锻造润滑剂性能的研究
SJ―3芯棒润滑剂的研制及其综合性能考察
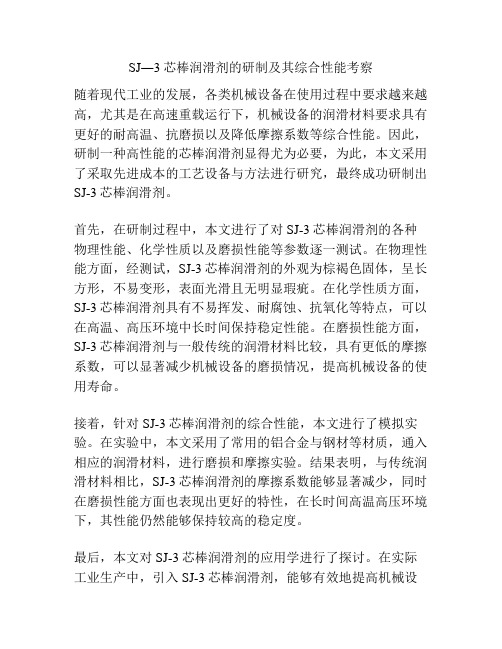
SJ―3芯棒润滑剂的研制及其综合性能考察随着现代工业的发展,各类机械设备在使用过程中要求越来越高,尤其是在高速重载运行下,机械设备的润滑材料要求具有更好的耐高温、抗磨损以及降低摩擦系数等综合性能。
因此,研制一种高性能的芯棒润滑剂显得尤为必要,为此,本文采用了采取先进成本的工艺设备与方法进行研究,最终成功研制出SJ-3芯棒润滑剂。
首先,在研制过程中,本文进行了对SJ-3芯棒润滑剂的各种物理性能、化学性质以及磨损性能等参数逐一测试。
在物理性能方面,经测试,SJ-3芯棒润滑剂的外观为棕褐色固体,呈长方形,不易变形,表面光滑且无明显瑕疵。
在化学性质方面,SJ-3芯棒润滑剂具有不易挥发、耐腐蚀、抗氧化等特点,可以在高温、高压环境中长时间保持稳定性能。
在磨损性能方面,SJ-3芯棒润滑剂与一般传统的润滑材料比较,具有更低的摩擦系数,可以显著减少机械设备的磨损情况,提高机械设备的使用寿命。
接着,针对SJ-3芯棒润滑剂的综合性能,本文进行了模拟实验。
在实验中,本文采用了常用的铝合金与钢材等材质,通入相应的润滑材料,进行磨损和摩擦实验。
结果表明,与传统润滑材料相比,SJ-3芯棒润滑剂的摩擦系数能够显著减少,同时在磨损性能方面也表现出更好的特性,在长时间高温高压环境下,其性能仍然能够保持较高的稳定度。
最后,本文对SJ-3芯棒润滑剂的应用学进行了探讨。
在实际工业生产中,引入SJ-3芯棒润滑剂,能够有效地提高机械设备的使用寿命和运行效率,从而达到促进生产效益、降低生产成本的目的。
综上,本文通过对SJ-3芯棒润滑剂的研制及其综合性能的考察,发现该润滑材料具有良好的抗磨损和降低摩擦系数等特性,在实际应用中具有广阔的推广应用前景。
除了上述内容,SJ-3芯棒润滑剂还具有一些其他的优点。
首先,该润滑剂易于使用。
其棒形设计使得加入机器设备时,不需要额外配备任何辅助设备,操作简单,方便快捷。
其次,SJ-3芯棒润滑剂在使用过程中不会掉落、分散,有效地避免了对环境的污染,符合现代企业对环境保护的要求。
机械装备中的润滑与润滑剂研究

机械装备中的润滑与润滑剂研究润滑是机械装备正常运行的关键因素之一。
机械装备中的润滑与润滑剂研究,正日益成为一个重要的领域,不仅涉及到机械运行的效率和寿命,也涉及到环境保护和能源消耗的问题。
本文将探讨润滑在机械装备中的作用以及润滑剂研究的最新进展。
润滑的作用不可忽视。
在机械装备运行过程中,润滑剂可以减少物体表面间的摩擦,降低磨损和能量损耗。
通过有效的润滑,机械装备的效率得以提高,运行寿命得以延长。
同时,润滑还能够减少噪音和振动,提升设备的可靠性和稳定性。
润滑剂的选择和研究是润滑技术的核心。
润滑剂可以分为液体、固体和气体三种形式。
在不同的机械装备中,选择合适的润滑剂对润滑效果起到至关重要的作用。
目前,润滑剂研究的重点主要是固润滑剂和润滑油的开发。
固润滑剂是一种非常有前景的研究方向。
传统的固润滑剂如石墨和硼化硅已经广泛应用于机械装备中。
它们具有优良的润滑性能和耐高温、耐腐蚀等特点。
然而,随着科学技术的发展,人们对固润滑剂的要求越来越高。
因此,研究人员开始利用纳米材料、液态金属等新技术开发新型固润滑剂。
这些新型固润滑剂具有更高的润滑性能和更广阔的应用领域。
润滑油在机械装备中起到了重要的作用。
它既可以减少物体表面间的摩擦,又可以冷却运动部件的温度。
目前,润滑油的研究主要集中在降低摩擦和磨损、防止泡沫和氧化、提高润滑油的黏度指数和减少摩擦力等方面。
研究人员通过添加特殊的添加剂和利用新技术,不断改善润滑油的性能。
近年来,人们对润滑技术也越来越重视环境保护和节能。
在润滑剂研究中,研究人员开始关注润滑剂对环境的影响以及研发节能型润滑剂。
例如,水基润滑剂在一些特殊环境下表现出了出色的润滑性能,并且对环境的影响较小。
此外,研究人员也在探索利用替代能源和新材料来代替传统润滑剂,以实现绿色润滑技术的发展。
总而言之,润滑在机械装备中的作用不可忽视,润滑剂研究也越来越受到重视。
随着科学技术的发展,研究人员不断寻求新的润滑剂和润滑技术,以提高机械装备的效率和寿命,减少能源消耗和环境污染。
高效润滑剂的研究与应用

高效润滑剂的研究与应用高效润滑剂是一种能够有效减少摩擦和磨损、提高机械设备运行效率的重要材料。
随着工业化进程的加快和机械设备的广泛应用,高效润滑剂的研究与应用变得越来越重要。
本文将从高效润滑剂的定义、分类、研究进展以及应用领域等方面进行探讨。
高效润滑剂是指具有较高的润滑性能、降低摩擦系数、减少磨损、提高机械设备运行效率的材料。
根据其成分和性质的不同,高效润滑剂可以分为多种类型,如液体润滑剂、固体润滑剂、纳米润滑剂等。
液体润滑剂主要由基础油和添加剂组成,可以分为矿物油和合成油两类。
固体润滑剂主要包括润滑脂和固体润滑材料,如石墨、二硫化钼等。
纳米润滑剂是一种由纳米材料制备而成的润滑剂,具有较高的润滑性能和稳定性。
近年来,高效润滑剂的研究取得了一系列重要进展。
一方面,研究人员通过改变润滑剂的成分和添加剂的种类和含量,提高了润滑剂的润滑性能和稳定性。
例如,添加磺酸盐类添加剂可以形成一层保护膜,减少接触磨损和摩擦,提高润滑剂的性能。
另一方面,研究人员通过纳米技术的应用,制备了一系列具有优异性能的纳米润滑剂。
例如,纳米颗粒可以填充润滑剂中的空隙,形成“纳米间隙润滑”,从而显著降低摩擦系数和磨损。
高效润滑剂在各个领域都有广泛的应用。
在工业领域,高效润滑剂可以提高机械设备的运行效率,减少能源消耗和环境污染。
在汽车领域,高效润滑剂可以降低发动机的磨损和摩擦,延长机械设备的使用寿命。
在航空航天领域,高效润滑剂可以提高飞机的性能,减少能耗和空气污染。
此外,高效润滑剂还可以应用于冶金、轴承、液压系统、电子器件等领域。
然而,高效润滑剂的研究和应用面临一些挑战。
首先,润滑剂的成本较高,需要进行进一步的降低。
其次,部分高效润滑剂对环境有一定的污染和毒性影响,需要进一步加强环境友好型润滑剂的研发。
另外,高效润滑剂的使用也需要与机械设备的设计和工艺技术相匹配,提高整体系统的效率。
综上所述,高效润滑剂的研究与应用是一个复杂而重要的领域。
金属塑性加工的润滑(金属加工之二)
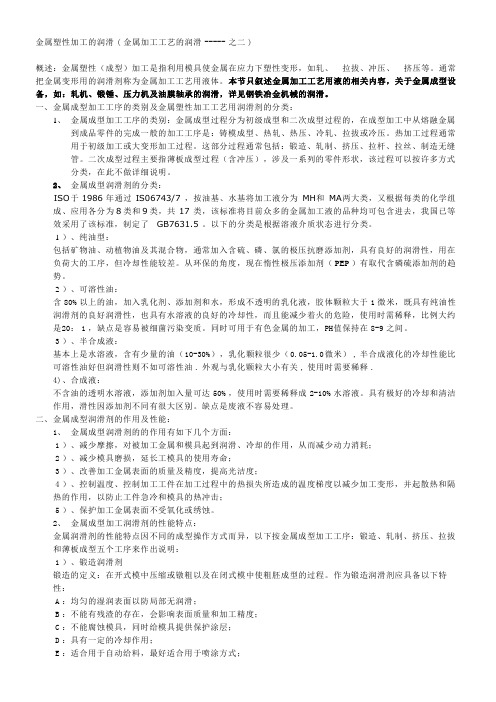
金属塑性加工的润滑(金属加工工艺的润滑-----之二)概述:金属塑性(成型)加工是指利用模具使金属在应力下塑性变形,如轧、拉拔、冲压、挤压等。
通常把金属变形用的润滑剂称为金属加工工艺用液体。
本节只叙述金属加工工艺用液的相关内容,关于金属成型设备,如:轧机、锻锤、压力机及油膜轴承的润滑,详见钢铁冶金机械的润滑。
一、金属成型加工工序的类别及金属塑性加工工艺用润滑剂的分类:1、金属成型加工工序的类别:金属成型过程分为初级成型和二次成型过程的,在成型加工中从熔融金属到成品零件的完成一般的加工工序是:铸模成型、热轧、热压、冷轧、拉拔或冷压。
热加工过程通常用于初级加工或大变形加工过程。
这部分过程通常包括:锻造、轧制、挤压、拉杆、拉丝、制造无缝管。
二次成型过程主要指薄板成型过程(含冲压),涉及一系列的零件形状,该过程可以按许多方式分类,在此不做详细说明。
2、金属成型润滑剂的分类:ISO于1986年通过IS06743/7,按油基、水基将加工液分为MH和MA两大类,又根据每类的化学组成、应用各分为8类和9类,共17类,该标准将目前众多的金属加工液的品种均可包含进去,我国已等效采用了该标准,制定了GB7631.5。
以下的分类是根据溶液介质状态进行分类。
1)、纯油型:包括矿物油、动植物油及其混合物,通常加入含硫、磷、氯的极压抗磨添加剂,具有良好的润滑性,用在负荷大的工序,但冷却性能较差。
从环保的角度,现在惰性极压添加剂(PEP)有取代含磷硫添加剂的趋势。
2)、可溶性油:含80%以上的油,加入乳化剂、添加剂和水,形成不透明的乳化液,胶体颗粒大于1微米,既具有纯油性润滑剂的良好润滑性,也具有水溶液的良好的冷却性,而且能减少着火的危险,使用时需稀释,比例大约是20:1,缺点是容易被细菌污染变质。
同时可用于有色金属的加工,PH值保持在8-9之间。
3)、半合成液:基本上是水溶液,含有少量的油(10-30%),乳化颗粒很少(0.05-1.0微米),半合成液化的冷却性能比可溶性油好但润滑性则不如可溶性油.外观与乳化颗粒大小有关,使用时需要稀释.4)、合成液:不含油的透明水溶液,添加剂加入量可达50%,使用时需要稀释成2-10%水溶液。
机械加工中切削润滑剂的性能研究
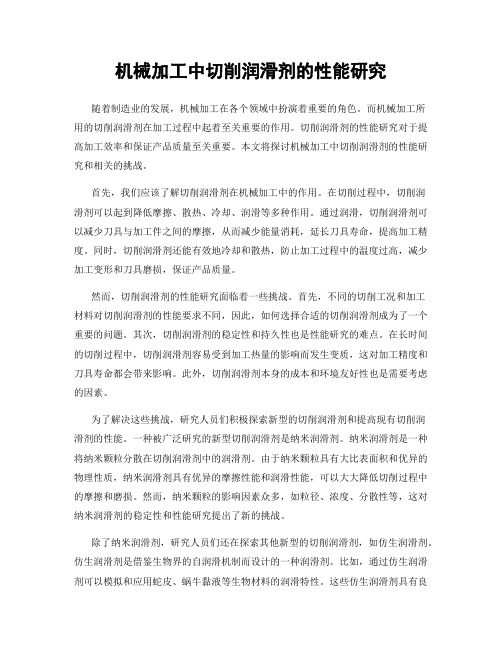
机械加工中切削润滑剂的性能研究随着制造业的发展,机械加工在各个领域中扮演着重要的角色。
而机械加工所用的切削润滑剂在加工过程中起着至关重要的作用。
切削润滑剂的性能研究对于提高加工效率和保证产品质量至关重要。
本文将探讨机械加工中切削润滑剂的性能研究和相关的挑战。
首先,我们应该了解切削润滑剂在机械加工中的作用。
在切削过程中,切削润滑剂可以起到降低摩擦、散热、冷却、润滑等多种作用。
通过润滑,切削润滑剂可以减少刀具与加工件之间的摩擦,从而减少能量消耗,延长刀具寿命,提高加工精度。
同时,切削润滑剂还能有效地冷却和散热,防止加工过程中的温度过高,减少加工变形和刀具磨损,保证产品质量。
然而,切削润滑剂的性能研究面临着一些挑战。
首先,不同的切削工况和加工材料对切削润滑剂的性能要求不同,因此,如何选择合适的切削润滑剂成为了一个重要的问题。
其次,切削润滑剂的稳定性和持久性也是性能研究的难点。
在长时间的切削过程中,切削润滑剂容易受到加工热量的影响而发生变质,这对加工精度和刀具寿命都会带来影响。
此外,切削润滑剂本身的成本和环境友好性也是需要考虑的因素。
为了解决这些挑战,研究人员们积极探索新型的切削润滑剂和提高现有切削润滑剂的性能。
一种被广泛研究的新型切削润滑剂是纳米润滑剂。
纳米润滑剂是一种将纳米颗粒分散在切削润滑剂中的润滑剂。
由于纳米颗粒具有大比表面积和优异的物理性质,纳米润滑剂具有优异的摩擦性能和润滑性能,可以大大降低切削过程中的摩擦和磨损。
然而,纳米颗粒的影响因素众多,如粒径、浓度、分散性等,这对纳米润滑剂的稳定性和性能研究提出了新的挑战。
除了纳米润滑剂,研究人员们还在探索其他新型的切削润滑剂,如仿生润滑剂。
仿生润滑剂是借鉴生物界的自润滑机制而设计的一种润滑剂。
比如,通过仿生润滑剂可以模拟和应用蛇皮、蜗牛黏液等生物材料的润滑特性。
这些仿生润滑剂具有良好的自润滑性能和自修复性能,可以降低切削摩擦和磨损,提高切削精度和加工效率。
机械润滑剂性能研究及应用
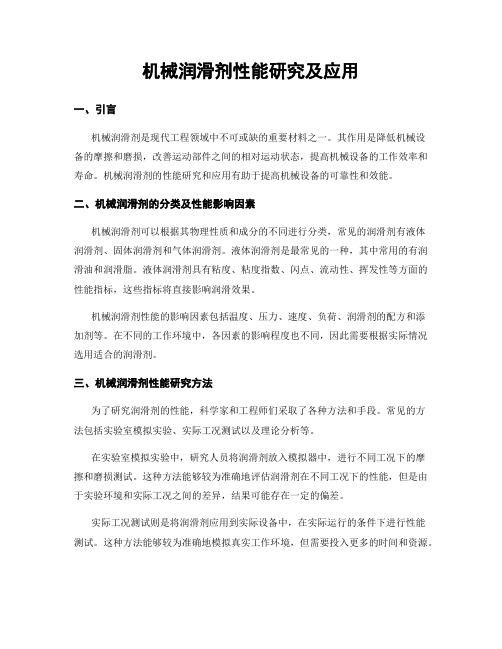
机械润滑剂性能研究及应用一、引言机械润滑剂是现代工程领域中不可或缺的重要材料之一。
其作用是降低机械设备的摩擦和磨损,改善运动部件之间的相对运动状态,提高机械设备的工作效率和寿命。
机械润滑剂的性能研究和应用有助于提高机械设备的可靠性和效能。
二、机械润滑剂的分类及性能影响因素机械润滑剂可以根据其物理性质和成分的不同进行分类,常见的润滑剂有液体润滑剂、固体润滑剂和气体润滑剂。
液体润滑剂是最常见的一种,其中常用的有润滑油和润滑脂。
液体润滑剂具有粘度、粘度指数、闪点、流动性、挥发性等方面的性能指标,这些指标将直接影响润滑效果。
机械润滑剂性能的影响因素包括温度、压力、速度、负荷、润滑剂的配方和添加剂等。
在不同的工作环境中,各因素的影响程度也不同,因此需要根据实际情况选用适合的润滑剂。
三、机械润滑剂性能研究方法为了研究润滑剂的性能,科学家和工程师们采取了各种方法和手段。
常见的方法包括实验室模拟实验、实际工况测试以及理论分析等。
在实验室模拟实验中,研究人员将润滑剂放入模拟器中,进行不同工况下的摩擦和磨损测试。
这种方法能够较为准确地评估润滑剂在不同工况下的性能,但是由于实验环境和实际工况之间的差异,结果可能存在一定的偏差。
实际工况测试则是将润滑剂应用到实际设备中,在实际运行的条件下进行性能测试。
这种方法能够较为准确地模拟真实工作环境,但需要投入更多的时间和资源。
理论分析则是通过建立数学模型和计算机仿真来模拟润滑剂的性能。
这种方法具有较好的可控性和预测性,能够在理论层面上解释和预测润滑剂的行为。
四、机械润滑剂性能的应用机械润滑剂的应用范围广泛,涵盖了工业、农业、航空航天等领域。
在工业生产中,润滑剂能够保护设备免受磨损和腐蚀,延长设备的使用寿命。
在农业领域,润滑剂可以降低农机设备的能耗,提高工作效率。
在航空航天领域,润滑剂则用于保护航空发动机和航天器的运转正常。
除了上述传统应用,近年来,机械润滑剂的研究还涉及到了新兴领域,如纳米润滑剂、生物润滑剂等。
润滑剂的流变特性研究与优化

润滑剂的流变特性研究与优化润滑剂是一种常见的工业材料,广泛应用于汽车、机械设备等领域。
它可以减少摩擦和磨损,提高机器的工作效率和使用寿命。
然而,润滑剂的质量和性能直接影响着机器的运行效果,因此研究和优化润滑剂的流变特性显得尤为重要。
流变特性是指润滑剂在受到外力作用下的变形行为和性质。
研究润滑剂的流变特性能够帮助我们了解其在实际工作过程中的表现,并优化其使用性能。
流变学是研究物质流动和形变特性的科学,通过研究润滑剂在力学、热学和化学等方面的反应,可以揭示其流变特性的内在机理。
在研究润滑剂的流变特性时,我们首先需要了解其黏度。
黏度是衡量润滑剂流动性的重要指标,它描述了润滑剂在外力作用下的抵抗程度。
黏度越高,润滑剂的流动越困难,摩擦和磨损也会增加。
因此,优化润滑剂的黏度对减少能量损失、延长机器寿命至关重要。
除了黏度,润滑剂的剪切变稀性也是了解其流变特性的重要参数。
剪切变稀性指的是润滑剂在经历剪切力作用下,其黏度随剪切速率的变化情况。
润滑剂的剪切变稀性常常表现为剪切变稀性指数,反映了润滑剂在剪切力下黏度变化的程度。
剪切变稀性的研究可以帮助我们选择最合适的润滑剂,在不同工况下保持恒定的黏度和流动性能。
此外,润滑剂的温度敏感性也是影响其流变特性的重要因素。
温度对润滑剂的黏度和剪切变稀性都有显著影响,温度升高会降低润滑剂的黏度,使其流动性更好。
因此,合理选择润滑剂的温度范围,以及调控润滑剂的温度敏感性,对于提高润滑剂的性能至关重要。
在研究和优化润滑剂的流变特性时,我们可以利用流变学的理论和实验方法。
例如,可以通过旋转黏度计测试润滑剂的黏度和剪切变稀性,通过控制温度和剪切速率,获取润滑剂在不同条件下的流变特性数据。
利用这些数据,我们可以建立润滑剂的流变模型,解释其流动和变形行为,为润滑剂的优化设计提供理论依据。
除了理论的研究方法,实验室中的测试也是了解润滑剂流变特性的重要手段。
通过改变润滑剂的成分、添加剂以及加工工艺,我们可以提高润滑剂的流变特性,使其更适应不同的工作条件。
机械工程中的润滑剂性能研究
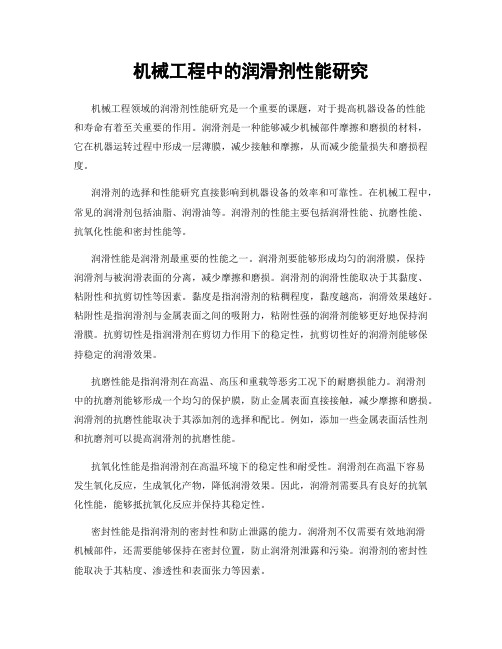
机械工程中的润滑剂性能研究机械工程领域的润滑剂性能研究是一个重要的课题,对于提高机器设备的性能和寿命有着至关重要的作用。
润滑剂是一种能够减少机械部件摩擦和磨损的材料,它在机器运转过程中形成一层薄膜,减少接触和摩擦,从而减少能量损失和磨损程度。
润滑剂的选择和性能研究直接影响到机器设备的效率和可靠性。
在机械工程中,常见的润滑剂包括油脂、润滑油等。
润滑剂的性能主要包括润滑性能、抗磨性能、抗氧化性能和密封性能等。
润滑性能是润滑剂最重要的性能之一。
润滑剂要能够形成均匀的润滑膜,保持润滑剂与被润滑表面的分离,减少摩擦和磨损。
润滑剂的润滑性能取决于其黏度、粘附性和抗剪切性等因素。
黏度是指润滑剂的粘稠程度,黏度越高,润滑效果越好。
粘附性是指润滑剂与金属表面之间的吸附力,粘附性强的润滑剂能够更好地保持润滑膜。
抗剪切性是指润滑剂在剪切力作用下的稳定性,抗剪切性好的润滑剂能够保持稳定的润滑效果。
抗磨性能是指润滑剂在高温、高压和重载等恶劣工况下的耐磨损能力。
润滑剂中的抗磨剂能够形成一个均匀的保护膜,防止金属表面直接接触,减少摩擦和磨损。
润滑剂的抗磨性能取决于其添加剂的选择和配比。
例如,添加一些金属表面活性剂和抗磨剂可以提高润滑剂的抗磨性能。
抗氧化性能是指润滑剂在高温环境下的稳定性和耐受性。
润滑剂在高温下容易发生氧化反应,生成氧化产物,降低润滑效果。
因此,润滑剂需要具有良好的抗氧化性能,能够抵抗氧化反应并保持其稳定性。
密封性能是指润滑剂的密封性和防止泄露的能力。
润滑剂不仅需要有效地润滑机械部件,还需要能够保持在密封位置,防止润滑剂泄露和污染。
润滑剂的密封性能取决于其粘度、渗透性和表面张力等因素。
目前,润滑剂性能研究已经成为机械工程领域中的热点课题。
研究人员通过实验和模拟分析等手段,不断探索润滑剂的改进和优化方法。
例如,研究人员通过添加纳米颗粒改善润滑剂的性能,使其在高温和高压下具有更好的润滑和抗磨损性能。
此外,还有人研究不同润滑剂之间的相容性和替代性,寻找更环保和高效的润滑剂替代品。
金属材料表面润滑剂的研究与优化

金属材料表面润滑剂的研究与优化一、前言金属材料作为重要的制造原材料,其表面润滑剂的研究与优化已成为近年来研究的热点。
随着人们对金属制造品质要求的不断提高,金属材料在生产过程中遇到的表面润滑问题越来越复杂,研究如何优化表面润滑剂的配方并应用于实践中,已成为各个领域工程技术人员共同面临的问题。
本文将就当前表面润滑剂研究领域中的现状、问题及发展趋势进行探讨,并对未来的研究方向提出一些建议。
二、表面润滑剂的研究现状(一)表面润滑剂的定义表面润滑剂是指在金属材料与工具或模具之间起润滑作用的物质。
表面润滑剂在工件表面形成润滑膜,减小工件表面与摩擦体之间的接触力,使得摩擦变得更加顺滑,以达到延长金属材料寿命、提高制造精度、减小能源损失等目的。
(二)表面润滑剂的研究进展自20世纪80年代以来,表面润滑剂的研究和应用有了长足的发展。
随着材料科学和表面技术的不断进步,表面润滑剂的配方和制备工艺得到了不断改进,研究范围也逐渐扩大。
目前,表面润滑剂的研究已经涉及到塑性加工、冷拔、冷轧、挤压、铸造和锻造等领域。
其中,在塑性加工方面,国内外学者已经提出了多种新型表面润滑剂,如有机硅润滑剂、纳米润滑剂、超高分子量聚乙烯润滑剂等。
在冷轧加工方面,研究者们已经探讨了多种新型表面润滑剂的制备方法,如微胶囊润滑剂、纳米润滑剂和有机硅润滑剂等。
这些新型表面润滑剂具有润滑效果好、无污染、易挥发等特点。
在挤压加工方面,新型表面润滑剂的研究也取得了重要进展。
如蜡液、挤压膏、纳米润滑剂和有机硅润滑剂等。
在铸造工艺中,许多新型表面润滑剂正在得到广泛应用,如氧化铝、石墨、纳米润滑剂和有机硅润滑剂等。
总之,近年来,全球各个领域的研究者们在表面润滑剂的研究领域取得了显著的进展,尤其是在新型润滑剂的制备和应用方面有很大的突破。
(三)表面润滑剂的问题表面润滑剂虽然在金属材料加工过程中发挥了重要作用,但也存在一些问题。
首先表面润滑剂涂覆等加工不太便捷,有时候甚至浪费了大量时间;另外,一些表面润滑剂在生产过程中污染环境,对人体健康也造成了潜在的威胁;此外,润滑剂的加工质量不佳对金属加工质量会形成污染。
锻造工艺润滑剂

锻造工艺润滑剂如前所述,锻造分自由锻和模锻,锻造过程可以在冲击(锤锻)条件下进行,也可在慢速(压力机锻造)条件下进行,加工温度分为室温和高温锻造。
不同的锻造工艺对润滑剂的要求也不同。
①锻造用润滑剂的作用与特性。
(a)锻造时施加润滑剂的作用如下:a.降低锻造负荷;b.促进金属在模具中流动;c.防止模具卡死;d.减少模具磨损;e.作为工件和模具间的热障;f.便于工件脱模。
(b)锻造用润滑剂应具备的特性a.能均匀地浸润金属的表面,以防局部无润滑。
b.没有残渣。
因为残渣可能在锻模深处产生积累不容易排除,从而影响锻件公差及工件表面质量。
此外,残渣也不能沉积在设备上。
c.润滑剂不能腐蚀模具,同时可以为模具提供保护涂层作用,具有优良的黏附性。
d.对模具具有一定的冷却作用。
e.适合于自动送进并自动喷涂在模具上。
f.不污染环境,废液容易处理,不形成对人体有害的物质。
g.储存稳定性好。
h.浓缩型润滑剂可稀释成满足于不同润滑要求的锻造工艺用润滑剂。
i.来源广、价格便宜。
②锻造工艺对润滑剂的要求。
锻造加工过程中的润滑剂有液体的,也有固体形态的锻造加工的特点,模具表面一般不易形成较厚的润滑膜。
综合起来考虑,一般要求润滑剂具有以下性能:(a)能够均匀地润湿金属表面,防止局部无润滑剂现象出现;(b)没有残渣,对于模具无腐蚀性;(c)黏附性好;(d)具有一定的冷却性能;(e)适合于自动给料和喷涂给料;(f)储存稳定性好;(g)不污染环境,废液容易处理,不形成对人体有害的物质。
机械润滑剂的性能优化与改进

机械润滑剂的性能优化与改进机械润滑剂是当前工业制造领域不可或缺的重要材料之一。
它的主要作用是减少机械零件间的摩擦和磨损,从而提高机械设备的运行效率和寿命。
然而,目前市场上的机械润滑剂在性能方面仍存在一些局限,因此,对机械润滑剂的性能优化和改进具有重要的研究意义和应用价值。
首先,机械润滑剂的耐高温性能是影响其使用效果的关键因素之一。
在高温环境下,机械润滑剂容易发生分解、氧化和揮发等现象,降低了其润滑性能。
因此,研发基于高温环境下的特殊润滑剂成为了当前的研究热点之一。
例如,利用纳米材料改性机械润滑剂的方式,可以提高其耐高温性能。
纳米材料具有较高的比表面积和界面活性,可以形成有效的润滑膜,提高机械润滑剂在高温下的稳定性和耐磨损性能。
其次,机械润滑剂在使用过程中容易产生污染物,对机械设备的运行稳定性和寿命造成不利影响。
为了解决这一问题,研究人员提出了新型绿色润滑剂的概念。
绿色润滑剂是指替代传统润滑剂的一类新型材料,它在润滑效果上至少不逊于传统润滑剂,并且具有更好的环境友好性。
例如,基于生物可降解材料的绿色润滑剂可以在使用过程中减少对环境的污染,并且可以降低整体生命周期成本。
绿色润滑剂的研究和应用对于推动机械润滑剂的可持续发展及环境保护具有重要意义。
此外,机械润滑剂的粘度和润滑性能也是需要优化和改进的方面之一。
传统的机械润滑剂在不同温度下的粘度特性并不稳定,这会导致机械设备在运行过程中出现润滑不足或润滑过度的问题。
因此,研发具有自适应性的润滑剂成为了新的研究方向。
自适应润滑剂可以根据所处环境的温度和压力条件自动调节其粘度,从而保持合适的润滑状态。
这不仅可以提高机械设备的效率,还可以降低能源消耗和维护成本。
除了润滑能力的改进,机械润滑剂的使用方法也需要进一步优化。
传统的机械润滑剂通常需要频繁添加和更换,这会增加运维成本并且对环境造成一定的影响。
因此,研究人员提出了延长润滑剂更换周期和减少添加量的方式。
例如,采用纳米包覆技术可以将润滑剂包裹在纳米颗粒中,使其在使用过程中释放速度更慢,从而减少了频繁添加的需求。
水基石墨润滑剂试验总结
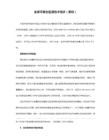
,
锻件经
,
但卡模 现 象 却 比用 重 油 时 明显 减少
。
二
。
。
一
。
验 试后模具硬度
二
注
图纸要求新模具硬度 为
,
润 滑 剂 经 喷枪 喷 出后 在 模 具 表 面 能 生 成 均 匀 而 薄 的 石 墨 膜
,
此 薄膜 呈 黑 灰 色
,
。
,
光亮
,
对 降
脱 模 非常 有 利 低 了 锻 件成 本
。
见表
内
表
水 基 石 墨润 滑剂
一
、
重 油润 滑时 脱 模 情 况 比较
・ ・
’
赢 巡
一
一巡掣几
竺
一
,
… 之 荃 签坚 竺 曼 竺 竺 早 生
矛二 日
, 一 队二
,
鹦
坠生
一
一
一
一
以
”
、 二 姗‘ 。 , 。 眼 我 举肌 供 ” 「
一
一
“。
。 。。 。 二 。 。
卜 …小 石 一 翌竺 一 … 缨 … … 三 少 了竺 些瞥曼 … 一 一一 鹦 燮
一
同 美 国
一
选
,
。
一
一
。
。
。
。
。
。
。
丝
原液冲稀 沉降“ 小时
,
,
一
后
】在 毫 升 处 有 沉 降 趋 势 不 分层
盼 邸
系 数 擦 摩
瞄 耀 呵 泌
———
,
但
】
, 六 、 叹月 又 比
,
,
铝合金热模锻润滑机理研究与应用

第!"卷第!期#$%&!" '$&!!"#$%&$'()*+,%&$)-./&"0"$1()*)年+月,-./()*)铝合金热模锻润滑机理研究与应用李伟华 董选普 陈晓君 吴香清!华中科技大学材料成形与模具技术国家重点实验室"湖北武汉0!))10#摘要 针对传统铝合金热模锻润滑剂进行成膜性和摩擦系数试验"结果表明"含磷酸盐水基石墨在模具表面形成化学反应膜"摩擦系数最小且随温度变化平稳$油基石墨和石墨润滑脂接触面大部分为薄膜润滑"试样表面光洁度较高%同时针对石墨和油斑难清理及环境污染的缺点"提出一种新型环保无石墨润滑剂"可降低摩擦系数和提高试样表面光洁%关键词 铝合金$热模锻$润滑机理!"#&$%&'()('*&+,,-&$%%%.'(/%&0%$%&%'&中图分类号 12'3)&$) 文献标识码 4 文章编号$%%%.'(/% 0%$% %'.56,6789:7-;7<<=+97>+?-?@=A B 8+97>+?-C 69:7-+,C@?87=A C +-A C7==?D :?>;+6@?8E +-EF #G 6+.:A 7"!"H 2I A 7-.<A "JKL HI +7?.*A -"G MI +7-E .N +-E!23435657849$:43$:7$;<435:=4%>$:?=.@4.AB =5C <$-%AD 5E F .$%$@7"G -4H F $.@I .=J 5:K =37$;2E =5.E 54.AD 5E F .$%$@7"L -F 4.0!))10"M F =.4#4B ,>879>&D F 5;=%?N ;$:?=.@O :$O 5:374.A ;:=E 3=$.E $5;;=E =5.3F $3;$:@=.@%-9:=E 4.3KP 5:535K 35A ;$:3:4A =3=$.4%4%-?=.-?4%%$7/D F 5:5K -%3K K F $P3F 433F 5E F 5?=E 4%:54E 3=$.;=%?=K ;$:?5A $.3F 5?$%A K -:;4E 5973F 5P 435:N 94K 5A @:4OF =35E $.N 34=.=.@O F $K O F 435"4.A 3F 5;:=E 3=$.E $5;;=E =5.3=K 3F 5K ?4%%5K 34.A K 349%5P =3F 35?O 5:43-:5E F 4.@=.@$?$K 3$;3F 5E $.34E 3K -:;4E 5953P 55.$=%N 94K 5A %-9:=E 4.3@:4O F =354.A @:4O F =35@:54K 5%-9:=E 43=$.34Q 5K $.3F =.;=%?%-9:=E 43=$.E $.A =3=$."4.A 3F 5K -:;4E 5$;K O 5E =?5.F 4K 4@$$A ;=.=K F /<54.P F =%5";$:3F 5@:4O F =354.A $=%K O $3K 4:5A =;;=E -%33$E %54.4.A 3F 5O :$9N %5?$;5.J =:$.?5.34%O $%%-3=$."4.5P 37O 5$;5.J =:$.?5.34%%7;:=5.A %7.$.N @:4O F =35%-9:=E 4.3KP 4K O -3;$:P 4:A /R 3E 4.:5A -E 5;:=E 3=$.E $5;;=E =5.34.A =?O :$J 53F 5K ?$$3F K -:;4E 5$;3F 5K 4?O%5/O 6DP ?8;,&4%-?=.-?4%%$7$F $3;$:@=.@$%-9:=E 43=$.?5E F 4.=K ?收稿日期 ())S N *(N )S $修订日期 ()*)N )!N !)基金项目 国家重大专项!())S H T )0))")**#$材料成形与模具技术国家重点实验室基金项目!)()(**)))+#作者简介 李伟华!*S U +V #男"硕士研究生$通讯作者&董选普电子信箱 %=P 5=F -4))1 *(+&E $?$A $.@T O?4=%&F -K 3&5A -&E . 随着我国航空航天工业的发展"铝合金热模锻件需求量越来越大"精度要求也越来越高"而锻件的质量直接与模具的润滑有关%但是国内针对铝合金热模锻的润滑研究相对较少"尤其是对铝合金热模锻润滑剂性能的分析(*0)"同时市场上针对铝合金热模锻的润滑剂类型单一"常为石墨系润滑剂(()"虽然石墨具有优良的高温润滑性"但石墨的黑和脏"使得热锻环境恶劣"危害工人健康"并污染环境(!)%因此"本文针对铝合金热模锻工艺"通过对水基石墨"油基石墨和石墨润滑脂这!种传统润滑剂进行成膜性和摩擦系数试验"对比分析了上述润滑剂的成膜性"摩擦系数"试样表面及环境污染情况"同时针对石墨的缺点"对传统模锻润滑剂进行改进"建立了新型环保润滑模型"配制了*种无石墨润滑剂"取得了良好的试验结果%* 试验材料及方法$&$ 试验材料国内模锻用润滑剂通常由!部分组成&!*#主要起润滑作用的基体"如胶体石墨"二硫化钼"硬脂酸盐等$!(#载体又称溶剂"如水"矿物油等$!!#改善润滑剂综合性能的添加剂"如增粘剂*抗氧化剂*极压剂*防锈剂和防腐剂等"同时根据载体的不同"可将润滑剂分为水基型"油基型和润滑脂!种类型(0)%本试验选用的润滑材料有胶体石墨"硬脂酸钠及硬脂酸钙"并配制了如表*试验用润滑剂%$&0 成膜性试验通常铝合金热模锻温度范围为!+)0U )W "模具预热的温度在(") 0()W "因此该成膜性试验模具的加热温度取其预热温度的上限即0()W "然后用喷涂或手工涂抹上润滑剂%该试验的目的是检验润滑剂的高温成膜延展性"对于油基体润滑剂可检测其燃烧情况"水基体润滑剂则可以检测粘结剂性能"同时还可分析其环境污染方面的问题%表$ 试验用润滑剂17B =6$ FA B 8+97->>6,>序号名称成分*水基石墨*水"胶体石墨(水基石墨(水"胶体石墨"磷酸钠!油基石墨*矿物油"胶体石墨0油基石墨(矿物油"胶体石墨"硬脂酸钙"石墨润滑脂矿物油"胶体石墨"硬脂酸钠$&' 摩擦系数试验本试验采用圆环镦粗法即将一定尺寸的圆环件在平砧间进行压缩变形"由圆环件的变形情况推算接触面上的摩擦系数%圆环试样材料为+X )(!8B (#"其尺寸及精度要求见图*%本试验测试了表*所列润滑剂的高温摩擦系数"其测试温度分别为!1)"!S )"0*)"0!)和0")W %测试时将配制好的润滑剂喷涂或手工刷涂在上下模具上"喷涂之前应用丙酮清洗模具和圆环试样表面"去除表面油污杂质等%图* 圆环试样尺寸及精度>=@&* 24?O %5K =H 54.A O :5E =K =$.$;:=.@( 试验结果分析0&$ 试验润滑剂成膜性分析表(为成膜性试验结果"从表(可以得出&水基石墨(中的磷酸盐与模具表面生成化学反应膜"膜的结合强度高"膜中石墨颗粒分布较均匀"多次使用该润滑剂则模具表面的石墨层很难清理"而水基石墨*则是石墨颗粒松散的附着在模具表面"用水很容易清洗掉$油基石墨*的铺展性要比水基石墨要好"但是油份烧损严重"致使石墨颗粒不能均匀分布"而油基石墨(中的硬脂酸盐在此温度下已熔化成液态"使得石墨颗粒分布较为均匀$石墨润滑脂中石墨分布与油基石墨(相同"但三者残留油膜均不易清理(")%另外从环保的角度来看&以上"种润滑剂均有不同程度的环境污染"水基石墨使用时产生的水汽和烟尘中混有一氧化碳和石墨颗粒"很容易对人体造成危害"还可能造成电器短路事故$油基石墨中油份烧损时产生的油烟均是一些不完全燃烧的气体和烟尘"对环境的危害更为严重%表0 成膜性试验17B =60 L Q <68+C 6->7=@+=C 序号使用方式环境影响成膜及铺展状态*喷涂水汽"烟尘成膜"不牢靠"颗粒分布不均(喷涂水汽"烟尘成膜"牢靠"颗粒分布均匀!刷涂油烟成膜"油份烧损严重"颗粒分布不均0刷涂油烟成膜"油份烧损严重"颗粒分布较均匀"刷涂水汽"油烟成膜"油份烧损严重"颗粒分布较均匀0&0 试验润滑剂摩擦系数分析图(为试验润滑剂的高温摩擦系数测试结果"从图(可以看出&在!1) 0")W 温度范围内"水基石墨(的摩擦系数最小"水基石墨*的最大"中间依次为油基石墨(*石墨润滑脂及油基石墨*$随着温度的升高"水基石墨**油基石墨*及水基石墨(摩擦系数均呈上升趋势"其中水基石墨*上升趋势最明显"增加将近了)&*("油基石墨*和水基石墨(则变化较为平稳$石墨润滑脂和油基石墨(的摩擦系数则随温度的升高而出现一定的波动"其差值不超过)&)"%由前面的分析可知"水基石墨*形成的润滑膜是石墨颗粒松散的附着在模具表面"压缩过程中很容易发生破坏从而产生粘模"而水基石墨(则在模具表生成化学反应膜"压缩过程中不容易破坏"但是石墨受环境因素如温度*水分*气氛等有部分消耗"使得其润滑性有一定的降低$油基石墨*则在模具表面形成化学吸附膜"模具与试样接触面大部分为边界流体润滑"而在油份烧损严重的地方则由石墨起润滑作用"而油基石墨(也是形成化学吸附膜"与油基石墨*不同的是在油份缺失的地方则是由硬脂酸盐和石墨共同起润滑作用"其中硬脂酸盐则呈液态或熔融态"增大了边界流体润滑面积"增强了模具与试样间的润滑$石墨润滑脂主要成分与油基石墨相同"其润滑原理是一致的%0&' 圆环试样表面分析图!为!S )W 下压制圆环试样的表面情况"从图!可以看出"整体上采用油基石墨和石墨润滑脂压制的圆环试样表面比水基石墨要光洁"油基石墨和石墨润滑脂的试样表面有残留油斑"水基石墨的试样表面则有残留石墨层"这都是很难清理的$水基石墨*的试样表面凹凸不平"这是由于石墨颗粒"1*第!期李伟华等&铝合金热模锻润滑机理研究与应用图( 试验用润滑剂高温摩擦系数>=@&( Y T O5:=?5.34%F=@F N35?O5:43-:5%-9:=E4.3;:=E3=$.E$5;;=E=5.3是松散的吸附在模具表面"压缩时润滑膜很容易破坏"致使试样与模具接触并产生粘模"而水基石墨(的试样表面则较为平整$油基石墨*刷涂到上下模具上时"润滑膜大部分为液态"油份烧损的部分则由石墨来起润滑作用"而油基石墨(和石墨润滑脂中油份烧损的部分"不仅有石墨还有液态的硬脂酸盐"在压缩的过程中石墨与模具接触较少"因此残留在试样表面的石墨颗粒比油基石墨*要少%图! !S)W圆环试样表面!4#水基石墨* !9#水基石墨( !E#油基石墨*!A#油基石墨( !5#石墨润滑脂>=@&! 2-:;4E5$;:=.@K4?O%543!S)W!4#L435:N94K5A@:4O F=35* !9#L435:N94K5A@:4O F=35( !E#Z=%N94K5A@:4O F=35* !A#Z=%N94K5A@:4O F=35( !5#[:4O F=35@:54K50&/ 传统润滑模型的改进及应用通过上述!方面的分析"能够对这"种润滑剂有较为清晰的了解"这"种润滑剂均为石墨系润滑剂"鉴于石墨的污染与难清理等问题"本文对传统的石墨型润滑剂进行改进"提出*种新型的润滑模型"如图0所示%本文采用硬脂酸钙为润滑材料(+)"乙醇为载体"再加入适量\#]"其中\#]作用有(点&一是使硬脂酸钙颗粒均匀分散在乙醇液体中$二是增强硬脂酸钙与金属模具表面的结合%当该润滑剂喷涂到模具表面时"乙醇迅速挥发掉"短时间内在\#]的作用下硬脂酸钙颗粒均匀分散于模具表面"随着压缩的进行"\#]开始软化和烧损"而硬脂酸钙也熔化成液态"于是在试样与模具表面形成了一层液态润滑膜"可明显减少粘模的发生%从图"可以看出"改进润滑剂的摩擦系数均比传统润滑剂要小"随温度变化也相对平稳"另外从图+可以看出"改进润滑剂的试样表面有明显的改善"残留的硬脂酸钙用热水很容易清理掉"整个测试过程中除了酒精迅速挥发外"其他对环境的污染均较小%图0 改进润滑模型>=@&0 R?O:$J5A%-9:=E43=$.?$A5%图" 改进润滑剂与传统润滑剂摩擦系数对比>=@&" R?O:$J5A%-9:=E4.3;:=E3=$.E$5;;=E=5.3E$?O4:5AP=3FE$.J5.3=$.4%%-9:=E4.3K! 结论!*#水基石墨(在模具表面形成化学反应膜使得其膜的稳定性均高于物理吸附的水基石墨**油基石墨**油基石墨(及油基石墨!"其摩擦系数也明显较小且随温度变化平稳%!(#油基石墨和石墨润滑脂大部分接触面为边界流体润滑状态使得其试样表面的光洁度均高于水基石墨"但是残留的油斑和石墨很难清理%+1*锻 压 技 术 第!"卷图+ !S)W改进润滑剂与传统润滑剂试样表面对比4 改进润滑剂 9 水基石墨( E 油基石墨( >=@&+ R?O:$J5A%-9:=E4.3$;K4?O%543!S)WE$?O4:5AP=3F E$.J5.3=$.4%%-9:=E4.3K4 R?O:$J5A%-9:=E4.3 9 L435:N94K5A@:4O F=35(E Z=%N94K5A@:4O F=35( ! 依照改进润滑膜型配制的润滑剂与传统润滑剂相比 摩擦系数明显降低 试样表面光洁得到改善 残留硬脂酸钙容易清理且对环境的污染减小参考文献* 朱本 高爱华 陈能秀 等/铝合金精密模锻润滑剂的研究与应用 , /中南冶金学院学报 *S S* (( ! (S0!))/ ( 姜瑞虎 于群/热锻润滑剂的开发与应用 , /山东机械 *S S0 0 !*!0/! 王文斌 胡汉国 张华豪/环保型热模锻压剂的研制及应用 , /汉南石油 ())( *+ ( """1/0 吴代斌/热模锻润滑剂的探讨 , /金属成形工艺 *S S!** 0 *+"*++/" 赵振铎 邵明志 张昭锋 等/金属塑性成形中的磨擦与润滑 < /北京 化学工业出版社 ())0/+ 聂振江/轻合金热模锻用粉末状无石墨工艺润滑剂 , /轻合金加工技术 *S1! " 00"*/11*第!期李伟华等 铝合金热模锻润滑机理研究与应用。
[氮化硼(BN)在锻造润滑剂上的应用]_锻压文献_氮化硼,锻造润滑剂
![[氮化硼(BN)在锻造润滑剂上的应用]_锻压文献_氮化硼,锻造润滑剂](https://img.taocdn.com/s3/m/ab9e8f62783e0912a2162ab8.png)
氮化硼(BN)在锻造润滑剂上的应用新闻摘要:目前在一些特殊合金的锻造制程中,会在胚料本体被覆一层玻璃系防氧剂,以达到加热过程中减少胚料氧化的效果.锻造过程中的润滑剂水溶性六方氮化硼来取代玻璃系防氧剂与石墨,生产成本并不会增加,但却可以显著改善锻造厂的工作环境,并将锻造产业带入绿色生产产业的行列之中。
氮化硼(BN)共有三种结晶构造,分别是六方氮化硼(HBN),密排六方氮化硼(WBN)和立方氮化硼(CBN)。
WBN和CBN是由HBN在高温、高压下转变而成,HBN在常压是稳定相,WBN和CBN是高压稳定相,在常压下是亚稳相。
虽然立方氮化硼(简称CBN),其硬度接近世界上最硬的金刚石,但是HBN却具有类似石墨的层状结晶结构(图一),其晶体结构为每一层由B、N原子相间排列成六角环网络,层内原子之间由很强的共价键所结合,所以结构紧密;层间则为分子键结合,结合力弱,所以层间容易受侧推剪力而互相滑动。
(层内B-N原子间距0.142nm,弹性模量为910Gpa,而层间原子间距为0.335nm,弹性模量只有30Gpa),并且HBN颜色为白色所以向来有白石墨之称。
由于六方氮化硼具有类似石墨的层状结晶结构,所以六方氮化硼也和石墨一样,具有很好的润滑性,和一般热间锻造常用的石墨润滑剂相比较,六方氮化硼虽然价格偏高,但如图二所示,石墨在使用温度超过400度的时候,石墨的润滑性能,将会急遽下降,但六方氮化硼在600℃时,摩擦系数仍然维持在0.2左右,润滑性能受温度的影响很小,所以可以看出六方氮化硼特别适用于高温锻造,并且HBN的颜色为白色,不会污染锻造制品,干净且环保。
目前在一些特殊合金的锻造制程中(例如钛合金锻造),会在胚料本体被覆一层玻璃系防氧剂,以达到加热过程中减少胚料氧化的效果并作为锻造过程中的润滑剂,但通常这些玻璃系防氧剂的润滑效果并不理想/,所以业者会在模具上再喷覆一层石墨,以加强锻造时的润滑效果。
其中由于玻璃系防氧剂被覆与去除过程所使用的溶剂会对环境造成污染,所以这样的制程并无法达到绿色生产的目标。
在不同润滑油下齿轮锻造材料摩擦特性研究
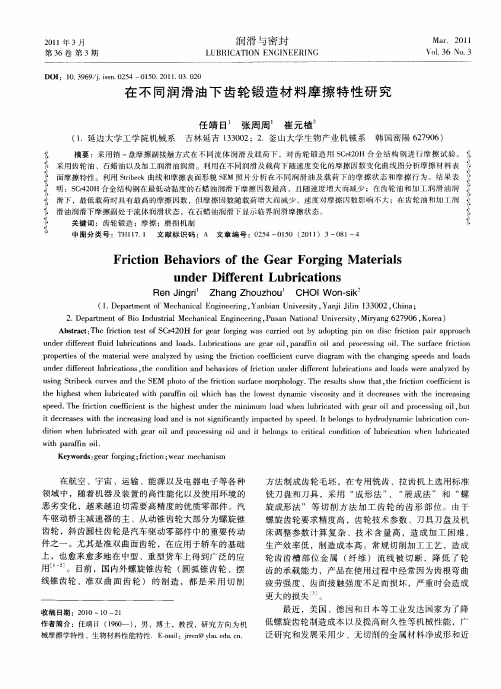
Ab ta tT e f c in ts fS 4 0 fr g a o gn a are u y a o t g p n o ic fit n p i a p o c sr c : h r t e to Cr 2 H o e rfr ig w sc rid o tb d p i i n ds rci ar p r a h i o n o u d rd f r n u d l b iain n o d . u rc t n r e rol p rf n ola d p o e sn i. h u fc rcin n e i e e tf i u rc t sa d la s L b ai sa e g a i , a af i n rc si g ol T e s ra e fit f l o i o i o p o et so h tra r n lz d b sn h rcin c e ce tc re da r m t h h n i p e sa d la s r p ri ft emae l e i wee a ay e y u i gt ef to o f i n u v iga wih t ec a gngs e d n o d i i u d rdfe e tlb c t n ,h o dto n e voso ito n e i ee tl b c to sa d la r n lz d b n e i r n u r ai s t ec n i n a d b ha ir ff cin u d rdf r n u r ain n o dswe ea ay e y f i o i r f i u i g Srb c u v sa d te S sn t e k c r e n h EM h t ft efit n s ra emop oo y T e rs lss o ta ,h rcin c e ce t s i p ooo h rci u c r h lg . h e ut h w h t t efito o f in o f i i t e hg e twh n lb iae t aa n 0lwh c a h o s y a c vs o iy a d i d c e s s wi h n ra ig h ih s e u rc td wi p rf i h i ih h s te lwetd n mi ic st n t e r a e t te ic e sn h s e d. h rcin c e ce ti h ih s n e h n mu la e u rc td wih g a i a d p o e sn i , u p e T e f t o f in ste h g e tu d rt e mii m o d wh n lb ae t e rol n rc sig ol b t i o i i i d c e s swi h n ra igla n sn tsg i c nl mp ce ys e d.tb ln st y rd n mi u rc to o — t e r a e t t ei ce sn o da d i o in f a tyi a td b p e I eo g oh d o y a c lb iain c n h i
《精锻机锻造锻透性及相关工艺研究》范文
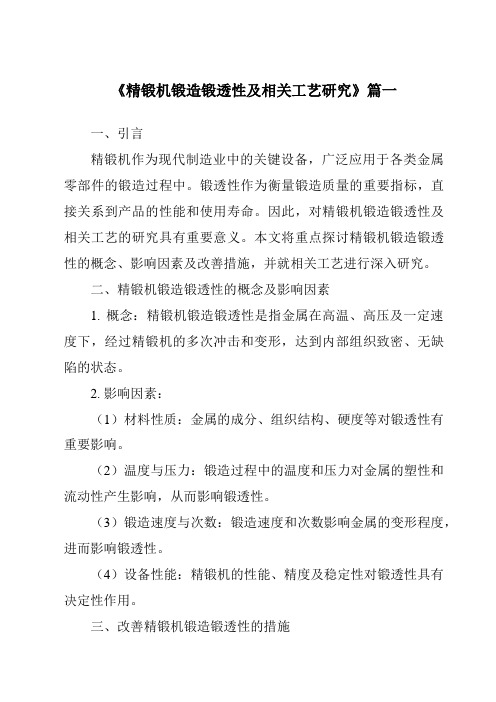
《精锻机锻造锻透性及相关工艺研究》篇一一、引言精锻机作为现代制造业中的关键设备,广泛应用于各类金属零部件的锻造过程中。
锻透性作为衡量锻造质量的重要指标,直接关系到产品的性能和使用寿命。
因此,对精锻机锻造锻透性及相关工艺的研究具有重要意义。
本文将重点探讨精锻机锻造锻透性的概念、影响因素及改善措施,并就相关工艺进行深入研究。
二、精锻机锻造锻透性的概念及影响因素1. 概念:精锻机锻造锻透性是指金属在高温、高压及一定速度下,经过精锻机的多次冲击和变形,达到内部组织致密、无缺陷的状态。
2. 影响因素:(1)材料性质:金属的成分、组织结构、硬度等对锻透性有重要影响。
(2)温度与压力:锻造过程中的温度和压力对金属的塑性和流动性产生影响,从而影响锻透性。
(3)锻造速度与次数:锻造速度和次数影响金属的变形程度,进而影响锻透性。
(4)设备性能:精锻机的性能、精度及稳定性对锻透性具有决定性作用。
三、改善精锻机锻造锻透性的措施1. 优化材料选择:选用成分稳定、组织致密的金属材料,提高其可锻性。
2. 控制温度与压力:合理控制锻造过程中的温度和压力,确保金属在最佳状态下进行变形。
3. 调整锻造速度与次数:根据产品需求,调整合适的锻造速度和次数,提高金属的变形程度。
4. 提高设备性能:对精锻机进行技术升级和改造,提高其性能、精度及稳定性。
四、相关工艺研究1. 预处理工艺:在锻造前,对金属进行预处理,如预热、退火等,以提高其可塑性和降低变形抗力。
2. 润滑工艺:在锻造过程中,采用合适的润滑剂,减少金属与模具之间的摩擦,降低能耗和提高产品质量。
3. 模具设计及制造工艺:优化模具设计,提高模具的精度和寿命,确保产品尺寸精度和表面质量。
同时,采用先进的制造工艺,提高模具的制造效率。
4. 后续处理工艺:对锻造后的产品进行后续处理,如淬火、回火等,以提高产品的硬度和耐腐蚀性。
五、结论精锻机锻造锻透性是衡量锻造质量的重要指标,对产品的性能和使用寿命具有重要影响。
高端机械制造业中的新型润滑液研究与应用
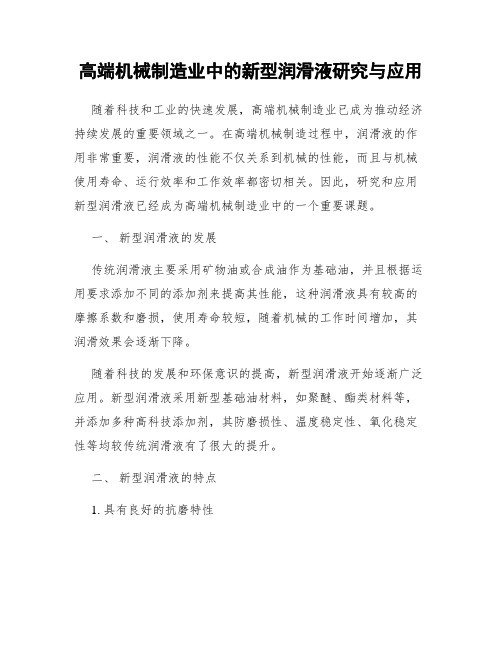
高端机械制造业中的新型润滑液研究与应用随着科技和工业的快速发展,高端机械制造业已成为推动经济持续发展的重要领域之一。
在高端机械制造过程中,润滑液的作用非常重要,润滑液的性能不仅关系到机械的性能,而且与机械使用寿命、运行效率和工作效率都密切相关。
因此,研究和应用新型润滑液已经成为高端机械制造业中的一个重要课题。
一、新型润滑液的发展传统润滑液主要采用矿物油或合成油作为基础油,并且根据运用要求添加不同的添加剂来提高其性能,这种润滑液具有较高的摩擦系数和磨损,使用寿命较短,随着机械的工作时间增加,其润滑效果会逐渐下降。
随着科技的发展和环保意识的提高,新型润滑液开始逐渐广泛应用。
新型润滑液采用新型基础油材料,如聚醚、酯类材料等,并添加多种高科技添加剂,其防磨损性、温度稳定性、氧化稳定性等均较传统润滑液有了很大的提升。
二、新型润滑液的特点1. 具有良好的抗磨特性新型润滑油能够形成润滑膜层,在机械的工作过程中,润滑膜可以有效地降低机械零件之间的磨损程度。
新型润滑液具有更高的黏度指数,比传统润滑液更加稳定,使用寿命更长。
2. 具有高温稳定性新型润滑液的基础油材料主要采用合成酯类材料等,其温度稳定性远远高于传统的矿物油或合成油,即使在极端温度下也能始终保持稳定的润滑特性。
3. 具有环保性新型润滑液使用的是环保型基础油材料,大多数材料经过环保认证,不会对环境造成污染。
在使用后,新型润滑液可以进行回收利用,有利于环境保护。
三、新型润滑液在高端机械制造业中的应用在高端机械制造业中,新型润滑液的应用越来越广泛。
随着机械制造技术的不断提高,对润滑要求也越来越高,新型润滑液的特点可以很好地满足各类机械的不同运用要求。
例如,在汽车制造业中,新型润滑液的抗磨损性、高温稳定性和环保性等都能够满足严格的要求。
在飞机、船舶等领域中,新型润滑液因其稳定性和抗摩擦性等特点,能够确保机械部件的运行效率并延长使用寿命。
总之,新型润滑液已经成为高端机械制造业中的一个重要部分。
基于优化锥形锻造法的热锻润滑剂性能评价
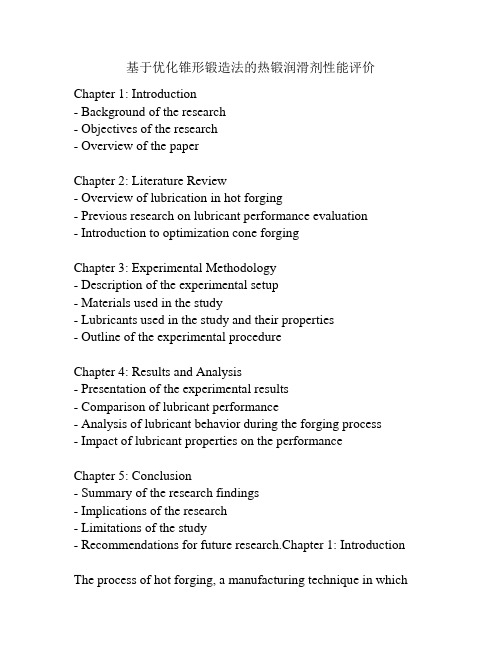
基于优化锥形锻造法的热锻润滑剂性能评价Chapter 1: Introduction- Background of the research- Objectives of the research- Overview of the paperChapter 2: Literature Review- Overview of lubrication in hot forging- Previous research on lubricant performance evaluation- Introduction to optimization cone forgingChapter 3: Experimental Methodology- Description of the experimental setup- Materials used in the study- Lubricants used in the study and their properties- Outline of the experimental procedureChapter 4: Results and Analysis- Presentation of the experimental results- Comparison of lubricant performance- Analysis of lubricant behavior during the forging process- Impact of lubricant properties on the performanceChapter 5: Conclusion- Summary of the research findings- Implications of the research- Limitations of the study- Recommendations for future research.Chapter 1: Introduction The process of hot forging, a manufacturing technique in whichmetal objects are formed at high temperatures by hammering or pressing, requires the use of significant amounts of lubrication in order to maintain efficient manufacturing production. The choice of lubricant plays a crucial role in determining the success of the forging process, by regulating friction and preventing wear on the tools and dies used in the forging process. The optimization cone forging process is a method of hot forging which is gaining popularity in industrial manufacturing settings, due to its ability to produce complex shapes with high accuracy and efficiency.The objective of this paper is to evaluate the performance of lubricants used in the optimization cone forging process. Specifically, we will examine lubricant behavior during the forging process, and compare the performance of different lubricants used in the process. Understanding the properties of lubricants and their impact on the forging process is crucial for identifying effective and efficient lubrication techniques for optimization cone forging.The paper is organized as follows. The second chapter will summarize previous research on lubrication in hot forging, as well as provide background on the optimization cone forging process. The third chapter will outline the experimental methodology used in our study, including the materials and lubricants used and the experimental procedure.Chapter 2: Literature ReviewLubrication is critical in the hot forging process, as it helps to regulate friction at the contact surfaces of the metal pieces, as well as between the tools and dies used for shaping the metal. Thechoice of lubricant is largely determined by its ability to reduce friction and wear on the tools, as well as its durability under high temperatures and pressures. Many studies have been conducted on improving the lubrication performance in hot forging, with various methods being used to evaluate lubricant performance. Common methods of evaluation include tribological testing, investigations into the film formation of lubricants, and finite element simulations.One method of hot forging which is gaining popularity in industrial settings is the optimization cone forging process. Optimization cone forging is a hot forging process in which the workpiece is shaped into a cone shape, with a cross-sectional area that is smaller at the base of the cone. The cone is then placed over a mandrel, which is forced through the center of the cone to complete the shaping process. Optimization cone forging has several advantages over other hot forging methods, including the ability to produce complex shapes with high accuracy and efficiency, and the ability to reduce material waste.Chapter 3: Experimental MethodologyIn this study, we evaluated the performance of several lubricants in the optimization cone forging process. The experiment was conducted using a custom-built forging setup, designed specifically for optimization cone forging. The setup consisted of a hydraulic press, a mandrel, and a pair of dies. The mandrel, which was made of steel, was used to shape the metal piece into a cone shape, while the dies were used to apply the force required to complete the forging process.Several different lubricants were used in the study, including mineral oil, graphite, and borax. Each of the lubricants used had different properties, including viscosity, density, and melting point, which were taken into account when selecting the lubricants used in the study. The lubricants were applied to the mandrel and dies using a spray gun, and the consistency and coverage of each lubricant was carefully controlled.For each trial, the metal piece was heated to a temperature of 1000°C, and then placed on the mandrel. The dies were then closed, and the hydraulic press was used to apply the required force to the dies to complete the forging process. The entire process was monitored in real-time using high-speed cameras, which allowed us to observe the lubricant behavior during the forging process.In order to assess the performance of each lubricant, we measured the force required to complete the forging process, as well as the temperature at the contact surfaces of the metal piece, the mandrel, and the dies. We also examined the surface finish of the metal piece and the wear on the mandrel and dies after each trial. These metrics were then compared to assess the performance of each lubricant.Chapter 4: Results and AnalysisThe performance of each lubricant was evaluated by measuring the force required to complete the forging process, the temperature at the contact surfaces of the metal piece, the mandrel, and the dies, and the surface finish of the metal piece. The results of each trial were compared to assess the performance of each lubricant.The force required to complete the forging process wassignificantly reduced when using the graphite lubricant, compared to the other lubricants tested. The cross-sectional area of the metal piece was also better maintained when using the graphite lubricant, resulting in a smoother surface finish. The borax lubricant performed well in terms of surface finish, but required a higher force to complete the forging process. The mineral oil lubricant performed poorly in all metrics, requiring a high force to complete the forging process and resulting in a rough surface finish on the metal piece.The temperatures at the contact surfaces were also monitored, with the borax lubricant resulting in the lowest temperatures at the contact surfaces, followed by the graphite lubricant and the mineral oil lubricant. The high temperatures experienced during the forging process can lead to oxidation and other forms of wear on the tools and dies, making lower temperatures at the contact surfaces desirable.Overall, the graphite lubricant performed the best in terms of reducing the force required to complete the forging process, maintaining the cross-sectional area of the metal piece, and resulting in a smooth surface finish. The borax lubricant performed well in terms of temperature control and surface finish, but required a higher force to complete the forging process. The mineral oil lubricant performed poorly in all metrics.Chapter 5: Conclusion and Future WorkThe results of this study highlight the importance of lubrication in the optimization cone forging process. The choice of lubricant iscritical in determining the success of the forging process, as it regulates friction and wear on the tools and dies used in the process. The graphite lubricant performed the best in terms of reducing the force required to complete the forging process, maintaining the cross-sectional area of the metal piece, and resulting in a smooth surface finish.Future work in this area could include exploring the impact of different types of lubricants on the optimization cone forging process. In this study, we tested three common lubricants, but there are many other lubricants with different properties that could be evaluated. Additionally, further investigations into the film formation of lubricants and the behavior of the lubricant during the forging process could provide a deeper understanding of the lubrication process.Finally, there is also potential to optimize the optimization cone forging process itself by exploring the impact of variables such as the temperature of the metal piece, the velocity of the mandrel, and the composition of the metal piece. By improving our understanding of the optimization cone forging process and the role of lubrication within it, we can improve the efficiency and quality of hot forging processes in manufacturing settings.。
气门锻压模具润滑改进及对比分析
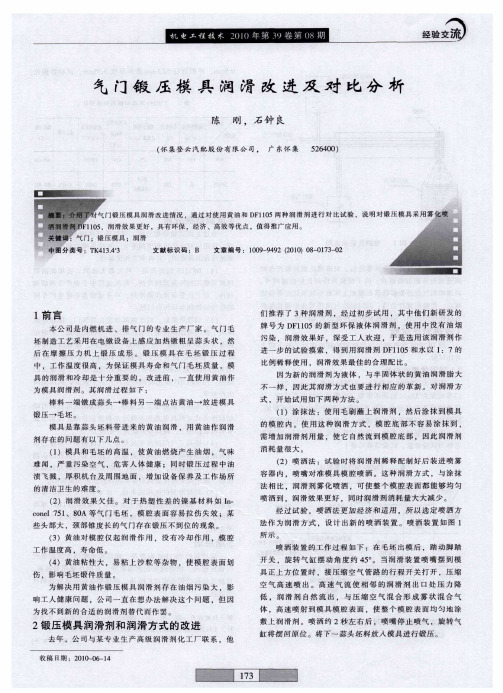
中 ,工 作 温 度很 高 ,为保 证 模 具 寿 命 和气 门 毛 坯 质 量 ,模 具 的 润 滑 和 冷 却 是 十 分 重 要 的 。改 进 前 ,一 直 使 用 黄 油 作
为 模 具 润 滑 剂 。 其润 滑过 程 如 下 : 棒 料 一 端 镦 成 蒜 头 一 棒 料 另 一 端 点 沾 黄 油 一 放 进 模 具
工 作 温 度 高 ,寿 命低 。
喷 洒 装 置 的工 作 过 程 如 下 :在 毛坯 出模 后 ,踏 动 脚 踏
( )黄 油 粘 性 大 , 易 粘 上 沙 粒 等 杂 物 。使 模 腔 表 面 划 4
伤 ,影 响 毛 坯 锻 件质 量 。
为 解 决 用 黄 油 作 锻 压 模 具 润 滑 剂 存 在 油 烟 污 染 大 . 影
开 关 , 旋 转 气 缸 摆 动 角度 约 4 。 当 润 滑 装 置 喷 嘴 摆 到 模 5。 具 正 上 方 位 置 时 ,接 压 缩 空 气 管 路 的行 程 开 关 打 开 ,压 缩 空 气 高 速 喷 出 。 高 速 气 流 使 相 邻 的 润 滑 剂 出 口处 压 力 降
响 工 人 健 康 问题 ,公 司一 直 在 想 办 法 解 决 这 个 问 题 ,但 因 为 找 不 到 新 的 合 适 的 润 滑 剂替 代 而 作 罢 。
低 ,润 滑 剂 自然 流 出 , 与 压 缩 空 气 混 合 形 成 雾 状 混 合 气
体 ,高 速 喷 射 到模 具模 腔 表 面 .使 整 个 模 腔 表 面 均 匀 地 涂 敷 上 润 滑 剂 。 喷洒 约 2秒 左 右 后 , 喷 嘴 停 止 喷 气 ,旋 转 气 缸将 摆 回原 位 。将 下~ 蒜 头 坯 料 放 入 模 具 进 行 锻 压 。
锻压机对润滑油的要求

锻压机对润滑油的要求很高,主要表现在以下几个方面:
1. 良好的润滑性能:锻压机在工作中会产生很大的负荷和摩擦力,因此要求润滑油具有良好的润滑性能,能够有效地减少摩擦和磨损,降低设备运行中的摩擦阻力,从而保护设备,延长设备使用寿命。
2. 良好的清洁性能:锻压机在工作中会产生金属屑和杂质,这些杂质会污染润滑油并影响润滑效果。
因此,要求润滑油具有良好的清洁性能,能够有效地清除油中的杂质和金属屑,保持油品的清洁度和透明度。
3. 良好的抗氧化性能:锻压机在工作中会产生高温和高压的环境,这种环境下润滑油容易氧化变质。
因此,要求润滑油具有良好的抗氧化性能,能够有效地延缓油品的氧化进程,保持油品的稳定性和性能。
4. 良好的抗泡性能:锻压机在工作中会产生大量的泡沫和气泡,这些泡沫和气泡会影响润滑油的流动性和润滑效果。
因此,要求润滑油具有良好的抗泡性能,能够有效地减少泡沫和气泡的产生,保持油品的流动性和润滑效果。
5. 适当的粘度:锻压机在工作中需要润滑油具有一定的粘度,以保持设备的润滑效果。
但是,过高的粘度会增加摩擦力和磨损,过低的粘度则无法提供足够的润滑效果。
因此,要求润滑油具有适当的粘度,根据设备的工作环境和条件选择合适的粘度等级。
总之,为了确保锻压机的正常运转和延长使用寿命,必须选择适
合的润滑油并加强对其维护和保养。