齿轮测量
齿轮测量仪操作规程

齿轮测量仪操作规程
《齿轮测量仪操作规程》
一、设备准备
1. 检查测量仪器是否完整,无损坏;
2. 确保电源连接正确且稳定;
3. 清洁测量仪器表面;
4. 确保测量仪器的环境温度和湿度符合要求。
二、测量前的准备
1. 将待测齿轮放置在测量仪器上,确保其安装牢固;
2. 调整测量仪器的参数,根据待测齿轮的规格进行调整;
3. 检查测量仪器的测量工具是否正常,如传感器、尺等。
三、测量操作
1. 打开测量仪器的电源,等待测量仪器进行自检;
2. 根据待测齿轮的要求,选择合适的测量模式;
3. 将测量仪器的传感器接触待测齿轮,开始测量;
4. 根据测量仪器的显示结果,进行记录。
四、测量后的处理
1. 关闭测量仪器的电源;
2. 清洁测量仪器和测量工具;
3. 根据测量结果,进行数据处理和分析;
4. 将测量仪器和测量结果报告存档。
五、安全注意事项
1. 在操作过程中,应严格按照操作规程进行操作;
2. 使用测量仪器时,应注意防止水或其它液体进入测量仪器内部;
3. 测量仪器有特殊要求的,应按照要求进行操作;
4. 在使用过程中,如出现异常情况,应立即停止操作并及时通知相关人员。
六、设备维护
1. 定期对测量仪器进行维护和保养;
2. 定期对测量仪器进行校准和检测;
3. 如发现测量仪器有损坏或故障,应及时联系维修人员处理。
以上即是关于齿轮测量仪操作规程的详细内容,希望每一位操作人员都能严格按照规程进行操作,确保测量结果的准确性和设备的安全使用。
齿轮综合测量方法

齿轮综合测量方法齿轮是机械传动中常用的零部件之一,用于实现两轴之间的转动传递。
齿轮的精度和质量直接影响到机械传动的性能和寿命。
因此,对齿轮进行综合测量是非常重要的。
齿轮的综合测量方法可以分为外观测量和功能测量两个方面。
下面将介绍一些常用的齿轮综合测量方法。
外观测量主要包括齿轮的尺寸测量和形状测量。
尺寸测量可以使用千分尺、游标卡尺等工具进行,主要测量齿轮的外径、齿高、齿顶直径和齿根直径等尺寸。
形状测量可以使用影像测量仪等设备进行,主要测量齿轮的齿形偏差、齿距偏差和齿向偏差等。
功能测量主要包括齿轮的传动误差和摆动测试。
传动误差是指齿轮在传动过程中产生的误差,可以通过齿轮测试台进行测量。
测试台上安装两个相互啮合的齿轮,并通过测量传感器测量齿轮的角度变化,从而得到齿轮的传动误差。
摆动测试是指齿轮在运转时产生的轴向和径向摆动,可以通过轴向和径向摆动测量仪进行测量。
此外,还可以采用光栅尺、振动传感器等设备对齿轮的转速和振动进行测量,以评估齿轮的运转稳定性和动力性能。
对齿轮进行综合测量时,需要注意以下几个方面。
首先,选择合适的测量设备和测量方法,确保测量结果的准确性和可靠性。
其次,要有严格的测量标准和规范,确保测量过程的一致性和可比性。
同时,还需要对测量结果进行分析和评估,及时发现齿轮的缺陷和不良现象,并采取相应的措施进行修复或更换。
综上所述,齿轮的综合测量方法是一项重要的工作,能够全面评估齿轮的质量和性能。
通过合理选择测量设备和方法,严格执行测量标准和规范,以及对测量结果进行分析和评估,能够提高齿轮的精度和可靠性,从而提高机械传动的性能和寿命。
齿轮测量基本方法原理
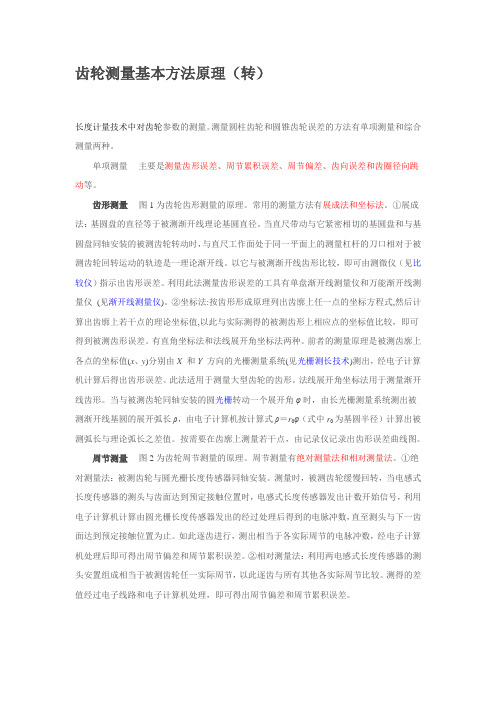
5、铣键槽----铣床。
6、滚齿-----滚齿机。
7、齿面淬火---高频淬火机床。
8、磨---外圆磨床。
锥齿轮用铣床可以加工
第一步当然是下料,锯切
第二步,车,外形
第三步,铣,齿形
如果需要可以磨削和淬火或调质
细长轴的齿轮轴加工工艺(以45号钢为例):
一、毛坯下料
二、调质处理(提高齿轮轴的韧性和轴的刚度)
加工的最后阶段是齿形的精加工阶段。这个阶段的目的,在于修正齿轮经过淬火后所引起的齿形变形,进一步提高齿形精度和降低表面粗糙度,使之达到最终的精度要求。在这个阶段中首先应对定位基准面(孔和端面)进行修整,因淬火以后齿轮的内孔和端面均会产生变形,如果在淬火后直接采用这样的孔和端面作为基准进行齿形精加工,是很难达到齿轮精度的要求的。以修整过的基准面定位进行齿形精加工,可以使定位准确可靠,余量分布也比较均匀,以便达到精加工的目的。
(一)工艺过程分析
图9-17所示为一双联齿轮,材料为40Cr,精度为7-6-6级,其加工工艺过程见表9-6。
从表中可见,齿轮加工工艺过程大致要经过如下几个阶段:毛坯热处理、齿坯加工、齿形加工、齿端加工、齿面热处理、精基准修正及齿形精加工等。
齿号
Ⅰ
Ⅱ
齿号
Ⅰ
Ⅱ
模数
2
2
基节偏差
±0.016
±0.016
齿数
20世纪70年代初,开始利用长光栅(或激光)、圆光栅等组成的测量系统、电子计算机自动控制系统和数据处理系统等组成的自动测量系统,在同一台齿轮量仪上测量齿向误差,齿形误差和周节偏差等。直齿圆柱齿轮的齿向误差也常在具有精密直线导轨的齿圈径向跳动仪上测量。
齿圈径向跳动测量以被测齿轮轴心线定位,利用带有球形测头或锥角等于2倍齿形角的圆锥形测头的测微仪,使测头位于齿高中部与齿廓双面接触。测头相对于齿轮轴心线的最大变动量即齿圈径向跳动。测量齿圈径向跳动的仪器是齿圈径向跳动仪。
齿轮测绘的步骤和技巧

齿轮测绘的步骤和技巧齿轮测绘是一种用于测量和绘制齿轮几何参数的技术。
通过齿轮测绘,可以准确地了解齿轮的尺寸、齿形、齿间隙等关键参数,从而进行齿轮的生产、加工和组装。
1.准备工作:首先需要准备一套齿轮测绘仪器,例如测量仪、投影仪、光栅尺等。
同时需要准备一套参考标准,包括齿轮测绘标准和检验规范。
2.精确测量:使用合适的测量仪器对齿轮进行精确测量。
首先测量齿轮的基本尺寸,包括齿轮直径、模数、压力角等。
然后测量齿轮的齿数和模数,可以采用光栅尺或齿轮测量仪进行。
3.测量齿形:齿形是齿轮的一个关键参数,可以通过投影仪进行测量。
将齿轮放在投影仪上,使用透明标尺轮廓描线法,将齿轮的齿形投影在投影屏上,然后使用目镜检查齿轮的齿形是否符合要求。
如果齿形有误差,可以采取修正措施。
4.校核测量:测量完齿形后,需要对测量结果进行校核。
可以随机选择几个点进行二次测量,并与初次测量结果进行比对。
如果测量结果相差不大,说明测量准确。
5.绘制齿轮图:将测量结果绘制成齿轮图,包括齿轮的齿形图、齿轮的几何参数图等。
可以使用CAD软件进行齿轮图绘制,确保图纸准确无误。
6.检验和调整:绘制齿轮图后,需要进行齿轮的检验和调整。
通过对齿轮图的比对,可以发现齿轮的偏差和误差,并采取相应的措施进行调整,确保齿轮的质量。
1.选择合适的测量仪器:齿轮测绘需要使用各种精密测量仪器,因此要选择合适的仪器,并进行校准和维护,以确保测量结果的准确性。
2.注意测量方法:齿轮测绘需要采用合适的测量方法和技术。
例如,测量齿形时可以使用投影仪,而测量齿距可以使用光栅尺等。
3.注意测量环境:齿轮测绘需要在稳定的环境中进行,避免震动和干扰对测量结果的影响。
同时还需注意气温、湿度等因素对测量结果的影响。
4.针对不同的齿轮种类采用不同的测量方法:不同类型的齿轮测绘方法是不同的,例如直齿轮和斜齿轮的测量方法不同,需要根据具体情况进行选择。
5.注意测量结果的分析和校准:测量结果要进行分析和校准,比对测量结果与标准值之间的差异,并进行合理的调整和修正。
齿轮测速原理

齿轮测速原理
齿轮测速原理是通过齿轮的旋转来测量物体的速度。
在齿轮测速原理中,通常使用一个传感器来检测齿轮的转速,然后根据齿轮的直径和转速来计算物体的速度。
齿轮的转速可以通过测量齿轮上的齿数来确定。
传感器通常会检测到每个齿槽的通过,然后记录下通过齿槽的时间间隔。
根据时间间隔和已知的齿数,可以计算出齿轮的转速。
一旦得到齿轮的转速,就可以通过齿轮的直径来计算物体的速度。
如果知道物体与齿轮的直接关系,可以直接使用齿轮的转速乘以齿轮的直径来计算物体的速度。
如果没有直接关系,可能需要使用其他的数据进行转换。
齿轮测速原理是一种简单且常用的测量物体速度的方法。
齿轮测速器广泛应用于工业领域,例如汽车、机械设备和风力发电等。
通过齿轮测速原理,可以准确地测量物体的速度,并根据需要进行进一步的数据处理和分析。
齿轮测量

上海同济高科技发展有限公司测控事业部
2015-2-5
目录 CONTENTS
1、齿轮测量概述 2、齿轮测量方法 3、齿轮M值测量 4、齿轮中心距测量
1、齿轮测量概述
齿轮是能互相啮合的有齿的机械零件,是传递运动与动力的关键零 部件。而齿轮传动是机械传动中应用最广的一种传动形式。它的传动比 准确,效率高,结构紧凑。 由于制造与安装等方面的原因,实际齿轮总是存在着误差。这种 误差对传动系统的精度与动态特性(特别是振动与噪声)有直接的影响。 此种要求多见于减速机、摩托车箱体、汽车变速箱等现代工业最常见的 场合。
4、齿轮中心距测量
成功案例展示:
啮合装置结构
测量仪操作界面谢谢观赏,有需求请联系。 本人账号头像上有联系方式 专业生产销售。
惠州东精科技有限公司
3、齿轮M值测量
齿轮M值专用检具,大小可调节,可进行 内齿、外齿测量的切换。
以外M值为例测量参数如下: 测量调节范围:0~160mm 测量力:0~40N 测量精度:<2.5μm 最大负重:6公斤 测头退位行程:14mm
3、齿轮M值测量 两种装置结构图
4、齿轮中心距测量 中心距是指两个互相啮合齿轮的圆心的距离L。
测量齿轮几何量可以用通用测量工具如公法线千分尺、万能齿轮 测量仪等进行测量,也可以用带表装置进行测量。对于高精度、大批 量精密齿轮的测量可以定做专用检具进行测量,例如气动综合测量仪、 电感综合测微仪等。
3、齿轮M值测量
M值就是齿轮的模数,计算公式为m=d/z,d为分度 圆直径,z为齿数。 为了方便计算,已对齿轮的模数标准化了,可参看国 家标准GB1357-87。外斜齿轮、内斜齿轮的M值计 算,可根据《齿轮手册》公尺计算。 对于齿轮M值的测量,常需要做M值测量检具。获得 参数的方法可以用千分表,更高精度的可以用电动 传感器等。
齿轮测量方法

实验七齿轮测量实验7—1齿轮齿单个齿距偏差与齿距累积总偏差的测量一、实验目的熟悉测量齿轮单个齿距偏差与齿距累积总偏差的方法。
加深理解单个齿距偏差与齿距累积总偏差的定义。
二、实验内容1.用周节仪或万能测齿仪测量圆柱齿轮齿距相对偏差。
2.用列表计算法或作图法求解齿距累积总偏差。
三、测量原理及计量器具说明单个齿距偏差乙,是指在分度圆上,实际齿距与公称齿距之差(用相对法测量时,公称齿距是指所有实际齿距的平均值1齿距累积总偏差F p是指在分度圆上,任意两个同侧齿面间的实际弧长与公称弧长之差的最大绝对值,即最大齿距累积偏差(F p max)与最小齿距累积偏差(F min)之代数差。
在实际测量中,通常采用某一齿距作为基准齿距,测量其余的齿距对基准齿距的偏差。
然后,通过数据处理来求解单个齿距偏差f pt和齿距累积总偏差FP,测量应在齿高中部同一圆周上进行,这就要求保证测量基准的精度。
而齿轮的测量基准可选用齿轮的内孔、齿顶圆和齿根圆。
为了使测量基准与装酉攥准一致,以内孔定位最好。
用齿顶圆定位时,必须控制齿顶圆对内孔的轴线的径向跳动。
在生产中,根据所用量具的结构来确定测量基准。
用相对法测量齿距相对偏差的仪器有周节仪和万能测齿仪。
1.用手持式周节仪测量图1为手持式周节仪的外形图,它以齿顶圆作为测量基准,指示表的分度值为0.005mm,测量范围为模数3—15 mm。
周节仪有4、5和8三个定位脚,用以支承仪器。
测量时,调整定位脚的相对位置,使测量头2和3在分度圆附近与齿面接触。
固定测量头2按被测齿轮模数来调整位置,活动测量头3则与指示表7相连。
测量前,将两个定位脚4、5前端的定位爪紧靠齿轮端面,并使它们与齿顶圆接触,再用螺钉6紧固。
然后将辅助定位脚8也与齿顶圆接触,同样用螺钉固紧。
以被测齿轮的任一齿距作为基准齿距,调整指示表7的零位,并且把指针压缩1 —2圈。
然后,逐齿测量其余的齿距,指示表读数即为这些齿距与基准齿距之差,将测得的数据记入表中。
齿轮测量方法范文

齿轮测量方法范文齿轮是传动机构中常见的一种零件,齿轮的形状和精度对传动系统的性能和寿命有重要影响。
因此齿轮的测量方法是非常重要的,下面将介绍一些常见的齿轮测量方法。
1.外径测量法齿轮的外径是最常见的尺寸要求之一,可以使用千分尺或者游标卡尺等传统测量工具来测量。
2.齿宽测量法齿宽是齿轮的另一个重要尺寸,可以使用游标卡尺或者外径千分尺来测量。
同时还可以使用齿宽测量仪等专用设备来进行更精确的测量。
3.齿顶高测量法齿顶高是齿轮齿形的一个重要参数,可以使用齿顶高测量仪来进行测量。
齿顶高测量仪是一种具有精确导引机构的测量设备,可以保证测量的准确性。
4.齿根高测量法齿根高也是齿轮齿形的一个重要参数,可以使用齿根高测量仪来进行测量。
齿根高测量仪与齿顶高测量仪原理类似,也具有精确导引机构,可以保证测量的准确性。
5.齿距测量法齿轮的齿距也是一个重要参数,可以使用齿距测量仪来进行测量。
齿距测量仪是一种精密的测量设备,可以直接测量出齿轮齿距的大小。
6.模数测量法模数是齿轮的设计参数之一,可以使用模数测量仪来进行测量。
模数测量仪是一种专用的测量设备,可以测量出齿轮的模数大小。
7.齿轮角度测量法齿轮的角度也是一个重要的测量参数,可以使用角度测量仪来进行测量。
角度测量仪可以测量出齿轮的齿轮片角、压力角等角度参数。
需要注意的是,在进行齿轮测量时,应尽量减小人为误差的影响。
可以通过选择合适的测量工具、合理安装工件以及使用专用测量设备等方式来提高测量的准确性。
此外,随着科技的进步,现代化的测量技术也被广泛应用于齿轮测量中。
例如,光电测量技术、激光测量技术等可以提高测量的精度和效率,为齿轮制造提供更加可靠的测量结果。
综上所述,齿轮的测量方法包括外径测量法、齿宽测量法、齿顶高测量法、齿根高测量法、齿距测量法、模数测量法和齿轮角度测量法等。
不同的测量方法适用于不同的齿轮尺寸和形状,选择适合的测量方法可以提高测量的准确性和效率。
同时,现代化的测量技术也为齿轮测量提供了更多的选择和可能性。
齿轮的测绘方法
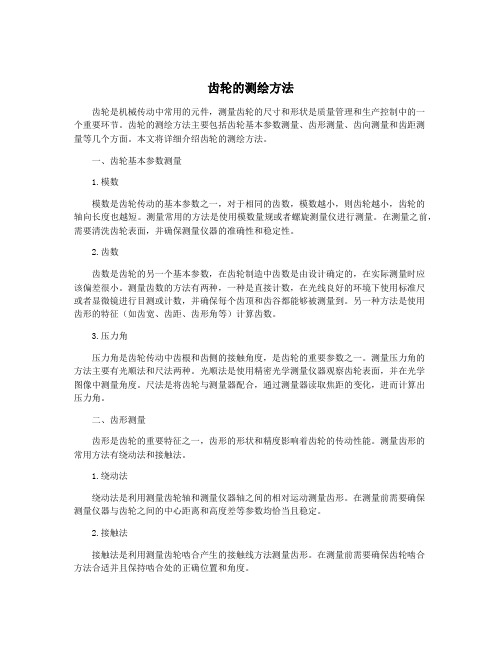
齿轮的测绘方法齿轮是机械传动中常用的元件,测量齿轮的尺寸和形状是质量管理和生产控制中的一个重要环节。
齿轮的测绘方法主要包括齿轮基本参数测量、齿形测量、齿向测量和齿距测量等几个方面。
本文将详细介绍齿轮的测绘方法。
一、齿轮基本参数测量1.模数模数是齿轮传动的基本参数之一,对于相同的齿数,模数越小,则齿轮越小,齿轮的轴向长度也越短。
测量常用的方法是使用模数量规或者螺旋测量仪进行测量。
在测量之前,需要清洗齿轮表面,并确保测量仪器的准确性和稳定性。
2.齿数齿数是齿轮的另一个基本参数,在齿轮制造中齿数是由设计确定的,在实际测量时应该偏差很小。
测量齿数的方法有两种,一种是直接计数,在光线良好的环境下使用标准尺或者显微镜进行目测或计数,并确保每个齿顶和齿谷都能够被测量到。
另一种方法是使用齿形的特征(如齿宽、齿距、齿形角等)计算齿数。
3.压力角压力角是齿轮传动中齿根和齿侧的接触角度,是齿轮的重要参数之一。
测量压力角的方法主要有光顺法和尺法两种。
光顺法是使用精密光学测量仪器观察齿轮表面,并在光学图像中测量角度。
尺法是将齿轮与测量器配合,通过测量器读取焦距的变化,进而计算出压力角。
二、齿形测量齿形是齿轮的重要特征之一,齿形的形状和精度影响着齿轮的传动性能。
测量齿形的常用方法有绕动法和接触法。
1.绕动法绕动法是利用测量齿轮轴和测量仪器轴之间的相对运动测量齿形。
在测量前需要确保测量仪器与齿轮之间的中心距离和高度差等参数均恰当且稳定。
2.接触法接触法是利用测量齿轮啮合产生的接触线方法测量齿形。
在测量前需要确保齿轮啮合方法合适并且保持啮合处的正确位置和角度。
齿向是指齿轮轴线上齿的高度、齿深等参数。
测量齿向的常用方法有直接测量法和间接测量法。
1.直接测量法直接测量法是通过测量齿根和齿顶高度来计算齿向。
齿根与齿顶高度的测量可以使用高度规或退卡尺等测量工具进行。
间接测量法是通过测量与齿向相关的参数来计算齿向,如模距、芝加哥弯曲器测得的齿形角和齿侧角等参数。
齿轮(双啮仪)齿轮的测量
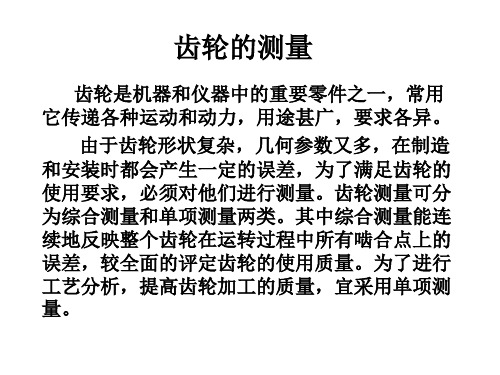
四、实验步骤
1、参看双啮仪简图,把浮动拖板调在中间位置。即转 动(左转)调整手轮约半转,此时浮动拖板处于可左 右转动2毫米的位置上。
2、转动手轮3,移动固定拖板使被测齿轮与测量齿轮 双面啮合为止,并用扳手把固定拖板锁紧。
3、放松手轮,是仪器处于工作状态。
4、在纪录转筒上裹上记录用的坐标纸,利用调位螺钉 将纪录笔调到记录纸的中间位置,并用螺钉将笔尖放 低与记录纸接触。
测量时,用手转动被测齿轮,它的径向误差 因素所显示的双啮中心距的微量变动,转换成浮 动拖板的往复运动,经杠杆机构和绳轮-摩擦轮 系由纪录器画出误差曲线,或由指示表直接表示。
在被测齿轮一转范围内,误差曲线的最高峰 与最低谷间纵坐标之差,或指示表指针正负最大 摆动量的绝对值之和,即为径向综合误差 ;当 被测齿轮每转过一齿时,误差曲线上相邻波峰与 波谷间纵坐标的最大差值,或指示表跟着摆动一 次,在各齿中的最大摆动量为径向一齿误差曲 线。
5、安装指示表,并使指针压缩一圈后对准“零” 位。
6、用手缓慢转动被测齿轮,记录器或指针表及开பைடு நூலகம்始工作。
7、按纪录曲线或指示表读数分别评定径向综合误 差 及径向一齿综合误差 ,并作出结论。
一、实验目的 1、了解双面啮合综合检查仪的测量原理; 2、练习应用双面啮合综合检查仪测量齿轮的径向
综合误差 Fi和径向一齿综合误差 fi; 3、练习分析动态测量的误差曲线。
二、仪器简介
三、仪器的工作原理与读数 被测齿轮与测量齿轮分别装于浮动拖板和固
定拖板的心轴上,两齿轮借弹簧的作用即可实现 双面啮合,又可在测量过程中实现双啮中心距的 变动。
(一)双面啮合综合测量齿轮误差
双面啮合测量齿轮误差是综合测量的一种形 式-将被测齿轮与作为理想精确的测量齿轮作无 侧隙的啮合时,检查它们中心距的的变化来间接 地综合性反映被测齿轮的加工误差。从远离上讲, 双啮合综合测量通常只能反映齿轮误差的径向分 量-几何偏心,以及基节偏差,齿形误差等误差 因素,且测量状态与工作状态不符,测量结果同 时受左右两齿廓误差的影响,因此它的反映不过 全面,也不很客观。但仪器结构简单,造价低, 测量效率高,操作方便。如能预先控制切向误差 分量,双啮仪可在大批量生产检验中检验6以下 中等精度的齿轮。
齿轮工程测量实验报告

齿轮工程测量实验报告实验目的本实验旨在通过测量齿轮的参数,了解和掌握齿轮的测量方法,对齿轮的质量进行评估,提高齿轮加工的精度和质量。
实验仪器与材料- 齿轮测量仪- 卷尺- 千分尺- 轴测仪- 齿轮样品实验原理齿轮是一种常用的传动元件,其质量直接影响到传动效果和传动能力。
齿轮的主要参数包括模数、压力角、齿距、齿宽等。
测量这些参数可以通过齿轮测量仪进行。
实验步骤1. 准备齿轮样品,确保样品无划痕、无损坏。
2. 使用卷尺测量齿轮的齿宽,并记录。
3. 使用千分尺测量齿轮齿距,并记录。
4. 使用轴测仪测量齿轮的压力角并记录。
5. 使用齿轮测量仪测量齿轮的模数,并记录。
6. 根据测量结果,评估齿轮的质量和加工精度。
实验结果与分析我们对多个样品的齿轮进行了测量,并得到以下测量结果:齿轮编号齿宽(mm)齿距(mm)压力角()模数(mm)1 5.23 15.67 20.12 2.002 5.19 15.74 19.98 2.013 5.28 15.58 20.05 2.00通过对实验结果的分析,我们可以发现样品1和样品2的齿宽、齿距、压力角和模数相差较小,可以认为它们的加工质量较高,可以满足实际工作的要求。
而样品3的参数与前两个样品的参数相差较大,说明其质量较差,需要重新评估和调整加工工艺。
实验结论通过本实验,我们学习了齿轮的常见参数测量方法,并对齿轮样品进行了评估。
根据实验结果,我们可以判断齿轮的加工质量和精度,并提出改进意见,以提高齿轮的传动效果和传动能力。
实验心得本实验使我对齿轮的测量方法有了更深入的了解。
在实验过程中,我学会了如何使用不同的测量工具进行齿轮参数的测量,并通过分析结果对齿轮的质量进行评估。
在实验中,我对实验结果进行了合理的分析和总结,并提出了改进意见。
通过这次实验,我不仅学到了实验技巧,更加深了对齿轮工程的认识和理解。
齿轮精度测量方法

齿轮精度测量方法齿轮精度测量方法是齿轮制造和检测领域内至关重要的环节,它直接关系到齿轮产品的质量及其在机械设备中的性能表现。
以下是对齿轮精度测量方法的详细介绍:****齿轮作为传动系统中的基础元件,其精度直接影响到整个机械设备的运行效率和稳定性。
因此,精确测量齿轮的各项精度指标显得尤为重要。
本文将详细阐述齿轮精度的测量方法,以供参考。
**一、齿轮精度测量概述**齿轮精度测量主要包括对齿轮的齿形误差、齿距误差、齿向误差、齿厚误差等指标的检测。
根据测量原理和设备的不同,测量方法可以分为以下几种:**二、展成法**展成法是一种传统的齿轮精度测量方法,利用展成仪或展成尺对齿轮进行测量。
其主要步骤如下:1.将展成仪或展成尺固定在齿轮的一个齿上。
2.沿着齿轮的齿面滑动展成仪,观察展成仪上的指示线与齿轮齿形之间的间隙。
3.通过计算和分析间隙值,得出齿轮的齿形误差、齿距误差等指标。
**三、光学测量法**光学测量法利用光学原理,通过光学显微镜、干涉仪等设备对齿轮进行非接触式测量。
其主要优点是测量精度高、速度快,适用于批量生产。
主要包括以下几种方法:1.齿形测量:利用光学显微镜观察齿轮齿形,通过与标准齿形对比,得出齿形误差。
2.齿距测量:利用干涉仪测量齿轮的齿距误差。
3.齿向测量:通过光学设备测量齿轮齿面的齿向误差。
**四、电感测量法**电感测量法利用电感传感器对齿轮进行非接触式测量,适用于各种齿轮的精度检测。
其主要优点是测量速度快、精度高、可靠性好。
主要包括以下几种方法:1.齿形测量:通过电感传感器检测齿轮齿形,计算得出齿形误差。
2.齿距测量:利用电感传感器测量齿轮的齿距误差。
3.齿厚测量:通过电感传感器测量齿轮的齿厚误差。
**五、综合测量法**综合测量法是将多种测量方法相结合,对齿轮进行全面、精确的测量。
例如,将展成法、光学测量法和电感测量法相结合,以提高测量精度和可靠性。
**六、结论**齿轮精度测量方法的选择应根据实际需求、测量设备条件以及测量精度要求等因素综合考虑。
齿轮测量

理论 弧长 分度圆
First Up Index
16页 第16页
3、齿距累积总偏差 Fp 、 是指齿轮同侧齿面任意弧段( 是指齿轮同侧齿面任意弧段 k=1 至 k=z )内的最大齿 内的最大齿 距累积偏差。它表现为齿距累积偏差曲线的总幅值。 距累积偏差。它表现为齿距累积偏差曲线的总幅值。
Fp
First Up Index
10页 第10页
第Ⅱ公差组项目
1 2 3 4 5
一齿切向综合误差Δf 及公差f 一齿切向综合误差Δfi′及公差fi
′
一齿径向综合误差Δfi″及公差fi ″ 一齿径向综合误差Δf 及公差f 齿形误差Δff及公差ff 齿形误差Δf 及公差f 基节偏差Δfpb及极限偏差± fpb 基节偏差Δf 及极限偏差± 齿距偏差Δf 及极限偏差± 齿距偏差Δfpt及极限偏差± fpt
Fir页
指实际基节与公称基节之差
实际基节
△fpb
公称基节
First
Up
Index
40页 第40页
First
Up
Index
41页 第41页
基节仪测量
测量时先按被测齿轮基节公称值组合量块。 1 测量时先按被测齿轮基节公称值组合量块。 按量块组尺寸调整相应的活动量爪1与固定量爪2之间的距离, 2 按量块组尺寸调整相应的活动量爪1与固定量爪2之间的距离, 使表指零位。 使表指零位。 3 然后将仪器放在被测齿轮 相邻两同侧面上, 相邻两同侧面上,使之与 齿面向切,此时读出表中 齿面向切, 的△fpb值 测量 爪1
18页 第18页
设计齿形可以是修正的理论渐开线,包括修缘 设计齿形可以是修正的理论渐开线, 齿形和凸齿形等 实际齿形
齿顶 齿形工 作部分
齿轮公法线测量方法及计算公式

齿轮公法线测量方法及计算公式嘿,咱今儿就来聊聊齿轮公法线测量方法和计算公式这档子事儿!你说齿轮啊,那可真是机械世界里的小精灵,别看它个头不大,作用可大着呢!就像咱生活中的各种小物件,虽小却不可或缺。
那要怎么知道这齿轮是不是合格呢,这就得靠公法线测量啦!测量齿轮公法线,就好比给齿轮来个全面体检。
咱得先准备好工具,就像医生要有听诊器一样。
然后呢,把齿轮放好,找准测量的位置,这可得仔细着点儿,不能马虎。
你想想,要是找错了地方,那不就跟医生看错了病一样嘛!具体咋测呢?哎呀,其实也不难。
就是用专门的量具,沿着齿轮的齿廓,轻轻地卡一下,读出数值来。
这过程就跟咱平时量身高似的,得站直了,量出来才准呢!那计算公式呢,就像是解开谜题的钥匙。
通过这个公式,咱就能把测量出来的数据转化成有用的信息。
比如说,判断这个齿轮是不是符合标准呀,能不能正常工作呀。
举个例子吧,就好比你有一堆积木,你得按照一定的规则去搭,才能搭出漂亮的城堡。
这公式就是那个规则,让一切都有条不紊。
你可别小看这测量和公式,它们可是保证机器正常运转的关键呢!要是没测好,齿轮出了问题,那机器可不就闹脾气啦,说不定还会罢工呢!想象一下,要是汽车的齿轮出了问题,那车还能跑吗?肯定得抛锚在路上啦!所以啊,这齿轮公法线测量和计算公式,那可真是马虎不得。
咱再深入说说这公式,它就像一个神奇的魔法咒语,能把复杂的数据变得清晰明了。
通过它,咱能知道齿轮的各种参数,就像了解一个人的性格特点一样。
而且啊,这测量和计算可不是一锤子买卖,得反复去做,就像咱每天都要吃饭一样。
只有这样,才能保证齿轮一直健康,机器一直正常工作。
总之呢,齿轮公法线测量方法和计算公式就像是机械世界的秘密武器,掌握了它们,咱就能让齿轮乖乖听话,为我们服务啦!你说是不是很有意思呢?别小瞧这小小的齿轮和它们的测量计算方法,这里面的学问可大着呢!。
直齿齿轮的测绘方法

直齿齿轮的测绘方法光电测量法是利用光电子技术测量直齿齿轮的尺寸和形状的一种方法。
该方法主要包括光学测量和光电测量两种方法。
光学测量是利用光学仪器测量直齿齿轮的尺寸和形状。
首先,使用显微镜和光纤测距仪等光学仪器观察和测量齿轮的外径、内径、齿高、齿厚等尺寸,并利用该方法直接测量齿形误差、齿向误差、法兰误差、中心距误差等。
光电测量是通过光电子技术测量直齿齿轮的尺寸和形状。
首先,使用测量机、编码器、光栅尺等光电子仪器观察和测量齿轮的外径、内径、模数、压力角等尺寸,并利用该方法计算齿形误差、齿向误差、法兰误差、中心距误差等。
机械测绘法是利用机械测量仪器测量直齿齿轮的尺寸和形状的一种方法。
该方法主要包括制面测量法、镜像测量法和三坐标测量法等。
制面测量法是通过制作满足特定要求的齿轮模板和制面样板,将其与待测齿轮进行比对,通过对比得出齿轮的尺寸和形状。
这种方法一般适用于小型齿轮的测量。
镜像测量法是通过齿轮的镜像与标准镜像进行比对,从而测量齿轮的尺寸和形状。
该方法主要适用于大型齿轮的测量。
三坐标测量法是利用三坐标测量仪测量直齿齿轮的三维坐标数据,并通过数学模型计算齿轮的尺寸和形状。
该方法适用于任何尺寸的齿轮测绘。
数值测绘法是利用计算机辅助设计和制造技术测绘直齿齿轮的尺寸和形状。
该方法主要包括数值测绘仪器和软件的应用。
通过计算机图形处理和模拟仿真,可以准确快速地测绘齿轮的尺寸和形状。
总之,直齿齿轮的测绘方法有光电测量法、机械测绘法和数值测绘法等多种方法,可以根据需要选择合适的方法进行测绘。
齿轮的测量方法

齿轮的测量方法齿轮是在机械、汽车、飞机、仪器仪表等中都有重要的应用,他的精度对传递运动的精度、平稳性、效率等有重要的影响,需要检验的参数有齿形(汗压力角)、周节、齿向、径向跳动等。
齿轮的测量方法直接决定齿轮测量出来的结果的精度,下面是几种常见的测量方法:一、CNC测量这类仪器实质上是含有一个回转角坐标的四坐标测量机,主要用于齿轮单项几何精度的检测,也可用于(静态)齿轮整体误差的测量。
工作方式是通过接口或网络的信息集成,将测量机、锥齿轮设计及锥齿轮加工机床连接一起,构建成锥齿轮闭环制造系统,还能用于反求工程对工件参数进行测定。
缺点:价格昂贵。
另,CNC测量方法只能用于量测齿轮。
二、齿轮单面啮合滚动点扫描测量仪这类仪器通常采用高精度圆光栅作为角度传感器,测量基本单元是齿轮上特制的测量棱线,分别为齿廓测量棱线和齿向(螺旋线)测量棱线。
测量重复性可达1至2μm,可测量锥齿轮的齿形、齿向、齿距偏差,齿面形貌偏差,切向综合偏差以及接触区。
缺点:这类仪器市场价格相对较高。
另,仪器对环境要求太高,稍有变化,精度就受影响。
三、齿轮在线测量分选机这类仪器主要应用于批量生产汽车轿车齿轮质量的最终检测,适用于车间现场,能满足批量生产汽车齿轮在线检测和自动分选的要求。
测量时可使用不同工装夹具,可分别对内、外齿轮,盘、轴齿轮进行测量。
配有数据处理系统和SPC统计分析软件,能对齿轮加工过程和工艺状况进行监测和预报。
缺点:这类仪器重复精度相对稍差,在选用上要特别注意。
四、激光齿轮测量仪这类仪器通常采用高精度气浮主轴,气浮导轨,还采用激光测长系统进行齿面精度检测。
这类仪器的测量精度和重复精度一般标称是0.2至0.3μm。
由于采用激光非接触测量方式,仪器可以测量齿面上非渐开线齿根部分几何形状,一般配置的软件可以模拟求得被测齿轮与其配对齿轮啮合时的传动误差并进行分析,所测数据和分析数据还可通过LAN共享。
缺点:价格昂贵、适用范围太窄。
齿轮精度测量方法

齿轮精度测量方法全文共四篇示例,供读者参考第一篇示例:齿轮的精度测量是指通过一系列的测量测试,来检测齿轮的各项关键参数,包括齿轮齿面的精度、齿轮的齿数、齿间隙等。
通过这些测量数据,我们可以判断齿轮是否符合设计要求,是否能够正常工作。
在进行齿轮精度测量之前,首先需要准备好相应的测量仪器和设备,例如齿轮测量器、光学投影仪、三坐标测量仪等。
同时还需要准备标准的测量标尺和量块等工具,以确保测量结果的准确性和可靠性。
在进行齿轮精度测量时,首先需要对齿轮进行表面清洁和检查,确保没有污垢和损坏。
然后进行齿面精度测量,通常采用的方法有光学投影测量和触发式测量。
在测量过程中,需要确保测量仪器的准确性和稳定性,以避免误差的产生。
除了齿面精度测量,还需要对齿轮的齿数和齿间隙等参数进行检测。
对于齿数的测量,可以采用标准的齿轮量块进行比对测量,以确保齿轮的齿数符合设计要求。
对于齿间隙的测量,可以采用测微计或者三坐标测量仪等设备进行测量,以保证齿轮的齿间隙符合要求。
在进行齿轮精度测量时,需要注意以下几点:1. 测量时需保持仪器的准确性和稳定性,避免误差的产生;2. 应该进行多次重复测量,以提高结果的可靠性;3. 测量后需要及时记录和分析数据,及时发现问题并进行纠正。
齿轮精度测量是一项复杂而重要的工作,需要仪器设备和专业知识的支持。
只有通过科学的测量和检测,我们才能确保齿轮的质量和精度,提高机械设备的工作性能和使用寿命。
希望以上内容对您有所帮助。
第二篇示例:齿轮是机械传动中常见的零部件,其精度对机械设备的运转性能和寿命有着重要影响。
对齿轮的精度进行准确的测量是非常重要的。
齿轮精度测量方法有许多种,本文将重点介绍几种常用的方法。
一、摆线齿轮精度测量方法摆线齿轮是机械传动中常用的一种齿轮,其齿轮精度的测量方法主要包括齿顶间隙、齿顶偏距和变位测量。
齿顶间隙是指两个齿顶之间的最小距离,可以用齿轮齿节测量器进行测量。
齿顶偏距是指齿轮齿面上各齿的齿顶点与理论齿顶轨迹的最大偏离值,可以用齿轮齿顶偏差仪进行测量。
齿轮测量方法

齿轮测量方法
嘿,齿轮测量方法呀,这事儿其实不难。
首先呢,你得有个齿轮摆在那儿。
咱先看看这齿轮的外观,有没有缺牙少角的地方。
要是有,那可不行哦,就像人掉了牙似的,不好看还不好用。
然后呢,拿个尺子量量齿轮的直径。
这直径可重要啦,要是大小不对,装到机器里说不定就卡壳啦。
量的时候仔细点,别量错了,不然可就麻烦了。
接着呢,数数齿轮的齿数。
这就跟数手指头似的,一个一个地数清楚喽。
齿数不对的话,和别的齿轮配合起来也不顺畅。
再看看齿轮的齿形。
这齿形得规整,不能歪歪扭扭的。
要是齿形不好,转起来就不平稳,会发出奇怪的声音。
“哎呀,那声音可难听了。
”
还有啊,得检查一下齿轮的齿距。
齿距要是不均匀,转起来也会不顺畅。
可以用个小工具,比如卡尺啥的,量量相邻两个齿之间的距离。
咱还可以把两个齿轮放在一起转一转,看看配合得好不好。
要是转起来很费劲,或者有卡顿的地方,那就得找找问题啦。
我给你讲个事儿吧。
有一次,我朋友的工厂里有个机器坏了,找了半天原因,最后发现是齿轮的问题。
他们一开始没注意齿轮的测量,随便装了个齿轮上去。
结果机器转起来一会儿快一会儿慢,还发出很大的噪音。
后来他们找来了专业的人,用各种方法测量齿轮,才发现那个齿轮的齿距不均匀,齿数也不对。
换了个合适的齿轮后,机器就正常运转啦。
“嘿,这齿轮可不能马虎啊。
”
总之呢,测量齿轮要仔细,外观、直径、齿数、齿形、齿距都得注意到。
这样才能保证齿轮好用,机器也能正常运转。
- 1、下载文档前请自行甄别文档内容的完整性,平台不提供额外的编辑、内容补充、找答案等附加服务。
- 2、"仅部分预览"的文档,不可在线预览部分如存在完整性等问题,可反馈申请退款(可完整预览的文档不适用该条件!)。
- 3、如文档侵犯您的权益,请联系客服反馈,我们会尽快为您处理(人工客服工作时间:9:00-18:30)。
/doc/view/31109.html收藏词条编辑词条齿轮测量创建时间:2008-08-02齿轮测量gear measurement图片:图片:图片:chilunceliang齿轮测量(卷名:机械工程)gearmeasurement长度计量技术中对齿轮参数的测量。
测量圆柱齿轮和圆锥齿轮误差的方法有单项测量和综合测量两种。
单项测量主要是测量齿形误差、周节累积误差、周节偏差、齿向误差和齿圈径向跳动等。
齿形测量图1为齿轮齿形测量的原理。
常用的测量方法有展成法和坐标法。
①展成法:基圆盘的直径等于被测渐开线理论基圆直径。
当直尺带动与它紧密相切的基圆盘和与基圆盘同轴安装的被测齿轮转动时,与直尺工作面处于同一平面上的测量杠杆的刀口相对于被测齿轮回转运动的轨迹是一理论渐开线。
以它与被测渐开线齿形比较,即可由测微仪(见比较仪)指示出齿形误差。
利用此法测量齿形误差的工具有单盘渐开线测量仪和万能渐开线测量仪(见渐开线测量仪)。
②坐标法:按齿形形成原理列出齿廓上任一点的坐标方程式,然后计算出齿廓上若干点的理论坐标值,以此与实际测得的被测齿形上相应点的坐标值比较,即可得到被测齿形误差。
有直角坐标法和法线展开角坐标法两种。
前者的测量原理是被测齿廓上各点的坐标值(x、y)分别由X和Y方向的光栅测量系统(见光栅测长技术)测出,经电子计算机计算后得出齿形误差。
此法适用于测量大型齿轮的齿形。
法线展开角坐标法用于测量渐开线齿形。
当与被测齿轮同轴安装的圆光栅转动一个展开角φ时,由长光栅测量系统测出被测渐开线基圆的展开弧长ρ,由电子计算机按计算式ρ=r0φ(式中r0为基圆半径)计算出被测弧长与理论弧长之差值。
按需要在齿廓上测量若干点,由记录仪记录出齿形误差曲线图。
周节测量图2为齿轮周节测量的原理。
周节测量有绝对测量法和相对测量法。
①绝对测量法:被测齿轮与圆光栅长度传感器同轴安装。
测量时,被测齿轮缓慢回转,当电感式长度传感器的测头与齿面达到预定接触位置时,电感式长度传感器发出计数开始信号,利用电子计算机计算由圆光栅长度传感器发出的经过处理后得到的电脉冲数,直至测头与下一齿面达到预定接触位置为止。
如此逐齿进行,测出相当于各实际周节的电脉冲数,经电子计算机处理后即可得出周节偏差和周节累积误差。
②相对测量法:利用两电感式长度传感器的测头安置组成相当于被测齿轮任一实际周节,以此逐齿与所有其他各实际周节比较。
测得的差值经过电子线路和电子计算机处理,即可得出周节偏差和周节累积误差。
齿向测量图3为齿轮齿向测量的原理。
齿向测量常用的有导程法和基圆螺旋角法。
这两种方法都是根据斜齿轮回转一周,与齿面接触的任一点沿轴向移动一个导程的原理。
①导程法:当滑架沿轴线方向移动时,安装在滑架上的正弦尺推动直尺并带动圆盘和与圆盘同轴安装的被测齿轮转动。
正弦尺的倾斜角度是按计算导程的方法调整的,测量头相对于被测齿轮作螺旋运动而测出齿向误差。
②基圆螺旋角法:在渐开线测量仪上增加度盘、测角读数显微镜(图中未表示)等进行测量。
当直尺带动基圆盘和被测齿轮转动时,电感式长度传感器的测头由固定在直尺上的滑块和滑架圆盘上倾斜的直槽控制着向下移动。
利用度盘等使直槽的倾斜角度等于被测齿轮的基圆螺旋角,因此测头相对于被测齿轮作螺旋运动而测出齿向误差。
采用此法的齿轮测量工具通常称为渐开线和螺旋线测量仪。
20世纪70年代初,开始利用长光栅(或激光)、圆光栅等组成的测量系统、电子计算机自动控制系统和数据处理系统等组成的自动测量系统,在同一台齿轮量仪上测量齿向误差,齿形误差和周节偏差等。
直齿圆柱齿轮的齿向误差也常在具有精密直线导轨的齿圈径向跳动仪上测量。
齿圈径向跳动测量以被测齿轮轴心线定位,利用带有球形测头或锥角等于2倍齿形角的圆锥形测头的测微仪,使测头位于齿高中部与齿廓双面接触。
测头相对于齿轮轴心线的最大变动量即齿圈径向跳动。
测量齿圈径向跳动的仪器是齿圈径向跳动仪。
综合测量通过测量齿轮与被测齿轮啮合传动来测量齿轮的传动精度。
测量齿轮是一种精度比被测齿轮高两级以上的齿轮,也有以测量蜗杆代替测量齿轮的。
综合测量有双面啮合法和单面啮合法两种。
①双面啮合法:利用测量齿轮与被测齿轮作双面啮合转动,以被测齿轮转动一转内的中心距最大变动量表示被测齿轮的径向综合误差。
利用此法的齿轮测量工具称为齿轮双面啮合检查仪(见齿轮综合检查仪)。
②单面啮合法:利用测量齿轮与被测齿轮在公称中心距下啮合转动,以转角误差形式表示被测齿轮的切向综合误差。
采用此法的齿轮测量工具有齿轮单面啮合检查仪和齿轮单面啮合整体误差测量仪(见齿轮整体误差测量技术)。
综合测量还可用于检查齿轮副接触斑点和噪声等。
对于圆锥齿轮,一般采用综合测量,以检验齿轮副的接触斑点为主,也有测量齿轮副径向综合误差、齿轮副切向综合误差和噪声的。
单项测量一般是测量周节累积误差和齿圈径向跳动,测量方法与圆柱齿轮的相同,但要保持测量头轴线垂直于圆锥素线。
70年代后期,人们开始利用三坐标测量机测量圆锥齿轮的齿形,并用绘图仪描绘出被测齿面的轮廓图形。
/content/wjzx/2009/2/12/105679.shtml齿轮测量技术100年的回顾与展望来源:网络来源日期:2009-2-12 点击:2141起源与历程齿轮的应用有着悠久的历史,而齿轮的科学研究却始于17世纪M1Camus发现齿轮传动的节点原理;1765年,LlEuler将渐开线齿形引入齿轮,100多年后,Fellows等人应用范成法高效地生产出渐开线齿轮,从此渐开线齿轮得到了广泛应用。
由于制造与安装等方面的原因,实际齿轮总是存在着误差。
这种误差对传动系统的精度与动态特性(特别是振动与噪声)有直接的影响。
因此,如何表征、测量、分析、利用和控制齿轮误差一直是不断探索的课题。
齿轮测量的基础是齿轮精度理论。
齿轮测量技术的发展历程是以齿轮精度理论的发展为前提的。
齿轮精度理论的发展实质上反映了人们对齿轮误差认识的深化。
迄今,齿轮精度理论经历了齿轮误差几何学理论、齿轮误差运动学理论和齿轮误差动力学理论的发展过程。
其中,齿轮误差动力学理论还处在探索中。
第一种理论将齿轮看作纯几何体,认为齿轮是一些空间曲面的组合,任一曲面都可由三维空间中点的坐标来描述,实际曲面上点的位置和理论位置的偏差即为齿轮误差。
第二种理论将齿轮看作刚体,认为齿轮不仅仅是几何体,也是个传动件,并认为齿轮误差在啮合运动中是通过啮合线方向影响传动特性的,因此啮合运动误差反映了齿面误差信息。
第三种理论将齿轮看作弹性体,对齿廓进行修形,“有意地”引入误差,用于补偿轮齿承载后的弹性变形,从而获取最佳动态性能,由此形成了齿轮动态精度的新概念。
齿轮精度理论的发展,导致了齿轮精度标准的不断丰富和更新,如传动误差、设计齿廓的引入等。
反过来,齿轮测量技术的发展也为齿轮精度理论的应用和齿轮标准的贯彻提供了技术支撑。
齿轮测量技术及其仪器的研发已有近百年的历史。
在这不短的发展历程中,有6件标志性事情:1)1923年,德国Zeiss公司在世界上首次研制成功一种称为“ToothSurfaceTester”的仪器,它实际上是机械展成式万能渐开线检查仪。
在此基础上经过改进,Zeiss公司于1925年推出了实用型仪器,并投入市场。
该仪器的长度基准采用了光学玻璃线纹尺,其线距为1μm。
该仪器的问世,标志着齿轮精密测量的开始。
在我国得到广泛使用的VG450就是该仪器的改进型。
2)50年代初,机械展成式万能螺旋线检查仪的出现,标志着全面控制齿轮质量成为现实。
3)1965年,英国研制出光栅式单啮仪,标志着高精度测量齿轮动态性能成为可能。
4)1970年,以黄潼年为主的中国工程师研发的齿轮整体误差测量技术,标志着运动几何法测量齿轮的开始。
5)1970年,美国Fellows公司在芝加哥博览会展出Microlog50,标志着数控齿轮测量中心的开始。
6)80年代末,日本大阪精机推出基于光学全息原理的非接触齿面分析机FS-35,标志着齿轮非接触测量法的开始。
2齿轮测量技术的演变整体上考察过去一个世纪里齿轮测量技术的发展,主要表现在三个方面[8]:1)在测量原理方面,实现了由“比较测量”到“啮合运动测量”,直至“模型化测量”的发展。
2)在实现测量原理的技术手段上,历经了“以机械为主”到“机电结合”,直至当今的“光-机-电”与“信息技术”综合集成的演变。
3)在测量结果的表述与利用方面,历经了从“指示表加肉眼读取”,到“记录器记录加人工研判”,直至“计算机自动分析并将测量结果反馈到制造系统”的飞跃。
与此同时,齿轮量仪经历了从单品种单参数仪器(典型仪器有单盘渐开线检查仪),单品种多参数仪器(典型仪器有齿形齿向检查仪),到多品种多参数仪器(典型仪器有齿轮测量中心)的演变。
2.1机械展成式测量技术20世纪70年代以前,齿轮测量原理主要以比较测量为主,其实质是相对测量。
具体方式有两种:一是将被测齿轮与一标准齿轮进行实物比较,从而得到各项误差;二是展成测量法,就是将仪器的运动机构形成的标准特征线与被测齿轮的实际特征线作比较,来确定相应误差;而精确的展成运动是借助一些精密机构来实现的。
不同的特征线需要不同的展成机构,同一展成运动可用不同的机械结构来实现。
比较测量的主要缺点是:测量精度依赖于标准件或展成机构的精度,机械结构复杂,柔性较差,同一个齿轮需要多台仪器测量。
从20世纪20年代至60年代末,各国对机械展成式测量技术的研究历经了近半个世纪。
早期着重于渐开线展成测量技术的研究,后来将展成测量思想移植到了螺旋线测量上,先后开发出多种机械式渐开线展成机构,如单盘式、圆盘杠杆式、正弦杠杆式、靠模式等。
尤以圆盘杠杆式应用最广,属于这一类的仪器有:ZeissVG450,CarlMahr890和891S,MAAGSP60和HP100,大阪精机GC-4H和GC-6H以及哈量3201。
对于齿廓误差测量而言,机械展成式测量技术仅限于渐开线齿廓误差测量上。
对于非渐开线齿轮的端面齿廓测量,采用展成法测量是十分困难的,因为展成机构太复杂并且缺乏通用性。
对于精确的螺旋展成机构,主要采用正弦尺原理,只是如何将正弦尺的直线运动精确地转换为被测工件的回转运动的方式各不相同。
这种机构在滚刀螺旋线测量上应用最为典型,例如,德国Fette 公司生产的UWM型滚刀测量仪,Zeiss厂生产的万能滚刀测量仪,前苏联ВНИИ设计的万能型滚刀测量仪,意大利Samputensili厂的Su-130型滚刀测量仪,美国Michigan公司生产的万能滚刀测量仪,Klingelnberg公司的PWF250/300,等等。
20世纪70年代以前,机械展成式测量技术已经发展成熟,并在生产实践中经受了考验。
迄今,基于这些技术的仪器仍是一些工厂检测齿轮的常用工具。