各种加工方法的切削力计算(车铣钻)
铣削力计算公式详解

铣削力计算公式详解铣削力是指铣削过程中刀具对工件所施加的力,它是铣削加工过程中重要的参数之一。
铣削力大小的计算对于工件的加工质量、工具的寿命以及加工效率都有着重要的影响。
铣削力的计算公式通常是根据铣削的工艺参数以及材料的性质来推导,下面我们将详细解释铣削力的计算公式。
一、铣削力的基本概念为了更好地理解铣削力的计算公式,首先我们需要了解铣削力的基本概念。
在铣削加工过程中,刀具在与工件接触时会产生力的作用。
这些力包括主轴的进给力、切削力和阻力等。
其中,切削力是指刀具在切削过程中与工件发生力的作用,它是决定加工质量和加工效率的重要因素。
铣削力的大小与工件的材料性质、切削刀具的材料和几何形状、切削速度、进给速度、切削深度等因素密切相关。
因此,在进行铣削加工时,需要对铣削力进行精确地计算和控制,以保证加工质量和工具寿命。
二、铣削力的计算公式在铣削加工中,刀具施加在工件上的切削力可以用力学原理进行计算,一般来说,可以参考以下的铣削力计算公式:1.切削力Fc的计算公式切削力Fc是铣削中最常见的力。
在进行铣削加工时,切削力的大小直接影响着刀具的磨损情况和加工表面的加工质量。
切削力Fc的计算公式通常如下:Fc = kc * ae * ap * f //(1)其中,Fc为切削力,单位为牛顿(N);kc为切削力系数,其大小与材料性质、切削条件和刀具类型等有关;ae为轴向切削深度,单位为毫米(mm);ap为径向切削深度,单位为毫米(mm);f为给进量,单位为毫米/刀齿(mm/tooth)。
切削力Fc的大小与刀具材料、刀具的结构和铣削参数等因素有关。
在实际的工程中,我们需要根据具体的加工情况和工件材料来确定切削力系数kc的数值,然后通过公式(1)来计算切削力Fc的大小。
2.主轴的进给力Fr的计算公式除了切削力之外,铣削加工中还存在着主轴的进给力Fr。
主轴的进给力是指主轴在刀具与工件接触时所施加的力,它也是影响加工质量和加工效率的重要因素。
铣床及加工中心铣削力计算

铣床及加工中心铣削力计算铣床及加工中心是现代机械加工中不可或缺的设备,广泛应用于各个行业的加工生产线中。
铣床及加工中心的铣削力计算是机械加工过程中的重要参数,对于加工件的质量和刀具的寿命都有着直接的影响。
下面将对铣床及加工中心的铣削力计算进行详细介绍。
首先,铣削力是指在铣削过程中切削刃对工件单位长度表面上的摩擦力。
它是描述切削刃与工件之间相互作用能量大小及其空间分布的物理量,通常用力矩的大小和方向来表示。
铣床及加工中心的铣削力计算需要考虑多种因素,如刀具材料、工件材料、切削参数、切削速度等。
刀具材料是铣削力计算的重要因素之一、刀具材料的硬度、抗磨性和热稳定性都会影响铣削力的大小。
刀具材料越硬、抗磨性越好,铣削力越小。
常用的刀具材料有高速钢、硬质合金和陶瓷等。
工件材料也是铣削力计算的重要因素之一、工件材料的硬度、韧性和热导率都会影响铣削力的大小。
工件材料越硬、韧性越差、热导率越低,铣削力越大。
常用的工件材料有铸铁、钢材、铝合金和高温合金等。
切削参数是铣削力计算中最直接影响铣削力大小的因素。
主要包括切削速度、进给量和切削深度三个参数。
切削速度越高,铣削力越大;进给量越大,铣削力越大;切削深度越大,铣削力越大。
切削速度是指切削刃在单位时间内与工件接触的次数,单位是米/分钟。
切削速度越高,铣削力越大,因为切削刃与工件接触时间越短,摩擦力越大。
进给量是指切削刃在单位时间内对工件进行切削的量,单位是毫米/转。
进给量越大,铣削力越大,因为切削刃与工件之间的切削面积越大,摩擦力越大。
切削深度是指切削刃在铣削过程中从工件表面到切削层顶部的距离,单位是毫米。
切削深度越大,铣削力越大,因为切削刃与工件接触的切削面积越大,摩擦力越大。
在实际应用中,铣床及加工中心的铣削力计算可以通过经验公式、实验测量和有限元分析等多种方法来进行。
比较常用的经验公式有帕斯卡公式和柯蒂斯公式。
帕斯卡公式是最为常用的铣削力计算公式之一,可以用来计算瞬时铣削力以及稳态铣削力。
机加工钻削公式和定义
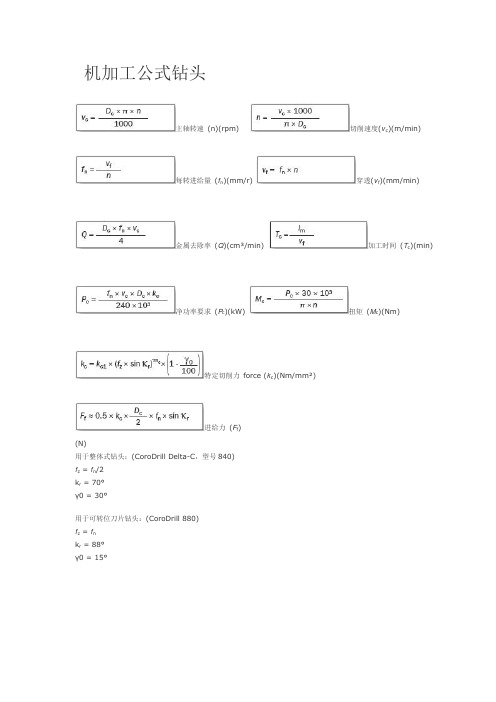
主轴转速 (n)(rpm) 每转进给量 (fn)(mm/r)
切削速度(vc)(m/min) 穿透(vf)(mm/min)
金属去除率 (Q)(cm³/min)
加工时间 (Tc)(min)
净功率要求 (Pc)(kW)
扭矩 (Mc)(Nm)
特定切削力 force (kc)(Nm/mm²)
进给力 (Ff) (N) 用于整体式钻头:(CoroDrill Delta-C,型号 840) fz = fn/2 kr = 70° γ0 = 30°
用于可转位刀片钻头:(CoroDrill 880) fz = fn kr = 88° γ0 = 15°
CoroDrill® 880
公式 2
净功率要求 (Pc)切削力 force (kc) (Nm/mm²)
进给力 (Ff) (N) 用于整体式钻头:(CoroDrill Delta-C,型号 840) fz = fn/2 kr = 70° γ0 = 30°
用于可转位刀片钻头:(CoroDrill 880) fz = fn kr = 88° γ0 = 15°
CoroDrill® 880
钻削定义
钻削生产率与穿透率 vf 密切相关。 可转位刀片钻头 – 一个中心刀片和一个周边刀片
中心刀片从切削速度零工作至 50%的 vc 最大值,周边刀片从 50% 的 vc 最大值直至 vc 最大值。中心刀片形成锥形切屑,而周边刀片形 成类似于使用大切削深度在内圆车削中形成的切屑。 整体式和焊接硬质合金钻头从中心到周边的两个切削刃。
背锥
整体式或焊接硬质合金钻头在其外径稍加研 磨成一定锥度,以提供间隙防止钻头卡滞在 孔中。 孔深
l4 最大推荐孔深度 计算刀具寿命刀具寿命(TL)可以用米表示的 距离、孔数或分钟数来测量。
切削力计算公式【终版】
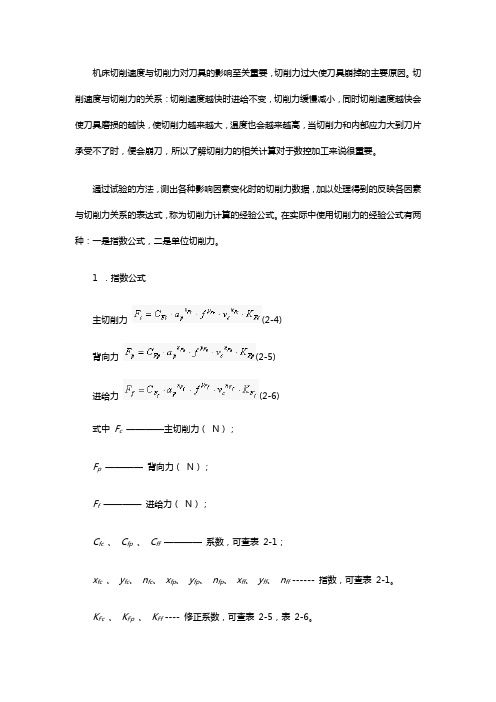
机床切削速度与切削力对刀具的影响至关重要,切削力过大使刀具崩掉的主要原因。
切削速度与切削力的关系:切削速度越快时进给不变,切削力缓慢减小,同时切削速度越快会使刀具磨损的越快,使切削力越来越大,温度也会越来越高,当切削力和内部应力大到刀片承受不了时,便会崩刀,所以了解切削力的相关计算对于数控加工来说很重要。
通过试验的方法,测出各种影响因素变化时的切削力数据,加以处理得到的反映各因素与切削力关系的表达式,称为切削力计算的经验公式。
在实际中使用切削力的经验公式有两种:一是指数公式,二是单位切削力。
1 .指数公式主切削力(2-4)背向力(2-5)进给力(2-6)式中F c————主切削力(N);F p————背向力(N);F f————进给力(N);C fc、C fp、C ff————系数,可查表2-1;x fc、y fc、n fc、x fp、y fp、n fp、x ff、y ff、n ff ------ 指数,可查表2-1。
K Fc、K Fp、K Ff ---- 修正系数,可查表2-5,表2-6。
2 .单位切削力单位切削力是指单位切削面积上的主切削力,用kc表示,见表2-2。
kc=Fc/A d=Fc/(a p·f)=F c/(b d·h d) (2-7)式中A D -------切削面积(mm 2);a p ------- 背吃刀量(mm);f - ------- 进给量(mm/r);h d -------- 切削厚度(mm );b d -------- 切削宽度(mm)。
已知单位切削力k c ,求主切削力F cF c=k c·a p·f=k c·h d·b d (2-8)式2-8中的k c是指f = 0.3mm/r 时的单位切削力,当实际进给量f大于或小于0.3mm /r时,需乘以修正系数K fkc,见表2-3。
表2-3 进给量?对单位切削力或单位切削功率的修正系数K fkc,K fpsf /(mm/r)0.1 0.15 0.2 0.25 0.3 0.350.40.45 0.5 0.6K fkc,K fps1.18 1.11 1.061.031 0.970.960.94 0.9250.9切削力的来源、切削分力金属切削时,切削层及其加工表面上产生弹性和塑性变形;同时工件与刀具之间的相对运动存在着摩擦力。
切削加工常用计算公式
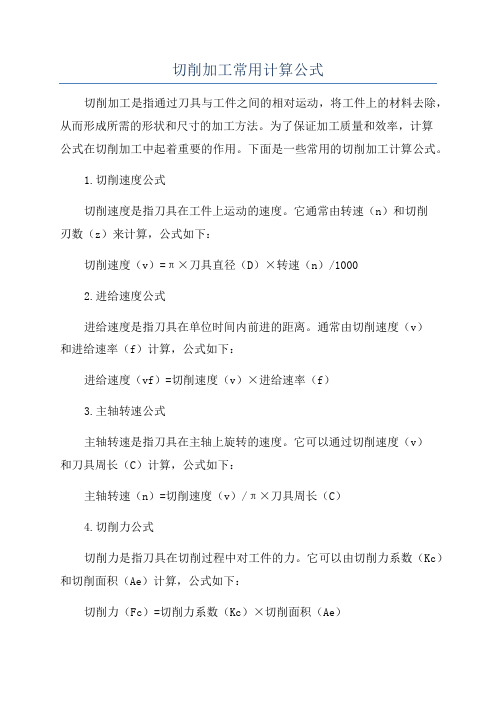
切削加工常用计算公式切削加工是指通过刀具与工件之间的相对运动,将工件上的材料去除,从而形成所需的形状和尺寸的加工方法。
为了保证加工质量和效率,计算公式在切削加工中起着重要的作用。
下面是一些常用的切削加工计算公式。
1.切削速度公式切削速度是指刀具在工件上运动的速度。
它通常由转速(n)和切削刃数(z)来计算,公式如下:切削速度(v)=π×刀具直径(D)×转速(n)/10002.进给速度公式进给速度是指刀具在单位时间内前进的距离。
通常由切削速度(v)和进给速率(f)计算,公式如下:进给速度(vf)=切削速度(v)×进给速率(f)3.主轴转速公式主轴转速是指刀具在主轴上旋转的速度。
它可以通过切削速度(v)和刀具周长(C)计算,公式如下:主轴转速(n)=切削速度(v)/π×刀具周长(C)4.切削力公式切削力是指刀具在切削过程中对工件的力。
它可以由切削力系数(Kc)和切削面积(Ae)计算,公式如下:切削力(Fc)=切削力系数(Kc)×切削面积(Ae)5.切削面积公式切削面积是指刀具与工件接触面积。
它通常由刀具进给量(f)和切削宽度(h)计算,公式如下:切削面积(Ae)=刀具进给量(f)×切削宽度(h)6.加工时间公式加工时间是指完成一个工件的所需时间。
它可以通过工件长度(L)和进给速度(vf)计算,公式如下:加工时间(T)= 工件长度(L)/ 进给速度(vf)7.表面粗糙度公式表面粗糙度是指工件表面的不平滑程度。
它可以由切削速度(v)和切削深度(a)计算,公式如下:表面粗糙度(Ra)=(v×a)/(n×f)8.切削时间公式切削时间是指切削工序所需的时间。
它可以通过切削时间系数(Tc)和加工长度(L)计算,公式如下:切削时间(Tc)=切削时间系数(Tc)×加工长度(L)这些公式在切削加工中起着重要的作用,可以帮助工程师和操作员计算和调整切削参数,以获得最佳的加工质量和效率。
切削力计算方法

一、切削力的来源,切削合力及其分解(见P26)(一)切削力的来源研究切削力,对进一步弄清切削机理,对计算功率消耗,对刀具、机床、夹具的设计,对制定合理的切削用量,优化刀具几何参数等,都具有非常重要的意义。
金属切削时,刀具切入工件,使被加工材料发生变形并成为切屑所需的力,称为切削力。
切削力来源于三个方面:1.克服被加工材料对弹性变形的抗力;2.克服被加工材料对塑性变形的抗力;3.克服切屑对前刀面的摩擦力和刀具后刀面对过渡表面与已加工表面之间的摩擦力。
(二)切削合力及其分解它们的合力Fr作用在前刀面上近切削刃处。
为了便于分析切削力的作用和测量、计算切削力的大小,通常将合力Fr,在按主运动速度方向、切深方向和进给方向作的空间直角坐标轴z、y、x上分解成三个为相互垂直的Fz、Fy和Fx三个分力。
1、主切削力Fz(切向力):主运动切削速度方向的分力。
Fz是最大的一个分力,它消耗了切削总功率的95%左右,是设计与使用刀具的主要依据,并用于验算机床、夹具主要零部件的强度和刚度以及机床电动机功率。
2、切深抗力Fy(径向力):切深方向的分力。
Fy不消耗功率,但在机床一工件一夹具一刀具所组成的工艺系统刚性不足对,是造成振动的丰要因素。
3、进给抗力Fx(轴向力):进给方向的分力。
Fx消耗了总功率5%左右,它是验算机床进给系统主要零、部件强度和刚性的依据。
注:在铣削平面对,上述分力亦称为:Fr——切向力、Fy——径向力、Fx——轴向力。
二、切削力的测定和切削力的经验公式(见P27)生产、实验中经常遇到切削力的计算。
目前切削力的理论计算公式只能供定性分析用。
因为切削力Fz 计算公式是在忽略了温度、正应力、第Ⅲ变形区变形与摩擦力等条件下推导出来的,故不能用于计算。
而求切削力较简单又实用的方法是利用测力仪直接测出或通过实验后整理成的实验公式求得。
1、用测力仪测量切削力测力仪的测量原理是利用切削力作用在测力仪的弹性元件上所产生的变形,或作用在压电晶体上产生的电荷经过转换后,读出Fz、Fx、Fy的值。
切削加工常用计算公式

切削加工常用计算公式文件排版存档编号:[UYTR-OUPT28-KBNTL98-UYNN208]
附录3:切削加工常用计算公式
1.车削加工
每次纵走刀时间t (min)
以上公式中符号说明
D —工件直径 (mm)
ap —背吃刀量(切削深度) (mm) f —每转进给量(mm/r)
lw —工件长度 (mm)
2. 铣削加工
铣削速度Vc (m/min)
主轴转速n (r/min)
每齿进给量fz (mm)
工作台进给速度Vf (mm/min)
金属去除率Q (cm3/min)
净功率P (KW)
扭矩M (Nm)
以上公式中符号说明
D —实际切削深度处的铣刀直径(mm)
Z —铣刀齿数
ap —轴向切深 (mm)
ae —径向切深 (mm)
3. 钻削加工
切削速度Vc (m/min)
主轴转速n (r/min)
每转进给量f (mm/r)
进给速度Vf (mm/min)
金属切除率Q (cm3/min)
净功率P (KW)
扭矩M (Nm)
以上公式中符号说明:
d —钻头直径 (mm)
kc1 —为前角γo=0、切削厚度hm=1mm、切削面积为1mm2时所需的切削力。
(N/mm2)
mc —为切削厚度指数,表示切削厚度对切削力的影响程度,mc值越大表示切削厚度的变化对切削力的影响越大,反之,则越
小
—前角(度)
γ
o。
CNC常用计算公式

CNC常用计算公式在数控加工中,常用的计算公式有:1.转速计算公式:转速(rpm)= 配置的主轴转速(rpm)/ 刀具直径(mm)* 主轴转鼓数(转/齿)2.进给速度计算公式:进给速度(mm/min)= 进给速度设定值(mm/min)/ 预设倍率3.切削速度计算公式:切削速度(m/min)= π × 刀具直径(mm)× 主轴转速(rpm)/ 10004.主轴转速计算公式:主轴转速(rpm)= 切削速度(m/min)× 1000 / π × 刀具直径(mm)5.驱动轴向力计算公式:驱动轴向力(N)= 刀具直径(mm)× 进给速度(mm/min)× 切削力系数6.切削力计算公式:切削力(N)= 轴向切削力(N)÷ cos(铣削角度)7.铣削力计算公式:铣削力(N)=铣削切削阻力(kB)×轴向力(kN)^铣削阻力指数8.主轴电机功率计算公式:主轴电机功率(kW)=铣削力(N)×铣削力系数(kW/N)9.等分计算公式:切削刀数 = 刀具直径(mm)× π / 距离圆周长度(mm)10.速度比计算公式:速度比=同刃次数/刀具齿数11.加工时间计算公式:加工时间(min)= 切削长度(mm) / 进给速度(mm/min) + 换刀时间(min)12.总加工时间计算公式:总加工时间(min)= 加工时间(min)× 加工个数 + 装夹时间(min)13.检测时间计算公式:检测时间(min)= 检测长度(mm) / 检测速度(mm/min) + 置零时间(min)14.总时间计算公式:。
切削力计算公式

铣削切削力计算类别: 工件材料:碳钢、青铜、铝合金、可锻铸铁等 刀具材料:高速钢 铣刀类型:端铣刀 公式:F=(Cp)*(ap)^(1.1)*(fz)^(0.80)*D^(-1.1)*B^(0.95)*z*(Kp) 参数:Cp = 294 参数:ap = 1.8 参数:fz = 0.5 参数:D = 8 参数:B = 8 参数:z = 4 参数:Kp = 0.75 计算结果= 707.914
按照主轴转速1000rpm进给速度01mm转钻穿18mm约需要时间1s
切削力计算公式
一、钻孔切削力和切削力矩计算 按照主轴转速1000rpm,进给速度0.1mm/转,钻穿1.8mm约需要时间1s。
切削力Ff 刀具材料:高速钢 加工方式:钻 公式:Ff=309*D*f^(0.8)*(Kp) 参数:D = 8 参数:f = 0.1 参数:Kp = 0.75(按铜合金多相平均HB>120) 计算结果= 293.839
常用切削速度计算公式
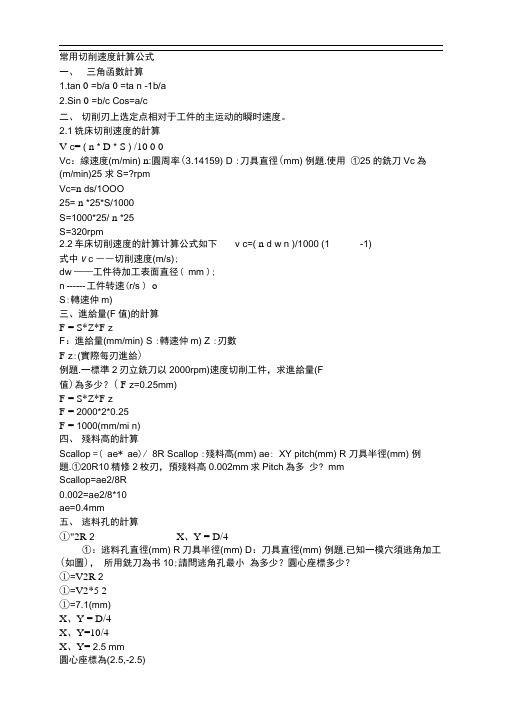
常用切削速度計算公式一、三角函數計算1.tan 0 =b/a 0 =ta n -1b/a2.Sin 0 =b/c Cos=a/c二、切削刃上选定点相对于工件的主运动的瞬时速度。
2.1铣床切削速度的計算V c= ( n * D * S ) /10 0 0Vc:線速度(m/min) n:圓周率(3.14159) D :刀具直徑(mm) 例題.使用①25的銑刀Vc為(m/min)25 求S=?rpmVc=n ds/1OOO25= n *25*S/1000S=1000*25/ n *25S=320rpm2.2车床切削速度的計算计算公式如下v c=( n d w n )/1000 (1 -1)式中v c ――切削速度(m/s);dw ——工件待加工表面直径( mm );n ------ 工件转速(r/s ) oS:轉速仲m)三、進給量(F值)的計算F = S*Z*F zF:進給量(mm/min) S :轉速仲m) Z :刃數F z:(實際每刃進給)例題.一標準2刃立銑刀以2000rpm)速度切削工件,求進給量(F值)為多少?(F z=0.25mm)F = S*Z*F zF = 2000*2*0.25F = 1000(mm/mi n)四、殘料高的計算Scallop =( ae* ae)/ 8R Scallop :殘料高(mm) ae: XY pitch(mm) R 刀具半徑(mm) 例題.①20R10精修2枚刃,預殘料高0.002mm求Pitch為多少? mmScallop=ae2/8R0.002=ae2/8*10ae=0.4mm五、逃料孔的計算①"2R 2 X、Y = D/4①:逃料孔直徑(mm) R刀具半徑(mm) D:刀具直徑(mm) 例題.已知一模穴須逃角加工(如圖),所用銑刀為书10;請問逃角孔最小為多少?圓心座標多少?①=V2R 2①=V2*5 2①=7.1(mm)X、Y = D/4X、Y=10/4X、Y= 2.5 mm圓心座標為(2.5,-2.5)六、取料量的計算Q=( ae* ap*F)/10 0 0Q: 取料量(cm3/min) ae:XY pitch(mm) ap : Z pitch(mm)例題.已知一模仁須cavity等高加工,①35R5的刀XY pitch是刀具的60%每層切1.5mm進給量為2000mm/min求此刀具的取料量為多少?Q=( ae* ap*F)/1000Q= 35*0.6*1.5*2000 /1000Q = 63 cm3/min七、每刃進給量的計算F z =h m * V ( D/ ap )F z:實施每刃進給量h m 理論每刃進給量ap : Z pitch(mm)D:刀片直徑(mm)例題(前提depo XY pitch 是刀具的60%)depo①35R5的刀,切削NAK80材料h m為0.15mm Z軸切深1.5mm 求每刃進給量為多少?F z =h m * V ( D/ ap )F z = 0.2* V 10/1.5F z= 0.5mm沖模刀口加工方法刀口加工深度=板厚—刀口高+鉆尖(0.3D)D表示刀徑鑽頭鑽孔時間公式T(min)=L(min)/N(rpm)*f(mm/rev) =nDL/1000vfL:鑽孔全長N:回轉數f:進刀量系數D:鑽頭直徑v:切削速度如圖孔深1 鑽頭孔全長L 則L=l+D/3T=L/Nf=nDL/1000vf系數表f 直徑mm 進刀mm/rev1.6~3.2 0.025~0.0753.2~6.4 0.05~0.156.4~12.8 0.10~0.2512.8~25 0.175~0.37525 以上0.376~0.6251英寸=25.4mm=8分25.4/牙數二牙距管牙計算公式例如25.4/18 = 1.414 牙距為5/16絲攻馬力(槍鑽)W=Md*N/97.410W:所要動力(KW)Md:扭矩(kg — cm)N:回轉數(r . p . m)扭矩計算公式如下:Md=1/20*f*ps*f為進給量mm/rev系數r為鑽頭半徑賽(mm)a:切削抵抗比值ps.在小進給時,一般鋼為5 0 0 kg/mtf; 一般鑄鐵為300kg/mtf; B1-400K立式升降台铣床主要参数介绍项目单位XA5032 B1-400K 工作面积宽*长mm 320*1250 400*1600工作台承载重量kg 500 800 T型槽数目个 3 3T型槽宽度mm 18 18T型槽间距mm 70 90X向(工作台纵向)手动/机动mm 700/680 900/880行程Y向(滑座横向)手动/机动mm 255/240 315/300 Z向(升降台垂向)手动/机动mm 370/350 385/365 最大回转角度deg ±45 ±45转速r/min 30-1500 300-1500转速级数Step 18 18锥孔ISO7 : 24 NO.50 ISO7 : 24 NO.50 主轴轴向移动距离mm 85 85 主轴端面至工作台距离最小/最大mm 45/415 30/500 主轴中心线至床身垂直导轨面距离mm 350 450切削进给速度mm/minX , Y : 23.5-1180, Z:8-394 X : 19-950 Y : 12.6-634 Z:6.3-317进给快速移动进给速度mm/min X, Y: 2300, Z: 770 X, Y: 2300, Z: 770 进给级数Step 18 18电动主轴电机功率KW 7.5 11机进给电机功率KW 1.5 3其他机床外形尺寸(长*宽*高)mm 2272*1770*2094 2556*2159*2298 机床净重(约)kg 2800 4250。
铣削力计算公式详解

铣削力计算公式详解铣削力是指在铣削加工过程中,机床刀具对工件所施加的力。
了解铣削力的大小和方向对于选择合适的刀具、确定加工参数、保证加工质量和延长刀具寿命都具有重要意义。
铣削力的计算涉及到多个参数和复杂的物理过程,本文将详细介绍铣削力的计算公式及其背后的物理原理。
1.铣削力的基本概念在进行铣削加工时,刀具在切削工件时会受到力的作用,这些力包括切削力、进给力、轴向力和切向力。
其中,切削力是最主要的力,其大小与切削参数、刀具特性、工件材料等有关。
铣削力的大小和方向对加工过程中的刀具选择、机床加工性能、加工质量等均有重要影响。
因此,进行铣削力的准确计算是十分重要的。
2.铣削力的计算参数铣削力的大小与多个参数有关,主要包括刀具和工件材料的物理性质、刀具几何参数、切削参数等。
(1)刀具和工件材料的物理性质刀具和工件材料的硬度、强度、韧性等物理性质会直接影响铣削力的大小。
一般来说,材料的硬度越大,切削力越大。
(2)刀具几何参数刀具几何参数包括刀具刃口半径、主偏角、切削刃数等,这些参数都会影响切削过程中的切削力的大小和方向。
(3)切削参数切削参数包括切削速度、进给速度、切削深度等,这些参数对切削力也会有显著影响。
3.铣削力计算的常用公式铣削力的计算是一个复杂的过程,需要考虑多个参数的相互作用。
根据不同的计算方法和模型,可以得到不同的计算公式。
下面介绍一些常用的铣削力计算公式。
(1)切削力计算公式切削力是铣削过程中最主要的力,其大小与切削参数、刀具特性和工件材料等有关。
常用的切削力计算公式包括切向切削力Fc、轴向切削力Fa和周向切削力Ff的计算公式。
Fc的计算公式一般为:Fc = k1 × k2 × k3 × k4 × k5 × k6× k7其中,k1为材料硬度系数,k2为主偏角系数,k3为刀具刃口半径系数,k4为进给系数,k5为切削速度系数,k6为切削深度系数,k7为切削角系数。
数控机床铣床切削力的计算与控制
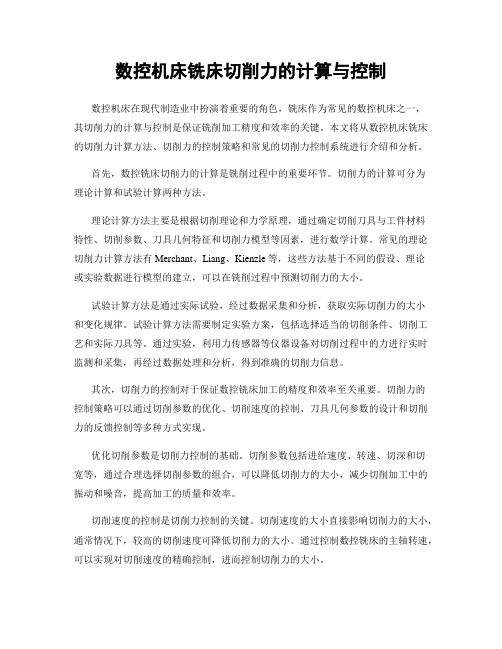
数控机床铣床切削力的计算与控制数控机床在现代制造业中扮演着重要的角色,铣床作为常见的数控机床之一,其切削力的计算与控制是保证铣削加工精度和效率的关键。
本文将从数控机床铣床的切削力计算方法、切削力的控制策略和常见的切削力控制系统进行介绍和分析。
首先,数控铣床切削力的计算是铣削过程中的重要环节。
切削力的计算可分为理论计算和试验计算两种方法。
理论计算方法主要是根据切削理论和力学原理,通过确定切削刀具与工件材料特性、切削参数、刀具几何特征和切削力模型等因素,进行数学计算。
常见的理论切削力计算方法有Merchant、Liang、Kienzle等,这些方法基于不同的假设、理论或实验数据进行模型的建立,可以在铣削过程中预测切削力的大小。
试验计算方法是通过实际试验,经过数据采集和分析,获取实际切削力的大小和变化规律。
试验计算方法需要制定实验方案,包括选择适当的切削条件、切削工艺和实际刀具等。
通过实验,利用力传感器等仪器设备对切削过程中的力进行实时监测和采集,再经过数据处理和分析,得到准确的切削力信息。
其次,切削力的控制对于保证数控铣床加工的精度和效率至关重要。
切削力的控制策略可以通过切削参数的优化、切削速度的控制、刀具几何参数的设计和切削力的反馈控制等多种方式实现。
优化切削参数是切削力控制的基础。
切削参数包括进给速度、转速、切深和切宽等,通过合理选择切削参数的组合,可以降低切削力的大小,减少切削加工中的振动和噪音,提高加工的质量和效率。
切削速度的控制是切削力控制的关键。
切削速度的大小直接影响切削力的大小,通常情况下,较高的切削速度可降低切削力的大小。
通过控制数控铣床的主轴转速,可以实现对切削速度的精确控制,进而控制切削力的大小。
刀具几何参数的设计对于切削力的控制有重要影响。
合理选择刀具的齿数、齿形、刃数和刀尖半径等几何参数,可以有效地降低切削力的大小,提高切削的稳定性和精度。
切削力的反馈控制是切削力控制的高级策略。
铣削力计算公式详解
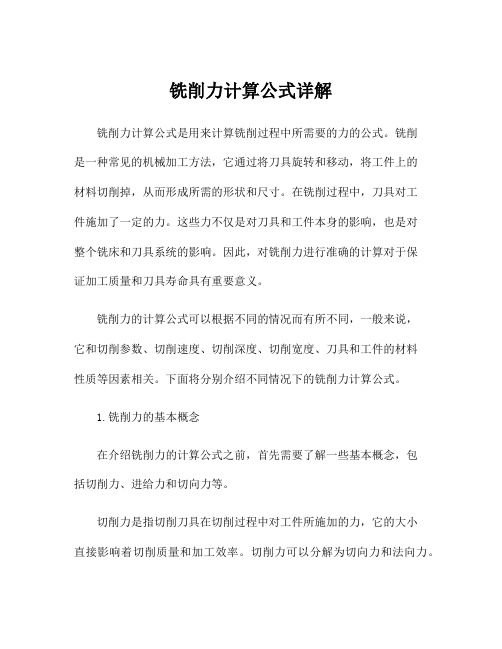
铣削力计算公式详解铣削力计算公式是用来计算铣削过程中所需要的力的公式。
铣削是一种常见的机械加工方法,它通过将刀具旋转和移动,将工件上的材料切削掉,从而形成所需的形状和尺寸。
在铣削过程中,刀具对工件施加了一定的力。
这些力不仅是对刀具和工件本身的影响,也是对整个铣床和刀具系统的影响。
因此,对铣削力进行准确的计算对于保证加工质量和刀具寿命具有重要意义。
铣削力的计算公式可以根据不同的情况而有所不同,一般来说,它和切削参数、切削速度、切削深度、切削宽度、刀具和工件的材料性质等因素相关。
下面将分别介绍不同情况下的铣削力计算公式。
1.铣削力的基本概念在介绍铣削力的计算公式之前,首先需要了解一些基本概念,包括切削力、进给力和切向力等。
切削力是指切削刀具在切削过程中对工件所施加的力,它的大小直接影响着切削质量和加工效率。
切削力可以分解为切向力和法向力。
切向力是指刀具在刀具进给方向上的力,它是刀具推进工件切削表面所产生的力,也是刀具的推进力。
切向力的大小决定了刀具的进给速度和切削深度。
法向力是指刀具对工件表面的垂直力,它是刀具沿着刀具旋转轴方向推压工件表面所产生的力,也是刀具的剪切力。
法向力的大小决定了刀具对工件的切削深度和切削精度。
进给力是指切削力在刀具进给方向上的分量,它是切向力在进给方向上的投影,也是切削负载。
进给力的大小直接影响着刀具的进给速度和切向力的大小。
切向力和法向力的计算公式可以根据不同情况而有所不同,一般来说,它们与切削参数、切削速度、切削深度、切削宽度、刀具和工件的材料性质等因素相关。
下面将分别介绍不同情况下的切向力和法向力的计算公式。
2.铣削力的计算公式铣削力的计算公式可以根据不同的情况而有所不同,下面将分别介绍不同情况下的铣削力的计算公式。
(1)标准铣削力的计算公式在标准铣削中,铣削力的大小可以通过下面的公式计算:Fc = kc * Ae * fFt = kc * Ae * f * tan(α)其中,Fc是切向力,Ft是法向力,kc是切削力系数,Ae是切削面积,f是进给量,α是刀具前角。
常用切削速度计算公式

常用切削速度計算公式一、三角函數計算1.tanθ=b/a θ=tan-1b/a2.Sinθ=b/c Cos=a/c二、切削刃上选定点相对于工件的主运动的瞬时速度。
2.1 铣床切削速度的計算Vc=(π*D*S)/1000Vc:線速度(m/min) π:圓周率(3.14159) D:刀具直徑(mm)例題. 使用Φ25的銑刀Vc為(m/min)25 求S=?rpmVc=πds/100025=π*25*S/1000S=1000*25/ π*25S=320rpm2.2 车床切削速度的計算计算公式如下v c=( π d w n )/1000 (1-1) 式中 v c ——切削速度 (m/s) ;dw ——工件待加工表面直径( mm );n ——工件转速( r/s )。
S:轉速(rpm)三、進給量(F值)的計算F=S*Z*FzF:進給量(mm/min) S:轉速(rpm) Z:刃數Fz:(實際每刃進給)例題.一標準2刃立銑刀以2000rpm)速度切削工件,求進給量(F值)為多少?(Fz=0.25mm)F=S*Z*FzF=2000*2*0.25F=1000(mm/min)四、殘料高的計算Scallop=(ae*ae)/8RScallop:殘料高(mm) ae:XY pitch(mm) R刀具半徑(mm)例題. Φ20R10精修2枚刃,預殘料高0.002mm,求Pitch為多少?mmScallop=ae2/8R0.002=ae2/8*10ae=0.4mm五、逃料孔的計算Φ=√2R2 X、Y=D/4Φ:逃料孔直徑(mm) R刀具半徑(mm) D:刀具直徑(mm)例題. 已知一模穴須逃角加工(如圖),所用銑刀為ψ10;請問逃角孔最小為多少?圓心座標多少?Φ=√2R2Φ=√2*52Φ=7.1(mm)X、Y=D/4X、Y=10/4X、Y=2.5 mm圓心座標為(2.5,-2.5)六、取料量的計算Q=(ae*ap*F)/1000Q:取料量(cm3/min) ae:XY pitch(mm) ap:Z pitch(mm)例題. 已知一模仁須cavity等高加工,Φ35R5的刀XY pitch是刀具的60%,每層切1. 5mm,進給量為2000mm/min,求此刀具的取料量為多少?Q=(ae*ap*F)/1000Q=35*0.6*1.5*2000/1000Q=63 cm3/min七、每刃進給量的計算Fz=hm * √(D/ap )Fz:實施每刃進給量hm:理論每刃進給量 ap:Z pitch(mm)D:刀片直徑(mm)例題 (前提depo XY pitch是刀具的60%)depoΦ35R5的刀,切削NAK80材料hm為0.15mm,Z軸切深1.5mm,求每刃進給量為多少?Fz=hm * √(D/ap )Fz=0.2*√10/1.5Fz=0.5mm沖模刀口加工方法刀口加工深度=板厚-刀口高+鉆尖(0.3D)D表示刀徑鑽頭鑽孔時間公式T(min)=L(min)/N(rpm)*f(mm/rev)=πDL/1000vfL:鑽孔全長N:回轉數f:進刀量系數D:鑽頭直徑v:切削速度如圖孔深l鑽頭孔全長L則L=l+D/3T=L/Nf=πDL/1000vf系數表f直徑mm進刀mm/rev1.6~3.2 0.025~0.0753.2~6.4 0.05~0.156.4~12.8 0.10~0.2512.8~25 0.175~0.37525以上0.376~0.6251英寸=25.4mm=8分25.4/牙數=牙距管牙計算公式例如25.4/18=1.414牙距為5/16絲攻馬力(槍鑽)W=Md*N/97.410W:所要動力(KW)Md:扭矩(kg-cm)N:回轉數(r.p.m)扭矩計算公式如下:Md=1/20*f*ps*f為進給量mm/rev系數r為鑽頭半徑賽(mm)α:切削抵抗比值ps.在小進給時,一般鋼為500kg/m㎡;一般鑄鐵為300kg/m㎡;。
铣床常用计算公式

常用計算公式一、三角函數計算1.tanθ=b/a θ=tan-1b/a2.Sinθ=b/c Cos=a/c二、切削刃上选定点相对于工件的主运动的瞬时速度。
2.1 铣床切削速度的計算Vc=(π*D*S)/1000Vc:線速度(m/min) π:圓周率(3.14159) D:刀具直徑(mm)例題. 使用Φ25的銑刀Vc為(m/min)25 求S=?rpmVc=πds/100025=π*25*S/1000S=1000*25/ π*25S=320rpm2.2 车床切削速度的計算计算公式如下v c=( π d w n )/1000 (1-1) 式中v c ——切削速度(m/s) ;dw ——工件待加工表面直径(mm );n ——工件转速(r/s )。
S:轉速(rpm)三、進給量(F值)的計算F=S*Z*FzF:進給量(mm/min) S:轉速(rpm) Z:刃數Fz:(實際每刃進給)例題.一標準2刃立銑刀以2000rpm)速度切削工件,求進給量(F 值)為多少?(Fz=0.25mm)F=S*Z*FzF=2000*2*0.25F=1000(mm/min)四、殘料高的計算Scallop=(ae*ae)/8RScallop:殘料高(mm) ae:XY pitch(mm) R刀具半徑(mm)例題. Φ20R10精修2枚刃,預殘料高0.002mm,求Pitch為多少?mmScallop=ae2/8R0.002=ae2/8*10ae=0.4mm五、逃料孔的計算Φ=√2R2X、Y=D/4Φ:逃料孔直徑(mm) R刀具半徑(mm) D:刀具直徑(mm)例題. 已知一模穴須逃角加工(如圖),所用銑刀為ψ10;請問逃角孔最小為多少?圓心座標多少?Φ=√2R2Φ=√2*52Φ=7.1(mm)X、Y=D/4X、Y=10/4X、Y=2.5 mm圓心座標為(2.5,-2.5)六、取料量的計算Q=(ae*ap*F)/1000Q:取料量(cm3/min)ae:XY pitch(mm) ap:Z pitch(mm)例題. 已知一模仁須cavity等高加工,Φ35R5的刀XY pitch是刀具的60%,每層切1.5mm,進給量為2000mm/min,求此刀具的取料量為多少?Q=(ae*ap*F)/1000Q=35*0.6*1.5*2000/1000Q=63 cm3/min七、每刃進給量的計算Fz=hm * √(D/ap )Fz:實施每刃進給量hm:理論每刃進給量ap:Z pitch(mm)D:刀片直徑(mm)例題(前提depo XY pitch是刀具的60%)depoΦ35R5的刀,切削NAK80材料hm為0.15mm,Z軸切深1.5mm,求每刃進給量為多少?Fz=hm * √(D/ap )Fz=0.2*√10/1.5Fz=0.5mm沖模刀口加工方法刀口加工深度=板厚-刀口高+鉆尖(0.3D)D表示刀徑鑽頭鑽孔時間公式T(min)=L(min)/N(rpm)*f(mm/rev)=πDL/1000vfL:鑽孔全長N:回轉數f:進刀量系數D:鑽頭直徑v:切削速度如圖孔深l鑽頭孔全長L則L=l+D/3T=L/Nf=πDL/1000vf系數表f直徑mm進刀mm/rev1.6~3.2 0.025~0.0753.2~6.40.05~0.156.4~12.80.10~0.2512.8~250.175~0.37525以上0.376~0.6251英寸=25.4mm=8分25.4/牙數=牙距管牙計算公式例如25.4/18=1.414牙距為5/16絲攻馬力(槍鑽)W=Md*N/97.410W:所要動力(KW)Md:扭矩(kg-cm)N:回轉數(r.p.m)扭矩計算公式如下:Md=1/20*f*ps*f為進給量mm/rev系數r為鑽頭半徑賽(mm)α:切削抵抗比值ps.在小進給時,一般鋼為500kg/m㎡;一般鑄鐵為300kg/m㎡;。
铣削力计算公式详解

铣削力计算公式详解铣削力是在铣削加工过程中切削刀具对工件所产生的力。
在进行铣削加工时,切削力的大小和刀工的功率直接关系到加工的效率和质量。
因此,对铣削力的计算和分析对于选用合适的切削参数和刀具具有很大的意义。
铣削力的计算是一个复杂的工程问题,涉及到材料力学、切削力学、热力学等多个领域的知识。
通常情况下,我们可以通过经验公式或者专业软件来计算和预测铣削力的大小。
下面将详细介绍铣削力的计算公式及其相关知识。
一、切削力的大小与刀具的进给量、转速、切削深度、切削速度等因素有关。
为了能够有针对性地确定切削参数,我们必须首先了解切削力的计算公式及其影响因素。
铣削力的计算公式通常可以通过以下几种方法进行估算:1.经验公式2.力矩平衡法3.数值模拟下面将分别对这三种方法进行详细介绍。
1.经验公式经验公式是根据大量的实验数据总结得出的,它可以简单、直观地估算切削力的大小。
通常情况下,经验公式需要根据不同的刀具和工件材料来选择不同的参数。
最常用的经验公式之一是菲利普公式,其计算公式为:F_c = K_c * D * d * f其中,F_c为切削力,K_c为切削力系数,D为刀具直径,d为切削深度,f为进给量。
菲利普公式是最简单、最常用的切削力计算公式之一。
但是,它只适用于一定范围内的切削参数和材料。
在实际应用中,由于不同的材料、刀具和加工条件的不同,菲利普公式可能会存在一定的误差。
因此,在进行铣削力计算时,还需要结合实际情况来选择合适的切削力计算公式。
2.力矩平衡法力矩平衡法是一种比较常见的精确计算切削力大小的方法。
它是基于切削力与切削热量之间的平衡关系来进行计算的。
通过分析刀具与工件之间的瞬时力平衡状态,可以得到切削力的大小。
这种方法对于复杂工件和刀具的铣削力计算特别有效。
力矩平衡法的基本思想是:对于切削过程中的每一小段切削刀具,刀具上的切削力与切屑推力之间存在一个平衡关系。
因此,我们可以通过对切屑推力的测量来间接测得切削力的大小。
切削加工常用计算公式
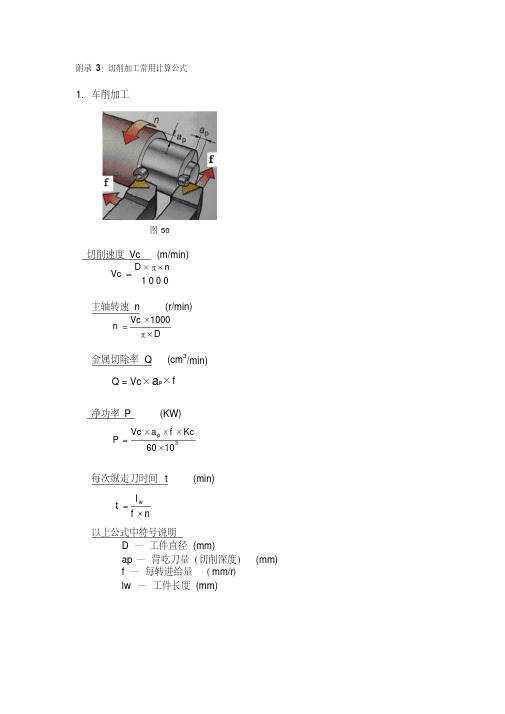
扭矩 M M
(Nm) P 30 10 3
n
以上公式中符号说明 D — 实际切削深度处的铣刀直径 Z — 铣刀齿数
ap — 轴向切深 (mm)
(mm)
ae — 径向切深 (mm)
3. 钻削加工
切削速度 Vc
(m/min)
Vc d
n
1000
主轴转速 n
(r/min)
Vc 1000 n
d
每转进给量 f Vf
mc — 为切削厚度指数, 表示切削厚度对切削力的影响程度, mc值越
大表示切削厚度的变化对切削力的影响越大,反之,则越小
γ o — 前角
(度)
3 、通过活动,使学生养成博览群书的好
习惯。
B 比率分析法和比较分析法不能测算出各因素的影响程度。√ C 采用约当产量比例法,分配原材料费用与分配加工费用所用的完工率都是一致的。X C采用直接分配法分配辅助生产费用时,应考虑各辅助生产车间之间相互提供产品或劳务的情况。错 C 产品的实际生产成本包括废品损失和停工损失。√ C 成本报表是对外报告的会计报表。× C 成本分析的首要程序是发现问题、分析原因。× C 成本会计的对象是指成本核算。×
f n
(mm/r)
进给速度 Vf
(mm/min)
Vf f n
金属切除率 Q (cm3/min) d f Vc
Q 4
净功率 P
(KW)
P
f Vc d kc 240 103
扭矩 M M
(Nm) P 30 10 3
n
以上公式中符号说明:
d — 钻头直径 (mm)
kc1 — 为前角 γo=0、切削厚度 hm=1m、m切削面积为 1mm2 时所需的切 削力。 (N/mm 2)
切削参数和计算公式 ppt课件

F力=Kc xfr xap
T= F力 x(D/2) =P x9549/RPM
切削参数和计算公式
镗削功率和扭矩计算
计算镗削功率时注意Vc减半, 即Vc镗=1/2Vc车
Vc xap xfr xkc P=
60037.2 T= F力 x(D/2)
=P x9549/RPM
举例:镗削奥氏体不锈钢,工件硬度HB200, 工 件直径75mm,切深3mm,走刀量0.2mm/r, 切削速 度115m/min, 材料单位切削力为2900N/mm2,加 工长度为100mm
“Start value”
Speed range
10 min. tool life 15 min. tool life 30 min. tool life
切削参数和计算公式
切削参数和计算公式
切削参数和计算公式
切削参数和计算公式
切削参数和计算公式
切削参数和计算公式
切削参数和计算公式
车削功率和扭矩计算
L Time= fr xN
Vc xap xfr xkc P=
60037.2
金属去除率V=230x2x0.2=92 立方厘米每分钟 每加工一个零件的时间=100/(0.2x976)=0.51分钟 车削功率P=(230x3x0.2x2900)/60037.2=6.7千瓦 车削力=2900 x0.2 x3=1740牛顿=177.5公斤 车削扭矩T=1740 x37.5=65牛顿米
切削参数和计算公式
选择切削参数的方法
一、根据刀片盒选择切削参数
二、参考样本上切削参数一栏中的切削速度推荐值 三、使用切削参数选择软件
切削参数和计算公式
Make use of the tools
Application range
各种加工方法的切削力计算(车、铣、钻)

各种加工方法的切削力计算
支持
收藏
问答
支付
引用
分享到:0
目录
•各种加工方法的切削力计算
o—车削切削力计算
o—钻削切削力计算
o—铣削切削力计算
内容
各种加工方法的切削力计算
计算夹具夹紧力,首先要计算切削力,切削力的计算经验公式很多,可根据实际情况选择应用。
切削力影响因素很多,主要是工件材料、刀具材料及几何参数、加工方式以及切削参数等,其它影响因素有切削温度、切削环境等。
车削切削力计算
钻削切削力计算
铣削切削力计算。