焦炉炭化室压力自动调节技术
焦炉炭化室压力自动调节技术的应用

c ha mbe r . By us i n g o f t h i s t e c h n o l o g y, l a r g e qu a n t i t y o f r a w c o ke o v e n g as c a n b e r e c o v e r e d, t he e n v i — r o n me n t o f c o ke o v e n b a t t e r y c a n b e i mp r o v e d, a nd t h e p r o b l e ms o f s mo k e l e a ka g e d u r i n g c o a l c h a r —
g i ng a nd n e g a t i v e p r e s s u r e i n t h e b o t t o m o v e n a t t h e e n d o f c o k i n g c a n be s o l v e d. The r e f o r e, i t i s i m—
摘 要 :介 绍 了 炭化 室压 力 自动调 节 技 术 的应 用 情 况 。本 项 技 术 能 回收 大 量 的荒 煤 气 , 改 善焦炉周边环境 , 解 决 装
煤 过 程 中烟 尘 外 逸 及 炭化 室结 焦 末 期 底 部 出现 负 压 的 问题 , 对延长焦炉寿命具有重要作用 ; 实用 性强 、 投 资少, 具 有 显著的经济效益。 关 键 词 :无 烟装 煤 ;自动 控 制 ; 节 能 环 保 中图 分 类 号 :T Q 5 2 2 文献 标 识 码 :B 文 章 编 号 :1 0 0 1 —3 7 0 9( 2 0 1 4 )0 2 — 0 0 3 3 — 0 3
科技成果——焦炉炭化室荒气回收和压力自动调节技术

科技成果——焦炉炭化室荒气回收和压力自动调节技术适用范围钢铁行业钢铁和化工行业焦炉行业现状以2×60孔6m顶装焦炉(年产焦炭120万t)为例,采用焦炉炭化室压力自动调节煤气增收技术,可回收荒煤气量约为477万m3/a,则增收荒煤气为4m3/tJ。
按其煤气热值折合成标准煤,相当于节约标准煤2917t/a、减排7700tCO2/a。
成果简介1、技术原理根据每孔炭化室煤气发生量变化,实时调节桥管水封阀盘的开度,实现整个结焦周期内炭化室压力调节,避免在装煤和结焦初期因炭化室压力过大产生煤气及烟尘外泄,并大量减少炭化室内荒煤气窜漏至燃烧室,实现装煤烟尘治理和焦炉压力稳定。
2、关键技术桥管阀体的研制;抗堵塞取压探头的研制;执行机构的选择与安装;控制系统的开发;负压集气管的压力调节与粉尘控制;炭化室底部压力的控制。
3、工艺流程在装煤过程中,该炭化室的桥管水封阀完全打开,由于集气管内为的负压使装煤时产生的荒煤气和烟尘大量导入集气系统而不外泄,回收了荒煤气并实现了对装煤烟尘的高效治理,装煤烟尘治理可取消传统的装煤除尘或配合现有装煤除尘。
装煤后进行炭化室压力单独调节,使炭化室在结焦全过程压力稳定,避免结焦末期集气管内荒煤气向炭化室倒流,防止炭化室底部出现负压和炉墙窜漏、冒烟、冒火现象发生,有利于焦炉稳定生产,对延长焦炉寿命具有重要作用。
主要技术指标技术水平1、技术鉴定及获奖情况2012年11月该技术通过中冶集团技术成果鉴定,技术创新水平达到国际先进;专利名称:一种焦炉炭化室压力自动调节装置,专利号:ZL200920008067.4;2012年11月该技术通过中冶集团技术成果鉴定,技术创新水平达到国际先进。
2、目前技术应用现状及产业化发展情况该技术现已在济钢8、9号焦炉和芜湖1、2号焦炉投产使用,用户反馈使用状况良好,经济效益显著。
淮北焦化5、6、7、8号焦炉正在建设施工阶段。
典型案例典型案例1应用单位:山东钢铁集团济南分公司项目名称:济钢8、9号焦炉炭化室压力自动调节煤气增收技术项目建设规模:2×60孔6m顶装焦炉。
焦炉炭化室压力自动调节技术

: !
工 业 技 术
Sci en ce an d Tech no l o gy I n nov at i o n He r al d
焦 炉 炭化 室 压 力 自动 调 节技 术
陈毅 赵希超 r ( 中冶焦耐工程 技术 有限公司 辽 宁大连 1 1 6 0 8 5 ) 摘 要: 为实现 焦炉炭化室压 力稳定, 改善焦炉炉顶环境 , 新开发一种焦炉碳 化室压 力自 动调节 技术 , 经过工程检验证 明, 斌技 术易于操作 , 运
c a r b o n i z a t i o n c h a mb e r ,b y u s e d i n t h e p r 0 j e c t ,t h i s t r u s t wo r t h y t e c h n o l o g y c a n b e o p e r a t e d e a s i l y .
囱1 焦 炉 炭化 室 压 力自 动 调节 装 置 示 意 图( 圆 形 集 气 管 )
一
现 了焦炉 炭 化 室 压 力的 稳 定 , 解 决 了原 系 统
如装 煤 时 荒 煤 气导 入集 气管 的 量不 够 , 使 大 压 , 导 致 炭化 室 炉 墙 串漏 , 对焦炉造成不良 化 室倒流 , 并 可解 决 炭 化 室 结 焦 末 期 焦 炉
量荒 煤气 外逸 , 严 重 影响 环 境 , 或 使 装 煤 除 影 响 等 。 国 外 有 采 用 一种 叫 P r o v e n 系统 的 炭 化 室 底 部 出现 负 压 的 问 题 , 有 利 于 焦 炉
生 产和稳 定运行。 它 采 用 一 种 叫做 固定 杯
煤 气 的 流 通 断 面 来 实 现 对 单 个 炭 化 室 压 力
7.63米大型焦炉单炭化室压力调节系统工艺设备及维护知识讲解和分析(内部工程师培训资料)

7.63米大型焦炉单炭化室压力调节系统工艺设备及维护知识讲解和分析(内部工程师培训资料)编写:王XX审核:X志X校对:XX伟2011.8.8二、单炭化室压力调节系统(PROVEN SYSTEM) (3)1、单炭化室压力调节系统构成 (3)2、单炭化室压力调节系统概述 (4)1.1、炼焦过程 (4)1.2、推焦过程 (5)1.3、装煤过程 (6)3、单炭化室压力调节系统的SFC时序图控制简介 (6)4 、PROVEN气源箱的简介 (8)5、PROVEN电液执行器的接线简介 (9)6、典型故障汇总 (10)6.12009.2.26A炉40#阀门定位器故障 (10)6.22009.6.25B炉16#上升管盖不能自动打开 (12)6.32009.9.19B炉30#阀门定位器不自动调节,压力为负压 (14)6.42009.11.5A炉3号上升管遇到的情况 (16)6.52010.1.28C炉的2号阀门定位器现场手动无法回0% (18)6.62010.3.2A炉62#手动自动均关不了上升管盖 (19)6.72010.12.13部分上升管装完煤后频繁冲洗固定杯,并且压力进度条变红 (21)6.82010.12.20B炉PR OVEN的系统光纤报警 (22)二、单炭化室压力调节系统(PROVEN SYSTEM)1、单炭化室压力调节系统构成单炭化室压力调节系统(简称单炭化室压力调节系统)用于对单个炭化室的压力进行精确调节。
该系统在集气管内,对应每孔炭化室的桥管末端安装一个形状像皇冠的管,上面开有多条沟槽,皇冠管下端设有一个“固定杯”,固定杯由三点悬挂,保持水平。
杯内设有执行机构控制的活塞杆及其相连的杯口塞,同时在桥管设有压力检测与控制装置。
炭化室压力调节是由调节杯内的水位也就是荒煤气流经该装置的阻力变化实现的。
在桥管上部有两个喷嘴喷洒的氨水流入杯内,测压压力传感器将检测到上升管部位的压力信号及时传到执行机构的控制器,控制器发出指令使执行机构控制活塞杆带动杯口塞升降,调节固定杯出口大小来调节杯内的水位,使炭化室压力保持在微正压力状态.水位越高,沟槽出口越小,荒煤气导出所受阻越大;水位越低,沟槽出口越大,荒煤气导出所受阻力越小,如图1-1。
焦炉炭化室压力单调技术的分析与比较

焦炉炭化室压力单调技术的分析与比较摘要:焦炉单孔炭化室压力调节技术是目前应用在大型焦炉环保领域的新技术之一。
对现有三种炭化室压力单调技术技术进行比对分析,对其各自的适用性以及功能效果进行综合性的剖析,结合我公司焦炉特性选用适合我公司焦炉特性的炭化室压力单调技术。
关键词:焦炉单孔炭化室;压力调节;技术分析1 引言焦炉单孔炭化室压力调节技术是进入21世纪以来,专门应对焦炉装煤以及结焦过程出现的污染物而研发的技术。
炭化室压力调节技术通过自动控制可对单孔炭化室的压力进行在线调节,使焦炉炭化室底部压力在整个结焦周期内均稳定地维持在微正压。
该技术克服了常规焦炉在结焦末期由于单个炭化室煤气发生量减少,没有调控手段而出现负压,从而吸入空气导致焦炭烧损、灼烧炉墙造成窜漏,影响煤焦系数及焦炉使用寿命及煤气产量等不利情况。
目前,国际上主流的炭化室压力调节技术主要有3 种: 德国的PROven 技术、意大利PW公司的SOPRECO 技术及我国中冶焦耐开发的具有自主知识产权的CPS 技术。
这3 种技术均可以实现上述功能,但技术路线各有特点。
2 三种技术的原理2.1 PROven技术工作原理PROven技术的原理如图1 所示。
集气管为负压状态生产,通过桥管处测压,反馈给控制系统,控制系统通过驱动气缸来实现控制意图。
其核心工作部件是一个底为锥形的固定杯( 位于集气管内部) ,通过气缸驱动气动执行机构操纵的中心拉杆控制其开关,同时,由中心拉杆带动的内套筒壁的溢流孔高度在底阀关闭时可调节杯内液位。
桥管下部沿圆周开有均布的长条缝,形成皇冠管,伸入固定杯,通过杯内的液位高度调节荒煤气的流通断面,从而调节炭化室压力。
图1 PROven 的系统构成2.2 SOPRECO技术工作原理SOPRECO 技术的原理如图2 所示。
集气管为负压状态生产,通过上升管根部测压,反馈给控制系统,控制系统通过驱动执行器来实现控制意图。
其核心工作部件是一个称为SOP RECO 阀的装置,该装置通过执行器控制半球阀,通过球型阀门的开度变化调节荒煤气的流通断面,从而调节炭化室压力。
炭化室压力独立调节系统在生产中焦炉的应用
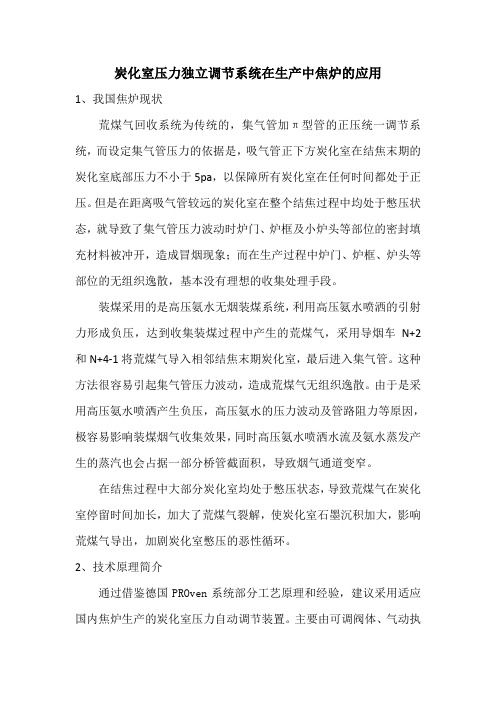
炭化室压力独立调节系统在生产中焦炉的应用1、我国焦炉现状荒煤气回收系统为传统的,集气管加π型管的正压统一调节系统,而设定集气管压力的依据是,吸气管正下方炭化室在结焦末期的炭化室底部压力不小于5pa,以保障所有炭化室在任何时间都处于正压。
但是在距离吸气管较远的炭化室在整个结焦过程中均处于憋压状态,就导致了集气管压力波动时炉门、炉框及小炉头等部位的密封填充材料被冲开,造成冒烟现象;而在生产过程中炉门、炉框、炉头等部位的无组织逸散,基本没有理想的收集处理手段。
装煤采用的是高压氨水无烟装煤系统,利用高压氨水喷洒的引射力形成负压,达到收集装煤过程中产生的荒煤气,采用导烟车N+2和N+4-1将荒煤气导入相邻结焦末期炭化室,最后进入集气管。
这种方法很容易引起集气管压力波动,造成荒煤气无组织逸散。
由于是采用高压氨水喷洒产生负压,高压氨水的压力波动及管路阻力等原因,极容易影响装煤烟气收集效果,同时高压氨水喷洒水流及氨水蒸发产生的蒸汽也会占据一部分桥管截面积,导致烟气通道变窄。
在结焦过程中大部分炭化室均处于憋压状态,导致荒煤气在炭化室停留时间加长,加大了荒煤气裂解,使炭化室石墨沉积加大,影响荒煤气导出,加剧炭化室憋压的恶性循环。
2、技术原理简介通过借鉴德国PROven系统部分工艺原理和经验,建议采用适应国内焦炉生产的炭化室压力自动调节装置。
主要由可调阀体、气动执行机构、控制系统、测压机构和生产通讯等部分组成。
该技术将单孔炭化室的桥管阀体改造成便于控制荒煤气流量的阀体翻板装置,翻板与气动执行机构连接。
装煤时执行机构调节阀体翻板完全打开,使炭化室直接与保持负压的集气管连通,形成负压通道,将炭化室内产生的荒煤气回收,实现了无烟装煤。
装煤结束后,当炭化室转入正常加热时,控制系统通过测压装置反馈的各点压力数据,控制对应的翻板开度,同时通过控制在不同结焦时期的桥管压力,实现炭化室底部在整个结焦过程中保持微正压状态。
在推焦作业时,执行机构及时关闭阀体翻板,炭化室完全与集气管隔断,以确保推焦作业的安全。
炭化室压力调节阀系统设计与优化

炭化室压力调节阀系统设计与优化摘要:本文介绍了一种炭化室压力调节阀系统的设计与优化,用于焦炉上的荒煤气流通压力调节。
该系统由桥管、上升管和调节机构组成,其中桥管与上升管内部连通,调节机构包括外壳、内筒、阀门盖和执行机构。
通过调节阀门盖和内筒底端的错开面积,实现荒煤气流通面积的调节,从而达到精确调节荒煤气流通压力的目的。
本文分为三个主要部分,首先阐述了系统的目标和重要性,指出炭化室压力调节在焦炭生产过程中的关键作用。
其次,详细描述了系统的设计原理和组成部件功能,包括荒煤气流通过程和压力调节原理。
然后,探讨了系统优化设计的策略,包括调节机构和流通面积控制的优化。
通过实验验证和结果分析,证明优化设计有效提高了系统的调节精度和稳定性。
本文的研究对于提高焦炭生产效率和质量具有重要的实际应用价值。
关键词:炭化室压力调节阀系统;焦炉;荒煤气;流通压力;优化设计焦炉生产过程中,炭化室的压力调节对于焦炭的质量和生产效率至关重要。
在传统的焦炉操作中,由于炭化室内荒煤气的流通压力往往难以精确控制,导致焦炭质量和产量不稳定。
为了解决这一问题,我们设计了一种炭化室压力调节阀系统,并对其进行了优化。
本文旨在介绍该系统的设计原理和优化策略,并通过实验验证其有效性。
通过对系统构成的详细介绍和流通面积控制策略的深入研究,我们期望能够提高炭化室压力调节的精确度和稳定性,为焦炉生产提供可靠的支持。
这项研究对于优化焦炭生产过程,提高焦炭质量和产量,具有重要的理论和实践意义。
1、系统设计与原理1.1 系统构成与组成部件功能介绍炭化室压力调节阀系统是一个关键的组成部分,用于焦炉上的荒煤气流通压力调节。
该系统由多个关键组成部件构成,包括桥管、上升管和调节机构。
首先,桥管与上升管是该系统的主要通道。
桥管与上升管的内部连通,构成了荒煤气的主要流通通路。
荒煤气从炭化室经过底座进入桥管,在桥管中流动并通过上升管进入调节机构。
这个连通的通道确保了荒煤气能够顺畅地从炭化室流向调节机构,为后续的压力调节提供了基础。
一种焦炉炭化室压力自动调节装置

膜从 萘油 直 接 制取 精萘 , 其 萘 含 量 符 合 国家 精 萘标 准, 且 萘收 率 大 于 8 8 % 。其 原 理 是 基 于 萘 油 与 一定
浓度 的表面活 性剂水溶 液形 成水包 油型 乳化液 , 两相
[ 1 2 ] 米杰 , 李香兰 , 王志忠. 用 乳 化 液 膜 法 从 萘 油 直 接 制 取 精 萘 的研 究[ J ] . 燃料化学学报 , 1 9 9 6 , 2 4 ( 4 ) : 3 4 8 — 3 5 1 .
制 装置 ( 3万 t / a ) 中抽 出部 分脱硫 萘 经结 晶 、 白土处 理、 蒸馏 获 得精 萘 。用加 氢精 制 法精 制 焦化 萘 可
获得 低 含硫 的萘 , 极 大 地 减 少 了 其他 化 学 处 理 带 来 的环境 污染 问题 , 工 业 上 一 般用 于 改善 苯 酐 用 萘 的 质量 , 但 鲜有 独立 的加 氢 精 制法 生产 精 萘 的工 业 装 置 。而且 加 氢精 制法 有氢气 来 源和 副产 品 四氢 萘处 理 的问题 , 所 以此 法在 工艺 上 亟待进 一 步改进 。 2 . 4 其他 分离 方法 1 )液膜 分离 技术 。液 膜分 离技 术是 一 种 快 速 、
[ 3 ] 郑伟. 精萘的生 产和 市场分 析 [ J ] . 化 学工程 与装 备 , 2 0 1 0, 3 9
( 1 2 ) : 1 4 . 煤焦油深加工产 品的开发 和应用进 展 [ J ] . 云 南化工 , 2 0 0 5 , 3 2 ( 1 ) : 4 5 — 4 6 . [ 5 ] 郝东珍 , 耿印权 , 吴九成. 对 已 洗 三混 馏 分 为原 料 采 用 单 炉 双 塔 双效蒸馏制取工业萘工艺的探讨 [ J ] . 河 北冶金 , 1 9 9 8 , 2 0( 2 ) :
炼焦焦炉炭化室均压调节方法
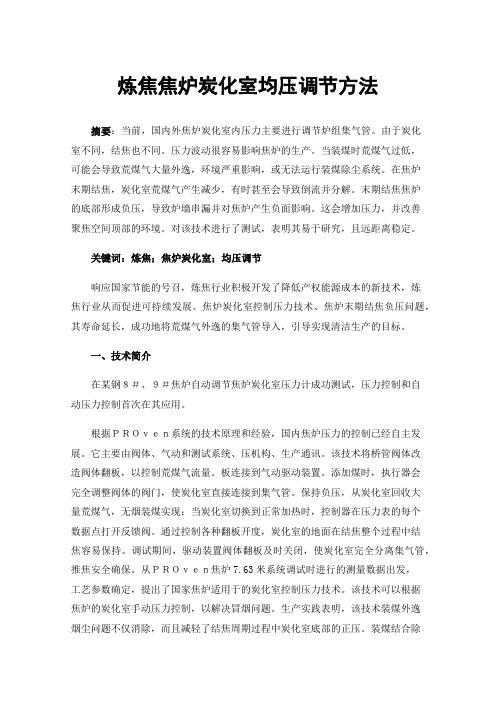
炼焦焦炉炭化室均压调节方法摘要:当前,国内外焦炉炭化室内压力主要进行调节炉组集气管。
由于炭化室不同,结焦也不同。
压力波动很容易影响焦炉的生产。
当装煤时荒煤气过低,可能会导致荒煤气大量外逸,环境严重影响,或无法运行装煤除尘系统。
在焦炉末期结焦,炭化室荒煤气产生减少,有时甚至会导致倒流并分解。
末期结焦焦炉的底部形成负压,导致炉墙串漏并对焦炉产生负面影响。
这会增加压力,并改善聚焦空间顶部的环境。
对该技术进行了测试,表明其易于研究,且远距离稳定。
关键词:炼焦;焦炉炭化室;均压调节响应国家节能的号召,炼焦行业积极开发了降低产权能源成本的新技术,炼焦行业从而促进可持续发展。
焦炉炭化室控制压力技术、焦炉末期结焦负压问题,其寿命延长,成功地将荒煤气外逸的集气管导入,引导实现清洁生产的目标。
一、技术简介在某钢8#、9#焦炉自动调节焦炉炭化室压力计成功测试,压力控制和自动压力控制首次在其应用。
根据PROven系统的技术原理和经验,国内焦炉压力的控制已经自主发展。
它主要由阀体、气动和测试系统、压机构、生产通讯。
该技术将桥管阀体改造阀体翻板,以控制荒煤气流量。
板连接到气动驱动装置。
添加煤时,执行器会完全调整阀体的阀门,使炭化室直接连接到集气管。
保持负压,从炭化室回收大量荒煤气,无烟装煤实现;当炭化室切换到正常加热时,控制器在压力表的每个数据点打开反馈阀。
通过控制各种翻板开度,炭化室的地面在结焦整个过程中结焦容易保持。
调试期间,驱动装置阀体翻板及时关闭,使炭化室完全分离集气管,推焦安全确保。
从PROven焦炉7.63米系统调试时进行的测量数据出发,工艺参数确定,提出了国家焦炉适用于的炭化室控制压力技术。
该技术可以根据焦炉的炭化室手动压力控制,以解决冒烟问题。
生产实践表明,该技术装煤外逸烟尘问题不仅消除,而且减轻了结焦周期过程中炭化室底部的正压。
装煤结合除尘,可以稍微对集气管压力,大量粉尘防止气动系统进入,保证正常运行生产系统。
单炭化室压力调节系统在7.0m焦炉上的应用实践

单炭化室压力调节系统在7.0m焦炉上的应用实践单炭化室压力调节系统在7.0m焦炉上的应用实践随着工业技术的不断发展,为了提高生产效率和质量,提高燃烧效率,节省能源等方面,各行各业都在不断的进行技术改进和创新。
在钢铁行业中,焦炉是重要的生产设备,炭化室的压力调节是其运行中非常重要的环节。
7.0m焦炉是钢铁行业中常用的焦炉设备之一,为了保证焦炉的正常运行,单炭化室压力调节系统在7.0m焦炉上得到了广泛的应用实践。
一、单炭化室压力调节系统的基本原理焦炉的炭化室内,煤焦炭在高温下逐渐转化成焦炭,同时也会氧化成水和一氧化碳等气体。
这些气体在炭化室内不断地产生,如果炭化室内的气体压力不能得到及时的调节,很容易导致焦炉的爆炸事故发生。
因此,单炭化室压力调节系统的基本原理就是在炭化室内产生的气体通过调节出口的气阀,实现调节炭化室内的气体压力。
二、单炭化室压力调节系统的主要设备1.气阀:是单炭化室压力调节系统中重要的设备之一,主要作用是根据实际情况调节出口气阀的开关情况,以达到调节炭化室内气体压力的目的。
2.压力传感器:是单炭化室压力调节系统中另一个重要的设备,用于监视炭化室内的压力变化,将监测到的压力信号传输到控制系统中。
3.控制系统:是单炭化室压力调节系统的核心部分,根据压力传感器传送的信息,实时控制气阀的开关状态,使得炭化室内的气体压力保持在一个安全的范围内。
三、单炭化室压力调节系统在7.0m焦炉上的应用实践1.提高生产效率通过单炭化室压力调节系统的应用,可以实现对炭化室内气体压力的精准控制,避免了因为气体压力不足或过高而导致炭化室内的气体无法流动,从而提高了生产效率。
2.提高燃烧效率通过单炭化室压力调节系统,可以根据实际的情况调节气阀的开关状态,保证炭化室内气体的均匀流动,从而达到提高燃烧效率的目的。
3.保障工作安全炭化室内的气体压力如果不能得到及时的调控,就会导致炭化室内的气体压力过高,从而引起爆炸事故,给工人的生命财产安全带来威胁。
焦炉炭化室压力自动调节技术

焦炉炭化室压力自动调节技术焦炉是制取高质量钢铁的重要设备,其工作原理是将焦炭放入焦炉内进行加热和炭化,产生高质量的煤气和焦炭。
在焦炉内进行炭化过程中,压力是关键因素之一。
因此,焦炉炭化室压力自动调节技术的应用能够使焦炉能够高效稳定地运作,并且将节省时间、成本和减少能源消耗。
焦炉炭化室压力自动调节技术的工作原理是通过传感器采集炭炉内部的压力数据,比较实际数据和预设值进行判断。
然后,控制系统将控制器的输出与变频器相结合,调整风机的转速,从而达到自动调节焦炉内压力的目的。
通过这种方式,工艺工人无需手动干预即可实现高质量、高效率的生产。
焦炉炭化室压力自动调节技术具有以下优点:1.提高了焦炉的稳定性:传统的焦炉炭化操作依靠人工控制炭炉内的空气流量和压力,可能因为不可避免的人为因素导致压力不稳定。
通过应用焦炉炭化室压力自动调节技术,可以实现高精度的压力调节,从而使焦炉内部的压力始终在稳定的状态下工作,最大程度地提高了生产的稳定性和一致性。
2.减少了能源消耗:使用焦炉炭化室压力自动调节技术可以将风机的转速和空气流量与焦炉炭化室内部的压力自动调节。
这种自动化的操作可以最大程度地节省能源使用,提高能源有效利用率,从而在减少能源使用的同时提高生产效率。
3.提高了生产效率:焦炉炭化室压力自动调节技术可以实现自动控制,相比较人工操作而言更为快速和准确。
这一特征不仅可以提高生产效率,还可以帮助企业减少错误率和重复率。
4.减少了人工干预:在传统的焦炉操作中,操作者需要通过观察和调整炭炉内部空气流量来控制压力。
通过使用焦炉炭化室压力自动调节技术,可以将人工干预降至最低。
这样,即可免除操作者人为干预的风险,并提高生产的安全性。
因此,由此可见,焦炉炭化室压力自动调节技术的应用,可以让焦炉生产成为更加安全、高效、准确和经济的过程。
企业只需要通过将传感器、控制器和变频器装置在设备上,即可让焦炉炭化室压力自动调节技术自行控制炭炉的压力,使企业的生产过程变得更加优化。
一种焦炉实现单孔炭化室压力调节装置

燃料与化工Fuel &Chemical ProcessesSep.2020Vol.51No.5图3 JH 煤脱灰前后的红外光谱表3 JH 煤脱灰前后郧值和基氏流动度对比煤样名称G T p /℃T max /℃T k /℃αmax /ddpm JH86426463486135JH(脱灰)8743446849053 实验结果与讨论以JH 煤为原料,采用浓盐酸-氢氟酸两步法制备脱灰煤[7-8],通过单因素实验以及对脱灰煤的相关表征,得出以下结论。
(1)单因素实验表明:反应温度、反应时间和反应环境对脱灰煤的G 值、灰分和收率均有不同程度的影响。
当反应时间为2h、反应温度为55℃、反应环境为N 2时,其脱灰煤性质指标M ad 为1.27%、A d 为0.51%、V daf 为26.14%、FC daf 为72.55%、G 值为87、收率为80%。
(2)酸洗处理可以脱除煤中大量矿物质,也会对煤的结构产生影响;酸洗处理对脂肪类物质影响较小,对含氧官能团和芳香结构影响较大。
(3)酸洗处理的煤样结构受到影响,起黏结作用的活性物质其内部结构受到破坏,导致流动性能大大降低。
参考文献[1]鲍卫仁,常丽萍,谢克昌.酸洗脱灰对原煤样品性能的影响研究[J].太原理工大学学报,2000,31(4):354-357.[2]张军,解强,李兰亭.煤质活性炭脱灰工艺的研究进展[J].煤化工,2007,35(2):20-23.[3]张文达,王鹏翔,孙绍增,等.酸洗脱灰对准东次烟煤结构和反应活性的影响[J].化工学报,2017,68(8):3291-3300.[4]张小科,于珊,张庆武,等.褐煤深度脱灰研究[EB /OL].,2012-05-23/2020-02-23.[5]贺成杰,杜美利,刘雷,等.酸洗脱灰对抚顺琥珀煤结构的影响[J].应用化工,2018,47(12):2609-2612.[6]齐炜,孙会青,裴贤丰,等.影响基氏流动度测定结果的相关因素探讨[J].煤质技术,2013(2):33-36.[7]柏静儒,王擎,魏艳珍,等.桦甸油页岩的酸洗脱灰[J].中国石油大学学报(自然科学版),2010,34(2):150-153,158.[8]蔡光义,马名杰,熊耀,等.窑街和龙口油页岩酸洗脱灰的影响因素[J].化工进展,2014,33(1):70-74,186.蔡明珠 编辑十十十十十十十十十十十十十十十十十十十十十十十十十十十十十十十十十十十十十十十十十十十十十十十一种焦炉实现单孔炭化室压力调节装置本实用新型涉及一种焦炉单孔炭化室压力调节装置,包括安装在桥管内的水封阀盘;还包括测压管和执行机构;所述测压管通过测压管导套安装,测压管导套固定在桥管壁上,测压管穿过测压管导套伸入桥管内,并且伸入端处于氨水喷嘴的喷洒范围内;执行机构安装在集气管操作台或集气管上,执行机构的动力输出端与水封阀盘的搬杆相连;测压管与执行结构均连接计算机控制系统。
- 1、下载文档前请自行甄别文档内容的完整性,平台不提供额外的编辑、内容补充、找答案等附加服务。
- 2、"仅部分预览"的文档,不可在线预览部分如存在完整性等问题,可反馈申请退款(可完整预览的文档不适用该条件!)。
- 3、如文档侵犯您的权益,请联系客服反馈,我们会尽快为您处理(人工客服工作时间:9:00-18:30)。
焦炉炭化室压力自动调节技术
摘要:为实现焦炉炭化室压力稳定,改善焦炉炉顶环境,新开发一种焦炉碳化室压力自动调节技术,经过工程检验证明,该技术易于操作,运行稳定。
关键词:焦炉碳化室压力自动调节
Abstract:A new technology of automatic pressure regulating for coke oven carbonization chamber can stabilize the pressure of coke oven carbonization chamber, by used in the project, this trustworthy technology can be operated easily.
Key words:the pressure of coke oven carbonization chamber automatic regulating
目前,国内外焦炉炭化室内压力,主要是通过集气管对整个炉组进行调节。
由于焦炉各个炭化室所处的结焦状态不同,易产生压力波动,对焦炉生产带来不良影响,如装煤时荒煤气导入集气管的量不够,使大量荒煤气外逸,严重影响环境,或使装煤除尘系统不能正常运行;焦炉结焦末期,炭化室内产生的荒煤气减少,有时甚至导致集气管内的荒煤气向该炭化室倒流并分解;并且在炭化室结焦末期焦炉炭化室底部出现负压,导致炭化室炉墙串漏,对焦炉造成不良影响等。
国外有采用一种叫Proven系统的单个炭化室压力调节系统,可以实现焦炉单个炭化室压力稳定,装煤时可以将大量荒煤气导入集气管中,防
止烟尘外溢,结焦末期又可以避免集气管内的荒煤气向焦炉炭化室倒流,并可解决炭化室结焦末期焦炉炭化室底部出现负压的问题,有利于焦炉生产和稳定运行。
它采用一种叫做固定杯的装置,在控制机构的控制下,通过改变荒煤气的流通断面来实现对单个炭化室压力的调节,解决了前述常规焦炉集气系统存在的问题。
但是,该系统相对复杂,对固定杯的制作要求高,且易粘结焦油,堵塞,影响系统稳定运行,给使用维护也带来了一定的难度。
中冶焦耐工程技术有限公司和济钢共同开发了一种焦炉炭化室单调系统,通过改变桥管阀体结构形式,并通过执行机构和计算机控制系统,实现焦炉炭化室压力的单独调解和控制。
该项技术已在济钢8、9#6m焦炉开发成功,于2010年11月全炉投产,经过2年多的检验,运行稳定,便于操作,通过对单个炭化室的单独压力调节,实现了焦炉炭化室压力的稳定,解决了原系统存在的上述问题,焦炉炉顶环境大有改善。
本项技术已在新兴铸管芜湖三山工程成功采用,现正在开工调试阶段。
1 技术方案
焦炉炭化室压力自动调节装置,它包括上升管、桥管阀体、桥管水封阀装置、集气管、计算机控制系统,流量调节装置、测压装置等。
焦炉炭化室在干馏过程中,荒煤气由炭化室经上升管、桥管阀体、桥管水封阀装置导入集气管再经管道在煤气鼓风机产生的负压作用下导出。
为了实现焦炉炭化室压力自动调节,将桥管阀体的筒体下端部,设计成倾斜面,通过控制水封阀盘的开度,实现改变气体流速,进而
实现控制单个炭化室压力的目的。
水封阀盘的开度由气动执行机构控制。
通过设置在桥管上的压力检测装置,根据检测压力通过计算机来实现每个炭化室压力的调节。
见图1:焦炉炭化室压力自动调节装置示意图(圆形集气管)、图2:焦炉炭化室压力自动调节装置示意图(U形集气管)。
为了实现每个炭化室压力的调节,还需配置计算机控制系统,在焦炉炭化室结焦周期一定的条件下,煤在炭化室干馏过程中产生的荒煤气量是一个由大到小逐步减小波动变化的过程,通过计算机控制系统根据每个炭化室所处的结焦时间和压力变化情况来调节每个水封阀盘开度的大小,达到控制荒煤气在水封阀通行截面、进而实现控制单个炭化室压力的目的。
为了使炭化室压力调节更准确,防止出现较大的偏差,还需在上升管上检测出每个焦炉炭化室的瞬时压力,即在
升管上设置测压装置,通过测压装置测出每个炭化室的即时压力,根据该即时压力与目标压力差,通过计算机控制系统发出控制指令,由气动执行机构控制水封阀盘的开度,最终实现对炭化室压力的稳定调节。
焦炉单个炭化室压力控制,实现焦炉炭化室压力的稳定,解决了由于压力波动带来的一些不良影响。
防止了由于焦炉炭化室负压造成炉墙串漏,改善炉顶环境,提高自动化操作水平,延长焦炉使用寿命。
采用本项技术可以很好解决焦炉装煤烟尘治理问题,可以取消高压氨水装置。
可取消装煤除尘,实现装煤烟尘治理,并且焦炉环境大有改观。
但回收系统需要配合改造。
2 试验简介
焦炉炭化室压力自动调节技术是在济钢8、9#新建焦炉上采用的,焦炉于2009年12月投产,2010年4月开始调试试验工作。
在试验前对原系统的集气管、桥管和炭化室底部压力进行了标定(见图3),由图可见常规焦炉集气系统在结焦中后期炭化室底部常出现负压,由于燃烧室与炭化室的压力差,长时间就会使砖缝石墨烧失,产生炉墙串漏,引起炉墙损坏,影响焦炉使用寿命。
经过半年多的安装调试和反复攻关试验,于2010年10月底完成了全炉的生产调试,投入运行。
调试中集气管压力调整在50、0、-50、-100、-150、-200、-250Pa,根据不同结焦时间,对桥管压力调节设定不同的设定值,目的就是防止炭化室底部出现负压,使每个炭化室压力在理想的工作范围。
投入运行后,实现了每个桥管压力的稳定调节,图4是桥管压力、炭化室底部压力和翻板开度的曲线图,图5是集气管压力在-100Pa时翻板开度和炭化室底部压力曲线图。
由图可见,炭化室底部压力在结焦周期内是处在一个合理范围内的。
3 结语
(1)焦炉炭化室压力自动调节技术,实现了单个炭化室压力的稳定调节,对焦炉稳定生产、延长焦炉使用寿命、改善炉顶环境和提高焦炉操作水平具有积极促进作用。
(2)可以实现取消装煤除尘,实现装煤烟尘治理,但回收系统需要配合改造,改造方式同7.63m引进焦炉。
(3)可以取消高压氨水装置。
参考文献
[1]李守成,马卫华,屈秀珍.7.63m焦炉PROven系统的操作与改进[J].燃料与化工,2010,41(6):21-22.
[2]陈玉村,邱全山,钱虎林,等.7.63m焦炉PROven系统的参数优化[J].燃料与化工,2010,41(4):18-21.。