球铁典型铸造缺陷极其防止
球墨铸铁常见缺陷的分析与对策
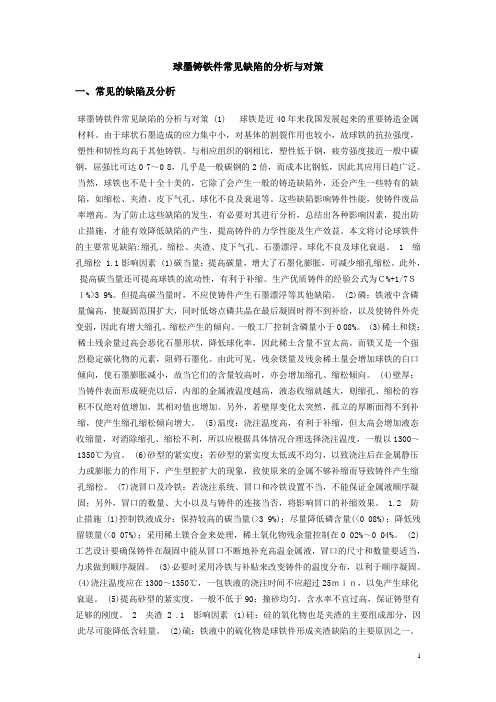
球墨铸铁件常见缺陷的分析与对策一、常见的缺陷及分析球墨铸铁件常见缺陷的分析与对策 (1) 球铁是近40年来我国发展起来的重要铸造金属材料。
由于球状石墨造成的应力集中小,对基体的割裂作用也较小,故球铁的抗拉强度,塑性和韧性均高于其他铸铁。
与相应组织的钢相比,塑性低于钢,疲劳强度接近一般中碳钢,屈强比可达0 7~0 8,几乎是一般碳钢的2倍,而成本比钢低,因此其应用日趋广泛。
当然,球铁也不是十全十美的,它除了会产生一般的铸造缺陷外,还会产生一些特有的缺陷,如缩松、夹渣、皮下气孔、球化不良及衰退等。
这些缺陷影响铸件性能,使铸件废品率增高。
为了防止这些缺陷的发生,有必要对其进行分析,总结出各种影响因素,提出防止措施,才能有效降低缺陷的产生,提高铸件的力学性能及生产效益。
本文将讨论球铁件的主要常见缺陷:缩孔、缩松、夹渣、皮下气孔、石墨漂浮、球化不良及球化衰退。
1 缩孔缩松 1.1影响因素 (1)碳当量:提高碳量,增大了石墨化膨胀,可减少缩孔缩松。
此外,提高碳当量还可提高球铁的流动性,有利于补缩。
生产优质铸件的经验公式为C%+1/7Si%>3 9%。
但提高碳当量时,不应使铸件产生石墨漂浮等其他缺陷。
(2)磷:铁液中含磷量偏高,使凝固范围扩大,同时低熔点磷共晶在最后凝固时得不到补给,以及使铸件外壳变弱,因此有增大缩孔、缩松产生的倾向。
一般工厂控制含磷量小于0 08%。
(3)稀土和镁:稀土残余量过高会恶化石墨形状,降低球化率,因此稀土含量不宜太高。
而镁又是一个强烈稳定碳化物的元素,阻碍石墨化。
由此可见,残余镁量及残余稀土量会增加球铁的白口倾向,使石墨膨胀减小,故当它们的含量较高时,亦会增加缩孔、缩松倾向。
(4)壁厚:当铸件表面形成硬壳以后,内部的金属液温度越高,液态收缩就越大,则缩孔、缩松的容积不仅绝对值增加,其相对值也增加。
另外,若壁厚变化太突然,孤立的厚断面得不到补缩,使产生缩孔缩松倾向增大。
球墨铸铁常见的铸造缺陷
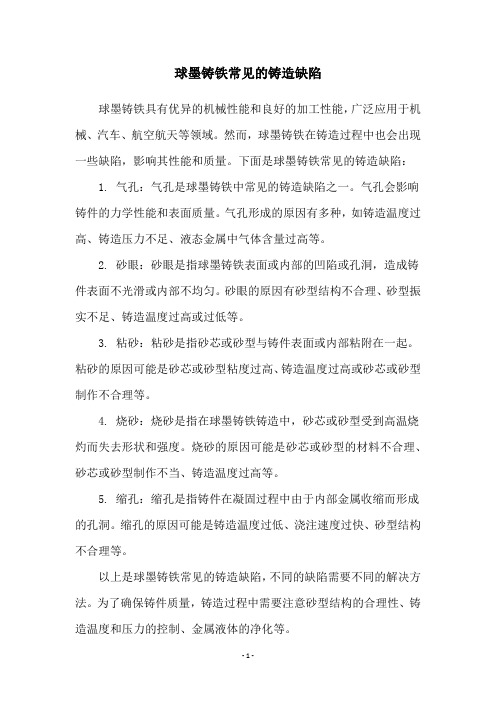
球墨铸铁常见的铸造缺陷
球墨铸铁具有优异的机械性能和良好的加工性能,广泛应用于机械、汽车、航空航天等领域。
然而,球墨铸铁在铸造过程中也会出现一些缺陷,影响其性能和质量。
下面是球墨铸铁常见的铸造缺陷:
1. 气孔:气孔是球墨铸铁中常见的铸造缺陷之一。
气孔会影响铸件的力学性能和表面质量。
气孔形成的原因有多种,如铸造温度过高、铸造压力不足、液态金属中气体含量过高等。
2. 砂眼:砂眼是指球墨铸铁表面或内部的凹陷或孔洞,造成铸件表面不光滑或内部不均匀。
砂眼的原因有砂型结构不合理、砂型振实不足、铸造温度过高或过低等。
3. 粘砂:粘砂是指砂芯或砂型与铸件表面或内部粘附在一起。
粘砂的原因可能是砂芯或砂型粘度过高、铸造温度过高或砂芯或砂型制作不合理等。
4. 烧砂:烧砂是指在球墨铸铁铸造中,砂芯或砂型受到高温烧灼而失去形状和强度。
烧砂的原因可能是砂芯或砂型的材料不合理、砂芯或砂型制作不当、铸造温度过高等。
5. 缩孔:缩孔是指铸件在凝固过程中由于内部金属收缩而形成的孔洞。
缩孔的原因可能是铸造温度过低、浇注速度过快、砂型结构不合理等。
以上是球墨铸铁常见的铸造缺陷,不同的缺陷需要不同的解决方法。
为了确保铸件质量,铸造过程中需要注意砂型结构的合理性、铸造温度和压力的控制、金属液体的净化等。
球墨铸铁常见的铸造缺陷

球墨铸铁常见的铸造缺陷球墨铸铁是一种用途广泛的合金材料,广泛应用于汽车、机械、农业机械、建筑设备等工业领域。
虽然球墨铸铁有很多优点,如高强度、高韧性、耐腐蚀和低温性能等,但它也有一些常见的铸造缺陷需要注意。
第一,浇口缺陷。
浇口是铸造过程中的关键部位,它是铸件的入口,直接关系到铸件的质量。
球墨铸铁的浇口缺陷主要包括翘口、裂纹和气孔等。
这些缺陷会导致铸件的强度降低,表面质量差,甚至无法使用。
第二,气孔缺陷。
气孔是铸铁材料中最常见的缺陷之一,也是球墨铸铁的重要缺陷类型。
气孔是由于铸造过程中未能完全去除空气或其他气体引起的。
气孔会导致铸件的强度下降,同时对铸件的密封和耐腐蚀性能也有影响。
第三,缩孔缺陷。
缩孔是铸件内部的气孔,是由于铸造过程中液态金属流动受阻引起的。
缩孔也会影响铸件的强度和维修性能,过多的缩孔会导致铸件完全失效。
第四,热裂缺陷。
球墨铸铁具有很好的耐热性能,但在铸造过程中可能会出现热裂缺陷。
热裂是由于铸件随着温度升高而产生的热应力引起的。
这种缺陷可能会导致铸件断裂,影响使用寿命。
为了避免这些缺陷的发生,需要在整个铸造过程中加强质量控制和监测。
对于浇口和气孔缺陷,可以在设计过程中优化铸件结构和浇注系统,加强铸造参数的控制和优化。
对于缩孔和热裂缺陷,需要加强熔炼和浇注过程的管理,避免过度的冷却和应力积累。
总之,球墨铸铁作为一种重要的铸造材料,在铸造过程中容易出现一些常见的缺陷。
加强质量控制和监测,优化铸造结构和参数控制,可以有效地减少这些缺陷的出现,提高球墨铸铁的质量和使用寿命。
浅析球墨铸铁件缺陷产生原因及防止措施

浅析球墨铸铁件缺陷产生原因及防止措施
1、坯料的缺陷:由于坯料的杂质含量过高,砂砾过大,沿铸缸边缘空隙较大等,都有可能导致炉内坯料缺陷大,从而产生球墨铸铁件缺陷。
2、成型工艺有问题:如砂芯型腔孔形不规则,型腔深度低,入型质量差,表面光洁度及粘结质量差等,都有可能产生球墨铸铁件缺陷。
3、浇注不合理:球墨铸铁件的浇注工艺过程中需要满足一定的条件,当不合理时,会导致溶质的不均匀分布,产生球墨铸铁件缺陷。
4、冷却不合理:冷却工艺是球墨铸铁件质量重要影响因素,冷却不合理,有可能使坯体结晶不良,从而产生球墨铸铁件缺陷。
二、防止球墨铸铁件缺陷的措施
1、提高坯料质量:在生产过程中,应加强原料检查,确保原料质量良好,并严格控制杂质含量,以减少成型过程中缺陷的发生。
2、改进成型工艺:应采用有利于消除和避免缺陷的成型工艺,如采用自动模具成型等技术,减少缺陷产生的可能性。
3、改善浇注工艺:采用有利于消除缺陷的浇注工艺,如采用连续浇铸或提高浇注压力,改善浇注品质,以减少球墨铸铁件缺陷。
4、优化冷却工艺:采用合理的冷却系统可以有效地控制坯体扩大速度,减少坯体内部残余应力,提高结晶度,以减少球墨铸铁件缺陷的产生。
三、结论
球墨铸铁件的缺陷的产生主要由坯料质量、成型工艺、浇注工艺以及冷却工艺不合理等原因引起。
因此,为防止球墨铸铁件缺陷的产生,应采取提高坯料质量、改进成型工艺、改善浇注工艺以及优化冷却工艺等措施。
只有这样,才能在生产过程中控制住缺陷,获得优良质量的球墨铸铁件。
浅析球墨铸铁件缺陷产生原因及防止措施
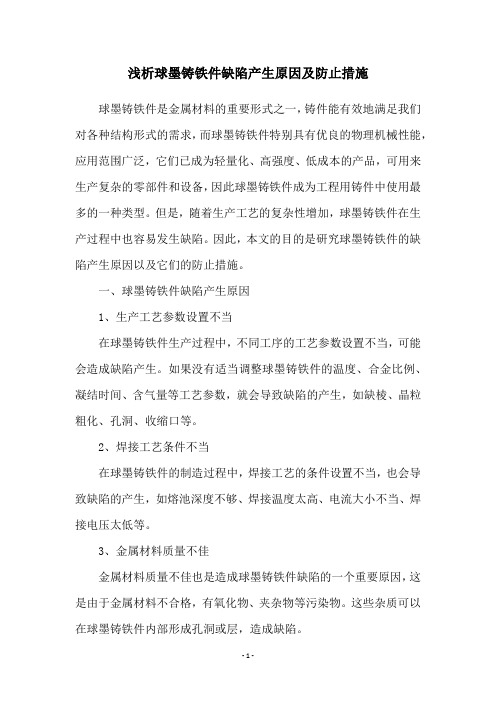
浅析球墨铸铁件缺陷产生原因及防止措施球墨铸铁件是金属材料的重要形式之一,铸件能有效地满足我们对各种结构形式的需求,而球墨铸铁件特别具有优良的物理机械性能,应用范围广泛,它们已成为轻量化、高强度、低成本的产品,可用来生产复杂的零部件和设备,因此球墨铸铁件成为工程用铸件中使用最多的一种类型。
但是,随着生产工艺的复杂性增加,球墨铸铁件在生产过程中也容易发生缺陷。
因此,本文的目的是研究球墨铸铁件的缺陷产生原因以及它们的防止措施。
一、球墨铸铁件缺陷产生原因1、生产工艺参数设置不当在球墨铸铁件生产过程中,不同工序的工艺参数设置不当,可能会造成缺陷产生。
如果没有适当调整球墨铸铁件的温度、合金比例、凝结时间、含气量等工艺参数,就会导致缺陷的产生,如缺棱、晶粒粗化、孔洞、收缩口等。
2、焊接工艺条件不当在球墨铸铁件的制造过程中,焊接工艺的条件设置不当,也会导致缺陷的产生,如熔池深度不够、焊接温度太高、电流大小不当、焊接电压太低等。
3、金属材料质量不佳金属材料质量不佳也是造成球墨铸铁件缺陷的一个重要原因,这是由于金属材料不合格,有氧化物、夹杂物等污染物。
这些杂质可以在球墨铸铁件内部形成孔洞或层,造成缺陷。
4、操作人员技术素养不足操作人员的技术素养也是产生缺陷的一个重要原因,如果操作人员缺乏技术素养,他们就不能熟练掌握工艺流程,也会导致生产过程中的缺陷。
二、防止球墨铸铁件缺陷的措施以上是球墨铸铁件缺陷的原因,那么如何防止缺陷产生呢?1、优化工艺参数设置在球墨铸铁件生产过程中,加强对工艺参数的监控,优化工艺参数设置,确保金属材料在加工上能满足一定的质量要求。
2、严格控制焊接工艺条件焊接是一项技术复杂的任务,因此我们应该在焊接工艺中严格控制各项工艺参数,确保球墨铸铁件能获得良好的焊接性能,从而防止缺陷的产生。
3、挑选优质金属材料在球墨铸铁件生产中,应该重视金属材料的质量,仅选用合格的金属材料,这样可以减少出现缺陷的概率。
4、提升操作人员技术素养提升操作人员的技术素养是防止球墨铸铁件缺陷的重要措施之一,建立科学的操作流程,以此来提高操作人员的技术水平,减少因技术不足而导致的缺陷。
球墨铸铁常见的铸造缺陷
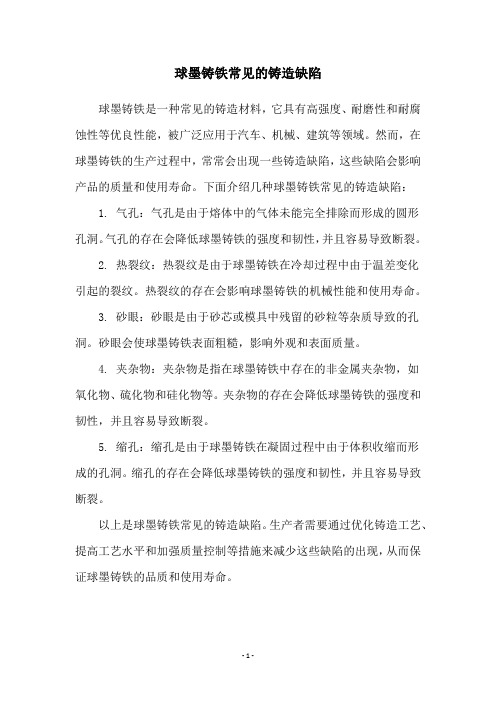
球墨铸铁常见的铸造缺陷
球墨铸铁是一种常见的铸造材料,它具有高强度、耐磨性和耐腐蚀性等优良性能,被广泛应用于汽车、机械、建筑等领域。
然而,在球墨铸铁的生产过程中,常常会出现一些铸造缺陷,这些缺陷会影响产品的质量和使用寿命。
下面介绍几种球墨铸铁常见的铸造缺陷:
1. 气孔:气孔是由于熔体中的气体未能完全排除而形成的圆形
孔洞。
气孔的存在会降低球墨铸铁的强度和韧性,并且容易导致断裂。
2. 热裂纹:热裂纹是由于球墨铸铁在冷却过程中由于温差变化
引起的裂纹。
热裂纹的存在会影响球墨铸铁的机械性能和使用寿命。
3. 砂眼:砂眼是由于砂芯或模具中残留的砂粒等杂质导致的孔洞。
砂眼会使球墨铸铁表面粗糙,影响外观和表面质量。
4. 夹杂物:夹杂物是指在球墨铸铁中存在的非金属夹杂物,如
氧化物、硫化物和硅化物等。
夹杂物的存在会降低球墨铸铁的强度和韧性,并且容易导致断裂。
5. 缩孔:缩孔是由于球墨铸铁在凝固过程中由于体积收缩而形
成的孔洞。
缩孔的存在会降低球墨铸铁的强度和韧性,并且容易导致断裂。
以上是球墨铸铁常见的铸造缺陷。
生产者需要通过优化铸造工艺、提高工艺水平和加强质量控制等措施来减少这些缺陷的出现,从而保证球墨铸铁的品质和使用寿命。
- 1 -。
球墨铸铁缺陷产生原因及应对措施
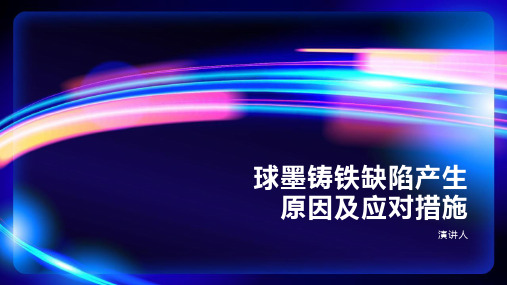
改进生产工艺
优化浇铸工艺:控 制浇铸温度、速度、
压力等参数,提高 1
铸件质量
加强质量控制:建 4
立完善的质量管理 体系,确保生产过
程符合标准要求
改进模具设计:优 化模具结构、尺寸、
2 材料等,提高铸件
成型精度
3
采用先进技术:如
快速凝固技术、电
磁搅拌技术等,提
高铸件性能
维护设备性能
01
定期检查设备,确保 其正常运行
设备维护不当:设备维护不及时,导致设备 性能下降,影响铸件质量
设备设计不合理:设备设计不合理,导致 生产过程中容易出现缺陷
球墨铸铁缺陷应对措 施
优化原材料选择
选择优质生 铁,降低杂
质含量
选用合适的 球化剂和孕 育剂,提高
球化效果
控制合金元 素含量,保 证化学成分
稳定
选用合适的 铸造工艺, 减少缺陷产
球墨铸铁缺陷产生 原因及应对措施
演讲人
目录
01. 球墨铸铁缺陷产生原因 02. 球墨铸铁缺陷应对措施 03. 球墨铸铁缺陷预防措施
球墨铸铁缺陷产生原 因
原材料质量
01 铁水成分:铁水中的碳、硅、锰等元素含 量对球墨铸铁的缺陷产生有很大影响
02 球化剂:球化剂的质量和加入量对球墨铸 铁的缺陷产生有很大影响
04
加强员工培训,提高员工的质量 意识和技能水平
定期检查设备
01
定期检查设备,确保设 备正常运行
02
定期更换磨损部件,避 免设备故障
03
定期清洁设备,保持设 备清洁
04
定期校准设备,确保设 备精度
05
定期培训员工,提高员 工操作技能
06
球铁的缺陷和防治
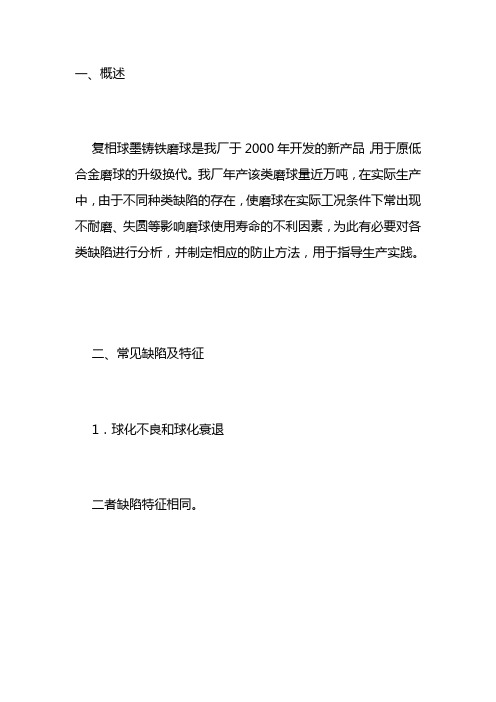
一、概述复相球墨铸铁磨球是我厂于2000年开发的新产品,用于原低合金磨球的升级换代。
我厂年产该类磨球量近万吨,在实际生产中,由于不同种类缺陷的存在,使磨球在实际工况条件下常出现不耐磨、失圆等影响磨球使用寿命的不利因素,为此有必要对各类缺陷进行分析,并制定相应的防止方法,用于指导生产实践。
二、常见缺陷及特征1.球化不良和球化衰退二者缺陷特征相同。
(1)宏观特征铸件断口为银灰色上分布芝麻状黑色斑点,其数量多、直径大,表明程度严重。
若全部呈暗灰色粗晶粒,表明球化不完全。
(2)金相组织集中分布大量厚片状石墨,其数量越多、面积越大,表明程度越严重,球化不完全时呈片状石墨。
(3)产生原因原铁液含硫高,以及严重氧化的炉料中含有过量反球化元素;处理后铁液残留镁和稀土量过低。
铁液中溶解氧量偏高是球化不良的重要原因。
选用低硫焦炭和金属炉料,必要时进行脱硫处理。
另外,应进行废钢除锈,以及增加球化剂中稀土元素用量,严格控制球化工艺。
2.缩孔和缩松特征和产生原因:缩孔产生于铁液温度下降发生一次收缩阶段。
如大气压把表面凝固薄层压陷,则呈现表面凹陷及局部热节凹陷,否则铁液中气体析出至顶部壳中聚集成含气孔的内壁光滑的暗缩孔,有时也与外界相通形成明缩孔,则内表面虽也光滑,但已被氧化。
球墨铸铁共晶凝固时间比灰铸铁长,呈粥状凝固,凝固外壳较薄弱,二次膨胀时在石墨化膨胀力作用下使外壳膨胀,松弛了内部压力。
因此在二次收缩过程中,最后凝固的热节部位内部压力低于大气压,被树枝晶分隔的小熔池处成为真空区,完全凝固后成为孔壁粗糙且排满树枝晶的疏松孔,即缩松缺陷。
宏观缩松产生于热节区残余铁液开始大量凝固的早期,包括了残余铁液的一次收缩和二次收缩,因而尺寸略大且内壁排满枝晶,呈灰暗疏松孔或蝇脚痕状黑点;微观缩松产生于二次收缩末期,共晶团或其集团间的铁液在负压下得不到补缩凝固收缩而成,常见于厚断面处。
3.皮下气孔(1)形貌特征铸件表皮下2~3mm处均匀或蜂窝状分布的球形、椭圆状或针孔状内壁光滑孔洞,直径0.5~3mm,可在热处理和抛丸清理后暴露或机加工时发现,小件中较多。
球墨铸铁常见的铸造缺陷
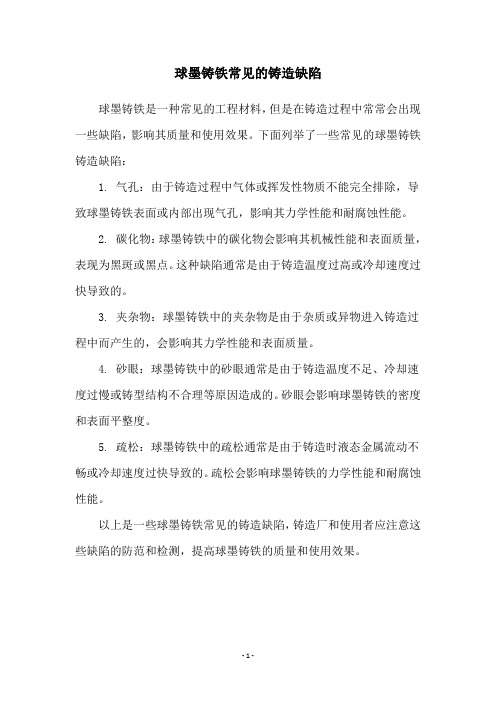
球墨铸铁常见的铸造缺陷
球墨铸铁是一种常见的工程材料,但是在铸造过程中常常会出现一些缺陷,影响其质量和使用效果。
下面列举了一些常见的球墨铸铁铸造缺陷:
1. 气孔:由于铸造过程中气体或挥发性物质不能完全排除,导致球墨铸铁表面或内部出现气孔,影响其力学性能和耐腐蚀性能。
2. 碳化物:球墨铸铁中的碳化物会影响其机械性能和表面质量,表现为黑斑或黑点。
这种缺陷通常是由于铸造温度过高或冷却速度过快导致的。
3. 夹杂物:球墨铸铁中的夹杂物是由于杂质或异物进入铸造过程中而产生的,会影响其力学性能和表面质量。
4. 砂眼:球墨铸铁中的砂眼通常是由于铸造温度不足、冷却速度过慢或铸型结构不合理等原因造成的。
砂眼会影响球墨铸铁的密度和表面平整度。
5. 疏松:球墨铸铁中的疏松通常是由于铸造时液态金属流动不畅或冷却速度过快导致的。
疏松会影响球墨铸铁的力学性能和耐腐蚀性能。
以上是一些球墨铸铁常见的铸造缺陷,铸造厂和使用者应注意这些缺陷的防范和检测,提高球墨铸铁的质量和使用效果。
- 1 -。
球墨铸铁常见缺陷的分析及防止方法

防止 产生 缺 陷的办 法 ,降低 废 品率 ,提高工 厂 的经 阻 碍石 墨化 的元 素 ,由此 可见 ,残 余稀 土 和镁会 增
济效 益 。本文 主要讨 论 我厂 稀土镁 球 墨铸铁 生产 中 加 球墨铸 铁 的 白 口倾 向 ,故它 们含 量较 高 时 ,会 增 常 见缺 陷 ( 松 、缩孔 、夹渣 、球 化 不 良及球化 衰 加 缩孔 、缩 松倾 向 。 缩
出现 缩孔 、缩 松 、夹渣 、球 化不 良及 球化 衰退 等缺 下 。
陷 。这些 缺 陷影 响 铸 件 性 能 ,使铸 件 废 品率 增 高 。
( )稀 土和镁 稀 土残余 量 过高会 恶 化石 墨形 3
为 了防止 这些 缺陷 的产 生 ,需对其 进 行分 析 ,提 出 状 ,降低 球 化率 ,因此稀 土含 量不 能过 高 。而镁 是
含硫 量过 高 ,硫与 镁 、稀 土生 成硫 化物 ,因其密 度 小 而上 浮到铁 液表 面 ,而 这些 硫化 物与 空气 中 氧发 从而 降低 了镁 和 稀 土 含 量 。 当铁 液 中 叫 >0 1 .%
( )硅 1
( )硫 2
硅 的 氧 化物 是 夹 渣 的 主要 组 成 部分 , 生反应 生 成 硫 ,硫 又 回到 铁 液 中 ,重 复 上述 过 程 ,
难 ,砂 型 紧实度 难 以保证 。 ( )将 3 芯芯头做 成活块 。造型 时先将芯 头 活 2 #
( )清 理 铸 件 时 ,发 现 其 底 面 有 较 大 面 积 粘 块取下来 ,舂实底 平 面 ,放 好 主体 模 样 ,舂 出 主型 2
缺陷特点、成因、预防(精)

讲解
球铁铸件的特有缺陷 裂 纹
特征:铸件冷却过程中收缩应力、热应力等铸造应力超过该断 面金属抗断裂能力形成的裂纹。
原因:碳硅含量低、碳化物形成元素增加、孕育不足、冷却过
快等都可以增加铸造应力。铸件壁厚差别大形状复杂也能产生
裂纹。 预防:提高碳当量降低含磷量增加孕育及必要的铸造工艺措施。
特征:气孔内壁粗糙,排满树枝晶,常见于热节处。
原因:碳当量低,增加缩孔缩松的倾向
预防:提高铸型刚度,提高铁液碳当量,适当降低浇注温度。
球铁铸件的特有缺陷
讲解
夹 渣
特征:分布于铸件浇注位置上表面、型芯的下面及死角处,破断
面上呈现暗黑色无光泽深浅不一的夹杂物,断续分布。 原因:一次夹渣中铁液含硫量高,氧化严重;二次夹渣中残留镁 量过高提高了氧化膜形成温度。 预防:降低原铁液硫、氧含量,提高出炉温度。
讲解
球铁铸件的特有缺陷 皮下气孔
特点:铸件表皮下2-3mm处均匀或者蜂窝状分布的球形、椭圆
形或针孔内壁光滑孔洞
原因:树脂砂粘结剂含氮较多,球墨铸铁糊状凝固特点使气体 通道较早被堵塞 预防:浇注温度不得低于1300℃,采用少氮或者无氮树脂砂, 减少铁液中的气体,可以预防。
球铁铸件的特有缺陷
讲解
缩 孔
每日铸造知识—如何防止球铁件主要常见缺陷?

每日铸造知识—如何防止球铁件主要常见缺陷?球铁件除了会产生一般的铸造不良外,还会发生一些特有的不良缺陷,如缩松、夹渣、皮下气孔、球化不良及衰退等。
为了降低这些不良,必须对其进行分析,总结出各种影响因素,提出防止措施,才能有效降低缺陷的产生,提高铸件的力学性能及生产效益。
本篇将主要讲解如何防止这些常见缺陷:缩孔、缩松、夹渣、皮下气孔、石墨漂浮、球化不良及球化衰退。
一、缩孔、缩松1影响因素(1)碳当量:提高碳量,增大了石墨化膨胀,可减少缩孔缩松。
此外,提高碳当量还可提高球铁的流动性,有利于补缩。
生产优质铸件的经验公式为C%+1/7Si%>3 9%。
但提高碳当量时,不应使铸件产生石墨漂浮等其他缺陷。
(2)磷:铁液中含磷量偏高,使凝固范围扩大,同时低熔点磷共晶在最后凝固时得不到补给,以及使铸件外壳变弱,因此有增大缩孔、缩松产生的倾向。
一般工厂控制含磷量小于0.08%。
(3)稀土和镁:稀土残余量过高会恶化石墨形状,降低球化率,因此稀土含量不宜太高。
而镁又是一个强烈稳定碳化物的元素,阻碍石墨化。
由此可见,残余镁量及残余稀土量会增加球铁的白口倾向,使石墨膨胀减小,故当它们的含量较高时,亦会增加缩孔、缩松倾向。
(4)壁厚:当铸件表面形成硬壳以后,内部的金属液温度越高,液态收缩就越大,则缩孔、缩松的容积不仅绝对值增加,其相对值也增加。
另外,若壁厚变化太突然,孤立的厚断面得不到补缩,使产生缩孔缩松倾向增大。
(5)温度:浇注温度高,有利于补缩,但太高会增加液态收缩量,对消除缩孔、缩松不利,所以应根据具体情况合理选择浇注温度,一般以1300~1350℃为宜。
(6)砂型的紧实度:若砂型的紧实度太低或不均匀,以致浇注后在金属静压力或膨胀力的作用下,产生型腔扩大的现象,致使原来的金属不够补缩而导致铸件产生缩孔、缩松。
(7)浇冒口及冷铁:若浇注系统、冒口和冷铁设置不当,不能保证金属液顺序凝固;另外,冒口的数量、大小以及与铸件的连接当否,将影响冒口的补缩效果。
球墨铸铁件常见缺陷的分析与对策
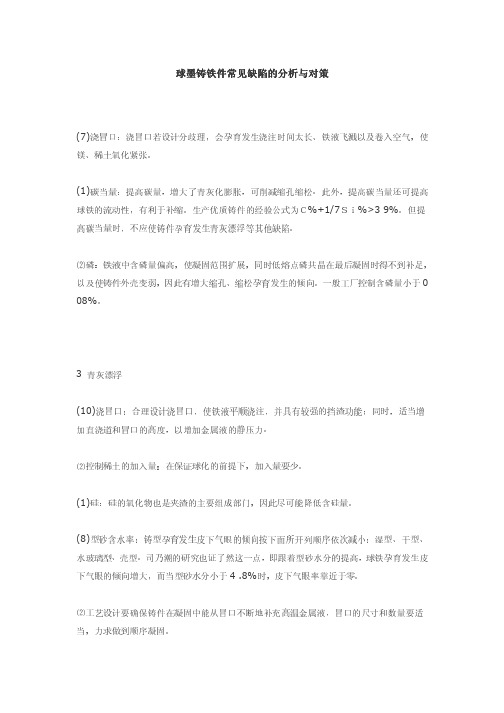
球墨铸铁件常见缺陷的分析与对策(7)浇冒口:浇冒口若设计分歧理,会孕育发生浇注时间太长、铁液飞溅以及卷入空气,使镁、稀土氧化紧张。
(1)碳当量:提高碳量,增大了青灰化膨胀,可削减缩孔缩松。
此外,提高碳当量还可提高球铁的流动性,有利于补缩。
生产优质铸件的经验公式为C%+1/7Si%>3 9%。
但提高碳当量时,不应使铸件孕育发生青灰漂浮等其他缺陷。
⑵磷:铁液中含磷量偏高,使凝固范围扩展,同时低熔点磷共晶在最后凝固时得不到补足,以及使铸件外壳变弱,因此有增大缩孔、缩松孕育发生的倾向。
一般工厂控制含磷量小于0 08%。
3 青灰漂浮(10)浇冒口:合理设计浇冒口,使铁液平顺浇注,并具有较强的挡渣功能;同时,适当增加直浇道和冒口的高度,以增加金属液的静压力。
⑵控制稀土的加入量:在保证球化的前提下,加入量要少。
(1)硅:硅的氧化物也是夹渣的主要组成部门,因此尽可能降低含硅量。
(8)型砂含水率:铸型孕育发生皮下气眼的倾向按下面所开列顺序依次减小:湿型、干型、水玻璃型、壳型。
司乃潮的研究也证了然这一点,即跟着型砂水分的提高,球铁孕育发生皮下气眼的倾向增大,而当型砂水分小于4 .8%时,皮下气眼率靠近于零。
⑵工艺设计要确保铸件在凝固中能从冒口不断地补充高温金属液,冒口的尺寸和数量要适当,力求做到顺序凝固。
(4)注意处理温度。
出炉温度应低于1460℃,以防球化剂紧张烧损;要防止高温下的氧化征象,盖好覆盖球化剂的铁板(厚度应>3mm);铁液扒渣后应用草木灰等盖好;当铁液温度>1350℃出现球化不良及衰退时,可补加球化剂;而当<1350℃时就不能补加球化剂,也不得浇注球铁件,只能补加其它铁液浇注不重要的灰铸铁件或芯骨等。
⑵硅:在碳当量不变的条件下,适当降低含硅量,有助于降低孕育发生青灰漂浮的倾向。
(4)浇注温度:浇注温度过低时,金属液内的金属氧化物等因金属液的粘度过高,不容易上浮至表面而残留在金属液内;温度过高时,金属液表面的熔渣变得太淡薄,不容易自液体表面去除,往往随金属液流入型内。
球铁典型铸造缺陷极其防止

球铁典型铸造缺陷极其防止1、球化不良与球化衰退(1)球化不良:球化不良是指球化处理没有达到预期的球化效果。
球化不良的金相组织为:集中分布的厚片状石墨和少量球状、团状石墨;有时还有水草状石墨。
随着球化不良的程度的加剧,集中分布的厚片状石墨的数量逐渐增多、面积增大,球化不良将使球墨铸铁的力学性能达不到响应牌号要求的指标。
关于球化不良产生的原因极其防止措施分述如下:1、原铁液含硫高 硫是主要反球化元素,含硫高会严重影响球化,一般原铁液的硫的质量分数要小于等于0.06%。
为保证球化,当原铁液含硫量偏高时,必须响应地提高球化剂的加入量,含硫量越高,则球化剂的消耗量也越多。
2、球化元素残留量低 为使石墨球化良好,球铁中必须含有一定量的残余镁和稀土,在我国现今生产条件下,残余镁量的质量分数不得小于0.03%,残余稀土量的质量分数不得小于0.02%。
3、铁液氧化 原材料中铁锈、污染以及铁液在熔化与过热中的氧化,导致铁液中的FeO 含量增多,因而在球化过程中要消耗更多的镁,致使残余镁量过低。
4、炉料含有反球化元素 当反球化元素超出允许范围时,就会影响球化效果,要注意废钢中可能含有钛,还要注意电镀材料、铝销、铅系涂料进入冲天炉。
稀土有中和反球化元素的能力,根据我国原生铁中含有较多的反球化元素的情况,我国球铁中的残余稀土量比国外的要多。
5、 孕育效果差 由于孕育效果差,或者孕育衰退,均会造成石墨球数量少,使得石墨球不圆整。
6、型砂水分高、含硫量高 由于界面反应,铁液中的镁与铸型表面中的氧、硫发生作用,致使铸件表面的残余镁量不足,形成一薄层的片状石墨。
解决的措施就是提高残余镁量,减少型砂含水量,型砂硫的质量分数应小于0.1%,或采用能获得还原性气氛的涂料。
在使用含硫硬化剂的树脂砂铸型中,可采用含有MgO 、CaO 的涂料。
2、球化衰退球化衰退的特点时:炉前球化良好,在铸件上球化不好;或者同一浇包的铁液,先浇注的铸件球化良好,后浇注的铸件球化不好。
铸造缺陷与防止(精选五篇)
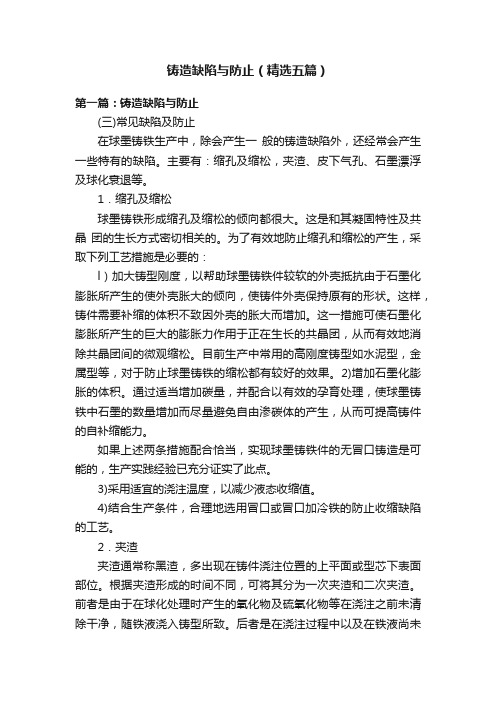
铸造缺陷与防止(精选五篇)第一篇:铸造缺陷与防止(三)常见缺陷及防止在球墨铸铁生产中,除会产生一般的铸造缺陷外,还经常会产生一些特有的缺陷。
主要有:缩孔及缩松,夹渣、皮下气孔、石墨漂浮及球化衰退等。
1.缩孔及缩松球墨铸铁形成缩孔及缩松的倾向都很大。
这是和其凝固特性及共晶团的生长方式密切相关的。
为了有效地防止缩孔和缩松的产生,采取下列工艺措施是必要的:l)加大铸型刚度,以帮助球墨铸铁件较软的外壳抵抗由于石墨化膨胀所产生的使外壳胀大的倾向,使铸件外壳保持原有的形状。
这样,铸件需要补缩的体积不致因外壳的胀大而增加。
这一措施可使石墨化膨胀所产生的巨大的膨胀力作用于正在生长的共晶团,从而有效地消除共晶团间的微观缩松。
目前生产中常用的高刚度铸型如水泥型,金属型等,对于防止球墨铸铁的缩松都有较好的效果。
2)增加石墨化膨胀的体积。
通过适当增加碳量,并配合以有效的孕育处理,使球墨铸铁中石墨的数量增加而尽量避免自由渗碳体的产生,从而可提高铸件的自补缩能力。
如果上述两条措施配合恰当,实现球墨铸铁件的无冒口铸造是可能的,生产实践经验已充分证实了此点。
3)采用适宜的浇注温度,以减少液态收缩值。
4)结合生产条件,合理地选用冒口或冒口加冷铁的防止收缩缺陷的工艺。
2.夹渣夹渣通常称黑渣,多出现在铸件浇注位置的上平面或型芯下表面部位。
根据夹渣形成的时间不同,可将其分为一次夹渣和二次夹渣。
前者是由于在球化处理时产生的氧化物及硫氧化物等在浇注之前未清除干净,随铁液浇入铸型所致。
后者是在浇注过程中以及在铁液尚未在铸型中凝固以前的一段时间内产生的渣。
一次渣的尺寸较大,二次渣一般很细小,在铸件的加工表面上表现为暗灰色无光泽的斑纹或云片状。
夹渣缺陷严重影响铸件的力学性能,特别是硬度、韧性及耐磨性,并能导致耐压铸件发生渗漏。
防止措施主要有:1)尽量降低原铁液的含硫量。
2)在保证石墨球化条件下,降低铁液的残留镁量和残留稀土量。
3)提高浇注温度,应不低于1350℃。
球墨铸铁常见缺陷及防止措施
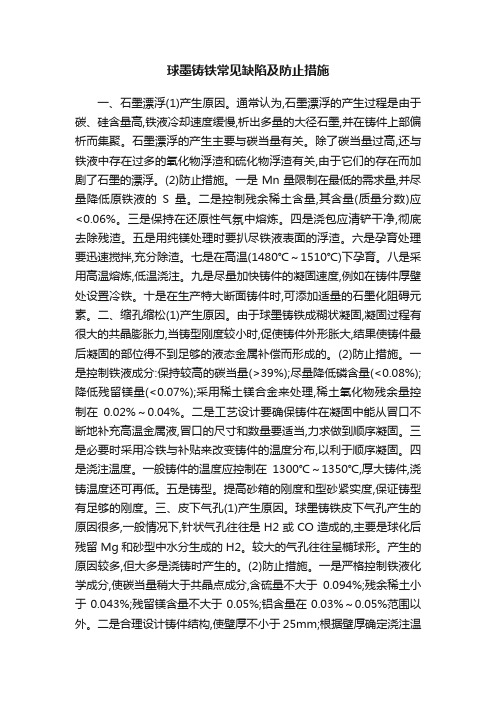
球墨铸铁常见缺陷及防止措施一、石墨漂浮(1)产生原因。
通常认为,石墨漂浮的产生过程是由于碳、硅含量高,铁液冷却速度缓慢,析出多量的大径石墨,并在铸件上部偏析而集聚。
石墨漂浮的产生主要与碳当量有关。
除了碳当量过高,还与铁液中存在过多的氧化物浮渣和硫化物浮渣有关,由于它们的存在而加剧了石墨的漂浮。
(2)防止措施。
一是Mn量限制在最低的需求量,并尽量降低原铁液的S量。
二是控制残余稀土含量,其含量(质量分数)应<0.06%。
三是保持在还原性气氛中熔炼。
四是浇包应清铲干净,彻底去除残渣。
五是用纯镁处理时要扒尽铁液表面的浮渣。
六是孕育处理要迅速搅拌,充分除渣。
七是在高温(1480℃~1510℃)下孕育。
八是采用高温熔炼,低温浇注。
九是尽量加快铸件的凝固速度,例如在铸件厚壁处设置冷铁。
十是在生产特大断面铸件时,可添加适量的石墨化阻碍元素。
二、缩孔缩松(1)产生原因。
由于球墨铸铁成糊状凝固,凝固过程有很大的共晶膨胀力,当铸型刚度较小时,促使铸件外形胀大,结果使铸件最后凝固的部位得不到足够的液态金属补偿而形成的。
(2)防止措施。
一是控制铁液成分:保持较高的碳当量(>39%);尽量降低磷含量(<0.08%);降低残留镁量(<0.07%);采用稀土镁合金来处理,稀土氧化物残余量控制在0.02%~0.04%。
二是工艺设计要确保铸件在凝固中能从冒口不断地补充高温金属液,冒口的尺寸和数量要适当,力求做到顺序凝固。
三是必要时采用冷铁与补贴来改变铸件的温度分布,以利于顺序凝固。
四是浇注温度。
一般铸件的温度应控制在1300℃~1350℃,厚大铸件,浇铸温度还可再低。
五是铸型。
提高砂箱的刚度和型砂紧实度,保证铸型有足够的刚度。
三、皮下气孔(1)产生原因。
球墨铸铁皮下气孔产生的原因很多,一般情况下,针状气孔往往是H2或CO造成的,主要是球化后残留Mg和砂型中水分生成的H2。
较大的气孔往往呈椭球形。
产生的原因较多,但大多是浇铸时产生的。
- 1、下载文档前请自行甄别文档内容的完整性,平台不提供额外的编辑、内容补充、找答案等附加服务。
- 2、"仅部分预览"的文档,不可在线预览部分如存在完整性等问题,可反馈申请退款(可完整预览的文档不适用该条件!)。
- 3、如文档侵犯您的权益,请联系客服反馈,我们会尽快为您处理(人工客服工作时间:9:00-18:30)。
球铁典型铸造缺陷极其防止1、球化不良与球化衰退(1)球化不良:球化不良是指球化处理没有达到预期的球化效果。
球化不良的金相组织为:集中分布的厚片状石墨和少量球状、团状石墨;有时还有水草状石墨。
随着球化不良的程度的加剧,集中分布的厚片状石墨的数量逐渐增多、面积增大,球化不良将使球墨铸铁的力学性能达不到响应牌号要求的指标。
关于球化不良产生的原因极其防止措施分述如下:1、原铁液含硫高 硫是主要反球化元素,含硫高会严重影响球化,一般原铁液的硫的质量分数要小于等于0.06%。
为保证球化,当原铁液含硫量偏高时,必须响应地提高球化剂的加入量,含硫量越高,则球化剂的消耗量也越多。
2、球化元素残留量低 为使石墨球化良好,球铁中必须含有一定量的残余镁和稀土,在我国现今生产条件下,残余镁量的质量分数不得小于0.03%,残余稀土量的质量分数不得小于0.02%。
3、铁液氧化 原材料中铁锈、污染以及铁液在熔化与过热中的氧化,导致铁液中的FeO 含量增多,因而在球化过程中要消耗更多的镁,致使残余镁量过低。
4、炉料含有反球化元素 当反球化元素超出允许范围时,就会影响球化效果,要注意废钢中可能含有钛,还要注意电镀材料、铝销、铅系涂料进入冲天炉。
稀土有中和反球化元素的能力,根据我国原生铁中含有较多的反球化元素的情况,我国球铁中的残余稀土量比国外的要多。
5、 孕育效果差 由于孕育效果差,或者孕育衰退,均会造成石墨球数量少,使得石墨球不圆整。
6、型砂水分高、含硫量高 由于界面反应,铁液中的镁与铸型表面中的氧、硫发生作用,致使铸件表面的残余镁量不足,形成一薄层的片状石墨。
解决的措施就是提高残余镁量,减少型砂含水量,型砂硫的质量分数应小于0.1%,或采用能获得还原性气氛的涂料。
在使用含硫硬化剂的树脂砂铸型中,可采用含有MgO 、CaO 的涂料。
2、球化衰退球化衰退的特点时:炉前球化良好,在铸件上球化不好;或者同一浇包的铁液,先浇注的铸件球化良好,后浇注的铸件球化不好。
球化衰退的原因是镁量和稀土量随着铁液停止时间的延长而发生衰退。
镁、稀土与氧的亲和力大于与硫的亲和力,所以孚在铁液表面的Mgs 、Ce 2S 3夹杂物与空气中的氧要发生下列反应:2MgS+O 2=2MgO+2S 2Ce 2S 3+3O 2=2Ce 2O 3+6S 此时,所产生的硫又进入铁液中,与镁、稀土发生作用:Mg+S=MgS2Ce+3S=Ce 2S 3 这样,随铁液停置时间的延长,硫不断和镁与稀土发生作用,不断生成MgS 、Ce 2S 3,它们又不断的被空气中的氧所氧化,循环进行。
结果,消耗了铁液中的镁和稀土,硫又重新从浮渣进入铁液中,出现“回硫现象”。
稀土铈、钇的沸点比镁高,在一般的铁液温度下它们不会发生汽化逸出。
此外,稀土铈、钇的硫化物、氧化物的熔点高、密度大,上浮速度慢。
所以,稀土铈、钇的减缓速度比镁要小,在1350~1400℃,镁的质量分数的衰减率是(0.001~0.004)%/Min;轻稀土铈的质量分数的衰减速率是(0.0006~0.002)%/min;重稀土钇的质量的衰减率是0.0008%/min。
各种球化元素的衰减速率与铁液中的含硫量有密切关系,含硫量越高,则衰减速率就越快。
减少球化衰退的措施列举如下:(1)缩短铁液的停置时间:从球化处理完成到浇注完毕,应在15min以内结束。
(2)降低原铁液含硫量:原铁液含硫高,则需要消耗更多的球化元素,另外,原铁液含硫量高,也是渣中的硫化物含量增大,促使“回硫现象”加剧,加速球化衰退。
(3)加强覆盖与扒渣:球化处理后加稀渣剂(例如珍珠岩)覆盖,并采取多次扒渣措施,可减少“回硫现象”。
(4)适当增加球化剂用量根据铁液中的含硫量,采取响应的增加球化剂用量的措施,是可行的,也是有效的,但不是最佳的。
治本的措施是力求把铁液中的含硫量降至最低。
另外,过多地加入球化剂,不仅增加成本,而且还会导致石墨球化程度的恶化。
3、缩孔和缩松特点:缩孔和缩松在球铁中要比在普通灰铁中更为普遍。
要防止它们,就必须给予更多的注意和控制。
能够明显看出的、尺寸较大而又集中的孔洞叫缩孔,不宜看清的、细小分散的孔洞叫缩松。
大多在铸件热节的上部产生缩孔。
在铸件热节处、在缩孔的下方往往有比较分散的缩松。
但是,对于一些壁厚均匀的中心,或者是在厚壁的中心部位,也可出现缩松。
有些缩松的体积很小,只有在显微镜下才能被发现。
这种缩松呈多角形,有时连续、有时断续,分布在共晶团边界。
这种缩松叫显微缩松。
奥氏体枝晶凝固后,残余的铁液则在枝晶间最后凝固,因得不到补缩而形成显微缩松。
球墨铸铁的缩孔与缩松体积比普通灰铸铁、白口铸铁和碳钢都要大。
(从铸铁成分一文中有表及数据说明),但是,在生产中,也可采用无冒口工艺得到健全的球铁铸件。
球墨铸铁缩孔和缩松增大的原因1、球状石墨在铁液中析出经过球化处理后,球状石墨会立即在铁液中析出,并且,随着温度的逐步降低,铁液中的石墨球逐渐长大。
石墨析出和长大的过程,伴随着液态金属的膨胀。
2、离异共晶转变球墨铸铁以离异共晶的方式进行共晶转变。
其凝固方式是内外几乎是同时进行的粥样凝固,因而容易形成显微缩松。
3、共晶膨胀量大由于呈粥样凝固,铸件在共晶转变期间要持续很长时间,球墨铸铁的共晶时间可比普通灰铸铁延长一倍还要多,由此,导致共晶转变的石墨化膨胀量大。
4、型壁移动在共晶凝固期间,由于粥样凝固,决定了铸件表面的凝固层很薄,以至不能建立其足够强度的凝固外壳,以抑制共晶凝固期间产生的石墨化膨胀,致使铸型内壁向外移动。
在铸型刚度不够的情况下,使型腔尺寸增大,由此导致缩孔缩松体积进一步增大。
5、球化处理使铁液的过冷度加大铁液经过球化处理后,原有的氢、氧、氮和CO 气体含量减少,铁液得到了净化,致使外来核心减少。
并且,铁液的过热温度越高,净化程度也越高,由此导致的过冷倾向也更加剧。
此外,球化元素镁和稀土均能与碳形成炭化物,由此减少了石墨化程度,加大了收缩倾向。
4、防止产生缩松和缩孔的措施1、铁液成分 碳、硅、锰、稀土、镁的含量必须适当。
含碳量高,可使缩孔和缩松的倾向减小,但含碳量过高,会产生石墨漂浮。
对于薄壁铸件来说,碳硅含量低时,易产生游离炭化物。
对于厚壁铸件,可采用较低碳量,并适当增加硅量。
锰易形成炭化物,容易促使形成缩孔缩松,为此,应当力求降低含锰量,尤其对于铸态铁素体球墨铸铁,更是如此。
在保证球化的前提下,不使镁和稀土残余量过高。
2、铁液状态 缩孔与缩松倾向小的铁液 所具有的冷却曲线的斜率应较小,过冷度要小。
共晶凝固时的膨胀要小,二次收缩也小。
要是曲线C 转变成A ,要满足的条件是:(1)冷却速度慢(2)碳当量高,析出石墨的倾向大。
(3)铁液中有效石墨核心数量多。
(4)良好的孕育效果。
3、铸型刚度 对于湿砂型来说,铸型硬度要在90(B 型硬度计)以上,希望能达到40MPa 的抗拉强度。
此外,砂箱的紧固也非常重要。
对于金属型覆砂(覆砂厚度8mm 左右)以及用自硬砂制作大型铸件时,可以实现无冒口铸造。
此时要满足的条件是:G ≥α1+α2+β式中G -由碳的石墨化而引起的铁液膨胀量;α1-铁液的液态收缩α2-凝固收缩β-铸型膨胀量。
4、浇铸温度 为了防止产生缩孔和缩松,就要使液态收缩量减小,浇注温度低是有利的。
但是,对于薄壁(10mm )铸件来说,容易出现炭化物。
此时,采用冒口补缩却难以发挥作用。
因此,适宜的浇注温度还取决于铸件的结构与铸件壁厚。
5、浇注系统 采取顺序凝固方式,对于铸件、冒口、冒口颈、内浇道和横浇道的设计和安放以及外冷铁的设置和在必要时使用金属型等,均是行之有效的防止缩孔与缩松地有效措施。
5、皮下气孔现象在球墨铸铁生产中最常见的缺陷之一就是皮下气孔。
在湿铸型、特别是比表面积大的小型铸件中最容易发生皮下气孔。
皮下气孔往往位于铸件表面以下0、5—1mm 处,孔径多为0、5—2mm 的针孔,内壁光滑(内表面有时附有石墨膜),呈均匀分布在铸件上表面或远离内浇到的部位,但在铸件则面和底部也偶而寸在。
在铸态时,皮下气孔不宜被发现;但是,铸件经热处理后,或是经机加工后则显露.皮下气孔影响铸件的表面质量,并且在出现皮下气孔的部位,往往伴随着片状石墨,因而恶化了该部位的力学性能。
产生的原因在把铸件表层去掉后,就会发现有许多小针孔,其中充满了硫化氢气体。
由此,可以推断发生的化学反应是:当铁液中的硫化镁与铸型中的水相遇时,则产生硫化氢。
MgS +H 2O →MgO +N 2S 结果是:形成的N 2S 气体在铸件快速凝固时,来不及上浮,就停留在靠近铸件表面上。
因此,这些气泡不仅呈球形,有的还成雨滴状,这些雨滴的尖端伸向铸件内部。
皮下气孔也可能是由产生的氢气造成的。
在经球化处理后的铁液中,会发生如下反应: (Fe 、Mg )C +N 2O (铸型中)→(Fe 、Mg )O +C 2H 2C 2H 2→2C (石墨膜)+H 2↑(气泡)Mg +N 2O (铸型中)→MgO +H 2↑(气泡)此外,在皮下气孔内,有时会发现渣状夹杂物,这些渣中Si 、Al 、Ng 、Ca 含量较高。
由此,形成的Al 2O 3、CaO 、MgO 、SiO 2、MnO 等可为气泡的异质形核提供结晶衬垫。
在温度大于1530℃时,会发生反应:SiO 2+2C →Si +2CO ↑在温度大于1400℃时,会发生反应:MnO +C →Mn +2CO ↑ 在温度大于720℃时,会发生反应:FeO +C →Fe +CO ↑上述的三个反应均会形成CO 气体,导致铁液中CO 气体过饱和程度,产生过大的析出压力,因而加剧了皮下气孔的形成。
皮下气孔的防止可采取如下措施:(1)采用湿型铸造时,必须严格控制型砂中的水分,其最高质量分数不得超过5、5%。
(2)提高浇注温度,特别是对于薄壁铸件,浇注温度不得低于1300℃。
(3)球化处理后扒渣,浇注前挡渣,以防止更多的MgS 随铁液进入铸型。
(4)球化处理后,令铁液静置片刻,这对MgS 颗粒上浮,进入渣中排除有利。
(5)提高铸型的透气性,有助于减轻皮下气孔。
(6)采用冰晶石粉可有效减轻皮下气孔,冰晶石粉与水发生如下反应:NaAlF 6+2H 2O →NaAlO 2+2HaF +4NF 由于冰晶石与水的作用,就避免了水与铁液中MgS 的作用。
(7)避免铁铁中含有铝,因为它易于水蒸气反应,而产生氢气孔:3H 2O +2Al →Al 2O 3+H 2↑ 为此,硅铁中铝的质量分数限制在0、5%—1、0%范围内。
如果铝的质量分数大于2%,则易生成氢气孔。
(8)在型砂中附加还原性的碳质添加物,可防止皮下气孔的产生。
(9)改进浇注系统设计。
6、夹渣加渣中有三种类型:第一型粗大渣是2Mg ·SiO 2+MgS 或+FeS ;第2型条状渣是MgO ,第3型细小渣是MgO +MgS ,它们是单独或是符合析出的。