齿轮箱齿轮啮合吃色分析
齿轮箱检查的步骤与注意事项
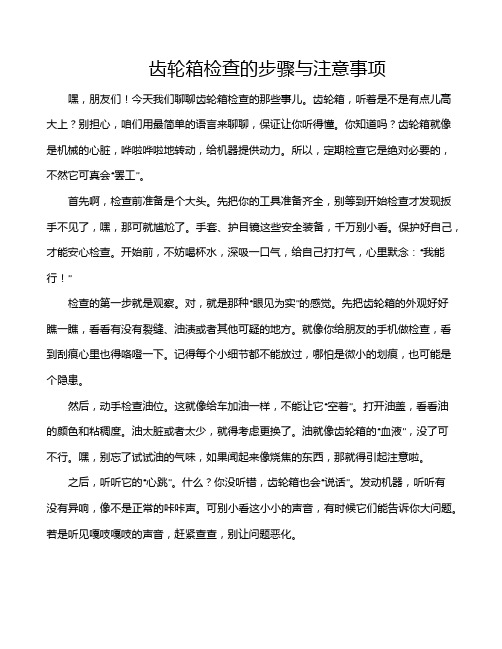
齿轮箱检查的步骤与注意事项嘿,朋友们!今天我们聊聊齿轮箱检查的那些事儿。
齿轮箱,听着是不是有点儿高大上?别担心,咱们用最简单的语言来聊聊,保证让你听得懂。
你知道吗?齿轮箱就像是机械的心脏,哗啦哗啦地转动,给机器提供动力。
所以,定期检查它是绝对必要的,不然它可真会“罢工”。
首先啊,检查前准备是个大头。
先把你的工具准备齐全,别等到开始检查才发现扳手不见了,嘿,那可就尴尬了。
手套、护目镜这些安全装备,千万别小看。
保护好自己,才能安心检查。
开始前,不妨喝杯水,深吸一口气,给自己打打气,心里默念:“我能行!”检查的第一步就是观察。
对,就是那种“眼见为实”的感觉。
先把齿轮箱的外观好好瞧一瞧,看看有没有裂缝、油渍或者其他可疑的地方。
就像你给朋友的手机做检查,看到刮痕心里也得咯噔一下。
记得每个小细节都不能放过,哪怕是微小的划痕,也可能是个隐患。
然后,动手检查油位。
这就像给车加油一样,不能让它“空着”。
打开油盖,看看油的颜色和粘稠度。
油太脏或者太少,就得考虑更换了。
油就像齿轮箱的“血液”,没了可不行。
嘿,别忘了试试油的气味,如果闻起来像烧焦的东西,那就得引起注意啦。
之后,听听它的“心跳”。
什么?你没听错,齿轮箱也会“说话”。
发动机器,听听有没有异响,像不是正常的咔咔声。
可别小看这小小的声音,有时候它们能告诉你大问题。
若是听见嘎吱嘎吱的声音,赶紧查查,别让问题恶化。
别忘了检查齿轮的啮合情况。
你知道齿轮就像朋友间的配合,啮合得好,一切顺利,啮合得不好,麻烦事儿一箩筐。
看看有没有磨损、松动,仔细检查每个齿轮的状况,感觉一下它们是不是“亲密无间”。
当然了,清洁工作也很重要。
给齿轮箱洗个澡,让它“焕然一新”。
用软刷子把污垢刷掉,别用力过猛,保护好每一个零件。
齿轮箱可不是“硬汉”,小心翼翼地对待,才能保持它的“年轻”。
别忘了检查所有的密封圈。
这些小玩意儿可真重要,能防止油漏。
就像生活中的朋友一样,密封圈要“紧紧相拥”,才能更好地工作。
四种齿轮的正确啮合条件
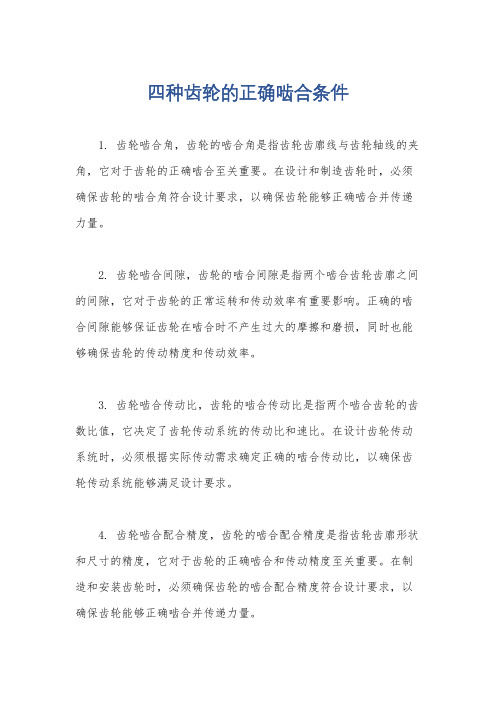
四种齿轮的正确啮合条件
1. 齿轮啮合角,齿轮的啮合角是指齿轮齿廓线与齿轮轴线的夹角,它对于齿轮的正确啮合至关重要。
在设计和制造齿轮时,必须确保齿轮的啮合角符合设计要求,以确保齿轮能够正确啮合并传递力量。
2. 齿轮啮合间隙,齿轮的啮合间隙是指两个啮合齿轮齿廓之间的间隙,它对于齿轮的正常运转和传动效率有重要影响。
正确的啮合间隙能够保证齿轮在啮合时不产生过大的摩擦和磨损,同时也能够确保齿轮的传动精度和传动效率。
3. 齿轮啮合传动比,齿轮的啮合传动比是指两个啮合齿轮的齿数比值,它决定了齿轮传动系统的传动比和速比。
在设计齿轮传动系统时,必须根据实际传动需求确定正确的啮合传动比,以确保齿轮传动系统能够满足设计要求。
4. 齿轮啮合配合精度,齿轮的啮合配合精度是指齿轮齿廓形状和尺寸的精度,它对于齿轮的正确啮合和传动精度至关重要。
在制造和安装齿轮时,必须确保齿轮的啮合配合精度符合设计要求,以确保齿轮能够正确啮合并传递力量。
总之,齿轮的正确啮合条件涉及到啮合角、啮合间隙、啮合传动比和啮合配合精度等多个方面,只有这些条件都得到满足,齿轮传动系统才能够正常运转并发挥其传动功能。
滚齿加工齿面啃齿原因分析
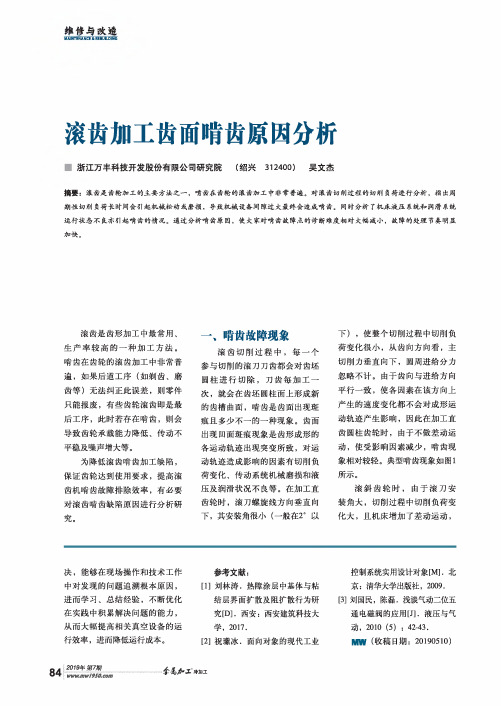
下),使整个切削过程中切削负 荷变化很小,从齿向方向看,主 切削力垂直向下,圆周进给分力 忽略不计。由于齿向与进给方向 平行一致,使各因素在该方向上 产生的速度变化都不会对成形运 动轨迹产生影响,因此在加工直 齿圆柱齿轮时,由于不做差动运 动,使受影响因素减少,啃齿现 象相对较轻。典型啃齿现象如图1 所示。
重。 (2)滚刀垂直导轨间隙过
大产生啃齿。刀架滑板沿立柱导 轨频繁的进给和快速返回,经 久使用,使滑动面磨损产生间 隙。滚齿切削过程中,刀刃成 排轮流从切入到切出,切削力 由小逐渐变大,再逐渐变小, 在工件和刀具之间产生周期性的 激振力,长时间运行该激振力会 使镶条松动,间隙增大。当进行 顺铳时,切削合力R的水平分力 P始终将工件与滚刀互相推开, 使刀架滑板和立柱导轨保持紧密 吻合,在滚刀加工时比较均匀平 稳,不致出现振动,但当接近终 端时,切入齿才开始脱离切削, 切削力减少,滑板与导轨逐渐 脱离吻合,刀架因自身质量而开 始倾斜低头,啃齿开始,当切削 完全停止时,滚刀低头至极限, 此时滚刀后半圆仍部分与工件进 行着空啮合,所以啃齿达到最 大,属末端啃齿。
一、啃齿故障现象
滚齿切削过程中,每一个 参与切削的滚刀刀齿都会对齿坯 圆柱进行切除,刀齿每加工一 次,就会在齿坯圆柱面上形成新 的齿槽曲面,啃齿是齿面出现斑 痕且多少不一的一种现象。齿面 出现凹面斑痕现象是齿形成形的 各运动轨迹出现突变所致,对运 动轨迹造成影响的因素有切削负 荷变化、传动系统机械磨损和液 压及润滑状况不良等。在加工直 齿轮时,滚刀螺旋线方向垂直向 下,其安装角很小(一般在2°以
84 竺煦第7顎 www.mwl950. com
余爲於》工®冷加工
维修与改罐
(a)末端啃齿
(b)对角啃齿
(c)中部啃齿
DF_4B_型机车齿轮箱故障原因分析及解决措施

DF 4B 型机车齿轮箱故障原因分析及解决措施陈立民,宋 勇(长春机务段,吉林长春130051) 中图分类号:U262.5 文献标识码:B 文章编号:100321820(2006)022******* 收修回稿日期:2005206214作者简介:陈立民(1973—),男,吉林长春人,工程师。
1 前言 机车齿轮箱是保证牵引电机小齿轮与动轮大齿轮啮合润滑的关键部件,齿轮箱故障一直是DF 4B 型机车走行部的惯性故障,其主要表现就是裂损和甩油。
该故障不但会造成齿轮箱油脂大量浪费,走行部不洁,加大乘务员工作量,而且会造成油脂不足,大齿轮的轮齿过热、打齿。
如我段7174号机车齿轮箱裂纹,齿轮箱内油脂全部漏出,导致大齿轮打掉5个齿,小齿轮的轮齿过烧报废。
齿轮箱甩油严重时,与车轴接磨也最严重,会造成切轴现象发生,后果不堪设想。
由于该故障的原因为存在设计缺陷,所以按工艺使用现有普通材料很难克服。
为此,我段应用了一种新技术,并基本控制了该惯性故障的发生。
2 故障原因分析 (1)由于单密封槽齿轮箱只有一道密封槽,所以密封效果差。
还由于结构不合理,壁板厚度、加强筋设置等都达不到要求,所以易裂损。
(2)齿轮箱螺栓采用标准螺栓(45号钢),紧固力矩不足,易松动。
另外,螺栓座由我段自己加工,采用A3钢,材质软且加工精度不够。
这些都导致了螺栓紧固后极易松动,部分螺栓跑一趟就松了,齿轮箱螺栓松必然使齿轮箱直接架在车轴上,导致油封口磨损加剧,尺寸加大,毡条磨平或窜出,齿轮箱油脂从油封口缝隙甩出。
部分齿轮箱个别螺栓松,导致齿轮箱晃动加剧,不松的螺栓受力增大且单独吃劲,导致螺栓座裂或壁板裂。
经过焊修处理后还是该部位受力大,周而复始大部分齿轮箱状态都不太好。
(3)车轴磨损严重,齿轮箱上的挡油环太小,起不到挡油的作用。
3 解决措施及效果 (1)采用双密封槽齿轮箱。
经过对比研究,双密封槽齿轮箱由于有两道密封槽,密封效果比单密封槽齿轮箱好。
双曲面齿轮的啮合噪声

1 双曲面齿轮的啮合噪声双曲面齿轮广泛应用于汽车主减速器,汽车主减速器的噪声主要包括齿轮的啮合噪声、轴承噪声和搅油噪声等,其中齿轮的啮合噪声是主要方面。
为减小齿轮的啮合噪声,一般可采取两种途径:第一是提高齿轮的加工精度;第二是控制齿轮的设计参数。
提高齿轮的加工精度虽然是一种非常有效的措施.但是一味追求很高的加工精度不仅在生产中有许多困难,造成成本的增加,而且潜力也不是很大。
笔者则是从控制齿轮的设计参数入手,结合现代优化设计理论和计算机技术,通过对双曲面齿轮基本设计参数的最佳选择,以达到最大程度降低双曲面齿轮啮合噪声的目的。
根据双曲面齿轮传动理论,齿轮副的啮合噪声随齿面重叠系数的增大而降低。
根据德国尼曼教授的计算公式,齿轮啮合噪声的声压级与重叠系数的4次根成反比。
一位日本学者提出了齿面重叠系数与双曲面齿轮的啮合噪声之间的定量关系,并指出当齿面重叠系数为1.95时,双曲面齿轮的啮合噪声最低。
实践也证明。
当双曲面齿轮的齿面重叠系数达到2.0时,啮合效果最好。
啮合噪声最低。
2 齿面重叠系数的计算双曲面齿轮传动的齿面重叠系数,是重叠系数沿瞬时回转轴的分量.它相当于斜齿圆柱齿轮中的轴向重叠系数.其值的大小是影响双曲面齿轮啮合噪声的主要因素。
其计算公式为:式中:K2为系数,与偏移距E有关b为主从动齿轮中点螺旋角的平均值,º;A。
为双曲面齿轮节锥节,mm;m为从动齿轮大端模数,mm。
3 优化数学模型的建立3.1确定目标函数本优化问题是以提高双曲面齿轮的传动平稳性和降低齿轮啮合噪声为设计目标的。
由于双曲面齿轮传动的齿面重叠系数=2.0时,齿轮的啮合噪声最低.因此,如果预先给定齿面重叠系数[]=2.0,则可定出目标函数如下:F=3.2确定设计变量影响齿面重叠系数的参数有主从动齿轮的中点平均螺旋角b、从动齿轮的大端端面模数m、从动齿轮齿面宽F、齿数Z1和Z2以及偏移距E。
当已知主减速器的减速比i o= Z2/Z1。
想要对齿轮箱进行振动分析,先要了解故障特征是什么?-振迪检测

想要对齿轮箱进行振动分析,先要了解故障特征是什么?—振迪检测想要对齿轮箱进行振动分析,首先要了解齿轮箱的故障特征,下面由振迪检测来为您叙述齿轮箱的故障特征。
正常状态频谱:正常状态频谱显示1X和2X转速频率和齿轮啮合频率GMF;齿轮啮合频率GMF通常伴有旋转转速频率边带;1、齿载荷的影响齿载荷的影响症状特征:齿轮啮合频率往往对载荷很敏感;高幅值的齿轮啮合频率GMF未必说明齿轮有故障;每次分析都应当在载荷下进行。
2、齿磨损齿磨损症状特征:激起自振频率同时伴有磨损齿轮的1X转速频率的边带说明齿磨损;边带是比齿轮啮合频率GMF更好的磨损指示;当齿轮的齿磨损时齿轮啮合频率的幅值可能不变。
3、齿轮偏心和侧隙游移齿轮偏心和侧隙游移症状特征:齿轮啮合频率GMF两侧较高幅值的边带说明,齿轮偏心侧隙游移和齿轮轴不平行;有故障的齿轮将调制边带;不正常的侧隙游移通常将激起齿轮自振频率振动。
全部的振动尖峰的幅值都较低,没有自振频率。
4、齿轮不对中齿轮不对中症状特征:齿轮不对中总是激起二阶或更高阶的齿轮啮合频率的谐波频率,并伴有旋转转速频率边带;齿轮啮合频率基频(1XGMF)的幅值较小,而2X和3X齿轮啮合频率的幅值较高;为了捕获至少2XGMF频率,设置充足高的分析频率Fmax很紧要。
5、断齿/裂齿断齿/裂齿症状特征:断齿或裂齿将产生该齿轮的1X转速频率的高幅值的振动;它将激起自振频率振动,并且在其两侧伴有旋转转速基频边带;利用时域波形指示断齿或裂齿故障;两个脉冲之间的时间间隔就是1X转速的倒数。
6、齿磨损摇摆的齿症状特征:摇摆的齿轮的振动是低频振动,常常疏忽它。
振迪检测可供给的振动分析服务,适用于齿轮箱、风机、鼓风机、冷却水塔等转动设备,假如您也有难以解决的设备故障问题,欢迎前来咨询,:(微信号相同)。
轧机齿轮箱日常点检要点

轧机齿轮箱日常点检要点
轧机齿轮箱日常点检时有四大步骤,第一步,检查排水孔有无漏油滴油,检查油位是否在中刻度以上,油色是否发黑浑浊,通过动态检查噪音,当发现异声时,使用听音棒听轴承运转声音,必要时打开观察孔或箱盖检查齿轮啮合和轴承情况。
第二步,检查箱体是否被异物打击,有无裂痕;第三步,检查齿轮箱是否存在金属磨损产生的发亮光泽;第四步,检查联轴节是否渗油,横向运动有无卡滞,径向有无明显运动,螺栓是否松动,有无断裂或松动缺失,进一步检查可以采用点检锤敲击的方式,检查螺栓紧固情况,针对较大规格的螺栓也要加强检查,比如采用拉拔法等检查紧固扭矩。
此外,齿轮箱运转时,禁止接触旋转部位,油池内最高温度禁止超过80摄氏度。
如果没有特殊要求,齿轮应选择着色探伤方法,剩磁感应强度应低于0.3特斯拉。
基于国产齿轮箱过程质量控制分析司建锋
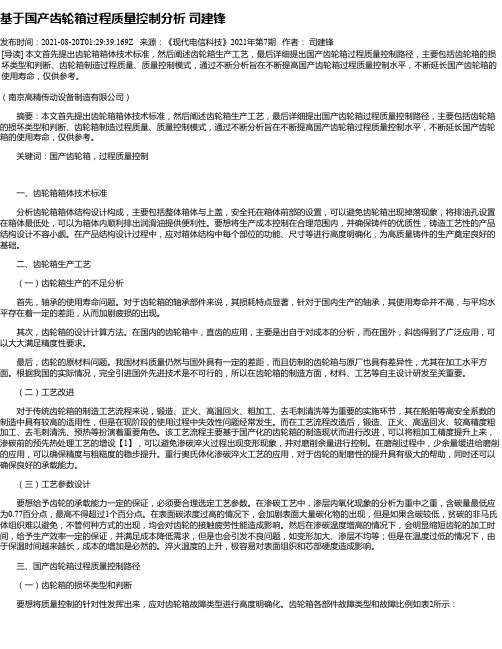
基于国产齿轮箱过程质量控制分析司建锋发布时间:2021-08-20T01:29:39.169Z 来源:《现代电信科技》2021年第7期作者:司建锋[导读] 本文首先提出齿轮箱箱体技术标准,然后阐述齿轮箱生产工艺,最后详细提出国产齿轮箱过程质量控制路径,主要包括齿轮箱的损坏类型和判断、齿轮箱制造过程质量、质量控制模式,通过不断分析旨在不断提高国产齿轮箱过程质量控制水平,不断延长国产齿轮箱的使用寿命,仅供参考。
(南京高精传动设备制造有限公司)摘要:本文首先提出齿轮箱箱体技术标准,然后阐述齿轮箱生产工艺,最后详细提出国产齿轮箱过程质量控制路径,主要包括齿轮箱的损坏类型和判断、齿轮箱制造过程质量、质量控制模式,通过不断分析旨在不断提高国产齿轮箱过程质量控制水平,不断延长国产齿轮箱的使用寿命,仅供参考。
关键词:国产齿轮箱,过程质量控制一、齿轮箱箱体技术标准分析齿轮箱箱体结构设计构成,主要包括整体箱体与上盖,安全托在箱体前部的设置,可以避免齿轮箱出现掉落现象,将排油孔设置在箱体最低处,可以为箱体内顺利排出润滑油提供便利性。
要想将生产成本控制在合理范围内,并确保铸件的优质性,铸造工艺性的产品结构设计不容小觑。
在产品结构设计过程中,应对箱体结构中每个部位的功能、尺寸等进行高度明确化,为高质量铸件的生产奠定良好的基础。
二、齿轮箱生产工艺(一)齿轮箱生产的不足分析首先,轴承的使用寿命问题。
对于齿轮箱的轴承部件来说,其损耗特点显著,针对于国内生产的轴承,其使用寿命并不高,与平均水平存在着一定的差距,从而加剧疲损的出现。
其次,齿轮箱的设计计算方法。
在国内的齿轮箱中,直齿的应用,主要是出自于对成本的分析,而在国外,斜齿得到了广泛应用,可以大大满足精度性要求。
最后,齿轮的原材料问题。
我国材料质量仍然与国外具有一定的差距,而且仿制的齿轮箱与原厂也具有差异性,尤其在加工水平方面。
根据我国的实际情况,完全引进国外先进技术是不可行的,所以在齿轮箱的制造方面,材料、工艺等自主设计研发至关重要。
论述齿轮啮合频率产生的机理及齿轮故障诊断方法
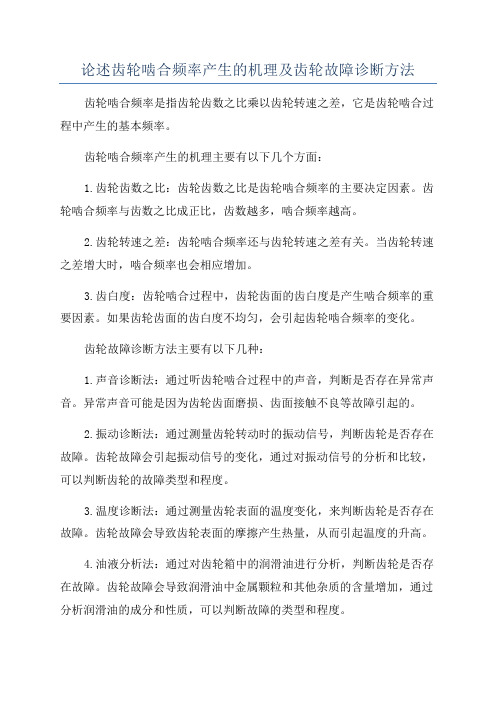
论述齿轮啮合频率产生的机理及齿轮故障诊断方法齿轮啮合频率是指齿轮齿数之比乘以齿轮转速之差,它是齿轮啮合过程中产生的基本频率。
齿轮啮合频率产生的机理主要有以下几个方面:1.齿轮齿数之比:齿轮齿数之比是齿轮啮合频率的主要决定因素。
齿轮啮合频率与齿数之比成正比,齿数越多,啮合频率越高。
2.齿轮转速之差:齿轮啮合频率还与齿轮转速之差有关。
当齿轮转速之差增大时,啮合频率也会相应增加。
3.齿白度:齿轮啮合过程中,齿轮齿面的齿白度是产生啮合频率的重要因素。
如果齿轮齿面的齿白度不均匀,会引起齿轮啮合频率的变化。
齿轮故障诊断方法主要有以下几种:1.声音诊断法:通过听齿轮啮合过程中的声音,判断是否存在异常声音。
异常声音可能是因为齿轮齿面磨损、齿面接触不良等故障引起的。
2.振动诊断法:通过测量齿轮转动时的振动信号,判断齿轮是否存在故障。
齿轮故障会引起振动信号的变化,通过对振动信号的分析和比较,可以判断齿轮的故障类型和程度。
3.温度诊断法:通过测量齿轮表面的温度变化,来判断齿轮是否存在故障。
齿轮故障会导致齿轮表面的摩擦产生热量,从而引起温度的升高。
4.油液分析法:通过对齿轮箱中的润滑油进行分析,判断齿轮是否存在故障。
齿轮故障会导致润滑油中金属颗粒和其他杂质的含量增加,通过分析润滑油的成分和性质,可以判断故障的类型和程度。
5.振弦诊断法:通过在齿轮上安装振弦传感器,采集齿轮振动信号,并通过信号分析来判断齿轮是否存在故障。
振弦传感器可以感知齿轮振动的幅值、频率等特征,通过与正常状态下的信号进行比较,可以判断故障的类型和程度。
综上所述,齿轮啮合频率是齿轮啮合过程中产生的基本频率,其机理主要与齿轮齿数之比、齿轮转速之差以及齿白度等因素有关。
针对齿轮故障的诊断方法包括声音诊断法、振动诊断法、温度诊断法、油液分析法以及振弦诊断法等。
这些方法可以通过检测齿轮的声音、振动、温度变化以及润滑油中的杂质等特征,来判断齿轮是否存在故障以及故障的类型和程度。
风电齿轮箱的工厂试验验证
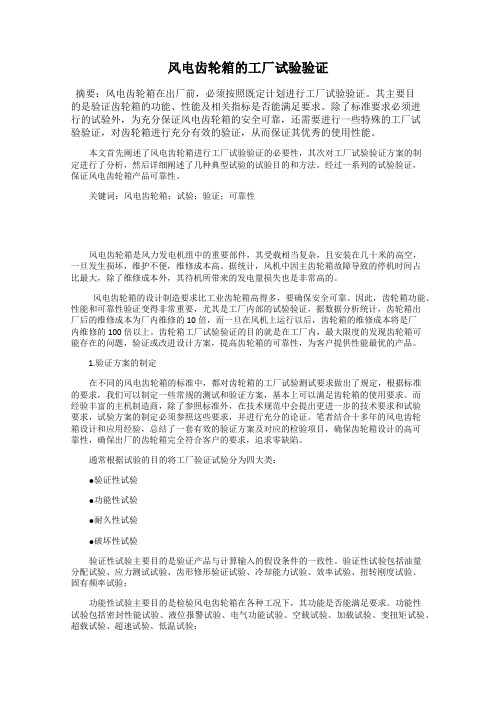
风电齿轮箱的工厂试验验证摘要:风电齿轮箱在出厂前,必须按照既定计划进行工厂试验验证。
其主要目的是验证齿轮箱的功能、性能及相关指标是否能满足要求。
除了标准要求必须进行的试验外,为充分保证风电齿轮箱的安全可靠,还需要进行一些特殊的工厂试验验证,对齿轮箱进行充分有效的验证,从而保证其优秀的使用性能。
本文首先阐述了风电齿轮箱进行工厂试验验证的必要性,其次对工厂试验验证方案的制定进行了分析,然后详细阐述了几种典型试验的试验目的和方法。
经过一系列的试验验证,保证风电齿轮箱产品可靠性。
关键词:风电齿轮箱;试验;验证;可靠性风电齿轮箱是风力发电机组中的重要部件,其受载相当复杂,且安装在几十米的高空,一旦发生损坏,维护不便,维修成本高。
据统计,风机中因主齿轮箱故障导致的停机时间占比最大,除了维修成本外,其待机所带来的发电量损失也是非常高的。
风电齿轮箱的设计制造要求比工业齿轮箱高得多,要确保安全可靠。
因此,齿轮箱功能、性能和可靠性验证变得非常重要,尤其是工厂内部的试验验证,据数据分析统计,齿轮箱出厂后的维修成本为厂内维修的10倍,而一旦在风机上运行以后,齿轮箱的维修成本将是厂内维修的100倍以上。
齿轮箱工厂试验验证的目的就是在工厂内,最大限度的发现齿轮箱可能存在的问题,验证或改进设计方案,提高齿轮箱的可靠性,为客户提供性能最优的产品。
1.验证方案的制定在不同的风电齿轮箱的标准中,都对齿轮箱的工厂试验测试要求做出了规定,根据标准的要求,我们可以制定一些常规的测试和验证方案,基本上可以满足齿轮箱的使用要求。
而经验丰富的主机制造商,除了参照标准外,在技术规范中会提出更进一步的技术要求和试验要求,试验方案的制定必须参照这些要求,并进行充分的论证。
笔者结合十多年的风电齿轮箱设计和应用经验,总结了一套有效的验证方案及对应的检验项目,确保齿轮箱设计的高可靠性,确保出厂的齿轮箱完全符合客户的要求,追求零缺陷。
通常根据试验的目的将工厂验证试验分为四大类:●验证性试验●功能性试验●耐久性试验●破坏性试验验证性试验主要目的是验证产品与计算输入的假设条件的一致性。
数控齿轮啮合实验报告(3篇)

第1篇一、实验目的1. 理解数控齿轮啮合的基本原理和过程。
2. 掌握数控齿轮啮合实验的步骤和方法。
3. 分析齿轮啮合过程中的误差来源及其影响。
4. 评估齿轮啮合质量,为齿轮加工提供参考依据。
二、实验原理齿轮啮合是指两个齿轮在运动过程中,相互接触并产生力的作用。
在数控齿轮啮合实验中,通过控制齿轮的加工参数和运动轨迹,实现齿轮的精确啮合。
实验主要涉及以下原理:1. 齿轮几何参数:包括模数、齿数、压力角、齿顶高、齿根高、齿宽等。
2. 齿轮啮合运动:包括展成运动、进给运动、分度运动等。
3. 齿轮啮合精度:包括齿形误差、齿向误差、齿距误差、齿间误差等。
三、实验仪器与设备1. 数控齿轮加工中心:用于加工齿轮毛坯。
2. 齿轮测量仪:用于测量齿轮的几何参数和啮合质量。
3. 三坐标测量机:用于测量齿轮的三维尺寸。
4. 计算机及软件:用于编程、数据处理和分析。
四、实验步骤1. 齿轮毛坯加工:根据设计要求,编程控制数控齿轮加工中心加工齿轮毛坯。
2. 齿轮测量:使用齿轮测量仪和三坐标测量机测量齿轮的几何参数,包括模数、齿数、压力角、齿顶高、齿根高、齿宽等。
3. 齿轮啮合实验:将加工好的齿轮安装到实验装置上,控制齿轮的运动,观察齿轮啮合过程中的现象。
4. 数据采集与处理:记录齿轮啮合过程中的关键数据,如齿形误差、齿向误差、齿距误差、齿间误差等。
5. 结果分析:对采集到的数据进行分析,评估齿轮啮合质量,找出误差来源及其影响。
五、实验结果与分析1. 齿形误差:齿形误差是指齿轮实际齿形与理论齿形之间的偏差。
通过实验发现,齿形误差主要来源于齿轮加工过程中的刀具磨损、加工精度和机床精度等因素。
齿形误差过大将影响齿轮的啮合性能和传动效率。
2. 齿向误差:齿向误差是指齿轮齿向与基准面之间的偏差。
齿向误差过大将导致齿轮啮合时产生轴向力,降低齿轮的承载能力和使用寿命。
3. 齿距误差:齿距误差是指齿轮相邻齿之间的齿距偏差。
齿距误差过大将导致齿轮啮合不平稳,产生振动和噪声。
齿轮箱振动信号频谱分析与故障诊断
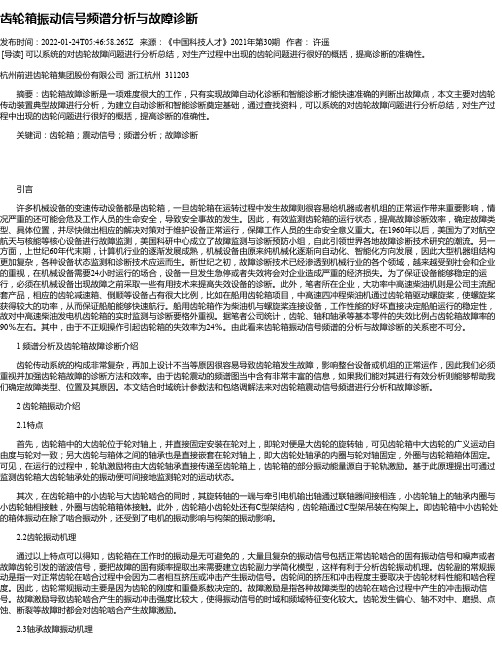
齿轮箱振动信号频谱分析与故障诊断发布时间:2022-01-24T05:46:58.265Z 来源:《中国科技人才》2021年第30期作者:许遥[导读] 可以系统的对齿轮故障问题进行分析总结,对生产过程中出现的齿轮问题进行很好的概括,提高诊断的准确性。
杭州前进齿轮箱集团股份有限公司浙江杭州 311203摘要:齿轮箱故障诊断是一项难度很大的工作,只有实现故障自动化诊断和智能诊断才能快速准确的判断出故障点,本文主要对齿轮传动装置典型故障进行分析,为建立自动诊断和智能诊断奠定基础,通过查找资料,可以系统的对齿轮故障问题进行分析总结,对生产过程中出现的齿轮问题进行很好的概括,提高诊断的准确性。
关键词:齿轮箱;震动信号;频谱分析;故障诊断引言许多机械设备的变速传动设备都是齿轮箱,一旦齿轮箱在运转过程中发生故障则很容易给机器或者机组的正常运作带来重要影响,情况严重的还可能会危及工作人员的生命安全,导致安全事故的发生。
因此,有效监测齿轮箱的运行状态,提高故障诊断效率,确定故障类型、具体位置,并尽快做出相应的解决对策对于维护设备正常运行,保障工作人员的生命安全意义重大。
在1960年以后,美国为了对航空航天与核能等核心设备进行故障监测,美国科研中心成立了故障监测与诊断预防小组,自此引领世界各地故障诊断技术研究的潮流。
另一方面,上世纪60年代末期,计算机行业的逐渐发展成熟,机械设备由原来纯机械化逐渐向自动化、智能化方向发展,因此大型机器组结构更加复杂,各种设备状态监测和诊断技术应运而生。
新世纪之初,故障诊断技术已经渗透到机械行业的各个领域,越来越受到社会和企业的重视,在机械设备需要24小时运行的场合,设备一旦发生急停或者失效将会对企业造成严重的经济损失。
为了保证设备能够稳定的运行,必须在机械设备出现故障之前采取一些有用技术来提高失效设备的诊断。
此外,笔者所在企业,大功率中高速柴油机则是公司主流配套产品,相应的齿轮减速箱、倒顺等设备占有很大比例,比如在船用齿轮箱项目,中高速四冲程柴油机通过齿轮箱驱动螺旋桨,使螺旋桨获得较大的功率,从而保证船舶能够快速航行。
风电齿轮箱背对背试验吃色异常分析

风电齿轮箱背对背试验吃色异常分析作者:***来源:《机电信息》2020年第21期摘要:对风力发电齿轮箱背对背试验吃色异常进行RCA分析,同时对潜在原因进行纠正,检查问题是否得到减缓甚至消除,以此判断根本原因或确定主要原因范围,并针对故障原因给出了改进建议。
关键词:风力发电;背对背试验;RCA;行星转动;吃色0 引言进入21世纪以来,风电行业进入高速发展期,全球多个国家都确立了未来风电等绿色能源在电力供应中所占的比重。
对于齿轮箱这一风机传动链中的关键部件的验证要求极高,其体现了齿轮箱能否符合风电高可靠性要求。
本课题针对风电齿轮箱试验中出现的一种异常问题进行RCA分析,得出解决方案,并最终通过试验验证了方案的有效性。
1 风电齿轮箱试验台位简介1.1 传统双馈型风机齿轮箱结构简介按照传递扭矩的大小,2 MW及以下双馈齿轮箱通常采用一级行星传动、两级平行轴传动(图1)。
1.2 试验台位简介齿轮箱验证过程中应尽量模拟真实工况设计、开发试验台并对齿轮箱进行充分验证。
本课题介绍的试验台属于四点支撑模式的背对背试验台。
两台齿轮箱低速端通过模拟主轴(刚性轴)连接,一台齿轮箱作为主试,连接发电机;另一台作为陪试,连接电动机;发电机发出的电能反馈到电动机中;一次试验验证两台齿轮箱(图2)。
2 齿轮吃色简介齿轮的吃色是齿轮箱验收的一项重要指标,直接体现为齿轮副啮合时的接触面积和位置。
位置正确、范围充分的吃色是保证齿轮箱在设计工况下达到满意使用寿命的先决条件,理想的吃色与设计及有限元模拟计算时相吻合。
常见的异常吃色有偏向一侧(即一侧啮合充分,一侧啮合不足)、齿顶或齿根吃色不充分等。
3 异常原因分析3.1 问题描述本课题主要介绍和分析行星级吃色异常问题——齿圈吃色走S,即齿圈的吃色宽度方向在一周范围内出现规律的偏移;假想把齿圈切开,并把齿圈宽度加宽后显示的吃色边界是个“S”型。
3.2 问题分析根据齿轮箱结构及试验台结构可以把整个系统分为两个部分:刚性轴两端通过收缩盘连接两台齿轮箱的行星架是第一部分;扭力臂连接齿圈以及后面平行级部分是第二部分。
齿轮箱齿轮啮合吃色分析

齿轮箱齿轮啮合吃色分析摘要:齿轮吃色是齿轮箱装配过程中的一个重要环节,它直接关系到齿轮箱的性能和寿命。
本文通过对影响齿轮吃色的因素进行分析提出一些改进的方法和建议,从而减少配磨次数,加快生产进度,提高生产效率。
关键字:吃色;齿轮箱;磨齿;装配1、齿轮啮合吃色介绍1.1 齿轮吃色介绍齿轮接触斑点一般采用涂色检查法,即所说的吃色。
所谓齿轮吃色,就是在装配过程中将齿轮一侧涂红丹,检验齿轮副在箱体内轻载下啮合所产生的接触斑点,再观察转后齿面上接触擦亮痕迹的分布位置,并在齿面展开图上计算百分比。
1.2 检查齿轮吃色的目的根据吃色的接触斑点的形状可用于评估轮齿间的载荷分布情况以及装配后的齿轮螺旋线和齿形精度。
2、影响齿轮啮合吃色因素分析2.1齿轮加工误差齿轮的加工误差会直接导致齿轮吃色出现问题,其中对齿轮吃色影响最大的是齿轮的螺旋线偏差和齿廓偏差。
螺旋线偏差会影响吃色的长度,关系到齿轮啮合时载荷的分布。
齿廓偏差会影响吃色的高度,关系到传动的平稳性、振动和噪音。
在齿轮加工过程中,齿轮端面的平面度和跳动,齿轮轴阶梯轴的同轴度以及内孔的精度会影响滚齿、磨齿时的基准精度,进而可能会导致齿轮的螺旋线偏差和齿廓偏差超差,最终影响吃色。
另外,磨齿的基准选择,工件和刀具的装夹、调整以及切削参数等都关系到最后的加工质量,因此,加工时要严格控制这些因素的精度。
2.2箱体加工误差箱体的加工误差也是影响齿轮吃色的一个重要因素,它可以分为以下两个方面。
一方面是箱体精铣平面误差,它包括箱体平面度误差和面与面之间的平行度误差。
精铣平面误差超差会导致轴安装倾斜,轴承受力不均匀,从而产生一个周期性的冲击使得齿轮啮合不平稳,影响齿轮接触斑点。
另一方面是箱体精镗孔误差,它包括孔的圆柱度、同轴度、平行度误差。
轴承孔圆柱度误差超差会导致轴与轴承座接触不够,使轴承产生跳动从而影响吃色形状;轴承孔同轴度误差超差会导致轴承孔与轴的中心线不重合,产生局部应力集中,影响吃色形状;轴承孔平行度误差超差会导致轴的中心线倾斜,使得齿轮接触偏向一端,从而影响吃色长度。
箱体变形对齿轮啮合的影响
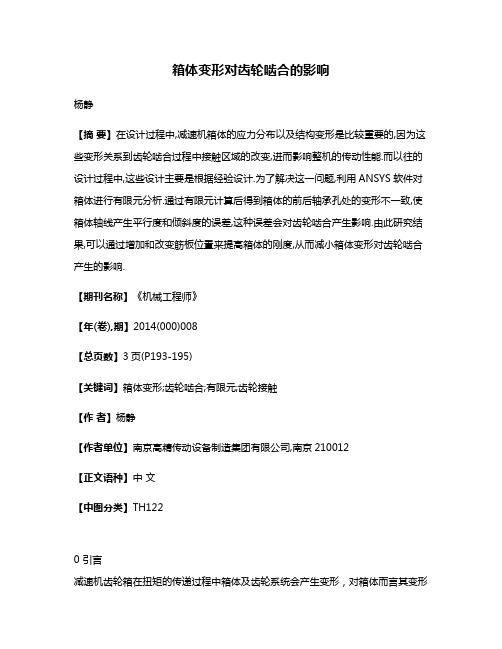
箱体变形对齿轮啮合的影响杨静【摘要】在设计过程中,减速机箱体的应力分布以及结构变形是比较重要的,因为这些变形关系到齿轮啮合过程中接触区域的改变,进而影响整机的传动性能.而以往的设计过程中,这些设计主要是根据经验设计.为了解决这一问题,利用ANSYS软件对箱体进行有限元分析.通过有限元计算后得到箱体的前后轴承孔处的变形不一致,使箱体轴线产生平行度和倾斜度的误差,这种误差会对齿轮啮合产生影响.由此研究结果,可以通过增加和改变筋板位置来提高箱体的刚度,从而减小箱体变形对齿轮啮合产生的影响.【期刊名称】《机械工程师》【年(卷),期】2014(000)008【总页数】3页(P193-195)【关键词】箱体变形;齿轮啮合;有限元;齿轮接触【作者】杨静【作者单位】南京高精传动设备制造集团有限公司,南京210012【正文语种】中文【中图分类】TH1220 引言减速机齿轮箱在扭矩的传递过程中箱体及齿轮系统会产生变形,对箱体而言其变形所带来的影响就是前后轴承孔的变形不再一致,进而轴线产生平行度和倾斜度的误差,这种误差会对齿轮的啮合产生影响。
现以本公司生产的齿轮箱为例,计算箱体变形对齿轮啮合的影响。
1 箱体变形的计算减速机的结构图如图1 所示,通过受力分析,采用专业三维造型软件Pro/E 进行三维造型,计算得到箱体的综合变形云图如图2 所示,应力云图如图3 所示。
图1 减速机结构图通过有限元计算后得到箱体的前后轴承孔处的变形不一致,这样就会产生轴线的误差,这种误差是由箱体本身受载变形后产生的,变形产生的误差最大处在第二和第三根轴系处,在有限元结果文件中取出此两轴承孔处节点变形,计算得到轴承孔处变形。
图2 箱体两侧轴承孔处变形图3 箱体综合应力云图2 无箱体变形时齿轮接触计算为了研究轴承孔处的变形对齿轮啮合的影响,这就需要有限元接触算法,通过计算有无误差的齿轮接触,比较齿轮接触应力的变化,得到误差对齿轮啮合的影响数据。
- 1、下载文档前请自行甄别文档内容的完整性,平台不提供额外的编辑、内容补充、找答案等附加服务。
- 2、"仅部分预览"的文档,不可在线预览部分如存在完整性等问题,可反馈申请退款(可完整预览的文档不适用该条件!)。
- 3、如文档侵犯您的权益,请联系客服反馈,我们会尽快为您处理(人工客服工作时间:9:00-18:30)。
齿轮箱齿轮啮合吃色分析
发表时间:2019-01-02T15:01:18.087Z 来源:《防护工程》2018年第29期作者:司建锋
[导读] 齿轮吃色是齿轮箱装配过程中的一个重要环节,它直接关系到齿轮箱的性能和寿命。
南京高精齿轮集团有限公司江苏南京 210031
摘要:齿轮吃色是齿轮箱装配过程中的一个重要环节,它直接关系到齿轮箱的性能和寿命。
本文通过对影响齿轮吃色的因素进行分析提出一些改进的方法和建议,从而减少配磨次数,加快生产进度,提高生产效率。
关键字:吃色;齿轮箱;磨齿;装配
1、齿轮啮合吃色介绍
1.1 齿轮吃色介绍
齿轮接触斑点一般采用涂色检查法,即所说的吃色。
所谓齿轮吃色,就是在装配过程中将齿轮一侧涂红丹,检验齿轮副在箱体内轻载下啮合所产生的接触斑点,再观察转后齿面上接触擦亮痕迹的分布位置,并在齿面展开图上计算百分比。
1.2 检查齿轮吃色的目的
根据吃色的接触斑点的形状可用于评估轮齿间的载荷分布情况以及装配后的齿轮螺旋线和齿形精度。
2、影响齿轮啮合吃色因素分析
2.1齿轮加工误差
齿轮的加工误差会直接导致齿轮吃色出现问题,其中对齿轮吃色影响最大的是齿轮的螺旋线偏差和齿廓偏差。
螺旋线偏差会影响吃色的长度,关系到齿轮啮合时载荷的分布。
齿廓偏差会影响吃色的高度,关系到传动的平稳性、振动和噪音。
在齿轮加工过程中,齿轮端面的平面度和跳动,齿轮轴阶梯轴的同轴度以及内孔的精度会影响滚齿、磨齿时的基准精度,进而可能会导致齿轮的螺旋线偏差和齿廓偏差超差,最终影响吃色。
另外,磨齿的基准选择,工件和刀具的装夹、调整以及切削参数等都关系到最后的加工质量,因此,加工时要严格控制这些因素的精度。
2.2箱体加工误差
箱体的加工误差也是影响齿轮吃色的一个重要因素,它可以分为以下两个方面。
一方面是箱体精铣平面误差,它包括箱体平面度误差和面与面之间的平行度误差。
精铣平面误差超差会导致轴安装倾斜,轴承受力不均匀,从而产生一个周期性的冲击使得齿轮啮合不平稳,影响齿轮接触斑点。
另一方面是箱体精镗孔误差,它包括孔的圆柱度、同轴度、平行度误差。
轴承孔圆柱度误差超差会导致轴与轴承座接触不够,使轴承产生跳动从而影响吃色形状;轴承孔同轴度误差超差会导致轴承孔与轴的中心线不重合,产生局部应力集中,影响吃色形状;轴承孔平行度误差超差会导致轴的中心线倾斜,使得齿轮接触偏向一端,从而影响吃色长度。
2.2齿轮箱装配误差
装配车间装配误差也会导致吃色不好。
例如,装配车间箱体的清洁、装夹固定、校水平,零件的自身精度及轴承的安装精度,以及吃色的判断和调整等都会影响齿轮啮合吃色。
3、提高齿轮啮合吃色质量措施
3.1加强齿轮加工质量控制,提高磨齿质量
3.1.1改善齿坯加工质量
齿坯加工,在齿轮的整个加工过程中占有重要的位置。
齿轮的孔、端面或外圆常作为齿形加工的定位、测量和装配的基准,其加工精度对整个齿轮的精度有着重要的影响。
另外,齿坯加工在齿轮加工总工时中占有较大的比例,因此齿坯加工在整个齿轮加工中占有重要的地位。
齿轮在加工、检验和装夹时的径向基准面和轴向基准面应尽量一致。
一般情况下,以齿轮孔和端面为齿形加工的基准面,所以齿坯精度中主要是对齿轮孔的尺寸精度和形状精度、孔和端面的位置精度有较高的要求;当外圆作为测量基准或定位、找正基准时,对齿坯外圆也有较高的要求。
3.1.2提高磨齿质量
磨齿,首先就是校正基准,对于齿轮轴来说,是校正两端轴颈的跳动≤0.01mm(高点应在同一方向)。
对于齿轮(备件,单独磨齿,不烘套在轴上),应该校正内孔及端面跳动≤0.01mm,这个端面为加工基准面。
基准面就是在精车和精磨时与内孔一刀下的端面。
其次,磨齿时左右两齿面要均匀磨削,以防两齿面的有效硬化层深度不一致,降低齿轮的强度,会容易形成点蚀,甚至断齿。
另外,两齿面不均匀磨削,还会产生磨削台阶。
对于变形小的齿轮,只要左右齿面进刀量相同,基本能保证两齿面均匀磨削。
对于变形量大的齿轮就要视具体情况而定了,若两齿面进刀量相同,很有可能有一个齿面磨削量很多,另一个齿面磨削量很少,甚至还有些许黑皮未磨掉,磨得多的齿齿根还会产生磨削台阶。
在这种情况下,我们就要想办法,通过架刀或单面磨削等方法加工,尽量使得两齿面能均匀磨出。
3.2提高箱体镗孔加工形位精度
箱体镗孔加工的形位精度对齿轮吃色的影响较大,对于跨度在设备能一刀加工范围内的小型箱体,首先要校正箱体中分面和端面,精度控制方面要求箱体一次装夹,一次校正,镗孔一刀加工。
轴向进刀方式:根据设备本身的精度状况,选择最优的轴向进刀方式:当工作台精度高,轴向进给可由工作台完成,这样可消除主轴垂头。
不管是哪种进给方式,其箱体校正和进给的方式要保持一致,这样尽可能的消除了机床误差。
对于跨度在设备一刀加工范围外的大型箱体,因箱体镗孔时需要调面,此时箱体发生了变动,若调面后直接镗孔,这样机床误差将被
带到箱体中,因此要保证箱体调面前后校正基准的统一。
所以在镗孔之前就先在箱体侧面光一辅助基准。
这样箱体在调面前后的基准均为中分面和侧面基准带。
校正解决后,应该找正孔中心,保证孔的位置度。
3.3严格把关装配流程,控制装配精度
3.3.1装配要求
首先零件在装配前必须清理和清洗干净,不得有毛刺、飞边、氧化皮、锈蚀、切削、油污、着色剂、防锈油和灰尘等。
装配前应对零部件的主要配合尺寸,特别是过盈配合尺寸及相关精度进行复查。
除有特殊要求外,装配前必须将零件的尖角和锐边倒钝。
装配过程中零件不允许磕碰、划伤和锈蚀。
输送介质的孔要检查是否通畅。
装配后无法再进入的部位要先涂底漆和面漆,油漆未干的零、部件不得进行装配。
机座、机身等基础件,装配时应校正水平(或垂直),其校水平的时候就是通过调整斜楔来达到要求的。
校水平的时候,需根据工艺指定的检测点进行,并且要标记出水平仪的位置,以备复检,以防齿轮吃色偏向一端。
3.3.2装配时对齿轮吃色的调整
装配吃色时需要不断地进行调整,以齿轮啮合吃色要求。
对于吃色长度不够偏一端的情况,首先要校正齿轮水平,之后再校正箱体的水平,之后重新吃色看结果,如果仍偏向一端则是齿轮齿向精度不好造成的,此时需要对齿轮齿向进行修整。
对于吃色高度不够的情况往往是齿轮加工原因,此时需要对齿轮重新磨齿。
吃色走S的情况往往都是由于箱体变形、轴承安装以及齿轮制造精度综合起来造成的,这种情况一般需要配磨。
装配车间用胶带粘下齿轮吃色后留下的接触斑点来作为配磨量的参考标准。
配磨基准通常应当为靠近轴承的两端轴颈、一端轴颈加上齿轮端面等,主要是考虑操作的方便性,便于校表。
注意最好不要用齿顶圆作基准,因为齿顶圆本身精度就不高。
齿轮吃色问题比较复杂,应尽量减少配磨次数,提高生产效率。
参考文献
[1]齿轮手册编委会. 齿轮手册第二版.北京:机械工业出版社2000.9.
[2]成大先主编. 机械设计手册第四版. 北京: 化学工业出版社2002.1.
[3]孙桓陈作模主编.机械原理第六版.高等教育出版社2000.8.
[4]洪钟德主编.简明机械设计手册.上海:同济大学出版社2002.5.
[5]黄天铭主编.机械加工工艺学.重庆:重庆大学出版社1998.6.
[6]吴昭同.齿轮加工误差与检验.《齿轮》,1984,NO6.。