钢 坯 检 验 标 准
产品标识管理规定

产品标识管理规定1 目的为了使产品在生产和交付全部过程中不出现混料、混钢、混序和错发等现象,规定对每批原材料、每个钢种、每个炉缶号有一个特定的标记,必要时加以记录,使其具有可识别性和可追溯性。
2 适用范围本规定适用于从原材料验收,产品加工到产品交付的全过程。
3 产品标识实施规定3。
1 标识形式标识可按生产需要采用钢印、轧辊刻标、标牌、标签、涂色、喷号、书写、记录等形式。
3.2 原材料入库保管要按要求分别堆放,并加以标识和记录.3.3 连铸坯、半成品转序,按钢种炉号搬运转接,加以明显标识和记录.3。
4 合格品入库、交付按钢种、炉号堆放、搬运、交付,必须加以明显标识和记录。
3.5 产品标识规定3。
5。
1炉号编制方法a。
炉号应按七位数编制;b。
首位数是年份号;c。
第二位数是炼钢炉的编号;d。
其它五位数是冶炼钢水各炉次的顺序号(00001~n);e。
此五位顺序号编排至年底,第二年再从“1"开始。
3.5。
2连铸坯标识规定:a.自用连铸坯应按炉号堆放并由炼钢厂负责逐支在一端喷上白色炉号(轧钢一厂半连轧热装热送坯除外),每一炉号要有明显的钢种标识。
轧钢一厂半连轧热装热送坯如果不能及时入炉,要按炉号堆放并由轧钢一厂负责标明炉号。
各炉号钢坯之间要明显的区分开,不能混淆。
b.商品连铸坯应由炼钢厂负责逐支在一端喷上白色炉号、钢号(牌号),按炉号管理,另一端按规定要求由炼钢厂负责进行涂色标识。
涂色标识见下表1。
c.仲裁连铸坯在每支端部进行涂色标识.涂色标识见下表2。
自用的由轧钢厂负责按生产票进行涂色标识,存放在炼钢厂坯料置场的由炼钢厂负责涂色标识。
d.自用连铸坯到达轧钢厂后需要改切的,改切后的坯料按炉号堆放,并标明炉号,各炉号钢坯之间要明显的区分开,不能混淆。
连铸坯涂色标识规定表注:上表中没有规定的新钢种由主管部门负责规定.仲裁连铸坯标识规定表注:上表中没有规定的新钢种由主管部门负责规定。
3。
5。
3半成品标识规定a.半成品钢坯按钢种炉号包装堆放,可采用挂标牌或挂标签标识,标牌或标签上应注明钢钟、炉号、规格、支数、班别、生产日期,必要时需在半成品钢坯表面用铅油书写钢种和炉号.b.半成品钢坯应在一端涂色标识,涂色标识规定见表1。
钢水、铸坯及钢锭的质量检验
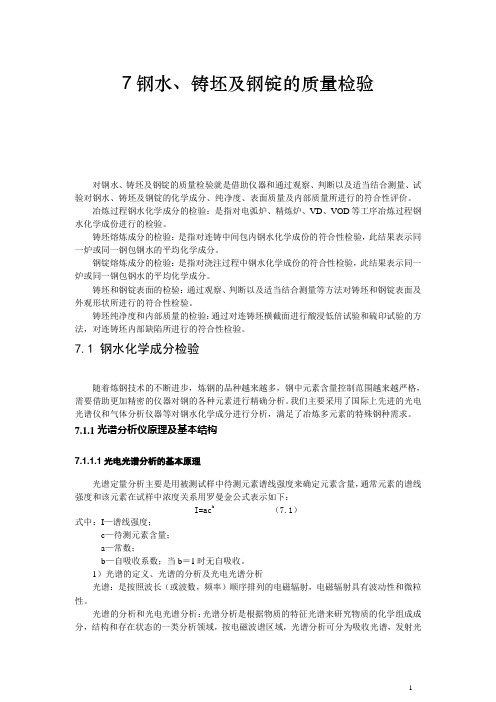
7钢水、铸坯及钢锭的质量检验对钢水、铸坯及钢锭的质量检验就是借助仪器和通过观察、判断以及适当结合测量、试验对钢水、铸坯及钢锭的化学成分、纯净度、表面质量及内部质量所进行的符合性评价。
冶炼过程钢水化学成分的检验:是指对电弧炉、精炼炉、VD、VOD等工序冶炼过程钢水化学成份进行的检验。
铸坯熔炼成分的检验:是指对连铸中间包内钢水化学成份的符合性检验,此结果表示同一炉或同一钢包钢水的平均化学成分。
钢锭熔炼成分的检验:是指对浇注过程中钢水化学成份的符合性检验,此结果表示同一炉或同一钢包钢水的平均化学成分。
铸坯和钢锭表面的检验:通过观察、判断以及适当结合测量等方法对铸坯和钢锭表面及外观形状所进行的符合性检验。
铸坯纯净度和内部质量的检验:通过对连铸坯横截面进行酸浸低倍试验和硫印试验的方法,对连铸坯内部缺陷所进行的符合性检验。
7.1 钢水化学成分检验随着炼钢技术的不断进步,炼钢的品种越来越多,钢中元素含量控制范围越来越严格,需要借助更加精密的仪器对钢的各种元素进行精确分析。
我们主要采用了国际上先进的光电光谱仪和气体分析仪器等对钢水化学成分进行分析,满足了冶炼多元素的特殊钢种需求。
7.1.1 光谱分析仪原理及基本结构7.1.1.1 光电光谱分析的基本原理光谱定量分析主要是用被测试样中待测元素谱线强度来确定元素含量,通常元素的谱线强度和该元素在试样中浓度关系用罗曼金公式表示如下:I=ac b(7.1)式中:I—谱线强度;c—待测元素含量;a—常数;b—自吸收系数;当b=1时无自吸收。
1)光谱的定义、光谱的分析及光电光谱分析光谱:是按照波长(或波数,频率)顺序排列的电磁辐射,电磁辐射具有波动性和微粒性。
光谱的分析和光电光谱分析:光谱分析是根据物质的特征光谱来研究物质的化学组成成分,结构和存在状态的一类分析领域,按电磁波谱区域,光谱分析可分为吸收光谱,发射光谱,光电光谱分析是利用了光电转换组件,将光信号转化成电流信号,然后通过计算机计算出待测元素的含量。
《五种低倍检验方法和枝晶腐蚀》技术介绍
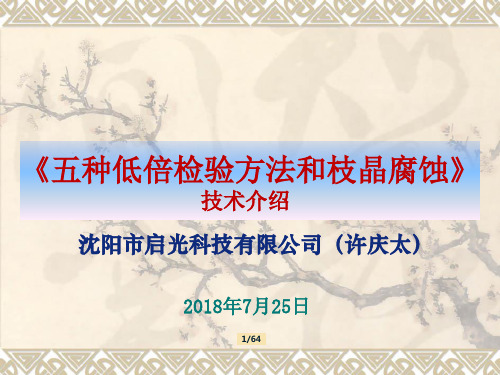
内部缺陷:偏析级别升高 内部缺陷:缩孔 和疏松级别升高
柱状晶发达
1
表面缺陷严重 6 激冷层薄、不均 5 二次晶间距大 内部缺陷:偏 析级别升高
图1-2 铸坯凝固 组织与缺陷的关系
树枝晶搭桥 柱状晶偏斜 内部缺陷:夹 杂物级别升高
2 3
凝固组织
4
等轴晶层厚
内部缺陷:裂纹 和偏析级别降低
中心缺陷级别升高:①中心疏松;②中心偏析;③中心裂纹;④缩孔
图1-3 铸 坯各种缺陷 之间的关系
板坯窄面凹陷或凸起
1
板坯宽面鼓肚 2
形状缺陷
3
方坯菱变(失方)
内部缺陷:三角区裂纹和角裂级别升高
6/64
内部缺陷:对角线裂纹级别升高
二 连铸坯低倍检验方法和对比
1、检验方法的发展(分四步)
①硫印检验→②热酸腐蚀/③电解腐蚀→④冷酸腐蚀→⑤枝晶腐蚀。
①硫印检验
一步
2/64
一
连铸钢坯的质量指标
连铸钢坯质量对钢材质量有直接影响,为了提高钢材质量,必须首先提 高连铸坯的质量,一般判断连铸坯的质量有五个指标。 1、洁净度 洁净度一般是指钢中夹杂物和杂质元素含量的多少,含量越少,钢的洁 净度越高。夹杂物主要是指氧化物和硫化物。杂质元素主要是指S、P和气体 N、H、O含量要少。杂质元素还包括微量元素铜、锡、铅、砷、锑、铋等。 钢材用途不同对洁净度的要求也不同,因此洁净度可定义为:当钢中的 非金属夹杂直接或间接影响钢种生产性能和使用性能时,该钢就不是洁净钢 。而如果钢中夹杂物的数量、尺寸、分布对产品的生产性能和使用性能都没 有影响,那么这种钢就可以认为是洁净钢。 国际会议认为,如果夹杂物直接或间接影响了产品的组织结构或使用性 能要求,那么钢就是不纯净的,如果夹杂物没有引起这些缺陷,那么可以认 为钢是洁净的,不用考虑夹杂物的数量、类型、大小和分布。 2、凝固组织 凝固组织是连铸坯在冷却凝固过程中形成的结晶形貌,即细小等轴晶(激 冷层、坯壳晶)、柱状晶、交叉树枝晶和等轴晶。对柱状晶偏斜角度和二次 晶间距也可以进行测量。
毛坯铸钢件检验规范

11.1 铸造厂和检验部应对铸件进行认真检验,检验验收项目及验收方法按表 5 进行。
表5
序 检验项目
号
试制产品
供方
检验部
正常生产产品
供方
检验部
备注
确认文件/复
确认文件/复
1 化学成分 每个炉批号
每个炉批号
验
验
确认文件/复
确认文件/复
2 机械性能 每个炉批号
每个炉批号
验
验
每个热处理 3 热处理
批
确认文件
CF3
CF8M
A002 A202 E308L-16 E316-16
CF3M
A022 E316L-16
WC6
R307 E5515-B2
WC9
R407 E9015-B3
7.5 合同规定铸件进行 MT、RT 或 UT 的,在焊补热处理后应进行相同的无损检测方法对
ASTM_E45-1997钢中非金属夹杂物评定方法中文[1]
![ASTM_E45-1997钢中非金属夹杂物评定方法中文[1]](https://img.taocdn.com/s3/m/31d090226edb6f1afe001f17.png)
ASTM E45-05 钢中夹杂物含量的评定方法1 范围1.1 本标准的试验方法为测定锻钢中非金属夹杂物含量的方法。
宏观试验法包括微蚀、断口、台阶和磁粉法。
显微试验法通常包括5种检测。
根据夹杂物形状而不是化学特点,显微法将夹杂物划分为不同类型。
这里主要讨论了金相照相技术,它允许形状类似的夹杂物之间略有不同。
这些方法在主要用来评定夹杂物的同时,某些方法也可以评估诸如碳化物、氮化物、碳氮化物、硼化物和金属间化合物的组成。
除了钢以外,其它合金在有些情况下也可以应用这些方法。
根据这些方法在钢中的应用情况,将分别给予介绍。
1.2 本标准适用于人工评定夹杂物含量。
其他ASTM标准介绍了用JK评级图的自动法(ASTM E1122 )和图像分析法(ASTM E1245 )。
1.3 按照钢的类型和性能要求,可以采用宏观法或显微法,也可以将二者结合起来,以得到最佳结果。
1.4 这些试验方法仅仅为推荐方法,对任何级别的钢而言,这些方法都不能作为合格与否的判据。
1.5 本标准未注明与安全相关的事项,如果有的话,也只涉及本标准的使用。
标准使用者应建立适当的安全和健康操作规程,并且在使用标准前应确定其适用性。
2 参考文献2.1 ASTM标准:A 295 高碳耐磨轴承钢技术条件A 485 强淬透性耐磨轴承钢技术条件A 534 耐磨轴承用渗碳钢技术条件A 535 特种性能的滚珠和滚柱轴承钢技术条件A 756 耐磨轴承用不锈钢技术条件A 866 耐磨轴承用中碳钢技术条件D 96 用离心法分离原油中水和沉淀物的试验方法E 3 制备金相试样指南E 7 金相显微镜术语E 381 钢棒,钢坯,钢锭和锻件的宏观试验法E 709 磁粉检测指南E 768 自动测定钢中夹杂物的试样的制备和评定操作规程E 1122 用自动图像分析法获得JK夹杂物等级的操作规程E 1245 用自动图像分析法确定金属中夹杂物或第二相含量的操作规程2.2 SAE标准:J421,磁粉法测定钢的清洁度等级J422,钢中夹杂物评定的推荐操作规程2.3 航空材料技术条件2300,高级飞行性能钢的清洁度:磁粉检测程序2301,飞行性能钢的清洁度:磁粉检测程序2303,飞行性能钢的清洁度:耐腐蚀马氏体钢磁粉检测程序2304,特种飞行性能钢的清洁度:磁粉检测程序2.4 ISO标准:ISO 3763,锻钢——非金属夹杂物的宏观评定法ISO 4967,钢——使用标准图谱的非金属夹杂物显微评定方法2.5 ASTM附加标准:钢中夹杂物评级图Ⅰ-r和评级图Ⅱ低碳钢的4张显微照片3 术语3.1 定义:3.1.1 本标准中用到的定义,见ASTM E7 。
铁道车辆用LZ50钢车轴及钢坯技术条件
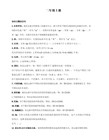
TB/T 2945—1999目次1 范围 (1)2 引用标准 (1)3 生产资格认证 (2)4 LZ50车轴钢代号和牌号 (2)5 技术要求 (2)6 验收方法和验收规则 (5)7 标记及质量证明书 (7)8 包装、保管及运输 (8)9 质量保证 (8)附录A(标准的附录) 力学性能、非金属夹杂物检验试样样坯的尺寸、试样切取部位 (9)附录B(标准的附录) 车轴标记及包装方法 (10)附录C(标准的附录) 超声波探伤 (12)附录D(标准的附录) 磁粉探伤 (16)TB/T 2945—1999前言本标准是在《铁道车辆用50钢车轴技术条件(暂行)》及《铁道车辆用50钢车轴钢坯订货技术条件(暂行)》的基础上制订。
本标准等效采用美国铁路协会AAR M—101—90“热处理及非热处理的碳素钢车轴标准”。
本标准的附录A、B、C、D为标准的附录。
本标准由铁道部标准计量研究所提出并归口。
本标准起草单位:铁道部科学研究院金属及化学研究所。
本标准主要起草人:刘淑华、郭灵彦、潘岳山、林吉忠。
中华人民共和国铁道行业标准TB/T 2945—1999eqv ARR M—101—90 铁道车辆用LZ50钢车轴及钢坯技术条件1 范围本标准规定了铁道车辆用LZ50钢车轴及钢的技术要求、试验方法、检验规则、标记、包装、质量证明书及质量保证等。
本标准适用于铁道车辆用LZ50钢车轴及钢坯的制造、订货和检验。
2 引用标准下列标准所包含的条文,通过在本标准中引用而构成为本标准的条文。
本标准出版时,所示版本均为有效。
所有标准都会被修订,使用本标准的各方应探讨使用下列标准最新版本的可能性。
GB 222—84 钢的化学分析用试样取样法及成品化学成分允许偏差GB 223 钢铁及合金化学分析方法GB 226—91 钢的低倍组织及缺陷酸蚀检验法GB 228—87 金属拉伸试验方法GB 1979—80 结构钢低倍组织缺陷评级图GB 4336—84 碳素钢和低合金钢光电发射光谱分析方法标准GB 10561—89 钢中非金属夹杂物显微评定方法GB 12814—81 铁道车辆用车轴型式与基本尺寸GB/T 19002—92 质量体系—生产和安装的质量保证模式YB/T 5148—93 金属平均晶粒度测定法ZBY 230—84 A型脉冲反射式超声探伤仪通用技术条件ZBY 231—84 超声探伤用探头性能测试方法ZBJ 04001—87 A型脉冲反射式超声探伤系统工作性能测试方法ASTM E 8—91 金属材料拉伸试验标准方法ASTM E 112—95 测定金属平均晶粒度的标准方法AAR M—1003 美国铁路协会(ARR)质量保证体系3 生产资格认证生产LZ50钢车轴及钢坯的工厂,应通过GB/T 19002(ISO 9002)或AAR M —1003体系认证,建立健全车轴生产过程的质量保证体系。
连铸坯、钢板检验规定
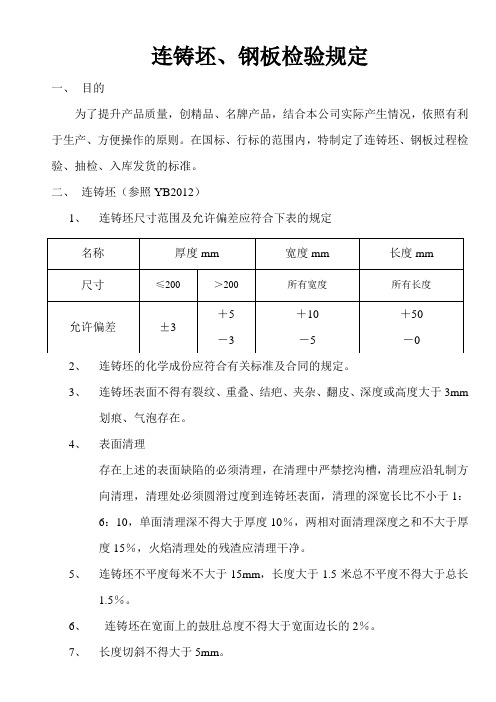
连铸坯、钢板检验规定一、目的为了提升产品质量,创精品、名牌产品,结合本公司实际产生情况,依照有利于生产、方便操作的原则。
在国标、行标的范围内,特制定了连铸坯、钢板过程检验、抽检、入库发货的标准。
二、连铸坯(参照YB2012)1、连铸坯尺寸范围及允许偏差应符合下表的规定2、连铸坯的化学成份应符合有关标准及合同的规定。
3、连铸坯表面不得有裂纹、重叠、结疤、夹杂、翻皮、深度或高度大于3mm划痕、气泡存在。
4、表面清理存在上述的表面缺陷的必须清理,在清理中严禁挖沟槽,清理应沿轧制方向清理,清理处必须圆滑过度到连铸坯表面,清理的深宽长比不小于1:6:10,单面清理深不得大于厚度10%,两相对面清理深度之和不大于厚度15%,火焰清理处的残渣应清理干净。
5、连铸坯不平度每米不大于15mm,长度大于1.5米总不平度不得大于总长1.5%。
6、连铸坯在宽面上的鼓肚总度不得大于宽面边长的2%。
7、长度切斜不得大于5mm。
8、测量位置厚度---以距侧边及端面部位约100-200mm处卡量。
宽度---在长度方向中部测量为准长度---连铸坯长度的最短距离处测量为准三、钢板(参照GB709)1、钢板尺寸范围及允许偏差应符合下表的规定宽度公差钢板的长度允许偏差注:厚度公差见附后表A四切边钢板:对角线按5-15mm验收,单边长度按0-8mm验收。
四毛边钢板:在宽度方向上单边距板边40mm不保性能,小缺陷不于修磨,长度距板头150mm内不保性能及不于修磨表面缺陷。
两头切钢板:单边长度按0-8mm验收,两端头凸凹小于150mm不于切头,大于150mm需切头。
2、表面不得有裂纹、重叠、结疤、夹杂、气泡、拉裂、氧化铁皮压入等缺陷存在。
3、钢板的化学成份应符合有关标准及合同的规定。
4、表面清理存在上述的表面缺陷应进行修磨,在清理中严禁挖沟槽,修磨应光滑过渡到钢板表面,清理深宽长比不小于1:6:10。
5、对于锅炉、压力容器、船体结构用的钢板和合同中规定的特殊用途的钢板,缺陷下面钢板的厚度应不小于相应钢板产品标准中规定的最小允许厚度。
圆管坯检验质量标准
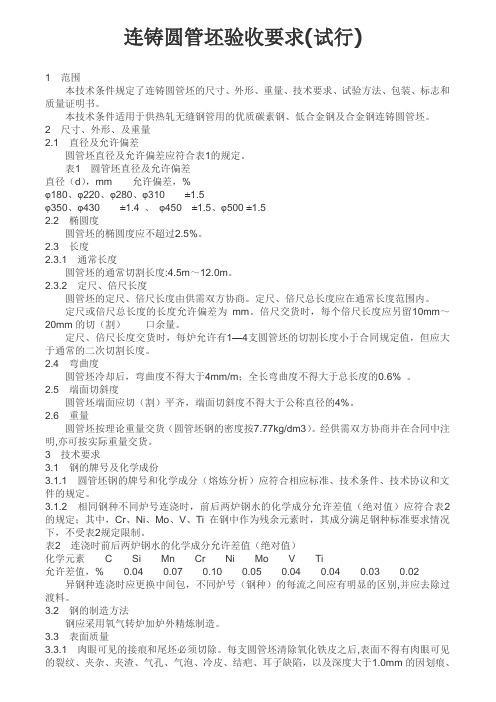
连铸圆管坯验收要求(试行)1 范围本技术条件规定了连铸圆管坯的尺寸、外形、重量、技术要求、试验方法、包装、标志和质量证明书。
本技术条件适用于供热轧无缝钢管用的优质碳素钢、低合金钢及合金钢连铸圆管坯。
2 尺寸、外形、及重量2.1 直径及允许偏差圆管坯直径及允许偏差应符合表1的规定。
表1 圆管坯直径及允许偏差直径(d),mm 允许偏差,%φ180、φ220、φ280、φ310 ±1.5φ350、φ430 ±1.4 、φ450 ±1.5、φ500 ±1.52.2 椭圆度圆管坯的椭圆度应不超过2.5%。
2.3 长度2.3.1 通常长度圆管坯的通常切割长度:4.5m~12.0m。
2.3.2 定尺、倍尺长度圆管坯的定尺、倍尺长度由供需双方协商。
定尺、倍尺总长度应在通常长度范围内。
定尺或倍尺总长度的长度允许偏差为mm。
倍尺交货时,每个倍尺长度应另留10mm~20mm的切(割)口余量。
定尺、倍尺长度交货时,每炉允许有1—4支圆管坯的切割长度小于合同规定值,但应大于通常的二次切割长度。
2.4 弯曲度圆管坯冷却后,弯曲度不得大于4mm/m;全长弯曲度不得大于总长度的0.6% 。
2.5 端面切斜度圆管坯端面应切(割)平齐,端面切斜度不得大于公称直径的4%。
2.6 重量圆管坯按理论重量交货(圆管坯钢的密度按7.77kg/dm3)。
经供需双方协商并在合同中注明,亦可按实际重量交货。
3 技术要求3.1 钢的牌号及化学成份3.1.1 圆管坯钢的牌号和化学成分(熔炼分析)应符合相应标准、技术条件、技术协议和文件的规定。
3.1.2 相同钢种不同炉号连浇时,前后两炉钢水的化学成分允许差值(绝对值)应符合表2的规定;其中,Cr、Ni、Mo、V、Ti在钢中作为残余元素时,其成分满足钢种标准要求情况下,不受表2规定限制。
表2 连浇时前后两炉钢水的化学成分允许差值(绝对值)化学元素 C Si Mn Cr Ni Mo V Ti允许差值,% 0.04 0.07 0.10 0.05 0.04 0.04 0.03 0.02 异钢种连浇时应更换中间包,不同炉号(钢种)的每流之间应有明显的区别,并应去除过渡料。
钢锭_坯_在轧制过程中出现翘皮及断裂等常见缺陷的原因分析和防止途径

甘肃冶金 2001年3月第1期钢锭(坯)在轧制过程中出现翘皮及断裂等常见缺陷的原因分析和防止途径贾 静(兰州钢铁公司 甘肃省 兰州市 730020)摘 要 分析了钢锭(坯)轧制过程中出现翘皮、裂纹、断裂等常见缺陷的原因,并且提出了解决问题的途径。
关键词 分析解决 缺陷 途径1 前言钢锭(坯)在轧制过程中会出现翘皮、裂缝、断裂等多种缺陷而致废。
由于种种原因,90年代初以来,特别是近几年里,钢锭(坯)轧裂和翘皮的数量骤然上升并有居高不下之势。
为此,我们将近几年来发生的钢锭(坯)轧废情况统计分析结果列于表1(数据以每年退换钢锭的数量为依据)。
表1 钢锭(坯)轧裂退换统计表年 份钢 种废品数量致 废 原 因小 时(t)1995 1996 1997 1998 1999Q195—Q235沸钢258钢锭重接19.08t,翘皮、断裂Q235镇静钢— Q195—Q235沸钢118翘皮、断裂150220M nSi连铸坯70夹杂、断裂20M nSi钢47断裂Q195—Q235沸钢44翘皮、断裂150220M nSi连铸坯80夹杂、断裂1502Q235连铸坯40脱方Q235镇静钢100纵裂纹、发纹Q195—Q235沸钢220翘皮、断裂Q235镇静钢110裂纹、断裂Q195—Q235沸钢20断裂、裂口Q235镇静钢240纵裂纹、裂口、断裂2582352643302609收稿日期:2000-12-28表1的统计结果表明: 早期镇静钢锭质量比沸腾钢锭的好,但近两年来质量有下滑趋势。
钢锭(坯)在轧制过程中退废的主要缺陷是翘皮、裂纹和断裂。
平均每年退换钢锭293t ,由此造成的经济损失30余万元。
根据金属学和钢的热塑性变形原理,结合现场生产的实际情况,作者对这些缺陷的成因从炼钢工艺和轧钢工艺两方面进行分析。
2 炼钢工艺对钢锭质量的影响2.1 化学成分的影响对于碳素结构钢来讲,就元素影响而言造成轧制过程中出现裂纹、断裂极为有关的元素有S 、M n 、P 、Cu 。
教材:连铸坯低倍检验标准及在生产中的应用
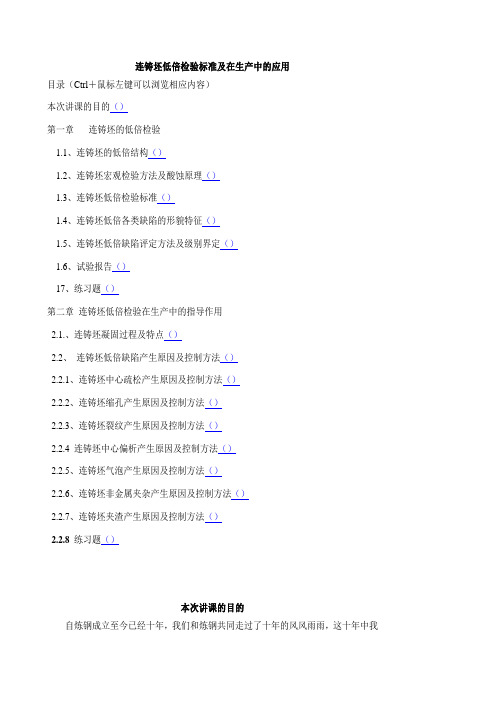
连铸坯低倍检验标准及在生产中的应用目录(Ctrl+鼠标左键可以浏览相应内容)本次讲课的目的()第一章连铸坯的低倍检验1.1、连铸坯的低倍结构()1.2、连铸坯宏观检验方法及酸蚀原理()1.3、连铸坯低倍检验标准()1.4、连铸坯低倍各类缺陷的形貌特征()1.5、连铸坯低倍缺陷评定方法及级别界定()1.6、试验报告()17、练习题()第二章连铸坯低倍检验在生产中的指导作用2.1.、连铸坯凝固过程及特点()2.2、连铸坯低倍缺陷产生原因及控制方法()2.2.1、连铸坯中心疏松产生原因及控制方法()2.2.2、连铸坯缩孔产生原因及控制方法()2.2.3、连铸坯裂纹产生原因及控制方法()2.2.4 连铸坯中心偏析产生原因及控制方法()2.2.5、连铸坯气泡产生原因及控制方法()2.2.6、连铸坯非金属夹杂产生原因及控制方法()2.2.7、连铸坯夹渣产生原因及控制方法()2.2.8练习题()本次讲课的目的自炼钢成立至今已经十年,我们和炼钢共同走过了十年的风风雨雨,这十年中我们炼钢人从零做起发展成为一个年产200多万吨的钢铁企业,而我们一起见证了炼钢在这十年中的发展壮大。
在这十年坎坷中我们走出了一条由向规模要效益到由向质量要效益之路。
现在随着公司改革的不断深入和二次创业号召的提出,公司及厂部对我们的生产经营提出了要求更严、目标更高的要求;特别是现在随国家经济政策的调整及市场不断的发展变化,更要求我们在生产中不能仅仅停留在提高产品的外观质量这一低层次上,而是要以提高产品的内在质量,不断适应市场需求为最终目标。
产品质量的好坏除了生产中严格贯彻标准化操作及不折不扣的执行工艺纪律外,还需要对产品进行外观及内在质量检验,通过质量检验结果进一步对工艺进行改进、优化及完善,而铸坯低倍检验是一个快捷、经济的检验铸坯内在质量的检验方法。
通过本次授课希望大家能够基本掌握以下内容:1、了解铸坯低倍检验方法及检验标准;2、掌握铸坯低倍组织缺陷类型、缺陷产生原因及在生产中控制不良品的方法。
热轧带钢及板坯标准要求及不同厚度精度范围

1、板坯尺寸要求板坯采用100%的连铸坯板坯厚度:210、230mm板坯宽度:950~1650mm板坯长度:长尺:9000~11000mm短尺:4500~5300mm最大坯重:厚度公差:±5mm宽度公差:±10mm长度公差:±30mm镰刀弯:长尺:≤50mm 短尺:≤25mm上下弯:长尺:≤50mm 短尺:≤25mm板坯表面不允许有裂纹、角裂、拉裂和结疤板坯端面不允许有肉眼可见的内裂板坯表面允许有深度不大于3mm的气孔、划痕、凹坑,以及深度不大于2mm的水纹2、产品的质量要求产品的尺寸、外形质量应符合GB709-88的规定①厚度偏差如表1-6所示②宽度偏差带宽≤1000mm+20mm带宽>1000mm +30mm③带钢的镰刀弯每米不大于3mm④塔形高度产品厚度<2.5mm 产品厚度≥2.5mm带宽≤1000mm60 5060带宽>1000mm 80 7080塔形的高宽比≤时适用表面质量要求产品表面质量的保证条件一般参照碳素钢和低合金钢的GB912—89适用于厚度≤4.0mm的产品与GB3274—88适用于厚度>4.0mm的产品的现行国标;1GB/912—89①钢板表面不允许有裂纹、结疤、折迭、气泡和夹杂,钢板不得有分层;②钢板和钢带的表面允许有深度和高度不大于厚度公差之半的折印、麻点、划伤、小拉痕、压痕以及氧化铁皮脱落所造成的表面粗糙等局部缺陷;对表面的薄层氧化铁皮,轻微铁锈和残余涂料、污迹等不影响表面检查的局部缺陷允许存在;③钢板和钢带表面的局部缺陷,允许用修磨方法清除,但清除深度不得大于钢板和钢带厚度公差之半;④钢带允许带缺陷交货,但缺陷部分,不得超过每卷总长度的8%;表1-6产品厚度精度注:带钢两端不考核的总长度<90/公称厚度,且最大不超过20m2GB/3274—88①钢板表面不得有气泡、结疤、拉裂、裂纹、折迭、夹杂和压入氧化铁皮,钢板不得有分层;②钢板表面允许有不妨碍检查表面缺陷的薄层氧化铁皮,铁锈,由于压入氧化铁皮脱落所引起的不显着的粗糙、划痕,轧辊造成的网纹及其它局部缺陷,但凸凹度不得超过钢板厚度公差之半,对低合金钢板和钢带并应保证不超过钢板允许的最小厚度;③钢板表面的缺陷,不允许焊补和堵塞,应用凿子或砂轮清理,清理处应平缓无棱角,清理深度不得超过钢板厚度负偏差范围,对低合金钢板并应保证不超过钢板的允许最小厚度;④成卷钢带允许带缺陷交货,但表面缺陷质量不正常部分,不得超过每卷钢带总长度的10%;⑤切边钢板和钢带的边缘,不得有锯齿形凸凹,但允许有深度不大于2mm,长度不大于25mm 的个别裂纹;不切边钢板和钢带,因轧制而产生的边裂及其它缺陷,其横向深度不得超过钢板和钢带宽度偏差之半,并且不得使钢板小于公称宽度;产品质量中的理化指标应根据不同的钢号、用途分别符合其相应交货标准的规定;①按现行国标生产的钢号与其对应的产品标准表1-7现行国标生产的钢号与其对应的产品标准②按日本标准生产的钢号与其对应的产品标准表1-8日本标准生产的钢号与其对应的产品标准③按德国标准生产的钢号与其对应的产品标准表1-9德国标准生产的钢号与其对应的产品标准④按美国材料实验室标准生产的钢号与其对应的产品标准表1-10美国材料实验室标准生产的钢号与其对应的产品标⑤按英国欧洲标准生产的钢号与其对应的产品标准表1-11英国欧洲标准生产的钢号与其对应的产品标准。
连铸圆坯BQB151-2003

≤0.17
0.10~0.35
0.40~0.80
≤0.035
≤0.035
St45.8
≤0.21
0.10~0.35
0.40~1.20
≤0.035
≤0.035
27MnSi
0.24~0.32
1.10~1.40
1.10~1.40
≤0.030
≤0.030
4.2 冶炼方法
钢由电炉冶炼,并根据不同钢种的技术要求采取相应的炉外精炼工艺。
4.3 交货状态
以连续浇铸的圆坯交货。
4.4 低倍
经供需双方协商,并在合同中注明,可进行低倍组织检验,指标由双方协议规定。
4.5 表面质量
4.5.1 圆坯表面不得存在肉眼可见的裂纹、结疤、砂眼、气孔、针眼等缺陷,但允许存在深度
小于 1.5mm 的机械划痕、印痕等缺陷。
4.5.2 圆坯表面缺陷允许清理。清理处应圆滑无棱角。清理深度不得超过 7mm,其长深比≥8,
圆坯原则上应是平直的,局部弯曲≤4mm/m,总的弯曲不得大于全长 0.4%。 3.3.2 不圆度
圆管坯的不圆度不得大于直径公差的 85%。 3.3.3 端面切斜
圆坯端面应与轴线垂直,切斜不得大于 6mm。 3.4 重量
圆坯按实际重量交货,经供需双方协商并在合同中注明,也可按理论重量交货。
4 技术要求 4.1 牌号及化学成分
0.17~0.37
0.50~0.80
≤0.035
≤0.035
St52.0
≤0.22
≤0.55
≤1.60
≤0.035
≤0.035
St55
0.33~0.41
0.17~0.37
0.50~0.80
拉伸试样国标

金属拉伸试验试样 GB 6397-86金属拉伸试验试样 GB 6397-86本标准规定了各种金属产品常温拉伸试验用试样的一般要求,试样应按有关标准或双方协议的规定选用。
本标准适用于钢铁和有色金属材料的通用拉伸试样。
如无特殊规定,棒、型、板(带)、管:线(丝)、铸件、压铸件和锻压件的试样,均按本标准规定执行。
1 样坯的切取、试样的制备及标志1.1样坯从制品上切取的部位和方向应按GB2975—82《钢材力学及工艺性能试验取样规定》、有关标准或双方协议的规定执行。
1.2切取样坯和机加工试样,均应严防因冷加工或受热而影响金属的力学性能,通常以在切削机床上进行为宜。
因烧割或冷剪法切取样坯时,边缘应留有足够的机加工余量,一般不小于制品的厚度,最低不小于20mm。
但对薄板(带)等则为例外,详见GB2975—82。
机加工试样时,切削、磨削深度及润滑(冷却)剂应适当,最后一道切、磨削深度不宜过大,以免影响性能。
建议保留机加工中心孔,以便必要时重新修整。
1.3从外观检查合格的板材、扁材或带材上切取的矩形样坯,一般应保留其原表面层,不予损伤。
试样毛刺须清除,尖锐棱边应倒圆,圆弧半径不宜过大。
由盘卷上切取的线和薄板、(带)试样,允许校直或校平,但矫正不得对试样的力学性能有显著影响。
对不测定伸长率的试样,则可不经矫正进行试验。
1.4不经机加工单铸试样表面上的夹砂、夹渣、毛刺、飞边等,必须加以清除。
1.5凡不符合本标准所规定的各项要求,表面有显著横向刀、磨痕或机械损伤,有明显淬火变形或裂纹以及肉眼可见冶金缺陷的试样,均不允许用于试验。
1.6试样标志一般应标在头部端面或侧边上(对小截面试样,可挂标志牌),以便试验时易于辨识。
2 试样的符号、名称及单位(见表1)表1符号 名称单位试样平行长度 mm试样原始标距d 0 圆形试样平行长度部分原始直径或圆管试样原始内径 D 0 圆管试样原始外径a 0 矩形、弧形试样或管壁的原始厚度b 0 矩形或弧形试样平行部分原始宽度 F 0 试样平行部分原始横截面积mm2 r带头试样从头部到平行部分过渡圆弧半径mm3 试样形状及尺寸的一般规定3.1拉伸试样分为比例和定标距两种,一般为经机加工试样和不经机加工的全截面试样,其横截面通常为圆形、矩形、异形以及不经机加工的全截面形状。
轧钢厂标准化作业指导书
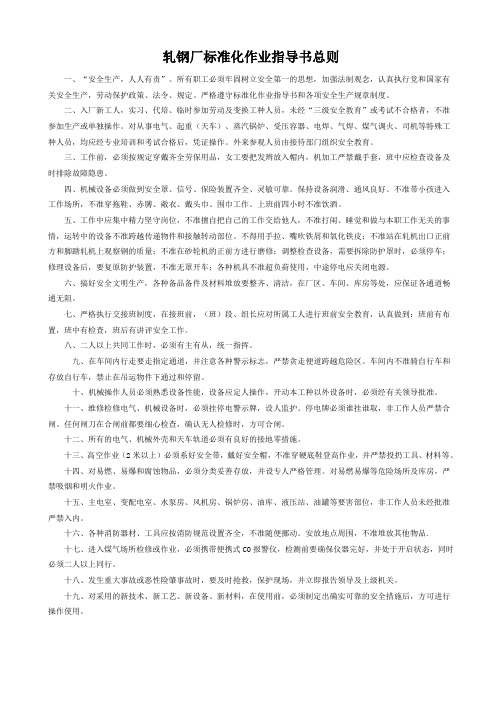
轧钢厂标准化作业指导书总则一、“安全生产,人人有责”。
所有职工必须牢固树立安全第一的思想,加强法制观念,认真执行党和国家有关安全生产,劳动保护政策、法令、规定。
严格遵守标准化作业指导书和各项安全生产规章制度。
二、入厂新工人,实习、代培、临时参加劳动及变换工种人员,未经“三级安全教育”或考试不合格者,不准参加生产或单独操作。
对从事电气、起重(天车)、蒸汽锅炉、受压容器、电焊、气焊、煤气调火、司机等特殊工种人员,均应经专业培训和考试合格后,凭证操作。
外来参观人员由接待部门组织安全教育。
三、工作前,必须按规定穿戴齐全劳保用品,女工要把发辫放入帽内,机加工严禁戴手套,班中应检查设备及时排除故障隐患。
四、机械设备必须做到安全罩、信号、保险装置齐全、灵敏可靠。
保持设备润滑、通风良好。
不准带小孩进入工作场所,不准穿拖鞋、赤膊、敞衣、戴头巾、围巾工作。
上班前四小时不准饮酒。
五、工作中应集中精力坚守岗位,不准擅自把自己的工作交给他人,不准打闹、睡觉和做与本职工作无关的事情,运转中的设备不准跨越传递物件和接触转动部位。
不得用手拉、嘴吹铁屑和氧化铁皮;不准站在轧机出口正前方和脚踏轧机上观察钢的质量;不准在砂轮机的正前方进行磨修;调整检查设备,需要拆除防护罩时,必须停车;修理设备后,要复原防护装置,不准无罩开车;各种机具不准超负荷使用,中途停电应关闭电源。
六、搞好安全文明生产,各种备品备件及材料堆放要整齐、清洁,在厂区、车间、库房等处,应保证各通道畅通无阻。
七、严格执行交接班制度,在接班前,(班)段、组长应对所属工人进行班前安全教育,认真做到:班前有布置,班中有检查,班后有讲评安全工作。
八、二人以上共同工作时,必须有主有从,统一指挥。
九、在车间内行走要走指定通道,并注意各种警示标志,严禁贪走便道跨越危险区。
车间内不准骑自行车和存放自行车,禁止在吊运物件下通过和停留。
十、机械操作人员必须熟悉设备性能,设备应定人操作,开动本工种以外设备时,必须经有关领导批准。
坯布的质量和质检标准【范本模板】

坯布质量标准一.坯布的规格1.幅宽:以英寸表示,公称幅宽的取舍为0。
5吋,表示方法为“〃"。
如63吋,写作63”,其中弹力系列织物,以在机筘幅表示。
2.原料的种类:各种原料采用不同的代号表示,分别为:棉C、涤纶T、锦纶N、粘纤R、氨纶S 、睛纶A、羊毛W、麻、L.3.各种原料加工方法的区分:—1.混纺纱以不同原料的代号加/表示,如涤粘混纺,则以T/R表示,如锦棉混纺,则以N/C表示,如原料为阳离子涤纶与粘纤维混纺,则以阳离子T/R或阳粘T/R表示,必要时表明混纺比,则在原料后面加注,如涤粘以65%和35%混纺,表示为T/R65/35。
—2.精梳棉纱以JC表示,半精梳以BJC表示,紧密纺和米通纱则以文字说明.-3.股线以英支与股数表示,如40S双股线写作40S/2,60S三股线写作60S/3-4.长丝复合产品有机械包覆与空气包覆的区别,如N140D+40D的空气包复丝写作N140D+40D空包丝,如为机包丝,则写作N140D+40D机包丝。
4.经纬支数-1.短纤系列以实际支数在右上角加S表示,如40英支写作40S。
化纤(短纤)系列,则在原料代号前注明:“棉型”、“中长型"、“毛型”字样,阳离子系列,则在原料代号前注明“阳离子”字样。
如涤粘中长,表示为中长T/R。
-2.长丝系列以旦数表示,如100旦长丝,写作100D-3.弹力系列以主体原料加氨纶丝的旦数表示,如精梳棉32S和氨纶40D的包芯纱写作JC32S+40D,其中氨纶丝不再以符号说明。
如包芯以后,实际支数仍为32S,则写作JC32S〔40D〕-4.长丝类原料与氨纶丝的复合产品,以长丝原料的旦数加氨纶丝的旦数表示。
如锦纶140D与氨纶40D 的复合丝写作N140D+40D,其中氨纶不再以符号说明。
—5.所有产品的经纬支数,其排列顺序均为经纱在前,纬纱在后,经纬纱之间以×号区分。
5.经纬密度-1.经纬密度以1英寸中间的根数表示。
YB 2012-2004连续铸钢板坯

连续铸钢板坯1范围本标准规定了非合金钢、低合金钢和合金钢连续铸钢板坯(以下简称连铸板坯)的尺寸、外形、重量及允许偏差、技术要求、试验方法、检验规则、运输、贮存、标志和质量证明书。
本标准适用于按GB/T 13304-1991中第二部分分类的非合金钢、低合金钢和合金钢连续铸钢板坯。
2规范性引用文件下列文件中的条款通过本标准的引用而成为本标准的条款。
凡是注日期的引用文件,其随后所有的修改单(不包括勘误的内容)或修订版均不适用于本标准,然而,鼓励根据本标准达成协议的各方研究是否可使用这些文件的最新版本。
凡是不注日期的引用文件,其最新版本适用于本标准。
GB/T 222 钢的化学分析用试样取样法及成品化学成分允许偏差GB/T 226 钢的低倍组织及缺陷酸蚀试验方法GB/T 247 钢板和钢带检验、包装、标志及质量证明书的一般规定GB/T 4236 钢的硫印检验方法GB/T 13304-1991 钢分类YB/T 4003 连铸钢板坯低倍组织缺陷评级图3定义下列术语和定义适用于本标准。
连铸板坯continuous casting slabs连铸板坯为横截面两相对边长度相等,四内角均为90º,长边长度大于短边2.5倍的铸坯。
4订货内容按本标准订货的合同应包括下列内容:a)标准编号;b)产品名称;c)牌号;d)交货重量(理论重量或实际重量);e)尺寸;f)特殊要求。
5尺寸、外形、重量及允许偏差5.1 尺寸及允许偏差5.1.1连铸板坯的尺寸及其允许偏差应符合表1的规定。
表1 连铸板坯的尺寸及其允许偏差单位为毫米5.1.2根据需方要求,连铸板坯可按定尺或非定尺交货,长度的具体尺寸由供需双方协商,定尺长度允许偏差+80mm。
5.1.3经供需双方协商,连铸板坯尺寸的正负偏差可在公差范围内进行适当调整。
5.2 外形连铸板坯的外形应符合表2的规定。
5.3 重量连铸板坯应按实际重量交货,经供需双方协商,也可按理论重量交货。
钢及钢产品 力学性能试验取样位置及试样制备

ICS 77.040.10H 20中华人民共和国国家标准GB/T 2975-1998 eqv ISO 377:1997钢及钢产品力学性能试验取样位置及试样制备Steel and steel products-Location and preparation of test pieces for mechanical testing代替:GB 2975-82批准部门:国家质量技术监督局1998-10-16 发布 1999-08-01 实施国家质量技术监督局发布前言本标准等效采用国际标准ISO 377:1997《钢及钢产品一力学性能试验的取样位置及试样制备》。
本标准主要技术内容,如应用范围、试样制备、取样位置等均与ISO 377相同。
根据我国具体情况,对于切取样坯时所留加工余量的规定较为详细,对于纵轧钢板横向取样作了明确规定。
本标准在GB 2975—82《钢材力学及工艺性能试验取样规定》的基础上,增加了术语及符号、试料的状态、产品厚度方向取样位置及方形钢管取样规定。
为与国际标准规定一致,对圆钢、六角钢、钢管的一些取样位置作了修改。
本标准自实施之日起代替GB 2975—82《钢材力学及工艺性能试验取样规定》。
本标准的附录A是标准的附录;本标准的附录B是提示的附录。
本标准由中华人民共和国原冶金工业部提出。
本标准由全国钢标准化技术委员会归口。
本标准主要起草单位:原冶金工业部钢铁研究总院、原冶金工业部信息标准研究院。
本标准主要起草人:李久林、梁新邦、高振英、姜清梅。
本标准1982年3月首次发布。
ISO前言ISO(国际标准化组织)是由各国标准化团体(ISO成员团体)组成的世界性的联合会。
制定国际标准的工作通常由ISO的技术委员会完成,各成员团体若对某技术委员会确立的项目感兴趣,均有权参加该委员会的工作。
与ISO保持联系的各国际组织(官方的或非官方的)也可参加有关工作。
在电工技术标准化方面,ISO与国际电工委员会(IEC)保持密切合作关系。
《连铸钢板坯低倍枝晶组织缺陷评级图》
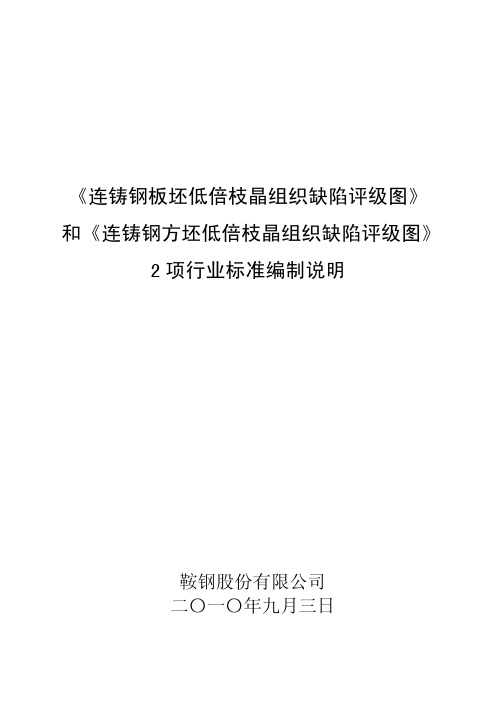
《连铸钢板坯低倍枝晶组织缺陷评级图》 和《连铸钢方坯低倍枝晶组织缺陷评级图》2项行业标准编制说明鞍钢股份有限公司二〇一〇年九月三日《连铸钢板坯低倍枝晶组织缺陷评级图》和《连铸钢方坯低倍枝晶组织缺陷评级图》2项行业标准编制说明1 工作概况1.1 任务来源连铸钢坯低倍枝晶组织缺陷是指连铸钢坯在凝固过程中形成的中心偏析、中心疏松、中心裂纹、中间裂纹、角部裂纹、三角区裂纹、皮下裂纹、皮下气泡、非金属夹杂物、蜂窝气泡、缩孔、夹渣、异金属夹杂、针孔气泡翻皮等缺陷。
而通过对缺陷出现的多少及严重程度进行评定,为连铸钢坯质量改进提供可靠依据。
目前,国内外连铸坯和钢材低倍检验有硫印检验、热酸蚀、冷酸蚀、电解腐蚀和枝晶腐蚀低倍检验五种方法。
前四种方法都有检验方法和缺陷评级国家标准,去年又发布了基于连铸钢坯枝晶腐蚀检验方法的GB/T 24178-2009《连铸钢坯凝固组织低倍评定方法》国家标准,但基于连铸钢坯枝晶腐蚀检验方法的低倍枝晶组织缺陷评级标准尚属空白。
据此,在钢标委下达的2010年第一批冶金产品行业标准项目计划中,提出了由鞍钢股份有限公司负责承担的《连铸钢板坯枝晶组织缺陷评级图》和《连铸钢方坯枝晶组织缺陷评级图》2项行业标准制定任务,计划号分别为“2010-0295T-YB”和“2010-0296T-YB”。
鞍钢经过十多年的实践,在枝晶腐蚀检验方法的运用和标准化方面已日臻成熟,已具备了制定连铸钢坯低倍枝晶组织缺陷评级图行业标准的基本条件。
计划编制的行业标准是与现行同类标准保持同一缺陷评级尺度为基础,在缺陷类别的划分、确保各类缺陷识别和评级的准确性及可操作性等方面,对现行同类标准进行有益完善和补充。
编制好此标准将对整个行业提高连铸钢坯低倍枝晶组织缺陷的检验水平,促进连铸钢坯质量的不断改进和提高起到积极的推动作用。
1.2 标准化对象简要介绍及制定标准的原则1.2.1 标准化对象简要介绍两标准分别规定了连铸钢板坯和方坯低倍枝晶组织缺陷评级的取样和试样腐蚀方法、缺陷分类、评定及检验报告。
锻件质量检验规范

XXXXX【文件编号:XXXX】锻件质量检验规范受控状态:分发编号:版本号:编制:审核:批准:发布时间:X 实施时间:XXX一主题内容与适用范围:本标准规定了对锻造工艺进行全过程质量控制的通用原则和要求。
本标准适用于锻造车间的锻造工艺质量控制。
二引用标准:GB 12361—2016 钢质模锻件通用技术条件GB 12362—2016 钢质模锻件公差及机械加工余量GB 13318 锻造车间安全生产通则GB/T 12363-2005 锻件功能分类JB 4249 锤上钢质自由锻件机械加工余量与公差JB 4385 锤上钢质自由锻件通用技术条件JB/T 6052 钢质自由锻件加热通用技术要求JB/T 6055 锻造车间环境保护导则GB/T7232金属热处理工艺GB/T231-2009金属材料布氏硬度GB/T13320-2007钢制模锻件金相组织评定图及评定方法三.锻件分类本标准质量控制所涉及的锻件分类按GB/T 12363 执行.四环境的控制:锻造厂的工作环境包括厂房地面、天窗、温度、通风、照明、噪声、通道、管道以及坯料、锻件和工夹模具的存放等均应按GB 13318 第3 章和JB/T 6055 第3、4 章的要求和国家的有关法规、法律制订本企业的具体实施要求。
五设备、仪表与工装的控制:5。
1 设备、仪表5。
1。
1 各类设备必须完好,并有操作规程和维修、检定制度。
5. 1. 2 各类在用主要设备必须挂有完好设备标牌,并有检验有效期及下次检定日期。
不合格设备及超过检定合格有效期的设备必须挂“停用”标牌。
5. 1. 3 设备的控制系统及检测显示仪表应定期检查,确保仪表和其精度的显示数值准确。
5。
1. 4 加热设备的温度显示及测点布置应正确反应加热区炉温及炉温均匀性。
5. 1。
5 所用设备都必须建立档案,其具体内容包括:a。
设备使用说明书b。
台时记录c.故障记录d.修理记录e。
历年检定报告及检定合格证。
5. 2 模具及其他工装5. 2。
- 1、下载文档前请自行甄别文档内容的完整性,平台不提供额外的编辑、内容补充、找答案等附加服务。
- 2、"仅部分预览"的文档,不可在线预览部分如存在完整性等问题,可反馈申请退款(可完整预览的文档不适用该条件!)。
- 3、如文档侵犯您的权益,请联系客服反馈,我们会尽快为您处理(人工客服工作时间:9:00-18:30)。
钢坯检验标准
连铸坯普碳钢化学成分执行《碳素结构钢》GB700-88标准;外观质量检验执行《连续铸钢方坯和矩形坯》YB2011-83标准。
外观检验主要参数指标
如下:
1、尺寸及其允许偏差
1.1、连铸方坯、矩形坯的尺寸及其允偏差应符合表1的规定。
表1 单位:mm
1.2、经供需双方协议,连铸坯尺寸的正负偏差可在公差范围内进行适当调
整。
1.3、根据需方要求,连铸坯长度可按尺寸和非定尺交货,定尺长度允许偏差+80mm。
表二单位:mm
2、外形标准
2.1、连铸坯横截面的对角线长度之差应符合表2的规定。
2.2、连铸坯的弯曲度每米不得大于20mm,总弯曲度不得大于总长度的2%。
2.3、连铸坯允许有鼓肚,但高度不得超过连铸坯边长的允许正偏差。
2.4、连铸坯端部的切斜不得大于20mm.
2.5、连铸坯端部因剪切变形造成的宽展不得大于边长的10%。
2.6、连铸坯不得有明显扭转。
3、表面质量
3.1 、连铸坯表面不得有肉眼可见的裂纹、重叠、翻皮、结疤、夹杂、深度或高度大于3mm的划痕、压痕、擦伤、气孔、皱纹、冷溅、耳子、凸块、凹坑和深度大于2mm的发纹。
连铸坯横截面不得有缩孔、皮下气泡。
3.2、连铸坯表面如存在上述缸陷,必须清除。
应沿纵向清除,清除处应圆滑无棱角。
清除宽度不得小于深度的6倍,长度不得小于深度的8倍。
表面清除的深度,单面不得大于连铸坯厚度的10%,两相对面清除深度之和不得大于厚度的15%,清除深度自实际尺寸算起。
4、化学成份
连铸坯化学成分应为熔炼分析成分。
如从连铸坯上取样分析化学成份时,允许有相应标准规定的成份偏差。
5、组批
连铸坯按批验收,每批由同一牌号、同一截面尺寸组成。
2004年8月23日
轧一联成计质处
碳素结构钢化学成份
GB700-88。