树脂注射成型工艺_一种新型低压成型工艺
12节-低压注塑成型
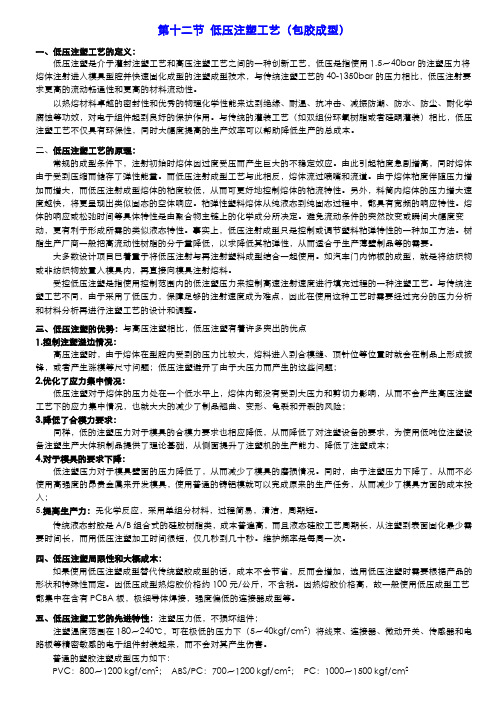
第十二节低压注塑工艺(包胶成型)一、低压注塑工艺的定义:低压注塑是介于灌封注塑工艺和高压注塑工艺之间的一种创新工艺,低压是指使用1.5~40bar的注塑压力将熔体注射进入模具型腔并快速固化成型的注塑成型技术,与传统注塑工艺的40-1350bar的压力相比,低压注射要求更高的流动畅通性和更高的材料流动性。
以热熔材料卓越的密封性和优秀的物理化学性能来达到绝缘、耐温、抗冲击、减振防潮、防水、防尘、耐化学腐蚀等功效,对电子组件起到良好的保护作用。
与传统的灌装工艺(如双组份环氧树脂或者硅酮灌装)相比,低压注塑工艺不仅具有环保性,同时大幅度提高的生产效率可以帮助降低生产的总成本。
二、低压注塑工艺的原理:常规的成型条件下,注射初始时熔体因过度受压而产生巨大的不稳定效应。
由此引起粘度急剧增高,同时熔体由于受到压缩而储存了弹性能量。
而低压注射成型工艺与此相反,熔体流过喷嘴和流道。
由于熔体粘度伴随压力增加而增大,而低压注射成型熔体的粘度较低,从而可更好地控制熔体的粘流特性。
另外,料筒内熔体的压力增大速度越快,将更呈现出类似固态的空体响应。
粘弹性塑料熔体从纯液态到纯固态过程中,都具有宽频的响应特性。
熔体的响应或松弛时间等具体特性是由聚合物主链上的化学成分所决定。
避免流动条件的突然改变或瞬间大幅度变动,更有利于形成所需的类似液态特性。
事实上,低压注射成型只是控制或调节塑料粘弹特性的一种加工方法。
树脂生产厂商一般把高流动性树脂的分子量降低,以求降低其粘弹性,从而适合于生产薄壁制品等的需要。
大多数设计项目已着重于将低压注射与再注射塑料成型结合一起使用。
如汽车门内饰板的成型,就是将纺织物或非纺织物放置入模具内,再直接向模具注射熔料。
受控低压注塑是指使用控制范围内的低注塑压力来控制高速注射速度进行填充过程的一种注塑工艺。
与传统注塑工艺不同,由于采用了低压力,保障足够的注射速度成为难点,因此在使用这种工艺时需要经过充分的压力分析和材料分析再进行注塑工艺的设计和调整。
几种特殊的塑胶成型工艺

几种特殊的塑胶成型工艺1.气体(水)辅助注射成型气体辅助注射成型是自往复式螺杆注塑机咨询世以来,注射成型技术最重要的进展之一。
它通过高压气体在注塑制件内部产生中空截面,利用气体积压,减少制品残余内应力,排除制品表面缩痕,减少用料,显示传统注射成型无法比拟的优越性。
气体辅助注射的工艺过程要紧包括三个时期:起始时期为熔体注射。
该时期把塑料熔体注人型腔,与传统注射成型相同,然而熔体只充满型腔的60%-95%,具体的注射量随产品而异。
第二时期为气体注人。
该时期把高压惰性气体注人熔体芯部,熔体前沿在气体压力的驱动下连续向前流淌,直至充满整个型腔。
气辅注塑时熔体流淌距离明显缩短,熔体注塑压力能够大为降低。
气体可通过注气元件从主流道或直截了当由型腔进人制件。
因气体具有始终选择阻力最小(高温、低粘)的方向穿透的特性,因此需要在模具内专门设计气体的通道。
第三时期为气体保压。
该时期使制件在保持气体压力的情形下冷却.进一步利用气体各向同性的传压特性在制件内部平均地向外施压,并通过气体膨胀补充因熔体冷却凝固所带来的体积收缩(二次穿透),保证制品外表面紧贴模壁。
气辅技术为许多原先无法用传统工艺注射成型的制件采纳注塑提供了可能,在汽车、家电、家具、电子器件、日常用品、办公自动化设备、建筑材料等几乎所有塑料制件领域差不多得到了广泛的应用,同时作为一项带有挑战性的新工艺为塑料成型开创了全新的应用领域。
气辅技术专门适用于制作以下几方面的注塑制品:1)管状、棒状制品:如手柄、挂钩、椅子扶手、淋浴喷头等。
采纳中空结构,可在不阻碍制品功能和使用性能的前提下;大幅度节约原材料,缩短冷却时刻和生产周期。
2)大型平板制件:如汽车外表板、内饰件格栅、商用机器的外军及抛物线形卫星天线等。
通过在制件内设置式气道,能够显著提高制品的刚度和表面质量,减小翘曲变形和表面凹陷,大幅度降低锁模力,实现用较小的设备成型较大的制件。
3)厚、薄壁一体的复杂结构制品:如电视机、运算机、打印机外壳及内部支撑和外部装饰件等。
聚碳酸酯的注射成型工艺

聚碳酸酯的注射成型工艺
聚碳酸酯的注射成型工艺是一种特殊的注射成型方式,它可以使用聚碳酸酯材料进行成型。
聚碳酸酯是一种合成树脂,具有良好的机械性能、耐寒性、耐腐蚀性、耐热性和机械加工性。
因此,它在许多工业领域中得到了广泛应用,例如汽车零部件、管道、滚筒辊等。
聚碳酸酯的注射成型通常采用熔融成型的方法,即将聚碳酸酯熔融后注入模具内,然后冷却固化。
此外,还可以采用低温注射成型,即在低温条件下使用冷压力将聚碳酸酯材料注入模具内,然后冷却固化。
在聚碳酸酯的注射成型过程中,必须首先将原料混合均匀,并经过热处理,使其具有足够的流动性,以便将其注入模具中形成所需的产品形状。
而且,将原料混合成聚碳酸酯的混合物时,必须注意混合物的温度,以保证其有足够的流动性和可塑性。
接下来,需要将混合的聚碳酸酯放入注射机中,并进行加热,使其具有足够的流动性。
然后,将熔融的聚碳酸酯以合适的压力注入模具内,以形成所需的产品形状。
接着,要进行冷却,使聚碳酸酯冷却固化,以保证其有良好的机械性能和耐久性。
最后,需要进行切割和抛光,以使产品具有良好的外观效果。
在切割过程中,要注意温度,以免损坏产品的外观和性能。
同时,也要注意产品的表面抛光,以使其具有良好的外观效果。
总之,聚碳酸酯的注射成型工艺是一种复杂的成型工艺,其成功完成的关键在于正确的选择和控制模具、原料、温度、压力等参数。
它的优势在于可以生产出高精度、复杂形状的产品,并具有良好的机械性能和耐久性。
环氧树脂碳纤维复合材料的成型工艺
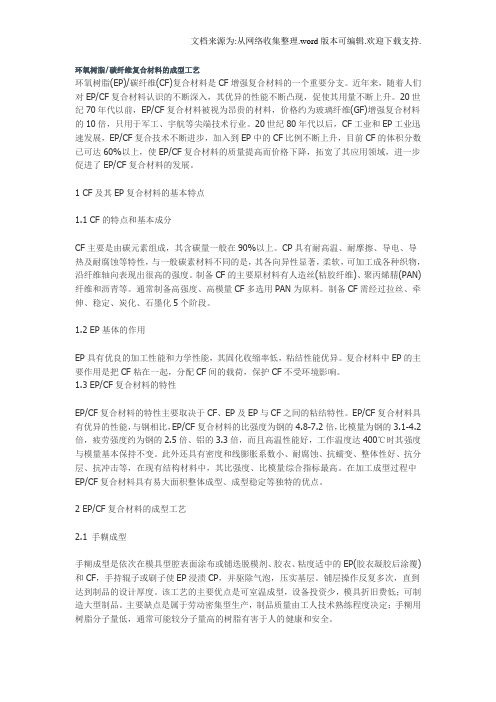
环氧树脂/碳纤维复合材料的成型工艺环氧树脂(EP)/碳纤维(CF)复合材料是CF增强复合材料的一个重要分支。
近年来,随着人们对EP/CF复合材料认识的不断深入,其优异的性能不断凸现,促使其用量不断上升。
20世纪70年代以前,EP/CF复合材料被视为昂贵的材料,价格约为玻璃纤维(GF)增强复合材料的10倍,只用于军工、宇航等尖端技术行业。
20世纪80年代以后,CF工业和EP工业迅速发展,EP/CF复合技术不断进步,加入到EP中的CF比例不断上升,目前CF的体积分数已可达60%以上,使EP/CF复合材料的质量提高而价格下降,拓宽了其应用领域,进一步促进了EP/CF复合材料的发展。
1 CF及其EP复合材料的基本特点1.1 CF的特点和基本成分CF主要是由碳元素组成,其含碳量一般在90%以上。
CP具有耐高温、耐摩擦、导电、导热及耐腐蚀等特性,与一般碳素材料不同的是,其各向异性显著,柔软,可加工成各种织物,沿纤维轴向表现出很高的强度。
制备CF的主要原材料有人造丝(粘胶纤维)、聚丙烯腈(PAN)纤维和沥青等。
通常制备高强度、高模量CF多选用PAN为原料。
制备CF需经过拉丝、牵伸、稳定、炭化、石墨化5个阶段。
1.2 EP基体的作用EP具有优良的加工性能和力学性能,其固化收缩率低,粘结性能优异。
复合材料中EP的主要作用是把CF粘在一起,分配CF间的载荷,保护CF不受环境影响。
1.3 EP/CF复合材料的特性EP/CF复合材料的特性主要取决于CF、EP及EP与CF之间的粘结特性。
EP/CF复合材料具有优异的性能,与钢相比,EP/CF复合材料的比强度为钢的4.8-7.2倍,比模量为钢的3.1-4.2倍,疲劳强度约为钢的2.5倍、铝的3.3倍,而且高温性能好,工作温度达400℃时其强度与模量基本保持不变。
此外还具有密度和线膨胀系数小、耐腐蚀、抗蠕变、整体性好、抗分层、抗冲击等,在现有结构材料中,其比强度、比模量综合指标最高。
低压结构发泡注塑成型技术
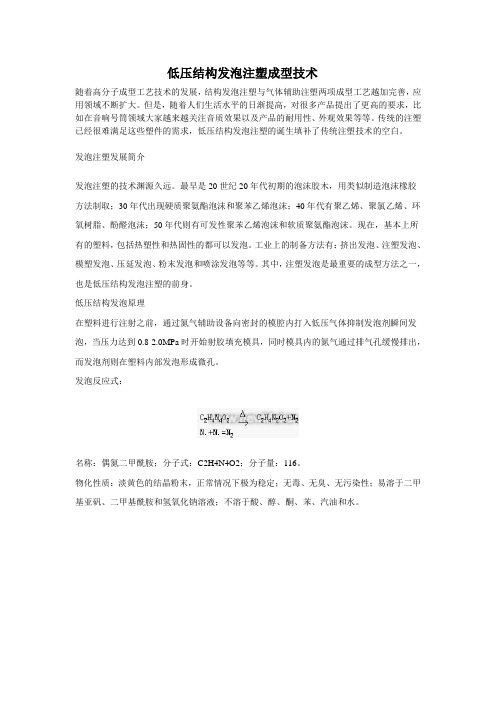
低压结构发泡注塑成型技术随着高分子成型工艺技术的发展,结构发泡注塑与气体辅助注塑两项成型工艺越加完善,应用领域不断扩大。
但是,随着人们生活水平的日渐提高,对很多产品提出了更高的要求,比如在音响号筒领域大家越来越关注音质效果以及产品的耐用性、外观效果等等。
传统的注塑已经很难满足这些塑件的需求,低压结构发泡注塑的诞生填补了传统注塑技术的空白。
发泡注塑发展简介发泡注塑的技术渊源久远。
最早是20世纪20年代初期的泡沫胶木,用类似制造泡沫橡胶方法制取;30年代出现硬质聚氨酯泡沫和聚苯乙烯泡沫;40年代有聚乙烯、聚氯乙烯、环氧树脂、酚醛泡沫;50年代则有可发性聚苯乙烯泡沫和软质聚氨酯泡沫。
现在,基本上所有的塑料,包括热塑性和热固性的都可以发泡。
工业上的制备方法有:挤出发泡、注塑发泡、模塑发泡、压延发泡、粉末发泡和喷涂发泡等等。
其中,注塑发泡是最重要的成型方法之一,也是低压结构发泡注塑的前身。
低压结构发泡原理在塑料进行注射之前,通过氮气辅助设备向密封的模腔内打入低压气体抑制发泡剂瞬间发泡,当压力达到0.8-2.0MPa时开始射胶填充模具,同时模具内的氮气通过排气孔缓慢排出,而发泡剂则在塑料内部发泡形成微孔。
发泡反应式:名称:偶氮二甲酰胺;分子式:C2H4N4O2;分子量:116。
物化性质:淡黄色的结晶粉末,正常情况下极为稳定;无毒、无臭、无污染性;易溶于二甲基亚矾、二甲基酰胺和氢氧化钠溶液;不溶于酸、醇、酮、苯、汽油和水。
发泡剂物性表结构发泡的特点结构发泡(Structural Foam Molding)属于化学发泡法,保留了传统注射成型工艺的许多优点,又避免了后者的部分缺陷,如制品强度不够、生产周期太长、模塑率低等。
采用结构发泡技术可以模塑大型复杂制品、使用低成本模具、多模腔可同时操作,从而降低制品生产成本。
结构发泡制品是一种具有致密表层的连体发泡材料,其单位重量强度和刚度比同种未发泡的材料高3~4倍。
低压发泡注塑与普通注塑的区别在于其模具的模腔压力较低,约2~7MPa,而普通注塑在30~60MPa之间。
这六种注塑成型,你认识几种?

这六种注塑成型,你认识几种?艾邦高分子开通议论功能啦!对文章有疑问或建议都可以在页面底部发布您的建议哦,快来参加议论吧 O(∩ _∩ )O 一、压缩注塑成型压缩注塑成型:(injection compressionmolding )是传统注塑成型的一种高级形式。
长处:它能增加注塑零件的流长比;采纳更小的锁模力和注塑压力;减少资料内应力;以及提升加工生产率。
注射压缩成型合用于各种热塑性工程塑胶制作的产品,如:大尺寸的曲面零件,薄壁,微型化零件,光学镜片,以及有优异抗冲击要求的零件。
答复“注塑” ,查察更多图片为压缩注塑成型表示图:(injection compression molding)应用事例:尽人皆知,光学透镜对其几何精度要求特别高、既要尺寸正确,又要变形小,而一般注塑成型就难以达到此要求。
二、排气注塑成型排气注塑成型:“排气”程序的目的是让在聚合-凝结过程中产生的挥发挥发性裂变产物排发出发的时机。
假如这些气体没法从型腔中排放出去,结果将会造成制品不完好,或是闭合处有气泡。
次序:1.当注塑体积达到大概80%-95% 时,注塑暂停;2.把模具打开大概 0.1-0.2mm 以便挥发性气体的排出;3.二次合模,并注塑节余注塑量。
图片为排气注塑成型图应用事例:制品:压滤机滤板1500x1500 穴数: 1 出 1 原料:PP 6%(流动指数 0.2 高粘度)注塑成型机: BU4000配6800T 储料缸成型工艺:压缩注射成型压滤机滤板三、低压注塑成型低压注塑工艺是一种使用很低的注塑压力将热熔资料注入模具并迅速固化的封装工艺,以热熔资料卓越的密封性和优异的物理、化学性能来达到绝缘、耐温、抗冲击、减振、防潮、防水、防尘、耐化学腐化等功能,对电子元件起到优异的保护作用。
图为低压注塑成型的模具设计皮革,木材,纤维织物,PVC/TPO/PUR 装修膜的敏感性要求降低注塑压力。
应用事例:汽车脚踏板感觉器?图片为汽车脚踏板感觉器,下列图为元件注塑前和注塑后的状况四、气辅注塑成型:( Gas-assisted injectionmolding)GAIM 过程:注塑阶段(部分) -充气阶段( N2)-气体保压阶段(冷却气压不变) -降压阶段 - 脱模阶段 GAIM 装置构成:气体压力生成器、气体控制单元、注气装置、气体回收装置答复“气辅注塑”,查察更多图片为气辅注塑成型原理图应用事例:五、水辅注塑成型水协助注塑成型技术是将部分熔体注入模腔后,经过设施将高压水注入熔体内,最后使工件成型的一种先进注塑工艺。
内饰塑料件工艺方法介绍

内饰塑料件工艺方法介绍汽车内饰塑料件成型方法主要有以下7种:1)注射成型注射成型简称注塑,是指物料在注射机加热料筒中塑化后,由螺杆或注塞注射入闭合模具的模腔中经过冷却形成制品的成型方法。
它广泛用于热塑性塑料的成型,也用于某些热固性塑料(如酚醛塑料、氨基塑料)的成型。
注射成型的优点是能一次成型外观复杂、尺寸精确、带有金属或非金属嵌件、甚至可充以气体形成空芯结构的塑料模制品;生产效率高,自动化程度高。
新型注射方法的出现更加巩固了其在汽车塑料加工中的地位。
各种车上的硬质仪表板一般采用PP、PC、ABS、ABS/PC等一次性注射成型。
就注射技术而言,已经开发了适应性很广的很多新技术。
如采用微型注射成型自动化生产毫克级的高尺寸精度制品,如汽车传感器等自动控制和电子控制部件。
注射成型细分,还可以分成以下几类。
(1)气体辅助注射成型。
气体辅助注射成型技术是一项新兴的塑料注射成型技术,其原理是利用高压气体在塑件内部产生中空截面,利用气体保压代替塑料注射保压,消除制品缩痕完成注射成型过程。
传统注射工艺不能将厚壁和薄壁结合在一起成型,且制件残余应力大,易翘曲变形,表面有缩痕。
新发展的气辅技术通过把厚壁的内部掏空,成功地生产出厚壁不均制品,而且制品外观表面性质优异,内应力低,轻质高强。
该工艺已用于成型汽车的前后挡板、门把手、保险杠等。
(2)水辅注射成型。
同气辅注射成型类似,水辅助注射成型先将一段熔体注入模腔,随后将水注入,通过挤破使工件成型,填充过程结束后,水可以继续提供保压压力,预防翘曲,水辅助注射成型可以直接冷却制品的内部,更适合较厚和较长的制品成型,能生产出均匀的薄壁制品,零件内表面平滑。
可以在更短的成型周期下,减少制品壁厚及减少残留的壁厚,对于大件且较薄的制品可使用较均匀而且较低的压力即可成型,从而节省了材料,拓展了应用范围循环使用水而可降低生产成本,适合成型管状的零件、汽车油管和其他流体系统、把手、行李架、汽车上的仪表板、缓冲器、门把手、离合器以及驾驶杆支持架等。
lfi工艺流程

lfi工艺流程
LFI工艺流程,即低压注射成型技术,是一种用于生产大型复杂结构的工艺方法。
该工艺流程可以生产高质量的产品,并且具有很高的生产
效率和经济效益。
LFI工艺流程主要包括以下四个步骤:
1. 准备材料:LFI工艺流程使用的材料一般是树脂和玻璃纤维。
树脂通常是双组份反应树脂,需要在一定比例下混合。
玻璃纤维是预先裁剪
成具有特定形状和长度的小块。
2. 混合材料:树脂和玻璃纤维混合后,需要进行搅拌和充分混合,以
确保材料能够均匀地涂在模具表面。
3. 喷涂模具:混合好的材料会通过喷枪喷涂在模具的内部表面上,一
边喷涂一边旋转模具,以确保材料覆盖整个模具表面。
4. 固化成型:喷涂完成后,模具会进行加热,以使树脂反应形成固体。
完成后的成型件会从模具上取下。
LFI工艺流程具有以下优点:
1. 生产速度快:LFI工艺流程是一种高效的生产方法。
可以生产多种结构的产品,并且可以在短时间内完成生产。
2. 生产成本低:LFI工艺流程使用的材料成本较低,可以大量生产大型产品,从而降低了生产成本。
3. 质量稳定:LFI工艺流程可以生产出表面质量高、精度高、尺寸稳定的产品。
4. 适用范围广:LFI工艺流程可以生产多种尺寸和形状的产品,可以适用于各种应用领域。
总之,LFI工艺流程是一种高效、经济、稳定的生产方法。
它可以用于生产各种大型复杂结构的产品。
在未来的发展中,LFI工艺流程将会得到进一步的改进和完善。
复合材料成型工艺接触低压成型工艺
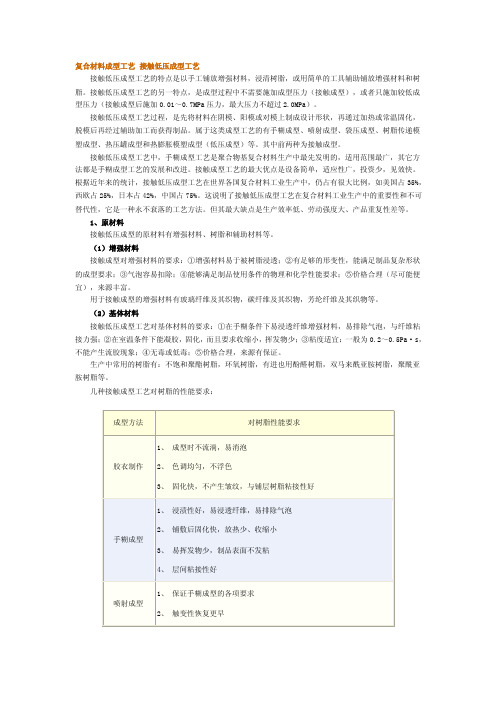
复合材料成型工艺接触低压成型工艺接触低压成型工艺的特点是以手工铺放增强材料,浸清树脂,或用简单的工具辅助铺放增强材料和树脂。
接触低压成型工艺的另一特点,是成型过程中不需要施加成型压力(接触成型),或者只施加较低成型压力(接触成型后施加0.01~0.7MPa压力,最大压力不超过2.0MPa)。
接触低压成型工艺过程,是先将材料在阴模、阳模或对模上制成设计形状,再通过加热或常温固化,脱模后再经过辅助加工而获得制品。
属于这类成型工艺的有手糊成型、喷射成型、袋压成型、树脂传递模塑成型、热压罐成型和热膨胀模塑成型(低压成型)等。
其中前两种为接触成型。
接触低压成型工艺中,手糊成型工艺是聚合物基复合材料生产中最先发明的,适用范围最广,其它方法都是手糊成型工艺的发展和改进。
接触成型工艺的最大优点是设备简单,适应性广,投资少,见效快。
根据近年来的统计,接触低压成型工艺在世界各国复合材料工业生产中,仍占有很大比例,如美国占35%,西欧占25%,日本占42%,中国占75%。
这说明了接触低压成型工艺在复合材料工业生产中的重要性和不可替代性,它是一种永不衰落的工艺方法。
但其最大缺点是生产效率低、劳动强度大、产品重复性差等。
1、原材料接触低压成型的原材料有增强材料、树脂和辅助材料等。
(1)增强材料接触成型对增强材料的要求:①增强材料易于被树脂浸透;②有足够的形变性,能满足制品复杂形状的成型要求;③气泡容易扣除;④能够满足制品使用条件的物理和化学性能要求;⑤价格合理(尽可能便宜),来源丰富。
用于接触成型的增强材料有玻璃纤维及其织物,碳纤维及其织物,芳纶纤维及其织物等。
(2)基体材料接触低压成型工艺对基体材料的要求:①在手糊条件下易浸透纤维增强材料,易排除气泡,与纤维粘接力强;②在室温条件下能凝胶,固化,而且要求收缩小,挥发物少;③粘度适宜:一般为0.2~0.5Pa·s,不能产生流胶现象;④无毒或低毒;⑤价格合理,来源有保证。
低压注塑成型工艺

24
二、低压注塑工艺应用案例
电子行业的连接器或传感器
Copyright © 2012 SINBON Electronics Co., Ltd. All rights reserved.
25
二、低压注塑工艺应用案例
电子行业线圈
Copyright © 2012 SINBON Electronics Co., Ltd. All rights reserved.
d.高低温稳定性:耐热循环、耐低温、耐高温(-40°C
~150°C);不含任何有毒物质,符合殴监RoHS指令;可回
收利用。
成型性能:
a.灵活和小型化的产品设计;
b.有 效的应力缓冲。
Copyright © 2012 SINBON Electronics Co., Ltd. All rights reserved.
员传感器、安全带锁传感器、机动车用ECU/空气质量传感 器、RF装置用天线、智能钥匙系统等。 b.可用于手机电池、天线、闪光灯以及其他需要防水、保护 或封装的易损零配件。 c.可用于PCB封装 d.扣环和线束 e.以及其他行业连接器/传感器的防水等
Copyright © 2012 SINBON Electronics Co., Ltd. All rights reserved.
27
Copyright © 2012 SINBON Electronics Co., Ltd. All rights reserved.
28
放映结束 感谢各位的批评指导!
谢 谢!
让我们共同进步
Copyright © 2012 SINBON Electronics Co., Ltd. All rights reserved.
低压成型工艺
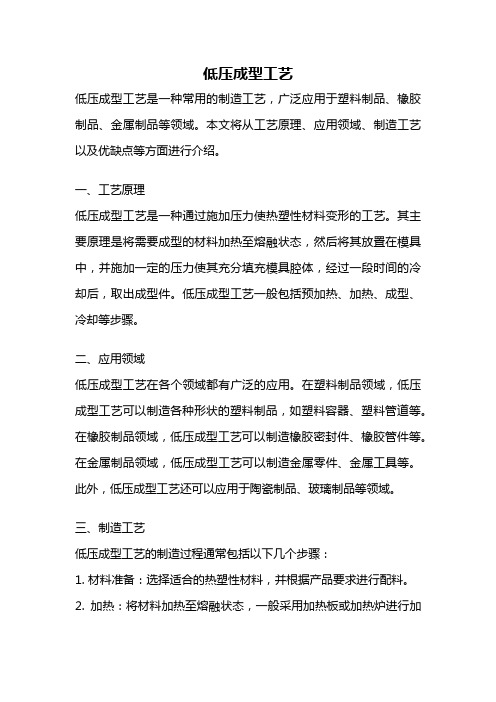
低压成型工艺低压成型工艺是一种常用的制造工艺,广泛应用于塑料制品、橡胶制品、金属制品等领域。
本文将从工艺原理、应用领域、制造工艺以及优缺点等方面进行介绍。
一、工艺原理低压成型工艺是一种通过施加压力使热塑性材料变形的工艺。
其主要原理是将需要成型的材料加热至熔融状态,然后将其放置在模具中,并施加一定的压力使其充分填充模具腔体,经过一段时间的冷却后,取出成型件。
低压成型工艺一般包括预加热、加热、成型、冷却等步骤。
二、应用领域低压成型工艺在各个领域都有广泛的应用。
在塑料制品领域,低压成型工艺可以制造各种形状的塑料制品,如塑料容器、塑料管道等。
在橡胶制品领域,低压成型工艺可以制造橡胶密封件、橡胶管件等。
在金属制品领域,低压成型工艺可以制造金属零件、金属工具等。
此外,低压成型工艺还可以应用于陶瓷制品、玻璃制品等领域。
三、制造工艺低压成型工艺的制造过程通常包括以下几个步骤:1. 材料准备:选择适合的热塑性材料,并根据产品要求进行配料。
2. 加热:将材料加热至熔融状态,一般采用加热板或加热炉进行加热。
3. 成型:将加热好的材料放置在模具中,并施加一定的压力使其充分填充模具腔体。
4. 冷却:经过一段时间的冷却,使成型件固化。
5. 脱模:将成型件从模具中取出。
6. 检验:对成型件进行外观质量和尺寸精度等方面的检验。
7. 后处理:根据需要进行修整、打磨、组装等工艺。
四、优缺点低压成型工艺具有以下优点:1. 成型件的尺寸精度高,表面质量好,能满足高精度要求。
2. 适用于各种形状的成型件,具有较大的设计自由度。
3. 成本相对较低,生产效率较高。
4. 适用于各种类型的材料,如塑料、橡胶、金属、陶瓷等。
然而,低压成型工艺也存在一些缺点:1. 设备投资较大,占地面积较大。
2. 需要专业的操作技术和经验,对操作人员的要求较高。
3. 对模具的制造和维护要求较高,成本较大。
低压成型工艺是一种常用的制造工艺,具有广泛的应用领域。
通过对工艺原理、应用领域、制造工艺以及优缺点的介绍,相信读者对低压成型工艺有了更深入的了解。
Injection-Compression Molding

Injection-Compression Molding一、前言射出壓縮成型(Injection-Compression Molding)為一新的製程技術,近年來在學界與業界引起了相當多的研究與討論,而此一製程技術目前已廣泛應用在需高精度尺寸及考慮光學性質的光學產品如DVD、CD-ROM或光學鏡片等的製造。
本文僅簡介射出壓縮成型的製程特性與射出壓縮成型模板控制,最後並以光學鏡片在本公司研發之全電式射出成型機上之應用為案例說明射出壓縮製程相較於傳統射出成型對於光學鏡片成品品質之影響。
二、射出壓縮製程特性射出壓縮成型其操作結合了射出成型以及壓縮成型兩種成型技術,此種製程主要是在一般傳統射出成型製程中之外加入模具壓縮的製程,亦即在充填之初模具不完全閉鎖,當部份塑料注入模穴後,再利用鎖模機構閉鎖模具,由模心模壁向模穴內熔膠施加壓力以壓縮成型來完成模穴充填。
此種成型方式不但可以降低充填模穴所需之射出壓力,且由於均勻加壓使得整個成型製程可以在低壓的環境下完成而得到模穴內熔膠均勻的壓力分佈(圖一)。
比起傳統的射出成型,射出壓縮成型具有以下優點:(1)降低射出壓力。
(2)降低殘餘應力。
(3)減少分子定向。
(4)均勻保壓減少不均勻收縮。
(5)克服凹陷及翹曲。
(6)減少成品雙折射率差。
(7)緩和比容積變化。
(8)增進尺寸精度(圖一)三、射出成型模板的控制射出壓縮成型方法中活動模板的位置控制直接影響射出階段的模穴厚度、流動阻力,以及成品的殘留應力;而在壓縮段活動模板的壓力速度直接對應熔膠的保壓及流動,也因此影響成品的收縮與翹曲狀況。
活動模板的控制模式可分為二種模:其中一種為壓力控制模式,亦即模板在射出階段前以低壓力鎖模,此時模具已密合只是鎖模力極低,在射出階段時再利用射出壓力迫使模具打開,以使模穴空間加大同時降低流動阻力,當完成射出動作後再使模具移動進行壓縮動作(圖二)。
第二則為位置控制模式,模板在射出前以預先定位某一位子,並預留較大的模穴空間,此時射出動作擠入熔膠並且可以低壓方式進入模穴,待射出完成後再進行壓縮工作(圖三)。
低压注塑成型工艺

Copyright © 2012 SINBON Electronics Co., Ltd. All rights reserved.
3
一、低压注塑工艺
2、低压注塑局限性和大概成本
如果使用低压注塑成型替代传统塑胶成型的话成本不会节 省,反而会增加成本,选用低压注塑时需要根据产品的形态和 特殊性而定.(低压成型热熔胶价格未税约RMB:100/KG)
d.高低温稳定性:耐热循环、耐低温、耐高温(-40°C
~150°C);不含任何有毒物质,符合殴监RoHS指令;可回
收利用。
成型性能:
a.灵活和小型化的产品设计;
b.有 效的应力缓冲。
Copyright © 2012 SINBON Electronics Co., Ltd. All rights reserved.
PVC--------80~120kgf/cm2
ABS/PC---700~1200kgf/cm2
ABS/PC---100~150kgf/cm2
Copyright © 2012 SINBON Electronics Co., Ltd. All rights reserved.
5
一、低压注塑工艺
4、低压注塑工艺的温度与压力对照
Copyright © 2012 SINBON Electronics Co., Ltd. All rights reserved.
6
一、低压注塑工艺
5、提高生产力 无化学反应:采用单组分材料 过程简易、清洁 周期短(仅几到几十秒)
传统灌封胶是AB组合式的树脂类,成本普遍偏高,而且灌封胶工 艺周期会很长,从灌封到表面固化一般都要4小时以上,完全固 化最少需要24小时以上.而用低压注塑加工时间很短,一般在 几秒到几十秒左右.
低压灌注
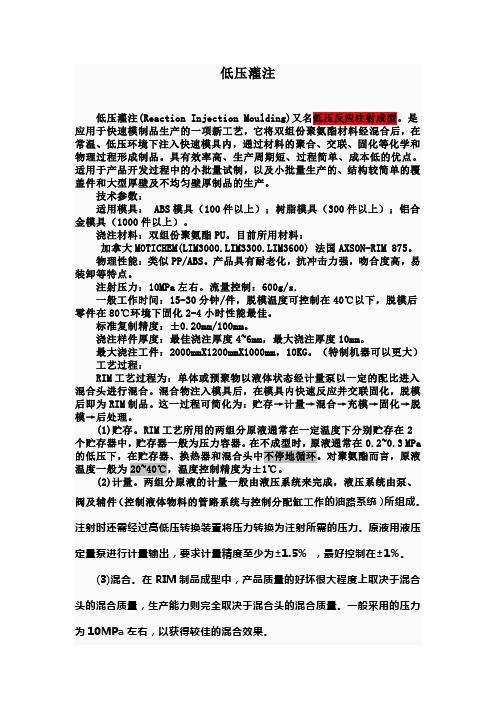
低压灌注低压灌注(Reaction Injection Moulding)又名低压反应注射成型。
是应用于快速模制品生产的一项新工艺,它将双组份聚氨酯材料经混合后,在常温、低压环境下注入快速模具内,通过材料的聚合、交联、固化等化学和物理过程形成制品。
具有效率高、生产周期短、过程简单、成本低的优点。
适用于产品开发过程中的小批量试制,以及小批量生产的、结构较简单的覆盖件和大型厚壁及不均匀壁厚制品的生产。
技术参数:适用模具: ABS模具(100件以上);树脂模具(300件以上);铝合金模具(1000件以上)。
浇注材料:双组份聚氨酯PU。
目前所用材料:加拿大MOTICHEM(LIM3000.LIM3300.LIM3600) 法国AXSON-RIM 875。
物理性能:类似PP/ABS。
产品具有耐老化,抗冲击力强,吻合度高,易装卸等特点。
注射压力:10MPa左右。
流量控制:600g/s.一般工作时间:15-30分钟/件,脱模温度可控制在40℃以下,脱模后零件在80℃环境下固化2-4小时性能最佳。
标准复制精度:±0.20mm/100mm。
浇注样件厚度:最佳浇注厚度4~6mm,最大浇注厚度10mm。
最大浇注工件:2000mmX1200mmX1000mm,10KG。
(特制机器可以更大)工艺过程:RIM工艺过程为:单体或预聚物以液体状态经计量泵以一定的配比进入混合头进行混合。
混合物注入模具后,在模具内快速反应并交联固化,脱模后即为RIM制品。
这一过程可简化为:贮存→计量→混合→充模→固化→脱模→后处理。
(1)贮存。
RIM工艺所用的两组分原液通常在一定温度下分别贮存在2个贮存器中,贮存器一般为压力容器。
在不成型时,原液通常在0.2~0.3 MPa 的低压下,在贮存器、换热器和混合头中不停地循环。
对聚氨酯而言,原液温度一般为20~40℃,温度控制精度为±1℃。
(2)计量。
两组分原液的计量一般由液压系统来完成,液压系统由泵、阀及辅件(控制液体物料的管路系统与控制分配缸工作的油路系统)所组成。
成型工艺

模压成型工艺缺点
模具设计制造复杂,压机及模具投资高,制品尺寸受设备
限制,一般只适合制造批量大的中、小型制品。
9
模压成型工艺的分类
(按增强材料物态和模压料品种分类)
(1)短纤维料模压法 (2)毡料模压法 (3)碎布料模压法
(4)层压模压法
(5)缠绕模压法 (6)织物模压法
(7)定向铺设模压法
按工艺分为两种:加压袋法、 真空袋法。 低压成型工艺 。 与手糊成型工艺的区别仅在于 加压固化工序。
32
一、加压袋法,是将经手糊或喷射成型后未固化的复合材料,放上一个橡皮
袋,固定好上盖板,如图所示,然后通入压缩空气或蒸汽(0.4~ 0.5MPa) ,使复合材料表面承受一定压力,同时受热固化而得制品。
连续纤维缠绕技术的缺点
不能缠绕任意结构形式的制品,特别是表面有凹部和形状不规则的制品; 缠绕成本高,只有在大批量生产时,才能获得较高的经济效益。
设备投资费用大,只有大批量生产时才可能降低成本。
22
6. 拉挤成型工艺
拉挤成型工艺中,首先将浸渍过树脂胶液的连续纤维束或带状织物 在牵引装置作用下通过成型模而定型; 其次,在模中或固化炉中固化,制成具有特定横截面形状和长度不受限制 的复合材料,如管材、棒材、槽型材、工字型材、方型材等。 一般情况下,只将预制品在成型模中加热到预固化的程度,最后固化是 在加热箱中完成的。
最常用的树脂是在室温或稍高温度下即可固化的不饱和聚酯等。 喷射法使用的模具与手糊法类似,而生产效率可提高数倍,劳动 强度降低,能够制作大尺寸制品。
18
5. 连续缠绕成型工艺
将浸过树脂胶液的连续纤维或布带,按照一定规律缠绕到芯模上,然
后固化脱模成为增强塑料制品的工艺过程,称为缠绕工艺。
【工艺】低压注塑工艺介绍
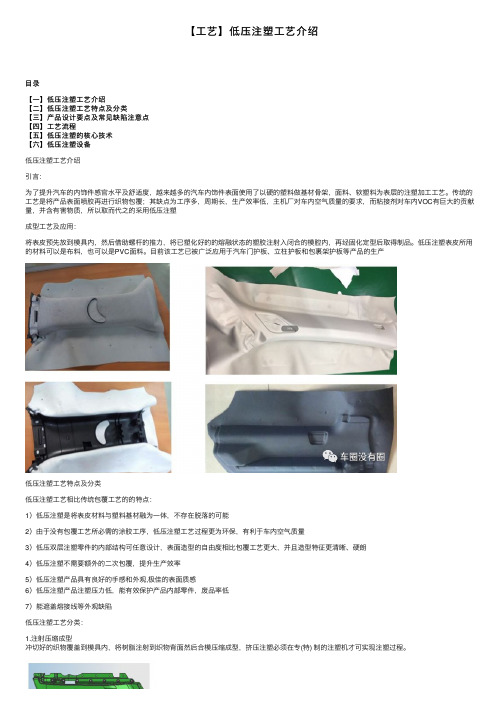
【⼯艺】低压注塑⼯艺介绍⽬录【⼀】低压注塑⼯艺介绍【⼆】低压注塑⼯艺特点及分类【三】产品设计要点及常见缺陷注意点【四】⼯艺流程【五】低压注塑的核⼼技术【六】低压注塑设备低压注塑⼯艺介绍引⾔:为了提升汽车的内饰件感官⽔平及舒适度,越来越多的汽车内饰件表⾯使⽤了以硬的塑料做基材⾻架,⾯料、软塑料为表层的注塑加⼯⼯艺。
传统的⼯艺是将产品表⾯喷胶再进⾏织物包覆;其缺点为⼯序多,周期长,⽣产效率低,主机⼚对车内空⽓质量的要求,⽽粘接剂对车内VOC有巨⼤的贡献量,并含有害物质,所以取⽽代之的采⽤低压注塑成型⼯艺及应⽤:将表⽪预先放到模具内,然后借助螺杆的推⼒,将已塑化好的的熔融状态的塑胶注射⼊闭合的模腔内,再经固化定型后取得制品。
低压注塑表⽪所⽤的材料可以是布料,也可以是PVC⾯料。
⽬前该⼯艺已被⼴泛应⽤于汽车门护板、⽴柱护板和包裹架护板等产品的⽣产低压注塑⼯艺特点及分类低压注塑⼯艺相⽐传统包覆⼯艺的的特点:1)低压注塑是将表⽪材料与塑料基材融为⼀体,不存在脱落的可能2)由于没有包覆⼯艺所必需的涂胶⼯序,低压注塑⼯艺过程更为环保,有利于车内空⽓质量3)低压双层注塑零件的内部结构可任意设计,表⾯造型的⾃由度相⽐包覆⼯艺更⼤,并且造型特征更清晰、硬朗4)低压注塑不需要额外的⼆次包覆,提升⽣产效率5)低压注塑产品具有良好的⼿感和外观,极佳的表⾯质感6)低压注塑产品注塑压⼒低,能有效保护产品内部零件,废品率低7)能遮盖熔接线等外观缺陷低压注塑⼯艺分类:1.注射压缩成型冲切好的织物覆盖到模具内,将树脂注射到织物背⾯然后合模压缩成型,挤压注塑必须在专(特) 制的注塑机才可实现注塑过程。
2.注射注塑成型冲切好的织物覆盖到模具内,然后合模直接注射成型,注射注塑则在⼀般的注塑机上就可实现。
注射压缩成型⼯艺特点:专(特)制低压注塑设备⼯作原理是在注射灌嘴对⾯挂上包覆物,前后模合模时预留若⼲距离(间隙),注塑灌嘴射出预定克重的注塑料,然后合模加压锁紧,继续射胶保压直到成型。
低压注塑成型工艺的特点
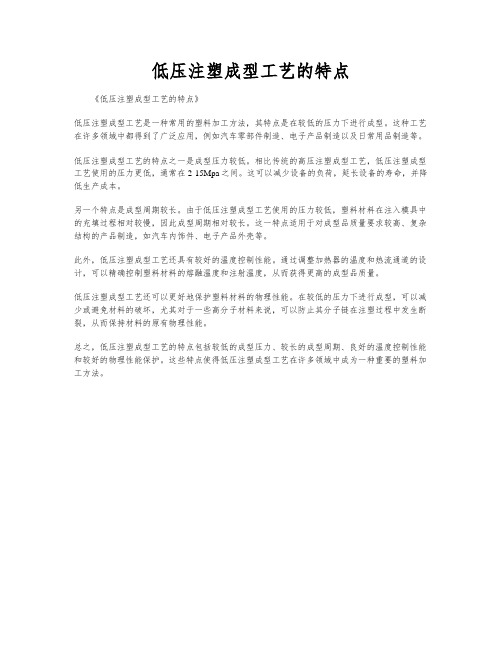
低压注塑成型工艺的特点
《低压注塑成型工艺的特点》
低压注塑成型工艺是一种常用的塑料加工方法,其特点是在较低的压力下进行成型。
这种工艺在许多领域中都得到了广泛应用,例如汽车零部件制造、电子产品制造以及日常用品制造等。
低压注塑成型工艺的特点之一是成型压力较低。
相比传统的高压注塑成型工艺,低压注塑成型工艺使用的压力更低,通常在2-15Mpa之间。
这可以减少设备的负荷,延长设备的寿命,并降低生产成本。
另一个特点是成型周期较长。
由于低压注塑成型工艺使用的压力较低,塑料材料在注入模具中的充填过程相对较慢,因此成型周期相对较长。
这一特点适用于对成型品质量要求较高、复杂结构的产品制造,如汽车内饰件、电子产品外壳等。
此外,低压注塑成型工艺还具有较好的温度控制性能。
通过调整加热器的温度和热流通道的设计,可以精确控制塑料材料的熔融温度和注射温度,从而获得更高的成型品质量。
低压注塑成型工艺还可以更好地保护塑料材料的物理性能。
在较低的压力下进行成型,可以减少或避免材料的破坏,尤其对于一些高分子材料来说,可以防止其分子链在注塑过程中发生断裂,从而保持材料的原有物理性能。
总之,低压注塑成型工艺的特点包括较低的成型压力、较长的成型周期、良好的温度控制性能和较好的物理性能保护。
这些特点使得低压注塑成型工艺在许多领域中成为一种重要的塑料加工方法。