有害元素对高炉炼铁的影响及控制措施
有害元素对宣钢高炉的影响
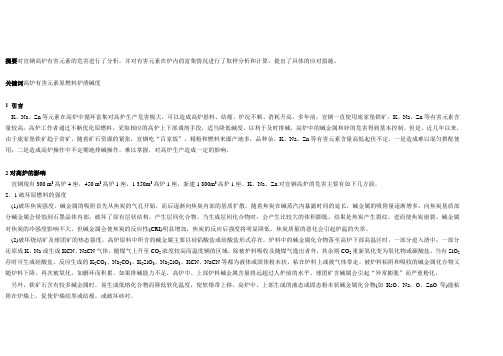
摘要对宣钢高炉有害元素的危害进行了分析,并对有害元素在炉内的富集情况进行了取样分析和计算,提出了具体的应对措施。
关键词高炉有害元素原燃料炉渣碱度1 引言K、Na、Zn等元素在高炉中循环富集对高炉生产危害极大,可以造成高炉悬料、结瘤、炉况不顺、消耗升高。
多年前,宣钢一直使用庞家堡铁矿,K、Na、Zn等有害元素含量较高,高炉工作者通过不断优化原燃料,采取相应的高炉上下部调剂手段,适当降低碱度,以利于及时排碱,高炉中的碱金属和锌的危害得到基本控制。
但是,近几年以来,由于庞家堡铁矿趋于贫矿,随着矿石资源的紧张,宣钢吃“百家饭”,精粉和燃料来源产地多,品种杂,K、Na、Zn等有害元素含量高低起伏不定,一是造成难以混匀搭配使用;二是造成高炉操作中不定期地排碱操作,难以掌握,对高炉生产造成一定的影响。
2对高炉的影响宣钢现有300 m3高炉4座,450 m3高炉1座,1 350m3高炉1座,新建1 800m3高炉1座。
K、Na、Zn对宣钢高炉的危害主要有如下几方面。
2.1破坏原燃料的强度(1)破坏焦炭强度。
碱金属的吸附首先从焦炭的气孔开始,而后逐渐向焦炭内部的基质扩散,随着焦炭在碱蒸汽内暴露时间的延长,碱金属的吸附量逐渐增多。
向焦炭基质部分碱金属会侵蚀到石墨晶体内部,破坏了原有层状结构,产生层间化合物。
当生成层间化合物时,会产生比较大的体积膨胀,结果是焦炭产生裂纹,进而使焦炭崩裂。
碱金属对焦炭的冷强度影响不大,但碱金属会使焦炭的反应性(CRI)明显增加,焦炭的反应后强度将明显降低。
焦炭质量的恶化会引起炉温的失常。
(2)破坏烧结矿及球团矿的热态强度。
高炉原料中所含的碱金属主要以硅铝酸盐或硅酸盐形式存在,炉料中的碱金属化合物落至高炉下部高温区时,一部分进入渣中;一部分还原成K、Na或生成KCN、NaCN气体,随煤气上升至CO2浓度较高而温度辆的区域,除被炉料吸收及随煤气逸出者外,其余则CO2重新氧化变为氧化物或碳酸盐,当有SiO2存时可生成硅酸盐。
烧结矿中有害元素对高炉的危害和抑制

烧结矿中有害元素对高炉的危害和抑制
为适应当前严峻的钢铁形势,进一步降低铁水成本,各钢铁企业都采用低价的外矿粉进行烧结,并充分利用烧结、炼铁、炼钢工序所产生的各种除尘灰,利用其低价和含有大量的C、Fe、CaO、MgO等有利成分的优势,来降低烧结料消耗,从而达到降低成本的目的。
但由于各种外矿粉及除尘灰都含一定量的K、Na、Zn等有害元素,大量配加会造成高炉碱负荷、锌负荷超标,高炉炉墙结厚结瘤,加剧炉缸侵蚀,影响炉况稳定顺行。
铁矿石有害成分对钢铁冶炼过程的影响
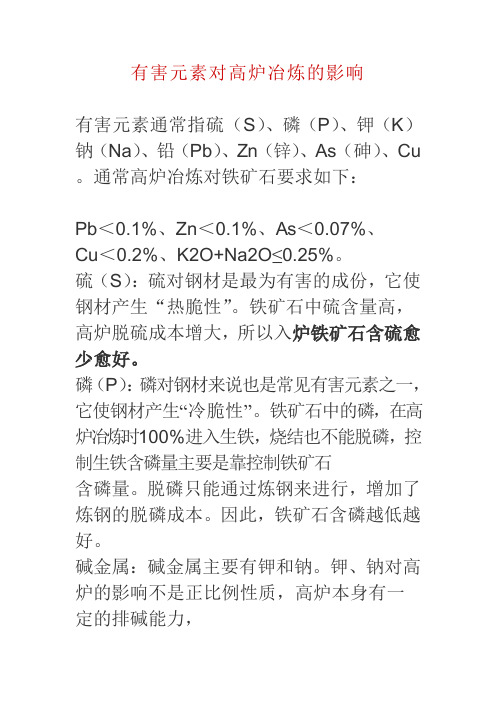
有害元素对高炉冶炼的影响有害元素通常指硫(S)、磷(P)、钾(K)钠(Na)、铅(Pb)、Zn(锌)、As(砷)、Cu 。
通常高炉冶炼对铁矿石要求如下:Pb<0.1%、Zn<0.1%、As<0.07%、Cu<0.2%、K2O+Na2O≤0.25%。
硫(S):硫对钢材是最为有害的成份,它使钢材产生“热脆性”。
铁矿石中硫含量高,高炉脱硫成本增大,所以入炉铁矿石含硫愈少愈好。
磷(P):磷对钢材来说也是常见有害元素之一,它使钢材产生“冷脆性”。
铁矿石中的磷,在高炉冶炼时100%进入生铁,烧结也不能脱磷,控制生铁含磷量主要是靠控制铁矿石含磷量。
脱磷只能通过炼钢来进行,增加了炼钢的脱磷成本。
因此,铁矿石含磷越低越好。
碱金属:碱金属主要有钾和钠。
钾、钠对高炉的影响不是正比例性质,高炉本身有一定的排碱能力,碱金属在控制范围内对高炉影响不大。
但是入炉铁矿石碱金属含量太多,超过高炉排碱能力,就会形成碱金属富集,导致高炉中上部炉料碱金属含量大大超过入炉料原始水平。
铁矿石含有较多的碱金属极易造成软化温度降低,软熔带上移,不利于发展间接还原,造成焦比升高。
球团含有碱金属会造成球团异常膨胀引起严重粉化,恶化料柱透气性。
碱金属对焦炭性能破坏也很严重。
另外,高炉中上部碱金属化合物黏附在炉墙上,促使炉墙结厚、结瘤并破坏砖衬。
因此,铁矿石含碱金属越低越好。
铅(Pb):铅在高炉中几乎全部被还原,由于密度高达11.34t∕m³,故沉于死铁层之下,易破坏炉底砖缝,有可能会造成炉底烧穿。
锌(Z n):锌很容易气化,锌蒸汽容易进入砖缝,氧化成为ZnO后膨胀,破坏炉身上部耐火砖衬。
砷(As):砷对钢材来说也是有害元素之一,它使钢材产生冷脆性,使得钢材焊接性能变差。
铁矿石中砷基本还原进入生铁,影响生铁质量。
此外砷在烧结过程中挥发,对环境影响较大。
铜(Cu):铜会使钢材“热脆”,钢材不易轧制和焊接。
少量铜能改善钢的耐蚀性。
在高炉冶炼中,铜全部还原进入生铁中。
高炉铁水有害元素分析与控制
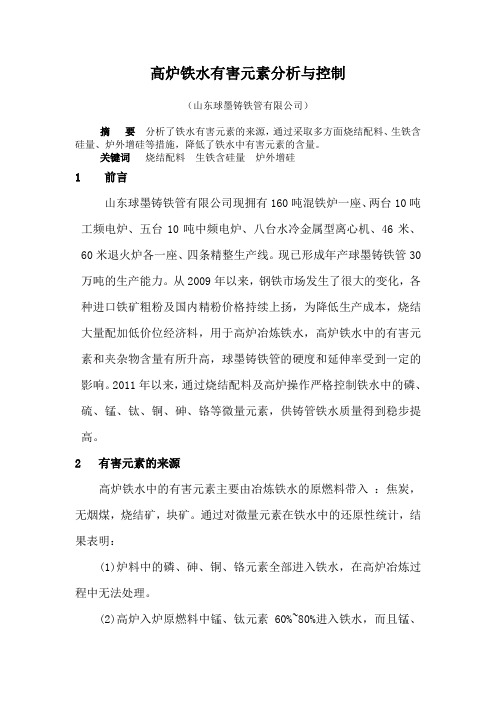
高炉铁水有害元素分析与控制(山东球墨铸铁管有限公司)摘要分析了铁水有害元素的来源,通过采取多方面烧结配料、生铁含硅量、炉外增硅等措施,降低了铁水中有害元素的含量。
关键词烧结配料生铁含硅量炉外增硅1 前言山东球墨铸铁管有限公司现拥有160吨混铁炉一座、两台10吨工频电炉、五台10吨中频电炉、八台水冷金属型离心机、46米、60米退火炉各一座、四条精整生产线。
现已形成年产球墨铸铁管30万吨的生产能力。
从2009年以来,钢铁市场发生了很大的变化,各种进口铁矿粗粉及国内精粉价格持续上扬,为降低生产成本,烧结大量配加低价位经济料,用于高炉冶炼铁水,高炉铁水中的有害元素和夹杂物含量有所升高,球墨铸铁管的硬度和延伸率受到一定的影响。
2011年以来,通过烧结配料及高炉操作严格控制铁水中的磷、硫、锰、钛、铜、砷、铬等微量元素,供铸管铁水质量得到稳步提高。
2 有害元素的来源高炉铁水中的有害元素主要由冶炼铁水的原燃料带入:焦炭,无烟煤,烧结矿,块矿。
通过对微量元素在铁水中的还原性统计,结果表明:(1)炉料中的磷、砷、铜、铬元素全部进入铁水,在高炉冶炼过程中无法处理。
(2)高炉入炉原燃料中锰、钛元素60%~80%进入铁水,而且锰、钛元素在铁水中含量与高炉铁水含硅量呈正相关性关系。
原始生铁含硅量的提高有助于有害元素含量的升高。
3 不同元素对铸铁管的危害供铸管铁水中一些元素达到一定值会对铸铁管的退火产生一定的影响,进而降低对铸铁管的产品质量:磷是铸铁中的常存元素,它对球墨铸铁的机械性能,尤其是冲击韧性和塑性有明显的不良影响,因此总是作为有害元素对待。
其主要原因是共晶团晶界产生的磷共晶脆相,磷共晶呈多角状分布于共晶团边界,急剧恶化球墨铸铁的力学性能,使球墨铸铁韧性下降;其次是磷阻碍珠光体的分解,又能固溶于铁素体中,这些都能降低韧性。
磷的质量分数每增加0.01%时,脆性转变温度升高4.0~4.5℃。
当磷的质量分数超过0.16%时,脆性转变温度已在室温以上,冲击断口出现脆性断裂。
高炉炼铁有害指标
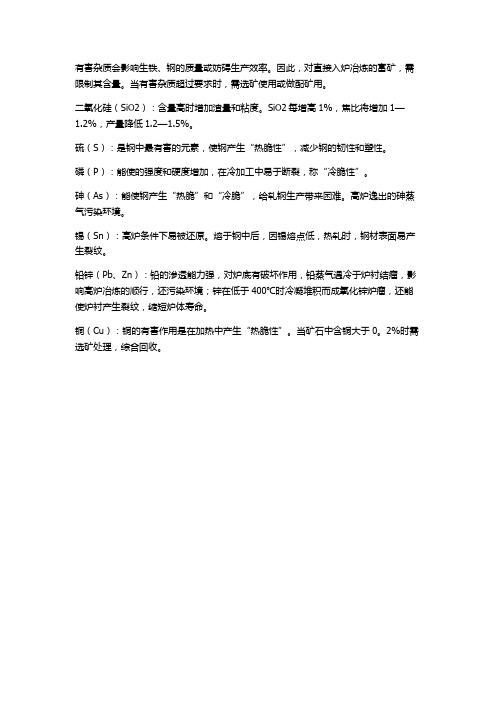
有害杂质会影响生铁、钢的质量或妨碍生产效率。
因此,对直接入炉冶炼的富矿,需限制其含量。
当有害杂质超过要求时,需选矿使用或做配矿用。
二氧化硅(SiO2):含量高时增加渣量和粘度。
SiO2每增高1%,焦比将增加1—1.2%,产量降低1.2—1.5%。
硫(S):是钢中最有害的元素,使钢产生“热脆性”,减少钢的韧性和塑性。
磷(P):能使的强度和硬度增加,在冷加工中易于断裂,称“冷脆性”。
砷(As):能使钢产生“热脆”和“冷脆”,给轧钢生产带来困难。
高炉逸出的砷蒸气污染环境。
锡(Sn):高炉条件下易被还原。
熔于钢中后,因锡熔点低,热轧时,钢材表面易产生裂纹。
铅锌(Pb、Zn):铅的渗透能力强,对炉底有破坏作用,铅蒸气遇冷于炉衬结瘤,影响高炉冶炼的顺行,还污染环境;锌在低于400℃时冷凝堆积而成氧化锌炉瘤,还能使炉衬产生裂纹,缩短炉体寿命。
铜(Cu):铜的有害作用是在加热中产生“热脆性”。
当矿石中含铜大于0。
2%时需选矿处理,综合回收。
朝阳钢铁高炉有害元素的分析及控制
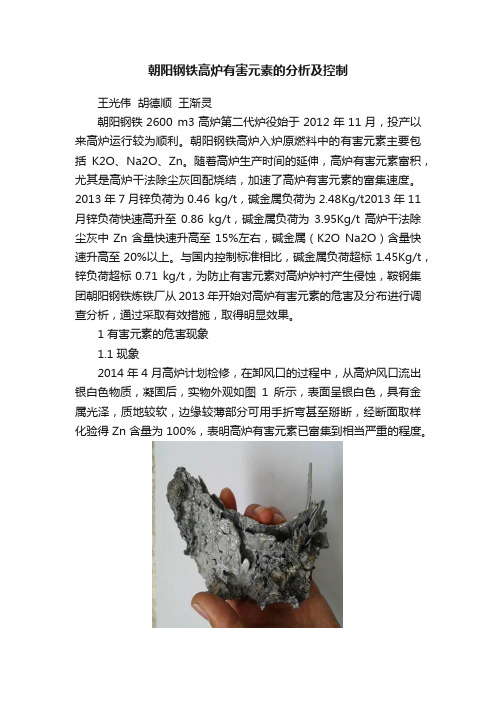
朝阳钢铁高炉有害元素的分析及控制王光伟胡德顺王渐灵朝阳钢铁2600 m3高炉第二代炉役始于2012年11月,投产以来高炉运行较为顺利。
朝阳钢铁高炉入炉原燃料中的有害元素主要包括K2O、Na2O、Zn。
随着高炉生产时间的延伸,高炉有害元素富积,尤其是高炉干法除尘灰回配烧结,加速了高炉有害元素的富集速度。
2013年7月锌负荷为0.46 kg/t,碱金属负荷为2.48Kg/t2013年11月锌负荷快速高升至0.86 kg/t,碱金属负荷为3.95Kg/t高炉干法除尘灰中Zn含量快速升高至15%左右,碱金属(K2O Na2O)含量快速升高至20%以上。
与国内控制标准相比,碱金属负荷超标1.45Kg/t,锌负荷超标0.71 kg/t,为防止有害元素对高炉炉衬产生侵蚀,鞍钢集团朝阳钢铁炼铁厂从2013年开始对高炉有害元素的危害及分布进行调查分析,通过采取有效措施,取得明显效果。
1 有害元素的危害现象1.1 现象2014年4月高炉计划检修,在卸风口的过程中,从高炉风口流出银白色物质,凝固后,实物外观如图1所示,表面呈银白色,具有金属光泽,质地较软,边缘较薄部分可用手折弯甚至掰断,经断面取样化验得Zn含量为100%,表明高炉有害元素已富集到相当严重的程度。
图1 风口流出白色物质1.2 危害1.2.1 炉体上涨有害元素富集造成高炉炉体上涨,主要表现在以下几个方面:高炉炉底板开焊,上涨约100 mm,如图2(a)所示;高炉炉体9 层平台标尺上涨约50 mm,如图2(b)所示;高炉冷却水管与平台联接处开焊,水管上移出现弯曲,如图2(c)所示;高炉上升管膨胀节发生位移,如图2(d)所示。
1.2.2 炉墙结厚2015 年9 月~2016 年2 月,由于高炉干法除尘灰无地存放及降成本需要,烧结开始回配干法除尘灰,烧结矿中Zn 含量和碱金属含量快速增加,高炉锌负荷升高至0.9 kg/t。
同时由于原料库存较低,导致入炉原燃料质量波动较大,入炉粉末增多,炉况波动大,造成2016 年3~5 月高炉炉墙结厚。
[教育]有害元素对高炉的危害含量和有效预防措施
![[教育]有害元素对高炉的危害含量和有效预防措施](https://img.taocdn.com/s3/m/3a049b3bd0d233d4b04e6946.png)
莱芜高炉解剖研究:碱金属平衡计算
•入炉原料中碱金属分 布
•产物中碱金属分布
•莱钢3#120高炉碱负荷(碱负荷为M2O的入炉量)为:
• 与全国碱负荷平均在3~4kg/tFe相比,高出45%~60%,处于较高水平。
碱金属平衡小结
3)在石墨晶格上形成使碳的边界连接变弱的一种放电体,这是焦炭反应 性增加的另一个原因。综上所述,无论用哪一种方法增碱,焦炭增碱 后的结果都大致一样,即随着含碱量的增加,焦炭的反应性相应升高 ,焦炭的体积膨胀,强度明显降低,易粉化。
高炉碱金属对铁矿石冶金性能的影响
1. 1)碱金属能明显促进烧结矿的还原,对降低焦比有利。 2. 2)少量碱金属能够提高烧结矿的软熔温度,使得高炉软
氰化钾在622℃熔化,1625℃气化;氰化钠在562℃熔化, 1530℃气化。因此在风口区它们能以气态的形式存在,它 随煤气流向上运动,当温度降低后它们便转变为液态。所 以在炉身下部、炉腰、炉腹和炉缸碱金属氰化物完全可能 以液体的形式出现。
•碱化物在高炉里的行为,我们还应了解它们的相对稳定性。
•高炉中碱金属的循环富集
[教育]有害元素对高炉的危 害含量和有效预防措施
提纲
1. 有害元素在高炉中的影响 2. 碱金属在高炉中的分布-高炉解剖 3. 有害元素的来源-碱金属平衡计算 4. 排减措施
•1碱金属对高炉的危害主要表现
1)提前并加剧CO2对焦炭的气化反应,缩小了间接还原区,扩大了 直接还原区,进而引起焦比升高;降低焦炭的粒度和强度,从而降 低料柱特别是软熔带气窗的透气性,引起风口破损。
携带着碱蒸气,碱金属氰化物和碱金属碳酸盐的高炉煤气在 自下而上的运动过程中,所携带的上述碱化物会沉积在内衬 和炉料上,而来不及反应和沉积的碱金属则随煤气和炉尘从 炉顶排出,大部分未还原的碱金属硅酸盐随炉渣排出。
有害元素对高炉操作的影响
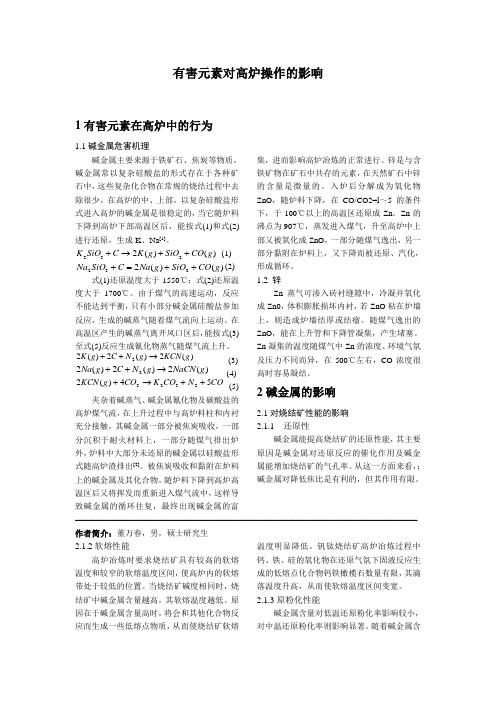
有害元素对高炉操作的影响1有害元素在高炉中的行为1.1碱金属危害机理碱金属主要来源于铁矿石、焦炭等物质,碱金属常以复杂硅酸盐的形式存在于各种矿石中,这些复杂化合物在常规的烧结过程中去除很少。
在高炉的中、上部,以复杂硅酸盐形式进入高炉的碱金属是很稳定的,当它随炉料下降到高炉下部高温区后,能按式(1)和式(2)进行还原,生成K 、Na [1]。
)()(2232g CO SiO g K C SiO K ++→+ (1))()(2232g CO SiO g Na C SiO Na ++=+(2)式(1)还原温度大于1550℃;式(2)还原温度大于1700℃。
由于煤气的高速运动,反应不能达到平衡,只有小部分碱金属硅酸盐参加反应,生成的碱蒸气随着煤气流向上运动。
在高温区产生的碱蒸气离开风口区后,能按式(3)至式(5)反应生成氰化物蒸气随煤气流上升。
)(2)(2)(22g KCN g N C g K →++ (3))(2)(2)(22g NaCN g N C g Na →++ (4) CON CO K COg KCN 54)(22322++→+ (5)夹杂着碱蒸气、碱金属氰化物及碳酸盐的高炉煤气流,在上升过程中与高炉料柱和内衬充分接触,其碱金属一部分被焦炭吸收,一部分沉积于耐火材料上,一部分随煤气排出炉外,炉料中大部分未还原的碱金属以硅酸盐形式随高炉渣排出[2]。
被焦炭吸收和黏附在炉料上的碱金属及其化合物,随炉料下降到高炉高温区后又将挥发而重新进入煤气流中,这样导致碱金属的循环往复,最终出现碱金属的富集,进而影响高炉冶炼的正常进行。
锌是与含铁矿物在矿石中共存的元素,在天然矿石中锌的含量是微量的。
入炉后分解成为氧化物ZnO ,随炉料下降,在CO/CO2=l ~5的条件下,于100℃以上的高温区还原成Zn 。
Zn 的沸点为907℃,蒸发进入煤气,升至高炉中上部又被氧化成ZnO ,一部分随煤气逸出,另一部分黏附在炉料上,又下降而被还原、汽化,形成循环。
高炉有害元素的控制
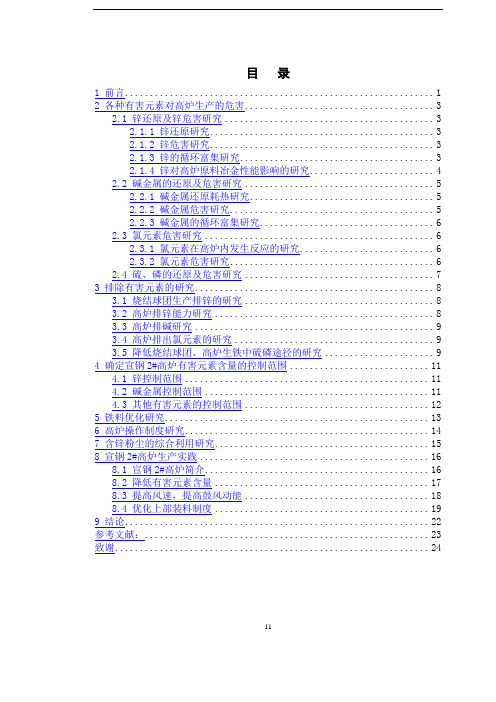
目录1 前言 (1)2 各种有害元素对高炉生产的危害 (3)2.1 锌还原及锌危害研究 (3)2.1.1 锌还原研究 (3)2.1.2 锌危害研究 (3)2.1.3 锌的循环富集研究 (3)2.1.4 锌对高炉原料冶金性能影响的研究 (4)2.2 碱金属的还原及危害研究 (5)2.2.1 碱金属还原耗热研究 (5)2.2.2 碱金属危害研究 (5)2.2.3 碱金属的循环富集研究 (6)2.3 氯元素危害研究 (6)2.3.1 氯元素在高炉内发生反应的研究 (6)2.3.2 氯元素危害研究 (6)2.4 硫、磷的还原及危害研究 (7)3 排除有害元素的研究 (8)3.1 烧结球团生产排锌的研究 (8)3.2 高炉排锌能力研究 (8)3.3 高炉排碱研究 (9)3.4 高炉排出氯元素的研究 (9)3.5 降低烧结球团、高炉生铁中硫磷途径的研究 (9)4 确定宣钢2#高炉有害元素含量的控制范围 (11)4.1 锌控制范围 (11)4.2 碱金属控制范围 (11)4.3 其他有害元素的控制范围 (12)5 铁料优化研究 (13)6 高炉操作制度研究 (14)7 含锌粉尘的综合利用研究 (15)8 宣钢2#高炉生产实践 (16)8.1 宣钢2#高炉简介 (16)8.2 降低有害元素含量 (17)8.3 提高风速,提高鼓风动能 (18)8.4 优化上部装料制度 (19)9 结论 (22)参考文献: (23)致谢 (24)111前言近几年来,随着钢铁市场的迅速发展,铁矿石资源日趋紧张,外粉价格大幅度上涨,导致生铁成本上升。
宣钢实施低成本战略,扩大使用当地资源的范围和数量。
张宣周边地区的精粉和块矿特点是,成份不稳定、有害元素含量较高。
在使用当地资源时,由于有害元素含量较高,致使高炉入炉有害元素含量升高,当有害元素富集到一定程度或炉料有害元素含量超过一定范围时,对高炉的危害很大,能使高炉操作炉型发生变化,破坏高炉顺行、高炉炉况失常;劣化炉料的冶金性能,能降低矿石的软化温度[1],造成球团低温粉化严重,使焦炭的气化反应能力增强,焦炭反应后强度急剧下降而粒度细化,造成料柱透气性变差,产生炉缸堆积,危及高炉冶炼的正常进行,高炉技术经济指标下降,焦比、燃料比升高,产量下降。
烧结矿中有害元素对高炉的危害和抑制

烧结矿中有害元素对高炉的危害和抑制简介高炉是一种冶金设备,用于在高温下还原矿石并将其转化为金属。
其中烧结矿是高炉冶炼的主要原料之一。
然而,不同来源的烧结矿中含有不同的有害元素,这些元素对高炉稳定运行产生了不良影响。
因此,研究有害元素在烧结矿中的存在和危害,以及抑制这些元素的方法,具有重要的理论和实际意义。
烧结矿中的有害元素硫硫是烧结矿中最主要的有害元素之一。
当烧结温度过高或气氛不足时,硫会在高炉中还原成为气态的硫化氢,对高炉冶炼的稳定性造成威胁。
此外,硫还会影响铁的机械性能和表面质量,降低钢的质量。
硅烧结矿中的硅,主要以二氧化硅的形式存在。
当烧结矿中的硅含量过高时,不仅会导致高炉堵塞和炉壁侵蚀,还会降低高炉的冶炼效率和产量。
锰烧结矿中的锰,主要以氧化锰的形式存在。
其含量过高会导致高炉铁水中的锰含量过高,影响铁的质量和冶炼工艺。
此外,锰还会影响钢的机械性能和表面质量。
钒烧结矿中的钒,主要以氧化钒的形式存在。
含量过高会降低铁的质量和机械性能,影响钢的质量。
有害元素的抑制方法硫的抑制方法一个有效的硫抑制方法是在烧结前给烧结矿中加入含铁的硫化物,例如二硫化钠、硫酸亚铁。
这些物质可以与矿物中的硫化物发生反应,将硫还原为亚硫化物或硫化物固体,有效地抑制了硫的释放。
硅的抑制方法硅的抑制方法主要包括混合烧结和高炉添加剂两种。
混合烧结是指将高硅的物质与烧结矿混合后进行烧结,利用烧结过程中的高温高压,将烧结矿和高硅物质结合为硅酸盐,并将其置于熔池底部。
这种方法可以有效减少烧结矿中硅含量。
高炉添加剂则是指在高炉中添加硅的内控剂和外控剂来抑制硅的释放。
内控剂为铁矿物中含有的定向形态的硅酸盐;外控剂为人工添加的一些化合物,例如硅酸钙、二氧化锆等。
锰的抑制方法锰的抑制方法主要是在高炉中加入含硅的烧结辅料。
这些辅料在高温下会与锰氧化物反应,生成含锰的硅酸盐和硫酸盐。
这些硅酸盐和硫酸盐可以在炉渣中固定锰,降低锰的含量。
钒的抑制方法钒的抑制方法主要是在烧结矿中加入石灰石和氧化镁等物质。
烧结矿中有害元素对高炉的危害和抑制
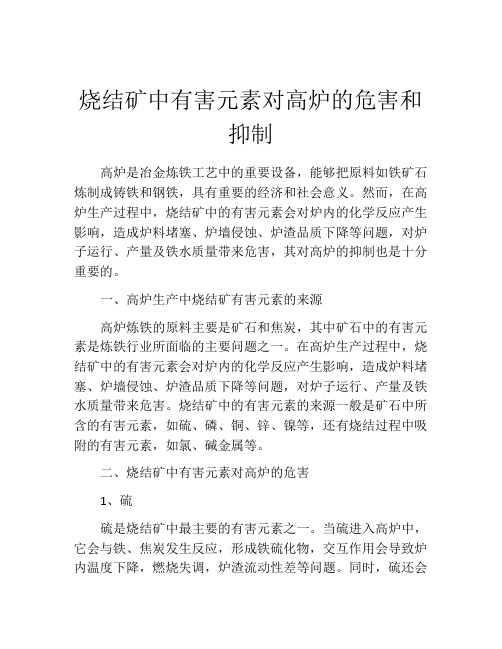
烧结矿中有害元素对高炉的危害和抑制高炉是冶金炼铁工艺中的重要设备,能够把原料如铁矿石炼制成铸铁和钢铁,具有重要的经济和社会意义。
然而,在高炉生产过程中,烧结矿中的有害元素会对炉内的化学反应产生影响,造成炉料堵塞、炉墙侵蚀、炉渣品质下降等问题,对炉子运行、产量及铁水质量带来危害,其对高炉的抑制也是十分重要的。
一、高炉生产中烧结矿有害元素的来源高炉炼铁的原料主要是矿石和焦炭,其中矿石中的有害元素是炼铁行业所面临的主要问题之一。
在高炉生产过程中,烧结矿中的有害元素会对炉内的化学反应产生影响,造成炉料堵塞、炉墙侵蚀、炉渣品质下降等问题,对炉子运行、产量及铁水质量带来危害。
烧结矿中的有害元素的来源一般是矿石中所含的有害元素,如硫、磷、铜、锌、镍等,还有烧结过程中吸附的有害元素,如氯、碱金属等。
二、烧结矿中有害元素对高炉的危害1、硫硫是烧结矿中最主要的有害元素之一。
当硫进入高炉中,它会与铁、焦炭发生反应,形成铁硫化物,交互作用会导致炉内温度下降,燃烧失调,炉渣流动性差等问题。
同时,硫还会造成铁水质量下降,甚至导致铸造中铁铸件断裂、孔洞等问题,严重影响了炼铁质量。
2、磷磷在烧结矿中常以磷酸化合物的形式存在,当烧结矿中的磷含量超过一定的限制时,容易对产生偏铁鱼、振落、炉墙侵蚀及炉气特性发生影响。
另外磷含量超过限制时,也会导致炼铁成本增加,因为过多的磷需要通过钙、镁等不含磷的材料来削减。
3、铜、锌、镍等烧结矿中还含有一些其他有害元素,如铜、锌、镍等,它们能够影响生铁的质量,因为这些元素会妨碍所需的化学反应的进行和生铁的结晶行为。
如果烧结矿中含有太多的这些元素,那么将会导致生铁中这些元素的含量增加,这将会影响这些元素的终末用途,从而限制产生符合标准的产品。
三、抑制烧结矿中有害元素的措施为了减少烧结矿中有害元素对高炉带来的危害,需要采取措施,抑制这些元素的含量,以确保高炉的正常运行和冶炼质量。
目前,常用的方法是采取改善烧结的工艺条件、精选矿石、还原剂等,以及加入一些抑制剂来减少有害元素的含量。
炼铁高炉入炉原料中有害微量元素分析解决方案工作报告
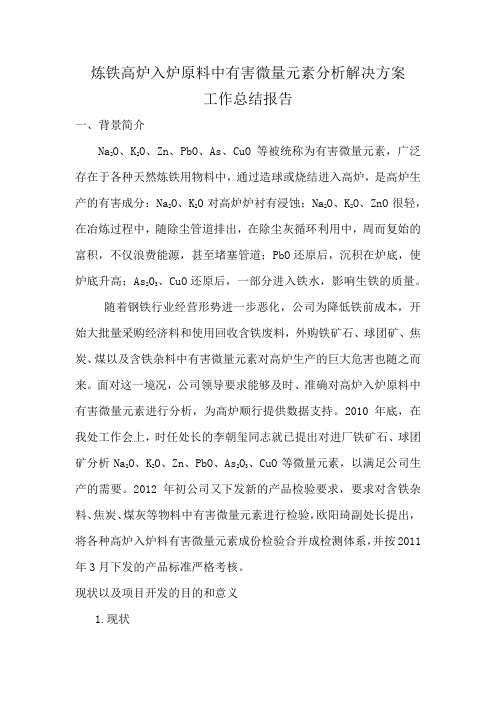
炼铁高炉入炉原料中有害微量元素分析解决方案工作总结报告一、背景简介Na2O、K2O、Zn、PbO、As、CuO等被统称为有害微量元素,广泛存在于各种天然炼铁用物料中,通过造球或烧结进入高炉,是高炉生产的有害成分:Na2O、K2O对高炉炉衬有浸蚀;Na2O、K2O、ZnO很轻,在冶炼过程中,随除尘管道排出,在除尘灰循环利用中,周而复始的富积,不仅浪费能源,甚至堵塞管道;PbO还原后,沉积在炉底,使炉底升高;As2O3、CuO还原后,一部分进入铁水,影响生铁的质量。
随着钢铁行业经营形势进一步恶化,公司为降低铁前成本,开始大批量采购经济料和使用回收含铁废料,外购铁矿石、球团矿、焦炭、煤以及含铁杂料中有害微量元素对高炉生产的巨大危害也随之而来。
面对这一境况,公司领导要求能够及时、准确对高炉入炉原料中有害微量元素进行分析,为高炉顺行提供数据支持。
2010年底,在我处工作会上,时任处长的李朝玺同志就已提出对进厂铁矿石、球团矿分析Na2O、K2O、Zn、PbO、As2O3、CuO等微量元素,以满足公司生产的需要。
2012年初公司又下发新的产品检验要求,要求对含铁杂料、焦炭、煤灰等物料中有害微量元素进行检验,欧阳琦副处长提出,将各种高炉入炉料有害微量元素成份检验合并成检测体系,并按2011年3月下发的产品标准严格考核。
现状以及项目开发的目的和意义1.现状(1)Na2O、K2O、Zn、PbO、As、CuO等检验项目在各种物料中的含量都很微少,想要准确测定微量或痕量的元素,一般都采用ICP分析或原子吸收分析方法。
这两种方法首先都需对待分析样品进行溶解,溶解的过程比较漫长,分析过程稍有差池就会造成分析失败,检验周期长、操作复杂也是这两种方法不可避免的缺点,对于大批量的进厂铁矿石、球团矿、焦炭、煤灰、含铁废料检验,已很难适应快速生产节奏的需要。
(2)X荧光仪分析速度快、对样品要求相对简单,在2011年已成功开发出铁矿石、球团矿微量元素快速分析方法,但该方法只适用于物质成份含量简单且相对稳定的铁矿石品种,焦炭、煤灰、含铁杂料等新品种因物相组成不同、成份结构复杂,不能简单用一种方法分析检验,需要一整套的系列分析解决方案,有针对性的对各种物料使用最为合适的分析方法。
高炉有害元素分析及控制

高炉有害元素分析及控制摘要:由于成矿原因和炼铁原料来源复杂,炼铁原料中含有锌杂质,因锌有害于高炉炼铁,要求入炉原料中锌含量应分别小于0.15 kg/t,而我国很多钢厂入炉原料中锌含量高于此标准。
近年来,国内钢铁产能过剩,钢铁价格持续低迷,钢企为节省成本少用国外铁矿石,多用周边品质差、价格低廉的国产矿石替代,使得有些高炉锌危害更加突出。
基于此,本文主要分析高炉内锌的主要来源以及对高炉的危害,提出了控制有害元素的措施和建议。
关键词:高炉炼铁;有害元素;锌元素;分析控制1锌在高炉中的行为机理1.1高炉内的循环铁矿石中的锌少量主要以铁酸盐(ZnO•Fe2O3)硅酸盐(2ZnO•SiO2)及硫化物(ZnS)的形式存在。
其锌硫化物先转化为复杂的氧化物,然后再在大于1000℃的高温区被CO还原为气态。
沸点为907℃时,加热为蒸汽,随煤气上升,到达温度较低的区域(580℃)时冷凝而再氧化。
再氧化形成的锌氧化细粒附着于上升煤气的粉尘时就被带出炉外,附着于下降的炉料时就再次进入高温区。
如此周而复始,就形成了在高炉内的富集现象。
1.2高炉内部的富集含矿物进入高炉后生成,固态ZnO,随炉料下降过程中被C、CO和Fe还原。
在高炉下部1000℃以上的高温区,ZnO还原出来的Zn全部被汽化为蒸汽分散于煤气中并随之上升,蒸汽到达高炉上部低温区时冷凝而再被氧化形成ZnO细粒,一部分随煤气从炉顶逸出炉外,一部分附着于下降的炉料再次进入高温区重新被还原和汽化,周而复始,形成了在高炉内的锌循环富集现象。
在高炉内的循环富集量可达到入炉料含量的10~30倍。
1.3在烧结、高炉系统间的循环富含锌元素的高炉煤气除尘灰被回收,用于烧结配料,含锌的烧结作为炼铁主原料重新进入高炉,形成了锌在烧结、高炉系统间的循环。
2锌对高炉危害2.1锌对高炉耐材及风口的破坏Zn被还原后,在>907℃时成为锌蒸汽,进入煤气中,渗入高炉上部耐材的缝隙,氧化后使其体积膨胀,破坏高炉上部的炉墙结构,严重时甚至可以导致炉壳胀裂,使煤气泄漏,造成一系列恶性事故。
有害元素对高炉炼铁的影响及控制措施
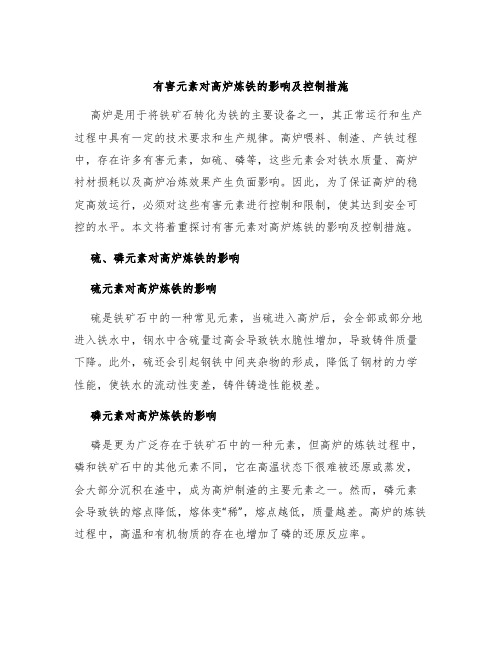
有害元素对高炉炼铁的影响及控制措施高炉是用于将铁矿石转化为铁的主要设备之一,其正常运行和生产过程中具有一定的技术要求和生产规律。
高炉喂料、制渣、产铁过程中,存在许多有害元素,如硫、磷等,这些元素会对铁水质量、高炉衬材损耗以及高炉冶炼效果产生负面影响。
因此,为了保证高炉的稳定高效运行,必须对这些有害元素进行控制和限制,使其达到安全可控的水平。
本文将着重探讨有害元素对高炉炼铁的影响及控制措施。
硫、磷元素对高炉炼铁的影响硫元素对高炉炼铁的影响硫是铁矿石中的一种常见元素,当硫进入高炉后,会全部或部分地进入铁水中,钢水中含硫量过高会导致铁水脆性增加,导致铸件质量下降。
此外,硫还会引起钢铁中间夹杂物的形成,降低了钢材的力学性能,使铁水的流动性变差,铸件铸造性能极差。
磷元素对高炉炼铁的影响磷是更为广泛存在于铁矿石中的一种元素,但高炉的炼铁过程中,磷和铁矿石中的其他元素不同,它在高温状态下很难被还原或蒸发,会大部分沉积在渣中,成为高炉制渣的主要元素之一。
然而,磷元素会导致铁的熔点降低,熔体变“稀”,熔点越低,质量越差。
高炉的炼铁过程中,高温和有机物质的存在也增加了磷的还原反应率。
控制措施在高炉炼铁的生产过程中,有害元素的控制是必不可少的一环。
下面将介绍一些常用的控制措施。
调整原料成分高炉熟料中的有害元素主要来源于铁矿石中,而铁矿石的含硫、含磷量的高低对高炉冶炼过程有很大的影响。
因此,一个有效的控制措施就是调整原料成分。
可以根据熟料化验分析结果预先掌握熟料成分,对成分含有过高有害元素的铁矿石进行挑选和筛选,或者采用掺混矿的方法控制高炉熟料的含硫、含磷量。
清洗高炉和加入流化剂在高炉生产过程中,很多有害元素都会在炉壁上结合和析出。
为了保证高炉正常运行和生产,必须定期对高炉进行清洗。
此外,加入流化剂,可以起到一定的促进还原反应和控制有害元素的效果。
在加入流化剂的过程中,可以调整流化剂的配比和添加时间,以达到较好的控制效果。
炼铁危险有害因素的控制措施炼铁危险有害因素的控制措施

炼铁危险有害因素的控制措施炼铁危险有害因素的控制措施(1)防止灼烫伤害防止灼烫伤害主要是要防止爆炸事故的发生。
煤气爆炸:预防的办法是将煤气放散到大气中,切断高炉与煤气系统的联系,并向炉顶及除尘器内通入蒸汽,保持正压力。
铁水穿漏:防止铁水穿漏和爆炸的措施是当铁水量减少不多,并确信铁水还未跑到炉外时,就加强冷却有浇穿危险的部位,并在炉周清除潮湿,用干沙填充。
在当发现铁水已泄漏出,还未发生爆炸,或者出铁量减少一半时,应立即休风使漏出铁水凝固,在确信铁水已凝固以后再进行检修。
在停炉时要尽可能地将渣铁出尽以减少炉底的静压力,同时所有工作人员应离开炉子。
并设立警卫人员不让任何人接近有危险的地区。
出铁出渣防爆:高温铁水及熔渣遇水时,水会被加热而迅速汽化产生爆炸,应采取措施防止铁水及熔渣遇水。
(2)防止机械伤害高炉出铁场和修理场焦炉机侧和焦侧作业频繁,环境复杂,必须建立严格安全确认制度,各种机械设备应确认周围环境和人员安全后,方可作业或移动。
2人或2人以上同机作业,必须有相应的协同配合制度和措施。
在生产中处理故障和异常或进行检修时,如机械设备中有可能移动、滑动的部件,必须采取安全可靠的固定措施后方能进行作业;对可能移动、滑动的危险方位或危险区域,应设立警戒牌或明显的警告标志。
(3)防止起重伤害起重机械及吊运作业事故频率高,伤害严重程度大,必须全面强化起重机械及作业的安全管理。
吊配合标准化,强化和推进起重和指吊标准化作业。
车安全装置齐全可靠。
根据现场产品和吊物吊挂作业的特性、特点,设置和制作各种安全可靠的安全专用的吊索吊具。
提高其中专业人员的安全素质,强化其中作业人员的特种作业培训教育。
(4)粉尘控制新建、改建的大高炉炉前渣沟、铁沟及水冲渣沟,应设活动封盖和相应的除尘装置。
中小型高炉应逐步达到上述要求。
碾泥室内应有良好的通风除尘设备。
(5)有毒有害气体控制煤气危险区域宜设置固定式一氧化碳检测报警装置。
炉顶放散管应设点火装置,在高炉休风时点燃炉顶煤气,使煤气在休风时能连续燃烧。
高炉有害元素研究
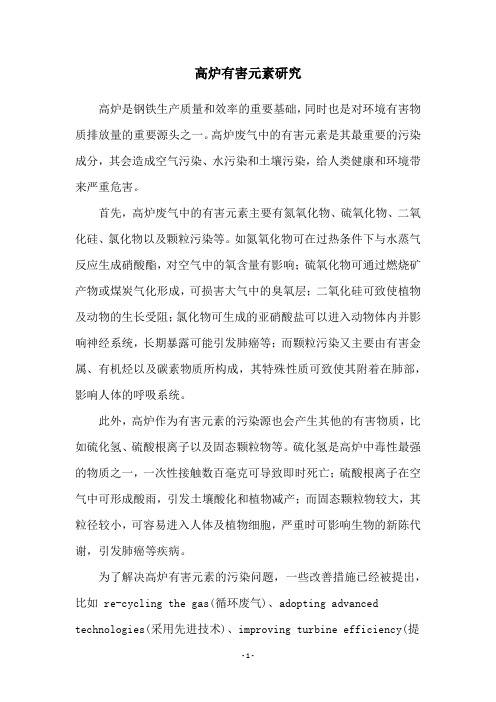
高炉有害元素研究高炉是钢铁生产质量和效率的重要基础,同时也是对环境有害物质排放量的重要源头之一。
高炉废气中的有害元素是其最重要的污染成分,其会造成空气污染、水污染和土壤污染,给人类健康和环境带来严重危害。
首先,高炉废气中的有害元素主要有氮氧化物、硫氧化物、二氧化硅、氯化物以及颗粒污染等。
如氮氧化物可在过热条件下与水蒸气反应生成硝酸酯,对空气中的氧含量有影响;硫氧化物可通过燃烧矿产物或煤炭气化形成,可损害大气中的臭氧层;二氧化硅可致使植物及动物的生长受阻;氯化物可生成的亚硝酸盐可以进入动物体内并影响神经系统,长期暴露可能引发肺癌等;而颗粒污染又主要由有害金属、有机烃以及碳素物质所构成,其特殊性质可致使其附着在肺部,影响人体的呼吸系统。
此外,高炉作为有害元素的污染源也会产生其他的有害物质,比如硫化氢、硫酸根离子以及固态颗粒物等。
硫化氢是高炉中毒性最强的物质之一,一次性接触数百毫克可导致即时死亡;硫酸根离子在空气中可形成酸雨,引发土壤酸化和植物减产;而固态颗粒物较大,其粒径较小,可容易进入人体及植物细胞,严重时可影响生物的新陈代谢,引发肺癌等疾病。
为了解决高炉有害元素的污染问题,一些改善措施已经被提出,比如 re-cycling the gas(循环废气)、adopting advanced technologies(采用先进技术)、improving turbine efficiency(提高汽轮机效率)、heat recovery(热回收)以及 using heat-resistant materials(使用耐热材料)等。
其中,采用循环废气技术可以重复利用污染物,减少污染的产生;而采用先进技术则可有效提高锅炉的效率,减少使用能源;同时,采用热回收技术可有效恢复热能,减少热量损失;此外,选用耐热材料也可以减少有害物质的排放,达到节能减排的目的。
总之,钢铁行业中高炉有害元素的污染越来越受到重视,相关政策及法规也将持续不断的完善。
冶炼中有害元素注意事项
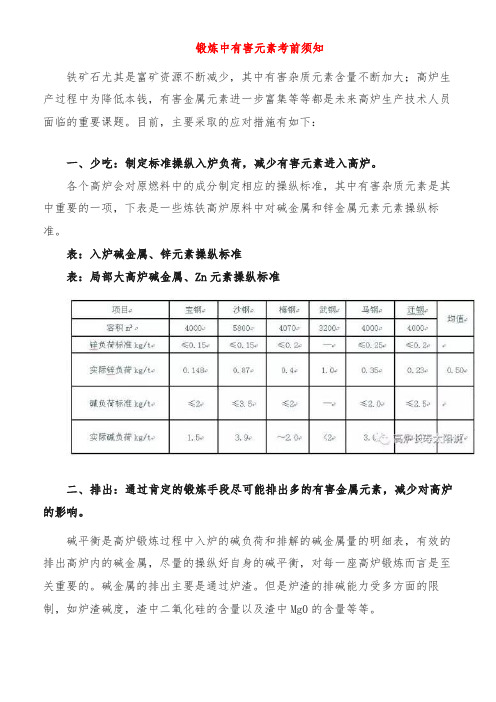
锻炼中有害元素考前须知铁矿石尤其是富矿资源不断减少,其中有害杂质元素含量不断加大;高炉生产过程中为降低本钱,有害金属元素进一步富集等等都是未来高炉生产技术人员面临的重要课题。
目前,主要采取的应对措施有如下:一、少吃:制定标准操纵入炉负荷,减少有害元素进入高炉。
各个高炉会对原燃料中的成分制定相应的操纵标准,其中有害杂质元素是其中重要的一项,下表是一些炼铁高炉原料中对碱金属和锌金属元素元素操纵标准。
表:入炉碱金属、锌元素操纵标准表:局部大高炉碱金属、Zn元素操纵标准二、排出:通过肯定的锻炼手段尽可能排出多的有害金属元素,减少对高炉的影响。
碱平衡是高炉锻炼过程中入炉的碱负荷和排解的碱金属量的明细表,有效的排出高炉内的碱金属,尽量的操纵好自身的碱平衡,对每一座高炉锻炼而言是至关重要的。
碱金属的排出主要是通过炉渣。
但是炉渣的排碱能力受多方面的限制,如炉渣碱度,渣中二氧化硅的含量以及渣中Mg0的含量等等。
有分析认为:炉渣排碱能力好的时候可以排出入炉碱量的95%,差的时候却只有65-80%。
而从炉顶煤气及炉尘排出的碱金属量少且波动很小,波动一般小于S%。
其中Zn、Pb无法通过炉渣排出,只能限制入炉数量。
例如:将高炉布袋灰、炼钢污泥等不再参加烧结矿。
对于碱金属的排出,主要手段是降低炉渣碱度,是K2O,Na2O与SiO2结合形成硅酸盐随炉渣排出炉外。
从理论上分析,为排解90%以上的碱,炉渣碱度应操纵在0.85-0.90;降低炉渣碱度的同时提高渣中〔MgO〕含量以同时满足排碱脱硫的要求,在三元碱度m〔CaO+MgO〕/m〔SiO2〕保持不变时用5%MgO替代5%CaO,炉渣排碱能力可提高20%。
在实际生产过程中不可能完全按照此方法进行,需要兼顾经济效益和排碱效果,往往采纳定期排碱操作,适度降低炉内碱金属富集。
高炉制定的排碱技术方案节选如下:1、排碱实施技术方案:〔1〕11月27日8:00,高炉调整炉料结构,两座高炉实际炉渣碱度降至1.11~1.14,高炉开始排碱。
有害元素对高炉炼铁的影响及控制措施
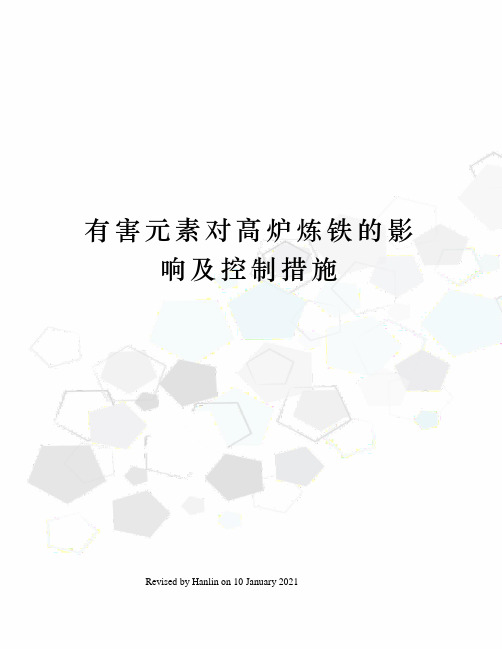
有害元素对高炉炼铁的影响及控制措施Revised by Hanlin on 10 January 2021有害元素对高炉炼铁的影响及控制措施l引言高炉炼铁原料中的有害元素主要有铅、锌、碱金属等。
锌在高炉内循环富集已严重影响高炉顺行和热制度稳定,渗入炉衬的zn蒸汽在炉衬内冷凝下来,造成高炉炉缸炉底砖衬上涨,风口大套上翘开裂、中套上翘变形、炉皮开裂、炉缸水温差上升等一系列后果,严重危害一代高炉寿命。
通过控制入炉原料有害元素含量,优化高炉操作,减少有害元素在高炉内循环富集,取得一定效果。
本文以新钢8#1050m。
高炉为例。
2有害元素的来源通过对原燃料检测成份分析可以看出,碱金属来源主要来焦炭,其次是烧结矿和球团矿,而zn的来源,主要是山上球团厂球团矿和烧结矿。
zn 的主要来源是生产烧结矿、球团矿的精矿粉,不法商贩将瓦期灰回收来的金属料加入精矿粉中,使原料Zn含量大大提高。
3对高炉的影响(1)有害元素破坏砖衬及炉体。
2004年3月份开始,陆续发现风口中套变形,继而出现大套法兰上翘开裂套冒煤气现象,并伴随煤气泄漏明显发展最终造成炉缸炉皮开裂。
(2)造成炉皮开裂,冷却板损坏。
由于有害元素在炉内富集,在炉身中下部软融带附近,有害元素吸附或渗透进入砖缝,造成砖衬被侵蚀和异常膨胀,使冷却板暴露在高温气流中易受冲击而损坏。
随着原燃质量下降,有害元素入炉增加,在内的富集增加,对砖衬的破坏力度加大。
造成炉皮开裂的主要原因是使用含Zn高的原料的结果,从风口粘结物取样分析可知,zn在炉知富集是造成炉缸炉皮开裂的主要原因。
(3)均压、管路堵塞。
由于zn含量大幅增加,随煤气排出的zn增加,随煤气逸出的zn元素,在均压管管路中凝集,造成管路堵塞。
2006年问_次发生管路堵塞现象,经过吹扫管路,立刻恢复正常均压。
(4)造成炉缸,炉底侵蚀速度加快。
碱金属,zn等有害元素易在炉内循环富集,K、Na以液态或固态粉状化合物粘附在炉衬上破坏砖衬,zn则以蒸汽形式渗入砖衬缝隙中,冷凝氧化成ZnO后体积膨胀损坏内衬,使高温铁水能够顺利渗入砖缝,造成水温差上升。
- 1、下载文档前请自行甄别文档内容的完整性,平台不提供额外的编辑、内容补充、找答案等附加服务。
- 2、"仅部分预览"的文档,不可在线预览部分如存在完整性等问题,可反馈申请退款(可完整预览的文档不适用该条件!)。
- 3、如文档侵犯您的权益,请联系客服反馈,我们会尽快为您处理(人工客服工作时间:9:00-18:30)。
编号:SM-ZD-70823
有害元素对高炉炼铁的影
响及控制措施
Through the process agreement to achieve a unified action policy for different people, so as to coordinate action, reduce blindness, and make the work orderly.
编制:____________________
审核:____________________
批准:____________________
本文档下载后可任意修改
有害元素对高炉炼铁的影响及控制
措施
简介:该方案资料适用于公司或组织通过合理化地制定计划,达成上下级或不同的人员之间形成统一的行动方针,明确执行目标,工作内容,执行方式,执行进度,从而使整体计划目标统一,行动协调,过程有条不紊。
文档可直接下载或修改,使用时请详细阅读内容。
l 引言
高炉炼铁原料中的有害元素主要有铅、锌、碱金属等。
锌在高炉内循环富集已严重影响高炉顺行和热制度稳定,渗入炉衬的zn蒸汽在炉衬内冷凝下来,造成高炉炉缸炉底砖衬上涨,风口大套上翘开裂、中套上翘变形、炉皮开裂、炉缸水温差上升等一系列后果,严重危害一代高炉寿命。
通过控制入炉原料有害元素含量,优化高炉操作,减少有害元素在高炉内循环富集,取得一定效果。
本文以新钢8#1050m。
高炉为例。
2 有害元素的来源
通过对原燃料检测成份分析可以看出,碱金属来源主要来焦炭,其次是烧结矿和球团矿,而zn的来源,主要是山上球团厂球团矿和烧结矿。
zn的主要来源是生产烧结矿、球团
矿的精矿粉,不法商贩将瓦期灰回收来的金属料加入精矿粉中,使原料Zn含量大大提高。
3 对高炉的影响
(1)有害元素破坏砖衬及炉体。
20xx年3月份开始,陆续发现风口中套变形,继而出现大套法兰上翘开裂套冒煤气现象,并伴随煤气泄漏明显发展最终造成炉缸炉皮开裂。
(2)造成炉皮开裂,冷却板损坏。
由于有害元素在炉内富集,在炉身中下部软融带附近,有害元素吸附或渗透进入砖缝,造成砖衬被侵蚀和异常膨胀,使冷却板暴露在高温气流中易受冲击而损坏。
随着原燃质量下降,有害元素入炉增加,在内的富集增加,对砖衬的破坏力度加大。
造成炉皮开裂的主要原因是使用含Zn高的原料的结果,从风口粘结物取样分析可知,zn在炉知富集是造成炉缸炉皮开裂的主要原因。
(3)均压、管路堵塞。
由于zn含量大幅增加,随煤气排出的zn增加,随煤气逸出的zn元素,在均压管管路中凝集,造成管路堵塞。
20xx年问_次发生管路堵塞现象,经过吹扫管路,立刻恢复正常均压。
(4)造成炉缸,炉底侵蚀速度加快。
碱金属,zn等有害元
素易在炉内循环富集,K、Na以液态或固态粉状化合物粘附在炉衬上破坏砖衬,zn则以蒸汽形式渗入砖衬缝隙中,冷凝氧化成ZnO后体积膨胀损坏内衬,使高温铁水能够顺利渗入砖缝,造成水温差上升。
(5)破坏焦炭强度,炉况顺行度下降。
碱金属的吸附首先从焦炭的气孔开始,而后逐步向焦炭内部扩散随着焦炭在碱金属蒸汽内暴露的时间延长,碱金属的吸附量逐渐增多,焦炭基质部分扩散的碱金属会侵蚀到石墨晶体内部,破坏原有的结构,使焦炭产生较大的体积膨胀,导致焦炭破碎,焦炭反应性增加,反应后强度降低。
20xx年高炉碱负荷达6.Okg /t铁左右,由于缺乏处理经验,使碱金属在炉内富集,破坏焦炭强度,炉况顺行度很差,通过采用高压操作,降低碱度,增加渣r}~MgO含量等措施排碱后,碱金属的危害逐步降低,炉况顺行度逐步好转,20xx年虽然碱负荷仍高达5.Okg /t铁左右,由于措施得当,高炉顺行度朱受到影响。
4 采取的措施
(1)减少zn元素入炉量。
制定严恪的原燃料采购标准,尽可然采川低锌原料,减少入炉锌量。
(2)增加烧结矿中Mgo含量。
考虑到碱金属对高炉带来许多不利因素,通过提渣中Mgo含量可降低渣中K,0、Na 的活度,提高炉渣排碱能力。
烧结矿Mgo含量原来的2.3%左右提高到日前的2.8%左右,使得日前炉渣Mgo含量由原来的7.O%左右提高到目前的9.O~10.O%。
(3)控制好炉渣碱度。
通过降低炉渣碱度到1.O5~1.15之间,炉渣流动性良好,对排碱有利。
(4)优化操作,提铁水质量,通过攻关等一系列措施,优化高炉操作。
20xx年以来,优质晶率保持在较高的水平,20xx年2月份至今一级品率基本在90%以上铁水粘度增加,流动性下降,使l150℃等温线上移,有效保护炉缸,使水温差稳定在1.4℃左右。
(5)采用钒钛矿护炉。
虽然目前水温差已下降到1.4℃左右,但受炉的变化、炉温波动等囚素影响,水温差也有较大波动,为确保炉缸工作稳定,保护内衬,20xx年6月份始开始用钒钛矿护炉,TiO入炉量维持在5kg/t铁左右,使用钒钛矿护炉以后,水温差稳定性明显好转,炉底温度也有所下降。
(6)合理控制气流分布。
根据炉衬温度的变化情况以及炉况表现,通过疏松边缘等措施,防止炉墙结厚,同时及时调整负荷,减少粘结物对高炉生产的影响。
(7)高炉灌浆。
针对8#高炉炉体实际情况,对高炉风口区及炉缸采用高压灌浆,压入无水泥桨,填充缝隙,有效阻止有害元素的入侵。
(8)定期对均压管路吹扫,确保管路畅通。
5 效果
通过采取一系列措施,有效控制了仃害元素对高炉带来的影响,目前,8#高炉炉况稳定顺行,炉缸水温差、炉衬温度稳定,各项技术经济指标有所改善。
这里填写您的企业名字
Name of an enterprise。