炭化室结焦过程(1)
应用化工技术炼焦学考试重点
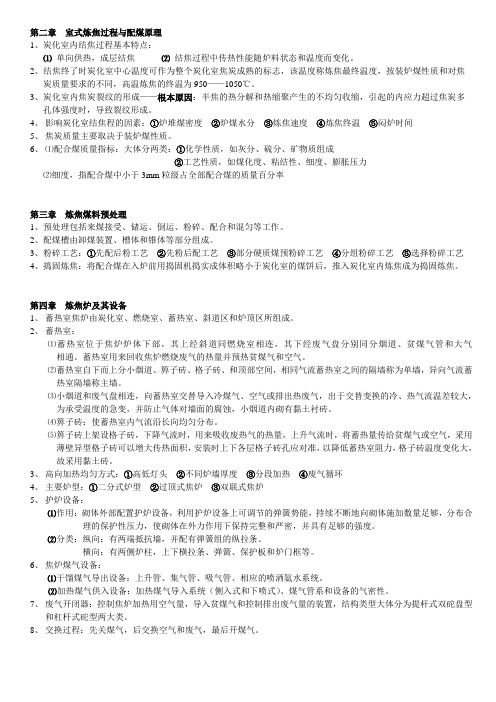
第二章室式炼焦过程与配煤原理1、炭化室内结焦过程基本特点:⑴单向供热,成层结焦⑵结焦过程中传热性能随炉料状态和温度而变化。
2、结焦终了时炭化室中心温度可作为整个炭化室焦炭成熟的标志,该温度称炼焦最终温度,按装炉煤性质和对焦炭质量要求的不同,高温炼焦的终温为950——1050℃。
3、炭化室内焦炭裂纹的形成——根本原因:半焦的热分解和热缩聚产生的不均匀收缩,引起的内应力超过焦炭多孔体强度时,导致裂纹形成。
4、影响炭化室结焦程的因素:①炉堆煤密度②炉煤水分③炼焦速度④炼焦终温⑤闷炉时间5、焦炭质量主要取决于装炉煤性质。
6、⑴配合煤质量指标:大体分两类:①化学性质,如灰分、硫分、矿物质组成②工艺性质,如煤化度、粘结性、细度、膨胀压力⑵细度,指配合煤中小于3mm粒级占全部配合煤的质量百分率第三章炼焦煤料预处理1、预处理包括来煤接受、储运、倒运、粉碎、配合和混匀等工作。
2、配煤槽由卸煤装置、槽体和锥体等部分组成。
3、粉碎工艺:①先配后粉工艺②先粉后配工艺③部分硬质煤预粉碎工艺④分组粉碎工艺⑤选择粉碎工艺4、捣固炼焦:将配合煤在入炉前用捣固机捣实成体积略小于炭化室的煤饼后,推入炭化室内炼焦成为捣固炼焦。
第四章炼焦炉及其设备1、蓄热室焦炉由炭化室、燃烧室、蓄热室、斜道区和炉顶区所组成。
2、蓄热室:⑴蓄热室位于焦炉炉体下部,其上经斜道同燃烧室相连,其下经废气盘分别同分烟道、贫煤气管和大气相通。
蓄热室用来回收焦炉燃烧废气的热量并预热贫煤气和空气。
⑵蓄热室自下而上分小烟道、箅子砖、格子砖、和顶部空间,相同气流蓄热室之间的隔墙称为单墙,异向气流蓄热室隔墙称主墙。
⑶小烟道和废气盘相连,向蓄热室交替导入冷煤气、空气或排出热废气,出于交替变换的冷、热气流温差较大,为承受温度的急变,并防止气体对墙面的腐蚀,小烟道内砌有黏土衬砖。
⑷箅子砖:使蓄热室内气流沿长向均匀分布。
⑸箅子砖上架设格子砖,下降气流时,用来吸收废热气的热量,上升气流时,将蓄热量传给贫煤气或空气,采用薄壁异型格子砖可以增大传热面积,安装时上下各层格子砖孔应对准,以降低蓄热室阻力,格子砖温度变化大,故采用黏土砖。
炼焦过程与配煤原理

本章内容:
第一节 第二节 第三节 第四节 炭化室内结焦过程特点 影响炭化室结焦过程的因素 配合煤的质量 配煤原理
第一节 炭化室内结焦过程特点
特点:1、单向供热,成层结焦;
2、结焦过程中的传热性能随炉料的状态和温度而变
化
一、温度变化与炉料动态
1、成层结焦过程与炼焦最终温度 由于单向供热,且炉料导热系数低,故在结焦过程的大 部分时间内炭化室中心面法线方向上炉料内温度梯度较大。 在同一时间内,离炭化室墙面不同距离的各层煤料因温度不
二、各层温度梯度、升温速度和焦炭质量
由以上的讨论可知,各层的温度梯度和升温速度不同, 因此 导致各层焦炭的质量也有一定的差异,如图所示。 靠近炉墙的煤料,温度梯度大,升温速度快,塑性温度区间 变宽,塑性体内煤热解产物之间作用改善,从而改善了焦炭
质量:真密度、导电率、显微强度增大,气孔率降低,反应
性降低,反应后强度提高。但裂纹深、粒度小。熔融性好, 致密。靠近炉墙面的焦炭面扭曲如菜花俗称占全部 配合煤的质量百分数。 常规炼焦时约为72~80%; 配型煤炼焦时约为85%; 捣固炼焦时应大于90%。 7、膨胀压力 膨胀压力与粘结性指标间不存在规律的 相关关系,只能实测。
G
焦煤
肥煤
瘦煤
气煤
Vdaf 配煤原理图
第四节 配煤原理
一、胶质层重叠原理 该原理要求配合煤中各单种煤的胶质体的 软化区间和温度间隔能较好的搭接,这样可使 配合煤料在炼焦过程中能在较大的温度范围内 处于塑性状态,从而改善粘结过程,并保证焦 炭的结构均匀性。不同的牌号的炼焦煤的塑性 温度区间如图所示。
定义:ΔS =G焦S焦) /(G煤×S煤) =(G焦/ G煤) × (S焦/S煤) = K × (S焦/S煤) 一般ΔS = 0.6--0.7, 即煤中的硫有60--70%转入焦炭中。 G气×S气 G煤×S煤 所以,S焦 = S煤×ΔS/K 焦 炉 式中:S焦——焦炭硫分,% S煤——入炉煤硫分,%; K——全焦率,%, 一般为74—75%。 K =G焦/ G煤 所以ΔS/K = 0.8--0.93, 即S焦/S煤 = 0.8--0.93
第二章 室式炼焦过程与配煤原理

第二章室式炼焦过程与配煤原理煤结焦过程的一般规律如《煤化学》所述,本章以室式炼焦工艺为对象,阐述炭化室内结焦过程的特点,进而讨论配合煤质量指标、配煤原理与焦炭质量预测。
第一节,尽化室内结焦过程特点炭化室内结焦过程的基本特点有二:一是单向供热、成层结焦;二是结焦过程中的传热性能随炉料状态和温度而变化。
基于此,炭化室内各部位焦炭质量与特征有所差异。
一、温度变化与炉料状态1.成层结焦过程- 炭化室内煤料热分解、形成塑性体、转化为半焦和焦炭所需的热量,由两侧炉墙提供,由于煤和塑性体的导热性很差,使从炉墙到炭化室的各个平行面之间温度差较大。
因此,在同一时间,离炭化室墙面不同距离的各层炉料因温度不同而处于结焦过程的不同阶段(图2-1右),焦炭总是在靠近炉墙处首先形成,而后逐渐向炭化室中心推移,这就是“成层结焦”,当炭化室中心面上最终成焦并达到相应温度时,炭化室结焦才终了,因此结焦终了时炭化室中心温度可作为整个炭化室焦炭成熟的标志,该温度称炼焦最终温度,按装炉煤性质和对焦炭质量要求的不同,该温度为950~1050。
2.炭化室炉料的温度分布√在同一结焦时刻内处于不同结焦阶段的各层炉料,由于热物理性质(比热、热导率、相变热等)和化学变化(包括反应热) 的不同,传热量和吸热量也不同,因此炭化室内的温度场是不均匀的。
图2—1左给出的等时线,标志着同一结焦时刻从炉墙初炭化室中心的温度分布;图2—1的等时线也可改绘制成以离炭化室墙的距离x和结焦时刻τ为坐标的等温(t)线(图2—2) 或以t-τ为坐标的等距线。
在图2—2中,两条等温线的温度图2一l 不同结焦时刻炭化室内各层炉料的状态和温度(等时线).图2-2 炭化室内炉料等温线差为Δt,两条等温线间的水平距离为时间差Δτ,垂直距离为距离差Δx。
Δt/Δτ表示升温速度,Δt/Δx表示温度梯度。
综合图2-1和2-2可以说明如下几点:1)任一温度区间,各层的升温速度和温度梯度均不相同。
炼焦作业

第二章 室式炼焦过程与配煤工艺

第二章室式炼焦过程与配煤工艺第一节煤在焦炉炭化室内的结焦过程一、炭化室内炉料的动态变化焦炉的炭化室是一个带锥度的窄长空间,煤料受两侧炉墙传递的热量加热,下面我们分析炼焦过程及其特点,并由此分析炭化室内各部位焦炭质量与特征。
1、成层结焦与温度变化在煤化学中我们知道,粘结性煤加热过程中,经历了干燥、热分解、形成塑性体、转化为半焦和焦炭的过程。
过程所需要的热量,由两侧炉墙提供。
绘出图(表明两侧加热),因煤和塑性层导热系数低,因此在整个成焦过程的大部分时间内,炭化室内与炉墙垂直方向上炉料的温度梯度较大(图2-1左)。
这样在结焦过程的大部分时间内,离炭化室墙面不同距离的各层炉料因所受到的温度不同而处于热解过程的不同阶段,整个炭化室内炉料的状态随时间而变化(图2-1右)。
靠近炉墙附近的煤先结成焦炭,而后焦炭层逐渐向炭化室中心推移,这就是常指的“成层结焦”。
炭化室中心面上的炉料温度始终最低,因此以结焦末期炭化室中心面的温度(焦饼中心温度)作为焦饼成熟度的标志,称为炼焦最终温度。
如图2-2所示,由于各层炉料距炉墙的距离不同,传热条件也就各不相同,最靠近炉墙的煤料升温速度最快,约5℃/min 以上,而位于炭化室中心部位的炉料升温速度最慢,约2℃/min以下,这种温度变化的差别必然导致焦炭质量的差异。
常规炼焦采用湿煤装炉,结焦过程中湿煤层被夹在两个塑性层之间,这样湿煤层内的水汽不易透过塑性层向两层外流出,致使大部水汽窜入内层湿煤中,并因内层温度低而冷凝下来,这样内层湿煤水分增加,加之煤的导热系数小,使得炭化室内中心煤料升温速度缓慢,长时间停留在水的蒸发温度以下,煤料水分愈多,结焦时间就愈长,炼焦的耗热量也就愈大。
2、炭化室内膨胀压力焦炉炭化室内产生膨胀压力的原因是成层结焦的结果,两个大体上平行于两侧炉墙面的塑性层从两侧向炭化室中心移动,炭化室底面温度和顶部温度也很高,在炭化室内煤料的上层和下层同样也形成塑性层,围绕中心煤料形成的塑性层如同一个膜袋(见图2-3),膜袋内的煤热解产生气体由于塑性层的不透气性使得膜袋产生膨胀的趋势,塑性层又通过外侧的半焦层和焦炭层将压力施加于炭化室的炉墙,这种压力称之为膨胀压力。
煤炭焦化
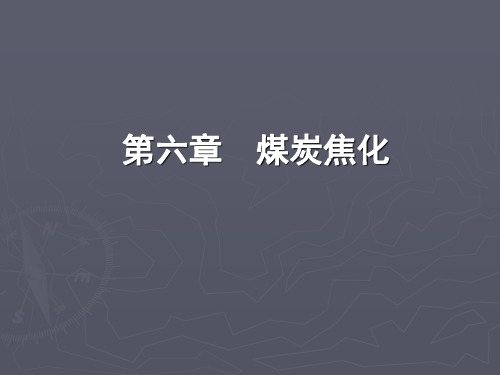
我国冶金焦炭质量标准
类别 I II III 抗碎强度 % ≥92.0 88.1~ 92.0 83.0~ 88.0 耐磨强度 % ≤7.0 ≤8.5 ≤10.5 灰分 % ≤12 ≤12.01~ 13.50 13.51~ 15.0 硫分 % ≤0.6 0.61~ 0.8 0.81~1.0 挥发分 % ≤1.9 ≤1.9 ≤1.9
第六章
煤炭焦化
概 述
1、粘结性煤在隔绝空气 的条件下加热至1000℃ 左右(高温干馏),得 到多孔性固体块状物— —焦炭。此过程称为煤 的焦化,所得到的最终 产物有焦炭、煤气和煤 焦油等, 2、炼焦化学产品:
名称
焦炭
焦炉煤气 焦油 粗笨 氨 硫磺
产率%
72-76
15-19 3.5-4.2 0.8-1.4 0.22-0.25 0.3-0.6
1—炭化室; 2—炉头; 3—隔墙; 4—立火道 炭化室的高度一般 4~6米,宽度450毫米 燃烧室的温度1300℃ 炭化室的温度1100℃
⑵蓄热室
1—主墙; 2—小烟道粘土衬 砖; 3—小烟道; 4—单墙; 5—篦子砖; 6—隔热砖。
⑶炉顶区
1—装煤孔 2—看火孔 3—烘炉孔 4—挡火砖
⑷斜道区:斜道是连接燃烧室立火道和蓄热 室的通道 。燃烧室的每个立火道都与两个 斜道和一个砖煤气道相连。 斜道区复杂,是焦炉使用砖型最多的区域。 ⑸焦炉基础和烟道
四、炼焦炉生产操作 1、装煤操作:
要求装满、装平、定量、均衡、减少烟尘排放。
2、焦炉的出炉操作: ⑴推焦: 焦炉的出炉应严格按推焦计划进行,保证整个 炉组各炭化室实现定时、准点出焦。
周转时间——某一孔炭化室相邻两次推焦或装煤的时间间隔。 推焦串序—— 一组焦炉各炭化室装煤、推焦的前后次序。
焦化厂工艺流程文字叙述及流程图

备煤炼焦所用精煤,一方面由外部购入,另一方面由原煤经洗煤后所得,洗精煤由皮带机送入精煤场。
精煤经受煤坑下的电子自动配料称将四种煤按相应的比例送到带式输送机上除铁后,进入可逆反击锤式粉碎机粉碎后(小于3mm占90%以上),经带式输送机送至焦炉煤塔内供炼焦用。
炼焦装煤推焦车在煤塔下取煤,捣固成煤饼后,按作业计划从机侧推入炭化室内。
煤饼在炭化室内经过一个结焦周期的高温干馏,炼成焦炭并产生荒煤气。
炭化室内的煤饼结焦成熟后,由装煤推焦机推出并通过拦焦机的导焦栅送入熄焦车内。
熄焦车由电机牵引至熄焦塔熄焦。
熄焦后的焦炭卸至凉焦台,冷却后送往筛焦楼进行筛分和外运。
煤在干馏过程中产生的荒煤气汇集到炭化室的顶部空间,经上升管、桥管进入集气管。
700℃的荒煤气在桥管内经过氨水喷洒后温度降至85℃左右,煤气和冷凝下来的焦油氨水一起经吸煤气管道送入煤气回收车间进行煤气净化及焦油回收。
焦炉加热燃用的净化煤气经预热器预热至45℃左右进入地下室,通过下喷管把煤气送入燃烧室立火道,燃烧后的废气经烟道、烟囱排入大气。
冷鼓由焦炉送来的80-83℃的荒煤气,沿吸煤气管道入气液分离器。
经气液分离后,煤气进入初冷器进行两段间接冷却;上段用32℃循环水冷却煤气,下段用16-18℃低温水冷却煤气,使煤气冷却至22℃,然后经捕雾器入电捕焦油器除去悬浮的焦油雾后进入鼓风机,煤气由鼓风机加压送至脱硫工段。
在初冷器下段用含有一定量焦油、氨水的混合液进行喷洒,以防止初冷器冷却水管外壁积萘,提高煤气冷却效果。
由气液分离器分离出的焦油氨水混合液自流入机械化氨水澄清槽,进行氨水、焦油和焦油渣的分离。
分离后的氨水自流入循环氨水中间槽,用泵送到焦炉集气管喷洒冷却荒煤气,多余的氨水(即剩余氨水)送入剩余氨水槽,焦油自流入焦油中间槽,然后用泵将焦油送至焦油贮槽,静置脱水后外售,分离出的焦油渣定期用车送至煤场掺入精煤中炼焦。
脱硫来自冷鼓工段的粗煤气进入脱硫塔下部与塔顶喷淋下来的脱硫液逆流接触洗涤后,煤气经捕雾段除去雾滴后全部送至硫铵工段。
炼焦工艺2

炭化室内煤料结焦过程的基本特点: (一)单向供热、成层结焦
(二)结焦过程中传热性能随炉料的状态 和温度而变化
炭化室中心面上煤料温度始终最低,最后成熟,因此结 焦末期炭化室中心面温度(焦饼中心温度)可以做为焦 饼成熟程度的标志,称为炼焦最终温度。 由于成层结焦,最先形成塑性层(胶质层)是在炭化室 的两侧,然后逐渐向炭化室中心面移动,塑性层内气体 膨胀,通过塑性层外侧的煤料(半焦、焦炭)对炭化室 墙施以侧压力(即膨胀压力),当塑性层在炭化室中心 面汇合时,这时膨胀压力达到最大值,通常所说的膨胀 压力即指最大值。
三、化学产品产率的估算
由于煤有机大分子中侧链数量可近似用煤的挥 发分表示,所以炼焦化学产品的产率与煤的挥 发分有密切关系。
四、室式结焦过程中煤料硫分、灰分与焦炭硫分、 灰分的关系
• 在炼焦过程中,煤中的硫大部分转入焦炭,只有少部 分随煤气排出。
• 在炼焦过程中,煤中灰分基本全部转入焦炭。因此, 只有降低煤中的灰分,才能降低焦炭灰分。
第二节 炼焦过程的化学产品
在炼焦过程中,会有大量的气体产生。 由于炭化室内是层层结焦,而塑性层(胶质层)的透气性 差,气体不容易穿过塑性层。 那么,在两侧胶质层之间的气体,只能向上流向炉顶,这部 分气体称为“里行气”,约占气态产物的20%~25%;大部 分气 态物质是在胶质层外侧,通过赤热的半焦及焦炭层和沿高温 炉墙到达炭化室顶部空间,这部分气体称为“外行气”,约 占 气态产物的75%~80%。 里行气和外行气最后全部在炉顶空间汇集导出。
2、外界条件的影响 随热解最终温度升高,焦油和焦炭的产率下降,煤气 产率增加,但煤气中氢含量增加,甲烷含量减少,因 此煤气热值降低;
从化学产品的产率和质量来说,适宜的炉顶空间温度 为750℃;炉顶空间容积应尽可能小,减少荒煤气在 此停留时间,避免二次热解过度; 随加热速度提高,煤气、焦油产率增加,焦炭产率减 少。
煤的焦化过程及机理

—、煤的热解及分类煤的热解也称为煤的干馏或热分解,是将煤在隔绝空气的条件下加热,煤在不同温度下发生一系列的物理变化和化学反应,生成气体(煤气)、液体(焦油)和固体(半焦或焦炭)等产物的过程。
煤的热解按照不同的方法有多种分类。
按照热解温度可分为低温热解(500~700℃)、中温热解(700~1000℃)和高温热解(1000~1200℃)。
按照加热速度可分为慢速热解(<1K/s)、中速热解(5~100K∕s)和闪速热解(500〜106K∕s)。
按照热解气氛可分为惰性热解(不加催化剂)、加氢热解和催化加氢热解。
按照固体颗粒与气体在床内的相对运动状态分为固定床热解、气流床热解和流化床热解等。
按照加热方式可分为内热式、外热式和内外热并用式热解。
按照热载体方式可分为固体热载体、气体热载体和气‐固热载体热解。
按照反应器内的压力可分为常压热解和加压热解。
二、煤的焦化煤的焦化又称煤炭高温干馏,是以煤为原料,在隔绝空气条件下,加热到950℃左右,经高温干馏生产焦炭,同时获得煤气、煤焦油并回收其他化工产品的一种煤转化工艺。
煤经焦化后的产品有焦炭、煤焦油、煤气和化学产品四类。
1、炼焦用煤及其结焦特性炼焦用煤主要有气煤、肥煤、焦煤、瘦煤,它们的煤化程度依次增大,挥发分依次减小,因此半焦收缩度依次减小,收缩裂纹依次减少,块度依次增加。
以上各种煤的结焦特性如下:(1)气煤气煤的煤化程度较小,挥发性大,煤的分子结构中侧链多且长,含氧量高。
在热解过程中,不仅侧链从缩合芳环上断裂,而且侧链本身又在氧键处断裂,所以生成了较多的胶质体,但黏度小,流动性大,其热稳定性差,容易分解。
在生成半焦时,分解出大量的挥发性气体,能够固化的部分较少。
当半焦转化成焦炭时,收缩性大,所以,成焦后裂纹最多、最宽、最长,大部分为纵裂纹,所以焦炭细长易碎。
配煤炼焦时加人适当的气煤,可以增加焦炭的收缩性,便于推焦和保护炉体,同时可以得到较多的化学产品。
我国气煤储存量大,在炼焦时应尽量多配气煤,以合理利用炼焦煤资源。
煤的成焦率和什么因素有关

煤的成焦率和什么因素有关?1 产品生成1.1煤的成焦过程炼焦煤在隔绝空气下加热,其有机质随温度的升高而发生一系列变化,形成气态(煤气)、液态(煤焦油)和固态(半焦或焦炭)产物。
煤的成焦过程可分为三个阶段:第一阶段(常温至300℃)是煤的干燥脱气阶段,释放出水分并析出CH4、CO和N2。
第二阶段(300℃~600℃)以解聚和分解反应为主,煤粘结成半焦。
通常烟煤在300℃后开始软化,伴随有煤气和煤焦油析出;中等煤化度的烟煤在此期间的一定温度范围内生成气、液、固三相共存的质体。
第三阶段(600℃~1000℃)是半焦变成焦炭的阶段,此阶段以缩聚反应为主,产生大量煤气(以H2为主),半焦经收缩形成有裂纹的焦炭。
1.2炭化室内结焦过程装炉煤结焦需要的热量是通过两侧炉墙提供的,热量从两侧炉墙传向炭化室中心。
因此,结焦过程是从两侧炭化室墙面处开始,逐渐移向炭化室中心的层状结焦过程。
当炭化室中心的焦饼温度达到950℃~1050℃时焦饼成熟。
结焦速度反映炭化室内的平均升温速度。
结焦速度过快,将使焦炭裂纹增多、块度变小。
当炭化室墙面附近的煤料形成塑性层时,炭化室顶部和底部的煤料也受热形成了塑性层,同时,煤料分解的气态产物不断产生,由于四面的塑性层均不易透过气体,炭化室内压力不断升高,塑性层膨胀,并通过半焦和焦炭层将膨胀压力传递给炭化室墙。
当塑性层在炭化室中心面汇合时,炭化室膨胀压力达到最大值。
通常所说的膨胀压力就是指这一最大值。
膨胀压力取决于装炉煤的特性、炉料散密度及结焦速度,提高膨胀压力有助于煤料颗粒的粘合、融熔,改善焦炭的物理性,但是膨胀压力过高,将对炭化室墙体造成损坏。
1.3炭化室内气体析出动态炭化室内的装炉煤在结焦过程中产生的气体产物(含液体产物的蒸汽)一部分通过两侧塑性层之间的煤层流向炭化室顶部空间,称为“里行气”,约占全部气态产物的10%~25%。
另外约占75%~90%的气态产物,通过半焦层和焦炭层以及焦炭与炭化室墙之间的缝隙流向炭化室顶部空间,称为“外行气”。
第二章 配煤炼焦的原理与配煤工艺

二、炼焦过程中化学产品的生成
煤炭高温干馏得到的炼焦化学产品的组成与煤 的性质和炼焦条件有关,煤热解生成的一次化学品
还要受到焦炉内炼焦条件的影响,有关内容祥见本
篇第五章内容。
第二节 配合煤质量与备煤炼焦工艺条件
由于煤在焦炉炭化室内结焦过程和煤成焦规律的要求,
使得工业炼焦必须采用多种煤配合炼焦。常规炼焦方法是将
3、炭化室内层温度变化与焦炭的质量关系
图2-4 不同煤的半焦收缩曲线 1-第一收缩峰;2-第二收缩峰
3、炭化室内层温度变化与焦炭的质量关系
从炭化室墙面到炭化室中心面处,温度梯度逐
渐减小,因而靠墙面处的焦炭粒度相对小于中心处
的焦炭粒度,这样就产生了相同的煤料在相同的炼
焦条件下结焦,其焦炭质量由于上述原因,不同的
因为焦炉炭化室的侧向供热,且炉料导热系数低,因 此在整个成焦过程的大部分时间内,炭化室内与炉墙垂直 方向上炉料的温度梯度较大(图2-1左)。这样在结焦过程的 大部分时间内,离炭化室墙面不同距离的各层炉料、所受 到的温度不同而处于热解过程的不同阶段,整个炭化室内 炉料的状态随时间而变化(图2-1右)。靠近炉墙附近的煤先 结成焦炭,而后焦炭层逐渐向炭化室中心推移,这就是所 谓的“成层结焦”。炭化室中心面上的炉料温度始终最低, 因此以结焦末期炭化室中心面的温度(焦饼中心温度)作为 焦饼成熟度的标志,称为炼焦最终温度。
的炉料升温速度最慢,约2℃/ min以下,这种温
度变化的差别必然导致焦炭质量的差异。
1.成层结焦与温度变化
图2-2 炭化室内各层炉料的温度变化 1-炭化室墙表面温度;2-炭化室墙附近的炉料温度;3-距 炉墙50~60mm处炉料温度
1.成层结焦与温度变化
焦化工艺讲解
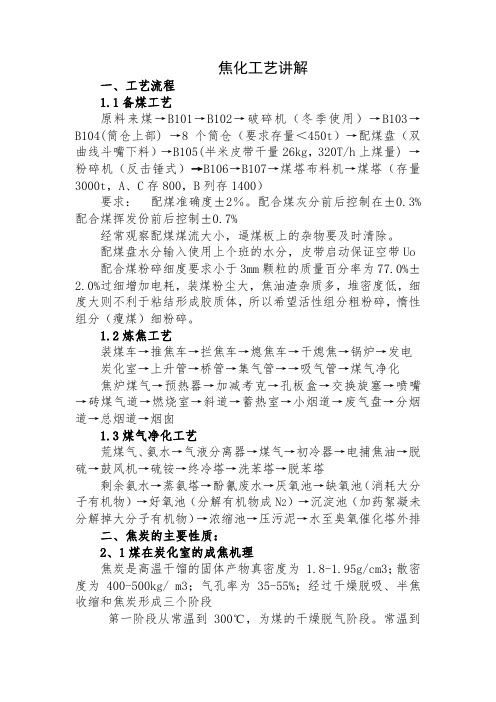
焦化工艺讲解一、工艺流程1.1备煤工艺原料来煤→B101→B102→破碎机(冬季使用)→B103→B104(筒仓上部) →8个筒仓(要求存量<450t)→配煤盘(双曲线斗嘴下料)→B105(半米皮带干量26kg,320T/h上煤量) →粉碎机(反击锤式)→B106→B107→煤塔布料机→煤塔(存量3000t,A、C存800,B列存1400)要求:配煤准确度±2%。
配合煤灰分前后控制在±0.3% 配合煤挥发份前后控制±0.7%经常观察配煤煤流大小,逼煤板上的杂物要及时清除。
配煤盘水分输入使用上个班的水分,皮带启动保证空带Uo 配合煤粉碎细度要求小于3mm颗粒的质量百分率为77.0%±2.0%过细增加电耗,装煤粉尘大,焦油渣杂质多,堆密度低,细度大则不利于粘结形成胶质体,所以希望活性组分粗粉碎,惰性组分(瘦煤)细粉碎。
1.2炼焦工艺装煤车→推焦车→拦焦车→熄焦车→干熄焦→锅炉→发电炭化室→上升管→桥管→集气管→→吸气管→煤气净化焦炉煤气→预热器→加减考克→孔板盒→交换旋塞→喷嘴→砖煤气道→燃烧室→斜道→蓄热室→小烟道→废气盘→分烟道→总烟道→烟囱1.3煤气净化工艺荒煤气、氨水→气液分离器→煤气→初冷器→电捕焦油→脱硫→鼓风机→硫铵→终冷塔→洗苯塔→脱苯塔剩余氨水→蒸氨塔→酚氰废水→厌氧池→缺氧池(消耗大分子有机物)→好氧池(分解有机物成N2)→沉淀池(加药絮凝未分解掉大分子有机物)→浓缩池→压污泥→水至臭氧催化塔外排二、焦炭的主要性质:2、1煤在炭化室的成焦机理焦炭是高温干馏的固体产物真密度为1.8-1.95g/cm3;散密度为400-500kg/ m3;气孔率为35-55%;经过干燥脱吸、半焦收缩和焦炭形成三个阶段第一阶段从常温到300℃,为煤的干燥脱气阶段。
常温到120 ℃前干燥;120~200℃,煤释放出吸附的CH1、CO2、CO等N2等气体,是一个脱吸过程;200~300℃,煤开始分解,生成CO2、CO、H2等气体,同时释放出结晶水及微量焦油。
炼焦厂结焦过程及配煤炼焦与生产操作实践

炼焦厂结焦过程及配煤炼焦与生产操作实践◎刘洋目前,由于世界范围内优质炼焦煤资源明显短缺并日趋严重,优质焦炭与优质煤源之间的矛盾是推动配煤炼焦技术以及非炼焦煤炼焦技术发展的主要原因和动力。
为了扩大炼焦煤源,将弱黏结煤和不黏结煤用于炼焦,适合于焦炉配煤炼焦的各种新技术,成为解决用较差的炼焦煤炼出优质焦炭的主要方法。
一、炭化室内的结焦过程(一)煤的成焦过程机理烟煤是组成复杂高分子有机物混合物,其基本结构单元是不同缩合程度的芳香核,核周边带有侧链,结构单元间以交联键连接。
高温炼焦过程大致分为以下阶段。
1.干燥预热阶段。
煤由常温加热到350℃失去水分。
2.胶质体形成阶段。
在煤受热到350-480℃时,有的侧链和交联键断裂,出现缩聚和重排反应,形成相对分子质量较小的有机物。
黏结性煤转化为胶质状态,相对分子质量较小的以气的形态析出或存在于胶质体中,相对分子质量较大的以固态形式存在于胶质体中,形成胶质体。
由于液相在煤粒表面形成,把诸多粒子汇集在一起,胶质体的形成对煤的黏结成焦非常重要。
不能形成胶质体的煤缺乏黏结性;黏结性好的煤热解时形成的胶质状的液相物质多,热稳定性好。
3.半焦形成阶段。
在温度超过胶质体固化温度480℃-650℃时,液相的热缩聚速度超过其热解速度,增加了气相和固相的生成,煤的胶质体不断固化,形成半焦。
胶质体的固化是液相缩聚的结果,此种缩聚出现于液相间或吸附了液相的固体颗粒表面。
4.焦炭形成阶段。
在当温度升高到650-1000℃时,半焦内的不稳定有机物不断热分解和热缩聚,这时热分解的产物主要是气体,前期主要是甲烷和氢,之后,气体相对分子质量越来越小,750℃以后主要是氢。
随着气体的析出,半焦的质量减少很多,体积收缩。
由于煤在干馏时是分层结焦的,在同一时刻,煤料内部各层处于的成焦阶段不同,收缩速度也不同;又由于煤中有惰性颗粒,因此产生较大的内应力,应力在大于焦饼强度时,焦饼上形成裂纹,焦饼分裂成焦块。
第02章室式结焦过程

室式结焦过程
3.煤热解中的缩聚反应
煤热解的前期以裂解反应为主,而后期则以缩聚反应为主。缩聚反 应对煤的热解生成固态产品(半焦或焦炭)影响较大。 (1)胶质体固化过程的缩聚反应,主要是在热解生成的自由基之间 的缩聚,其结果生成半焦。 (2)半焦分解,残留物之间的缩聚,生成焦炭。缩聚反应是芳香结 构脱氢。苯、萘、联苯和乙烯参加反应。如:
室式结焦过程
羧基热稳定性低,200℃就开始分解,生成CO2和H2O。 羰基在400℃左右裂解成CO,羟基不易脱除,到700℃~ 800℃以上,有大量氢存在,可氢化生成H2O。含氧杂环在
500℃以上也可能断开,生成CO。
(4)煤中低分子化合物的裂解,是以脂肪结构为主的低 分子化合物,其受热后,可分解成挥发性产物。
室式结焦过程
第一节 炭化室内的结焦过程
炭化室内煤料结焦过程的基本特点有二,一是单向供热、 成层。
一、温度变化与炉料动态 1.成层结焦过程及炼焦最终温度 在同一时间内,距炉墙不同距离的各层煤料的温度不同, 炉料的状态也不同,各层处于结焦过程的不同阶段,总是在 炉墙附近先结焦而后逐层按照焦炭层、半焦层、塑性层、干 煤层、湿煤层等逐层向炭化室中心推移,这就是成层结焦。 结焦末期炭化室中心面温度(焦饼中心温度)可以作为 焦饼成程度的标志,称为炼焦最终温度。
室式结焦过程
(3)第三阶段550(600℃)~1000℃ 应为主体,由半焦转变成焦炭。 ①550(或600℃)~750℃,半焦分解析出大量气体。主 该阶段以缩聚反
要是H2和少量CH4,称为热解的二次气体。一般在700℃时析
出的氢气量最大,在此阶段基本上不产生焦油。半焦因分解 出气体收缩而产生裂纹。
(100 26.5) 100 K 1 75.58% 100 1.0478
焦化厂炼焦工艺流程理论
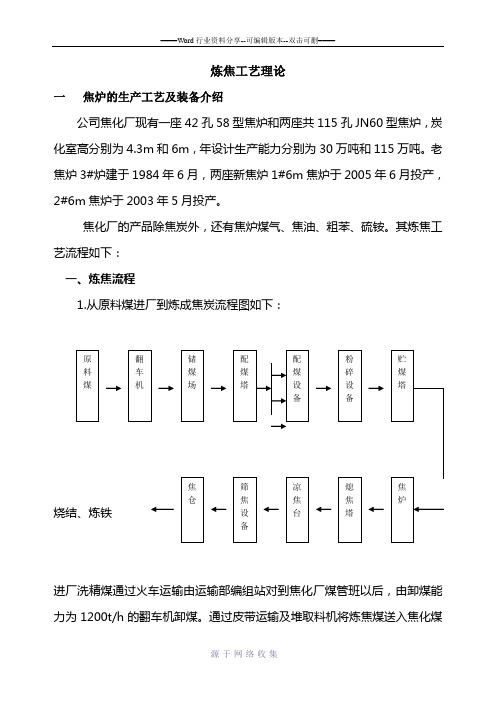
炼焦工艺理论一 焦炉的生产工艺及装备介绍公司焦化厂现有一座42孔58型焦炉和两座共115孔JN60型焦炉,炭化室高分别为4.3m 和6m ,年设计生产能力分别为30万吨和115万吨。
老焦炉3#炉建于1984年6月,两座新焦炉1#6m 焦炉于2005年6月投产,2#6m 焦炉于2003年5月投产。
焦化厂的产品除焦炭外,还有焦炉煤气、焦油、粗苯、硫铵。
其炼焦工艺流程如下:一、炼焦流程1.从原料煤进厂到炼成焦炭流程图如下:烧结、炼铁进厂洗精煤通过火车运输由运输部编组站对到焦化厂煤管班以后,由卸煤能力为1200t/h的翻车机卸煤。
通过皮带运输及堆取料机将炼焦煤送入焦化煤场,共有3台堆取料机,每台堆煤能力600t/h,取煤能力300t/h。
焦化煤场分为两个主煤场和东、西两个副煤场,煤场长均为275m,主煤场宽50m,副煤场宽30m,储煤能力一般情况下为9万吨左右。
通过煤场分类堆储后,炼焦煤由堆取料机取煤后经皮带运输送往12个配煤塔,通过圆盘给料机和电子皮带秤按比例进行不同煤种的配合,再送往粉碎机粉碎。
有两台可逆锤式粉碎机,每台生产能力500t/h,一开一备。
粉碎后的配合煤送入贮煤塔,装入焦炉炭化室炼焦。
煤在焦炉炭化室内隔绝空气加热,两座老焦炉的设计结焦时间为18h,新焦炉结焦时间19h,当焦饼中心温度达到1000℃±50℃时,焦炭成熟,推出炭化室,熄焦后送往筛焦楼,将焦炭筛分成大于40mm,40~25mm,25~10mm,小于10mm,四种规格,分别送炼铁、烧结工序。
2.煤的成焦过程:烟煤隔绝空气加热到950~1050℃,经过干燥、热解、熔融、粘结、固化、收缩等阶段最终制得焦炭,这一过程叫做高温炼焦(或高温干馏)。
室温200℃300℃450℃550℃1000℃煤焦炭煤在干馏时,首先释放吸附在煤表面的气体和水蒸汽,大部分非结合态的水在低于105℃时释出,因煤种不同,煤热解开始析出气体的温度不同,烟煤为350~400℃,无烟煤为400~450℃,主要是由于含氧量和化学结构不同,热稳定性增加,从而分解温度升高。
煤炭焦化过程及结焦机理分析

2011年1月(下)[摘要]炼焦是煤在隔绝空气环境下的热分解过程,它是复杂的物理化学过程,煤的热分解机理和配合煤在加热过程中的相互作用对合理利用炼焦煤资源具有理论和实践意义。
本文以煤的热解原理为指导,分析了煤的热解过程,解焦的粘结机理和收缩机理。
[关键词]煤炭;焦化;热解煤炭焦化过程及结焦机理分析马艳(七煤(集团)公司煤气厂,黑龙江七台河154600)炼焦是煤在隔绝空气环境下的热分解过程,它是复杂的物理化学过程,既有普通高分子有机化合物的分解,还有与不同煤的结构不同的特殊性。
煤的热分解机理和配合煤在加热过程中的相互作用对合理利用炼焦煤资源具有理论和实践意义。
1煤的热解原理煤是以有机物为主,夹杂少量无机矿物质的固体可燃矿物,因此,煤的分子结构具有明显的有机化合物的特征,而不同成煤时代形成的煤层,分子结构差别较大,通常来说煤的分子结构的基本单元是大分子芳香族稠环化合物的六碳环平面网格,在大分子稠环周围,连接许多烃类的侧链结构、氧键和各种官能团。
侧链和氧键又将大分子的碳网格在空间以不同角度互相连接,构成了煤的复杂的大分子结构,碳原子主要集中在六碳环平面网格中,氢、氧等原子主要集中在碳网周围及侧链中,煤的变质程度的加深,其基本结构单元六碳环平面网格变大,侧链不断减少。
在煤的热分解过程中,侧链不断断裂,生成小分子的气态和液态,断掉侧链和氢的碳原子网格逐渐缩合加大,在高温度下生成焦炭。
煤结构中侧链的含氧官能团含量越高,就容易分解和断裂,如果煤的侧链较少,碳网平面热稳定性较强,在煤的热解过程中,煤的结构很难分解。
2煤的热解过程煤在炭化室高温下进行热解和焦化,发生复杂的物理和化学变化,经过干燥、预热、软化、膨胀、熔融、固化和收缩炼制成焦炭。
煤的炼焦过程就是高温热分解,即高温干馏过程。
1)干燥和预热湿煤装炉后,炭化室中心煤料温度升到100℃以上所需的时间,约为结焦时间的一半左右,这是水的汽化潜热大而煤的导温系数小。
焦化主要工艺流程介绍

焦化主要⼯艺流程介绍焦化系统主要车间⼯艺流程介绍主要车间组成:⼀、备煤车间:预粉碎机室、粉碎机室、配煤室、煤塔顶层、转运站及通廊等组成。
⼆、炼焦车间:2×65 孔5.5m 复热式捣固焦炉、熄焦塔、粉焦沉淀池、焦台、装煤出焦地⾯站、筛贮焦楼、转运站、输送机通廊等组成。
三、煤⽓净化车间:冷凝⿎风⼯段、脱硫⼯段、硫铵⼯段(含蒸氨系统)、终冷洗涤及粗苯蒸馏⼯段、油库⼯段。
四、⼲熄焦车间:包括提升机、⼲熄焦塔、余热锅炉、循环风机、环境除尘风机。
五、余热发电车间:包括除盐⽔泵房、汽轮机、发电机、循环⽔泵房等。
《焦化⼯艺简图》1 备煤车间1.1. 概述备煤车间是为2×65 孔 5.5m 复热式捣固焦炉制备装炉煤,⽇处理炼焦煤料约5397.8t,含⽔分~10%,年处理煤量~195.2 万t(湿)。
本项⽬所需炼焦⽤煤,采⽤带式输送机运输。
1.2. ⼯艺流程备煤系统采⽤先配煤后粉碎的⼯艺流程。
整个系统主要由配煤室、预粉碎机室、粉碎机室、煤塔顶层以及相应的带式输送机通廊和转运站组成,并设有煤制样室等⽣产辅助设施。
1.3. ⼯艺设施及主要设备1.3.1. 配煤⼯段配煤⼯段是把各种牌号的炼焦⽤煤,根据配煤试验确定的配⽐进⾏配合,使配合后的煤料能够炼制出符合质量要求的焦炭,同时达到合理利⽤煤炭资源,降低⽣产成本的⽬的。
由带式输送机运来的各单种煤由可逆配仓带式输送机分别布⼊配煤槽中。
配煤槽直径为8m 共10 个,双排布置,分别为4 个和6 个槽,4 个槽的⼀排⽤于贮存需预粉碎的煤种;6 个槽的⼀排⽤于贮存不需预粉碎的煤种。
煤的总储量达到6500t,能够满⾜ 2 座焦炉28 ⼩时的⽣产⽤湿煤量。
配煤槽采⽤等截⾯收缩率型双曲线钢⽃嘴,对含⽔分⾼和煤泥量⼤的煤,有良好的适应性,操作稳定,可防⽌煤在配煤槽内棚料,提⾼配煤的准确性。
⽃嘴上安装空⽓炮振煤装置,在配煤室设置液压升降平台,以便于空⽓炮检修。
⽃嘴内衬采⽤超⾼分⼦量聚⼄烯衬板。
炭化室结焦过程(2)
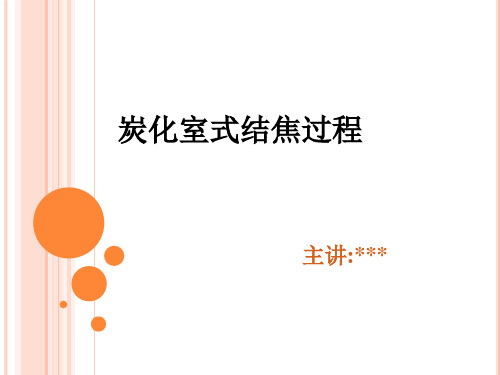
表2-1 不同热解温度下固体残留物碳网的尺寸
处理温 度 /℃ 碳网尺寸/ 处理 温度/ ℃ 碳网尺寸/
焦 煤 原煤 (室温) 300 400 500 17 17 21 21
气 煤
焦 煤
气 煤
16 16 19 22
600 700 800 1100
26 ─ 38 46
24 30 35 37
在 700℃以后,碳网尺寸增大较快,其原 因是由于缩聚反应在该温度下剧烈的结果。 半焦外型的变化产生裂纹,半焦热缩聚必然 引起体积收缩,而焦块的刚性阻止其收缩, 半焦内便产生了内应力。随着温度的升高, 其内应力不断增加,当内应力大于半焦本身 的强度时,使半焦破裂形成裂纹。当温度达 到 1000℃时,形成具有一定机械强度和一定 块度的银灰色并具有金属光泽的焦炭。
相产物中,以脂肪化合物居多。
胶质体的概念
当煤样在隔绝空气条件下加热至一定温 度时,煤粒开始分解并有气体产物析出, 随着温度的不断上升,有焦油析出,在 350-420℃时,煤粒的表面上出现了含 有气泡的液相膜,此时液相膜开始软化, 许多煤粒的液相膜汇合在一起,形成了 气、液、固三相为一体的黏稠混合物, 这种混合物称为胶质体。
炭化室式结焦过程
主讲:***
三、煤的黏结和成焦机理
具有黏结性的煤,在高温热解时,从粉煤分解 开始,经过胶质状态到生成半焦的过程称为煤的黏 结过程。 而从粉煤开始分解到最后形成焦块的整个过程 称为结焦过程,如图2-4所示。
图2-4 黏结与成焦过程阶段示意图
三、煤的黏结和成焦机理
由图可见
① 煤的结焦过程大体可分为黏结过程和半焦
(△t ),即 △t= t固- t软 。它表示煤粒处在胶质 体状态所停留的时间,也反映了胶质体的热稳定性。 如果温度间隔大,则胶质体停留时间长,其热稳定 性好,煤粒间有充分的时间互相接触,有利于黏结。 反之,胶质体停留时间短,很快分解,煤粒间的黏 结性也差。
- 1、下载文档前请自行甄别文档内容的完整性,平台不提供额外的编辑、内容补充、找答案等附加服务。
- 2、"仅部分预览"的文档,不可在线预览部分如存在完整性等问题,可反馈申请退款(可完整预览的文档不适用该条件!)。
- 3、如文档侵犯您的权益,请联系客服反馈,我们会尽快为您处理(人工客服工作时间:9:00-18:30)。
焦炉
为了使结焦和加热分开,缩短结焦时间,出
现了倒焰式焦炉。
由于炼焦化学产品焦油和氨找到了用途,促
使人们设计出燃烧室和炭化室完全隔开的焦 炉,即所谓副产品回收焦炉。
燃烧室出来的废气温度很高,此部分废热没
有回收,有的用来加热废热锅炉,这种没有 废热回收的焦炉,称作废热式焦炉。
为了少耗热量,省出焦炉煤气,由废热式进
一步发展到回收废热的蓄热式焦炉。
蓄热式焦炉在每个炭化室下方均有一个或两
个蓄热室,蓄热室填有蓄热用的格子砖。当 废气经过蓄热室时,废气将格子砖加热,格 子砖蓄存了热量,气流方向换向后,格子砖 把蓄存的热量再传给冷的空气,使蓄存热量 又带回燃烧室。
现代焦炉 概述 焦炉主要构成部分(三大室)
①炭化室 煤隔绝空气干镏的地方,焦炭形成的场 所。 ②燃烧室 是煤气燃烧的地方,煤气与空气在其中 混合燃烧,产生的热量传给炉墙,间接加 热炭化室中煤料,对其进行高温干馏。 ③蓄热室 回收燃烧室废气的热量来预热空气和贫 煤气的地方。
炭化室式结焦过程
主讲:***
一、 炼焦炉的发展
煤在焦炉内隔绝空气加热到1000℃,可获得
焦炭、化学产品和煤气。此过程称高温干馏 或高温炼焦,一般简称炼焦。焦炭主要用于 高炉炼铁。煤气可以用来合成氨,生产化学 肥料或用作加热燃料。炼焦所得化学产品种 类很多,主要有硫铵、吡啶碱、苯、甲苯、 二甲苯、酚、萘、蒽和沥青等。
炼焦主要产品焦炭,是炼铁原料,所以炼焦
是伴随钢铁工业发展起来的。初期炼铁是用 木炭,由于木材逐渐缺乏,使炼铁发展受到 限制,人们才开始寻求焦炭炼铁,1725年 焦炭炼铁有
一部分煤被烧掉。称为成堆干馏或土法炼焦。 土法炼焦成焦率低,焦炭灰分高,结焦时间 长,化学产品不能回收,综合利用差。