现场改善方案及几点建议
现场品质效率管理改善建议

现场品质效率管理改善建议提案人:杨建国 [2015/8/19]生产现场问题点及改善方案:1、在生产现场,首件,良品与不良品以及呆滞现场区域物料一般无任何标识,基本上都是靠熟悉产品的人为区分,这样很容易出现判断失误,产品标识用于区分不同客户,不同机种,不同批次,数量,产品状况等,有效的标识可防止产品在使用过程中发生混淆,实现产品的可追溯性(1133的横梁批量性不良,查不到什么时候什么人生产的;1133的客户端退回不良方孔条再次出现在生产现场)。
改善方案:【1、在物料上面标示首件标签,良品标签,不良品标签,转序标签,产品随线流转卡,待处理标签,标签上必须有产品名称,产品数量,生产时间,确认人;2、待处理产品,待加工产品,待转序产品,不良品,报废品都要设置固定的区域,每个放置物料的区域都有标示牌标示出产品的状态;3、不良品必须要标明产品的不良原因,便于生产返修和品质判断,免得不良品有不良漏返修直接转出工序或者发到客户】2、在生产加工过程中已经加工好的产品和待加工的产品堆放在一起,容易出现漏加工,因此产生的不良品影响了后工序的加工以及客户端的投诉(1214的漏冲桥,1133方孔条整条漏压铆,0480的条码用在1265上面,1214的小支架有没折弯的直板)。
改善方案:【1、生产应该在生产前先清理工作台面,生产下一批次产品时不允许有上一批次的产品和配件以及标签还滞留在加工现场,条码标签已由品质专人管控;2、为了有效的防止产品在生产过程中出现部分产品漏加工,当工段没有加工好的产品应该放在待加工的产品区域,绝对不能和已加工好的产品混放在一起,特别是其他人员(包括领导和检验人员)接触产品和自己休息回来时,生产员工要检查已经加工过的产品有无漏加工的;3、当工段已经加工好的产品贴好随线流转卡(标明生产日期,当班生产组长,检验员,操作员),做到可追溯性】3、生产现场存在呆滞无用物料未及时处理(如升版前的物料,客户退回来的1133方孔条)改善方案:【当一款产品生产完,现场多余之物料及不良品及时合理的处理并做好标识,做到当日事当日理,现场不存在呆滞物料】4、压铆在沉孔的时候没有吹铁屑的装置,产品在加工过程中有划伤和压痕;冲压也没有进行吹废料(1722门楣一个三角形的深压伤)改善方案:【1、压铆在进行钳工操作在没有配备吹风装置的情况下必须用气枪吹去铁屑,保持台面的清洁;2、冲压必须不定时的进行产品检验和模具表面的清理】5、前处理之后送上来的产品没有在24小时内进行喷涂操作,甚至还有几个月以前的产品,起不到前处理产品应有的效果(1257的配件)改善方案:【前处理处理过的产品应该在24小时之内进行喷涂,48小时之内的产品必须再次检测之后才能上线,48小时之外的产品必须返前处理进行再处理】6、对于已经喷涂做过表面处理的喷涂件产品摆放凌乱,产品与产品之间未有效的做好保护措施,只是用拉伸膜围住栈板是无法防止产品的碰伤刮伤等外观不良,喷涂件产品对如压铆螺柱螺母保护没到位,每次生产都有回牙后才能组装的情况,还有保护胶纸和保护胶塞在喷涂前吹灰时有部分直接掉落,没有起到保护的作用,既大大影响生产效率又影响品质同样也浪费成本(1722的装配漏回牙)改善方案:【1、喷涂前一定要对压铆螺母,螺柱,螺纹孔进行喷涂保护,不能漏保护,也不能保护不到位;2、在喷涂前贴保护和装胶塞的人员必须保证保护的质量,吹灰的人员在发现保护掉落时必须挑选出来进行重新保护;3、喷涂好的产品须放在有纸板垫在栈板上面,产品与产品每层之间必须用隔板隔开,然后用打包膜缠上】7、组装车间生产配件产品有时摆放在地面作业,电镀件拆包后直接堆放在一块,现场有多个喝完没喝完的饮料瓶,造成车间摆放凌乱对如产品外观也存在极大的影响,同时也影响车间5S及生产效率(1257的配件装配,电镀件直接成堆放置)。
生产现场改善方案

生产现场改善方案生产现场改善方案简介:该方案适用于通过合理的计划制定,实现不同人员之间的统一行动方针,明确执行目标、内容、方式和进度,从而使整体计划目标统一、行动协调、过程有条不紊。
本文档可直接下载或修改,使用时请详细阅读内容。
本人很高兴加入XXX,也感谢XXX及涂总的信任。
本人将尽心尽职,提高公司品质和效率,降低成本、节约资源,以最少的投入创造最高的利润。
同时,也希望领导的支持和帮助。
以下是我对公司现状分析及改善方案。
现状分析1、生产方面:1)没有生产流程图、标准工时、作业指导书、产能评估报告等,不清楚人员排布是否合适。
2)生产线缺乏辅助治具(工具、夹具)。
3)现场7S管控不足。
4)无生产看板,无法反映该线在做什么,现场管理无法把握现状。
5)人员纪律松散,工衣着装颜色统一,不利于目视管理,难以分辨管理、员工、QC和助拉。
6)现场规划不合理,生产制程不顺畅。
7)产品制程划分不合理,组装部分和焊接PCB板、焊线或焊零部件混淆。
8)生产线缺乏物料员,物料管控失控。
9)缺乏异常问题的检导,如生产品质例会、新产品导入会议。
10)现场管理的专业技能需要进一步提升,执行力差。
2、品质方面1)来料检验控制没有标准及依据(电子料、五金、线材、塑胶、包材)。
2)缺乏品质过程控制相关规定。
3)出货检验没有标准性。
4.工程方面存在以下问题:缺乏成品检验基准书、外观检验标准、部件检验基准书以及制程生产的流程图、SOP、BOM(完整性)和工夹具。
5.来料检验项目没有记录档案,无法追溯和控制。
3.生产管理方面存在以下问题:1.新产品导入(PP\MP\试产)没有召开产前会议。
2.产品没有标准工时,导致计划安排有一定难度和不确定性。
3.欠料问题特别严重。
4.公司缺乏体系运作的模式。
针对以上问题,我提出以下改善方案:一、培训教育方面:1.组织各部门管理人员进行专业知识、理论知识和技能方面的培训和考核,以提升自我管理能力。
同时,制定培训计划大纲和试卷,对管理能力进行评估。
现场改善工作规划怎么写
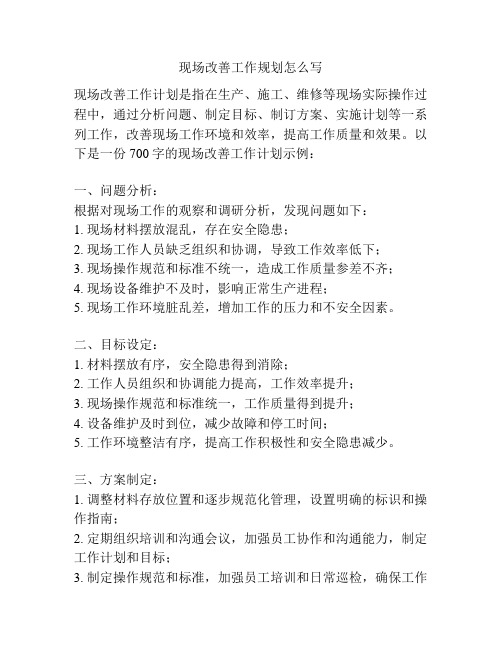
现场改善工作规划怎么写现场改善工作计划是指在生产、施工、维修等现场实际操作过程中,通过分析问题、制定目标、制订方案、实施计划等一系列工作,改善现场工作环境和效率,提高工作质量和效果。
以下是一份700字的现场改善工作计划示例:一、问题分析:根据对现场工作的观察和调研分析,发现问题如下:1. 现场材料摆放混乱,存在安全隐患;2. 现场工作人员缺乏组织和协调,导致工作效率低下;3. 现场操作规范和标准不统一,造成工作质量参差不齐;4. 现场设备维护不及时,影响正常生产进程;5. 现场工作环境脏乱差,增加工作的压力和不安全因素。
二、目标设定:1. 材料摆放有序,安全隐患得到消除;2. 工作人员组织和协调能力提高,工作效率提升;3. 现场操作规范和标准统一,工作质量得到提升;4. 设备维护及时到位,减少故障和停工时间;5. 工作环境整洁有序,提高工作积极性和安全隐患减少。
三、方案制定:1. 调整材料存放位置和逐步规范化管理,设置明确的标识和操作指南;2. 定期组织培训和沟通会议,加强员工协作和沟通能力,制定工作计划和目标;3. 制定操作规范和标准,加强员工培训和日常巡检,确保工作质量;4. 建立设备维护计划和保养记录,保证设备正常运行和故障处理;5. 加强现场卫生管理,定期清洁检查,营造良好的工作环境。
四、实施计划:1. 第一周:调研现场问题,制定改善方案,安排培训计划;2. 第二周:开始调整材料存放位置,逐步规范管理;3. 第三周:开展员工培训和沟通会议,制定目标和工作计划;4. 第四周:制定操作规范和标准,加强员工培训和日常巡检;5. 第五周:建立设备维护计划和保养记录,进行设备维护;6. 第六周:加强现场卫生管理,进行清洁检查。
五、监控评估:1. 每周组织现场巡查和评估,监控改善效果;2. 定期召开改善工作会议,总结经验和探讨问题;3. 根据实际情况,及时调整和优化工作计划和方案。
六、预期效果:通过以上的改善措施,预期实现以下效果:1. 提高现场工作效率,减少生产周期和成本;2. 提高工作质量和标准化水平,降低不良率;3. 减少设备故障和停工时间,提高生产效率;4. 提升员工工作积极性和工作满意度;5. 创造良好的工作环境,保障员工安全和健康。
品质现场改善方案
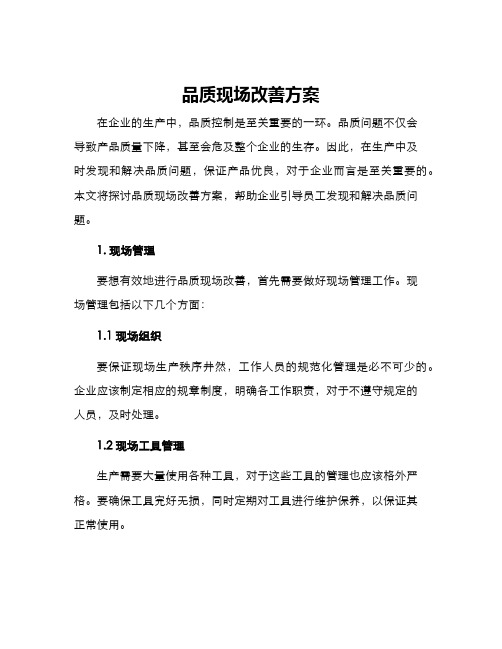
品质现场改善方案在企业的生产中,品质控制是至关重要的一环。
品质问题不仅会导致产品质量下降,甚至会危及整个企业的生存。
因此,在生产中及时发现和解决品质问题,保证产品优良,对于企业而言是至关重要的。
本文将探讨品质现场改善方案,帮助企业引导员工发现和解决品质问题。
1. 现场管理要想有效地进行品质现场改善,首先需要做好现场管理工作。
现场管理包括以下几个方面:1.1 现场组织要保证现场生产秩序井然,工作人员的规范化管理是必不可少的。
企业应该制定相应的规章制度,明确各工作职责,对于不遵守规定的人员,及时处理。
1.2 现场工具管理生产需要大量使用各种工具,对于这些工具的管理也应该格外严格。
要确保工具完好无损,同时定期对工具进行维护保养,以保证其正常使用。
2. 品质分析企业应该及时分析各个品质环节的数据,以发现品质问题。
品质分析可以通过以下几个方面实现:2.1 数据分析要进行数据分析,企业需要收集和分析大量的数据。
通过分析这些数据,并确认品质差异的来源,以对品质现场改善提供有力的依据。
2.2 加工工艺分析在生产过程中,企业应该针对加工工艺进行逐一分析,找出可能影响品质的工艺环节,并采取措施予以改进。
3. 质量培训在品质现场改善的目标中,质量培训是至关重要的一环。
员工能够掌握和遵守标准操作程序和规定,才能最大程度地确保产品的质量。
4. 品质反馈企业应该建立完善的品质反馈制度,及时反映前线工作者发现的品质问题,为上级领导层制定改善措施提供帮助。
5. 品牌建设品牌是企业的软实力,是市场竞争的重要因素。
企业的品牌形象不仅能够吸引顾客,也能提高企业的市场地位。
因此,企业在进行品质现场改善时,应该重点侧重于品牌建设。
6. 总结品质现场改善是企业经营中非常重要的一个环节,企业应该进一步加强品质现场管理、进行品质分析、进行质量培训等方面的工作,并建立健全的品质反馈制度和品牌建设。
只有这样,企业才能真正提升产品的品质水平,赢得市场和客户的信任。
现场改善方案及几点建议

持续推进5S管理及现场改善活动
总结词
提高现场管理水平,优化生产环境。
详细描述
制定5S推行计划,明确责任人和实施步骤 。定期组织5S检查和评估,及时发现和整 改问题。同时,鼓励员工参与现场改善活动 ,提出改进建议,持续优化生产环境。
建立完善的质量管理体系并持续改进
总结词
详细描述
提升产品质量,提高客户满意度。
02
问题分析与定位
对反馈的问题进行深入分析,找 出问题的根本原因,为制定改进 措施提供依据。
03
改进措施实施与跟 踪
制定具体的改进措施并加以实施 ,同时对实施效果进行跟踪和评 估,确保问题得到有效解决。
质量成本的核算与控制
核算质量成本
将质量成本进行分类和核算,包括预防成本、鉴定成本、内部故障 成本和外部故障成本等,以全面了解产品质量对企业运营的影响。
配送计划制定
根据订单信息和库存状况 ,制定合理的配送计划, 确保订单及时送达的同时 避免库存积压。
配送技术升级
采用先进的配送技术,如 智能配送系统、无人机配 送等,提高配送效率和准 确性。
05
CATALOGUE
建议与展望
加强员工培训与团队建设
总结词
提升员工技能和素质,增强团队协作能力。
详细描述
制定定期的员工培训计划,包括技能培训、安全培训、质量意识培训等,提高员 工的专业技能和安全意识。同时,加强团队建设,提高员工的归属感和团队协作 能力。
供应商分级管理
根据供应商的综合能力,将供应商进行分级管理,对关键 供应商进行重点监控和合作,以实现供应链的稳定和高效 。
供应商绩效评估
定期对供应商的绩效进行评估,包括交货准时率、质量合 格率、服务响应速度等指标,以便及时调整供应商选择策 略。
现场管理的意义及改善建议方案-管理资料

现场管理的意义及改善建议方案-管理资料第一部分:“现场管理”无处不在所有工作的展开都离不开具体的时间和空间,由此便构成了一个又一个的具体现场,。
同时,所有的工作都离不开具体的成果和价值,当然,这就需要在特定的现场中完成特定的管理。
之所以要强调现场管理,就是因为它在企业的管理中发挥着至关重要的作用,因为如果不在现场管理的背景下去谈论管理,将导致人们陷入从理论到理论、从概念到概念的破坏性的沟通中,当我们脱离了任何一个具体的现场而去谈论问题的时候,都不可能将问题谈论清楚。
因此可以这样讲,不论人们在管理一词之前加上了怎么样的定语,如人事管理、成本管理、品质管理、交货期管理等,但只要这些管理没有融入到现场管理之中,都将失去其存在的价值。
现场管理可使企业全面改善经营环境,提高整体经营素质。
它讲究在低成本高效率的前提下,开展企业全方位的环境整洁,包括企业自然环境、作业环境尤其是人文环境的整洁,目的是使自然环境美观化,作业环境合理化,内外经营环境全面优化,从而起到鼓舞士气,增强团队协调作战能力的作用,使企业由营销产品走向营销企业直至进行营销企业文化的境界,使各方面达到最优境界。
换言之,也就是企业通过各环节的现场管理最终而达到一个整洁、秩序、美观、效率、成本、充满士气的整体工作氛围。
一、为什么要强调现场管理坦率地讲,在100多年的发展过程中,管理学已经演变成为一个非常复杂的系统,单从一系列的词汇中,我们就可以看到这个体系的复杂性——战略管理、人力资源管理、采购管理、供应链管理、质量管理、危机管理、财务管理……在这样的背景下,如果不强调现场管理,就会使太多的管理陷入职能化,在职能化管理的名义下,将一个活生生的、有机的企业经营管理系统,拆分成一个一个僵硬的、固化的“职能”,从而使发现问题、解决问题的过程受到各种各样的干扰。
不论是什么样的管理,如果不能够解决问题,如果不能够为其他环节、其他领域中的管理提供价值,那么这样的管理是不被企业需要的,也是没有价值的。
现场改善计划和行动计划

现场改善计划和行动计划
目的:
通过分析工厂现场的风险点和不足,制定改善计划和具体行动,以提高工厂整体安全管理水平。
一、现场识别和评估
1. 通过工厂现场视察,识别存在的风险点,包括:
- 機器操作区域无安全障壁
- 操作人员无个人防护装备
- 操作程序缺少详细說明
2. 使用风险评估表对每個风险点进行风险等級分析
二、改善目标和措施
根据风险分析结果,制定以下改善目标和措施:
1. 目标:消除存在高风险可能的地方
措施:为所有机器设置安全罩及隔离区
2. 目标:降低中风险可能性
措施:为所有操作人员提供安全装备,并制定详细操作规程
3. 目标:杜絕低风险事件的發生
措施:开展安全培训及作业管制
三、实施计划
1. 责任单位:安全管理部门
2. 实施日期:2021年6月1日-2021年8月31日
3. 具体任务安排:参照附件
4. 资源保障:根据实施计划安排所需人力、物力支持
四、效果评估
实施完工后使用相同的评估表对现场进行再评估,调查员工意见,检查达成情况,并写出评估报告。
以上为一份简单的"现场改善计划和行动计划"样本,实际应根据企业的实际情况进行修改完善。
品质现场改善方案

品质现场改善方案背景在制造业企业中,提高产品质量和生产效率是企业不断发展的核心目标之一。
然而,由于复杂的生产流程和制造环境,实现这一目标是比较困难的。
然而,采用现场改善方案可以提高产品质量和生产效率,对企业的发展具有积极的意义。
现场改善的优点现场改善是一种通过持续改善和优化生产流程和制造环境,提高质量和效率的方法。
它的优点如下:1.提高产品质量:通过现场改善,可以及时发现和解决生产中的问题,减少缺陷率和损失。
2.提高生产效率:现场改善能够优化生产流程和制造环境,提高生产效率,降低成本,提高利润。
3.增强员工意识:通过现场改善,员工可以深刻地认识到生产环节中的问题,在持续改善的过程中不断学习和成长。
现场改善的步骤现场改善是一种系统的方法,它包括以下几个步骤:1.观察:通过观察生产过程和环境,发现问题和不足。
2.分析:对问题和不足进行深入分析,找出根本原因。
3.解决:通过提出和实施改善方案,解决问题和不足,达到持续改善的目的。
4.检查:对改善方案进行评估和检查,发现问题和不足并持续改进。
实施品质现场改善方案的建议在实施品质现场改善方案时,建议遵循以下几个原则:1.确定目标和可行性:在实施品质现场改善方案前,需要明确目标和可行性,分析其影响和成本,确定实施方式和时间。
2.建立协作机制:在实施品质现场改善方案过程中,需要建立协作机制,包括形成改善团队,明确任务和责任,以及确保信息沟通和汇报等。
3.关注质量细节:在实施品质现场改善方案时,需要关注质量细节,包括设备状态、环境卫生、员工工作状态等,确保所有因素都得到优化。
4.持续改进:品质现场改善并非一次性的活动,需要持续改进。
在实施品质现场改善方案后,需要对效果进行评估和反馈,并根据结果制定下一步的改进计划。
总结品质现场改善方案是提高产品质量和生产效率的重要方法。
在实施改善方案时,需要遵循一定的步骤和原则,监督质量细节,持续改进。
通过品质现场改善方案,企业可以不断提高其竞争力和市场占有率,实现长期的稳定发展。
现场改善方案及几点建议ppt

通过采用精益生产理念和工具,加强 现场管理和人员培训,提高员工素质 和技能水平,实现生产过程的可控和 稳定,提高生产效率和产品质量。
实施改善方案后,生产效率和产品质 量得到了显著提升,缩短了产品交货 期,提高了客户满意度,为公司创造 了更大的经济效益和社会效益。
对未来工作的展望
进一步完善生产流程和设备布局,持续优化生产计划 和物料管理,实现生产过程的进一步优化和提升。
03
提高生产安全性
自动化设备可以提高生产安全性,减 少工伤和职业病的发生率。
改善方案三:优化现场布局
提高空间利用率
通过合理的现场布局设计,可以提高空间利用率 ,降低生产成本。
提高物流效率
通过合理的现场布局设计,可以提高物流效率, 降低物流成本。
提高员工工作效率
通过合理的现场布局设计,可以提高员工工作效 率,提高生产效益。
03
对改善方案的几点建议
加强员工培训和意识教育
总结词
详细描述
提升员工技能与素质
总结词
通过定期的内部培训、外部培训以及在线学 习,提高员工的专业技能和综合素质,增强 员工的生产效率意识。
详细描述
培养自主管理意识
推行员工自主管理,培养员工的主人翁意识 ,提高员工发现问题、解决问题的能力,降 低生产事故发生率。
深入推进精益生产理念和工具的应用,扩大精益管理 的覆盖面,提高公司的整体精益管理水平。
加强与供应商的合作与协调,推动供应商参与改善, 降低采购成本和库存成本。
加强员工的培训和教育,提高员工的素质和技能水平 ,培养一支高素质、高效率的优秀员工队伍。
THANK YOU.
2023
现场改善方案及几点建议
目录
• 引言 • 现场改善方案 • 对改善方案的几点建议 • 结论
生产现场改善方案

生产现场改善方案生产现场改善是指通过不断优化和改进生产现场的各种因素,以提高生产效率、降低生产成本、提升产品质量和保障员工安全等目标的一系列措施。
在生产现场改善中,我们可以采取以下方案来提升生产效率和质量。
一、标准化工作流程标准化工作流程是生产现场改善的基础,它可以确保每一项工作都按照固定的程序进行,并且能够无差错地完成。
通过标准化工作流程,可以减少工作中的浪费和瑕疵,提高生产效率和质量。
标准化工作流程的实施需要进行详细的工作流程分析和标准操作程序的制定,包括设备设置、原材料准备、工艺操作、质量检验等各个环节。
同时,还需要进行相关员工培训,确保每一位员工都能够准确地遵循标准操作程序进行工作,并且能够熟练地应对各种工作场景。
二、自动化设备的应用在现代生产中,自动化设备的应用可以大大提高生产效率和质量。
自动化设备能够取代人工操作,减少人为的误差和疲劳,提高生产效率,减少生产时间。
同时,自动化设备能够提供更高的精确度和稳定性,减少产品瑕疵率,提高产品质量。
在引入自动化设备时,需要评估投资回报率,并进行详细的设备选型和安装调试。
同时,还需要进行相关员工培训,让员工熟练掌握自动化设备的操作和维护,确保设备的正常运转。
三、现场布局的优化现场布局是生产现场改善的重要内容之一,它能够影响到生产效率和安全性。
通过优化现场布局,可以减少物料和人员的移动距离,缩短物料和信息的传递时间,提高生产效率。
同时,优化现场布局还能够提高生产现场的安全性,减少事故发生的概率。
在优化现场布局时,需要进行详细的现场调研和分析,了解现场的工作流程和各个设备之间的关系。
同时,还需要考虑人员的工作条件和安全要求,合理分配工作空间和通道。
最后,需要进行现场布局的调整和改进,确保布局的合理性和可行性。
四、供应链管理的优化供应链管理是生产现场改善的重要组成部分,它关系到物料的准时供应、库存的控制和质量的保障。
通过优化供应链管理,可以提高物料的及时性和准确性,减少物料的浪费和停工现象。
品质现场改善方案

品质现场改善方案前言现场品质作为制造企业的关键指标之一,是客户评价企业产品质量的重要因素。
企业预计和满足客户的品质需求、加强品质管理和品质改进,提高品质水平和品牌竞争力就显得尤其重要。
因此,我们需要制定一些现场品质改善方案,并在实践中不断完善。
现状在目前的生产实践中,我们发现以下一些问题:1.产品品质不稳定,存在较大波动。
2.现场操作人员不熟练,操作规范不统一。
3.机器设备维护不到位,设备故障率较高。
4.现场管理不规范,缺乏品质意识。
问题1:产品品质不稳定在生产现场,我们经常会发现产品品质存在较大波动的情况。
有时,产品在生产过程中的某些环节出现了问题,导致产品品质下降。
而另一些时候,产品的品质稳定性并不好,同一批次的产品在品质方面存在较大差异。
这些问题都严重影响了产品质量,降低了客户满意度,同时也影响了公司的声誉和市场竞争力。
问题2:现场操作人员不熟练现场操作人员在生产过程中负责设备操作和产品加工等关键环节。
如果操作人员缺乏必要的技能和经验,不仅会出现操作失误,还可能影响产品的品质。
在日常实践中,我们发现一些操作人员存在操作疏忽的情况,可能会让某些产品出现问题,增加了后续处理难度和产品成本等。
问题3:机器设备维护不到位在生产过程中,机器设备维护是非常关键的一环。
如果机器设备维护不到位,就容易出现机器设备故障、停机等问题。
这些问题不仅会影响生产效率,还会对产品品质产生不良的影响。
因此,对机器设备的维护和管理必须高度重视。
问题4:现场管理不规范现场管理是保证产品质量的重要保障。
我们发现在现场生产过程中,有时候操作规范不统一、现场管理混乱,有些操作员根据习惯操作或者因为管理不到位,而不按规定操作。
这些问题都严重影响了品质的稳定性和改进效果。
改善方案针对上述问题,我们有以下改善方案:方案1:品质监控为了确保产品品质的稳定性,我们需要加强品质监控环节,让每一个产品都能被全面地监测并记录。
针对具体的产品制造过程,需要细分并量化主要关键参数,确保过程符合产品品质要求。
生产车间现场改善方案
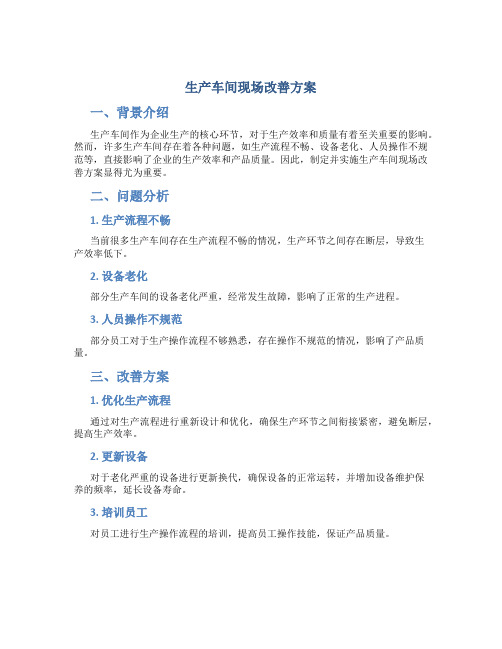
生产车间现场改善方案一、背景介绍生产车间作为企业生产的核心环节,对于生产效率和质量有着至关重要的影响。
然而,许多生产车间存在着各种问题,如生产流程不畅、设备老化、人员操作不规范等,直接影响了企业的生产效率和产品质量。
因此,制定并实施生产车间现场改善方案显得尤为重要。
二、问题分析1. 生产流程不畅当前很多生产车间存在生产流程不畅的情况,生产环节之间存在断层,导致生产效率低下。
2. 设备老化部分生产车间的设备老化严重,经常发生故障,影响了正常的生产进程。
3. 人员操作不规范部分员工对于生产操作流程不够熟悉,存在操作不规范的情况,影响了产品质量。
三、改善方案1. 优化生产流程通过对生产流程进行重新设计和优化,确保生产环节之间衔接紧密,避免断层,提高生产效率。
2. 更新设备对于老化严重的设备进行更新换代,确保设备的正常运转,并增加设备维护保养的频率,延长设备寿命。
3. 培训员工对员工进行生产操作流程的培训,提高员工操作技能,保证产品质量。
四、实施步骤1. 制定改善计划根据问题分析,制定具体的改善方案和实施计划。
2. 落实责任人明确改善方案的责任人,确保改善工作有序进行。
3. 实施改善方案按照制定的改善方案,逐步实施生产车间现场改善工作。
4. 监督检查定期对改善工作进行监督检查,及时发现问题并采取措施纠正。
五、改善效果评估1. 生产效率提升优化生产流程和更新设备,生产效率得到提升,产能得到增加。
2. 产品质量提高员工操作水平提升和设备更新,产品质量得到提高,消除了质量问题带来的损失。
3. 员工满意度提升通过培训员工,提高了员工的工作技能和工作积极性,增加了员工的满意度。
六、结语生产车间现场改善是企业提高生产效率和产品质量的一个重要举措,通过优化生产流程、更新设备和培训员工,可以实现生产车间的现场改善,对于企业的发展具有重要意义。
希望以上改善方案能够为企业的生产车间改善工作提供一定的参考和指导。
现场改善方案及几点建议

减少不良品率
加强原材料质量控制
01
严格把控原材料质量,从源头控制产品质量。
引入精益生产理念
02
通过引入精益生产理念,优化生产工艺,减少生产过程中的浪
费。
加强员工技能培训
03
定期对员工进行技能培训,提高员工技能水平,降低操作失误
率。
提升员工技能和素质
制定完善的培训计划
根据员工岗位需求,制定完善的培训计划,提高员工技能水平。
定期组织班组长培训学习,提高 班组长的管理能力和技能水平。
实践锻炼
让班组长参与实际管理工作,通过 实践锻炼提高管理能力。
经验交流
组织班组长之间进行经验交流,分 享管理经验和方法,共同提高。
03
员工培训与激励
加强员工技能培训
岗前培训
在新员工入职时,提供岗位技能、职责等方面的 培训,确保员工具备基本的业务能力和知识。
THANKS
感谢观看
整理
定期清理现场,去除不必要的 物品,保证现场空间的有效利 用。
清扫
保持工作区域的清洁卫生,为 员工创造良好的工作环境。
素养
提高员工素质,培养良好习惯 ,形成积极向上的工作氛围。
定期检查设备维护情况
定期检查
对设备进行定期检查,及 时发现并解决潜在问题。
维护保养
按照设备保养规范进行保 养,延长设备使用寿命。
04
结论与展望
总结现场改善方案及建议
总结方案
通过对现场进行全面细致的观察和分析,我们提出以下几项 改善方案:改进生产流程、优化设备布局、提高员工技能和 意识、加强质量控制等。这些方案旨在提高生产效率、减少 浪费、降低成本并提高产品质量。
建议
5S现场改善方案

5S现场改善方案5S现场改善方案是一种提高工作环境和效率的方法,其名称来自于五个日语单词的首字母,包括整理 (Seiri)、整顿 (Seiton)、清洁(Seiso)、清楚 (Seiketsu) 和素养 (Shitsuke)。
下面是一个关于如何实施5S现场改善方案的建议。
整理 (Seiri):第一步是去除和清理所有不必要的物品,只保留必需的物品。
这可以通过对工作区进行仔细检查,并将不再需要的物品标记出来、搬出工作区来实现。
这样可以减少杂物堆积,提高工作效率。
整顿 (Seiton):清洁 (Seiso):保持工作区域的清洁和整洁是5S现场改善方案的重要一环。
每个员工都应该负责保持自己的工作区域的清洁,并定期进行全面清洁。
这不仅可以提高工作效率,还可以改善安全性和员工的工作环境。
清楚 (Seiketsu):素养 (Shitsuke):素养是5S现场改善方案的最后一步,意味着培养好的习惯和行为。
员工应该经过培训和教育,以了解5S的原则和重要性,并在工作中将其付诸实践。
此外,管理层应该提供支持和激励措施,以鼓励员工坚持这些良好的习惯。
为了成功实施5S现场改善方案,以下是一些建议和步骤:1.制定计划:确定实施5S方案的目标、时间表和相关资源。
明确责任分工和参与人员。
2.培训员工:向所有员工提供有关5S原则和实施的培训。
确保他们理解5S的重要性和所需的行为和习惯。
3.进行现场评估:对工作区进行详细评估,确定需要进行整理和整顿的区域和物品。
4.实施整理:将不需要的物品清除出工作区。
对于需要留下的物品,为其分配适当的位置。
5.实施整顿:使用合适的容器和工具,为每个物品提供固定位置,并确保每个员工能够方便地找到和使用所需的物品。
6.实施清洁:要求每个员工负责保持自己的工作区的清洁,并定期进行全面清洁。
7.确保清楚:制定标准化程序和方法,确保所有员工遵守这些标准。
8.强化素养:通过奖励和认可良好行为来激励员工,鼓励他们继续保持好的习惯和行为。
5S现场改善的方案
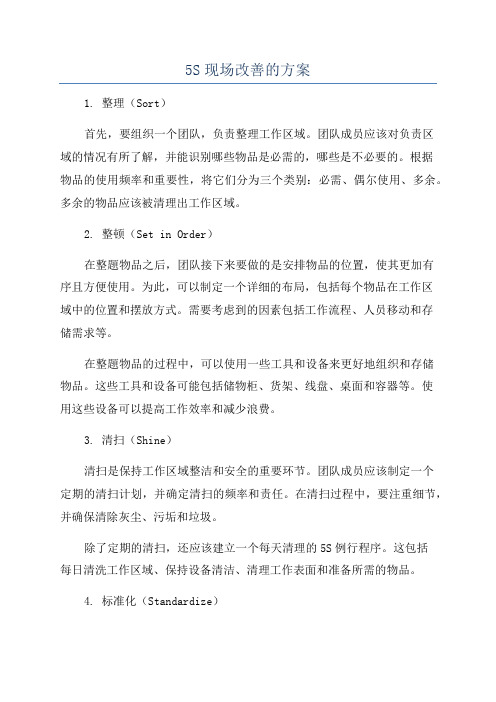
5S现场改善的方案1. 整理(Sort)首先,要组织一个团队,负责整理工作区域。
团队成员应该对负责区域的情况有所了解,并能识别哪些物品是必需的,哪些是不必要的。
根据物品的使用频率和重要性,将它们分为三个类别:必需、偶尔使用、多余。
多余的物品应该被清理出工作区域。
2. 整顿(Set in Order)在整題物品之后,团队接下来要做的是安排物品的位置,使其更加有序且方便使用。
为此,可以制定一个详细的布局,包括每个物品在工作区域中的位置和摆放方式。
需要考虑到的因素包括工作流程、人员移动和存储需求等。
在整題物品的过程中,可以使用一些工具和设备来更好地组织和存储物品。
这些工具和设备可能包括储物柜、货架、线盘、桌面和容器等。
使用这些设备可以提高工作效率和减少浪费。
3. 清扫(Shine)清扫是保持工作区域整洁和安全的重要环节。
团队成员应该制定一个定期的清扫计划,并确定清扫的频率和责任。
在清扫过程中,要注重细节,并确保清除灰尘、污垢和垃圾。
除了定期的清扫,还应该建立一个每天清理的5S例行程序。
这包括每日清洗工作区域、保持设备清洁、清理工作表面和准备所需的物品。
4. 标准化(Standardize)标准化是确保整理、整顿和清扫工作持续进行的一种方法。
为此,可以制定一套标准化的程序和作业指导书,并确保团队成员遵守。
作业指导书可以包括物品的分类标准、清扫的频率、布局的要求和工具的使用等。
除了作业指导书,还可以建立一套报告和评估机制,以确保5S程序的有效性和持续改进。
定期的例行检查和审查可以帮助发现问题,并采取相应的改进措施。
5. 素养(Sustain)保持5S程序的成功需要团队成员的积极参与和持续努力。
为此,可以制定一套培训计划,以提高团队成员的5S素养和意识。
培训内容可以包括5S方法的基本原理、操作技巧和反馈机制等。
此外,还可以设立鼓励机制,激励团队成员积极参与5S改善活动。
鼓励可以采取多种形式,包括表彰、奖励和晋升等。
现场改善方案及几点建议
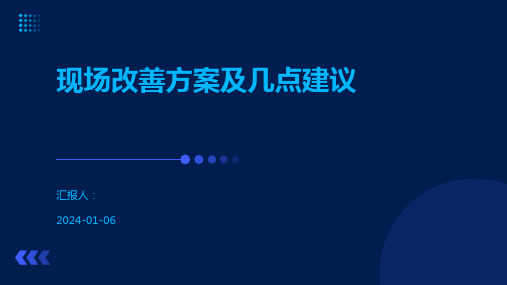
持续改进
根据评估结果和生产实际情况,对标准作业 指导书进行持续改进。
目视化管理
标识管理
对现场物品、区域、设备等进 行明确标识,方便识别。
颜色管理
利用不同颜色区分物品、区域 或状态,提高视觉效果。
图形管理
利用图表、图示等形式展示数 据、流程等信息,便于理解。
看板管理
设置看板,展示关键指标、目 标、计划等信息,提高管理效
03
设备与工装管理
设备维护保养
定期检查
制定设备检查计划,定期对设备进行全面检查,确保 设备处于良好状态。
预防性维护
实施预防性维护,定期更换易损件,清洗和润滑关键 部位,预防设备故障。
应急维修
建立应急维修机制,对突发故障进行快速响应和处理 ,尽快恢复生产。
工装夹具优化
分析和改进
对现有工装夹具进行分析,找出 存在的问题和改进点,进行优化
率。
02
人员培训与激励
培训计划
01
定期培训
制定定期培训计划,确保员工不 断更新知识和技能,提高工作效 率。
针对性培训
02
03
培训效果评估
根据员工的岗位和职责,提供针 对性的培训课程,以满足工作需 求。
对培训计划进行定期评估,了解 员工的学习成果,以便调整培训 内容和方式。
激励机制
薪酬激励
提供具有竞争力的薪酬福利,激发员工的工作积极性和创造力。
建立应急预案,组织应急演练,提高应对突发事 件的能力。
环境因素控制
识别现场环境因素,评估其对 环境的影响,制定相应的控制
措施。
加强废弃物分类、回收和处 理工作,减少对环境的污染
。
合理利用资源,降低能源消耗 ,提高能源利用效率。
现场改善方案及几点建议

合理安排生产设备、物料、工具等的布局,减少员工走动距离和时 间,提高工作效率。
加强现场沟通与协调
加强与员工的沟通与协调,及时解决现场问题,确保生产顺利进行 。
引入先进技术,提升产品质量
采用先进的生产设备和技术
引入先进的生产设备和技术,提高生产效率和 产品质量。
实施质量管理体系
建立完善的质量管理体系,确保产品质量符合 要求,提高客户满意度。
THANKS
谢谢您的观看
04
总结与展望
总结本次改善方案及建议的成果
提升生产效率
通过优化生产流程和减少浪费 ,现场改善方案成功提高了生
产效率。
提高产品质量
通过改进生产工艺和加强质量 控制,现场改善方案有助于提 高产品质量。
降低成本
通过减少原材料浪费和能源消 耗,现场改善方案有效降低了 生产成本。
增强员工参与度
通过员工参与改进过程,现场 改善方案增强了员工的归属感
通过培训和实践,提高员 工的技能水平和操作熟练 度。
培养员工安全意识
加强员工的安全培训,提 高员工的安全意识,减少 事故发生。
建立激励机制
通过建立激励机制,激发 员工的工作积极性和创造 力。
03
几点建议
加强现场管理,提高工作效率
制定合理的生产计划和流程
根据市场需求和产能,制定合理的生产计划和流程,减少生产中 的停顿和等待时间,提高工作效率。
加强质量意识培训
加强员工的质量意识培训,让员工认识到质量的重要性,提高员工对产品质量 的责任心。
加强员工培训,提高员工素质
加强技能培训
加强员工的技能培训,提高员作精神,提高团 队合作效率。
建立激励机制
现场改善方案及几点建议

Luzhou Detian Ceramics Co., Ltd
何志 2016.6.27
尊敬的刘总、李总并各位领导:
本人加入得天陶瓷已一个多月的时间。期间耗时半个月对公司所有车间的生产流
程有了一个初步的熟悉,对于公司的工艺流程及生产管理现状已经有了一个初步的认识。后 定职于整个公司最重要也是最关键的成型车间,在此期间发现了一系列急需改善的问题点。 根据本人以前的工作经验,拟定了部分的改善思路与几点建议。由于本人以前未接触过陶瓷 行业,肯定存在诸多认识不到位之处,还望各位领导指教。 以上 何志 2016.6.27
排拉方式:
通过现场实测数据分析,此排拉的瓶颈岗位在于精坯外观全检。 瓶颈岗位时间:N/T=6.46S 标准工时:3600S/6.5S=553个; 若每日上班8H,其中,作业时间7.5H,则全天产能为7.5H*553个=4153个; 若按现阶段产能,共需6组人完成每日25000的产能; 目前仅有4人,实行抽检的方式,若导入全检,则总人力需求为6组*2人=12人,需求8人; 增加的人力成本: 全检人员采用计时的方式,若每人每月2000元工资,则月增加人力成本2000*8=16000元; 若采取全检的方式,其他不看,仅瓶底泥渣一项就提升大约2%的成瓷良率水平。减 少报废的件数:25000*0.02=500件;每月节省500件*30天=15000件; 假设成瓷的报废成本为2元/个,则减少报废15000件*2元=30000元,相比人力成本支出可节约 公司成本30000元-16000元=14000元。 故根据以上数据得出结论,必须在精坯检导入全检的方式,以提升成瓷的良率水平。 若成型的制程改善比较明显,能大大提升直通率,才可考虑由全检变更为抽检。这样才 能最大限度的为公司节省成本。若导入流水线,则可将全检集成在流水线,这样成型车间的 精坯可直接到达烧成车间,进入窑炉烧制,提高坯架车周转效率。
品质现场改善方案

品质现场改善方案背景品质控制是任何企业的重要部分。
无论何时,都需要不断努力来确保产品和服务的质量达到最高水平。
本文将提供一些品质现场改善方案,帮助企业在现场操作过程中提高生产效率和品质。
现场改善方案1. 排序在品质控制过程中,排序是一个关键的步骤。
通过将产品分类为良品、次品和废品,并对每种品质类型进行归类,可以在生产线上及时识别和处理不合格品,并及时作出决策。
同时,排序也可以帮助提高员工对产品的关注和认识程度,更好地推动品质改善工作。
2. 停止生产并深入调查当出现产品不合格的情况时,立即停止生产并深入调查,找出问题的根本原因,并制定具体的解决方案。
为了确保迅速解决问题,建议成立品质问题解决小组,并在问题发生后立即启动解决程序。
3. 引入新技术和新设备对于一些品质问题,可能需要引入新的技术和设备来解决。
例如,引入新的工艺和生产设备,可以提高生产效率和生产质量。
此外,通过引入新的质量控制工具和测试方法,可以帮助企业更好地监管产品品质。
4. 更改员工工作方式员工的态度和工作方式对产品质量的影响是不可小觑的。
在品质改善过程中,企业应该通过培训和奖励机制等方式,激励员工更好地投入工作,并改变不良的工作态度,保证产品品质卓越。
5. 进行标准化管理品质标准是决定产品质量的关键。
对于具有复杂产品结构的企业,建立完整的标准化管理体系非常必要。
通过标准化管理,可以制定统一的品质标准,建立完整的品质控制流程,并确保生产的每一个环节都符合标准要求。
结论以上是一些品质现场改善方案,希望为企业提高生产效率和产品品质提供帮助。
品质控制不是一个静态过程,而是需要与时俱进,不断寻求新的创新方法。
只有建立一个完整的品质控制系统,才能确保产品品质卓越,最终赢得市场竞争优势。
- 1、下载文档前请自行甄别文档内容的完整性,平台不提供额外的编辑、内容补充、找答案等附加服务。
- 2、"仅部分预览"的文档,不可在线预览部分如存在完整性等问题,可反馈申请退款(可完整预览的文档不适用该条件!)。
- 3、如文档侵犯您的权益,请联系客服反馈,我们会尽快为您处理(人工客服工作时间:9:00-18:30)。
3、精坯检验重新排拉布线(导入全检)
从品质部每日数据中选取一周的数据得知成瓷的良率仅78.34%。个人认为主要的原因为 成型的检验采用抽检的方式,我觉得这是很不合理的。因为在进素烧窑之前所有的报废品都 是可以走返工流程的,期间的成本损耗相对较少(仅有水电+人工成本),但素烧成瓷后,所 有的产品只有倒入垃圾堆,变成实实在在的公司成本损失(水电气+人工+原料+窑炉等部分设 备折旧)故在采取制程验证改善前五项不良的基础之上,在精坯导入全检的方式,将不良品 尽可能多的拦截下来,该返修的返修,该送原料车间的送入原料车间走FA流程,以提高后段 的直通率水平。
2、流水线的初步评估
其实最有效的工作流程优化是导入流水线作业,故也初步进行了流水线导入的评估。
1、两条线实际嫁动时间9.5H;两条线最低产能=2*13200=26400;(跑顺后正常产能为27470+) 2、两条线人力需求:24*2=46人;以上岗位车间现有人力56人,节省10人,多余的人力可以进行产线轮休安排,保证员工休息时间充足。 3、以上排拉布线方法为现阶段的工作效率,随着员工工作熟练度的提升,产能只会越来越高。建议按此方式进行排拉。 目前的问题点: 1、员工工资的计算方式变更,由于是流水线,无法较好的统计单人产量,建议按照团体完成的产量计算工资。 2、员工的工资模拟,需拿出一定的数据进行模拟,然后与现在的工资进行对比,若工资更高或持平则可以导入,否则员工意见会较大。 3、洗坯处需重新设计水管布线方式,工程量较大,需工程部门评估。 导入的好处: 1、由于工序细分,则管理可以做到更加精细化,从而保证产品质量的稳步提升。减少修洗坯的批量性质量问题发生的几率。
以上
何志 2016.6.27
目录:
第一部分、成型车间工作改善
第二部分、公司层面建议事项
精益生产推行—洗坯流程优化、流水线导入、
精坯检验导入全检
实行班长巡检工作流程 全制程验证改善不良 车间目视化改善-6S与看板管理 员工培训改善
技术部增加当站PE--工艺工程师/技术员 增加每日生产例会-各部门提高工作效率 增加IPQC起到过程监督的作用 厂房改造以降低车间温度--留住人员 员工正激励机制重新修订
第一部分、成型车间工作改善
一、精益生产推行
1、洗坯工作流程优化 目前整个成型车间全部是分站式作业,比如洗坯的员工,同一车产品要做四道工序: 修坯体--->磨瓶颈--->洗瓶口、量尺寸,再将已喷釉的产品拉来进行洗坯。整个流程全 部由一个作业员完成。在不停的从坯架车上取放造成动作浪费。故考虑将该工序人员重新排 拉组合,以流水方式完成这三道工序,最大程度的减少搬运的距离、频繁的动作浪费。且让 员工的操作越来越简单,有助于工作效率的提升。
2、缩短成型车间产品生产周期1天左右。(现阶段产品生产周期基本在3天左右,改善后生产周期基本在2天左右) 3、所有装满产品的坯架车只有4个状态,粘接后待修坯、修坯后待烘烤、烘烤后待投流水线、精坯待转素烧窑。便于进行区域规划,利于成型车间的
6S改善。 4、可考虑增设IPQC的岗位,便于进行制程巡检管控,有利于质量的提升。 5、导入流水线可考虑增加气枪吹瓶口的动作,消除瓶底/瓶颈内泥渣(此项已验证可行,可将除多余粘接料外的所有注浆、粘接掉入的泥渣清除干净) 6、流水线导入可在线尾部增加自动气枪,专门吹除瓶口外部泥渣,效果较好(此项已验证可行,能有效吹除瓶口外部残余泥渣) 7、中间各工序可以省去部分坯架车的积压,提高坯架车的周转效率。
N/T
标准工时
洗坯
19.9
15.9
27.2
13.7
25.8
16.2
18
15.5
16.1
19.5 18.78 18.78
192
由以上数据可知:
洗坯的标准产能为192个/H,若每日工作7.5H,则全天产能为192*7.5=1440个。
若需完成25000以上产能,则需要17人。
以上排拉修坯人员总数需求为17+21=38人平均上班8H可完成每日25000的产能目标。
这只是基于目前的现状所测得的数据,其实一线操作人员的操作越简单越好,每天都在
做同样的简单工作,对于技术的熟练度提升是有相当大的帮助。
优点: 极大的提高员工的工作效率,减少人员配置: 目前的现状洗坯的员工需要40人工作10H才能完成当天2.5W精坯的目标,现在38人在8H
就能完成。如果将工作时间提高到目前的10H,有效嫁动时间为9.5H: 修坯体的人员6组即18人就可完成当日产量目标,节约3人; 洗坯的人员由17人减少为14人,节约3人; 综上所述:一共节约6人。这只是基于现状的数据所计算出来,随着员工动作的单一、效
泸州得天陶瓷有限公司
Luzhou Detian Ceramics Co., Ltd
何志 2016.6.27
尊敬的刘总、李总并各位领导:
本人加入得天陶瓷已一个多月的时间。期间耗时半个月对公司所有车间的生产流 程有了一个初步的熟悉,对于公司的工艺流程及生产管理现状已经有了一个初步的认识。后 定职于整个公司最重要也是最关键的成型车间,在此期间发现了一系列急需改善的问题点。 根据本人以前的工作经验,拟定了部分的改善思路与几点建议。由于本人以前未接触过陶瓷 行业,肯定存在诸多认识不到位之处,还望各位领导指教。
率会提升得比较明显,后期所需的人力只会更少。 目前的困难点:
由于公司本工序采用的是计件方式,若导入可能工资的计算方式会进行调整,由个人计 件变更为小组计件。对于各组员工速度的匹配度在管理上增加了一定的难度。
这只是成本最低的方案,最优化的方案是导入流水线,将烘烤完毕之后的所有工序导入流 水线作业的模式,最大限度的提高产品的周转效率、降低动作浪费和搬运的浪费。
4.9
7.7
5.9
6.1
7.1
5.8
6.9
5.1
6.2
由以上数据可知: 瓶颈岗位为修坯,一组三人每小时标准产能为489个。 若每日工作7.5H,则全天产能为489*7.5=3667个。 若每日完成25000以上,则需要7组人力,共计21人。
工序
第1次 第2次 第3次 第4次 第5次 第6次 第7次 第8次 第9次 第10次 T/T
工序 修坯 磨瓶颈 洗瓶口,量尺寸
第1次 第2次 第3次 第4次 第5次 第6次 第7次 第8次 第9次 第10次 T/T
N/T
标准工时
7.6
6.4
7.5
5.9
7.6
9.1
7.2
8.9.6
5.3
5.5
8.6
6.3
5.5
5.9
6.3
5.3
5.94
7.36
489
5.7
6.8