解决磨削裂纹的启示
中频淬火凸轮轴磨削裂纹产生原因及对策
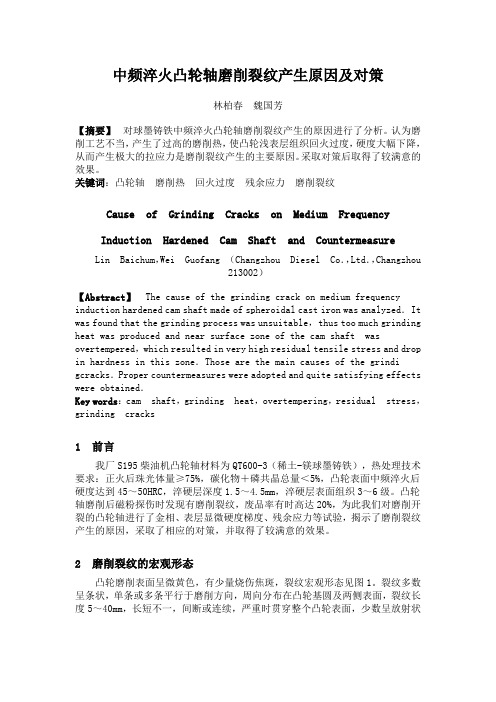
中频淬火凸轮轴磨削裂纹产生原因及对策林柏春魏国芳【摘要】对球墨铸铁中频淬火凸轮轴磨削裂纹产生的原因进行了分析。
认为磨削工艺不当,产生了过高的磨削热,使凸轮浅表层组织回火过度,硬度大幅下降,从而产生极大的拉应力是磨削裂纹产生的主要原因。
采取对策后取得了较满意的效果。
关键词:凸轮轴磨削热回火过度残余应力磨削裂纹Cause of Grinding Cracks on Medium FrequencyInduction Hardened Cam Shaft and CountermeasureLin Baichum,Wei Guofang (Changzhou Diesel Co.,Ltd.,Changzhou213002)【Abstract】The cause of the grinding crack on medium frequency induction hardened cam shaft made of spheroidal cast iron was analyzed.It was found that the grinding process was unsuitable,thus too much grinding heat was produced and near surface zone of the cam shaft was overtempered,which resulted in very high residual tensile stress and drop in hardness in this zone.Those are the main causes of the grindi gcracks.Proper countermeasures were adopted and quite satisfying effects were obtained.Key words:cam shaft,grinding heat,overtempering,residual stress,grinding cracks1 前言我厂S195柴油机凸轮轴材料为QT600-3(稀土-镁球墨铸铁),热处理技术要求:正火后珠光体量≥75%,碳化物+磷共晶总量<5%,凸轮表面中频淬火后硬度达到45~50HRC,淬硬层深度1.5~4.5mm,淬硬层表面组织3~6级。
磨削裂纹产生的原因及措施
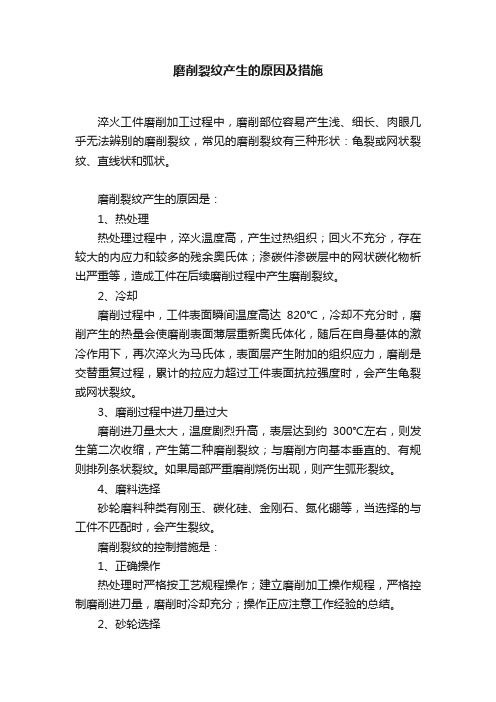
磨削裂纹产生的原因及措施淬火工件磨削加工过程中,磨削部位容易产生浅、细长、肉眼几乎无法辨别的磨削裂纹,常见的磨削裂纹有三种形状:龟裂或网状裂纹、直线状和弧状。
磨削裂纹产生的原因是:1、热处理热处理过程中,淬火温度高,产生过热组织;回火不充分,存在较大的内应力和较多的残余奥氏体;渗碳件渗碳层中的网状碳化物析出严重等,造成工件在后续磨削过程中产生磨削裂纹。
2、冷却磨削过程中,工件表面瞬间温度高达820℃,冷却不充分时,磨削产生的热量会使磨削表面薄层重新奥氏体化,随后在自身基体的激冷作用下,再次淬火为马氏体,表面层产生附加的组织应力,磨削是交替重复过程,累计的拉应力超过工件表面抗拉强度时,会产生龟裂或网状裂纹。
3、磨削过程中进刀量过大磨削进刀量太大,温度剧烈升高,表层达到约300℃左右,则发生第二次收缩,产生第二种磨削裂纹;与磨削方向基本垂直的、有规则排列条状裂纹。
如果局部严重磨削烧伤出现,则产生弧形裂纹。
4、磨料选择砂轮磨料种类有刚玉、碳化硅、金刚石、氮化硼等,当选择的与工件不匹配时,会产生裂纹。
磨削裂纹的控制措施是:1、正确操作热处理时严格按工艺规程操作;建立磨削加工操作规程,严格控制磨削进刀量,磨削时冷却充分;操作正应注意工作经验的总结。
2、砂轮选择1)尽可能选用锋利的砂轮,切削速度快,磨削效率高,磨削表面不易过热。
2)正确选择砂轮结构和硬度级别,以获得自由磨削效应。
3)陶瓷和金属作粘结剂的砂轮,适用于磨削热较高的场合;树脂粘结砂轮,适用磨削热较小的场合。
脆性较大的粘结剂,磨粒容易脱落,有利于使砂轮保持锐利状态。
4)SiC磨料磨削钢和铁基耐热合金时,产生强烈的化学磨损,刚玉类磨料磨削钢时无此反应。
相反,刚玉类磨料磨削玻璃、硅酸盐类陶瓷涂层时,会产生强烈的化学反应,SiC磨料无此反应。
3、如果已产生磨削裂纹,如果未超过加工余量,可进行多次低温回火,去除磨削应力,再按正确的磨削加工方法加工,磨去裂纹深度进行挽救。
20CrMnTi渗碳齿轮磨削裂纹的分析与解决
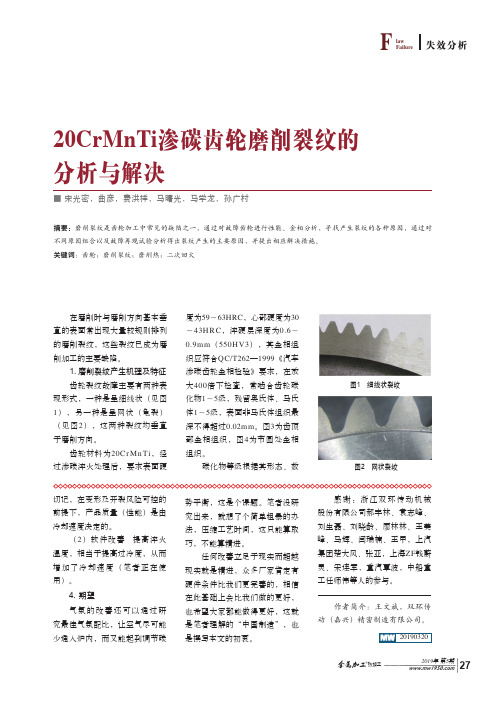
图1 细线状裂纹
图2 网状裂纹
感谢:浙江双环传动机械股份有限公司郝丰林、袁志峰、刘生磊、刘晓龄、廖林林、王美峰、马辉、闫瑞楠、王甲,上汽集团楚大风、张亚,上海ZF钱蔚灵、宋连军,重汽覃波,中船重
图3 齿顶部金相组织
图4 节圆处金相组织
量、大小、分布情况确定,具体
说明如表1所示。
残留奥氏体等级按其含量多
少确定,马氏体等级按其针体大
小确定,具体说明如表2所示。
通过对故障齿轮进行金相、
性能分析,齿轮金相组织及热处
图5 裂纹齿轮金相
图6 导致磨削裂纹的鱼骨图分析。
解决丝锥磨槽裂纹难题
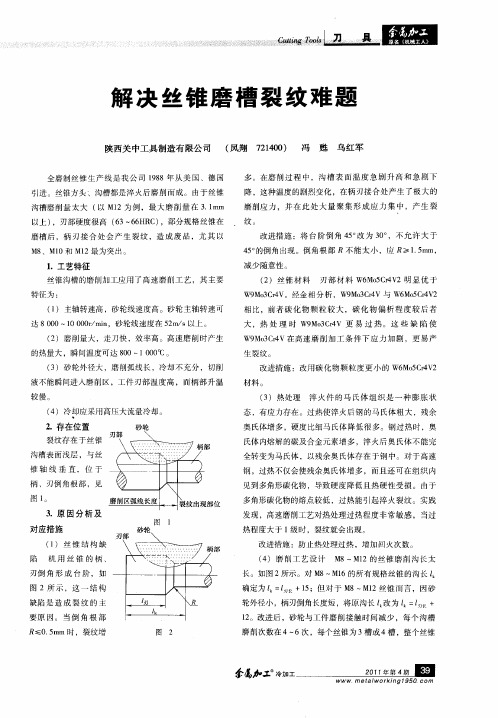
1 .工艺特征
丝锥沟槽 的磨 削加工应用 了高速磨 削工艺 ,其主要
特征为 :
( )主轴转速高 ,砂轮线速度高。砂 轮主轴转速可 1
达 800~1 0  ̄mn 0 00 0 i,砂 轮 线速 度 在 5 m s以上 。 2/
相比 ,前 者碳 化 物颗 粒 较大 ,碳 化 物 偏析 程 度较 后 者 大 ,热 处 理 时 W9 o C M 3 MV 更 易 过 热 。这 些 缺 陷 使 W9 3 NV在高速磨 削 加工 条件 下应 力 加剧 ,更 易产 MoC
w w w m et wor ng I D om a1 ki 95 c
27 第 期■ 01 4 年
盈霉
_ /
搿譬 囊。 糍 。
从 以上磨 削过程 不难发 现 ,刃头端 穿过 冷却喷 嘴 , 冷却 时间长 ,切削 液
压力 大 ;而刃末端 还 没有到达冷却 喷嘴中 心,就 脱 离 了 冷 却 ,
度在 2 m 以上 ,造成磨削 区切 削液不能 及时到达 ,冷 0m
图
3
改进措施 :为 了加强刃末端 处冷却效 果 ,可以调慢
工作 台下降速度 ,延长柄刃交接 处冷却时 间。此办 法效 果不错 ,裂纹率明显下 降。另外 ,也 可增大切削液 的流
多角形碳化物 的熔点较低 ,过热 能引起淬 火裂纹 。实践
3 原 因分 析 及 .
发现 , 高速磨削工艺对热处理过热 程度非 常敏感 ,当过
图 1
对应措施
( ) 丝 锥 结 构 缺 1
热程度大于 1 级时 ,裂纹就会出现。
改 进 措 施 :防 止 热 处 理 过 热 ,增加 同火 次数 。
材料 。
( )热处理 3
磨床磨削裂纹原因的分析与对策

磨床磨削裂纹的产生原因分析与对策分析磨削裂纹的产生原因,与磨削前各加工过程所产生的缺陷,如材料表层中存在网状碳化物、非金属夹杂、组织疏松、成分偏析、晶界上的淬火变形等有关;裂纹通常与烧伤同时出现。
当工件表层的残余拉应力超过材料的抗拉强度时,就会产生磨削裂纹。
磨削裂纹的产生原因和减小磨削裂纹的方法如下:1、正确选用砂轮,例如可采用颗粒较粗、较软、组织较疏松的砂轮;保证修整后砂轮的锋利。
2、保证磨削时的冷却条件,设法使冷却液能有效地渗透到工件的磨削区中。
3、合理选择磨削用量,例如提高工件的转速,采用较小的径向进给量等。
磨削时如果磨削工艺参数选择或操作不当,工件表面温度达到150~200度时表面因马氏体分解,体积缩小,而中心马氏体不收缩,使表层承受拉应力而开裂,产生的裂纹会与磨削方向垂直,裂纹相互平行。
当磨削温度在200度以上时,表面由于产生索氏体或托氏体,这时表层发生体积收缩,而中心则不收缩,使表层拉应力超过脆断抗力而出现龟裂现象。
4、工件表面渗层碳浓度过高,会使工件表面产生过多的残余奥氏体.从而容易导致产生烧伤和裂纹。
因此,表面碳浓度增加,则降低了磨削性能,一般表面碳浓度应控制在0.75%-0.95%范围以内。
5、碳化物分布应均匀,粒度平均直径不大于0.001m;碳化物形态应为球状、粉状或细点状沿网分布,不允许有网状或角状碳化物。
6、热处理时.表面或环境保护不当会产生表面氧化,这样在工件上就会产生一层薄的脱碳层,这层软的脱碳层会引起砂轮过载或过热,从而造成表面回火,工件磨削时容易出现裂纹。
7、如果冷却不充分,磨削时零件表面温度有时可能高达820~840度或更高,则由于磨削形成的热量足以使表面薄层重新奥氏体化,并再次淬火而形成淬火马氏体,表面形成二次淬火的金相组织。
此外,磨削形成的热量使零件表面温度升高极快,这种组织应力和热应力导致磨削表面出现磨削裂纹。
8、使用金刚滚轮修整砂轮的内滚道磨床加工的零件有裂纹,还与配置的金刚滚转速、转向、金刚石的粒度、磨损情况、修砂轮时电主轴的转速、修砂轮时与滚轮磨合停留的时间等因素有关。
磨削烧伤裂纹的产生及控制

磨削烧伤裂纹的产生及控制文章简述了磨齿的原理和方法,主要研究磨削裂纹的形态及产生裂纹的原因,及提出提高含碳量从标准的0.8%~0.9%提高到1%~2%。
并从热处理和冷加工方面,如工艺参数、冷却介质、工作环境,磨具等方面提出一系列防止磨齿裂纹的措施。
标签:磨削烧伤;裂纹;塑性变形;磨削余量;磨削用量磨齿是齿轮精加工的一种方法,磨齿不仅能纠正齿轮预加工产生的各项误差,而且能加工淬硬的齿轮,加工精度高。
1 磨齿的原理和方法锥砂轮磨齿原理。
在这里我们提到的都是指外齿轮,锥砂轮磨齿是按照齿轮和齿条的啮合原理进行的。
砂轮相当于假象齿条上的一个齿,齿轮的节圆沿齿条的节线作纯滚动。
被磨齿轮装在头架的主轴上,沿节线一面作横向往复移动,一面通过传动机构使被磨齿轮随主轴绕自身轴线作反复转动,被磨齿轮的移动和转动必须保持一定的相对关系,齿轮旋转一转,其移动距离应等于被磨齿轮节圆的圆周长,这样就可以磨出要求的渐开线齿形。
在磨斜齿轮时,砂轮和齿轮的相对运动相当于斜齿条的啮合原理进行的。
斜齿条的倾斜角等于斜齿轮的螺旋角,砂轮往复运动的斜线和齿轮轴线之间的夹角也应等于这一倾斜角;砂轮锥面的角度应等于斜齿条的法向齿形角。
磨完一个齿槽后,应进行分度磨下一个齿槽,工件的分度运动是当工件从一端展成到另一端时,进行一次分度,也可以进行双行程分度,即当工件展成一个往复后,进行一次分度。
为了磨出齿轮整个宽度上的齿面,砂轮还必须沿齿轮轴向进行往复运动。
2 磨齿烧伤裂纹的产生我们公司使用从德国引进的数控磨齿机,这种磨齿机的生产效率低于其他磨齿机,可以同时磨削轮齿的两面,砂轮刚性好,磨削用量也较大,所以难免产生磨削烧伤、裂纹。
这两种常见现象均属于磨齿工序的表面质量问题,它是由齿轮的材料、热处理的方式和磨削三个方面的原因所产生的现象。
从表面上看这一问题与生产效率相矛盾,然而没有质量就没有效益,这是我们都清楚的,众所周知的。
所以它是对应统一的关系。
磨齿过程中,裂纹主要是金属晶体产生塑性变形。
整体硬质合金刀具磨削裂纹的原因分析及其工艺改进

整体硬质合金刀具磨削裂纹的原因分析及其工艺改进1 引言整体硬质合金刀具在航空航天业、模具制造业、汽车制造业、机床制造业等领域得到越来越广泛的应用,尤其是在高速切削领域占有越来越重要的地位。
在高速切削领域,由于对刀具安全性、可靠性、耐用度的高标准要求,整体硬质合金刀具内在和表面的质量要求也更加严格。
而随着硬质合金棒材尤其是超细硬质合金材质内在质量的不断提高,整体硬质合金刀具表面的质量情况越来越受到重视。
众所周知,硬质合金刀具的使用寿命除了与其耐磨性有关外,也常常表现在崩刃、断刃、断裂等非正常失效方面,磨削后刀具的磨削裂纹等表面缺陷则是造成这种非正常失效的重要原因之一。
这些表面缺陷包括经磨削加工后暴露于表面的硬质合金棒料内部粉末冶金制造缺陷(如分层、裂纹、未压好、孔洞等)以及磨削过程中由于不合理磨削在磨削表面造成的磨削裂纹缺陷,而磨削裂纹则更为常见。
这些磨削裂纹,采用肉眼、放大镜、浸油吹砂、体视显微镜和工具显微镜等常规检测手段往往容易造成漏检,漏检的刀具在使用时尤其是在高速切削场合可能会造成严重的后果,因此整体硬质合金刀具产品磨削裂纹缺陷的危害很大。
因此对整体硬质合金刀具磨削裂纹的产生原因进行分析和探讨,并提出有效防止磨削裂纹的工艺改进措施具有很重要的现实意义。
2 整体硬质合金刀具磨削裂纹的原因分析1.整体硬质合金刀具的磨削加工特点硬质合金材料由于硬度高,脆性大,导热系数小,给刀具的刃磨带来了很大困难,尤其是磨削余量很大的整体硬质合金刀具。
硬度高就要求有较大的磨削压力,导热系数低又不允许产生过大的磨削热量,脆性大导致产生磨削裂纹的倾向大。
因此,对硬质合金刀具刃磨,既要求砂轮有较好的自砺性,又要有合理的刃磨工艺,还要有良好的冷却,使之有较好的散热条件,减少磨削裂纹的产生。
一般在刃磨硬质合金刀具时,温度高于600℃,刀具表面层就会产生氧化变色,造成程度不同的磨削烧伤,严重时就容易使硬质合金刀具产生裂纹。
浅析整体硬质合金刀具磨削裂纹的产生及其工艺改进措施

引 言
高效率 高精度硬质合 金刀具是一种 以高性能硬质合金材料
1 . 3 砂轮原 因
整体硬质合金刀具磨刃过程 中, 砂轮 的线速 度和径 向进给量
砂轮硬度越高 、 粒度越细 、 磨损得越厉害 , 都使磨削温度升 为基础的精密刀具 ,是钨材 料产业链 中技术 含量和 附加价值最 越 大, 高得很快, 则越容 易使硬质合金 刀具产生磨削裂纹及磨 削烧伤 。 高的产品之一, 也 是 支 持 先 进 加 工 制造 技术 发 展 的关 键 工 具 。因 砂轮修整 不合格 , 工作表 面产生较大 的跳 动 , 或者在 进行 为硬 质 合 金 刀 具 有 比较 大 的脆 性 , 容易发生裂纹现象 , 所 以 必 须 此 外 , 刃磨时振动过于猛烈 ,那么硬质合金 刀具就很容易产生崩刃等 在刀刃磨削的过程 中注意控 制温度 ,并且选 择合适的砂轮 以及
金磨削表面 的瞬 时温度会 达到很高 ,在温度 的快速增长 下将 导 要求相对较高的加工场合很难进行运用 。使用晶须增韧补强技
致热变形 的产 生。此 外, 又 因为硬 质合金 的抗弯 强度 比较低 , 有 术可 以对这个 问题进行有效 的解 决。在硬质合金刀具材料 中加 很大的刚性模量 , 在正常温度 下根 本没有塑性 , 无法通过 自身的 入晶须能对裂纹扩展 的能量进行 吸收,吸收能量的大小决定于 塑 性 变 形 来 消 除热 应 力 , 因而 在 磨 削 热 的 作 用 下 , 将 使 得 硬 质 合 晶须与基体的结合状 态 。晶须增韧补强技术 能全 面提高整体硬 金刀具的磨削表面产 生局 部热应力值高 于硬 质合金 自身 的强度 质合金刀具材料的硬度、 韧性等综合性能。 极限, 从 而 导 致 裂 纹 的产 生 。 2 . 1 . 1 晶须 的 选 用及 添加 方 式
磨削裂纹的形成与分析

磨削裂纹的形成:发动机上用的各种轴类零件如驱动轴、凸轮轴、曲轴、摇臂轴等在加工过程中需要热处理,但热处理后淬硬或经过渗碳淬火的轴类零件,在磨削过程中由于表面显微组织发生转变而形成大量的裂纹,即磨削裂纹。
下面就磨削裂纹的形成及特征加以阐述。
一、磨削裂纹的产生:(一)磨削裂纹的生成轴类零件在磨削过程中要产生大量的热量,这些热量只限于表面极薄的区域内,它足以使其表面温度达到800℃以上,而且升温极快。
如果磨削时冷却不够充分,将导致表面层的显微组织重新奥氏体化,并再次淬火成为马氏体。
因而使工件表面层产生极大的附加组织应力,同时由于表面温升极快,造成很大的热应力,当组织应力和热应力叠加超过了材料的强度极限时,被磨削的表面就会出现磨削裂纹。
(二)磨削裂纹形成的影响因素:1、组织结构所谓组织结构方面的影响因素有碳化物的形态与分布,残余奥氏体的数量以及非金属夹杂物。
显微组织中碳化物的形态、分布影响着磨削裂纹的生成,如果碳化物数量较多,颗粒较大,分布不均或集聚存在时,将明显地分割金属的基体,降低其强度。
尤其当以断续网状析出时,则会严重地削弱晶间结合力,明显地影响热传导,从而加剧磨削裂纹生成。
如果碳化物细小、分布均匀,则有利于分散磨削应力,从而减少生成磨削裂纹的机率。
零件磨削时显微组织中的残余奥氏体因受磨削热的影响必将发生分解,逐渐转变为马氏体,引起工件表面体积膨胀,而导致组织应力的产生,进而促进裂纹的形成。
因此,工件内部残余奥氏体量较高时,易于产生磨削裂纹。
2、热处理工艺经过淬火而不进行回火的轴件,对磨削裂纹的形成是非常敏感的。
因为磨削时产生的磨削热足以使表层淬火马氏体发生转变,碳化物析出,体积减少。
造成了工件表面与内部的比容差,引起较大的内应力,进而形成裂纹。
轴件有时回火不足,在磨削时也容易形成裂纹。
由此可见,对淬火后的零件必须进行充分地回火。
但是为了保证工件达到一定硬度的要求,回火温度不能任意提高。
因此必须采用合适的磨削工艺,使工件表面受热的温度不超过回火温度。
解决平面磨削产生的磨削裂纹现象方法
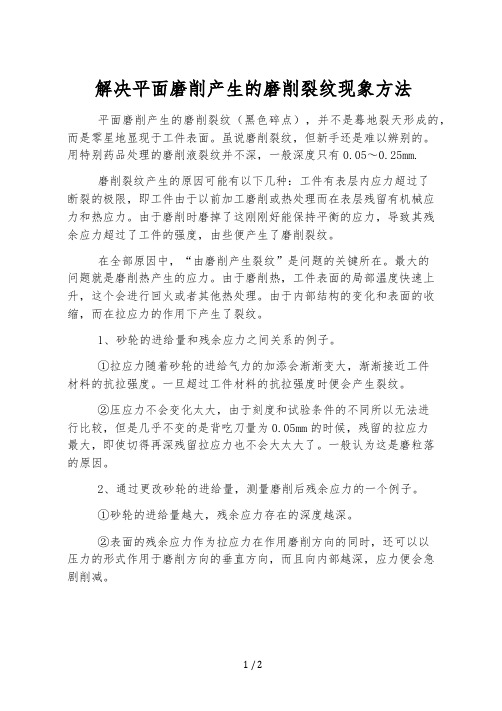
解决平面磨削产生的磨削裂纹现象方法平面磨削产生的磨削裂纹(黑色碎点),并不是蓦地裂天形成的,而是零星地显现于工件表面。
虽说磨削裂纹,但新手还是难以辨别的。
用特别药品处理的磨削液裂纹并不深,一般深度只有0.05~0.25mm.磨削裂纹产生的原因可能有以下几种:工件有表层内应力超过了断裂的极限,即工件由于以前加工磨削或热处理而在表层残留有机械应力和热应力。
由于磨削时磨掉了这刚刚好能保持平衡的应力,导致其残余应力超过了工件的强度,由些便产生了磨削裂纹。
在全部原因中,“由磨削产生裂纹”是问题的关键所在。
最大的问题就是磨削热产生的应力。
由于磨削热,工件表面的局部温度快速上升,这个会进行回火或者其他热处理。
由于内部结构的变化和表面的收缩,而在拉应力的作用下产生了裂纹。
1、砂轮的进给量和残余应力之间关系的例子。
①拉应力随着砂轮的进给气力的加添会渐渐变大,渐渐接近工件材料的抗拉强度。
一旦超过工件材料的抗拉强度时便会产生裂纹。
②压应力不会变化太大,由于刻度和试验条件的不同所以无法进行比较,但是几乎不变的是背吃刀量为0.05mm的时候,残留的拉应力最大,即使切得再深残留拉应力也不会大太大了。
一般认为这是磨粒落的原因。
2、通过更改砂轮的进给量,测量磨削后残余应力的一个例子。
①砂轮的进给量越大,残余应力存在的深度越深。
②表面的残余应力作为拉应力在作用磨削方向的同时,还可以以压力的形式作用于磨削方向的垂直方向,而且向内部越深,应力便会急剧削减。
③作用于沿磨削方向和垂直方向时,先变成压应力而后蓦地变成与磨削方向一致的拉应力。
当达到最大值时渐渐削减,最后成为微小的压应力。
砂轮的硬度和残留拉就力的关系,硬度在G、H、I、J之间,硬度越高,残留的残余应力也就越大。
砂轮的速度(圆周速度)对残余应力的影响。
转速(圆周速度)一旦超过去1500m/min,残余应力就会急剧加大。
此外,由于工件的材料不同也有易发生磨削裂纹和不易发生磨削裂纹的差别。
蜗杆类零件磨削裂纹及对策

2018年 第7期热加工H热处理eatTreatment59蜗杆是机床回转部件中的重要零件,工作时蜗杆螺旋表面与蜗轮齿面相对滑动,容易发生磨损,因此蜗杆常用渗碳钢经渗碳淬火处理,以获得较高的硬度,防止蜗杆螺旋表面发生磨损。
蜗杆类零件的精度要求很高,加工工艺复杂、工序长,如在加工过程中出现问题,将造成重大损失。
我公司一种蜗杆零件在磨削加工时出现磨削裂纹,导致零件报废,严重影响了生产进度。
1. 蜗杆材料及主要工艺流程此蜗杆材料为20CrMnTiH ,形状如图1所示,热处理要求为渗碳淬火,渗碳层深1.1~ 1.5m m ,淬火后表面硬度58HRC 。
蜗杆加工工艺流程:下料→锻造→正火→粗车→除应力→精车→渗碳→螺纹处去碳→淬火→粗磨→无损检测→时效→精磨。
热处理过程:锻件正火→渗碳→淬火→低温回火→矫直→除蜗杆类零件磨削裂纹及对策■ 贾云峰摘要:20CrMnTiH 钢制蜗杆经渗碳淬火后磨削时发现裂纹,经分析认为,淬火温度偏高,淬火后残留奥氏体较多,在回火不充分时,在磨削热的影响下残留奥氏体发生转变,产生较大内应力,导致磨削时形成裂纹。
通过增加回火时间、增加冰冷定性,可有效解决这一现象。
关键词:蜗杆;磨削;裂纹;残留奥氏体扫码了解更多应力→低温时效。
热处理工艺过程曲线如图2所示。
渗碳淬火后,经检验碳化物1级,渗碳层深1.32mm ,表面硬度59~60HRC 。
2. 裂纹现象描述粗磨后蜗杆齿面出现磨削裂纹,裂纹极细,直线状,深度较浅,形态为通常所说的“发纹”,裂纹不平行,呈散射线状,如图3所示。
3. 磨削裂纹产生原因分析磨削裂纹与一般淬火裂纹明显不同,淬火裂纹粗而深,数量少;磨削裂纹只发生在磨削面上,数量较多,深度较浅,且深度基本一致。
较轻的磨削裂纹垂直于或接近垂直于磨削方向呈条状裂纹。
此蜗杆齿面是螺旋状曲面,磨削方向如图3中箭头所图 1图 22018年 第7期 热加工H热处理eatTreatment60示,裂纹垂直于磨削方向,符合磨削裂纹的特征。
摩托车发动机轴类件磨削裂纹分析及应对

制 定 了改善 措施 ,经长期 实践 证 明 ,效果 良好 ,满 足 了用 户 的需 求 ,现 在 基本根 除 了此 问题 的发生 。
发 动机 工作 中起 着 关键 作 用 ,其 质量 的优 劣直 接 影响 发动 机 的品 质和 性 能。 济南 轻骑 发动 机有 限 公 司是 摩 托车 发动 机 生产 企业 ,其 使 用的 中 间轴 、驱 动轴 、变 挡轴 及部 分销
f r a in o r c s Th r f r ,i h eane u tn t sh g e n t e ine ft e p rs ra r c sw i e o m to fca k . e e o e ft e rt i d a se ie i i h ri h n ro a t,g e tc a k l b h l e sl o nd ai fu . y
式中 : 广_ 凸轮靠模该段 曲线的曲率半径 ,m m
, 广 工件 凸轮该 段 曲线 的 曲率半 径 ,mm
由 图 3看 到 ,以 工 件 凸轮 基 圆 中心 O 为 圆心 ,以 选 定 的 凸轮 靠模 基 圆半 径 风 为半 径作 靠 模 基 圆 ,然 后 以 工 件 凸轮轮 廓 各段 曲线 的几 何 中心 0 = 12 )为 圆心 , ( ,…
解决磨削裂纹的新思路、新途径
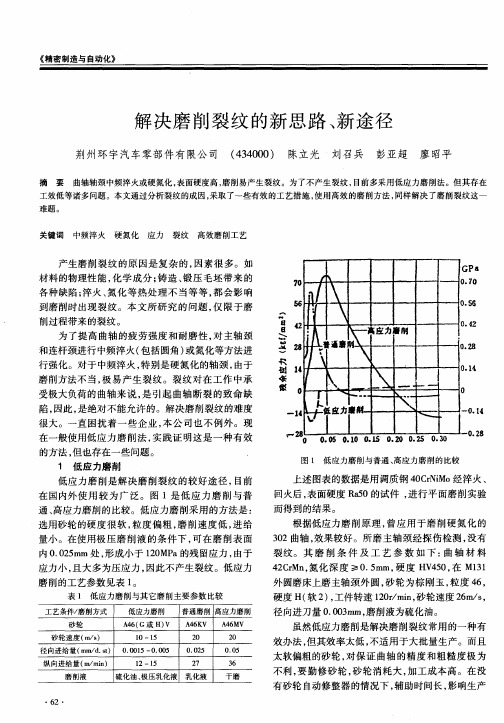
裂纹。
53 保持砂轮微刃锋利的方法是: . ①选用物理 性能好的磨料; ②勤修砂轮, 采用能自 动修整砂轮的
参考文献
[〕 1 孟少农主编,机械加工工艺手册》 ,, 章。 《 1 1 4 3 机械工业出 版社, 9 年 18 9 [〕 2 朱培瑜等著,淬火裂纹及磨削裂纹》 机械制造》1 3 《 《 ,8 年 9
1期 0
图2 冷却喷嘴
《 精密制造与自动化》
解决磨削裂纹的新思路、 新途径
荆州环宇汽车零部件有限公司 (300 陈立光 刘召兵 彭亚超 廖昭平 440 )
摘 要 曲轴轴颈中 频淬火或硬氮化, 表面硬度高, 磨削易产生裂纹。为了不产生裂纹, 前多采用低应力磨削法。 目 但其存在 工效低等诸多问题。本文通过分析裂纹的成因, 采取了一些有效的工艺措施, 使用高效的磨削方法, 同样解决了磨削裂纹这一
1 低应力磨削
渊 l\ ’ }
卜 通奋
。\ / \ } }
I、
训
1
I }} “m ”
i
\
人
‘. ̄. .一 习
一 { 入
戈}
a 卜 l }
{ 一 !
一I ‘
、 ̄
图1 低应力磨削与普通、 高应力磨削的比较
低应力磨削是解决磨削裂纹的较好途径, 目前 在国内外使用较为广泛。图 1 是低应力磨削与普 通、 高应力磨削的比较。低应力磨削采用的方法是: 选用砂轮的硬度很软, 粒度偏粗, 磨削速度低, 进给 量小。在使用极压磨削液的条件下, 可在磨削表面 内005 形成小于 10 P 的残留应力, . m处, 2m 2M a 由于 应力小, 且大多为压应力, 因此不产生裂纹。低应力 磨削的工艺参数见表 I o
磨削烧伤、磨削裂纹及控制措施
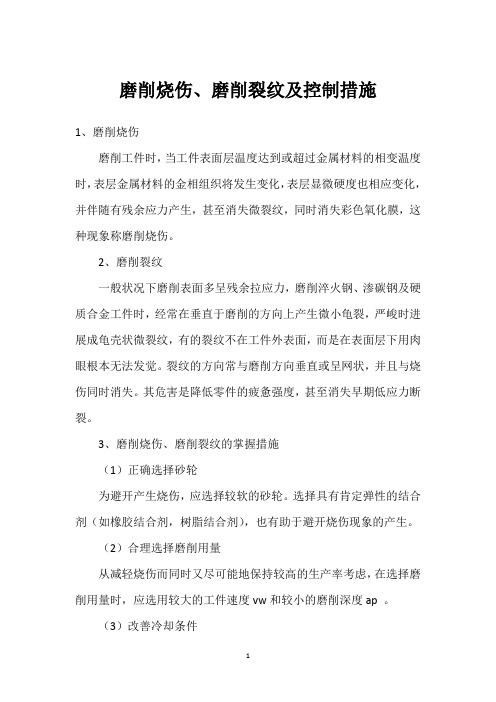
磨削烧伤、磨削裂纹及控制措施1、磨削烧伤磨削工件时,当工件表面层温度达到或超过金属材料的相变温度时,表层金属材料的金相组织将发生变化,表层显微硬度也相应变化,并伴随有残余应力产生,甚至消失微裂纹,同时消失彩色氧化膜,这种现象称磨削烧伤。
2、磨削裂纹一般状况下磨削表面多呈残余拉应力,磨削淬火钢、渗碳钢及硬质合金工件时,经常在垂直于磨削的方向上产生微小龟裂,严峻时进展成龟壳状微裂纹,有的裂纹不在工件外表面,而是在表面层下用肉眼根本无法发觉。
裂纹的方向常与磨削方向垂直或呈网状,并且与烧伤同时消失。
其危害是降低零件的疲惫强度,甚至消失早期低应力断裂。
3、磨削烧伤、磨削裂纹的掌握措施(1)正确选择砂轮为避开产生烧伤,应选择较软的砂轮。
选择具有肯定弹性的结合剂(如橡胶结合剂,树脂结合剂),也有助于避开烧伤现象的产生。
(2)合理选择磨削用量从减轻烧伤而同时又尽可能地保持较高的生产率考虑,在选择磨削用量时,应选用较大的工件速度vw和较小的磨削深度ap 。
(3)改善冷却条件① 采纳高压大流量法此法不但可以增加冷却作用,而且也增加了对砂轮的冲洗作用,使砂轮不易堵塞。
② 安装带空气挡板的喷嘴此法可以减轻高速回转砂轮表面处的高压附着气流作用,使磨削液能顺当喷注到磨削区。
③ 采纳磨削液雾化法或内冷却法采纳特地装置将磨削液雾化,使其带走大量磨削热,增加冷却效果;也可采纳内冷却砂轮,其工作原理如图所示。
经过严格过滤的磨削液由锥形套1经空心主轴法兰套2引入砂轮的中心腔3内,由于离心力的作用,磨削液经由砂轮内部有径向小孔的薄壁套4的孔隙甩出,直接浇注到磨削区。
图内冷却砂轮结构1-锥形盖2-主轴法兰套3-砂轮中心腔4-薄壁套。
浅谈磨削裂纹
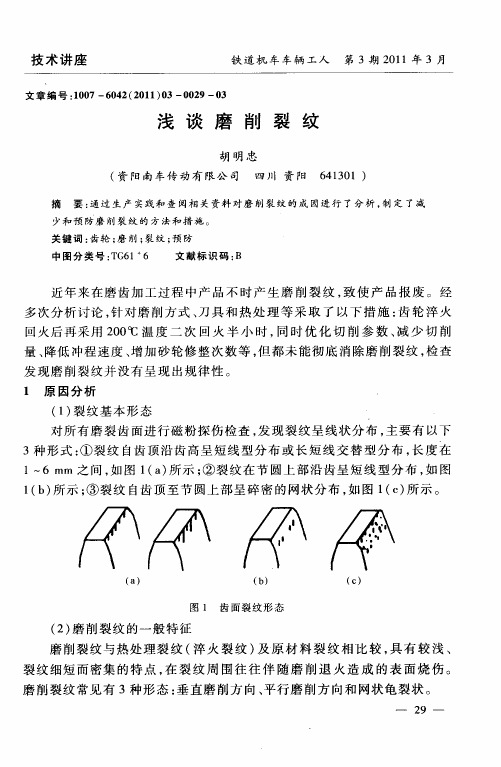
铁道机车车辆工人 第 3期 2 1 年 3月 01
文 章 编 号 :0 7— 0 2 2 1 ) 3— 0 9一O 10 6 4 (0 1 0 0 2 3
浅 谈 磨 削 裂 纹
胡 明 忠 ( 阳 南 车传 动 有 限公 司 四川 资 阳 6 1 0 资 4 3 1)
深度 较深 的特 性 。对 于无 法用 肉眼 观察 的细 小裂 纹 可 以通 过 磁粉 探伤 和烧 伤 检测 两种 方 式加 以辨别 , 中烧 伤 检 测 可 准确 辨 别 出裂 纹 产 生部 位 的磨 其 削烧 伤状 。一般 磨 削裂纹 都 是 由 于局 部 热应 力 过 大 , 生 较 大 的 拉应 力 而 产 导 致裂 纹 , 烧伤 检测 可看 出裂 纹 部位 呈严 重 的烧伤 痕 迹 。另外 , 齿 面裂 经 对 纹 部 位进 行酸 腐蚀 检查 也 是一 种可 靠 的检测 方法 。 ( ) 齿 过程 中诱 发磨 削 裂纹 的几 种原 因 3磨
1 原 因 分 析
( ) 纹 基 本 形 态 1裂
对所 有磨 裂 齿 面进 行磁 粉 探伤 检 查 , 现裂 纹 呈线 状 分 布 , 要有 以 下 发 主 3种 形 式 : 裂纹 自齿 顶 沿 齿高 呈 短线 型分 布 或 长 短 线交 替 型分 布 , ① 长度 在 1 m 之 间 , 图 1 a 所 示 ; 裂 纹在 节 圆上 部沿 齿 呈短 线 型 分 布 , 图 ~6 m 如 () ② 如 1 b 所 示 ; 裂 纹 自齿 顶至 节 圆上 部呈 碎 密 的 网状 分 布 , 图 1 c 所 示 。 () ③ 如 ()
生 拉应 力 , 种拉 应力 与热 处理 后 的残余 应 力相 叠加 而形 成 了磨 削裂纹 。 这
2 预 防 措 施
感应淬火曲轴磨削裂纹原因分析

感应淬火曲轴磨削裂纹原因分析摘要:淬火曲轴作为发动机的核心部件之一,其质量和可靠性直接影响汽车的安全性和性能。
曲轴的磨削过程是其制造过程中的重要环节之一,但在磨削过程中常常出现裂纹现象,大大降低了曲轴的质量和寿命。
本文通过对淬火曲轴磨削裂纹的原因分析,旨在为曲轴生产厂家提供技术参考和改进方向,进一步提高淬火曲轴的质量和可靠性。
关键词:淬火曲轴;磨削;裂纹;原因分析正文:一、淬火曲轴磨削裂纹的原因在磨削淬火曲轴的过程中,裂纹是经常出现的一种质量问题。
其原因主要有以下几个方面:1.材料质量问题淬火曲轴的材料通常采用高强度钢材,但由于制造过程中的管制不够严格,很容易出现材料的强度、硬度不一致的情况,从而导致曲轴表面的磨削裂纹问题。
2.磨削工艺问题磨削淬火曲轴需要考虑到工艺的严谨性和合理性,如果磨削速度过快,磨削力度过大,很容易引起曲轴表面的变形和热裂纹;同时磨削过程中必须保证润滑剂充足,否则会因为摩擦产生高温而导致热裂纹。
3.工艺温度不合适淬火曲轴的磨削需要在特定的温度环境下进行,如果温度过高或者过低,都会导致材料的变形和热裂纹。
二、解决淬火曲轴磨削裂纹的措施磨削淬火曲轴时出现裂纹问题,不利于提高曲轴的质量和可靠性,因此有必要采取相应的措施来解决。
在实践中,可以采用以下方法:1.材料选择和管制生产厂家需要对材料进行选择和管制,确保曲轴的材料质量达标,硬度、强度等参数的一致性和稳定性。
2.改进磨削工艺厂家需要对磨削工艺进行改进,严格控制磨削速度、力度和润滑剂的充足性,避免产生高温而导致热裂纹。
3.控制磨削温度生产厂家需要对磨削温度进行严格控制,避免温度过高或过低而产生变形和热裂纹。
三、结论淬火曲轴作为发动机的核心部件之一,其质量和可靠性直接影响汽车的安全性和性能。
磨削淬火曲轴时出现裂纹问题,严重降低了曲轴的质量和寿命。
通过对淬火曲轴磨削裂纹原因的分析和解决方法的探讨,可以为曲轴生产厂家提供一定的技术参考和改进方向,进一步提高淬火曲轴的质量和可靠性。
轴承零件磨削裂纹防止措施
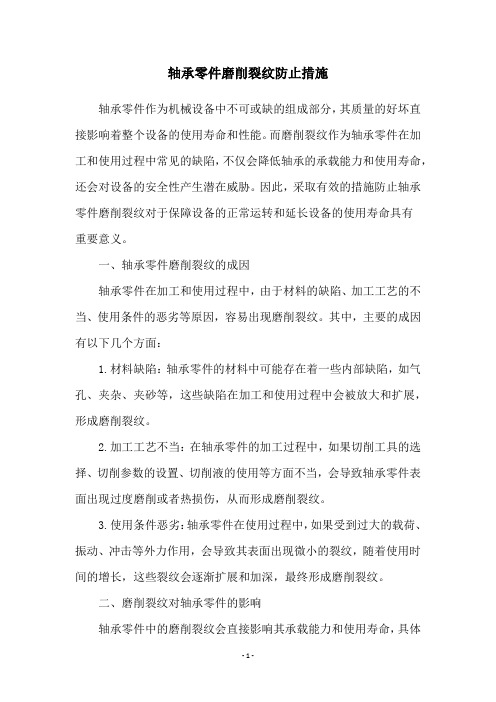
轴承零件磨削裂纹防止措施轴承零件作为机械设备中不可或缺的组成部分,其质量的好坏直接影响着整个设备的使用寿命和性能。
而磨削裂纹作为轴承零件在加工和使用过程中常见的缺陷,不仅会降低轴承的承载能力和使用寿命,还会对设备的安全性产生潜在威胁。
因此,采取有效的措施防止轴承零件磨削裂纹对于保障设备的正常运转和延长设备的使用寿命具有重要意义。
一、轴承零件磨削裂纹的成因轴承零件在加工和使用过程中,由于材料的缺陷、加工工艺的不当、使用条件的恶劣等原因,容易出现磨削裂纹。
其中,主要的成因有以下几个方面:1.材料缺陷:轴承零件的材料中可能存在着一些内部缺陷,如气孔、夹杂、夹砂等,这些缺陷在加工和使用过程中会被放大和扩展,形成磨削裂纹。
2.加工工艺不当:在轴承零件的加工过程中,如果切削工具的选择、切削参数的设置、切削液的使用等方面不当,会导致轴承零件表面出现过度磨削或者热损伤,从而形成磨削裂纹。
3.使用条件恶劣:轴承零件在使用过程中,如果受到过大的载荷、振动、冲击等外力作用,会导致其表面出现微小的裂纹,随着使用时间的增长,这些裂纹会逐渐扩展和加深,最终形成磨削裂纹。
二、磨削裂纹对轴承零件的影响轴承零件中的磨削裂纹会直接影响其承载能力和使用寿命,具体表现在以下几个方面:1.降低承载能力:磨削裂纹会导致轴承零件的强度和韧性降低,从而使其在受到载荷时容易发生断裂或疲劳破坏,降低其承载能力。
2.影响使用寿命:磨削裂纹会使轴承零件的表面粗糙度增加,从而导致摩擦系数增大,摩擦热增加,最终使轴承零件的使用寿命缩短。
3.安全风险增加:磨削裂纹会在轴承零件受到过载、振动等作用时进一步扩展和加深,最终导致轴承零件的断裂,从而对设备的安全性产生潜在威胁。
三、轴承零件磨削裂纹防止措施为了有效地防止轴承零件的磨削裂纹,可以采取以下措施:1.合理选择材料:在选择轴承零件材料时,要选择质量好、无内部缺陷的材料,以减少磨削裂纹的产生。
2.优化加工工艺:在轴承零件的加工过程中,要根据不同的工件材料和零件结构合理选择切削工具和切削参数,同时要加强切削液的使用,以减少磨削裂纹的产生。
产生齿轮磨削裂纹的影响因素及措施
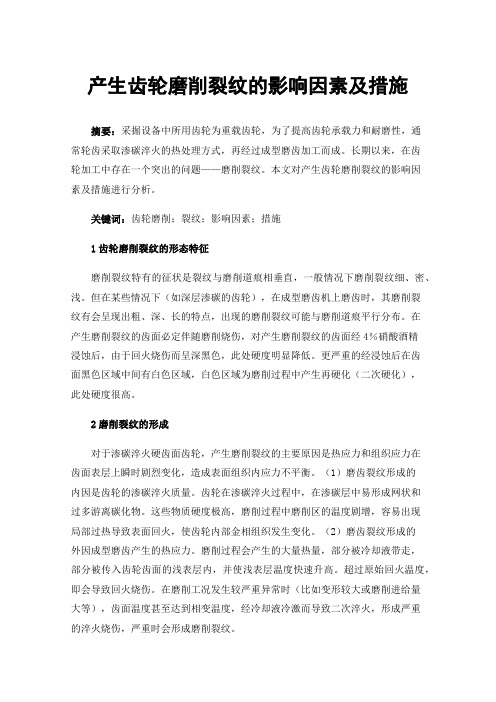
产生齿轮磨削裂纹的影响因素及措施摘要:采掘设备中所用齿轮为重载齿轮,为了提高齿轮承载力和耐磨性,通常轮齿采取渗碳淬火的热处理方式,再经过成型磨齿加工而成。
长期以来,在齿轮加工中存在一个突出的问题——磨削裂纹。
本文对产生齿轮磨削裂纹的影响因素及措施进行分析。
关键词:齿轮磨削;裂纹;影响因素;措施1齿轮磨削裂纹的形态特征磨削裂纹特有的征状是裂纹与磨削道痕相垂直,一般情况下磨削裂纹细、密、浅。
但在某些情况下(如深层渗碳的齿轮),在成型磨齿机上磨齿时,其磨削裂纹有会呈现出粗、深、长的特点,出现的磨削裂纹可能与磨削道痕平行分布。
在产生磨削裂纹的齿面必定伴随磨削烧伤,对产生磨削裂纹的齿面经4%硝酸酒精浸蚀后,由于回火烧伤而呈深黑色,此处硬度明显降低。
更严重的经浸蚀后在齿面黑色区域中间有白色区域,白色区域为磨削过程中产生再硬化(二次硬化),此处硬度很高。
2磨削裂纹的形成对于渗碳淬火硬齿面齿轮,产生磨削裂纹的主要原因是热应力和组织应力在齿面表层上瞬时剧烈变化,造成表面组织内应力不平衡。
(1)磨齿裂纹形成的内因是齿轮的渗碳淬火质量。
齿轮在渗碳淬火过程中,在渗碳层中易形成网状和过多游离碳化物。
这些物质硬度极高,磨削过程中磨削区的温度剧增,容易出现局部过热导致表面回火,使齿轮内部金相组织发生变化。
(2)磨齿裂纹形成的外因成型磨齿产生的热应力。
磨削过程会产生的大量热量,部分被冷却液带走,部分被传入齿轮齿面的浅表层内,并使浅表层温度快速升高。
超过原始回火温度,即会导致回火烧伤。
在磨削工况发生较严重异常时(比如变形较大或磨削进给量大等),齿面温度甚至达到相变温度,经冷却液冷激而导致二次淬火,形成严重的淬火烧伤,严重时会形成磨削裂纹。
3产生齿轮磨削裂纹的影响因素3.1首次磨齿切削量成型磨齿一般采用双面磨削,加工前由于留有磨量且热处理过程会有变形,由于机床对中时所测磨削余量不准确,造成首次切削量比较大,导致磨齿过程齿面热急增,引起齿面表层回火或二次淬火。
- 1、下载文档前请自行甄别文档内容的完整性,平台不提供额外的编辑、内容补充、找答案等附加服务。
- 2、"仅部分预览"的文档,不可在线预览部分如存在完整性等问题,可反馈申请退款(可完整预览的文档不适用该条件!)。
- 3、如文档侵犯您的权益,请联系客服反馈,我们会尽快为您处理(人工客服工作时间:9:00-18:30)。
解决磨削裂纹的新思路、新途径
产生磨削裂纹的原因是复杂的,因素很多。
如材料的物理性能,化学成分;铸造、锻压毛坯带来的各种缺陷;淬火、氮化等热处理不当等等,都会影响到磨削时出现裂纹。
本文所研究的问题,仅限于磨削过程带来的裂纹。
为了提高曲轴的疲劳强度和耐磨性,对主轴颈和连杆颈进行中频淬火(包括圆角)或氮化等方法进行强化。
对于中频淬火,特别是硬氮化的轴颈,由于磨削方法不当,极易产生裂纹。
裂纹对在工作中承受极大负荷的曲轴来说,是引起曲轴断裂的致命缺陷,因此,是绝对不能允许的。
解决磨削裂纹的难度很大。
一直困扰着一些企业。
现在一般使用低应力磨削法,实践证明这是一种有效的方法,但也存在一些问题。
1 低应力磨削
低应力磨削是解决磨削裂纹的较好途径,目前在国内外使用较为广泛。
低应力磨削采用的方法是:选用砂轮的硬度很软,粒度偏粗,磨削速度低,进给量小。
在使用极压磨削液的条件下,可在磨削表面内0.025mm处,形成小于120MPa的残留应力,由于应力小,且大多为压应力,因此不产生裂纹。
低应力磨削的工艺参数见表1。
上述表的数据是用调质钢40CrNiMo经淬火、回火后,表面硬度Ra50的试件,进行平面磨削实验而得到的结果。
根据低应力磨削原理,曾应用于磨削硬氮化的302曲轴,效果较好。
所磨主轴颈经探伤检测,没有裂纹。
其磨削条件及工艺参数如下:曲轴材料42CrMn,氮化深度≥0.5mm,硬度HV450,在M131外圆磨床上磨主轴颈外圆,砂轮为棕刚玉,粒度46,硬度H(软2),工件转速120r/min,砂轮速度26m/s,径向进刀量0.003mm,磨削液为硫化油。
虽然低应力磨削是解决磨削裂纹常用的一种有效办法,但其效率太低,不适用于大批量生产。
而且太软偏粗的砂轮,对保证曲轴的精度和粗糙度极为不利,要勤修砂轮,砂轮消耗大,加工成本高。
在没有砂轮自动修整器的情况下,辅助时间长,影响生产效率。
为此提出了探讨高效无裂纹磨削工艺的课题。
2 磨削应力及裂纹产生过程
曲轴的机械加工过程中,会产生残留应力,磨削加工也不例外,有关研究表明,它的残留应力是由塑变应力、热变应力及相变应力三部分构成。
对于表面淬火的曲轴,特别是硬氮化的曲轴,表面是一层硬壳,硬度为HV≥420(HR15N≥82),硬则脆,脆极易产生裂纹。
脆则塑性差,因此硬而脆的表面,产生塑性变形应力的可能性很小,可以不考虑。
磨削过程由摩擦、挤压及切削三过程组成。
磨削过程中的摩擦和挤压剧烈时,它的能量绝大部分将转化为热能,其中传入工件的达到了80%,大量的热能使磨削区域的温度达到500℃-800℃,而磨粒的切削刃与切屑接触点的温度,瞬时值可达1000℃,传入工件的高温又集中于磨削部位的表层,表层温度高,里层温度低,表层及里层受热膨胀的体积大小因温度差不能同步,相互之间的牵制作用,形成了热变应力。
对于表面硬度高的轴颈,这是磨削中残留应力的最主要部分。
磨削时的表层温度若超过720℃左右的相变温度时,表层组织要发生相变,不同的金相组织,其体积大小是不同的,体积的增大与缩小,与金相组织的类型有关,外层金相组织改变而内层不变,相互之间的牵制作用,形成了相变应力,若将磨削时的表层温度控制在720℃范围内,不产生相变,也就不会形成相变应力。
当磨削时表层温度超过相变温度720℃时,在温度剧升和相变的双重因素作用下,表层的体积向外膨胀,沿周边伸长,温度向内层传递较慢,里层温度低,膨胀也慢,它阻碍外层膨胀,使外层在周边上不能伸长,造成外层的压应力,这时不会产生裂纹。
当磨削液使工件冷却时,表层迅速收缩,这时里层温度变化不大,不能同步收缩,里层对表面极薄层收缩的阻碍作用,形成表层的拉应力,使表层开裂,出现裂纹。
总之,拉应力产生裂纹,压应力有利于提高工件的疲劳强度。
3 不产生磨削裂纹的工艺途径
从产生裂纹的机理中可知,产生裂纹的根本原因,是磨削过程产生了高温。
因此,磨削时工件不产生高温,或将高温在传入工件表层前将其带走,从这两方面着手,才是解决磨削裂纹的根本途径。
高温绝大多数来源于磨削过程中的摩擦和挤压,减少摩擦和挤压是降低温度的关键。
只有磨粒刃口锋利时,磨削过程是切削过程占主导地位,摩擦、挤压很轻微,产生的热量小,表层温度自然就低了。
只要做到刃口锋利,并能维持较长时间的锋利。
加强润滑,减小摩擦、挤压,也延长了锋利刃口的寿命。
当刃口钝化时,应及时修整砂轮。
基于上述认识,决定从下列五个方面开展工作。
3.1 砂轮磨料是关键,选择合适的砂轮。
对磨料性能的要求是硬度高,抗弯强度大,耐热性能好(热稳定性好)刃口锋利,且自锐能力强,耐磨性能高,能长期维护刃口锋利。
磨料中棕刚玉价位低,其性能较差。
白玉较好,铬刚玉、单晶刚玉和微晶刚玉则更好一些。
有一些混合磨料性能也能满足要求。
最理想的磨料为立方氮化硼(CBN)各种性能均优于刚玉类磨料,其显微硬度是刚玉的3—5倍,抗弯强度为其3.5
倍,耐磨性能是刚玉的100倍。
因此能长时间保持刃口的锋利,不会产生烧伤和裂纹。
但其价格昂贵,修整困难。
通过试验找到了价位适中,又能满足工艺要求的砂轮。
3.2 要使用自动砂轮修整器。
必须做到磨一个轴颈,修一次砂轮,始终保持砂轮刃口的锋利性。
3.3 选择润滑性能好的磨削液,如含极压成份的切削液,硫化切削油等。
在保证工艺要求的前提下,要考虑环保要求。
3.4 具有较大压力和流量的供液装置。
磨削时能将充分的磨削液送入磨削区,进行高效的润滑、冷却和清洗,将热量带走,降低磨削区的温度,并避免砂轮堵塞。
3.5 具有高效的磨削液过滤装置。
磨削液中的砂粒,铁屑等杂质,不仅对曲轴的精度、粗糙度有不利影响,而且它会破坏润滑膜,成为裂纹源。
因此必须将磨削液中的杂质过滤清除。
4 无裂纹的高效磨削
四年前,根据前述分析和思路,选择了合适的磨床,完善其功能。
进行了一系列试验,从中优选出较好的工艺方案,用于批量生产。
基本解决了淬火和硬氮化处理的曲轴,在普通磨削(磨削V=30m/s)和高速磨削(V=50m/s)的条件下无裂纹。
这几年,已用于各类曲轴的大批量生产。
其中,很多曲轴出口国外,取得了好的经济效果。
以磨削302硬氮化曲轴连杆颈为例,介绍其有关参数。
使用的磨床是KA500×1250CNC-S(德)半自动连杆颈磨床,该磨床具有数控砂轮修整器,磨完一个连杆颈后,能自动修整砂轮一次。
使用压力大、流量大的水泵,三个喷嘴对砂轮清洗,润滑冷却磨削区。
压力1.5-1.8Mpa。
主喷嘴流量10-14L/S,用于砂轮及轴颈外圆的冷却润滑。
每个支喷嘴流量6-8L/S,用于圆角及侧面。
实验证明流量过小或过大均会产生裂纹。
流量大小,还要根据工件材质和热处理状况进行调整。
磨削液使用磁性过滤器和涡旋分离器双重过滤系统净化处理,净化率可达到大于99%。
砂轮使用刚玉类混合磨料,60粒度,M级(中1)硬度,高速磨削V=50m/s。
其主要参数与低应力磨削的比较见表2。
由于使用了高速磨削,其进给量又比低应力磨削大,生产效率高,是低应力磨削的3~5倍。
5 结论
5.1 低应力磨削是解决磨削裂纹的有效途径,使用比较广泛。
但是使用砂轮的硬度低,粒度粗,对保证工件的精度和粗糙度不利,磨削效率低,不利于大批量生产。
使用硫化切削油,气味重,有污染,不利于工人操作。
5.2 不产生磨削裂纹的关键因素是较长时间保持砂轮微刃的锋利。
锋利的刃口,减缓了磨削过程中的摩擦挤压过程,从而降低了磨削区的温度。
若降至600℃以下,或更低。
磨削液能将热量迅速带走,磨削部位表、里层温度低,梯度小,也就不会出现裂纹。
5.3 保持砂轮微刃锋利的方法是:①选用物理性能好的磨料;②勤修砂轮,采用能自动修整砂轮的磨床,磨一个连杆颈修一次砂轮;③采取润滑性能好的水基极压磨削液;④使用压力较大,流量充分的磨削液的供液装置,并具有净化率高的过滤系统。
5.4 无裂纹高效磨削的优点是:效率高,更容易保证工件的加工质量(精度和粗糙度),可使用水基磨削液,改善了磨削环境,优于低应力磨削。
但目前国内有不少的磨床不具备所需的功能,若能按上述要求改装,亦能达到同样的目的。
5.5 无裂纹高效磨削工艺,还需要进一步研究完善,优选出更佳的工艺参数。