120t区域精炼工艺3-16
炼钢工艺简介及能源介质消耗

参数 300吨 13% 4个 1.4-1.7Nm3·t-1·min-1 8个 0.04-0.3Nm3·t-1·min-1 8-10min
产品一流 管理一流 环境一流 效益一流
三、工艺设备简介及能源消耗
2、炼钢作业区-转炉脱磷
加3废钢
兑铁
降枪开氧 点火
吹炼
加辅料造 渣
倒渣
溅渣护炉
合金化
出钢
提枪闭氧
过程能源消耗: 1)转炉倾动耗电,氧枪、副枪升降耗电; 2)氧枪吹氧、吹氮,底吹吹氮、吹氩,氧枪孔、副枪孔
三、工艺设备简介及能源消耗
5、精炼作业区-钢包
主要参数
项目
参数
钢包
39个
烤包器
8个
倾翻
4个
钢包烘烤时间
8-44h
渣罐烘烤时间
2h
产品一流 管理一流 环境一流 效益一流
精炼作业区能源介质情况(CAS+RH+LF+钢包):
项目 耗电 氧气 氮气 氩气 煤气消耗 煤气回收 蒸汽消耗 蒸汽回收
单位 kwh/t m3/t m3/t m3/t m3/t m3/t kg/t kg/t
提升能力
30吨
பைடு நூலகம்
提升行程
7000mm
提升速度
7.0m/min
停止精度
±30mm
正常100~120rpm,新搅拌头
搅拌头的转速
时最大150rpm
类型
绞盘式提升和搅拌设备
炼铁—炼钢界面采用了铁水罐一罐到底 技术。铁水脱后硫≤0.002%比例达到98% ,采用一键式脱硫。
产品一流 管理一流 环境一流 效益一流
消耗的主要能源:电
拥有两座泵站,主要设备 有: 2座旋流井,6台中速罐、 20台高速罐、4台稀土磁盘、2 套高效澄清器、2套压滤机设 备及冷却塔、空冷器、供水泵 等,包括14个循环水系统,主 要为全厂各工序提冷却水和循 环水质处理。
与永锋螺纹钢对标分析报告

与永锋螺纹钢对标分析报告莱钢螺纹钢与永锋合金成本差距较大,主要是因为轧制工艺不同造成的成分设计差别较大,具体如下:一、成分设计原因造成的合金成本差距对比莱钢及永锋螺纹钢成分设计标准,永锋在钢种锰及钒成分上与莱钢差值较大,是影响莱钢与永锋螺纹钢合金对标结果的主要因素。
1.莱钢1月份主要冶炼螺纹钢种有HRB400-2/HRB400E-2、HRB400-3/HRB400E-3、HRB400E-2Cr、HRB500E-2几种,其锰、钒成分设计标准及产量比例如下:2.永锋60t转炉1月份主要冶炼螺纹钢种有HRB400①、HRB400③、HRB400E②、500B-1,其锰、钒成分设计标准及产量比例如下:3.永锋120t转炉1月份主要冶炼螺纹钢种有HRB400①、HRB400③、HRB400④、HRB400E①、HRB400E②、HRB400E③、HRB400E⑤、HRB500①、HRB500③、HRB500E④、500B-1、HPB300①、HPB300②、Q235,其锰、钒成分设计标准及产量比例如下:4.按照永锋60t及120t转炉的产量比例及各自加权平均锰、钒成分,计算出永锋1月份新老两区加权锰、钒成分如下:5.计算莱钢与永锋锰、钒成分偏差导致的成本值,具体如下:综合上述,因成分设计标准及品种结构不同,莱钢螺纹钢合金成本比永锋高99.45982元/吨。
二、永锋新区120t转炉精炼工艺生产螺纹钢的优缺点(一)优点1.减轻转炉炉体维护压力。
由于采取炉炉进精炼处理,转炉放钢温度较低,一般控制在1620-1630℃之间,比我厂螺纹钢放钢温度1650-1660℃低30℃左右。
由于放钢温度低,转炉终点钢水氧化性相对较弱,合金收得率较高,钢水及炉渣对炉衬侵蚀也较轻。
2.采取进精炼处理工艺后,转炉可以按下限值配锰成分(若钢种锰成分下限为0.70%,则转炉就按0.70%目标配锰成分),成分低于下限值炉次通过在精炼炉加合金粉面进行微调。
Q195L钢包渣不改质不钙处理工艺试验阶段总结

Q195L钢包渣不改质不钙处理工艺试验阶段总结按照公司2013年4月份板坯Q195L直供工艺开发会议的要求,第一炼钢厂结合技术部对现有供冷轧的热轧板卷按照用途细分工艺流程,在满足下游用户要求的基础上,实现工序成本的进一步优化。
第一炼钢厂于5月份开始在120t板坯区域对Q195L进行炉后吹氩站简易精炼后Ca处理直供连铸机浇注,同时对钢包顶渣不改质、钢水吹氩站搬出前不进行钙处理的直供工艺进行实验开发。
一、工艺实施方案描述1、工艺流程铁水扒渣→转炉→板坯连铸(开浇炉次可采用经LF精炼工艺)2、化学成分3、入炉铁水S<0.030%、铁块S<0.050%4、过程温度控制:5、钢包脱氧:钢包到吹氩站目标Als>0.020%或钢包目标氧含量<6ppm(可根据需要定氧)。
6、软吹氩时间≥8min后搬出上机;7、连铸机单浇次计划浇注时间10-12h,目标浇注时间12-14h,浇铸过程使用圆形浸入水口,单浇次允许换浸入水口2次;二、实验过程二、实施效果及评价9月2日实验过程已经实现换一次浸入水口浇铸Q195L钢水16罐,浇铸10h12min(随后按照现有直供工艺连浇)。
浇注过程钢水可浇性与经RH处理钢水的可浇性相近,浇注过程存在缓慢连续的絮流,结晶器钢水液位波动基本稳定在±5mm内,与其它钢厂直供或CAS处理钢水可浇性基本相同。
计划进一步实验以便稳定钢水浇注状态。
三、成本比较四、存在问题1、该工艺转炉炉后吹氩站不造白渣,不具备钢水炉后脱S条件,为控制钢水S含量,需严格控制铁水、冷料的S含量,同时提高及稳定转炉吹炼过程脱S率,以便稳定成品材的有害元素S含量;2、目前浇铸状态应不稳定,应需对钢水可浇性及工艺控制进行进一步的跟踪规范;3、热轧板卷的表面质量及性能需进一步细致跟踪。
五、下一步工作计划1.继续进行全浇次生产试验,以便进一步优化工艺及操作;2.结合技术部对该工艺的产品质量进行进一步细致跟踪,以便确定产品最终的用途。
炼钢-精炼工艺介绍
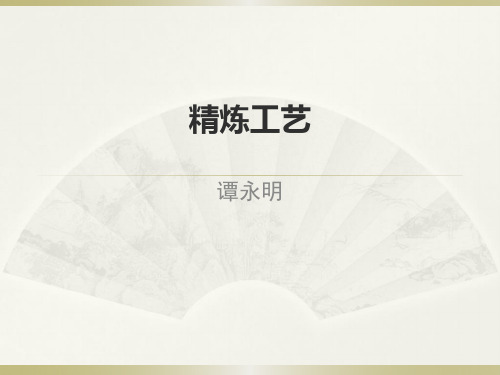
CAS底吹排渣工艺
4、CAS工艺
排渣效果(裸露钢液面面积)主要与渣层厚度、渣粘度和底吹氩 能力等有关。在底吹排渣过程中,随着底吹氩气流量增大,排渣 面积增大,但当底吹氩气流量达到一定值后,进一步增大底吹氩 气流量,其排渣效果变化不大。应选择较佳的底吹氩排渣流量, 防止钢水散热过多和减少氩气消耗量。
1.3增碳剂 袋装20Kg/包,要求固定碳含量≥94%,S≤0.5%,H2O≤0.5% 粒度3-8mm。
1、精炼过程用原料
1.4常用气体 1.4.1惰性气体 氮气、氩气等为冶金用惰性气体。主要用于二次钢水的保
护与隔离,以及对钢水精炼时的搅拌、吸气、去杂质等。 对人体的危害表现为窒息性伤害,浓度达到25g/m3时有危 险。 要求:干燥、干净、无杂质、水分<1%、纯度≥99.9%、 氧气<6PPm、氮气<20PPm、氧气+氮气≯20PPm 1.5钢包炉用材料 1.5.1冶金石灰: 采用转炉炼钢用活性石灰,保存期不得大于10天。
Si
74.0~80.0 72.0~80.0
化学成份,%
Mn
Cr
P
不大于
0.4
0.3
0.035
0.5
0.5
0.04
Si-Ca-Ba包芯线:
Si%
Ca% Ba% P%
≥50
≥14
≥14
≤0.02
Si-Ca包芯线:
Si%
Ca%
≥50
≥28
Al线:
P% ≤0.02
S% ≤0.03
S% ≤0.03
1、精炼过程用原料
二级 一级 特级
CaO% ≥85.0 ≥90.0 ≥92.0
SiO2% ≤3.5 ≤2.5 ≤1.5
炉外精炼-RH

炉外精炼的基本原理:(1)吹氩的基本原理:氩气是一种惰性气体,从钢包底部吹入钢液中,形成大量小气泡,其气泡对钢液中的有害气体来说,相当于一个真空室,使钢中[H][N]进入气泡,使其含量降低,并可进一步除去钢中的[O],同时,氩气气泡在钢液中上沲而引起钢液强烈搅拌,提供了气相成核和夹杂物颗粒碰撞的机会,有利于气体和夹杂物的排除,并使钢液的温度和成分均匀。
(2)真空脱气的原理:钢中气体的溶解度与金属液上该气体分压的平方根成正比,只要降低该气体的分压力,则溶解在钢液中气体的含量随着降低。
(3)LF炉脱氧和脱硫的原理:炉外精炼的任务:炉外精炼是把由炼钢炉初炼的钢水倒入钢包或专用容器内进一步精炼的一种方法,即把一步炼钢法变为二步炼钢法。
炉外精炼可以完成下列任务:(1)降低钢中的硫、氧、氢、氮和非金属夹杂物含量,改变夹杂物形态,以提高钢的纯净度,改善钢的机械性能;(2)深脱碳,在特定条件下把碳降到极低含量,满足低碳和超低碳钢的要求;(3)微调合金成分,将成分控制在很窄的范围内,并使其分布均匀,降低合金消耗,提高合金元素收得率;将钢水温度调整到浇铸所需要的范围内,减少包内钢水的温度梯度。
RH真空循环脱气法LF具有加热和搅拌功能的钢包精炼法处理过程:用钢包车将钢包送入处理位,使真空室下降或使钢包提升,以便使吸嘴浸入钢包内的钢液以下500mm。
然后启动真空泵。
由于真空室内压力下降,钢包内钢水被吸入真空室中。
由于吸嘴中的一个喷入氩气,另一个没有,钢水便开始反复循环。
这时就可采取各种处理措施,例如脱气、吹氧、化学成分及温度调整等。
处理结束时使系统破真空。
随后退出吸嘴,将钢包送至后处理位置或交接位置。
冶金效果:在短时间就可达到较低的碳(<15ppm)、氢(<1.5ppm)、氧含量(<40ppm);仅有略微的温度损失;不用采取专门的渣对策;可准确调整化学成分,Al,Si等合金收得率在90~97%。
汽车钢板以及电工钢等是RH钢生产的典型产品。
26 首钢贵阳特殊钢公司电炉炼钢工程工艺设计

首钢贵阳特殊钢公司电炉炼钢工程工艺设计武国平宋宇(北京首钢国际工程技术有限公司, 北京,100043)摘要本文介绍了首钢贵阳特殊钢公司电炉炼钢厂的工艺流程和设备配置,分析了各电炉厂的布置形式,阐述了同跨布置和多跨并列布置各自的优缺点,并简要介绍了首钢贵阳特殊钢公司电炉炼钢工程工艺设计的特点。
立式连铸机、透气砖拆除机构、连铸机整体除尘等设备均为国内首例,粉尘排放指标低于20mg/ Nm3,各项工序能耗指标均低于国家标准。
关键词电炉工艺设计先进设备Process Design of EAF Project of Shougang Guiyang Special SteelCompanyWu Guoping, Song Yu(Beijing shougang international engineering technology co.ltd, beijing, 100043)Abstract An introduce of the process flow and equipments of shougang guiyang special steel company EAF plant is made out in this paper. Besides, the layout forms of several EAF plants are analyzed. The effects and defects of single span layout and appositional multi-span layout are illuminated. The characteristics of the process design of the shougang guiyang special steel company EAF project are given out briefly as also. The equipments, such as vertical CCM and vent brick removal machine, are the domestic first cases. Dust emission index is lower than 20mg/ Nm3. In the meanwhile, power consumption index of working procedures are under the level of national standards.Key Words EAF Process Design Advanced Equipments前言首钢贵阳特殊钢有限责任公司(简称贵钢),地处贵州省会城市贵阳城市中心。
120t转炉-LF—CC短流程20CrMnTiH窄淬透性带生产工艺

第 1期 ( 总第 15期 ) 4
2 3 晶粒度 等级 .
采 用 步 进 式 加 热 炉 ,预 热 段 温 度 控 制 在 30℃ , 0 加热段 温 度 控 制 在 13 0℃ 以下 ,均 热 段 0 温 度 控 制 在 1 5 - 0 o 开 轧 温 度 不 低 于 2 0 4 1 C,
对 2CMn i 轮钢取 样做金 相见 图 3 0 r TH齿 ,由图
可 见 组 织 全 部 正 常 ( + P) 统 计 10 炉 F 。 0
2 CMn i 0 r TH齿轮钢 晶粒 度 ,晶粒 度等 级稳 定 在 7 5 .
莱钢 科技
? ’ ‘ 。 …‘…‘…‘ …‘…。…‘…‘ 。 。 ?
21 0 0年 2月
÷实践与创新 ÷
; . . . . . . 二 ….….….….….….….
10 转 炉 一L t 2 F—C C短 流 程 2 Mn i 0 r TH C
窄 淬 透 性 带 生产 工 艺
放 钢碳 0 0 % ~0 1 % ,严 格 控 制 转 炉 下 渣 ,采 .8 .3
用刺状 挡 渣 球 挡 渣 ,钢 包 渣 层 厚 度 要 求 控 制 在 7 0 m 以下 。脱氧 采用 铝锰 钛 铁 ,能 有 效脱 除钢 水 中 m
的氧 ,并且 对炉 渣也 有一 定 的脱氧 能力 ,放 钢后 期
小型车 间 。该生 产线 自投 产 以来 ,通过调 整工 艺措
施 ,形 成 了 2 CMn i 0 r TH齿 轮钢 窄淬透 性 生产工 艺 。
1 2 CMn i 0 r TH齿轮钢生产工艺
2 CMn i 0 r TH齿轮 钢 生 产 工 艺 为 :10 t 底 复 2 顶
炼钢厂基本工艺流程图
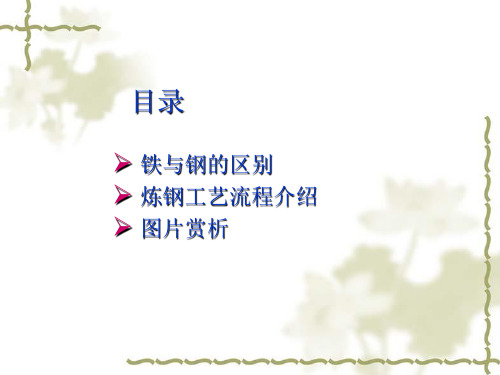
➢ 铁与钢的区别 ➢ 炼钢工艺流程介绍 ➢ 图片赏析
铁和钢的区别
➢ 化学成分
铁:C 4.1~4.3%,Si 0.25~0.50%, Mn 0.2~0.5%, P ≤0.12%,S ≤0.035%
钢:C <2.1% P ≤0.045%,S ≤0.050% 例:普通碳素结构钢Q195
C 0.06~0.12%,Si 0.12~0.30%, Mn 0.25~0.50%, P≤ 0.045%, S0.050%
铁水[S]: 0.035→≤0.010%
• 3:搅拌形式:KR、喷粉 • 4:目前较为先进的是铁水‘三脱’,目的是解放
转炉,提高钢水纯净度
铁水准备
N2
Mg粒
脱硫渣
铁水 铁水脱硫示意图
三、转炉
• 1:功能:降碳、提温、去S,P、脱H,O,N
去夹杂物、合金化
• 2:顶底复吹,顶枪吹氧,底吹Ar,N2,O2 • 3: 渣料:石灰、白云石、铁皮、萤石等,岀
• 1. 浇铸温度控制 • 2. 钢水成份控制 • 3. 拉速控制 • 4. 冷却控制 • 5. 液面控制 • 6. 连铸新技术、新措施
1. 浇注温度控制
连铸钢水工艺要求是,保证浇铸性能的前提下具有 较低的过热度。出钢温度是控制连铸浇铸温度的 基础与保证,提高出钢温度的命中率。钢水保温 的方法有以下几种办法:
• 2:加入石灰、预熔渣、萤石、铝粉、矾土(主要
成分:AL2O3)、电石造渣
• 3:贵重及收的率不稳定的合金元素尽量在LF炉
配,例如:Nb、V、Ni、Ti、Al、B等
• 4:缺点:增碳、增硅、回磷、增氮
电极准备 设备准备 通电准备 冷却水准备 合金及辅料准备 液压准备
测温取样 供电操作 造渣操作 吹氩操作 合金调整 温度调整
钢铁脱硫之KR定向快速脱硫技术的应用

钢铁脱硫之KR定向快速脱硫技术的应用关键词:脱硫技术脱硫剂脱硫效率山东钢铁股份有限公司济南分公司炼钢厂120t转炉区域配备3座KR 铁水预处理,3座120t的顶底复吹转炉、配有副枪,2台单流直弧型板坯连铸机,2台单流直弧型中薄板连铸机,精炼区配有CAS站、3座LF精炼炉、1座VD精炼炉、1座RH精炼炉等,目前120t转炉区域的工艺装备水平已具备了交通运输、石油化工、重型机械、海洋工程、核电军工等行业用钢的冶炼基础条件。
随着对产品质量要求的不断提升以及降本增效工作不断深入推进,济钢炼钢厂铁水预处理如何在现有条件下,更有效地既满足炼钢工业的快节奏高品质要求,又要满足降成本的需要,发挥更重要更关键的作用,成为一项新的课题。
1、KR定向快速脱硫技术的应用1.1倒罐坑测温取样技术1.1.1提高KR铁水成分预知率铁水采样测温地点由操作室改为倒罐坑,并利用倒罐坑附近风动送样装置送HM样,节省了大量时间,保证在铁水处理前能够按需备料。
如图1所示,采用倒罐坑取样,可节省吊运进站倾翻的环节,约可节省4min的时间。
通过4min的时间,可有效提高成分预知率至98%。
根据铁水成分备料,避免了二次投料。
图1优化取样流程1.1.2优化预报铁水成分为有效利用炼铁铁水成分,对单罐、单包铁水成分由倒罐站负责直接报KR岗位和调度,对不同罐次混包的铁水,根据不同罐次出铁量和铁水硫含量进行计算,第一时间传递至KR岗位。
有效预报铁水成分信息,为KR处理提供指导。
如表1所示,从9月1日当天数据中可以看出,炼铁化验信息与炼钢化验信息差异很小,有很大的参考价值。
表1优化预报铁水成分1.2强流化高压送投料技术受厂房工艺布局的影响,料仓位置距离KR处理位较远,且脱硫剂输送管道不能取直线进入,导致脱硫剂的输送过程中易发生堵料,投料受影响,脱硫效率无法保证。
经过技术改进,在由给料泵至投料管中间的输送管道,每隔5m增加助吹阀1个,提高压送效果,增加运输能力,也解决了堵料的痼疾。
(完整word)不锈钢AOD精炼工艺的应用和发展
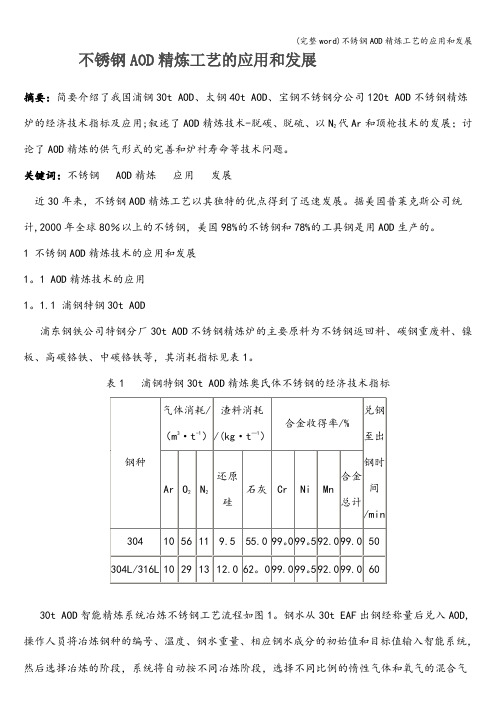
不锈钢AOD精炼工艺的应用和发展摘要:简要介绍了我国浦钢30t AOD、太钢40t AOD、宝钢不锈钢分公司120t AOD不锈钢精炼代Ar和顶枪技术的发展;讨炉的经济技术指标及应用;叙述了AOD精炼技术-脱碳、脱硫、以N2论了AOD精炼的供气形式的完善和炉衬寿命等技术问题。
关键词:不锈钢 AOD精炼应用发展近30年来,不锈钢AOD精炼工艺以其独特的优点得到了迅速发展。
据美国普莱克斯公司统计,2000年全球80%以上的不锈钢,美国98%的不锈钢和78%的工具钢是用AOD生产的。
1 不锈钢AOD精炼技术的应用和发展1。
1 AOD精炼技术的应用1。
1.1 浦钢特钢30t AOD浦东钢铁公司特钢分厂30t AOD不锈钢精炼炉的主要原料为不锈钢返回料、碳钢重废料、镍板、高碳铬铁、中碳铬铁等,其消耗指标见表1。
表1 浦钢特钢30t AOD精炼奥氏体不锈钢的经济技术指标30t AOD智能精炼系统冶炼不锈钢工艺流程如图1。
钢水从30t EAF出钢经称量后兑入AOD,操作人员将冶炼钢种的编号、温度、钢水重量、相应钢水成分的初始值和目标值输入智能系统,然后选择冶炼的阶段,系统将自动按不同冶炼阶段,选择不同比例的惰性气体和氧气的混合气体从风口和顶枪同时进行吹炼。
操作人员可通过计算机提示加入合金及渣料,达到终点碳后,系统计算还原剂加入量,并进行还原冶炼。
图1 AOD智能精炼系统冶炼不锈钢工艺流程在整个精炼过程中,随着碳含量的降低和钢水温度的升高,氧气与隋性气体的比率从6:1连续变化到1:3。
在保证成品含氮量的前提下,可最大限度的以N2代替Ar。
1.1。
2 太钢40t AOD1999年太钢对18t AOD进行改造,先后建成40t AOD 3座,生产能力达到30~35万t/a。
通过提高供氧强度,提高碱度,降低氧化末期温度,控制冷却气体的流量,改善熔池内的物化反应,对传统的氧氢比由过去的2~3个台阶,增为4~6个,脱碳初期O2/A r(N2)由3:1改为6:1.双渣法操作改为单渣法操作,铬的回收率达到99%(表2)。
RH炉真空精炼技术操作规程

炼钢厂安全技术操作规程汇总第四部分RH炉真空精炼技术操作规程目录前言: (4)1.RH真空处理的工艺流程 (5)2. RH真空处理模式、周期 (6)3.各种能源介质的参数 (7)4.RH钢水真空处理 (8)4.1处理前的准备工作 (8)4.2开始处理 (9)4.3提升气体 (9)4.4真空泵的操作 (9)4.5合金化 (10)4.6温度控制 (11)4.7测温取样 (12)4.8处理结束 (12)5.检漏操作标准 (13)6. RH浸渍管的喷补 (14)7. RH真空室的更换 (16)7.1准备 (16)7.2操作 (16)8. RH各部位耐材干燥烘烤加热 (17)8.1要求 (17)8.2真空室在线天然气加热操作 (17)8.3真空室升温制度 (17)8.4底部烘烤制度 (17)8.5插入管烘烤制度 (18)9. RH各部位使用更换及修理 (19)9.1插入管更换 (19)9.2 底部更换 (20)10. RH内衬砌筑标准 (21)10.1 砌筑基本要求 (21)10.2插入管砌筑与浇注 (22)10.3循环管砌筑 (22)10.4炉底与下部槽砌筑................................................................ - 22 -10.5上部槽砌筑 (23)11.验收标准 (25)11.1新插入管验收标准 (25)11.2新底部验收标准 (25)11.3新上部验收标准 (25)12.紧急事故处理对策 (26)12.1处理中液压升降不能动作 (27)12.2真空处理中钢包穿包 (27)12.3真空处理中突然穿真空槽.................................................... - 27 -12.4真空处理中突然停电 (27)12.5真空处理中突然停机械冷却水............................................ - 28 -12.6真空处理中突然停冷凝水或蒸汽........................................ - 28 -12.7真空处理中突然停仪表压缩空气........................................ - 28 -12.8氧枪使用过程中或提枪后发现漏水处理办法 ................... - 29 - 12.9氧枪使用中断链条或驱动失灵------------------------------------- 29 -附录炼钢厂安全技术操作规程汇总总目录第一部分. 铁水KR脱硫技术操作规程第二部分.转炉炼钢技术操作规程第三部分.LF炉炼钢技术操作规程第四部分.RH炉真空精炼技术操作规程第五部分.一号连铸机技术操作规程第六部分.二号连铸机技术操作规程前言:本RH炉主要功能有:1)、脱气(氢、氮)处理及去除钢中夹杂物;2)、轻处理碳脱氧;3)微调钢水成份;4)自然脱碳、强制脱碳;5)加铝吹氧升温,进行钢水温度调整。
第二炼钢厂设备简介
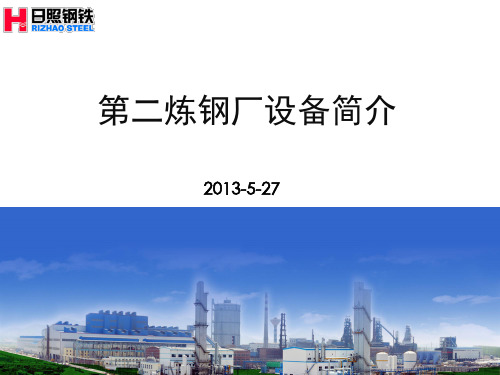
高压供电线路说明:
1. 第二炼钢厂从110KV 3#变电站受电,共分为八路:四路35kV供4台精 炼炉用电,两路10KV供转炉低压设备、高压电机等等用电,另两路 10KV供板坯高配室。 2. 35KV经过21000KVA的变压器变电成二次电压240V,二次电流 33716-37444A供电极拉弧加热。每个精炼炉进线都配有大、小滤波 电容。
障而引起事故的发生,主卷扬动力由两台电动机提供,保证了动力的
充分供给;主卷扬减速机内部传送使用棘轮棘爪形式,充分保证双驱 的平衡性和安全性能。这12台起重机担负着全厂液体金属的吊运工作,
是全厂的生产运输核心。
其余39台行车生产厂家分别为银川起重机厂、山东起重机厂及新 乡市起重机厂等国内著名起重机制造生产,行车质量好技术先进,运
21
行车运行现场图
钢水6# - 200/75t
连铸2# - 75/20t
22
4、第二炼钢厂电气系统介绍
23
4.1
高压系统介绍
公司供输电线路来自日照供电公司220kV岚山站(距日钢4km)和
供输电线路:
220kV安东站(距日钢7km)的同塔双回的四路外供电源、电厂8台发电 机组的四条110kV并网线、三条110kV内部联络线、两条分厂110kV直 供线及TRT发电、转炉余热发电、烧结余热发电的10kV并网线构成。 供输电线路可用裕量充足。
15
连铸设备先进工艺技术
1. 5#、6#机(R8M)、7#、8#、9#机(R9M)采用精确连续弯曲连续 矫直直弧型设计。 2. 连续称重、可升降、碟式钢包回转台,配有事故回转系统。 3. 结晶器液面自动控制技术。 4. 钢包、中间包全程吹氩保护浇注。 5. 塞棒吹氩控制。 6. 5#6#连铸机采用四连杆振动,设备运行稳定可靠;7-9#连铸机采用结 晶器液压振动技术,可以实现正弦和非正弦振动。 7. 自动配水模型,不同钢种采用不同水表,水量根据拉速变化自动控制 调节。 8. 红外线测量铸坯长度,铸坯自动切割。 9. 铸坯去毛刺。 10. 铸坯自动喷号、识别。 11. 采用电磁搅拌技术,提高铸坯内部质量。 12. 钢水收得率高,达到99%以上。
炼钢优化生产组织降低成本实践

炼钢优化生产组织降低成本实践摘要:面对严峻的钢铁市场形势,钢铁企业利润空间不断压缩,成本精细化管理在钢铁企业管理中的地位显得尤为重要。
文章从炼钢精细化生产组织出发,浅析高效生产对降低炼钢成本的应用。
关键字:高效生产;天车物流系统,成本1前言在全球市场经济高速发展、企业间竞争日趋激烈的今天,全国钢铁产能过剩及产品同质化日趋严重,钢铁行业进入了微利时代,成本控制仍是企业生存的最后一道防线,钢铁企业纷纷通过生产组织优化、工艺技术改革创新来控制降低生产成本。
管理日趋智能化、网络化,同时对于炼钢企业,对从铁水入厂到连铸出坯的整个生产过程进行物料跟踪,突破生产瓶颈,提高调度质量,从而提高生产的组织管理和过程控制水平。
2天车物流系统优化改造在天车物流改造前,某钢厂炼钢生产用的天车,包括倒罐间、废钢跨、加料跨、精炼跨和钢水跨区域均无法实时跟踪天车运行,即无法准确跟踪铁水、废钢和钢水等物料的周转情况;炼钢用的钢包包号无法自动识别,无法对钢包周转过程的运转状态和位置信息进行实时监测。
生产调度无法第一时间了解现场生产实际信息,无法监控全局,影响制约炼钢生产管理效率提升,对生产调度组织产生不利影响。
2.1天车物流技术方案2.1.1在倒罐间、废钢跨、加料跨、精炼跨、钢水跨天车走台增加地址识别设备;在钢包、废钢斗的本体增加标签,在相应区域安装标签识别系统。
在钢包烘烤区域增加触摸屏,用于输入及显示钢包烘烤信息并上传至天车物流系统。
2.1.2天车定位系统按部署的位置分为天车部分、通讯传输部分和地面部分。
天车部分包括数据采集系统、位置信息传输系统。
通讯传输部分以无线传输方式实现与服务终端的数据传输。
天车定位精度≤1m。
2.1.3与MES通讯协议需遵循某钢XCOM通讯规约,并支持可手动调整通讯IP和端口功能。
2.2天车物流功能设计2.2.1天车部分在天车轨道按定位精度要求,沿天车轨道按间隔安装放置天车定位装置,保证定位精度。
通讯传输采用数传无线网络,目的在于实现车间内天车移动的实时数据通讯,使天车设备与地面控制室通讯。
铜冶炼工艺介绍全解

火法熔炼步骤
熔炼:主要是造锍熔炼,其目的是铜精矿中的部分铁和其他金属氧化, 并与脉石和熔剂等造渣除去,产出适合吹炼所需要的冰铜。 吹炼:目的是进一步脱除冰铜中的硫、铁等杂质,回收精矿中的硫,获 取粗铜。 火法精炼:是利用杂质对氧的亲和力大于铜,而其又不溶于铜液等性质, 通过氧化造渣或挥发除去,获得纯度较高的阳极铜。 现代铜精矿冶金的通常步骤和工艺流程如下:
红色
灰黑色 红蓝色 黄色 红蓝色 灰黑色 灰黑色
硫化 矿物
黄铜矿 斑铜矿 硫砷铜矿 黝铜矿
铜的主要矿物
赤铜矿 Cu2O 88.8 7.14 红色
黑铜矿
氧化 孔雀石 蓝铜矿 硅孔雀石 胆矾
CuO
CuCO3· Cu(OH)2 2CuCO3· Cu(OH)2 CuSiO3· 2H2O CuSO4· 5H2O
工艺流程总述
我公司火法冶炼工艺采用富氧底吹造锍熔炼、铜锍底吹 吹炼、粗铜回转式阳极炉精炼工艺。工艺过程为湿精矿加入 氧气底吹熔炼炉自热熔炼产出72%的铜锍。经冷却破碎后的 铜锍由加料系统加入到吹炼炉中吹炼成粗铜,液态粗铜加入 到回转式阳极炉精炼并浇铸产出阳极送电解精炼。主要设备 有Φ4.8×20m氧气底吹炉一台,Φ4.4×20m 底吹连续吹炼 炉1台,Φ4.0×12.5m阳极炉2台。 液态熔炼渣和液态转炉 渣送缓冷渣场缓冷后送炉渣选矿车间用浮选法回收铜,产出 的渣精矿返回熔炼炉,渣尾矿外卖。熔炼炉和吹炼炉产出的 高温烟气经余热锅炉回收余热(产生的蒸汽用于发电),再 经电收尘器收尘后送硫酸车间制酸。阳极炉氧化期烟气经降 温除尘后送制酸系统,还原期含二氧化硫很少,经降温除尘 后和全厂环保通风的气体一起进行脱硫,脱硫装置采用活性 焦脱硫吸附解析装置回收二氧化硫,并将二氧化硫送制酸, 脱硫后的烟气通过120m的环保烟囱排放。
精馏车间技术操作规程

精馏车间技术操作规程1、工艺流程及技术指标锌是一种白而略带蓝灰色的金属,质地较软。
纯锌具有良好的延展性,其化学性质较为爽朗,广泛应用于化工、医药等行业。
本车间是以ISP熔炼车间产出的粗锌为原料,采纳精镏法生产合格精锌的过程。
精镏法是目前广泛采纳的一种粗锌精炼方法。
精馏法的精炼原理是利用粗锌中的杂质各具不同沸点的特性,要紧金属的沸点为:锌的沸点为906.97℃,镉的沸点为767.58℃,铅的沸点为1525℃,铁的沸点为3235℃,铜的沸点为2270℃,锡的沸点为2735℃。
通过分馏过程,使锌与其他杂质分离,从而得到高纯度的锌,并使铅、镉、铟等金属分别得到富集。
锌的精馏过程分为两个时期,在两种结构不同,原理相似的密闭作业的精馏塔内进行。
第一时期是在铅塔中进行,使粗锌中的锌、镉与其他高沸点的杂质铅铁等分离,产出馏余锌与含镉锌;第二时期是在镉塔中进行,使锌与镉分离,产出高镉锌和高纯度的精馏锌。
产出的馏余锌经熔析炉精炼,并辅之锌精馏加铝工艺,去掉杂质铁,富集铅、铟等有价金属,产出B#锌(也叫无镉锌)。
1.1工艺流程作业程序概述:第一将粗锌加入熔化炉内,经自动给料器、铅塔加料器、加料管流入铅塔。
由上层蒸发盘之溢流孔至下层蒸发盘时,一面受燃烧室加热升温,一面与上升金属蒸汽进行热交换,从而使锌充分受热,镉与锌大部分蒸发,同时与上升气流夹带的高沸点金属铅雾一并上升至回流部分,利用回流盘的分凝回流作用,铅雾被洗涤下来,锌镉蒸汽进入铅塔冷凝器得到含镉锌。
部分锌和高沸点的杂质,经铅塔底部、下延部进入精炼炉,经加铝熔析精炼后,得到#B锌、硬锌和富铟粗铅。
#B锌作为原料返回熔化炉,含镉锌经镉塔加料器、加料管进入镉塔。
在镉塔内同样进行分凝与回流过程后进入大冷凝器,使锌与镉蒸汽进一步分离富集,高镉锌蒸汽进入小冷凝器,产出高镉锌,做为精镉生产的原料。
由镉塔脱去镉的纯锌液经下延部进入纯锌炉,按时放出铸锭、得到精锌。
1.2要紧经济技术指标1)一座单铅塔日处理粗锌量:54—63吨。
sphc浅精炼工艺生产实践

终点 (O) /(106) 钢芯铝 /kg
终点 (C) /% 碳粉 /kg
<420准
421~480 40
0.045~0.06 10
481~530 60
>0.06 0
531~570 80 -
571~600 100 -
>600 120 -
工艺模式
TFe
浅精炼工艺要求转炉终点提供足够的出钢 温度,出钢过程进行脱氧合金化及渣洗,在高 温钢流冲击和底吹氩强搅下,合金及渣洗料快 速熔化。出钢期间,可根据转炉终点氧含量及 成分化验结果补加脱氧剂及石灰。出钢结束后, 在氩站加入精炼预熔渣进行钢包精炼处理,利 用钢水高温条件快速造渣高效脱硫。当钢水送 到 LF 精炼站,根据氩站的测温取样结果微调成 分,然后进行钙处理,上连铸机浇铸,SPHC 钢 种的成分控制要求见表 1。
还需要缩短整个处理时长,减少温降。试验炉 次温度与时间的控制见表 4。浅精炼工艺有效地 避免了 LF 精炼电极升温。出钢温度由原工艺的 1 631.71 ℃提高到 1 646.52 ℃,略微升高的出钢 温度对转炉炉衬的影响不大。同时,浅精炼工 艺中转炉钢水到连铸平台之间的处理时长相比 原工艺节约了 14.4 min,促进了 SPHC 钢种生产 的高效稳定。
(二) 出钢脱氧合金化与渣洗
转炉出钢过程一般持续 4~6 min。利用高 温钢流和底吹氩气的强大搅拌力,实现脱氧合 金化及渣洗。出钢物料加入顺序为出钢 1/4 时加 入石灰 450 kg、精炼渣球 150 kg 作为渣洗料; 钢芯铝 190 kg、中碳锰 130 kg 进行脱氧合金化。 此外,出钢过程避免下渣并根据终点氧含量及 成分化验结果补加钢芯铝和碳粉,表 2 为出钢 后补加物料参考标准。
[河北]钢铁厂炼钢系统工程施工组织设计
![[河北]钢铁厂炼钢系统工程施工组织设计](https://img.taocdn.com/s3/m/b9c69312df80d4d8d15abe23482fb4daa58d1df7.png)
XX炼钢系统一期工程施工组织总设计XX工程指挥部XX年XX月第一章.编制说明1.1工程名称XX公司钢铁厂一期一步炼钢系统工程。
1.2编制依据1.2.1本单位施工类似工程的经验,尤其是唐钢160吨、120吨转炉和宣钢120吨转炉炼钢施工经验的积累。
1.2.2国家现行规范、规程、标准。
GB/T19001:2000、GB/T24001:2004、GB/T28001:2001整合型管理体系标准和我公司编制的技术操作规程、工法汇编1.2.3本公司施工能力、技术装备状况制定的。
1.3编制原则本施工组织设计编制遵循符合性、先进性和经济性原则1.3.1符合性原则本施工组织设计的编制符合首钢XXX公司要求。
本施工组织设计的编制符合大型炼钢工程施工流程及300吨转炉炼钢工程特点,并结合我公司施工能力、技术装备状况。
1.3.2先进性原则先进性原则是在满足符合性原则的基础上,以我公司的技术、装备、员工素质为前提,采取科学的方法,优化的配置,完善的措施,采用先进的施工工艺和施工方法,确保工期、质量目标的实现。
1.3.3经济性原则经济性原则是以符合性为前提,先进性为目标,在施工方案和组织管理选择上,选择成本达到最佳点且先进的施工方案和管理措施。
1.4适用范围本施工组织设计是为XX公司钢铁厂一期一步炼钢系统工程编制的。
开工后再编制施工阶段具体的专项、分项施工方案、施工技术措施。
1.5本工程拟采用的规范标准(略)第二章.工程综合说明2.1建设规模和环境特征2.1.1建设规模项目建设一期一步建成2套KR脱硫装置;1座脱磷转炉(具备常规炉功能);2座脱碳转炉;1套双工位RH真空处理装置;1套双工位LF钢包精炼炉;1套CAS精炼装置。
计划XX年XX月开工,XX年XX月底建成。
2.1.2环境特征(1)工程地质条件曹妃甸岛地处滦河冲积扇的前部,新生代以来,在古老的基底岩石上部堆积了巨厚的松散层,主要是晚更新世(Q3)及全新世(Q4)海相、陆相及海陆相交互层,多为粉、细砂,部分为粘性土层。
- 1、下载文档前请自行甄别文档内容的完整性,平台不提供额外的编辑、内容补充、找答案等附加服务。
- 2、"仅部分预览"的文档,不可在线预览部分如存在完整性等问题,可反馈申请退款(可完整预览的文档不适用该条件!)。
- 3、如文档侵犯您的权益,请联系客服反馈,我们会尽快为您处理(人工客服工作时间:9:00-18:30)。
2020年4月5日
12
LF精炼工艺
1.温度控制工艺 1.1埋弧加热:减少吸氮;提高加热效率。 1.2加热终了温度确定:TLF终了=T中+ΔT1+ΔT2
TLF终了-最后一次加热结束后的钢包钢水温度。 T中-中间包标准温度。 ΔT1-过程温降。 ΔT2-补偿温度。
2020年4月5日
13
2.还原渣精炼工艺
采用不同的包芯线、金属线,喂线技术可具有脱氧、脱硫、 夹杂物变性、防止水口堵塞等功能。
2020年4月5日
5
6.升温 加热是调节钢液温度的一项常用手段。 炉外精炼设备大多配备加热手段。 采用电弧加热的方法有LF等炉外精炼方 法,有些DH、RH的真空室内也设有电 阻加热。还采用化学热法升温,即利用 加铝(或碳、硅)吹氧氧化的化学热, 使钢液升温,如CAS—OB、RH—OB、
一、炉外精炼采用的手段及其功能
1.渣洗 渣洗是能适量脱硫、脱氧、去夹杂、提高钢水纯净度的最
简便的精炼手段。早在二十世纪30年代就已开始应用。 渣洗工艺有一定的缺陷,如不能去除钢中气体,甚至可能
增氮和造成二次氧化。为增强钢渣反应界面,应使钢、渣 尽可能混匀、乳化,而为使乳化的合成渣尽可能上浮,又 需要足够的镇静时间。另外,渣洗效果精炼渣的性能影响 非常大。
2020年4月5日
4
5.喂线 喂线是通过喂线机将钙、铝、硅钙、钡系合金等制成的包芯 线或铝等金属线高速加入到钢液的方法。具有如下特点: ·合金收得率高; ·能解决特种合金的加入问题; ·避免合金加入时的吸氮; ·投资费用少,应用范围广,操作简便。 喂线技术可单独应用。也可应用到各种精炼方法中。目前各 种炉外精炼方法中都添加了喂线设施,并且以推广到中间包 喂线、结晶器喂线。
尽管渣洗有上述缺陷,但由于其操作方便、简洁,与其他 精炼手段综合应用,可以有效的脱硫、脱氧和吸附夹杂。 应用渣洗的炉外精炼方法有CAS、LF、VD等。
2020年4月5日
1
2.搅拌 搅拌是绝大部分炉外精炼方法都采用的基本手段。
冶金反应的速率与钢液被搅动的程度有关,因为搅拌可以扩大反应界面, 加快传质,改善动力学条件,从而提高钢—渣—气的反应速度。炉外精 炼方法,除了要创造最佳的热力学条件外,还必须提供最佳的动力学条 件,因此搅拌几乎成为各种炉外精炼的必选。
2020年4月5日
14
精炼渣的要求:
合适的成分 低的熔化温度 低氧势 合适的粘度 高碱度 适当的渣量
2020年4月5日
15
要取得良好的精炼效果,控制好精炼渣的成分至关重要。 对于LF处理来说,主要要控制以下几个方面:
适当的高碱度:高碱度渣有利于脱氧、脱硫和吸附夹杂, 但是随着碱度的增加,渣的流动性降低 ,降低了精炼反应的
2020年4月5日
3
4.喷吹 喷吹也称喷射,是将反应剂利用气流直接加入冶金 熔体中的一种炉外精炼方法。由于它简便、高效, 所以也经常作为一种精炼手段,组合到其他炉外精 炼方法中。
喷吹技术利用气体的搅拌作用增加了粉状精炼剂和 钢液的接触界面,显著改善冶金反应的动力学条件。 因此可以实现快速脱硫、脱磷、脱氧,提高合金收 得率,促使夹杂物变性等功能。 RH配备喷吹功能,可以进行深脱硫,生产超低硫钢。
VOD等。
2020年4月5日
6
二、LF精炼工艺
2020年4月5日
7
LF工艺流程
1.只经LF处理的钢水
到等待位
吹氩
到处理位
测温、取样、定氧
加渣料
预加热及补加渣料
合金微调
主加热
测温、取样、定氧
喂线
吹氩结束
加保温剂
钢水出站Biblioteka 2020年4月5日8
2.经LF/VD(RH)处理的钢水
到等待位
吹氩
到处理位
动力学条件。同时,由于高碱度的精炼渣会形成点状夹杂, 对轴承钢等钢种产生较大的影响,因此应根据实际需要控制 适当的碱度。
低SiO2含量:SiO2含量的增加,势必增加石灰的加入量, 造成消耗的增加和处理时间的延长,同时SiO2含量过高时, 在高温和低氧势的精炼处理过程中,易发生Si的还原,最终 影响成分的精确控制或造成成分出格。
2020年4月5日
10
LF炉主要设备
LF设备主要包括:加热电源、炉盖、电极 及控制装置、钢包车、钢包、除尘系统、 底吹搅拌装置、加料系统。
2020年4月5日
11
LF的作用
提高生产能力 降低出钢温度 提高合金收得率 均匀钢水的成分和温度 精确控制钢水的成分和温度 协调炉机节奏 钢水的脱硫和脱氧 去除钢中的夹杂物以及夹杂物的变性处理
测温、取样、定氧
加渣料
预加热及补加渣料
合金微调
主加热
测温、取样、定氧
吹氩结束
钢水出站
2020年4月5日
9
LF主要技术参数
公称容量:120t 最大钢水处理量:150t 最小钢水处理量:100t 电极电流密度(国产电极):27A/cm2 电极直径:450mm 电极最大电流:45KA LF变压器功率(连续负载):26MVA 最大升温速度:5℃/min
LF炉利用白渣进行钢水精炼,实现钢水脱氧、脱硫,去除 夹杂,白渣精炼是LF炉工艺操作的核心,也是提高钢水纯 净度的重要保证。 目前LF精炼渣一般采用CaO-SiO2-Al2 O3 -MgO渣系 CaO主要来源于加入的石灰和初炼炉渣 SiO2和Al2O3主要来源于初炼炉渣、脱氧产物和耐火材料 以及造渣料。 MgO来源于初炼炉渣、钢包和炉盖耐火材料。
搅拌作为一种炉外精炼手段,搅拌强度、持续时间应当可以按精炼要求 控制。
较早出现的搅拌方法,是利用钢液本身的位能,依靠钢液的冲击,促使 钢水搅动。 真空碳氧反应产生的CO气泡产生熔池搅拌,但搅拌强度较弱,持续的时 间也不可能太长,精确控制也比较困难。 RH、DH等方法利用压差造成部分钢水位能差异,利用钢液回流搅动熔 池,是一种简便可行的办法。 单纯的搅拌可以均匀成分、温度,促进夹杂物聚合、上浮。
2020年4月5日
2
3.真空 真空是炉外精炼中广泛采用的手段。真空对有气相参加,且 反应前后气相分子数不同的反应均产生影响,促使反应向生 成气相多的方向进行。
现在各种炉外精炼方法中,真空度通常有几十帕,对于钢液 脱气、碳脱氧、超低碳钢脱碳等反应均能起到作用。只要提 高真空度,并若辅以吹氩、脱碳反应或延长真空脱气时间, [H]含量可降到2ppm以下。 氮在钢水中传质慢,同时由于钢中固氮元素的影响,脱氮效 率低一些,一般在20~30%。