汽车副车架装焊要点及其调整方法
车身前副车架安装点设计指南

车身前副车架安装点设计规范1 范围本标准规定了车身前副车架安装点设计要点及其判断标准等。
本标准适用于新开发的M1类和N1类汽车车身前副车架安装点设计。
2 规范性引用文件下列文件对于本文件的应用是必不可少的。
凡是注日期的引用文件,仅注日期的版本适用于本文件。
凡是不注日期的引用文件,其最新版本(包括所有的修改单)适用于本文件。
《GB 11566-2009 乘用车外部凸出物》《GB/T19234-2003 乘用车尺寸代码》《GB/T 709-2006 热轧钢板和钢带的尺寸、外形、重量及允许偏差》《GB/T 710-2008 优质碳素结构钢热轧薄钢板和钢带》《GB/T4780-2000 汽车车身术语》《整车车身设计公差与装配尺寸链分析》《螺栓连接的装配质量控制》3 术语和定义3.1 车身结构3.1.1车身结构是各个零件的安装载体。
3.2 副车架3.2.1副车架最早的应用原因是可以降低发动机舱传递到驾驶室的振动和噪音。
副车架与车身的连接点就如同发动机悬置一样。
通常一个副车架总成需要由四个悬置点与车身连接,这样既能保证其连接刚度,又能有很好的震动隔绝效果。
副车架能分5级减小震动的传入,对副车架来说,在性能上主要目的是减小路面震动的传入,以及提高悬挂系统的连接刚度,因此装有副车架的车驾驶起来会感觉底盘非常扎实,非常紧凑。
而副车架悬置软硬度的设定也面临着像悬挂调校一样的一个不可规避的矛盾。
所以工程师们在设计和匹配副车架时通常会针对车型的定位和用途选择合适刚度的橡胶衬垫。
由于来自发动机和悬挂的一部分震动会先到达副车架然后再传到车身,经过副车架的衰减后振动噪声会有明显改善。
副车架发展到今天,可以简化多车型的研发步骤。
这是因为悬挂、稳定杆、转向机等底盘零件都可以预先安装在一起,形成一个所谓的超级模块,然后再一起安装到车身上。
3.3前副车架安装点3.3.1前副车架安装点指安装在车身的安装孔中心线与安装面下平面交点的位置(XYZ 坐标)及装配孔公称尺寸。
汽车副车架焊接变形及控制方法
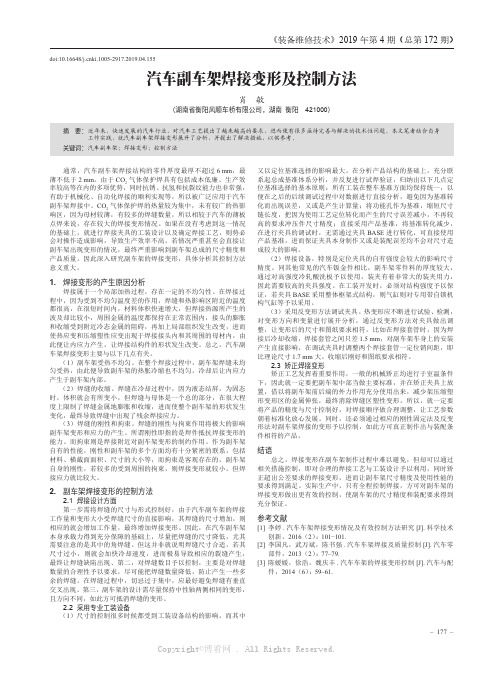
– 177 –《装备维修技术》2019年第4期(总第172期)doi:10.16648/ki.1005-2917.2019.04.155汽车副车架焊接变形及控制方法肖敏(湖南省衡阳风顺车桥有限公司,湖南 衡阳 421000)摘要: 近年来,快速发展的汽车行业,对汽车工艺提出了越来越高的要求,进而便有很多亟待完善与解决的技术性问题。
本文笔者结合自身工作实践,就汽车副车架焊接变形展开了分析,并提出了解决措施,以供参考。
关键词: 汽车副车架;焊接变形;控制方法通常,汽车副车架焊接结构的零件厚度最厚不超过6mm ,最薄不低于2mm 。
由于CO 2气体保护焊具有包括成本低廉、生产效率较高等在内的多项优势,同时抗锈、抗氢和抗裂纹能力也非常强,有助于机械化、自动化焊接的顺利实现等,所以被广泛应用于汽车副车架焊接中。
CO 2气体保护焊的热量较为集中,未有较广的热影响区,因为母材较薄,有较多的焊缝数量,所以相较于汽车的薄板点焊来说,存在较大的焊接变形情况。
如果在没有考虑到这一情况的基础上,就进行焊接夹具的工装设计以及确定焊接工艺,则势必会对操作造成影响,导致生产效率不高,若情况严重甚至会直接让副车架出现变形的情况,最终严重影响到副车架总成的尺寸精度和产品质量。
因此深入研究副车架的焊接变形,具体分析其控制方法意义重大。
1. 焊接变形的产生原因分析焊接属于一个局部加热过程,存在一定的不均匀性。
在焊接过程中,因为受到不均匀温度差的作用,焊缝和热影响区附近的温度都很高,在很短时间内,材料体积快速增大,但焊接热源所产生的波及却比较小,周围金属的温度都保持在正常范围内,接头的膨胀和收缩受到附近冷态金属的阻碍,再加上局部组织发生改变,进而使热应变和压缩塑性应变出现于焊接接头内和其周围的母材内,由此便让内应力产生,让焊接结构件的形状发生改变。
总之,汽车副车架焊接变形主要与以下几点有关。
(1)副车架受热不均匀。
在整个焊接过程中,副车架焊缝未均匀受热,由此便导致副车架的热胀冷缩也不均匀,冷却后让内应力产生于副车架内部。
浅谈汽车副车架的焊接工艺

浅谈汽车副车架的焊接工艺李萌浩金超长城汽车股份有限公司技术中心,河北省汽车工程技术研究中心,河北保定 071000摘要:在汽车中,副车架作为汽车悬架的重要组成部分,同时也是汽车中底盘零部件的关键零件,它的焊接工艺是和它的整体质量有着密不可分的关系的。
本文就对汽车中的副车架的焊接定位和其焊接工艺进行深入的探讨。
关键词:汽车;副车架;焊接工艺中图分类号:TG44 文献标识码:A 文章编号:1671-5810(2015)60-0100-021 前副车架的分类按照前副车架的结构形式可分为2大类。
1.1 整体开放式结构焊接件的大块为大板型的结构,多为冲压板件合成焊接,承载和传递主要的负荷,其组成中有带稳定杆的连接支架、摆臂安装支架、转向器安装支架、差速器支架等结构件,完成前副车架的功能性作用,安装时四周辅以衬套管或衬套管支架与车身装配连接。
1.2 框架式封闭结构在前副车架主体上增加前横梁、纵梁,以增加防撞吸能的功能,功能更强。
广泛用于SUV的车型上,实际上是第一类前副车架的一种变型。
2 副车架制造工艺分析2.1 工艺流程在工艺流程和工序编排上,副车架架构清晰,分总成少,生产线多采用主体式一字线流水布局,过程清晰、分支少、过程稳定,过程能力指数CPK值高,有着很强的过程稳定性。
焊装工艺流程为:分总成焊接→主体焊装单元1→主体焊装单元2→主体焊装单元3→主体焊装单元n→焊后处理单元→补焊清渣单元→检测单元→成品打标。
2.2 焊接工艺成型要点2.2.1 副车架主体是大板冲压件的合成焊接,主体关键焊装工序采用上下板扣合的方式,先行将上下板扣合后进行焊接,上下板形成一个整体,因此焊接工艺采用焊接完成后待其有一定的焊接伸缩,释放部分的内应力,再与其他零件进行焊接。
工艺上要考虑焊接变形的影响,这种零件往往在上下板搭接处形成一条长焊缝,有的多达1m,甚至更长。
焊接完成后焊接变形不可避免,焊接变形按下式进行估算计算。
式中:k1为修正系数,与焊接方法和材料有关,见表1;aw为焊缝截面积,mm2;L为焊接长度,mm;A为构件截面积,mm2;△L为纵向总收缩变形量,mm。
副车架的安装形式及应注意的问题

副车架的安装形式及应注意的问题1. 引言副车架,在汽车领域中扮演着重要的支撑和稳定作用。
它的安装形式和相关注意事项直接关系到车辆的安全性和稳定性。
本文将全面评估副车架的安装形式及应注意的问题,并据此撰写一篇有价值的文章,以便读者更深入地理解和掌握这一重要主题。
2. 副车架的安装形式2.1 接触式副车架接触式副车架是直接连接到车辆底盘的副车架,能够提供更加牢固的支撑,适合用于承载重量较大的货车或越野车等车辆。
然而,在使用中需要注意接触面的保养和检查,以确保副车架的稳定性和安全性。
2.2 悬挂式副车架悬挂式副车架则是通过悬挂系统连接到车辆底盘的副车架,可以提供更加灵活的支撑和稳定。
它适合用于一般的轿车和小型车辆,但在安装时需要特别注意悬挂系统的调整和保养,以确保副车架与车辆的协调性和稳定性。
3. 应注意的问题3.1 安装位置选择在安装副车架时,需要根据车辆的结构和用途选择合适的安装位置。
不同的安装位置会对车辆的稳定性和操控性产生不同的影响,因此需要仔细考虑和评估。
3.2 固定方式副车架的固定方式通常包括螺栓固定和焊接固定两种。
在选择固定方式时,需要考虑到车辆本身的结构和材质,以及副车架的制造材料和工艺,以确保固定牢固且安全可靠。
3.3 副车架的材料和工艺副车架的材料和工艺直接关系到其承载能力和使用寿命。
要注意选择高强度、耐腐蚀的材料,并确保工艺精湛,以提高副车架的稳定性和安全性。
4. 总结与回顾通过全面评估副车架的安装形式及应注意的问题,我们深入探讨了接触式副车架和悬挂式副车架的特点,以及安装位置选择、固定方式和材料工艺等方面的注意事项。
这些内容为我们更深入地理解和掌握副车架的安装提供了重要的参考和指导。
在实际的使用中,我们需要根据车辆的实际情况和需要,结合专业建议,选择合适的副车架安装形式,并在安装过程中注意相关的问题,以确保车辆的安全和稳定。
5. 个人观点与理解对我来说,副车架的安装形式及应注意的问题是汽车安全和稳定性的重要保障,需要我们在选择、安装和使用过程中高度重视。
汽车车架的焊接修复工艺文档_(2)

汽车车架的焊接修复工艺车架是汽车装配的基础,汽车的绝大部分部件和总成其位置都是通过车架来固定的。
因此,车架是汽车的主要承载件,汽车处于静态时,车架所受载荷为静载荷。
它包括车架和车身的自身质量及安装在车架上各总成与附件的质量,有时还包括乘客和行李的质量。
汽车处于动态时,车架承受的载荷为动载荷。
汽车在平坦的道路上以较高车速行驶时会产生垂直动载荷,它的大小取决于作用在车架上的静载荷及其在车架上的分布,同时,还取决于静载荷作用处的垂直加速度值。
受这种载荷作用,车架会产生弯曲变形。
汽车在崎岖不平的路面上行驶时,前后几个车轮可能不在同一平面上而产生斜对称动载荷,这主要是汽车在不平道路上行驶产生的。
其大小取决于道路不平整度以及车身、车架和悬架的刚度。
受这种载荷作用,车架也会产生扭转变形。
另外,由于汽车的使用工况不是固定的,而是受道路、气候条件及其它因素影响而产生相当频繁且无规律的变化。
因此,车架所受动载荷除以上两种外,还将承受其它一些动载荷的作用。
例如,当汽车加速或制动时,会导致车架前、后部分的载荷重新分配;汽车转弯时,离心力将使车架受到侧向力的作用;经常行驶于坏路的汽车,还承受冲击载荷的作用等;当前一轮正面撞在路面凸包上时,将使车架产生水平方向的剪切变形;安装在车架上的各总成工作时所产生的力等;这些无规律且不断变化的载荷引起车架变形的形式和状况也是随机的。
因此,车架的基本变形除纯弯曲、纯扭转变形外,还有弯曲与扭转的复合变形。
通常,车架承受的是无规律的交变重复载荷,车架的损坏主要是疲劳损坏,其主要形式是断裂,而疲劳裂纹则起源于纵梁或横梁的边缘处。
1. 车架的焊接方法车架纵梁断裂的修补与加固应视其裂纹的长短及所在的部位,采取不同的修理方法。
(1)当裂纹较短且在受力不大的部位时,可直接用电火花焊修。
焊修时应在裂纹的末端钻直径5mm的止裂孔,以消除应力,防止裂纹扩展(如图1a,虚线为砂纸打磨范围)。
沿裂纹开焊修坡口,坡口为90°,深度为纵梁厚度的2/3(如图1b)。
汽车起重机副车架焊接变形的原因及预防工艺

文 章 编 号 :0 5 1 9 (0 2 0 —0 90 10 — 0 0 2 0 ) 50 2 — 2
汽 车起 重 机 副 车 架焊 接 变 形 的 原 因及 预 防 工 艺
钟 安 庆 , 维 斌 郭
( 州 重 型 机 械 股 份 有 限 公 司 , 宁 锦 州 1 1 0 ) 锦 辽 2 0 1
图 2 温 度 应 力 及 残 余 应 力 分 布 示 意 图
收 稿 日期 :2 0 — 42 0 20 — 0
作 者简 介 :钟安 庆 ( 9 7 ) 男 , 宁锦 州人 , 州 重型机 械股份 有 限公 司工程 师 。 1 5一 , 辽 锦
维普资讯
3 0
辽 宁 工 学院学报 ( 自然 科 学 版 )
第 2 第 5期 2卷
平 整性 和连 接 的稳 定性 。这是 在 焊 接两 道环 焊缝 过 程 中 , 由
2 纵 向弯 曲
在焊 接 过 程 中 , 不按 副 车 架 结 构 特点 确 定 工 艺 方法 , 如 会 出现纵 向弯 曲 。 () 车 架上 盖板 是 由三 块 厚 度 不 同的 钢 板 拼 接 而成 , 1副 见 图 3 因为上盖 板有 两道 横焊 缝 , 车架 纵截 面上 焊缝分 布 . 使
摘
要 :从汽 车起 重机 副车 架 的两种 焊接 变形 , 析其 变形 的原 因 , 提 出相应 的工 艺措施 。 分 并
文献标 识 码 : B
关键 词 :副车 架 ; 焊接 ; 变形原 因 ; 艺措施 工
中 图分 类 号 : TG4 4 0
Ca e e d ng D e o m a i n a c us s of W l i f r to nd Te hn0l g c l 0 ia
汽车车架焊接变形及控制方法
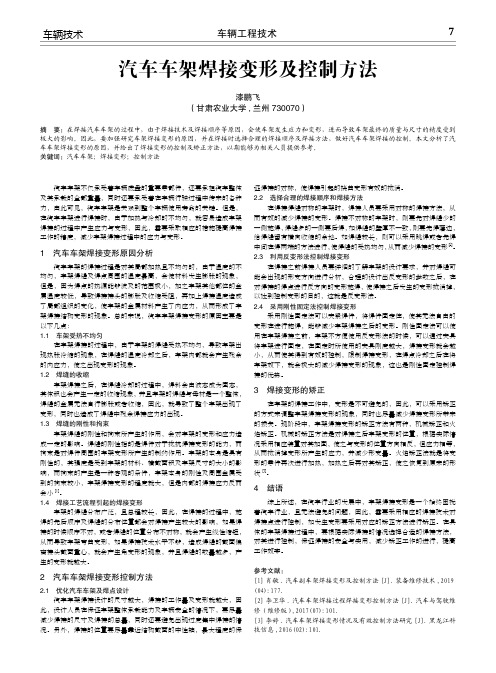
车辆工程技术7车辆技术 汽车车架不仅承受着车辆底盘的重要零部件,还要承担汽车整体及其承载的全部重量,同时还要承受着在车辆行驶过程中传来的各种力,由此可见,汽车车架是关系到整个车辆使用寿命的关键。
但是,在汽车车架进行焊接时,由于加热与冷却的不均匀,就容易造成车架焊接的过程中产生应力与变形,因此,需要采取相应的措施提高焊接工作的精度,减少车架焊接过程中的应力与变形。
1 汽车车架焊接变形原因分析 汽车车架的焊接过程是对其局部加热且不均匀的,由于温度的不均匀,车架焊缝及焊点周围的温度最高,会使材料发生膨胀的现象,但是,因为焊点的热源能够波及的范围极小,加之车架其他部位的金属温度较低,导致焊接接头的膨胀及收缩受阻,再加上焊接温度造成了局部组织的变化,使车架的金属材料产生了内应力,从而形成了车架焊接结构变形的现象。
总的来说,汽车车架焊接变形的原因主要是以下几点:1.1 车架受热不均匀 在车架焊接的过程中,由于车架的焊缝受热不均匀,导致车架出现热胀冷缩的现象,在焊缝的温度冷却之后,车架内部就会产生残余的内应力,使之出现变形的现象。
1.2 焊缝的收缩 车架焊接之后,在焊缝冷却的过程中,焊料会由液态成为固态,其体积也会产生一定的收缩现象,并且车架的焊缝与母材是一个整体,焊缝的金属无法自行膨胀或者收缩,因此,就导致了整个车架出现了变形,同时也造成了焊缝中残余焊接应力的出现。
1.3 焊缝的刚性和拘束 车架焊缝的刚性和拘束所产生的作用,会对车架的变形和应力造成一定的影响。
焊缝的刚性指的是焊件对于抵抗焊接变形的能力,而拘束是对焊件周围的车架变形所产生的制约作用。
车架的本身是具有刚性的,其强度是受到车架的材料、横截面积及车架尺寸的大小的影响,而拘束的产生是一种客观的条件,车架本身的刚性及周围金属受到的拘束较小,车架焊接变形的程度就大,但是内部的焊接应力反而会小[1]。
1.4 焊接工艺流程引起的焊接变形 车架的焊缝分布广泛,且总程较长,因此,在焊接的过程中,施焊的先后顺序及焊缝的分布位置都会对焊接产生较大的影响,如果焊接的时候顺序不对,或者焊缝的位置分布不对称,就会产生线性缩短,从而导致车架弯曲变形,如果焊接技术水平不够,造成焊缝的截面偏离接头截面重心,就会产生角变形的现象,并且焊缝的数量越多,产生的变形就越大。
汽车车架焊接工艺分析

汽车车架焊接工艺分析作者:刘美娜来源:《时代汽车》2019年第03期摘要:介绍汽车车架结构形式及分类,研究车架常用生产工艺形式,为实际生产过程中车架生产工艺的选择提供参考。
分析车架焊接工艺及流程,为车架焊接工艺的进一步优化奠定了基础。
关键词:车架;焊接;工艺流程车架设计作为新车型设计开发过程中的一项重要工作,已越来越受重视。
车架是整个汽车的基体,汽车上绝大多数部件和总成都是通过车架来固定其位置的。
车架的功能是支撑连接汽车的各个零部件,并承受来自车内外的各种载荷。
因此,车架的焊接性直接影响零部件的装配性、整车的耐久性能及碰撞性能等。
随着汽车工业技术的进步以及市场竞争愈加激烈,为缩减产品开发周期以及制造成本,对车型的平台化要求越来越高,需要更多的考虑工艺流程一致性设计[1]。
1 车架结构形式车架组成部分为前副车架和后副车架。
前副车架的结构形式一般可分为整体开放式结构和框架式封闭结构两大类。
整体开放式结构如图1所示,焊接件为大板型结构,多为冲压板件合成焊接,承载和传递主要负荷,其组成中有带稳定杆的连接支架、摆臂安装支架、转向器安装支架、差速器支架等结构件,完成前副车架功能性作用,安装时四周辅以衬套管或衬套管支架与车身装配连接。
典型框架式封闭结构如图2所示,在前副车架主体上增加前横梁、纵梁,以增加防撞吸能的功能,功能更强,广泛用于SUV的车型上,实际上是第一类前副车架的一种变型。
后副车架常见结构形式为框架式封闭结构和扭力梁结构,分别如图3、4所示。
2 车架工艺可行性分析目前国内生产车架的工艺方法为铆接和焊接两种方式。
大中型载重汽车的车架多采用铆接结构,而乘用车、皮卡、轻型货车的车架多采用焊接结构。
焊接结构也有两种,一种是冲压焊接结构,另外一种是矩形管焊接车架。
目前皮卡车和定位于越野功能的SUV车型的车架多采用冲压焊接结构,对于钢制车架焊接方法为CO2气体保护焊,对于铝制车架常采用CMT技术[2]。
2.1 焊接可行性分析焊接可行性分析是前/后副车架焊接工艺分析的主要内容,对副车架的焊接性分析最终应达到焊接操作最方便、焊接成本最低、焊接质量最优、焊接效率最高的目的。
常见副车架(厚板件)焊接基本技术
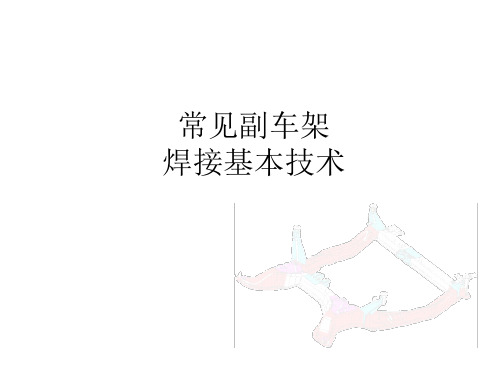
冷裂纹是在焊后冷却过程中产生的,大多产生在基体金属或基体金属与焊缝交界的熔合线上。 其产生的主要原因是由于热影响区或焊缝内形成了淬火组织,在高应力作用下,引起晶粒内部的 破裂,焊接含碳量较高或合金元素较多的易淬火钢材时,最易产生冷裂纹。
2) 焊缝过凹 因焊缝工作截面的减小而使接头处的强度降低。 3) 焊缝咬边 在工件上沿焊缝边缘所形成的凹陷叫咬边。它不仅减少了接头 工作截面,而且在咬边处造成严重的应力集中。 4) 焊瘤 熔化金属流到溶池边缘未溶化的工件上,堆积形成焊瘤,它与工件 没有熔合焊瘤对静载强度无影响,但会引起应力集中,使动载强度降低。 5) 烧穿 烧穿是指部分熔化金属从焊缝反面漏出,甚至烧穿成洞,它使接头 强度下降。
1、工件焊后一般都会产生变形,如 果变形量超过允许值,就会影响使用。
2、焊缝的外部缺陷 1)焊缝增强过高 如图所示,当焊
接坡口的角度开得太小或焊接电流 过小时,均会出现这种现象。焊件 焊缝的危险平面已从M-M平面过渡 到熔合区的N-N平面,由于应力集 中易发生破坏,因此,为提高压力 容器的疲劳寿命,要求将焊缝的增 强高铲平。
焊点结构如图所示:
R总
电极
ew w c
w
被焊工件
ew
电极
焊点结构示意图
δ——焊件板厚,d——电极直径, dn——熔核直径,dr——塑性环直径, hn——熔核高度,△——压痕深度。
点焊的原理图
其中R总——焊接区总电阻 Rew——电极与焊件之间接触电阻 Rw——焊件内部电阻 Rc——焊件之间接触电阻 电阻焊产生的热量公式:Q=I2Rt
2
8
2500--5000
3
汽车副车架焊接热变形控制方案分析 钱在
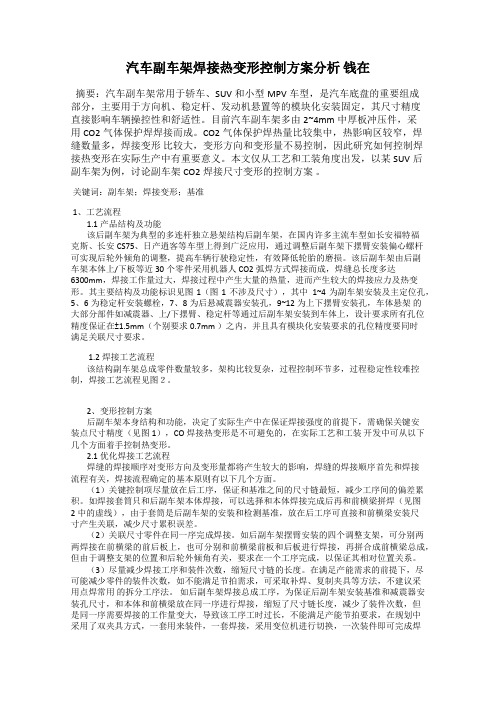
汽车副车架焊接热变形控制方案分析钱在摘要:汽车副车架常用于轿车、SUV和小型MPV车型,是汽车底盘的重要组成部分,主要用于方向机、稳定杆、发动机悬置等的模块化安装固定,其尺寸精度直接影响车辆操控性和舒适性。
目前汽车副车架多由2~4mm中厚板冲压件,采用CO2气体保护焊焊接而成。
CO2气体保护焊热量比较集中,热影响区较窄,焊缝数量多,焊接变形比较大,变形方向和变形量不易控制,因此研究如何控制焊接热变形在实际生产中有重要意义。
本文仅从工艺和工装角度出发,以某SUV后副车架为例,讨论副车架CO2焊接尺寸变形的控制方案。
关键词:副车架;焊接变形;基准1、工艺流程1.1产品结构及功能该后副车架为典型的多连杆独立悬架结构后副车架,在国内许多主流车型如长安福特福克斯、长安CS75、日产逍客等车型上得到广泛应用,通过调整后副车架下摆臂安装偏心螺杆可实现后轮外倾角的调整,提高车辆行驶稳定性,有效降低轮胎的磨损。
该后副车架由后副车架本体上/下板等近30个零件采用机器人CO2弧焊方式焊接而成,焊缝总长度多达6300mm,焊接工作量过大,焊接过程中产生大量的热量,进而产生较大的焊接应力及热变形。
其主要结构及功能标识见图1(图1不涉及尺寸),其中1~4为副车架安装及主定位孔,5、6为稳定杆安装螺栓,7、8为后悬减震器安装孔,9~12为上下摆臂安装孔,车体悬架的大部分部件如减震器、上/下摆臂、稳定杆等通过后副车架安装到车体上,设计要求所有孔位精度保证在±1.5mm(个别要求0.7mm )之内,并且具有模块化安装要求的孔位精度要同时满足关联尺寸要求。
1.2焊接工艺流程该结构副车架总成零件数量较多,架构比较复杂,过程控制环节多,过程稳定性较难控制,焊接工艺流程见图2。
2、变形控制方案后副车架本身结构和功能,决定了实际生产中在保证焊接强度的前提下,需确保关键安装点尺寸精度(见图1),CO焊接热变形是不可避免的,在实际工艺和工装开发中可从以下几个方面着手控制热变形。
汽车副车架焊接变形的控制方法
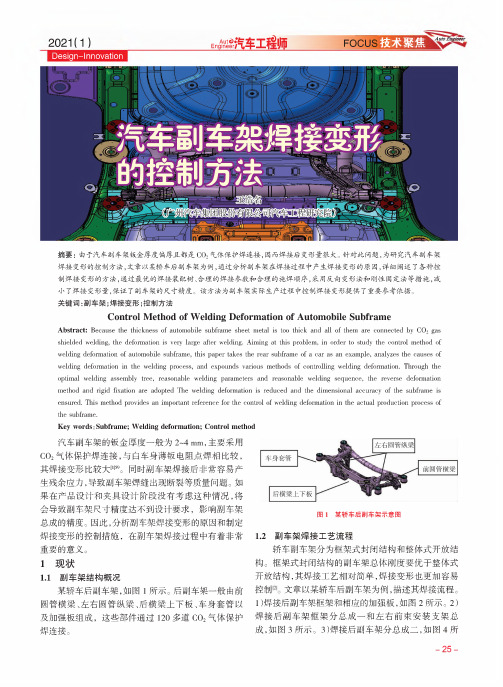
2021(1)E点韶汽车工穩师FOCUS亦*—汽-王浩名(广州汽车集团般份有限公司汽车工程研究院)In摘要:由于汽车副车架钣金厚度偏厚且都是co#气体保护焊连接,因而焊接后变形量很大。
针对此问题,为研究汽车副车架焊接变形的控制方法,文章以某轿车后副车架为例,通过分析副车架在焊接过程中产生焊接变形的原因,详细阐述了各种控制焊接变形的方法,通过最优的焊接装配树、合理的焊接参数和合理的施焊顺序,采用反向变形法和刚性固定法等措施,减小了焊接变形量,保证了副车架的尺寸精度。
该方法为副车架实际生产过程中控制焊接变形提供了重要参考依据。
关键词:副车架;焊接变形;控制方法Control Method of Welding Deformation of Automobile Subframe Abstract:Because the thickness of automobile subframe sheet metal is too thick and all of them are connected by C07gas shielded welding,the deformation is very large after welding.Aiming at this problem,in order to study the control method of welding deformation of automobile subframe,this paper takes the rear subframe of a car as an example,analyzes the causes of welding deformation in the welding process,and expounds various methods of controlling welding deformation.Through the optimal welding assembly tree,reasonable welding parameters and reasonable welding sequence,the reverse deformation method and rigid fixation are adopted The welding deformation is reduced and the dimensional accuracy of the subframe is ensured.This method provides an important reference for the control of welding deformation in the actual production process of the subframe.Key words:Subframe?Welding deformation?Control method汽车副车架的钣金厚度一般为2〜4mm,主要采用CO2气体保护焊连接,与白车身薄钣电阻点焊相比较,其焊接变形比较大22。
副车架的改装分析及设计要点

疲劳破坏是由于构件外部形状的突变以及材料不均匀等原因,使构件某些局部应力特别高。而汽车是一个复杂的多质量振动系统,振动意味着交变应力长期重复出现,在交变应力的作用下,应力较高的点或材料有缺陷的点逐步形成了裂纹。当裂纹扩展到一定程度时,遇到偶然的超载冲击,构件就会沿薄弱的截面发生突然脆性断裂。
2 副车架的结构分析
专用汽车在使用中,其副车架纵梁出现的裂纹、断裂及焊缝撕裂现象,以自卸汽车尤为严重。下面以自卸汽车为例,对副车架所受的静载荷、动载荷和疲劳破坏三方面进行分析。
2 . 1 静载荷分析
副车架所受的静载荷主要有焊接应力和静弯曲应力等。
2 . 1 . 1焊接应力
副车架在焊接加工过程中产生的焊接应力对其焊缝的强度及冲击值都有较大影响,特别是三项应力集中的部位,极易产生裂纹。若焊接尺寸过长、焊缝不均匀,均可使焊接应力增大。焊接应力影响较大的部位,一般出现在纵梁焊有腹板处,如图l 中a 、b 、c 、d 等处。
专用汽车副车架的改装分析及设计耍点专用汽车的各种专用装置都直接或间接地安装在汽车底盘车架简称主车架上过近几年对专用汽车使用情况的调斉发现专用汽车副车架出现裂纹断裂及焊缝撕裂现象是专用汽车使用中存在的主耍问题而副车架的载荷分析是否正确结构设计是否合理则是产生这些现象的重要原因
专用汽车副车架的改装分析及设计要点
3 . 1 副车架纵梁(简称副梁)的前端形状
为避免副梁前端刚度的突然变化对主车架造成的应力集中,同时为防止汽车制动时和超载后副车架对主车架冲击而产生的附加集中应力,通常在设计中将副梁的前端做成逐步过渡的形式,如图3 所示。
3 . 2 腹板的采用
副车架纵梁多数采用槽形截面,在承受较大载荷部位,采用腹板将槽形盒封闭,以提高副梁的抗弯疲劳强度和抗扭疲劳强度。梁的截面尺寸取决于专用汽车的种类及所受载荷的大小;腹板的厚度为副梁厚度的70 %以上,长度可视所受载荷的大小及受载面长短而定。采用图4 所示的腹板形状,可使腹板刚性圆滑过渡,减小应力集中,提高副梁的抗弯及抗扭能力。
车架的焊接工艺与技术要点

车架的焊接工艺与技术要点车架是汽车的重要组成部分,它的焊接工艺与技术对于整个车身的牢固性和稳定性有着至关重要的影响。
正确的焊接工艺与技术能够提高车架的强度、耐久度和安全性,使汽车在运行过程中更加稳定可靠。
本文将介绍车架焊接的工艺要点以及使用的技术。
1. 车架焊接工艺要点(1)选择合适的焊接方法:车架焊接主要采用气体保护焊、电弧焊和激光焊等方法。
在选择焊接方法时需考虑车架的材料和形状,并根据实际情况选择最合适的焊接方法。
(2)合理的焊接顺序:在车架焊接过程中,要合理安排焊接顺序,先焊接刚性部位,再焊接强度要求较低的部位,最后焊接易变形的部位。
这样可以最大程度地减少因焊接引起的形变问题。
(3)控制焊接参数:焊接参数包括焊接电流、电压、速度和温度等。
在焊接过程中,应根据焊接材料和厚度,精确控制焊接参数,确保焊缝的质量和强度。
(4)保证焊缝的质量:焊接过程中,应采用适当的焊接材料和填充物,确保焊缝的质量达到标准要求。
焊接接头应具备足够的强度和密封性,以保证车身在行驶中的稳定性和安全性。
2. 常用的焊接技术(1)气体保护焊:气体保护焊是一种常用的焊接技术,它通过在焊接区域注入保护气体,防止焊接过程中的氧化和污染。
常见的气体保护焊有氩弧焊和氩气保护焊。
这种焊接技术适用于焊接不锈钢、铝合金和钛合金等材料,具有焊缝质量好、成型美观等优点。
(2)电弧焊:电弧焊是一种常见的焊接技术,它利用电弧的高温作用将焊条与焊件熔化,并形成焊缝。
电弧焊分为手工电弧焊、气体保护电弧焊和直流电弧焊等多种形式。
这种焊接技术适用于焊接普通碳钢和合金钢等材料,具有成本低、适用范围广等优势。
(3)激光焊:激光焊是一种高能量密度的焊接技术,它利用激光束的热效应将焊接材料熔化并连接在一起。
激光焊具有速度快、热影响区小等优点,适用于焊接薄板、复杂形状和高强度材料,如汽车车架等。
3. 车架焊接的技术要求和挑战(1)焊接质量要求高:车架是汽车的重要结构部件,对焊接质量的要求较高。
乘用车车架的焊接及质量控制_liuyt
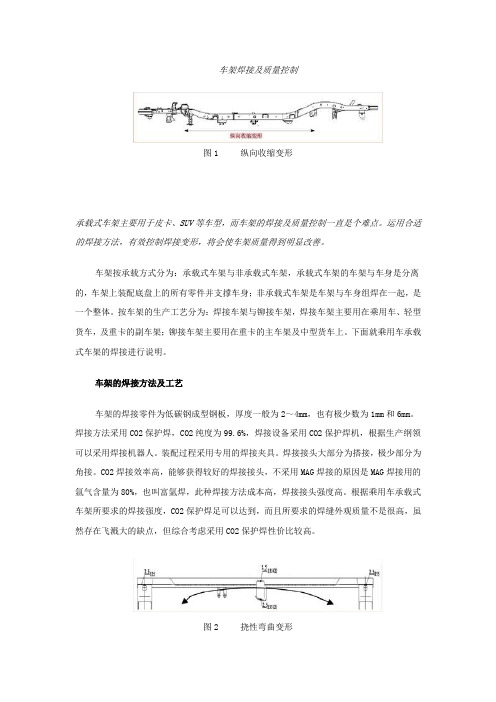
车架焊接及质量控制图1 纵向收缩变形承载式车架主要用于皮卡、SUV等车型,而车架的焊接及质量控制一直是个难点。
运用合适的焊接方法,有效控制焊接变形,将会使车架质量得到明显改善。
车架按承载方式分为:承载式车架与非承载式车架,承载式车架的车架与车身是分离的,车架上装配底盘上的所有零件并支撑车身;非承载式车架是车架与车身组焊在一起,是一个整体。
按车架的生产工艺分为:焊接车架与铆接车架,焊接车架主要用在乘用车、轻型货车,及重卡的副车架;铆接车架主要用在重卡的主车架及中型货车上。
下面就乘用车承载式车架的焊接进行说明。
车架的焊接方法及工艺车架的焊接零件为低碳钢成型钢板,厚度一般为2~4mm,也有极少数为1mm和6mm。
焊接方法采用CO2保护焊,CO2纯度为99.6%,焊接设备采用CO2保护焊机,根据生产纲领可以采用焊接机器人。
装配过程采用专用的焊接夹具。
焊接接头大部分为搭接,极少部分为角接。
CO2焊接效率高,能够获得较好的焊接接头,不采用MAG焊接的原因是MAG焊接用的氩气含量为80%,也叫富氩焊,此种焊接方法成本高,焊接接头强度高。
根据乘用车承载式车架所要求的焊接强度,CO2保护焊足可以达到,而且所要求的焊缝外观质量不是很高,虽然存在飞溅大的缺点,但综合考虑采用CO2保护焊性价比较高。
图2 挠性弯曲变形表为CO2气体保护焊的具体参数,需要说明的是,对不同厚度的零件进行焊接时,规范参数可先按薄件选取,再按总厚度的算术平均厚度通过试片试焊修正;焊接工艺文件如无特殊要求,可执行本守则规定,有特殊要求时,应按焊接工艺文件执行;夏天室内作业开风扇时,风扇不能直接对着焊接区域,气体流量可适当增加,只要不产生气孔即可;随着操作者焊接技能的提高,焊接速度的增加,焊接电流及电压可适当增加。
车架的焊接变形控制由焊接而引起的焊接制件尺寸的改变称为焊接变形,焊接变形为塑性变形,即当外力或其他因素去除后变形仍然存在,物体不能恢复原状。
小车架焊接变形的控制技术
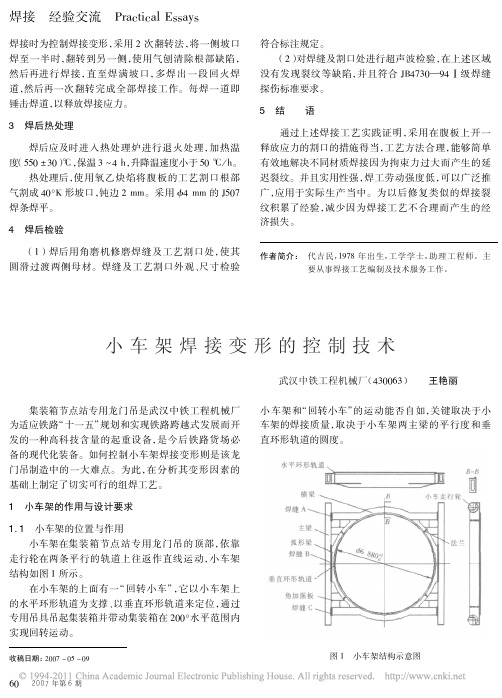
!""# 年第 $ 期
( 立) 后纵 ( 平) 。先焊上下盖板内的焊缝, 后焊裸露在 表面的焊缝; 先焊结构的横 ( 立) 焊缝, 后焊结构的纵 ( 平) 焊缝。垂直焊缝与水平焊缝相交时先焊垂直焊 缝。平行焊缝同时同方向焊接。尽量采用对称焊接, 焊缝分布不对称时先焊焊缝较少的一侧。长焊缝采取 从中间向两端分段退焊。多层焊时, 各层之间的焊缝 方向应相反, 其接头应相互错开。各部分单独组焊时 尽量使焊缝能比较自由地收缩。 %" #$ 焊接工艺 ( $ )主梁、 横梁的上下翼板与腹板的焊缝均采用 . 形坡口, 预留间隙 $ / # "", 采取 ! 层或多层施焊。 (# ) 采用 -0# 气体保护焊, 1’&23#45 焊丝, 直径 电压 #’ / #) .; 其 !$6 # ""。打底焊电流 $&’ / ##’ +, 余各层电流 ##’ / #7’ +, 电压 #) / #& .。 ( ! )由于主梁的截面不大 ( )$’ "" ( %$’ "" ) 且 比较长 ( & 7)’ "") , 故直线度!! "" 难以控制。为此 将整个主梁做成 ! 段, 中间用法兰联接。组焊时, 先将 两处的法兰上好, 把两端和中间视作一个整体进行放 样、 组装、 焊接。 ( ) )在大组装时, 采用 # 名焊工沿圆弧直径方向 对称同时同方向施焊, 最好一次焊完, 避免重复受热增 加变形。 ( 7 )在焊接垂直和水平环形轨道时, 采取跳焊法, 由两人一段圆弧一段圆弧进行施焊。 ( * )小车架定位焊完成后, 一方面先在四角弧形 梁外定位焊工艺板和角支撑, 另一方面在图 $ 的水平、 垂直方向焊刚性固定 “ 十字撑” , 以增强其刚性并检测 调整变形, 防止焊接过程中因焊接应力过大导致焊接 变形。 ( % )由于弧形梁焊接时一般都会引起 弧 长 的 收 缩, 故在焊前组装时先增大弧形梁内圆弧半经 # "" 左 右,以补偿弧长的收缩。 &$ 结$ $ 论 通过分析小车架变形的因素, 选择了合理的焊接 参数和组装顺序, 制定了合理的焊接工艺, 采取了刚性 固定、 反变形控制等控制变形的有力措施。此工艺不 仅达到设计要求、 保证了质量, 而且缩短了工期, 达到 了事半功倍的效果, 为今后类似结构的焊接变形控制 提供了参考。
汽车副车架装焊要点及其调整方法

汽车副车架装焊要点及其调整方法概述:副车架在整车性能的一个关键部件,装焊出质量符合要求的副车架是保证整车的调试的前提,在整车中车的动力部分安装在副车架上它又和车架紧固连接,我们知道车架是整车的承重部分而副车架连接在车架的底部承担着整车的全部重量,副车架的强度是由结构设计和焊接方法及其焊接质量来保证的,这里不在详加分析,现在我们主要来阐述副车架在装焊中的调整方法,如何在工装夹具上装焊出符合设计要求的副车架,供参考借鉴。
副车架属于承重受力结构,一般采用中厚板CO2焊组焊构成,除的合理的安排装焊工艺外,在装焊的各道工序中施加预制其变形量,工装夹具如何调整十分重要,只靠三座标的精度检测标定副车架夹具,忽略了焊接变形的影响是装焊不出质量达标的副车架的。
焊接结构的副车架大多采用管梁拼焊和板件拼焊形式,大同小异结构不尽相同,这里重点介绍副车架工装夹具调整方面的方法。
板件拼焊形式副车架对于非配合安装面非一般可以不做过多的要求,从副车架分析它的主体作用只是承重过渡到每个安装点的连接,主体并不与车的动力配合,只要副车架和车的动力底盘部分的安装点面准确就不会影响整车的技术参数性能,因此夹具三坐标标定精度后,如何根据副车架总成检具调校修正焊接变形保证各安装点、面的准确,达到副车架的技术质量要求是副车架夹具调整的关键环节。
下面分别介绍副车架各道工序的工装夹具调校。
一、副车架上板、副车架下班、左/右连接支柱、左/右摆臂安装板组焊总成一序夹具调校夹具精度按整车数模标定后,首先分析焊接过程变形趋势和变形量,副车架上下板焊接采用了CO2段焊,焊道在上下板结合处的上边口,焊接变形虽有使上下板产生下凹的趋势单由于采用了断焊板件的受热量较小工艺上又要求采用对称焊接的方法因此下凹变形量很小也无扭曲趋势,不会影响副车架主体尺寸,可以不考虑预制下凹的反变形,左/右连接支座和副车架上下板连接处在整车中受力很大最大,采用了CO2 通焊,焊道长工件结合处受热线能量很大,产生很大的热变形,冷却后整个左/右连接支座向内侧收缩,收缩估算值可达到1.5-2mm,在左/右连接支座上的前安装座孔可以通过对前安装座定位销和前安装座定位面实现预制变形的调整,将其左/右连接支柱定位销向外移动1.5-2mm,依据计算左/右连接支柱定位销向外移动后左/右连接支柱定位面也同时下调约1mm用以抵消焊接收缩变形回位后达到较准确的位置,预制变形量究竟何值最佳,还要通过副车架的试焊上总成检具检侧前安装座的误差量进一步的调校夹具此处的定位销即可实现,这只是左/右连接支柱和车架底盘的一个安装位置,而左/右连接支柱还有另一个极其重要的安装点,即左/右连接支柱组件上的三角摆臂安装支座,三角摆臂安装支座夹具上虽有定位销定位但无法克服焊接收缩变形使三角摆臂安装支座向内侧收缩,使两个三角摆臂安装支座间的开档距离尺寸变小,通过对此处强行外挤办法来预制克服其变形量,外挤调节量还是要通过副车架上检具验证调整来实现其位置的准确性并达到总装配走正公差的要求,这是对副车架总成一序的重要基础安装点、面的基本调节方法,也是为副车架总成各轴套焊接位置的准确性鉴定必要的条件。
自卸车副车架的焊接工艺分析
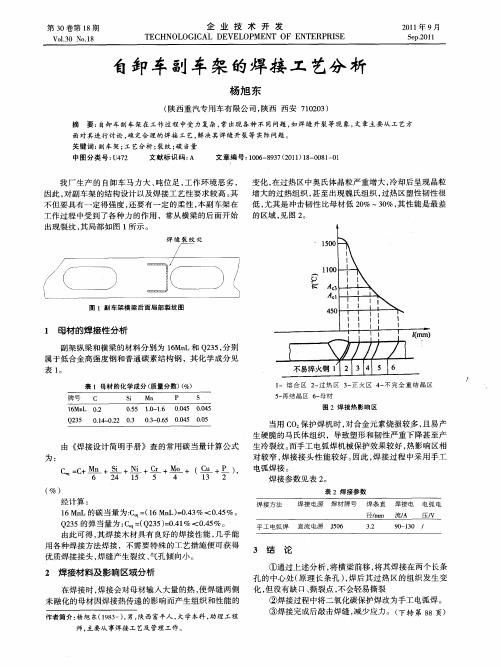
限 的 曲线 1 。 7
3 保 护 联锁 环 节 分 析 . 3 ⑤手柄 处于左边“~ ” , 2 5位 与右边“ — ” 2 5 位一样 , 凸轮 本控制线路有过 电流、 失压 、 短路 、 安全 门、 极限位置 控制器分别把转子电阻分段切除 ,对应 的机械特性 曲线 及紧急操作等保护环节 。其 中主电路 的过 电流保护 由串 如图中第 3 4 限的曲线 2 ~ ’电动机工作点 的速度 接在主电路 中的过电流继 电器来实现 ,其控制触点串接 ,象 ’ 5, 即下降速度依次降低 。 因此下降重物时 , 一开始应将手柄 在接触器 K M的控制 回路 中,一旦发生过电流 , I K 动作 ,
杨 旭 东
( 陕西重汽专用车有限公司 , 陕西 西安 7 0 0 ) 12 3
摘 要 : 自卸 车 副 车 架 在 工 作 过 程 中 受 力 复 杂 , 出现 各 种 不 同 问题 , 焊 缝 开 裂 等现 象 , 章 主要 从 工 艺 方 常 如 文
面 对 其进 行 讨 论 , 定合 理 的 焊接 工 艺 , 决 其 焊 缝 开 裂 等 实 际 问题 。 确 解 关键 词 : 车 架 ; 艺分 析 ; 纹 ; 当量 副 工 裂 碳 中 图分 类 号 : 4 2 U7 文献标识码 : A 文章 编 号 :06 83 (0 1 1— 0 1 0 10 — 97 2 1) 8 08 — 1
5 再 结 晶 区 6 母 材 一 一
图 2 焊 接 热 影 响 区
当用 C : O 保护焊机时 , 对合金元 素烧损较多 , 且易产
生硬脆 的马氏体 组织 ,导致塑形和韧性严重下 降甚至产 而手工 电弧焊机械保护效果较好 , 热影 响区相 由 《 焊接设计 简明手册 》查的常用碳 当量计算公式 生冷裂纹 。 为: 对较窄 , 焊接接头性 能较好 。 因此 , 焊接过 程 中采用手工 电弧焊接 。 C :+ C 坠 + 坠 + 堕 + +坠 + ( + ) P , 6 2 4 1 5 5 4 l 2 3 焊接参数见表 2 。
副车架的安装形式及应注意的问题

副车架的安装形式及应注意的问题副车架的安装形式及应注意的问题1. 前言在汽车制造过程中,副车架的安装是极其重要的一环。
副车架通常位于汽车底盘的后部,起到支撑和增强底盘结构的作用。
在本文中,我们将深入探讨副车架的安装形式及应注意的问题。
通过对这一主题的全面评估,希望能够帮助读者更深入地理解副车架的重要性以及安装时需要注意的细节。
2. 副车架的安装形式副车架的安装形式多种多样,根据不同的汽车类型和用途,有以下几种常见的安装形式:2.1 焊接式安装焊接式安装是最常见的一种副车架安装形式。
在这种形式下,副车架通过焊接的方式与汽车底盘连接在一起。
这种安装形式简单、可靠,常用于大型商用车辆和工程车辆中。
但需要注意的是,焊接过程中要确保副车架与底盘的连接牢固,焊接点要均匀分布,以保证整个车架的稳定性。
2.2 螺栓式安装螺栓式安装主要包括副车架与底盘的螺栓连接和螺栓紧固。
这种安装形式具有灵活性高、维修方便的优点,常用于小型乘用车和跨界SUV 等。
在螺栓紧固过程中,需要注意选择合适的螺栓材质和规格,并逐个顺序紧固,以确保副车架与底盘的连接紧密可靠。
2.3 悬挂式安装悬挂式安装是一种相对较复杂的安装形式。
在这种形式下,副车架通过悬挂装置与汽车底盘连接。
这种安装形式主要用于一些特殊用途的车辆,如越野车和赛车等。
悬挂式安装需要考虑到悬挂装置的强度和稳定性,以及车架与底盘之间的协调性。
3. 安装时应注意的问题在进行副车架的安装时,除了选择合适的安装形式,还需要注意以下几个问题:3.1 安装位置的选择副车架的安装位置应根据车辆的结构和布局进行选择。
一般来说,副车架应位于后轴后方,并与主车架相连。
在选择安装位置时,需要考虑到副车架对车辆行驶性能和操控稳定性的影响,以及与其他零部件的协调性。
3.2 强度和刚度的要求副车架的安装需要考虑到其强度和刚度的要求。
副车架应具备足够的强度,能够承受车辆行驶过程中的各种力和振动。
副车架的刚度也要适中,既要保证车辆的稳定性,又要有一定的弹性,以吸收路面不平和碰撞力。
车架钢结构组装和焊接变形控制

车架钢结构组装和焊接变形控制发布时间:2021-05-17T10:17:41.903Z 来源:《基层建设》2020年第30期作者:李成东王俊峰蔡天云朱喜东葛云龙[导读] 摘要:随着世界轨道交通装备行业的不断发展,我国已经成为世界上的机车制造大国之一。
中车齐齐哈尔车辆有限公司黑龙江齐齐哈尔 161002摘要:随着世界轨道交通装备行业的不断发展,我国已经成为世界上的机车制造大国之一。
在机车的制造过程中,新技术和新工艺不断得到应用,新标准也不断得到认可和执行。
车架是整个机车的主要承载部件,车上和车下都可能装有大型的电气、制动、系统等元件,所以,在设计和生产过程中必须考虑车架的强度和刚度。
车架由不同形式的钢结构焊接而成,在车架组装和焊接过程中,特别是焊接后,会产生各种各样的变形,当变形超过规定时,必须进行矫正,才能进入到下工序,否则后续部件的装配可能出现无法预估的问题,甚至导致整个机车的性能受到影响。
而有些变形是我们在车架组装前就可以预知的,这些变形可以在组装过程中通过一些手段进行有效地改善,有些变形则需要在焊后进行调修,以达到标准的要求。
关键词:车架钢结构;组装;焊接变形1 车架钢结构变形的原因及形式车架变形可大致分为整体变形,即整个车架形状和尺寸发生了变化;另一类是局部变形,它是指发生在焊接结构某部位的局部变形。
整体变形主要包括收缩变形,弯曲变形和扭曲变形,是指焊缝在受热到冷却过程中各个方向发生收缩后引起的变形。
焊缝的纵向和横向收缩时,会引起整个结构的长度缩短和宽度变窄收缩变形;焊缝在结构中布置不对称时会产生弯曲和扭曲变形,装配质量差、焊件摆放不合理、焊接顺序错误、焊接方向颠倒时也会产生弯曲和扭曲变形。
通常在焊缝弯曲变形、扭曲变形时,也会同步发生纵向和横向收缩。
局部变形主要以角变形、波浪变形和错边变形为主。
温度沿板厚方向分布不均匀和熔化金属沿板厚方向收缩量不一致时会发生角变形,在厚板对接衔头容易出现;薄板结构焊接时,纵向和横向的压应力使得其失去稳定,从而产生波浪变形;两个零件在焊接过程中,发生装夹时夹紧程度不一致、刚度各不相同、物理性质不同时,或遇到装配不良、电弧偏离坡口中心问题时,容易引起错边变形。
- 1、下载文档前请自行甄别文档内容的完整性,平台不提供额外的编辑、内容补充、找答案等附加服务。
- 2、"仅部分预览"的文档,不可在线预览部分如存在完整性等问题,可反馈申请退款(可完整预览的文档不适用该条件!)。
- 3、如文档侵犯您的权益,请联系客服反馈,我们会尽快为您处理(人工客服工作时间:9:00-18:30)。
汽车副车架装焊要点及其调整方法
概述:
副车架在整车性能的一个关键部件,装焊出质量符合要求的副车架是保证整车的调试的前提,在整车中车的动力部分安装在副车架上它又和车架紧固连接,我们知道车架是整车的承重部分而副车架连接在车架的底部承担着整车的全部重量,副车架的强度是由结构设计和焊接方法及其焊接质量来保证的,这里不在详加分析,现在我们主要来阐述副车架在装焊中的调整方法,如何在工装夹具上装焊出符合设计要求的副车架,供参考借鉴。
副车架属于承重受力结构,一般采用中厚板CO2焊组焊构成,除的合理的安排装焊工艺外,在装焊的各道工序中施加预制其变形量,工装夹具如何调整十分重要,只靠三座标的精度检测标定副车架夹具,忽略了焊接变形的影响是装焊不出质量达标的副车架的。
焊接结构的副车架大多采用管梁拼焊和板件拼焊形式,大同小异结构不尽相同,这里重点介绍副车架工装夹具调整方面的方法。
板件拼焊形式副车架对于非配合安装面非一般可以不做过多的要求,从副车架分析它的主体作用只是承重过渡到每个安装点的连接,主体并不与车的动力配合,只要副车架
和车的动力底盘部分的安装点面准确就不会影响整车的技术参数性能,因此夹具三坐标标定精度后,如何根据副车架总成检具调校修正焊接变形保证各安装点、面的准确,达到副车架的技术质量要求是副车架夹具调整的关键环节。
下面分别介绍副车架各道工序的工装夹具调校。
一、副车架上板、副车架下班、左/右连接支柱、左
/右摆臂安装板组焊总成一序夹具调校夹具精度按整车数模标定后,首先分析焊接过程变形趋势和变形量,副车架上下板焊接采用了CO2段焊,焊道在上下板结合处的上边口,焊接变形虽有使上下板产生下凹的趋势单由于采用了断焊板件的受热量较小工艺上又要求采用对称焊接的方法因此下凹变形量很小也无扭曲趋势,不会影响副车架主体尺寸,可以不考虑预制下凹的反变形,左/右连接支座和副车架上下板连接处在整车中受力很大最大,采用了CO2 通焊,焊道长工件结合处受热线能量很大,产生很大的热变形,冷却后整个左/右连接支座向内侧收缩,收缩估算值可达到1.5-2mm,在左/右连接支座上的前安装座孔可以通过对前安装座定位销和前安装座定位面实现预制变形的调整,将其左/右连接支柱定位销向外移动1.5-2mm,依据计算左/右连接支柱定位销向外移动后左/右连接支柱定位面也同时下调约1mm用以抵消焊接收缩变形回位后达到较准确的位置,预制变形量究竟何值最佳,还要通过副车架的试焊上
总成检具检侧前安装座的误差量进一步的调校夹具此处的
定位销即可实现,这只是左/右连接支柱和车架底盘的一个安
装位置,而左/右连接支柱还有另一个极其重要的安装点,即
左/右连接支柱组件上的三角摆臂安装支座,三角摆臂安装支
座夹具上虽有定位销定位但无法克服焊接收缩变形使三角
摆臂安装支座向内侧收缩,使两个三角摆臂安装支座间的开
档距离尺寸变小,通过对此处强行外挤办法来预制克服其变
形量,外挤调节量还是要通过副车架上检具验证调整来实现
其位置的准确性并达到总装配走正公差的要求,这是对副车
架总成一序的重要基础安装点、面的基本调节方法,也是为
副车架总成各轴套焊接位置的准确性鉴定必要的条件。
副车架上板副车架上板
左连接支柱右连接支柱左摆臂安装右摆臂安装
前安装座定
位销
前安装座定
位面
二、 副车架总成一序总成和各安装轴套组焊(副车
架二序)夹具调校
副车架二序的装焊夹具调校精度标定后也是通过副车架上检具检侧其各安装座、套来实现对夹具进行校调,这里主要是前安装座和后安装座精调难度较大,其它座、套由于结构是坐在副车架下板上的副车架下板拖住其底面高度位置由副车架下板平面来决定的,因此无需考虑轴、套Z 向高度,只根据副车架在检具上的误差精调各定位销位置即可,而前安装座和后安装座不但要在检具上观察其位置还要观察其Z 向面和检具检测的贴合检测面可以判断出轴套是否倾斜,如有倾斜进一步调整其定位销的角度,直至调整到副车架试件与检具贴合为止。
三角摆臂安
装支座 三角摆臂安
装支座定位
三、 左/右连接支柱总成的夹具调整
左/右连接支柱总成是由左右连接支柱、左/右连接支柱加强板、三角摆臂安装支座组件构成的,因左/右连接支柱冲压件型面不够准确误差较大,只靠夹具标定精度是难以装焊出和装配有关的点和面准确的组件,也就是本文概述中提到的非配合安装面非一般可以不做过多的要求,这就有一个如何根据实际工件状态将需要的点和面调整到正确的位置问题,方法是在总成检具上将三件需要和车架、动力部分相关的安装点、固定为正确的位置然后CO 2点定,按点定的样件去调整该夹具,夹具的调整其关键是保证左/右连接支柱加强板下平面到三角摆臂安装支座安装点的距离就不会影响该组件在副车架总成上的焊接位置,完全可以保证安装点、面的准确,外形为非配合面这样调整夹具消除了工件误差就不影响副车架与车的动力部分安装精度和车架的安装精度(左/右连接支柱总成对称调整方法相同)。
前安装座贴
合面 转向器副定位套管 后安装座贴合面
后悬置前安装座 后悬置后安装座
由此可见对于副车架的焊接变形分析和副车架在整车上安装配合关系是非常重要的,掌握变形规律,分清配合和非配合关系,合理的调整夹具就可以保证副车架装焊质量的。
杜宝和
2014-1-21 左连接支柱 左连接支柱
加强板 三角摆臂安装支座
需要保证左
右连接支柱
加强板此处
的面 需要保证三角摆臂安装
支座的安装
点。