数控机床刀柄系统的选择
ATC、APC和刀柄的选择配置3

1.ATC的选择在具备综合加工能力的一些数控机床上,如加工中心、车削中心和带交换冲头的数控冲床等,自动交换装置是这些设备的基本特征附件,它的工作质量直接关系到整机的质量,也是构成设备投资中的重要组成部分(经费占整机成本的10%~30%)。
因此,在选择主机设备时必须得重视所配A TC自动换刀装置的工作质量和刀具储存量。
目前加工中心自动换刀装置的配套较为规范,以下以加工中心的ATC装置为例来说明其选择原则。
现场经验表明,在加工中心的使用故障中有50%左右与ATC装置有关,但A TC又是提高设备加工效率的基本部件,因此建议用户应在满足使用要求的前提下,尽量选用结构简单和可靠性高的ATC,这样也可以相应地降低整机价格。
下面介绍与ATC装置相关的主要技术参数。
(1)刀柄型号刀柄型号取决于机床主轴装刀柄孔的规格。
现在绝大部分加工中心机床主轴孔都是采用ISO规定的7:24锥孔,常用的有40号、45号、50号等,个别的还有30号和35号。
机床规格越小,刀柄规格也应选小的,但小规格刀柄对加工大尺寸孔和长孔很不利,所以对一台机床如果有大规格的刀柄可选择时,应该尽量选择大的,但刀库容量和换刀时间都要受到影响。
近年来加工中心和数控铣床都向高速化方向发展,许多实验数据表明:当主轴转速超过10000r/min以上时,7:24锥孔由于离心力作用会有一定涨大,影响刀柄的定位精度。
为此,一种观点是建议采用德国VDI推荐的短锥刀柄HSK系列,另外,在日本已有部分商品的锥面和端面同时接触的过定位锥面刀柄,但在定心精度和重复定位精度方面,HSK系列要好一些,目前在国内还很少有厂家生产。
对同一种锥面规格的刀柄有日本BT标准、美国CA T标准、德国VDI标准等,他们规定机械手爪夹持的尺寸不一样,刀柄的拉紧钉尺寸也不一样,所以选择时必须考虑齐全,对已经拥有一定数量数控机床的用户或即将采购一批数控机床的用户,应尽可能选择互相能通用的、单一标准的刀柄系列。
数控刀具的选择方法
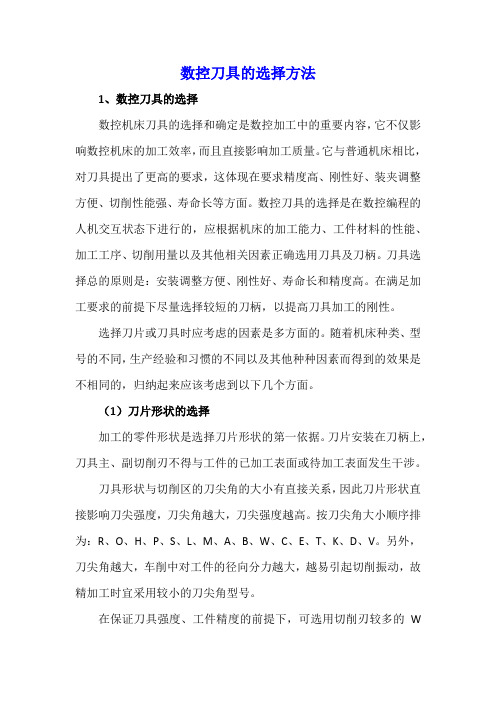
数控刀具的选择方法1、数控刀具的选择数控机床刀具的选择和确定是数控加工中的重要内容,它不仅影响数控机床的加工效率,而且直接影响加工质量。
它与普通机床相比,对刀具提出了更高的要求,这体现在要求精度高、刚性好、装夹调整方便、切削性能强、寿命长等方面。
数控刀具的选择是在数控编程的人机交互状态下进行的,应根据机床的加工能力、工件材料的性能、加工工序、切削用量以及其他相关因素正确选用刀具及刀柄。
刀具选择总的原则是:安装调整方便、刚性好、寿命长和精度高。
在满足加工要求的前提下尽量选择较短的刀柄,以提高刀具加工的刚性。
选择刀片或刀具时应考虑的因素是多方面的。
随着机床种类、型号的不同,生产经验和习惯的不同以及其他种种因素而得到的效果是不相同的,归纳起来应该考虑到以下几个方面。
(1)刀片形状的选择加工的零件形状是选择刀片形状的第一依据。
刀片安装在刀柄上,刀具主、副切削刃不得与工件的已加工表面或待加工表面发生干涉。
刀具形状与切削区的刀尖角的大小有直接关系,因此刀片形状直接影响刀尖强度,刀尖角越大,刀尖强度越高。
按刀尖角大小顺序排为:R、O、H、P、S、L、M、A、B、W、C、E、T、K、D、V。
另外,刀尖角越大,车削中对工件的径向分力越大,越易引起切削振动,故精加工时宜采用较小的刀尖角型号。
在保证刀具强度、工件精度的前提下,可选用切削刃较多的W型、T型刀片。
此外,某些刀片形状的使用范围有其专用性。
如D型、V型车削刀片一般只在仿形车削时才使用。
R型刀片在仿形、车削盘类零件(车轮)、曲面加工时采用。
(2)刀片主切削刃后角的选择当刀片后角选N型0°时,刀片可正反使用,这样可以降低刀片成本。
此时刀柄上的刀片安装面不是水平的,当刀片与刀体组合后,刀具形成正的后角,只是刃倾角为负。
由于数控机夹刀片一般都有断屑槽,故前角也为正值。
因此N型刀片被较多选用,选用时注意考虑槽形。
另外,由于该型刀具的刃倾角为负,在进行曲面加工时,刀具上切削点位置不同,且不在同一中心高上,故在进行较大的精密曲面加工时会造成误差。
研究数控铣削加工刀具系统的选择原则

研究数控铣削加工刀具系统的选择原则数控铣削加工刀具系统的选择原则是:应根据机床的加工能力、工件材料的性能、加工工序、切削用量以及其他相关因素正确选用刀具及刀柄等。
刀具系统选用总的原则是:适用、安全、经济。
①适用是要求所选择的刀具能达到加工的目的,完成材料去除,并达到预定的加工精度。
如粗加工时,选择有足够刚性的刀具能快速去除材料;而精加工时,为了能把结构形状全部加工出来,要使用较小的刀具加工到每一个角落。
再如,切削低硬度材料时,可以使用高速钢刀具;而切削高硬度材料时,就必须要用涂刀具、硬质合金刀具等。
②安全指的是在有效去除材料的同时,不会产生刀具的碰撞、折断等。
要保证刀具及刀柄不会与工件相碰撞或者挤擦,避免造成刀具或工件的损坏。
如加长的直径很小的刀具切削硬质材料时,很容易折断,选用时一定要慎重。
③经济指的是能以最小的成本完成加工。
在同样可以完成加工的情形下,选择相对综合成本较低的方案,而不是选择最便宜的刀具。
刀具的耐用度和精度与刀具价格关系非常大。
必须引起注意的是,在大多数情况下,选择好的刀具虽然增加了刀具成本,,但由此带来的加工质量和加工效率的提高,可以使总体成本比使用普通刀具更低,产生更好的效益。
如进行钢材切削时,选用高速钢刀具,其进给只能达到100mm/min;而采用同样大小的硬质合金刀具,其进给可以达到500mm/min以上,可以大幅缩短加工时间,虽然刀具价格较高,但总体成本反而更低。
通常情况下,优先选;经济性良好的可转位刀具。
选择刀具时还要考虑安装调整方便、刚性好、耐用度和精席高。
在满足加工要求的前提下,使刀具的悬伸长度尽可能短,以提高刀具系统的刚性和切削稳定性。
在加工中心上,各种刀具分别装在刀库上,按程序规定随时进行选刀和换刀动作。
因此,必须采用标准刀柄,以便使钻、镗、扩、铣削等工序用的标准刀具能迅速、准确地装到机床主轴或刀库上。
编程人员应了解机床上所用刀柄的结构尺寸、调整方法以及调整范围,以便在编程时确定刀具的径向和轴向尺寸,便于编程时输人程序中。
数控机床刀具选择和合理使用

数控机床刀具选择和合理使用数控加工刀具必须适应数控机床高速、高效和自动化程度高的特点,一般应包括通用刀具、通用连接刀柄及少量专用刀柄。
刀柄要联接刀具并装在机床动力头上,因此已逐渐标准化和系列化。
数控刀具的分类有多种方法。
根据刀具结构可分为:①整体式;②镶嵌式,采用焊接或机夹式联接,机夹式又可分为不转位和可转位两种;③特殊型式,如复合式刀具、减震式刀具等。
根据制造刀具所用的材料可分为:①高速钢刀具;②硬质合金刀具;③金刚石刀具;④其他材料刀具,如立方氮化硼刀具、陶瓷刀具等。
从切削工艺上可分为:①车削刀具,分外圆、内孔、螺纹、切割刀具等多种;②钻削刀具,包括钻头、铰刀、丝锥等;③镗削刀具;④铣削刀具等。
为了适应数控机床对刀具耐用、稳定、易调、可换等的要求,近几年机夹式可转位刀具得到广泛的应用,在数量上达到整个数控刀具的30%~40%,金属切除量占总数的80%~90%。
数控刀具与普通机床上所用的刀具相比,有许多不同的要求,主要有以下特点:①刚性好(尤其是粗加工刀具)、精度高、抗振及热变形小;②互换性好,便于快速换刀;③寿命高,切削性能稳定、可靠;④刀具的尺寸便于调整,以减少换刀调整时间;⑤刀具应能可靠地断屑或卷屑,以利于切屑的排除;⑥系列化、标准化,以利于编程和刀具管理。
刀具的选择是在数控编程的人机交互状态下进行的。
应根据机床的加工能力、工件材料的性能、加工工序、切削用量以及其它相关因素正确选用刀具及刀柄。
刀具选择总的原则是:安装调整方便、刚性好、耐用度和精度高。
在满足加工要求的前提下,尽量选择较短的刀柄,以提高刀具加工的刚性。
选取刀具时,要使刀具的尺寸与被加工工件的表面尺寸相适应。
生产中,平面零件周边轮廓的加工,常采用立铣刀;铣削平面时,应选硬质合金刀片铣刀;加工凸台、凹槽时,选高速钢立铣刀;加工毛坯表面或粗加工孔时,可选取镶硬质合金刀片的玉米铣刀;对一些立体型面和变斜角轮廓外形的加工,常采用球头铣刀、环形铣刀、锥形铣刀和盘形铣刀。
24数控刀具的选择nld

(4)加工平面工件周边轮廓时,常采用立铣刀。
(5)为了提高槽宽的加工精度,减少铣刀的种类,加工 时可采用直径比槽宽小的铣刀,先铣槽的中间部分,然后 利用刀具半径补偿功能铣削槽的两边。
(6)加工立体曲面或变斜角轮廓外形时,常采用球头铣 刀、环形铣刀、鼓形铣刀、锥形铣刀、盘形铣刀等。
铣刀; (4)曲面加工常采用球头铣刀; (5)加工曲面较平坦的部位常采用环形铣刀; (6)加工空间曲面、模具型腔或凸模成形表面多选用模
具铣刀; (7)加工封闭的键槽选择键槽铣刀。
3.铣削刀具的选择方法
铣刀类型应与工件表面形状及尺寸相适应。 (1)硬质合金可转位式面铣刀 主要用于铣削平面 粗铣时铣刀直径选小一些,因粗铣切削力大,选小
数控镗铣类工具系统
一、数控刀具的基本知识 (一).刀具系统的组成
1.主要由两部分组成:一是刀具部分,二是工具 柄部(刀柄)、接杆(接柄)和夹头等装夹工具部分。
我国的镗铣类 数控机床及加工中 心多采用7:24圆 锥刀柄,并采用相 应型式的拉钉拉紧 结构与机床主轴相 配合。
2.刀柄及其标准
数控铣床的刀柄一 般采用7:24(莫氏锥度) 锥面与主轴孔配合定位, 刀柄及其尾部供主轴内 拉刀机构用拉钉已实现 标准化,有国际标准和 各国国家标准.
(7)当加工余量较小,且表面粗糙度要求较高时,可选 用镶立方氮化硼刀片或镶陶瓷刀片的面铣刀,以便能进行 高速切削。
谢谢观看/欢迎下载
BY FAITH I MEAN A VISION OF GOOD ONE CHERISHES AND THE ENTHUSIASM THAT PUSHES ONE TO SEEK ITS FULFILLMENT REGARDLESS OF OBSTACLES. BY FAITH I BY FAITH
数控刀具中刀柄的应用知识

数控刀具中刀柄的应用知识数控刀具中刀柄的应用知识加工中心的主轴锥孔通常分为两大类,即锥度为7:24的通用系统和1:10的HSK真空系统。
7:24锥度的通用刀柄锥度为7:24的通用刀柄通常有五种标准和规格,即NT(传统型)、DIN 69871(德国标准)、IS0 7388/1 (国际标准)、MAS BT(日本标准)以及ANSI/ASME(美国标准)。
NT型刀柄德国标准为DIN 2080,是在传统型机床上通过拉杆将刀柄拉紧,国内也称为ST;其它四种刀柄均是在加工中心上通过刀柄尾部的拉钉将刀柄拉紧。
目前国内使用最多的是DIN 69871型(即JT)和MAS BT 型两种刀柄。
DIN 69871型的刀柄可以安装在DIN 69871型和ANSI/ASME主轴锥孔的机床上,IS0 7388/1型的刀柄可以安装在DIN 69871型、IS0 7388/1 和ANSI/ASME主轴锥孔的机床上,所以就通用性而言,IS0 7388/1型的刀柄是最好的。
(1)DIN 2080型(简称NT或ST)DIN 2080是德国标准,即国际标准ISO 2583 ,是我们通常所说NT型刀柄,不能用机床的机械手装刀而用手动装刀。
(2)DIN 69871 型(简称JT、DIN、DAT或DV)DIN 69871 型分两种,即DIN 69871 A/AD型和DIN 69871 B 型,前者是中心内冷,后者是法兰盘内冷,其它尺寸相同。
(3)ISO 7388/1 型(简称IV或IT)其刀柄安装尺寸与DIN 69871 型没有区别,但由于ISO 7388/1 型刀柄的D4值小于DIN 69871 型刀柄的D4值,所以将ISO 7388/1型刀柄安装在DIN 69871型锥孔的机床上是没有问题的,但将DIN 69871 型刀柄安装在ISO 7388/1型机床上则有可能会发生干涉。
(4)MAS BT 型(简称BT)BT型是日本标准,安装尺寸与DIN 69871、IS0 7388/1 及ANSI 完全不同,不能换用。
数控刀柄标准
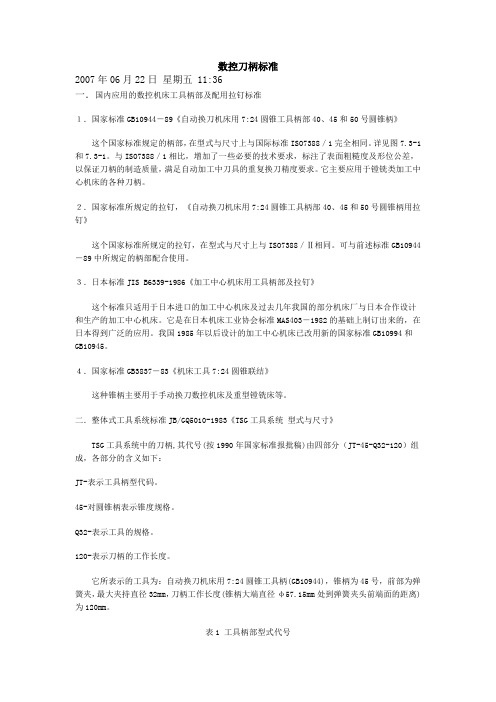
数控刀柄标准2007年06月22日星期五 11:36一.国内应用的数控机床工具柄部及配用拉钉标准1.国家标准GB10944-89《自动换刀机床用7:24圆锥工具柄部40、45和50号圆锥柄》这个国家标准规定的柄部,在型式与尺寸上与国际标准ISO7388/1完全相同。
详见图7.3-1和7.3-1。
与ISO7388/1相比,增加了一些必要的技术要求,标注了表面粗糙度及形位公差,以保证刀柄的制造质量,满足自动加工中刀具的重复换刀精度要求。
它主要应用于镗铣类加工中心机床的各种刀柄。
2.国家标准所规定的拉钉,《自动换刀机床用7:24圆锥工具柄部40、45和50号圆锥柄用拉钉》这个国家标准所规定的拉钉,在型式与尺寸上与ISO7388/Ⅱ相同。
可与前述标准GB10944-89中所规定的柄部配合使用。
3.日本标准JIS B6339-1986《加工中心机床用工具柄部及拉钉》这个标准只适用于日本进口的加工中心机床及过去几年我国的部分机床厂与日本合作设计和生产的加工中心机床。
它是在日本机床工业协会标准MAS403-1982的基础上制订出来的,在日本得到广泛的应用。
我国1985年以后设计的加工中心机床已改用新的国家标准GB10994和GB10945。
4.国家标准GB3837-83《机床工具7:24圆锥联结》这种锥柄主要用于手动换刀数控机床及重型镗铣床等。
二.整体式工具系统标准JB/GQ5010-1983《TSG工具系统型式与尺寸》TSG工具系统中的刀柄,其代号(按1990年国家标准报批稿)由四部分(JT-45-Q32-120)组成,各部分的含义如下:JT-表示工具柄型代码。
45-对圆锥柄表示锥度规格。
Q32-表示工具的规格。
120-表示刀柄的工作长度。
它所表示的工具为:自动换刀机床用7:24圆锥工具柄(GB10944),锥柄为45号,前部为弹簧夹,最大夹持直径32mm,刀柄工作长度(锥柄大端直径φ57.15mm处到弹簧夹头前端面的距离)为120mm。
刀柄系统(1)

刀柄系统-锥柄形式
7:24工具锥柄的刀柄系统占所有加工中心 刀柄的80%以上;
HSK工具系统能够提高系统的刚性和稳定 性以及在高速加工时的产品精度,并缩短刀 具更换的时间,在高速加工中发挥很重要 的作用。
刀柄系统-锥柄形式
7:24工具系统
旋转刀具及配套应用
刀柄系统-加工中心刀具配置图
刀柄系统-锥柄形式
用于连接机床和切削用刀具的数控工具系统,具 有卡具的功能和量具的精度,直接关系到刀具是 否得到正确使用,切削是否达到理想效果的关键 因素所在。包括:
加工中心用7:24锥柄刀柄系统:包括BT、SK、 CAT、DIN等各种标准;NT在早期数控铣床上用的 较多。
注意事项:夹紧时要用专用扳 手夹紧,在加工时如受力过大, 很容易造成三爪断裂。
强力型刀柄
功能:用于铣刀,铰刀等直柄刀具及 工具的夹紧。
优缺点:夹紧力比较大,夹紧精度较 好,更换不同的筒夹来夹持不同柄径 的铣刀,铰刀等。在加工过程中,强 力型刀柄前端直径要比弹簧夹头刀柄 大,容易产生干涉。
角度头
功能:为了能在三轴的加 工叫心实现第四轴的加工。
工作原理:是通过机床主 轴带动角度头内的齿轮运 转传递力矩,从而实现角 度转换。
注意事项:安装原理跟油 路刀柄一样。使用时应注 意当机床正转时,角度头 是反转的,机床反转时, 角度头是正转的。
无极变速加速器
工作原理:通过电主轴箱控制加 速器转动,可实现高速旋转,不 需要主轴旋转。
镗 1.整体式精镗刀 的选择方法
整体式精镗刀主要用在批量产品的生产 线近些年来,市场结构、市场需要日新月异, 产品周期日益缩短,这就要求加工机械以及 加工刀具具有更充分的柔性。所以在实际应 用中,尽管其价格比较低廉,我们并不是十
加工中心常用刀柄类型及其使用场合
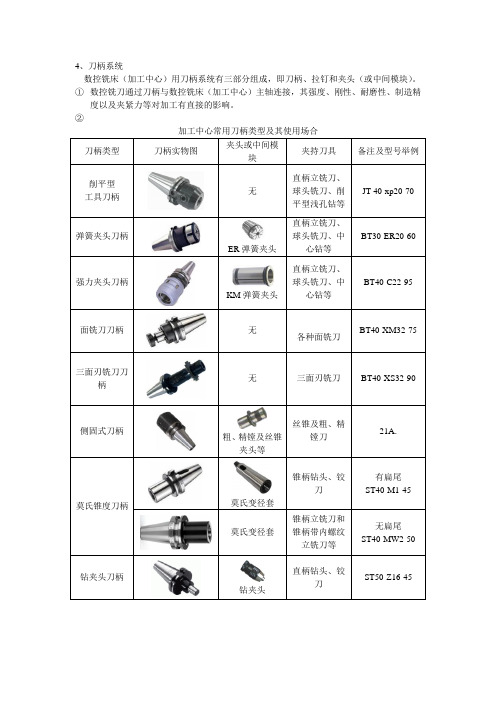
4、刀柄系统数控铣床(加工中心)用刀柄系统有三部分组成,即刀柄、拉钉和夹头(或中间模块)。
①数控铣刀通过刀柄与数控铣床(加工中心)主轴连接,其强度、刚性、耐磨性、制造精度以及夹紧力等对加工有直接的影响。
②加工中心常用刀柄类型及其使用场合刀柄类型刀柄实物图夹头或中间模块夹持刀具备注及型号举例削平型工具刀柄无直柄立铣刀、球头铣刀、削平型浅孔钻等JT-40-xp20-70弹簧夹头刀柄ER弹簧夹头直柄立铣刀、球头铣刀、中心钻等BT30-ER20-60强力夹头刀柄KM弹簧夹头直柄立铣刀、球头铣刀、中心钻等BT40-C22-95面铣刀刀柄无各种面铣刀BT40-XM32-75三面刃铣刀刀柄无三面刃铣刀BT40-XS32-90侧固式刀柄粗、精镗及丝锥夹头等丝锥及粗、精镗刀21A.莫氏锥度刀柄莫氏变径套锥柄钻头、铰刀有扁尾ST40-M1-45莫氏变径套锥柄立铣刀和锥柄带内螺纹立铣刀等无扁尾ST40-MW2-50钻夹头刀柄钻夹头直柄钻头、铰刀ST50-Z16-45丝锥夹头刀柄无机用丝锥ST50-TPG875整体式刀柄粗、精镗刀头整体式粗、精镗刀BT40-BCA30-1605、拉钉加工中心拉钉(图1-1)的尺寸也已标准化,ISO或GB规定了A型和B型两种形式的拉钉,其中A型拉钉用于不带钢球的拉紧装置,而B型拉钉用于带钢球的拉紧装置。
刀柄及拉钉的具体尺寸可查阅有关标准的规定。
6、弹簧夹头及中间模块弹簧夹头有两种,即ER弹簧夹头(图1-2a)和KM弹簧夹头(图1-2b)。
其中ER弹簧夹头的夹紧力较小,适用于切削力较小的场合;KM弹簧夹头的夹紧力较大,适用于强力铣削。
a)b)图1-1 拉钉图1-2 弹簧夹头a)ER弹簧夹头b)KM弹簧夹头中间模块(图1-3)是刀柄和道具之间的中间联接装置,通过中间模块的使用,提高了刀柄的通用性能。
例如,镗刀、丝锥与刀柄的联接就经常使用中间模块。
a)b)c)图1-3 中间模块a)精镗刀中间模块b)攻螺纹夹套c)钻夹头接柄。
数控机床自动换刀装置的选择及刀柄的配置

到整个 数控机 床 尤其 是 J 中心 的 质量 。A C装置 的 jq n- T
投资 往往 占整 机 的 3 % ~5 %。 因此 ,用户 十 分 重视 0 0 A C的质 量和 刀库储存 量 。 T
刀具 的管理也会 相应 复杂化 。
j q 中心 使用专 用 的工 具 系统 ,各 国都有 相 应 的 j - n
标准 系列 。我 国有 成 都工 具 研 究所 制 订 的 T G工 具 系 S
统 刀柄 。
有一些新 的机床 用 户往 往 把 刀库 作 为一 个 车 间 的
工具 室来对 待 ,在更 换 不 同工 件时 想 用 什么 刀 具就 从
5 0
l 7
l 0
5
但是 ,如选 用 的加 工 中心 机 床 准备 用 于 柔性 单 元 (MC F )或柔 性制 造 系 统 ( MS F )中 ,其 刀库 容 量 应 选
取 大容 量刀库 ,甚至 配置 可交换 刀库 。 2 选择 刀柄应 注意 的 问题
( )A C刀库 中储存 刀具 的数 量 ,从 十几把 到 10 2 T 0 把等 ,一 般 刀 库 的 容 量 不 宜 选得 太 大 , 因为 容 量 大 , 刀库 的结 构 复 杂 ,成本 高 ,故 障 率 也 会 相 应 地 增 加 ,
维普资讯
・
28 ・ 2
《 机床与液 压》 20 .o4 02 N .
数控机床 自动换刀装置的选择及 刀柄 的配置
陈 义 庄
( 株洲职 业技 术 学院 ,4 20 ) 10 0
摘要 :介绍数控 机床 自动换 刀装置 的选择 及刀柄配置 应注意 的问题 : 关键词 :数探 机床 ;自动换 刀装置 ;刀库 ;刀柄
第三章数控刀具的选用

山特维克可乐满车刀的夹紧方式选择
22
第三章 数控刀具的选用
刀片形状的选择
可 正型(前角)刀片:
转 对于内轮廓加工,小 型机床加工,工艺系
位 统刚性较差和工件结
车 刀
构形状较复杂应优先 选择正型刀片。 负型(前角)刀片:
的 选
对于外圆加工,金属 切除率高和加工条件 较差时应优先选择负
用 型刀片。
23
则宜大些
28
第三章 数控刀具的选用
刃倾角是前刀面
倾斜的角度。重
切削时,切削开
始点的刀尖上要
承受很大的冲击
刃
力,为防止刀尖 受此力而发生脆
倾
性损伤,故需有
角 的
刃倾角。推荐车 削时为3°~5°; 铣削时10°~15°
刃倾角的影响
作 用
刃倾角为负时,切屑流向工件;为正 时,反向排出 刃倾角为负时,切削刃强度增大,但切 削背向力也增加,易产生振动
第三章 数控刀具的选用
刀片形状的选择
可
一般外圆车削常用80°
转
凸三角形、四方形和
位
80 °菱形刀片;仿形 加工常用55 °、35 °
车
菱形和圆形刀片;
刀
在机床刚性、功率允 许的条件下,大余量、
的
粗加工应选择刀尖角
选
较大的刀片,反之选 择刀尖角较小的刀片。
用
根据加工轮廓 选择刀片形状
24
第三章 数控刀具的选用
合金工具代替。
12
第三章 数控刀具的选用
硬质合金刀具
新型硬质合金 刀具加工实例
普通
数
硬质
控 刀 具
合金
超细晶粒 硬质合金
粒径在1μm以下,这种材料具有 硬度高、韧性好、切削刀可靠性 高等优异性能
1 数控机床常用刀柄的分类

1 数控机床常用刀柄的分类与普通加工方法相比,数控加工对刀具的刚度、精度、耐用度及动平衡性能等方面要求更为严格。
刀具的选择要注重工件的结构与工艺性分析,结合数控机床的加工能力、工件材料及工序内容等因素综合考虑。
数控加工常用刀柄主要分为钻孔刀具刀柄、镗孔刀具刀柄、铣刀类刀柄、螺纹刀具刀柄和直柄刀具类刀柄(立铣刀刀柄和弹簧夹头刀柄)。
2 数控机床常用刀柄的选择刀柄结构形式数控机床刀具刀柄的结构形式分为整体式与模块式两种。
整体式刀柄其装夹刀具的工作部分与它在机床上安装定位用的柄部是一体的。
这种刀柄对机床与零件的变换适应能力较差。
为适应零件与机床的变换,用户必须储备各种规格的刀柄,因此刀柄的利用率较低。
模块式刀具系统是一种较先进的刀具系统,其每把刀柄都可通过各种系列化的模块组装而成。
针对不同的加工零件和使用机床,采取不同的组装方案,可获得多种刀柄系列,从而提高刀柄的适应能力和利用率。
刀柄结构形式的选择应兼顾技术先进与经济合理:①对一些长期反复使用、不需要拼装的简单刀具以配备整体式刀柄为宜,使工具刚性好,价格便宜(如加工零件外轮廓用的立铣刀刀柄、弹簧夹头刀柄及钻夹头刀柄等);②在加工孔径、孔深经常变化的多品种、小批量零件时,宜选用模块式刀柄,以取代大量整体式镗刀柄,降低加工成本;③对数控机床较多尤其是机床主轴端部、换刀机械手各不相同时,宜选用模块式刀柄。
由于各机床所用的中间模块(接杆)和工作模块(装刀模块)都可通用,可大大减少设备投资,提高工具利用率。
刀柄规格数控刀具刀柄多数采用7:24 圆锥工具刀柄,并采用相应型式的拉钉拉紧结构与机床主轴相配合。
刀柄有各种规格,常用的有40 号、45 号和50 号。
目前在我国应用较为广泛的有ISO7388-1983、GB10944-1989、MAS403-1982、ANSI/ASME B5.50-1985 等,选择时应考虑刀柄规格与机床主轴、机械手相适应。
刀柄的规格数量整体式的TSG 工具系统包括20 种刀柄,其规格数量多达数百种,用户可根据所加工的典型零件的数控加工工艺来选取刀柄的品种规格,既可满足加工要求又不致造成积压。
数控加工刀具的选择原则及如何选用?

摘要:现代刀具显著的特点是结构的创新速走加快。
随着计算机应用领域的不断扩大,机械加工也开始运用数拉技术,这时刀具选择与切削用量提出了更高的要求。
本文就扣何确定数控加工中的刀具选择与切削用全进行了探讨。
关键词:数控技术;机械加工;刀具选择一、科学选择数控刀具1、选择数控刀具的原则刀具寿命与切削用量有密切关系。
在制定切削用量时,应首先选择合理的刀具寿命,而合理的刀具寿命则应根据优化的目标而定。
一般分最高生产率刀具寿命和最低成本刀具寿命两种,前者根据单件工时最少的目标确定,后者根据工序成本最低的目标确定。
选择刀具寿命时可考虑如下几点根据刀具复杂程度、制造和磨刀成本来选择。
复杂和精度高的刀具寿命应选得比单刃刀具高些。
对于机夹可转位刀具,由于换刀时间短,为了充分发挥其切削性能,提高生产效率,刀具寿命可选得低些,一般取15-30min。
对于装刀、换刀和调刀比较复杂的多刀机床、组合机床与自动化加工刀具,刀具寿命应选得高些,尤应保证刀具可靠性。
车间内某一工序的生产率限制了整个车间的生产率的提高时,该工序的刀具寿命要选得低些当某工序单位时间内所分担到的全厂开支M较大时,刀具寿命也应选得低些。
大件精加工时,为保证至少完成一次走刀,避免切削时中途换刀,刀具寿命应按零件精度和表面粗糙度来确定。
与普通机床加工方法相比,数控加工对刀具提出了更高的要求,不仅需要冈牲好、精度高,而且要求尺寸稳定,耐用度高,断和排性能坛同时要求安装调整方便,这样来满足数控机床高效率的要求。
数控机床上所选用的刀具常采用适应高速切削的刀具材料(如高速钢、超细粒度硬质合金)并使用可转位刀片。
2、选择数控车削用刀具数控车削车刀常用的一般分成型车刀、尖形车刀、圆弧形车刀以及三类。
成型车刀也称样板车刀,其加工零件的轮廓形状完全由车刀刀刃的形伏和尺寸决定。
数控车削加工中,常见的成型车刀有小半径圆弧车刀、非矩形车槽刀和螺纹刀等。
在数控加工中,应尽量少用或不用成型车刀。
刀柄系统的分类与选择
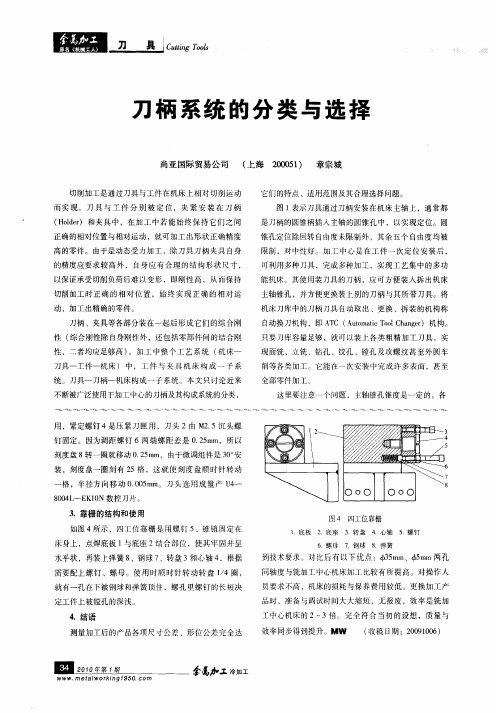
’
80 L E 1N数 控 刀 片 。 04 - K 0
o o o
1r
\
o o o
3 .靠栅的结构和使用
如图 4所示 ,四工位靠 栅是用 螺钉 5、锥销 固定 在
1 .底板
图4 四工位靠栅
2 .底座 3 .转盘 4 .心轴 5 螺 钉 .
床身上 ,点焊底板 1 与底座 2 结合部位 ,使其牢 固并 呈 水平状 ,再装上弹簧 8 、钢球 7 、转盘 3 和心轴 4 ,根据
■ I 。I I
刀 具 l tg t Ci un
 ̄ I
刀 柄 系统 的分 类 与 选 择
尚亚 国际贸易公司 ( 上海 20 5 ) 章宗城 0 0 1
切削加工是通过刀具与工件在机床上相对切 削运 动
它们 的特点 、适用范围及其合理选择问题 。 图 1表示刀具通过刀柄安装 在机床主轴上 ,通常都
现面铣 、立铣 、钻孑 、铰孔 、镗孔 及攻螺纹甚 至外 圆车 L
削等各类加工 。它能在一次安装 中完成许 多表面 ,甚 至
全 部 零件 加 工 。
不断被广泛使用于加工中心的刀柄及其构成系统的分类 ,
‘ … l 。
这里要注意一个问题 ,主紧刀 匣用 ,刀头 2由 M25沉头螺 . 钉 固定。因为调距 螺钉 6两端螺 距差 是 02 rm,所 以 .5 a
需要配上螺 钉 、螺母。使用 时顺时 针转动转 盘 14圈 , / 就有一孔在下被钢球 和弹簧顶住 ,螺孔里螺钉 的长短决
定工 件 上 被 镗孔 的深 浅 。
6 .螺母
7 .钢球
8 .弹簧
到技术要求。对比后有 以下 优点 :西 5 m bm 3 m 、( m两孔 5
数控刀柄标准

数控刀柄标准本文有爱数控 提供一.国内应用的数控机床工具柄部及配用拉钉标准1.国家标准GB10944-89《自动换刀机床用7:24圆锥工具柄部40、45和50号圆锥柄》这个国家标准规定的柄部,在型式与尺寸上与国际标准ISO7388/1完全相同。
详见图7.3-1和7.3-1。
与ISO7388/1相比,增加了一些必要的技术要求,标注了表面粗糙度及形位公差,以保证刀柄的制造质量,满足自动加工中刀具的重复换刀精度要求。
它主要应用于镗铣类加工中心机床的各种刀柄。
2.国家标准所规定的拉钉,《自动换刀机床用7:24圆锥工具柄部40、45和50号圆锥柄用拉钉》这个国家标准所规定的拉钉,在型式与尺寸上与ISO7388/Ⅱ相同。
可与前述标准GB10944-89中所规定的柄部配合使用。
3.日本标准JIS B6339-1986《加工中心机床用工具柄部及拉钉》这个标准只适用于日本进口的加工中心机床及过去几年我国的部分机床厂与日本合作设计和生产的加工中心机床。
它是在日本机床工业协会标准MAS403-1982的基础上制订出来的,在日本得到广泛的应用。
我国1985年以后设计的加工中心机床已改用新的国家标准GB10994和GB10945。
4.国家标准GB3837-83《机床工具7:24圆锥联结》这种锥柄主要用于手动换刀数控机床及重型镗铣床等。
二.整体式工具系统标准JB/GQ5010-1983《TSG工具系统型式与尺寸》TSG工具系统中的刀柄,其代号(按1990年国家标准报批稿)由四部分(JT-45-Q32-120)组成,各部分的含义如下:JT-表示工具柄型代码。
45-对圆锥柄表示锥度规格。
Q32-表示工具的规格。
120-表示刀柄的工作长度。
它所表示的工具为:自动换刀机床用7:24圆锥工具柄(GB10944),锥柄为45号,前部为弹簧夹,最大夹持直径32mm,刀柄工作长度(锥柄大端直径φ57.15mm处到弹簧夹头前端面的距离)为120mm。
数控机床刀具的选择

装面铣刀
M
装有扁尾莫氏锥柄刀具
TQW
倾斜式微调镗刀
XDZ
装直角端铣刀
G C 规格
攻螺纹夹头
TQC
倾斜式粗镗刀
XD
装端铣刀
切内槽工具
TZC
直角形粗镗刀
用数字表达工具旳规格,其含义随工具不同而异。有些工具该数字为轮廓尺寸D-L;有些工具 该数字表达应用范围。还有表达其他参数值旳,如锥度号等。
疲劳强度、切削稳定性高于Al2O3 基陶瓷刀具,主要用于端铣和切有 氧化皮旳毛坯工件,也可对铸铁、 淬硬钢进行精加工和半精加工。
c. 塞隆(Sialon)陶瓷
Si3N4中加入Al2O3等形成旳新 材料。迄今陶瓷中强度最高旳材 料,化学稳定性和抗氧化能力都 很好。
③ 超硬刀具材料
金刚石和立方氮化硼旳统称,用于超精 加工和硬脆材料加工。
a.聚晶金刚石(PCD)
硬度高、耐磨性好,但耐热性差、 强度低、脆性大,与铁亲和力强,用 于高速精细车削、镗削有色金属及其 合金和非金属材料,不宜加工黑色金 属。
b. 立方氮化硼( CBN)
硬度和耐磨性仅次于金刚石,但 热稳定性好,主要用于加工高硬度(6470HRC)旳淬硬钢、冷硬铸铁、高温合金 等难加工材料。
③ 粉末冶金高速钢 能够防止熔炼钢产
生旳碳化物偏析。其强度、韧性比熔炼 钢有很大提升。可用于加工超高强度钢、 不锈钢、钛合金等难加工材料。用于制 造大型拉刀和齿轮刀具,尤其是切削时 受冲击载荷旳刀具效果更加好。
(2)硬质合金(Cemented Carbide)
1)一般硬质合金
①钨钴类(YG)
WC+Co,强度好,硬度和耐磨性较差, 用于加工脆性材料、有色金属和非金属 材料。常用牌号:YG3、YG6、YG8、 YG6X。数字表达Co旳百分含量, Co多 韧性好,用于粗加工; Co少用于精加 工。
数控机床的刀柄选择与使用要点

数控机床的刀柄选择与使用要点刀柄是数控机床上非常重要的配件之一,它直接影响到机床的加工效率和加工质量。
正确选择和使用刀柄对于实现高效加工具有重要意义。
本文将介绍数控机床刀柄的选择和使用要点,供读者参考。
首先,在选择刀柄时应考虑以下几个要点。
刀柄材质:刀柄的材质应根据加工材料的种类和切削性能来选择。
常用的材料有硬质合金、高速钢等。
硬质合金刀柄具有耐磨性好、强度高等特点,适用于加工难加工材料和大批量生产;高速钢刀柄则适用于加工薄壁零件和散热要求高的情况。
刀柄接口:刀柄接口分为直柄和刀杆两种形式。
直柄简单易用,适合加工小批量产品;而刀杆则适合大批量生产,可以提高加工效率。
刀柄长度:刀柄的长度应根据具体的加工情况来选择。
一般来说,加工较深孔或需要进行倒角的工件,应选择较长的刀柄;而加工薄壁零件则需要选择较短的刀柄。
刀柄形状:刀柄的形状应根据加工工件的轮廓和不同切削操作来选择。
常见的刀柄形状有直柄、插削刀柄、铣刀柄等。
直柄适用于钻孔、扩孔和镗孔等操作;插削刀柄适用于斜面、槽面等面铣削;铣刀柄适用于铣削面。
其次,在使用刀柄时还需注意以下要点。
刀柄的安装:刀柄的安装应遵循机床的使用说明书和刀具的生产厂家提供的指导。
安装前需检查刀柄与夹头的匹配度,确认无松动或损坏,以免造成事故或工件加工不合格。
刀柄的保养:刀柄在使用过程中需定期进行保养和清洁。
保持刀柄表面的清洁并定期涂抹润滑油,以减少磨损和延长使用寿命。
同时,应定期检查刀柄是否出现裂纹或变形,如有异常应及时更换。
刀柄的刀具安装:刀柄与刀具的安装应牢固可靠,避免出现刀具脱落或垂直度偏差过大的情况。
在安装过程中应确保刀具与工件的角度、位置和切削深度等参数符合要求。
刀柄的切削参数:刀柄在使用过程中需要根据具体加工工件选择合适的切削参数,如切削速度和进给速度。
选择合适的切削参数有助于提高加工效率和加工质量。
刀柄的修磨和更换:刀柄在经过一段时间的使用后,可能会出现磨损或损坏的情况。
- 1、下载文档前请自行甄别文档内容的完整性,平台不提供额外的编辑、内容补充、找答案等附加服务。
- 2、"仅部分预览"的文档,不可在线预览部分如存在完整性等问题,可反馈申请退款(可完整预览的文档不适用该条件!)。
- 3、如文档侵犯您的权益,请联系客服反馈,我们会尽快为您处理(人工客服工作时间:9:00-18:30)。
数控机床刀柄系统的选择
工具系统的选择是数控机床配置中的重要内容之一,因为工具系统不仅影响数控机床的生产效率,而且直接影响零件的加工质量。
根据数控机床(或加工中心)的性能与数控加工工艺的特点优化刀具与刀柄系统,可以取得事半功倍的效果。
1数控机床常用刀柄的分类
与普通加工方法相比,数控加工对刀具的刚度、精度、耐用度及动平衡性能等方面要求更为严格。
刀具的选择要注重工件的结构与工艺性分析,结合数控机床的加工能力、工件材料及工序内容等因素综合考虑。
数控加工常用刀柄主要分为钻孔刀具刀柄、镗孔刀具刀柄、铣刀类刀柄、螺纹刀具刀柄和直柄刀具类刀柄(立铣刀刀柄和弹簧夹头刀柄)。
2数控机床常用刀柄的选择
1)刀柄结构形式
数控机床刀具刀柄的结构形式分为整体式与模块式两种。
整体式刀柄其装夹刀具的工作部分与它在机床上安装定位用的柄部是一体的。
这种刀柄对机床与零件的变换适应能力较差。
为适应零件与机床的变换,用户必须储备各种规格的刀柄,因此刀柄的利用率较低。
模块式刀具系统是一种较先进的刀具系统,其每把刀柄都可通过各种系列化的模块组装而成。
针对不同的加工零件和使用机床,采取不同的组装方案,可获得多种刀柄系列,从而提高刀柄的适应能力和利用率。
刀柄结构形式的选择应兼顾技术先进与经济合理:①对一些长期反复使用、不需要拼装的简单刀具以配备整体式刀柄为宜,使工具刚性好,价格便宜(如加工零件外轮廓用的立铣刀刀柄、弹簧夹头刀柄及钻夹头刀柄等);②在加工孔径、孔深经常变化的多品种、小批量零件时,宜选用模块式刀柄,以取代大量整体式镗刀柄,降低加工成本;③对数控机床较多尤其是机床主轴端部、换刀机械手各不相同时,宜选用模块式刀柄。
由于各机床所用的中间模块(接杆)和工作模块(装刀模块)都可通用,可大大减少设备投资,提高工具利用率。
2)刀柄规格
数控刀具刀柄多数采用7:24圆锥工具刀柄,并采用相应型式的拉钉拉紧结构与机床主轴相配合。
刀柄有各种规格,常用的有40号、45号和50号。
目前在我国应用较为广泛的有ISO7388-1983、GB10944-1989、MA S403-1982、ANSI/ASMEB5.50-1985等,选择时应考虑刀柄规格与机床主轴、机械手相适应。
3)刀柄的规格数量
整体式的TSG工具系统包括20种刀柄,其规格数量多达数百种,用户可根据所加工的典型零件的数控加工工艺来选取刀柄的品种规格,既可满足加工要求又不致造成积压。
考虑到数控机床工作的同时还有一定数量
的刀柄处于预调或刀具修磨中,因此通常刀柄的配置数量是所需刀柄的2~3倍。
4)刀具与刀柄的配套
关注刀柄与刀具的匹配,尤其是在选用攻螺纹刀柄时,要注意配用的丝锥传动方头尺寸。
此外,数控机床上选用单刃镗孔刀具可避免退刀时划伤工件,但应注意刀尖相对于刀柄上键槽的位置方向:有的机床要求与键槽方位一致,而有的机床则要求与键槽方位垂直。
5)选用高效和复合刀柄
为提高加工效率,应尽可能选用高效率的刀具和刀柄。
如粗镗孔可选用双刃镗刀刀柄,既可提高加工效率,又有利于减少切削振动;选用强力弹簧夹头不仅可以夹持直柄刀具,也可通过接杆夹持带孔刀具等。
对于批量大、加工复杂的典型工件,应尽可能选用复合刀具。
尽管复合刀具与刀柄价格较为昂贵,但在加工中心上采用复合刀具加工,可把多道工序合并成一道工序、由一把刀具完成,有利于减少加工时间和换刀次数,显著提高生产效率。
对于一些特殊零件还可考虑采用专门设计的复合刀柄。
6)强化工具系统管理工作
随着数控机床数量增加,刀柄的数量会急剧增多。
一套拥有5~8台数控机床的柔性制造系统,刀柄数量可达1000把以上。
如何使这些刀具得到合理有效的利用,是刀具管理的重点工作。
其内容包括:刀柄采购或补充计划的提出;刀具数据的预调;刀具的调度与保管;刀具寿命情况判断与控制等。
3数控机床刀柄的发展
1)特殊功能的刀柄
近年来,加工中心上出现了一些特殊功能的刀柄,主要有以下类型。
增速刀柄(增速头):能实现自动换刀。
如日本NIKKEN公司的NXSE增速头,在机床主轴速度为4000r/m in时,刀具可在0.8s内转速达到20000r/min。
多轴刀柄:它能同时加工多个孔,相当于多轴加工头。
多轴与增速刀柄组合使用可构成双功能的多轴增速刀柄。
内冷却刀柄:该刀柄与芯部开有冷却液通道的麻花钻或深孔钻配合使用,利用特殊的供油系统,将高压切削液喷注到切削部位,实现良好的冷却与润滑,并排除切屑。
转角刀柄:这种刀柄的头部可作30º、45º、60º、90º等角度旋转,具有五面加工功能。
安装在立式加工中心上,可使立式加工中心具有卧式加工中心的功能,可用于深型腔的底部清角作业。
2)新型高速切削刀柄
随着数控机床高精度高速切削技术的发展,适应高速切削的刀柄系统好得到研制与开发。
如德国OTT
公司的HSK刀柄和美国Kenamental公司的KM刀柄等,其轴向定位精度可达0.001mm,且在高速旋转下,刀夹锁紧更为牢固,径向跳动不超过5μm。
HSK刀柄是一种典型的1:10短锥面、锥柄和主轴端面同时接触的双定位型空心刀柄,其主要特点为:
·采用锥面、端面过定位的结合形式,能有效地提高工具系统的连接刚度,且重复定位精度高;
·采用空心结构和缩短锥部长度,刀柄质量较轻,可缩短换刀移动距离,加快换刀速度,有利于实现高速自动换刀;
·采用1:10锥度,锥柄较短,楔形效果好,有较强的抗扭能力,且能抑制因振动而产生的微量移位;
·刀柄与主轴间由扩张爪锁紧,转速越高,扩张爪的离心力(扩张力)越大,锁紧力越大,具有良好的高速性能。
·为提高刀具系统在高速状态下的动平衡精度,可在刀柄上安装自动校正动平衡装置。