机械加工检验标准定稿版
机械加工件检验标准
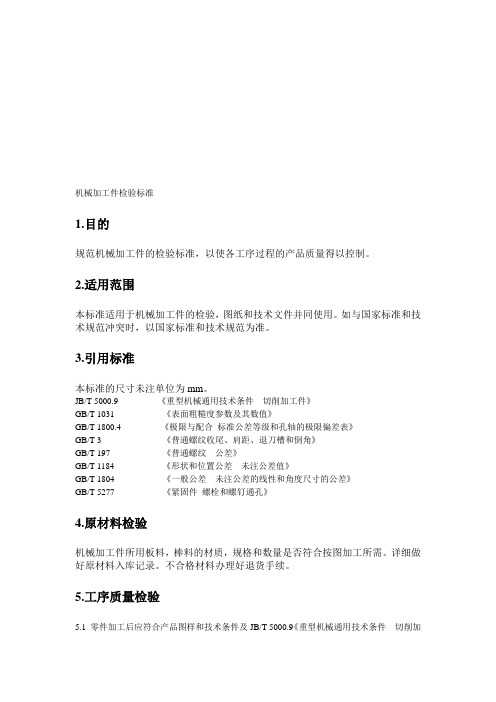
机械加工件检验标准1.目的规范机械加工件的检验标准,以使各工序过程的产品质量得以控制。
2.适用范围本标准适用于机械加工件的检验,图纸和技术文件并同使用。
如与国家标准和技术规范冲突时,以国家标准和技术规范为准。
3.引用标准本标准的尺寸未注单位为mm。
JB/T 5000.9 《重型机械通用技术条件切削加工件》GB/T 1031 《表面粗糙度参数及其数值》GB/T 1800.4 《极限与配合标准公差等级和孔轴的极限偏差表》GB/T 3 《普通螺纹收尾、肩距、退刀槽和倒角》GB/T 197 《普通螺纹公差》GB/T 1184 《形状和位置公差未注公差值》GB/T 1804 《一般公差未注公差的线性和角度尺寸的公差》GB/T 5277 《紧固件螺栓和螺钉通孔》4.原材料检验机械加工件所用板料,棒料的材质,规格和数量是否符合按图加工所需。
详细做好原材料入库记录。
不合格材料办理好退货手续。
5.工序质量检验5.1 零件加工后应符合产品图样和技术条件及JB/T 5000.9《重型机械通用技术条件切削加工件》规定。
5.2 零件应按工序检查、验收,在前道工序检查合格后方可转入下道工序。
5.3 铸钢件、铸铁件、有色金属铸件、锻件加工后如发现有砂眼、缩孔、夹渣、裂纹等缺陷时,在不降低零件强度和使用性能的前提下,允许按照相关标准的有关规定修补,经检验合格后方可继续加工。
5.4 加工后的零件不允许有毛刺,除产品图样有要求外,不允许有尖棱、尖角。
5.5 精加工后的零件不允许直接摆放在地面上,应采取必要的支撑、保护措施。
加工面不允许有锈蚀和影响性能、寿命或外观的磕碰、划伤等缺陷。
5.6 精加工后的配合面、摩擦面和定位面等工作表面不允许打印标记。
5.7 最终工序为热处理的零件,热处理后表面不应有氧化皮。
精加工后的配合面、齿面不应有退火、发蓝、变色的现象。
5.8 对于生产图样中要求电镀锌或热镀锌的零件,图中要求的配合面尺寸为含镀层后的尺寸。
机械加工件检验标准

机械加工件检验标准1.目的规范机械加工件的检验标准,以使各工序过程的产品质量得以控制。
2.适用范围本标准适用于机械加工件的检验,图纸和技术文件并同使用。
如与国家标准和技术规范冲突时,以国家标准和技术规范为准。
3.引用标准本标准的尺寸未注单位为mm。
JB/T 5000.9 《重型机械通用技术条件切削加工件》GB/T 1031 《表面粗糙度参数及其数值》GB/T 1800.4 《极限与配合标准公差等级和孔轴的极限偏差表》GB/T 3 《普通螺纹收尾、肩距、退刀槽和倒角》GB/T 197 《普通螺纹公差》GB/T 1184 《形状和位置公差未注公差值》GB/T 1804 《一般公差未注公差的线性和角度尺寸的公差》GB/T 5277 《紧固件螺栓和螺钉通孔》4.原材料检验机械加工件所用板料,棒料的材质,规格和数量是否符合按图加工所需。
详细做好原材料入库记录。
不合格材料办理好退货手续。
5.工序质量检验5.1 零件加工后应符合产品图样和技术条件及JB/T 5000.9《重型机械通用技术条件切削加工件》规定。
5.2 零件应按工序检查、验收,在前道工序检查合格后方可转入下道工序。
5.3 铸钢件、铸铁件、有色金属铸件、锻件加工后如发现有砂眼、缩孔、夹渣、裂纹等缺陷时,在不降低零件强度和使用性能的前提下,允许按照相关标准的有关规定修补,经检验合格后方可继续加工。
5.4 加工后的零件不允许有毛刺,除产品图样有要求外,不允许有尖棱、尖角。
5.5 精加工后的零件不允许直接摆放在地面上,应采取必要的支撑、保护措施。
加工面不允许有锈蚀和影响性能、寿命或外观的磕碰、划伤等缺陷。
5.6 精加工后的配合面、摩擦面和定位面等工作表面不允许打印标记。
5.7 最终工序为热处理的零件,热处理后表面不应有氧化皮。
精加工后的配合面、齿面不应有退火、发蓝、变色的现象。
5.8 对于生产图样中要求电镀锌或热镀锌的零件,图中要求的配合面尺寸为含镀层后的尺寸。
机械加工检验标准及方法
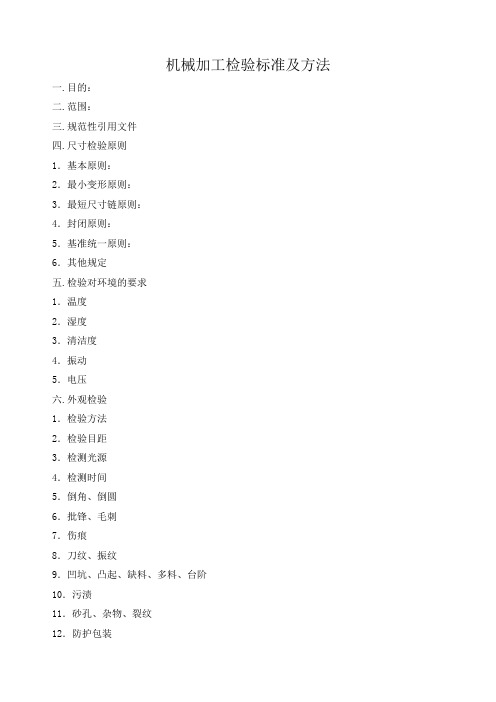
机械加工检验标准及方法一.目的:二.范围:三.规范性引用文件四.尺寸检验原则1.基本原则:2.最小变形原则:3.最短尺寸链原则:4.封闭原则:5.基准统一原则:6.其他规定五.检验对环境的要求1.温度2.湿度3.清洁度4.振动5.电压六.外观检验1.检验方法2.检验目距3.检测光源4.检测时间5.倒角、倒圆6.批锋、毛刺7.伤痕8.刀纹、振纹9.凹坑、凸起、缺料、多料、台阶10.污渍11.砂孔、杂物、裂纹12.防护包装七.表面粗糙度的检验1.基本要求2.检验方法:3.测量方向4.测量部位5.取样长度八.线性尺寸和角度尺寸公差要求1.基本要求2线性尺寸未注公差九.形状和位置公差的检验1.基本要求3.检测方法十.螺纹的检验1.使用螺纹量规检验螺纹制件2.单项检验十一.外协加工件的检验规定1.来料检验2.成品检验计划十二.判定规则附注:1.泰勒原则一.目的:为了明确公司金属切削加工检验标准,使检验作业有所遵循,特制定本标准。
二.范围:本标准适用于切削加工(包括外协、制程、出货过程)各检验特性的检验。
在本标准中,切削加工指的是:车削加工、铣削加工、磨削加工、镗削加工、刨削加工、孔加工、拉削加工和钳工作业等。
本标准规定了尺寸检验的基本原则、对环境的要求、外观检验标准、线性尺寸公差要求、形位公差要求、表面粗糙度的检验、螺纹的检验和判定准则。
注:本标准不适用于铸造、锻造、钣金、冲压、焊接加工后的检验,其检验标准另行制定。
本标准不拟对长度、角度、锥度的测量方法进行描述,可参看相关技术手册;形位公差的测量可参看GB/T1958-1980;齿轮、蜗杆的检验可参看相关技术手册。
三.规范性引用文件下列文件中的条款通过本标准的引用而成为本标准的条款。
凡是注日期的引用文件,其随后所有的修改单(不包括勘误的内容)或修订版均不适用于本标准,然而,鼓励根据本标准达成协议的各方研究是否可使用这些文件的最新版本。
凡是不注日期的引用文件,其最新版本适用于本标准GB/(ISO2859-1:1989)计数抽样程序第1部分:按接收质量限(AQL)检索的逐批检验抽样计划GB/T1804-2000(ISO2768-1:104989)一般公差未注公差的线性和角度尺寸的公差GB/T1184-1996(ISO2768-2:1989)形状和位置公差未注公差值GB/T1958-1980形状和位置公差检测规定GB/T1957-1981光滑极限量规Q/抽样检查作业指导书Q/产品的监视和测量控制程序Q/不合格品控制程序四.尺寸检验原则1.基本原则:所用验收方法应只接收位于规定的尺寸验收极限的工件。
机械加工件检验行业标准
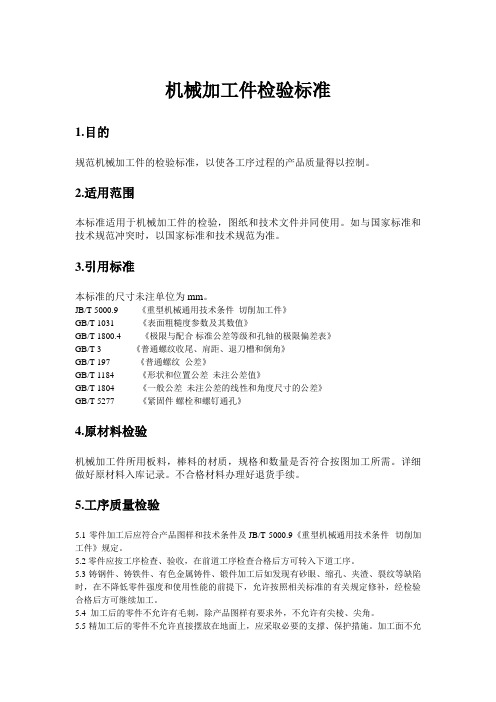
机械加工件检验标准1.目的规范机械加工件的检验标准,以使各工序过程的产品质量得以控制。
2.适用范围本标准适用于机械加工件的检验,图纸和技术文件并同使用。
如与国家标准和技术规范冲突时,以国家标准和技术规范为准。
3.引用标准本标准的尺寸未注单位为mm。
JB/T 5000.9 《重型机械通用技术条件切削加工件》GB/T 1031 《表面粗糙度参数及其数值》GB/T 1800.4 《极限与配合标准公差等级和孔轴的极限偏差表》GB/T 3 《普通螺纹收尾、肩距、退刀槽和倒角》GB/T 197 《普通螺纹公差》GB/T 1184 《形状和位置公差未注公差值》GB/T 1804 《一般公差未注公差的线性和角度尺寸的公差》GB/T 5277 《紧固件螺栓和螺钉通孔》4.原材料检验机械加工件所用板料,棒料的材质,规格和数量是否符合按图加工所需。
详细做好原材料入库记录。
不合格材料办理好退货手续。
5.工序质量检验5.1 零件加工后应符合产品图样和技术条件及JB/T 5000.9《重型机械通用技术条件切削加工件》规定。
5.2 零件应按工序检查、验收,在前道工序检查合格后方可转入下道工序。
5.3 铸钢件、铸铁件、有色金属铸件、锻件加工后如发现有砂眼、缩孔、夹渣、裂纹等缺陷时,在不降低零件强度和使用性能的前提下,允许按照相关标准的有关规定修补,经检验合格后方可继续加工。
5.4 加工后的零件不允许有毛刺,除产品图样有要求外,不允许有尖棱、尖角。
5.5 精加工后的零件不允许直接摆放在地面上,应采取必要的支撑、保护措施。
加工面不允许有锈蚀和影响性能、寿命或外观的磕碰、划伤等缺陷。
5.6 精加工后的配合面、摩擦面和定位面等工作表面不允许打印标记。
5.7 最终工序为热处理的零件,热处理后表面不应有氧化皮。
精加工后的配合面、齿面不应有退火、发蓝、变色的现象。
5.8 对于生产图样中要求电镀锌或热镀锌的零件,图中要求的配合面尺寸为含镀层后的尺寸。
机械加工件检验标准
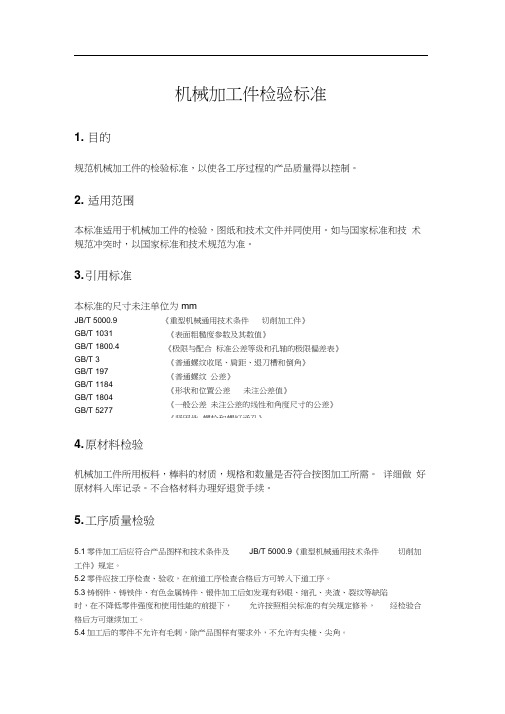
机械加工件检验标准1. 目的规范机械加工件的检验标准,以使各工序过程的产品质量得以控制。
2. 适用范围本标准适用于机械加工件的检验,图纸和技术文件并同使用。
如与国家标准和技术规范冲突时,以国家标准和技术规范为准。
3. 引用标准本标准的尺寸未注单位为mmJB/T 5000.9 GB/T 1031 GB/T 1800.4 GB/T 3GB/T 197 GB/T 1184 GB/T 1804 GB/T 5277《重型机械通用技术条件切削加工件》《表面粗糙度参数及其数值》《极限与配合标准公差等级和孔轴的极限偏差表》《普通螺纹收尾、肩距、退刀槽和倒角》《普通螺纹公差》《形状和位置公差未注公差值》《一般公差未注公差的线性和角度尺寸的公差》《紧固件螺栓和螺钉通孔》4. 原材料检验机械加工件所用板料,棒料的材质,规格和数量是否符合按图加工所需。
详细做好原材料入库记录。
不合格材料办理好退货手续。
5. 工序质量检验5.1零件加工后应符合产品图样和技术条件及JB/T 5000.9《重型机械通用技术条件切削加工件》规定。
5.2零件应按工序检查、验收,在前道工序检查合格后方可转入下道工序。
5.3铸钢件、铸铁件、有色金属铸件、锻件加工后如发现有砂眼、缩孔、夹渣、裂纹等缺陷时,在不降低零件强度和使用性能的前提下,允许按照相关标准的有关规定修补,经检验合格后方可继续加工。
5.4加工后的零件不允许有毛刺,除产品图样有要求外,不允许有尖棱、尖角。
5.5精加工后的零件不允许直接摆放在地面上,应采取必要的支撑、保护措施。
加工面不允许有锈蚀和影响性能、寿命或外观的磕碰、划伤等缺陷。
5.6精加工后的配合面、摩擦面和定位面等工作表面不允许打印标记。
5.7最终工序为热处理的零件,热处理后表面不应有氧化皮。
精加工后的配合面、齿面不应有退火、发蓝、变色的现象。
5.8对于生产图样中要求电镀锌或热镀锌的零件,图中要求的配合面尺寸为含镀层后的尺寸。
5.9表面电镀锌涂层的质量要求:1)镀层外观光滑细致、无起泡、起层、剥落、烧焦及海绵状沉淀;2)经铬酸钝化后,应具有绿黄略带有红色的彩虹色;3)镀层表面允许有不严重的流痕及轻微的刮痕印,允许工件边缘色彩稍淡;4)钝化膜有一定的光泽,不到呈暗褐无光的泥巴色;5)钝化膜应牢固,用布揩擦不掉;在50C〜60C的热水中煮1小时,颜色无显著减退。
机械加工件检验标准【范本模板】

机械加工件检验标准1.目的规范机械加工件的检验标准,以使各工序过程的产品质量得以控制。
2.适用范围本标准适用于机械加工件的检验,图纸和技术文件并同使用。
如与国家标准和技术规范冲突时,以国家标准和技术规范为准。
3.引用标准本标准的尺寸未注单位为mm.JB/T 5000.9 《重型机械通用技术条件切削加工件》GB/T 1031 《表面粗糙度参数及其数值》GB/T 1800。
4 《极限与配合标准公差等级和孔轴的极限偏差表》GB/T 3 《普通螺纹收尾、肩距、退刀槽和倒角》GB/T 197 《普通螺纹公差》GB/T 1184 《形状和位置公差未注公差值》GB/T 1804 《一般公差未注公差的线性和角度尺寸的公差》GB/T 5277 《紧固件螺栓和螺钉通孔》4.原材料检验机械加工件所用板料,棒料的材质,规格和数量是否符合按图加工所需.详细做好原材料入库记录。
不合格材料办理好退货手续。
5.工序质量检验5。
1 零件加工后应符合产品图样和技术条件及JB/T 5000.9《重型机械通用技术条件切削加工件》规定。
5。
2 零件应按工序检查、验收,在前道工序检查合格后方可转入下道工序。
5。
3 铸钢件、铸铁件、有色金属铸件、锻件加工后如发现有砂眼、缩孔、夹渣、裂纹等缺陷时,在不降低零件强度和使用性能的前提下,允许按照相关标准的有关规定修补,经检验合格后方可继续加工.5。
4 加工后的零件不允许有毛刺,除产品图样有要求外,不允许有尖棱、尖角。
5。
5 精加工后的零件不允许直接摆放在地面上,应采取必要的支撑、保护措施。
加工面不允许有锈蚀和影响性能、寿命或外观的磕碰、划伤等缺陷。
5。
6 精加工后的配合面、摩擦面和定位面等工作表面不允许打印标记。
5。
7 最终工序为热处理的零件,热处理后表面不应有氧化皮.精加工后的配合面、齿面不应有退火、发蓝、变色的现象。
5.8 对于生产图样中要求电镀锌或热镀锌的零件,图中要求的配合面尺寸为含镀层后的尺寸。
机械加工检验标准及方法【范本模板】

机械加工检验标准及方法一。
目的:二. 范围:三. 规范性引用文件四。
尺寸检验原则1.基本原则:2.最小变形原则:3.最短尺寸链原则:4.封闭原则:5.基准统一原则:6.其他规定五。
检验对环境的要求1.温度2.湿度3.清洁度4.振动5.电压六。
外观检验1.检验方法2.检验目距3.检测光源4.检测时间5.倒角、倒圆6.批锋、毛刺7.伤痕8.刀纹、振纹9.凹坑、凸起、缺料、多料、台阶10.污渍11.砂孔、杂物、裂纹12.防护包装七. 表面粗糙度的检验1.基本要求2.检验方法:3.测量方向4。
测量部位5.取样长度八. 线性尺寸和角度尺寸公差要求1.基本要求2 线性尺寸未注公差九.形状和位置公差的检验1.基本要求3.检测方法十.螺纹的检验1.使用螺纹量规检验螺纹制件2.单项检验十一。
外协加工件的检验规定1.来料检验2. 成品检验计划十二.判定规则附注:1.泰勒原则一。
目的:为了明确公司金属切削加工检验标准,使检验作业有所遵循,特制定本标准。
二. 范围:本标准适用于切削加工(包括外协、制程、出货过程)各检验特性的检验。
在本标准中,切削加工指的是:车削加工、铣削加工、磨削加工、镗削加工、刨削加工、孔加工、拉削加工和钳工作业等。
本标准规定了尺寸检验的基本原则、对环境的要求、外观检验标准、线性尺寸公差要求、形位公差要求、表面粗糙度的检验、螺纹的检验和判定准则。
注:本标准不适用于铸造、锻造、钣金、冲压、焊接加工后的检验,其检验标准另行制定.本标准不拟对长度、角度、锥度的测量方法进行描述,可参看相关技术手册;形位公差的测量可参看GB/T1958—1980;齿轮、蜗杆的检验可参看相关技术手册。
三。
规范性引用文件下列文件中的条款通过本标准的引用而成为本标准的条款。
凡是注日期的引用文件,其随后所有的修改单(不包括勘误的内容)或修订版均不适用于本标准,然而,鼓励根据本标准达成协议的各方研究是否可使用这些文件的最新版本。
凡是不注日期的引用文件,其最新版本适用于本标准GB/T 2828。
机加工检验标准定稿版
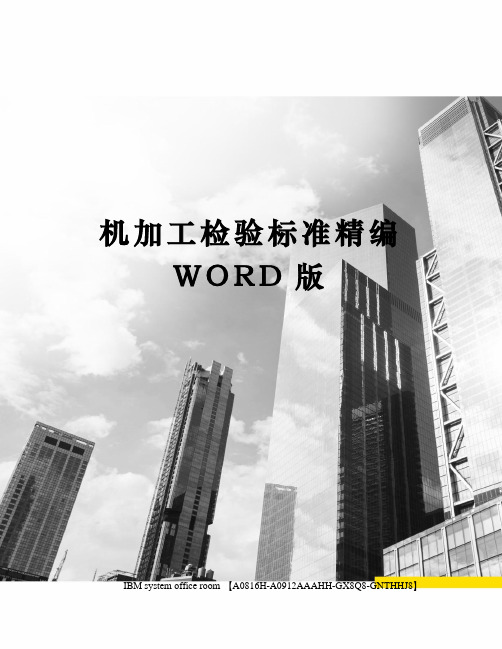
机加工检验标准精编
W O R D版
IBM system office room 【A0816H-A0912AAAHH-GX8Q8-GNTHHJ8】
一.目的:
为了明确公司金属切削加工检验标准,使检验作业有所遵循,特制定本标准。
二.范围:
本标准适用于切削加工(包括外协、制程、出货过程)各检验特性的检验。
本标准规定了尺寸检验的基本原则、对环境的要求、外观检验标准、线性尺寸公差要求、形位公差要求、表面粗糙度的检验、螺纹的检验和判定准则。
注:本标准不适用于铸造、锻造、钣金、冲压、焊接加工后的检验,其检验标准另行制定。
QC应认真按图纸及技术要求,如有疑问需及时沟通,做到按图纸要求检验。
按图纸要求测量基准测量,如未规定则尽可能使测量基准与设计基准吻合。
正确使用测量用具,使用量规、千分尺等须轻轻用力推入或旋入,不得用力过猛,使用卡尺、千分尺、百分表、千分表应先校正量具,调好零位,QC本着“先重要,后次要”的测量原则,图纸尺寸有公差要求的,严格按图纸尺寸进行检验。
为避免量具反复改变尺寸,造成量具误差,量具需与铸件放置同一温度,一个尺寸统一测量、多点位测量保证测量结果的正确性,并填写相应质量记录。
编制:审核:批准:。
机械加工检验要求规范(参考模板)

机械加工检验规范编制:审核:批准:日期:1、范围本检验规程适用本公司机械加工产品的检验。
2、检验依据国家标准、行业标准、API标准、图纸工艺等技术文件、质量计划等3、检验内容3.1 尺寸的检验3.1.1 基本原则所用验收方法应只接收位于规定尺寸极限之内的工件。
3.1.2常用量具钢直尺(钢板尺)、钢卷尺(盒尺)、塞尺(厚薄规)、游标卡尺、高度游标卡尺、深度游标卡尺、外径千分尺、内径千分尺、内径量表、量块3.1.3量具的选择3.1.3.1量具的选择原则A、保证测量精确度;B、保证测量的经济性,从计量器具成本、耐磨性、检验时间方便性等来考虑合理性;3.1.3.2量具具体选择A、根据零件的公差选用,取测量精度系数为二分之一到五分之一;B、根据计量器具的不确定度允许值选用;C、根据零件的大小选用;D、根据零件的表面质量选用;E、根据零件的批量来选用;3.1.3.3量具精度选择原则A、根据本公司的实际情况及以上的原则确定以下量具精度具体的选用原则;3.1.4尺寸检测方法①轴径——中低精度轴径的实际尺寸通常用卡尺、千分尺、专用量表等普通计量器具进行检测。
②孔径——通常用卡尺、内径千分尺、内径规、内径摇表、内测卡规等普通量具、通用量仪;高精度深孔和精密孔等的测量常用内径百分表(千分表)或卧式测长仪(也叫万能测长仪)测量,用小孔内视镜、反射内视镜等检测小孔径。
③长度、厚度——长度尺寸一般用卡尺、千分尺、专用量表、测长仪、比测仪、高度仪、气动量仪等;厚度尺寸一般用塞尺、间隙片结合卡尺、千分尺、高度尺、量规;壁厚尺寸可使用超声波测厚仪或壁厚千分尺来检测管类、薄壁件等的厚度,用膜厚计、涂层测厚计检测刀片或其他零件涂镀层的厚度;用螺距规检测螺距尺寸值。
④表面粗糙度——a.目测检查:工件表面粗糙度比规定的粗糙度明显地好,不需用更精确的方法检验时,可用目测法检验判定;工件表面粗糙度比规定的粗糙度明显不好时,不需用更精确的方法检验时,可用目测法检验判定;工件表面存在明显影响表面功能的表面缺陷,选择目视法检验判定。
机械加工件检验标准

机械加工件检验标准1.目的规范机械加工件的检验标准,以使各工序过程的产品质量得以控制。
2.适用范围本标准适用于机械加工件的检验,图纸和技术文件并同使用。
如与国家标准和技术规范冲突时,以国家标准和技术规范为准。
3.引用标准本标准的尺寸未注单位为mm。
JB/T 5000.9 《重型机械通用技术条件切削加工件》GB/T 1031 《表面粗糙度参数及其数值》GB/T 1800.4 《极限与配合标准公差等级和孔轴的极限偏差表》GB/T 3 《普通螺纹收尾、肩距、退刀槽和倒角》GB/T 197 《普通螺纹公差》GB/T 1184 《形状和位置公差未注公差值》GB/T 1804 《一般公差未注公差的线性和角度尺寸的公差》GB/T 5277 《紧固件螺栓和螺钉通孔》4.原材料检验机械加工件所用板料,棒料的材质,规格和数量是否符合按图加工所需。
详细做好原材料入库记录。
不合格材料办理好退货手续。
5.工序质量检验5.1 零件加工后应符合产品图样和技术条件及JB/T 5000.9《重型机械通用技术条件切削加工件》规定。
5.2 零件应按工序检查、验收,在前道工序检查合格后方可转入下道工序。
5.3 铸钢件、铸铁件、有色金属铸件、锻件加工后如发现有砂眼、缩孔、夹渣、裂纹等缺陷时,在不降低零件强度和使用性能的前提下,允许按照相关标准的有关规定修补,经检验合格后方可继续加工。
5.4 加工后的零件不允许有毛刺,除产品图样有要求外,不允许有尖棱、尖角。
5.5 精加工后的零件不允许直接摆放在地面上,应采取必要的支撑、保护措施。
加工面不允许有锈蚀和影响性能、寿命或外观的磕碰、划伤等缺陷。
5.6 精加工后的配合面、摩擦面和定位面等工作表面不允许打印标记。
5.7 最终工序为热处理的零件,热处理后表面不应有氧化皮。
精加工后的配合面、齿面不应有退火、发蓝、变色的现象。
5.8 对于生产图样中要求电镀锌或热镀锌的零件,图中要求的配合面尺寸为含镀层后的尺寸。
机械加工检验标准

B面:产品于使用者正面不可见部分如左右侧面
C面:产品底面及背面
品名:Paint涂装&涂料
Inspection Item
检验项目
Quality Standard
品质需求
Defect Class
缺点等级
MA
MI
1.Color
色差
以色差计划测:光源0.65ΔE<1
ˇ
ˇ
6.Hard Testing
硬度试验
以三菱F-H铅笔笔尖磨平,以45。斜角1kg,荷重于试验面反向推书测验以橡皮去除面笔迹后,检视表面,不得任何刮伤。
ˇ
7.Impact Testing
冲击试验
以冲击试验机,球径0.5",荷重500g自由落下,高度350mm,直接冲击喷涂表面,涂料不得有破裂或脱落现象。
允许:A面:10cm×10cm内允许0.3mm以内1点
B面:10cm×10cm内允许0.4mm以内2点
C面:10cm×10cm内允许0.6mm以内2点
ˇ
3.2刮伤允许
A面:长度≦3mm容许1点宽度≦0.2mm
B面:长度≦5mm容许2点宽度≦0.3mm
C面:长度≦8mm容许2点宽度≦0.4mm
ˇ
检验区域:检查表面依零件组装后之位置可分为A.B.C三面
以50Hel或5%NaOH以棉花吸附,静置于涂膜上24hrs后进行方格硬度冲击试验,不得有破裂或脱落现象。
ˇ
检验项目
Quality Standard
品质需求
Defect Class
缺点等级
MA
MI
1.Appearance
外观检验
1.1实物与图面不符
- 1、下载文档前请自行甄别文档内容的完整性,平台不提供额外的编辑、内容补充、找答案等附加服务。
- 2、"仅部分预览"的文档,不可在线预览部分如存在完整性等问题,可反馈申请退款(可完整预览的文档不适用该条件!)。
- 3、如文档侵犯您的权益,请联系客服反馈,我们会尽快为您处理(人工客服工作时间:9:00-18:30)。
3.Rusttesting
盐雾试验
以5%盐雾喷洒经24hrs不可有生锈现象
ˇ
品名:Foundry压铸类
Inspection Item
检验项目
Quality Standard
品质需求
Defect Class
缺点等级
MA
MI
1.Appearance
外观检验
1.1实物与图面不符
ˇ
1.2毛边须修平整,宽度不可超过0.3mm,长度不可超过3mm
2.Luster
光泽度
以光泽度计量测:角度60,光泽度15±3
ˇ
3.Thickness
涂膜厚度
以膜厚计划量测:3~5um(金属件)
10~12um(塑件)
ˇ
4.Density
涂膜状态
喷点粗细,疏忽比照样品,涂装表面不得有起泡沙孔,喷漆不均或流痕之现象。
ˇ
5.Pane Testing
方格测试
以百格刮刀刻划1mm方格×100格,再以3m(600#)胶带密压着于试验面以90°急速拉起,涂膜不得有任何脱落。
ˇ
10.Rust Testing
耐盐雾试验
5%NaCI于盐水喷雾状试验机试验72hrs后进行方格硬度冲击试验,不得有破裂或脱落现象。
ˇ
11.Ultraviole Test
耐照射试验
15w,140v紫外灯距离30cm照射4hrs,色泽不得有差异及物性降低现象。
ˇ
12.Acid- Alkali Test耐酸碱性试验
ˇ
6.Hard Testing
硬度试验
以三菱F-H铅笔笔尖磨平,以45。斜角1kg,荷重于试验面反向推书测验以橡皮去除面笔迹后,检视表面,不得任何刮伤。
ˇ
7.Impact Testing
冲击试验
以冲击试验机,球径0.5",荷重500g自由落下,高度350mm,直接冲击喷涂表面,涂料不得有破裂或脱落现象。
ˇ
1.4目视不能有毛边(毛边需要在0.1mm以下)
ˇ
1.5污点气泡允许范围如下:
面积10cm×10cm,
(距离样品约30cm,目视检验3~5秒,白光源≧500LUX),
A面:1.0mm以内2点,
B面:1.0mm以内3点
C面:1.0mm以内4点
ˇ
1.6刮伤允许:面积10cm×10cm,
A面:长度≦10mm宽度≦0.5mm容许2点
A面:产品于使用者正面可见部分如面板上盖
B面:产品于使用者正面不可见部分如左右侧面
C面:产品底面及背面
品名:Paint涂装&涂料
Inspection Item
检验项目
Quality Standard
品质需求
Defect Class
缺点等级
MA
MI
1.Color
色差
以色差计划测:光源0.65ΔE<1
ˇ
允许:A面:10cm×10cm内允许0.3mm以内1点
B面:10cm×10cm内允许0.4mm以内2点
C面:10cm×10cm内允许0.6mm以内2点
ˇ
3.2刮伤允许
A面:长度≦3mm容许1点宽度≦0.2mm
B面:长度≦5mm容许2点宽度≦0.3mm
C面:长度≦8mm容许2点宽度≦0.4mm
ˇ
检验区域:检查表面依零件组装后之位置可分为A.B.C三面
ˇ
1.3目视不得有变形、裂伤、气孔≦0.4mm
ˇ
1.4孔位、孔柱不可阻塞、断裂
ˇ
1.5表面不得有油渍及其它异物
ˇ
2.Dimensions
尺寸量测
依照工程部之图面量测
ˇ
3.RustTesting
耐盐雾试验
5%Na CI于盐水喷雾试验机试验48hrs,无锈蚀现象。
ˇ
品名:Plastic塑料件
Inspection Item
以50Hel或5%NaOH以棉花吸附,静置于涂膜上24hrs后进行方格硬度冲击试验,不得有破裂或脱落现象。
ˇ
机械加工检验标准
品名:Stamping/Machine冲压/机加工件
Inspection Item
检验项目
Quality Standard
品质需求
Defect Class
缺点等级
Байду номын сангаасMA
MI
1.Appearance
外观检验
1.1实物与图面不符
ˇ
1.2不可有变形、缺件、混料、错料
ˇ
1.3切断面生锈,只容许有黑皮、锈斑现象
B面:长度≦10mm宽度≦0.5mm容许4点
C面:长度≦10mm宽度≦0.3mm容许5点
ˇ
1.7表面不可有油渍、色渍、脏污
ˇ
1.8 工艺折弯印一般不予关注,但不可对功能性产生影响。
ˇ
2.Dimensions
尺寸检验
2.1实物与图面不符
ˇ
2.2文字位置偏移及倾斜度10cm内允许0.5。
ˇ
2.3电镀膜厚度除图面另有规定外,应在3~5um
ˇ
1.6目视不得有变形、裂伤
ˇ
1.7孔位、孔柱不可阻塞、断裂
ˇ
1.8表面不得有油渍、色渍
ˇ
2.Dimensions
尺寸量测
2.1依照工程部之图面量测
ˇ
2.2文字位置偏移及倾斜度10mm内允许0.5。
ˇ
3.Scart/Dirt/Eyewinker
异物污点及刮伤
(不得见底)
3.1距离样品约30cm目视检验3~5秒(自光源≧500LUX)
ˇ
8.Impregnant Test
耐溶剂试验
95%浓度之药用酒精,加压于棉布或纱布上,行程50mm来回50次,涂膜不得见底或漆附着于棉布。
ˇ
9.Temperture Test
耐温差试验
以温度循环机:60℃至-5℃间以30分钟为cycle,共计10cycle,再做方格硬度冲击试验,不得有破裂或脱落现象。
检验项目
Quality Standard
品质需求
Defect Class
缺点等级
MA
MI
1.Appearance
外观检验
1.1实物与图面不符
ˇ
1.2色差不允许(ΔE<1)
ˇ
1.3以印刷表面不可有流漆、剥落、浮起、龟裂
ˇ
1.4表面字体印刷应鲜明可读,不可断裂模糊
ˇ
1.5射出口、孔位毛边须修平整(毛边<0.2mm)