影响.....................................................................................................................................- 10 - 4.6 坯料预热温度对破坏系数的影响 .......................................................................................................................- 11 - 个人小结..............................................................................................................................................................................- 12 - 参考文献..............................................................................................................................................................................- 23 - 附表《塑性成型计算机模拟》课程设计成绩评定表第一章课程设计内容及任务分配1.1 概述挤压是对放在容器(挤压筒)内的金属坯料施加外力,使之从特定的模孔中流出,获得所需要断面形状和尺寸的一种塑性加工方法,有正挤压、反挤压、组合挤压、连续挤压、静液挤压等多种形式。
注塑成型过程仿真模拟

注塑成型过程仿真模拟注塑成型过程仿真模拟注塑成型是一种常用的塑料加工方法,通过在模具中加热和压力的作用下,将熔融的塑料材料注入模具中,形成所需的产品形状。
然而,在实际生产中,由于材料和工艺的复杂性,注塑成型过程中常常会出现一些问题,如产品缺陷、模具磨损等。
为了解决这些问题,提高生产效率和产品质量,注塑成型过程仿真模拟应运而生。
注塑成型过程仿真模拟是利用计算机技术对注塑成型过程进行数字化模拟和分析的方法。
通过建立注塑成型的数学模型,并运用计算流体力学和有限元分析等方法,可以模拟和预测材料的流动、温度分布、变形等情况,从而优化模具设计和工艺参数,提高生产效率和产品质量。
注塑成型过程仿真模拟的基本流程包括几何建模、网格划分、物理参数设定、边界条件设定、数值计算和结果分析等步骤。
首先,根据实际产品的几何形状,利用计算机辅助设计软件进行三维几何建模。
然后,将几何模型转化为计算所需的网格模型,即将几何体划分为无数小的单元格,以便进行数值计算。
接下来,根据材料的物理参数,设定模拟过程中的温度、压力、速度等参数,并确定边界条件,如模具表面的温度和压力。
然后,利用数值方法对模型进行计算,得出模拟结果。
最后,对模拟结果进行分析,评估模具设计和工艺参数的合理性,并根据需求进行优化。
注塑成型过程仿真模拟具有多方面的优势。
首先,它可以提前发现和解决注塑成型过程中可能出现的问题,如翘曲、热应力、气泡等缺陷,从而避免因产品缺陷导致的生产损失。
其次,它可以优化模具设计和工艺参数,提高生产效率和产品质量。
再次,它可以减少试模次数,节省原材料和时间成本。
此外,注塑成型过程仿真模拟还可以提供详细的数值结果和可视化的模拟图像,为工程技术人员提供参考和决策依据。
总之,注塑成型过程仿真模拟是一种有效的工具,可以帮助企业解决注塑成型过程中的问题,提高生产效率和产品质量。
随着计算机技术的不断发展和成熟,注塑成型过程仿真模拟将会得到更广泛的应用和推广。
Deform圆柱体压缩过程模拟.
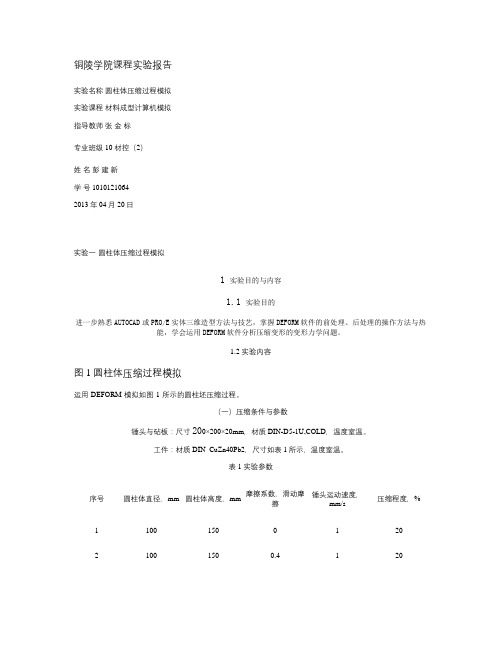
铜陵学院课程实验报告实验名称圆柱体压缩过程模拟实验课程材料成型计算机模拟指导教师张金标专业班级 10 材控(2)姓名彭建新学号 10101210642013年04月20日实验一圆柱体压缩过程模拟1 实验目的与内容1.1 实验目的进一步熟悉AUTOCAD或PRO/E实体三维造型方法与技艺,掌握DEFORM软件的前处理、后处理的操作方法与热能,学会运用DEFORM软件分析压缩变形的变形力学问题。
1.2 实验内容图1 圆柱体压缩过程模拟运用DEFORM模拟如图1所示的圆柱坯压缩过程。
(一)压缩条件与参数锤头与砧板:尺寸200×200×20mm,材质DIN-D5-1U,COLD,温度室温。
工件:材质DIN_CuZn40Pb2,尺寸如表1所示,温度室温。
表1 实验参数序号圆柱体直径,mm 圆柱体高度,mm 摩擦系数,滑动摩擦锤头运动速度,mm/s压缩程度,%1 100 150 0 1 202 100 150 0.4 1 203 100 250 0 1 204 100 250 0.4 1 20(二)实验要求(1)运用AUTOCAD或PRO/e绘制各模具部件及棒料的三维造型,以stl格式输出;(2)设计模拟控制参数;(3)DEFORM前处理与运算(参考指导书);(4)DEFORM后处理,观察圆柱体压缩变形过程,载荷曲线图,通过轴对称剖分观察圆柱体内部应力、应变及损伤值分布状态;(5)比较方案1与2、3与4、1与3和2与4的模拟结果,找出圆柱体变形后的形状差别,说明原因;(6)提交分析报告(纸质和电子版)、模拟数据文件、日志文件。
2 实验过程2.1工模具及工件的三维造型根据给定的几何尺寸,运用AUTOCAD或PRO/E分别绘制坯料、锤头和砧板的几何实体,文件名称分别为workpiece,topdie,bottomdie,输出STL格式。
2.2 压缩过程模拟2.2.1 前处理建立新问题,单位制度选择,添加对象,定义对象的材料模型,调整对象位置关系,模拟控制设置,实体网格化,设置对象材料属性,设置主动工具运行速度,工件体积补偿,边界条件定义,保存k文件,2.2.2 生成库文件在工具栏上点击Database generation按钮在Type栏选中New选项选择路径(英文)填入数据库文件名(英文),如forging 点击Check按钮没有错误信息则点击Generate按钮完成模拟数据库的生成。
dynaform作业
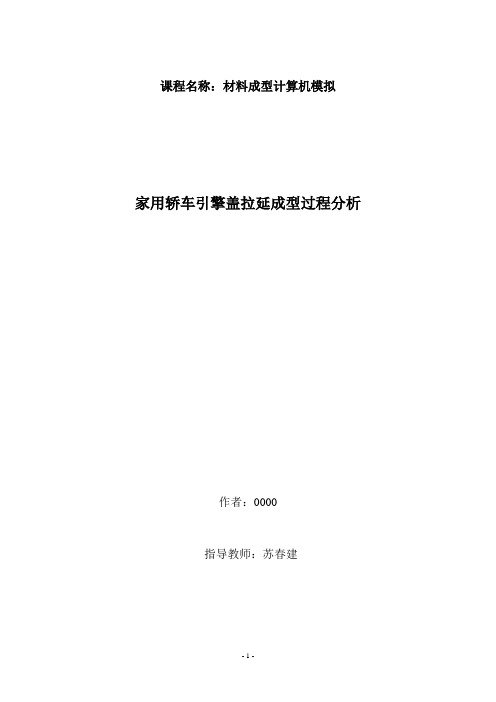
课程名称:材料成型计算机模拟家用轿车引擎盖拉延成型过程分析作者:0000指导教师:苏春建图1操作目录一.创建Dynaform数据二.导入模型三.划分网格四.检查和修补网格五.自动调节冲压方向六.创建压料面七.创建工艺补充面八.压料面的裁剪九.创建板料十.排样输出报告十一.偏移出Punch十二.创建压边圈十三.偏移出压边圈和凸模十四.工具定义十五.工具摘要十六.自动定位工具十七.测量Die的运动行程十八.定义Die的运动曲线十九.定义压边圈的压力曲线二十.预览工具的运动二十一.设置分析参数,求解计算二十二.后处理一.创建Dynaform数据库启动dynaform软件后,程序自动创建默认的数据库和文件Untitled.df 。
选择Fil e→save as 菜单项,修改文件名,将所建立的数据库保存在自己指定的目录下。
二.倒入模型选择File-Import菜单项,将上面建立的part.igs的模型文件(如图1)分别倒入数据库中,选择Parts-edit菜单项,在对话框中修改零件层的名称为PART。
三.自由划分网格1>选择菜单DFE,再选择Mesh Tool。
2>选择Select Surface按钮。
3>点击Displayed Surf按钮选择所有的曲面,点击OK接受所有高亮度显示的曲面。
4>如图2,在参数组中输入最大单元尺寸为1000mm,最小单元尺寸为200mm,点击Apply,点击Yes接受划分的网格,点击Exit退出曲面网格划分对话框(如图3)。
图3 图2四.检查和修补网格1>选择DFE-Preparation-MODER CHECK。
图42>点击Boundary Display图标,点击按钮<Clear hightlight>清楚高亮显示的边界(如图5)。
3>点击Plate Normal图标,查看消息提示框确认所有单元的法向量方向一致(如图6)。
- 1、下载文档前请自行甄别文档内容的完整性,平台不提供额外的编辑、内容补充、找答案等附加服务。
- 2、"仅部分预览"的文档,不可在线预览部分如存在完整性等问题,可反馈申请退款(可完整预览的文档不适用该条件!)。
- 3、如文档侵犯您的权益,请联系客服反馈,我们会尽快为您处理(人工客服工作时间:9:00-18:30)。
2.2 网格划分成功
3.物性参数Visual-Cast
3.0 参数设置流程
3.1 模拟参数设置 3.2 定义实体单元类型 3.3 换热系数 3.4 运行条件设置 3.5 重力方向
3.1 模拟参数设置
3.2 定义实体单元类型
3.3 换热系数
3.4 运行条件设置
3.5 重力方向
(3). 计算机模拟分析
由于铸件技术要求中不允许出现裂纹,对铸件应力场进行模拟。如图3.12所示,模拟 铸件热裂与冷裂。可以看出浇注系统和冒口的合理设置、浇注温度和开箱时间的适 当,避免了较大的收缩应力和应力集中,且没有妨碍到铸件的正常收缩,使得热裂 与冷裂显著减少。
谢谢 观赏
材料成型计算机模拟
——铝合金壳体
班级:成型1304班 主讲:张阳 (20132384) 成员:杨梦奇 (20132354)
蔡圣 (20132379)
一、设计流程
➢1.实体建模 ➢2.分析材料,技术要求确定模拟(微观组织,应力场等) ➢3.运用模拟软件模拟,根据模拟结果分析缺陷,再重新设计工艺方案
(冷铁,冒口,出气孔,浇筑系统等) ➢4.确定最终方案,完成说明书(工艺,工装)
二、软件介绍——PROCAST
三、模拟流程
1.造型实体导入软件 2.网格划分。(Visual-Mesh)
软件界面示意
3.物性赋值(各种物理参数)(Visual-Cast)
ห้องสมุดไป่ตู้
4.观察运行结果(Visual-Viewer)
2.划分网格Visual-Mesh
2.1 划分网格流程
1.检查表面连接 2.合并相交面 3.检查并分离相交体
四、模拟结果Visual-Viewer
五、模拟结果分析与改进
• (1)铸件充型过程的模拟分析 • (2)补缩系统的分析与改进 • (3)计算机模拟分析
(1). 铸件充型过程的模拟与分析
经过前期的模拟分析和比较,选择了该种浇注系统
(1). 铸件充型过程的模拟与分析
如图所示为 充型50%时 的速度场, 可以看出充 型较平稳。
(2). 补缩系统的分析与改进
优化方案:使用普通冒 口无法达到预期效果, 鉴于该铸件壁厚较薄, 且中间型腔较大,冒口 和冷铁的配合使用效果 不明显,保温冒口有较 好的补缩效果,故使用 保温冒口。将冒口优化 为保温冒口后,再次进 行模拟,由图3.9可见缩 松缩孔全部集中在冒口 的位置,该补缩系统设 计合理。
(1). 铸件充型过程的模拟与分析
右图为边缘凸台 (截面)缩松缩 孔现象,可以看 出边缘凸台无缩 松缩孔现象的存 在。
(2). 补缩系统的分析与改进
(2). 补缩系统的分析与改进
补缩方案一: 使用普通冒口 和出气孔进行 模拟,可见缩 松缩孔并未消 除。
(2). 补缩系统的分析与改进
为了进一步分析该方案缩松 缩孔缺陷产生的原因,我们 对该方案冒口浇注系统凝固 70%温度场进行分析,如图 所示。可以看出冒口金属液 过早凝固,早于厚大部位到 达固相线,冒口金属液无法 对厚大部位进行补缩。
(3). 计算机模拟分析
采用本工艺方案得 到不同时间的凝固 温度场,如图3.10所 示。可知,该铸件 凝固过程基本符合 由下到上、从外到 里的顺序凝固原则, 能获得内部致密、 表面完整的铸件。
(3). 计算机模拟分析
对铸件的不同时间的 速度场进行模拟分析, 如图3.11所示。可知, 整个充型过程为均匀 平稳,能够减少缺陷 的产生。
(1). 铸件充型过程的模拟与分析
分析: 铸件充型 100%时的Air Entrainment (裹气情况) 可以看出裹气 较少,该浇注 系统设置合理, 内浇道避开紊 流区。
(1). 铸件充型过程的模拟与分析
分析: 右图为铸件厚 大部位(截面) 的缩松缩孔现 象,缩孔缩松 分布较为集中, 利于设置冒口 的补缩。