数控切割机下料编程操作流程
数控编程流程
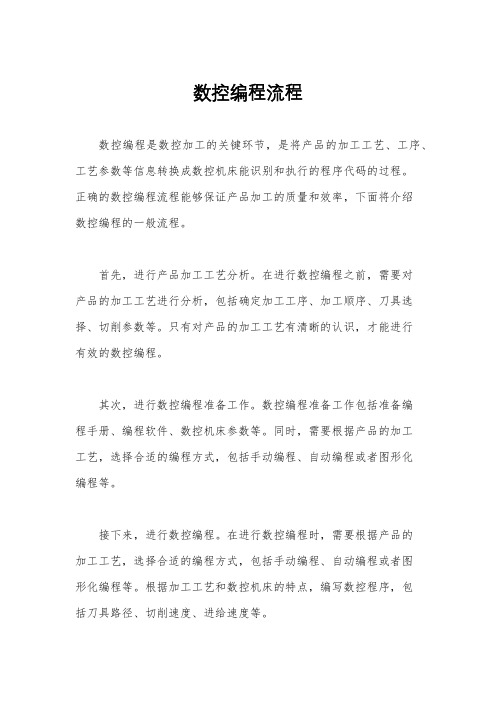
数控编程流程数控编程是数控加工的关键环节,是将产品的加工工艺、工序、工艺参数等信息转换成数控机床能识别和执行的程序代码的过程。
正确的数控编程流程能够保证产品加工的质量和效率,下面将介绍数控编程的一般流程。
首先,进行产品加工工艺分析。
在进行数控编程之前,需要对产品的加工工艺进行分析,包括确定加工工序、加工顺序、刀具选择、切削参数等。
只有对产品的加工工艺有清晰的认识,才能进行有效的数控编程。
其次,进行数控编程准备工作。
数控编程准备工作包括准备编程手册、编程软件、数控机床参数等。
同时,需要根据产品的加工工艺,选择合适的编程方式,包括手动编程、自动编程或者图形化编程等。
接下来,进行数控编程。
在进行数控编程时,需要根据产品的加工工艺,选择合适的编程方式,包括手动编程、自动编程或者图形化编程等。
根据加工工艺和数控机床的特点,编写数控程序,包括刀具路径、切削速度、进给速度等。
然后,进行数控程序的调试。
在编写完数控程序后,需要进行数控程序的调试,包括在模拟软件中进行程序的仿真和验证,确保程序的正确性和可靠性。
同时,需要根据数控机床的实际情况,对程序进行调整和优化,以提高加工效率和质量。
最后,进行数控程序的执行和监控。
当数控程序调试完成后,可以将程序下载到数控机床中进行执行。
在执行过程中,需要对加工情况进行实时监控,确保加工的精度和质量达到要求。
总之,数控编程是数控加工的重要环节,正确的数控编程流程能够保证产品加工的质量和效率。
通过对产品加工工艺的分析、数控编程准备工作、数控编程、数控程序的调试以及数控程序的执行和监控等环节的合理安排和有效实施,能够有效提高数控加工的效率和质量,满足不同产品加工的需求。
数控切割编程作业指导书

数控切割编程作业指导书1 目的规范下料切割工艺,提升下料件的切口成型质量,降低切割缺陷的形成几率,提高产品的外观质量。
2 范围适用于原材料切割下料的加工过程,同时适用于以火焰切割、等离子切割等为切割方式的切割下料过程。
3职责3.1 产品承制部门/工区负责施工及施工过程的组织、监控及现场管理等。
3.2 编程人员职责3.2.1 熟练、正确地使用FASTCAM软件中的各个模块,了解AUTOCAD的基本操作。
3.2.2 在板材套料时最大化板材利用率,为企业降本增效。
3.2.3 设定正确的切割补偿、切割方向等参数,保证切割质量。
3.2.4 利用切割机的特点,选择合适的套料类型,提高切割速度。
3.2.5 能正确识读船体结构图纸,提取结构尺寸。
3.2.6 熟练掌握经常涉及到的船体工艺规范。
4 工作程序4.1 工作流程4.1.1由作业长开下料单(或其他部门开具的横向联系单),明确所需零件的规格、数量。
4.1.2 清楚所要排版的板材的规格、数量。
4.1.3 使用编程软件编程。
4.1.4 保存的零件图应按船名、日期、队伍、规格等分类归档,使其具有可追溯性。
4.1.5输出切割代码拷贝至数控切割机。
4.1.6通知数控切割机操作工下料,对图纸上不明确的地方向操作工交代清楚。
4.2 编程流程图4.3 使用FASTCAM软件作图时的注意事项:4.3.1 在安装使用软件前应先了解公司内使用的数控切割机控制器类型,在安装FASTCAM时应选择适合的控制器类型,否则会导致输出的NC码与控制器不兼容情况。
(本公司现今四台数控切割机控制器类型均为EDGE)。
4.3.2 在进行补偿设置时,一定要注意左补偿内轮廓的方向是逆时针行走,外轮廓是顺时针行走。
右补偿内轮廓是顺时针,外轮廓是逆时针。
否则,将来的工件切割时就会出现尺寸上的偏差。
4.3.3 考虑到等离子切割时气流旋转方向的问题,选择切割方向时应该保证需要的边在切割路径的右边。
即内轮廓的方向是逆时针切割,外轮廓是顺时针切割。
数控切割机编程及加工工艺控制
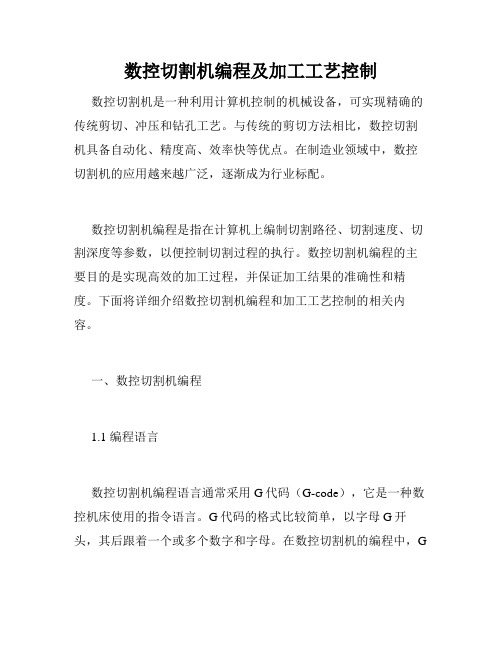
数控切割机编程及加工工艺控制数控切割机是一种利用计算机控制的机械设备,可实现精确的传统剪切、冲压和钻孔工艺。
与传统的剪切方法相比,数控切割机具备自动化、精度高、效率快等优点。
在制造业领域中,数控切割机的应用越来越广泛,逐渐成为行业标配。
数控切割机编程是指在计算机上编制切割路径、切割速度、切割深度等参数,以便控制切割过程的执行。
数控切割机编程的主要目的是实现高效的加工过程,并保证加工结果的准确性和精度。
下面将详细介绍数控切割机编程和加工工艺控制的相关内容。
一、数控切割机编程1.1 编程语言数控切割机编程语言通常采用G代码(G-code),它是一种数控机床使用的指令语言。
G代码的格式比较简单,以字母G开头,其后跟着一个或多个数字和字母。
在数控切割机的编程中,G代码被用来控制机床工作的轴的运动方式和速度,以及加工刀具的位置、加工参数、工艺路线等方面。
1.2 切割路径切割路径是指在加工平面上绘制的切割轮廓。
在数控切割机编程中,切割路径由一系列直线和曲线组成。
数控切割机对于不同的曲线要求不同,如直线的表示为L,圆弧的表示为C。
其中,圆弧的表示方式包括圆心坐标、半径、起始角度和终止角度等参数。
编程时需要精确计算每条线路的长度、夹角和速度等参数。
1.3 切割深度切割深度是指工件表面下切割工具走过的距离。
在数控切割机编程中,切割深度需要与切割速度和转速配合控制。
在计算切割深度时,需要考虑工件材料的硬度、切割刀具的形状、切割厚度等因素。
1.4 切割速度切割速度是指切割工具在切割时的移动速度。
在数控切割机编程中,切割速度用切割工件的速度来表示。
切割速度的大小取决于工件的材料、形状、切割工具的形状、刃口的数量等多个因素。
在编程时,需要根据实际情况合理设置切割速度,以保证切割的效率和精度。
二、加工工艺控制数控切割机的加工切割时需要通过一系列的精确控制来实现精度的保证。
在加工过程中,需要控制的因素有切割厚度、切割深度、切割速度、进给速率、冷却方式等。
数控切割机下料编程操作流程

数控切割机下料编程收配过程之阳早格格创做一、使用autoCAD步调绘佳图形后,面打“文献”菜单中“输出”选项,将文献存为“dxf”文献典型(如果FastCAM步调收援“DWG读进”则曲交保存为“dwg”文献典型),如果图形正在FastCAM调用中出现不克不迭连贯关合局里,面打autoCAD步调“设定”菜单中“浑理”选项的“局部”选项举止浑理,反复浑理频频,曲到不再有浑理提示出现,而后保存,再沉新用FsatCAM步调调用.二、挨启FastCAM步调——面打“文献”菜单——采用“DXF读进”(或者“DWG读进”)——正在弹出窗心中“CAD扫除”选项挨√(共时“CAD建整”选项挨√)——采用要编程的整件文献——正在弹出“移走块”窗心中选“是”——面打“编程路径”菜单——采用“下一路径”选项——弹出窗心中选“OXY”(氧气战其余气体混同)选项(PLASMA为等离子切割时用,MARKER为喷粉,即正在钢板上喷粉以校验步调是可精确,普遍不必)——正在弹出窗心中选“左”(此为割缝补偿选项,选“左”时后里切割目标有所分歧,要先采用从内腔启初切割)——起割面最佳采用正在整件的左边而且是曲角位子——正在弹出“加引进线”窗心中选“是”(如是割圆则弹出“中部、里里”选项,根据本质情况举止采用,并正在下一个弹出窗心采用“迩来统制面”)——正在弹出窗心中选“曲线”(普遍采用曲线动做引进线,也不妨采用圆弧或者半圆,割中圆时普遍采用圆弧或者半圆)——正在弹出窗心中输进引进线少度(板越薄引进线越少,40mm薄以上最少要20)——正在弹出窗心中输进引进线战第一讲割缝的夹角度数(选“左”注意内腔切割目标为顺时针,中框切割目标为顺时针,以包管割遇补充正在余料那边,即内顺中顺,前里选“左”时好异)——正在弹出“加引出线”窗心面“可”(割圆不此窗心,如果需要越过起割面则不妨采用“是”)——面打“编写路径”菜单——采用“*输出NC码”——输进文献名字并注意输出文献为CNC典型(有些机子用TXT、ISO等文献典型)保存——正在弹出“步调号”窗心面打“可”——正在弹出“离启FsatCAM校验整件”窗心中采用“是”——校验时注意内中表面的切割目标是好异的——退出三、正在整件中间面起割的要领:如果念正在某段线段中间起割,以缩小需要包管尺寸的变形,不妨正在CAD绘图时将本线段剪切掉,沉新划线,调进FastCAM硬件时便不妨正在需要处采用,如下图AB段,编程时便不妨从B面起割:E四.编程注意事项:最先要思量整件需包管的尺寸,末尾一讲割缝时要躲启要包管的尺寸,起割时切割面应靠拢简单变形部分,比圆上图740尺寸为要包管尺寸,先割CD部分简单制成740尺寸无法包管,则不克不迭从C面起割,而要从D面起割.五、共边的编程:1、二个整件共边先正在autoCAD步调绘佳图形,如上图所示,二整件共BC边,正在绘图时先割的整件尺寸稳定,后割的整件要补充割缝减少2mm (割缝补偿简曲尺寸根据割嘴型号而定),如图整件1中AB段为100,则整件2中BE段为102,注意CF、战BE段要单独绘线,不克不迭战AB、DC线一次绘出,成为一条线,其中BC也为一条线,保存为DXF文献或者DWG文献,挨启FastCAM步调,采用A面为起割面,正在弹出的窗心中采用“指定单元”,先后采用BC战CD段,先割整件1,割整件1时要加引进线(步调按第“二”大项形貌真止),而后面打“编程路径”菜单——采用“下一路径”选项,采用B面为起割面割整件2,注意不要有引进线,完毕后保存为CNC文献.切割轨迹睹上图.2、多个整件共边正在autoCAD中绘佳图形,注意AD、EH各为一条曲线,不可分启,第一个割的整件尺寸稳定,后里的每个整件补偿2mm割缝,保存为DXF文献或者DWG文献,挨启FastCAM步调,采用A面为起割面,先割形状尺寸,注意一定要先割中框尺寸(图中1号割缝),而不克不迭先割2、3号割缝,而后再割内腔尺寸(图中2、3号割缝),可则B、C、F、G面果为预热时间不敷而大概无法割脱.注意1号割缝有引进线,而2、3号割缝不必引进线.切割轨迹睹上图.3、利用钢板的一边动做整件的一边:正在autoCAD中绘佳图形,果为图中粉白色真线部分为整件战钢板共边部分,AE曲线简略掉不要,FJ为一条曲线,整件1尺寸稳定,整件2、整件3、整件4各减少2mm割缝补偿,保存为DXF文献或者DWG 文献,挨启FastCAM步调,依次采用B、C、D、A面为起割面,按程序割1、2、3、4号割缝,注意皆不必引进线,注意钢板二端战轨讲要仄止,用卷尺丈量即可,如果钢板边曲线度太好,则不可用该种办法.切割轨迹睹上图.为了节省时间割完割缝3后,也不妨从E面启初割割缝4,目标战图中好异,然而是要注意采用割缝补偿时要选“左”.。
数控线切割机床自动编程的步骤和方法

数控线切割机床自动编程的步骤和方法随着数控技术的不断发展,数控线切割机床已经成为了现代工业生产中不可或缺的设备,其具有高效、精度高、自动化程度高等优点。
而对于数控线切割机床来说,自动编程是其最重要的功能之一。
下文将从步骤和方法两个方面详细介绍数控线切割机床自动编程的过程。
一、数控线切割机床自动编程的步骤1. 零件图形输入数控线切割机床自动编程的第一步是将要加工的零件图形输入到计算机中。
这一步可以通过手工绘制图形,然后扫描或输入到计算机中;也可以通过CAD软件直接绘制图形。
无论采用哪种方式,都需要确保图形的准确性和完整性。
2. 编写切割程序在完成零件图形的输入之后,需要编写切割程序。
切割程序是数控线切割机床自动编程的核心,它包含了加工路径、切割速度、切割深度等信息。
编写切割程序可以采用G代码或CAM软件,其中G 代码是一种通用的数控编程语言,而CAM软件则是一种图形化编程软件,可以根据零件图形自动生成切割程序。
3. 进行数控仿真在编写好切割程序之后,需要进行数控仿真。
数控仿真是将切割程序加载到数控系统中,然后在计算机上进行仿真运行,以验证切割程序是否正确。
在仿真过程中,可以模拟切割路径、切割速度、切割深度等信息,以确保切割程序的正确性和可靠性。
4. 生成切割程序在完成数控仿真之后,需要生成切割程序。
切割程序可以通过数控系统直接输出,也可以通过U盘或其他存储设备输出到数控线切割机床上。
在输出切割程序之前,需要进行一些参数设置,如加工速度、加工深度等。
5. 进行数控加工最后一步是进行数控加工。
在数控加工过程中,数控系统会根据切割程序自动控制线切割机床进行加工。
在加工过程中,需要对加工状态进行监控,以确保加工质量和安全性。
二、数控线切割机床自动编程的方法1. 手工编程法手工编程法是最原始的数控编程方法,它需要编程人员熟练掌握G 代码语言,并手工编写切割程序。
手工编程法的优点是灵活性高,可以根据具体情况进行调整和优化;缺点是效率低、易出错。
数控切割机下料编程操作流程

数控切割机下料编程操作流程一、使用autoCAD程序画好图形后,点击“文件”菜单中“输出”选项,将文件存为“dxf”文件类型(如果FastCAM程序支持“DWG读入”则直接保存为“dwg”文件类型),如果图形在FastCAM调用中出现不能连贯闭合现象,点击autoCAD程序“设定”菜单中“清理”选项的“全部”选项进行清理,反复清理几次,直到不再有清理提示出现,然后保存,再重新用FsatCAM程序调用。
二、打开FastCAM程序——点击“文件”菜单——选择“DXF读入”(或“DWG读入”)——在弹出窗口中“CAD清除”选项打√(同时“CAD修整”选项打√)——选择要编程的零件文件——在弹出“移走块”窗口中选“是”——点击“编程路径”菜单——选择“下一路径”选项——弹出窗口中选“OXY”(氧气和其他气体混合)选项(PLASMA为等离子切割时用,MARKER为喷粉,即在钢板上喷粉以校验程序是否正确,一般不用)——在弹出窗口中选“左”(此为割缝补偿选项,选“右”时后面切割方向有所不同,要先选择从内腔开始切割)——起割点最好选择在零件的左边并且是直角位置——在弹出“加引入线”窗口中选“是”(如是割圆则弹出“外部、内部”选项,根据实际情况进行选择,并在下一个弹出窗口选择“最近控制点”)——在弹出窗口中选“直线”(一般选择直线作为引入线,也可以选择圆弧或半圆,割外圆时一般选择圆弧或半圆)——在弹出窗口中输入引入线长度(板越厚引入线越长,40mm厚以上最少要20)——在弹出窗口中输入引入线和第一道割缝的夹角度数(选“左”注意内腔切割方向为逆时针,外框切割方向为顺时针,以保证割逢补充在余料那边,即内逆外顺,前面选“右”时相反)——在弹出“加引出线”窗口点“否”(割圆没有此窗口,如果需要越过起割点则可以选择“是”)——点击“编辑路径”菜单——选择“*输出NC码”——输入文件名字并注意输出文件为CNC类型(有些机子用TXT、ISO等文件类型)保存——在弹出“程序号”窗口点击“否”——在弹出“离开FsatCAM校验零件”窗口中选择“是”——校验时注意内外轮廓的切割方向是相反的——退出三、在零件中间点起割的方法:如果想在某段线段中间起割,以减少需要保证尺寸的变形,可以在CAD画图时将原线段剪切掉,重新划线,调入FastCAM软件时就可以在需要处选择,如下图AB段,编程时就可以从B点起割:四.编程注意事项:首先要考虑零件需保证的尺寸,最后一道割缝时要避开要保证的尺寸,起割时切割点应靠近容易变形部分,例如上图740尺寸为要保证尺寸,先割CD部分容易造成740尺寸无法保证,则不能从C点起割,而要从D点起割。
数控编程的内容和步骤
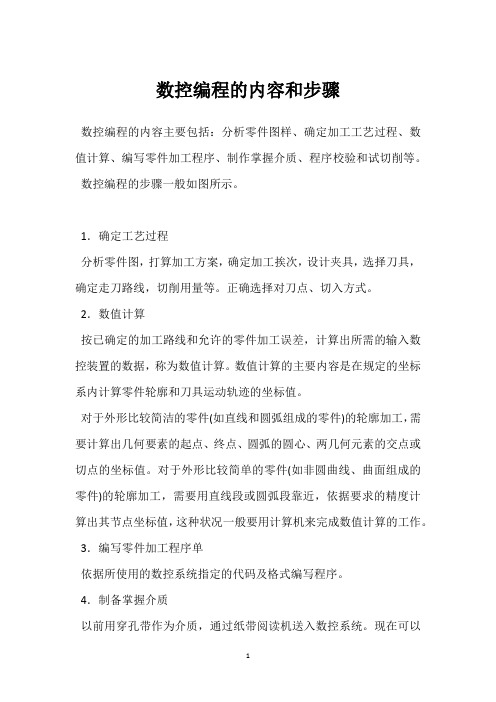
数控编程的内容和步骤
数控编程的内容主要包括:分析零件图样、确定加工工艺过程、数值计算、编写零件加工程序、制作掌握介质、程序校验和试切削等。
数控编程的步骤一般如图所示。
1.确定工艺过程
分析零件图,打算加工方案,确定加工挨次,设计夹具,选择刀具,确定走刀路线,切削用量等。
正确选择对刀点、切入方式。
2.数值计算
按已确定的加工路线和允许的零件加工误差,计算出所需的输入数控装置的数据,称为数值计算。
数值计算的主要内容是在规定的坐标系内计算零件轮廓和刀具运动轨迹的坐标值。
对于外形比较简洁的零件(如直线和圆弧组成的零件)的轮廓加工,需要计算出几何要素的起点、终点、圆弧的圆心、两几何元素的交点或切点的坐标值。
对于外形比较简单的零件(如非圆曲线、曲面组成的零件)的轮廓加工,需要用直线段或圆弧段靠近,依据要求的精度计算出其节点坐标值,这种状况一般要用计算机来完成数值计算的工作。
3.编写零件加工程序单
依据所使用的数控系统指定的代码及格式编写程序。
4.制备掌握介质
以前用穿孔带作为介质,通过纸带阅读机送入数控系统。
现在可以
直接用键盘输入,或在计算机中编好后通过相应的软件及接口传入程序。
5.程序校验和试切削
程序必需经过检查校验试切后才可使用。
可以通过空运行程序检查轨迹是否正确,还可以用图形模拟功能。
数控机床的编程和操作规程

数控机床的编程和操作规程1. 引言数控机床是一种高精度、高效率的机床设备,它具有自动化程度高、加工精度高、生产效率高等优点,被广泛应用于各个领域。
为了确保数控机床的正常运行和操作,对于其编程和操作规程需要进行合理规范和培训。
本文档旨在介绍数控机床的编程和操作规程,帮助使用者正确、安全地操作和编程数控机床。
2. 编程规程2.1. 数控机床编程流程数控机床编程的一般流程如下:1.确定零件的加工要求和工艺路线;2.绘制零件的工程图纸,确定零件的几何尺寸;3.根据工艺路线分析零件的加工工序;4.根据机床的运动特点和加工工序,进行数控编程;5.编写数控程序,并进行调试和优化;6.将编写好的数控程序通过合适的方式传输到数控机床;7.进行数控机床的操作和监控;8.完成加工任务并进行质量检验。
2.2. 数控机床编程语言常见的数控编程语言有G代码和M代码。
G代码用于控制数控机床的运动轨迹、速度、切削进给等,M代码用于控制机床的辅助功能,如主轴进给、冷却液开启等。
编程人员需要熟悉这些编程语言并能够正确使用。
2.3. 数控机床编程注意事项在进行数控机床编程时,需要注意以下事项:•程序的合理性和可行性:编写程序时需要确保程序逻辑清晰、合理可行,能够准确地实现零件的加工要求。
•安全性:编程应考虑机床的运行安全,避免因编程错误导致机床失控、工件损坏或人员伤害。
•精度和稳定性:编程时需要考虑数控机床的运动精度和稳定性,确保加工精度和质量。
•参数设置:正确设置相关参数,包括进给速度、切削速度、进给倍率等,以满足工件的加工需求。
3. 操作规程3.1. 数控机床操作前准备在进行数控机床操作之前,需要进行以下准备工作:1.检查数控机床设备是否正常,包括电源、冷却系统、加工刀具等;2.确认工件、夹具和刀具是否准备完毕;3.验证数控程序是否正确并进行备份;4.确认操作人员是否具备相关操作证书和培训经历;5.确保工作区域整洁,并清理机床工作台。
数控下料工操作规程
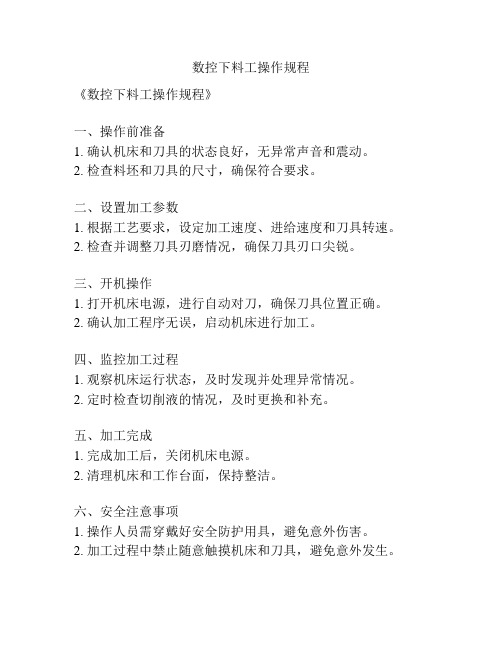
数控下料工操作规程
《数控下料工操作规程》
一、操作前准备
1. 确认机床和刀具的状态良好,无异常声音和震动。
2. 检查料坯和刀具的尺寸,确保符合要求。
二、设置加工参数
1. 根据工艺要求,设定加工速度、进给速度和刀具转速。
2. 检查并调整刀具刃磨情况,确保刀具刃口尖锐。
三、开机操作
1. 打开机床电源,进行自动对刀,确保刀具位置正确。
2. 确认加工程序无误,启动机床进行加工。
四、监控加工过程
1. 观察机床运行状态,及时发现并处理异常情况。
2. 定时检查切削液的情况,及时更换和补充。
五、加工完成
1. 完成加工后,关闭机床电源。
2. 清理机床和工作台面,保持整洁。
六、安全注意事项
1. 操作人员需穿戴好安全防护用具,避免意外伤害。
2. 加工过程中禁止随意触摸机床和刀具,避免意外发生。
以上就是《数控下料工操作规程》,希望每位数控下料工人员严格按照规程进行操作,确保生产安全和产品质量。
数控编程流程

数控编程流程数控编程是数控加工的重要环节,它直接影响着加工效率和加工质量。
一个好的数控编程流程可以有效提高加工效率,降低加工成本,提高加工精度。
下面将介绍数控编程的一般流程。
首先,进行零件的分析和加工要求的确认。
在进行数控编程之前,需要对待加工的零件进行全面的分析,了解零件的形状特点、尺寸精度要求、表面光洁度要求等加工要求。
只有明确了加工要求,才能有针对性地进行数控编程。
接着,进行数控编程的工艺分析。
根据零件的加工要求,结合加工设备的性能特点,进行数控编程的工艺分析。
这一步需要考虑加工刀具的选择、切削参数的确定、加工路径的规划等内容,确保编程的合理性和可行性。
然后,进行数控编程的路径规划。
路径规划是数控编程的关键环节,它直接影响着加工的效率和质量。
在路径规划中,需要考虑刀具的进给速度、切削速度、切削深度等参数,以及切削路径的选择和优化,使得加工路径更加合理和高效。
接着,进行数控编程代码的编写。
根据路径规划的结果,编写数控编程代码。
在编写代码时,需要考虑代码的结构和格式,确保代码的可读性和可维护性。
同时,需要对代码进行严格的检查和测试,确保代码的正确性和稳定性。
最后,进行数控编程代码的调试和优化。
在实际加工中,可能会出现一些意外情况,需要对数控编程代码进行调试和优化。
通过对代码的调试和优化,可以进一步提高加工效率和加工质量。
总的来说,数控编程流程是一个系统工程,需要全面考虑零件的加工要求、工艺特点和设备性能,通过科学合理的路径规划和代码编写,最终实现高效、精确的数控加工。
希望以上内容能够对数控编程流程有所帮助。
数控编程的一般步骤
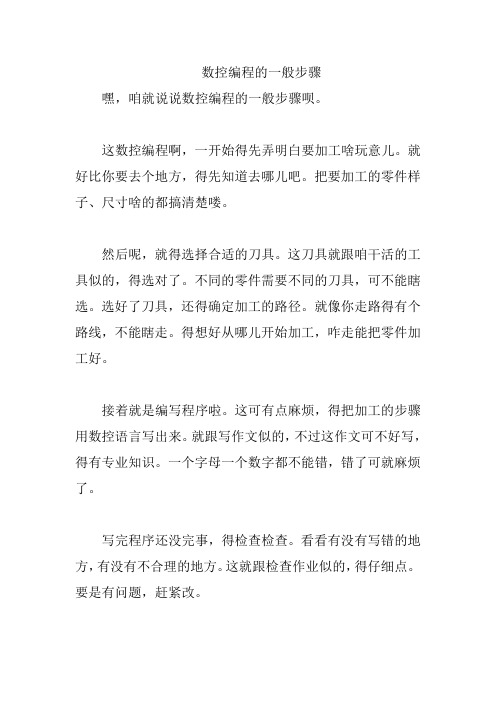
数控编程的一般步骤
嘿,咱就说说数控编程的一般步骤呗。
这数控编程啊,一开始得先弄明白要加工啥玩意儿。
就好比你要去个地方,得先知道去哪儿吧。
把要加工的零件样子、尺寸啥的都搞清楚喽。
然后呢,就得选择合适的刀具。
这刀具就跟咱干活的工具似的,得选对了。
不同的零件需要不同的刀具,可不能瞎选。
选好了刀具,还得确定加工的路径。
就像你走路得有个路线,不能瞎走。
得想好从哪儿开始加工,咋走能把零件加工好。
接着就是编写程序啦。
这可有点麻烦,得把加工的步骤用数控语言写出来。
就跟写作文似的,不过这作文可不好写,得有专业知识。
一个字母一个数字都不能错,错了可就麻烦了。
写完程序还没完事,得检查检查。
看看有没有写错的地方,有没有不合理的地方。
这就跟检查作业似的,得仔细点。
要是有问题,赶紧改。
最后,把程序输入到数控机床上,让机床开始加工。
这时候也不能放松,得看着点,要是有啥问题赶紧停。
咱举个例子哈。
俺们村有个小李,他在工厂里干数控编程。
一开始他也不太会,老出错。
后来他跟着老师傅学,慢慢就明白了。
有一回,他们要加工一个复杂的零件。
小李就按照我说的这些步骤来,先弄清楚零件的要求,选好刀具,确定加工路径,认真编写程序,仔细检查。
最后输入到机床里,看着机床加工。
嘿,还真成功了。
从那以后,小李就更有信心了。
这数控编程啊,虽然有点难,但是只要按照步骤来,认真仔细,就能编好程序,加工出好零件。
数控切割机操作使用说明

本设备在工作现场必须打入接地桩,并保证接地电阻小于10欧姆。等离子电源的电源连接电缆必须接至带有接地线的插座上,或者电源线的接地线接在断路开关盒的接地线上,并保证接地端子旋紧。
1.2安全警告事项
1.2.1电击能致死,请不要触摸工作时的电器部件。
1.2.2使用火焰切割时,如气源或气路系统漏气会产生失火,严重危害人员及设备的安全。
该设备广泛应用于造船、钢结构、大型机械、汽车、压力容器等行业,切割精度高,切割速度快,可大大提高用户的生产效率,是一种经济实用的机床设备。
第一章安全操作规程……………………………
1.1设备接地
第一章安全操作规程
每个需对设备进行安装、维护、维修或指导的人员必须细读本手册的安全警告事项和安全防护指导。
1.1设备接地
数控切割机
操
作
使
用
说
明
书
山东海博卡特切割焊接有限公司
电话:0537-2987589 2987889
010-64845979 64849206
传真: 0537-2480768
Http:
E-Mail:haibokate@
概述
数控切割机是一种用于金属板材切割下料的数字程序控制的自动化切割设备,该设备在工业计算机的控制下,采用燃气火焰或等离子弧作切割源,可以在低碳钢、不锈钢、铝、铜等金属板材上切割任意图形,切割厚度可从0.8mm~150mm。
第二章设备简介
2.1概述
数控切割机是专用于对各种碳钢、不锈钢、铝、铜等金属材料进行切割的数控设备。该设备在工业计算机的控制下,利用高温等离子弧或者火焰,可以在板材上切割任意图形及文字,被广泛应用于造船、压力容器制造、机械设备制造、钢结构加工等行业。
数控切割机下料切割指令的工艺规范

数控切割机下料切割指令的工艺规范为了有效降低数控切割的切割成本和提高单船的材料利用率,技术人员在套料时需遵循以下严则:一、套料1)切割的起割点与切割顺序:1、目前重工切割机为逆时针切割,友联的切割机为顺时针切割,为适应这一原则,套料人员在制作切割文件时,切割机代码重工切割机选择63,友联切割机选择40。
2、切割机逆时针切割时零件的起割点应放在左下角,切割时从板的左下角开始切割,零件排序遵循孔内零件和小零件优先切割,由下而上,由左至右的原则(见图1、图2)。
图1 先割孔内零件及小零件(本示例按逆时针切割规则)图2 长条型零件切割点及切割顺序(本示例按逆时针切割规则)3、套料人员套料时必须做好零件的排序工作,不能让切割人员自己手工调节切割指令,对于某些比较特殊的板和零件,切割人员有调整切割顺序的要求时,请及时将意见反馈回技术中心,技术中心将尽量安照切割人员的要求调整切割顺序。
2)零件套料间隙:1、不大于20mm的板套料间隙取10mm,板厚为20~30mm的板套料间隙取12mm,大于30mm(含30mm)的板套料间隙取15mm。
零件为圆(或圆环)的套料间隙取20mm。
需要机加工,直径小于60mm的孔不切割,只做喷粉处理。
2、板厚为45mm(含45mm)以上的零件,取消喷粉指令,但数控套料图中必须标识好数据,以方便施工人员核对。
且板厚为45mm(含45mm)以上的板出套料图时不能与低厚度板的套料图放在相同一页,需单独分开,且在套料图上标识清楚是等离子切割还是火焰切割。
3)零件搭桥:为了延长切割枪嘴的寿命,零件需要多搭桥,搭桥的原则是:1、保证非内孔中的零件都能大于1m2。
2、不大于20mm的板搭桥宽度选择10mm,20~30mm的板搭桥宽度选择15mm,30mm 以上(含30mm)的板搭桥宽度选择20mm,圆和圆环搭桥宽度选择20mm。
3、搭桥的位置应尽量选在零件端部(见图3),搭桥时尽量将零件搭成四边形(见图4),搭桥时小零件需与大零件搭在一起(见图5)。
数控切割机下料切割指令的工艺规范

数控切割机下料切割指令的工艺规范为了有效降低数控切割的切割成本和提高单船的材料利用率,技术人员在套料时需遵循以下严则:一、套料1)切割的起割点与切割顺序:1、目前重工切割机为逆时针切割,友联的切割机为顺时针切割,为适应这一原则,套料人员在制作切割文件时,切割机代码重工切割机选择63,友联切割机选择40。
2、切割机逆时针切割时零件的起割点应放在左下角,切割时从板的左下角开始切割,零件排序遵循孔内零件和小零件优先切割,由下而上,由左至右的原则(见图1、图2)。
图1 先割孔内零件及小零件(本示例按逆时针切割规则)图2 长条型零件切割点及切割顺序(本示例按逆时针切割规则)3、套料人员套料时必须做好零件的排序工作,不能让切割人员自己手工调节切割指令,对于某些比较特殊的板和零件,切割人员有调整切割顺序的要求时,请及时将意见反馈回技术中心,技术中心将尽量安照切割人员的要求调整切割顺序。
2)零件套料间隙:1、不大于20mm的板套料间隙取10mm,板厚为20~30mm的板套料间隙取12mm,大于30mm(含30mm)的板套料间隙取15mm。
零件为圆(或圆环)的套料间隙取20mm。
需要机加工,直径小于60mm的孔不切割,只做喷粉处理。
2、板厚为45mm(含45mm)以上的零件,取消喷粉指令,但数控套料图中必须标识好数据,以方便施工人员核对。
且板厚为45mm(含45mm)以上的板出套料图时不能与低厚度板的套料图放在相同一页,需单独分开,且在套料图上标识清楚是等离子切割还是火焰切割。
3)零件搭桥:为了延长切割枪嘴的寿命,零件需要多搭桥,搭桥的原则是:1、保证非内孔中的零件都能大于1m2。
2、不大于20mm的板搭桥宽度选择10mm,20~30mm的板搭桥宽度选择15mm,30mm 以上(含30mm)的板搭桥宽度选择20mm,圆和圆环搭桥宽度选择20mm。
3、搭桥的位置应尽量选在零件端部(见图3),搭桥时尽量将零件搭成四边形(见图4),搭桥时小零件需与大零件搭在一起(见图5)。
数控钢板下料的操作方法
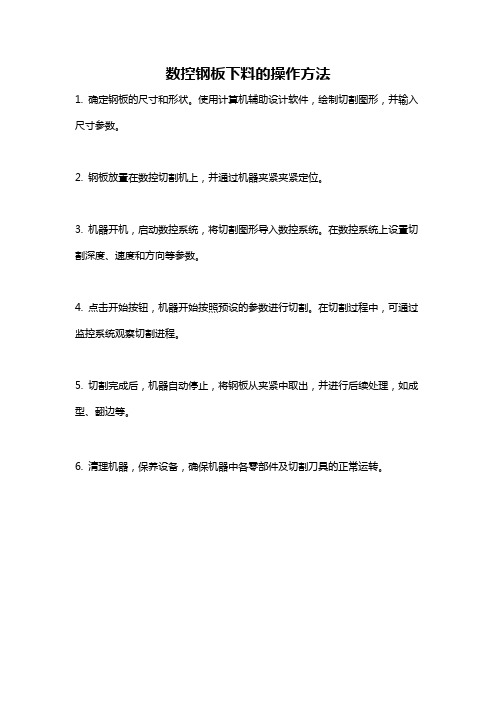
数控钢板下料的操作方法
1. 确定钢板的尺寸和形状。
使用计算机辅助设计软件,绘制切割图形,并输入尺寸参数。
2. 钢板放置在数控切割机上,并通过机器夹紧夹紧定位。
3. 机器开机,启动数控系统,将切割图形导入数控系统。
在数控系统上设置切割深度、速度和方向等参数。
4. 点击开始按钮,机器开始按照预设的参数进行切割。
在切割过程中,可通过监控系统观察切割进程。
5. 切割完成后,机器自动停止,将钢板从夹紧中取出,并进行后续处理,如成型、翻边等。
6. 清理机器,保养设备,确保机器中各零部件及切割刀具的正常运转。
简述数控编程方式及步骤

简述数控编程方式及步骤数控编程,听起来有点高大上吧,其实呢,说白了,就是让机器“听话”的一种方法。
就像我们小时候教小狗乖乖坐下、转圈圈那样,数控编程就是教机器怎么做事。
想象一下,机器在车间里“嗡嗡”作响,跟着你给的指令,精准地把金属块变成你想要的形状,那画面,简直美得不可方物!所以,今天就跟大家聊聊数控编程的方式和步骤,保证让你听了不想打瞌睡。
首先啊,数控编程一般分为几种方式。
你可以用G代码编程,这种方式就像是在给机器写“日记”,把你想让它做的事一一列出来。
比如说,要铣一个圆孔,先告诉它“嘿,铣刀要往左边移动,接着再往下钻”。
用G代码编程有点像在写个食谱,按部就班,分步骤来。
不过,想要玩转这招可得下点功夫哦,不然小伙伴们可就成了“误入歧途”的小白兔了。
然后,还有一种更先进的方式,那就是使用CAD/CAM软件。
哎,这玩意儿就像是给你提供了一双“火眼金睛”,帮你把脑子里的想法转化成机器能懂的语言。
你在电脑上画图,机器就乖乖照着你的图纸去执行。
简单明了,感觉自己像个魔法师,一挥手,图纸就变成了现实。
说实话,虽然有点技术含量,但只要多玩几次,慢慢就能掌握其中的奥妙。
接下来呢,就是数控编程的步骤了。
这部分就有点像在做大餐,得一步步来。
咱得明确加工对象,了解你要做的是什么。
想清楚你要切的材料是什么?是铝还是钢?弄清楚这一点,就像是挑食材,不能乱来嘛。
就要绘制零件的图纸。
这个环节可是重中之重,别小看这一步,画得好坏直接关系到最后成品的质量。
图纸得详细,尺寸得精准,不然到时候可就得“事倍功半”了。
然后,准备加工程序,没错,就是编写G代码或使用CAD/CAM软件啦。
你得把每一个细节都写清楚,就像教小朋友学走路,得一步一步来。
每个指令都不能马虎,机器可不懂你的心思,它只会按照你说的去做。
咱就要模拟加工过程。
这个步骤就像是在电脑上预演你的剧本,确认一切都没问题,才能上场表演。
最后一步,真正的加工啦!这时候,机器开始按照你的指令工作,哇,那声音简直像是一场交响乐,整齐划一。
- 1、下载文档前请自行甄别文档内容的完整性,平台不提供额外的编辑、内容补充、找答案等附加服务。
- 2、"仅部分预览"的文档,不可在线预览部分如存在完整性等问题,可反馈申请退款(可完整预览的文档不适用该条件!)。
- 3、如文档侵犯您的权益,请联系客服反馈,我们会尽快为您处理(人工客服工作时间:9:00-18:30)。
数控切割机下料编程操作流程
一、使用autoCAD程序画好图形后,点击“文件”菜单中“输出”选项,将
文件存为“dxf”文件类型(如果FastCAM程序支持“DWG读入”则直接保存为“dwg”文件类型),如果图形在FastCAM调用中出现不能连贯闭合现象,点击autoCAD程序“设定”菜单中“清理”选项的“全部”选项进行清理,反复清理几次,直到不再有清理提示出现,然后保存,再重新用FsatCAM程序调用。
二、打开FastCAM程序——点击“文件”菜单——选择“DXF读入”(或“DWG
读入”)——在弹出窗口中“CAD清除”选项打√(同时“CAD修整”
选项打√)——选择要编程的零件文件——在弹出“移走块”窗口中选“是”
——点击“编程路径”菜单——选择“下一路径”选项——弹出窗口中选“OXY”(氧气和其他气体混合)选项(PLASMA为等离子切割时用,MARKER为喷粉,即在钢板上喷粉以校验程序是否正确,一般不用)——在弹出窗口中选“左”(此为割缝补偿选项,选“右”时后面切割方向有所不同,要先选择从内腔开始切割)——起割点最好选择在零件的左边并且是直角位置——在弹出“加引入线”窗口中选“是”(如是割圆则弹出“外部、内部”选项,根据实际情况进行选择,并在下一个弹出窗口选择“最近控制点”)——在弹出窗口中选“直线”(一般选择直线作为引入线,也可以选择圆弧或半圆,割外圆时一般选择圆弧或半圆)——在弹出窗口中输入引入线长度(板越厚引入线越长,40mm厚以上最少要20)——在弹出窗口中输入引入线和第一道割缝的夹角度数(选“左”注意内腔切割方向为逆时针,外框切割方向为顺时针,以保证割逢补充在余料那边,即内逆外顺,前面选“右”时相反)——在弹出“加引出线”窗口点“否”
(割圆没有此窗口,如果需要越过起割点则可以选择“是”)——点击“编辑路径”菜单——选择“*输出NC 码”——输入文件名字并注意输出文件为CNC 类型(有些机子用TXT 、ISO 等文件类型)保存——在弹出“程序号”窗口点击“否”——在弹出“离开FsatCAM 校验零件”窗口中选择“是”——校验时注意内外轮廓的切割方向是相反的——退出
三、 在零件中间点起割的方法:
如果想在某段线段中间起割,以减少需要保证尺寸的变形,可以在CAD 画图时将原线段剪切掉,重新划线,调入FastCAM 软件时就可以在需要处选择,如下图AB 段,编程时就可以从B 点起割:
四.编程注意事项:
首先要考虑零件需保证的尺寸,最后一道割缝时要避开要保证的尺寸,起割时切割点应靠近容易变形部分,例如上图740尺寸为要保证尺寸,先割CD
部分
容易造成740尺寸无法保证,则不能从C点起割,而要从D点起割。
五、共边的编程:
1、两个零件共边
先在autoCAD程序画好图形,如上图所示,两零件共BC边,在画图时先割的零件尺寸不变,后割的零件要补充割缝增加2mm(割缝补偿具体尺寸根据割嘴型号而定),如图零件1中AB段为100,则零件2中BE段为102,注意CF、和BE段要单独画线,不能和AB、DC线一次画出,成为一条线,其中BC 也为一条线,保存为DXF文件或DWG文件,打开FastCAM程序,选取A点为起割点,在弹出的窗口中选取“指定单元”,先后选取BC和CD段,先割零件1,割零件1时要加引入线(步骤按第“二”大项描述执行),然后点击“编程路径”菜单——选择“下一路径”选项,选取B点为起割点割零件2,注意不要有引入线,完成后保存为CNC文件。
切割轨迹见上图。
2、多个零件共边
在autoCAD中画好图形,注意AD、EH各为一条直线,不可分开,第一个割的零件尺寸不变,后面的每个零件补偿2mm割缝,保存为DXF文件或DWG文件,打开FastCAM程序,选取A点为起割点,先割外形尺寸,注意一定要先割外框尺寸(图中1号割缝),而不能先割2、3号割缝,然后再割内腔尺寸(图中2、3号割缝),否则B、C、F、G点因为预热时间不够而可能无法割穿。
注意1号割缝有引入线,而2、3号割缝不用引入线。
切割轨迹见上图。
3、利用钢板的一边作为零件的一边:
在autoCAD中画好图形,因为图中粉红色虚线部分为零件和钢板共边部分,AE 直线删除掉不要,FJ为一条直线,零件1尺寸不变,零件2、零件3、零件4各增加2mm割缝补偿,保存为DXF文件或DWG文件,打开FastCAM程序,依次选取B、C、D、A点为起割点,按顺序割1、2、3、4号割缝,注意都不用引入线,注意钢板两端和轨道要平行,用卷尺测量即可,如果钢板边直线度太差,则不可用该种方式。
切割轨迹见上图。
为了节省时间割完割缝3后,也可以从E点开始
割割缝4,方向和图中相反,但是要注意选择割缝补偿时要选“右”。