天然气MRC液化工艺电气部分技术方案
天然气液化项目工艺技术方案
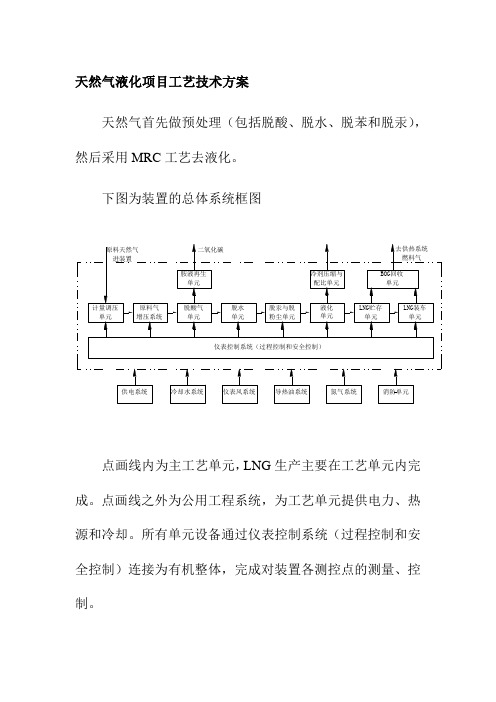
天然气液化项目工艺技术方案天然气首先做预处理(包括脱酸、脱水、脱苯和脱汞),然后采用MRC 工艺去液化。
下图为装置的总体系统框图点画线内为主工艺单元,LNG 生产主要在工艺单元内完成。
点画线之外为公用工程系统,为工艺单元提供电力、热源和冷却。
所有单元设备通过仪表控制系统(过程控制和安全控制)连接为有机整体,完成对装置各测控点的测量、控制。
1.1天然气制液态天然气(LNG)◆原料天然气过滤与调压单元原料天然气从界区来,首先进入过滤分离器,过滤掉可能存在的机械杂质、灰尘,并分离出其中的液体(主要为游离水和液态烃),为后续系统提供洁净的天然气。
洁净的原料天然气进入调压器,将压力调整并稳定至1.0MPa.G,然后经计量后进入后续单元。
原料气进装置设置有事故联锁切断阀,在事故发生后将切断进入装置的原料气源,同时通过旁路放空原料气,保证装置、人员及上游设施的安全。
◆原料天然气脱酸性气单元从原料天然气过滤与压缩单元来的天然气从吸收塔下部进入,自下而上通过吸收塔;再生后的MDEA溶液(贫液)从吸收塔上部进入,自上而下通过吸收塔,逆向流动的MDEA溶液和天然气在吸收塔内充分接触,气体中的H2S和CO2被吸收而进入液相,未被吸收的组份从吸收塔顶部引出,进入脱碳气冷却器和分离器。
出脱碳气分离器的气体进入原料气干燥单元,冷凝液去MDEA地下槽。
处理后的天然中CO2含量小于50ppmV,H2S含量小于4ppmV。
吸收了H2S和CO2的MDEA溶液称富液,至闪蒸塔,降压闪蒸出的天然体送往界外燃料系统。
闪蒸后的富液与再生塔底部流出的溶液(贫液)换热后,升温到~98℃去再生塔上部,在再生塔进行汽提再生,直至贫液的贫液度达到指标。
出再生塔的贫液经过溶液换热器、贫液泵进入贫液冷却器,贫液被冷却到~40℃,从吸收塔上部进入。
再生塔顶部出口气体经酸气冷却器,进入酸气分离器,出酸气分离器的气体送往安全泄压系统,冷凝液去MDEA 地下槽。
10万方天然气液化装置工艺流程培训内容(刘康)
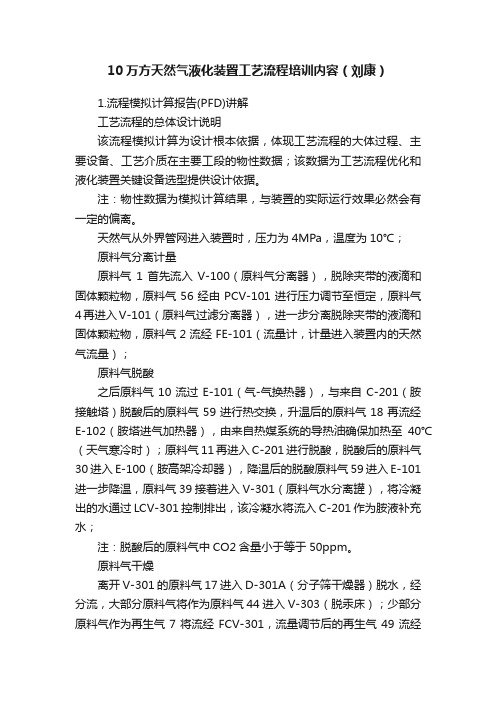
10万方天然气液化装置工艺流程培训内容(刘康)1.流程模拟计算报告(PFD)讲解工艺流程的总体设计说明该流程模拟计算为设计根本依据,体现工艺流程的大体过程、主要设备、工艺介质在主要工段的物性数据;该数据为工艺流程优化和液化装置关键设备选型提供设计依据。
注:物性数据为模拟计算结果,与装置的实际运行效果必然会有一定的偏离。
天然气从外界管网进入装置时,压力为4MPa,温度为10℃;原料气分离计量原料气1首先流入V-100(原料气分离器),脱除夹带的液滴和固体颗粒物,原料气56经由PCV-101进行压力调节至恒定,原料气4再进入V-101(原料气过滤分离器),进一步分离脱除夹带的液滴和固体颗粒物,原料气2流经FE-101(流量计,计量进入装置内的天然气流量);原料气脱酸之后原料气10流过E-101(气-气换热器),与来自C-201(胺接触塔)脱酸后的原料气59进行热交换,升温后的原料气18再流经E-102(胺塔进气加热器),由来自热媒系统的导热油确保加热至40℃(天气寒冷时);原料气11再进入C-201进行脱酸,脱酸后的原料气30进入E-100(胺高架冷却器),降温后的脱酸原料气59进入E-101进一步降温,原料气39接着进入V-301(原料气水分离罐),将冷凝出的水通过LCV-301控制排出,该冷凝水将流入C-201作为胺液补充水;注:脱酸后的原料气中CO2含量小于等于50ppm。
原料气干燥离开V-301的原料气17进入D-301A(分子筛干燥器)脱水,经分流,大部分原料气将作为原料气44进入V-303(脱汞床);少部分原料气作为再生气7将流经FCV-301,流量调节后的再生气49流经H-301(再生气电加热器),加热升温后的再生气27进入D-301B (分子筛干燥器)进行分子筛再生;之后再生气28进入E-301(再生气冷却器),冷却至45℃后的再生气29进入V-302(再生气分离器)分离出冷凝的水分,之后再生气12进入K-301(再生气循环压缩机)增压,增压后的再生气进入E-302(再生气压缩机冷却器)降温,降温后的再生气38与原料气11会合,重新进入C-201开始新的循环。
C_3_MRC混合制冷剂组成对液化天然气流程的影响_蒙芸
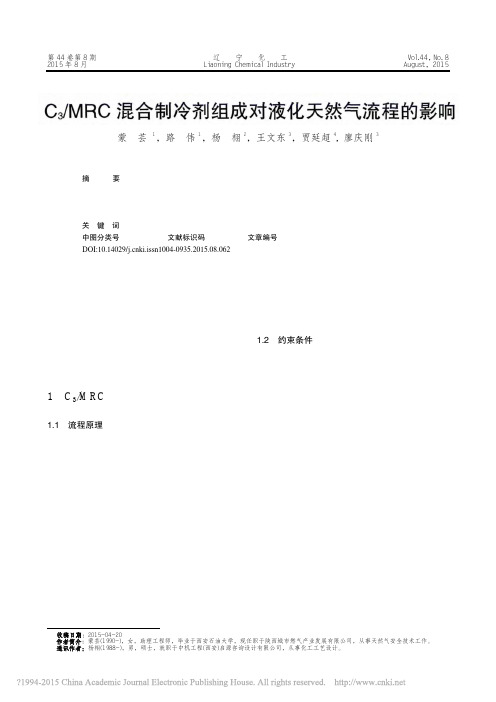
(2)在混合制冷剂循环天然气液化流程中,每
1 C3/MRC 液化天然气流程原理及约 束条件
1.1 流程原理 丙烷预冷混合制冷剂循环天然气液化流程(见
图 1,2)是由一个开式制冷循环(天然气液化循环) 和两个闭式制冷循环(丙烷压缩预冷循环、混合制 冷剂循环、)三部分组成[2]。
原料天然气在天然气液化循环中,经过丙烷预 冷循环预冷后,逐级换热冷却,最后节流降压,使 液化天然气得以在常压下贮存。丙烷压缩预冷循环 主要是预冷天然气和混合制冷剂;混合制冷剂循环 主要是用于深冷和液化天然气。混合制冷剂经两级 压缩,中间冷却后进入气液分离器,产生的富丙烷 液相经第一换热器冷却后节流,降温降压,与返流 的混合制冷剂混合回流第一换热器内完全气化,为 其提供冷能,冷却天然气和被分离的气液两相物 流。而产生的富乙烷气相被部分冷凝成气液两相后
950
辽宁
(7)第一个压缩机的出口压力不能超过第二个
化工
2015 年 8 月
压缩机的出口压力,且出口温度不能超过 150 ℃。
图 1 丙烷预冷混合制冷剂循环天然气液化流程图
图 2 丙烷压缩预冷循环图
2 混合制冷剂组成对液化流程的影 响
原料气和混合制冷剂的初始设定值见表 1。该 流程中,混合制冷剂组成、压力和温度等参数对流 程的可行性、压缩机耗功、混合制冷剂的流量和换
5)保持 MR 流量不变时,适当减少混合制冷剂 中丙烷组分的量,该流程所需的 LNG 流量增加;适 当增加混合制冷剂中氮气组分的量,该流程所需的 比功耗降低。
6)该流程混合制冷剂的最优配比是:甲烷 0.436,
952
辽宁
乙烷 0.393,丙烷 0.099,氮气 0.072,此时流程压缩 机比功耗为 7.692 kW·h/kmol。
一种混合制冷剂循环_MRC_液化天然气流程的理论分析_石玉美

3本文得到国家自然科学基金的资助(59576001)。
33石玉美,女,1970年生;1998年毕业于上海交通大学制冷与低温工程研究所,获工学博士学位;现为上海交通大学动力与能源工程学院制冷与低温工程研究所教师,主要从事天然气物性及液化流程的研究,已发表论文近二十篇。
地址:(200030)上海华山路一九五四号。
电话:(021)62932602。
图1 带回热的混合制冷剂循环液化天然气流程一种混合制冷剂循环(MRC )液化天然气流程的理论分析3石玉美33 顾安忠 汪荣顺 鲁雪生(上海交通大学) 石玉美等.一种混合制冷剂循环(MRC )液化天然气流程的理论分析.天然气工业,2000;20(3):92~95 摘 要 将天然气液化有利于天然气的运输、有利于边远天然气的回收并能降低天然气的储存成本。
在天然气液化流程中,用得最多的液化循环是混合制冷剂循环液化天然气流程。
它具有机组设备少、流程简单、投资省及管理方便等优点。
为此,对这类流程进行了理论分析。
系统介绍了一带回热的典型混合制冷剂循环液化天然气流程的计算方法;并进行了全流程的模拟,得到了流程各节点压力、温度、焓、熵、气液两相流量、总流量、气液两相摩尔分率;同时还计算了流程中压缩机耗功、丙烷预冷量、制冷剂流量、各换热器的换热量等表示流程性能的参数。
主题词 制冷剂 循环 天然气液化 流程 模拟 计算 1972年至1999年,有8个不同的国家用了混合制冷剂循环液化天然气流程。
马来西亚准备在Bin 2tulu 建造的第三座LN G 加工厂也将采用这种液化流程〔1,2〕。
目前,我国在天然气液化流程方面的定量研究工作做得很少,随着我国天然气的不断勘探、开采和使用,需要对天然气的液化进行深入的研究,自主开发这方面的软件。
针对带回热的混合制冷剂循环液化天然气流程进行了系统模拟。
带回热的混合制冷剂循环液化天然气流程是低压制冷剂在进压缩机之前,与被水冷却后的高压制冷剂进行回热,充分利用低压制冷剂的冷量;同时也使低压制冷剂进入压缩机时温度升高,避免压缩机液击事故的发生。
液化天然气的工艺流程 毕业论文
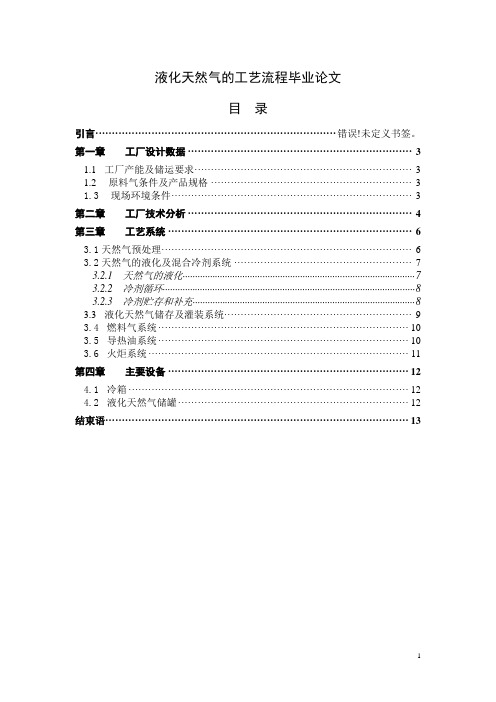
液化天然气的工艺流程毕业论文目录引言.........................................................................错误!未定义书签。
第一章工厂设计数据 .. (3)1.1工厂产能及储运要求 (3)1.2原料气条件及产品规格 (3)1.3现场环境条件 (3)第二章工厂技术分析 (4)第三章工艺系统 (6)3.1天然气预处理 (6)3.2天然气的液化及混合冷剂系统 (7)3.2.1 天然气的液化 (7)3.2.2 冷剂循环 (8)3.2.3 冷剂贮存和补充 (8)3.3液化天然气储存及灌装系统 (9)3.4燃料气系统 (10)3.5导热油系统 (10)3.6火炬系统 (11)第四章主要设备 (12)4.1冷箱 (12)4.2液化天然气储罐 (12)结束语 (13)前言2004年我国建成投运了目前国内规模最大的基本负荷型液化天然气(LNG)工厂,曰处理天然气150万m3,LNG年产量约为43万吨。
该工厂由德国Linde 公司提供天然气处理和液化技术,由德国 Tractebel Gas Enginering(TGE)公司提供LNG的储存和灌装配送技术。
工厂的原料气来自附近土哈丘东采油厂的油气田。
生产的LNG灌装在集装箱罐中,通过公路运输到各个接收站,然后,LNG被汽化并经过较短的管线输送给工业和民用客户。
本文对该工厂的工艺流程进行技术分析,以期对国内液化天然气工厂的设计提供一些有益的借鉴。
第一章工厂设计数据1.1 工厂产能及储运要求工厂为基本负荷型液化天然气生产工厂,每年连续运行时间8000h,液化能力54t/h,操作弹性50%~100%。
LNG储罐容积为30000m3,能满足10天产量的储存。
LNG配送灌装系统每天连续14h灌装100个集装箱罐,其中90%公路运输,。
1.2 原料气条件及产品规格通过管道输送来的原料气来自附近的油气田,原料气组成见表1。
mrc天然气液化流程的工作原理

mrc天然气液化流程的工作原理下载温馨提示:该文档是我店铺精心编制而成,希望大家下载以后,能够帮助大家解决实际的问题。
文档下载后可定制随意修改,请根据实际需要进行相应的调整和使用,谢谢!并且,本店铺为大家提供各种各样类型的实用资料,如教育随笔、日记赏析、句子摘抄、古诗大全、经典美文、话题作文、工作总结、词语解析、文案摘录、其他资料等等,如想了解不同资料格式和写法,敬请关注!Download tips: This document is carefully compiled by theeditor. I hope that after you download them,they can help yousolve practical problems. The document can be customized andmodified after downloading,please adjust and use it according toactual needs, thank you!In addition, our shop provides you with various types ofpractical materials,such as educational essays, diaryappreciation,sentence excerpts,ancient poems,classic articles,topic composition,work summary,word parsing,copy excerpts,other materials and so on,want to know different data formats andwriting methods,please pay attention!MRC 天然气液化流程是一种混合制冷剂循环的天然气液化工艺,其工作原理如下:1. 原料气预处理:将天然气进行净化处理,去除其中的杂质和水分,以保证后续液化过程的顺利进行。
混合制冷剂循环(MRC)液化天然气流程的设备模拟

6 多股 流 换 热 器 换 热 过 程 的 热 力 学 模 拟
多 股 流 换 热 器 在流 程 中 实现 低 压 制 冷 剂 冷 量 向天 然 气 和 高 压制 冷 剂 传递 , 天 然 气 吸 收冷 量 后 降温 , 往 液 化 并 提 高 液 化 率 的 目标 逼 近 ; 高 压 制冷 剂 吸 收 冷 量后 能部 分 液 化 , 使
离器 、 混合 器 、 多 股流 换热 器这 五类 设备 的热 力学 状 态的计 算方 法 , 并 与国 外流 程计 算 中的相 应模 块计 算结果 相 比较 , 模拟 结果 十分 接近 , 从 而表 明所进 行的设 备热 力学 状态模 拟是 正确 的 a
关 键 三 , 竺, , 竺 液 — 一, 流 程 设 备皂 一 /; , 荫 枝, 刁 J , “ ' R I P c 一
前 言
混 合制 冷循 环液 化 天 然 气 的典 型 流 程 中 , 涉 及 的设 备 有 混 合制 冷剂 压缩 机 、 多 股 流换 热器、 汽液分离器 、 节 流阀、 物流混合器等设备。 由于循 环 中 设 备类 别 多 , 且流 程 复 杂 。本研 究利 用 模 块理 论 , 将 流 程 中涉 及到 的 设 备 分 类 进行 模 块 化处 理 , 使 其 各 成 为 一 个 独 立 的 数据 处 理 块 , 以便 在 流 程计 算 中 可 以重 复调
得 到 充分 利 用 。 同
Xmo l a ,
A :H { 一 H l+ H 2 ; Fa= F1+ F2 ;
…
1 3: Zmo l 一 ( Zmo l “× F L+ Zmo l × F2 ) / Fa
( 2 )
C、 D、 E三 步 分 别 与 压 缩 机 计 算过 程 的 G H、 I 三步相 同。
mrc液化工艺

mrc液化工艺
MRC液化工艺是一种新型的液化技术,它采用了先进的分离技术和高效的能量转换技术,可以将各种物质液化成为易于储存和运输的液态。
MRC液化工艺的应用范围非常广泛,可以用于石油、天然气、化工、医药等领域。
MRC液化工艺的核心技术是分离技术。
它采用了高效的分离设备,可以将混合物中的各种成分分离出来,从而实现液化。
这种分离技术可以有效地提高液化效率,降低能耗,减少环境污染。
MRC液化工艺还采用了高效的能量转换技术。
它可以将各种能源转换成为液化所需的能量,从而实现液化。
这种能量转换技术可以有效地提高液化效率,降低能耗,减少环境污染。
MRC液化工艺的应用非常广泛。
在石油行业中,它可以将原油、石油气等液化成为易于储存和运输的液态。
在天然气行业中,它可以将天然气液化成为LNG,从而实现长距离运输。
在化工行业中,它可以将各种化学物质液化成为易于储存和运输的液态。
在医药行业中,它可以将各种药物液化成为易于储存和运输的液态。
MRC液化工艺是一种非常先进的液化技术,它可以将各种物质液化成为易于储存和运输的液态。
它的应用范围非常广泛,可以用于石油、天然气、化工、医药等领域。
随着技术的不断发展,MRC液化工艺将会在各个领域中发挥越来越重要的作用。
天然气液化项目自控技术方案
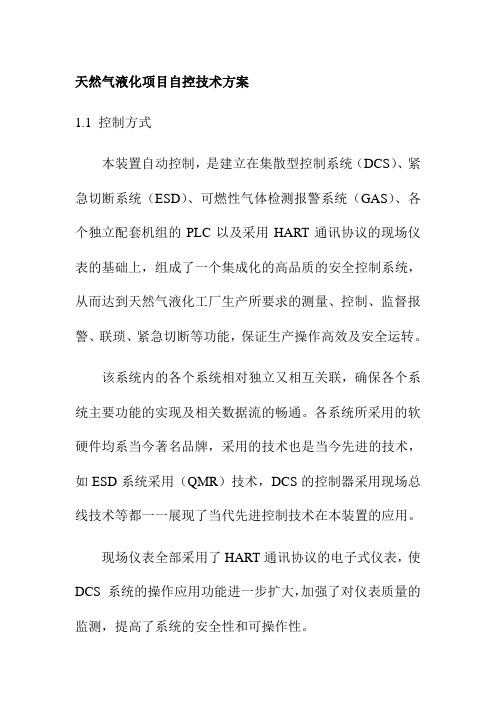
天然气液化项目自控技术方案1.1 控制方式本装置自动控制,是建立在集散型控制系统(DCS)、紧急切断系统(ESD)、可燃性气体检测报警系统(GAS)、各个独立配套机组的PLC以及采用HART通讯协议的现场仪表的基础上,组成了一个集成化的高品质的安全控制系统,从而达到天然气液化工厂生产所要求的测量、控制、监督报警、联琐、紧急切断等功能,保证生产操作高效及安全运转。
该系统内的各个系统相对独立又相互关联,确保各个系统主要功能的实现及相关数据流的畅通。
各系统所采用的软硬件均系当今著名品牌,采用的技术也是当今先进的技术,如ESD系统采用(QMR)技术,DCS的控制器采用现场总线技术等都一一展现了当代先进控制技术在本装置的应用。
现场仪表全部采用了HART通讯协议的电子式仪表,使DCS 系统的操作应用功能进一步扩大,加强了对仪表质量的监测,提高了系统的安全性和可操作性。
1.2 检测和控制方案本装置检测和控制方案中,除了常规仪表和单回路、串级回路外,尚有以下特殊仪表及控制回路。
●冷罐液位测量控制:为了对特大型冷罐低温液位测量、控制采用了SMART 储罐伺服液位计,该仪表可对冷罐液位精确测量±2mm外,还可对罐内介质密度、平均温度进行测量,并采用了4-20mA 输出或用HART总线与DCS进行通讯。
●分析测量:本装置采用了大量分析仪表,对工艺过程质量进行全面监测。
分析仪表有:工业气相色谱仪、水份仪、密度计、浊度计、热值仪、红外分析仪、总硫分析仪、氧分析仪、pH 和电导仪。
●称量控制:采用质量流量计、预设控制器、控制阀与DCS一同组成对槽车罐装的精确定量控制。
●防喘振控制:对循环气压缩机Ⅱ级,都采用了防喘振措施。
它们根据所控段的入口压力及出口段的温度、压力、流量控制相应的旁路流量以达到对压缩机的保护和安全运转。
●程序控制:A-251A/B分子筛干燥器的吸附、再生过程由DCS实现程序控制。
紧急切断(停车)系统(ESD):根据安全等级划分(SLA1001),本装置将有17个安全回路(SILI 13个,SIL 3个,NE 1个)进入EDS系统。
天然气液化流程工艺选择优化
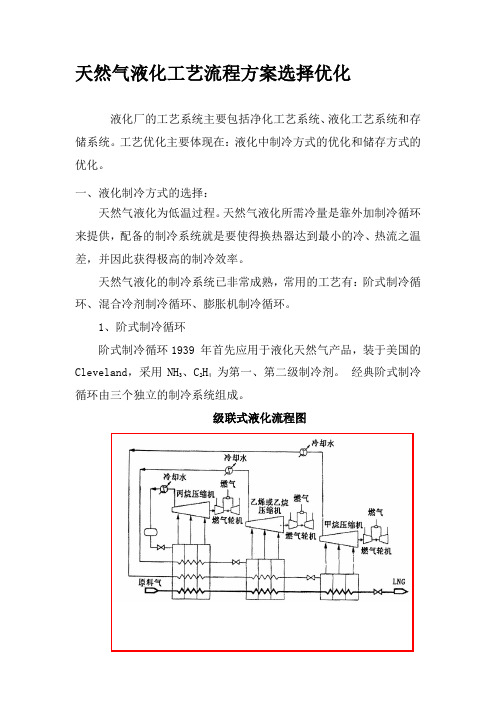
天然气液化工艺流程方案选择优化液化厂的工艺系统主要包括净化工艺系统、液化工艺系统和存储系统。
工艺优化主要体现在:液化中制冷方式的优化和储存方式的优化。
一、液化制冷方式的选择:天然气液化为低温过程。
天然气液化所需冷量是靠外加制冷循环来提供,配备的制冷系统就是要使得换热器达到最小的冷、热流之温差,并因此获得极高的制冷效率。
天然气液化的制冷系统已非常成熟,常用的工艺有:阶式制冷循环、混合冷剂制冷循环、膨胀机制冷循环。
1、阶式制冷循环阶式制冷循环1939 年首先应用于液化天然气产品,装于美国的Cleveland,采用NH3、C2H4为第一、第二级制冷剂。
经典阶式制冷循环由三个独立的制冷系统组成。
级联式液化流程图第一级采用丙烷做制冷剂,经过净化的天然气在丙烷冷却器中冷却到-35~-40℃,分离出戊烷以上的重烃后进入第二级冷却。
由丙烷冷却器中蒸发出来的丙烷气体经压缩机增压,水冷却器冷却后重新液化,并循环到丙烷冷却器。
第二级采用乙烯做制冷剂,天然气在第二级中被冷却到-80~-100℃,并被液化后进入第三级冷却。
第三级采用甲烷做制冷剂,液化天然气在甲烷冷却器中被过冷到-150~-160℃,然后通过节流阀降压,温度降到-162℃后,用泵输送到LNG 贮槽。
甲烷冷却器中蒸发出来的气体经增压、水冷后,在丙烷冷却器中冷却、在乙烯冷却器中液化后,循环到甲烷冷却器。
经典阶式制冷循环,包含几个相对独立、相互串联的冷却阶段,由于制冷剂一般使用多级压缩机压缩,因而在每个冷却阶段中,制冷剂可在几个压力下蒸发,分成几个温度等级冷却天然气,各个压力下蒸发的制冷剂进入相应的压缩机级压缩。
各冷却阶段仅制冷剂不同,操作过程基本相似。
从发展来看,最初兴建LNG 装置时就用阶式制冷循环的着眼点是:能耗最低,技术成熟,无需改变即可移植用于LNG 生产。
随着发展要求而陆续兴建新的LNG 装置,这时经典的阶式制冷循环就暴露出它固有的缺点:1)经典的阶式制冷循环由三个独立的丙烷、乙烯、甲烷制冷循环复迭而成。
天然气工程液化厂项目工艺装置及辅助生产设施设计方案
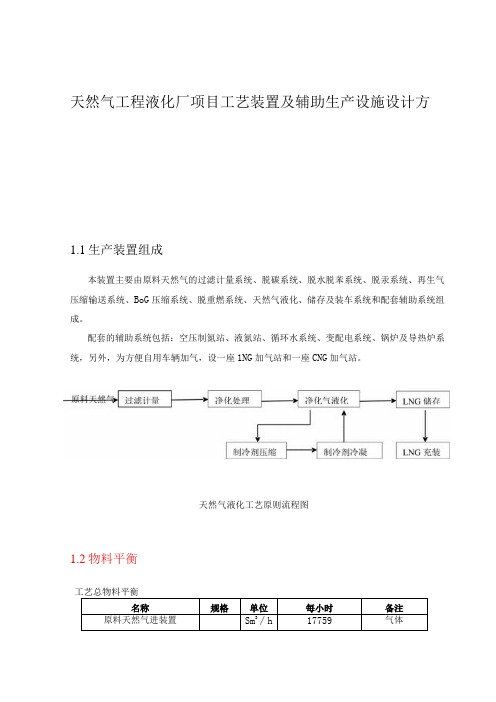
天然气工程液化厂项目工艺装置及辅助生产设施设计方1.1生产装置组成本装置主要由原料天然气的过滤计量系统、脱碳系统、脱水脱苯系统、脱汞系统、再生气压缩输送系统、BoG压缩系统、脱重燃系统、天然气液化、储存及装车系统和配套辅助系统组成。
配套的辅助系统包括:空压制氮站、液氮站、循环水系统、变配电系统、锅炉及导热炉系统,另外,为方便自用车辆加气,设一座1NG加气站和一座CNG加气站。
天然气液化工艺原则流程图1.2物料平衡详细的物料平衡见物料平衡数据表13工艺装置1.3.1工艺原理与特点1.3.1.1净化方案比较针对可研中提出的净化方案,根据工艺状况及原料气的组份特点,提出了新的净化方案,现将两种方案比较如下(以IOOX1O'iW/d为基础):方案A(可研推荐的方案):分子筛脱碳脱水、减压升温再生、再生气加压、TEG脱水后返回上游配气站方案B(实施方案):分子筛脱碳脱水+等压升温再生、再生气加压后等压脱水后返回上游配气站综合比较结果,本设计采用方案B,并经过设计联络会确认。
1.3.1.2净化装置根据天然气体成份和净化气产品质量要求,本净化工艺采用变温变压吸附法(PTSA)脱除天然气中的二氧化碳、硫化氢以及水分;采用恒压变温吸附法(TSA)脱除再生气中的水分;采用专用脱汞剂实现汞的吸附脱除。
下图为不同温度下的吸附等温线示意图:从上图B-C和AfD可以看出:在压力一定时,随着温度的升高,吸附容量逐渐减小;从上图BfA和CfD可以看出:在温度一定时,随着压力的升高吸附容量逐渐增大。
实际上,变温吸附正是利用上图B-C段(或AfD段)的特性来实现的;变压吸附是利用上图BfA段(或CfD 段)的特性来实现的;变温变压吸附过程正是利用上图中吸附剂在A-B及B-C段的特性来实现吸附与解吸的。
吸附剂在常温和压力较高时(A点)大量吸附原料气中的某些杂质组分,然后在高温和压力较低时(C点)使吸附的杂质组分得以充分解析。
新型天然气液化装置工艺流程及设备特点分析
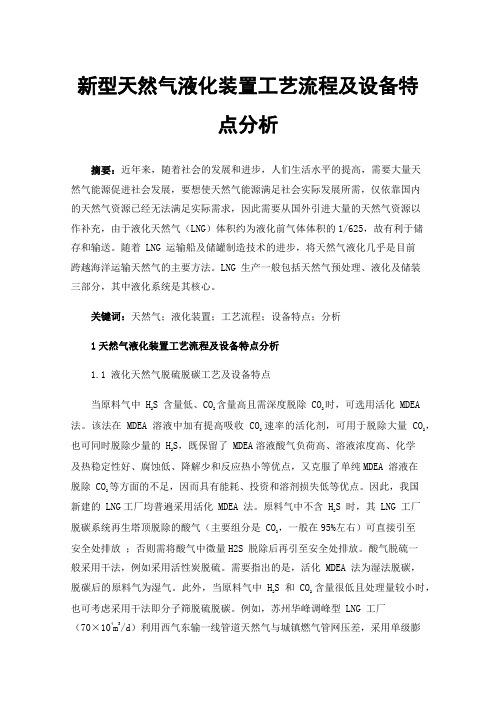
新型天然气液化装置工艺流程及设备特点分析摘要:近年来,随着社会的发展和进步,人们生活水平的提高,需要大量天然气能源促进社会发展,要想使天然气能源满足社会实际发展所需,仅依靠国内的天然气资源已经无法满足实际需求,因此需要从国外引进大量的天然气资源以作补充,由于液化天然气(LNG)体积约为液化前气体体积的1/625,故有利于储存和输送。
随着 LNG 运输船及储罐制造技术的进步,将天然气液化几乎是目前跨越海洋运输天然气的主要方法。
LNG 生产一般包括天然气预处理、液化及储装三部分,其中液化系统是其核心。
关键词:天然气;液化装置;工艺流程;设备特点;分析1天然气液化装置工艺流程及设备特点分析1.1 液化天然气脱硫脱碳工艺及设备特点当原料气中 H2S 含量低、CO2含量高且需深度脱除 CO2时,可选用活化 MDEA法。
该法在 MDEA 溶液中加有提高吸收 CO2速率的活化剂,可用于脱除大量 CO2,也可同时脱除少量的 H2S,既保留了 MDEA溶液酸气负荷高、溶液浓度高、化学及热稳定性好、腐蚀低、降解少和反应热小等优点,又克服了单纯MDEA 溶液在脱除 CO2等方面的不足,因而具有能耗、投资和溶剂损失低等优点。
因此,我国新建的 LNG工厂均普遍采用活化 MDEA 法。
原料气中不含 H2S 时,其 LNG 工厂脱碳系统再生塔顶脱除的酸气(主要组分是 CO2,一般在95%左右)可直接引至安全处排放;否则需将酸气中微量H2S 脱除后再引至安全处排放。
酸气脱硫一般采用干法,例如采用活性炭脱硫。
需要指出的是,活化 MDEA 法为湿法脱碳,脱碳后的原料气为湿气。
此外,当原料气中 H2S 和 CO2含量很低且处理量较小时,也可考虑采用干法即分子筛脱硫脱碳。
例如,苏州华峰调峰型 LNG 工厂(70×104m3/d)利用西气东输一线管道天然气与城镇燃气管网压差,采用单级膨胀机制冷、部分液化的液化工艺。
该厂预处理系统先采用分子筛(4A)和活性炭复合床层脱水脱苯,再采用分子筛(13X)脱硫脱碳。
新型天然气液化装置工艺流程及设备特点分析
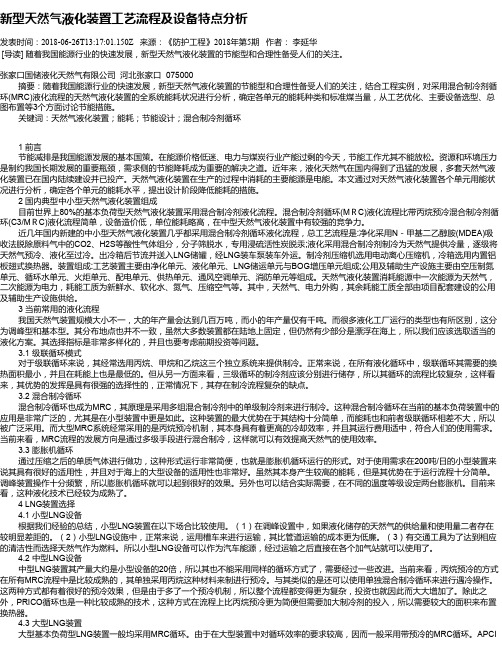
新型天然气液化装置工艺流程及设备特点分析发表时间:2018-06-26T13:17:01.150Z 来源:《防护工程》2018年第5期作者:李延华[导读] 随着我国能源行业的快速发展,新型天然气液化装置的节能型和合理性备受人们的关注。
张家口国储液化天然气有限公司河北张家口 075000摘要:随着我国能源行业的快速发展,新型天然气液化装置的节能型和合理性备受人们的关注,结合工程实例,对采用混合制冷剂循环(MRC)液化流程的天然气液化装置的全系统能耗状况进行分析,确定各单元的能耗种类和标准煤当量,从工艺优化、主要设备选型、总图布置等3个方面讨论节能措施。
关键词:天然气液化装置;能耗;节能设计;混合制冷剂循环1 前言节能减排是我国能源发展的基本国策。
在能源价格低迷、电力与煤炭行业产能过剩的今天,节能工作尤其不能放松。
资源和环境压力是制约我国长期发展的重要瓶颈,需求侧的节能降耗成为重要的解决之道。
近年来,液化天然气在国内得到了迅猛的发展,多套天然气液化装置已在国内陆续建设并已投产。
天然气液化装置在生产的过程中消耗的主要能源是电能。
本文通过对天然气液化装置各个单元用能状况进行分析,确定各个单元的能耗水平,提出设计阶段降低能耗的措施。
2 国内典型中小型天然气液化装置组成目前世界上80%的基本负荷型天然气液化装置采用混合制冷剂液化流程。
混合制冷剂循环(MRC)液化流程比带丙烷预冷混合制冷剂循环(C3/MRC)液化流程简单,设备造价低,单位能耗略高,在中型天然气液化装置中有较强的竞争力。
近几年国内新建的中小型天然气液化装置几乎都采用混合制冷剂循环液化流程,总工艺流程是:净化采用N-甲基二乙醇胺(MDEA)吸收法脱除原料气中的CO2、H2S等酸性气体组分,分子筛脱水,专用浸硫活性炭脱汞;液化采用混合制冷剂制冷为天然气提供冷量,逐级将天然气预冷、液化至过冷。
出冷箱后节流并送入LNG储罐,经LNG装车泵装车外运。
制冷剂压缩机选用电动离心压缩机,冷箱选用内置铝板翅式换热器。
C3MRC天然气液化流程工艺参数优化及用能分析

第 49 卷第 10 期
邓俊哲, 等: C3 / MRC 天然气液化流程工艺参数优化及用能分析
表 1 原料气和混合制冷剂组分
Table 1 Composition of feed gas and mixed refrigerant( mol% )
组分
N2
原料气
混合冷剂
C2
91
5. 4
52. 5
摘 要: 利用化工模拟软件 HYSYS 建立 C3 / MRC 工艺仿真模型, 以现场运行参数对模型进行修正, 在已建模型基础上,
对其进行优化。 以系统能耗为优化目标, 制冷剂的压力以及制冷剂的组成配比为优化变量, 建立优化模型, 得到最优冷剂配比以
及优化后各关键节点的相关参数。 对比优化前后的参数, 发现在当天然气液化率相同时, 保证 LNG 产量不变及产品气品质达标的
3189
335. 1
-122. 7
-84. 05
2970
3189
330
-160
-77. 06
275. 1
-160. 9
-160
-92. 22
270
3189
-161. 9
L-MR
MR19
-75. 47
-104. 80
2970
2910
300
270
270
240
1257
3000
0
-75. 47
-101. 90
—
—
0. 2
n-C5
基于该 C3 / MR 装置的特点, 采用化工模拟软件 HYSYS 对
C3 / MRC 工艺流程 HYSYS 模型如图 1 所示, 该模型以原料气与
32. 5
天然气液化项目初步技术方案措施

50×104Nm3/d天然气液化项目初步技术方案重庆耐德工业股份有限公司2012.6目录一、总论 (1)1概述 (1)2装置组成 (1)二、技术说明 (3)1项目概况 (3)2通用信息 (3)3标准规范 (4)4原料规格 (18)5工艺及控制 (21)6物料平衡 (56)7化学品首次充装(以下为初步计算,最终以详细计算为准) (56)8电气负荷表(以下为初步计算,最终以详细计算为准) (58)9技术性能及保证值 (58)三、预算报价 (60)四、付款方式 (63)五、工期及业绩 (64)1、工程周期 (64)2业绩 (65)一、总论1概述本建设项目为建立50×104Nm3/d天然气液化的工艺和配套公用工程和辅助设施。
建成的天然气液化工厂,具有先进的工艺,消耗及能耗达国内先进水平,在确保工艺性能的基础上最大化实现的设备国产化,操作维护简易,符合国家环保及节能要求。
2装置组成本装置按照设计分工划分为:工艺生产装置区(ISBL)、非工艺生产装置区(OSBL)。
装置组成区域功能描述备注ISBL工艺生产装置区010 原料气分离、计量及再生气增压020 脱酸性气体030 脱水040 脱苯预留接口050 天然气液化060 蒸发气070 冷剂储配080 放空系统OSBL非工艺生产装置区110 LNG储存120 LNG装车210 空压站220 氮压站230 给排水系统240 脱盐水系统250 消防系统260 热媒炉系统310 中心控制室320 变电所区域功能描述备注330 管廊二、技术说明1项目概况项目名称:50×104Nm3/d天然气液化处理建设地点:投资方:建设规模:天然气处理总能力50×104Nm3/d的天然气液化装置,按年开工时间330天考虑。
在计划停工间隔内连续操作3年生产操作弹性:生产能力的50%~110%LNG储存天数约10天(LNG储罐有效工作容积5000m3)设计寿命不小于25年2通用信息(1)缩写词本项目的主要缩写词如下:OSBL 生产装置区域外ISBL 生产装置区域内MCC 电机控制中心Motor Central ControlBOD 设计基础Basis of DesignBEP 基础设计Basic Engineering PackageDDP 详细设计Detail Design PackageEIA 环境影响评价Environmental Impact AssessmentLNG 液化天然气OP 操作压力OT 操作温度DP 设计压力DT 设计温度MW 分子量(2)单位温度:℃压力:MPa.G(说明:MPa.G表示表压,Mpa.A表示绝压)流量:Nm3/h(0℃,0.101325Mpa.A)功率:KW天然气组分组成:mol%一般情况下,本项目将全部采用国际单位制(SI制),除另有说明之外。
天然气液化工艺部分技术方案(MRC)..

天然气液化工艺部分技术方案(MRC)一、天然气液化属流程工业,具有深冷、高压,易燃、易爆等特征,在生产中具有极高的危险性,既有比较高的温度(280℃)和压力(50Bar),也有低温(-170℃),这些单元之间紧密相连,中间缓冲地带比较小,对参数的变化要求严格,这对LNG液化装置连续生产自动化提出了很高的要求。
LNG装置的制冷剂配比与产量和收率直接相关,因此LNG生产过程中控制品质占有非常突出的位置。
整个生产过程需要很多自动化硬件和配套的软件来实现。
以保证生产装置的安全、稳定、高效运行,不仅是提高效益的关键,而且对生产人员、生产设备,以及整个厂区安全都十分重要。
二、工艺过程简述LNG工艺流程图参见P&ID图1、原料气压缩单元来自界区外的天然气经过过滤器除去部分碳氢化合物、水和其它的液体及颗粒。
35MPa(G)的原料气进入脱CO2单元。
3、脱水脱酸气单元原料气进入2台切换的干燥器,在这里原料气所含有的所有水分和CO2被脱除,干燥器出口原料气中水的露点在操作压力下低于-100℃。
经过分子筛干燥单元,在这里原料气再经过两个过滤器中的一个进行脱粉尘过滤。
4、液化单元进入冷箱的天然气在中被冷却至-35℃,在这个温度点冷箱分离罐中,脱除大部分重烃;天然气继续冷却至-70℃,在这个温度点,天然气在冷箱分离器中,脱除全部重烃,出口的天然气中C5+重烃含量降至70ppm以下;甲烷气继续冷却至-155℃,节流后进入冷箱分离罐中分离,液体部分即为液化天然气被送至液化天然气储罐中储存,气相部分返回冷箱复温后用作分子筛干燥单元的再生气。
5、储运单元来自液化单元的液化天然气进入液化天然气储罐中储存,产量为420m3,储罐容量为4500 m3,储存能力为10天。
6、制冷剂压缩单元按一定比例配比的制冷剂,经过制冷压缩机增压至1.3MPa(G)后经中间冷却器冷却后,进入中间分离罐中分离,气体部分进入制冷剂压缩机二级增压至 4.9MPa(G)并与来自分离罐的液体混合后进入后冷却器冷却,进入分离罐中分离,气体部分流至冷箱顶部,液体部分经制冷剂泵送至冷箱顶部与气体部分混合后进入冷箱换热器冷却,冷却后的低温制冷剂由换热器底部流出,经节流阀节流降压降温后返回换热器,作为返流制冷剂为原料气和正流制冷剂降温液化提供冷量,低压制冷剂复温后出冷箱换热器。
天然气液化流程
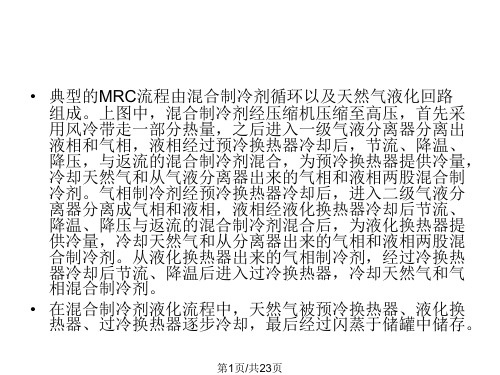
计算未知变量;多个未知变量求解时,不仅要满足能量平 衡还要满足约束条件来获得解决方案。HYSYS中冷却器 和 LNG换热器模型如图所示。LNG换热器可以包含多股 冷流和热流,图中以三股为例,其中 5-6、3-4 为冷流, 1-2 为热流。
第20页/共23页
• 混合制冷剂经两级压缩压缩至高压,首先用水冷却,带走一部分热量, 然后通过丙烷预冷循环预冷。预冷后进入气液分离器分离成气相和液 相,液相经第一换热器冷却后,节流、降温、降压,与返流的混合制 冷剂混合后,为第一个换热器提供冷量,冷却天然气和从分离器出来 的气相和液相两股混合制冷剂。气相制冷剂经第一换热器冷却后,进 入气液分离器分离成气相和液相,液相经第二个换热器冷却后节流、 降温、降压,与返流的混合制冷剂混合后为第二个换热器提供冷量, 冷却天然气和从分离器出来的气相和液相两股混合制冷剂。从第二换 热器出来的气相制冷剂,经第三换热器冷却后,节流、降温后进入第 三换热器,冷却天然气和气相混合制冷剂。
• C3/MRC工艺综合了阶式循环工艺和MRC工艺的特长,具有流程简单、 效率高、运行费用低、适应性强等优点,是目前最为合理的天然气液 化工艺和基地型LNG工厂首选工艺。世界上采用这种工艺的基地型 LNG工厂占所有基地型LNG工厂的2/3。
第5页/共23页
• AsPenPlus是一种广泛应用于化工过程的研究开发,设计, 生产过程的控制,优化及技术改造等方面的性能优良的软 件。“过程工程的先进系统” (AdvancedSystemrProcessEngineering,简称AsPEN.为 举世公认的标准大型流程模拟软件,应用案例数以百万计。 其包括56种单元操作模型,含5000种纯组分、5000对二 元混合物、3314种固体化合物、40000个二元交互作用参 数的数据库。
- 1、下载文档前请自行甄别文档内容的完整性,平台不提供额外的编辑、内容补充、找答案等附加服务。
- 2、"仅部分预览"的文档,不可在线预览部分如存在完整性等问题,可反馈申请退款(可完整预览的文档不适用该条件!)。
- 3、如文档侵犯您的权益,请联系客服反馈,我们会尽快为您处理(人工客服工作时间:9:00-18:30)。
一、概述天然气液化属流程工业,具有深冷、高压,易燃、易爆等特征,在生产中具有极高的危险性,既有比较高的温度(280℃)和压力(50B ar),也有低温(-170℃),这些单元之间紧密相连,中间缓冲地带比较小,对参数的变化要求严格,这对L NG液化装置连续生产自动化提出了很高的要求。
LNG装置的制冷剂配比与产量和收率直接相关,因此LN G生产过程中控制品质占有非常突出的位置。
整个生产过程需要很多自动化硬件和配套的软件来实现。
以保证生产装置的安全、稳定、高效运行,不仅是提高效益的关键,而且对生产人员、生产设备,以及整个厂区安全都十分重要。
二、工艺过程简述LN G工艺流程图参见P&I D图1、原料气压缩单元来自界区外的天然气经过过滤器除去部分碳氢化合物、水和其它的液体及颗粒。
35MP a(G)的原料气进入脱CO2单元。
3、脱水脱酸气单元原料气进入2台切换的干燥器,在这里原料气所含有的所有水分和CO2被脱除,干燥器出口原料气中水的露点在操作压力下低于-100℃。
经过分子筛干燥单元,在这里原料气再经过两个过滤器中的一个进行脱粉尘过滤。
4、液化单元进入冷箱的天然气在中被冷却至-35℃,在这个温度点冷箱分离罐中,脱除大部分重烃;天然气继续冷却至-70℃,在这个温度点,天然气在冷箱分离器中,脱除全部重烃,出口的天然气中C5+重烃含量降至70pp m以下;甲烷气继续冷却至-155℃,节流后进入冷箱分离罐中分离,液体部分即为液化天然气被送至液化天然气储罐中储存,气相部分返回冷箱复温后用作分子筛干燥单元的再生气。
5、储运单元来自液化单元的液化天然气进入液化天然气储罐中储存,产量为420m3,储罐容量为4500 m3,储存能力为10天。
6、制冷剂压缩单元按一定比例配比的制冷剂,经过制冷压缩机增压至1.3MPa(G)后经中间冷却器冷却后,进入中间分离罐中分离,气体部分进入制冷剂压缩机二级增压至 4.9MPa(G)并与来自分离罐的液体混合后进入后冷却器冷却,进入分离罐中分离,气体部分流至冷箱顶部,液体部分经制冷剂泵送至冷箱顶部与气体部分混合后进入冷箱换热器冷却,冷却后的低温制冷剂由换热器底部流出,经节流阀节流降压降温后返回换热器,作为返流制冷剂为原料气和正流制冷剂降温液化提供冷量,低压制冷剂复温后出冷箱换热器。
二、控制系统及自动化仪表(一)工艺过程对自动控制的要求1、高度的自动化LNG液化工艺连续性强,安全要求高,中间缓冲余量小,操作频繁要求高,没有控制系统难以保证生产过程的安全平稳及优化,因此LNG液化装置采用D CS,ES D,FGS系统集中在控制室,从而实现高度自动化集中管理。
2、高质量的仪表LNG需要很多仪表,整套装置仪表设备几百台,每台仪表的正常运行都关系到某一参数或设备的工作节点的正常操作。
除考虑易燃易爆场所的要求外,每个仪表具有高的可靠性和稳定性。
现场仪表精度在 1.0,1.5,远传仪表达到0.25级以上。
3、高精度的计量仪表采用高精度的仪表用来检测LNG的入口天然气流量和LNG,LPG装车的计量。
入口天然气采用涡轮转子流量计,精度0.5级,LN G、LP G装车采用科氏质量流量计进行计量,流量精度0.05,密度精度0.0002g/c m3。
4、在线分析仪表在LNG的生产过程中,入口天然气的成分发生变化对制冷剂的配比有很大的影响,对天然气和制冷剂的在线分析是十分重要的,以防止LN G液化装置的能耗过大。
冷箱对入口天然气的含水量要求也是十分严格的,否则长期运行将堵塞冷箱。
5、防爆防雷LN G装置内有防爆区和非防爆区,非防爆区包括有明火的锅炉单元,P S A 制氮和仪表空气单元。
其它入冷箱单元、预处理单元、纯化单元、压缩机厂房等为防爆区域,在这些区内的所有仪表采用本安型仪表,特殊状态时采用隔爆型和正压防爆型仪表。
自控系统在LNG液化装置中占有十分重要的地位,D CS、ES D系统构成复杂的数据网络,容易受到各种原因导致的浪涌电压的干扰和破坏。
现场变送器、模拟数字信号控制回路、调节阀、电磁阀和分别加装防雷模块予以保护,电源系统采用3级防护、分级泄放的电源防护系统。
以及做好等电位连接。
(二)电源和气源1、电源DCS和ES D系统设置2台15KVA的UPS(不间断电源)供电,UP S的供电时间1小时。
系统内使用的电源分别为24VD C和220VAC。
2、气源仪表气源系统由2台无油压缩机、水分离罐、再生干燥器、储气罐组成。
压力:0.7MP a露点:-40℃(0.7MP a时)温度:常温,无油无尘2台120m3/h的压缩机互为备用,10m3(1.0MPa)空气储罐。
不间断供气时间30分钟。
(三)仪表选型1、温度仪表LN G装置的温度范围-170℃到300℃,装置的测温元件全部采用P t100热电阻来实现。
热电阻均为铠装型,按不同的区域配置保护管。
特殊设备如冷箱内的温度检测采用铝保护管。
2、流量仪表除了用于计量的入口天然气流量计(涡轮转子流量计)和LNG、LPG装车流量计(科氏质量流量计),均采用截流装置配差压变送器来进行测量。
截流装置采用孔板来实现,取压方式法兰取压。
气体流量配压力和温度补偿,差压变送器的差压范围选择6KP a(6000mm H2O)。
重要的位置采用流量开关作为ESD紧急停车系统信号检测。
如:原料气压机和制冷剂压机的水冷系统。
3、压力仪表压力参数的检测通过压力变送器将信号传送到控制室供D CS或ESD系统使用,关键位置配压力开关将信号传送至ES D或D CS系统用于报警和联锁。
就地仪表采用不锈钢压力表和普通压力表实现,压机和泵的出口采用耐震压力表。
4、液位仪表需要远传的液位信号根据不同的介质采用不同的检测方式,预处理部分选择法兰差压变送器把信号传到控制室,冷箱内重烃类T>-70℃的液位采用电容式液位计实现。
LN G采用差压变送器传输信号。
关键部位如;LN G储罐使用2套液位检测系统。
就地液位指示采用磁浮子液位计和玻璃板液位计。
需要报警和联锁的液位计采用液位开关实现。
5、调节阀LNG装置的调节阀主要有低温调节阀和常温调节阀,冷箱内使用的低温调节阀采用长颈型单座调节阀,颈长:600m m,阀体材质为铝合金。
常温型调节阀根据不同的介质、压力、Cv值选用不同结构形式的调节阀,所有的调节阀都配有阀门定位器,关键阀门有阀位信号返回器何手轮装置。
如冷箱制冷剂J-T阀。
低温阀不设置前后截止阀和旁通阀,常温调节阀设置前后阀和旁通阀组。
6、1分析仪表LN G装置采用的在线分析仪表有:1台在线工业色谱仪和1台实验室色谱分别用于天然气成分和制冷剂成分的在线分析,主要分析的有:甲烷,乙烷,丙烷,异物烷,二氧化碳等。
采用的方式PCD和FI D检测室。
在线露点仪,分析进冷箱的天然气露点。
7、仪表防护保温远传仪表安装在仪表箱内,需要冬季保温的采用防爆电伴热加以解决。
仪表部分清单如下:(四)集散式控制系统(DCS)集散控制系统(D CS)主要实现主要工艺参数的显示、趋势记录、历史事件的记录、报警、控制、打印、制表及流程图画面动态显示等功能。
D CS系统为整个系统的核心,工艺过程的所有常规控制、复杂控制和逻辑控制均由D CS来完成,当工艺参数越限时,能记忆、显示、打印并报警。
1、DCS系统组成DCS系统采用浙大中控JX-300XP系统,JX-300XP覆盖了大型集散系统的安全性、冗余功能、网络扩展功能、集成的用户界面及信息存取功能,除了具有模拟量信号输入输出、数字量信号输入输出、回路控制等常规DCS的功能,还具有高速数字量处理、高速顺序事件记录(SO E)、可编程逻辑控制等特殊功能;它不仅提供了功能块图(SCF BD)、梯形图(S CLD)等直观的图形组态工具,又为用户提供开发复杂高级控制算法(如模糊控制)的类C语言编程环境S CX。
系统规模变换灵活,可以实现从一个单元的过程控制,到全厂范围的自动化集成。
系统配置图如下:2、DCS配置的原则A、系统由过程站、数据通讯系统和人机接口组成。
系统易于组态、易于使用、易于扩展。
B、D CS 系统作为整个系统的处理整个工艺过程的参数的显示、趋势记录、历史事件的记录、报警、控制、打印、制表及流程图画面动态显示等功能。
当工艺参数超越设定值时,能记忆、显示、打印并报警。
对操作人员的操作过程进行记录。
关键参数修改权限设置。
C、DCS系统配置满足装置任何工况下的监控要求(包括紧急故障处理),CP U及通信总线负荷率控制在设计规定的指标之内并留有20%裕度。
D、DCS处理器采用100%冗余配置,重要I/O 点应考虑采用非同一板件的冗余配置,每个I/O机架应有20%的在线I/O备用量。
E、系统电源有可靠的后备手段采用在线式UP S电源,备用电源的切换时间应小于5ms。
系统电源故障在控制室内设有独立于DCS之外的声光报警。
F、主系统DCS及与主系统连接的所有相关系统(包括ES D、压缩机P LC、装车独立的P LC)的通信负荷率不大于50%,其接口设备(板件)通过冗余总线连接稳定可靠。
G、DCS的系统接地设计按照(HG/T-20513-2000)技术要求进行,所有进入DCS系统的控制信号的电缆采用的屏蔽电缆,且有良好的单端接地。
H、所有的执行机构、阀门等外围设备,在失电、失气、失信号或DCS 系统失灵的情况下,能够向安全方向动作或保持原位(安装保位阀)。
I、DCS系统容量以最终P&ID图为准,留有20%余量。
系统具有强大可扩展性,只需增加I/O模板就可以实现对系统的扩展。
J、在线修改功能,系统可以在线修改程序而不影响系统的运行。
K、DCS系统采用分布式控制,I/O远程单元可以安装在现场控制箱内。
通过冗余总线方式与处理器连接。
L、系统的兼容性,可以与RS485,RS232等多种方式与其他不同的系统连接。
WebField JX-300XP 系统配置清单1用户:哈工大雪贝低温设备有限公司项目:系统规模系统配置(五)ES D联锁停车系统天然气液化属流程工业,具有低温、高压,易燃、易爆等特征,在生产中具有极高的危险性,因此实现生产装置的安全、稳定、高效运行不仅是提高效益的关键,而且对生产人员、生产设备,人员安全都十分重要。
在本装置采用国际先进的ESD(Em erge nc y Shut d ow n,紧急停车)系统实现装置的安全控制。
LN G液化装置ES D系统构成:液化单元和公用工程区实现联锁保护控制,以确保装置在发生电力、循环水装置或仪表系统等公共故障时天然气的切断与排放得到有效的控制。
当装置区发生火灾等紧急情况时,ES D接收F GS 系统的信号,控制停止切断相关的设备。
ESD设备采用的是西门子公司的AS414F/HF系统对装置进行联锁控制,安全级别达到SI L2。