WB铜线工艺
《WB焊线工艺技术资料》教案
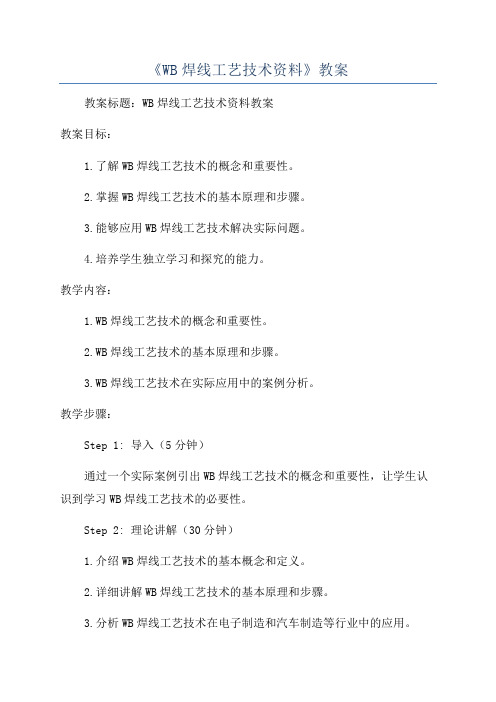
《WB焊线工艺技术资料》教案教案标题:WB焊线工艺技术资料教案教案目标:1.了解WB焊线工艺技术的概念和重要性。
2.掌握WB焊线工艺技术的基本原理和步骤。
3.能够应用WB焊线工艺技术解决实际问题。
4.培养学生独立学习和探究的能力。
教学内容:1.WB焊线工艺技术的概念和重要性。
2.WB焊线工艺技术的基本原理和步骤。
3.WB焊线工艺技术在实际应用中的案例分析。
教学步骤:Step 1: 导入(5分钟)通过一个实际案例引出WB焊线工艺技术的概念和重要性,让学生认识到学习WB焊线工艺技术的必要性。
Step 2: 理论讲解(30分钟)1.介绍WB焊线工艺技术的基本概念和定义。
2.详细讲解WB焊线工艺技术的基本原理和步骤。
3.分析WB焊线工艺技术在电子制造和汽车制造等行业中的应用。
Step 3: 案例分析(30分钟)选择几个实际的案例,让学生根据所学的WB焊线工艺技术知识进行分析和解决问题,培养学生的应用能力和解决问题的能力。
Step 4: 课堂练习(20分钟)组织学生进行课堂练习,包括选择题和应用题,帮助学生巩固所学知识,并发现问题和提出解决方法。
Step 5: 总结和评价(15分钟)对本节课学习的内容进行总结,并让学生评价自己的学习效果和对WB焊线工艺技术的理解和应用能力。
Step 6: 作业布置(5分钟)布置相关的作业,要求学生进一步巩固和应用所学的WB焊线工艺技术知识。
教学手段:1.课堂讲解:通过讲解和示范,向学生介绍WB焊线工艺技术的基本原理和步骤。
2.案例分析:通过实际案例,带领学生深入了解WB焊线工艺技术的应用和解决问题的方法。
3.课堂练习:通过练习,检查学生对所学知识的掌握程度,发现问题并及时纠正。
4.提问互动:通过提问和学生的回答,激发学生的学习兴趣,加深对知识的理解。
教学评价:1.通过课堂练习和作业布置,检查学生对WB焊线工艺技术的掌握情况。
2.参与度评价:通过观察学生的课堂表现和参与度评价他们的学习态度和积极性。
BSOB参数优化

图17 Bump植球后LGTL报警 21
铜线SSB工艺参数优化方法(技术总结)
三、小结
1、 Accu Bump与Flex Bump。Accu Bump植球模式参数设置比较简 单, Flex Bump参数设置比较复杂,但是效果好,特别是对Bump球 上打完二焊点后鱼尾离芯片表面距离太小的产品有很好的改善。 2、 Accu Bump与Flex Bump中,采用Force 模式比Position模式稳定, Position刚开始加工还可以,随着加工过程中劈刀的磨损后,就会出
一、技术方案
现有KNS WB机器SSB线弧的植球模式有两种Accu Bump与Flex
Bump。Accu Bump植球模式的示意图与劈刀(capillary)运动轨迹如 下图所示:
图2 Accu Bump模式示意图
图3 Accu Bump模式劈刀运动轨迹
4
铜线SSB工艺参数优化方法(技术方案) 工艺参数优化方法
Cap offset 为负
/ /
Fold Rtn Offset需要略大于Fold Offset
/ / / 原则上应与Fold Rtn Offset一致 ,为了2nd 更好的粘结,故设置略 高。
Cap Bond Offset 需要等 于 Fold Rtn Offset,才能 使Capillary的Face Angle 和Bump切出来的平面吻合。
Bump Force
/
Bump Lift Threshold
Bump Height Separation Height Fold Offset Fold Rtn Offset Fold Factor SSB USG SSB Force Cap Bond Offset
Face Angle
铜线键合注意

铜丝键合工艺及操作注意事项对键合铜丝产生弹坑问题的相关原理的解释键合铜丝作为微电子工业的新型材料,已经成功替代键合金丝应用于半导体器件后道封装中。
随着单晶铜材料特性的提升和封装键合工艺技术及设备的改进,铜丝在硬度,延展性等指标方面已逐渐适应了半导体的封装要求。
其应用已从低端产品向中高端多层线、小间距焊盘产品领域扩展。
因而,在今后的微电子封装发展中,铜丝焊将会成为主流技术。
采用铜丝键合工艺不但能降低半导体器件制造成本,更主要的是作为互连材料,铜的物理特性优于金。
目前,铜丝键合工艺中有两个方面应予以高度重视:一是铜丝储存及使用条件对环境要求高,特别使用过程保护措施不当易氧化;二是铜丝材料特性选择、夹具选择、设备键合参数设置不当在生产制造中易造成芯片焊盘铝挤出、破裂、弹坑、焊接不良等现象发生,最终将导致产品电性能及可靠性问题而失效。
因此,铜丝键合应注意以下工艺操作事项及要求,以确保铜丝键合的稳定及可靠性。
1、铜焊线的包装和存放:铜具有较强的亲氧性,在空气中铜丝容易氧化,所以铜丝必须存放于密封的包装盒中以减少环境空气中带来的氧化现象。
于是要求各卷铜焊线必须采用吸塑包装,并在塑料袋内单独密封。
贮藏时间一般为在室温(20~25℃)下4~6个月。
铜丝一旦打开包装放于焊线机上,铜丝暴露于空气中即可产生氧化。
原则上要求拆封的铜丝在48小时(包括焊线机上的时间)内用完为好,最长不超过72小时。
2、惰性保护气体:对于铜丝球焊来说,在成球的瞬间,放电温度极高,由于剧烈膨胀,气氛瞬时呈真空状态,但这种气氛很快和周围的大气相混合,常造成焊球变型或氧化。
氧化的焊球比那些无氧化层的焊球明显坚硬,而且不易焊接。
目前,铜丝键合新型EFO工艺增加了一套铜丝专用装置(K&S公司配置相对封闭的防氧化保护装置),是在成球及楔线过程中增加惰性气体保护功能,以确保在成球的一瞬间与周围的空气完全隔离,以防止焊球氧化。
通常保护气体有两种防氧化方式:一种是采用纯度为5个“9”以上的100%氮气作为保护气体;另一种是采用90~95%氮气和5~10%氢气的保护加还原的混合气体。
wire bond工艺技术

wire bond工艺技术Wire bond是一种常用的芯片封装工艺技术,它是将芯片与封装载体之间的信号线连接起来的方法。
Wire bond的优点是连接可靠性高、尺寸小、成本低,广泛应用于集成电路、传感器等领域。
Wire bond工艺技术的主要步骤包括准备和清洁芯片表面、铜线制备、焊接及后处理等环节。
首先是芯片准备和清洁。
在进行Wire bond之前,需要对芯片表面进行清洁和除尘处理,以便后续工艺操作的顺利进行。
清洁的方法主要包括化学溶液的浸泡和超声波清洗。
这一步骤能够有效去除芯片表面的污染物,确保后续连接的质量。
第二步是铜线制备。
铜线是连接芯片与封装载体的关键部分,它需要具备良好的导电性和可塑性。
在制备铜线时,首先需要选择合适的铜线直径。
铜线的直径选择会影响Wire bond连接的功耗和可靠性,一般根据具体芯片的要求来选择合适的直径。
然后,通过铜线切割机将铜线切割成合适的长度。
最终得到的铜线需要经过质量检测,确保铜线的质量符合要求。
接下来是焊接环节。
在Wire bond中,焊接是最关键的步骤之一。
通过焊接,将铜线与芯片上的金属焊盘连接起来。
焊接的方法有热压焊接和超声波焊接两种。
热压焊接是利用热压头和金属焊盘之间的力和温度来实现连接,而超声波焊接则是利用超声波的振动来产生热量,将铜线与金属焊盘焊接在一起。
焊接完成后,需对焊接质量进行检测,确保焊点的电气性能和可靠性。
最后是后处理。
后处理主要包括铜线修整和封装载体连接测试。
铜线修整是将焊接连接的铜线进行修整,确保连接的牢固和稳定。
封装载体连接测试是对整个Wire bond连接进行测试,检测连接的电气性能和可靠性。
总之,Wire bond工艺技术是一种常用的芯片封装工艺。
通过对芯片准备和清洁、铜线制备、焊接及后处理等步骤的操作,能够实现芯片与封装载体之间的可靠连接。
Wire bond具有连接可靠性高、尺寸小、成本低等优点,广泛应用于集成电路、传感器等领域。
pcb 铜线 制作工艺

pcb 铜线制作工艺
PCB铜线制作工艺是指设计和制造PCB(印刷电路板)所需的铜线制作技术和流程。
以下是该工艺的简要介绍:
1.压膜:将处理过的基板铜面贴上抗蚀干膜,通过热压方式使干膜与铜面紧
密贴合。
2.曝光:利用光线照射作用将原始底片上的图像转移到感光底板上。
3.显影:用碱液将未发生化学反应的干膜部分冲掉,使需要保留的铜线部分
暴露出来。
4.蚀刻:用药液将显影后露出的铜蚀掉,形成所需的线路图形。
5.去膜:利用强碱将保护铜线的抗蚀层剥掉,使线路图形得以露出。
6.冲孔:利用CCD对位冲出检验作业的定位孔及铆钉孔,并进行后续处理。
7.表面处理:根据需要,可以采用热风整平、有机涂覆、电镀镍金、化学沉
镍金、金手指、沉银和沉锡等多种表面处理方式,以增加PCB的导电性能和美观度。
在实际应用中,不同厂商和工艺流程可能略有差异,但总体上遵循类似的流程和原理。
以上示例仅供参考,如有需要可咨询相关行业专家。
WB焊线工艺技术资料
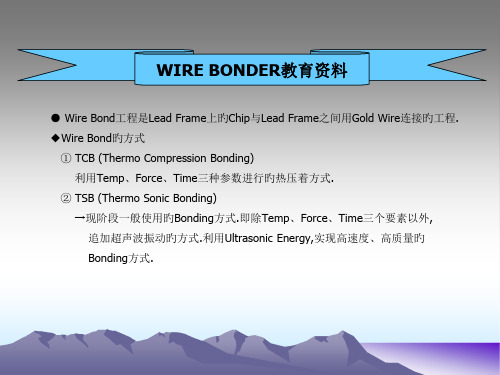
⑴ 参数设定
KEY
MAIN
1.BONDING SET UP
如下设定:
CLAMP CLOSE: [ **] g [ 80] g
⑵ Manual模式下,使用W/C键 执行闭合Clamp旳操作.
⑶ 调整VR2 使Tension Gauge旳测量成果到达”80g±5g”.
⑷ 参数设定
CLAMP CLOSE: [ **] g [ 10] g
超声波 发生器
*主要:超声波振動旳安定化 Torque Wrench
装配Capillary时拧紧Screw,管理 Torque Tool冶具
管理安装Capillary旳長度,专用JIG.
4 . Cut Wire Clamp & Spark Rod调整
4-1. Wire Clamp调整措施
1.准备 必要JIG: Tension Gauge (150g) : 示波器 : 扩展板 (HDV-550 )
按下列条件模拟设定
KEY SUB MAINTENNANCE
W/C OPEN: [ ①] g [ 60] g CLOSE: [ ②] g [ 80] g Interval: [ 100] ms
HEAD1
4-1-5-1. Cut Clamp OPEN 调整
将①旳值分别设定为”-20,-15,-10,-5,0,5,10,15,20”这九个数值来确认波形.从中选定波形振幅最小旳所 相应旳数值. 再将选定旳数值±2g 反复进行波形确认,从而选定最适合旳参数值.
Tension Gauge
⑴ 参数设定
KEY
MAIN
1.BONDING SET UP
如下设定: CLAMP OPEN: [ **] g [ 60] g
wb工艺流程 -回复
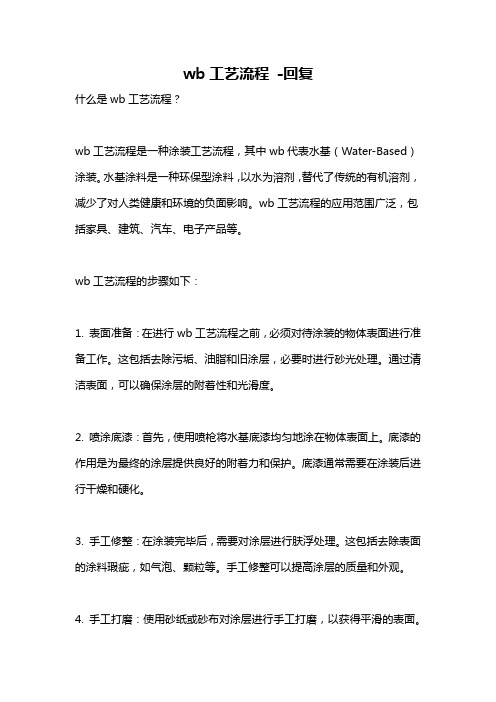
wb工艺流程-回复什么是wb工艺流程?wb工艺流程是一种涂装工艺流程,其中wb代表水基(Water-Based)涂装。
水基涂料是一种环保型涂料,以水为溶剂,替代了传统的有机溶剂,减少了对人类健康和环境的负面影响。
wb工艺流程的应用范围广泛,包括家具、建筑、汽车、电子产品等。
wb工艺流程的步骤如下:1. 表面准备:在进行wb工艺流程之前,必须对待涂装的物体表面进行准备工作。
这包括去除污垢、油脂和旧涂层,必要时进行砂光处理。
通过清洁表面,可以确保涂层的附着性和光滑度。
2. 喷涂底漆:首先,使用喷枪将水基底漆均匀地涂在物体表面上。
底漆的作用是为最终的涂层提供良好的附着力和保护。
底漆通常需要在涂装后进行干燥和硬化。
3. 手工修整:在涂装完毕后,需要对涂层进行肤浮处理。
这包括去除表面的涂料瑕疵,如气泡、颗粒等。
手工修整可以提高涂层的质量和外观。
4. 手工打磨:使用砂纸或砂布对涂层进行手工打磨,以获得平滑的表面。
手工打磨可消除涂层中的凹陷和瑕疵,提高涂层的质量和外观。
5. 涂装面漆:在涂装表面准备完成后,进行面漆喷涂。
面漆可以给物体提供所需的颜色和光泽。
根据具体需求,可以选择哑光、半光泽或高光泽的涂层。
6. 干燥和固化:涂装完毕后,需要进行干燥和固化处理。
干燥时间通常根据涂料的类型和厚度而变化。
一般情况下,涂层需要在室温下持续干燥几小时或几天。
确保涂层完全干燥和固化后,方可进行下一步处理。
7. 最终修整:在涂装干燥固化后,进行最终的修整和抛光工作。
这一步骤可以消除涂层上的细微瑕疵,使表面更加光滑和亮丽。
通过以上步骤,wb工艺流程完成了涂装作业。
这种环保的工艺流程不仅保护了人类健康和环境,还能提供高质量的涂装效果。
在日益关注环境保护和可持续发展的背景下,wb工艺流程的应用前景十分广阔。
试谈半导体铜线工艺流程

试谈半导体铜线工艺流程首先,半导体铜线工艺流程的第一步是材料准备。
在这一步骤中,需要使用高纯度的铜材料,以确保制造出的铜线具有良好的导电性能和稳定的性能。
同时,还需要进行材料的预处理、清洗和表面处理,以确保铜材料的表面光滑和清洁,为后续的加工工艺做好准备。
接下来,是制备铜线的加工工艺。
在这一步骤中,首先需要将铜材料通过拉丝机进行拉丝加工,将铜材料拉制成所需直径的铜丝。
随后,需要进行铜丝的成型、切割和整形加工,以制备成所需规格和尺寸的铜线材料。
然后,是铜线的表面处理和包覆工艺。
在这一步骤中,需要对铜线进行表面涂层处理,以提高其抗氧化、耐腐蚀和焊接性能。
同时,还需要对铜线进行包覆加工,以保护其表面不受外界环境的影响,同时增强其连接性能和耐用性。
最后,是铜线的测试和检验工艺。
在这一步骤中,需要对制备好的铜线进行严格的测试和检验,以确保其性能和质量符合要求。
测试包括导电性能、抗拉强度、耐腐蚀性能等方面的检测,以确保铜线符合半导体器件的制造标准和要求。
综上所述,半导体铜线工艺流程是一个复杂而重要的半导体制造工艺,包括材料准备、加工工艺、表面处理和包覆、测试和检验等多个环节。
只有经过严格的工艺流程和质量监控,才能制备出高质量的半导体铜线,确保半导体器件的性能和可靠性。
半导体铜线工艺流程在半导体制造中扮演着至关重要的角色。
铜线是半导体器件中不可或缺的一部分,用于连接不同的元件和传输电信号。
为了确保半导体器件的性能和可靠性,铜线的制备必须经过严格的工艺流程和质量监控。
在进行半导体铜线工艺流程时,首先需要精心挑选适用的铜材料。
通常采用高纯度的铜材料,以确保铜线具有较低的电阻率和良好的导电性能。
在今天的半导体制造工艺中,通常使用电沉积铜(EDC)或铜箔作为主要的铜材料。
在选择和准备铜材料之后,需要进行表面处理,以确保其表面的平整度和纯净度。
这一步骤是至关重要的,因为表面的光滑度和清洁度直接影响着铜线的导电性能和成型质量。
wbbga封装流程详解
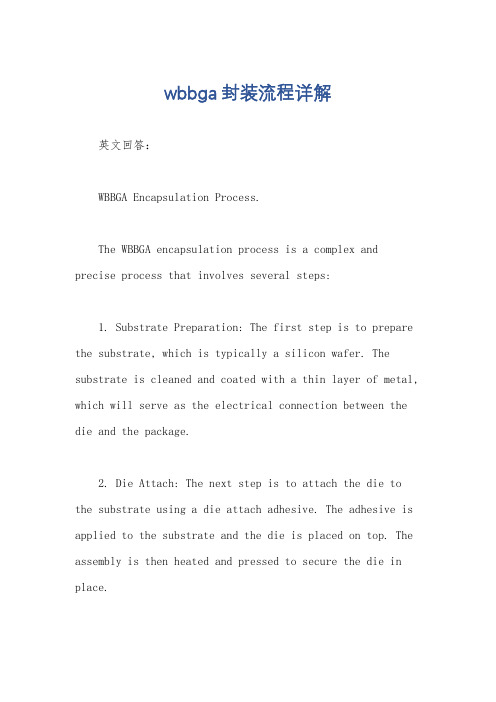
wbbga封装流程详解英文回答:WBBGA Encapsulation Process.The WBBGA encapsulation process is a complex and precise process that involves several steps:1. Substrate Preparation: The first step is to prepare the substrate, which is typically a silicon wafer. The substrate is cleaned and coated with a thin layer of metal, which will serve as the electrical connection between the die and the package.2. Die Attach: The next step is to attach the die to the substrate using a die attach adhesive. The adhesive is applied to the substrate and the die is placed on top. The assembly is then heated and pressed to secure the die in place.3. Wire Bonding: Once the die is attached, the next step is to wire bond the die to the substrate. This involves using thin gold wires to connect the electrical terminals on the die to the corresponding terminals on the substrate.4. Encapsulation: The next step is to encapsulate the assembly in a protective material. This is typically done using a mold compound, which is a liquid that is dispensed around the assembly and then cured to form a solid.5. Soldering: The next step is to solder the assembly to the circuit board. This involves applying solder to the terminals of the package and then heating the assembly to melt the solder and form a connection.6. Testing: The final step is to test the assembly to ensure that it is functioning properly. This involves performing a series of electrical tests to check for any defects or errors.中文回答:WBBGA封装流程详解。
wb制程工艺

wb制程工艺WB制程工艺简介什么是WB制程工艺?•WB制程工艺是一种用于集成电路制造的先进工艺。
•WB表示“wafer bonding”的缩写,即晶圆键合技术。
•它是一种将两张或多张晶圆通过一定的加工工艺进行键合的方法。
WB制程工艺的优势•高精度:WB制程工艺能够实现亚微米级别的精度要求,有利于集成电路性能的提升。
•低损耗:采用WB制程工艺可以避免传统线路连接的一些损耗,提高了电路的稳定性。
•多功能性:WB制程工艺可以实现不同材料之间的键合,因此可用于制造各种特殊功能的集成电路。
WB制程工艺的应用1.三维封装技术–通过WB制程工艺,不同层次的电路可以进行高精度的键合,实现三维封装。
–三维封装可以提高电路的集成度和性能,广泛应用于高性能计算、通信等领域。
2.光电器件制造–WB制程工艺可以用于制造光电器件,如光通信元件和图像传感器。
–通过键合不同材料的晶圆,可以实现光电器件的高密度集成和高性能。
3.生物芯片制造–生物芯片中需要将感兴趣的生物分子固定在芯片上,以实现生物分析、检测等功能。
–WB制程工艺可以将具有生物活性的材料键合在芯片表面,以实现生物芯片的制造。
4.传感器制造–WB制程工艺在传感器制造中的应用也越来越广泛。
–通过键合传感器晶圆和电路晶圆,可以实现传感器的高灵敏度和高可靠性。
结语•WB制程工艺作为一种先进的集成电路制造工艺,具有高精度、低损耗和多功能性的优势。
•它在三维封装、光电器件制造、生物芯片制造和传感器制造等领域都有广泛的应用前景。
•随着技术的不断进步,WB制程工艺将继续发展,为集成电路的制造带来更多可能性。
WB制程工艺发展趋势引言•WB制程工艺在集成电路制造领域取得了显著的进展,但还有许多挑战需要克服。
•本文将探讨WB制程工艺的发展趋势,以及当前面临的问题和解决方案。
1. 增强键合强度和精度•目前,WB制程工艺的键合强度和精度已经较高,但在某些应用中仍存在不足之处。
•随着对集成电路性能要求的不断提高,未来的发展方向将是进一步增强键合强度和精度。
引线键合工艺参数对封装质量的影响因素分析

引线键合工艺参数对封装质量的影响因素分析目前IC器件在各个领域的应用越来越广泛,对封装工艺的质量与检测技术提出了更高的要求,如何实现复杂封装的工艺稳定、质量保证和协同控制变得越来越重要。
目前国外对引线键合工艺涉与的大量参数和精密机构的控制问题已有较为深入的研究,并且已经在参数敏感度和重要性的排列方面有了共识。
我国IC封装研究起步较晚,其中的关键技术掌握不足,缺乏工艺的数据积累,加之国外的技术封锁,有必要深入研究各种封装工艺,掌握其间的关键技术,自主研发高水平封装装备。
本文将对引线键合工艺展开研究,分析影响封装质量的关键参数,力图为后续的质量影响规律和控制奠定基础。
2. 引线键合工艺WB随着前端工艺的发展正朝着超精细键合趋势发展。
WB过程中,引线在热量、压力或超声能量的共同作用下,与焊盘金属发生原子间扩散达到键合的目的。
根据所使用的键合工具如劈刀或楔的不同,WB分为球键合和楔键合。
根据键合条件不同,球键合可分为热压焊、冷超声键合和热超声键合。
根据引线不同,又可分为金线、铜线、铝线键合等。
冷超声键合常为铝线楔键合。
热超声键合常为金丝球键合,因同时使用热压和超声能量,能够在较低的温度下实现较好的键合质量,从而得到广泛使用。
2.1 键合质量的判定标准键合质量的好坏往往通过破坏性实验判定。
通常使用键合拉力测试(BPT)、键合剪切力测试(B ST)。
影响BPT结果的因素除了工艺参数以外,还有引线参数(材质、直径、强度和刚度)、吊钩位置、弧线高度等。
因此除了确认BPT的拉力值外,还需确认引线断裂的位置。
主要有四个位置:⑴第一键合点的界面;⑵第一键合点的颈部;⑶第二键合点处;⑷引线轮廓中间。
BST是通过水平推键合点的引线,测得引线和焊盘分离的最小推力。
剪切力测试可能会因为测试环境不同或人为原因出现偏差,Liang等人 [1]介绍了一种简化判断球剪切力的方法,提出简化键合参数(RBP)的概念,即RBP=powerA ×forceB×timeC,其中A,B,C为调整参数,一般取0.80, 0.40,0.20。
试谈半导体铜线工艺流程
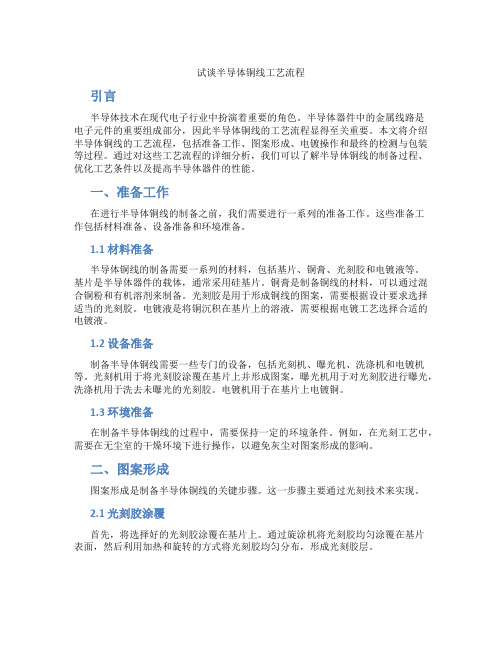
试谈半导体铜线工艺流程引言半导体技术在现代电子行业中扮演着重要的角色。
半导体器件中的金属线路是电子元件的重要组成部分,因此半导体铜线的工艺流程显得至关重要。
本文将介绍半导体铜线的工艺流程,包括准备工作、图案形成、电镀操作和最终的检测与包装等过程。
通过对这些工艺流程的详细分析,我们可以了解半导体铜线的制备过程、优化工艺条件以及提高半导体器件的性能。
一、准备工作在进行半导体铜线的制备之前,我们需要进行一系列的准备工作。
这些准备工作包括材料准备、设备准备和环境准备。
1.1 材料准备半导体铜线的制备需要一系列的材料,包括基片、铜膏、光刻胶和电镀液等。
基片是半导体器件的载体,通常采用硅基片。
铜膏是制备铜线的材料,可以通过混合铜粉和有机溶剂来制备。
光刻胶是用于形成铜线的图案,需要根据设计要求选择适当的光刻胶。
电镀液是将铜沉积在基片上的溶液,需要根据电镀工艺选择合适的电镀液。
1.2 设备准备制备半导体铜线需要一些专门的设备,包括光刻机、曝光机、洗涤机和电镀机等。
光刻机用于将光刻胶涂覆在基片上并形成图案,曝光机用于对光刻胶进行曝光,洗涤机用于洗去未曝光的光刻胶。
电镀机用于在基片上电镀铜。
1.3 环境准备在制备半导体铜线的过程中,需要保持一定的环境条件。
例如,在光刻工艺中,需要在无尘室的干燥环境下进行操作,以避免灰尘对图案形成的影响。
二、图案形成图案形成是制备半导体铜线的关键步骤。
这一步骤主要通过光刻技术来实现。
2.1 光刻胶涂覆首先,将选择好的光刻胶涂覆在基片上。
通过旋涂机将光刻胶均匀涂覆在基片表面,然后利用加热和旋转的方式将光刻胶均匀分布,形成光刻胶层。
2.2 曝光接下来,将光刻胶层暴露在特定的光源下,以形成所需的图案。
通过光刻机和曝光机,将光刻胶层进行曝光。
2.3 显影曝光之后,需要进行显影,以去除未曝光的光刻胶。
将基片放入洗涤机中,在显影液的作用下,未曝光的光刻胶将被洗掉,只剩下所需的图案。
2.4 退光刻胶经过显影之后,还需要进行退光刻胶的处理。
镀锡铜线生产工艺流程及质量控制要点
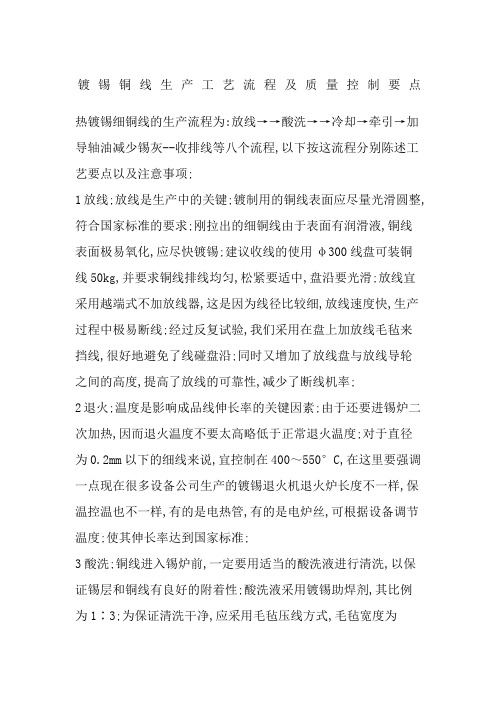
镀锡铜线生产工艺流程及质量控制要点热镀锡细铜线的生产流程为:放线→→酸洗→→冷却→牵引→加导轴油减少锡灰--收排线等八个流程,以下按这流程分别陈述工艺要点以及注意事项;1放线;放线是生产中的关键;镀制用的铜线表面应尽量光滑圆整,符合国家标准的要求;刚拉出的细铜线由于表面有润滑液,铜线表面极易氧化,应尽快镀锡;建议收线的使用φ300线盘可装铜线50kg,并要求铜线排线均匀,松紧要适中,盘沿要光滑;放线宜采用越端式不加放线器,这是因为线径比较细,放线速度快,生产过程中极易断线;经过反复试验,我们采用在盘上加放线毛毡来挡线,很好地避免了线碰盘沿;同时又增加了放线盘与放线导轮之间的高度,提高了放线的可靠性,减少了断线机率;2退火;温度是影响成品线伸长率的关键因素;由于还要进锡炉二次加热,因而退火温度不要太高略低于正常退火温度;对于直径为0.2mm以下的细线来说,宜控制在400~550°C,在这里要强调一点现在很多设备公司生产的镀锡退火机退火炉长度不一样,保温控温也不一样,有的是电热管,有的是电炉丝,可根据设备调节温度;使其伸长率达到国家标准;3酸洗;铜线进入锡炉前,一定要用适当的酸洗液进行清洗,以保证锡层和铜线有良好的附着性;酸洗液采用镀锡助焊剂,其比例为1∶3;为保证清洗干净,应采用毛毡压线方式,毛毡宽度为20cm,定期用酸洗液浇注毛毡特强调:请按线径越大浓度越高的原则使用,用工业软水配比效果较好;请将配好的助焊助焊剂倒入助焊槽内放入毛毡让其慢慢稀释,不可将助焊剂直接浇入毛毡上面,在生产过程中,开机速度过快,应该多放一些趟水布,经常更换,防止水槽的水过多带到铜线上,影响助焊剂浓度,造成其它问题出现,水带的越少,锡渣就越少,也不造成炸锡;4;锡炉设备和锡炉温度对产品的质量起着关键作用;目前锡炉有3种,一是整个锡炉材料由两个铸铁锅形成的且锅底成三角行由电热管控温,生产大规格容易扁线,锡渣多不容易操作,二是整体为不锈钢锅体,控温为电炉丝,锡锅大好操作,控温均匀,锡渣少三是日本不锈钢锡锅由三段控温,使用效果更佳更科学,锡炉温偏低,镀锡铜线表面毛糙、线表面容易产生锡瘤;炉温偏高,则镀锡铜线易发黄;容易断线,经过反复试验,锡的熔点为231°C,锡炉的温度以250--260°C为宜根据生产规格适当调节锡炉温度生产出的成品线表面镀层光滑、连续,伸长率也达到国家标准;锡炉中的锡在加热时,表面氧化很快,会造成浪费;为防止这一点,可在熔化的锡液表面覆盖一层云母、木炭粉等,但管理不上会造成脏乱,以隔绝空气与锡液表面的接触;最好不要经常刮动锡液表面锡与铜线结合的好坏,除了铜线表面需酸洗外,锡液本身的纯度也是重要因素;因此锡液的成分应每1.2月检测一次,其中铜含量不得超过1%,如超过1%应进行再生处理或换锡;5挡锡模;目前很多公司没有使用建议还是在收线部分安装挡锡模装置;使用挡锡模主要防止锡粒和操作不当带到铜线上影响下道工序生产,一般有拉丝模和陶瓷模;采用拉丝挡锡模,镀锡铜线表面质量好,但价格高;一般采用废拉丝模具使用,生产中要注意对模架角度的调整,以保证锡炉中的压线支点、刮锡模中心点及导轮上的支撑点在一条直线上;避免线表面刮伤镀锡模的孔径也是影响镀锡铜线质量的一个关键因素;孔径偏小,则断线频繁;孔径偏大,锡层则偏厚,影响涂层的质量,且耗锡量增加,成本提高;经过生产试验及对产品性能的测试,镀锡模的孔径应比铜线外径大0.05mm为好;6冷却方式;对于线径小于0.2mm的镀锡铜线,宜采用空冷,生产中要控制好牵引和镀锡铜线出炉之间的距离即可;对于线径为0.2~0.6mm的镀锡铜线,采用风冷方式比较好,它可以有效避免镀锡铜线因冷却不够在收线后产生线间粘锡现象,保证镀锡铜线的表面质量;7加导轴油,应该是一个比较重要的工序,镀锡铜线或多或少都有锡灰产生,在电子线生产绞线过程中如7/0.127,7/0.16;11/0.16,11/0.127,17/0.178,41/0.16,41/0.1 5对绞距严格,镀锡线有锡灰会造成整股断线,应该加加导轴油防止锡灰产生;8收线、牵引速度;收线、牵引速度应依据线径大小而定,同时也考虑退火及铜线在锡炉中的时间牵引速度过快,会导致退火不充分而影响伸长率,同时也增加了断线机率;速度太慢则铜线在中时间太长,线会发硬;。
半导体铜工艺
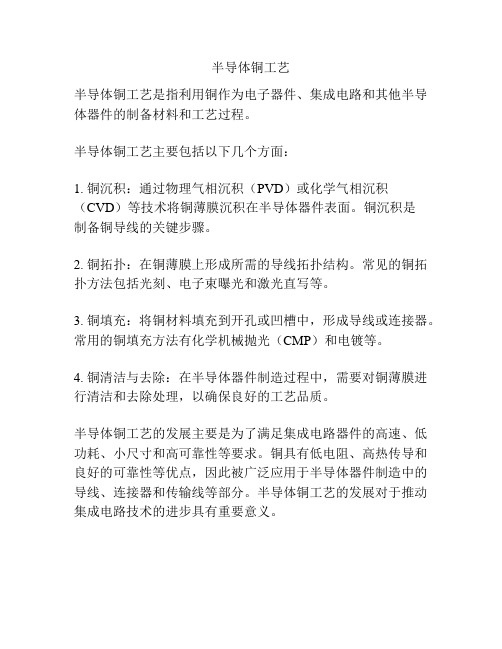
半导体铜工艺
半导体铜工艺是指利用铜作为电子器件、集成电路和其他半导体器件的制备材料和工艺过程。
半导体铜工艺主要包括以下几个方面:
1. 铜沉积:通过物理气相沉积(PVD)或化学气相沉积(CVD)等技术将铜薄膜沉积在半导体器件表面。
铜沉积是
制备铜导线的关键步骤。
2. 铜拓扑:在铜薄膜上形成所需的导线拓扑结构。
常见的铜拓扑方法包括光刻、电子束曝光和激光直写等。
3. 铜填充:将铜材料填充到开孔或凹槽中,形成导线或连接器。
常用的铜填充方法有化学机械抛光(CMP)和电镀等。
4. 铜清洁与去除:在半导体器件制造过程中,需要对铜薄膜进行清洁和去除处理,以确保良好的工艺品质。
半导体铜工艺的发展主要是为了满足集成电路器件的高速、低功耗、小尺寸和高可靠性等要求。
铜具有低电阻、高热传导和良好的可靠性等优点,因此被广泛应用于半导体器件制造中的导线、连接器和传输线等部分。
半导体铜工艺的发展对于推动集成电路技术的进步具有重要意义。
wb工艺技术浅析

wb工艺技术浅析WB工艺是一种广泛应用于精密制造工业的连接工艺,在电子、机械、汽车等行业都有广泛的应用。
WB工艺的全称是湿接焊(Wet Bonding),它是一种采用金属活性片或活动形式的松紧型胶粘剂来连接两个或多个件的工艺。
WB工艺的主要特点是连接力强、耐久性好、连接迅速、易于操作,同时具有无污染、无损伤、无残留等优点。
在传统的连接工艺中,常常使用的是焊接和铆接等方法,这些方法需要经过多道工序,而且易造成热变形和压力集中等问题。
而WB工艺可以避免这些问题,同时保持连接的稳固性。
WB工艺的实施过程中,首先需要准备好所需要连接的两个件,然后将金属活性片或者活动形式的松紧型胶粘剂置于两个件的接头处。
接着将两个件对准,并施加足够的压力,以保证连接的稳固。
在施加压力后,粘接剂会迅速凝固,在凝固的过程中形成强力的粘合。
整个连接过程一般只需数秒钟左右,非常快速高效。
WB工艺的应用领域非常广泛。
在电子行业,WB工艺常用于连接电子元件、电池等;在机械行业,WB工艺常用于连接各种机械件、零部件等;在汽车行业,WB工艺常用于连接车身结构、座椅等。
此外,WB工艺还可以应用于航空航天、医疗器械等领域。
尽管WB工艺具有许多优点,但也存在一些局限性。
首先,WB工艺对连接的件要求较高,需要具备一定的表面光洁度和粘合性。
其次,由于WB工艺是一种胶粘剂连接工艺,所以连接的件不能承受过高的温度和压力。
最后,由于WB工艺是一种湿接焊技术,对环境的湿度要求较高,不能在过于干燥的环境中施工。
总的来说,WB工艺是一种非常实用的精密连接技术。
它通过金属活性片或活动形式的松紧型胶粘剂来连接,具有连接力强、耐久性好等特点。
它在电子、机械、汽车等行业都有广泛的应用,可以大大提高生产效率和连接质量。
然而,WB工艺也有一定的局限性,在实际应用中需要充分考虑材料的特性和环境条件。
PCB表面处理技术-8章-WB

二、有机助焊保护膜成膜原理
主要成分是烷基苯骈咪唑、有机酸,并添加有Pb2+、Cu2+、Zn2+等金属
离子。
由于烷基苯骈咪唑与铜之间的络合反应,通过氢键和范德华力的双重
作用,在铜表面生成烷基苯骈咪唑络合物膜,该络合物具有优良的耐热
性。
Cu2+、Zn2+等金属离子加入到溶液中,在成膜过程中Cu、Zn填充于络合
本章主要介绍物理吸咐粘 结而成的表面膜层技术
ROHS禁令:
禁6种物质:Pb,Hg,Cr6+ (六价铬),PBB(多溴联苯), PBDE(多溴联苯乙醚)。
表面处 理方式 无铅喷 锡 OSP
化学镍 金 化学锡
化学银
电镀镍 金 化学钯
PCB常用表面处理工艺及其特点
表面层特性
镀层不平坦、主要适用于大焊垫、宽线距。不适合用于精细 线路、细密零件之组装。 镀层均一、表面平坦、不具接触之功能,无法从外观检查, 不适合多次reflow。 镀层均一、表面平坦、接触性好、可焊性好、可打线、可协 助散热,且有一定耐磨性。 镀层均一、表面平坦、对防焊(覆盖膜)攻击性大、锡须隐 患难以管控。耐热性差、对环境要求高,易老化、变色。 镀层均一、表面平坦、可耐多次组装作业,具按键接触功 能,可打线。对环境要求高,容易老化、变色。 镀层不均一,接触性好、可打线、耐磨性好,不适用于焊接 (存在金脆)。 镀层均一、表面平坦。制程处在试验阶段。
PCB常用表面处理工艺比较
表面处理 方式
无铅喷锡 OSP
化学镍金
化学锡 化学银
应用比 例 20% 2025% 3035%
5-10%
5-10%
成本
低 最低
高
低 中
芯片的wb封装工艺流程
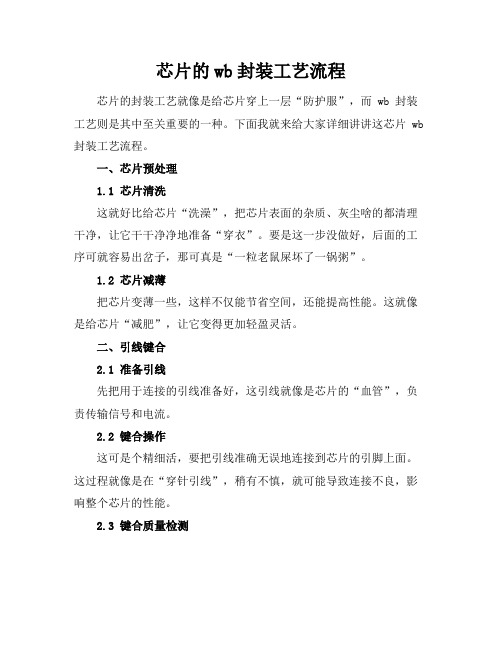
芯片的wb封装工艺流程芯片的封装工艺就像是给芯片穿上一层“防护服”,而 wb 封装工艺则是其中至关重要的一种。
下面我就来给大家详细讲讲这芯片 wb 封装工艺流程。
一、芯片预处理1.1 芯片清洗这就好比给芯片“洗澡”,把芯片表面的杂质、灰尘啥的都清理干净,让它干干净净地准备“穿衣”。
要是这一步没做好,后面的工序可就容易出岔子,那可真是“一粒老鼠屎坏了一锅粥”。
1.2 芯片减薄把芯片变薄一些,这样不仅能节省空间,还能提高性能。
这就像是给芯片“减肥”,让它变得更加轻盈灵活。
二、引线键合2.1 准备引线先把用于连接的引线准备好,这引线就像是芯片的“血管”,负责传输信号和电流。
2.2 键合操作这可是个精细活,要把引线准确无误地连接到芯片的引脚上面。
这过程就像是在“穿针引线”,稍有不慎,就可能导致连接不良,影响整个芯片的性能。
2.3 键合质量检测完成键合后,得好好检查一下,看看有没有“漏网之鱼”,确保每一个连接都是牢固可靠的。
这一步可不能马虎,不然就可能“千里之堤毁于蚁穴”。
三、封装成型3.1 模具准备选择合适的模具,就像是给芯片找一个合适的“家”。
3.2 注入封装材料把专门的封装材料注入模具,将芯片包裹起来。
这就像是给芯片盖上一层“被子”,保护它不受外界的干扰和损害。
芯片的 wb 封装工艺流程是一个非常复杂且精细的过程,每一个步骤都需要严格把控,容不得半点马虎。
只有这样,才能生产出高质量、高性能的芯片,为我们的电子设备提供强大的“心脏”。
希望大家通过我的介绍,对芯片的 wb 封装工艺流程有了更清楚的了解。
wb变压器包铜箔原理
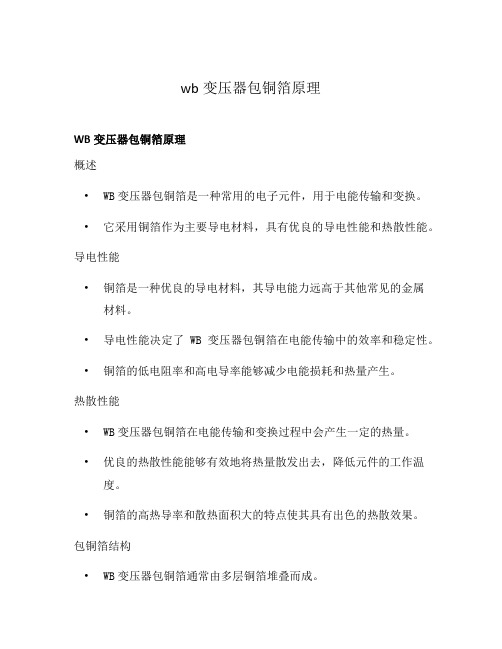
wb变压器包铜箔原理WB变压器包铜箔原理概述•WB变压器包铜箔是一种常用的电子元件,用于电能传输和变换。
•它采用铜箔作为主要导电材料,具有优良的导电性能和热散性能。
导电性能•铜箔是一种优良的导电材料,其导电能力远高于其他常见的金属材料。
•导电性能决定了WB变压器包铜箔在电能传输中的效率和稳定性。
•铜箔的低电阻率和高电导率能够减少电能损耗和热量产生。
热散性能•WB变压器包铜箔在电能传输和变换过程中会产生一定的热量。
•优良的热散性能能够有效地将热量散发出去,降低元件的工作温度。
•铜箔的高热导率和散热面积大的特点使其具有出色的热散效果。
包铜箔结构•WB变压器包铜箔通常由多层铜箔堆叠而成。
•每层铜箔之间通过绝缘材料隔开,以防止电流短路和绝缘破坏。
•包铜箔结构的设计和制造精度对于元件的性能和可靠性至关重要。
工作原理•WB变压器包铜箔通过电流在铜箔中的流动来实现电能传输和变换。
•当电流通过铜箔时,铜箔产生磁场,进而驱动变压器的工作。
•铜箔的导电性能保证了电流的顺畅传输,达到预期的能量变换效果。
应用领域•WB变压器包铜箔广泛应用于电子设备、电力系统和通讯网络等领域。
•在电子设备中,它用于电源模块、电路板和信号传输等重要部件。
•在电力系统中,它被用于变压器、整流器和逆变器等电能变换装置。
结论•WB变压器包铜箔作为一种重要的电子元件,具有优良的导电性能、热散性能和可靠性。
•它在电能传输和变换过程中扮演着重要的角色,推动了电子技术的发展和应用。
•随着科技的进步和需求的增长,WB变压器包铜箔将持续发展和创新,为各行各业提供更高效、可靠的电能解决方案。
电能传输和变换的基本原理•电能传输是指将电能从发电站等地方通过输电线路送到终端使用者的过程。
•变换是指将电能从一种形式转换成另一种形式的过程,如从高压到低压、交流到直流等。
变压器的基本工作原理•变压器是一种电力设备,用于改变交流电的电压和电流。
•它基于电磁感应原理工作,主要由两个线圈(即一次侧线圈和二次侧线圈)和一个铁芯构成。
WB工艺技术

2.1.2.2 等离子种类
(1)低温及高温等离子体 等离子体可分为高温等离子体和低温等离子体两类,在等离子体中,不同 微粒的温度实际上是不同的,所具有的温度是与微粒的动能即运动速度质量有关, 把等离子体中存在的离子的温度用Ti表示,电子的温度用Te表示,而原子、分子 或原子团等中性粒子的温度用Tn表示,对于Te大大高于Ti和Tn的场合,即低压体 气的场合,此时气体的压力只有几百个帕斯卡,当采用直流电压或高频电压做电 场时,由于电子本身的质量很小,在电池中容易得到加快,从而可获得平均可达 数电子伏特的高能量,对于电子,此能量的对应温度为几万度(K),而弟ห้องสมุดไป่ตู้由 于质量较大,很难被电场加速,因此温度仅几千度。由于气体粒子温度较低(具 有低温特性),因此把这种等离子体称为低温等离子体。当气体处于高压状态并 从外界获得大量能量时,粒子之间的相互碰撞频率大大增加,各种微粒的温度基 本相同,即Te基本与Ti及Tn相同,我们把这种条件下得到的等离子体称为高温等 离子体,太阳就是自己界中的高温等离子体。由于高温等离子体对物体表面的作 用过于强烈,因此在实际应用中很少使用,目前投入使用的只有低温等离子体。
等离子体清洗技术的最大特点是不分处理对象的基材类 型,均可进行处理,对金属、半导体、氧化物和大多数高 分子材料,如聚丙烯、聚脂、聚酰亚胺、聚氯乙烷、环氧、 甚至聚四氟乙烯等都能很好地处理,并可实现整体和局部 以及复杂结构的清洗。正确的等离子体清洗不会在表面产 生损伤层,表面质量得到保证;由于是在真空中进行,不 污染环境,保证清洗表面不被二次污染。
(2)电子与物体表面的作用 一方面电子对物质表面的撞击作用,可以促使吸附在物质表 面的气体分子发生分解和解析,另一方面大量的电子撞击有利引起 化学反应。出于电子质量极小,因此比离子的移动速度要快得多, 当进行等离子处理时,电子要比离子更早到达物质表面,并使表面 带有负电荷,这有利于引发进一步反应。 (3)离子与物质表面的作用 通常指的是带正电荷的阳离子的作用,阳离子有加速度冲向 带负电荷表面的倾向,此时是物质表面获得相当大的动能,足以撞 击去除表面上附着的颗粒性物质,我们把这种现象成为溅射现象, 而通过离子的冲击作用可极大促进物体表面化学反应发生的几率。 (4)紫外线与物体表面的作用 紫外线具有很强的光能,可使附着在物体表面的物质的分子 键发生断裂而分解,而且紫外线具有很强的穿透能力,可透过物质 表面深达数微米而产生反应作用。
- 1、下载文档前请自行甄别文档内容的完整性,平台不提供额外的编辑、内容补充、找答案等附加服务。
- 2、"仅部分预览"的文档,不可在线预览部分如存在完整性等问题,可反馈申请退款(可完整预览的文档不适用该条件!)。
- 3、如文档侵犯您的权益,请联系客服反馈,我们会尽快为您处理(人工客服工作时间:9:00-18:30)。
铜线键合工艺
A、铜线工艺对框架的特殊要求-------铜线对框架的的要求主要有以下几点:
1、框架表面光滑,镀层良好;* y/ I! I; ~) M# \' F7 a3 k
2、管脚共面性良好,不允许有扭曲、翘曲等不良现象
管脚粗糙和共面性差的框架拉力无法保证且容易出现翘丝和切线造成的烧球不良,压焊过程中容易断丝及出现tail too short ;
B、保护气体----安装的时候保证E-torch上表面和right nozzle 的下表面在同一个平面上.才能保证烧球的时候,氧化保护良好.同时气嘴在可能的情况下尽量靠近劈刀,以保证气体最大范围的保护
C、劈刀的选用——同金线相比较,铜线选用劈刀差别不是很大,但还是有一定的差异:
1、铜线劈刀T 太小2nd容易切断,造成拉力不够或不均匀
2、铜线劈刀CD不能太大,也不能太小,不然容易出现不粘等现象
3、铜线劈刀H与金线劈刀无太大区别(H比铜丝直径大8µm即可,太小容易从颈部拉断)
4、铜线劈刀CA太小线弧颈部容易拉断,太大易造成线弧不均匀;
5、铜线劈刀FA选用一般要求8度以下(4-8度)
6、铜线劈刀OR选用大同小异
D压焊夹具的选用
铜线产品对压焊夹具的选用要求非常严格,首先夹具制作材料要选用得当,同时夹具表面要光滑,要保证载体和管脚无松动要,否则将直接影响产品键合过程中烧球不良、断线、翘丝等一系列焊线问题。
二、铜线的特性及要求
切实可行的金焊线替代产品。
铜焊线,机械、电气性质优异,适用于多种高端、微间距器件,引线数量更高、焊垫尺寸更小。
铜焊线,不仅具有铜焊线显著的成本优势,而且降低了铜焊点中的金属间生长速度,这样就为大功率分立封装带来了超一流的可靠性。
铜焊线的成本优势:由于铜的成本相对较低,因此人们更愿意以铜作为替代连接材料。
对于1mil焊线,成本最高可降低75%*,2mil可达90%*,具体则取决于市场状况。
铜焊线的优异性能:铜线的导热导电性能显著优于金线和铝线,因此能够以更细的焊线直径达到更好的散热性能及更高的额定功率。
与金相比,铜的机械性质更强,这样在模压和封闭过程中可以得到优异的球颈强度和较高的弧线稳铜焊线的包装与存放
铜具有较强的亲氧性,因此必须对铜焊线进行保护以延长其保存期。
为此各卷铜焊线均采用吸塑包装,并在塑料袋内单独密封; 除了以上优点为,铜线还有以下特性:
1.铜线易氧化,原则上拆封的铜线48小时用完。
2.铜线硬度高,容易产生弹坑、不粘、断丝、、烧球不良
三、铜线和金线在键合工艺参数的区别
1.铜线压焊工艺参数与金线相比较最大的变化是加大了contact force,以增加产品的可焊性,为了减小弹坑风险,一般情况下1mil以下铜线采用LOW-Power模式,而1.2mil以上一般采用High-power模式
球不良原因:吹气保护不好
铜线开封后防止时间太长.线有氧化(72小时)
Tail length 不稳定导致烧球不好
Capillary 选择型号不对
Action:
调整吹气装置和E-TORCE位置,保证保护良好
更换铜线& Y0 D. u) [8 J& w, o% k* d
调整2nd 焊接参数(base power and base force)保证tail length 稳定.2 p5 d" t2 m9 V' s, |) N' f/ c 选用合适的capillary 如果报警后可以直接从capillary 穿下线,应该是base power 较小,应该调大base power或者减小base force t/ ^, A1 z, `1 C* i
如果报警后线不能直接穿下capillary,必须把线拔除再穿的话,应该减小base power 或者增大base force.
四、铜线对生产效率和产品质量的影响H' @) J0 N; K3 ?* t/ _# j# T
1、产能相对较低---铜线硬度要强于金线,压焊过程中断丝几率和不粘相对增大,考虑到可焊性等因素,压焊速度相对较慢,正常情况下设备利用率是金线设备的2/3左右。
2、偏心球、烧球不良(高尔夫球)产生较多----铜线2nd焊点切线稍有异常,将直接影响1st焊点烧球,气体保护范围太小或框架、夹具异常均会影响1st焊点烧球,所以在出现以上现象是,首先应排除硬件原因,然后再从参数方面解决。
- O3 h8 A4 w& |. B
3、不粘产生频繁----由于铜线的特殊性,键合过程中不粘现象较为严重,在铜线键合过程中出现不粘,应从以下方面解决:2 T J9 V8 V( s6 l8 Z0 i' U* u% V
A、要保证拆封的铜线无氧化,沾污,拆封的铜线要在48小时内用完。
B、夹具表面平整光滑,载体无松动
C、保证烧球的时候,氧化保护良好" t: U( n( m# D
D、切线正常,无偏心球
E、装片平整度,胶量充足(胶量不足缺胶直接影响不粘,1.2mil以上铜线最为明显),固化温度均匀;L0 f1 c7 W: z, l- r: y
F、劈刀选用合理
G、参数调整
4、弹坑风险增加---由于铜线硬度要强于金线,且容易产生氧化,弹坑几率风险大大增加.为了减小铜线弹坑风险,需从以下方面解决:) f- J' k: E4 A
A、配备专人每班做例行弹坑验证,包括更换品种,夹具及设备维修后。
2 z8 `5 x* l, ^7 i6 u- f, ?# H
B、加强过程监控---更换劈刀、修改1st、EFO参数后必须作弹坑试验;
C、对一些硬件如气嘴、流量(保护气体),夹具,压缩空气等每班最少做一次检查,同时提醒作业员随时检查。
D、及时和客户沟通,铜线产品Pad测试点(探针印)小于20%,同时要保证一定的铝层厚度' i6。