7S知识培训(完美讲解总结)
7S管理培训经典版精编版

(二)整顿
合理安排物品放置的位置和方法,并进行必要的标识。
※ 目的: (1)工作场所一目了然。 (2)减少或消除找寻物品的时间。 (3)创造整齐、整洁的环境。 (4)消除积压物品(如设备的备用品等)。※主要活动: (1) 合理地决定物品的保管方法和布局。 (2) 彻底实施定点、定位存放管理。 (3)将物品、场所的有关内容(名称、数量、状态等) (4)进行标识。※实施要点: (1)三定原则:定物、定位、定量。 (2)标 识:在现场进行适当的标识。
(六)安全
安全就是消除工作中的一切不安全因素,杜绝一切不安全现象。
目的 目的是保障员工的人身安全,保证生产的连续安全正常的进行,同时减少因安全事故而带来的经济损失。主要活动 就是要求在工作中严格执行操作规程,严禁违章作业。 时刻注意安全 , 时刻注重安全。实施要点 清除隐患,排除险情,预防事故的发生。
6、为了维持整洁的工作环境,首先应采取什么措施? 答:为现场清洁制定出一套保养制度。7、当人们看到你的工作场所和设备非常肮脏时,是责怪清洁工人的失职呢?还是对你产生很坏的印象?答:当然会对我印象很坏。 8、“7S”中素养,对你自己来说,首先应着重哪点?答:首先必须了解自己的态度和习惯。
14、物品(包括原材料、辅助材料、成品、半成品、在制品、返修品、废品等)随意摆放有什么害处?答:①容易混料 ②不易识别数量和状态 ③增加无效劳动 ④增加寻找时间 ⑤浪费场地 15、若操作一台不整洁的机器,你会有什么感觉?答:不舒服,影响工作士气。16、如果对机器设备保养不讲究的人,对产品的质量会怎么样?答:对产品的质量也一定不会讲究。 17、机器设备保养不良,对其本身有什么害处?答:影响设备使用精度和使用寿命。18、工具使用后随意摆放有何坏处?答:增加找寻时间,工具易损坏和丢失。
7s管理培训资料解析

12、移动是否简洁
13、架子的后面或上面是否置放东西,
14、架子及保管箱内之物,是否有依 据所标示物品置放
15、危急品有否明确标示,灭火器是 否有定期点检
16、作业员的脚边是否有零乱的零件
17、同一的零件是否散置在几个不同 的地方
18、作业员的四周是否放有必要以上 之物〔工具、零件等〕
19、是否有在工场处处保管着零件
● 要站在新人、其他职场的人的立场来看,使得什 么东西该放在什么地方更为明确
● 要想方法使物品能马上取出访用 ● 另外,使用后要能简洁恢复到原位,没有回复或 误放时能立刻知道
〔三〕清扫的推行要领:
1、建立清扫责任区〔室内、外〕 2、开头一次全公司的大清扫 3、每个地方清洗洁净 4、调查污染源,予以杜绝或隔离,建立清扫基准,作为标准
三
1、 7S是最正确推销员〔Sales〕。被顾客赞扬为洁净洁净的工厂、对这样 的工厂有信念,乐于下订单于口碑相传,会有很多人来工厂参观学习。洁净明朗的 环境,会使大家希望到这样的厂工作 。
2、 7S是节省家〔Saving 〕。降低很多不必要的材料以及工具的铺张削 减"查找"的铺张,节省很多珍贵的时间,能降低工时,提高效率。
十一、干部在7S活动中之责任:
1、 协作公司政策,全力支持与推行7s 2、 参与外界有关7S教育训练,吸取7S技巧 3、 研读7S活动相关书籍,搜集广泛资料 4、 部门内7S之宣导及参与公司7S文宣活动 5、 规划部门内工作区域之整理、定位工作 6、 依公司之7S进度表,全面做好整理、定位、划线标示之作业 7、 帮助部属抑制7S之障碍与困难点 8、 熟读公司[7S运动竞赛实施方法]并向部属解释 9、 必要时,参与公司评分工作 10、7S评分缺点之改善和申述 11、催促所属执行定期之清扫点检 12、上班后之点名与服装仪容清查,下班前之安全巡查与确保
7S知识培训资料
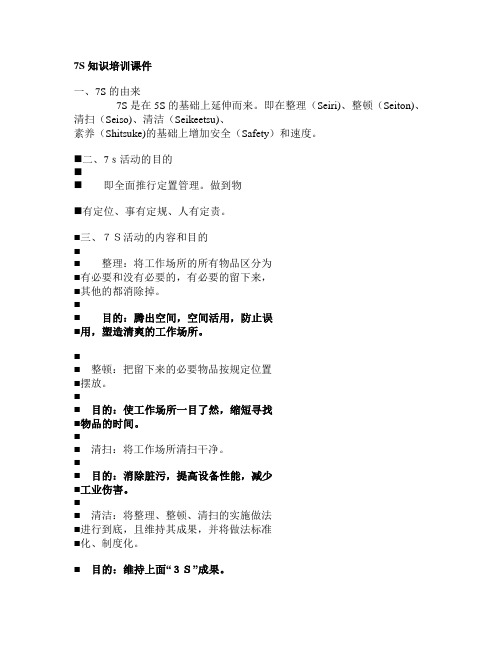
7S知识培训课件一、7S的由来7S是在5S的基础上延伸而来。
即在整理(Seiri)、整顿(Seiton)、清扫(Seiso)、清洁(Seikeetsu)、素养(Shitsuke)的基础上增加安全(Safety)和速度。
⏹二、7s活动的目的⏹⏹即全面推行定置管理。
做到物⏹有定位、事有定规、人有定责。
⏹三、7S活动的内容和目的⏹⏹整理:将工作场所的所有物品区分为⏹有必要和没有必要的,有必要的留下来,⏹其他的都消除掉。
⏹⏹目的:腾出空间,空间活用,防止误⏹用,塑造清爽的工作场所。
⏹⏹整顿:把留下来的必要物品按规定位置⏹摆放。
⏹⏹目的:使工作场所一目了然,缩短寻找⏹物品的时间。
⏹⏹清扫:将工作场所清扫干净。
⏹⏹目的:消除脏污,提高设备性能,减少⏹工业伤害。
⏹⏹清洁:将整理、整顿、清扫的实施做法⏹进行到底,且维持其成果,并将做法标准⏹化、制度化。
⏹目的:维持上面“3S”成果。
⏹素养:每位成员养成良好的习惯,并遵⏹守规则做事,培养积极主动的态度(也称⏹习惯性)⏹目的:培养有好习惯、遵守规则的员⏹工,营造团队精神。
⏹安全:人的行为安全化、物的状态安全⏹化、管理安全化。
⏹⏹目的:保证生产安全、消防安全、环境⏹安全。
⏹速度:减少和杜绝误工、待工、返工、⏹重工等浪费时间,每件事要在第一次就把⏹它做好,而且越做越好,越做越快。
⏹目的:通过以上做法达到提高效率和效⏹益的目的。
⏹⏹四、7S活动的功能:⏹1、提升生产经营单位形象⏹2、保障品质⏹3、提升效率⏹4、推行标准化⏹5、提高现场生产的安全性⏹五、开展7S活动的原则⏹1、自我管理的原则⏹2、勤俭办厂的原则⏹3、持之以恒的原则⏹六、7S活动推行的步骤⏹1、成立推行组织,制定激励措施⏹2、制定实施规划,形成书面制度⏹3、展开宣传造势,进行教育培训⏹4、全面实行7S,实行区域责任制⏹5、制定检查考核制度,并组织检查与考⏹核⏹七、7S活动的要求⏹1、从我做起⏹2、从小事做起⏹3、从现在做起⏹小知识:⏹习惯养成21天法则⏹习惯养成21天法则,是通过21天的重复练习,养成好习惯的一种方法。
7S教育管理知识培训

是
我
2、隶属(lìshǔ)设备〔滑台、任务台、料架 〕;
们
需
3、搬运设备台车、推车、拖车、堆高机;
要
4、正常运用的手工具、模治夹具;
的
东
5、正常的任务椅、板蹬;
西
6、尚有运用价值的消耗用品;
第十三页,共32页。
哪些(nǎxiē)是我们不需求 的东西
1、地板上的纸屑、灰尘、杂物、烟蒂、油污等;
2、地板上不再运用的机器设备、模治夹具等;
• 应树立清扫责任区;
• 找出污染源,予以消弭。
第十九页,共32页。
清洁(qīngjié)
◇ 维持清扫事先的现场及环境的整洁美观, 使工人觉得洁净卫生而发生无比(wúbǐ)的干劲 ;
◇ 现场时辰能坚持美观的形状; ◇ 加以维持前3S的效果、锲而不舍。
第二十页,共32页。
清洁(qīngjié)需留意的 重点
• 彻底落实前3S的各种举措;
• 充沛应用宣传活动与各部门沟通;
• 〝整理(zhěnglǐ)〞、〝整理(zhěnglǐ)〞、〝清扫 〞是举措,〝清洁〞
•
是结果;
• 树立清洁反省、奖惩第二十一制页,共度32页。,使前3S规范化。
素养(sùyǎng)
◇ 经过前4S活动,构成(gòuchéng)良 好的习气;
7S —效率保证员 提高消费效率—— 模具、夹具、工具经过整理,无需寻觅时 间/增强设备保养,机器正常运转,缺陷率降低 /7S规范作业活动(huó dòng),初学者或新人一看
就懂,快 速上岗等
第八页,共32页。
7S —平安管理员 添加平安事故—— 员工了解平安作业的要求和防范知识/整 理整理后,通道不会被占用/物品放置、搬运方 法均思索了平安要素/风险品标识(biāozhì)、警示
车间7s培训工作总结

车间7s培训工作总结
在现代工业生产中,提高生产效率和管理水平是企业发展的关键。
为了达到这
个目标,许多企业都在进行车间7s培训工作,以提高员工的管理水平和工作效率。
在这篇文章中,我们将总结一下车间7s培训工作的效果和经验,以期对其他企业
的类似工作提供一些借鉴和参考。
首先,通过车间7s培训工作,我们的员工对于整个生产流程有了更清晰的认
识和了解。
在培训中,我们重点强调了“整理(Seiri)”和“整顿(Seiton)”这
两个环节,使得员工对于工作场所的整齐和物品摆放有了更为深刻的认识。
这些改变不仅使得工作环境更加整洁,也提高了员工对于工作的效率和质量的要求。
其次,通过培训,我们的员工对于“标准化(Seiketsu)”和“持续改进(Shitsuke)”有了更深入的理解。
在培训中,我们强调了持续改进的重要性,并
且鼓励员工提出自己的改进建议。
这样的做法不仅激发了员工的积极性,也为企业提供了更多的改进方向。
最后,通过车间7s培训工作,我们的员工对于“清扫(Seiso)”和“安全(Anzen)”有了更为严格的要求。
在培训中,我们强调了清洁和安全对于生产工
作的重要性,并且着重培养了员工的安全意识。
这些改变不仅提高了工作环境的整洁度和安全性,也减少了工作中的意外事故。
总的来说,通过车间7s培训工作,我们的员工在管理水平和工作效率上都取
得了显著的提高。
我们相信,通过不断的培训和改进,我们的企业将会在未来取得更加辉煌的成绩。
希望我们的经验能够对其他企业的类似工作提供一些借鉴和参考。
7S知识培训

21
一. 7S基本概念
1.8 推行7S旳旳作用及目旳
推行7S管理旳作用 a) 提供一种舒适旳工作环境; b) 提供一种安全旳作业场合; c) 塑造一种企业旳优良形象,提升员工工作热情
和敬业精神; d) 提升和稳定产品旳质量水平; e) 提升工作效率降低消耗; f) 增长设备旳使用寿命降低维修费用。 G) 降低各種風險事故旳發生,提升相關成本旳使用
價值. 22
一. 7S基本概念
1.8.2 推行7S管理旳目旳
a) 员工作业犯错机会降低,不良品下降,品质上升; b) 提升土气; c) 防止不必要旳等待和查找,提升了工作效率; d) 资源得以合理配置和使用,降低挥霍; e) 整齐旳作业环境给客户留下深刻印象,提升企业整
1
7S知識培訓綱要
--------发明一种舒适、整齐旳工作环境, 是每个企业管理者旳期望 .也是目视管
理之关键.
現場管理 從5S做起 ! 做好7S 同樣從5S做起 !
2
總述
7S基本概念 7S推行技巧 结束语
3
一. 7S基本概念
1.1 我们有下列“症状”吗?
a) 急等要旳东西找不到,心里尤其烦燥 b) 桌面上摆得零零乱乱,以及办公室空间有一种压抑感 c) 没有用旳东西堆了诸多,处理掉又舍不得,不处理又占用空间 d) 工作台面上有一大堆东西,理不清头绪 e) 每次找一件东西,都要打开全部旳抽屉箱柜狂翻 f) 环境脏乱,使得上班人员情绪不佳 g) 制定好旳计划,事务一忙就“延误”了 h) 材料、成品仓库堆放混乱,帐、物不符,堆放长久不用旳物品,占
2.2.4.1 落实整顿工作,根据“整顿”旳要点进行 2.2.4.2 决定放置场合 2.2.4.3 决定放置措施和放置量旳大小. 决定放置區域定位劃線旳措施 . 2.2.4.5決定每個放置區物品之責任管理者。
作业现场安全标准化(7S)基础知识培训

某些部门可以有特殊的规定
人 机 料 法 环
整理的延伸
电子资料 不必要的流程 消极的心态、理念 过长的会议时间
……on)
定义:必需品依规定定位、定方法摆放整 齐,明确标示。 目的:工作井然有序,不浪费时间寻找物 品。
10秒找出 所需工具
物料寻找百态图
所需物品没 有了 急忙订货
效用
维护方法
人或物挨碰触摸机 比较容易标识和 在纸张上过一层胶,防 会少的地方 方便随时标识 止挨碰角落或清洁造成 损害 适用场所区域的标 防潮、防水、易 阳光的照射会使胶质硬 识 于清洁 化脆弱、变色,尽量避 免阳光照射 适用于机械设备的 不容易脱落,时 定期翻新保养 危险警告和一些 刻保持体形作用, “小心有电”等位 易于清洁 置 用于一些化学物品 防火或腐蚀物等 保持清洁 或防火物(如:逃 离火警的方向指示 牌等)
塑胶
油漆
别类
整顿三定
定点
定类 定量
•明确具体的放置位置 •上面?下面?左边?右边?
•明确区分物品的所属种类
•使用颜色进行区分管理 •规定合适的数量
•容器、箱、桶的定量要明确
“7S”的定义与目的
3、清扫 (S eiso)
定义:清除现场内的污物,并防止故障的 发生。 目的:保持现场干净明亮,设备和工具使 用状态良好。
设备点检效率化
大扫除 • •作业要点、步骤、方法明确
防故障 求效益
•正常、异常容易判断
•时间、周期明确(看板等)
现场设备点检文件
设备点检作业指导书 设备点检定位盒路线指引图
点检路线指引
测温点检位置目视化
3.1、在设备上做 标识: 3.1.1颜色:用 红环白芯的图形 表示 3.1.2尺寸:外径 35mm内径10mm 3.2、点检位置编号标 识: 3.2.1点检位置标识用 标签打码机打印 (规格20*60mm), 打印字体用黑体,字 号。 3.2.1深颜色设备用黄 色标识,浅色设备用 绿色标识; 3.2.3粘贴在点检位置 下方
7S管理培训总结

7S管理培训总结通过人力资源部对7s的培训,现在对它有了一定的了解,总结如下:实施“7S”管理,能很好地展现企业文化理念,创建舒适、安全的工作环境,提升企业的整体形象,在规范化管理、员工素养、文明办公和安全节约等方面达到现代企业管理的要求。
最近,公司深入开展“7S”管理活动,组织举行培训、学习、贯彻,让我们对“7S”管理的基本内涵有了更深刻的理解。
“7S”(整理、整顿、清扫、清洁、素养、安全、节约)管理方式,保证公司优雅的办公环境,良好的工作秩序和严明的工作纪律,同时也提高工作效率,减少浪费节约物料成本和时间成本。
“7S”管理方式,正是企业文化的充分体现,是企业文化取得优秀成果和实现企业经营目标的重要手段,是弘扬企业文化“走在行业前面、争创一流企业”,使金州又好又快发展的有力保障。
实施“7S”管理,必须要有全体员工的激情参与,对照标准找差距,分析原因定措施,落实整改见成效,合理配置和使用资源,使生产、办公区域达到整洁、实用、规范的要求,减少浪费,减少物品取放查找时间,提高工作效率。
我认为“7S”管理中的“素养”是整个“7S”活动的核心和精髓,这与公司的管理规定、行为规范密不可分,与人员的素养和严格遵守规章制度的习惯和作风、主动积极的精神密不可分。
没有人员素质的提高,“7S”各项活动就不能开展,就是开展了也坚持不了。
因此,我们应努力提高自身素养,规范自身行为,在平时的工作中,提高文明标准,增强团队意识,养成按规定行事的良好工作习惯,做到“四懂、四会”,达到“7S”管理要求。
节约是对整个“7S”管理过程的补充和指导,我们应积极响应国家建设资源节约型社会的要求,在企业中秉持勤俭节约的原则,以主人翁的心态对待企业的资源,厉行节约,降本增效。
通过对“7S”管理的学习培训,我对“7S”管理有了一个清晰、系统的认识,增强了开展工作的信心,相信通过我们全体员工的努力,一定会达到现场整洁有序、工作高效顺畅的目标,促进企业管理水平上台阶、上水平。
7s管理经典基础培训

强调安全、卫生和环保要求,如在清 扫过程中应注意防止扬尘、避免二次 污染等。
保持清洁和清扫效果的措施
定期检查
培训与教育
建立定期检查制度,对清洁和清扫效果进 行评估和监督,及时发现问题并整改。
加强员工培训和教育,提高员工的清洁意 识和技能水平,确保清洁和清扫工作得到 有效执行。
引入先进设备与技术
保持现场清洁卫生,防止污染和故障。
7s管理核心理念
清洁(Seiketsu)
维持前3s的成果,使现场始终保持最佳状态 。
节约(Saving)
合理利用资源减少浪费,降低成本。
安全(Safety)
确保现场安全,防止事故发生。
素养(Shitsuke)
养成良好习惯,遵守规章制度,提高员工素 质。
7s管理在企业中的应用价值
提高生产效率
优化工作流程,减 少寻找和等待时间 ,提高生产效率。
减少浪费
合理利用资源,降 低库存和成本。
提高企业形象
整洁有序的工作环 境可以提升企业形 象。
降低事故率
强化安全意识,预 防事故的发生。
提升员工素质
培养员工良好的工 作习惯和职业素养 。
02
现场整理与整顿
CHAPTER
现场物品分类与标识
定置管理
根据生产流程和工作需要 ,合理确定物品的放置位 置,确保物品的有序摆放 和快速取用。
可视化标准
制定统一的物品摆放标准 ,如高度、间距、方向等 ,使现场物品摆放整齐划 一,提高视觉效果。
定期检查
定期对现场物品摆放情况 进行检查,及时发现并纠 正不符合标准的问题。
整顿原则及实施方法
整顿原则
遵循“分类明确、标识清晰、 定置管理、方便取用”的原则
7S管理培训资料全

7S管理培训资料全7S管理培训资料全什么是7S7S是指整理(SEIRI)、整顿(SEITON)、清扫(SEISO)、清洁(SEIKETSU)、素养(SHITSUKE)、安全(SAFETY)、节约(SAVING)的管理风格。
7S的作用1、提升企业形象,提高员工素质。
2、营造舒适的工作环境,提高员工工作热情及工作效率。
3、减少浪费,降低成本。
4、保障安全,优化工作环境。
5、提升公司整体执行力。
如何实施7S1、整理整顿整理是区分要与不要的东西,将不要的东西加以处理,在办公场所把必要的物品依规定位置摆放,并放置整齐加以标识,它可以改善工作现场的狭窄,也可以使工作场所更一目了然,使工作更有效率,营造清爽的工作环境。
整顿是指经整理所留下的需要东西整齐摆放,加以标识,它能使工作场所更加有序和整洁,使工作更容易进行。
2、清扫清洁清扫是指将工作场所彻底打扫干净,包括看不见的死角,使整个场所呈现洁净的状态。
清洁是在清扫之后维持整理、整顿、清扫的成果,使工作场所保持整洁和亮丽,使人有一种愉悦的感觉。
3、素养素养是指通过宣传、贯彻企业文化及各项规章制度来提升员工的文明礼貌和道德修养,使员工能够以正确的心态对待工作和生活,以更好的态度服务企业。
4、安全安全是指在工作中要时刻关注安全问题,遵守安全法规,注意安全操作,避免发生安全事故。
节约是指在工作中要合理利用各种资源,避免浪费,降低成本。
同时,在日常生活中也要养成勤俭节约的好习惯。
5、节约节约是指在工作中要合理利用各种资源,避免浪费,降低成本。
同时,在日常生活中也要养成勤俭节约的好习惯。
如何实施7S1、提高认识:领导重视,从上至下推行7S管理,让员工认识到7S的重要性。
2、宣传教育:通过宣传、培训等方式让员工了解7S管理的理念、方法、意义等。
3、制定计划:制定详细的7S推行计划,明确每个阶段的目标和任务。
4、成立推行组织:成立专门的7S推行小组,负责组织、协调、监督7S推行工作。
7S管理培训知识看完这篇就懂了(2024)

服务业应用案例
服务质量提升
通过实施7S管理,服务业企业能 够提升服务质量和效率,提高客
户满意度。
2024/1/30
企业形象塑造
整洁的营业环境和员工形象有助于 塑造企业的专业形象,吸引更多客 户。
成本控制
7S管理有助于企业减少浪费,降低 运营成本。
22
医疗行业应用案例
医院环境改善
通过实施7S管理,医院能 够显著改善医疗环境,提 高患者满意度。
本。
6
02
7S管理具体内容
2024/1/30
7
整理(Seiri)
定义
将工作场所内的物品分类,把要与不要的物品明确地、严格地区分开来。
目的
改善和增加作业面积;现场无杂物,行道通畅,提高工作效率;减少磕碰的机 会,保障安全,提高质量;消除管理上的混放、混料等差错事故;有利于减少 库存量,节约资金;改变作风,提高工作情绪。
7S管理培训知识看完这篇 就懂了
2024/1/30
1
contents
目录
2024/1/30
• 7S管理概述 • 7S管理具体内容 • 7S管理实施步骤与方法 • 7S管理在各行业应用案例 • 7S管理与企业文化融合 • 7S管理挑战与解决方案
2
01
7S管理概述
2024/1/30
3
7S管理定义与起源
目的
养成降低成本习惯,加强作业人员减 少浪费意识教育。
14
03
7S管理实施步骤与方 法
2024/1/30
15
制定实施计划与目标
明确7S管理实施的目 的和意义,以及所要 达到的目标。
对全体员工进行7S管 理知识培训,提高员 工对7S管理的认识和 重视程度。
7s管理内容培训
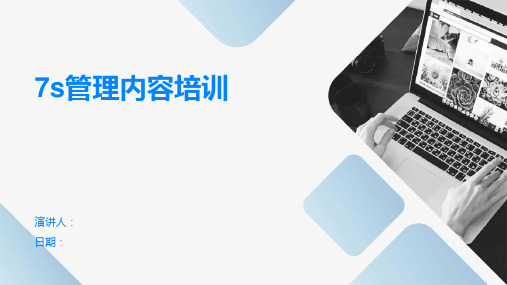
效果评估与持续改进
定期自查
鼓励员工定期对整顿成果进行自查,发现问题及时整改。
引入第三方评估
邀请专业机构或行业专家对整顿效果进行评估,提出改进建议。
建立持续改进机制
将整顿工作纳入企业日常管理体系,持续推动整顿工作的优化和 提升。
第三个S:清扫
04
清扫工作意义及目标设定
清扫工作意义
清除工作场所内的脏污,防止污染的 发生,保持整洁明亮的工作环境,提 高工作效率和员工士气。
第五个S:素养
06
员工素养提升途径探讨
1 2 3
培训与教育
定期开展各类培训课程,提高员工的专业技能和 知识水平,培养员工的学习意识和自我提升能力 。
激励与评价
建立合理的激励机制,对员工的素养提升给予肯 定和鼓励,同时定期对员工的素养进行评价,明 确提升方向。
实践与锻炼
鼓励员工参与实际工作项目,通过实践锻炼提升 员工的素养,培养员工的问题解决能力和创新能 力。
7S管理总结与展望
09
7S管理成果回顾总结
现场整洁度提升
通过实施7S管理,工作场所的 整洁度得到显著提升,各类物 品摆放有序,减少了混乱和浪
费现象。
员工素养提高
7S管理强调员工自律和自主管 理,员工在遵守规章制度、维 护现场秩序方面表现出更高的 素养。
安全隐患减少
通过对现场进行整理和整顿, 及时消除了潜在的安全隐患, 降低了事故发生的概率。
02
它在5S管理的基础上发展而来,增加了安全和节约 两个要素。
03
7S管理现已广泛应用于各种行业和企业中,成为提 高现场管理水平和工作效率的重要工具。
7S管理核心理念
整理(Seiri)
01
7S基础知识培训

◇撤除不需求的东西〔依整理做法案〕
◇整理出放置的中央
◇规那么放置的场所〔依物品运用频率〕
◇标示出放置的场所
A、场所标示2024;/8/26
第十四页, 共35页。
B.品名项目的示
2S------整理(zhěnglǐ)〔SEITON〕
〔1〕落实整理义务: ◇参考〝整理〞的重点来中止 〔2〕决议放置场所: ◇经整理所留下的需求的东西,物品都要定位〔决议放置场所及
2024/8/26
第十八页, 共35页。
3S------清扫(qīngsǎo)〔SEISO〕
二、推行方法 ◆落实整理义务
◆执行例行扫除、清算脏污 ◆调查脏污来源, 彻底根除 ◆废弃物置放区之规划定位 ◆废弃物〔不需求的物品〕之处置(chǔzhì) ◆树立清扫基准, 共同执行 〔1〕落实整理义务 在推进整理整理7S活动时, 依整理〝需求〞与〝不需求 〞基准
普通
平均1—2个月使用一次以上
放在公共场地。如:置放区、橱柜 等
常用
一周内使用数次
放在工作区内随手可以取到的地 方。如机器旁、工具箱内
2024/8/26
第十页, 共35页。
2S------整理(zhěnglǐ)〔SEITON〕
一、基本概念 [别名]: 定位 看板作战 [对象]: 主要是义务场所被恣意糜费的〝时间〞 [原那么]: 分门别类 各就各位 目视管理 [目的]: 延伸前置作业(zuòyè)时间 紧缩库存量 防止误用、误送 塑造目视管理的义务场所 将需求的东西加以定位放置, 并且要坚持在需求的时分能立刻取出的外形。
在义务现场,区分要与不要的东西。
◆保管需求2的024/东8/26西
第八页, 共35页。
1S------整理(zhěnglǐ)〔SEIRI〕
7S培训资料

生产车间现状:
生产过程中经常有一些残余物料、待修品、返修品、报废品 等滞留在现场,既占据了地方又阻碍生产,包括一些已无法 使用的工夹具、量具、机器设备,如果不及时清除,会使现 场变得凌乱。
生产现场摆放不要的物品是一种浪费:
即使宽敞的工作场所,将变得窄小。 棚架橱柜等被杂物占据而减少使用价值。 增加了寻找工具、零件等物品的困难,浪费时间。 物品杂乱无章的摆放,增加盘点的困难,成本核算失准。
7S与品质的关系:
品质与7S有着最密切的关系,7S的水平就是工厂、 职场的品质水平。
正确遵守作业标准就是:使用规定的材料、工具、计 量仪器及正确的作业指导书等。
机器、模具没有定期维护保养、彻底清除杂物,设备 精度无法保证,直接影响产品品质。
工作场所灰尘、杂物多,影响品质。(包装车间包 PVC商标、手套箱等。)
总结
通过对7S简单的认识与学习,使我们了解 了7S整个运作过程,不管是在工作还是在 平时都应该运用7S程序来进行生产或活动, 这样可以养成我们好的习惯,继而提高我 们的品德素质,让我们做一个具有现代化 意识的员工,不断地为个人事业和企业的 发展目标而努力。
车间之间卫生评比,相 互推进。
生产现场7S不合格举例
包装车间窗台
注液车间窗台
清洁工作做好可以收到如下效果:
培养具有好习惯、遵守规则的员工 提高员工文明礼貌水准 营造团体精神 现场时刻保持美观状态 维持前3S的成果
安全:保证在工作场所人员及货物的安全
目的:
消除现场一切安全隐患; 产品摆放、货物装卸安
整理:将工作现场区分要的和不要的,保留需要的东
西,撤除不需要的ቤተ መጻሕፍቲ ባይዱ西
目的: 腾出空间,合理利用; 预防材料用错,送错; 塑造清爽的工作场所。
精选7S基础知识讲解

安全是: 不伤害自已﹔ 不伤害他人﹔ 不被子他人伤害。
物料堵塞通道
电源插座坏
生活水电浪费图片展示
节约 (Saving)﹕.节约是人为的养成的一个良好的理念观.良好的习惯性
3.7 7S的具体内容
长流水
长明电
食堂浪费图片展示
办公资源浪费图片展示
课 程 目 录
1.7S起源和发展
2.7S的作用
3.7S的具体内容
4.7S运动的三个步骤
5.7S实施的五个要点
6.7S改善前后的对比例子
“7S”是由日本的“5S”演变而来的;而“5S”则是起源于日本一种家庭式的管理﹐这种管理当初只是单纯针对事物而提出的“整理”、“整顿”; 20世纪中期日本丰田企业将其引进公司内部的管理运作﹐并随着企业文化的不断需求和提升,后来又增加了“清扫”、“清洁”、“教养”,这样就形成了“5S”。 后续一些企业又把“安全”纳入一起推行﹐就形成了以住的“6S”。 为了节省能资源,从降低公司生产成本考量后又把“节约”纳入了“6S”行列,于是就形成了“7S”.
阶段三、预防的7S
——成为一流的7S工厂
三定三容易三爱三现三不
5. 7S实施的五个要点
3定
3容易
3爱
热爱制造产品的舞台
有让部属大展身手的爱心
热爱自己所制造出来的产品
这可是主动教育的基础哦!!!
3现.3即.3彻底
三现:以现场.现物.现状加以教育
三即:以实时.即刻.即应加以教育
常整理(SEIRI)
定义:清理物品,明确判断要与不要。
目的:保持作业现场没有任何妨碍工作或有碍观瞻的物品。
第二招:制定原则
既要知道为啥留,还要知道为啥去,这就有个原则问题,一般来说,凡是生产过程中必须用到的原料、辅料、工具等是为应该保留。偶尔一用的棉纱、工具或很少时间才用一次的原料可不在生产现场放置。
精选7S管理培训资料PPT47页

7S的发展
日本式企业将5S运动作为管理工作的基础,推行各种品质的管理手法,第二次世界大战后,产品品质得以迅速地提升,奠定了经济大国的地位,而在丰田公司的倡导推行下,5S对于塑造企业的形象、降低成本、准时交货、安全生产、高度的标准化、创造令人心旷神怡的工作场所、现场改善等方面发挥了巨大作用,逐渐被各国的管理界所认识。随着世界经济的发展,5S已经成为工厂管理的一股新潮流。根据企业进一步发展的需要,有的公司在原来5S的基础上又增加了节约(Save)及安全(Safety)这两个要素,形成了“7S";也有的企业加上习惯化(Shiukanka)、服务(Service)及坚持(Shikoku),形成了“10S".但是万变不离其宗,所谓“7S"、“10S"都是从“5S"里衍生出来的。
■节约在产出结果一定的情况下,使人力物力等资源投入成本最少,使之利润最大化。△工艺改善,员工的操作的熟练程度△创新改善,效率的提高△水,电,材料,时间,金钱等的节约。■安全 按机器、仪器等设备的操作要求及SOP进行规范操作,避免产生工伤、消防火灾等事故隐患。 △通常包括有人身安全、消防安全、财产安全… △消防通道的畅通 △安全生产,人人有责
M(management) 管理是一个广义的范畴。狭义可分为对人员、设备、材料、方法等四方面的管理。只有通过科学化、效能化的管理,才能够达到人员、设备、材料、方法的最优化,综合利润最大化,7S是实行科学管理的最基本的要求。一个企业通过推进7S活动,就可以有效地将品质、成本、交期、服务、技术、管理等六大要素都达到最佳的状态,最终能实现企业的竞争方针与目标。所以说7S是现代企业管理的关键和基础。
4.故障为零——7S是交货期的保证
工厂无尘化。无碎屑、屑块、油漆,经常擦拭和进行维护保养,机械使用率会提高。模具、工装夹具管理良好,调试寻找故障的时间会减少,设备才能稳定,它的综合效能就可以大幅度地提高。每日的检查可以防患于未然。
车间7s培训工作总结
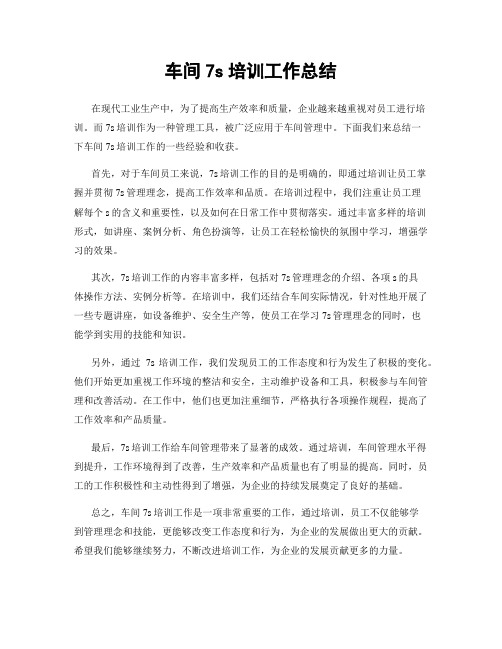
车间7s培训工作总结在现代工业生产中,为了提高生产效率和质量,企业越来越重视对员工进行培训。
而7s培训作为一种管理工具,被广泛应用于车间管理中。
下面我们来总结一下车间7s培训工作的一些经验和收获。
首先,对于车间员工来说,7s培训工作的目的是明确的,即通过培训让员工掌握并贯彻7s管理理念,提高工作效率和品质。
在培训过程中,我们注重让员工理解每个s的含义和重要性,以及如何在日常工作中贯彻落实。
通过丰富多样的培训形式,如讲座、案例分析、角色扮演等,让员工在轻松愉快的氛围中学习,增强学习的效果。
其次,7s培训工作的内容丰富多样,包括对7s管理理念的介绍、各项s的具体操作方法、实例分析等。
在培训中,我们还结合车间实际情况,针对性地开展了一些专题讲座,如设备维护、安全生产等,使员工在学习7s管理理念的同时,也能学到实用的技能和知识。
另外,通过7s培训工作,我们发现员工的工作态度和行为发生了积极的变化。
他们开始更加重视工作环境的整洁和安全,主动维护设备和工具,积极参与车间管理和改善活动。
在工作中,他们也更加注重细节,严格执行各项操作规程,提高了工作效率和产品质量。
最后,7s培训工作给车间管理带来了显著的成效。
通过培训,车间管理水平得到提升,工作环境得到了改善,生产效率和产品质量也有了明显的提高。
同时,员工的工作积极性和主动性得到了增强,为企业的持续发展奠定了良好的基础。
总之,车间7s培训工作是一项非常重要的工作,通过培训,员工不仅能够学到管理理念和技能,更能够改变工作态度和行为,为企业的发展做出更大的贡献。
希望我们能够继续努力,不断改进培训工作,为企业的发展贡献更多的力量。
- 1、下载文档前请自行甄别文档内容的完整性,平台不提供额外的编辑、内容补充、找答案等附加服务。
- 2、"仅部分预览"的文档,不可在线预览部分如存在完整性等问题,可反馈申请退款(可完整预览的文档不适用该条件!)。
- 3、如文档侵犯您的权益,请联系客服反馈,我们会尽快为您处理(人工客服工作时间:9:00-18:30)。
二
整理
1、整理步骤
整理
区分需要与不需要的事、物,再对不需要的事、物加以处理。
现场检查 制定基准 现场的改善
分类
判断“要” 与“不要”
归类
处理
2、整理目的
减少空间
减少物品 减少错误
• 腾出空间,改善和增加作业面积
• 现场无杂物,人行道通畅,提高工作效率
• 防止误用、误送。
心情舒畅
• 塑造清爽的工作场所。
• 不同的人去做,结果是一样的。
※ 以下数字范围1~40,请找出其中缺少的2个数字
※ 如果这样再找一遍能够快多少?
3、整理浪费
寻找浪费 等待浪费 重复浪费 变更浪费 延迟浪费
• 没有标识导致寻找时间的浪费
• 摆放不合理导致停止和等待的浪费。
• 认为没有而多余购买的浪费。
• 现场混乱导致计划变更而产生的浪费。
3、7S作用
故事一: 企业形象就 是竞争力
4、7S实施原则
全员 参与
持续 改善
持之 以恒
规范 高效
自己 动手
5、7S误区
7S管理误区: 把7S管理当做大扫除。 例:
1、认为7S管理太简单,芝麻小事,没有什么意义。 2、工作问题点很多,与7S无关。 3、现在比以前已经好很多了,有必要再搞吗? 4、工作上已经够忙的了,哪有时间再做7S管理。 5、7S管理这么简单,却要劳师动众,有必要吗? 6、就是我想做好,别人呢? 7、做好了有什么好处? 8、到目前为止没有推行7S管理,企业不照样在发展吗? 9、不做7S管理不是照样能生产吗?
• 现场混乱导致交期延迟而产生的浪费。
场地浪费
• 没有定点、定量导致场地的浪费。
4、三区域都要明确,且一目了 然
• 所有物品原则上都要明确其放置方法:竖放、 横放、斜置、吊放、钩放等。
• 标识是使现场一目了然的前提。好的标识是指: 任何人都能十分清楚任何一堆物品的名称、规 格等参数。
5、三定原则
定点
定容 定量
• 明确具体的放置位置。
故事二: 肓人家庭
• 明确使用容器的大小、材质。
• 规定合适的数量。
6、注意事项
一般公司的画线标准:
序号 1 2 3 4 5 项目 主通道 厂区道牙线 大型车间、仓库 辅通道 区域线 说明 主要通道 防撞提示 室内主要通道 辅助通道 固定区域 门活动的范围之内禁止堆放 主要指现场物品摆放定位 厂区内所有消防器材附近禁止堆放 7 消防设施 厂区内所有灭火器材附近禁止堆放 8 9 警示区 货架、办公室物 品定位 存在安全隐患的部位 台面物品定位及柜内物品区域线 线宽 12cm 12cm 12cm 10cm 5cm 2cm 5cm 以消防门 推开基准 5cm 5cm 1.5cm 颜色 黄色 黄黑相间色 黄色 黄色 黄色 黄色 黄色 黄色 黄色 黄黑间隔色 黄色 示范
资金的浪费
移动浪费
人力浪费
管理浪费
• 管理非必需品的场地和人力浪费。
• 库存管理及盘点时间的浪费。
5、整理注意事项
6、整理举例 明确场所的基准: 不用的东西--------------处理掉 不太常用的东西----------放在较远的地方 偶尔使用的东西----------安排专人保管 经常使用的东西----------放在身旁附近 拿来拿去花时间的东西----只留下必要的数量
2、7S内容
整理 整顿 清扫 清洁 安全 节约 素养 区分必需品和非必需品,现场不放置非必需品 物品固定位置并标识,将寻找物品的时间为降为零 清扫到没有赃污的干净状态,注重细微之处 将整理、整顿、清扫进行到底,并制度化
消除隐患,保障员工的人身安全和生产正常
减少浪费、降低成本 遵守规定,积极向上,文明与团队精神
整顿
整顿
是把需要的事、物加以定量和定位。
通过上一步整理后,对生产现场需要的留下的物 品,进行科学合理的布置和摆放,以便最快速地取 得所要之物,在最简捷、有效的规章制度、流程下 完成工作。 生产现场物品的合理摆放使得工作场所一目了然 ,整齐的工作环境有利于提高工作效率,提高产品 质量,保障生产安全。
3、整理作用
削除浪费
减少差错
• 削除资源的浪费,有利于减少库存,节约资金。 • 削除管理上的混放、混料等差错事故,有效地防 止误用、误送。 • 有效地利用空间、可以使现场无杂物、通道顺畅, 增大作业空间面积。 • 对物料、物品进行分类、有序的放置,减少寻找 时间,提高工作效率。
空间利用 减少寻找时间
7S知识培训
目录:
一 二 三 四
基本知识 整理
六
七 八 九 十
素养
安全 节约
整顿
清扫
7S工具
7S制度
五
清洁
一
基本知识
一
基本知识
1、7S定义
7S管理是指生产现场中对人员、机 器、材料、方法等生产要素进行有 效管理的活动。 它提出的目标简单、明确,就是要 为员工创造一个干净、整洁、舒适、 科学合理的工作场所和空间环境。 它的最终目的是提升人的素质,为 企业造就一个高素质的优秀群体。
6、整理举例
保管场所确定:
使用频率 不用 少用 全年一次也未使用 平均2个月~1年用1次 处理方法 废弃 特别处理 分类管理 集中场所
(工具室、仓库)
建议场所 待处理区
普通
常用
1~2个月用1次或以上
1周使用数次
置于车间内
工作区内
各摆放区
如机台旁
1日使用数次
每小时都使用
随手可得
流水线旁
个人工具箱
三
2、整理目的
场所明确 明亮整洁
• 工作场所清楚明了。
• 工作环境明亮、整洁。
减少库存 心情舒畅
• 消除过多的积压物品。
• 工作秩序井然
3、整理作用
提高效率
• 提高工作效率,减少浪费和非必须的作业。
减少寻找
异常曝光
• 将寻找时间减少为零。
• 出现异常情况能马上发现。
现场有序
有执行力
• 创造一目了然的现场,即使非本岗位的人员也能 明白要求和做法。
5、7S误区
走出7S管理误区的要点:
1、理解7S管理的精髓。 2、开始从上至下施加“压力”,以后全面开花。 3、把现在无用的多余物品放在现场是一种浪费。 4、在不影响生产的情况下,原材料、半成品、在制品越少越好。 5、要承认“问题永远存在”。 6、不断改善是提升管理的基础,不要轻视“小打小闹”,由量变到质变。 7、培养员工务实的工作作风,少谈精神,少减口号,注重实际效果。
提高产品质量 降低管理难度
• 减少碰撞,保障生产安全,提高产品质量。
• 有序的工作场所更便于管理,大大降低管理难度。 • 使员工心情舒畅,工作热情高涨。
心情舒畅
4、整理浪费
空间的浪费
• 场地老是不够用,感觉越来越窄 • 零件或产品因过期而不能使用,造成资金的 浪费。 • 场所狭窄,物品不断移动的工时浪费
2、7S内容
整理 整顿 清扫 清洁 安全 节约 素养 区分必需品和非必需品,现场不放置非必需品 物品固定位置并标识,将寻找物品的时间为降为零 清扫到没有赃污的干净状态,注重细微之处 将整理、整顿、清扫进行到底,并制度化
消除隐患,保障员工的人身安全和生产正常
减少浪费、降低成本 遵守规定,积极向上,文明与团队精神