超声波检测工艺规程
超声波检测工艺规程

超声波检测工艺规程1适用范围1.1 本工艺适用于板厚为6-250mm得板材、碳素钢与低合金钢锻件、母材壁厚8—400mm得全焊透熔化焊对接焊缝及壁厚大于等于4mm,管径为57—1200mm碳素钢与低合金石油天然气长输、集输与其她油气管道环向对接焊缝、钢质储罐对接焊缝得超声波检测等、1。
2 本工艺规定了使用A型脉冲反射式超声波探伤仪进行检测过程中,对受检设备做出准确判定应遵循得一般程序与要求。
1、3 引用标准JB4730/T—2005《承压设备无损检测》SY/T4109-2005《石油天然气钢质管道无损检测》GB11345-89《钢焊缝手工超声波探伤方法与探伤结果得分级》JB/T9214-1999《A型脉冲反射式超声探伤系统测试方法》JB/T10062-1999《超声探伤用探头性能测试方法》GB50128—2005《立式圆筒形钢制焊接储罐施工及验收规范》2对检测人员得要求2、1 从事超声波检测人员必须经过培训,持证上岗。
只有取得质量技术监督部门颁发得超声波检测技术等级证书得人,方可独立从事与该等级相应得超声波检测工作、2、2 检测人员应具有良好得身体素质,其校正视力不得低于 5.0,并每年检查一次。
2、3检测人员应严格执行《检测作业安全防护指导书》与其它安全防护规定,确保安全生产。
3检测程序3、1根据工程特点与本工艺编制具体得《无损检测技术方案》。
3.2受检设备经外观检查合格后,由现场监理或检验员开据《无损检测指令》或《无损检测委托单》到检测中心。
3。
3 检测人员按指令或委托单要求进行检测准备,技术人员根据实际情况编制《探伤工艺卡》、3、4 检测人员按《超声波探伤仪调试作业指导书》等工艺文件进行设备调试。
3.5 外观检查合格后,施加耦合剂,实施检测,做好《超声波检测记录》。
3。
7 根据检测结果与委托单,填写相应得回执单或合格通知单、若有返修,还应出据《返修通知单》,标明返修位置等。
将回执单与返修通知单递交监理或检验员,同时对受检设备进行检验与试验状态标识。
超声波检测工艺规程完整
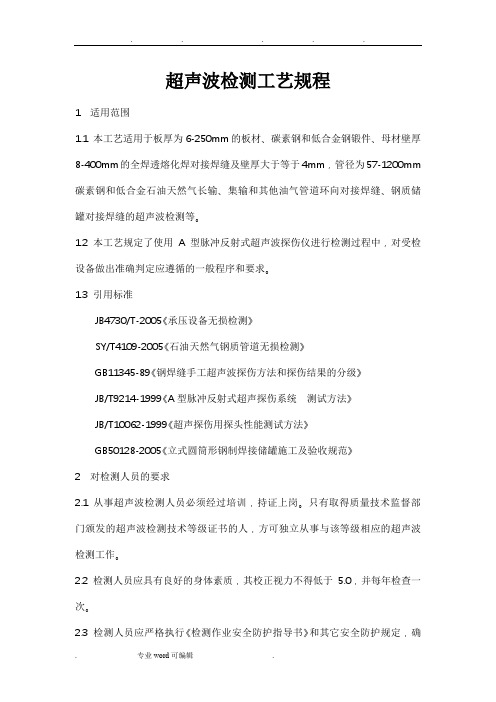
超声波检测工艺规程1适用范围1.1 本工艺适用于板厚为6-250mm的板材、碳素钢和低合金钢锻件、母材壁厚8-400mm的全焊透熔化焊对接焊缝及壁厚大于等于4mm,管径为57-1200mm 碳素钢和低合金石油天然气长输、集输和其他油气管道环向对接焊缝、钢质储罐对接焊缝的超声波检测等。
1.2 本工艺规定了使用A型脉冲反射式超声波探伤仪进行检测过程中,对受检设备做出准确判定应遵循的一般程序和要求。
1.3 引用标准JB4730/T-2005《承压设备无损检测》SY/T4109-2005《石油天然气钢质管道无损检测》GB11345-89《钢焊缝手工超声波探伤方法和探伤结果的分级》JB/T9214-1999《A型脉冲反射式超声探伤系统测试方法》JB/T10062-1999《超声探伤用探头性能测试方法》GB50128-2005《立式圆筒形钢制焊接储罐施工及验收规范》2对检测人员的要求2.1 从事超声波检测人员必须经过培训,持证上岗。
只有取得质量技术监督部门颁发的超声波检测技术等级证书的人,方可独立从事与该等级相应的超声波检测工作。
2.2 检测人员应具有良好的身体素质,其校正视力不得低于5.0,并每年检查一次。
2.3检测人员应严格执行《检测作业安全防护指导书》和其它安全防护规定,确保安全生产。
3检测程序3.1 根据工程特点和本工艺编制具体的《无损检测技术方案》。
3.2 受检设备经外观检查合格后,由现场监理或检验员开据《无损检测指令》或《无损检测委托单》到检测中心。
3.3 检测人员按指令或委托单要求进行检测准备,技术人员根据实际情况编制《探伤工艺卡》。
3.4 检测人员按《超声波探伤仪调试作业指导书》等工艺文件进行设备调试。
3.5 外观检查合格后,施加耦合剂,实施检测,做好《超声波检测记录》。
3.7 根据检测结果和委托单,填写相应的回执单或合格通知单。
若有返修,还应出据《返修通知单》,标明返修位置等。
将回执单和返修通知单递交监理或检验员,同时对受检设备进行检验和试验状态标识。
超声波检测工艺规程

1.适用范围:适用于母材厚度为8mm到100mm的全熔透铁素体钢焊缝,也可用于厚度大于100mm的其它类型焊缝,材料。
但是应用时必须考虑部件的几何声学性能,同时设定足够的灵敏度使标准的验收等级可以使用。
2.检测人员:2.1从事焊缝检测检测的人员,应根据EN 473或相关工业区中等同的标准规定,获得相应的资格水平。
2.2从事焊缝检测人员必须掌握超声波探伤的基础知识,具有足够的焊缝超声波探伤经验,并掌握一定的材料、焊接基础知识。
熟知与要检测的焊缝接头相关连的测试问题。
如工件的材质、坡口形式、焊接工艺、缺陷可能出现的位置等。
3.检测设备3.1检测中使用任何设备,必须与欧洲相关标准的要求一致,设备的有关EN标准出版之前,可采用相类似的国家标准。
3.2探头的频率应在2MHZ~5MHZ之间,但选择的频率应符合规定的验收等级。
3.3当要求采用超声波束从对面反射技术和横波进行检测,必须确保超声波束与对立面之间呈斜角,斜角不能小于35°最好不大于70°,在不只使用一个探头角度处,至少使用一个角度探头,才能满足要求,使用一个探头角度,应保证焊接熔融面能检测到,或者尽可能的接近正常斜度,当规定使用2个或多个探头角度时,工称超声波束角度之间应大于或等于10°。
4.设备鉴定4.1在进行检测之前,应设定范围和灵敏度,在检测过程中,至少每4小时要对这些设定值进行一次确认,无论什么时候,只要系统参数值发生了变化,或者相关设定值发生了变化,也需要进行检测。
4.2在检测过程之中发现灵敏度和范围的偏差不在允许范围之内,都应进行重新5.仪器的校准与检测灵敏度5.1试块采用主要是国际焊接学会的IIW-I、IIW-II试块以及¢3mm长横孔试块,和¢1mm、¢1.5mm、¢2mm、¢3mm、¢6mm平底孔试块。
5.2 应使用下列方法之一来设定参考等级5.2.1 直径3mm的横孔5.2.2 使用基于圆盘形反射体(DSR)的使用量距系统(DGS)的横向波和纵向波5.2.3 参照基准一个1mm深的矩形槽5.2.4 窜列DDSR=6mm(适用于所有厚度)4种方法参考线、评定线、和记录线见下表6.准备与检测6.1检测面应无焊接飞溅,锈蚀、油垢或其它影响探头平滑移动和耦合的异物,如有深坑应补焊,必要时应使用砂轮机打磨或其他方法修正,检测表面的不平整度应确保焊缝表面与探头表面间隙不超过0.5mm,如果表面粗糙度不大于6.3μm机加工表面,或者不大于喷丸处理12.5μm,则认为检测面是满足要求的。
超声波检测工艺规程完整
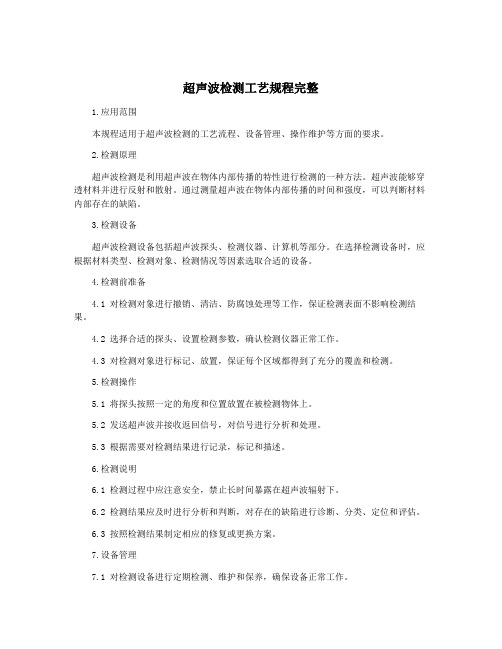
超声波检测工艺规程完整1.应用范围本规程适用于超声波检测的工艺流程、设备管理、操作维护等方面的要求。
2.检测原理超声波检测是利用超声波在物体内部传播的特性进行检测的一种方法。
超声波能够穿透材料并进行反射和散射。
通过测量超声波在物体内部传播的时间和强度,可以判断材料内部存在的缺陷。
3.检测设备超声波检测设备包括超声波探头、检测仪器、计算机等部分。
在选择检测设备时,应根据材料类型、检测对象、检测情况等因素选取合适的设备。
4.检测前准备4.1 对检测对象进行撤销、清洁、防腐蚀处理等工作,保证检测表面不影响检测结果。
4.2 选择合适的探头、设置检测参数,确认检测仪器正常工作。
4.3 对检测对象进行标记、放置,保证每个区域都得到了充分的覆盖和检测。
5.检测操作5.1 将探头按照一定的角度和位置放置在被检测物体上。
5.2 发送超声波并接收返回信号,对信号进行分析和处理。
5.3 根据需要对检测结果进行记录,标记和描述。
6.检测说明6.1 检测过程中应注意安全,禁止长时间暴露在超声波辐射下。
6.2 检测结果应及时进行分析和判断,对存在的缺陷进行诊断、分类、定位和评估。
6.3 按照检测结果制定相应的修复或更换方案。
7.设备管理7.1 对检测设备进行定期检测、维护和保养,确保设备正常工作。
7.2 对设备进行合理的存放和保管,防止损坏和丢失。
7.3 对设备使用情况进行合理管理,定期进行维修和更新。
8.操作人员8.1 检测操作人员应具备相关的技术知识和操作经验,熟悉检测工艺流程和设备使用方法。
8.2 操作人员应严格遵守检测规程,确保检测过程的质量和安全性。
8.3 操作人员应定期接受培训和考核,提高技能水平和工作质量。
9.文件记录9.1 对检测过程进行记录,包括检测对象、探头角度、检测参数、检测结果等方面。
9.2 对设备使用情况进行记录,包括定期维护、保养、更新等情况。
9.3 对检测报告进行存档,确保检测结果的可靠性和可查询性。
超声波检测规程

超声波检测规程1校准与复核校准应在试块上进行,校准中应使超声主声束垂直对准反射体的轴线,以获得稳定和最大的反射信号。
在开始使用仪器时,应对仪器的水平线性和垂直线性进行测定,在使用过程中,每隔三个月至少应对仪器的水平线性和垂直线性进行一次测试。
在探头开始使用时,应对探头进行一次全面的性能校准。
斜探头在使用前应进行前沿距离、折射角、主声束偏离、灵敏度余量和分辨力的校准。
使用过程中,每次使用前应校准前沿距离、折射角和主声束偏离。
直探头的始脉冲占宽、灵敏度余量和分辨力应根据使用的频度每隔一个月或三个月检查一次。
2检测工艺对于具体部件的检测,中级或高级检验人员应根据相应的标准编制检测工艺卡,经审批后实施。
工艺卡应包括如下内容:检验等级、材料种类、规格、检验时机、坡口形式、焊接工艺方法、表面状态及灵敏度补偿、耦合剂、仪器型号、探头及扫查方式、灵敏度、试块、缺陷位置标定方法、报告要求、操作人员资格、执行标准等。
3检验程序工件准备一表面检查、委托检验一接受委托、指定检验员一了解焊接情况一确定检测工艺卡一选定无损检测方法、仪器、探头、试块一校准仪器和探头一制作距离波幅曲线一调整无损检测灵敏度一校准与复核一涂布耦合剂一粗无损检测一标示缺陷位置一精无损检测一评定缺陷一复核一记录一报告一审核一存档。
对于不合格焊缝的重新无损检测,仍然遵从此程序的要求。
4检验前的准备根据被检部件的材质、规格、性质和结构形状选定无损检测标准,确定检验等级,确定检测工艺卡。
对选定的仪器、探头的性能及其组合性能应进行测试,并符合要求。
制作距离一波幅曲线及综合补偿测定:斜探头前沿距离、K值的测定应在SGB-4试块上进行,前沿距离、K值至少应测量三次,取其平均值。
调节扫描速度、扫描比例,按照选定的标准要求制作距离波幅曲线,并计入综合补偿,绘制在坐标纸上。
综合补偿测定按选定的标准进行。
检测面和检测范围的确定应保证检查到工件被检部分的整个体积,检验前应用80#或100#砂纸去除检测面上的毛刺等,以利于声耦合和探头的移动并减少探头磨损。
特种设备超声波检测通用工艺规程和工艺卡
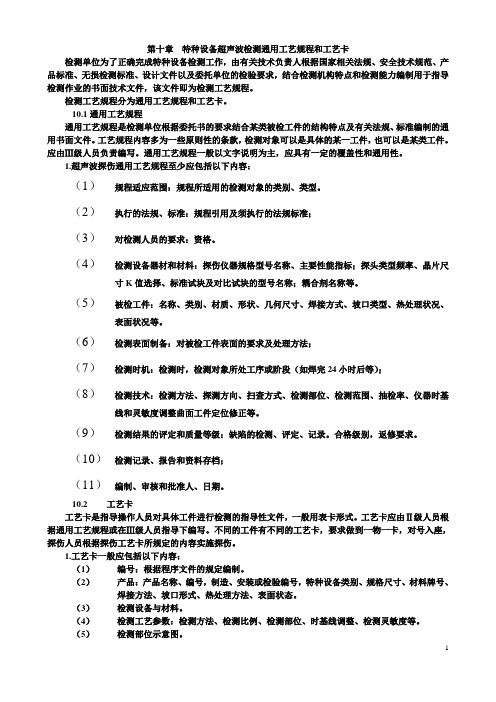
第十章特种设备超声波检测通用工艺规程和工艺卡检测单位为了正确完成特种设备检测工作,由有关技术负责人根据国家相关法规、安全技术规范、产品标准、无损检测标准、设计文件以及委托单位的检验要求,结合检测机构特点和检测能力编制用于指导检测作业的书面技术文件,该文件即为检测工艺规程。
检测工艺规程分为通用工艺规程和工艺卡。
10.1通用工艺规程通用工艺规程是检测单位根据委托书的要求结合某类被检工件的结构特点及有关法规、标准编制的通用书面文件。
工艺规程内容多为一些原则性的条款,检测对象可以是具体的某一工件,也可以是某类工件。
应由Ⅲ级人员负责编写。
通用工艺规程一般以文字说明为主,应具有一定的覆盖性和通用性。
1.超声波探伤通用工艺规程至少应包括以下内容:(1)规程适应范围:规程所适用的检测对象的类别、类型。
(2)执行的法规、标准:规程引用及须执行的法规标准;(3)对检测人员的要求:资格。
(4)检测设备器材和材料:探伤仪器规格型号名称、主要性能指标;探头类型频率、晶片尺寸K值选择、标准试块及对比试块的型号名称;耦合剂名称等。
(5)被检工件:名称、类别、材质、形状、几何尺寸、焊接方式、坡口类型、热处理状况、表面状况等。
(6)检测表面制备:对被检工件表面的要求及处理方法;(7)检测时机:检测时,检测对象所处工序或阶段(如焊完24小时后等);(8)检测技术:检测方法、探测方向、扫查方式、检测部位、检测范围、抽检率、仪器时基线和灵敏度调整曲面工件定位修正等。
(9)检测结果的评定和质量等级:缺陷的检测、评定、记录。
合格级别,返修要求。
(10)检测记录、报告和资料存档;(11)编制、审核和批准人、日期。
10.2工艺卡工艺卡是指导操作人员对具体工件进行检测的指导性文件,一般用表卡形式。
工艺卡应由Ⅱ级人员根据通用工艺规程或在Ⅲ级人员指导下编写。
不同的工件有不同的工艺卡,要求做到一物一卡,对号入座,探伤人员根据探伤工艺卡所规定的内容实施探伤。
超声检测工艺规程

超声检测工艺规程(Q/HS R.Z.17-2010)1、主题内容与适用范围1.1为了加强压力容器焊接质量监督和无损检测管理,保证产品质量符合有关条例、规程、标准、图样技术要求,特制定本规程。
它将几种检测方法共性的内容编入一般要求之中,将几种具体的检测方法中特殊性的问题编在一起。
1.2检测范围包括压力容器原材料、零部件和焊缝的超声波检测。
1.3检测工艺卡是本规程的补充,由Ⅱ级或Ⅲ级人员按合同要求编写,其参数规定的更具体。
2、引用标准JB/T4730-2005 《承压设备无损检测》GB150-2011 《钢制压力容器》JB/T7913-1999 《超声波检测用钢制对比试块的制作与校验方法》JB/T9214-1999 《A型脉冲反射式超声波探伤系统工作性能测试方法》JB/T10061-1999 《A型脉冲反射式超声波探伤仪通用技术条件》JB/T10062-1999 《超声波探伤探头性能测试方法》JB/T10063-1999 《超声波探伤用1号标准试块技术条件》3、检测人员3.1 检测人员必须经过技术培训,按《锅炉压力容器无损检测人员资格考核规则》进行考核监定,取得与其工作相适应的资格证书,并负相应的技术责任。
3.2 无损检测责任工程师,应由具有锅炉压力容器无损检测高级或中级的资格者担任,有权拒绝受理不按标准、规程、条例等进行的任何检测。
3.3为了有效地检出焊缝中的缺陷,检测人员除了具备超声波探伤的检测技术外,还应对焊接过程、焊接接头和坡口形式以及焊缝中常见缺陷有所了解。
4、超声波探伤仪、探头和系统性能4.1 超声波探伤仪我公司现用的超声波探伤仪为HS-I A型脉冲反射式超声波探伤仪,检测人员应能对其性能进行测定,测定方法按JB/T9214-1999的规定进行。
在使用过程中,每隔三个月至少应对仪器的水平线性和垂直线性进行一次测定。
水平线性误差不大于1%,垂直线性误差不大于5%。
其余指标应符合JB/T10061-1999的规定。
3UT--超声检测通用工艺规程-83
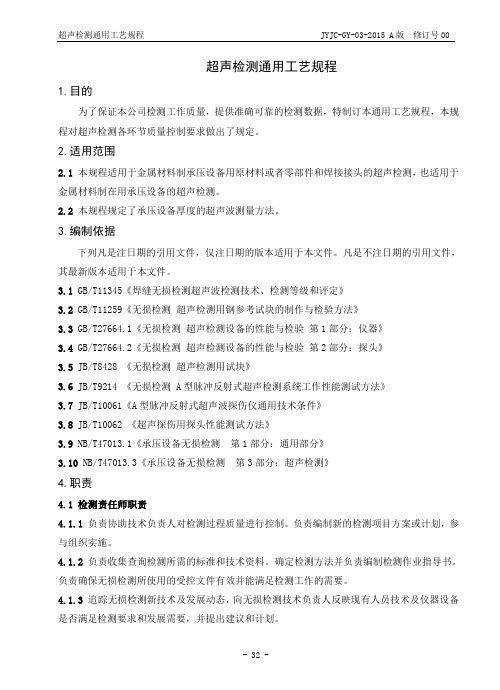
超声检测通用工艺规程1.目的为了保证本公司检测工作质量,提供准确可靠的检测数据,特制订本通用工艺规程,本规程对超声检测各环节质量控制要求做出了规定。
2.适用范围2.1 本规程适用于金属材料制承压设备用原材料或者零部件和焊接接头的超声检测,也适用于金属材料制在用承压设备的超声检测。
2.2本规程规定了承压设备厚度的超声波测量方法。
3.编制依据下列凡是注日期的引用文件,仅注日期的版本适用于本文件。
凡是不注日期的引用文件,其最新版本适用于本文件。
3.1 GB/T11345《焊缝无损检测超声波检测技术、检测等级和评定》3.2 GB/T11259《无损检测超声检测用钢参考试块的制作与检验方法》3.3 GB/T27664.1《无损检测超声检测设备的性能与检验第1部分:仪器》3.4 GB/T27664.2《无损检测超声检测设备的性能与检验第2部分:探头》3.5 JB/T8428 《无损检测超声检测用试块》3.6 JB/T9214 《无损检测 A型脉冲反射式超声检测系统工作性能测试方法》3.7 JB/T10061《A型脉冲反射式超声波探伤仪通用技术条件》3.8 JB/T10062 《超声探伤用探头性能测试方法》3.9 NB/T47013.1《承压设备无损检测第1部分:通用部分》3.10 NB/T47013.3《承压设备无损检测第3部分:超声检测》4.职责4.1 检测责任师职责4.1.1负责协助技术负责人对检测过程质量进行控制。
负责编制新的检测项目方案或计划,参与组织实施。
4.1.2负责收集查询检测所需的标准和技术资料。
确定检测方法并负责编制检测作业指导书。
负责确保无损检测所使用的受控文件有效并能满足检测工作的需要。
4.1.3追踪无损检测新技术及发展动态,向无损检测技术负责人反映现有人员技术及仪器设备是否满足检测要求和发展需要,并提出建议和计划。
4.1.4负责编制《金属检验专业施工组织设计》、专业检测方案或工艺卡。
超声12无损检测工艺规程

超声12无损检测工艺规程.doc超声无损检测工艺规程1. 引言介绍超声无损检测技术(UT)的基本概念,以及其在工业检测中的重要性和应用领域。
2. 目的和适用范围明确本工艺规程的制定目的,以及适用的检测对象和环境。
3. 术语和定义列出与超声无损检测相关的专业术语和定义。
4. 检测设备和仪器4.1 超声波检测仪器详细描述所需超声波检测仪器的技术参数和性能要求。
4.2 探头和配件列出所需探头类型、规格以及耦合剂、楔块等配件的要求。
5. 检测前的准备5.1 设备检查与校准确保所有检测设备和仪器处于良好状态,并进行必要的校准。
5.2 工件表面准备描述工件表面的清洁、打磨等准备工作,以确保良好的超声波耦合。
5.3 安全与防护强调检测过程中的安全防护措施,包括个人防护装备和环境安全。
6. 检测工艺流程6.1 检测参数设置根据工件材料、厚度和预期缺陷类型,设置超声波频率、增益、延迟等参数。
6.2 探头选择与耦合选择合适的探头类型和角度,确保探头与工件表面有良好的耦合。
6.3 扫描与数据采集详细描述探头在工件表面的移动路径和速度,以及数据采集的方法。
6.4 数据分析与缺陷识别介绍如何通过分析超声波信号来识别和定位潜在的缺陷。
7. 缺陷评定与分类7.1 缺陷评定标准根据相关标准,如ASTM、EN等,对检测到的缺陷进行评定。
7.2 缺陷分类和报告将缺陷按照严重程度分类,并编制详细的检测报告。
8. 质量控制与保证8.1 内部质量控制描述内部质量控制流程,包括定期的设备校准、人员培训和检测复核。
8.2 第三方审核与认证如果适用,说明第三方审核和认证的要求和流程。
9. 检测记录与文档管理9.1 检测记录详细记录每次检测的参数、结果和环境条件。
9.2 文档管理确保所有检测记录和报告得到妥善保存和管理。
10. 维护与校准10.1 设备维护定期对超声波检测设备进行维护,以保持其性能和精度。
10.2 定期校准按照制造商的建议和行业标准进行设备的定期校准。
as2207超声波工艺规程
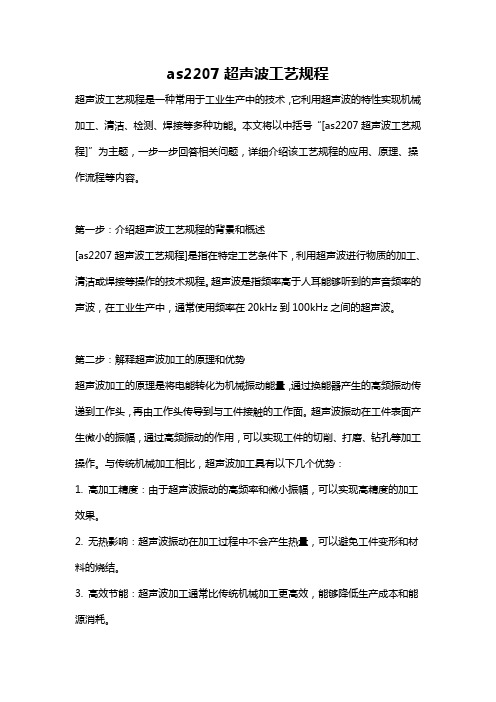
as2207超声波工艺规程超声波工艺规程是一种常用于工业生产中的技术,它利用超声波的特性实现机械加工、清洁、检测、焊接等多种功能。
本文将以中括号“[as2207超声波工艺规程]”为主题,一步一步回答相关问题,详细介绍该工艺规程的应用、原理、操作流程等内容。
第一步:介绍超声波工艺规程的背景和概述[as2207超声波工艺规程]是指在特定工艺条件下,利用超声波进行物质的加工、清洁或焊接等操作的技术规程。
超声波是指频率高于人耳能够听到的声音频率的声波,在工业生产中,通常使用频率在20kHz到100kHz之间的超声波。
第二步:解释超声波加工的原理和优势超声波加工的原理是将电能转化为机械振动能量,通过换能器产生的高频振动传递到工作头,再由工作头传导到与工件接触的工作面。
超声波振动在工件表面产生微小的振幅,通过高频振动的作用,可以实现工件的切削、打磨、钻孔等加工操作。
与传统机械加工相比,超声波加工具有以下几个优势:1. 高加工精度:由于超声波振动的高频率和微小振幅,可以实现高精度的加工效果。
2. 无热影响:超声波振动在加工过程中不会产生热量,可以避免工件变形和材料的烧结。
3. 高效节能:超声波加工通常比传统机械加工更高效,能够降低生产成本和能源消耗。
第三步:说明超声波清洁的应用领域和原理超声波清洁是指利用超声波振动产生的空化效应,将液体中的微小气泡快速落入溶液中,产生溶液剧烈的涌流和冲击效应,以去除工件表面的污垢和杂质。
超声波清洁广泛应用于电子、医疗、汽车、机械制造等行业。
其原理是通过声波振动在液体中产生超过30万次/秒的微气泡的产生和破裂,从而在污垢表面产生冲击力和剪切力,将污垢从工件表面分离。
第四步:详述超声波焊接的工艺流程和应用情况超声波焊接是通过超声波振动将物体的表面进行摩擦热焊接的技术,通常应用于塑料、金属、橡胶等材料的焊接。
其工艺流程包括以下几个步骤:1. 准备工作:根据焊接材料的性质和要求选择合适的焊接设备和工具。
超声波检测工艺规程

超声波检测工艺规程-一、目的本规程旨在规范超声波检测工艺的流程、方法和操作,确保检测结果的准确性和可靠性,为工程质量提供有力保障。
二、适用范围本规程适用于金属材料、非金属材料以及复合材料的超声波检测,包括焊缝、铸件、锻件等。
三、工艺参数1.探头选择:根据被检测材料的性质、厚度、表面状态等因素选择合适的探头。
2.频率选择:根据检测要求和被检测材料的特性选择合适的超声波频率。
3.灵敏度设置:根据检测要求调整超声波检测仪的灵敏度。
4.耦合剂选择:根据被检测材料的特性选择合适的耦合剂。
5.环境条件:确保检测环境干燥、无尘、无强磁场干扰。
四、操作步骤1.准备工作:检查超声波检测设备是否完好,确保电源、探头、耦合剂等准备就绪。
2.校准仪器:根据检测要求,对超声波检测仪进行校准,确保仪器处于最佳工作状态。
3.涂抹耦合剂:在被检测材料表面涂抹耦合剂,以确保超声波能够顺利传播。
4.放置探头:将探头放置在被检测材料表面,确保探头与材料表面紧密接触。
5.启动仪器:开启超声波检测仪,调整合适的参数,进行超声波检测。
6.记录数据:在检测过程中,及时记录超声波信号的波形、振幅等信息。
7.分析数据:对采集到的数据进行整理和分析,判断被检测材料的质量状况。
8.撰写报告:根据检测结果撰写超声波检测报告,包括被检测材料的信息、检测条件、数据分析和结论等。
9.清理现场:在完成检测后,清理现场,包括清理耦合剂、关闭仪器等。
五、注意事项1.在操作过程中,务必遵循安全操作规程,确保人身安全。
2.避免在强磁场环境下进行检测,以免影响检测结果。
3.在放置探头时,应确保探头与材料表面紧密接触,避免空气间隙影响超声波传播。
4.在分析数据时,应综合考虑材料的性质、厚度、加工工艺等因素,确保检测结果的准确性。
5.对可疑的检测结果,应进行复检或采用其他检测方法进行验证,以确保检测结果的可靠性。
6.在撰写报告时,应清晰、准确地描述检测条件、数据分析和结论,为工程质量提供有力支持。
超声波检测工艺规程(完整资料).doc

【最新整理,下载后即可编辑】超声波检测工艺规程1适用范围1.1 本工艺适用于板厚为6-250mm的板材、碳素钢和低合金钢锻件、母材壁厚8-400mm的全焊透熔化焊对接焊缝及壁厚大于等于4mm,管径为57-1200mm碳素钢和低合金石油天然气长输、集输和其他油气管道环向对接焊缝、钢质储罐对接焊缝的超声波检测等。
1.2 本工艺规定了使用A型脉冲反射式超声波探伤仪进行检测过程中,对受检设备做出准确判定应遵循的一般程序和要求。
1.3 引用标准JB4730/T-2005《承压设备无损检测》SY/T4109-2005《石油天然气钢质管道无损检测》GB11345-89《钢焊缝手工超声波探伤方法和探伤结果的分级》JB/T9214-1999《A型脉冲反射式超声探伤系统测试方法》JB/T10062-1999《超声探伤用探头性能测试方法》GB50128-2005《立式圆筒形钢制焊接储罐施工及验收规范》2对检测人员的要求2.1 从事超声波检测人员必须经过培训,持证上岗。
只有取得质量技术监督部门颁发的超声波检测技术等级证书的人,方可独立从事与该等级相应的超声波检测工作。
2.2 检测人员应具有良好的身体素质,其校正视力不得低于5.0,并每年检查一次。
2.3检测人员应严格执行《检测作业安全防护指导书》和其它安全防护规定,确保安全生产。
3检测程序3.1 根据工程特点和本工艺编制具体的《无损检测技术方案》。
3.2 受检设备经外观检查合格后,由现场监理或检验员开据《无损检测指令》或《无损检测委托单》到检测中心。
3.3 检测人员按指令或委托单要求进行检测准备,技术人员根据实际情况编制《探伤工艺卡》。
3.4 检测人员按《超声波探伤仪调试作业指导书》等工艺文件进行设备调试。
3.5 外观检查合格后,施加耦合剂,实施检测,做好《超声波检测记录》。
3.7 根据检测结果和委托单,填写相应的回执单或合格通知单。
若有返修,还应出据《返修通知单》,标明返修位置等。
02超声检测通用工艺规程 NB T47013

1 适用范围1.1本部分规定了承压设备采用A型脉冲反射式超声检测仪检测工件缺陷的超声检测方法和质量分级要求。
1.2本部分适用于金属材料制承压设备用原材料或零部件和焊接接头的超声检测,也适用于金属材料制在用承压设备的超声检测。
1.3本部分规定了承压设备厚度的超声测量方法。
1.4与承压设备有关的支承件和结构件的超声检测,也可参照本部分使用。
2 编制依据NB/T 47013.1-2015《承压设备无损检测》第1部分:通用要求NB/T 47013.3-2015《承压设备无损检测》第3部分:超声检测3 一般要求3.1 超声波检测人员3.1.1从事承压设备超声波检测的人员,应按照国家特种设备无损检测人员考核的相关规定取得相应无损检测人员资格。
3.1.2超声检测人员应具有一定的金属材料、设备制造安装、焊接及热处理等方面的基本知识,应熟悉被检工件的材质、几何尺寸及透声性等,对检测中出现的问题能做出分析、判断和处理。
3.2 检测设备和器材3.2.1 仪器和探头产品质量合格证明超声检测仪器产品质量合格证中至少应给出预热时间、低电压报警或低电压自动关机电压、发射脉冲重复频率、有效输出阻抗、发射脉冲电压、发射脉冲上升时间、发射脉冲宽度(采用方波脉冲作为发射脉冲的)以及接收电路频带等主要性能参数;探头应给出中心频率、带宽、电阻抗或静电容、相对脉冲回波灵敏度以及斜探头声束性能(包括探头前沿距离(人射点)、K值(折射角β等)等主要参数。
3.2.2检测仪器、探头和组合性能3.2.2.1检测仪器采用A型脉冲反射式超声检测仪,其工作频率按-3dB测量应至少包括O.5MHz~10MHz频率范围,超声仪器各性能的测试条件和指标要求应满足NB/T 47013.3-2015附录A的要求并提供证明文件,测试方法按GB/T 27664.1的规定。
3.2.2.2 探头圆形晶片直径一般不应大于40mm,方形晶片任一边长一般不应大于40mm,其性能指标应符合NB/T 47013.3-2015附录B的要求并提供证明文件,测试方法按GB/T 27664.2的规定。
AWS D1.1超声波UT检测工艺规程

目的在不损伤被检物使用性能情况下而主要用于探测材料、构件、焊缝或设备等被检物的各种内部缺陷(如:夹渣、裂纹、未焊透等)并判断其位置大小、形状和种类,从而判定被检物的质量状况和质量等级。
1、适用范围本程序适于使用脉冲反射式超声仪的超声检测工艺。
2、人员要求无损探伤人员资质审定需符合 SNT-TC-1A 的要求,或 ISO9712 的要求。
3、职责质检科负责焊缝超声波探伤的实施。
4、依据本程序按照 AWS D1.1(钢结构焊接规范)第六章检验中超声波检测部份编制5、使用仪器及辅助材料5.1 超声波探伤仪(GUN30北京时代、PXUT-330南通友联)5.2 标准试块( IIW)5.3 探头5.4 耦合剂(化学浆糊)6、超声波探伤检测程序根据板厚的不同选择折射角,应选择合适的折射角进行检测,检测角度的选择可以参照 AWS D1.1 表 6.7 或根据检验员的试验结果选择可靠的折射角也可利用多种角度探头对同一工件进行多次检测从而选择最优的折射角度,常规检测可按下表规定选择:7、超声波探伤仪及探头的性能:7.1灵敏度余量仪器和试块,使用 IIW 试块使从 R100 处的反射回波高度在荧光屏上达到75%。
仪器具有至少 40 分贝灵敏度余量。
7.2.时间轴线性(水平线性)按照 AWS D1.1 6.30.1 进行签定7.3.放大线性(垂直线性)按照 AWS D1.1 6.30.2 进行鉴定。
7.4.分辨力按照 AWS D1.1 6.29.2.5 进行鉴定,以至少能分辨三个反射波为合格。
7.5.角度探头的鉴别按照 AWS D1.1 6.29.2.2 进行签定,角度误差必须在±2º范围之内。
8.0 试验表面的准备8.1 所有的焊接飞溅物、锈蚀、油漆、毛刺都应在检验前清除干净。
9.0 焊缝检测9.1 扫查:图 3 为常用扫查方法。
图39.2 最大指示:当在萤光屏上出现不连续性指示时,必须对来自不连续性的可达最大指示进行调节,使得显示器上产生水平对比基准轨迹的偏离。
超声波检测工艺规程

超声波检测工艺规程1.1目的本规程规定了检测人员的资格、仪器探头试块、检测范围、方法和质量分级等。
1.2检测范围超声检测采用A型脉冲反射式超声探伤仪,检测范围包括原材料,铸件,锻造件,焊缝的缺陷检测。
1.3检测人员检测人员应取得中国机械工程学会或国家质量技术监督局颁发的二级(包括二级)以上证书,并严格执行审核制度。
1.4引用标准:GB11345-1989《钢焊缝手工超声波探伤方法和探伤结果分级》GB /T6402《钢锻件超声波检验方法》GB50235-1997《工业金属管道工程施工及验收规范》GB50148-1993《工业金属管道工程质量检验》JB/T7913-1995《超声波检测用钢制对比试块的制作与校验方法》JB/T9214-1999《A型脉冲反射式超声波探伤系统工作性能测试方法》JB/T10061-1999《A型脉冲反射式超声波探伤仪通用技术条件》JB/T10063-1999《超声探伤用1号标准试块技术条件》JB/T10062-1999《超声探伤用探头性能测试方法》GB/T6402-2008,《钢锻件超声检测方法》GB/T7233-1987《铸钢件超声探伤及质量评级方法》1.5探伤仪HS620超声波探伤仪,工作频率为1〜5MHz至少在荧光屏满刻度的80%范围内呈线性显示;误差在土1dB内,最大累计误差不超过1dB;水平线性误差w 1%垂直线性误差w 5% 1.6探头常用探头有单直探头、单斜探头、双晶探头等,在达到所检工件的最大检测声程时,其1.7超声检测一般方法有效灵敏度余量》10dB。
1.7超声检测一般方法1.7.1检测复盖率检测时应尽量扫查到工件的整个被检区域,探头的每次扫查复盖率应〉探头直径的15%1.7.2探头的移动速度探头的扫查速度不超过150mm/s1.7.3扫查灵敏度扫查灵敏度至少比基准灵敏度高6dB。
1.7.4耦合剂采用机油、甘油等不损伤工作表面的耦合剂。
1.7.5检测面检测面应经外观检查合格,所有影响超声检测的锈蚀、飞溅和污物均应清除,其表面粗糙度符合检测要求。
超声波检测工艺规程及检测工艺卡

超声波检测工艺规程及检测工艺卡1.1人员资格1.1.1检测人员都必须经过技术培训,并按照原劳动部文件“锅炉压力容器无损检测人员资格考核规则”进行考核鉴定,还应持有经业主认定的专业培训合格的岗位证。
1.1.2检测人员较正视力不得低于1.0。
1.2仪器、探头、试块和耦合剂1.2.1超声波探伤仪a 使用PXUT-350A型脉冲反射式数字超声波探伤仪,其工作频率为4-5MHZ,仪器荧光屏满刻度的80%范围内呈线性显示。
探伤仪有80dB以上的连续可调衰减器,步进级每档不大于2dB。
水平线性误差不大于1%,垂直线性不大于5%,其余指标符合ZBY230《A型脉冲反射式超声波探伤仪通用技术条件》规定。
b超声波探伤仪能储存100幅以上图形,且能清晰打印出探伤发现的缺陷波形图。
1.2.2探头选用频率为2.5MHz和5MHz两种单斜探头,晶片有效面积不大于500mm2,且任意一边长不大于25mm,单斜探头声束轴线水平偏离角不应大于2°,前沿距离不应大于10 mm,且探头的接触面应与管壁对中,吻合良好,主声束垂直方向不应有明显双峰。
按照管道实际壁厚选择探头K值。
1.2.3试块选用SGB-5、6标准试块和SRB未焊透对比试块。
1.2.4耦合剂使用化学浆糊耦合剂,均匀涂布在焊缝两侧探头移动区,保证良好的透声性能。
1.3检测方法1.3.1距离-波幅曲线:用SGB—5试块测绘距离—波幅曲线,评定线,定量线和判废线满足下表:1.3.2检测灵敏度:不低于评定线灵敏度,扫查灵敏度在基准灵敏度的基础上提高4dB。
1.3.3探伤表面探头移动区应平滑,无飞溅、锈蚀、油垢及其它污物,以保证良好的声学接触。
如需检验横向缺陷,应将焊缝磨平。
探头移动区:T=5~30时,P≥nKT+50P--探头移动区mm;T—单壁厚度mm;K为探头K值; n--反射次数1.3.4探测方式和扫查方式a探测方式以一种K值探头用一、二次波在焊缝单面双侧进行探测。
超声波检测工艺规程
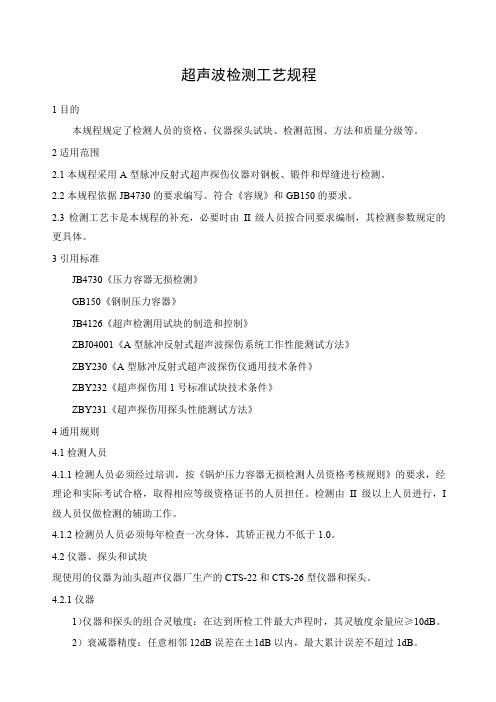
超声波检测工艺规程1目的本规程规定了检测人员的资格、仪器探头试块、检测范围、方法和质量分级等。
2适用范围2.1本规程采用A型脉冲反射式超声探伤仪器对钢板、锻件和焊缝进行检测。
2.2本规程依据JB4730的要求编写。
符合《容规》和GB150的要求。
2.3检测工艺卡是本规程的补充,必要时由II级人员按合同要求编制,其检测参数规定的更具体。
3引用标准JB4730《压力容器无损检测》GB150《钢制压力容器》JB4126《超声检测用试块的制造和控制》ZBJ04001《A型脉冲反射式超声波探伤系统工作性能测试方法》ZBY230《A型脉冲反射式超声波探伤仪通用技术条件》ZBY232《超声探伤用1号标准试块技术条件》ZBY231《超声探伤用探头性能测试方法》4通用规则4.1检测人员4.1.1检测人员必须经过培训,按《锅炉压力容器无损检测人员资格考核规则》的要求,经理论和实际考试合格,取得相应等级资格证书的人员担任。
检测由II级以上人员进行,I 级人员仅做检测的辅助工作。
4.1.2检测员人员必须每年检查一次身体,其矫正视力不低于1.0。
4.2仪器、探头和试块现使用的仪器为汕头超声仪器厂生产的CTS-22和CTS-26型仪器和探头。
4.2.1仪器1)仪器和探头的组合灵敏度:在达到所检工件最大声程时,其灵敏度余量应≥10dB。
2)衰减器精度:任意相邻12dB误差在±1dB以内,最大累计误差不超过1dB。
3)水平线性:水平线性误差不大于1%。
4)垂直线性:在荧光屏满刻度的80%范围内呈线性显示。
垂直线性误差不大于5%。
4.2.2探头1)晶片有效面积除另有规定外一般不应超过50mm,且任意一边长不大于25mm。
2)单斜探声束轴线水平偏离角不应大于2°,主声束垂直主方向不应有明显的双峰。
3)直探头的远场分辨力应大于或等30dB,斜探头的远场分辨力应大于或等于6dB。
仪器和探头的系统性应按ZBJ04001和ZBY231的规定进行测试。
超声波检测通用工艺规程

超声波检测通用工艺规程1.要紧内容与适用范围本规程规定了焊缝超声检测人员具有的资格、仪器、探头、试块、检测技术方式和质量分级等。
本规程适用于本公司生产的厚度为6mm~30mm钢制承压设备全熔化焊的超声检测。
不适用于铸钢及奥氏体钢焊缝,外径小于159mm的钢管对接焊缝,内径小于或等于250mm或内外径之比小于80%的纵向焊缝检测。
本规程按JB4730的要求编写,符合《容规》和GB150等要求。
检测工艺卡是本规程的补充,由Ⅱ级人员按本规程等要求编制,其检测参数规定的更具体。
2.引用标准、法规JB/T4730-2005《承压设备无损检测》GB150-1998《钢制压力容器》JB/T9214-1999《A型脉冲反射式超声波探伤系统工作性能测试方式》JB/T10061-1999《A型脉冲反射式超声波探伤仪通用技术条件》JB/T10062-1999《超声探伤用探头性能测试方式》3.检测人员3.1检测人员必需通过培训,按《特种设备无损检测人员考核与监督治理规那么》的要求。
领导论和实践考试合格,取得相应品级资格证书的人员担任。
3.1.1检测人员每一年应检查一次躯体,其矫正视力不低于1.0。
4.探伤仪、探头和试块4.1探伤仪采纳A型脉冲反射式超声波探伤仪器,其工作频率范围为0.5 MHz~10MHz,仪器至少在荧光屏满刻度的80%范围内呈线性显示。
仪器应具有80dB以上的可调衰减器,步进级每档不大于2Db,其精度为任意相邻12 dB的误差在±1dB 之内,最大累计误差不超过1dB.。
水平线性误差不大于1%,垂直线性误差不大于5%。
4.2探头4.2.1晶片面积一样不该超过500mm2,且任意一边长原那么上不大于25 mm 。
4.2.2单斜探头声束轴线水平偏离角不该大于2度,主声束垂直方向不该有明显的双峰。
4.3仪器和探头的系统性能4.3.1在达到所检工件的最大检测声程时,其灵敏度余量应≥10dB。
4.3.2直探头的远场分辨力应大于或等于30 dB ,斜探头的远场分辨力应大于或等于6dB 。
- 1、下载文档前请自行甄别文档内容的完整性,平台不提供额外的编辑、内容补充、找答案等附加服务。
- 2、"仅部分预览"的文档,不可在线预览部分如存在完整性等问题,可反馈申请退款(可完整预览的文档不适用该条件!)。
- 3、如文档侵犯您的权益,请联系客服反馈,我们会尽快为您处理(人工客服工作时间:9:00-18:30)。
超声波检测工艺规程1适用范围1.1 本工艺适用于板厚为6-250mm的板材、碳素钢和低合金钢锻件、母材壁厚8-400mm的全焊透熔化焊对接焊缝及壁厚大于等于4mm,管径为57-1200mm碳素钢和低合金石油天然气长输、集输和其他油气管道环向对接焊缝、钢质储罐对接焊缝的超声波检测等。
1.2 本工艺规定了使用A型脉冲反射式超声波探伤仪进行检测过程中,对受检设备做出准确判定应遵循的一般程序和要求。
1.3 引用标准JB4730/T-2005《承压设备无损检测》SY/T4109-2005《石油天然气钢质管道无损检测》GB11345-89《钢焊缝手工超声波探伤方法和探伤结果的分级》JB/T9214-1999《A型脉冲反射式超声探伤系统测试方法》JB/T10062-1999《超声探伤用探头性能测试方法》GB50128-2005《立式圆筒形钢制焊接储罐施工及验收规范》2对检测人员的要求2.1 从事超声波检测人员必须经过培训,持证上岗。
只有取得质量技术监督部门颁发的超声波检测技术等级证书的人,方可独立从事与该等级相应的超声波检测工作。
2.2 检测人员应具有良好的身体素质,其校正视力不得低于5.0,并每年检查一次。
2.3检测人员应严格执行《检测作业安全防护指导书》和其它安全防护规定,确保安全生产。
3检测程序3.1 根据工程特点和本工艺编制具体的《无损检测技术方案》。
3.2 受检设备经外观检查合格后,由现场监理或检验员开据《无损检测指令》或《无损检测委托单》到检测中心。
3.3 检测人员按指令或委托单要求进行检测准备,技术人员根据实际情况编制《探伤工艺卡》。
3.4 检测人员按《超声波探伤仪调试作业指导书》等工艺文件进行设备调试。
3.5 外观检查合格后,施加耦合剂,实施检测,做好《超声波检测记录》。
3.7 根据检测结果和委托单,填写相应的回执单或合格通知单。
若有返修,还应出据《返修通知单》,标明返修位置等。
将回执单和返修通知单递交监理或检验员,同时对受检设备进行检验和试验状态标识。
3.8 返修后,按要求重新进行检测。
3.9 在检测过程中应有Ⅱ或Ⅲ级人员在现场。
所有的检测工作完成后,由具有超声波Ⅱ或Ⅲ级人员出据《超声波检测报告》,由技术负责人或其授权人审核。
4探伤仪、探头、试块和系统性能的一般要求4.1 探伤仪采用A型脉冲反射式探伤仪,工作频率范围为0.5-10MHz,仪器至少在荧光屏满刻度80%范围内呈线性显示。
探伤仪应具有80dB以上的连续可调衰减器,步进级每档不大于2dB,其精度为任意相邻12dB误差在±1dB以内,最大累计误差不超过1dB,水平线性误差不超过1%,垂直线性误差不超过5%。
4.2 探头晶片有效面积一般不应超过500mm2,且任一边长不应大于25mm。
单斜探头声束轴线水平偏离角不应大于2º,主声束垂直方向不应有明显的双峰。
4.3 探伤仪和探头的系统性能4.3.1 在达到所探工作的最大检测声程时,其有效灵敏度余量应大于或等于10dB。
4.3.2 仪器和直探头组合的始脉冲宽度:对于频率为5 MHz的探头,其占宽不得大于10mm;对于频率为2.5MHz的探头,其占宽不得大于15mm。
4.3.3 直探头的远场分辨力应大于或等于30dB,斜探头的远场分辨力应大于或等于6dB。
4.4 超声波检测的一般要求4.4.1 检测时,应尽量扫查到工作的整个被检区域,探头的每次扫查复盖率应大于探头直径的15%。
4.4.2 探头的扫查速度不应超过150mm/s。
当采用自动报警装置扫查时,不受此限。
4.4.3 扫查灵敏度至少应比基准灵敏度高6dB。
4.4.4 应采用透声性好且不损伤受检设备表面的耦合剂,如机油、浆糊、甘油和水等。
4.4.5 检测面应经外观检查合格,所有影响超声检测的锈蚀、飞溅和污物都应予以清除,其表面粗糙度应符合检测要求。
4.4.6 在制作距离--波幅曲线时,应考虑各种耦合补偿。
4.5 校准4.5.1 校准应在标准试块上进行,校准中应使超声主声束垂直对准反射体的轴线,以获得稳定的和最大的反射信号。
4.5.2 仪器在开始使用时,应对其水平线性进行测定。
使用中,每隔三个月至少应对仪器的水平线和垂直线性进行一次测定。
4.5.3 斜探头使用前,应进行前沿距离、K值、主声束偏离、灵敏度余量和分辨力等的校准。
使用过程中,每个工作日应校准前沿距离、K值和主声束偏离。
直探头使用前检查始脉冲占宽、灵敏度余量和分辨力。
4.6 仪器和探头系统的复核4.6.1 复核的时机:每次检测前均应对扫描线、灵敏度进行校核,遇有下列情况应随时进行重新校核:a)校准后的探头、耦合剂和仪器调节旋纽发生改变时;b)检测者怀疑扫描量程或灵敏度有变化时;c)连续工作4小时以上时;d)工作结束时。
4.6.2 每次检查结束前,应对扫描量程进行复核。
如果任意一点在扫描线上的偏移超过扫描读数的10%,则扫描量程应予以重新调整,并对上一次复核以来所有的检测部位进行复验。
4.6.3每次检查结束前,应对扫查灵敏度进行复核,距离--波幅曲线的校核一般不少于3点。
校核时,如曲线上任何一点幅度下降2dB,则应对上一次以来所有的检测结果进行复检;如幅度上升2dB,则应对所有的记录信号进行重新评定。
4.7 试块4.7.1 试块应妥善保管,各种缺欠孔要经常清理。
4.7.2 试块选择应注意外形尺寸应能代表被检工件的特征,试块的厚度应与被检工作的厚度相对应。
如果涉及到两种或两种以上不同厚度的部件进行熔焊时,试块的厚度应由其最大厚度来确定。
4.7.3 现场检测时,可以采用其它型式的等效试块。
4.8 探伤仪、探头、试块和系统性能测试按《超声波探伤仪调试作业指导书》进行。
5 钢板的超声检测本条适用于板厚6~250mm的板材的超声检测和缺欠等级评定。
5.1 探头的选用按下表进行。
5.2 标准试块5.2.1 用双晶直探头检测壁厚小于或等于20mm的钢板时,采用CBⅠ标准试块。
5.2.2 用单晶直探头检测壁厚大于20mm的钢板时,采用CBⅡ标准试块。
试块厚度与被检钢板厚度相近。
5.3 检测时机对于要求淬火、正火或回火处理的钢板,检测应在热处理后进行。
5.4 检测灵敏度5.4.1 板厚小于或等于20mm时,用CBⅠ试块将工件等厚部位第一次底波高度调整到满刻度的50%,再提高10dB作为基准灵敏度。
5.4.2 板厚大于20mm时,应将CBⅡ试块Ф5平底孔第一次反射波高调整到满刻度的50%作为检测灵敏度。
5.4.3板厚大于探头的三倍近场区时,也可取钢板无缺欠的完好部位的第一次底波来校准灵敏度,其结果应与5.4.2条相一致。
5.5 检测方法5.5.1 检测面可选钢板的任一轧制平面进行检测。
若检测人员认为需要或设计上有要求时,也可对钢板的上下两轧制平面分别进行检测。
5.5.2 扫查方式a) 探头沿垂直于钢板压延方向,按间距不大于100mm的平行线进行扫查。
在钢板剖口预定线两侧各50mm(当板厚超过100mm时,以板厚的一半为准)内应作100%扫查。
b) 根据合同、技术协议书或图样的要求,也可进行其它形式的扫查。
5.6 缺欠记录5.6.1 在检测过程中出现下列三种情况之一者及作为缺欠:a) 缺欠第一次反射波(F1)波高大于或等于满刻度的50%,即F1≥50%者。
b) 当底面第一次反射波(B1)波高未达到满刻度,此时,缺欠第一次反射波(F1)波高与底面第一次反射波(B1)之比大于或等于的50%,即B1≤100%,而F1/ B1≥50%者。
c) 当底面第一次反射波(B1)波高低于满刻度的50%,即B1<50%者。
5.6.2 缺欠的边界或指示长度的测定方法a) 检出缺欠后,应在它的周围继续进行检测,以确定缺欠的延伸及范围。
b) 用双晶直探头确定缺欠的边界或指示长度时,探头的移动方向应与探头的隔声层相垂直,使缺欠波下降到检测灵敏度条件下荧光屏满刻度的25%或使缺欠第一次反射波高与底面第一次反射波高之比为50%。
此时,探头中心的移动距离即为缺欠的指示长度,探头中心点即为缺欠的边界点。
两种方法测得的结果以较严重者为准。
c) 用单直探头确定缺欠的边界或指示长度时,移动探头,使缺欠第一次反射波高下降到检测灵敏度条件下荧光屏满刻度的25%或使缺欠第一次反射波与底面第一次反射波高之比为50%。
此时,探头中心的移动距离即为缺欠的指示长度,探头中心点即为缺欠的边界点。
两种方法测得的结果以较严重者为准。
d) 确定5.6.1 c)条边界或指示长度时,移动探头,使底面第一次反射波升高到荧光屏满刻度的50%。
此时,探头中心的移动距离即为缺欠的指示长度,探头中心点即为缺欠的边界点。
e) 当采用第二次缺欠波和第二次底波来评定缺欠时,检测灵敏度应以相应的第二次反射波来校准。
5.7 缺欠的评定方法5.7.1 缺欠指示长度的评定准则:一个缺欠按其指示的最大长度作为该缺欠的指示长度。
若单个缺欠的指示长度小于40mm时,可不做记录。
5.7.2 单个缺欠指示面积的评定规则a)一个缺欠按其指示的最大面积作为该缺欠的单个指示面积。
当其小于下表时,可不作记录。
b) 多个缺欠其相邻间距小于100mm或间距小于相邻小缺欠的指示长度(取其较大值)时,其各缺欠面积之和作为单个缺欠指示面积。
5.7.3 缺欠面积占有率的评定规则:在任一1m×1m检测面积内,按缺欠所占的百分比来确定。
如钢板面积小于1m×1m,可按比例折算。
5.8 钢板缺欠等级评定5.8.1 缺欠等级划分见5.7.2的表格。
5.8.2 在坡口预定线两侧各50mm(板厚超过100mm时,以板厚的一半为准)内,缺欠的指示长度大于或等于50mm时,则应评为Ⅴ级。
5.8.3 在检测过程中,检测人员如确认钢板中有白点、裂纹等危害性缺欠存在时,则应评为Ⅴ级。
6锻件的超声检测本条适用于碳素钢和低合金钢锻件的超声检测和缺欠等级评定。
不适用于奥氏体钢等粗晶材料的超声检测,也不适用于内外径之比小于80%的环形和筒形锻件的周向横波检测。
6.1 试块6.1.1 纵波直探头标准试块采用CSⅠ和CSⅡ、CSⅢ试块,也可自行加工其他对比试块。
6.1.2 纵波双晶直探头标准试块a) 工件检测距离小于45mm时,应采用CSⅡ试块。
b) 纵波双晶直探头标准试块的形状和尺寸应符合JB4730表5和图5的规定。
6.1.3 检测面是曲面时,应采用CSⅢ标准试块来测定由于曲率不同而引起的声能损失,其形状和尺寸符合JB4730图6的规定。
6.2 检测时机原则上应安排在热处理后,槽、孔、台阶加工前进行。
若热处理后锻件形状不适合超声检测时,也可在热处理前进行,但在热处理后仍应对锻件进行尽可能完全的检测。
检测面的表面粗糙度Ra为6.3um。
6.3 检测方法锻件一般应进行纵波检测。