轧辊深孔加工工艺研究
探讨如何提高轧辊加工效率

探讨如何提高轧辊加工效率发布时间:2021-06-28T15:02:58.103Z 来源:《工程管理前沿》2021年第6期作者:何可李伟高炎[导读] 伴随着社会经济的不断增长与工业发展的突飞猛进何可李伟高炎武汉钢铁有限公司湖北武汉 430000摘要:伴随着社会经济的不断增长与工业发展的突飞猛进,各项生产技术都在不断改革提升经济效益。
结合工作经验,对轧辊加工流程及工艺改进进行了分析探讨,最终提高了轧辊加工效率,希望能为相关工作提供参考。
关键词:轧辊;车削;孔型;钢坯引言随着数控加工技术的发展,数控轧辊车床以加工精度高、质量稳定、加工能力强等特点在轧辊生产厂家、型钢厂逐步得到普及应用。
但因数控编程技术、刀具材质、工人操作水平等因素的影响,型钢轧辊孔型加工效率相对较低。
据了解,各型钢厂同规格轧辊加工效率相差30%以上。
1高速钢轧辊高碳高速钢复合轧辊(简称高速钢轧辊)是近年来发展最快且应用前景最广的热轧辊材料,它的成分是较为复杂的合金钢,在热处理工艺淬火后,即使在空气中冷却也能硬化。
其工作层材料采用高碳钢,轧辊的芯部材料采用球墨铸铁、石墨钢或锻钢等,两种不同的材料通过离心铸造或者采用CPC工艺复合而成,基体组织一般为回火马氏体+贝氏体+碳化物,碳化物以高度弥散形式分布在基体中,所以具有很高的耐磨性、强韧性,导致车削加工难度大。
高速钢轧辊特点是热稳定性好、淬透性好,碳化物硬度高,容易形成氧化膜,具有良好的抗热裂性和耐磨性能,对冷却水的要求远远低于硬质合金的要求,它的单槽轧制量能达到铸铁轧辊的4-5倍。
有利于轧材负公差控制,提高轧材表面质量。
主要是应用在线棒材成品和成品前机架以及切分轧制预切、切分孔型为主而研发的新型材质轧辊,硬度可达HSD78~90,具有很高的耐磨性,同时具有良好的抗冲击性能,抗热疲劳性好。
随着高速钢轧辊在线棒材轧钢厂的普及,研发制造厂家随之迅速蔓延,但是各厂家在高速钢轧辊铸造过程中添加的合金元素有所差异,为此在加工、使用方面,切削难易程度和在线使用效果并非完全一致,整体上主要包含有钨、钼、铬、钒、铌等碳化物形成元素。
数控加工技术在型钢轧辊加工中的研究与应用

数控加工技术在型钢轧辊加工中的研究与应用【摘要】本文通过对型钢轧辊数控加工中刀具选择、装夹辅助工具设计和数控程序简化编制等方面技术进行研究与应用,缩短了轧辊加工辅助时间,充分发挥了数控加工技术的优点,实现了型钢轧辊加工质量和效率的显著提高,开创了行业技术的领先水平。
【关键词】型钢轧辊数控加工技术程序刀具1.引言近几年,随着中国机械制造业的不断壮大,数控加工技术在机制加工中应用非常广泛。
由于受型钢轧辊孔型断面复杂、重量大、装卡难等方面的影响,成型刀加工仍占绝大部分,数控加工技术目前仍处于探索阶段。
随着轧机设备的升级换代,轧辊加工难度和质量要求也越来越高,型钢轧辊数控加工技术也得到了不断发展。
攀钢轨梁厂型钢轧辊数控加工技术通过近年来的研究与应用,不论其质量和效率在国内同行业中均处于领先水平。
2.型钢轧辊加工工艺介绍目前,国内几个主要型钢厂的轧辊加工仍采用成型刀进行加工,随着轧辊材质的不断升级,这种加工方式的不足则越来越明显。
一方面成型刀加工后轧辊孔型精度和表面粗糙度均较差,另一方面受刀具制作工艺影响,成型刀难以满足高硬度轧辊加工。
数控加工技术的发展则成功解决了成型刀具加工存在的这两个问题,但随之而来的问题是刀具制作成本高、轧辊加工效率低。
型钢轧辊孔型具有断面复杂、局部尺寸小、位置尺寸关联性强等特点,攀钢的重轨轧辊孔型就是型钢轧辊孔型较为复杂的一种,其数控加工难度较大,经分析制约其数控加工技术应用主要体现在三个方面:一是孔型切入深度大,刀具选择困难;二是加工效率低,难以满足生产需要;三是数控编程技术难度大,职工不易掌握。
3.型钢轧辊数控加工技术研究与应用为了充分发挥数控加工技术精度高,以提高轧辊加工质量。
本文从轧辊数控加工技术的刀具优化选择、加工效率的提高、数控编程技术的简化等方面进行研究,成功实现了数控加工技术在型钢轧辊中的应用。
3.1 刀具的设计与选择数控机床刀具除数控磨床和数控电加工机床外,其他的数控机床都必须采用数控刀具。
轧辊孔型加工管理

轧辊是轧钢生产中必不可少的关键设备,与产品的质量是不可分的,八钢股份公司线材厂主要生产6.5mm、8mm、10mm的盘圆。
其工艺布局为480×3/ 430×5/ 350×2/ 320×2/ 300×4/ 280×8的复二重半连轧布置,共24付机架,轧制24道,四线轧制。
线材厂因为轧制道次多,投入轧辊数量和轧辊资金也较多。
线材厂每年仅轧辊消耗就占用资金500多万元,如不对轧辊进行科学有效的管理,必然造成大量的损失,并且随着线材产品产量和质量的不断提高,也对轧辊管理提出了更高的要求,因此加强轧辊管理有着重要意义。
六年多来通过对轧辊管理知识的学习以及在生产中的不断实践,探索出一套轧辊管理方法,在实践中应用取得了较好效果。
2 线材轧辊管理的特点及内容轧辊按材质可分为锻钢、铸钢和铸铁轧辊、特种轧辊,根据浇注方法不同可分为常法浇注轧辊和复合离心浇注轧辊;为提高轧辊的耐磨性,也可以适当添加一定比例的合金元素,如中镍、铬、钼等。
轧辊管理是指从选择轧辊材质、轧辊采购计划的制定、轧辊孔型样板的加工和管理、轧辊孔型的加工及检查、轧辊加工车削量和车削次数的确定等一系列工作,具有系统性。
对轧辊实施精细管理的工作。
其特点是:(1)具有系统性、连续性;(2)理论性和实践性强;(3)必须环环相扣,精细合理。
2.1 轧辊材质的选择轧辊材质好,轧辊使用周期就长,轧辊消耗数量就越少,反之则越多。
线材厂根据所用轧机特点,对轧辊材质进行了比较。
线材厂轧机分为粗轧机列、中轧机列、精轧机列,每个机列在轧钢时的轧制任务不同,对轧辊的性能要求也不同,粗轧一般要考虑轧辊强度,多选用锻钢和铸钢轧辊,或选用球墨半冷硬和球墨冷硬轧辊。
锻钢和铸钢轧辊的强度大,不易发生断辊,但其硬度低、耐磨性差、使用周期短、更换轧辊频繁;因球墨铸铁轧辊的辊身工作层中有石墨,使轧辊耐磨性、抗热裂性能得到提高,优于锻钢、铸钢轧辊,所以线材厂粗、中轧在满足强度要求的前提下,选用了中镍、铬、钼球墨无限冷硬铸铁轧辊;精轧机列主要对轧辊的耐磨性有要求,故选用中镍、铬、钼无限冷硬铸铁轧辊,又由于复合离心辊的性能在满足生产技术要求方面优于常法辊。
轧波辊铣床加工工艺窍门

轧波辊铣床加工工艺窍门1、轧波辊加工工艺分析轧波辊总长800mm,直径Ф99,材料为45#钢调质(HRC28——32),轴上有1mm宽、凹5mm深细槽20条(均匀分布)。
在第一条细槽上有17个凹环形槽均匀分布,其中心间距为34mm,起始点中心尺寸为14.5mm。
在第二条细槽上有8个环形凹槽均匀分布,其中心间距为68mm,起始点中心尺寸为65.5mm。
在第三条细槽等同于第一条细槽。
在第四条细槽上有9个环形凹槽均匀分布,其中心间距为68mm,起始点中心尺寸为31.5mm。
以上四条细槽为一组循环,轧波辊一周共20条细槽,分5组循环,环形凹槽的总数为255个。
用现有的立式铣床加工有一定难度。
如20条细槽宽度仅为1mm,深度为5mm,长度为545mm,宽度加工公差仅为0.1mm。
由于锯片铣刀在加工时存在较大的摆动现象,且加工长度为545mm,另外由于每条细槽上的环形凹槽的数量、间距均不同,所以必须要借助辅助夹具来完成。
2、轧波辊的加工工艺流程1.备料:锻打,毛坯尺寸为Ф110X850(两件)2.热处理:退火3.车:直径粗车,长度车到800mm4.热处理:调质HRC28——325.精车:Ф110车到Ф99.8(留磨量0.6——0.8),Ф35留磨量0.3,Ф50车到尺寸6.万磨:Ф99,Ф35磨到尺寸7.铣:20个细槽铣到尺寸,255个环形凹槽铣到尺寸8.线切割:255个镶块割到尺寸9.钳:镶1mm压条及环形镶块10.外圆磨:Ф102磨到尺寸11.钳:去除毛刺3、辅助夹具的作用及制造要求使用辅助夹具的目的是为了铣20条,1mm宽的细槽。
因此,刀片夹紧块的使用能保证锯片铣刀在加工过程中尽可能保持稳定,保护刀片和增加刀片强度。
偏心弹簧夹头可使环型凹槽3mm宽度,适当加大0.08——0.1mm便于钳工镶环形镶块。
环型定位块的作用就是保证环形槽的间距达到工艺要求的尺寸。
4、所需量具、刀具、夹具、设备1.工具:高度尺、百分表、游标卡尺2.刀具:锯片铣刀,规格:Ф60X1.0XФ16,齿数60键槽直柄铣刀,规格:Ф3,Ф83.夹具:环形凹槽定位块4.设备:X——4000立式铣床,F11125型万能分度头5、工件的装夹找正及划线1.将分度头安放在铣床工作台面T型槽内,应注意擦净分度头尾座底面和定位块侧面,然后用M16T型螺栓旋紧分度头。
轧辊锻造工艺的研究与应用

在各类冷热连 轧板带钢 轧机 和宽厚 板轧机 轧辊 中 ,
经过广大轧辊科技人 员和生产企业共 同努力,开展科技创
锻钢工作辊和锻钢支承辊所 占的 比例很大 。作为轧 机的 重要承载件和消耗性备件 ,锻钢轧辊 因其具有致密 的 内 部组织和优 良的力学性能 而被 广泛使用 ,长期 以来 一直 受到人们的重点 关注。锻钢轧辊 的品种规格多 ,性 能质 量要求高 ,制造工艺过程 复杂,是 机械制造行业 的主导 产 品之一 。锻钢轧辊 主要包括 : ( ) 冷轧工作辊 1 辊身直径 30~ 5 r 0 6 0 m,重 量 3~ a
建立起轧辊锻造变形过程 的应力一 应变场和温度场模 犁 ,
使轧辊的锻造变形工艺过 程更加清晰有序 ,消除 了很多
合金钢 材料及大 型合金 钢钢锭 的加热 .保 证加 热质量 , 为轧辊 的锻造成形创造条 件,广大科技 人员研究升发 了 “ 分段加 热,高温扩散” 等加热 工 艺,解 决 r 热方法 加 和保证 加热温度均匀等技 术问题 :为减 少能源消耗和 牛 产成本 ,还研 究 成功 不 少节 能降 耗 的新工 艺 和新技
随着轧制工艺技术的进步和大量先进轧机的建设使用 , 近1 0年来 ,对锻钢轧辊的要求不仅数量多 ,而且质量要求
向高性能化 、 大型化及高合金化发展 ,轧辊锻造工 艺对
模拟技术提 出了更高要求 。为此 ,经过广大 科技工作 者 的努力 ,具有迅速准确 ,成本低廉 的计算机 数值模拟技
术终于在 2 0世纪 7 0年代研究 成功。这一新技 术用于轧
术 ,在 生产府用 中取得了明显效果
不确定因素,大大提高了轧辊 锻造 : E艺的准确性干 可靠 u
性 。最 近 儿年 , 国 内邢 台 轧辊 股 份 有 限 公 司 、 中 同 ・ 重
轧辊孔型加工工艺流程

轧辊孔型加工工艺流程下载温馨提示:该文档是我店铺精心编制而成,希望大家下载以后,能够帮助大家解决实际的问题。
文档下载后可定制随意修改,请根据实际需要进行相应的调整和使用,谢谢!并且,本店铺为大家提供各种各样类型的实用资料,如教育随笔、日记赏析、句子摘抄、古诗大全、经典美文、话题作文、工作总结、词语解析、文案摘录、其他资料等等,如想了解不同资料格式和写法,敬请关注!Download tips: This document is carefully compiled by theeditor.I hope that after you download them,they can help yousolve practical problems. The document can be customized andmodified after downloading,please adjust and use it according toactual needs, thank you!In addition, our shop provides you with various types ofpractical materials,such as educational essays, diaryappreciation,sentence excerpts,ancient poems,classic articles,topic composition,work summary,word parsing,copy excerpts,other materials and so on,want to know different data formats andwriting methods,please pay attention!轧辊孔型加工工艺流程详解轧辊是钢铁行业中的重要工具,其孔型设计和加工工艺直接影响到钢材的形状、尺寸精度和表面质量。
轧机平衡块深孔加工的工艺研究的开题报告
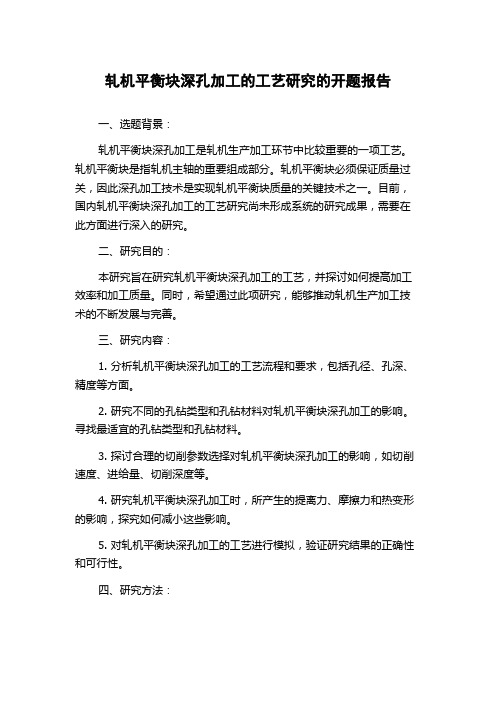
轧机平衡块深孔加工的工艺研究的开题报告一、选题背景:轧机平衡块深孔加工是轧机生产加工环节中比较重要的一项工艺。
轧机平衡块是指轧机主轴的重要组成部分。
轧机平衡块必须保证质量过关,因此深孔加工技术是实现轧机平衡块质量的关键技术之一。
目前,国内轧机平衡块深孔加工的工艺研究尚未形成系统的研究成果,需要在此方面进行深入的研究。
二、研究目的:本研究旨在研究轧机平衡块深孔加工的工艺,并探讨如何提高加工效率和加工质量。
同时,希望通过此项研究,能够推动轧机生产加工技术的不断发展与完善。
三、研究内容:1. 分析轧机平衡块深孔加工的工艺流程和要求,包括孔径、孔深、精度等方面。
2. 研究不同的孔钻类型和孔钻材料对轧机平衡块深孔加工的影响。
寻找最适宜的孔钻类型和孔钻材料。
3. 探讨合理的切削参数选择对轧机平衡块深孔加工的影响,如切削速度、进给量、切削深度等。
4. 研究轧机平衡块深孔加工时,所产生的提离力、摩擦力和热变形的影响,探究如何减小这些影响。
5. 对轧机平衡块深孔加工的工艺进行模拟,验证研究结果的正确性和可行性。
四、研究方法:1. 文献资料法:并结合国内外相关领域的研究成果,了解和掌握轧机平衡块深孔加工的基本情况,为后续研究提供理论支持。
2. 实验研究法:通过对轧机平衡块进行实验验证,寻找最适宜的加工工艺参数组合,以提高加工质量和效率。
3. 数值模拟法:运用数值模拟技术,对轧机平衡块深孔加工的工艺进行模拟分析,验证研究结果的正确性和可行性。
五、预期结果:通过上述研究方法进行轧机平衡块深孔加工工艺的研究,可得到以下预期结果:1. 轧机平衡块深孔加工的工艺流程和要求已经形成一个比较完整的体系。
2. 寻找到了最适宜的孔钻类型和孔钻材料,并得出了合理的切削参数选择对轧机平衡块深孔加工的影响。
3. 研究出在加工过程中降低提离力、摩擦力和热变形的方法,提高了加工效率和加工质量。
4. 数值模拟技术证明了实验研究结果的正确性和可行性。
轧辊加工智能化研究孙韶锋
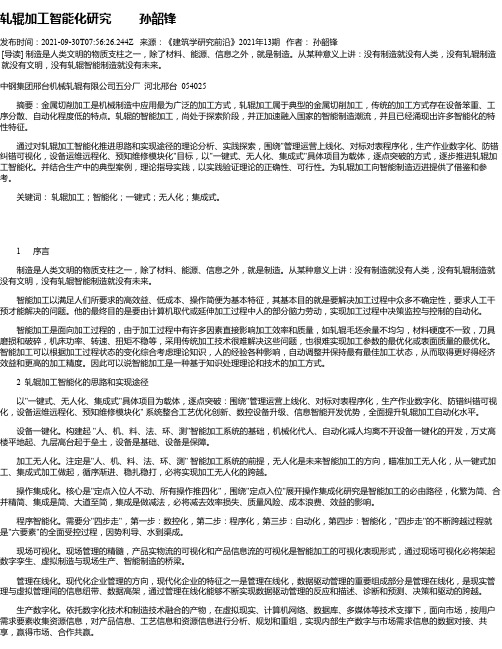
轧辊加工智能化研究孙韶锋发布时间:2021-09-30T07:56:26.244Z 来源:《建筑学研究前沿》2021年13期作者:孙韶锋[导读] 制造是人类文明的物质支柱之一,除了材料、能源、信息之外,就是制造。
从某种意义上讲:没有制造就没有人类,没有轧辊制造就没有文明,没有轧辊智能制造就没有未来。
中钢集团邢台机械轧辊有限公司五分厂河北邢台 054025摘要:金属切削加工是机械制造中应用最为广泛的加工方式,轧辊加工属于典型的金属切削加工,传统的加工方式存在设备笨重、工序分散、自动化程度低的特点。
轧辊的智能加工,尚处于探索阶段,并正加速融入国家的智能制造潮流,并且已经涌现出许多智能化的特性特征。
通过对轧辊加工智能化推进思路和实现途径的理论分析、实践探索,围绕"管理运营上线化、对标对表程序化,生产作业数字化、防错纠错可视化,设备运维远程化、预知维修模块化"目标,以"一键式、无人化、集成式"具体项目为载体,逐点突破的方式,逐步推进轧辊加工智能化。
并结合生产中的典型案例,理论指导实践,以实践验证理论的正确性、可行性。
为轧辊加工向智能制造迈进提供了借鉴和参考。
关键词:轧辊加工;智能化;一键式;无人化;集成式。
1 序言制造是人类文明的物质支柱之一,除了材料、能源、信息之外,就是制造。
从某种意义上讲:没有制造就没有人类,没有轧辊制造就没有文明,没有轧辊智能制造就没有未来。
智能加工以满足人们所要求的高效益、低成本、操作简便为基本特征,其基本目的就是要解决加工过程中众多不确定性,要求人工干预才能解决的问题。
他的最终目的是要由计算机取代或延伸加工过程中人的部分脑力劳动,实现加工过程中决策监控与控制的自动化。
智能加工是面向加工过程的,由于加工过程中有许多因素直接影响加工效率和质量,如轧辊毛坯余量不均匀,材料硬度不一致,刀具磨损和破碎,机床功率、转速、扭矩不稳等,采用传统加工技术很难解决这些问题,也很难实现加工参数的最优化或表面质量的最优化。
周期冷轧辊孔型数控车削加工分析
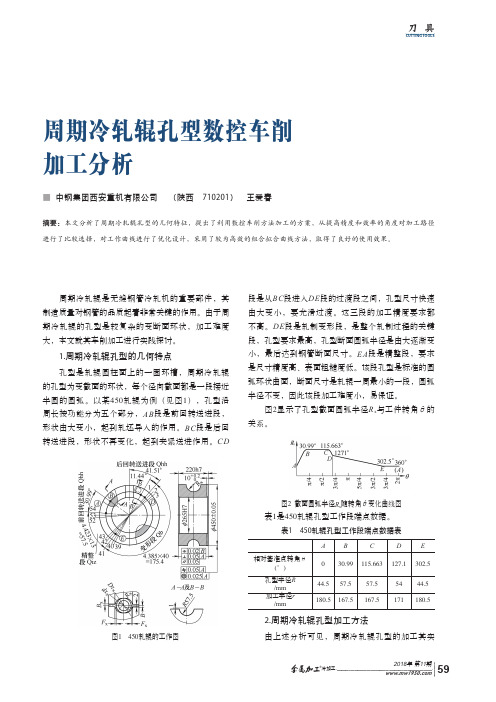
2018年 第11期冷加工59CUTTING TOOLS刀 具周期冷轧辊孔型数控车削加工分析■■中钢集团西安重机有限公司 (陕西 710201) 王爱春摘要:本文分析了周期冷轧辊孔型的几何特征,提出了利用数控车削方法加工的方案,从提高精度和效率的角度对加工路径进行了比较选择,对工作曲线进行了优化设计,采用了较为高效的组合拟合曲线方法,取得了良好的使用效果。
周期冷轧辊是无缝钢管冷轧机的重要部件,其制造质量对钢管的品质起着非常关键的作用。
由于周期冷轧辊的孔型是较复杂的变断面环状,加工难度大,本文就其车削加工进行实践探讨。
1.周期冷轧辊孔型的几何特点孔型是轧辊圆柱面上的一圈环槽,周期冷轧辊的孔型为变截面的环状,每个径向截面都是一段接近半圆的圆弧。
以某450轧辊为例(见图1),孔型沿周长按功能分为五个部分,AB 段是前回转送进段,形状由大变小,起到轧坯导入的作用。
BC 段是后回转送进段,形状不再变化,起到夹紧送进作用。
CD段是从BC 段进入DE 段的过渡段之间,孔型尺寸快速由大变小,要光滑过渡。
这三段的加工精度要求都不高。
DE 段是轧制变形段,是整个轧制过程的关键段,孔型要求最高,孔型断面圆弧半径是由大逐渐变小,最后达到钢管断面尺寸。
EA 段是精整段,要求是尺寸精度高、表面粗糙度低。
该段孔型是标准的圆弧环状曲面,断面尺寸是轧辊一周最小的一段,圆弧半径不变,因此该段加工难度小,易保证。
图2显示了孔型截面圆弧半径R x 与工件转角θ的关系。
图2 截面圆弧半径R x 随转角θ变化曲线图表1是450轧辊孔型工作段端点数据。
表1 450轧辊孔型工作段端点数据表AB C D E 相对基准点转角θ(°)030.99115.663127.1302.5孔型半径R /mm 44.557.557.55444.5加工半径r /mm180.5167.5167.5171180.52.周期冷轧辊孔型加工方法由上述分析可见,周期冷轧辊孔型的加工其实图1 450轧辊的工作图2018年 第11期冷加工60CUTTING TOOLS刀 具是一种复杂的非圆回转曲面加工问题。
轧辊孔型数控车削加工工艺参数优化研究
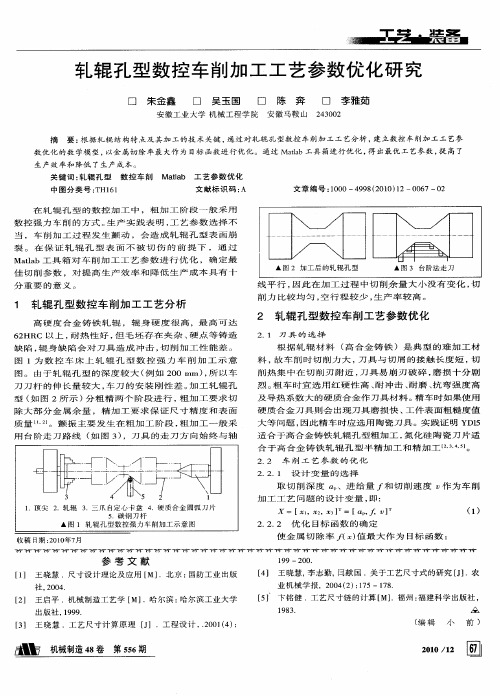
数 优 化 的数 学模 型 , 以金 属 切 除 率 最 大作 为 目标 函数 进 行 优 化 。通 过 Maa 具 箱 进 行 优 化 , 出最优 工 艺参 数 , 高 了 tb工 l 得 提
生 产 效 率 和 降低 了生 产 成 本 。
关键词 : 轧辊 孔 型
数控 车 削 Malb 工 艺 参 数 优 化 t a 文献标识码 : A 文 章 编 号 :0 0—4 9 (0 0 1 10 9 82 1 )2—0 6 0 7—0 2
佳 切 削 参 数 ,对 提 高 生 产 效 率 和 降 低 生 产 成 本 具 有 十
分 重要 的意义 。
线 平 行 , 此 在 加 工 过 程 中 切 削余 量 大 小 没 有 变 化 , 因 切 削 力 比较 均 匀 , 行 程 较 少 , 产 率 较 高 。 空 生
1 轧 辊 孔 型 数 控 车 削 加 工 工 艺 分 析
中 图分 类 号 :H1 1 T 6
在 轧 辊 孔 型 的 数 控 加 工 中 ,粗 加 工 阶 段 一 般 采 用
数 控 强 力 车 削 的 方 式 。 产 实 践 表 明 , 艺 参 数 选 择 不 生 工
当 , 车 削 加 工 过 程 发 生 颤 动 ,会 造 成 轧 辊 孔 型 表 面 崩 裂 。 在 保 证 轧 辊 孔 型 表 面 不 被 切 伤 的 前 提 下 , 通 过 MalbZ 具 箱 对 车 削 加 工 工 艺 参 数 进 行 优 化 , 确 定 最 t ] a Z
设计 变量 的选择 2 2.1 .
除 大 部 分 金 属 余 量 ,精 加 工 要 求 保 证 尺 寸 精 度 和 表 面
质 量 。颤 振 主 要 发 生 在 粗 加 工 阶 段 , 加 工 一 般 采 粗 ( 图 3 ,刀 具 的 走 刀 方 向 始 终 与 轴 如 ) 用 台 阶走 刀路线
深度改造机组穿孔辊加工工艺分析

深度改造机组穿孔辊加工工艺分析龚晗① 朱旭毅(常州宝菱重工机械有限公司 江苏常州213019)摘 要 改善现有穿孔辊加工工艺,加速穿孔辊的生产制造。
以140深度改造机组某种穿孔辊为研究对象,分析并改善其加工工艺,通过逐步分析每一道加工工序,发现工艺中可取之处与不足之处,并加以优化改善。
基于原有加工工艺,形成一套新的穿孔辊加工工艺,保留原有工艺长处的同时,进一步提升穿孔辊的加工质量与加工速度,在满足客户要求的同时缩短加工周期,更好又快的生产。
成功优化现有的穿孔辊加工工艺,可以应用于穿孔辊的加工生产。
关键词 无缝钢管;轧辊;40Cr;加工工艺中图法分类号 TG TH161 文献标识码 ADoi:10 3969/j issn 1001-1269 2024 01 016AnalysisofProcessinPerforatingRollGongHan ZhuXuyi(ChangzhouBaolingHeavy&IndustrialMachineryCo.,Ltd.,Changzhou213019)ABSTRACT Improvetheexistingperforatingrollerprocessingtechnology,acceleratetheproductionofperforatingroller.Takingakindofperforatingrollof140deepretrofitunitastheresearchobject,theprocessingtechnologyisanalyzedandimproved.Byanalyzingeachprocessstepbystep,theadvantagesanddisadvantagesoftheprocessarefound,andtheprocessisoptimizedandimproved.Basedontheoriginalprocessingtechnology,anewprocessingtechnologyofperforatingrollisformed,whichcanimprovetheprocessingqualityandspeedofperforatingrollwhileretainingtheadvantagesoftheoriginaltechnology,inmeetingcustomerrequirementswhileshorteningtheprocessingcycle,betterandfasterproduction.Finally,theexistingperforatingrollerprocessingtechnologyissuccessfullyoptimized,whichcanbeappliedtotheperforatingrollerprocessingproduction.KEYWORDS Seamlesssteelpipe;Roller;40Cr;Processingtechnology1 前言作为生产无缝钢管的穿孔机设备上的重要零件之一,穿孔辊的质量关乎着穿孔机的生产质量与生产寿命,但穿孔辊本身来说却是作为易消耗品的存在,到达使用寿命后就要更换。
轧辊的孔型设计
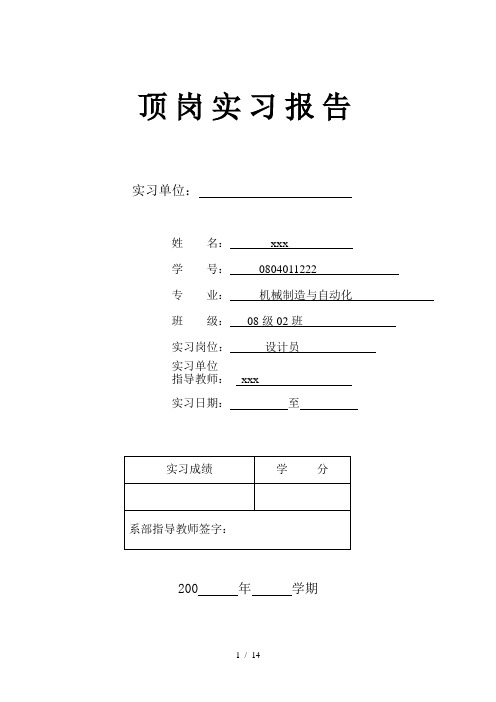
顶岗实习报告实习单位:姓名:xxx学号:0804011222专业:机械制造与自动化班级:08级02班实习岗位:设计员实习单位指导教师:xxx实习日期:至200 年学期目录第一章:公司简介……………………….......... ………………………………………………..2页第二章:焊管冷弯轧辊概述................ ………………………………………………3页第1节:焊管机组的简介…………………………………………………………..3页第2节:轧辊的孔型设计简介……………………………………………………..4页第三章:轧辊的孔型设计概述…………………………………………………………………..5页第1节:成型机轧辊孔型设计概述. ………………………………………………..5页第2节:成型机孔型计算程序…………………………………………………………8页第四章:双半径孔型设计…………………….. ………………………………………………..8页第五章:实习总结………………………………... ………………………………………………12页第一章:公司简介石家庄石轴轧辊制造有限公司是集设计、制造、售后服务于一身的专业轧辊制造企业。
本公司汇集了一批轧辊专业的优秀工程师、产品开发人员。
专门生产焊管设备配套使用的轧辊、纵剪刀片等产品。
公司专业孔型设计人员具有丰富的模具设计、实践经验,并在设计中采用德国Copra 软件进行优化。
融合欧美日等国的优点,结合成型机组的特点及用户要求,对轧辊进行优化设计,其孔型设计方案得到国内多名专家的肯定和认可。
先进的设计、精良的制造深得用户的赞誉。
我们在此顶岗实习期间,学到了不少的知识,主要是针对圆管的轧辊孔型的设计,以及冷弯型钢的轧辊设计。
轧辊的的孔型设计是根据孔型按开口位置分为开口孔型和闭口孔型。
按形状分为简单断面孔型,和复杂断面孔型。
复杂断面孔型又称异形孔型,包括斜形孔型、蝶形孔型、弯腰孔型,和万能孔型。
轧辊孔型数控车削加工工艺参数优化研究

轧辊孔型数控车削加工工艺参数优化研究朱金鑫;吴玉国;陈奔;李雅茹【摘要】根据轧辊结构特点及其加工的技术关键,通过对轧辊孔型数控车削加工工艺分析,建立数控车削加工工艺参数优化的数学模型,以金属切除率最大作为目标函数进行优化.通过Matlab工具箱进行优化,得出最优工艺参数,提高了生产效率和降低了生产成本.【期刊名称】《机械制造》【年(卷),期】2010(048)012【总页数】2页(P67-68)【关键词】轧辊孔型;数控车削;Matlab;工艺参数优化【作者】朱金鑫;吴玉国;陈奔;李雅茹【作者单位】安徽工业大学机械工程学院,安徽马鞍山,243002;安徽工业大学机械工程学院,安徽马鞍山,243002;安徽工业大学机械工程学院,安徽马鞍山,243002;安徽工业大学机械工程学院,安徽马鞍山,243002【正文语种】中文【中图分类】TH161在轧辊孔型的数控加工中,粗加工阶段一般采用数控强力车削的方式。
生产实践表明,工艺参数选择不当,车削加工过程发生颤动,会造成轧辊孔型表面崩裂。
在保证轧辊孔型表面不被切伤的前提下,通过Matlab工具箱对车削加工工艺参数进行优化,确定最佳切削参数,对提高生产效率和降低生产成本具有十分重要的意义。
1 轧辊孔型数控车削加工工艺分析高硬度合金铸铁轧辊,辊身硬度很高,最高可达62HRC以上,耐热性好,但毛坯存在夹杂、硬点等铸造缺陷,辊身缺陷会对刀具造成冲击,切削加工性能差。
图1为数控车床上轧辊孔型数控强力车削加工示意图。
由于轧辊孔型的深度较大(例如200 mm),所以车刀刀杆的伸长量较大,车刀的安装刚性差。
加工轧辊孔型(如图2所示)分粗精两个阶段进行,粗加工要求切除大部分金属余量,精加工要求保证尺寸精度和表面质量[1,2]。
颤振主要发生在粗加工阶段,粗加工一般采用台阶走刀路线(如图3),刀具的走刀方向始终与轴线平行,因此在加工过程中切削余量大小没有变化,切削力比较均匀,空行程较少,生产率较高。
数控车床在型钢轧辊孔型加工中的应用分析

数控车床在型钢轧辊孔型加工中的应用分析发布时间:2022-10-27T09:15:11.910Z 来源:《科技新时代》2022年第11期6月作者:王雷陈瑶[导读] 我国经济的不断发展,科学技术也在不断进步,我们可以根据型钢轧辊的自身结构特征、安装的方式以及不同的加工方法等要求王雷陈瑶中车大连机车车辆有限公司辽宁大连 116021摘要:我国经济的不断发展,科学技术也在不断进步,我们可以根据型钢轧辊的自身结构特征、安装的方式以及不同的加工方法等要求,来对普通扎辊车床在加工的过程中存在的问题进行研究和分析,将数控车床在型钢轧辊孔型加工中的优势进行有效的利用。
因此,本文将针对数控车床在型钢扎昆孔型加工中的应用进行浅要的分析,简单的介绍了数控机床在加工中的主要优势,以及普通扎辊车床在加工中出现的问题,为了实现型钢轧辊加工高质量进行,奠定良好的基础,实现高效率的工作要求。
关键词:数控车床;型钢轧辊;孔型加工;应用分析引言想要热轧型钢能够高质量的进行生产,就需要优秀的孔型系统,和良好的配辊形式,这样才能有针对性的,对产品的尺寸进行更加精准的打量,对其表面质量[这里不对吧、]进行严谨的把控,有效地提高其力学性能进一步的降低轧辊以及电力的损耗。
我国的科学技术在不断的发展和进步,所代表的社会生产能力也得到了有效的提高,所以人们对于产品的质量以及生产线的工作效率也提出了更高的要求。
所以我们要满足市场的需要,进一步是扎辊加工的质量得到明显提升,提高生产线的工作效率。
以前传统的轧辊车床已经无法满足时代的需要,现阶段很多公司利用高精度的数控技术,来对型钢轧辊的孔型进行加工,并且取得了卓越的成效,提高了生产效率。
一、普通轧辊车床加工轧辊的流程及存在的问题1.1 普通轧辊车床加工轧辊的流程普通轧辊车床以H型钢三辊开坯斜扎孔型为代表,它是由很多个孔型以及只推辊环所构成的,所以横截面的形状比较复杂,一部分的尺寸很小,但是切入的深度大,部分区域的尺寸有很强的关联性。
- 1、下载文档前请自行甄别文档内容的完整性,平台不提供额外的编辑、内容补充、找答案等附加服务。
- 2、"仅部分预览"的文档,不可在线预览部分如存在完整性等问题,可反馈申请退款(可完整预览的文档不适用该条件!)。
- 3、如文档侵犯您的权益,请联系客服反馈,我们会尽快为您处理(人工客服工作时间:9:00-18:30)。
轧辊深孔加工工艺研究
————————————————————————————————作者:————————————————————————————————日期:
轧辊深孔加工工艺研究-工程论文
轧辊深孔加工工艺研究
王进义WANG Jin-yi
(宝钢轧辊科技有限责任公司,常州213019)
(Baosteel Roll Technology Co.,Ltd.,Changzhou 213019,China)
摘要:由于目前在机加工行业内加工高精度深孔是一个很大的难题,没有一种很好的解决办法,通常的加工办法往往加工效果差,精度低,因此,本文介绍了一种轧辊生产过程中高精度端部深孔的加工工艺方案,对如何选择机床设备、定位基准和装夹方法、工艺规程及参数的选择以及内孔尺寸公差的测量方法进行了详细的介绍,解决了一些加工工艺难题,和加工深孔的难题。
Abstract:In machinery industry,the manufacture of high precision deep hole is a difficult problem at present. The processing effect of ordinary processing methods usually is poor,and the precision is low. Therefore,this paper introduces production process the high precision processing scheme of end hole of the roll. The measurement methods on how to select the machine tool equipment. Positioning and clamping method,technological process and parameter selection and the hole size tolerance are introduced in detail to solve the problem of deep-hole drilling.
关键词:轧辊;深孔加工;加工工艺
Key words:roll;deep-hole drilling;processing technology
中图分类号:TG53 文献标识码:A 文章编号:1006-4311(2015)
18-0056-03
作者简介:王进义(1980-),男,河北沧州人,工程师,硕士,技术人员,研究方向为机加工工艺。
0 引言
小孔加工一般采用麻花钻在普通钻床、车床、镗铣床上加工,大孔采用车床或镗床先进行钻加工、然后进行镗加工。
通常讲的深孔一般是指长径比大于10的孔,而对于长径比大于50mm的深孔而言由于受到加长钻头刚性的影响,在加工过程中要保证加工的不偏心实现起来有很大的困难。
1 轧辊深孔的加工
1.1 深孔加工的特点
孔加工的几大问题:排屑、散热和导向问题,主要表现在:
①钻孔时不能直接观察刀具的切削状况,工作过程中只能凭借听声音、看切屑、摸振动等外观现象来判断切削过程是否正常;
②孔的长径比大、钻杆细而长、刚性低、易振动、钻孔易走偏,因此,支撑及导向十分重要;
③切削热不易散出,工作条件恶劣,必须采用有效的冷却方式。
1.2 轧辊深孔加工难点分析
工件深孔如图1所示,材料为H13锻钢,成品重量3555kg,装配图如图2所示,出口产品。
设计要求:孔深5050mm由三个台阶孔组成,最外端内孔粗糙度Ra0.8,里面两深孔为60度锥面连接,同轴度φ0.1mm,装配深度450mm,装配间隙端部塞尺0.1塞不进,过盈量0.28-0.35mm。
针对这种总长较长,长径比大、同轴度要求高的精密产品,加工此种产品的难度如下:
①轧辊吨位较重长度较长装夹定位困难;
②内孔较深,粗糙度Ra0.8,同轴度≤φ0.1mm;
③装配过盈量0.28-0.35mm,装配辊颈部分长450mm,必须保证装配面的圆柱度;
④辊身淬火,因此热装时温度不能高于回火温度,增加了装配的难度,同时对
孔的尺寸精度要求提出了更高的要求。
在此种情况下,加工此类深孔对位置及加工效果要求较高,加工难度大,为此本文进行了详细的分析和探索,制定了切实有效的加工工艺方案。
1.3 加工设备的确定
如何正确选择加工设备是保证加工质量很重要的环节,加工设备的选择是否得当,对于产品的加工质量,生产效率有很大的影响。
该辊内孔如在车床上加工难度较大:工件较长,装夹困难,易变形,需多中心架支撑,并需要设计辅助工装;刀杆处于悬臂状态,刚性差,加工时会产生振动和让刀现象;加工两内孔锥度连接面时加工难度较大。
综上所述,选择车床加工,不但操作复杂,生产效率低,加工质量无法保证。
因此,为缩短加工工序步骤,前期粗镗孔可采用车床加工,最终工序需采用数控镗对内孔进行精加工。
鉴于以上状况,结合宝钢轧辊科技有限责任公司设备及工件特点,确定最终孔的加工选择在TK6916数控镗床上加工。
1.4 加工工艺措施
最优工艺方案的选择就是确定一条达到产品质量的最低成本或最少加工时间的工艺路线。
要达到图纸设计要求,首先必须从工艺上保证工件的加工精度。
如何在多种加工工艺路线中选择一种最优方案是本文关注的问题。
1.4.1 孔的加工工艺规程
①产品半精车后在车床上进行钻导向孔φ100深100mm;
② 按图纸要求用深孔钻进行钻深孔φ100、φ180及圆锥过渡部分;
③车床上镗孔φ210(0,+0.029)至φ200,深475mm,车出圆角R5;
④实配闷头,并进行粗磨、淬火、精车等工序;
⑤拆除闷头,以外圆为基准,对φ210(0,+0.029)孔进行精镗加工;
⑥检验内孔尺寸及粗糙度等保证满足图纸要求。
1.4.2 精镗孔时工件的定位与装夹
轧辊在镗床工作台上初步定位之后,以镗床主轴为基准进行找正,确定工件与镗床之间的相对位置,找正用百分表测试的方法控制工件在水平方向和垂直方向的误差,一般控制在0.02mm以内。
轧辊找正定位后,为了减少变形和夹紧力,采用压板将轧辊加紧固定,在安全可靠的前提下,大大减少了加工时的振动,提高了加工精度。
1.4.3 切削参数的选择
为了避免内孔产生圆柱度超差,且内孔无法采用磨削加工,因此,采用高速镗削的方法,切削过程中保证切屑和加工表面的塑性变形小,并提高了表面的加工粗糙度。
内孔加工是连续切削,因此采用YT15钨钴钛类合金刀具进行加工。
镗加工时需先进行粗镗加工,粗加工后需根据外圆检验镗杆是否发生了移动,检验无变化后进行最终的精镗加工,为了避免因为温度的变化影响加工精度,内孔精镗的最后一刀最好在环境变化较小的晚上进行,并一次性连续走刀加工完成。
1.4.4 冷却润滑
冷却润滑液在深孔加工中主要起冷却、润滑、冲刷、减振和消声的作用。
加工中产生的切削抗力,消耗很多的能量,而且其切向和径向分力作用在导向块上,与孔壁产生较大的摩擦力,都转化为很多的切削热,这些热量主要靠冷却润滑液把它带走。
冷却润滑液在导向块与孔壁之间建立起液压支撑,可降低导向块的摩擦,减小
功率消耗。
冷却润滑液的冲刷作用,是靠一定的压力和流量的冷却液将切屑由切削区冲刷出来,实现排屑作用。
由于在工作区内部充满了一定压力的油液,能减弱由切削运动和摩擦作用所产生的振动和噪音。
1.4.5 尺寸测量
在加工完成后测量内孔尺寸时,如果不抽出镗杆,内径千分尺无法测量,若抽出镗刀杆,测量后需要重新找正,很不方便。
可采用在镗排上过镗杆中心位置钻一安装内径千分尺的孔,使内径千分尺延长杆能插进去,如图3所示。
使用时,只要将将内径千分尺插入镗杆上径向孔内,移动工作台,固定测头接触产品内孔,用于转动微分头接触内孔,紧固微分头,然后拿出,便可准确测量内孔的实际尺寸。
2 实施的效果
该产品已经按照此种工艺方案顺利实施,加工后的产品经过三坐标测量仪和圆度仪全尺寸合格,内孔尺寸和形位公差完全满足了产品图纸设计要求,而且工艺保证能力稳定,产品质量可靠。
在用户检测合格后已经顺利实行了装配验收,装配后间隙达到了满意效果,受到用户好评,并最终顺利完成了成品的交货。
本加工方案,提高了精密大孔的加工效率,解决了一定的加工难题,是一种可
靠可行的加工方法,实用性强,其经验可供内孔加工同行参考和推广使用。
参考文献:
[1]王峻.深孔加工技术[M].哈尔滨:哈尔滨工业大学出版社,2004.
[2]孟少农.机械加工工艺手册[M].北京:机械工业出版社,1998.
[3]赵如意.深孔加工振动产生原因以及减震方法研究[D].中北大学,2011.。