零件加工检验表
零件及部件加工检验批质量验收记录

零件及部件加工检验批质量验收记录编号:
填表说明:
1、检验批容量填写: 同一检验批内,填写构件的总数
2、最小/实际检查数量栏中,实际检查数量:按实填写且不少于最小数量。
1)材料进场:质量证明文件全数检查;抽样数量按进场批次和产品的抽样检验方案确定。
2)2~5:全数检查。
3)螺栓球、焊接球加工:每种规格抽查 5%, 且不应少于3个。
4)制孔:按钢构件数量抽查 10%, 且不应少于3件。
5)材料规格尺寸:全数检查。
6)钢材表面质量:全数检查。
7)切割精度:按切割面数抽查 10%, 且不应少于3个。
8)矫正质量:全数检查。
9)边缘加工精度:按加工面数抽查 10%, 且不应少于3个。
10)螺栓球、焊接球加工精度:每种规格抽查 5%, 且不应少于3个。
11)管件加工精度:按杆件数抽查 10%, 且不应少于3个。
12)制孔精度:按规格抽查 10%, 且不应少于3个。
表头中“施工依据”栏目应依照实
际的施工操作依据填写,如施工企业的操作规程、工法、施工工艺标准。
钢构件(单节、多节钢柱)组装检验批质量验收记录编号:。
机械零件质量检验报告表模板

机械零件质量检验报告表模板【中英文实用版】英文文档内容:Mechanical Part Quality Inspection Report TemplateIntroduction:This report template is designed to provide a comprehensive overview of the quality inspection process for mechanical parts.It includes essential details such as the part number, inspection date, and inspector"s name.The template also lists the specific criteria and standards that the parts are evaluated against, including dimensional accuracy, material specifications, and surface finish.sections:1.Part Identification:- Part Number: [Insert Part Number]- Description: [Insert Part Description]- Manufacturer: [Insert Manufacturer Name]- Lot/Serial Number: [Insert Lot/Serial Number]2.Inspection Date:- [Insert Inspection Date]3.Inspector"s Name:- [Insert Inspector"s Name]4.Inspection Criteria:- Dimensional Accuracy: [Insert applicable standards and tolerances]- Material Specifications: [Insert applicable material standards and requirements]- Surface Finish: [Insert applicable surface finish standards and requirements]- Other: [Insert any other relevant inspection criteria]5.Inspection Results:- [Insert detailed description of inspection results, including any deviations from the specified criteria]6.Conclusion:- [Insert conclusion statement regarding the overall quality of the parts]- [Insert any necessary recommendations or corrective actions]7.Signatures:- [Insert Inspector"s Signature]- [Insert Supervisor"s Signature]- [Insert Date]ote: This template can be customized to meet specific company or project requirements.中文文档内容:机械零件质量检验报告模板引言:本报告模板旨在提供关于机械零件质量检验过程的全面概述。
机械零件加工验收检验记录

NO:
加工商
北京机械有限责任公司
零件名称
图 纸
编 号
检验依据
数 量
检 验
日 期
序号检验项目技 术 求检验规则实测记录
合格勾选
备 注
1
零件材质
图纸要求
目测
2
零件数量
内容、数量、规格、性能应符合要求
全检
3
零件外观
表面应光洁无划痕、污渍等;
目测
4
外形尺寸
外形尺寸应符合图纸要求
测量
5
关键安装孔
是否符合
公差要求
游标卡尺测量
6
关键轴径
是否符合
公差要求
游标卡尺测量
7
线性尺寸
是否符合
公差要求
游标卡尺测量
结论:
检验员:复核:
调机首件检验记录表

目
1
2
3
SIP要求检验项目
检测结果 1
检测结果2
检测结果 3
备注
结果判定: 本批生产 其它说明:
□首件合格,可以正式生产
检验 员:
完成时 间:
□首件不合格,须要重新调机
□特采,限
确认 人:
确认时 间:
调机首件检验记录表
日期:
班次:
机床号:
生产调机员填写: 物料编 码:
零件名 称:
零件图 号:
零件批 号:
版本:
生产单号:
加工工序:
详细送检时间:
SOP要求检验项 测量结果 测量结果 测量结果
目
1
2
3
SOP要求检验项目
测量结果 1
测量结果2
测量结果 3
品质检验填写:
SIP要求检验项 检测结果 检测结果 检测结果
钢零部件加工检验批质量验收记录

C7陕西省建设工程质量验收技术资料统一用表检验批质量验收记录表钢零部件加工检验批质量验收记录Ⅱ一般项目7.4.2边缘加工允许偏差应符合表7.4.2的规定。
7.2.2气割的允许偏差应符合表7.2.2的规定。
检查数量:按切割面数抽查10%,且不应少于3个。
检验方法:观察检查或用钢尺、塞尺检查。
7.2.3机械剪切的允许差应符合7.2.3的规定.检查数量:按切割面数抽查10%,且不应少于3个。
检验方法:观察检查或用钢尺、塞尺检查。
7.3矫正和成型Ι主控项目7.3.1碳素结构钢在环境温度低于-16°C、低合金结构钢在环境温度低于-12°C时,不应进行冷矫正和冷弯曲。
碳素结构钢和低合金结构在加热矫正时,加热温度不应超过900°C。
低合金结构钢在加热矫正后应自然冷却。
检查数量:全数检查。
检验方法:检查制作工艺报告和施工记录。
7.3.2当零件采用热加工成型时,加热温度应控制在900-1000°C;碳素结构钢和低合金结构钢在温度分别下降到700°C和800°C之前,应结束加工;低合金结构钢应在自然冷却。
检查数量:全数检查。
检验方法:检查制作工艺报告和施工记录。
Ⅱ一般项目7.3.3矫正后的钢材表面,不应有明显的凹面或损伤,划痕深度不得大于0.5 mm,且不应大于该钢材厚度负允许偏差的1/2。
检查数量:全数检查。
检验方法:观察检查和实测检查。
7.3.4冷矫正和冷弯曲的最小曲率半径和最大弯曲矢高应符合表7.3.4(略)的规定。
检查数量:按冷矫正和冷弯曲的件数抽查10%,且不少于3个。
检验方法:观察检查和实测检查。
7.3.5钢材矫正后的允许偏差,应符合表7.3.5(略)的规定。
检查数量:按矫正件数抽查10%,且不应少于3件。
检验方法:观察检查和实测检查。
7.4边缘加工I主控项目7.4.1气割或机械剪切的零件,需要进行边缘加工时,其刨削量不应小于2.0mm。
过程检验记录表
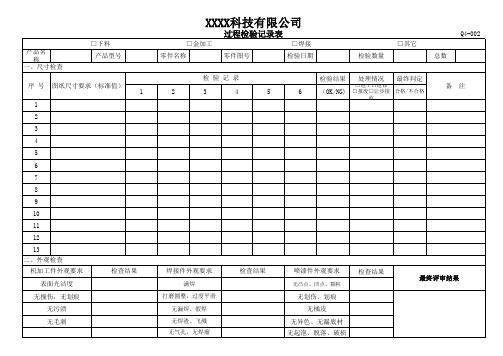
Q4-002 □焊接 □其它 检验数量 检验结果 处理情况
□返工□返修 收
□金加工 零件名称 零件图号
产品型号
检验日期
总数 最பைடு நூலகம்判定 备 注
图纸尺寸要求(标准值)
1
2
3
4
5
6
(OK/NG) □报废□让步接 合格/不合格
检查结果
喷漆件外观要求
无凸点、凹点、颗粒
检查结果
最终评审结果
无划伤、划痕 无橘皮 无异色、无漏底材 无起泡、脱落、破损
XXXX科技有限公司
过程检验记录表
□下料 产品名称 一、尺寸检查 检 验 记 录 序 号 1 2 3 4 5 6 7 8 9 10 11 12 13 二、外观检查 机加工件外观要求 表面光洁度 无撞伤,无划痕 无污渍 无毛刺 检查结果 焊接件外观要求
满焊 打磨圆整,过度平滑 无漏焊、假焊 无焊渣、飞溅 无气孔,无焊瘤
钢结构工程检验批质量验收记录表
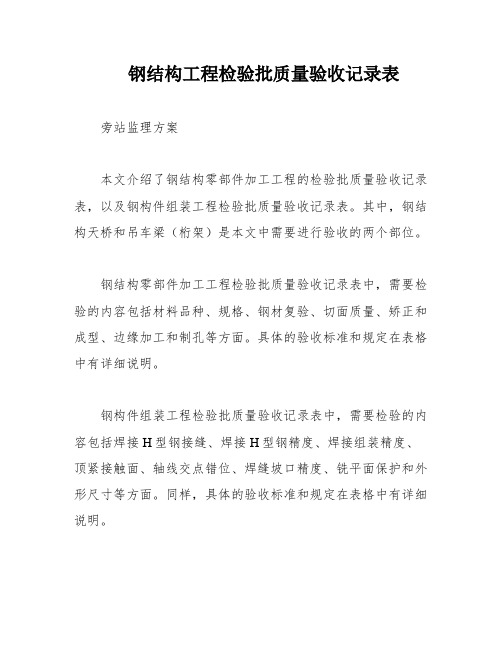
钢结构工程检验批质量验收记录表旁站监理方案本文介绍了钢结构零部件加工工程的检验批质量验收记录表,以及钢构件组装工程检验批质量验收记录表。
其中,钢结构天桥和吊车梁(桁架)是本文中需要进行验收的两个部位。
钢结构零部件加工工程检验批质量验收记录表中,需要检验的内容包括材料品种、规格、钢材复验、切面质量、矫正和成型、边缘加工和制孔等方面。
具体的验收标准和规定在表格中有详细说明。
钢构件组装工程检验批质量验收记录表中,需要检验的内容包括焊接H型钢接缝、焊接H型钢精度、焊接组装精度、顶紧接触面、轴线交点错位、焊缝坡口精度、铣平面保护和外形尺寸等方面。
同样,具体的验收标准和规定在表格中有详细说明。
在进行验收时,需要由专业工长(施工员)进行检查评定,并由施工单位进行检查评定记录。
如果符合验收标准和规定,则为合格,否则为不合格。
最后,本文提供了监理(建设)单位验收结论的空白表格,需要由专业监理工程师进行填写,并由建设单位项目专业技术负责人进行签字确认。
总之,本文提供了一份完整的钢结构零部件加工工程和钢构件组装工程的验收记录表格,有助于确保工程质量的合格性。
项目经理XXX加强分包项目经理施工执行标准名称及编号为《钢结构工程施工质量验收规范》(GB-2001)。
其中,多层板叠螺栓孔第9.2.1条规定施工单位检查评定记录监理(建设)单位验收记录通过率应达标。
经检查,主控项目符合要求,一般项目抽样检查均符合设计及规范要求。
针对涂料性能第4.9.1条,涂装基层验收、涂层厚度、涂料质量、表面质量、附着力测试、标志等方面的验收,施工单位检查评定记录应符合设计标准要求。
经检验,涂层符合要求,无结皮、结块、误涂、漏涂,标志清晰。
施工班组长表示主控项目检验合格,一般项目抽样检验符合设计及规范要求。
针对钢结构防火涂料涂装工程的验收,施工单位检查评定记录应符合《钢结构工程施工质量验收规范》(GB-2001)的规定。
涂层表面质量的验收应符合第14.3.6条。
机械加工检验记录表
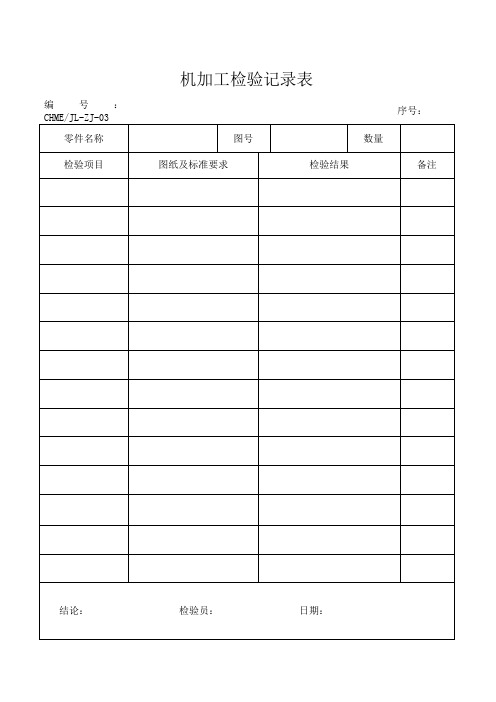
(4)氧气瓶氧气泄露或爆炸事故;
(5)起重设备伤害事故;
(6)厂房设施倒塌伤人事故。
(7)放射性、中暑、窒息、急性中毒事故。
(8)其他性质较为严重、产生较大社会影响的安全生产事故。
1.4应急预案体系
机械加工企业安全生产事故应急预案体系包括:
综合应急预案一个:《机械加工企业厂安全生产事故综合应急预案》;
(5)《锅炉压力容器事故应急处置方案》;
(6)《危险(油或化工)库房事故应急处置方案》
(7)《安全生产事故医疗救护现场处置方案》。
机械加工企业安全生产事故应急预案体系示意图(略)。
1.5工作基本原则
应急工作坚持以人为本、安全第一;统一指挥,分级负责;依靠科学,依法规范;预防为主,平战结合的基本原则。
2.3.5火灾事故
机械加工企业生产加工车间或办公场所使用的取暖设备(火炉或电炉)失火,或热加工车间(铸造、锻造、热处理)及电炉等设备因由有高温使用不当发生火事故等。
2.3.6厂房设施倒塌伤人事故
机械加工企业的生产加工车间厂房设施因使用年久老化失修造成坍塌伤人事故等。
专项应急预案三个:
(1)《机械加工设备事故专项应急预案》;
(2)《起重设备事故专项应急预案》;
(3)《火灾专项事故应专项急预案》。
现场处置方案十一个:
(1)《热加
(3)《厂房设施倒塌事故现场处置方案》;
(4)《电气设备漏电及触电事故现场处置方案》;
(4)预防为主,平战结合。贯彻落实“安全第一、预防为主、综合治理”的方针,做好预防、预测、预警和预报工作,做好事故风险评估、救援物资储备、应急队伍建设、应急装备完善、定期进行预案演练等工作,提高企业应对各类事故的整体能力。
2024年金属切削机床磨削加工安全检查表

2024年金属切削机床磨削加工安全检查表编号:xxxx-xx-xxxx
日期:____年
一、基本信息:
1. 设备名称:
2. 设备型号:
3. 设备编号:
4. 检查人员:
5. 检查日期:
二、安全防护措施:
1. 设备是否配备全封闭防护罩,罩门是否完好:是/否
2. 是否安装安全门开关,门是否能正常关闭:是/否
3. 控制系统是否具备紧急停机按钮,按钮是否能正常工作:是/否
三、设备运行状况:
1. 设备外观是否整洁无损,有无漏油脱落等现象:是/否
2. 设备电源插头是否接地可靠:是/否
3. 设备电气系统是否正常运行,线路是否有漏电带电现象:是/否
四、刀具和磨削部分:
1. 刀具是否完好无损:是/否
2. 切削液供给系统是否正常:是/否
3. 磨削部分是否松动或缺失:是/否
4. 机床滑动部位是否润滑良好:是/否
五、操作人员安全:
1. 操作人员是否穿戴个人防护装备(安全眼镜、耳塞等):是/否
2. 操作人员是否熟悉设备操作规程:是/否
3. 操作人员是否经过安全培训:是/否
4. 操作人员是否注意机床运行状况,及时发现异常并采取相应措施:是/否
六、应急救援设施:
1. 设备周围是否设有灭火器、灭火器是否在有效期内:是/否
2. 是否配备急救箱,急救箱内药品是否完整有效:是/否
3. 是否设有紧急电话和急救电话:是/否
七、其他安全问题:
(备注栏)
备注:
(填写对设备存在问题的具体描述和处理措施)
以上为金属切削机床磨削加工安全检查表,共____字。
五金行业来料检验报告表单
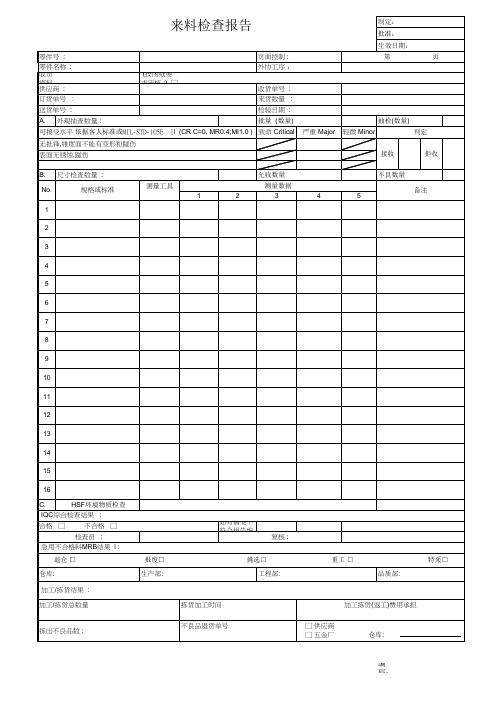
零件号 :
页面控制 :
零件名称 : 收货 资料 供应商 :
(按图纸要 求审核 :) □
外协工序 : 收货单号 :
订货单号 :
来货数量 :
送货单号 :
检验日期 :
A. 外观抽查数量 :
批量 (数量)
可接受水平 依据客人标准或MIL-STD-105E Il (CR C=0, MR0.4;MI1.0 ) 致命 Critical
退仓 □
仓库:
加工/拣货结果 :
加工/拣货总数量
测量工具 1
允收数量
测量数据
2
3
报废□ 生产部:
如有需要不 符合报告编
复核 :
挑选□ 工程部:
拣货加工时间
不良数量
4
5
备注
重工 □
品质部:
特采□
加工拣货(返工)费用承担
拣出不良品数 :
不良品退货单号
□ 供应商 □ 五金厂
仓库:
编 码:
无批锋,锥度面不能有变形和踫伤
表面无锈蚀,踫伤
严重 Major
制定:
批准:
生效日期:
第
页
抽检(数量)
轻微 Minor
判定
接收
拒收
B. 尺寸检查数量 :
No.
规格或标准
1
2
3
4
5
6
7
8
9
10
11
12
13
14
15
16
C.
HSF环境物质检查
IQC综合检查结果 :
格料MRB结果 l :
机加工首件检验记录表

总结
最终判定结果
□合格 □不合格
是否同意量产: □是 □否
检验员签名:
注意事 1、所有项目均需连续检查最少2件。 项 2、根据质量统计的不良项目进行持续跟进。
1、产品新开机生产时,由最终工序准备好2个样件置于待检区,并通知检验员,检查判定合格后生产。
填写 2、检验员判定合格后从样品中随机挑选1个样件,进行首件标识。并连同巡检记录表一起置于产线最终检查工位。 说明 3、适用范围:产品新开机、变更工艺/参数、变更材料等均需要进行首件检查。
4、检查结果:合格项目打“√”,不合格项目打“×”,无此检查项目打“0”;本表单保留一年。
机加工首件检验记录表
编号: 版本:A/0
零件号
首件 信息 □开机首检
□其他:
产品名称 □生产参数变更 □材料变更
项目
检验标准
12原料来自机台编号生产日期检验依据
□工程图纸 □标准样件 □产品标准 □其它
实测值
3
4
5
判定
检验时间
时 分
备注
检查 尺寸 记录
外观
□变形 □孔毛刺 □飞边毛刺 □划伤 □疤瘤 □烧穿 □未焊透
机械加工检验记录表常用
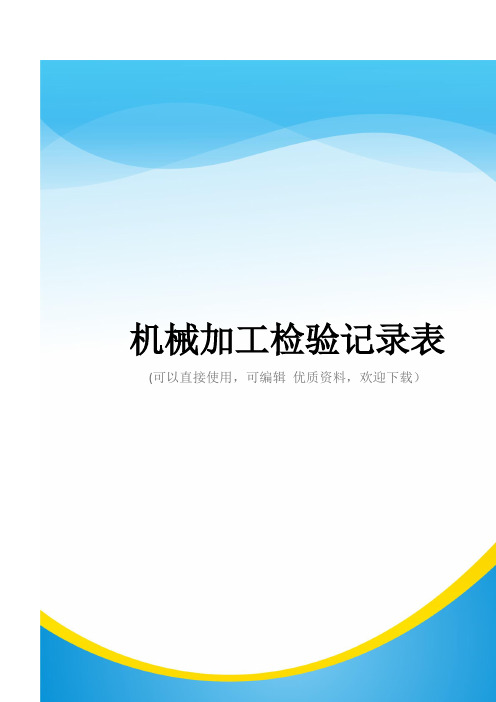
机械加工检验记录表(可以直接使用,可编辑优质资料,欢迎下载)编号:CHME/JL-ZJ-03岗位安全职责总经理1.工作内容及要求1.1总经理对本公司生产指挥和经营管理工作统一领导,全面负责。
1.2负责贯彻执行国家有关质量的法律、法规及方针政策,制定、发布质量方针并组织实施。
1.3批准并建立和完善与质量体系相适应的组织机构,明确职责、权限及相互关系,负责管理评审和内部质量审核及签署报告。
1.4决定重大质量决策,对公司的工作质量、产品质量和服务质量负全责。
1.5充分调动公司各方面的积极因素,发挥副经理及各职能部门的作用,确保公司质量方针目标的实现。
1.6负责职工的思想、文化、业务教育,组织职工进行技术创新,支持合理化建议活动。
2.责任与权限2.1总经理有企业经营管理工作的决策权和生产指挥权。
2.2总经理负责主持经理办公会议,研究解决生产经营和行政管理中的决策问题,对经营管理中的重大问题,意见不一致时,经理有权作出决定。
3.检查与考核3.1总经理的工作由董事会负责检查和考核。
3.2总经理应严以律己,自觉接受董事会的监督、检查。
管理者代表1.作内容及要求1.1管理者代表在公司总经理领导下工作。
1.2负责公司质量管理和质量保证等工作的组织和协调。
1.3负责建立、实施并保持质量体系的正常运行。
1.4负责组织内部质量体系审核,并将年度审核结果报告给总经理。
1.5协助总经理做好管理评审工作。
1.6负责质量体系文件的修改工作。
1.7负责对员工进行质量意识教育。
1.8按时完成领导交办的各项工作、任务。
2.责任与权限2.1对总经理负责,执行总经理决定,有权对总经理的工作提出建议。
2.2对保证公司质量体系有效运行负责,有权下达质量管理工作指令,并监督实施。
3.检查与考核3.1由总经理负责检查与考核。
3.2按对公司质量管理和质量保证工作的贡献和失误,由总经理视其情况,给予奖罚。
销售主管1.工作内容及要求1.1销售经理在总经理直接领导下,负责销售部的各项工作。
主要零件检验记录表
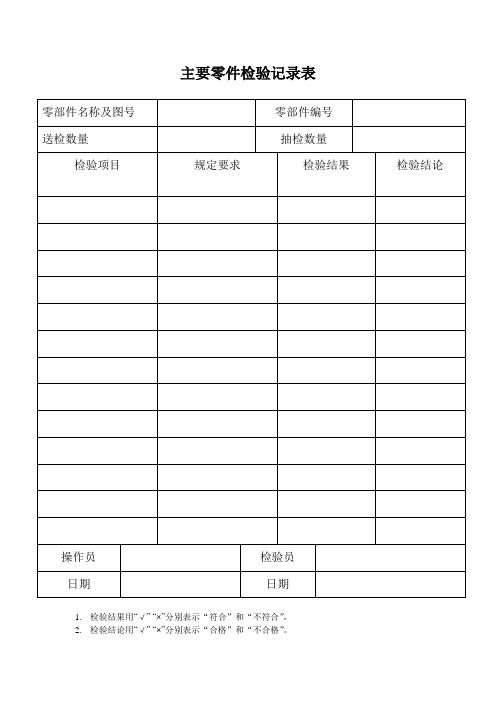
1.检验结果用“√”“×”分别表示“符合”和“不符合”,2.检验结论用“√”“×”分别表示“合格”和“不合格”。
1.检验结果用“√”“×”分别表示“符合”和“不符合”,2.检验结论用“√”“×”分别表示“合格”和“不合格”。
1.检验结果用“√”“×”分别表示“符合”和“不符合”,2.检验结论用“√”“×”分别表示“合格”和“不合格”。
1.检验结果用“√”“×”分别表示“符合”和“不符合”,2.检验结论用“√”“×”分别表示“合格”和“不合格”。
1.检验结果用“√”“×”分别表示“符合”和“不符合”,2.检验结论用“√”“×”分别表示“合格”和“不合格”。
1.检验结果用“√”“×”分别表示“符合”和“不符合”,2.检验结论用“√”“×”分别表示“合格”和“不合格”。
1.检验结果用“√”“×”分别表示“符合”和“不符合”,2.检验结论用“√”“×”分别表示“合格”和“不合格”。
1.检验结果用“√”“×”分别表示“符合”和“不符合”,2.检验结论用“√”“×”分别表示“合格”和“不合格”。
1.检验结果用“√”“×”分别表示“符合”和“不符合”,2.检验结论用“√”“×”分别表示“合格”和“不合格”。
1.检验结果用“√”“×”分别表示“符合”和“不符合”,2.检验结论用“√”“×”分别表示“合格”和“不合格”。
1.检验结果用“√”“×”分别表示“符合”和“不符合”,2.检验结论用“√”“×”分别表示“合格”和“不合格”。
1.检验结果用“√”“×”分别表示“符合”和“不符合”,2.检验结论用“√”“×”分别表示“合格”和“不合格”。
1.检验结果用“√”“×”分别表示“符合”和“不符合”,2.检验结论用“√”“×”分别表示“合格”和“不合格”。