五机械加工表面质量PPT课件
合集下载
机械加工表面加工质量

❖ 脆性材料:加工脆性材料时,其切削呈碎粒状,
由于切屑的崩碎而在加工表面留下许多麻点,使表 面粗糙。
机械加工表面加工质量
(2)切削速度的影响 (3)进给量的影响
加工塑性材料时,切削速度对
表面粗糙度的影响(对积屑瘤和鳞 刺的影响)见如图4-41所示。
此外,切削速度越高,塑性变 形越不充分,表面粗糙度值越小
(1)磨削用量
▪ 砂轮的转速↑ →材料塑性变形↓ → 表面粗
糙度值↓ ;
▪磨削深度↑、工件速度↑ → 塑性变形↑ →表
面粗糙度值↑ ; 为提高磨削效率,通常在开始磨削时采
用较大的径向进给量,而在磨削后期采用较 小的径向进给量或无进给量磨削,以减小表 面粗糙度值。
机械加工表面加工质量
(2)工件材料
•太硬易使磨粒磨钝 →Ra ↑ ; •太软容易堵塞砂轮→Ra ↑ ; •韧性太大,热导率差会使磨
影响显微硬度因素
•塑变引起的冷硬
•金相组织变化引起 的硬度变化
表面物理力学 性能
影响残余应力因素
•冷塑性变形 •热塑性变形 •金相组织变化
影响金相组织变化 因素
•切削热
机械加工表面加工质量
1. 表面层的冷作硬化
(1) 表面层加工硬化的产生
定义:机械加工时,工件表面层金属受到 切削力的作用产生强烈的塑性变形,使晶 格扭曲,晶粒间产生剪切滑移,晶粒被拉 长、纤维化甚至碎化,从而使表面层的强 度和硬度增加,这种现象称为加工硬化, 又称冷作硬化和强化。
机械加工表面加工质量
三、表面层金相组织变化与磨削烧伤
1.表面层金相组织变化与磨削烧伤的产生
切削加工中,由于切削热的作用,在工件的加 工区及其邻近区域产生了一定的温升。
定义:磨削加工时,表面层有很高的温度,当 温度达到相变临界点时,表层金属就发生金相组织 变化,强度和硬度降低、产生残余应力、甚至出现 微观裂纹。这种现象称为磨削烧伤。
由于切屑的崩碎而在加工表面留下许多麻点,使表 面粗糙。
机械加工表面加工质量
(2)切削速度的影响 (3)进给量的影响
加工塑性材料时,切削速度对
表面粗糙度的影响(对积屑瘤和鳞 刺的影响)见如图4-41所示。
此外,切削速度越高,塑性变 形越不充分,表面粗糙度值越小
(1)磨削用量
▪ 砂轮的转速↑ →材料塑性变形↓ → 表面粗
糙度值↓ ;
▪磨削深度↑、工件速度↑ → 塑性变形↑ →表
面粗糙度值↑ ; 为提高磨削效率,通常在开始磨削时采
用较大的径向进给量,而在磨削后期采用较 小的径向进给量或无进给量磨削,以减小表 面粗糙度值。
机械加工表面加工质量
(2)工件材料
•太硬易使磨粒磨钝 →Ra ↑ ; •太软容易堵塞砂轮→Ra ↑ ; •韧性太大,热导率差会使磨
影响显微硬度因素
•塑变引起的冷硬
•金相组织变化引起 的硬度变化
表面物理力学 性能
影响残余应力因素
•冷塑性变形 •热塑性变形 •金相组织变化
影响金相组织变化 因素
•切削热
机械加工表面加工质量
1. 表面层的冷作硬化
(1) 表面层加工硬化的产生
定义:机械加工时,工件表面层金属受到 切削力的作用产生强烈的塑性变形,使晶 格扭曲,晶粒间产生剪切滑移,晶粒被拉 长、纤维化甚至碎化,从而使表面层的强 度和硬度增加,这种现象称为加工硬化, 又称冷作硬化和强化。
机械加工表面加工质量
三、表面层金相组织变化与磨削烧伤
1.表面层金相组织变化与磨削烧伤的产生
切削加工中,由于切削热的作用,在工件的加 工区及其邻近区域产生了一定的温升。
定义:磨削加工时,表面层有很高的温度,当 温度达到相变临界点时,表层金属就发生金相组织 变化,强度和硬度降低、产生残余应力、甚至出现 微观裂纹。这种现象称为磨削烧伤。
机械加工质量培训课件PPT(共 104张)

例: ①滚刀用阿基米德蜗杆代替渐开线蜗杆 (近似的刀具轮廓); ②模数铣刀铣齿(近似的刀具轮廓); ③用公制丝杆车蜗杆或英制螺纹。 (近似的加工运动)
2.1 机械加工精度
i工 机件 (蜗 床杆 丝) 杆 PP螺 1螺 ZZ距 距 21ZZ34
例1. 在公制车床上车模数为2mm蜗杆时,挂轮计算式为 :
z1 z2
z3 z4
P(P机 (1 床 蜗丝 杆杆 螺螺 距距 )) ,若P=6mm,
Z 1 1,1 Z 2 0 7,Z 0 3 8,Z 0 4 1,2 求加0 工后蜗杆螺距
误差是多少?
i
P1=2
P=6
解: i工 机件 (蜗 床杆 丝) 杆 PP螺 1螺 ZZ距 距 21ZZ34 P ห้องสมุดไป่ตู้iP Z Z2 1Z Z3 4P1 71 0 2 800 066.2857
1)主轴回转误差。 纯径向跳动误差 轴向窜动误差 纯角度摆动误差
①主轴纯径向跳动误差对加精度的影响。 产生的主要原因:主轴支承轴颈的圆度误差、轴承工作表面的
圆度误差等。 a. 切削力F的作用方向不变(见图2-5 车外圆的情形)
2
R
1
3
R3
R1 △R
o o′
理论位置
实际位置
R
4
车外圆时它使加工面产生圆度和圆柱度误差。
@加工质量与设备、工艺方法、工艺措施有关。
2.1 机械加工精度
2.1.1 概述 1、机械加工精度(简称加工精度):是指零件在机械加工后
的几何参数(尺寸、几何形状和表面间相互位置)的实际值和理 论值相符合的程度。
2、加工误差:实际参数与理论参数的差值
2.1 机械加工精度
2.1.2 影响加工精度的因素及其分析 在机械加工中,零件的尺寸、几何形状和表面间相互位置的
2.1 机械加工精度
i工 机件 (蜗 床杆 丝) 杆 PP螺 1螺 ZZ距 距 21ZZ34
例1. 在公制车床上车模数为2mm蜗杆时,挂轮计算式为 :
z1 z2
z3 z4
P(P机 (1 床 蜗丝 杆杆 螺螺 距距 )) ,若P=6mm,
Z 1 1,1 Z 2 0 7,Z 0 3 8,Z 0 4 1,2 求加0 工后蜗杆螺距
误差是多少?
i
P1=2
P=6
解: i工 机件 (蜗 床杆 丝) 杆 PP螺 1螺 ZZ距 距 21ZZ34 P ห้องสมุดไป่ตู้iP Z Z2 1Z Z3 4P1 71 0 2 800 066.2857
1)主轴回转误差。 纯径向跳动误差 轴向窜动误差 纯角度摆动误差
①主轴纯径向跳动误差对加精度的影响。 产生的主要原因:主轴支承轴颈的圆度误差、轴承工作表面的
圆度误差等。 a. 切削力F的作用方向不变(见图2-5 车外圆的情形)
2
R
1
3
R3
R1 △R
o o′
理论位置
实际位置
R
4
车外圆时它使加工面产生圆度和圆柱度误差。
@加工质量与设备、工艺方法、工艺措施有关。
2.1 机械加工精度
2.1.1 概述 1、机械加工精度(简称加工精度):是指零件在机械加工后
的几何参数(尺寸、几何形状和表面间相互位置)的实际值和理 论值相符合的程度。
2、加工误差:实际参数与理论参数的差值
2.1 机械加工精度
2.1.2 影响加工精度的因素及其分析 在机械加工中,零件的尺寸、几何形状和表面间相互位置的
机械加工表面质量PPT51页课件

5.2 加工表面质量对零件使用性能的影响
*
3. 表面纹理对耐磨性的影响
表面纹理的形状及刀纹方向对耐磨性的影响,纹理形状及刀纹方向影响有效接触面积与润滑液的存留。
4.表面层产生的金相组织变化对零件耐磨性的影响
金相组织的变化引起基体材料硬度的变化,进而影响零件的耐磨性。
5.2 加工表面质量对零件使用性能的影响
5.2 加工表面质量对零件使用性能的影响
*
2.表面层冷作硬化与残余应力对耐疲劳性的影响 适度的表面层冷作硬化能提高零件的疲劳强度; 残余应力有拉应力和压应力之分, 残余拉应力:易使已加工表面产生裂纹并使其扩展而降低疲劳强度。 残余压应力:能够部分地抵消工作载荷施加的拉应力,延缓疲劳裂纹的扩展,从而提高零件的疲劳强度。
5.4 影响加工表面层物理机械性能的因素
*
衡量表面层加工硬化程度的指标有下列三项: 1)表面层的显微硬度H; 2)硬化层深度h; 3)硬化程度N N=(H-H0)/H0×100% 式中 H0——工件原表面层的显微硬度。
粗糙度越大,耐腐蚀性越差
压应力提高耐腐蚀性,拉应力反之则降低耐腐蚀性
总结:
*
机械加工中,表面粗糙度形成的原因大致可归纳为几何因素和物理力学因素两个方面。
(一)切削加工时表面粗糙度的影响因素
1. 几何因素
刀尖圆弧半径rε 主偏角kr、副偏角kr′ 进给量f
5.3 影响加工表面粗糙度的因素
(一)表面质量对零件耐磨性的影响
5.2 加工表面质量对零件使用性能的影响
零件磨损三个阶段:初期磨损阶段;正常磨损阶段;剧烈磨损阶段
零件耐磨性的影响因素: 摩擦副的材料;润滑条件;表面质量(接触面积)。
图5-1 磨损过程的基本规律
*
3. 表面纹理对耐磨性的影响
表面纹理的形状及刀纹方向对耐磨性的影响,纹理形状及刀纹方向影响有效接触面积与润滑液的存留。
4.表面层产生的金相组织变化对零件耐磨性的影响
金相组织的变化引起基体材料硬度的变化,进而影响零件的耐磨性。
5.2 加工表面质量对零件使用性能的影响
5.2 加工表面质量对零件使用性能的影响
*
2.表面层冷作硬化与残余应力对耐疲劳性的影响 适度的表面层冷作硬化能提高零件的疲劳强度; 残余应力有拉应力和压应力之分, 残余拉应力:易使已加工表面产生裂纹并使其扩展而降低疲劳强度。 残余压应力:能够部分地抵消工作载荷施加的拉应力,延缓疲劳裂纹的扩展,从而提高零件的疲劳强度。
5.4 影响加工表面层物理机械性能的因素
*
衡量表面层加工硬化程度的指标有下列三项: 1)表面层的显微硬度H; 2)硬化层深度h; 3)硬化程度N N=(H-H0)/H0×100% 式中 H0——工件原表面层的显微硬度。
粗糙度越大,耐腐蚀性越差
压应力提高耐腐蚀性,拉应力反之则降低耐腐蚀性
总结:
*
机械加工中,表面粗糙度形成的原因大致可归纳为几何因素和物理力学因素两个方面。
(一)切削加工时表面粗糙度的影响因素
1. 几何因素
刀尖圆弧半径rε 主偏角kr、副偏角kr′ 进给量f
5.3 影响加工表面粗糙度的因素
(一)表面质量对零件耐磨性的影响
5.2 加工表面质量对零件使用性能的影响
零件磨损三个阶段:初期磨损阶段;正常磨损阶段;剧烈磨损阶段
零件耐磨性的影响因素: 摩擦副的材料;润滑条件;表面质量(接触面积)。
图5-1 磨损过程的基本规律
机械加工质量及其控制概述ppt68页课件

第一节 概述
二、机械加工表面质量
(一)表面质量的概念
粗糙度太大、太小都不耐磨
适度冷硬能提高耐磨性
对疲劳强度的影响
对耐腐蚀性能的影响
对工作精度的影响
粗糙度越大,疲劳强度越差
适度冷硬、残余压应力能提高疲劳强度
粗糙度越大、工作精度降低
残余应力越大,工作精度降低
粗糙度越大,耐腐蚀性越差
压应力提高耐腐蚀性,拉应力反之则降低耐腐蚀性
本章提要
机械产品质量取决于零件的加工质量和产品的装配质量,机器零件的加工质量是整台机器质量的基础。 机器零件的加工质量一般用机械加工精度和加工表面质量两个重要指标表示,它的高低将直接影响整台机器的使用性能和寿命。 机械产品加工的首要任务,就是保证零件的机械加工质量要求。 本章重点讨论影响机械加工精度和表面质量的因素及其控制方法。
(1)主轴回转误差
第二节 机械加工精度的影响因素及控制
一、工艺系统几何误差对加工精度的影响
(一)机床的几何误差
(1)主轴回转误差
第二节 机械加工精度的影响因素及控制
一、工艺系统几何误差对加工精度的影响
(一)机床的几何误差
主轴回转误差的基本形式
车床上车削
镗床上镗削
内、外圆
端面
螺纹
孔
端面
纯径向跳动
机械加工中,采用近似的成形运动或近似的刀刃形状进行加工,虽然会由此产生一定的原理误差,但却可以简化机床结构和减少刀具数,只要加工误差能够控制在允许的制造公差范围内,就可采用近似加工方法。
原始误差
工艺系统动误差
工艺系统受力变形
刀具磨损
残余应力引起变形
测量误差
工艺系统热变形
第二节 机械加工精度的影响因素及控制
二、机械加工表面质量
(一)表面质量的概念
粗糙度太大、太小都不耐磨
适度冷硬能提高耐磨性
对疲劳强度的影响
对耐腐蚀性能的影响
对工作精度的影响
粗糙度越大,疲劳强度越差
适度冷硬、残余压应力能提高疲劳强度
粗糙度越大、工作精度降低
残余应力越大,工作精度降低
粗糙度越大,耐腐蚀性越差
压应力提高耐腐蚀性,拉应力反之则降低耐腐蚀性
本章提要
机械产品质量取决于零件的加工质量和产品的装配质量,机器零件的加工质量是整台机器质量的基础。 机器零件的加工质量一般用机械加工精度和加工表面质量两个重要指标表示,它的高低将直接影响整台机器的使用性能和寿命。 机械产品加工的首要任务,就是保证零件的机械加工质量要求。 本章重点讨论影响机械加工精度和表面质量的因素及其控制方法。
(1)主轴回转误差
第二节 机械加工精度的影响因素及控制
一、工艺系统几何误差对加工精度的影响
(一)机床的几何误差
(1)主轴回转误差
第二节 机械加工精度的影响因素及控制
一、工艺系统几何误差对加工精度的影响
(一)机床的几何误差
主轴回转误差的基本形式
车床上车削
镗床上镗削
内、外圆
端面
螺纹
孔
端面
纯径向跳动
机械加工中,采用近似的成形运动或近似的刀刃形状进行加工,虽然会由此产生一定的原理误差,但却可以简化机床结构和减少刀具数,只要加工误差能够控制在允许的制造公差范围内,就可采用近似加工方法。
原始误差
工艺系统动误差
工艺系统受力变形
刀具磨损
残余应力引起变形
测量误差
工艺系统热变形
第二节 机械加工精度的影响因素及控制
机械加工质量及其控制培训教材(PPT 122页)

镗床:主轴受力方向不断改变,故主要取决于主轴轴承孔的形 状精度。
主轴径向跳动 将会造成什么
加工误差?
28
② 轴向窜动
滑动轴承主轴的轴向窜动量取决于止推(承载)轴承副 中端面与主轴轴线垂直度较高者
影响滚动轴承主轴轴向窜动的主要 因素有:
滚道与轴线的垂直度 滚动体形状误差(轴向间隙变化) 尺寸一致性(承载不均而降低刚度)
基本成形运动 (回转、直线)
成形运动法 相互位置关系 (几何关系) 均准确
保证形 状精度 的条件
速度关系 (运动关系)
非成形运动法 足够的检测精度
19
机械制造新技术:
数控(Numerical Control—NC)技术 加工中心(MC) 工业机器人(Industrial Robot)技术 自适应控制机床(Adaptive Control Machine Tools) 计算机辅助制造(Computer Aided Manufacturing-CAM) 计算机数控机床(Computerized Numerical Control-CNC)
若粗糙度值过小,可能增加制造成本,且可能破坏润滑油膜,造成干摩擦。
加工表面硬化到一定程度能使耐磨性有所提高,但硬化过 度反会使结晶组织出现过度变形,甚至产生裂纹或剥落,使磨损 加剧,使耐磨性降低 。
10
(2)影响疲劳强度
交变载荷作用时,表面粗糙度、划痕及微裂纹等均会引起 应力集中,从而降低疲劳强度。
20
机械制造新技术:
可变制造系统 柔性制造单元 数字化制造 无人化机械制造厂
现阶段:
生物加工的纯铜微齿轮
互联网技术的迅猛发展(e-制造、网络控制、 分子开关)
工业生产追求更大的投入产出经济效益
8:机械加工表面质量PPT课件
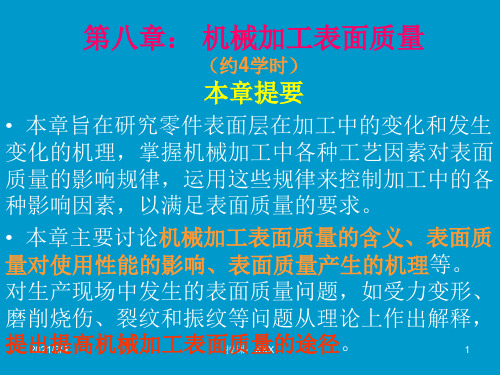
⑵热态塑性变形
机械加工时,切削或磨
削热使工件表面局部温
升过高,引起高温塑性
变形(图8.10为因加工
温度而引起残余应力的
202示1/3/9意图)
授课:X的高温会引 起表面的相变。
• 实际机械加工后的表面 层残余应力及其分布, 是上述三方面因素综合 作用的结果,在一定条 件下,其中某一或二种 因素可能主导作用。(图 8.11所示为三类磨削条 件下产生的表面层残余 应力)
• 磨削淬火钢时表面层烧伤有以下三种:
①回火烧伤
磨削区温度超过马氏体转变温度而未超过相变温度;
②淬火烧伤
磨削区温度超过相变温度 (用冷却液时);
③退火烧伤
不用冷却液进行干磨削时,磨削区温度超过相变温
202度1/3/,9 工件表层被退火。授课:XXX
13
8.3.2.2影响磨削加工时金相组织 变化的因素
8.1.2.4对零件的其它影响
• 表面质量对零件的配合质量、密封性能及磨擦系 数都有很大的影响。表面粗糙度值越大,对动配
合来说,使用不久就会使配合性质发生变化;对
静配合来说,压装时会减少过盈量。表面层有裂
纹、加工痕迹等各种缺陷,在动载荷的作用下,
可能引起应力集中等。
2021/3/9
授课:XXX
7
8.2机械加工后的表面粗糙度 8.2.1切削加工后的表面粗糙度
• 表面粗糙度、表面波度。 ⑵表面层的物理机械性能
• 表面导冷作硬化、表面层金相组织的变化、 表面层残余应力
2021/3/9
授课:XXX
2
2021/3/9
授课:XXX
3
8.1.2表面质量对零件使用性能的影响 8.1.2.1对零件耐磨性的影响
机械制造工艺课件第四章机械加工表面质量

★★★
机械制造工艺
★★★
第四章
第一节
第二节 第三节 第四节
机械加工表面质量
基本概念
表面粗糙度的形成及其影响因素 加工表面力学物理性能的变化及其影响因素 机械加工中的振动
★★★
机械制造工艺
基本慨念
★★★
第一节
零件机械加工表面质量是指零件在机械加工后 表面层的微观几何形状误差和力学物理性能。零件 机械加工后表面层中存在着表面粗糙度、表面波度、 表面加工纹理等微观几何形状误差以及伤痕等缺陷, 零件表面层在加工过程中还会产生加工硬化、金相 组织变化及残余应力等现象。上述种种因素综合作 用的结果,直接影响了零件的寿命及可靠性,从而 影响产品的质量和使用性能。
★★★
机械制造工艺
★★★
图4-2
初期磨损量与零件表面粗糙度 1—轻载荷 2—重载荷
★★★
机械制造工艺
★★★
2、表面质量对零件疲劳强度的影响
零件在交变载荷的作用下,其表面微观不平的凹谷 处和表面层的缺陷处容易引起应力集中而产生疲劳裂纹, 造成零件的疲劳破坏。试验表明,减小零件表面粗糙度 值可以使零件的疲劳强度有所提高。因此,对于一些承 受交变载荷的重要零件,如曲轴其曲拐与轴颈交接处精 加工后常进行光整加工,以减小零件的表面粗糙度值, 提高其疲劳强度。
★★★
机械制造工艺
★★★
图4-3
表面残留面积
★★★
机械制造工艺
★★★
金属切削过程幻灯片
★★★
机械制造工艺
★★★
2、影响表面粗糙度的工艺因素及改善措施
(1)切削用量的影响 进给量大,切屑变形也大,切屑 与刀具前刀面的摩擦以及后刀面与已加工表面的摩擦加剧, 从而增大工件表面粗糙度值。因此,减小进给量利于减小工 vc 件表面粗糙度值。 切削速度对表面粗糙度的影响因工件材料而异。对于塑 性材料,一般情况下,低速或高速切削时,不会产生积屑瘤, 故加工表面粗糙度值都较小,但在中等切削速度下,塑性材 料的工件容易产生积屑瘤或鳞刺,且塑性变形较大,如图4-4 所示。对于脆性材料,加工表面粗糙度主要是由于脆性挤裂 碎裂而成,与切削速度关系较小。所以精加工塑性材料时往 往选择高速或低速精切,以获得较小的表面粗糙度值。
机械制造工艺
★★★
第四章
第一节
第二节 第三节 第四节
机械加工表面质量
基本概念
表面粗糙度的形成及其影响因素 加工表面力学物理性能的变化及其影响因素 机械加工中的振动
★★★
机械制造工艺
基本慨念
★★★
第一节
零件机械加工表面质量是指零件在机械加工后 表面层的微观几何形状误差和力学物理性能。零件 机械加工后表面层中存在着表面粗糙度、表面波度、 表面加工纹理等微观几何形状误差以及伤痕等缺陷, 零件表面层在加工过程中还会产生加工硬化、金相 组织变化及残余应力等现象。上述种种因素综合作 用的结果,直接影响了零件的寿命及可靠性,从而 影响产品的质量和使用性能。
★★★
机械制造工艺
★★★
图4-2
初期磨损量与零件表面粗糙度 1—轻载荷 2—重载荷
★★★
机械制造工艺
★★★
2、表面质量对零件疲劳强度的影响
零件在交变载荷的作用下,其表面微观不平的凹谷 处和表面层的缺陷处容易引起应力集中而产生疲劳裂纹, 造成零件的疲劳破坏。试验表明,减小零件表面粗糙度 值可以使零件的疲劳强度有所提高。因此,对于一些承 受交变载荷的重要零件,如曲轴其曲拐与轴颈交接处精 加工后常进行光整加工,以减小零件的表面粗糙度值, 提高其疲劳强度。
★★★
机械制造工艺
★★★
图4-3
表面残留面积
★★★
机械制造工艺
★★★
金属切削过程幻灯片
★★★
机械制造工艺
★★★
2、影响表面粗糙度的工艺因素及改善措施
(1)切削用量的影响 进给量大,切屑变形也大,切屑 与刀具前刀面的摩擦以及后刀面与已加工表面的摩擦加剧, 从而增大工件表面粗糙度值。因此,减小进给量利于减小工 vc 件表面粗糙度值。 切削速度对表面粗糙度的影响因工件材料而异。对于塑 性材料,一般情况下,低速或高速切削时,不会产生积屑瘤, 故加工表面粗糙度值都较小,但在中等切削速度下,塑性材 料的工件容易产生积屑瘤或鳞刺,且塑性变形较大,如图4-4 所示。对于脆性材料,加工表面粗糙度主要是由于脆性挤裂 碎裂而成,与切削速度关系较小。所以精加工塑性材料时往 往选择高速或低速精切,以获得较小的表面粗糙度值。
机械加工表面质量
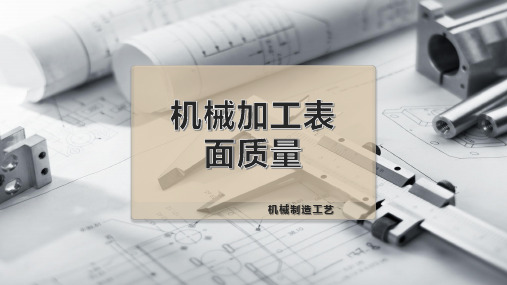
③ 金相组织变化引起 的残余应力。
切削过程中,在切削力作用下, 金属切削层产生剧烈的塑性变 形,使金属表层的比容积增大, 体积增大,但其变化受到与之 相连的里层金属的阻碍而在表 面层产生残余压应力,里层产 生残余拉应力。
切削过程中,在切削热的作用 下,加工表面的表面层产生热 膨胀,但金属基体温度较低, 阻碍表层金属的热塑变形而使 表层产生压应力。
(2)切削用量的影响
切削用量中,对加工硬化影
响最大的是切削速度和进给量。随
着进给量增大,切削力也增大,表
面层金属的塑性变形增大,硬化程
度加剧。但当进给量过小(如ƒ为
0.05~0.08 mm)时,可能使切
削厚度小于刀具刃口半径,此时刀
具与工件摩擦力加剧,使加工硬化 现象反而增大。背吃刀量对表层金
图3-32 切削用量对加工硬化的影响
3)砂轮修整质量的影响 砂轮的修整是恢复砂轮的正确形状与磨削能力。。
4)磨削用量的影响 提高砂轮速度vs有利于减小磨削表面粗糙度。砂轮速度vs越大,单位时间内参与切 削的磨粒越多,残余面积减小;同时,会使工件表面金属来不及变形,表面粗糙度降低, 如图3-31(a)所示。 工件速度vw增大,塑性变形增大,同时会使单位时间内磨削工件表面的磨粒数减少, 表面粗糙度增大,如图3-31(b)所示。 横向进给量(背吃刀量ap)对表层金属塑性变形的影响很大。增大背吃刀量,单颗 磨粒的磨屑厚度增大,磨削力增大,工件变形增大,表面粗糙度增大,如图3-31(c)所 示。
(a)
(b)
(c)
图3-31 磨削用量对表面粗糙度的影响
1.3 影响零件表面层物理力学性能的主要因素及其控制措施
1.表面层的加工硬化
1)加工硬化产生的原因 机械加工过程中,工件表面层受切削力作用,产生塑性变形,使晶格扭曲、 畸变,晶粒间产生滑移,晶粒被拉长,形成纤维状组织,使表面层金属的硬度增 加,这种现象称为加工硬化或冷作硬化。
- 1、下载文档前请自行甄别文档内容的完整性,平台不提供额外的编辑、内容补充、找答案等附加服务。
- 2、"仅部分预览"的文档,不可在线预览部分如存在完整性等问题,可反馈申请退款(可完整预览的文档不适用该条件!)。
- 3、如文档侵犯您的权益,请联系客服反馈,我们会尽快为您处理(人工客服工作时间:9:00-18:30)。
2.表面层物理力学性能
由于机械加工中力因素和热因素的综合作用,加工表面层金属的物理力学 性能和化学性能发生一定的变化,主要表现在以下几个方面:
1)表面层加工硬化(冷作硬化)。 2)表面层金相组织变化。 3)表面层产生残余应力。
第一节 机械加工表面质量的含义及其对零件使用性能的影响
1.表面质量对零件耐磨性的影响
图5-11
影响零件表面层物理力学 性能的因素及其改善措施
第三节 影响零件表面层物理力学性能的因素及其改善措施
一、表面层的加工硬化
1.加工硬化的产生及衡量指标
在机械加工过程中,工件表面层金属受切削力的作用,产生强烈的塑性变 形,使金属的晶格扭曲,晶粒被拉长、纤维化甚至破碎而引起的表面层的强度 和硬度增加,塑性降低,物理性能(如密度、导电性、导热性等)也有所变化。 这种现象称为加工硬化,又称为冷作硬化或强化。切削热在一定条件下会使金 属在塑性变形中产生回复现象,使金属失去加工硬化中所得到的物理力学性能, 这种现象称为弱化。
2)当工件表面层温度超过相变温度Ac3,如果这时有充分的切削液,则表面层 将急冷形成二次淬火马氏体,硬度比回火马氏体高,但很薄,只有几微米厚,其 下为硬度较低的回火索氏体和托氏体,导致表面层总的硬度降低,这称为淬火烧
第三节 影响零件表面层物理力学性能的因素及其改善措施
3)当工件表面层温度超过相变温度Ac3,则马氏体转变为奥氏体,如果这时无 切削液,则表面硬度急剧下降,工件表层被退火,这种现象称为退火烧伤。
零件的磨损可分为三个阶段:初期磨损阶段、正常磨损阶段、急剧磨损阶 段。
图5-3
图5-4
第一节 机械加工表面质量的含义及其对零件使用性能的影响
图5-5
第一节 机械加工表面质量的含义及其对零件使用性能的影响
2.表面质量对零件疲劳强度的影响
在交变载荷作用下,零件表面粗糙度、划痕、裂纹等缺陷最易形成应力集 中,并发展成疲劳裂纹,导致零件疲劳破坏。
表面残余应力会引起零件变形,使零件形状和尺寸发生变化,因此对配合 性质也有一定的影响。
第一节 机械加工表面质量的含义及其对零件使用性能的影响
三、表面完整性的概念
表面完整性的内容主要有: (1)表面形貌 (2)表面缺陷 (3)微观组织与表面层的冶金化学特性 1)微观裂纹。 2)微观组织变化,包括晶粒大小和形状、析出物和再结晶等的变化。 3)晶间腐蚀和化学成分的优先溶解。 4)对于氢氧等元素的化学吸收作用所引起的脆性等。 (4)表面层物Βιβλιοθήκη 力学性能 (5)表面层其他工程技术特性
图5-7 图5-8
第二节 影响表面粗糙度的工艺因素及其改善措施
二、磨削加工的表面粗糙度
(1)与磨削砂轮有关的因素 主要是砂轮的粒度、硬度以及对砂轮的修整等。 (2)与工件材质有关的因素 包括材料的硬度、塑性、导热性等。
图5-9
图5-10
第二节 影响表面粗糙度的工艺因素及其改善措施
(3)与加工条件有关的因素 包括磨削用量、冷却条件及工艺系统的精度与抗振性等。
第三节 影响零件表面层物理力学性能的因素及其改善措施
图5-12
图5-13
第三节 影响零件表面层物理力学性能的因素及其改善措施
磨削裂纹和残余应 力有着密切的关系,当 残余应力超过材料的强 度极限,材料表面就会 产生裂纹。影响产生磨 削裂纹的因素很多,主 要是围绕着“热”。
图5-14
第三节 影响零件表面层物理力学性能的因素及其改善措施
表面残余应力对疲劳强度的影响极大。 表面层的加工硬化对疲劳强度也有影响。
3.表面质量对零件耐蚀性的影响
零件的耐蚀性在很大程度上取决于表面粗糙度值。 表面残余应力对零件耐蚀性也有较大影响。
第一节 机械加工表面质量的含义及其对零件使用性能的影响
4.表面质量对配合性质的影响
相配零件间的配合关系是用过盈量或间隙值来表示的。对间隙配合而言, 表面粗糙度值太大,会使配合表面很快磨损而增大配合间隙,改变配合性质, 降低配合精度。对过盈配合而言,装配时配合表面的波峰被挤平,减小了实际 过盈量,降低了连接强度,影响了配合的可靠性。所以对有配合要求的表面都 要求有较小的表面粗糙度值。
机械制造工艺学
WE WILL DO A GREAT JOB ! 主讲人:
第五章 机械加工表面质量
01
机械加工表面质量的含义及其 对零件使用性能的影响
0 影响表面粗糙度的工艺因素及 2 其改善措施
0 影响零件表面层物理力学性能 3 的因素及其改善措施
0 4
工艺系统的振动及其控制措施
机械加工表面质量的含义 及其对零件使用性能的影响
第一节 机械加工表面质量的含义及其对零件使用性能的影响
一、机械加工表面质量的含义
图5-1
第一节 机械加工表面质量的含义及其对零件使用性能的影响
表面质量的含义有两方面内容。
1.表面的几何特征
(1)表面粗糙度 (2)表面波度 (3)纹理方向
图5-2
第一节 机械加工表面质量的含义及其对零件使用性能的影响
2.影响磨削烧伤的因素及其改善措施
三、表面层金相组织变化与磨削烧伤
1.表面层金相组织变化与磨削烧伤原因
磨淬火钢时,在工件表面层上形成的瞬时高温将使表面金属产生以下三种金 相组织变化:
1)如果工件表面层温度未超过相变温度Ac3(一般中碳钢为720℃),但超过马 氏体的转变温度(一般中碳钢为300℃),这时马氏体将转变为硬度较低的回火托氏 体或索氏体,这称为回火烧伤。
影响表面粗糙度的 工艺因素及其改善措施
第二节 影响表面粗糙度的工艺因素及其改善措施
一、切削加工的表面粗糙度
1.几何因素
图5-6
第二节 影响表面粗糙度的工艺因素及其改善措施
2.物理因素
影响切削加工表面粗糙度的物理因素: (1)工件材料的影响 (2)刀具几何参数的影响 (3)切削用量的影响 (4)刀具材料与刃磨质量的影响 (5)冷却润滑液的影响
第三节 影响零件表面层物理力学性能的因素及其改善措施
第三节 影响零件表面层物理力学性能的因素及其改善措施
二、表面层的残余应力
1.表面层残余应力产生的原因
表面层残余应力的产生,主要有以下三种原因: (1)冷态塑性变形引起的残余应 (2)热态塑性变形引起的残余应力 (3)金相组织变化引起的残余应力
2.影响表面层残余应力及磨削裂纹的因素
由于机械加工中力因素和热因素的综合作用,加工表面层金属的物理力学 性能和化学性能发生一定的变化,主要表现在以下几个方面:
1)表面层加工硬化(冷作硬化)。 2)表面层金相组织变化。 3)表面层产生残余应力。
第一节 机械加工表面质量的含义及其对零件使用性能的影响
1.表面质量对零件耐磨性的影响
图5-11
影响零件表面层物理力学 性能的因素及其改善措施
第三节 影响零件表面层物理力学性能的因素及其改善措施
一、表面层的加工硬化
1.加工硬化的产生及衡量指标
在机械加工过程中,工件表面层金属受切削力的作用,产生强烈的塑性变 形,使金属的晶格扭曲,晶粒被拉长、纤维化甚至破碎而引起的表面层的强度 和硬度增加,塑性降低,物理性能(如密度、导电性、导热性等)也有所变化。 这种现象称为加工硬化,又称为冷作硬化或强化。切削热在一定条件下会使金 属在塑性变形中产生回复现象,使金属失去加工硬化中所得到的物理力学性能, 这种现象称为弱化。
2)当工件表面层温度超过相变温度Ac3,如果这时有充分的切削液,则表面层 将急冷形成二次淬火马氏体,硬度比回火马氏体高,但很薄,只有几微米厚,其 下为硬度较低的回火索氏体和托氏体,导致表面层总的硬度降低,这称为淬火烧
第三节 影响零件表面层物理力学性能的因素及其改善措施
3)当工件表面层温度超过相变温度Ac3,则马氏体转变为奥氏体,如果这时无 切削液,则表面硬度急剧下降,工件表层被退火,这种现象称为退火烧伤。
零件的磨损可分为三个阶段:初期磨损阶段、正常磨损阶段、急剧磨损阶 段。
图5-3
图5-4
第一节 机械加工表面质量的含义及其对零件使用性能的影响
图5-5
第一节 机械加工表面质量的含义及其对零件使用性能的影响
2.表面质量对零件疲劳强度的影响
在交变载荷作用下,零件表面粗糙度、划痕、裂纹等缺陷最易形成应力集 中,并发展成疲劳裂纹,导致零件疲劳破坏。
表面残余应力会引起零件变形,使零件形状和尺寸发生变化,因此对配合 性质也有一定的影响。
第一节 机械加工表面质量的含义及其对零件使用性能的影响
三、表面完整性的概念
表面完整性的内容主要有: (1)表面形貌 (2)表面缺陷 (3)微观组织与表面层的冶金化学特性 1)微观裂纹。 2)微观组织变化,包括晶粒大小和形状、析出物和再结晶等的变化。 3)晶间腐蚀和化学成分的优先溶解。 4)对于氢氧等元素的化学吸收作用所引起的脆性等。 (4)表面层物Βιβλιοθήκη 力学性能 (5)表面层其他工程技术特性
图5-7 图5-8
第二节 影响表面粗糙度的工艺因素及其改善措施
二、磨削加工的表面粗糙度
(1)与磨削砂轮有关的因素 主要是砂轮的粒度、硬度以及对砂轮的修整等。 (2)与工件材质有关的因素 包括材料的硬度、塑性、导热性等。
图5-9
图5-10
第二节 影响表面粗糙度的工艺因素及其改善措施
(3)与加工条件有关的因素 包括磨削用量、冷却条件及工艺系统的精度与抗振性等。
第三节 影响零件表面层物理力学性能的因素及其改善措施
图5-12
图5-13
第三节 影响零件表面层物理力学性能的因素及其改善措施
磨削裂纹和残余应 力有着密切的关系,当 残余应力超过材料的强 度极限,材料表面就会 产生裂纹。影响产生磨 削裂纹的因素很多,主 要是围绕着“热”。
图5-14
第三节 影响零件表面层物理力学性能的因素及其改善措施
表面残余应力对疲劳强度的影响极大。 表面层的加工硬化对疲劳强度也有影响。
3.表面质量对零件耐蚀性的影响
零件的耐蚀性在很大程度上取决于表面粗糙度值。 表面残余应力对零件耐蚀性也有较大影响。
第一节 机械加工表面质量的含义及其对零件使用性能的影响
4.表面质量对配合性质的影响
相配零件间的配合关系是用过盈量或间隙值来表示的。对间隙配合而言, 表面粗糙度值太大,会使配合表面很快磨损而增大配合间隙,改变配合性质, 降低配合精度。对过盈配合而言,装配时配合表面的波峰被挤平,减小了实际 过盈量,降低了连接强度,影响了配合的可靠性。所以对有配合要求的表面都 要求有较小的表面粗糙度值。
机械制造工艺学
WE WILL DO A GREAT JOB ! 主讲人:
第五章 机械加工表面质量
01
机械加工表面质量的含义及其 对零件使用性能的影响
0 影响表面粗糙度的工艺因素及 2 其改善措施
0 影响零件表面层物理力学性能 3 的因素及其改善措施
0 4
工艺系统的振动及其控制措施
机械加工表面质量的含义 及其对零件使用性能的影响
第一节 机械加工表面质量的含义及其对零件使用性能的影响
一、机械加工表面质量的含义
图5-1
第一节 机械加工表面质量的含义及其对零件使用性能的影响
表面质量的含义有两方面内容。
1.表面的几何特征
(1)表面粗糙度 (2)表面波度 (3)纹理方向
图5-2
第一节 机械加工表面质量的含义及其对零件使用性能的影响
2.影响磨削烧伤的因素及其改善措施
三、表面层金相组织变化与磨削烧伤
1.表面层金相组织变化与磨削烧伤原因
磨淬火钢时,在工件表面层上形成的瞬时高温将使表面金属产生以下三种金 相组织变化:
1)如果工件表面层温度未超过相变温度Ac3(一般中碳钢为720℃),但超过马 氏体的转变温度(一般中碳钢为300℃),这时马氏体将转变为硬度较低的回火托氏 体或索氏体,这称为回火烧伤。
影响表面粗糙度的 工艺因素及其改善措施
第二节 影响表面粗糙度的工艺因素及其改善措施
一、切削加工的表面粗糙度
1.几何因素
图5-6
第二节 影响表面粗糙度的工艺因素及其改善措施
2.物理因素
影响切削加工表面粗糙度的物理因素: (1)工件材料的影响 (2)刀具几何参数的影响 (3)切削用量的影响 (4)刀具材料与刃磨质量的影响 (5)冷却润滑液的影响
第三节 影响零件表面层物理力学性能的因素及其改善措施
第三节 影响零件表面层物理力学性能的因素及其改善措施
二、表面层的残余应力
1.表面层残余应力产生的原因
表面层残余应力的产生,主要有以下三种原因: (1)冷态塑性变形引起的残余应 (2)热态塑性变形引起的残余应力 (3)金相组织变化引起的残余应力
2.影响表面层残余应力及磨削裂纹的因素